
3й курс 5 семестр / Sbornik_k_r_i_rasch_-graf_zad
.pdf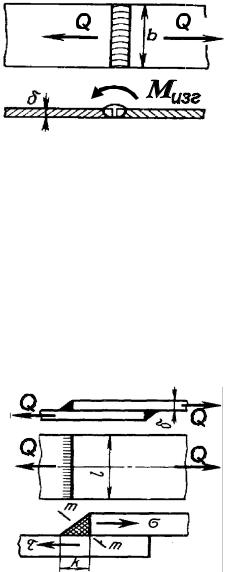
квалифицированного (высокооплачиваемого) сварщика, либо применением автоматической сварки, а также специальными приспособлениями, в которых деталь фиксируется до полного остывания.
Общее условие проектирования сварных соединений – обеспечение равнопрочности шва и свариваемых деталей.
Расчёт на прочность сварных швов
По ориентации относительно приложенных сил различают: лобовые швы – перпендикулярные силам; фланговые швы – параллельны силам; косые швы – под углом к силам.
Эти виды швов в различных сочетаниях применяются в разных соединениях.
ЛОБОВОЙ ШОВ
Рис.7.1.
Соединения встык обычно выполняются лобовыми швами. При качественной сварке соединения разрушаются не по шву, а в зоне температурного влияния. Поэтому рассчитываются на прочность по сечению соединяемых деталей без учёта утолщения швов. Наиболее частые случаи – работа на растяжение и на изгиб.
Напряжения растяжения:
раст = Q / S = Q / b ≤ [ раст]шва.
Напряжения изгиба: изг = Mизг / W = 6 Mизг / b 2 ≤ [ изг]шва. Допускаемые напряжения шва [ раст]шва и [ изг]шва принимаются в
размере 90% от соответствующих допускаемых напряжений материала свариваемых деталей.
|
Соединения внахлёстку |
выполняются |
||||
ЛОБОВОЙ ШОВ. |
||||||
лобовыми, фланговыми и косыми швами. |
|
|||||
|
|
|||||
|
Лобовые швы в инженерной практике |
|||||
|
рассчитывают |
только |
по |
касательным |
||
|
напряжениям. |
За |
расчётное |
сечение |
||
|
принимают биссектрису m-m, где обычно |
|||||
|
наблюдается разрушение. Расчёт только по |
|||||
|
касательным напряжениям не зависит от угла |
|||||
|
приложения нагрузки. |
|
|
|
||
Рис.7.2. |
При этом τ = Q / (0,707 k l) ≤ [τ']шва. |
|
51
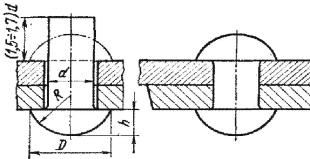
Фланговые швы характерны неравномерным распределением напряжений, поэтому их рассчитывают по средним касательным напряжениям. При действии растягивающей силы касательные напряжения равны:
τ = Q / (2*0,707 l) ≤ [τ']шва.
При действии момента: τ = M / (0,707 k l) ≤ [τ']шва.
Если швы несимметричны, то нагрузка на фланговые швы распределяется по закону рычага Q1,2 = Q l1,2 / ( l1 + l2), где l1 и l2 – длины швов.
При этом швы рассчитывают по соответствующим нагрузкам, а длины швов назначают пропорционально этим нагрузкам. Касательные напряжения в швах
τ1,2 = Q1,2 / (1,414 l1,2 ) ≤ [τ']шва.
Косые швы рассчитываются аналогичным образом. Нагрузка Q раскладывается на проекции в продольном и нормальном направлениях к шву, а далее выполняются расчёты лобового и флангового швов.
Комбинированные лобовые и фланговые швы рассчитывают на основе принципа распределения нагрузки пропорционально несущей способности отдельных швов. При действии силы Q касательные напряжения равны:
τQ = Q / [0,707 k ( 2lф+ lл )] ≤ [τ']шва.
Если действует момент M, то
τM = M / [0,707 k lл ( lф+ lл /6)] ≤ [τ']шва.
При совместном действии силы и момента касательные напряжения складываются τ = τМ + τQ ≤ [τ']шва.
