
Chemical Tankers / Day 3 / Day 3 Topic 5 Tank Cleaning Guidelines
.pdf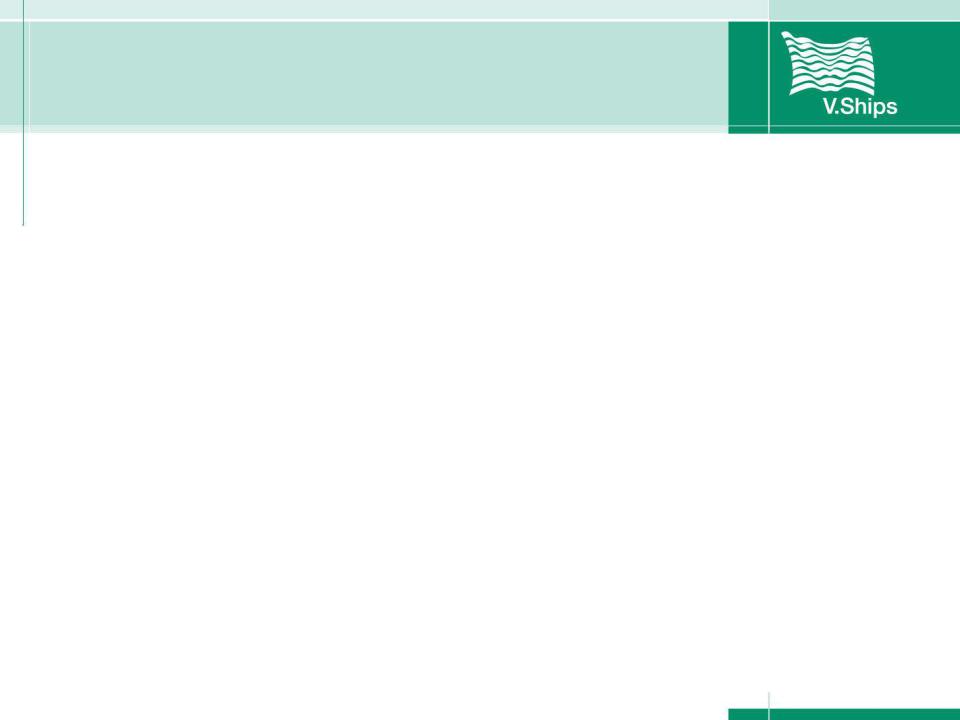
5.3 Industry best practice in tank cleaning
Vegetable Oils – non-drying
RBD Palm Olein Oil should be started with warm (10C above melting point) water wash followed by hot water wash.
An alkaline detergent or vegetable oil cleaner may be injected into the wash water during first cycle of hot washing. Re-circulation with Caustic/soap solution may be necessary in epoxy coated tanks.
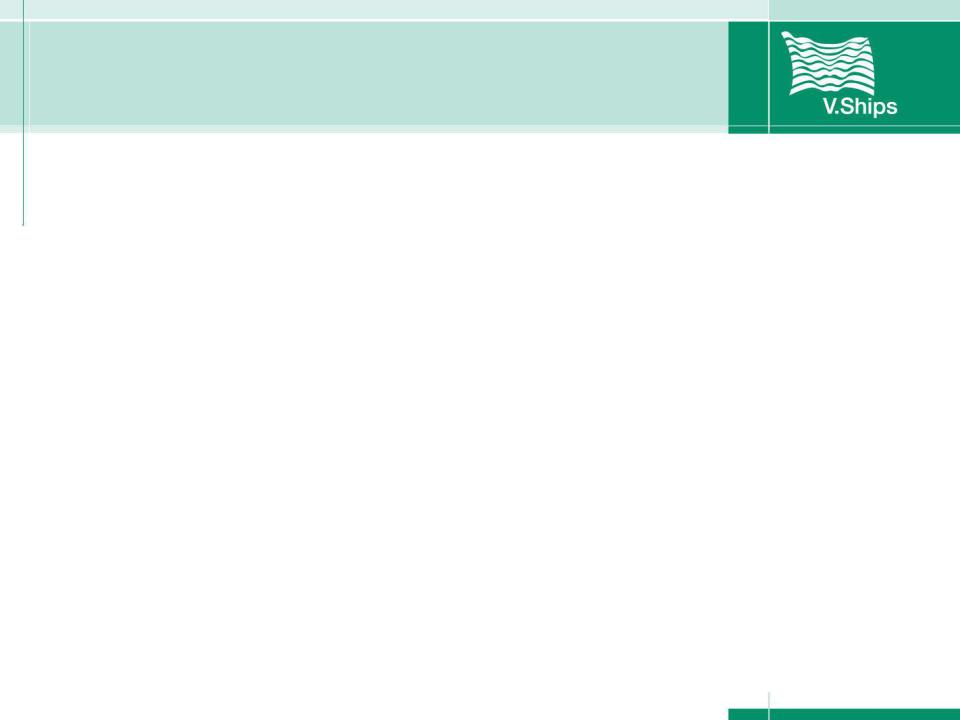
5.3 Industry best practice in tank cleaning
Acids
Acids are divided to water soluble acids (acetic, formic, sulfuric) and non water soluble acids, generally those which derive their acid content from processes, during which they are progressively refined (fatty acids). The percentage of acid is generally quite small, so other factors such as melting point, solubility in solvents are more important.
