
СВМ
.pdf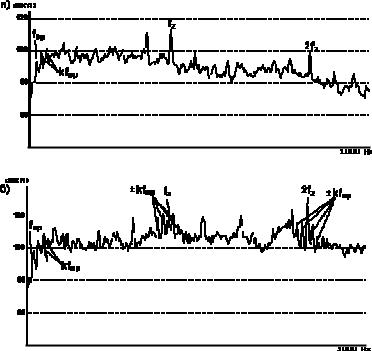
результате роста этих интервалов появляется возможность использования переносной аппаратуры для измерения и анализа вибрации.
И в том и в другом случае эффективность мониторинга зависит от количества компонент вибрации, доступных для измерения. Чтобы увеличить их число в машинах с вращающимися узлами производится узкополосный спектральный анализ вибрации, наиболее эффективный для анализа периодических компонент сигнала. В качестве примера на рис. 2.1 приведены спектры вибрации машины (редуктора) без дефектов и после появления дефектов шестерен, сопровождающихся ростом уровня (мощности) многих составляющих спектра вибрации.
Рисунок.2.1. Спектры вибрации подшипникового узла редуктора. а) - бездефектный редуктор; б) - редуктор с дефектом шестерни.
fвр - частота вращения оси редуктора; fz - зубцовая частота.
Мониторинг вибрационного состояния машины в этом случае заключается в сравнении уровня отдельных составляющих с указанными на рисунке 2.2 порогами и анализ изменений уровня отдельных составляющих за время эксплуатации.
11
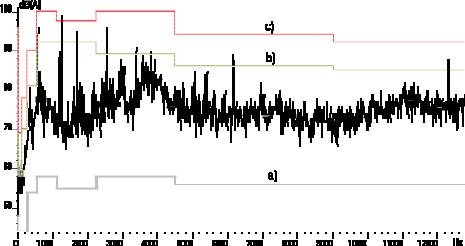
Рисунок.2.2. Мониторинг вибрационного состояния машины. а) - порог слабого сигнала вибрации; б) - порог среднего сигнала вибрации; в) - порог сильного сигнала вибрации.
В практической диагностике машин по вибрации существует два основных подхода к решению диагностических задач. В первом случае диагностика выполняется только после обнаружения изменений вибрационного состояния машины средствами мониторинга и ее задачей является интерпретация этих изменений.
Второй подход заключается в использовании тех методов и средств диагностики, которые обнаруживают основные виды дефектов на этапе их зарождения еще до того, как произойдут существенные энергетические изменения в сигнале вибрации машины в целом. Обнаружение дефектов на этапе зарождения дает возможность наблюдать за их развитием и своевременно планировать работы по ремонту и обслуживанию машины. Такой подход достаточно часто называют мониторингом дефектов, и он может осуществляться в течение нескольких лет, пока совокупность имеющихся дефектов как по глубине, так и по количеству, не приведет к ситуации, близкой к аварийно-опасной.
Для обнаружения зарождающихся дефектов во вращающихся узлах используются естественные диагностические признаки, определяемые путем спектрального анализа самого сигнала вибрации или колебаний мощности его компонент (спектральный анализ огибающей).
Так, основным признаком дефектов в подшипниках является изменение свойств сил трения и возбуждаемой ими высокочастотной вибрации. Эти изменения, заключающиеся либо в появлении микроударов, либо в периодическом изменении коэффициента трения при контакте дефектных участков поверхностей трения, легко обнаруживаются при спектральном анализе огибающей высокочастотных составляющих вибрации корпуса подшипникового узла, возбуждаемых силами трения, см. рис. 2.3.
