
Chemical Tankers / Day 3 / Day 3 Topic 5 Tank Cleaning Guidelines
.pdf
5.3 Industry best practice in tank cleaning
Isocyanides
When tank is to be re-circulated with chlorinated solvent (MEC or MCB), ensure that the tank lining is resistant to the particular chlorinated solvent being used. Re-circulate the tank for Two hours under positive N2 pressure and then clean the tank as after chlorinated solvent last cargo by a water washing for at least Four hours.
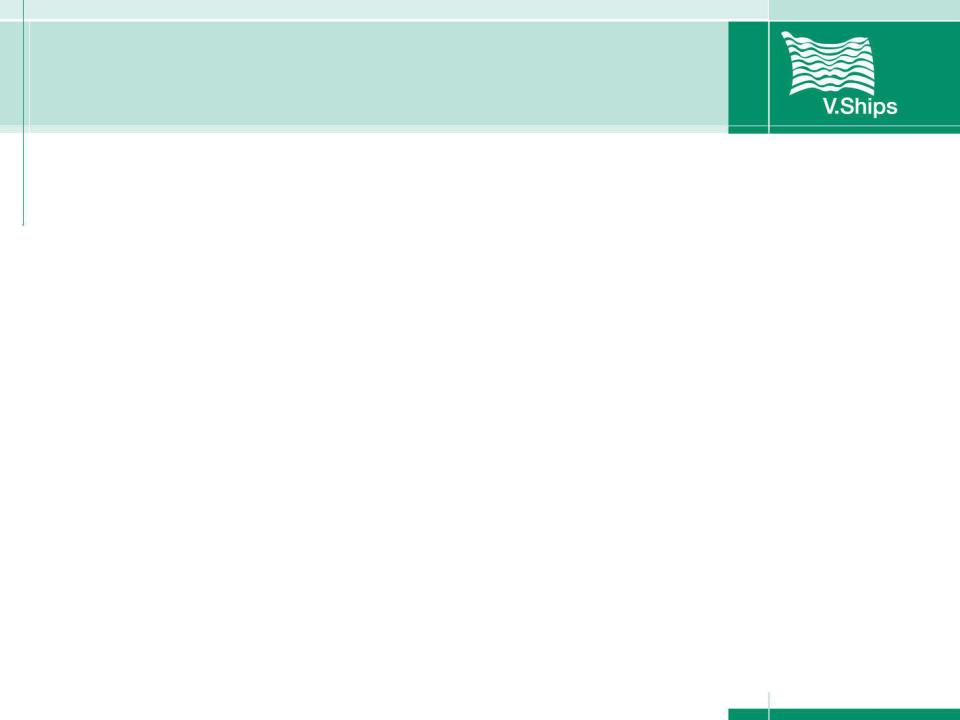
5.3 Industry best practice in tank cleaning
Isocyanides
Before cleaning with water all cargo lines, vent lines, stripping lines & fixed tank cleaning machines must be blown with N2 to ensure all free cargo residues have been removed. Keep tank tight and under positive N2 pressure until actual cleaning is performed. Prior introducing any water to the tank the cargo pump should be turning over at slow speed.

5.3 Industry best practice in tank cleaning
Isocyanides
It is important that as much water at ambient temperature (about 19C at least) is introduced at the initial stage. A sufficient amount of water is key to this process. It may be necessary to supplement fixed cleaning machines with portable machines. Clean for at least 6 hours. The areas with white powder remaining after cleaning should be dealt with immediately by use of white spirit.

5.3 Industry best practice in tank cleaning
Vegetable Oils
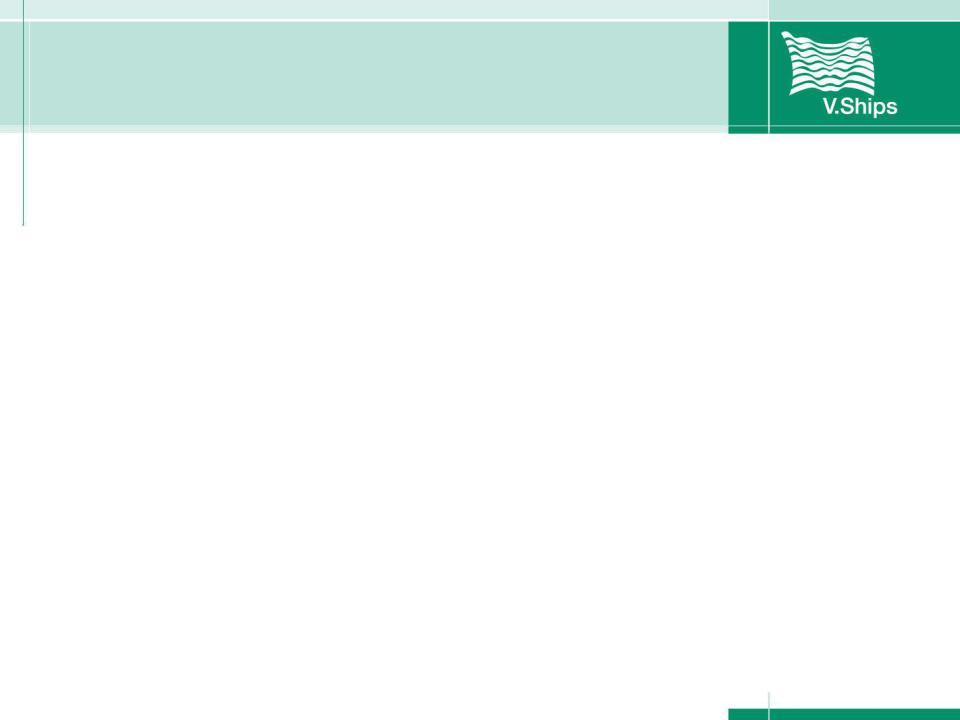
5.3 Industry best practice in tank cleaning
Animal and Vegetable Oils
Animal and Vegetable Oils easily saponify when combined with Caustic Soda. To saponify means converting the oil into soap, or, in practice bringing into suspension. However, alkaline cleaners can only be used if the tank is made from stainless steel or coated with epoxy based coat.

