
Метода по станкам
.pdf5. НАПРАВЛЯЮЩИЕ МЕТАЛЛОРЕЖУЩИХ СТАНКОВ
5.1. Назначение и основные типы направляющих
Направляющие должны обеспечивать точность перемещения движения или положения рабочего органа станка в статическом состоянии, быть жесткими, долговечными, обладать хорошими демпфирующими свойствами.
Встанках получили применение направляющие с различным характером трения: направляющие смешанного трения, жидкостного трения, аэростатические и направляющие качения.
Направляющие смешанного трения характеризуются высоким и непостоянным по величине трением. Существенную разницу для этих направляющих составляет значение силы трения покоя (силы трогания) по сравнению с трением движения, которое, в свою очередь, сильно зависит от скорости скольжения.
Значительное трение в направляющих смешанного трения вызывает износ и снижение долговечности деталей. Главные достоинства направляющих смешанного трения – высокая контактная жесткость и хорошие демпфирующие свойства.
Наиболее целесообразная область применения направляющих смешанного трения – универсальные станки с ручным управлением.
Направляющие жидкостного трения используются в станках в ос-
новном в виде гидростатических направляющих, так как для создания гидродинамического эффекта скорости движения, как правило, недостаточны. Жидкостное трение в гидростатических направляющих устраняет потерю устойчивости и возможность скачкообразного движения при малых скоростях, они обеспечивают высокую чувствительность при позиционировании и отработке малых перемещений.
Внаправляющих жидкостного трения отсутствует износ, и долговечность их практически не ограничена.
Высокое демпфирование в направляющих обеспечивает высокое качество поверхности при окончательной обработке деталей.
Недостатки направляющих жидкостного трения связаны с необходимостью использования сложной системы циркуляции, сбора и тщательной очистки масла, а также с трудностями фиксации узла станка после его перестановки в заданную позицию. Жесткость направляющих жидкостного трения ниже жесткости направляющих других типов.
Целесообразная область применения направляющих жидкостного трения – станки с высокими требованиями к точности и шероховатости поверхностей обрабатываемых деталей.
91
Аэростатические направляющие имеют значительно меньшее тре-
ние при движении по сравнению с направляющими жидкостного трения. При прекращении подачи воздуха обеспечивается надежная фиксация подвижного узла. Аэростатическим направляющим не требуется циркуляционная система подачи воздуха.
К недостаткам аэростатических направляющих относится их склонность к автоколебаниям, небольшая грузоподъемность, невысокая надежность.
Применяются аэростатические направляющие для точного позиционирования слабо нагруженных узлов станков.
Направляющие качения обладают малым трением и износом, а при условии надежной защиты от загрязнений обеспечивают высокую долговечность, высокую контактную жесткость, особенно роликовые направляющие. Недостатками направляющих качения являются высокая чувствительность к загрязнениям и погрешностям изготовления, высокая стоимость.
Направляющие качения применяют в обрабатывающих центрах сверлильно-фрезерно-расточной группы, станках с ЧПУ высокой точности малых и средних размеров, круглошлифовальных, бесцентровошлифовальных станках.
Формы направляющих прямолинейного движения в станках следующие: прямоугольные (плоские), треугольные (призматические), трапециевидные (ласточкин хвост) и цилиндрические. Каждая из этих форм может быть в виде охватываемых и охватывающих направляющих (рис. 5.1). Часто используют сочетания направляющих различной формы. Например, одна из направляющих выполнена прямоугольной, а другая треугольной или в виде половины трапециевидной формы.
Прямоугольные направляющие просты по форме, технологичны при изготовлении и сборке. В охватываемом варианте исполнения эти направляющие, как и все другие формы, плохо удерживают смазку, а в охватывающем варианте хорошо удерживают смазку, но нуждаются в надежной защите от загрязнений. Для регулировки зазоров требуются планки или клинья. Прямоугольные охватываемые направляющие применяются для поперечин, стоек, в протяжных, тяжелых токарных и агрегатных станках.
