
Детали машин / 2-я часть
.pdf
Значение среднего окружного модуля
Вычисленные значения
Средние делительные диаметры шестерни и колеса
Внешние диаметры шестерни и колеса (по вершинам зубьев)
Окружная скорость на среднем делительном диаметре
Следовательно, по ГОСТ 1643 – 81 передача выполнена по 8-й степени точности (согласно таблице 2.6).
Проверочный расчет Расчет на контактную выносливость рабочих поверхностей зубьев
Условие контактной прочности рабочих поверхностей зубьев
где - расчетное контактное напряжение, МПа;
– коэффициент, учитывающий форму зубьев;
- коэффициент, учитывающий механические свойства материала зубчатых колес ;
коэффициент, учитывающий суммарную длину контактных линий
- исходная расчетная окружная сила, отнесенная к среднему диаметру шестерни при расчете на контактную выносливость, Н;
- коэффициент нагрузки.
Для прямозубой некорригированной передачи стальными зубчатыми колесами имеем и
;
~ 77 ~
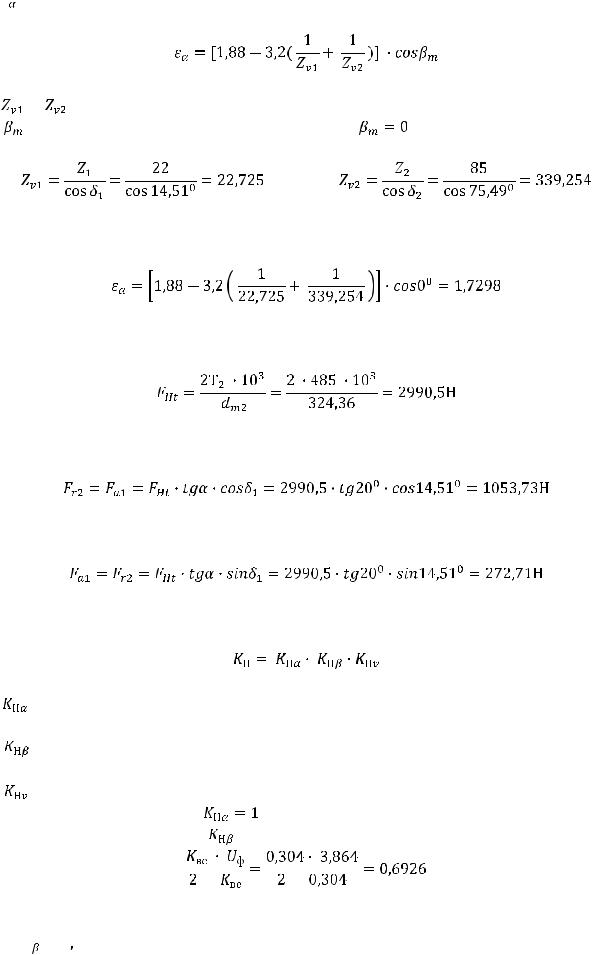
где - коэффициент торцового перекрытия
где |
и |
|
эквивалентные числа зубьев шестерни и колеса; |
|
|
||||
|
- угол наклона зубьев. Для прямозубых передач |
. |
Тогда получаем
Силы, действующие в зацеплении:
-окружная
-радиальная для шестерни, равная осевой для колеса
-осевая для шестерни, равная радиальной для колеса
где - угол зацепления.
где |
|
|
коэффициент, учитывающий распределение нагрузки между зубьями, при расчете на |
||||||||
|
|
||||||||||
контактную прочность. |
|
|
|
|
|
|
|
||||
|
|
- коэффициент, учитывающий неравномерность распределения нагрузки по ширине |
|||||||||
венца конического колеса, при расчете на контактную прочность. |
|||||||||||
|
- коэффициент, учитывающий динамическую нагрузку, возникающую в зацеплении. |
||||||||||
|
Для прямозубой передачи |
|
|
|
|
|
|
|
|||
|
Для выбора коэффициента |
|
уточняем отношение |
||||||||
|
|
|
|
|
|
|
|
|
|
|
|
|
|
|
|
|
|
|
|
|
|
|
|
При твердости рабочих поверхностей зубьев НВ ≤ 350 и роликовых опорах валов принимаем
~ 78 ~
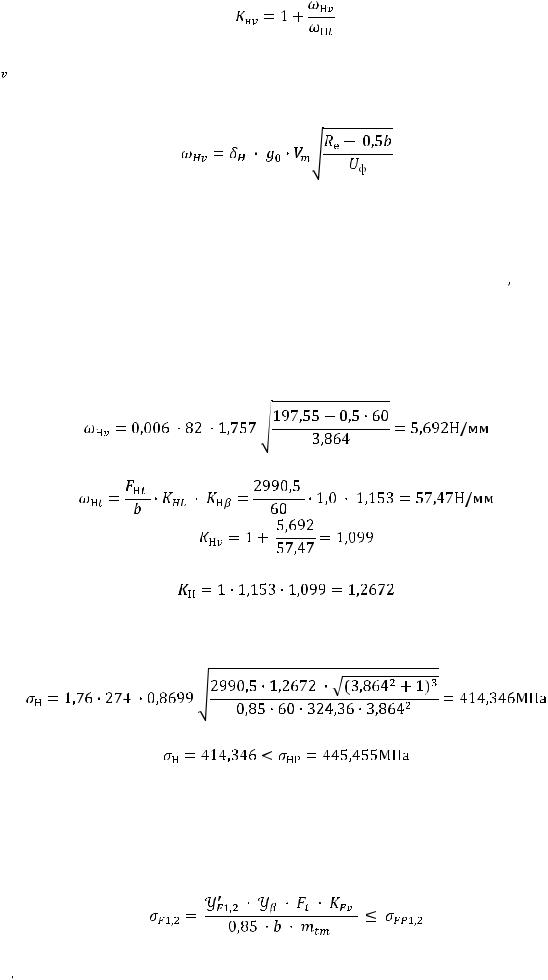
где - удельная окружная динамическая сила, Н/мм;
- удельная расчетная окружная сила, Н/мм.