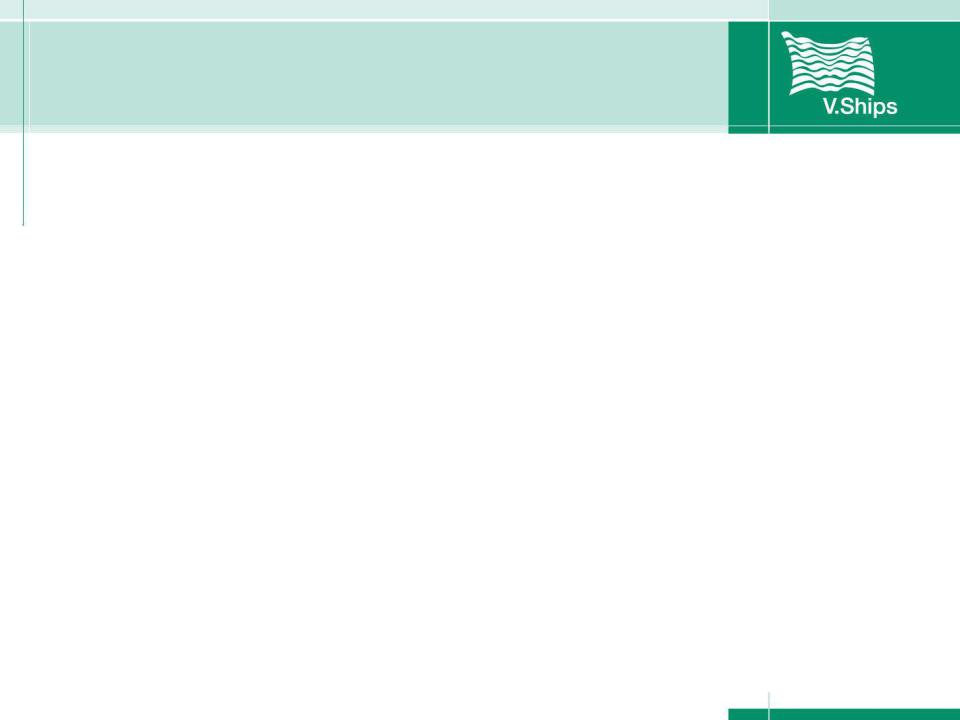
5.3 Industry best practice in tank cleaning
Acids – water soluble
Acids that are water-soluble can usually be cleaned using ambient temperature water. With all water-soluble acids it is important that initial cleaning is done with large amount of water being introduced into the tank at the beginning. The violent chemical reaction between acid and the water is thus rapidly and progressively reduced.