Тавровые и угловые швы соединяют элементы в перпендикулярных плоскостях. Выполняются либо стыковым швом с разделкой кромок (а), либо угловым без разделки кромок (б). При нагружении изгибающим моментом и силой прочность соединения оценивают:
для стыкового шва (а) по нормальным напряжениям
= 6M/ (b 2) + Q / (l ) ≤ [ раст]шва,
для углового шва (б) по касательным напряжениям
τ = 6M/(1,414 l2k)+ Q / (1,414 l k ) ≤ [τ']шва.
Заклёпочные соединения
Образуются с помощью специальных деталей – заклёпок. Заклёпка имеет грибообразную форму и выпускается с одной головкой (закладной) вставляется в совместно просверленные детали, а затем хвостовик ударами молотка или пресса
расклёпывается, образуя вторую ЗАКЛЁПКА головку (замыкающую). При этом
детали сильно сжимаются, образуя прочное, неподвижное неразъёмное соединение.
Рис.7.3. 52
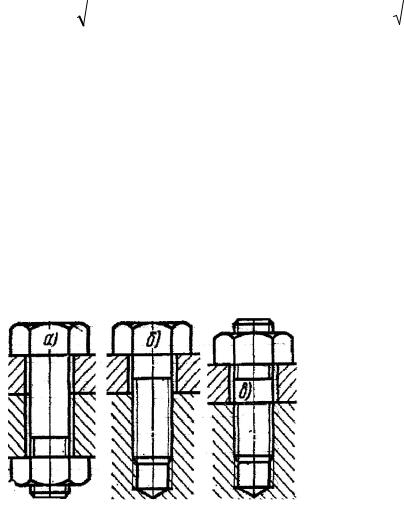
Достоинства заклёпочного соединения: 1.соединяют не свариваемые детали (Al);
2.не дают температурных деформаций;
3.детали при разборке не разрушаются. Недостатки заклёпочного соединения:
1.детали ослаблены отверстиями;
2.высокий шум и ударные нагрузки при изготовлении;
3.повышенный расход материала.
Заклёпки изготавливают из сравнительно мягких материалов: Ст2, Ст3, Ст10, Ст15, латунь, медь, алюминий.
Заклёпки испытывают сдвиг (срез) и смятие боковых поверхностей. По этим двум критериям рассчитывается диаметр назначаемой заклёпки. При этом расчёт на срез – проектировочный, а расчёт на смятие – проверочный.
Здесь и далее имеем в виду силу, приходящуюся на одну заклёпку.
При |
|
одной |
|
плоскости среза |
При |
|
двух плоскостях среза |
||||||
метр заклёпки: |
|
|
|
ладки с двух сторон): |
|
|
|||||||
|
|
|
|
|
|
d |
|
|
|
|
|
. |
|
dзакл |
|
|
срез ). |
закл |
|
2P /( |
) |
||||||
|
|
4P /( |
|
|
|
|
срез |
|
|
Напряжения смятия на боковых поверхностях заклёпки см = P/Sd ≤ [ ]см, где: S – толщина наименьшей из соединяемых деталей. При проектировании заклёпочных швов как, например, в цистернах, необходимо следить, чтобы равнодействующая нагрузок приходилась на центр тяжести шва.
Следует симметрично располагать плоскости среза относительно линии действия сил, чтобы избежать отрыва головок.
Кроме того, необходимо проверять прочность деталей в сечении, ослабленном отверстиями.
Резьбовые соединения
Являются наиболее совершенным, а потому массовым видом разъёмных соединений. Применяются в огромном количестве во всех машинах, механизмах, агрегатах и узлах.
Основные детали соединения имеют наружную либо внутреннюю винтовую нарезку (резьбу) и снабжены огранёнными поверхностями для захвата гаечным ключом.
Рис.7.5.
53
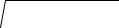
Болт – длинный цилиндр с головкой и наружной резьбой. Проходит сквозь соединяемые детали и затягивается гайкой (а) – деталью с резьбовым отверстием. Винт – внешне отличается от болта, но завинчивается в резьбу одной из соединяемых деталей (б). Шпилька – винт без головки с резьбой на обоих концах
(в).
Расчёт на прочность резьбовых соединений
Осевая нагрузка винта передаётся через резьбу гайке и уравновешивается реакцией её опоры. Каждый из Z витков резьбы нагружается силами F1, F2, … FZ.