где – коэффициент, учитывающий влияние для вида зубчатой передачи и модификации профиля головки зуба;
- коэффициент, учитывающий влияние разности шагов в зацеплении шестерни и колеса. Принимаем зубья прямыми без модификации. Тогда при НВ ≤ 350
(приложе-
ние 2)
Для конической передачи коэффициент выбирают со сдвигом на одну графу грубее по степени точности в сравнении с цилиндрической передачей. Принимаем по приложению 3 значение
Действительные контактные напряжения
Условие прочности выполнено.
Расчет зубьев на выносливость при изгибе
Условие прочности имеет вид
где - действительные напряжения изгиба материала шестерни и колеса МПа;
~ 79 ~
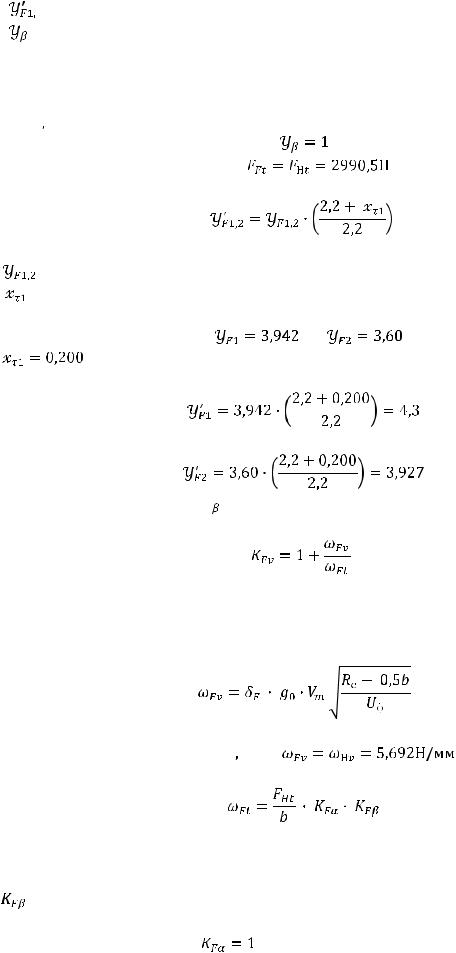
- коэффициент, учитывающий форму зуба шестерни и колеса;
- коэффициент, учитывающий наклон зубьев;
- исходная расчетная окружная сила, отнесенная к среднему диаметру шестерни при расчете на изгиб;
- коэффициент, учитывающий динамическую нагрузку при расчете на изгиб;
- допускаемое напряжение изгиба для материала шестерни и колеса, МПа.
Для прямозубой конической передачи |
. |
При расчете на изгиб принимают |
|
где |
- коэффициент формы зуба шестерни и колеса; |
|
|
|
- коэффициент толщины зуба шестерни. |
|
|
|
Коэффициент формы принимают по эквивалентному числу зубьев. В рассматриваемом |
||
случае по таблице 2.9 принимаем |
и |
. Тогда по таблице 2.16 принима- |
|
ем |
. |
|
|
|
Следовательно |
|
|
|
|
|
|
Для прямозубой передачи = 1,0
где - удельная окружная динамическая сила при расчете на изгиб, Н/мм;
- удельная расчетная окружная сила при расчете на изгиб, Н/мм.
