
- •ОГЛАВЛЕНИЕ
- •1. МЕТОДИЧЕСКИЕ УКАЗАНИЯ ПО ВЫПОЛНЕНИЮ ЛАБОРАТОРНЫХ РАБОТ
- •Введение
- •Техника безопасности
- •ОБЩИЕ СВЕДЕНИЯ
- •2.1. ЦЕЛЬ И ЗАДАЧИ КУРСОВОГО ПРОЕКТА
- •2.2. ТЕМАТИКА КУРСОВОГО ПРОЕКТА
- •2.3. СОДЕРЖАНИЕ И ОБЪЕМ КУРСОВОГО ПРОЕКТА
- •Раздел 1. ОБОСНОВАНИЕ ВЫБОРА ТИПА СОЕДИНЕНИЙ, СХЕМЫ СВАРКИ
- •Раздел 2. ОПИСАНИЕ ОСНОВНОГО МАТЕРИАЛА И ЕГО СВАРИВАЕМОСТИ
- •Раздел 3. ОБОСНОВАНИЕ ВЫБОРА ЦИКЛА СВАРКИ И РАСЧЕТ ПАРАМЕТРОВ РЕЖИМА СВАРКИ
- •Раздел 4. ВЫБОР СВАРОЧНОГО ОБОРУДОВАНИЯ
- •Раздел 8. КОНТРОЛЬ КАЧЕСТВА СВАРНЫХ СОЕДИЕНИЙ
- •Раздел 9. ТЕХНИКО-ЭКОНОМИЧЕСКАЯ ОЦЕНКА ПРОЕКТА
- •ЗАКЛЮЧЕНИЕ И ВЫВОДЫ
- •2.5. ВЫПОЛНЕНИЕ И ЗАЩИТА ПРОЕКТА
- •2.6. ВАРИАНТЫ ЗАДАНИЙ НА КУРСОВОЙ ПРОЕКТ
- •БИБЛИОГРАФИЧЕСКИЙ СПИСОК
1. МЕТОДИЧЕСКИЕ УКАЗАНИЯ ПО ВЫПОЛНЕНИЮ ЛАБОРАТОРНЫХ РАБОТ
Введение
Самостоятельное проведение лабораторных работ помогает студентам лучше усваивать теоретический материал, совершенствовать конкретное инженерное мышление и приобщает студентов к научно - исследовательской работе.
По курсу “Контактная сварка” предусматриваются лабораторные работы по технологии и оборудованию контактной сварки.
В каждой работе дано краткое описание конструкции машины и принципа ее работы. Приведены конструкции основных узлов различных контактных машин и схемы их работы.
Для выполнения работ в расположение студента предоставляются контактные машины, описания, чертежи и схемы, необходимые справочные материалы, приборы, инструмент, спецодежда, свариваемые заготовки и т. д.
Перед началом лабораторных работ и в процессе их проведения необходимо обратить внимание на инструктаж и мероприятия по технике безопасности (заземление, изоляционные коврики, сигнальные лампы, защитные очки, спецодежда и т. д.).
Техника безопасности
При выполнении лабораторных работ необходимо соблюдать правила техники безопасности. Наибольшую опасность представляют: поражение электрическим током, ожоги от брызг расплавленного металла, травмы от движущихся частей приводов машины.
Вторичное напряжение контактных машин мало (до 36 В) и не является опасным для человека. Студент может подвергнуться воздействию высокого напряжения лишь в случае пробоя или замыкания первичной обмотки сварочного трансформатора на вторичный виток. Чтобы избежать этого, вторичную цепь машины соединяют с корпусом, который должен быть надежно заземлен. Каждая машина имеет отдельный сетевой рубильник и предохранители, смонтированные на отдельном или групповом щите. Все части сварочной машины, находящиеся под напряжением свыше 36 В, надежно защищены от попадания в них влаги, случайных прикосновений, механических повреждений и брызг расплавленного металла. Во время работы дверцы машины закрываются.
4
Пол около машины должен быть сухим, покрыт деревянной решеткой или резиновым ковриком.
Подключать прерыватели, переставлять планки, вилки, ножи и т. д. переключателей ступеней сварочного трансформатора, заменять электроды и исправлять части машины можно только после отключения машины от источника питания.
Первичное напряжение машины 380 или 220 вольт опасно для жизни человека.
Прежде чем приступить к ознакомлению и изучению машины, необходимо отключить ее от сети, приняв меры против возможной подачи напряжения к месту работы. На всех выключателях и разъединителях следует вывешивать плакаты “Не включать работают люди”.
Отсутствие напряжения проверяется исправным указателем напряжения.
Чтобы защитить студента от ожогов, возможных при выплеске расплавленного металла в процессе сварки, необходимо предусмотреть местную защиту в зоне сварки в виде щитков полузакрытого типа, изготовленных из прозрачного пластика. Каждому студенту выдают бесцветные очки закрытой формы, рукавицы, брезентовую куртку или фартук. Для безопасности подвижные узлы машины снабжаются защитными кожухами, окрашенными в особый цвет.
При контактной сварке, в особенности стыковой, выделяется значительное количество пыли, загрязняющей воздух. Сварка цветных металлов сопровождается выделением вредных газовых веществ. Поэтому в лабораториях, где работают студенты, должна быть предусмотрена общая приточно-вытяжная вентиляция.
Для выполнения работ студенты разбиваются на бригады по 2 3 человека. В каждой бригаде преподавателем назначается ответственный за технику безопасности, который следит за ходом работы и координирует действия остальных членов бригады.
5
Лабораторная работа 1
ИЗУЧЕНИЕ КОНСТРУКЦИЙ И ПРИНЦИПА ДЕЙСТВИЯ КОНТАКТНОЙ ТОЧЕЧНОЙ МАШИНЫ
Цель работы - ознакомиться с конструкцией универсальных машин для контактной сварки, детально изучить конструкцию, и принцип действия вcех узлов и систем одной из контактных машин, приобрести навыки в управлении машиной и настройке параметров режима сварки, рассчитать некоторые элементы контактной машины.
Оборудование и материалы
1.Машина для точечной сварки с электронным реле времени. 2.Описание машины, контакторов, реле времени, необходимые чертежи
и схемы. 3.Штангенциркули.
4.Образцы для пробной сварки.
Теоретические сведения
Особенности конструкции точечных машин
На рис. 1.1 и рис. 1.2 представлены конструктивные схемы точечных машин прессового и радиального типа. Как видно из рисунков, основными узлами любой точечной машины являются: привод давления 1, служащий для перемещения электрода и создания усилия на свариваемых деталях; верхняя и нижняя консоли 2 с токоподводами, воспринимающие механические усилия при сжатии свариваемых деталей; корпус или станина 3 машины для сборки всех узлов и восприятия усилия при сжатии свариваемых деталей; верхний и нижний электродержатели 4 со сменными электродами для подвода сварочного тока и создания механического усилия на деталях; источник сварочного тока 5 сварочный трансформатор с переключателем ступеней; прерыватель сварочного тока 6, регулятор работы машины 7.
К каждому из этих узлов предъявляются требования, обусловленные назначением точечной машины.
Привод давления точечных машин
Привод давления точечных машин должен обеспечивать постоянство усилия на электродах при колебаниях давления пневматической или гидравлической сетей, необходимый темп сварки и точность хода электродов. При сварке особо ответственных конструкций из легких сплавов и нержавеющих сталей привод давления должен иметь малую инерционность.
6
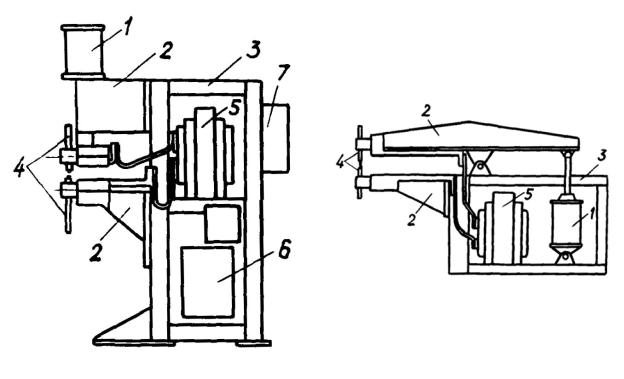
Рис. 1.1. Конструктивная схема точечной |
Рис. 1.2. Конструктивная схема точечной |
машины прессового типа |
машины радиального типа |
Механизмы сжатия, применяемые в точечных машинах, делятся на педальные, рычажные, электромеханические, пневматические и гидравлические.
Часто допускается комбинация отдельных видов привода пневмогидравлический, электропневматический и другие. Вид привода обуславливается назначением машины, ее мощностью, производительностью и требованиями к качеству сварки.
Работа механизма сжатия связана с включением и выключением сварочного тока. Для обеспечения качественной сварки ток должен включаться после сжатия электродов. Во время сварки некоторых материалов целесообразно применять переменные усилия сжатия электрода (рис. 1.7).
Педальный привод (рис. 1.3) применяется на машинах малой мощности. Для регулирования и создания более или менее постоянного усилия на электродах между педалью и кронштейном привода электрода вводят промежуточный элемент – пружину.
Электромеханический привод давления применяется в машинах, работающих в массовом производстве, где требуется относительно высокая производительность и постоянство режима сварки.
В отличие от педального привода кронштейн электродов приводится в движение вращающимся кулачком. Подбирая соответствующий профиль кулачка, можно задать необходимый цикл усилия на электродах. На рис. 1.4 показана одна из конструкций электромоторного привода давления. На одном
7
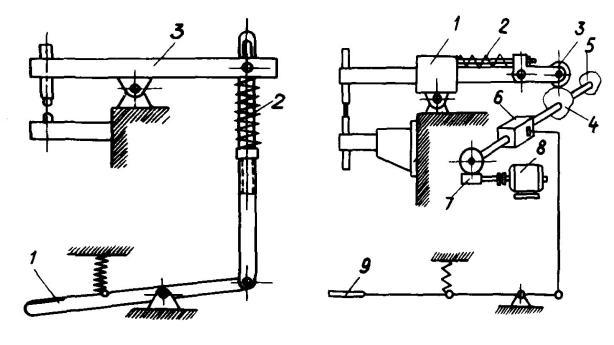
валу с кулачком давления устанавливается и токовый кулачок, воздействующий на концевой выключатель.
Рис. 1.3. Педальный привод точечных ма- |
Рис. 1.4. Электромоторный привод давле- |
|
шин малой мощности: 1 - педаль; |
ния точечных машин: 1 - рычаг; |
|
2 - пружина; 3 - рычаг |
2 - пружина; |
3 - ролик; |
|
4 - рабочий кулак; 5 |
- токовый мотор; |
|
9 - педаль управления |
Гидравлический привод широко применяется в многоточечных и подвесных машинах. Принципиально конструкция его не отличается от конструкции пневматических приводов последних. Только роль воздуха выполняет жидкость. Жидкость несжимаема. Просачиваясь через уплотнения поршня в нерабочую полость цилиндра, она создает препятствие перемещению поршня в крайнее положение. Поэтому необходимо принимать меры по удалению жидкости из нерабочих полостей цилиндра.
При двустороннем действии цилиндра жидкость вытесняется автоматически вместе с подъемом или опусканием поршня. При одностороннем действии удаление жидкости и возврат поршня производится возвратной пружиной. Питание цилиндров жидкостью осуществляется от насосной установки пневмогидравлического устройства.
На рис. 1.5 представлены гидрокинематические схемы точечных машин одностороннего и двустороннего действия с питанием от пневмогидравлического устройства и насосной станции.
8
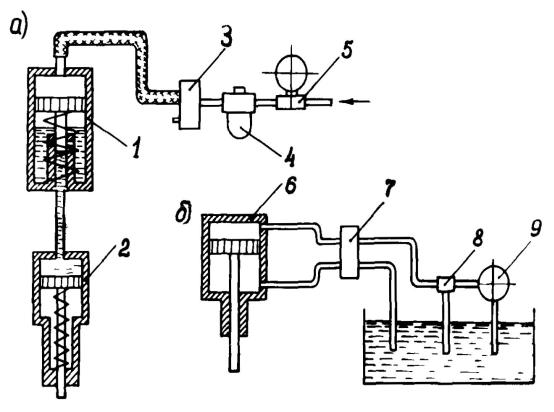
Пневматические схемы
Для обеспечения взаимодействия всех узлов машины, имеющих пневматический или гидравлический приводы, и получения заданных характеристик движения исполнительного органа все элементы привода объединены в единую систему - пневматическую или гидравлическую.
В большинстве случаев каждая такая система состоит из силовых распределительных и рабочих элементов. Пневматическим приводом давления точечных машин должны являться следующие функции:
1 возвратно-поступательное движение электрода с заданной производительностью и ходом электродов; 2 создание усилия на электродах и поддержание его постоянным при колебаниях давления воздушной сети; 3
регулирование усилия на электродах; 4 выполнение заданной программы усилия на электродах в процессе сварки.
Рис. 1.5. Типовые гидрокинематические схемы точечных машин: а - одностороннего действия с питанием от пневмогидравлического устройства; б - двустороннего действия с питанием от насосной установки; 1 - пневмогидравлический цилиндр; 2 - рабочий цилиндр; 3 - пневматический клапан; 4 - лубрикатор; 5 - редуктор; 6 - рабочий цилиндр; 7 - гидравлический золотник; 8 - предохранительный клапан; 9 - насос
Привод должен иметь минимальную инерционность, наименьшие габариты и быть надежным в эксплуатации. Ниже приведены наиболее распространенные пневматические схемы приводов точечных машин.
9
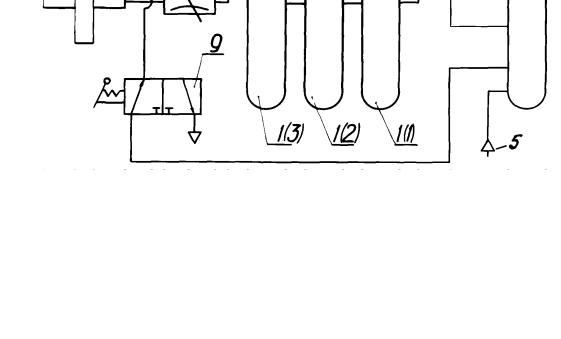
На рис. 1.6 показана пневматическая схема машин МТ. Усилие на электродах создается пневматическим цилиндром, имеющим два поршня - рабочий 10 и вспомогательный 11. Движением рабочего поршня управляет двухходовой электропневматический клапан 6. Плавность хода достигается дросселирующими клапанами 7. Давление воздуха в рабочей камере цилиндра регулируется редуктором 2.
Для создания постоянства усилия на электродах и независимости его от пропускной способности пневматической сети, на машине установлены ресиверы 1. Движущие части верхнего и нижнего поршней смазываются маслом при помощи лубрикатора 4. Управление верхней камерой вспомогательного поршня производится трехходовым ручным краном 9. Воздушные ресиверы 1 служат для поддержания постоянного давления в камере цилиндра. Пневматическая система подключается к воздушной сети посредством запорного вентиля 5. Накопившаяся вода в ресиверах удаляется через спускные краны.
Рис. 1.6. Пневматическая схема машин типа МТ
Открытием запорного вентиля схема подключается к воздушной сети. При включении трехходового крана 9 воздух сетевого давления поступает в верхнюю камеру вспомогательного поршня и опускает его до упора регулировочных гаек. Число ходов рабочего поршня и порядок включения воздушных полостей цилиндра устанавливается электропневматическим клапаном 6, а величина усилия на электродах, регулированием давления воздуха в рабочих полостях цилиндра с помощью редуктора 2, имеющего манометр 3. Воздух в рабочую среднюю камеру цилиндра поступает через отверстие, расположенное в верхнем штоке 8 вспомогательного поршня 11.
10
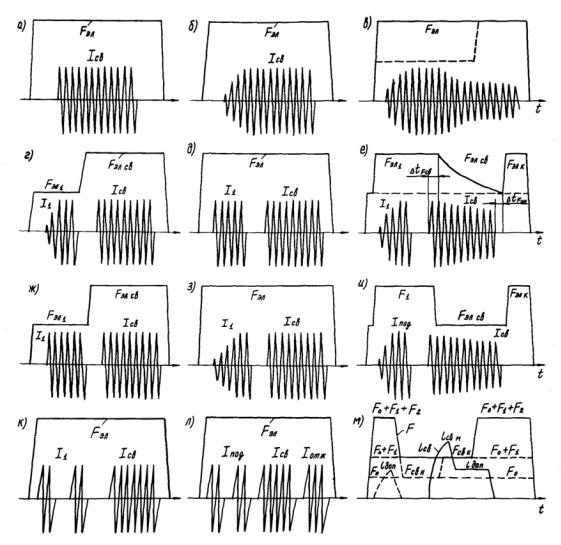
Отличительная особенность пневматической схемы машин типа МТ отсутствие ресивера, который размещается между редуктором и лубрикатором. Кроме того, в этой схеме имеется отстойник для сбора воды.
По рассмотренной пневмосхеме выполняется простейший цикл сварки (рис. 1.7 а). На рис. 1.8 показана пневмосхема машины средней мощности типа МТПУ-300. Пневматический привод этой машины позволяет производить сварку при постоянном или переменном усилии сжатия электродов. Воздух в камеры над поршнем 5 и под ним подается под одинаковым давлением, которое регулируется редуктором 1 с манометром 2. Благодаря этому сварочное усилие при сварке с проковкой поддерживается более стабильным, чем в системах, основанных на раздельной регулировке давления воздуха в камерах.
Рис. 1.7. Циклограммы сварочного тока и усилия, на электродах контактных точечных машин
Переход от Fсв к Fков осуществляется путем выпуска воздуха из нижней камеры. Для ускорения выпуска воздуха между цилиндром и клапаном 4 установлен дросселирующий клапан, который не препятствует поступлению
11
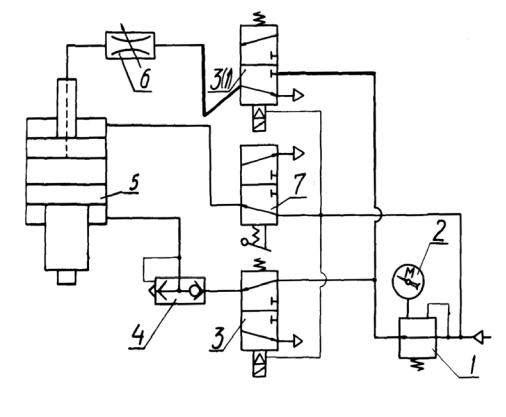
воздуха в цилиндр, но весьма быстро выбрасывает сжатый воздух из цилиндра в атмосферу, как только клапан 3(2) прекращает подачу воздуха. Усилие нарастает за очень короткий промежуток времени (0,01-0,02 сек) в зависимости от объема камеры. Впуск и выпуск воздуха в рабочую камеру происходит через клапан 3(1) и дросселирующий клапан 6. Подъем верхнего вспомогательного поршня выполняется ручным краном 7.
Пневматический привод и электрическая схема машины МТПУ-300 позволяют производить сварку по циклограммам, показанным на рис. 1.7 а, б, в, г, д, ж, з.
Рис. 1.8. Пневматическая схема машины МТПУ-300
Каждая из приведенных схем имеет достоинства и недостатки и применяется только в той области, где ее преимущества могут быть использованы наилучшим образом.
Основные циклограммы сварочного тока и усилия сжатия электродов, воспроизводимые современными машинами, показаны на рис. 1.7 а - м.
Конструкция пневматических механизмов давления
Для точечных контактных машин средней мощности преимущественно используются пневматические механизмы сжатия. В зависимости от назначения контактной машины конструкция механизмов сжатия может быть различной. Ниже рассматриваются устройства механизмов сжатия, типовых контактных машин типа МТ (рис.1.9 а, б).
12
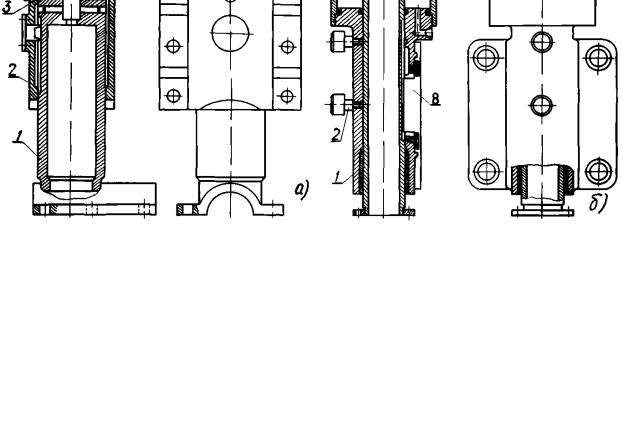
Опускание верхнего электрода и сжатие деталей при сварке осуществляется пневматическим приводом, состоящим из цилиндра с двумя крышками и двух поршней со штоками. Силовые цилиндры приводов имеют два поршня, образующих три камеры А, Б и В.
Верхняя камера А служит для воздуха, удерживающего верхний поршень 6 в положении, которое обеспечивает необходимый рабочий ход верхнего электрода. Рабочий ход электрода регулируют при помощи регулировочной гайки 4, устанавливая верхний поршень в нужное положение. Если предварительно поднять поршень, то рабочий ход увеличится.
Рис. 9. Механизмы сжатия контактных машин типа МТП (а) и МТ (б)
Средняя камера Б служит для воздуха, создающего рабочее давление на электродах. При подаче в нее сжатого воздуха через отверстие в штоке верхнего поршня шток 3 нижнего поршня 7, связанный с ползуном 1, будет опускать верхний электрод вниз и создавать давление на свариваемых деталях, ползун 1 перемещается в направляющем стакане 2.
Нижняя камера В служит для воздуха, поднимающего электрод. В корпусе крышки 5 имеется отверстие для подвода сжатого воздуха в камеру А.
Основной отличительной особенностью механизма сжатия (рис..9 б) является его плавающий цилиндр. Конструкция нижней крышки цилиндра
13

обеспечивает направление движения штока нижнего поршня, а также крепление привода на кронштейне передней рамы корпуса машины. Возможность поворота штока вокруг оси предотвращается шпонкой 8, установленной в гнезде нижней крышки.
Крепление крышек с цилиндром выполнено проволочными кольцами, заведенными в канавки крышки и штока. При демонтаже цилиндра проволочные кольца изымаются из гнезд поворотом крышек. К нижней части ползуна крепится плита, в которой устанавливается электрододержатель.
Рис. 1.10. Механизм сжатия машин типа |
Рис. 1.11. Механизм сжатия для контактных |
МТПУ |
машин малой мощности типа МТПК |
На рис. 1.10 показана конструкция механизма сжатия электродов контактных машин повышенной мощности. Пневматический привод позволяет производить сварку при постоянном или переменном усилии сжатия электро-
дов. Отношение ковочного усилия к сварочному колеблется в пределах 2 2,5 и не зависит от величины усилий, так как оно определяется отношением площади рабочей части нижнего поршня 3 к площади штока 8, приваренного к поршню. Воздух в верхнюю и нижнюю камеры цилиндра 2 поступает под одинаковым давлением, которое регулируется редуктором пневматической схемы. Благодаря этому заданное усилие при сварке с проковкой поддерживается более стабильным, чем в системах, основанных на раздельной регули-
14
ровке давления воздуха в камерах. Усилие от штока в через набор тарельчатых пружин передается к ползуну, на котором устанавливается колодка с электрододержателем и электродом. С помощью пружин предотвращается заклинивание подвижных частей привода и обеспечивается перемещение верхнего в процессе тепловых деформаций деталей независимо от перемещения поршня 3 без заметного изменения усилия сжатия деталей. Механизм сжатия имеет роликовые направляющие и легкий силуминовый ползун, что практически устраняет влияние сил трения и массы подвижных частей на величину усилия сжатия.
Переход от Fсв к Fков достигается выпуском воздуха из нижней камеры. Силовой цилиндр 2 закрывается крышками 1 и 4, которые стягиваются шпильками 7. Впуск и выпуск воздуха из рабочей средней камеры происходит через отверстия, расположенные в штоке верхнего поршня 5. Величина перемещения штока 8 регулируется положением верхнего поршня при помощи гайки 6.
На рис. 1.11 изображен механизм сжатия машины малой мощности. Пневмопривод состоит из цилиндра 6 с двумя крышками 1 и 7, поршня 5 (свободно перемещающегося по штоку 3), демпфирующей пружины 4 и уплотнительных манжет 8. На нижнем штоке закреплена токопроводящая колодка для установки электрода. Крышки прижимаются к цилиндру шпильками 2. В верхней крышке предусмотрено отверстие для прохода сжатого воздуха в верхнюю камеру. Воздух воздействует на плавающий поршень цилиндра через демпфирующую пружину и передает усилие на шток 3. При выпуске сжатого воздуха из верхней камеры цилиндра и впуске сжатого воздуха в нижнюю камеру поршень поднимается вверх.
В специализированных машинах могут использоваться различные конструкции механизмов сжатия, но все они в какой-то мере будут подобны рассмотренным.
Пневматическая аппаратура управления
Для управления пневматическими механизмами в контактных машинах имеется специальная пневматическая аппаратура, электропневматические клапаны для распределения воздуха, воздушные редукторы для регулирования и поддержания постоянства давления воздуха, дросселирующие клапаны для регулирования скорости хода исполнительных механизмов, лубрикаторы для смазки воздушных цилиндров.
Выпуск и впуск сжатого воздуха в камеры пневматических цилиндров или камер производится посредством различного типа электропневматических клапанов.
На рис. 1.12 показан ЭПК-6, работающий на переменном токе напряжением 220 или 380 В.
Клапан состоит из стальной втулки 2 с двумя рядами отверстий. По краям втулки 2 запрессованы кольца с внутренними кольцевыми выточками,
15
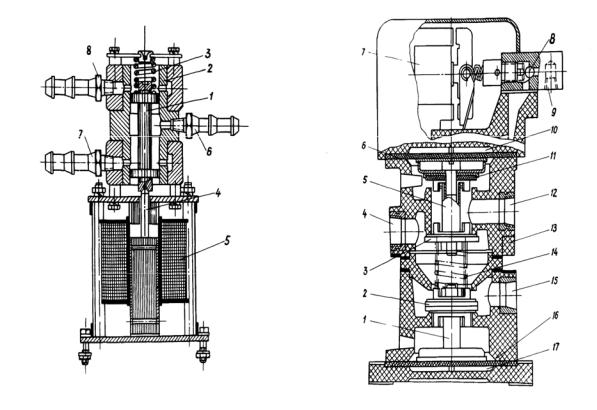
не перекрывающими отверстие втулки 2, и ниппелями 7 и 8 для соединения клапана с рабочими полостями пневматического цилиндра. Внутри втулки 2 расположен стальной притертый плунжер 1, перемещающийся вниз под действием пружины 3 и вверх под действием толкателя 4, связанного с якорем электромагнита 5. Воздух подводится к клапану через ниппель 6. При включенном электромагните плунжер 1 под действием пружины 3 находится в нижнем положении. Воздух через ниппель 6, внутреннюю полость клапана и ниппель 7 поступает в одну из полостей цилиндра. Вторая полость цилиндра через ниппель 8 и кольцевые отверстия втулки 2 сообщается с атмосферой.