В общем случае нагрузки на витках не одинаковы. Задача о распределении нагрузки по виткам статически неопределима и была решена русским учёным Н.Е. Жуковским в 1902 г. на основе системы уравнений для стандартной шестигранной гайки. При расчётах неравномерность рагрузки учитывают эмпирическим (опытным) коэффициентом Km, который равен 0,87 для треугольной, 0,5 – для прямоугольной и 0,65 для трапецеидальной резьбы.
Основные виды разрушений у крепёжных резьб – срез витков, у ходовых - износ витков. Следовательно, основной критерий работоспособности
для расчёта крепёжных резьб – прочность по касательным напряжениям среза, а для ходовых резьб – износостойкость по напряжениям смятия.
Условие прочности на срез:
F / (πd1HKKm) ≤ [τ] для винта; τ = F / (πdHKKm) ≤ [τ] для гайки,
где: H –высота гайки или глубина завинчивания винта в деталь, K=ab/p или K=ce/p
– коэффициент полноты резьбы, Km – коэффициент неравномерности нагрузки по виткам.
Условие износостойкости на смятие:
см = F / (πd2HZ) ≤ [ ]см,
где: Z – число рабочих витков.
Равнопрочность резьбы и стержня винта является важнейшим условием назначения высоты стандартных гаек. Так, приняв в качестве предельных напряжений пределы текучести материала и учитывая, что τТ ≈ 0,6 Т условие равнопрочности резьбы на срез и стержня винта на растяжение предстанет в виде:
τ = F/(πd1HKKm)= = 0,6σТ = 0,6 F /[(π/4) d12]. При K = 0,87 и Km = 0,6 получаем H
≈ 0,8d1, а учитывая, что d1 = d окончательно принимаем высоту нормальной стандартной крепёжной гайки H ≈ 0,8d.
В расчёте болтов сначала находят силу, приходящуюся на один болт. Затем всё многообразие компоновок резьбовых соединений может быть сведено к трём простейшим расчётным схемам.
А. Болт вставлен в отверстия с зазором.
Соединение нагружено продольной силой Q. Болт растянут.
Условие прочности на растяжение запишется в виде: растрезьб резьбраст .
Напряжения растяжения в резьбе растрезьб 4Q/ dвнутр2 .
Из условия прочности на растяжение находим внутренний диаметр резьбы
резьбы болта dвнутр 4Q /( раст ).
54

Найденный внутренний диаметр резьбы округляют до ближайшего большего по ГОСТ 9150-59. Там же указан конкретный типоразмер-номер (наружный диаметр резьбы) болта.
Б. Болт вставлен в отверстия без зазора. Соединение нагружено поперечной силой Р.
При этом болт работает на срез. Внутренний диаметр резьбы
резьбы
рассчитывается аналогично случаю с растяжением: dвнутр 4P /( срез ).
Порядок назначения номера болта также аналогичен предыдущему случаю.
В. Болт вставлен с зазором.
Соединение нагружено поперечной силой F.
Сила затяжки болта V должна дать такую силу трения между деталями, которая была бы больше поперечной сдвигающей силы F.
Болт работает на растяжение, а от момента затяжки испытывает ещё и кручение, которое учитывается повышением нормальных напряжений на 30% (в 1,3 раза).
резьбы
Тогда dвнутр 4 *1,3*V /( раст ).
По опыту многочисленных расчётов принимают величину требуемой растягивающей силы V в зависимости от сдвигающей поперечной силы F
V = 1,2 F/ f.
резьб
Тогда внутренний диаметр резьбы болта dвнутр 6,24F /( f раст ), где: f – коэффициент трения.
Во всех случаях в расчёте находится внутренний диаметр резьбы, а обозначается резьба по наружному диаметру. Распространённая ошибка состоит в том, что рассчитав, например, внутренний диаметр резьбы болта 8мм, назначают болт М8, в то время как следует назначить болт М10, имеющий наружный диаметр резьбы 10мм, а внутренний 8мм.
Концентрация напряжений во впадинах витков резьбы учитывается занижением допускаемых напряжений резьбы на 40% по сравнению с соответствующими допускаемыми напряжениями материала.
Решение задач рассматривается в [6] c. 43-45, 50-55, 62-63, 96-99.
