
Технология No17
.pdfЛабораторная работа № 17 ПАРАМЕТРЫ СВАРКИ И НАПЛАВКИ И МЕТОДИКА ИХ ОПРЕДЕЛЕНИЯ
1.Цель работы
Изучить основные характеристики процесса плавления электродного материала при ручной сварке и наплавке покрытыми электродами, влияние на них рода и силы тока, марки электродов.
2. Общие сведения и указания по работе
Сварку применяют для устранения механических повреждений в деталях (трещин, отколов, пробоин), а ни плавку — для нанесения металлических покрытий на поверхности деталей с целью компенсации их износа
Сварка — это процесс получения неразъемного соединения посредством установления межатомных связей между соединяемыми частями при их нагревании или пластическом деформировании.
Наплавка — нанесение слоя расплавленного металла на пил пиленную металлическую поверхность путем плавления присадочного материала теплотой кислородно-ацетиленового примени, электрической или плазменной дугой и др.
При сварке покрытыми электродами наплавляемый металл и прилегающие к нему участки основного металла нагреваются до температуры плавления. При этом в наплавленном и основном металле протекают процессы, которые оказывают влияние на качество восстанавливаемых деталей. К ним относятся металлургические процессы, протекающие в наплавленном металле, структурные изменения и образование внутренних напряжений и деформации в основном металле.
В процессе плавления металла протекают следующие металлургические процессы: окисление металла, насыщенно его азотом и водородом, выгорание легирующих элементов.
Окисление наплавленного металла и выгорание легирующих элементов (углерода, марганца, кремния и др.) происходят в результате соединения их с кислородом воздуха. Из воздуха в наплавленный металл проникает также азот, который образует нитриды, несколько повышающие предел прочности металла, но ухудшающие его пластичность. Для защиты металла от окисления, выгорания легирующих элементов и насыщения азотом при сварке и наплавке применяют электродные обмазки и флюсы, которые при плавлении образуют шлак, надежно изолирующий металл от окружающей среды. Хорошие результаты также дает сварка в среде защитных газов.
Насыщение металла водородом повышает пористость и плавленого металла и способствует возникновению в нем значительных внутренних напряжений. Водород проникает в наплавленный металл из влаги, которая содержится в гигроскопичных электродных обмазках и флюсах, поэтому перед употреблением их рекомендуется просушивать.
Разбрызгивание металла при сварке и наплавке происходит в результате восстановления окислов железа углеродом. При этой реакции образуются углекислый и угарный газы, которые интенсивно расширяются, разбрызгивая расплавленный металл, увеличивая потери присадочного металла. Чтобы уменьшить разбрызгивание рекомендуется при сварке применять электроды с пониженным содержанием углерода, тщательно очищать детали от окислов и вводить в состав электродных обмазок и флюсов вещества, содержащие раскисляющие элементы (марганец, кремний).
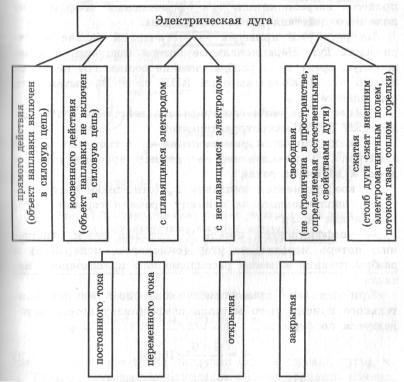
Структурные изменения в основном металле возникают вследствие неравномерного нагрева детали в околошовной зоне (зоне термического влияния), в результате чего механические свойства металла в ней снижаются. Размеры зоны термического влияния зависят от теплофизических свойств свариваемого металла, способа сварки и ее режима. Наибольшие размеры зона термического влияния имеет при газовой сварке (до 25—30 мм). При дуговой сварке она значительно меньше и составляет 3—5 мм. С увеличением сварочного тока, напряжения и мощности сварочной дуги зона термического влияния увеличивается, а с увеличением скорости сварки уменьшается. Размеры зоны термического влияния можно значительно уменьшить правильным выбором режимов сварки и наплавки.