Рис. 1.12.Двухходовой |
Рис. 1.13. Электропневматический |
электропневматический клапан ЭПК-6 |
клапан КПЭМ-10-3 |
При включенном электромагните якорь электромагнита 5 поднимается вверх толкателем 4, перемещает плунжер в верхнее положение. При этом воздух начинает поступать через ниппель 8 во вторую полость цилиндра, другая же полость через ниппель 7 соединяется с атмосферой.
Клапан предназначен для работы в пневматической сети с давлением до 5 кг/см2 и обеспечивает до 150 200 включений в минуту.
Широкое распространение в пневматических системах клапаны типа КПЭМ (рис. 1.13). Корпуса клапанов изготовляют из пластмассы или силумина. Клапан состоит из корпуса 13, имеющего разъемы для удобства внутренних устройств, толкателя 1, 5, дисковых клапанов 2, 3 и 11 с резиновыми
16
уплотняющими прокладками, пружины 14, двух диафрагм 6 и 16, шарикового клапана 8 и электромагнита 7.
Подвод и отвод воздуха осуществляется через отверстия 4, 12, 15. Питание воздухом лидера управляемого шарикового клапана производится через отверстие 9.
При выключенном электромагните 7 шариковый клапан прикрывает доступ воздуха в наддиафрагменные полости 10 и 17. Под действием пружины 14 и рабочего давления воздуха, поступающего в среднюю полость через отверстие 4, дисковые клапаны 2 и 3 прижимаются к седлам и перекрывают их. Вследствие этого воздух через отверстие 4, внутреннюю полость клапана
иотверстие 15 поступает в одну из полостей цилиндра. Через отверстие 12 и верхнюю полость клапан сообщается с атмосферой.
При выключении электромагнита шариковый клапан под сетевым давлением воздуха, поступающего через отверстие 9, открывается и воздух поступает в наддиафрагменные полости 10 и 17. Под действием усилия, развиваемого диафрагмами, толкатели 1 и 5 перемещают дисковые клапаны 2, 3, 11
исжимают пружину 14. В этом случае воздух через отверстие 12 поступает в полость цилиндра, ранее соединенную с атмосферой, выход в которую перекрывается дисковым клапаном 11. Полость цилиндра, ранее находящаяся под давлением, через открытое клапаном 2 отверстие и нижнюю полость клапана
соединяется с атмосферой.
Клапаны работают при давлении воздуха до 6 кг/см2 и обеспечивают до 150 - 200 включений в минуту. Клапаны типа КПЭМ выпускаются с различным сечением проходных отверстий для воздуха, что дает возможность устанавливать их на машинах малой и большой мощности.
Впоследнее время на контактных машинах типа МТ устанавливаются пневматические клапаны типа КПЭ-4-1 (рис. 1.14).
Для регулирования давления сжатого воздуха в рабочих камерах цилиндров служат пневматические редукторы, позволяющие плавно снижать давление от сетевого до нуля (рис. 1.15).
Основными элементами редуктора являются: винт 1, вращением которого можно регулировать давление, пружина 2, резиновая мембрана 3, резиновая шайба 6, связанная с мембраной через хомутик 8, сопло 5.
Воздух под сетевым давлением поступает через канал 4. При сжатии пружины 2 винтом 1 резиновая мембрана 3 выгибается внутрь корпуса редуктора и отодвигает от сопла 5 через хомутик 8 шайбу 6. Сжатый воздух, подаваемый через клапан 4, поступает через сопло 5 и выходной канал 7 в пневматическую систему машины. С повышением давления в пневматической сети машины возрастает давление и в камере корпуса редуктора. Под действием этого давления мембрана 3 будет выгибаться в противоположную сторону. Когда давление пружины и давление сжатого воздуха, действующего на мембрану, уравновесятся, сопло 5 перекроется резиновой шайбой 6 и подача воздуха в пневматическую сеть машины прекратится.
17
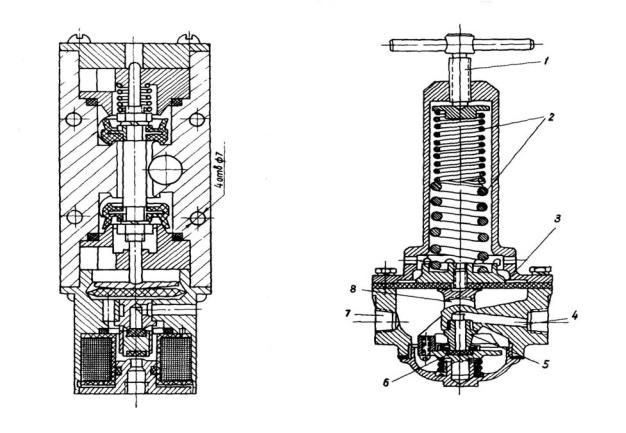
Рис. 1.14. Электропневматический |
Рис. 1.15. Воздушный редуктор типа ВР-1 |
клапан КПЭ-4-1 |
|
С изменением давления сжатого воздуха в сети машины будет изменяться и давление в камере редуктора, действующее на мембрану. Если давление в сети машины будет падать, то мембрана под действием пружины выгнется и откроет проход воздуха через сопло 5. При уравновешивании давления редуктор вновь перекроет доступ сжатому воздуху в машину.
Для смазки подвижных частей пневматической аппаратуры и исполнительных механизмов применяются различные конструкции лубрикаторов.
На рис. 1.16 показан лубрикатор типа ЛП. Лубрикатор состоит из силуминового корпуса, внутри которого проходит канал 7 с небольшим сужением в центре для прохода воздуха. В месте сужения канала выполнены отверстия и установлен шариковый клапан 3, соединяющий через отверстия 1 внутреннюю полость 8, образованную пластмассовым бачком, в который заливается масло.
Сжатый воздух во время работы машины поступает через канал 7 в направлении, указанном стрелкой, и через трубку 4, нормально закрытую шариком 3 с пружиной 2, и отверстие 1 попадает во внутреннюю полость лубрикатора 8 и создает в ней избыточное давление. Под действием давления воздуха масло по трубке 9 поднимается в соединенную в ней камеру, откуда каплями стекает в канал 7. Количество подаваемого масла регулируется винтом 5 и легко наблюдается через прозрачную втулку 6. При очередной подаче воздуха падающие капли распыляются и вместе с воздухом попадают к местам смазки.
18
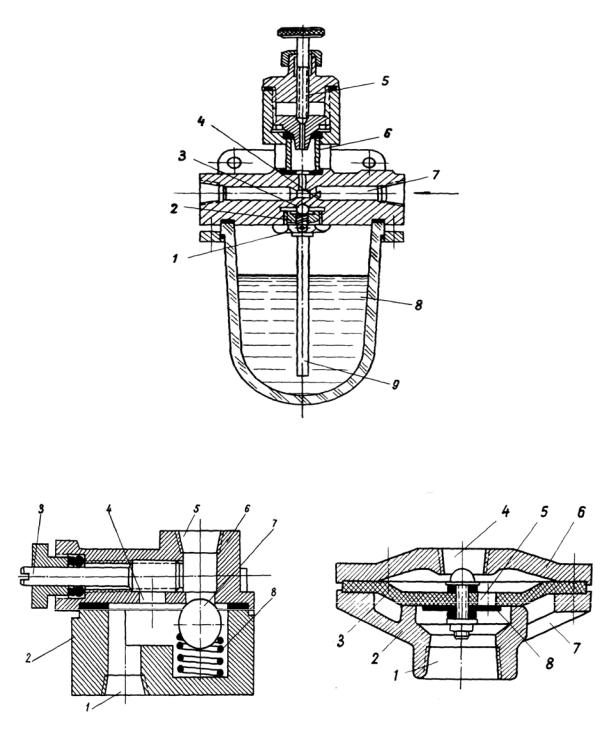
Рис. 1.16. Лубрикатор типа ЛП
Рис. 1.17а. Дросселирующий клапан |
Рис. 1.17б. Выходной клапан типа |
типа КДП-1-1 |
КПВМ-15/25 |
Для регулирования скорости перемещения исполнительных механизмов и смягчения ударов во время работы применяются дросселирующие клапаны. Дросселирующие клапаны обеспечивают свободный проход воздуха в одном
направлении и торможение прохода воздуха в другом.
На рис. 1.17 а приведен дросселирующий клапан типа КДП-1-1. Клапан состоит из литого силуминового корпуса 2, имеющего отверстия 1 и 5, крыш-
19
ки 6, шарика 7, пружины 8, регулирующего винта 3. При подаче воздуха в канал 5 последний отжимает шарик и свободно проходит в канал 1 и далее в пневматический цилиндр. При обратном движении воздуха шарик закрывает отверстие, которое изменяется винтом 3. Величиной открытия канала регулируют скорость выхода воздуха из системы.
На рис. 1.17 б показан выхлопной клапан типа КПВМ-15/25, служащий для быстрого выпуска воздуха в атмосферу, минуя электропневматические клапаны.
Клапан состоит из литого силуминового корпуса 2 с отверстиями 1 и 7, крышки 6 с отверстием 4, резиновой диафрагмы 3 с отверстием 5 и клапана 8.
При подаче воздуха через отверстие 4 резиновая диафрагма 3 прижимается к седлу корпуса 2 и перекрывает отверстие 7. Воздух через отверстие 5, отжимая клапан, поступает через канал 1 в рабочую камеру цилиндра. При выключении электропневматического клапана и прекращения подачи воздуха в канал 4 резиновая диафрагма 3 под действием избыточного давления в цилиндре поднимается и открывает свободный выход воздуха через отверстие 7. Благодаря большим проходным сечениям 7 достигается более быстрый выход воздуха из рабочих камер цилиндра, чем при работе одного электропневматического клапана.
Электроды и электрододержатели
Всвязи с необходимостью токопровода и передачи механических усилий на свариваемые детали предъявляются высокие требования к материалу электродов. Электроды должны обладать высокой электропроводимостью, высокой механической прочностью при больших температурах и высокой теплопроводности. Для обеспечения стойкости электродов последние, как правило, имеют водяное охлаждение.
Материалом для изготовления электродов служат в основном сплавы меди с хромом, кадмием, бериллием и другими присадками, обеспечивающими сплаву высокую твердость при достаточной электропроводности. Наибольшее распространение при изготовлении электродов получили сплавы: ЭВ, МЦ4, МЦ5Б, БрХ-07, НБТ.
Конструктивное выполнение электродов (рис. 1.18) зависит от конфигурации деталей. Контактная поверхность электрода заправляется по плоскости или по сфере. Крепление электрода в электрододержателе должно обеспечить легкий съем и замену электрода, быть достаточно надежным и предохраняющим электрод от случайных выпадений. Это условие обеспечивается конусом или резьбой на посадочной части электрода.
Взависимости от усилий, действующих на электроды, применяется и различная конусность. Наибольшее распространение в настоящее время получил конус Морзе. Применяются также конусности 1:10 и 1:15.
20
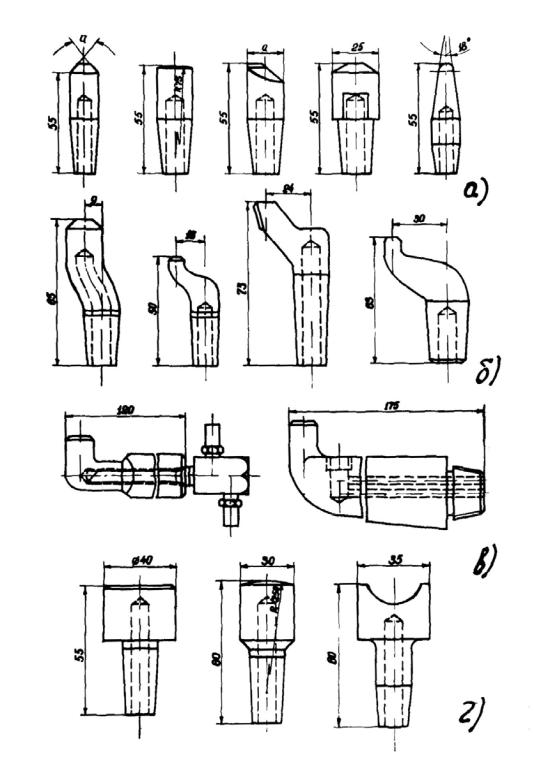
Рис. 1.18. Электроды для точечных машин
Сменные электроды крепятся в электрододержателях (рис. 1.19), закрепляемых в консолях машин. Конструкция электрододержателя должна обеспечивать токоподвод и подачу охлаждающей воды к электроду.
Электрододержатели закрепляются в токоведущих консолях точечных машин (рис. 1.20). При сварке деталей сложной конфигурации используется
21
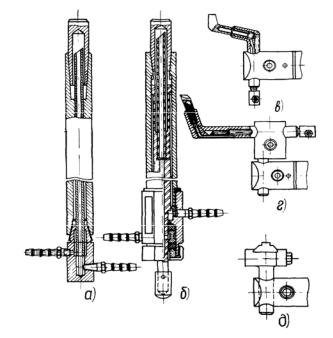
специальная оснастка электрододержателей и консолей (рис. 1.21). Электрододержатели и консоли изготовляются из меди и ее сплавов.
Регулятор цикла сварки
Рассмотрим распространенный регулятор контактной сварки РКС801ЛМ. Регулятор предназначен для управления циклом сварки контактных машин переменного тока. Он обеспечивает:
•управление тиристорным контактором и двумя электропневматическими клапанами сжатия
•работу машин контактной сварки в одиночном и автоматическом режимах (в автоматическом режиме выдержка времени «предварительное сжатие» исключается;
•регулирование величины сварочного тока с цифровой индикацией выбранного значения;
•один - два импульса сварочного тока в течение одного цикла сварки;
•плавное нарастание переднего фронта первого импульса сварочного тока (модуляция) с цифровой индикацией выбранного значения;
•автоматическую настройку коэффициента мощности cos с изменением полярности включения/выключения первой полуволны сварочного тока;
•стабилизацию действующего значения сварочного тока при колебаниях напряжения питающей сети;
•сохранение вводимых параметров в памяти регулятора;
•импульсную сварку (от 1 до 3-х импульсов сварочного тока).
Рис. 1.19. Электрододержатели для универсальных точечных машин:
а - типовой цилиндрический; б - цилиндрический с устройством для выбивки электродов; в, г - наклонный и горизонтальный;
д - для крепления электродов с плоской рабочей поверхностью
22
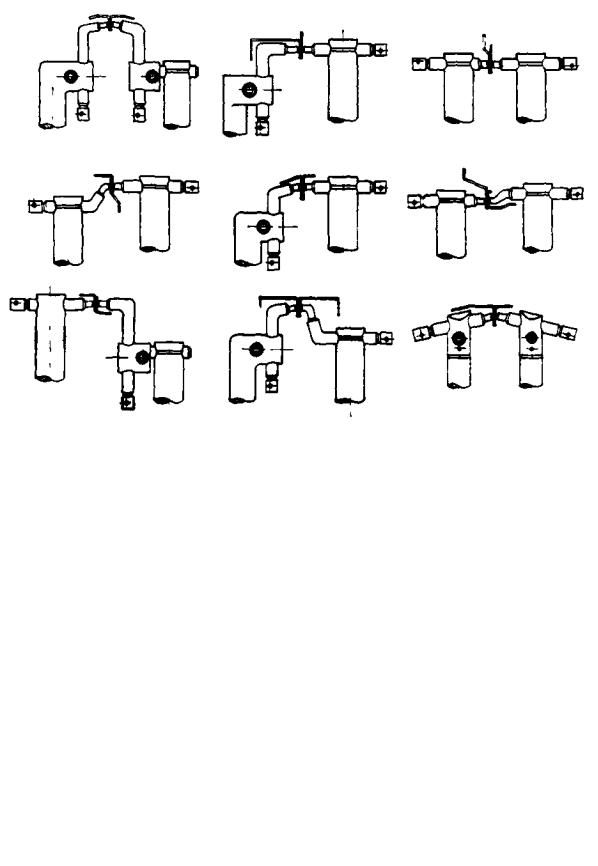
Рис. 1.20. Конструкция консолей для универсальных точечных машин:
а- для машин небольшой мощности; б - для крепления электродов с охлаждением;
в- для машин средней мощности; г, д - для наклонного и горизонтального крепления электрододержателя; е - для машин средней и большой мощности
Рис. 1.21. Электрододержатели для сварки деталей сложной конфигурации
23
Регулятор выполнен в виде конструктивного блока соединяемого. На передней панели расположены органы управления и индикации:
-кнопки задания параметров цикла сварки
-кнопки задания величины нагрева 1 и 2, модуляции, количества пульсаций -ток 1;
-переключатели управления режимами работы;
-светодиодные индикаторы позиций и величин сварочного цикла;
-индикатор наличия напряжения сети;
-индикаторы работы клапанов 1 и 2; На задней панели расположены:
-разъем для подключения регулятора к контактной машине;
-сетевой предохранитель;
-предохранители клапанов;
-клемма заземления.
Прерыватели тока
В подавляющем большинстве машин для контактной электросварки, как однофазных, так и трехфазных (с выпрямлением во вторичном контуре, конденсаторных), подключение сварочного трансформатора производится вентильными контакторами. Исключением являются машины для стыковой сварки, некоторые индивидуальные машины с малым числом включений, например трубные станы, а также шовные машины малой мощности с непрерывным процессом сварки, в которых находят применение электромеханические контакторы. Основными достоинствами вентильных контакторов, обеспечивающими их широкое использование, являются: а безинерционность включения сварочного тока; б выключение сварочного тока при его переходе через нулевое значение; в возможность осуществления программного управления сварочным током относительно несложным способом; г возможность безыскровой коммутации больших токов (в случае применения игнитронов), достигающих нескольких тысяч ампер.
В машинах мощностью, не превышающей примерно 400 кВ-А, в настоящее время применяются тиристорные контакторы, так как они обладают рядом достоинств по сравнению с игнитронными: а меньшее падение напряжения (1,5-2,0 В на тиристорах вместо 15-20 В на игнитронах), что обеспечивает более высокий КПД тиристорных контакторов; б больший срок службы; в более простая аппаратура управления, так как для поджигания игнитронов требуются вспомогательные вентили. Меньшие габариты тиристоров по сравнению с игнитронами, а также отсутствие необходимости во вспомогательных вентилях позволяют уменьшить габариты контакторов, их массу. К преимуществам тиристорных контакторов следует также отнести значительно меньший расход охлаждающей воды. В машинах большой мощности продолжают применять игнитронные контакторы, при этом в качестве вспомогательных вентилей для поджигания игнитронов используют тиристо-
24
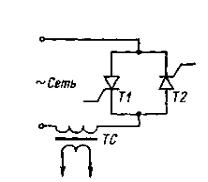
ры. С ростом пропускной способности тиристоров по току следует ожидать дальнейшего уменьшения области применения игнитронов.
В контактных машинах применяются в основном тиристорные контакторы с встречно-параллельным включением вентилей (рис. 1.22). Вентили включаются в питающую сеть последовательно с первичной обмоткой сварочного трансформатора. Каждый вентиль пропускает ток только в одном направлении (один полупериод переменного тока). При симметричной работе обоих вентилей в установившемся режиме через сварочный трансформатор будут последовательно протекать симметричные импульсы тока противоположной полярности. В схеме с встречно-параллельным соединением вентилей их одновременное включение невозможно, так как малое падение напряжения на работающем вентиле исключает возможность включения параллельного. Поэтому длительность протекания тока через каждый из вентилей при их включении через полупериод (угол ), что соответствует наиболее распространенному режиму, ограничена углом ≤ . Угол, при котором вентиль может быть открыт, ограничен при этом углом сдвига фаз между напряжением питания сварочной машины и током через нее с одной стороны и угломс другой.
Рис. 1.22. Схема однофазных тиристорных контакторов: T1, T2 тиристоры; ТС трансформатор сварочный.
Наибольшее распространение получила серия тиристорных контакторов КТ четырех типов на токи от 250 до 1400А (при ПВ = 20%). Контакторы рассчитаны на совместную работу с регуляторами цикла сварки серии РЦС. В контакторах применена встречно-параллельная схема включения тиристоров. Система охлаждения тиристоров водяная. Контакторы выполнены в виде открытой вертикальной конструкции. Они предназначаются для установки внутри сварочной машины или аппаратного шкафа.
Принципиальная схема контакторов типа КТ-1 приведена на рис. 1.23. Контакторы рассчитаны на синхронное включение. В их конструкции предусмотрен промежуточный трансформатор, обеспечивающий изоляцию источника импульсов управления от управляющих электродов и катода тиристоров, находящихся под сетевым напряжением. Контакторы рассчитаны на импульсы управления, следующие с частотой 100 Гц. В контакторе КТ-1 приме-
25
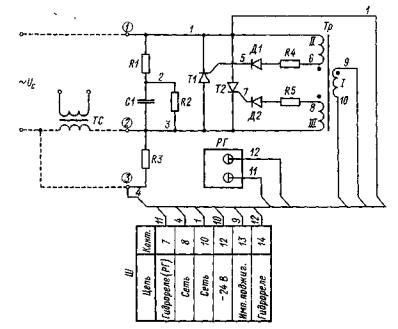
нены тиристоры типа ТВ-200. Скорость нарастания напряжения на тиристорах ограничивается цепью R1C1. Для разряда конденсатора С1 после отключения контактора от сети служит резистор R2. Резистор R3 ограничивает повышение напряжения на контакторе, возникающее при холостом ходе и малой мощности трансформатора вследствие резонанса в цепи R1C1-ТС. Возможные импульсные перенапряжения достигают 900 В. Максимальная скорость нарастания напряжения на тиристорах в конце каждой полуволны тока с учетом действия цепи R1C1 составляет 10-12 В/мкс. Максимальная скорость нарастания тока 9 А/мкс.
Рис. 1.23. Электрическая схема тиристорного контактора типа КТ-1
По экспериментальным данным, контактор КТ-1 может работать в течение 500 ч в форсированном режиме при токе 400 А и длительности импульса тока через контактор 2 с.
Порядок выполнения работы
1.Ознакомиться с основными узлами системами универсальных точечных машин общего назначения.
2.Выявить технологические возможности представленной машины. 3.По прилагаемым описанию, схемам и чертежам изучить конструкцию
ивзаимодействие всех узлов машины.
4.Разобрать принцип работы электрической силовой схемы машины, привода сжатия электродов.
5.Ознакомиться с регулятором работы машины.
6.Рассмотреть пневматическую схему и систему охлаждения.
26
7.При вынутых ножах переключателя ступеней опробовать работу машины. Включая машину в сеть, следует соблюдать осторожность, так как напряжение - 380 В.
8.Произвести пробную сварку листовых заготовок.
9.Отключить машину.
Содержание отчета
Указать марку машины, ее технологические возможности, пределы регулирования параметров режима сварки. Описать устройства регулирования режима сварки. Изобразить возможные циклы сварки, которые может обеспечить данная машина. Нарисовать пневматическую схему машины с ее кратким пояснением. Вычертить силовую принципиальную электрическую схему машины с пояснением работы контактора, переключателя ступеней. Записать последовательность операций и действий при подготовке машины к работе. Определить условную плотность тока во внешних элементax сварочного контура (контактной поверхности электрода, электроде, электрододержателе, хоботе, гибкой шине).
Контрольные вопросы
1.Общее устройство машины для контактной точечной сварки.
2.Виды приводов усилия сжатия электродов.
3.Устройство и принцип работы пневмопривода машины МТ-807.
4.Устройство и принцип работы пневмопривода машины МТПУ-300, его отличие от предыдущего. Какие циклы сварки он может обеспечить?
5.Почему пневмопривод применяется гораздо чаще, чем другие виды приводов?
6.Преимущества и недостатки, область применения поршневых и диафрагменных приводов.
7.Составные части пневмопривода?
8.Перечислите детали сварочного контура, материал, из которого они изготовлены.
9.Требования к электродам точечной машины, материал электродов.
10.Назначение, устройство и принцип работы прерывателя тока.
11.Включение и подготовка машины к работе.
12.Техника безопасности при работе на установках контактной сварки.
27
Лабораторная работа 2
ИЗУЧЕНИЕ КОНСТРУКЦИИ И ПРИНЦИПА ДЕЙСТВИЯ КОНТАКТНОЙ ШОВНОЙ МАШИНЫ
Цель работы ознакомиться с конструкцией и принципом действия типовых контактных шовных машин, детально изучить конструкцию и принцип действия всех узлов и систем одной шовной машины, приобрести навыки в управление машиной и настройке параметров режима сварки, рассчитать некоторые элементы контактной машины.
Оборудование и материалы
1.Шовная машина.
2.Описание машины, чертежи и схемы.
3.Измерительный инструмент.
4.Образцы для пробной сварки.
Теоретические сведения
Отличие шовной сварки от точечной в том, что одним из электродов служит вращающийся ролик, а другим ролик или неподвижная планка. В отдельных случаях вращающийся ролик заменяется поворачивающимся сектором.
При шовной свайке точки могут ставиться с перекрытием, образуя сплошной прочноплотный шов, или на некотором расстоянии друг от друга, образуя прочный шов. Благодаря этим особенностям основные узлы - привод давления, корпус, верхние и нижние консоли, источник сварочного тока (трансформатор) - по своей конструкции аналогичны существующим узлам точечных машин.
Так как электродами шовных машин являются вращающиеся ролики, то неотъемлемой частью конструкции шовных машин будет привод вращения роликов.
На рис. 2.1 показана наиболее распространенная шовная машина МШ- 20-13. Машины МШ выпускаются в двух исполнениях: для сварки продольных и поперечных швов. Они имеют пневматический привод механизма сжатия с вертикальным ходом верхнего ролика. Нижний токоподводящий вал сварочного ролика приводится во вращение электродвигателем через редуктор и карданную передачу.
Система токоподвода представляет собой скользящие контакты через вращающиеся токоведущие валы, на которых крепятся роликовые электроды.