Треугольные направляющие в изготовлении сложнее прямоугольных, они обладают свойством автоматического выбора зазоров под действием собственного веса узла. Область применения охватываемых направляющих – станины токарных, револьверных, координатнорасточных станков. Охватывающими направляющими снабжают станины продольно-строгальных станков.
92
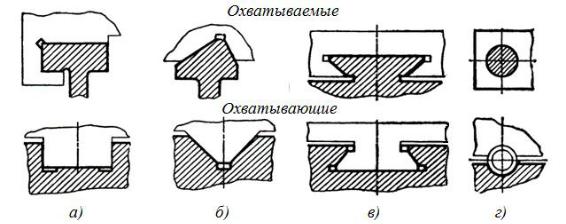
Рис. 5.1. Основные формы направляющих:
а – прямоугольные; б – треугольные; в – трапециевидные; г – цилиндрические
Трапециевидные направляющие имеют малые габариты по высоте, регулируются одним клином и планкой. Эти направляющие сложны в изготовлении, плохо работают при большом опрокидывающем моменте, в них возникают большие силы трения. Охватываемые направляющие используют в салазках суппортов токарных станков, охватывающие – для столов фрезерных станков, станин поперечно-строгальных станков.
Цилиндрические направляющие охватываемого типа имеют низкую жесткость, их применяют в основном при малой длине хода. При охватывающем варианте у этих направляющих сложно изготовить полукруглые пазы.
5.2. Направляющие смешанного трения
5.2.1. Материалы направляющих
Материалы, применяемые для направляющих смешанного трения, должны обладать высокой износостойкостью. Коэффициент трения движения необходимо иметь низкий и малозависящий от скорости движения, коэффициент трения покоя также должен быть низкий.
Направляющие неподвижной детали целесообразно изготовлять из более твердого и износостойкого материала по сравнению с материалом для направляющих подвижной детали.
Направляющие их серого чугуна. Чугунные направляющие из серо-
го чугуна, выполненные за одно целое с базовой деталью, наиболее просты и дешевы, но при интенсивной работе не обеспечивают необходимой долговечности. Износостойкость чугунных направляющих прецизионных станков повышают легированием материала станин или накладных планок никелем, хромом, молибденом. С этой же целью
93
производят поверхностную закалку одной из сопряженных поверхностей до 48…53 HRCэ с нагревом токами высокой частоты или газопламенным методом, а также применяют объемную закалку планок из легированного чугуна.
Износостойкость чугунных направляющих можно повысить применением специальных покрытий. Хромирование направляющих (слой хрома толщиной 25…30 мкм обеспечивает твердость направляющей до 62…72 HRCэ) повышает износостойкость в 4–5 раз по сравнению со стальными закаленными направляющими.
Пару чугун-чугун рекомендуется использовать для направляющих станков, выполняющих легкие работы, хорошо защищенных от загрязнений, с удовлетворительным смазыванием, для неответственных направляющих.
Направляющие из стали. Накладные направляющие имеют вид массивных планок прямоугольной и треугольной форм. Их рабочая поверхность должна обладать высокой износостойкостью при абразивном изнашивании. Поэтому твердость поверхности должна быть не менее 58 HRCэ. Для этих целей рекомендуется сталь 18ХГТ, упрочняемая цементацией и последующей объемной закалкой, сталь 8ХФ, подвергаемая закалке с индукционным нагревом, сталь ШХ15СГ с объемной закалкой. Для направляющих станков высокой точности рекомендуется азотируемые стали 30Х3МФ и 38ХМЮА.
Стальные направляющие рекомендуются для станков с числовым программным управлением, а также для легких и средних универсальных.
Накладные направляющие крепят к базовой детали по всей их длине. При механическом креплении винтами или креплении клеем необходимо предусматривать надежную фиксацию центрирующими выступами в поперечном направлении. Примеры конструкций накладных направляющих приведены на рис. 5.2, а–и.