12
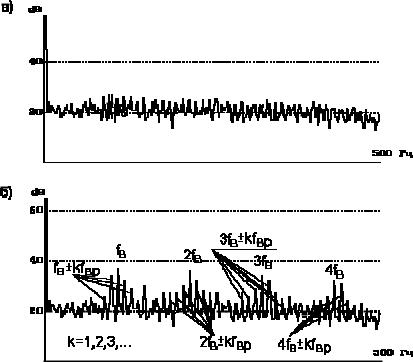
Рисунок.2.3 Спектр огибающей вибрации подшипника без дефектов (а) и подшипника с раковиной на внутреннем кольце (б).
fвр - частота вращения внутреннего кольца подшипника;
fв - частота перекатывания тел качения по внутреннему кольцу подшипника. При обнаружении дефектов в узлах механических передач, в частности,
зубчатых, ременных, с упругими муфтами и других, основное внимание уделяется таким признакам дефектов, как появление динамических нагрузок на элементы передачи, в частности, подшипники. Эти нагрузки приводят, во-первых, к росту определенных компонент вибрации, а, во-вторых, к флуктуациям сил трения в подшипниках, и, как следствие, к колебаниям мощности высокочастотной вибрации. Таким образом, по совокупности результатов измерения спектров вибрации и ее огибающей можно успешно обнаруживать и идентифицировать зарождающиеся дефекты механических передач.
По сигналу вибрации могут быть обнаружены практически все виды зарождающихся дефектов во вращающемся оборудовании без привлечения для диагностики других видов физических процессов. А это означает, что для перехода на обслуживание и ремонт этого оборудования по фактическому состоянию могут использоваться переносные системы вибрационной диагностики, не требующие встраивания измерительных датчиков в оборудование и его узлы.
13

3.Структура систем вибрационного мониторинга и диагностики
Новое поколение систем мониторинга и диагностики вращающегося оборудования отличается от существующих тремя основными свойствами.
Первое - использование для глубокой диагностики только сигнала вибрации без привлечения таких параметров машин и их узлов, как температура, давление, спектральный состав смазки и других. Это обусловлено тем, что при больших затратах на измерение и анализ этих параметров результаты, в основном, дублируют информацию, получаемую при анализе вибрации.
Второе - обязательные для глубокой диагностики измерение и анализ высокочастотной вибрации основных узлов машин, которая в наибольшей степени изменяет свои свойства при наличии дефектов в стадии зарождения.
Третье - автоматическая постановка диагноза после каждого измерения вибрации c идентификацией всех дефектов, без чего невозможен переход от вибрационного мониторинга к мониторингу дефектов.
Таким образом, основные изменения в новых системах относятся только к глубокой диагностике машин, что определяет преемственность в развитии систем мониторинга и диагностики. Существующие системы мониторинга состояния вращающегося оборудования с использованием датчиков вибрации и других физических величин могут просто дополняться новыми средствами глубокой диагностики машин и их узлов.
Структура простейшей переносной системы глубокой диагностики вращающегося оборудования имеет вид, показанный на рис.3.1. В нее входит датчик вибрации, устройство для анализа сигнала вибрации, компьютер и программное обеспечение для диагностики узлов этого оборудования. Для машин, частота вращения которых в момент измерения вибрации точно неизвестна, кроме датчика вибрации используется еще и датчик оборотов ротора.
Рисунок.3.1.Простейшая переносная система глубокой диагностики вращающегося оборудования.
а) - сборщик данных - анализатор СД-11;
б) - персональный компьютер типа Notebook;
14
в) - интерфейсный кабель для обеспечения связи между СД-11 и компьютером; г) - датчик вибрации.
Основным требованием, предъявляемым к датчику вибрации, является возможность измерения как высокочастотных, так и низкочастотных составляющих виброускорения. Устройство для анализа вибрации должно обеспечивать узкополосный спектральный анализ как самого сигнала вибрации, так и огибающей его высокочастотных составляющих, предварительно выделенных из сигнала полосовым фильтром. Устройство может быть выполнено либо в виде отдельного прибора, как это показано на рисунке, либо в виде плат для персонального компьютера.