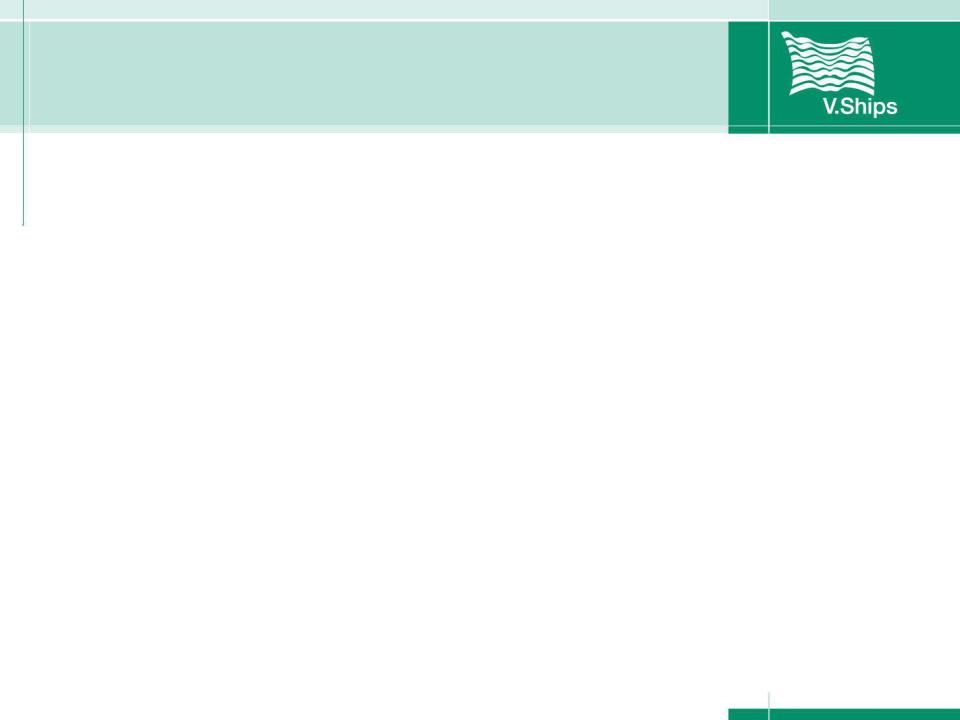
5.3 Industry best practice in tank cleaning
Acids – water soluble
It is important that portable machines supplement fixed machines where necessary to introduce larger volume of water. Ensure that melting point of product is less than washing water temperature.
Very important that all areas of the tanks, lines, drains, dead ends, valve plugs are completely flushed with water and not any acid traces remain.
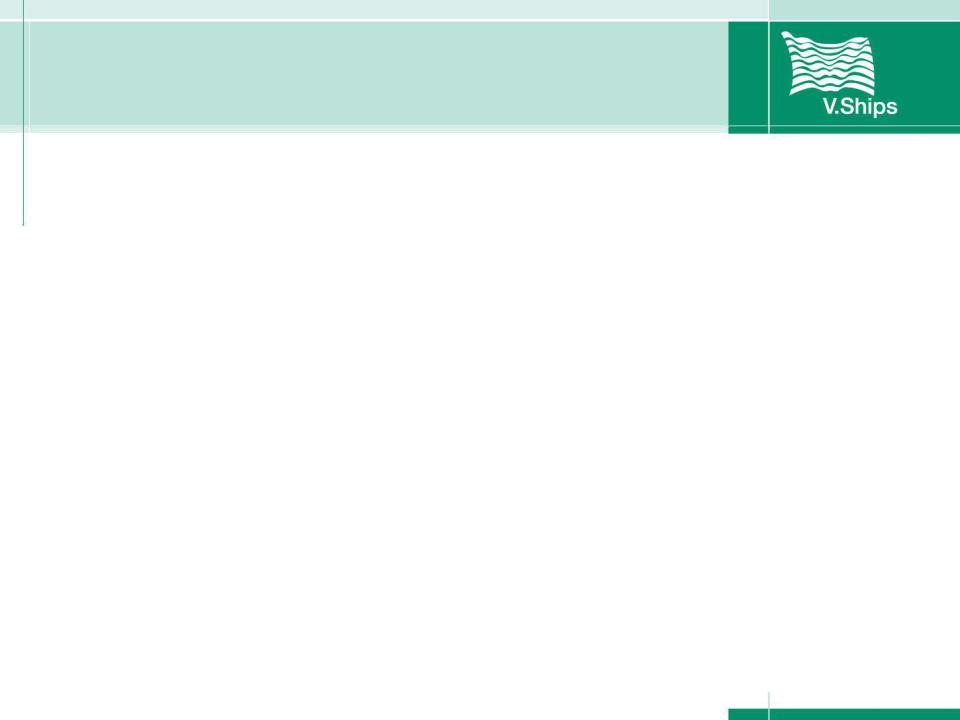
5.3 Industry best practice in tank cleaning
Acids – non water soluble
If washing can not start immediately, keep tank atmosphere moist and warmer than the melting point of product. Tank should be washed ambient or if the product was heated to discharge, at water equal to discharge temperature. Usage of emulsifier or alkaline cleaner will most probably be required during initial stage of washing.