Направляющие из наполненного фторопласта. Наполненный фто-
ропласт – это полимерный материал с наполнителем из бронзы, кокса, графита, дисульфида молибдена, играющий роль смазочного материала.
Наполненный фторопласт Ф4К15М5-Л-ЭА в виде ленты толщиной 1,7 мм с помощью эпоксидной смолы наклеивают на направляющие стола, суппорта, салазок. Коэффициент трения в направляющих из наполненного фторопласта в паре с чугуном или закаленной сталью составляет 0,04…0,6 и в области низких скоростей скольжения мало изменяется. Для таких направляющих характерны малая сила трения, высокая износостойкость, достаточная контактная жесткость. Направляющие из
94
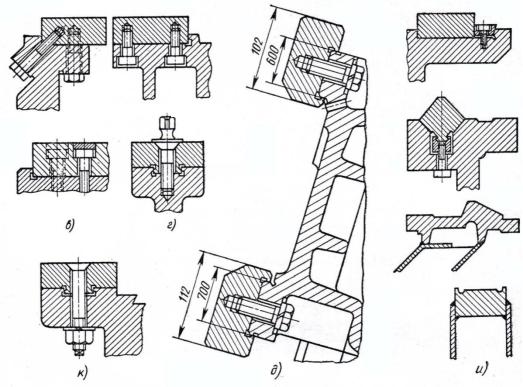
наполненного фторопласта применяют в станках с ЧПУ, тяжелых и высокоточных.
Конструкция накладной направляющей из наполненного фторопласта приведена на рис. 5.3.
е)
а) б)
ж)
в) |
|
г) |
|
|
|
з)
к) |
|
д) |
|
и) |
|
|
|
|
|
Рис. 5.2. Конструкции накладных направляющих
Лента 1 помещается в углубление, обработанное на направляющей стола 2 (см. рис. 5.3, б). Для фиксации ленты и повышения прочности крепления ее концов к обоим торцам стола больших габаритов приклеивают текстолитовые планки 3, которые дополнительно крепят винтами 4. Если планки не предусмотрены, расстояние от конца приклеенной накладки до торца стола должно составлять 5 мм (рис. 5.3, в). Для защиты боковых кромок направляющих от смазочного масла и охлаждающей жидкости используют антифрикционные пастообразные эпоксидные компаунды (см. рис. 5.3, г). Смазочные канавки на горизонтальных направляющих из наполненного фторопласта выполняют тех же конфигураций, что и на чугунных. Чаще всего используют поперечные канавки с подводом масла в каждую из них (см. рис. 5.3, а). Ширину канавки в выбирают в зависимости от ширины направляющей с:
с, мм |
20..30 |
30…40 |
40…60 |
60…100 |
100…200 |
200…300 |
в, мм |
4 |
6 |
8 |
10 |
18 |
25 |
95
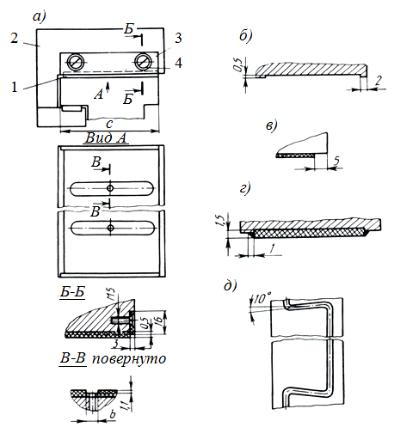
Рис. 5.3. Конструкции накладных направляющих из наполненного фторопласта
На направляющих узлов, перемещающихся вертикально, смазочную канавку изготавливают S-образной формы (см. рис. 5.3, д); с целью лучшего удержания масла поперечные ее участки делают с небольшим наклоном.