28
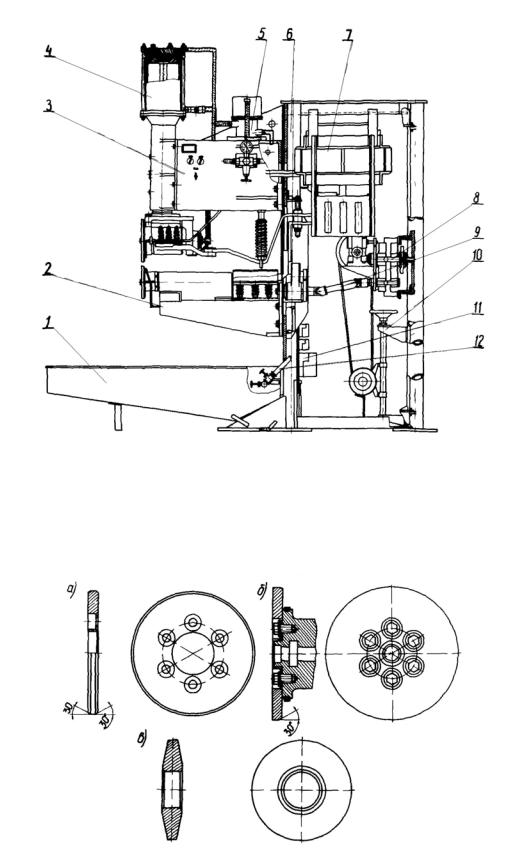
Рис. 2.1. Шовная машина МШ 20-13: 1 - водосборная ванна; 2 - нижняя консоль; 3 - верхняя консоль; 4 - силовой пневмо–цилиндр;
5 - электропневмоклапан; 6 - стойки корпуса; 7 - сварочный трансформатор; 8 - редуктор; 9 - карданный вал; 10 - устройство для натяжения ремня;
11 - блок управления педальной кнопкой; 12 - патрубки водяного охлаждения
Рис. 2.2. Электроды шовных машин: а - ролик с двусторонней заточкой и креплением на шпильках; б - с односторонней заточкой и креплением на шпильках;
в - с двусторонней заточкой и посадкой на втулку
29

Система водяного охлаждения служит для охлаждения витка сварочного трансформатора, контактных колодок, хоботов и роликовых электродов. Для этой цели в токоведущих частях сверлят отверстия. Иногда по периферии охлаждаемой поверхности приваривают трубки, по которым течёт вода. Охлаждение роликовых электродов может быть внутренним или наружным.
Рис. 2.3. Конструкция токоподводов шовных машин МШ:
а - токоподвод верхнего электрода; б - токоподвод нижнего электрода машины для поперечной сварки; в - токоподвод нижнего электрода для продольной сварки; 1 - ролик, 2 - токоведущий вал, 3 - охлаждающая трубка, токоподводящая колодка, 5 - сальник, 6 - ниппели водяного охлаждения
30
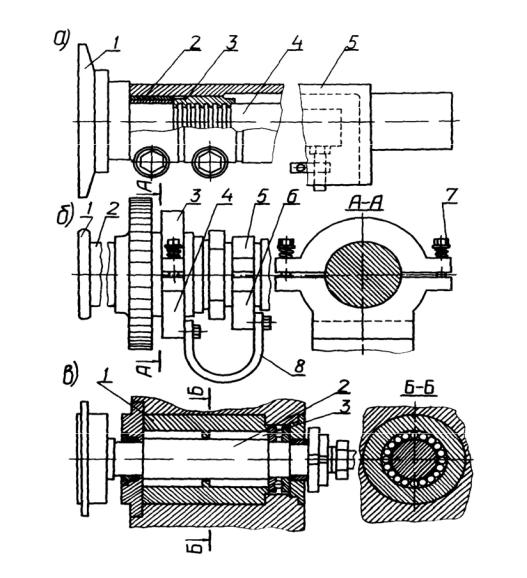
Рис. 2.4. Конструкция токоподводов шовных машин: а - токоподвод нижнего ролика машины для поперечной сварки (1 - ролик, 2, 3 - бронзовые токоподводящие втулки, 4 - токоподводящий вал, 5 - механизм привода вращения вала); б - токоподвод нижнего приводного ролика (1 - ролик, 2 - токоподводящий вал, 3, 4, 5, 6 - токоподводящие колодки, 7 - регулировочный винт, 8 - токоподводящая шина); в - токоподвод ведомого ролика с игольчатыми подшипниками (1 - токоподводящая втулка,
2 - токоподводящий вал, 3 - игольчатый подшипник)
На рис. 2.2 представлены различные конструкции электродов шовных машин. Для обеспечения необходимой стойкости ролики изготовляют из различных электродных сплавов Бр.Х, ЭВ, МЦ, НБТ. При работе электроды интенсивно охлаждаются водой.
На рис. 2.3 и 2.4 показаны конструкции токоподводов шовных машин. Для надёжной работы токоподвод трущейся пары выполняют из разных материалов и применяют токопроводящую граффито-касторовую смазку.
Вращение роликов шовных машин осуществляется механизмами при-
вода (рис. 2.5 и 2.6).
31
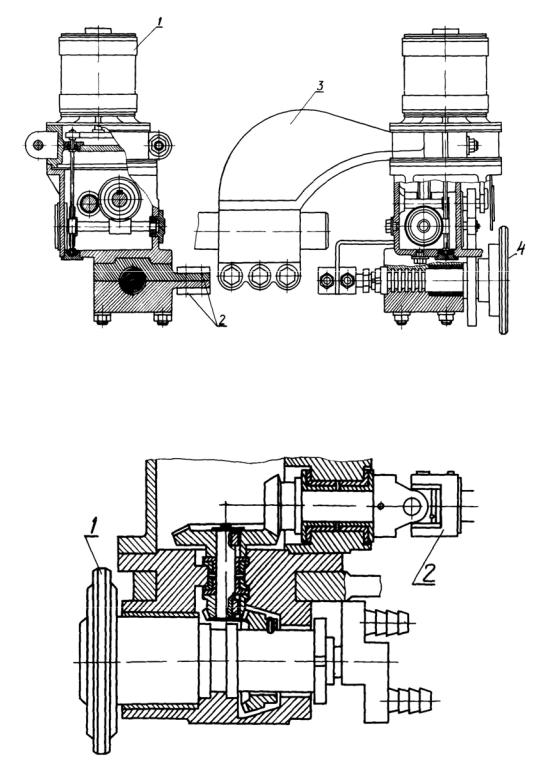
Рис. 2.5. Механизм привода верхнего ролика шовной машины для поперечной и продольной сварки: 1 - электромотор; 2 - токоподводящие шины;
3 - кронштейн привода; 4 – ролик
Рис. 2.6. Механизм привода верхнего ролика шовной машины для поперечной и продольной сварки с приводом от карданного вала: 1 - ролик; 2 - карданный вал
На рис. 2.7 конструкция привода роликов шовной машины типа МШПБ-150 для сварки бензобаков.
Общая кинематическая схема механизма привода шовной машины типа МШПР-300/1200-2 приведена на рис. 2.8.
32
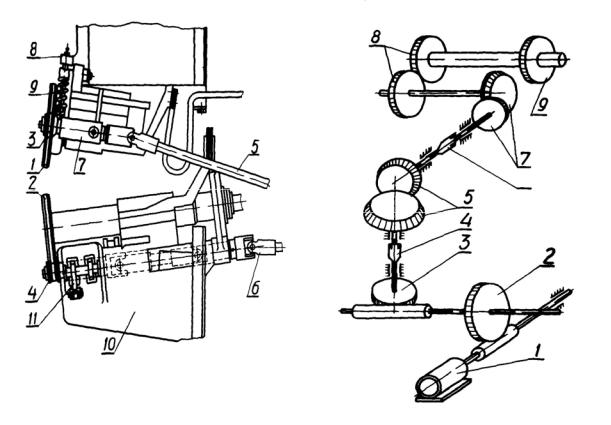
Рис. 2.7. Механизм привода ролика шовной |
Рис. 2.8. Кинематическая схема машины |
машины МШПБ для сварки бензобаков: |
МШПР - 300/1200 - 2: 1 - электродвигатель; |
1 и 2 ролики; 3 и 4 - стальные шарошки; |
2 и 3 червячные пары; 4 и 6 - карданные |
5 и 6 карданные валы; 7, 8, 9 - опорные |
валы; 5 и 7 - пары конических шестерен; |
кронштейны; 10 - консоль; |
8 - цилиндрические пары; |
11 - опоры шарошек |
9 - сварочный ролик |
Вшовных машинах применяется в основном плавное регулирование скорости сварки.
Скорость вращения роликов регулируется при помощи шестерен в передаточном редукторе, промежуточным вариатором, изменением вращения оборотов у приводных двигателей постоянного тока и т. д.
Привод сжатия роликов у шовных машин может быть пружинный, электромеханический, пневматический, гидравлический.
Встандартных машинах для продольной сварки принудительное вращение имеет верхний ролик. Нижний ролик начинает вращаться в процессе поступательного движения свариваемого изделия в результате трения между рабочей поверхностью ролика и деталью. При принудительном вращении обоих роликов необходимо обеспечить равенство линейных скоростей на их рабочих контактных поверхностях.
Схемы приводов шовных машин во многих случаях выполняются по типу приводов давления точечных машин. Основное требование приводов и
схем шовных машин обеспечение постоянства усилия сжатия роликов в процессе сварки.
33
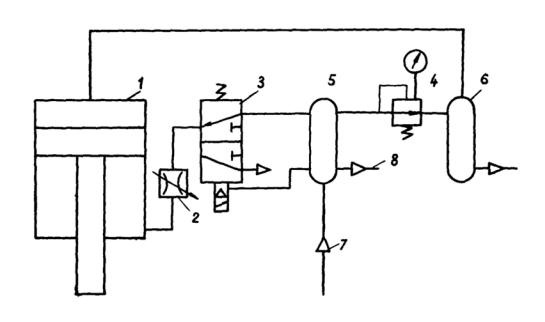
На рис. 2.9 приведена типичная пневматическая схема привода давления шовных машин типа МШ.
По этой схеме однопоршневой цилиндр 1 своей верхней камерой соединен с группой ресиверов 6, давление в которых регулируется редуктором 4. Нижняя камера цилиндра через дросселирующий клапан 2 и электропневматический шланг 3 соединена с ресивером 5, подключенным через запорный вентиль 7 к воздушной сети. При включенном электропневматическом клапане 3 воздух из сети подается в нижнюю камеру цилиндра и поднимает поршень вверх. Воздух, находящийся в верхней камере, вытесняется в ресивер и несколько сжимается.
Рис. 2.9. Пневматическая схема привода давления шовных машин типа МШ: 1 - силовой цилиндр; 2 - дросселирующий клапан; 3 - электропневмоклапан;
4 - воздушный редуктор; 5 и 6 - ресиверы; 7 - воздушный кран; 8 - краны для слива воды
При выключении клапана 3 воздух из нижней камеры через дроссель 2, смягчающий удары электродов при опускании, выходит в атмосферу, и поршень под давлением воздуха, находящегося в ресивере 6, опускается и создает рабочее давление на роликах. Благодаря тому, что верхняя камера не соединяется с атмосферой и воздух из нее не расходуется, давление в камере легко регулируется и поддерживали постоянным. Влага, накопившаяся в ресивере, периодически выпускается через спускные краны 8.
Схемы питания и управления шовных машин
Питание сварочного контура шовных машин производится однофазным током промышленной частоты при непрерывной его подаче, отдельными импульсами тока промышленной частоты, импульсами тока низкой частоты, импульсами тока за счет энергии, накопленной в конденсаторах.
Циклограммысварочноготокаиусилиянаэлектродахпоказанынарис. 2.10.
34
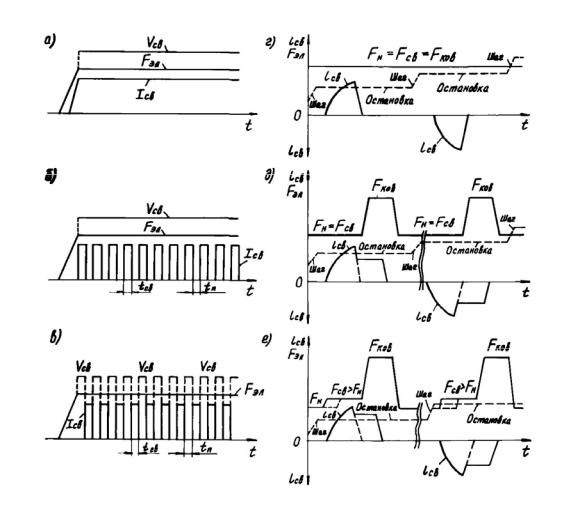
Питание сварочного контура током промышленной частоты при непрерывной его подаче (рис. 2.10 а) применяется только на машинах малой мощности для сварки изделий из малоуглеродистой стали толщиной до 1 мм.
Наиболее широкое распространение в шовных машинах находит питание сварочного контура импульсами тока промышленной частоты (рис. 2.10 б). Применение импульсной подачи тока обеспечивает высокое качество сварки, а также большую стойкость электродов по сравнению со сваркой при непрерывной подаче тока.
Рис. 2.10. Циклограммы сварочного тока и усилия на электродах шовных машин; непрерывная подача сварочного тока с постоянным усилием на электродах и скоростью сварки: а, б - сварка отдельными импульсами тока; в - шаговая сварка с прерывистым перемещением свариваемых деталей и импульсным включением сварочного тока во время остановки роликов; г, д, е - циклограммы работы трехфазной роликовой шаговой машины МШШТ-1000 Г
Для импульсного включения сварочного тока питание сварочного контура однофазных машин производится через тиристорные контакторы. Последние обычно снабжены устройством отсчета длительности импульса сва-
35
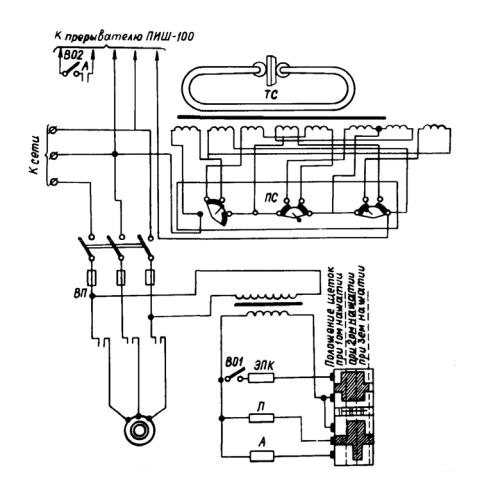
рочного тока, а также паузы между импульсами. Это обеспечивает более точную дозировку энергии, выделяемой при сварке. В тиристорных контакторах предусматривается стабилизация сварочного тока при колебаниях напряжений питающей сети.
Рис. 2.11. Электрическая силовая схема шовной машины типа МШП
Для питания шовных машин с повышенным вылетом электродов, рассчитанных на большие сварочные токи (более 50000 А), применяются преобразователи частоты.
При шовной сварке деталей малой толщины используют конденсаторные машины.
На рис. 2.11 приведена принципиальная схема шовных машин с питанием импульсами переменного тока промышленной частоты. Питание сварочного контура осуществляется через игнитронный прерыватель.
Регулировка эффективного значения сварочного тока может производиться ступенчато изменением коэффициента трансформации сварочного
трансформатора ТС (переключатель ступеней ПС), или плавно изменением угла зажигания тиристоров прерывателя.
Управляют шовной машиной с помощью специальной трехпозиционной педальной кнопки барабанного типа. При первом нажатии кнопки вклю-
36
чается катушка пневмоэлектрического клапана, через который подается воздух для зажатия свариваемых изделий. При втором нажатии педальной кнопки дополнительно включается электромагнитный пускатель П, включающий электродвигатель вращения сварочных роликов. Одновременно через промежуточное реле А включается тиристорный прерыватель. При третьем нажатии педали отключается питание катушки электропневматического клапана, пускателя и реле. Схема приходит в исходное состояние (выключается сварочный ток, прекращается вращение роликов и снимается усилие на роликах).
Порядок выполнения работы
1.Ознакомиться с типом и технологическими возможностями шовной машины.
2.По прилагаемым описанию, схемам и чертежам разобрать конструкцию и взаимодействие всех узлов машины.
3.Изучить конструкцию узла верхнего ролика (привода вращения и токоподвода).
4.Изучить электрическую и пневматическую схемы водяного охлаждения машины.
5.Ознакомиться с конструкцией педальной кнопки.
6.При включенном сварочном токе опробовать работу машины. Вклю-
чив машину в сеть, будьте осторожны! Напряжение 380 В.
7.Подробно ознакомиться с техникой регулировки параметров режима
сварки.
8.Установить определенный режим сварки и произвести сварку образцов. Откорректировать режим сварки.
9.Отключить машину.
Содержание отчета
Указать марку машины, ее технологические возможности, пределы регулирования параметров режима сварки. Описать, какими устройствами производится регулирование параметров режима сварки. Нарисовать и описать возможные циклы сварки, которые может обеспечить данная машина. Привести пневматическую схему машины с ее кратким пояснением. Вычертить силовую принципиальную электрическую схему машины с ее кратким пояснением. Записать последовательность операций при подготовке машины к работе. Определить возможные минимальную и максимальную скорости перемещения свариваемых деталей. Описать способы центровки сварочных роликов. Произвести расчет нижнего токоподводящего хобота машины и сравнить расчетные данные с реальными.
37
Контрольные вопросы
1.Основные узлы шовной машины. Их разновидности, назначение, принцип работы, конструктивное оформление.
2.Виды шовной сварки. Их преимущества и недостатки.
3.Устройство и принцип работы тиристорного контактора?
4.Как осуществляется токоподвод к сварочным роликам?
5.Укажите места смазки трущихся деталей машины (ответы сопровождать демонстрацией на машине).
6.Как осуществляется ступенчатая и плавная регулировка скорости
сварки?
7.Как подготовить машину к работе?
8.Какова техника настройки машины на заданный режим?
9.Техника безопасности при работе на шовных машинах.
38
Лабораторная работа 3
ИЗУЧЕНИЕ КОНСТРУКЦИИ И ПРИНЦИПА ДЕЙСТВИЯ КОНТАКТНОЙ СТЫКОВОЙ МАШИНЫ
Цель работы ознакомиться с конструкцией универсальных машин для стыковой сварки, детально изучить конструкцию и принцип действия всех узлов и систем одной контактной машины, приобрести навыки в управлении машиной и настройке параметров режима сварки, рассчитать некоторые элементы контактной машины.
Оборудование и материалы
1.Машина для стыковой сварки.
2.Описание, чертежи и схемы машины.
3.Набор линейного измерительного инструмента.
4.Образцы для пробной сварки.
Теоретические сведения
Машины для стыковой сварки по своей конструкции резко отличаются от приведенных выше точечных, шовных и рельефных машин.
На рис. 3.1 приведена конструктивная схема стыковой машины. В отличие от точечных, шовных и рельефных машин электроды стыковых машин в большинстве случаев выполняют не только функцию токоподвода, но и удерживают свариваемые детали от проскальзывания при возникновении усилий при сварке. В отдельных случаях, например в цепесварочных автоматах, они осуществляют отдельно зажатие и токоподвод к деталям. Сварочные усилия создаются отдельным приводом подачи и осадки. Раздельное размещение зажимов и привода подачи и осадки сказывается и на конструкции станины, которая в стыковых машинах должна служить не только для размещения всех узлов и деталей, но и воспринимать значительные механические усилия, возникающие при сварке.
Передвижение подвижной плиты стыковых машин осуществляется приводом подачи и осадки. В задачу последнего входит перемещение свариваемых деталей с заданной скоростью и создание усилия на свариваемых поверхностях. Возврат плиты в исходное положение также производится приводом подачи. В зависимости от мощности и назначения стыковой машины приводы подачи и осадки используют рычажными, винтовыми, грузовыми, пружинными, электромоторными, пневматическими и гидравлическими. Во многих случаях комбинируют различные типы привода. Например, привод оплавления выполняется электромоторным, а осадка - с помощью пневмогидравлических устройств.
39

Рис. 3.1. Типовая схема стыковой машины: 1 - переключатель ступеней; 2 - направляющие; 3 - направляющие втулки; 4 - верхние электроды; 5 - неподвижный зажим; 6 - подвижный зажим; 7 - нижние электроды; 8 - привод оплавления и осадки; 9 - панель управления; 10 - соединительные шины; 11 - трансформатор; 12 - станина машины
На рис. 3.2 представлены механизмы подачи рычажного типа с коленчатыми рычагами. Максимальное усилие осадки достигается при выпрямленном положении рычагов.
Вмашинах для сварки сопротивлением в большинстве случаев применяют пружинный привод (рис. 3.3). Максимальное усилие, развиваемое пружинным приводом, достигает 6 кН. В автоматических машинах применяются электромоторный, пневматический и гидравлический приводы.
Вмашинах для сварки оплавлением применяются единые приводы оплавления и осадки - механический (машина МСМУ-150) или гидравлический (машина МСГ-300, МСГ-500 и др.), а также раздельные кулачковые электродвигательные приводы при оплавлении и пневматические (машина ЦСТ-200), пневмогидравлические (МСЛ-300, МСЛ-500 и др.) или гидравлические (машина Л-120) приводы при осадке.
Конструкция электропривода подачи, применяемого, в частности, на машине МСО-606, представлена на рис. 3.4. Вращательное движение электродвигателя преобразуется в поступательное движение подвижной плиты посредством кулака. Максимальное усилие осадки, развиваемое в электромоторных приводах, доходит до 350 кН.
Вмашинах с пневматическим и гидравлическим приводом движение подвижной плиты осуществляется пневматическими или гидравлическими цилиндрами, подача воздуха или жидкости в которые регулируется при помощи различных пневматических, пневмогидравлических или гидравличе-
ских схем. Максимальное усилие осадки пневматических приводов до 150 кН, а гидравлических до 1000 кН и выше.
40
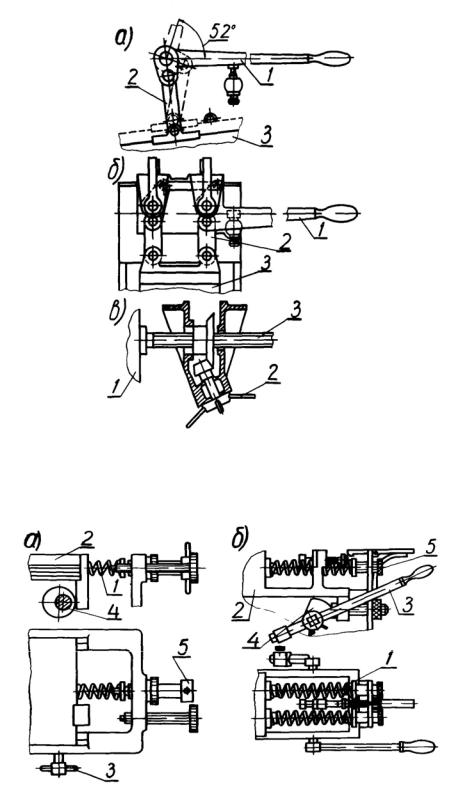
Рис. 3.2. Механизмы подачи: а - рычажного типа с одним коленчатым рычагом; б - рычажного типа с двумя коленчатыми рычагами (1 - рукоятка-рычаг; 2 - серьга;
3 - подвижная плита); в - штурвального типа (1 - подвижная плита, 2 - штурвал, 3 - винт)
Рис. 3.3. Пружинный механизм подачи: а - с одной пружиной; б - с двумя пружинами; 1 - пружина, 2 - подвижная плита; 3 - рукоятка; 4 - эксцентрик; 5 - винт
для регулировки натяга пружины
41
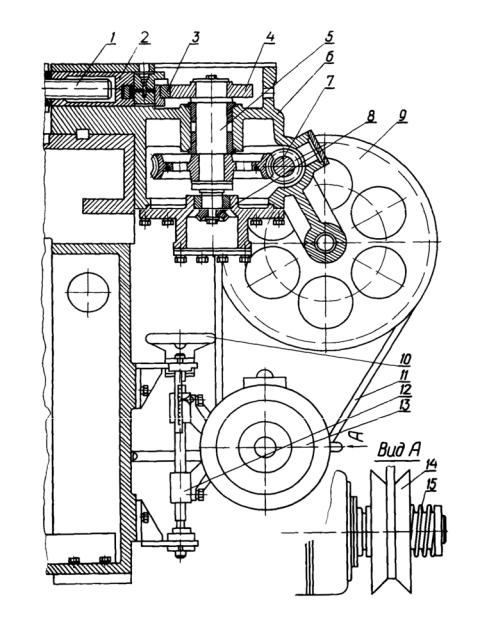
Управление пневматическими или гидравлическими цилиндрами привода подачи и осадки производится золотниками или клапанами, объединенными общей пневматической или гидравлической схемой.
Зажимы стыковых машин должны обеспечить надежное зажатие свариваемых деталей и подвод сварочного тока к изделию. В зависимости от конфигурации изделия подвод тока выполняется односторонним (к одним нижним губкам) или двусторонним (к верхним и нижним губкам). По своей конструкции зажимы должны обеспечивать легкую установку свариваемых деталей, быстрое зажатие без применения инструмента и легкое удаление свариваемых изделий.
Рис. 3.4. Электромоторный привод подачи стыковой машины: 1 - регулировочный винт; 2 - ползун; 3 - ролик; 4 - кулак; 5 - вал; 6 - редуктор; 7 - червяк; 8 - коническая шестерня привода механизма управления; 9 - шкивы; 10 - маховик регулировочного винта;
11 - ремень; 12 - подвижная каретка; 13 - электродвигатель; 14 - вариатор; 15 - пружина
42
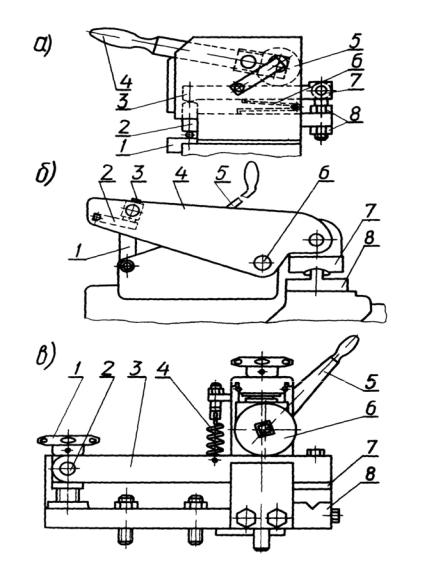
В зависимости от мощности и типа машин применяют различные типы зажимов эксцентриковые, рычажные, винтовые, пневматические, пневмогидравлические и гидравлические. Каждый из этих зажимов характеризуется усилиями зажатия и быстротой действия, определяющей производительность машины.