Задача 5.1
Определить допускаемую силу F, которая может быть приложена к рычагу, исходя из прочности стыкового сварного шва (рис. 5.1). Размер рычага у места сварки axb. Материал рычага сталь СтЗ. Нагрузка статическая. Сварка ручная.
55
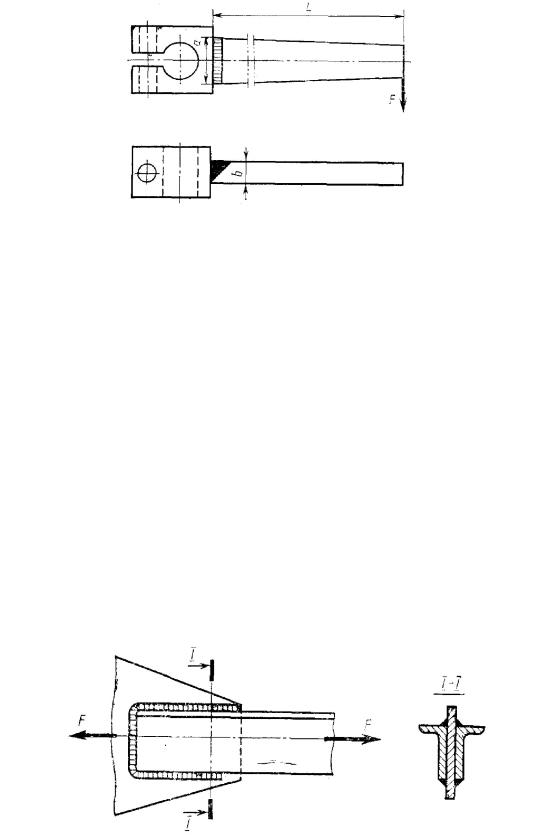
Рис.5.1
Таблица 5.1
Параметры |
|
|
|
|
Варианты |
|
|
|
|
|
|
|
|
|
|
|
|
|
|
|
|
|
1 |
2 |
3 |
4 |
5 |
6 |
7 |
8 |
9 |
10 |
|
|
|
|
|
|
|
|
|
|
|
L, м |
0,6 |
0,6 |
0,65 |
0,65 |
0,7 |
0,75 |
0,75 |
0,8 |
0,85 |
0,9 |
|
|
|
|
|
|
|
|
|
|
|
а, м |
40 |
50 |
50 |
60 |
70 |
80 |
80 |
90 |
90 |
100 |
|
|
|
|
|
|
|
|
|
|
|
b, м |
5 |
6 |
6 |
8 |
8 |
10 |
10 |
12 |
12 |
12 |
|
|
|
|
|
|
|
|
|
|
|
Задача 5.2
Рассчитать на равнопрочность швы сварного соединения косынки с растяжками в виде двух уголков, подобрав при этом номер уголков (рис. 5.2). На соединение действует сила F. Нагрузка статическая. Сварка ручная.
Рис.5.2
56
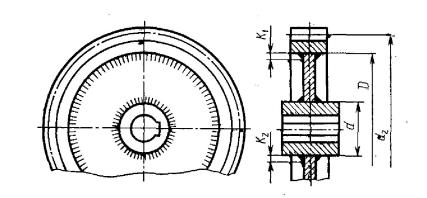
Таблица 5.2
Параметры |
|
|
|
|
|
Варианты |
|
|
|
|
||
|
|
|
|
|
|
|
|
|
|
|
|
|
|
1 |
2 |
3 |
4 |
|
5 |
|
6 |
7 |
8 |
9 |
10 |
|
|
|
|
|
|
|
|
|
|
|
|
|
F, kH |
60 |
70 |
80 |
90 |
|
100 |
|
110 |
120 |
130 |
140 |
150 |
|
|
|
|
|
|
|
|
|
|
|
|
|
|
|
|
|
|
Задача 5.3 |
|
|
|
|
|
Проверить прочность сварных швов, соединяющих диск с ободом и со ступицей (рис. 5.3). Материал диска — сталь СтЗ, а ступицы и обода — сталь 35. Передаваемая валом мощность Р при угловой скорости , толщина швов:
K1 =8 мм, К2= 10 мм. Нагрузка статическая. Сварка ручная электродом
Э42.