5.3 Industry best practice in tank cleaning
Vegetable Oils - drying or semi-drying
Drying and semi-drying vegetable and animal oils react with oxygen to form a varnish-like polymeric film. This is very difficult to remove from the bulkheads. Heat increases the reaction speed.
Therefore the initial washing of these products must be done with
water at ambient temperature without any delay after unloading of
cargo.

5.3 Industry best practice in tank cleaning
Vegetable Oils - drying or semi-drying
If full tank cleaning in port is not possible after discharge, a quick wash should be given to the tanks to ensure the atmosphere in the tank remains moist. As an alternative, a low pressure steam or limited hand-hosing may be applied.
Heated cargoes in adjacent tanks should be avoided.

5.3 Industry best practice in tank cleaning
Vegetable Oils - drying or semi-drying
In case of doubt as to whether oil is non-drying or drying, always use ambient water first. Initial washing must be done using ambient fresh or salt water. Basic cleaning should be done for 3 hours followed by 3 hours hot washing (80C).

5.3 Industry best practice in tank cleaning
Vegetable Oils – non-drying
The most common non-drying oils from this group are palm and coconut oils. It is very important that the tanks are cleaned soonest upon completion of discharge. All possible means should be applied for ensuring that the atmosphere remains moist, such as the injection of low pressure steam, quick wash or hand-hosing.
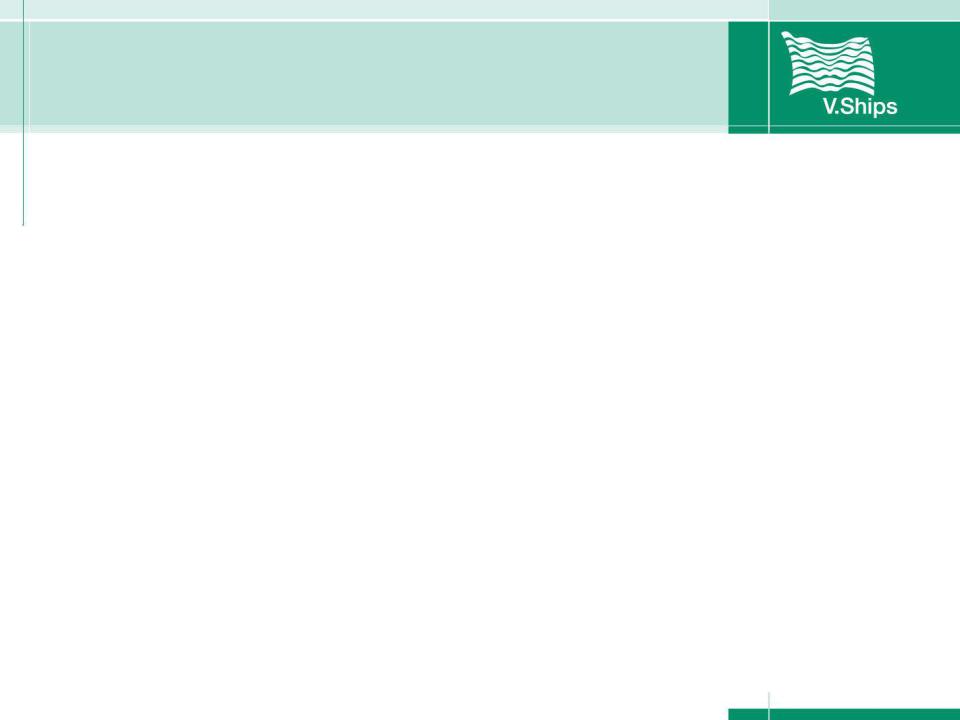
5.3 Industry best practice in tank cleaning
Vegetable Oils – non-drying
Palm Oil, RBD Palm Oil, Coconut Oil, Refined Coconut Oil may be started to clean directly with a hot water (80C).
Palm Kernel Oil, RBD Palm Kernel Oil, Palm Stearine, RBD Palm Stearine, Palm Mid Fraction Oils need to be started with ambient water wash for 3 hours followed by hot water wash.