Для небольших усилий при сварке деталей малых сечений применяют эксцентриковые зажимы (рис. 3.5). Благодаря простоте конструкции и достаточной производительности эксцентриковые зажимы нашли широкое применение в машинах малой мощности для сварки сопротивлением проволок.
Рис. 3.5. Зажимы эксцентрикового типа для стыковых машин: а - с прямолинейным ходом верхней губки ( 1 - нижняя губка; 2 - верхняя губка; 3 - нажимная планка; 4 - рукоятка; 5 - эксцентрик; 6 - возвратная пружина; 7 - регулировочный винт; 8 - регулирование гайки ); б - с радиальным ходом верхней губки ( 1 - эксцентрик; 2 - планка; 3 - опорный винт; 4 - рычаг; 5 - рукоятка; 6 - ось; 7 - верхняя губка; 8 - нижняя губка); в - прямого действия
(1 - регулировочные винты; 2 - ось; 3 - нажимная планка; 4 - возвратная пружина; 5 - рукоятка; 6 - эксцентрик; 7 - верхняя губка; 8 - нижняя губка)
43
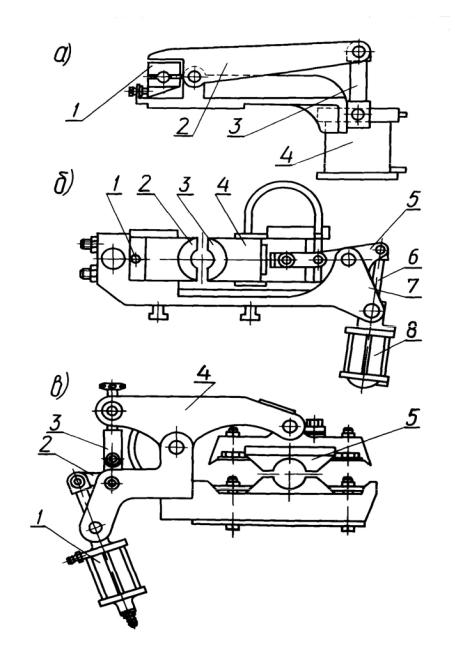
Рис. 3.6. Быстродействующие зажимы рычажного типа с пневматическим приводом:
а- с радиальным ходом верхней губки (1 - верхняя губка; 2 - рычаг; 3 - шток; 4 - цилиндр);
б- с горизонтальным ходом губки (1 - регулировочный винт; 2 - неподвижная губка;
3 - подвижная губка; 4 - ползун; 5 - коленчатый рычаг; 6 - шток; 7 - основание зажима; 8 - цилиндр); в - с радиальным ходом верхней губки и выламывающимися рычагами (1 - цилиндр; 2 - коленчатый рычаг; 3 - рычаг; 4 - силовой рычаг; 5 - верхняя губка)
Различные быстродействующие зажимы рычажного типа с пневматическим приводом приведены на рис. 3.6. Зажимы такого типа широко используются на различных стыковых машинах для сварки стержней, труб, ободьев и других деталей. Применение пневматического привода позволяет создать усилие зажатия до 100 кН.
44
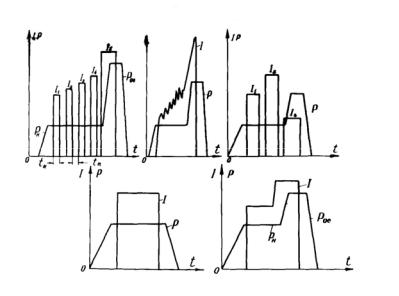
На рис. 3.7 представлены основные циклы сварки, которые выполняются контактными машинами для стыковой сварки.
Питание сварочного контура стыковых машин малой и средней мощности (до 300 - 500 кВА) производится однофазным переменным током. Более мощные машины выпускаются как с однофазным, так и с трехфазным питанием, с преобразованием частоты тока, питающий сварочный контур.
Рис. 3.7. Графики тока и давления при стыковой сварке цветных и черных металлов
В машинах средней и большой мощности, а также в машинах малой мощности, предназначенных для сварки оплавлением цветных металлов и сплавов, весь цикл сварки, за исключением зажатия свариваемых деталей, полностью автоматизированы.
Электрическая схема должна обеспечивать следующим цикл работы стыковой машины в наиболее сложном режиме: 1 зажатие свариваемых деталей; 2 включение сварочного трансформатора; 3 включение системы подачи подвижного зажима (привод оплавления); 4 подачу подвижного зажима до соприкосновения деталей; 5 выдержку времени нагрева свариваемых деталей (после их соприкосновения); 6 отвод деталей; 7 выдержку времени на распространение тепла вдоль свариваемых деталей; 9 осадку; 10выключение сварочного тока; 11 возвращение всех элементов машины в исходное положение
Трансформаторы машин контактной сварки
Трансформатор является источником питания сварочной установки. Он преобразовывает электрическую энергию сети стандартного напряжения в энергию с низким вторичным напряжением (0,2-25 В) и большим током (1000-300000 А). Трансформаторы могут быть со стержневым, броневым или кольцевым сердечником.
45
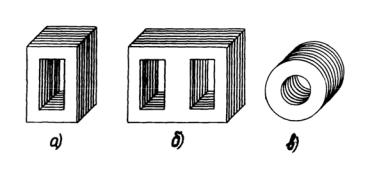
На рис. 3.8 представлены различные типы сердечников трансформаторов машин контактной сварки.
Вторичная обмотка трансформаторов машин контактной сварки состоит обычно из одного витка. Благодаря большим силам тока и необходимости получения минимальных габаритов трансформатора вторичные витки охлаждаются водой. Так как массивные витки изготовлять нерационально из-за больших дополнительных потерь, диски обмотки делаются толщиной не более 20 мм.
Витки могут быть литыми или полученными из катаного материала. В качестве материала для изготовления литых витков служит медь или алюминий (сплавы). Охлаждающие трубки размещаются внутри витка. Наибольшее распространение получили вторичные витки, изготовленные из катаного материала. Диски обмотки выштамповываются из меди марки M1, M2 или МЗ, ввариваются в колодку, служащую для присоединения шин вторичного контура машины. Охлаждающие трубки привариваются по наружному периметру дисков.
В отдельных случаях для улучшения условий охлаждения и снижения габаритов трансформатора вторичный виток выполняется из трубки или штампуется из двух половин, свариваемых по периметру, для обеспечения прохода воды внутри витка.
На рис. 3.9 показаны типовые конструкции дисковых вторичных витков трансформаторов машин контактной сварки.
Контактные колодки, в которые ввариваются диски обмотки, выполняют из того же материала, что и диски.
Сердечник 1 (рис. 3.10) наиболее распространенного трансформатора броневого типа обычно набирают из тонких (0,3 - 0,5 мм) полос электротехнической стали (Э11, Э12, Э41, Э42), изолированных друг от друга бумагой или лаком. На центральном стержне он имеет первичную 2 и вторичную 3 обмотки, которые для предупреждения смещения расклиниваются. Для предотвращения перегрева вторичная обмотка обычно охлаждается водой. Полосы стягиваются специальными стяжными рампами 7 при помощи изолированных шпилек 8. Трансформатор стержневого типа не имеет центрального стержня.
Рис. 3.8. Типы сердечников трансформаторов машин контактной сварки; а - стержневой; б - броневой; в - кольцевой
46
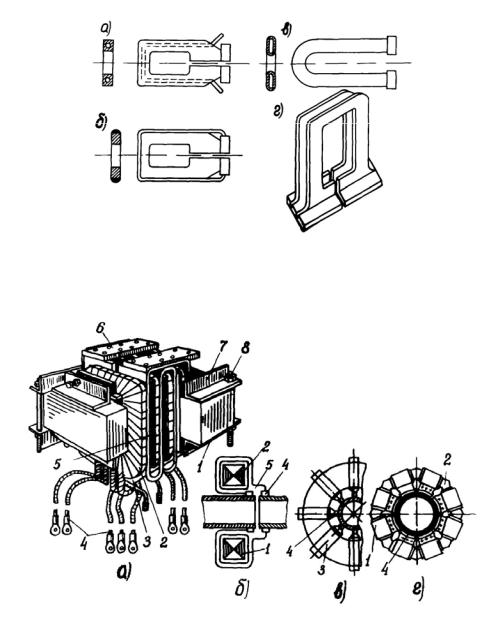
Рис. 3.9. Конструкция дисковых вторичных витков трансформаторов:
а - литой с залитой трубкой охлаждения; б - штампованный виток с приваренной трубкой охлаждения, в - виток из трубки; г - виток, собранный из двух дисков
Рис. 10. Трансформаторы контактных машин: а - броневой (1 - сердечник; 2 - первичная обмотка; 3 - вторичный виток; 4 - выводы; 5 - трубка для охлаждения;
6 - контактные плиты; 7 - стяжные рамки; 8 - шпильки), б, в, г - кольцевые (1 - первичная обмотка; 2 - сердечник; 3 - вторичная обмотка; 4 - токосъемные губки; 5 - концы секций)
Первичная обмотка, подключается к сети. Она может иметь 10 44 витков сечением 1 600 мм2, намотанных в однорядные цилиндрические или многорядные дисковые катушки с выводами 4 для ступенчатого регулирования сварочного тока.
Дисковые катушки изготовляют из медной прямоугольной полосы, покрытой изоляцией, с прокладкой из тонкого прессшпана (0,3 мм).
Дисковые обмотки для уменьшения рассеяния магнитного потока помещают между секциями вторичного витка, сваренного из меди или отлитого из алюминия и охлаждаемого водой по трубкам 5. Окна сердечника и обмо-
47
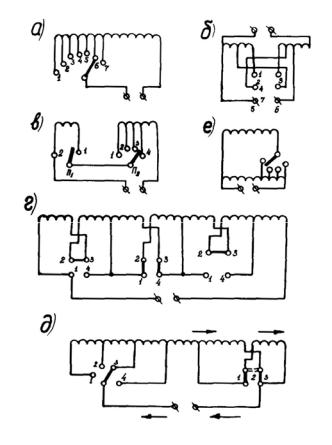
ток для лучшего охлаждения трансформатора и защиты от металлических частиц заливают теплопроводной компаундной кварцбитумной массой. Вторичная обмотка с контактными плитами 6 присоединяется токоподводами к зажимам.
Рис. 3.11. Схемы регулирования вторичных напряжений: а - секционирование обмоток без разрыва; б - секционирование с двумя переключателями; в - секционирование с разрывом; г - секционирование с параллельными соединениями части обмоток;
д- секционирование с параллельными соединениями всей обмотки;
е- регулирование с помощью автотрансформатора
Трансформаторы кольцевого типа (рис. 3.10 б-г) имеют сердечник 2, набранный из полос в виде кольца, на котором размещаются поочередно секции первичной 1 и вторичной 3 обмоток. Концы секции 5 соединяют с губками 4, которые прижимаются к деталям по всему ее периметру. При такой конструкции трансформатора обеспечивается равномерный подвод тока к деталям, уменьшается длина токопровода, а следовательно, контур и потребляемая из сети мощность.
При ступенчатой регулировке сварочного тока широко применяется секционирование с переключением секций первичной обмотки на параллельное или последовательное соединение. Для регулирования тока мощности в машинах с первичным током до 250 А применяют штепсельные, а для боль-
ших токов барабанные переключатели. Пластинчатые переключатели используются в основном в машинах малой мощности.
48
Регулирование сварочного тока контактных машин в большинстве случаев производится переключением числа витков первичной обмотки трансформатора. Переключение витков осуществляется по различным схемам, которые вместе с переключателями ступеней должны обеспечивать достаточно плавно-ступенчатое регулирование вторичного напряжения.
Наиболее часто применяемые схемы регулирования вторичного напряжения трансформаторов машин контактной сварки представлены на рис. 3.11 а-е.
Порядок выполнения работы
1.Ознакомиться с конструкцией основных узлов стыковых машин.
2.Ознакомиться с типом и технологическими возможностями представленной машины.
3.По прилагаемым описанию, схемам и чертежам детально разобрать конструкцию и взаимодействие всех узлов машины.
4.Изучить электрическую силовую схему и схему управления машины.
6.Детально разобраться в технике настройки параметров режима свар-
ки (установленную длину свариваемой заготовки, величину осадки с током и без тока, величину сварочного тока, времени сварки, скорость оплавления и осадки).
6.При включенном сварочном токе опробовать работу машины.
7.Произвести пробную сварку образцов.
Содержание отчета
Отчет содержит: марку машины; ее технологические возможности; пределы регулирования параметров режима сварки; кинематическую схему машины; электрическую схему; пневматическую схему; технику настройки режима; последовательность операций при сварке; цикл сварки.
Контрольные вопросы
1.Какие механизмы зажатия и осадки свариваемых деталей вы знаете?
2.Каким образом осуществляется настройка сварочных губок машины?
3.Какова техника настройки машины на данный режим?
4.Последовательность операций при сварке.
5.Каково устройство и принцип действия электромоторного привода?
6.Какие отличительные особенности устройства трансформатора для контактной сварки?
7.Вопросы, связанные с сопровождением демонстрации на машине:
а) подготовить машину к работе; б) установить определенные параметры режима сварки; в) сделать пробную сварку; г) отключить машину;
д) техника безопасности при стыковой сварке.
49
Лабораторная работа 4
ИЗУЧЕНИЕ КОНСТРУКЦИИ И ОЗНАКОМЛЕНИЕ С ТЕХНОЛОГИЕЙ СВАРКИ НА КОНДЕНСАТОРНЫХ МАШИНАХ
Цель работы - изучить конструкцию конденсаторной машины, овладеть навыками настройки машины, выявить технологические возможности, установить влияние параметров режима на тепловую эффективность разряжаемой энергии, ознакомиться с техникой подбора режима сварки.
Оборудование и материалы
1.Конденсаторная машина ТКМ -7М.
2.Описание машины с поясняющими чертежами и схемами.
3.Электронный осциллограф.
4.Микрометр, набор образцов, штангенциркуль.
5.Необходимый инструмент.
6.Заготовки для сварки.
Теоретические сведения
Конденсаторные машины представляют собой комплекс, состоящий из батарей конденсаторов, выпрямляемого устройства, сварочного трансформатора, выключателя сварочного тока, разных вспомогательных устройств и станка, на котором выполняется определенная механическая работа.
Конденсаторные машины для точечной сварки в основном работают по принципу использования разряда конденсаторов на первичную обмотку сварочного трансформатора (рис. 4.1 б). Однако существуют точечные конденсаторные машины с использованием бестрансформаторного разряда конденсаторов (рис. 4.1 а и рис. 4.2 а-в).
При ударной конденсаторной сварке (рис. 4.1 а) обкладки заряженного конденсатора Ср подключаются непосредственно к свариваемым деталям 4 и 5, из которых одна крепится жестко, а другая может перемещаться в направляющих 2. Если освободить защелку 1, удерживающую подвижную деталь 4, то под действием пружины 3 эта деталь начнет быстро перемещаться по направлению к неподвижной детали 5 и ударится об нее.
Перед соударением деталей возникает мощный дуговой разряд за счет энергии, накопленной в конденсаторе Ср.
Электрический разряд оплавляет торцы обеих деталей, которые после соударения свариваются между собой под действием усилия осадки, развиваемого пружиной 3.
50
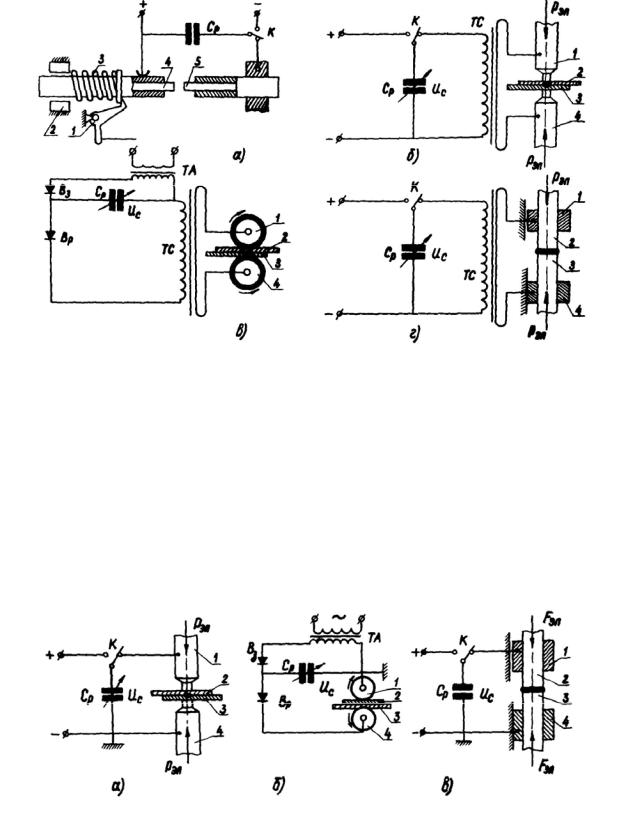
Рис. 4.1. Схемы конденсаторной сварки: а – ударно-конденсаторной оглавлением; б - точечной; в - шовной; г – стыковой
При точечной трансформаторной сварке (рис. 4.1 б) разряд конденсатора Ср преобразуется при помощи сварочного трансформатора ТС. В левом положении ключа К заряжается конденсатор Ср от источника постоянного тока. Если перебросить ключ К в правое положение, то происходит разряд конденсатора на первичную обмотку сварочного трансформатора. При этом во вторичной обмотке индуктируется ток большой силы, который сваривает между собой зажатые электродами 1 и 4 детали 2 и 3.
Рис. 4.2. Схемы бестрансформаторной сварки: а - точечной; б - шовной; в - стыковой (1 и 4 - электроды, 2 и 3 - свариваемые детали)
Действие шовной сварки (рис. 4.1 в) основано на периодическом получении с заданной частотой дозированной зарядки и разряда конденсатора Ср
51
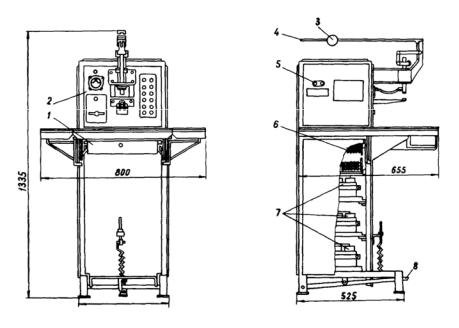
на перемещающихся между роликами 1 и 4 свариваемых деталей 2 и 3. Зарядка до Ua max амплитудного значения напряжения вторичной обмотки выпрямительного трансформатора ТА осуществляется через вентильный элемент В3. Накопленная в процессе зарядки энергия поступает через вентильный элемент Вр в первичную обмотку сварочного трансформатора ТС. Это обуславливает кратковременный импульс тока, при котором на деталях 2 и 3 образуется сплошной линейный шов, состоящий из ряда перекрывающих друг друга сварных точек.
При стыковой трансформаторной сварке сопротивлением (рис. 4.1 г) свариваемые детали 2 и 3 закрепляются в губках 1-4 стыковой машины. После этого обе детали сводятся до соприкосновения и сжимаются усилием Рэл. Затем переключением ключа К в правое положение осуществляется разряд конденсатора Ср на первичную обмотку сварочного трансформатора ТС. Происходит сварка деталей 2 и 3 в месте стыка.
На рис. 4.2 показаны схемы бестрансформаторной сварки.
На рис. 4.3 представлен общий вид серийной конденсаторной машины
ТКМ-7М, а на рис. 4.4 ее электрическая схема. На рис. 4.5 изображена кинематическая схема машины.
Электрическая схема питается от напряжения 220 В. Для регулировки напряжения зарядки конденсаторов предусмотрен автотрансформатор АТ (латр). При подаче напряжения на выходные зажимы схемы получает питание первичная обмотка стабилизирующего выпрямительного трансформатора СTB. Сразу же после этого начинается зарядка конденсаторов Ср от селенового выпрямителя ВС.
Рис. 4.3. Общий вид машины ТКМ-7М: 1 - ящик для инструмента и принадлежностей; 2 - блок управления; 3 - передвижной груз для изменения усилия на электродах; 4 - рычаг грузового механизма; 5 - штепсельный разъем; 6 - выпрямительный блок
со стабилизатором; 7 - блоки конденсаторов; 8 - педаль
52
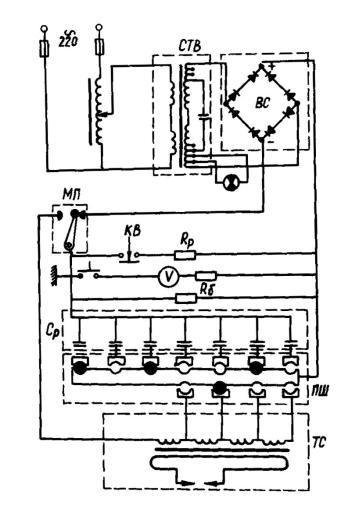
Рис. 4.4. Электрическая схема машины ТКМ-7М: ТС - сварочный трансформатор; ПШ - штекерный переключатель емкости; СТВ - стабилизирующий трансформатор; МП - механический переключатель; KB - концевой выключатель; С - блок конденсаторов
При переключении механического переключателя МП из правого положения в левое происходит замыкание цепи зарядки конденсаторов и их немедленный разряд на первичную обмотку сварочного трансформатора ТС. Индуктирование импульса тока во вторичном витке ТC обуславливает сварку деталей.
После опускания педали машины переключается контактор МП из левого в правое положение, и конденсаторы снова заряжаются для сварки следующей точки. Балластное сопротивление Rб подключено наглухо к обоим зажимам находящихся в работе конденсаторов, и полностью гасит (в течение 25 30 сек) их остаточный заряд после отключения машины от питающей сети. В схеме имеется разрядное сопротивление Rp, включенное через нормально разомкнутые контакты выключателя КВ. Замыкание контактов обеспечивает полный разряд находящихся в работе конденсаторов на разрядное сопротивление Rp.
53

Количество энергии, аккумулируемой батареей конденсаторов, зависит от емкости конденсаторов и напряжения на них:
W Cp U 2a max ,ват.с.б,
2
где Ср - емкость конденсаторов, мкФ; Ua - напряжение на конденсаторах, В. Изменяя емкость батареи конденсаторов, а также коэффициент транс-
формации сварочного трансформатора, можно регулировать количество расходуемой энергии на сварку. При этом расходуется довольно точное количество тепла в течение определенного времени, что благоприятно сказывается на стабильности сварки.
Кратковременность импульса тока большой силы и точная его дозировка по величине и производительности обусловили применение конденсаторных машин для сварки цветных металлов и их сплавов.
Преимущества конденсаторной сварки - малая мощность, потребляемая из сети, высокий cos , сравнительно малые потери энергии, накопленной конденсаторами, и высокая точность настройки режимов сварки. К недостаткам можно отнести повышенное напряжение в первичной цепи сварочного трансформатора, высокую стоимость конденсаторов и невозможность получения мягкого режима сварки.
Подбор и установка режимов сварки
Основными параметрами, определяющими режим точечной конденсаторной сварки, являются: величина включения емкости, коэффициент трансформации, напряжения зарядки конденсаторов, усилие на электродах.
На рис. 4.6 представлены зависимости формы кривой сварочного тока конденсаторных машин от регулируемых параметров.
С повышением емкости конденсаторов максимальное значение iCВ растет незначительно, но заметно возрастает длительность разряда, то есть время сварки tСВ (рис. 4.6 а).
При увеличении напряжения существенно увеличивается ток iСВ и незначительно время tСВ (рис. 4.6 б). С возрастанием коэффициента трансформации, что соответствует уменьшению вторичного напряжения сварочного трансформатора, заметно уменьшается ток iсв и увеличивается время сварки
tсв (рис. 4.6 в).
При увеличении индуктивности в сварочном контуре уменьшается ток iСВ, возрастает время tCB (рис. 4.6 г), С повышением суммарного сопротивления сварочного контура уменьшается ток iCB и увеличивается время tСВ.
Необходимое для сварки количество тепла возрастает с увеличением диаметра сварных точек и толщины свариваемых металлов, а также их удельного веса и теплоемкости. Высокое усилие на электродах обуславливает
54
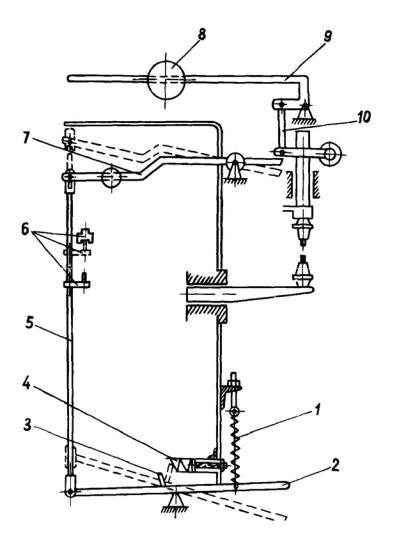
уменьшение контактных сопротивлений, вызывает необходимость увеличения тока и времени сварки, что практически может быть достигнуто за счет включения дополнительной емкости или поднятия напряжения зарядки конденсаторов.
Рис. 4.5. Кинематическая схема машины ТКМ - 7М: 1 - пружина; 2 - педаль; 3 - упорный рычаг; 4 - пружинный упор; 5 - рычаг с приводом; 6 - механический переключатель; 7 - рычаг с противовесом; 8 - передвижной груз;
9 - рычаг грузового механизма; 10 - рычаг механизма сжатия электрода
С увеличением собственного электрического сопротивления свариваемых деталей уменьшается сварочный ток.
Подбор режима сварки следует начинать с включения заведомо недостаточной емкости, установкой наибольшего усилия сжатия и большего коэффициента трансформации, то есть режима, вызывающего непровар. Затем, сварив опытную точку и разрушив ее, постепенно уменьшают усилия сжатия, увеличивают емкость конденсаторов и уменьшают коэффициент трансформации.