Внутренние напряжения и деформации возникают в деталях в результате неравномерного (местного) нагрева и структурных превращений, происходящих в зоне термического влияния. Местный нагрев детали и структурные изменения в металле вызывают локальное изменение объема металла, которое создает условия для возникновения внутренних напряжений. Если внутренние напряжения превышают предел текучести материала детали, то возникают деформации. Внутренние напряжения и деформации могут быть значительно снижены путем нагрева деталей перед сваркой, медленного охлаждения после сварки, а также путем применения специальных приемов сварки и наплавки.
Наиболее распространенным источником тепла при сварке является электрическая дуга, которая представляет собой электрический разряд в газах, возбуждаемый и поддерживаемый между наплавляемой поверхностью и электродом. Электропроводность газа обусловлена электронами и ионами, возникающими при его термической ионизации и упорядоченно движущимися в столбе дуги. Степень ионизации составляет несколько процентов. Такой ионизированный газ называют низкотемпературной плазмой. Кинетическая и потенциальная энергия частиц плазмы преобразуется в тепловую и приводит к плавлению основного, электродного или другого присадочного материала. Классификация электрических дуг при сварке и наплавке приведена на рис. 17.1
Рис. 17.1. Классификация электрических дуг
Для характеристики дуги как источника энергии принят ряд параметров. Один из них
—мощность, которую рассчитывают по формуле
|
Ψ Uд в, |
(17.1) |
где Ψ — |
корректирующий коэффициент; |
|
Uд — |
напряжение дуги, В; |
|
в— |
сила тока, А. |
|
При наплавке используется не вся мощность дуги, а лишь ее часть, которую называют
эффективной мощностью и определяют но формуле |
|
эф |
(17.2) |
где — эффективный коэффициент полезного действия процесса нагрева детали или эффективный коэффициент полезного действия источника нагрева.
На рис. 17.2 приведен энергетический баланс электрических дуг. Нерациональные потери мощности в окружающую среду и на разбрызгивание составляют не менее 20 — 25 % . Наиболее высокий КПД имеет закрытая дуга под флюсом.
Процесс плавления электрода под действием дуги оценивается рядом макрохарактеристик:
—коэффициентом расплавления р (отношение массы электрода,
расплавленного за единицу времени горения дуги, к величине тока);
—коэффициентом наплавки н (отношение массы металла, наплавленного за
единицу времени горения дуги, к величине тока);
— коэффициентом потерь Ψ, который равен отношению потерь металла на угар (окисление, испарение) и разбрызгивание к массе расплавленного присадочного металла.
При наплавке плавящимся электродом без дополнительного присадочного металла коэффициент потерь определяется по формуле
Ψ |
н |
· 100 % |
(17.3) |
|
|||
|
|
|
где G — количество расплавленного электродного металла, г;н — количество наплавленного металла, г.
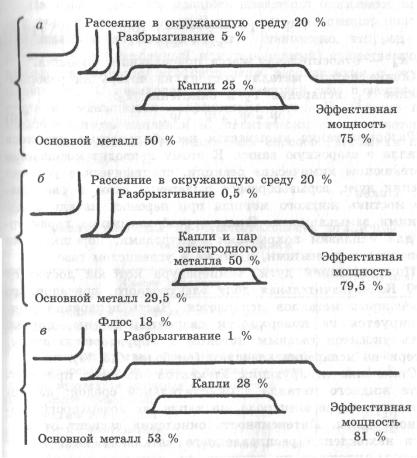
Рис. 17.2. Энергетический баланс электрической дуги при различных способах наплавки:
а — плавящимся электродом в открытой атмосфере; б — в среде аргона; в — под флюсом
Подставив в формулу значения для G и н получим
Ψ |
р в н в ! |
1 " |
н |
! · 100 |
(17.4) |
|
|
||||
|
р в |
|
р |
|
где t — основное время наплавки (время горения дуги), ч.
Если в качестве дополнительного присадочного материала используется металлический порошок,
Ψ 1 " |
н |
! · 100 (17.5) |
|
||
|
р#$п! |
где &п — относительная масса присадочного порошка.