Рис.5.3
Таблица 5.3
Параметры |
|
|
|
|
Варианты |
|
|
|
|
|
|
|
|
|
|
|
|
|
|
|
|
|
1 |
2 |
3 |
4 |
5 |
6 |
7 |
8 |
9 |
10 |
|
|
|
|
|
|
|
|
|
|
|
P, kBт |
24 |
28 |
32 |
34 |
36 |
38 |
40 |
42 |
44 |
46 |
|
|
|
|
|
|
|
|
|
|
|
, рад/с |
12 |
15 |
9 |
12 |
18 |
20 |
24 |
27 |
32 |
36 |
|
|
|
|
|
|
|
|
|
|
|
D, м |
0,6 |
0,65 |
0,7 |
0,67 |
0,65 |
0,66 |
0,62 |
0,65 |
0,68 |
0,7 |
|
|
|
|
|
|
|
|
|
|
|
d, м |
0,18 |
0,18 |
0,25 |
0,22 |
0,2 |
0,2 |
0,19 |
0,19 |
0,2 |
0,22 |
|
|
|
|
|
|
|
|
|
|
|
Задача 5.4
К конструкции (рис. 5.4), состоящей из косынки и двух уголков, приложена сила F. Определить номер профиля уголков и число заклепок. Материал косынки и заклепок — сталь СтЗ.
57
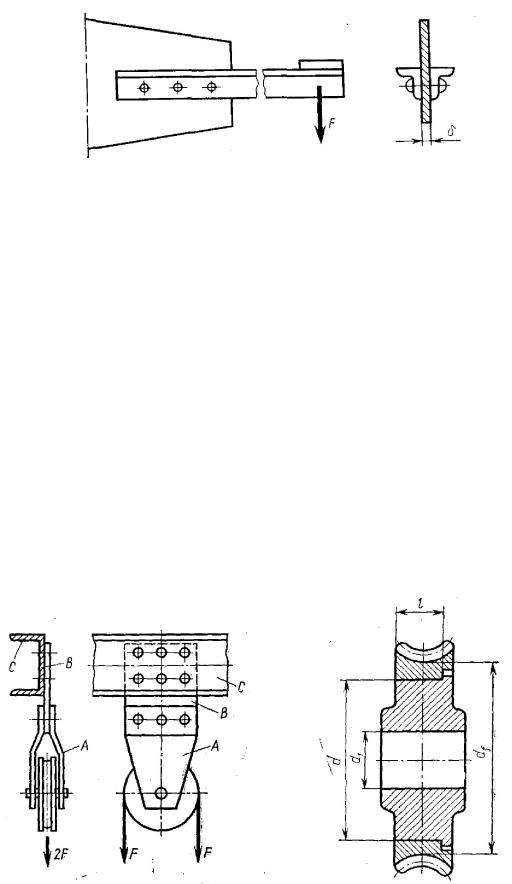
Рис.5.4
Таблица 5.4
Параметры |
|
|
|
|
Варианты |
|
|
|
|
|
|
|
|
|
|
|
|
|
|
|
|
|
1 |
2 |
3 |
4 |
5 |
6 |
7 |
8 |
9 |
10 |
|
|
|
|
|
|
|
|
|
|
|
F, kH |
35 |
40 |
45 |
50 |
55 |
60 |
65 |
70 |
75 |
80 |
|
|
|
|
|
|
|
|
|
|
|
, мм |
10 |
10 |
10 |
12 |
12 |
12 |
12 |
15 |
15 |
15 |
|
|
|
|
|
|
|
|
|
|
|
Задача 5.5
Рассчитать заклепки, крепящие скобы А к косынке В, и косынку со швеллером С (рис. 5.5). Сила, действующая на блок, 2F.
Рис.5.5 |
Рис.5.6 |
58
Таблица 5.5
Параметры |
|
|
|
|
Варианты |
|
|
|
|
|
|
|
|
|
|
|
|
|
|
|
|
|
1 |
2 |
3 |
4 |
5 |
6 |
7 |
8 |
9 |
10 |
|
|
|
|
|
|
|
|
|
|
|
F , kH |
10 |
12 |
14 |
17 |
20 |
25 |
30 |
35 |
40 |
45 |
|
|
|
|
|
|
|
|
|
|
|
Задача 5.6
Рассчитать цилиндрическое соединение с натягом зубчатого венца и ступицы червячного колеса (рис. 5.6). Диаметр посадочной поверхности d, ее длина l. Передаваемый червячным колесом крутящий момент Тк. Венец выполнен из бронзы БрАЖ9-4, а ступица из чугуна СЧ 12-28.