55
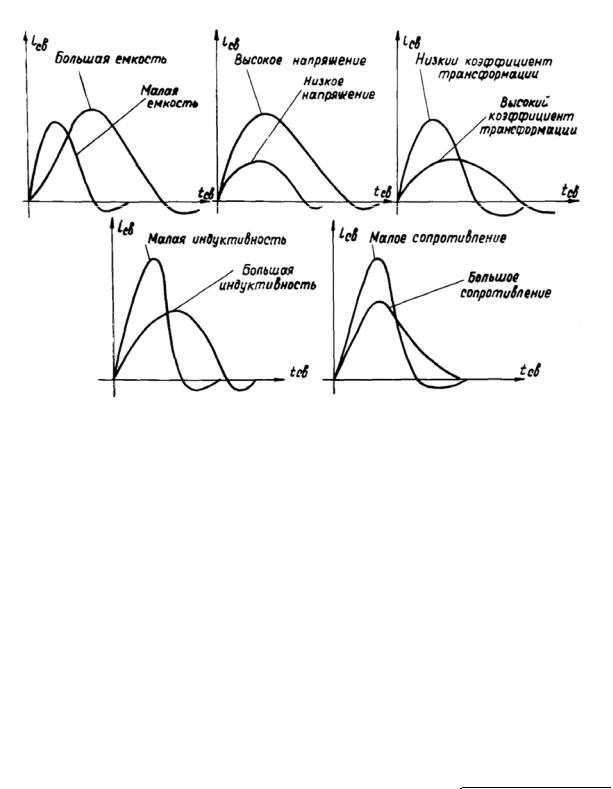
Рис. 4.6. Зависимость формы кривой сварочного тока конденсаторных машин от регулируемых параметров: емкости, напряжения зарядки, коэффициента трансформации, индуктивности, сопротивления
Следует помнить, что детали, предназначенные для сварки, должны быть очищены от грязи, краски, масла, окислов и т. п. Точки, сваренные на правильно выбранном режиме и по зачищенной поверхности листов, считаются хорошего качества, если выполнены следующие требования:
1)полностью отсутствуют внешние дефекты (подплавление, большие вмятины, наружные выплески трещины и т. д.);
2)диаметр литого ядра равен 3 5 толщинам наиболее тонкого из свариваемых листов.
В табл. 4.1 приведены ориентировочные режимы точечной сварки латуни Л62 на машине ТКМ-7.
|
|
|
|
Таблица 4.1 |
|
Толщина |
Емкость конден- |
Коэффициент |
Усилия сжатия; Н |
Разрушающая на- |
|
пакета лис- |
саторов, мкФ. |
трансформации, |
|
грузка на точку, Н |
|
тов, мм |
|
КТn |
|
30 |
|
0,05+0,05 |
70 |
100 |
50 |
|
|
|
|
|
|
|
|
0,1+0,1 |
100 |
100 |
60 |
110 |
|
0,2+0,2 |
180 |
100 |
80 |
300 |
|
0,3+0,3 |
250 |
100 |
100 |
420 |
|
|
|
|
|
|
|
0,5+0,5 |
460 |
125 |
120 |
550 |
|
0,6+0,6 |
680 |
125 |
160 |
- |
|
|
|
56 |
|
|
|
Порядок выполнения работы
1.По представленным описанию, схемам и чертежам ознакомиться с устройством, работой и технологическими возможностями машины.
2.Подробно изучить электрическую схему машины.
3.При включенном сварочном токе опробовать работу и взаимодействие переключателя и механизма нажатия.
ПОМНИТЕ, ЧТО БАТАРЕИ КОНДЕНСАТОРОВ ИМЕЮТ ВЫСОКОЕ НАПРЯЖЕНИЕ! Соприкосновение с ними может вызвать электрический разряд, опасный для жизни человека. Поэтому ознакомление с конструкцией машины следует начинать только после того, когда будете убеждены в полной разрядке конденсаторов при отключенной от сети машине.
4.Выявить возможные пределы регулирования основных параметров режима сварки. Произвести пробную сварку образца.
5.Подключить осциллограф к сварочной цепи для визуального наблюдения на его светящемся экране кривой сварочного тока. С экрана осциллографа зарисовать диаграмму сварочного тока при коротком замыкании элек-
тродов: а при минимальном и максимальном коэффициенте трансформации; б при половинном и полном включении конденсаторов; в при двух значениях напряжения зарядки конденсаторов.
6. Подготовить образцы для сварки: а) пластинки из цветных металлов;
б) проволочки диаметром 0,5-2,0 мм из цветных металлов или малоуглеродистой стали.
7.Опытным путем подобрать режим сварки для пластинок, для стержней (сварка под прямым углом) и для сварки проволочки к пластинке. Оптимальные режимы сварки записать в таблицу.
8.При сварке на пластинах исследовать влияние параметров режима на качество сварного соединения, изменяя при этом в одну и другую сторону один из параметров режима.
9.Оценить качество сварных точек по внешнему виду, разрушить их и выявить влияние каждого параметра режима сварки на прочность точки.
Содержание отчета
В отчете отразить тип и технологические возможности машины. Привести электрическую схему машины с ее кратким пояснением. Изобразить кинематическую схему механизации сжатия с отметкой его звеньев. Вычертить графики осциллографирования сварочного тока с необходимым пояснением. Занести в таблицу оптимальные режимы сварки и результаты исследования при сварке пластинок. Определить количество энергии, израсходованной при сварке пластинок, проволочек с пластинкой на оптимальном режиме.
57
Контрольные вопросы
1.Преимущества и недостатки конденсаторной сварки деталей.
2.Как влияют отдельные параметры режима сварки на энергию импульса сварочного тока?
3.Техника сварки на конденсаторной машине.
4.Подобрать режим сварки.
5.Основные правила безопасности при работе на конденсаторных ма-
шинах.
6.Как влияет качество подготовки поверхности образцов на устойчивость процесса сварки и величину проплавления образцов?
7.Объясните работу схемы конденсаторной сварки, изображенной на рис. 4-1 и 4-2 (тип схемы указывается преподавателем).
58
Лабораторная работа 5
АВТОМАТИЗАЦИЯ ИЗМЕРЕНИЯ ПАРАМЕТРОВ ПРИ КОНТАКТНОЙ СВАРКЕ
Цель работы – Получить практический навык работы с автоматическим измерительным комплексом М-05. Научится проводить измерения основных параметров режима контактной точечной сварки.
Оборудование и материалы
-Измерительный комплекс М-05.
-Установка контактной точечной сварки МТПУ-300.
-Образцы для сварки.
-Трансформатор тока УТТ-5.
-Шунт токоизмерительный.
-Соединительные провода.
-Тензометрические датчики
-Тензометрическая станция П-3ВМ.
-Приборы и устройства для разрушения образцов и исследования размеров литого ядра.
Теоретические сведения
5.1. Устройство и принцип действия измерительно-регистрирующего комплекса
Программно – аппаратный измерительный комплекс состоит из персонального компьютера (в дальнейшем – ПК) с установленной на нём измерительной программой и сопряжённого с ним измерительного блока (ИБ), к которому подключены датчики Д. Его обобщённая структурная схема приведена на рис. 5.1.
Датчики Д производят преобразование физических величин в низковольтные аналоговые сигналы. Эти сигналы подаются на входы ИБ, который преобразует их в цифровой код и передаёт результат в ПК по стандартному коммуникационному интерфейсу. ПК осуществляет всю последующую обработку измерительной информации, отображение результатов измерения и их хранение.
Измерительный блок состоит из двух функциональных модулей: модуля аналого-цифрового преобразования (АЦП) и микропроцессорного модуля управления. Первый из них непосредственно производит усиление, предварительную обработку и оцифровку входных сигналов, а второй осуществляет приём команд от ПК и, в соответствии с ними,
59
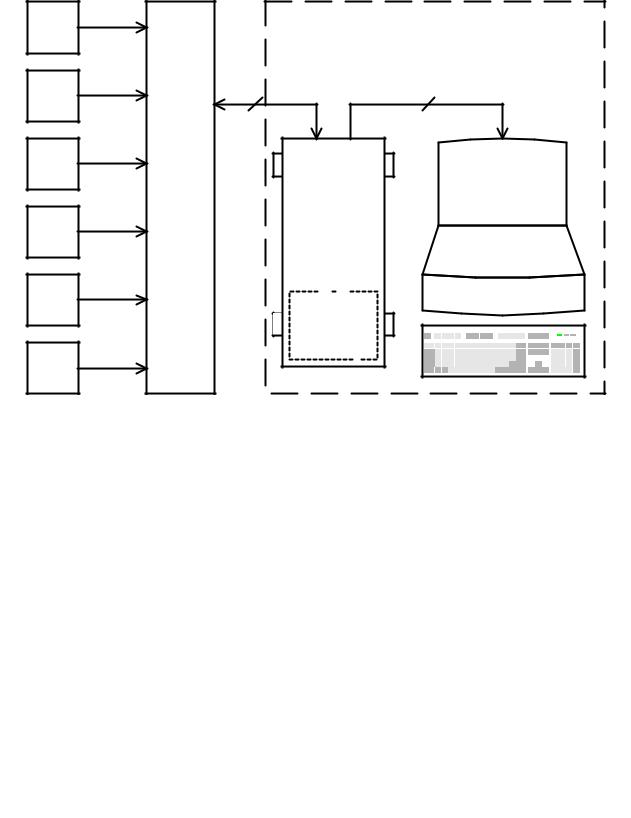
конфигурирование модуля АЦП, пуск и управление процессом преобразования, а так же считывание результатов и передачу их в ПК.
Д1
Д2
Д3
Д4
Д5
Д6
|
RS232C (Com) |
|
|
преобразованияиусиления |
Измерительный( блок) |
Персональный компьютер |
|
обработкиБокл информации |
Блок |
||
|
|
|
|
|
|
|
отображения |
|
|
|
информации |
Блок |
|
Блок |
|
|
хранения |
|
|
|
|
данных |
|
Рис. 5.1. Структурная схема измерительного комплекса
Модуль управления состоит из микропроцессора МП, узла интерфейса УИ, запоминающих устройств ПЗУ и ОЗУ, логики управления УЛ. Основным элементом модуля является МП, который собственно и реализует основные функции управления ИБ в соответствии с заданной программой. УИ служит для согласования электрических характеристик последовательного интерфейса МП со стандартом RS232C (по этому же стандарту работают коммуникационные порты ПК – COM) и обеспечивает гальваническую развязку внутренних электрических цепей блока от внешних. ПЗУ и ОЗУ предназначены для хранения соответственно программы начальной загрузки, рабочей программы и результатов преобразований. УЛ аппаратно поддерживает функции модуля, программная реализация которых невозможна.
Модуль АЦП состоит из нормирующих усилителей НУ, устройств выборки – хранения УВХ, мультиплексора МС и собственно аналого – цифрового преобразователя, управление которыми осуществляется МП по локальной шине ЛШ. Сигналы от внешних датчиков поступают на входы НУ с программируемыми коэффициент передачи. Функции НУ – ослабление
60
синфазных помех, наводимых на внешние соединительные провода, защита от перенапряжений и формирование на входах следующих по схеме устройств номинальных (то есть максимальных, которые не приводят к перегрузке) уровней сигналов. УВХ, которые включены по схеме после НУ, в режиме ‘выборка’ работают в качестве обычных повторителей входного сигнала, а в режиме ‘хранение’ сохраняют на своих выходах уровень, имевший место на момент поступления одноименной команды, в течение времени, необходимого для работы АЦП. Таким образом, происходит предварительная дискретизация сигналов по времени, что обеспечивает синхронность преобразования различных каналов, и исключает грубые ошибки АЦП типа «пропуск кода». МС во время преобразования последовательно подключает к входу АЦП сигналы от различных каналов. АЦП по командам МП производит преобразование входных аналоговых сигналов в цифровой код и выдачу результатов на шину данных для сохранения и дальнейшей передачи в ПК.
В отличие от ИБ и измерительной программы, ПК является универсальным средством; его структуре посвящен достаточно широкий выбор источников информации.
5.2. Аппаратные средства компьютера
Рекомендуемая конфигурация компьютера: процессор Pentium 166 MMX и выше; ОЗУ 32 Мб и более. Требуется 3 Мб свободного дискового пространства для программы и свободное место под файлы полученных данных, наличие одного свободного Com-порта. Операционная система – Windows 95, 98. Для работы необходима мышь.
5.3. Техническая характеристика
Основные технические данные измерительного блока сведены в таблицу 5.1.
|
Основные технические данные |
Таблица 5.1 |
||
|
|
|
|
|
|
|
|
|
|
№ |
Наименование |
Значение |
|
|
п/п |
|
|||
|
|
|
|
|
1 |
Число каналов |
8 |
|
|
2 |
Тип входа |
дифф. пара |
||
3 |
Диапазон значений напряжений входных сигналов, Вольт: |
|
|
|
3.1 |
минимальное значение для каналов 1-3 |
-0.1..+0.1 |
|
|
3.2 |
минимальное значение для каналов 4-8 |
-0.05..+0.05 |
||
3.3 |
максимальное значение для каналов 1-3 |
-100..+100 |
|
|
3.4 |
максимальное значение для каналов 4-8 |
-0.1..+0.1 |
|
|
4 |
Устанавливаемые пределы входного напряжения, Вольт: |
|
|
|
|
|
0.1, |
0.25, |
0.5, |
4.1 |
для каналов 1-3 |
1.0, 2.5, 5 ,10, |
||
|
|
25, 50, 100 |
|
61
|
Окончание табл. 5.1 |
|||||
|
|
|
|
|
||
4.2 |
для каналов 4-8 |
0.05, 0.1 |
|
|
||
5 |
Полоса частот входного сигнала, не более, кГц |
3.5 |
|
|
|
|
6 |
Подавление синфазного сигнала на частоте 50 Гц, дБ, не менее |
60 |
|
|
|
|
7 |
Прохождение сигнала на частоте 50 Гц из канала в канал, дБ, не |
60 |
|
|
|
|
|
более |
|
|
|
|
|
8 |
Максимально допустимое амплитудное значение входного синфазного напряже- |
|||||
ния, не более, Вольт: |
|
|
|
|
||
|
|
|
|
|
||
8.1 |
для каналов 1-3 при установленных пределах входного напря- |
100 |
|
|
|
|
жения 25, 50, 100 Вольт |
|
|
|
|||
8.2 |
для каналов 1-3 при установленных пределах 0.1, 0.25, 0.5, 1.0, |
12 |
|
|
|
|
|
2.5 ,5.0 ,10 Вольт |
|
|
|
|
|
8.3 |
для каналов 4-8 |
12 |
|
|
|
|
9 |
Максимально допустимое значение модуля постоянного напряжения |
, приложен- |
||||
ного к любому из входов не более, Вольт: |
|
|
|
|
||
|
|
|
|
|
||
9.1 |
для каналов 1-3 |
200 |
|
|
|
|
9.2 |
для каналов 4-8 |
16 |
|
|
|
|
10 |
Максимально допустимое значение модуля суммарного по прямому |
и инверсному |
||||
входам разность потенциалов между входами разных каналов, не более, Вольт |
|
|||||
|
|
|||||
10.1 |
для каналов 1,2,3 при установленных пределах входного напря- |
24 |
|
|
|
|
жения 25, 50, 100 Вольт |
|
|
|
|||
10.2 |
для каналов 1,2,3 при установленных пределах 0.1, 0.25, 0.5, 1.0, |
12 |
|
|
|
|
|
2.5 ,5.0 ,10 Вольт |
|
|
|
|
|
10.3 |
для каналов 4 - 8 |
12 |
|
|
|
|
11 |
Минимальное входное сопротивление аналоговых входов, не |
10e6 |
|
|
|
|
|
менее, Ом |
|
|
|
|
|
12 |
Напряжение смещения, мВ, не более: |
|
|
|
|
|
12.1 |
для каналов 1-3 |
50 |
|
|
|
|
12.2 |
для каналов 4-8 при установленном пределе 0.05 Вольт |
0.47 |
|
|
|
|
12.3 |
для каналов 4-8 при установленном пределе 0.1 Вольт |
0.67 |
|
|
|
|
13 |
Разрядность цифрового представления, бит (включая знак) |
8 |
|
|
|
|
14 |
Напряжение собственных шумов, дБ, не более |
-40 |
|
|
|
|
|
|
20, |
50, |
|
100, |
|
15 |
Частота опроса каждого канала, Гц |
200, |
|
|
500, |
|
1000, |
5000, |
|||||
|
|
|||||
|
|
10000 |
|
|
||
16 |
Точность установки частоты опроса каждого канала, не хуже |
10e-2 |
|
|
||
17 |
Количество точек регистрации для каждого канала |
8 |
(min) |
– |
||
61440 (max) |
||||||
|
|
|||||
18 |
Класс точности прибора в диапазоне 50..100% от максимального |
3 |
|
|
|
|
|
значения |
|
|
|
|
|
19 |
Частота питающей сети, Гц |
50±2 |
|
|
||
20 |
Масса прибора, не более, кг |
5 |
|
|
|
|
21 |
Условия эксплуатации прибора: |
|
|
|
|
|
21.1 |
Температура окружающего воздуха, °C |
20±15 |
|
|
||
21.2 |
Относительная влажность воздуха, % |
65±15 |
|
|
||
21.3 |
Атмосферное давление, кПа (мм рт. ст.) |
100±4 |
|
|
||
(750±30) |
|
|
||||
|
|
|
|
62
Прибор обеспечивает проведение регистрации по произвольным каналам из имеющихся. Управление прибором осуществляется с помощью стандартных средств PC (клавиатура, мышь). Результаты в процессе работы индицируются на экране монитора PC, а также могут сохраняться на его стандартных носителях (FDD, HDD). Формат выходных данных при сохранении данных в файл – ASCI файл (*.txt). Прибор имеет пылезащитное исполнение.
5.4. Краткое описание программного обеспечения
Для устройств, создаваемых в соответствии с принятой концепций (PCbased CDA&AS, см. введение), программное обеспечение с одной стороны, во многом ответственно за способность выполнять требуемые измерительные функции, и с другой – полностью определяет возможности по вторичной обработке результатов, их визуализации и документированию.
Программное обеспечение (ПО) комплекса M-05 можно разделить на три составляющих: программу начальной загрузки (ПНЗ) ИБ, измерительную программу ИБ (ИП ИБ) и измерительную программу ПК (ИП ПК). Рис 2.2 иллюстрирует общую структуру ПО и связи между составляющими. В процессе измерений ПК осуществляет связь с ИБ по последовательному интерфейсу. ИП, выполняемая ПК, взаимодействует с программами ИБ посредством определенного набора команд. При помощи этого набора производится загрузка ИП ИБ, конфигурирование аппаратных элементов ИБ, пуск АЦ преобразования с заданными параметрами и ввод в ПК результатов.
Здесь следует подробнее указать преимущества, получаемые от использования метода динамической загрузки ИП ИБ. Первое – возможность отладки программ без использования дополнительных отладочных средств в процессе разработки. Второе – возможность оперативно исправлять ошибки, выявленные в процессе эксплуатации. Третье – возможность вносить дополнительные функции при расширении области применения ИК. И, наконец, четвёртое. При проведении разных экспериментов даже в пределах одного направления от ИК могут потребоваться характеристики, предельные значения которых одновременно не могут быть обеспечены. Так, например, проведение длительного измерения с вводом большого объёма (превышающего ёмкость встроенного ОЗУ данных ИБ) результатов АЦ преобразования или контроль параметров параллельно с измерением («на лету») требует передачи информации непосредственно в ПК. При этом максимальная частота, с которой управляющий МП ИБ может принимать данные от АЦП без пропусков, заметно ниже из-за необходимости одновременно осуществлять обмен с ПК. С другой стороны, при исследовании коротких процессов, когда объёма ОЗУ достаточно, имеется возможность увеличить частоту дискретизации АЦП. Реализация двух разных алгоритмов с противоречивыми требованиями в рамках одной ИП проблематична, поэтому рациональным решением является загрузка
63
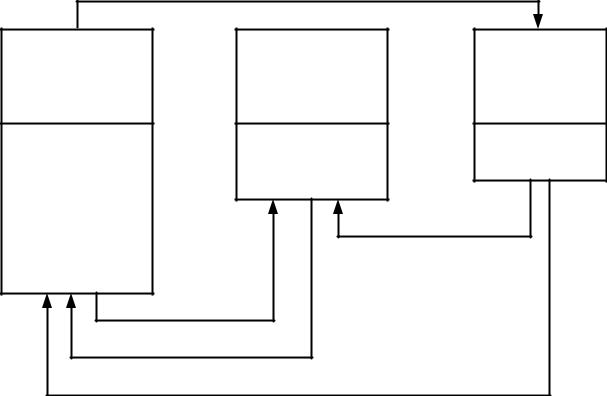
оптимальной ИП для конкретной задачи. Тем более, технически реализовать аппаратную поддержку такой возможности довольно просто, а удельный вес связанных с этим расходов невелик.
ПК производит обработку введённых первичных данных (которые, по сути, являются результатом АЦ преобразования) в соответствии с заданными алгоритмами и указанными функциональными соответствиями. Результатом этих действий становится т. н. вторичная измерительная информация, представляемая в виде принятых для измеряемых параметров физических величин и в форме, удобной для восприятия человеком. На основе именно этой информации делаются выводы о результатах эксперимента. При необходимости полученные результаты могут сохраняться средствами ПК и обрабатываться универсальными программными средствами.
|
команды на верификацию и загрузку |
|
|
Измерительная |
Измерительная |
Программа |
|
начальной |
|||
программа ПК |
программа ИБ |
||
загрузки ИБ |
|||
|
|
||
- управление ИБ; |
- управление ИБ |
- верификация |
|
- получение и об- |
- АЦ преобразо- |
- загрузка ИП |
|
работка данных; |
вание |
|
|
- визуализация и |
перезагрузка |
||
хранение |
|||
|
|
||
полученных |
|
|
|
результатов |
|
|
|
команды |
|
||
результаты |
|
||
|
результаты верификации |
|
|
|
Рис. 5.2. Общая структура ПО |
|
Общий алгоритм выполнения команд таков. МП ИБ в режиме прерывания принимает из регистра данных последовательного порта поток байт и записывает его в буфер размером 32 байта. Если буфер приёма заполняется более, чем на 14 байт, МП сбрасывает интерфейсный сигнал готовности к приёму, в результате чего дальнейшая передача от ПК должна прекратиться до установки этого сигнала. В фоновом процессе производится проверка буфера и обработка принятых байт. Если при этом буфер
64
опустошается более, чем до 15 байт, сигнал готовности устанавливается вновь. При обработке производится возврат, байт за байтом, принятой последовательности.
Программа начальной загрузки начинает выполняться МП ИБ непосредственно после включения питания, её назначение – загрузка ИП ИБ. В этом режиме возможности прибора ограничены приёмом и выполнением набора из двух команд при скорости интерфейса 9600 бод.
После запуска ИП ПК в первую очередь пытается загрузить файл установок пользователя, в котором заданы значения некоторых переменных окружения, используемых программой. Редактированием этого файла пользователь может задать номер порта, к которому подключен ИБ, и указать скорость связи с ним (она должна соответствовать той, для которой написан загружаемый код ИП ИБ), и, в определённых рамках, настроить интерфейс пользователя.
Вслед за этим ИП ПК производит проверку наличия подсоединённого к указанному COM-порту ИБ. Если ответ не приходит, программа выводит на монитор соответствующее сообщение и завершает работу (рис. 3.6). Если идентифицируется прибор под управлением ПНЗ, производится загрузка в него ИП ИБ, которая должна содержаться в файле с определённым именем и расширением; после этого, а также, если идентифицируется прибор c уже загруженной ИП (такое может произойти при повторном запуске ИП ПК), в ИБ передаются команды текущей конфигурации и ИП ПК переходит в диалоговый режим.
В диалоговом режиме ИП ПК ожидает команды пользователя и выполняет их по мере поступления. Основные функции, реализуемые ИП ПК
вэтом режиме, следующие:
Настройка интерфейса пользователя – расположение окон, вид графиков, установка активных каналов.
Конфигурация ИБ – установка диапазонов амплитуд, количества точек на канал и частоты дискретизации по времени.
Измерение – передача на ИБ команды пуска преобразования и, по его завершении, ввод результатов в ПК, вычисление соответствующих физических величин и представление их в графическом виде. При этом в случае косвенного измерения физических величин для расчета истинных значений могут использоваться данные файла установок пользователя. Масштабные коэффициенты применяются для датчиков с линейными характеристиками (токовых трансформаторов, шунтов, делителей напряжения), и результат получается перемножением на них данных АЦ преобразования с учётом диапазона. Таблицы соответствий представляют собой двумерные массивы, в которых с определённым шагом приведены зависимости величины измеряемого параметра от показаний датчика, и применяются для датчиков с нелинейными
65
характеристиками (например, термопар). Результат получается выбором из таблицы значения, соответствующего результату АЦ преобразования с учётом диапазона. Для нахождения промежуточных значений (когда результат АЦ преобразования попадает между точками, указанными в таблице) используется линейная интерполяция.
Просмотр результатов и вторичная обработка – отображение графиков и отдельных их фрагментов в увеличенном масштабе, вычисление статистических характеристик сигналов.
Документирование результатов – вывод на печать и запись в файл.
5.5. Подготовка комплекса к работе
5.5.1. Установка программного обеспечения
В состав ИП входят следующие объекты:
CVI\ – папка, содержащая файлы шрифтов и другие, необходимых для работы программы;
cvirt.dll – файл библиотек, необходимых для работы программы;
cvirte.dll – файл библиотек, необходимых для работы программы;
k.tcc – файл с таблицей соответствия температур напряжениям для термопар;
m5.bin – файл, содержащий измерительную программу ИБ;
m5.exe – измерительная программа ПК;
m5.reg – файл с параметрами инсталляции m5.exe на ПК;
m5.set – файл настроек пользователя (см. приложение 2);
m5.uir – файл настроек m5.exe, создаётся автоматически;
PCOMM.DLL – драйвер COM-порта ПК, используется m5.exe;
reg.bat – пакетный файл с процедурой инсталляции m5.exe на ПК. Все перечисленные объекты необходимо скопировать в один каталог,
например, C:\M05\, и в командной строке Windows (Пуск/Выполнить/) запустить reg.bat.
5.5.2. Настройка программного обеспечения
После установки ИП на ПК можно провести её настройку редактированием файла установок пользователя m5.set. Образец этого файла приведён в приложении 2. Если файл отсутствует либо в нём не указаны какие-либо значения, используются значения по умолчанию. Возможны следующие настройки:
“com” – определяет номер последовательного порта, к которому подключен ИБ.
“baud” – указывает скорость обмена с ИБ по интерфейсу RS232C. Допустимы значения 9600, 19200, 57600, значение по умолчанию –
66
9600 kbps. Максимальная скорость обмена возможна при расположении ИБ и ПК вблизи друг от друга, когда длина интерфейсного кабеля невелика. Работа на высокой скорости более комфортна, так как уменьшаются паузы, связанные с передачей данных. При большой длине кабеля, а так же в условиях сильных помех, такая работа может оказаться невозможной, и скорость потребуется уменьшить. Рекомендуемое и используемое по умолчанию значение – 3.
“binfile” – указывает имя файла с ИП ИБ. Следует отметить, что код программы должен соответствовать указанному BAUD. Значение по умолчанию – M5.BIN.