5.2.2.Расчет направляющих
Врезультате расчета находят размеры направляющих, удовлетворяющие критериям износостойкости и жесткости. По требованию износостойкости ограничивают допустимые давления на рабочих гранях направляющих, а по требованию жесткости лимитируют контактные деформации. Давления на рабочих поверхностях направляющих определяют приближенным методом, справедливым для тех случаев, когда собственная жесткость сопряженных базовых деталей существенно больше контактной жесткости направляющих. При этом предполагают, что по длине направляющих давление в контакте изменяется линейно,
апо ширине остается постоянным.
Методику расчета направляющих на износостойкость рассмотрим применительно к прямоугольным направляющим. Ширина их рабочих граней на рис. 5.4 обозначена буквами а, b, с, расстояние между середи-
96
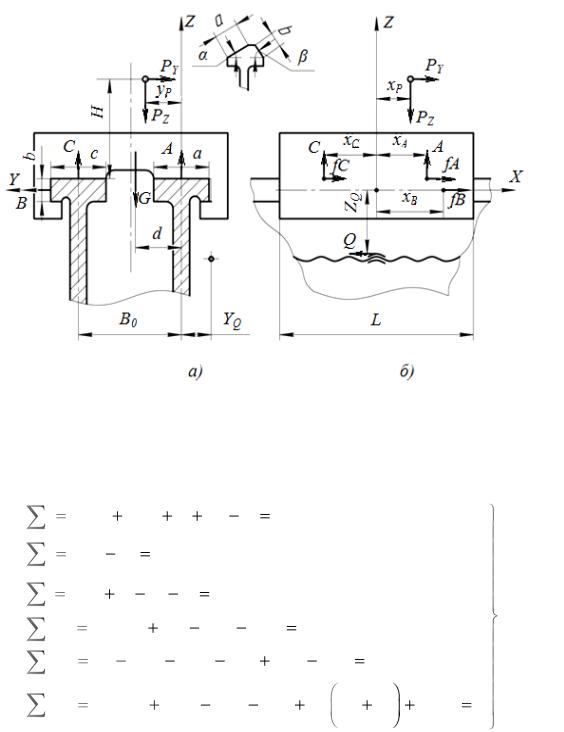
нами граней – буквой В0, длина стола – L. Начало координат выбрано так, чтобы ось Z делила пополам ширину а направляющей и длину L стола.
Расчетную схему изображают для подвижного узла при действии на него всех сил: составляющих силы резания, массы узла, тяговой силы, реакций на рабочих гранях направляющих и соответствующих сил трения.
Рис. 5.4. Расчетная схема направляющих смешанного трения
По расчетной схеме и выбранной системе координат составляют уравнения равновесия подвижного узла (рис. 5.4, а) и привода с ходовым винтом (рис. 5.4, б).
|
0; Px |
f ( A B C) Q 0; |
|
|
|
|
(5.1) |
|||||
x |
|
|
|
|
|
|||||||
|
|
|
|
|
|
|
|
|
|
|
||
y |
0; B |
Py |
0; |
|
|
|
|
|
|
|
||
|
|
|
|
|
|
|
|
|
|
|
||
z |
0; A |
C |
Pz G |
0; |
|
|
|
|
|
|
||
|
|
|
|
|
|
|
|
|
|
|
||
M x |
0; Pz yp |
Gd CB0 Py H 0; |
|
|
|
|
||||||
M y |
0; |
Px H Pz xp |
Cxa |
AxA |
QzQ |
0; |
|
|
||||
M y |
0; Px yp |
Py xp |
QyQ |
BxB |
fB B0 |
|
C |
fCB0 |
0. |
|||
|
|
|||||||||||
2 |
||||||||||||
|
|
|
|
|
|
|
|
|
|
В системе уравнений семь неизвестных A, B, C, xA, xB, xC, Q.