Системы глубокой диагностики машин по вибрации могут выпускаться для предремонтной дефектации машин, для их выходного контроля после изготовления или ремонта, для наблюдения за состоянием машин или их узлов в процессе эксплуатации. Отличаются они лишь особенностями программного обеспечения. Так, машины после ремонта и монтажа на месте эксплуатации не имеют достаточной приработки, поэтому для их диагностики в большей степени используется низкочастотная и среднечастотная вибрация, а эталон бездефектной машины (узла) автоматически строится по множеству одинаковых машин. При предремонтной дефектации в полной мере используются и диагностические признаки дефектов, содержащиеся в высокочастотной вибрации, а эталон также строится по множеству машин. В процессе эксплуатации, в отличие от предремонтной дефектации, эталоны строятся по первым трем измерениям, а после последующих измерений автоматически адаптируются.
Простейшая система глубокой диагностики вращающегося оборудования при отсутствии системы мониторинга легко может взять на себя ее функции. Необходимо только дополнительно использовать программное обеспечение для мониторинга, назначением которого является планирование измерений, хранение результатов измерений в базе данных, сравнение их с пороговыми значениями, устанавливаемыми автоматически или вручную пользователем, и наблюдение за развитием изменений, происходящих в сигнале вибрации или в его отдельных спектральных составляющих.
Эта же простейшая система может быть использована для балансировки машин на месте их эксплуатации. Необходимо лишь дополнить ее программой балансировки, производящей расчет балансировочных масс, а также обнаруживающей ошибки оператора и дефекты, ограничивающие эффективность балансировки.
Рассматриваемая система глубокой диагностики может быть расширена и до стационарной системы мониторинга и диагностики. Для этого, кроме отмеченной ранее программы мониторинга, необходимо дополнить систему группой датчиков вибрации и электронным управляемым коммутатором (между датчиками и устройством анализа сигнала вибрации), программой автоматического управления системой, обеспечивающей планирование и автоматическое управление измерениями, и выходным устройством сигнализации (рис.3.2).
15

Рисунок.3.2 Стационарная система мониторинга и глубокой диагностики вращающегося оборудования :
а) компьютер с программным обеспечением; б) управляемый компьютером сборщик данных СД-11 с расширителем на 8
каналов и датчиком оборотов; в) интерфейсный кабель управления и передачи данных; г) датчик оборотов; д) датчики вибрации.
В такой системе число датчиков вибрации, стационарно установленных на машине (группе машин) может быть минимальным, но после срабатывания устройства сигнализации оператор должен будет провести с помощью переносной части системы дополнительные измерения вибрации в тех точках, где необходимо анализировать сигнал вибрации для глубокой диагностики узлов машины.
Вторая проблема также связана с диагностикой подшипников качения, когда для получения достоверных результатов необходимо измерять вибрацию в течение нескольких десятков оборотов при постоянных нагрузке и частоте вращения. На прокатных станах нагрузка и частота вращения, например, валков клетей постоянна лишь в течение нескольких оборотов, которых для достоверной диагностики подшипников явно не хватает. Для решения этой проблемы в системах диагностики используются несколько накапливаемых временных отрезков вибрации, измерение которой производится одновременно с измерением частоты вращения и нагрузки.
Еще одна проблема возникает при диагностике подшипников и шестерен низкооборотных ступеней многоступенчатых редукторов, в которых частота вращения входной и выходной ступени могут отличаться более, чем на порядок. В этом случае на корпусе практически всех подшипниковых узлов вибрация, в основном, определяется силами, действующими в самой высокооборотной ступени. Для диагностики низкооборотных ступеней приходится принимать такие меры, как переход на измерение только локальной высокочастотной вибрации, в диапазоне частот выше 10 кГц, которая по амплитуде в тысячи раз слабее низкочастотной. А для этого приходится использовать анализирующую аппаратуру с высокими
16
линейностью и динамическим диапазоном, превышающими 70-80 дБ. Такого рода аппаратура выпускается лишь немногими производителями.