“wonder” – определяет положение графиков на экране ПК. Возможны значения 1 – cascade (один поверх другого, максимальный размер графиков) или 2 – tile (одновременное отображение), по умолчанию – 1. В процессе работы вариант вывода графиков может меняться, данный параметр определяет лишь их начальное положение.
“titleX” (“TITLE1”.. “TITLE8”) – заголовок графика с номером X,
может быть произвольной строкой символов без пробела, по умолчанию имеет значение “НапряжениеX”.
“axisyX” (“axisy1”.. “axisy8”) – наименование и размерность физической величины, отображаемой по оси ординат графика с номером X. Может быть произвольной строкой символов без пробела, по умолчанию имеет значение “U,V”.
“scaleX” (“scale1”.. “scale8”) – масштабный множитель канала X,
учитывающий линейную составляющую передаточной функции цепи преобразования измеряемой величины в напряжение, которое подаётся на измерительный вход прибора. По умолчанию значение этого параметра принимается за 1, то есть считается, что измеряется напряжение и сигнал снимается непосредственно с источника. В том случае, когда используются дополнительные цепи преобразования, параметр необходимо корректировать. В общем случае он обратно пропорционален коэффициенту передачи такой цепи. Например, если в канале 1 используется делитель 2:1, то необходимо указать
scale1=2.
На рис. 5.3 приведён пример установки для измерения тока с использованием токового трансформатора с коэффициентом 100:1, нагруженного на шунт 1Ом. Коэффициент передачи такой цепи равен:
K=Kтт*Rш
где Kтт – коэффициент передачи токового трансформатора, а Rш – сопротивление шунта
67
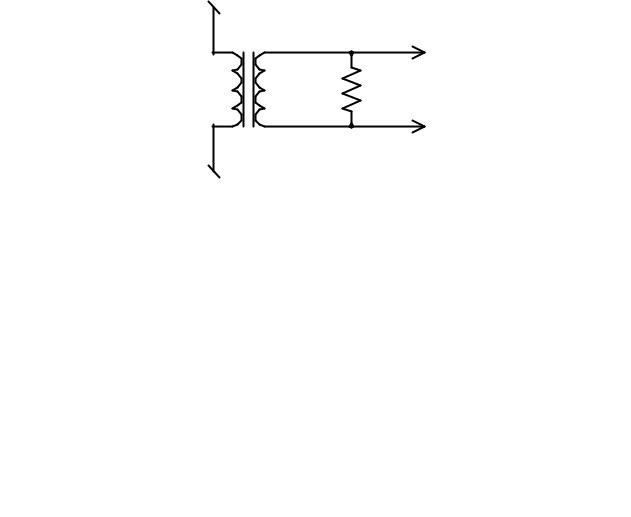
В численном выражении это будет равно:
K=1/100*2.5=0.025,
соответственно scaleX = 40 (при этом не забыть axisyX=I, A).
“tccX” (“tcc1”.. “tcc8”) – параметр канала X, учитывающий нелинейную составляющую передаточной функции цепи преобразования измеряемой величины в напряжение. По умолчанию этот параметр не используется, то есть считается, что передаточная функция линейна. В случае же использования ему присваивается имя файла, содержащего двумерный массив, в котором передаточная функция протабулирована с некоторым шагом. Как указывалось в п. 5.4, результат получается выбором из таблицы соответствующего результату АЦП значения с учётом диапазона, а для нахождения промежуточных значений используется линейная интерполяция.
I св 100А макс.
Rш 100:1 2.5Ом
Uизм
Рис. 5.3 Пример входной цепи для измерения тока
Например, при измерении температуры с использованием хромельалюмелевой термопары по каналу X следует указать tccX=k.tcc
5.5.3. Подключение измерительного блока
ИБ соединяется с ПК через свободный COM-порт посредством нульмодемного кабеля, в котором используются 4 сигнальные линии и 2 линии заземления – сигнальное и защитное. Кабель должен иметь стандартные 9- контактные разъёмы типа DB-9f. Распайка кабеля приведена на рис. 5.4.
Кабели питания ИБ и ПК, имеют провода заземления, которые должны быть соединены с общим контуром заземления. Питать ИБ следует от той же фазы, что и ПК.
68
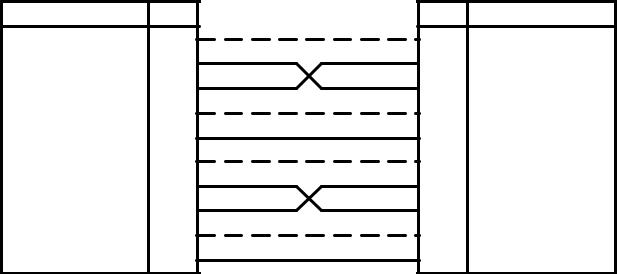
Сигнал |
Конт |
Конт |
Сигнал |
Не подключен |
1 |
1 |
Не подключен |
TxD |
2 |
2 |
TxD |
RxD |
3 |
3 |
RxD |
Не подключен |
4 |
4 |
Не подключен |
Сигнальная земля |
5 |
5 |
Сигнальная земля |
Не подключен |
6 |
6 |
Не подключен |
RTS |
7 |
7 |
RTS |
CTS |
8 |
8 |
CTS |
Не подключен |
9 |
9 |
Не подключен |
Защитная земля |
К |
К |
Защитная земля |
DB9 розетка |
|
|
DB9 розетка |
|
Рис. 5.4. Распайка интерфейсного кабеля |
|
5.5.4. Подключение объектов
Для ввода в ИБ подлежащих обработке сигналов предназначены разъёмы, расположенные на лицевой панели (см. рис. 5.5). Их назначение приведено в приложении 1.
При работе в условиях значительных сетевых наводок и помех необходимо предпринять меры, ослабляющих их влияние на измерительную информацию. Провода, соединяющие объекты, особенно расположенные на удалении от ИБ, необходимо располагать рядом, лучше использовать скрученную пару. В некоторых случаях может потребоваться использование экранированной витой пары, экранирующая оплётка которой должна иметь надёжный электрический контакт с корпусом прибора (для этого можно использовать клеммы XT4). Наилучший же результат в данном случае даст использование двужильного экранированного кабеля в сочетании со специальным экранированным разъёмом (таким, как XP1).
При измерении электрических величин с использованием внешних делителей необходимо обеспечить соответствие величин входных сигналов требованиям п. 10 технических характеристик измерительного комплекса. На рис. 5.6 приведены примеры правильного и неправильного подключения объектов при многоканальных измерениях.
При измерениях с использованием внешних понижающих цепей (шунтов, токовых трансформаторов и делителей) рекомендуется обеспечивать передачу на вход ИБ сигналов в диапазоне 2.5 В, так как в этом диапазоне ИБ имеет минимальные погрешности.
69
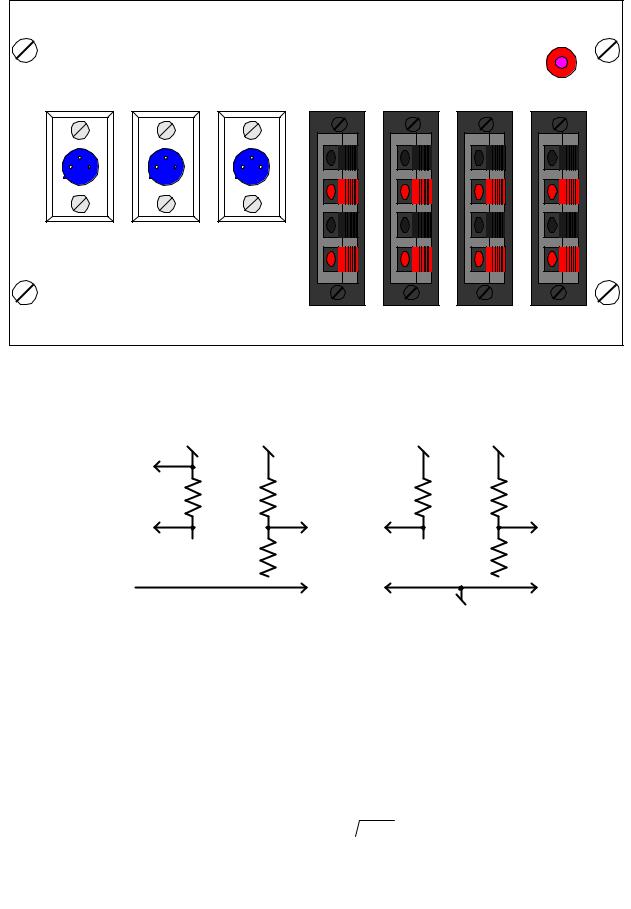
XP1 |
XP2 |
|
XP3 |
XT1 |
XT2 |
XT3 |
XT4 |
|
2 3 |
1 |
2 3 1 |
2 |
3 1 |
|
1 |
|
|
|
|
|
|
|
|
2 |
|
|
|
|
|
|
|
|
3 |
|
|
|
|
|
|
|
|
4 |
|
|
|
|
Рис. 5.5. Размещение разъемов на лицевой панели |
|
|
Фаза1 |
Фаза2 |
|
Фаза1 |
Фаза2 |
|||
Uизм1 |
R |
ш1 |
R |
ш3 |
R |
ш1 |
R |
ш3 |
|
|
|
|
|
Общий Rш2
Rш4
Uизм2 Uизм1
Rш2 Rш4
Uизм2
Общий Неправильно Правильно
Рис. 5.6. Пример правильного и неправильного подключения объектов к измерительному блоку
Так, для схемы, представленной на рис. 5.6, для измерения напряжений в трехфазной электрической сети 220 В коэффициент передачи делителей можно выбрать так:
КД 2,5 UФ
2 К
Здесь K – коэффициент, определяющий запас по амплитуде. Практически его значение удобно подобрать при расчете элементов делителя
70
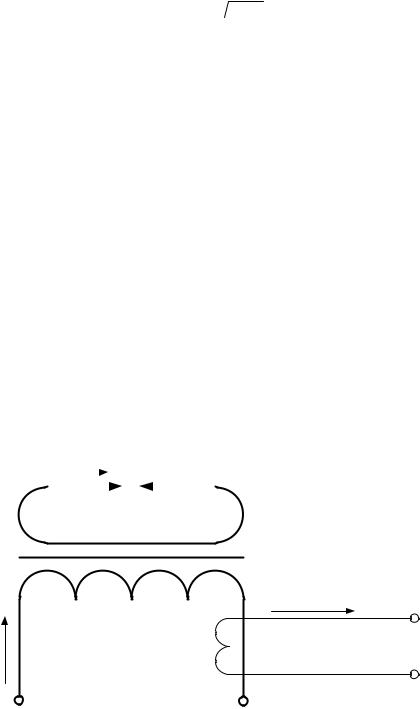
напряжения, чтобы обеспечить рациональные значения элементов. Таким образом,
КД 2,5 220
2 К 0,0080353
К
Учитывая входное сопротивление ИБ можно порекомендовать делители с KД=0.0075.
5.6. Выбор способов измерения
5.6.1. Измерение электрических величин
Главным электрическим параметром при большинстве видов сварки и наплавки является сила сварочного тока. При его измерении применяют трансформаторы тока и наружные шунты.
Мы будем использовать трансформатор тока УТТ-5.
Для контактной сварки, характеризующейся большими значениями сварочного тока, проще всего измерить ток в первичной обмотке сварочного трансформатора и умножить его значение на коэффициент трансформации сварочного трансформатора (оно приводится в техпаспорте контактной машины). Таким образом, трансформатор тока надевается на шину, подводящую ток к первичной обмотке (рис. 5.7).
|
Iсв |
|
|
|
Свариваемые |
|||
|
|
|
|
|
детали |
|||
|
|
|
|
|
|
|
|
|
|
|
|
|
|
|
|
|
|
|
|
|
|
|
|
|
|
|
|
Сварочный |
|
трансформатор |
|
Iрег |
|
Вход |
I1 |
АЦП |
U1 = 380 B
Рис. 5.7. Измерение тока при контактной сварке
Кроме трансформатора тока, при контактной сварке можно использовать токоизмерительный шунт. Он, как и в этом случае, подключается к первичной обмотке сварочного трансформатора. В данном случае измеряется падение напряжения на шунте, значение которого пересчитывается в значение тока умножением на тип шунта. Например,
71
используем шунт 300 А – 75 мВ. Это значит, что при пропускании через шунт тока величиной 300 А падение напряжения на шунте будет составлять 75 мВ. Допустим, что при наших измерениях получено значение 55 мВ. Искомое значение тока составляет ((300*55)/75) = 220 А.
Необходимо отметить, что выбор номера входа АЦП обуславливается величиной ожидаемого сигнала. При высокоуровневом сигнале подключение осуществляется к каналам 1-3 (более 12 В), при низкоуровневом сигнале – к каналам 4-8. Это относится как к измерению тока, так и во всех других случаях.
Измерение напряжения для контактной сварки осуществляется так: с помощью соединительных проводов сигнал снимается напрямую с зоны сварки. Провода цепляются к электродам, например – между электродом и электрододержателем. Второй конец провода подключается к каналам АЦП напрямую, т.к. снимаемые напряжения не превышают значений, указанных в технической характеристике прибора.
5.6.2. Измерение неэлектрических величин
Для контактной сварки большую важность представляет измерение усилия сжатия электродов. Изменение Fсв. в процессе сварки решено фиксировать с помощью тензометрических датчиков сопротивления. Последние наклеивались на подножку нижней консоли сварочной машины. Сигнал от них усиливается тензостанцией ПЭ П38М, после чего подается на вход АЦП (рис.5.8).
Предварительно с помощью динамометра определяется зависимость между сигналом тензостанции и усилием электродов. В рабочем диапазоне (до 10 кН) эта зависимость носит линейный характер.
Стабильность работы схемы и идентичность условий службы тензометров при тарировке и непосредственно при проведении опытов достигается поддержанием постоянного напряжения, питающего аппаратуру, надежностью контактов в местах соединения и, при необходимости, устойчивой компенсации изменения сопротивления тензодатчиков от температуры.
Креплению тензодатчика к детали должно уделяться большое внимание, так как именно через пленку клея происходит передача деформации с детали на тензорезистор. При высоких температурах нарушение технологии может привести к весьма существенным погрешностям, вызываемым ползучесть клея. Однако при комнатных температурах погрешность очень мала (около 1%).
Следует отметить, что для успешного проведения измерений болты, крепящие нижнюю консоль сварочной машины к станине, следует ослабить. В результате этого более заметна деформация, возникающая от действия пневмоцилиндра.
72
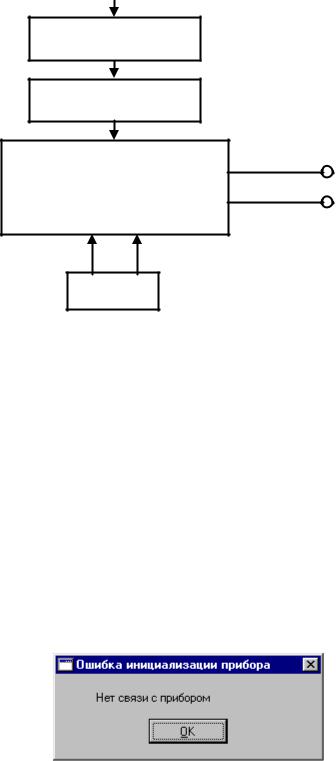
Сеть
Стабилизатор
напряжения
Блок питания
Тензометрический |
Вход |
усилитель |
АЦП |
Датчик
Рис. 5.8. Блок-схема включения аппаратуры при работе с тензодатчиками
5.7. Проведение измерений
Выполнив действия, предписанные пунктом 5.5, можно приступать к проведению измерений. Для примера проведём измерение наводок от сети на два разных предмета.
После запуска ИП ПК она пытается установить связь с ИБ. Если в течение определённого времени не будет получен код идентификации, на экране монитора появится сообщение (рис. 5.9) и программа завершит работу. В этом случае необходимо проверить, подано ли питание на ИБ и подключен ли он к указанному в файле M5.set порту. Кроме этого, причиной сбоя может быть несоответствие параметров baud и binfile в том же файле. Если же связь успешно установлена, в ИБ передаётся ИП ИБ и комплекс готов к работе, о чём свидетельствует окно ИП ПК, подобное показанному на рис. 5.10.
Рис. 5.9. Сообщение об ошибке
Представление графиков при старте ИП определяет, как уже говорилось, параметр ‘winorder’ файла M5.set. Рис. 5.10 иллюстрирует случай, когда на экран одновременно выводятся все графики, т.н. титульный вывод. В этом ре-
73
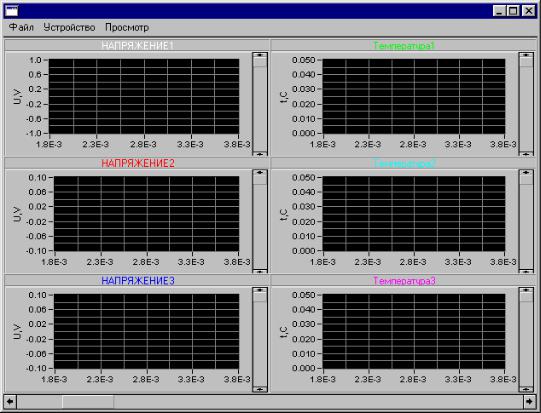
жиме при помощи мыши можно произвольным образом масштабировать графики (рис. 5.11), создавая наиболее удобный для данного эксперимента режим визуализации. Если щёлкнуть по окну ИП левой кнопкой мыши, появится диалоговое окно конфигурации вывода (рис. 5.12), в котором можно выбрать каскадный (кнопка ‘Cascade) вывод графиков. В этом случае графики располагаются один за другим (рис. 5.13), что иногда может быть более удобным. Вернуться вновь к титульному выводу можно кнопкой ‘Title’ в том же окне. Кроме этого, в окне конфигурации вывода можно настроить и другие параметры графиков – запрет / разрешение вывода заголовков графиков, осей X и Y, масштабной сетки и полосы прокрутки, выбрав для себя наиболее удобный режим вывода.
Диалоговое окно конфигурации вывода, помимо указанного выше, позволяет отключать неиспользуемые каналы ввода, что позволяет эффективнее использовать как ресурсы ИБ, так и место на экране. Отключив все каналы, кроме первых двух и проведя автомасштабирование последовательным переключением режимов ‘Title’ и ‘Cascade’, получим окно ИП, представленное на рис. 5.14.
Рис. 5.10. Титульный вывод графиков
74
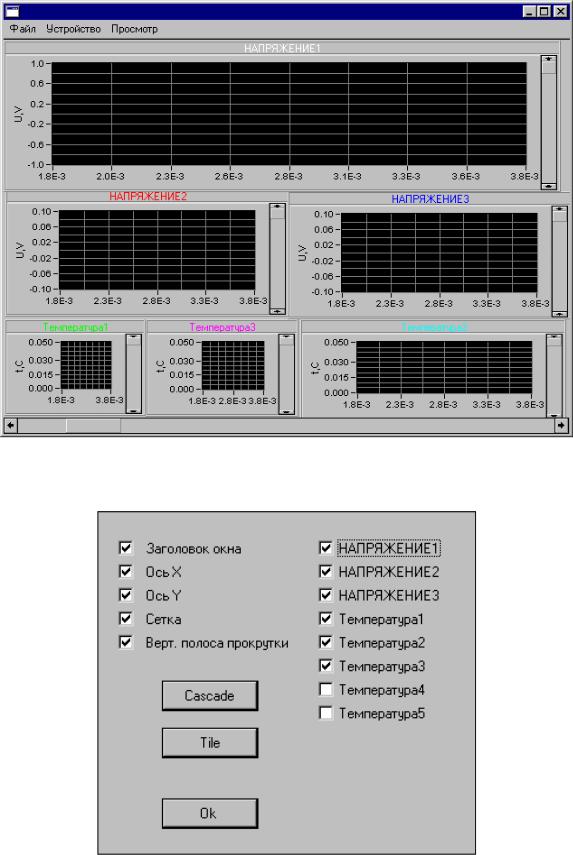
Рис. 5.11. Вариант расположения окон при титульном выводе графиков
Рис. 5.12. Диалоговое окно конфигурации вывода
75
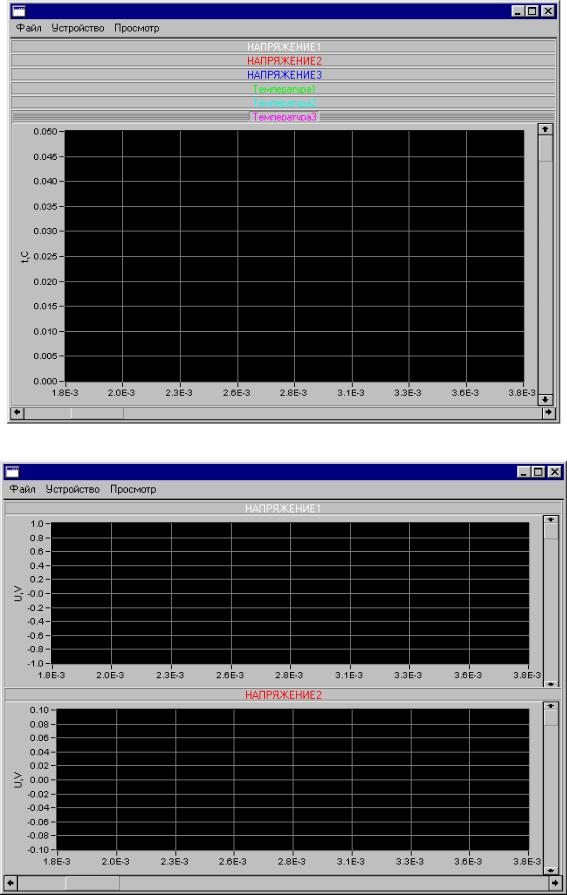
Рис. 5.13. Каскадный вывод графиков
Рис. 5.14. Рабочее окно ИП при работе в двухканальном режиме
76
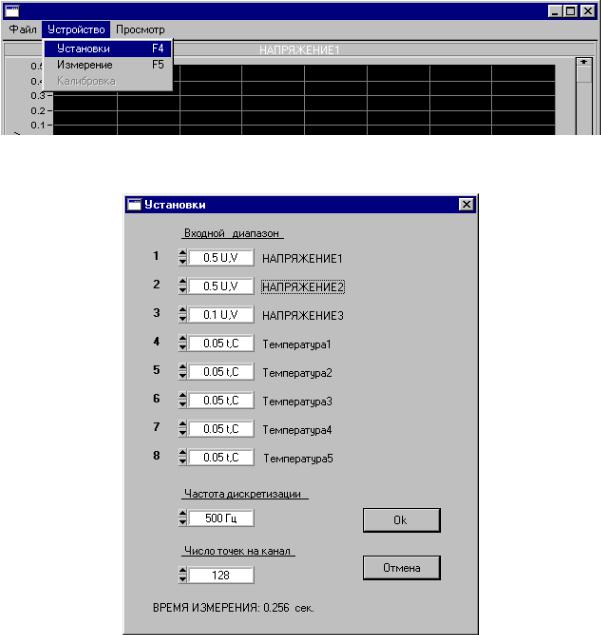
Для проведения эксперимента необходимо привести параметры АЦ преобразователя ИБ в соответствие с параметрами входных сигналов. Вызов окна установки параметров производится клавишей F4 или через меню ‘Устройство/Установки’ (рис. 5.15). Окно (рис. 5.16) содержит следующие элементы настройки: амплитудный диапазон для каждого из каналов, частота
Рис. 5.15. Вызов окна установок параметров преобразования
Рис. 5.16. Окно установок параметров преобразования
дискретизации АЦП (общая для всех каналов) и количество точек преобразования для каждого канала. Кроме этого, в нижней части окна индицируется время, в течении которого будет вестись преобразование (оно равно отношению количества точек и частоты). Установка нужного значения осуществля-
77
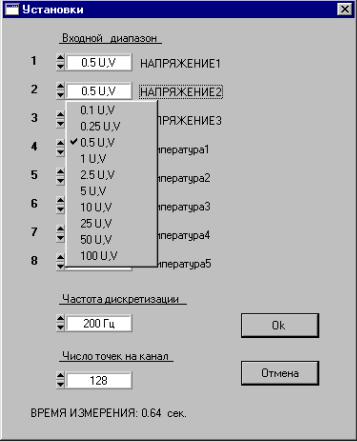
ется нажатием кнопок ‘больше’, ‘меньше’ на соответствующем элементе, либо выбором в меню, предлагаемом по щелчку правой кнопкой мыши по элементу (рис. 5.17). Здесь следует отметить, что максимальное количество точек преобразования – величина непостоянная и зависит от количества выбранных каналов (общее количество точек – 60 K, на канал – пропорционально меньше). Соответственно, количество предлагаемых на выбор вариантов может меняться. Так же, линейка частот дискретизации расширяется при переходе от многоканального режима к одноканальному.
Итак, имеется два сигнала с частотой сети (50Гц) и амплитудой порядка 1 В. Для проведения измерения установим амплитудные диапазоны 1В и минимальную частоту дискретизации, удовлетворяющую теореме Котельникова (значение частоты дискретизации должно быть выше удвоенного значения максимальной частоты сигнала), т.е. 200 Гц. Задав 16 точек преобразования, получим время 0.08 секунд, что соответствует четырём периодам сигнала.
Рис. 5.17. Выбор значений в окне установок параметров
Измерение можно провести нажатием клавиши F5 или через меню ‘Устройство / Преобразование’. Результат представлен на рис. 5.18. Как видно из рисунка, для первого канала выбран слишком низкий диапазон (происходит ограничение сигнала), а для второго – слишком высокий (график –
78
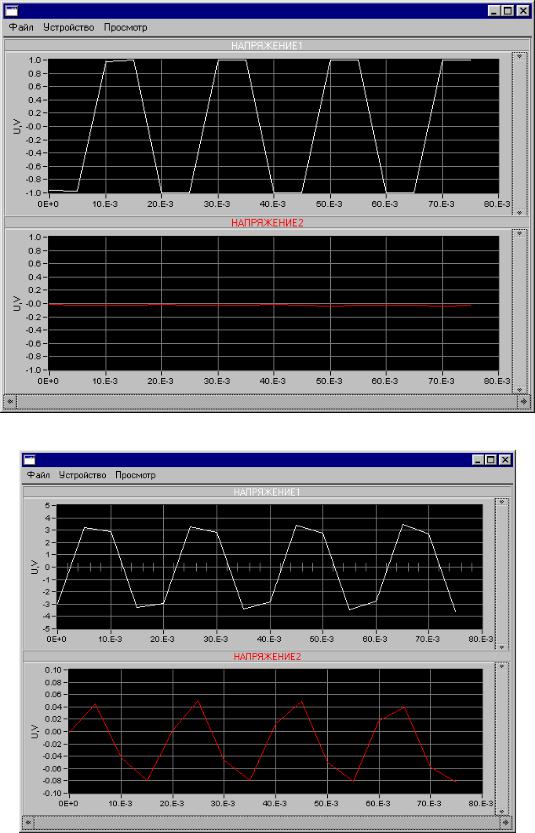
вблизи нуля). Установив первый диапазон 5 В, а второй – 0.1 В, и проведя повторное измерение, получим результат, представленный на рис.5.19.