Таблица 5.6
Параметры |
|
|
|
|
Варианты |
|
|
|
|
|
|
|
|
|
|
|
|
|
|
|
|
|
1 |
2 |
3 |
4 |
5 |
6 |
7 |
8 |
9 |
10 |
|
|
|
|
|
|
|
|
|
|
|
Tk , H м |
1000 |
1000 |
1100 |
1100 |
1200 |
1200 |
1300 |
1300 |
1400 |
1400 |
|
|
|
|
|
|
|
|
|
|
|
d f , мм |
300 |
310 |
320 |
330 |
340 |
350 |
360 |
370 |
380 |
390 |
|
|
|
|
|
|
|
|
|
|
|
l , мм |
50 |
52 |
54 |
56 |
58 |
60 |
62 |
64 |
66 |
68 |
|
|
|
|
|
|
|
|
|
|
|
d1 , мм |
65 |
67 |
70 |
72 |
74 |
76 |
78 |
80 |
82 |
85 |
|
|
|
|
|
|
|
|
|
|
|
d , мм |
270 |
280 |
290 |
300 |
310 |
320 |
330 |
340 |
350 |
360 |
|
|
|
|
|
|
|
|
|
|
|
Задача 5.7
Определить количество и диаметр болтов, соединяющих барабан грузовой лебедки диаметром D1 с зубчатым колесом. Болты расположены по окружности диаметром D2 (рис. 5.7). Грузоподъемность лебедки F. Нагрузка постоянная. Расчет выполнить для болтов, установленных в отверстие с зазором и без зазора.
59
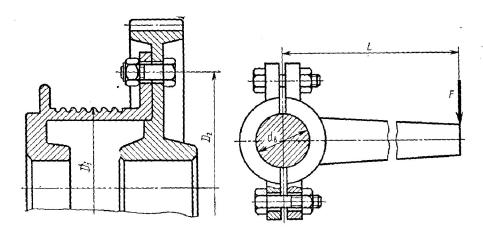
Рис.5.7 |
Рис.5.8 |
Таблица 5.7
Параметры |
|
|
|
|
Варианты |
|
|
|
|
|
|
|
|
|
|
|
|
|
|
|
|
|
1 |
2 |
3 |
4 |
5 |
6 |
7 |
8 |
9 |
10 |
|
|
|
|
|
|
|
|
|
|
|
F , kH |
12 |
15 |
17 |
19 |
21 |
23 |
25 |
27 |
29 |
31 |
|
|
|
|
|
|
|
|
|
|
|
D1, м |
0,2 |
0,25 |
0,3 |
0,35 |
0,37 |
0,4 |
0,42 |
0,45 |
0,47 |
0,5 |
|
|
|
|
|
|
|
|
|
|
|
D2 , м |
0,35 |
0,4 |
0,45 |
0,5 |
0,52 |
0,55 |
0,58 |
0,6 |
0,62 |
0,65 |
|
|
|
|
|
|
|
|
|
|
|
Задача 5.8
Рассчитать болты клеммового соединения рычага с валиком диаметром dB (рис.5.8). На конце рычага приложена постоянная нагрузка F . Материал болтов – сталь Ст3.
Таблица 5.8
Параметры |
|
|
|
|
|
Варианты |
|
|
|
|
|
|
|
|
|
|
|
|
|
|
|
|
|
|
1 |
2 |
3 |
4 |
|
5 |
6 |
7 |
8 |
9 |
10 |
|
|
|
|
|
|
|
|
|
|
|
|
F , kH |
1,5 |
1,2 |
1,1 |
1,4 |
|
0,9 |
1,3 |
0,9 |
0,8 |
1,1 |
1,3 |
|
|
|
|
|
|
|
|
|
|
|
|
L , м |
0,4 |
0,4 |
0,3 |
0,2 |
|
0,2 |
0,2 |
0,3 |
0,3 |
0,4 |
0,4 |
|
|
|
|
|
|
|
|
|
|
|
|
dB , мм |
60 |
60 |
55 |
55 |
|
45 |
40 |
40 |
40 |
50 |
50 |
|
|
|
|
|
|
|
|
|
|
|
|
|
|
|
|
|
60 |
|
|
|
|
|