;
где - коэффициент, учитывающий распределение нагрузки между зубьями при расчете на изгиб;
- коэффициент, учитывающий распределение нагрузки по ширине венца конического
колеса. |
|
Для прямозубой передачи |
. |
При выбранных ранее роликовых опорах валов, НВ ≤ 350 и величине найденного отноше-
~ 80 ~
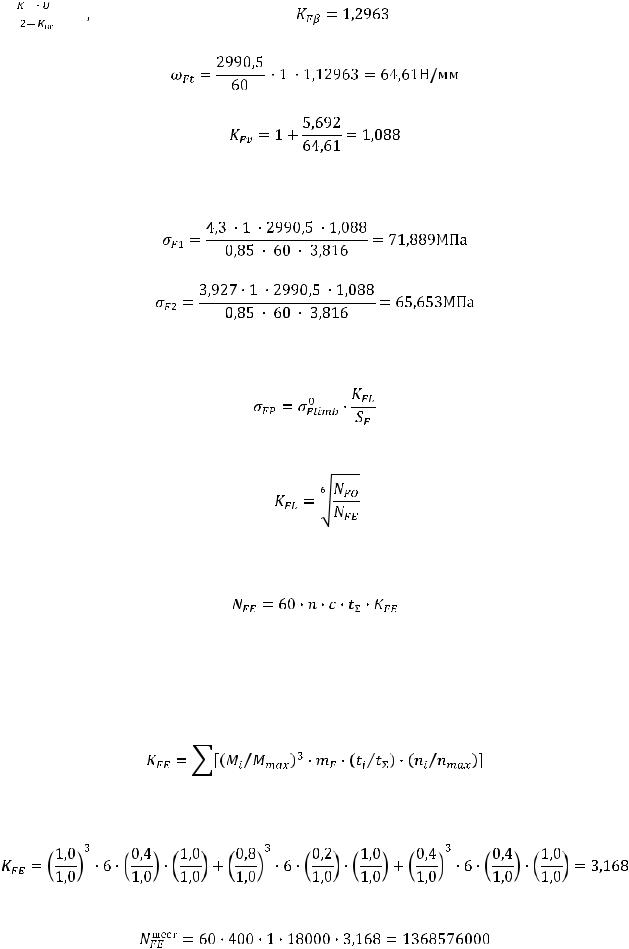
ния по таблице 2.14 имеем
Тогда получаем
Допускаемые напряжения находим по формуле
где KFL - коэффициент долговечности
где NFO - базовое число циклов нагружения; для всех сталей ;
где n - частота вращения, мин-1; nшест = 400 мин-1 и nкол = 100 мин-1. с = 1 - число колѐс, находящихся в зацеплении;
= 18000 - продолжительность работы передачи в расчѐтный срок службы, час; КFE - дополнительный множитель для эквивалентной циклической долговечности.
где mF = 6 - для сталей нормальной прочности.
Тогда
~ 81 ~
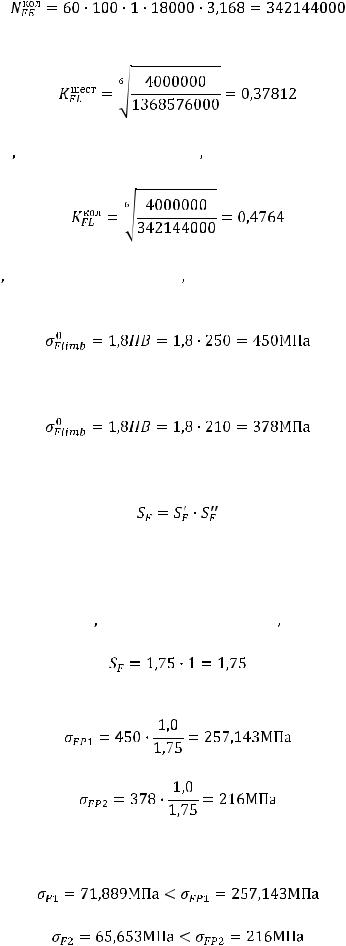
В итоге получаем
Так как , то принимаем
Так как , то принимаем
Для шестерни по таблице 2.13
Для колеса по таблице 2.13
Коэффициент безопасности находим по формуле
где - коэффициент, учитывающий нестабильность свойств материала зубчатого колеса и ответственность передачи, принимаем
(таблица 2.13);
- коэффициент, учитывающий способ получения заготовки зубчатого колеса:
(для штамповок и поковок);
;
Принимаем . Тогда
Допускаемые напряжения
Условие прочности выполнено.