Рис. 5.18. Результат измерения для U1=U2=1В, FД=200Гц, N=16, T=0.08с
Рис. 5.19. Результат измерения для U1=5В, U2=0.1В, FД=200Гц, N=16, T=0.08с
79
Ограничения в первом канале уже нет, а график второго канала – максимально возможный.
Изображения сигналов, представленные рис.5.18 и рис.5.19, лишь отдалённо напоминают ожидавшуюся синусоиду. Это происходит из-за небольшого временного разрешения АЦП при заданной частоте дискретизации, всего порядка 4 точки на период входного сигнала. Проведя повторный эксперимент с частотой дискретизации 1 КГц (20 точек на период, всего 64 точки), получим гораздо более точное изображение сигнала (рис. 5.20). На этих графиках хорошо видны тонкие детали - искажения формы, присутствие гармоник высших порядков (особенно на втором графике). При измерении с параметрами 2 КГц, 128 точек (40 точек на период) изображение ещё лучше (рис. 5.21). В общем случае, о достаточности частоты дискретизации можно судить по тому, насколько точно повторяется форма сигнала от измерения к измерению при постоянной частоте, и насколько улучшается изображение при переходе на более высокую частоту.
Команды меню ‘Просмотр’ позволяют более детально рассмотреть полученные результаты (рис. 5.22). ‘In__2X’ (клавиша стрелка влево) увеличивает разрешение по времени в 2 раза, ‘Out_2X’ (стрелка вправо) уменьшает разрешение по времени в 2 раза, ‘OutFull_X’ (End) возвращает график в исходное состояние. Аналогично, ‘In__2Y’ (PgDown) увеличивает разрешение по амплитуде в 2 раза, ‘Out_2Y’ (PgUp) уменьшает его в 2 раза, ‘OutFull_Y’ (Home) возвращает график в исходное состояние. Во время просмотра, используя полосы прокрутки, можно перемещать график по вертикали и горизонтали. Манипуляции по оси времени производятся одновременно со всеми графиками, по оси амплитуд – с выбранным.
В меню ‘Просмотр’, кроме этого, имеется команда ‘Параметры сигнала’ (дублируется клавишей F12), использование которой позволяет вывести статистические параметры сигналов – среднее значение (постоянную составляющую) и среднеквадратическое отклонение (действующее значение переменной составляющей). Результат использования этой команды представлен на рис. 5.23.
По окончании измерений результаты можно вывести на принтер и сохранить в текстовом виде, используя соответствующие команды меню ‘Файл’ (рис. 5.24). При выполнении команды ‘Файл \ Сохранить’ сигналы (дублируется клавишей F2) появляется стандартное окно Windows (рис. 5.25), позволяющее выбрать имя и место расположения создаваемого файла с результатами.
Завершается работа программы стандартным способом – при помощи команды ‘Файл \ Выход’ либо нажатием копки ‘Закрыть’ (‘Крест’) на окне программы.
80
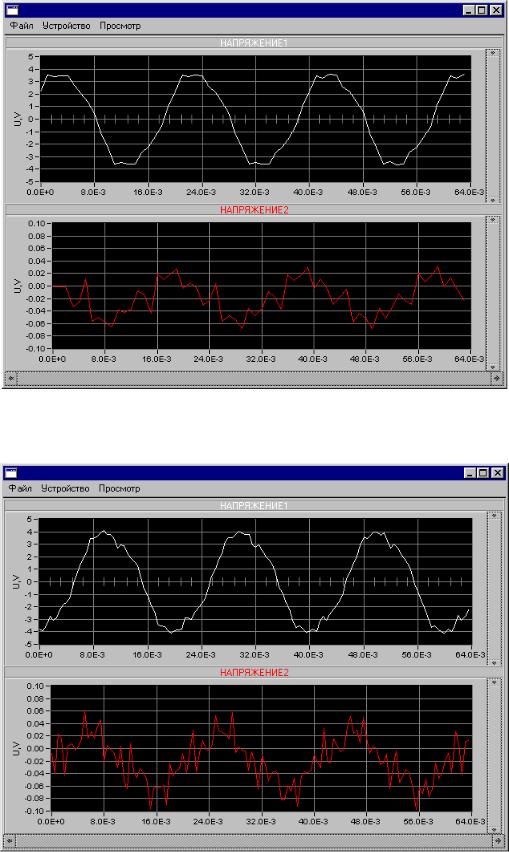
Рис. 5.20. Результат измерения для U1=5В, U2=0.1В, FД=1000Гц, N=64, T=0.064с
Рис. 5.21. Результат измерения для U1=5В, U2=0.1В, FД=2000Гц, N=128, T=0.064с
81
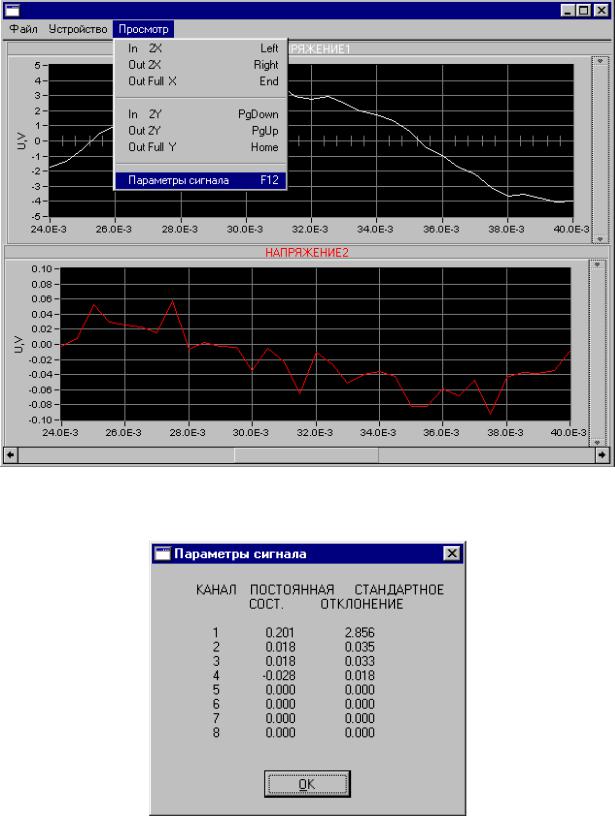
Рис. 5.22. Просмотр результатов измерения
Рис. 5.23. Вывод статистических параметров сигналов
82
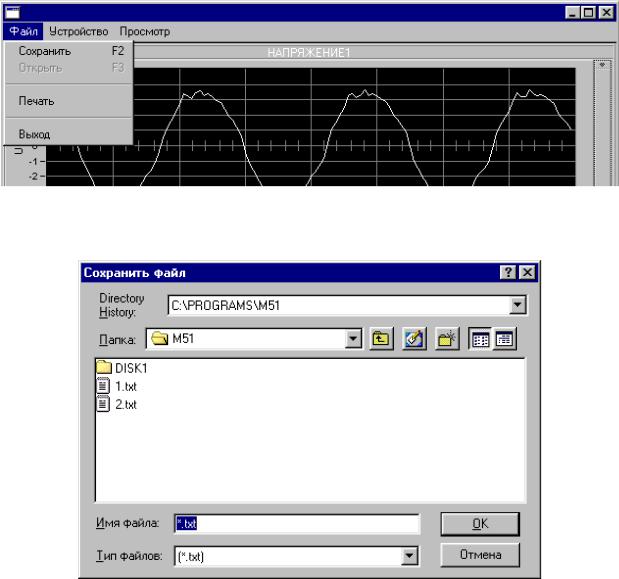
Рис. 5.24. Команды меню ‘Файл’
Рис. 5.25. Окно сохранения результатов
Порядок работы
1.Проверить исправность и работоспособность комплекса М-05.
2.Проверить исправность установки МТПУ-300.
3.Подготовить измерительный комплекс к работе. (Согласно пункту 5.5 данной работы). Особое внимание обратить на правильность заземления комплекса и установки.
4.Подсоединить трансформатор тока к шине первичной обмотки сварочного трансформатора. Выходные клеммы трансформатора тока соединить
свходным каналом № 1 АЦП измерительного комплекса. (Рис. 5.7)
5.Для измерения напряжения между электродами один конец соединительных проводов закрепить между электродами и электрододержателями, а
83
другой конец соединить с входным каналом № 2 АЦП измерительного комплекса.
6.Для измерения усилия сжатия электродов наклеить тензодатчики на нижнюю консоль сварочной машины, соединить их с тензостанцией согласно п. 5.6.2. От тензостанции сигнал подать на входной канал № 4 АЦП измерительного комплекса.
7.Привести параметры АЦП измерительного блока в соответствие с ожидаемыми параметрами входных сигналов. Выставить все необходимые установки параметров преобразования.
8.Используя окно конфигурации вывода, отключить неиспользуемые каналы измерительного комплекса и получить рабочее окно прибора в трехканальном режиме.
9.Провести пробный запуск сварочной установки.
10.Установить необходимые режимы сварки: ступень сварочного трансформатора, время сварки, усилие сжатия электродов, фазовую регулировку тока, число импульсов тока, характер изменения усилия сжатия.
11.Провести сварку на выбранном режиме с одновременным фиксированием сварочного тока, напряжения на электродах и усилия сжатия.
12.Посмотреть результаты измерения. В случае появления наводок от посторонних источников напряжения проверить заземление измерительного комплекса и сварочной установки, и провести эксперимент повторно.
13.Сохранить в файл результаты измерения.
14.Разрушить образец, измерить диаметр и высоту ядра.
15.Провести серию экспериментов, меняя параметры режима сварки: ступень сварочного трансформатора, время сварки, усилие сжатия электродов, фазовую регулировку тока, число импульсов тока, характер изменения усилия сжатия. Фиксировать сварочный ток, напряжение на электродах и усилие сжатия. Разрушать образцы, при этом измеряя диаметр и высоту ядра.
16.Посмотреть и оценить результаты измерений. Сделать выводы о взаимодействии параметров режима сварки.
17.Составить отчет о проделанной работе.
Содержание отчета
-Нарисовать схему измерительного комплекса.
-Перечислить необходимые установки параметров преобразования.
-Нарисовать схему подключения датчиков к сварочной установке и к измерительному комплексу.
-Привести графики полученных результатов. (Либо построить диаграммы с помощью программы MS-Excel, либо получить графики, используя
«печать экрана» (кнопка «PRINT SCREEN»)).
-Указать выводы по работе.
84
Контрольные вопросы
1.Объясните принцип действия измерительного комплекса.
2.Как влияет схема заземления измерительного комплекса и сварочной установки на качество измерения.
3.Объясните, как выбранные в установках параметров измерения входные диапазоны каналов, частота дискретизации и число точек на канал влияют на точность измерения.
4.Объяснить принцип действия токоизмерительного шунта.
5.Объяснить принцип действия тензодатчиков.
6.Как влияет изменение ступени сварочного трансформатора, времени сварки и усилия сжатия электродов на изменение геометрические параметры сварной точки.
7.Для чего применяется ковочное усилие при контактной точечной
сварки.
8.Как меняется осциллограмма сварочного тока при фазовой регулировке тока.
9.Назовите программы, с помощью которых можно обработать результаты измерений, представленные в текстовых файлах, и представить их в наглядной форме.
85
Лабораторная работа 6
ОПРЕДЕЛЕНИЕ ЭЛЕКТРИЧЕСКИХ ПАРАМЕТРОВ КОНТАКТНОЙ МАШИНЫ
Цель работы приобрести опыт работы с приборами в реальных условиях, выявить основные параметры машины, научиться определять по заданному режиму ступень сварочного трансформатора и строить внешние характеристики контактных машин.
Оборудование и материалы
1.Контактная машина (по указанию преподавателей).
2.Измерительный комплекс М-05.
3.Трансформатор тока УТТ-5.
4.Шунт токоизмерительный.
5.Соединительные провода.
6.Стальные и медные пластины или стальные и медные трубки, охлаждаемые проточной водой.
7.Передвижной лабораторный стол с набором необходимых проводов и инструмента.
Теоретические сведения
К электрическим параметрам контактной машины относятся напряжения первичной и вторичной цепей сварочного трансформатора, ток в первичной обмотке и ток сварки, электрическое сопротивление сварки. Графическая зависимость между рабочим током и напряжением называется внешней характеристикой. Обычно внешние характеристики контактных машин падающие, но они могут быть крутыми и пологими. Пересечение внешней характеристикой (рис. 6.1 а) оси абсцисс в точке I2 соответствует короткому замыка-
нию (Rсв = 0, Uсв = 0), а пересечение оси ординат в точке U2 холостому ходу
(U2 = U20 I2 = 0 и R = ).
При определенном вторичном напряжении U2 ток короткого замыкания будет тем больше, чем меньше общее сопротивление сварочной машины.
Площадь прямоугольника ОАБС (рис. 6.1 а) пропорциональна полезной мощности, затрачиваемой непосредственно на сварку. С изменением общего сопротивления металла в месте сварки изменяется напряжение на электродах и вторичный ток. В этом случае полезная мощность определяется площадью ОА'В'С', которая не будет равна первоначальной площади.
86
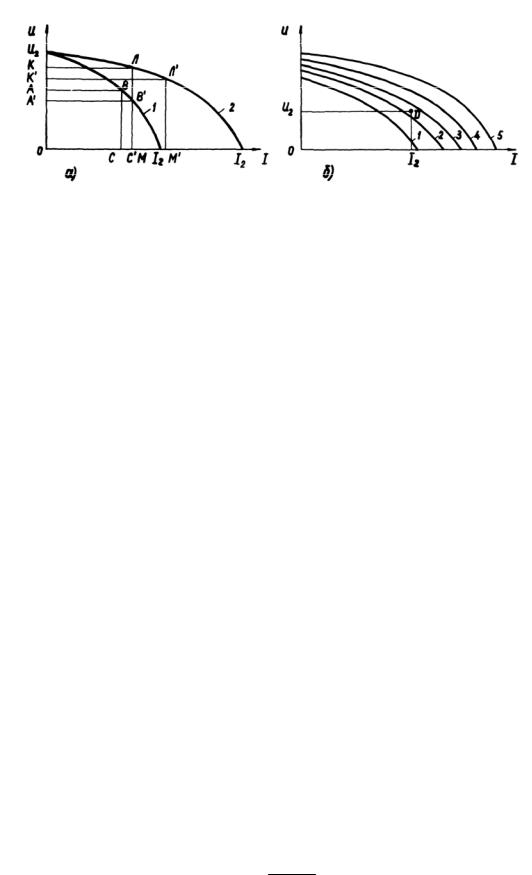
Рис. 6.1. Внешние характеристики контактных машин: а крутопадающая и пологопадающая; б пример определения ступени сварочного трансформатора
При крутопадающей характеристике 1 изменение площадей незначительно и полезная мощность мало изменяется. При пологой характеристике 2 разница в площадях ОК'Л'М' и ОКЛМ будет уже значительной, что вызовет заметное изменение полезной мощности.
Для получения одинаковых по качеству сварных соединений при работе на точечных и шовных машинах нежелательно изменять их электрические параметры. Целесообразно, чтобы точечные и шовные машины имели крутопадающие характеристики.
Для стыковых машин, наоборот, обычно рекомендуется пологая внешняя характеристика. В этом случае при уменьшении сопротивления сварочной цепи машины в момент возникновения перемычек между оплавляемыми торцами резко увеличивается ток, ускоряющий их нагрев и разрушение. В результате процесс оплавления идет устойчивее.
Внешние характеристики позволяют при заданном сварочном токе и известном сопротивлении свариваемых деталей определить вторичное напряжение. Откладывая ток и напряжение на внешних характеристиках 1 5 данной машины (рис. 6.1 б) по пересечению их в точке Д, можно найти ступень включения трансформатора, на которой должна осуществляться сварка. Это важно знать при разработке технологического процесса контактной сварки.
Полезная мощность Pсв, затрачиваемая машиной непосредственно на сварку:
РСВ IСВ2 RСВ .
Номинальная мощность контактной машины, то есть мощность машины при сварке на номинальной ступени и при номинальном первичном напряжении,
РНОМ U10001 I1 ,
87
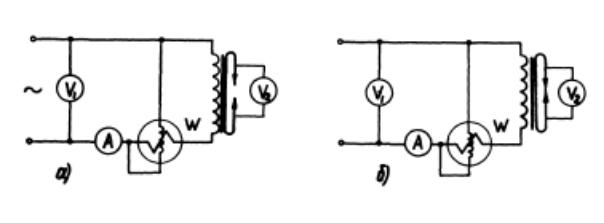
где Pном номинальная мощность машины; U1 номинальное напряжение; I1 ток, потребляемый машиной из сети на номинальной ступени.
Для построения внешней характеристики проводят опыт холостого хода, опыт короткого замыкания и замеряют электрические параметры (U1, I1) при различных нагрузках (по схемам рис. 6.2).
Рис. 6.2. Схемы опытов: а - холостого хода, б - короткого замыкания
Опыт холостого хода делается для всех ступеней трансформатора при разомкнутой вторичной цепи. С помощью трансформатора тока, проводов и измерительного комплекса М-05 определяют ток холостого хода I0, напряжение питающей сети U0, э. д. с. вторичной обмотки трансформатора Е2 и потери холостого хода P0 (Использование измерительного комплекса М-05 описано в лабораторной работе №5). Эти данные позволяют найти крайнюю точку внешней характеристики при I2 = 0, U2 = E2 и коэффициент трансформации Ктр для всех ступеней включения трансформатора
КТР U1 ,
E2n
где Ктр и Е2n соответственно коэффициент трансформации и э.д.с. вторичной обмотки n-й ступени. Опыт холостого хода позволяет определить число витков первичной обмотки трансформатора на различных ступенях включения
n 2 Ктрn ,
где n число витков первичной обмотки на n-й ступени; 2 число витков
вторичной обмотки (обычно 2 = 1).
Опыт короткого замыкания проводят при замкнутых электродах (губках). При невозможности непосредственного контакта, например на стыковых машинах, электроды замыкают через массивный медный стержень при минимальном разводе зажимных устройств. При коротком замыкании для ступени n замеряют первичный ток короткого замыкания Iкзn, напряжение питающей сети U1 и потребляемую мощность машины Ркзn. Эти замеры дают
88
другую крайнюю точку внешней характеристики (при I2 = Iкзn и U2 = 0) и коэффициент мощности машины (для ступени n) в режиме короткого замыкания:
cos n |
U1 I |
кзn . |
||
|
|
Pкзn |
|
|
Ток первичной обмотки сварочного трансформатора можно измерить с помощью трансформаторов тока или измерительных шунтов. Для определения промежуточных точек внешней характеристики этой же ступени измеряют все электрические параметры при различных сопротивлениях вторичной цепи. С целью измерения этих параметров между электродами (губками, роликами) машины зажимают пластины или трубки, разные по собственному электрическому сопротивлению. Чтобы не допустить перегрева зажатых между электродами деталей, следует интенсивно охлаждать их проточной водой. Практически целесообразно для стыковых машин в качестве меняющегося сопротивления между губками применять металлические трубки, а для точечных и роликовых машин - пластины. В зависимости от количества пластин, зажатых между электродами, изменяется и электрическое сопротивление между ними, а следовательно, и ток во второй цепи I2. Материалом пластин может служить нержавеющая сталь. Для предотвращения сваривания этих пластин следует между ними устанавливать медные вставки. Величину вторичного тока I2 рассчитывают по коэффициенту трансформации для данной ступени:
I2 I1 I0 12 ,
где I1 ток первичной обмотки при коротком замыкании; I0 ток первичной обмотки при холостом ходе; 1, 2 число витков соответственно в первичной и вторичной обмотках сварочного трансформатора.
Полученные опытные данные холостого хода каждой ступени и короткого замыкания для нескольких ступеней, а также расчеты дают возможность графически построить внешнюю характеристику машины.
Индуктивное сопротивление контура определяется его площадью, а активное длиной, сечением токопроводов и величиной переходных сопротивлений. Эти сопротивления сравнительно невелики и измеряются в микроомах.
Переходные сопротивления сварочного контура зависят в основном от состояния поверхности контактов, тщательности сборки и усилия сжатия (рис. 6.3). При различной обработке контактируемых поверхностей медь медь и медь сталь переходное сопротивление вначале резко падает, а потом заметно стабилизируется.
89
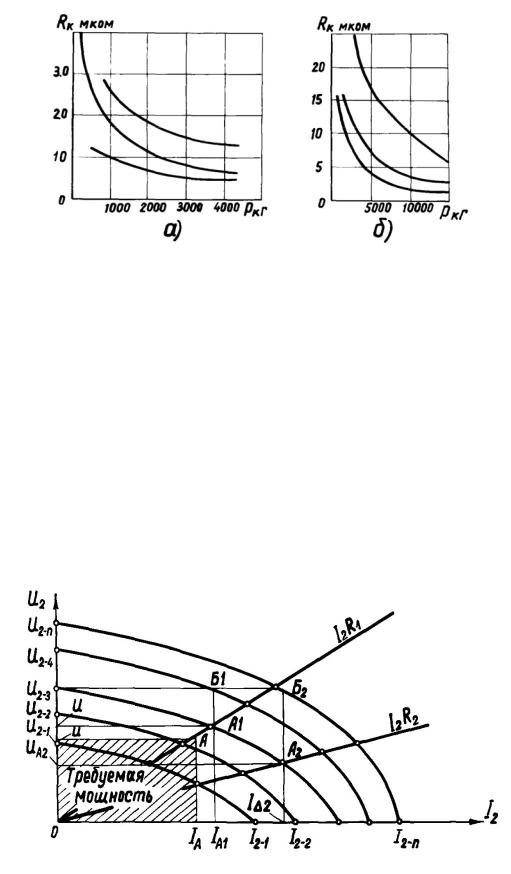
Рис. 6.3. Зависимость сопротивления контактов медь медь (а) и медь сталь (б) от усилия сжатия поверхностей
Например, при сварке оплавлением для заданного тока и известного сопротивления R (рис. 6.4) характеристики позволяют выбирать требуемую ступень регулирования мощности трансформатора имеющейся машины (ступень U2-3 для точки А1). Эта мощность выражается площадью прямоугольни-
ка UA А IA О (pис. 6.4).
Трансформатор на наиболее приемлемой ступени внешней характеристики обеспечит мощность в соответствии с прямоугольником UА1Al IA1 О. Теряемая при оплавлении в сварочном контуре машины мощность будет равна прямоугольнику UA1A1Б1U2-3. Для стадии осадки при сварке оплавлением с нагрузкой I2R2 полезная мощность будет соответствовать прямоугольнику UА2А2I2O, а теряемая прямоугольнику UА2А2Б2U2-3.
Рис. 6.4. Внешние характеристики стыковых машин
90
Порядок выполнения работы
Опыт холостого хода
1.Составить схему подключения датчиков и измерительного комплекса для опыта холостого хода и согласовать ее построение с преподавателем.
2.Подключить необходимые измерительные приборы и предъявить их для проверки лаборанту.
3.При разомкнутой вторичной цепи на всех ступенях включения изме-
рить ток для холостого хода I0, напряжение питающей сети U1, э.д.с. вторичной обмотки трансформатора E1 и потери холостого хода Р0.
4.Вычислить коэффициент трансформации для всех ступеней включения. Результаты замеров и вычислений записать в таблицу.
5.Разобрать схему.
Опыт короткого замыкания
1.Составить схему подключения датчиков и измерительного комплекса для опыта короткого замыкания и согласовать ее с преподавателем.
2.Подключить необходимые измерительные приборы и предъявить их для проверки лаборанту.
3.Замкнуть вторичную цепь и на первой ступени замерить ток коротко-
го замыкания в первичной обмотке I1, напряжение питающей сети U1 и потребляемую мощность.
4.Установить между электродами (губками) машины детали с различ-
ным электросопротивлением; измерить ток в первичной обмотке I1, напряжение сети U1, напряжение на электродах U2 и потребляемую из сети мощность Р1. Опыт проделать на первой, средней и предпоследней ступенях включения. Количество деталей с различным сопротивлением должно быть не менее 5 шт.
5.Пользуясь данными опыта холостого хода, вычислить сварочный ток I2 во вторичной цепи. Результаты замеров и вычислений записать в таблицу.
6.Разобрать схему.
7.На основании табличных данных построить внешние характеристики
U2 = f(I2) и зависимость потребляемой мощности из сети тока во вторичной цепи Р = f(I2). Для построения крайних точек внешних характеристик следует использовать данные опыта холостого хода и короткого замыкания.
Содержание отчета
Отчет должен содержать схему включения приборов с указанием их характеристик, результаты измерений и подсчетов в виде таблиц и графиков, пример определения ступени трансформатора, выводы по работе.
91
Контрольные вопросы
1. С какой целью строятся внешние характеристики контактных ма-
шин?
2.Каким образом влияет крутизна внешней характеристики на процесс стыковой, точечной и роликовой сварки?
3.Влияние активного и индуктивного сопротивления на внешнюю характеристику контактной машины.
4.Какими факторами определяется ступень крутизны внешней характеристики машины?
5.Как определяется ступень трансформатора для сварки деталей?
6.Какое влияние оказывает усилие сжатия электродов величину контактных сопротивлений между пластинами?
7.Способы измерения сварочного тока. Какое оборудование при этом применяется?
92
Лабораторная работа 7
ИЗУЧЕНИЕ КОНСТРУКЦИИ МАШИН И ИССЛЕДОВАНИЕ ТЕХНОЛОГИИ ОДНОСТОРОННЕЙ
КОНТАКТНОЙ ТОЧЕЧНОЙ СВАРКИ
Цель работы: изучить особенности односторонней сварки. Выявить влияние основных технологических параметров на качество сварного соединения. Овладеть методикой определения сварочного тока и времени его протекания, напряжения на электродах, усилия сжатия и диаметра сварной точки.
Оборудование и материалы
1.Экспериментальная установка ПИСФУ на базе МТП-400-3.
2.Датчики и измерительно-регистрирующий комплекс для наблюдения и записи параметров режима.