97
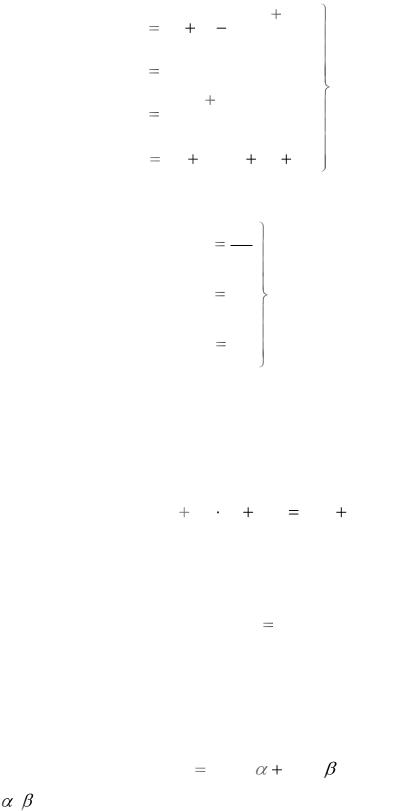
Из первых четырех уравнений определяем реакции на гранях направляющих и тяговую силу:
A |
PZ G |
|
PZ yp |
Gd |
; |
|
|
|
B0 |
|
|||
|
|
|
|
|
|
|
B |
PY ; |
|
|
|
|
|
C |
PZ yp |
Gd |
; |
|
(5.2) |
|
|
|
|
|
|
||
B0 |
|
|
|
|
||
|
|
|
|
|
|
Q PX f PZ PY G .
Реакции на гранях направляющих позволяют определить величину средних давлений:
A PA aL ;
P |
B |
; |
(5.3) |
|
|
|
|||
B |
bL |
|
||
|
|
|||
P |
C |
. |
|
|
|
|
|||
C |
cL |
|
||
|
|
Для определения максимальных значений давлений необходимо предварительно найти координаты равнодействующей xA, xB, xC. Для этого к оставшимся неиспользованными двум последним уравнениям равновесия составляют дополнительное уравнение перемещений. Предполагаем, что момент внешних сил относительно оси Y равен моменту от реакций в направляющих:
PZ xp PX H Qza AxA Cxc . |
(5.4) |
А также считаем, что момент внешних сил распределяется между двумя направляющими пропорционально их жесткости, т. е пропорционально ширине:
AxA |
|
a |
|
|
|
|
|
. |
(5.5) |
CxC |
c |
Полученное уравнение (5.5) вместе с двумя уравнениями равновесия позволяет определить координаты xA, xB, xC. Если одна из направляющих треугольная, то ее заменяют в уравнении (5.5) плоской призматической направляющей с приведенной шириной
d a cos2 bcos , (5.6)
где , – углы наклона рабочих граней треугольной направляющей.
98
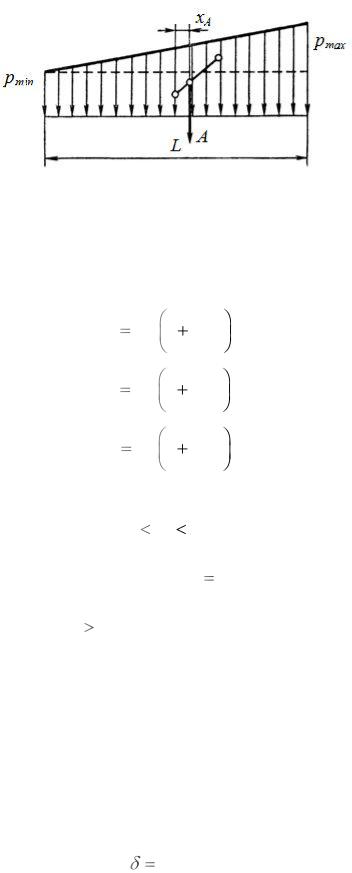
Рис. 5.5. Распределение давлений по длине рабочей поверхности направляющих
Максимальные давления (рис 5.5) на рабочих гранях направляющих определяют по формуле, связывающей давления с равнодействующей и координатой ее приложения,
|
p |
|
|
|
A |
|
|
1 |
|
|
6xA |
; |
(5.7) |
||||||
|
|
|
|
|
|
|
|
|
|
|
|||||||||
|
max A |
|
aL |
|
|
L |
|
|
|
|
|
|
|||||||
|
|
|
|
|
|
|
|
|
|
|
|
|
|||||||
|
pmax B |
|
B |
|
1 |
|
|
6xB |
|
; |
(5.8) |
||||||||
|
|
|
|
|
|
L |
|
||||||||||||
|
|
|
|
|
bL |
|
|
|
|
|
|
|
|
||||||
|
pmax C |
|
C |
1 |
|
|
6xC |
|
|
. |
(5.9) |
||||||||
|
|
|
|
|
L |
|
|||||||||||||
|
|
|
|
|
cL |
|
|
|
|
|
|
|
|
||||||
Если в формуле (5.7) xA = 0, то распределение давлений вдоль на- |