Наконец в металлургическом производстве часто используется мощный, регулируемый по частоте электропривод с машинами постоянного тока, в котором регулирование производится статическими преобразователями напряжения. Это напряжение содержит большое количество переменных составляющих, создающих пульсирующие моменты, которые возбуждают значительную вибрацию машины постоянного тока. Чтобы обнаружить на ее фоне вибрацию, вызванную дефектами в электромагнитной системе машины, необходимо иметь информацию о спектральном составе напряжения в момент диагностирования и автоматически вычесть из спектра вибрации те составляющие, которые вызваны пульсациями питающего напряжения.
Вывод. Новое поколение систем мониторинга и глубокой диагностики вращающегося оборудования по вибрации дает возможность в кратчайшее время перейти на обслуживание и ремонт по фактическому состоянию как основного, так и вспомогательного оборудования металлургического производства.
Для этого не требуется на все виды оборудования устанавливать дорогостоящие стационарные системы непрерывного мониторинга. Достаточно использовать переносные системы мониторинга и глубокой диагностики, позволяющие обнаруживать практически все виды дефектов на стадии зарождения, за много месяцев до аварии, и своевременно планировать сроки и объемы ремонта.
4.Технические средства контроля вибрационного состояния машин вибродиагностики
4.1Структура основных видов приборов для измерения и анализа сигналов вибрации
К техническим средствам контроля вибрации относятся датчики, которые измеряют виброперемещение, виброскорости и виброускорения. Основным элементом датчика является пьезоэлектрический кристалл, поверхность которого металлизирована. Работа датчика основана на прямом и обратном пьезоэффектах. При приложении усилия к пьезокристаллу на его поверхности появляется электрический заряд, чем больше усилие, тем больше заряд.
Обратный пьезоэффект заключается в следующем: при подведении переменного напряжения к поверхности кристалла, он начинает вибрировать с частотой подаваемого напряжения.
17
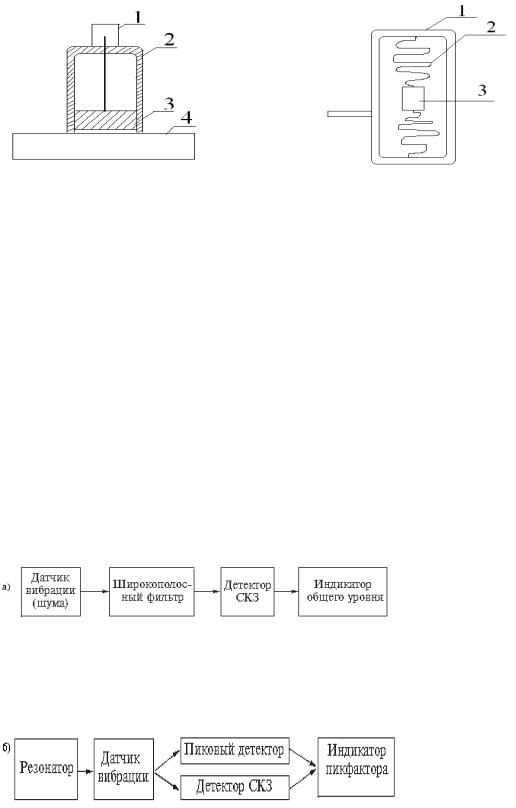
Рисунок.4.1 Измеритель перемещения |
Рисунок.4.2 Вилометр |
|
1.разьем |
|
1.корпус |
2.корпус |
|
2.пружина |
3.пьезокристалл |
|
3.цилиндр |
4.магнит |
|
|
В зависимости от того, какую электрическую величину измеряет датчик, они |
||
подразделяются на 3 группы: |
|
|
- акселерометр – для |
измерения |
ускорения и преобразование его в |
электрический сигнал; |
|
|
-велометр – используется для преобразования скорости в электрический сигнал;
-проксиметр – используется для получения сигнала, пропорционально перемещению.
Для контроля и диагностики неисправностей используются стационарные и переносные вычислительные устройства.
Рассмотрим структуру основных видов приборов для измерения и анализа сигналов вибрации.
Рисунок 4.3. Структура основных видов приборов для измерения и анализа сигналов вибрации и шума.
СКЗ - среднеквадратичное значение.
Рисунок 4.4. Структура основных видов приборов для измерения и анализа сигналов вибрации и шума.