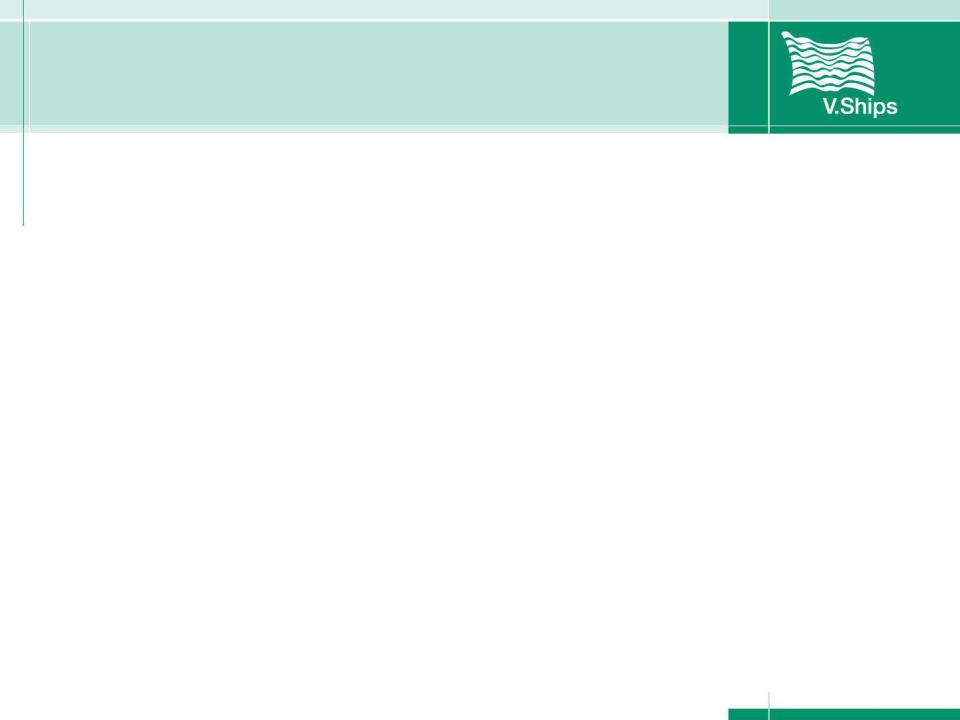
5.3 Industry best practice in tank cleaning
Acids – non water soluble
In stainless steel tanks, a white powder residues on the wall after initial washing may be removed by heated acid cleaner re-circulation. For epoxy coated tanks, a caustic/emulsifier water solution may be made after initial washing and re-circulated for at least 3 hours.
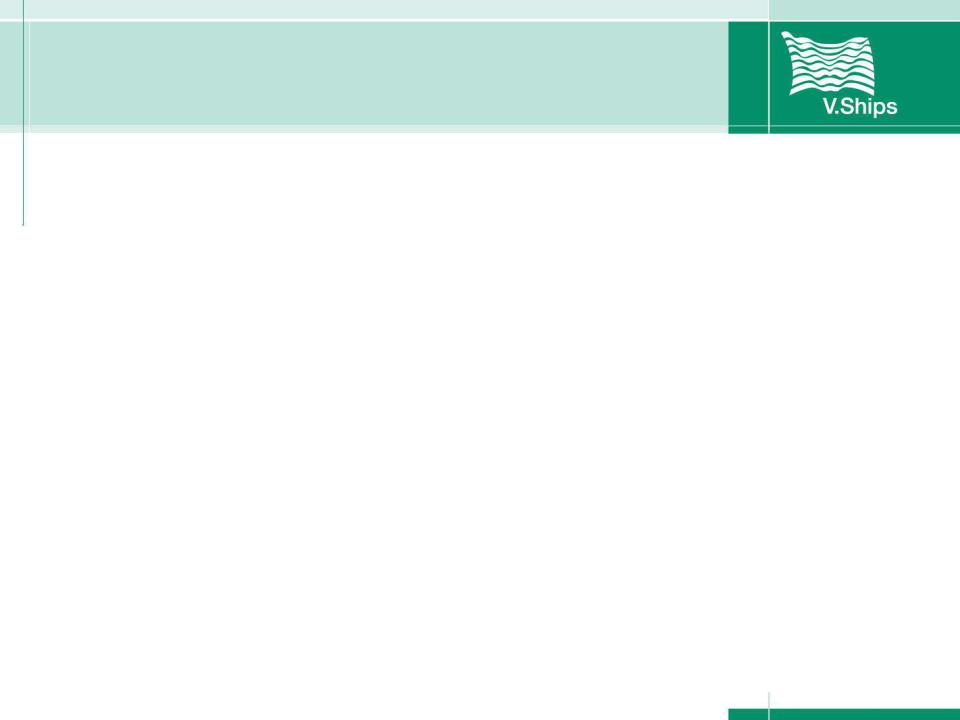
5.3 Industry best practice in tank cleaning
Hydrocarbon mixtures