|||||||||||||||||||
правляющей равномерное. При 0 |
xA |
|
|
L |
получается трапецеидальный |
||||||||||||||
6 |
|||||||||||||||||||
|
|
|
|
|
|
|
|
|
|
|
|
|
|
|
|
||||
закон распределения давлений, а при |
xA |
|
1 |
|
давления распределяются |
||||||||||||||
|
6 |
|
|||||||||||||||||
|
|
|
|
|
|
|
|
|
|
|
|
|
|
|
|||||
по треугольнику. Когда |
xA |
1 |
, |
рабочая грань направляющей нагружена |
|||||||||||||||
6 |
|||||||||||||||||||
|
|
|
|
|
|
|
|
|
|
|
|
|
|
|
|
|
|
не по всей длине, а нагрузка действует на нижнюю планку.
Считается, что износостойкость направляющих будет достаточной, когда при малой скорости скольжения максимальное давление не выше 2,5…3 МПа, при большой скорости – не выше 1…1,2 МПа. Допустимое среднее давление равно половине допустимого максимального, для направляющих прецизионных и тяжелых станков – 0,1…0,2 МПа.
Расчет направляющих на жесткость включает определение контактных деформаций их рабочих граней. Предполагается, что деформа-
ции пропорциональны давлениям р на гранях: |
|
kp , |
(5.10) |
99
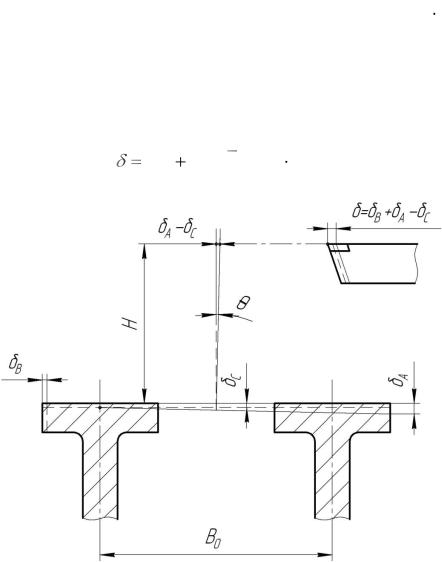
где k – коэффициент контактной податливости, который устанавливают экспериментально или ориентировочно принимают k = 10 мкм мм2/Н.
Контактные деформации приводят к точке приложения сил резания (рис. 5.6) и учитывают по тем направлениям, которые влияют на точность обработки. Поперечное смещение инструмента относительно детали (в направлении оси Y) образуется за счет поперечного и углового перемещений подвижного узла.
kp |
|
k |
pA pC |
Н мкм, |
(5.11) |
|
B |
B0 |
|||||
|
|
|
|
|||
|
|
|
|
|
Рис. 5.6. Расчетная схема жесткости направляющих
Упругие перемещения на направляющих входят как составляющая часть в общее упругое перемещение всей несущей системы и лимитируют их требования к точности обработки.
5.3. Гидродинамические направляющие
Создание жидкостного трения, основанного на гидродинамическом эффекте, в направляющих прямолинейного и кругового движений возможно только при достаточно больших скоростях в приводах главного движения.
Гидродинамические направляющие имеют клиновые скосы и поперечные канавки для их разделения (см. рис. 5.7).
100