18
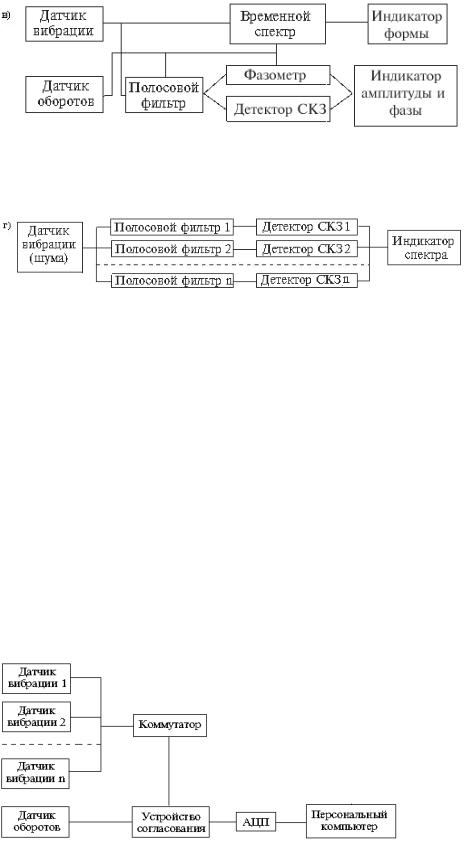
Рисунок 4.5. Структура основных видов приборов для измерения и анализа сигналов вибрации и шума.
.
Рисунок 4.6. Структура основных видов приборов для измерения и анализа сигналов вибрации и шума.
Датчики предназначены для преобразования вибрации в электрический сигнал, полосовой фильтр из общего сигнала выделяет сигналы с заданной частотой, СКЗ- блоки вычисляют среднеквадратическое значение. Последний блок вычисляет и индицирует частотный спектр.
Из наиболее часто используемых средств измерений, реализуемых на базе вычислительной техники, можно выделить анализаторы формы, спектральные анализаторы и анализаторы спектра огибающей. Функции анализатора формы заключаются в измерении амплитуд и фаз отдельных составляющих сигнала и в сравнительном анализе формы отдельных участков сигнала, начало и конец которых определяется углом поворота вала. Наиболее доступным средством измерения и анализа сигналов в настоящее время можно считать персональный компьютер с устройствами преобразования сигналов вибрации и шума в цифровую форму и ввода их в оперативную память компьютера. Еще как правило, устанавливается не один датчик, а несколько. Тогда это будет иметь вид:
Рисунок 4.7. Структура системы диагностики с ПВМ
В этой схеме представлен коммутатор.
Устройства обработки информации могут быть как переносимыми, так и стационарными.
19

4.2Технические средства, используемые в системах вибрационного мониторинга.
Переносные приборы.
Прибор Leonova™ Infinity
Диагностический прибор Leonova™ Infinity - это небольшой переносной прибор для регулярного мониторинга и диагностики состояния производственного оборудования. Прибор Leonova™ Infinity на базе операционной системы Windows с цветным сенсорным дисплеем может производить измерения условий работы, состояния смазки и состояния подшипников качения по методу ударных импульсов SPM®, а также спектральный анализ ударных импульсов SPM Спектр™, выполнять измерения интенсивности вибрации по стандартам ISO, мощный спектральный виброанализ EVAM®, измерения скорости вращения, температуры и аналоговых сигналов по напряжению и току, а также выполнять центровку валов и балансировку роторов.
Прибор Bearing Checker
Прибор Bearing Checker - это очень компактный переносной прибор, который производит быстрые и легкие измерения условий работы, состояния смазки и состояния подшипников качения по методу ударных импульсов SPM®, а также измеряет температуру поверхностей с помощью инфракрасного датчика. Прибор Bearing Checker может также использоваться совместно с шумоизолирующими наушниками в качестве электронного стетоскопа для прослушивания собственных шумов работающего оборудования и в качестве течеискателя для поиска внутренних утечек газов и жидкостей.
20