If the last cargo was Toluene, Benzene, Xylene, Pygas or CPP there is a high risk of contamination of next cargo by traces detectable only by Gas Chromatograph analysis. The following cargoes are very sensitive to such contaminations:
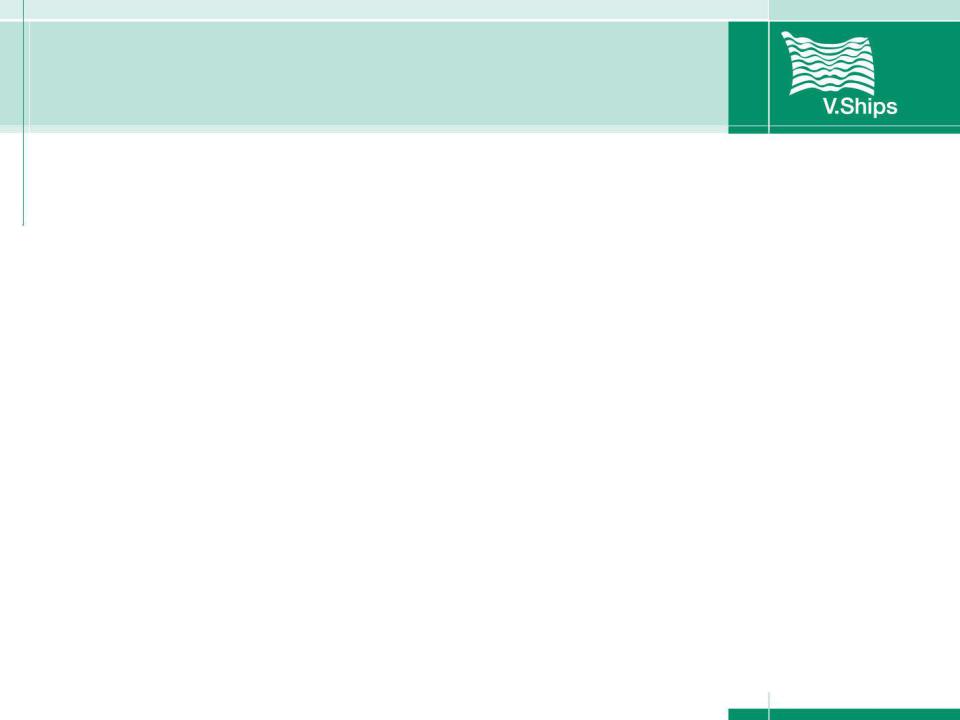
5.3 Industry best practice in tank cleaning
Hydrocarbon mixtures
Light Alcohols (Ethanol, IPA), Glycols (Ethyl, Propyl, Voranols, Polyols), Mineral Oils (Baby Oils, Medicinal Oils), Caustic soda.
The cleaning time should be extended after cleaning of “ene” cargoes to 4 hours by hot water in stainless steel tanks, 6 hours by hot water in zinc coated tanks.