Общие потери металла состоят из потерь на разбрызгивание Ψ , испарение Ψ' и
окисление Ψ(: |
|
Ψ Ψ * Ψ'+Ψ( |
(17.6) |

Разбрызгивание вызывается нестабильностью переноса металла в сварочную ванну. К этому приводят интенсивно протекающие химические реакции, специфические условия горения дуги, взрывообразное выделение газов и разрушение мостика жидкого металла при переносе капель с короткими замыканиями. Сильное разбрызгивание характерно для наплавки покрытыми электродами, порошковыми проволоками и лентами, а также в углекислом газе.
Под действием дуги, температура которой достигает 6000 К, незначительная доля электродного, присадочного и основного металлов испаряется. Часть испарений конденсируется на поверхности сварочной ванны, другая часть уносится газовым потоком в окружающую среду. Потери на испарение невелики (не более 0,5 %).
Окисление легирующих элементов отмечено при контакте жидкого металла с окислительной средой: на оплавленном торце электрода, на капле, на поверхности сварочной ванны. Интенсивность окисления зависит от времени нахождения расплавленного металла в виде капли и ванны, площади их поверхности, температуры, концентрации и активности легирующих элементов.
Технологический процесс наплавки должен обеспечивать минимальные потери электродного и дополнительного присадочного материала при максимальной производи-
тельности, которая оценивается по коэффициенту наплавки н или количеству металла, наплавленного в единицу времени. Для расчета производительности наплавки плавящимся электродом используют формулу
н в,
н
(17.7)
где н " производительность наплавки, кг/ч;н " коэффициент наплавки, г/А • чв сварочный ток, А.
На характеристики процесса плавления оказывают влияние род, полярность и сила тока; тип соединения; положение шва в пространстве и т. д. Установлено, что род сва-1 «очного тока (постоянный или переменный) существенно не на величину коэффициентов расплавления р и наплавки н. С переходом на переменный ток в некоторой степени
уменьшается коэффициент потерь Ψ. Однако производительность наплавки н практически не изменяется.
Производительность различных способов наплавки приведена в табл. 17.1.
Таблица 17.1
Ориентировочная производительность различных способов наплавки
Способ наплавки |
Производительность, |
|
кг/ч |
Ручная наплавка покрытыми электродами |
1-3 |
Механизированная наплавка под флюсом: |
|
одним электродом |
2-15 |
многоэлектродная или электродной лентой |
5-30 |
Механизированная наплавка в углекислом |
|
газе |
1-8 |
Механизированная наплавка самозащитной |
|
порошковой проволокой: |
|
одним электродом |
2-10 |
двумя электродами |
5-20 |
Механизированная наплавка порошковой |
|
лентой: |
|
одним электродом |
10-20 |
двумя электродами |
до 40 |
Вибродуговая наплавка |
1-4 |
Электрошлаковая наплавка |
до 150 |
Плазменная наплавка |
до 30 |
Наплавка погружением в расплав |
10-35 |
Индукционная наплавка |
до 20 |
|
|
3. Необходимые материалы
Для выполнения работы необходимо иметь следующие материалы:
1)пластины из малоуглеродистой и нержавеющей стали Х18Н9Т (200x100x10) мм;
2)электроды тонкопокрытые типа Э 34 (dэл = 4 мм);
3) электроды с толстым покрытием марок ОММ-5, УОНИ-13/45 типа Э 42-Р,
Э42А-Ф; марки АНО-4 типа Э 46-Т или другой марки (dэл = 4 мм);
4)электроды, имеющие стержни из нержавеющей стали, например, типа ЭА-1Ба
марки ЦТ-15; 5) электрод из порошковой проволоки с покрытием УОНИ-13/45.
4. Оборудование, приспособления, инструмент
На рабочем месте должно быть следующее оборудование и инструмент:
1)сварочный пост постоянного и переменного тока с электроизмерительными приборами;
2)весы циферблатные с гирями;
3)секундомер;
4)штангенциркуль;
5)масштабная линейка;
6)бачок для охлаждения проб.