3.Образцы для сварки.
4.Спецодежда, необходимый инструмент.
Общие сведения
Сущность, достоинства и недостатки односторонней сварки
По способу подвода тока к свариваемому изделию различают двустороннюю и одностороннюю контактную сварку.
Достоинствами односторонней сварки (далее – ОКТС) по сравнению с двусторонней является увеличение производительности за счет постановки одновременно двух и более точек и меньшая электрическая мощность оборудования из-за небольших размеров сварочного контура. Также в связи с односторонним подводом тока облегчается механизация и автоматизация процесса сварки. И, наконец, в ряде конструкций не всегда возможен двусторонний подвод электродов к месту соединения.
Основной особенностью процесса является то, что в большинстве случаев через контакт между свариваемыми листами проходит не весь ток, подводимый электродами. Часть общего тока I2 (рис.7.1) шунтируется через деталь, контактирующую с токоподводящими электродами, не участвуя в процессе сварки.
Сам по себе ток шунтирования вреден тем, что вызывает непроизводительную потерю мощности и энергии. Для процесса сварки намного страшнее следствия наличия этого тока. В месте контактирования электрода с деталью выделяется излишнее тепло, что ведет к выплеску и наплывам металла на поверхности сварных точек со стороны электродов высотой 10 – 15 % от толщины листа. При повышенных токах шунтирования
93
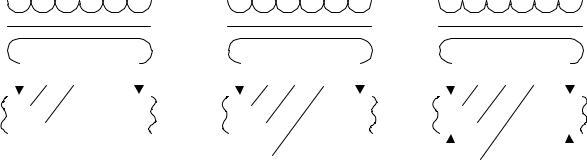
переходный контакт может оказаться основным очагом выделения тепла, и сварка может оказаться вообще неосуществимой.
Происходит это потому, что общий ток сварочного трансформатора I2 приходится повышать на величину тока IД1. Плотность тока в контакте повышенная, что, кроме выплеска, ведет к износу электродов. Кроме того, на поверхности детали образуются очень заметные вмятины, что ухудшает внешний вид сварной конструкции.
Ток шунтирования также искажает электрическое и тепловое поле в приэлектродной области. Поэтому наплывы и выплески металла наблюдаются в местах со стороны электродов.
Литая зона в продольном сечении, проходящем через оси электродов, имеет несколько большую ширину и иную форму, чем в поперечном сечении. Фактический диаметр ядра (dЯФ), определяемый в месте соединения деталей, может оказаться значительно меньше номинального диаметра dЯ. Иногда наблюдается недостаточное проплавление детали, которая не контактирует с токоподводящими электродами.
Вследствие нагрева деталей токами IД1 и IД2, под действием усилия сжатия электродов FСВ происходит их коробление и деформация, вызванные потерей прочности. Это приводит к ухудшению качества сварных соединений.
Основные схемы сварки
|
|
|
|
IД1 IД2 |
|
|
|
|
|
|
IД1 IД2 IШ |
|
|
|
|
|
|
|
|
IД1 IД2 IШ |
|
|
|||||||
|
|
|
|
|
|
||||||||||||||||||||||||
|
|
|
|
|
|
|
|
|
|
|
|
|
|
|
|
|
|
|
|
|
|
|
|
|
|
|
|
|
|
|
|
|
|
|
|
|
|
|
|
|
|
|
|
|
|
|
|
|
|
|
|
|
|
|
|
|
|
|
|
|
|
|
|
|
|
|
|
|
|
|
|
|
|
|
|
|
|
|
|
|
|
|
|
|
|
|
|
|
|
|
|
|
|
|
|
|
|
|
|
|
|
|
|
|
|
|
|
|
|
|
|
|
|
|
|
|
|
|
|
|
|
|
|
|
|
|
|
|
|
|
|
|
|
|
|
|
|
|
|
|
|
|
|
|
|
|
|
|
|
|
|
|
|
|
|
|
|
|
|
|
|
|
|
|
|
|
|
|
|
|
|
|
|
|
|
|
|
|
|
|
|
|
|
|
|
|
|
|
|
|
|
|
|
|
|
|
|
|
|
|
|
|
|
|
|
|
|
|
|
|
|
|
|
|
|
|
|
|
|
|
|
|
|
|
|
|
|
|
|
|
|
|
|
|
|
|
|
|
|
а). |
б). |
в). |
Рис. 7.1. Основные схемы ОКТС: а)Сварка без подкладки, б)сварка на подкладке, в) сварка на короткозамкнутых электродах
На практике встречаются различные случаи односторонней сварки. На рис. 9 приведены самые распространенные схемы ОКТС. ОКТС без применения подкладки (рис. 7.1 а) допускает применение простого универсального оборудования и в этом смысле превосходит другие виды данной сварки. Однако сварное соединение получается лишь при соблюдении некоторых условий протекания процесса сварки, так как процесс характеризуется самыми большими относительными (в % к I2) и абсолютными значениями тока шун-
94
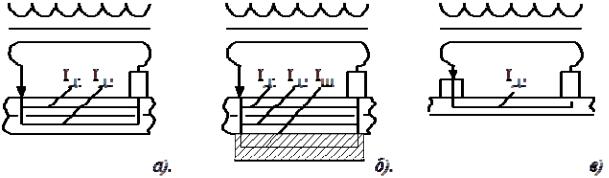
тирования IД1. В частности, необходимо, чтобы сопротивление детали, расположенной со стороны токоподвода (в дальнейшем эта деталь будет именоваться «верхней») было намного больше сопротивления другой детали («нижней»). На практике данная схема применима лишь при достаточно большом расстоянии между одновременно свариваемыми точками, а также соблюдении разнотолщинности деталей не менее чем 1:3. Нижняя деталь должна быть достаточно жесткой, чтобы не деформироваться под действием теплоты, выделяемой при прохождении сварочного тока IСВ = IД2. Вследствие больших значений тока шунтирования IД1 при сварке практически неизбежны наружные выплески, наплывы металла со стороны другого электрода, а также процесс массопереноса в контакте электрод – деталь.
На рис. 7.1 б показана схема сварки с использованием токоподводящей подкладки. Подкладка выполняется из меди и ее сплавов. Обладая малым сопротивлением, она заставляет ток вторичной обмотки сварочного трансформатора I2 распределяться на 3 ветви; причем сварочный ток будет являться сумма токов IД2и IД3. Значения IД3велики по сравнению с токами IД1 и IД2, следовательно, и процент сварочного тока в общем токе I2 будет высоким. Предельное расстояние между точками уменьшается.
Одним из вариантов использования подкладки является сварка с использованием электродов, замкнутых медным шунтом (рис. 7.1 в). Такая форма подкладки хороша тем, что подведенные нижние электроды концентрируют ток в местах образования сварных точек. Однако технологически ее применять сложнее, чем вариант на рис. 7.1.б, так как нужно соблюдать взаимное расположение (соосность) пар электродов.
Сварка с холостым электродом (рис. 7.2) используется там, где невозможен двусторонний подвод тока и не требуется получение двух сварных точек. Холостой электрод, выполненный в виде массивного (по сравнению с рабочим электродом) цилиндра или прямоугольника, может присоединяться как к верхней, так и к нижней детали. В случае присоединения к верхней детали он не дает образовываться второму литому ядру из-за сильно увеличенного пятна контакта. Плотность тока оказывается недостаточной для образования сварной точки.
Рис. 7.2. Схемы сварки с использованием холостого электрода
95
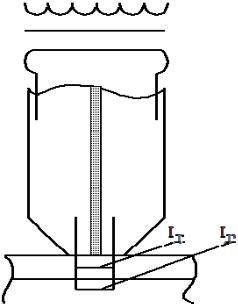
Сварка сдвоенным электродом (рис. 7.3) получила широкое применение в приборостроении, особенно в радиоэлектронном производстве. В машиностроении такая сварка не применяется.
Рис. 7.3. Схемы сварки сдоенным электродом
Краткие сведения о технологии сварки
Все технологические особенности, применяемые при ОКТС, прямо или косвенно направлены на устранение или уменьшение вредного влияния тока шунтирования: уменьшение его относительной и абсолютной величины, устранению выплеска и т. д.
Основной технологический прием – использование токоведущей подкладки, располагающейся под свариваемыми деталями. Кроме значительного снижения тока шунтирования, она предохраняет от нежелательных деформаций свариваемые детали. Рекомендуется применять ее, где только возможно. Желательно использовать водяное охлаждение подкладок, причем внутреннее предпочтительнее внешнего. Толщина ее должна составлять не менее 10 мм.
При сварке разных деталей (деталей из материалов с различным удельным электросопротивлением, а также деталей различных габаритов – длины и ширины) появляется возможность уменьшить IД1, размещая со стороны электродов деталь с большим сопротивлением, т. е. более тонкую и узкую деталь, а также деталь из материала с большим удельным электросопротивлением.
Большое влияние на величину IД1 оказывает расстояние между электродами. При прочих равных условиях, чем оно больше, тем меньше IД1, а значит, стабильнее процесс сварки.
Для уменьшения вероятности наружного выплеска рекомендуется снижать плотность тока в контакте токоподводящий электрод - верхняя деталь
96
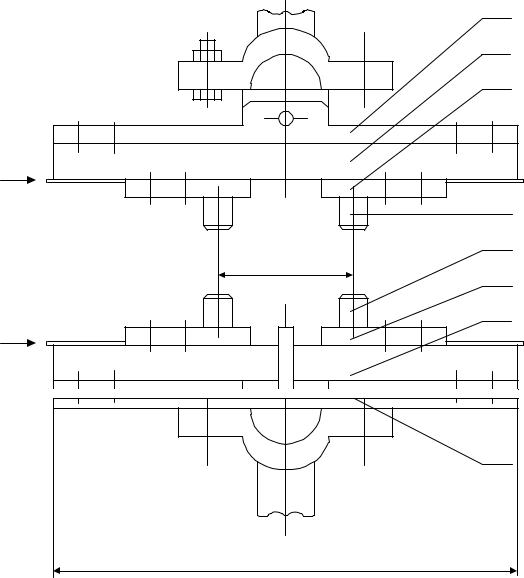
путем увеличения контактной поверхности электрода на 15-20% по сравне- |
|
нию с двусторонней сваркой деталей таких же толщин, а также использовать |
|
сферическую форму электрода с большим радиусом. Сферическая форма |
|
контакта электродов также уменьшает вероятность появления наплывов ме- |
|
талла на поверхности сварных точек со стороны электродов. |
|
Краткое описание экспериментальной установки |
|
для исследования процесса односторонней сварки |
|
Экспериментальная установка изготовлена |
|
на базе универсальной машины МПТ-400 |
|
Внешний контур машины превращен в систему с односторонним подводом |
|
тока (рис. 7.4). |
|
|
4 |
|
5 |
|
6 |
|
7 |
|
3 |
L |
2 |
|
|
|
1 |
|
8 |
400 |
|
Рис. 7.4. Внешний контур установки |
|
97
Для этого с машины были сняты верхний и нижний хоботы с электрододержателями и электродами. На кронштейн нижнего хобота установлены две токоподводящие колодки. 1. В их пазах размещены электрододержатели 2 с электродами 3, которые имеют возможность перемещаться относительно друг друга. На шток механизма сжатия, на кронштейне, установлено коромысло 4 с шунтирующей колодкой 5. В пазах шунтирующей колодки находятся электрододержатели 6 с электродами 7, также имеющими возможность перемещаться относительно друг друга. Токоподводящие колодки разделены между собой изоляционными прокладками 8.
Водяное охлаждение подведено как к токоподводящим, так и к шунтирующим электродам. Вода поступает через каналы в электрододержателях и каналы в самих колодках.
Для изменения расстояния между электродами необходимо ослабить болты, крепящие колодки к кронштейнам, переместить колодки на необходимое расстояние и затянуть болты. При этом обратить внимание на симметричность расположения колодок и на соосность токоподводящих и шунтирующих электродов.
Для замены электродов нужно ослабить болты, крепящие колодки к кронштейнам, затем вынуть колодки из пазов кронштейна. С помощью молотка и металлического прутка выбить электроды, после чего на их место поставить новые и установить колодки на место.
В качестве шкафа управления процессом сварки использовали ШУ ПСЛТ – 1200, который обеспечивает:
- длительность операции «Импульс» сварочного тока от 1 до 20 перио-
дов;
-длительность операции «Пауза» (между импульсами сварочного тока) от 0 до 20 периодов;
-максимальную длительность нарастания переднего фронта первого импульса сварочного тока (модуляцию) не менее 15 периодов;
-пределы регулирования действующего значения сварочного тока (фазовое регулирование) от 30 до 100%.
Усилие сжатия электродов создается пневматическим приводом поршневого типа. На рис.7.5 показана пневматическая схема механизма сжатия. Подобная система со шкафом управления ПСЛТ-1200 может обеспечить изменение усилия на электродах за время цикла сварки.
Цилиндр 5 имеет два поршня: нижний, передающий давление электроду,
иверхний, ограничивающий движение нижнего вверх. Таким образом, цилиндр включает в себя три камеры: А, В, и С.
Воздух из сети поступает через вентиль 11, проходит через фильтрвлагоотделитель 10 и собирается в ресиверах 9(1) и 9(2). Редуктор 1(1) с манометром 2(1) регулирует давление воздуха в рабочей камере В, а редуктор1(2) – в камере С. Из ресиверов воздух проходит через лубрикаторы 8, после чего поступает к управляющим клапанам.
98
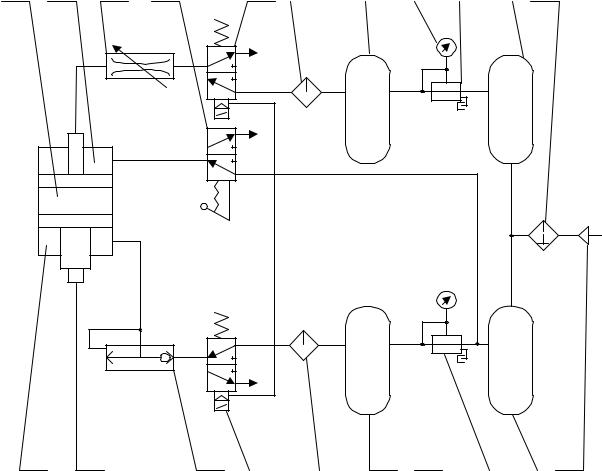
В |
А |
7 |
6 |
3(1) |
8(1) |
9(4) |
2(1) |
1(1) |
9(1) |
10 |
|
|
С |
5 |
4 |
3(2) |
|
8(2) |
9(3) |
2(2) |
1(2) |
9(2) |
11 |
|
|
|
Рис. 7.5. |
Пневматическая схема установки. |
|
|
|
Полость цилиндра А наполняется воздухом через ручной кран. Впуск и выпуск воздуха в рабочую полость В осуществляется через отверстие в верхнем штоке посредством электропневматического клапана 3(1) и дросселирующего клапана 7. В полость С воздух подается через клапан 3(2).
Усилие FСВ создается в полости В воздухом, работающим с противодавлением в полости С. Переход от FСВ к FК осуществляется путем выпуска воздуха из камеры С, для чего между цилиндром и электропневмоклапаном 3(2) установлен выхлопной клапан 4. Усилие нарастает за короткий промежуток времени (0,01-0,02 сек.).
Модернизированная машина имеет возможность производить одностороннюю сварку с усилием 100 – 1600 кг с. в пределах 30 – 400 мм между свариваемыми точками.
Трансформатор имеет 16 ступеней. Номинальный ток во вторичной обмотке 40 кА. Вторичное напряжение меняется от 4,7 В. на первой ступени до 9,7 В. на последней.
Мощность машины – 365 кВА. Продолжительность включения – 20%.
99

Номинальная ступень регулирования вторичного напряжения – 15. Коэффициент мощности при коротком замыкании на номинальной сту-
пени (cos ) – 0,28.
Порядок выполнения работы
1.Произвести внешний осмотр установки, включить охлаждение и воздушный компрессор, проверить заземление.
2.Подключить используемые датчики и измерительный комплекс (согласно схеме и указаниям, приведенным ниже).
3.Включить машину в сеть, проверить работу всех узлов.
4.Произвести сварку с регистрацией параметров режима. Исследовать (по заданию преподавателя):
4.1.Влияние схемы сварки на размеры литого ядра и параметры
режима.
Указания: Сварка образцов из Ст.3 толщиной 1+2 мм. (тонкая деталь со стороны токоподводящих электродов). Использовать три схемы сварки:
А). Сварка без подкладки, Б). Сварка на подкладке,
В). Сварка на короткозамкнутых электродах.
Для всех схем применить одинаковые устанавливаемые парамет-
ры (lЭ, U2, FСВ, tСВ, dЭ). Регистрировать I2, dT, наличие или отсутствие выплеска. Осмотреть полученные образцы, сравнить характер температурного поля по цветам побежалости.
Заполнить таблицу:
№ п. п. |
Схема сварки |
I2 |
dT |
Выплеск |
Прим. |
|
кА |
мм |
есть-нет |
||||
|
|
|
dЭ = ____ мм., lЭ = ____ мм., U2 = ____ В., tСВ = ____ с., FСВ = ____ Н.
4.2. Влияние толщины деталей на размеры литого ядра и параметры режима.
Указания: По схеме без применения подкладки произвести сварку образцов из Ст.3 толщиной:
А). 1+2 мм, Б). 1+3 мм, В). 1+5 мм, Г). 1+10 мм.
100
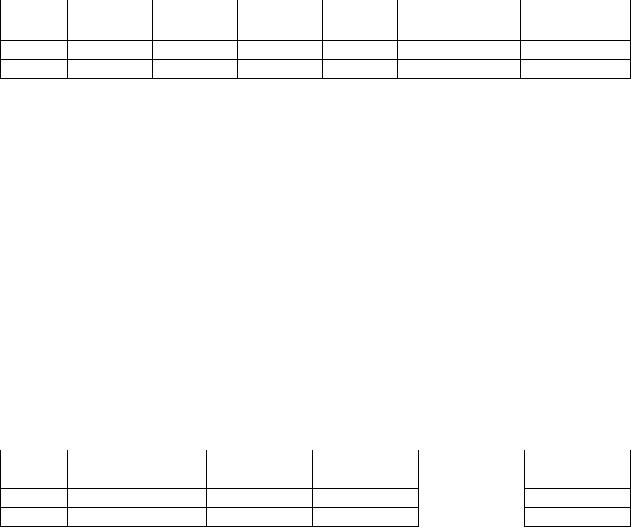
Применить одинаковые устанавливаемые параметры (lЭ, U2, FСВ, tСВ, dЭ). Регистрировать I2, dT, наличие или отсутствие выплеска. Сравнить характер температурного поля. Заполнить таблицу, построить
|
|
|
|
1 |
|
|
|
|
|
|
1 |
|
графики зависимостей: |
I2 |
|
|
|
, |
dТ |
|
|
|
|
||
f |
|
|
|
f |
|
|
. |
|||||
|
|
|
2 |
|
|
|
|
|
2 |
|
№ п. п. |
1 |
2 |
I2 |
dT |
Выплеск |
Прим. |
|
мм |
мм |
кА |
мм |
есть-нет |
|||
|
|
dЭ = ____ мм., lЭ = ____ мм., U2 = ____ В., tСВ = ____ с., FСВ = ____ Н.
4.3. Влияние расстояния между электродами на размеры литого ядра и параметры режима.
Указания: По схеме без применения подкладки произвести сварку образцов из Ст.3 толщиной 1+3 мм. при:
А). lЭ = 35 мм, Б). lЭ = 50 мм, В). lЭ = 100 мм, Г). lЭ = 150 мм, Д). lЭ = 200 мм, Е). lЭ = 400 мм.
Использовать образцы одинаковой ширины. Применить одинако-
вые устанавливаемые параметры (U2, FСВ, tСВ, dЭ). Регистрировать I2, |
|||||||
dT, наличие или отсутствие выплеска. Заполнить таблицу, построить |
|||||||
графики зависимостей: |
I2 f lЭ , |
dТ f lЭ . |
|
|
|||
№ п. п. |
lЭ |
I2 |
dT |
|
Выплеск |
Прим. |
|
мм |
кА |
мм |
есть-нет |
||||
|
|
dЭ = ____ мм., U2 = ____ В., tСВ = ____ с., FСВ = ____ Н.
4.4. Влияние жесткости режима сварки на размеры литого ядра и дефекты сварного соединения.
Указания: По схеме без применения подкладки произвести сварку образцов из Ст.3 толщиной 1+3 мм., lЭ = 40 мм. Использовать режимы:
А). I2= 13кА, tСВ = 0,1 с, Б). I2 = 11 кА, tСВ = 0,2 с, В). I2 = 9 кА, tСВ = 0,3 с, Г). I2 = 7,5 кА, tСВ = 0,4 с, Д). I2 = 6 кА, tСВ = 0,8 с.
101

Необходимой величины тока вторичной обмотки сварочного трансформатора добиться ступенчатой (путем переключения ступе-
ней) или плавной (путем изменения коэффициента мощности) регу-
лировкой.
Во всех случаях использовать одинаковые dЭ, FСВ, ширину образцов. После сварки разрушить образцы. Оценить изменение dT, наличие или отсутствие выплеска, непровара и др. дефектов, характер температурного поля по цветам побежалости. Заполнить таблицу.
№ п. п. |
I2 |
tСВ |
dT |
Дефекты |
Прим. |
|
кА |
с |
мм |
||||
|
|
|
dЭ = ____ мм., lЭ = ____ мм., FСВ = ____ Н.
4.5. Влияние модуляции переднего фронта импульса тока на наличие выплеска и размер литого ядра.
Указания: По схеме без применения подкладки произвести сварку образцов из Ст.3 толщиной 1+3 мм. На жестких и мягких режимах:
А). без модуляции,
Б). tМОД = 2 пер. (0,04 с), В). tМОД = 4 пер. (0,08 с), Г). tМОД = 7 пер. (0,14 с), Д). tМОД = 10 пер. (0,2 с).
Во всех случаях применить одинаковые устанавливаемые параметры (lЭ, U2, FСВ, tСВ, dЭ). Регистрировать I2, dT, наличие или отсутст-
|
|
t |
МОД |
|
|
вие выплеска. Заполнить таблицу, построить графики |
dТ |
|
|
|
|
|
|
||||
f |
|
|
|||
|
|
|
tСВ |
для сварки на мягком и жестком режимах.
№ п. п. |
I2 |
tСВ |
tМОД |
dT |
Выплеск |
Прим. |
|
кА |
c |
c |
мм |
есть-нет |
|||
|
|
dЭ = ____ мм., lЭ = ____ мм., U2 = ____ В., FСВ = ____ Н.
Изобразить форму импульса тока вторичной обмотки. Проанализировать зависимость наличия выплеска от времени модуляции и отношения времени модуляции к времени сварки.
4.6. Влияние цикла сварки на величину тока шунтарования, размеры литого ядра и наличие дефектов сварки.
Указания: Зарисовать возможные циклы сварки. По схеме без применения подкладки произвести сварку одинаковых образцов на каждом из них. При этом регистрировать:
102
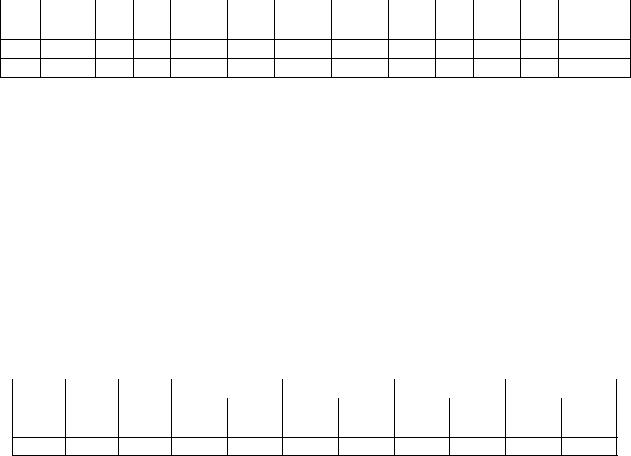
FН – начальное усилие на электродах,
FК – ковочное усилие на электродах,
I2 под – силу тока вторичной обмотки подогревающего импульса, I2 св - силу тока вторичной обмотки сварочного импульса,
IД1 под - силу тока, текущего по верхней детали, подогревающего импульса,
IД1 св - силу тока, текущего по верхней детали, сварочного импуль-
са,
tПОД – время подогревающего импульса, tП – время паузы между импульсами, tСВ – время сварочного импульса,
dT – диаметр точки. Заполнить таблицу:
№ |
№ |
FН |
FК |
I2 под |
I2 св |
IД1 под |
IД1 св |
tПОД |
tП |
tСВ |
dT |
Прим. |
|
Н |
Н |
кА |
кА |
кА |
кА |
с |
с |
с |
мм |
||||
п.п. |
цикла |
|
dЭ = ____ мм., lЭ = ____ мм., 1 = ____ мм., 1 = ____ мм.
Оценить характер температурного поля на каждом образце по цветам побежалости. Проанализировать изменение dT в зависимости от использования различных циклов сварки. Сделать вывод о целесообразности того или иного цикла.
4.7. Размеры и форму ядра на примере сварки многослойного пакета.
Указания: Подготовить пакеты из пяти заготовок Ст.3 толщиной 1 мм. Сварить по схеме без применения подкладки на мягком и жестком режимах с регистрацией основных параметров. После этого разрушить образцы и исследовать продольный и поперечный диаметр ядра во всех четырех плоскостях разрыва. Заполнить таблицу:
№ |
I2 |
tСВ |
d1-1 |
d2-2 |
d3-3 |
d4-4 |
|||||
прод. |
попер |
прод. |
попер |
прод. |
попер |
прод. |
попер |
||||
п.п. |
|
|
|
|
|
|
|
|
|
|
|
кА |
с. |
мм. |
мм. |
мм. |
мм. |
мм. |
мм. |
мм. |
мм. |
||
|
dЭ = ____ мм., lЭ = ____ мм., FСВ = ____ Н.
Зарисовать по полученным данным форму ядра в продольном и поперечном сечении для сварки на жестком и мягком режимах.
5. Составить отчет о проделанной работе согласно п. 4, проанализировать результаты, сформулировать выводы.
103
Контрольные вопросы
1.Сущность и схемы односторонней сварки.
2.Достоинства и недостатки односторонней сварки.
3.Методы уменьшения величины тока шунтирования.
4.Методы устранения или снижения вероятности возникновения вы-
плеска.
5.Влияние различных технологических факторов на размеры сварной
точки:
а) жесткости режима, б) расстояния между электродами,
в) разнотолщинности деталей, г) схемы сварки.
104