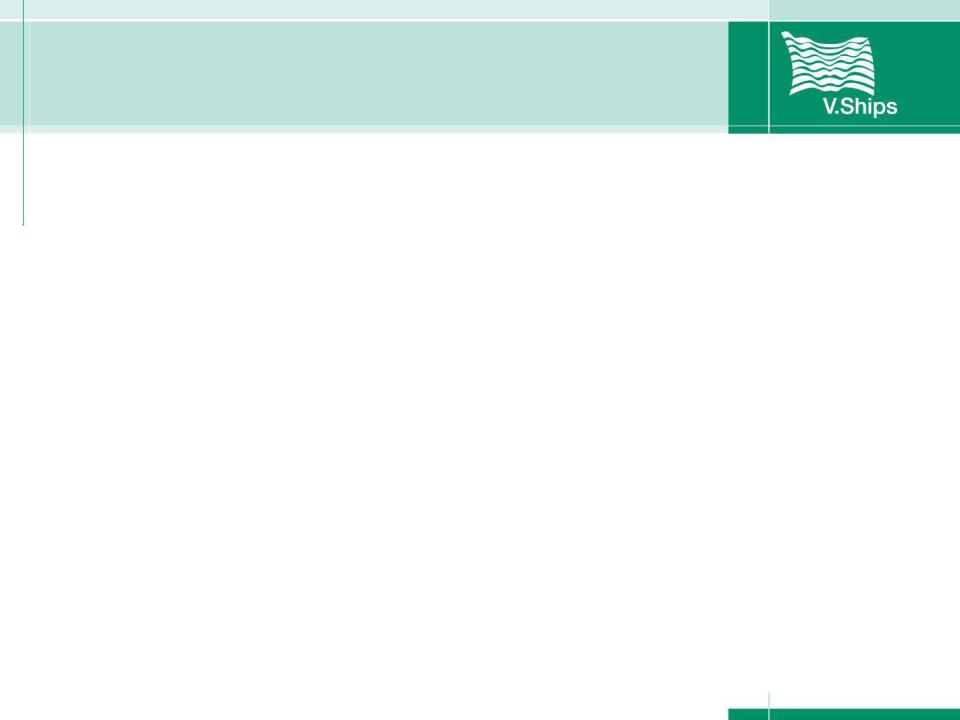
5.3 Industry best practice in tank cleaning
Hydrocarbon mixtures
The epoxy coated tanks should be started with ambient water (but minimum 5C above the melting point of cargo) for 3 hours, followed by warm water wash (55-60C) for 1 hour. Ventilation alone should not be considered.
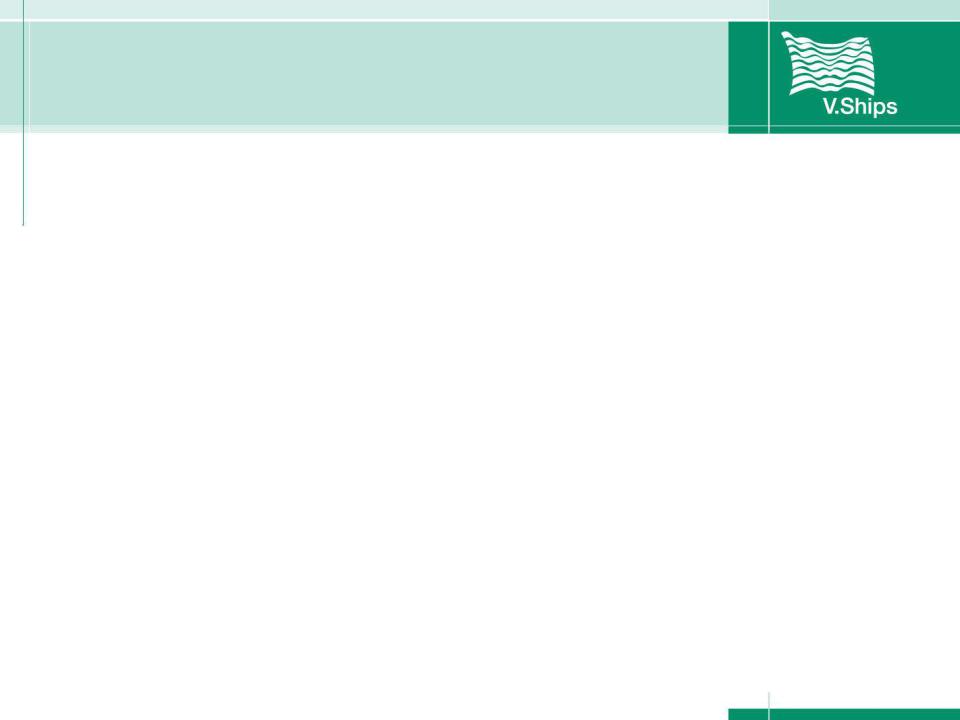
5.3 Industry best practice in tank cleaning
Hydrocarbon mixtures, Lubricating Oils
The products in this group are generally not water-soluble. Although some require quite high discharge temperatures, unless knowledge of the particular product dictates otherwise, initial washing should be done with ambient water.