5.Порядок выполнения работы
Определение коэффициентов расплавления, наплавки, потерь металла на угар и разбрызгивание при наплавке валиков электродами разных марок дугой постоянного тока выполняется в следующей последовательности:
1)зачистить пластину;
2)взвесить пластину с точностью до 1 г;
3)замаркировать концы электродов условными обозначениями;
4)определить вес (г) металлического стержня электрода по формуле
- |
|
/01 |
34, |
(17.8) |
|
||||
т |
|
2 |
|
|
|
|
|
|
где - т " диаметр стержня, см; 3 " удельная плотность, г/см3;
4 " длина электрода, см.
Определить для какой-либо марки электрода с толстым покрытием коэффициент покрытия ки путем взвешивания и расчета по формуле
|
к |
6эл 6 т |
|
(17.9) |
|
|
|||
|
п |
6 т |
|
|
|
|
|
||
где -эл — |
вес покрытого электрода, г; |
|
||
- т — |
вес стержня, г; |
|
|
|
5) подобрать силу сварочного тока (например, |
160 А) немаркированным электродом |
на вспомогательной пластине. При переходе к наплавке электродами другой марки установленная по амперметру сила тока будет изменяться, поэтому необходимо в процессе наплавки отмечать действительное значение силы тока по амперметру, которое затем использовать при расчетах;
6) наплавить на пластину валик электродом типа Э Н4, оставляя огарок длиной не более 40 мм. Зафиксировать точное время горения дуги и силу тока;
7)определить вес огарка взвешиванием;
8)охладить пробу с наплавленным валиком, высушить, тщательно очистить от брызг и шлака;
9)взвесить пробу с наплавленным валиком;
10)определить коэффициенты расплавления р и наплавки н по следующим
формулам:
р |
|
(8 6 т 6ог! |
|
|
в · |
||
|
|
||
н |
(8 п.н. д.н.! |
||
|
в · |
||
|
|
где - т — вес стержня, г; -ог— вес огарка, г;
п.н.— вес пластины после наплавки валика, г;д.н.— вес пластины до наплавки, г;в — сила сварочного тока, А;
t — время горения дуги, с.
(17.10)
(17.11)
11)определить теоретическую производительность процесса наплавки по формуле
(17.7);
12)по ранее указанной методике проделать п.п. 3— 10 электродами марок
УОНИ-13/45, ЦТ-15 и порошковым электродом на постоянном токе обратной полярности, электродом марки АНО-4 на переменном токе.
Для одной марки электродов опыт повторить три раза в одинаковых условиях и определить среднее значение параметров.
На основании расчетных данных построить графики зависимости оср, осн, Сн от /св для данной марки электродов.
Данные всех измерений и результаты расчетов записать в табл. 17.2.
Таблица 17.2 Результаты определения параметров наплавки
№ |
Вес |
|
Вес электрода, |
Режим плавления |
Характеристики процесса наплавки |
||||
п/ |
пластины, г |
г |
|
|
|
|
|
|
|
п |
|
|
|
|
|
|
|
|
|
|
|
|
|
|
|
|
|
|
|
|
до |
посл |
до |
огар- |
сила |
время |
Коэффициенты |
Произво- |
|
|
на- |
е |
на- |
ков |
тока, |
горения |
|
|
дитель- |
|
пла |
напл |
плав- |
|
А |
дуги, с |
|
|
ность, |
|
вки |
авки |
ки |
|
|
|
|
|
|
|
|
|
|
|
|
кг/ч |
|||
|
|
|
|
|
|
|
|
|
|
|
|
|
|
|
|
|
расплав- |
наплавки, |
|
|
|
|
|
|
|
|
ления, |
г/Ач |
|
|
|
|
|
|
|
|
г/Ач |
|
|
|
|
|
|
|
|
|
|
|
|
6. Содержание отчета
Отчет должен содержать:
1) определение цели и методику постановки опытов, примеры расчетов;
2)таблицу замеров и результатов расчетов;
3)графики;
4)выводы и анализ полученных результатов.