~ 82 ~
Расчет закрытой червячной передачи
Червячную передачу применяют, когда геометрические оси валов пере-
крещиваются в пространстве (обычно под прямым углом). Передача состоит из червяка и червячного колеса. По профилю вдоль оси червяки бывают архимедо-
вы, эвольвентные и конволютные; по форме поверхности, на которой образуется резьба, – цилиндрические и глобоидные. Передачи с глобоидными червяками об-
ладают повышенной нагрузочной способностью, но в изготовлении и монтаже значительно сложнее, чем передачи с цилиндрическими червяками. В курсовом проектировании рассматриваются только передачи с цилиндрическим архимедо-
вым червяком, который имеет в осевом сечении витка прямолинейный профиль равнобедренной трапеции, а в торцовом сечении витки очерчены архимедовой спиралью. Движение в червячной передаче осуществляется по принципу винто-
вой пары – при движении витки червяка скользят по зубьям колеса.
Большая скорость скольжения, неблагоприятные условия смазки в червяч-
ных передачах служат причиной пониженного КПД, повышенного износа и склонности к заеданию. Поэтому материалы червячной пары должны обладать антифрикционными свойствами, износостойкостью и пониженным сопротивле-
нием к заеданию.
Венец червячного колеса изготовляют преимущественно из бронзы, реже из чугуна. При скоростях скольжения 2…5м/с рекомендуется применять более доступные по сравнению с оловянно-фосфористыми безоловянные бронзы (на-
пример, БрАЖ9-4), которые обладают повышенными механическими характери-
стиками, но имеют пониженные противозадирные свойства. Применение червяч-
ных колес из серого чугуна также лимитируется заеданием и допускается только для тихоходных малонагруженных передач.
Наилучшее качество работы червячной передачи обеспечивают червяки,
изготовленные как из цементируемых сталей (20Х, 18ХГТ) с твердостью термо-
обработки НRC 58…63, так и среднеуглеродистых сталей (45; 40ХН) с поверхно-
стной закалкой до твердости НRC 50…55. С повышением твердости рабочих по-
верхностей витков сопротивление заеданию увеличивается.
~ 83 ~
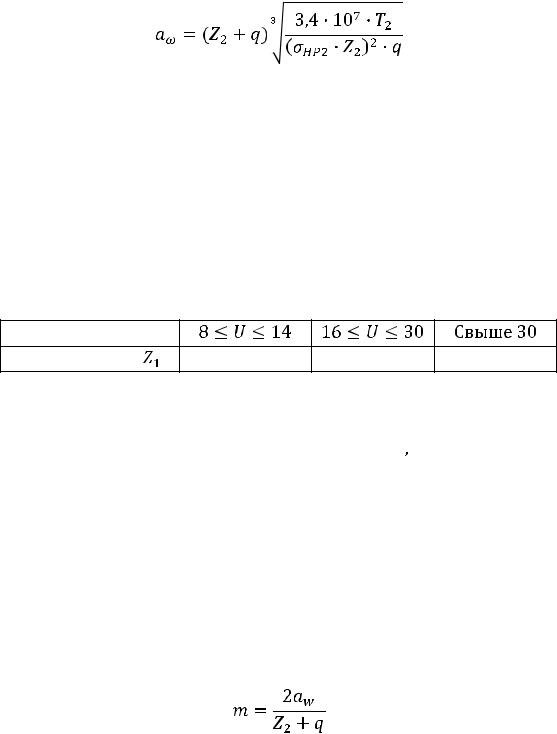
1. Определяем главный параметр – межосевое расстояние из условия кон-
тактной выносливости
где – число зубьев червячного колеса; зависит от числа заходов червяка
и передаточного числа U и определяется по таблице 2.17;
q – коэффициент диаметра червяка;
– вращающий момент на тихоходном валу редуктора, Нм;
допускаемое контактное напряжение материала червячного колеса, со-
ответствующее эквивалентному числу циклов перемены напряжений. NHE, MПа.
Таблица 2.17 – Число витков червяка
Передаточное число |
|
|
|
Число заходов |
4 |
2 |
1 |
Для обеспечения необходимой жесткости червяка рекомендуется прини-
мать значение коэффициента диаметра червяка с округлением до стандартного ближайшего значения из ряда: 8 – 10 – 12,5 – 16 – 20.
2. Полученное расчетное значение межосевого расстояния округляем до стандартного ближайшего из ряда: 80 – 100 – 125 – 140 – 160 – 180 – 200 – 225 –
250 – 280 – 315 – 355 – 400 – 450 – 500мм (жирным шрифтом выделены значения второго ряда).
3.Определяем осевой модуль зацепления
иокругляем его до стандартного значения по таблице 2.18.
Таблица 2.18 – Значения модулей червячных передач (ГОСТ 2144-76)
1-й ряд |
1,0 |
2,0 |
2,5 |
3,15 |
4,0 |
5,0 |
6,3 |
8,0 |
10,0 |
12,5 |
16 |
20 |
2-й ряд |
1,5 |
3,0 |
3,5 |
6,0 |
7,0 |
12,0 |
--- |
--- |
--- |
--- |
--- |
--- |
|
|
|
|
|
~ 84 ~ |
|
|
|
|
|
|
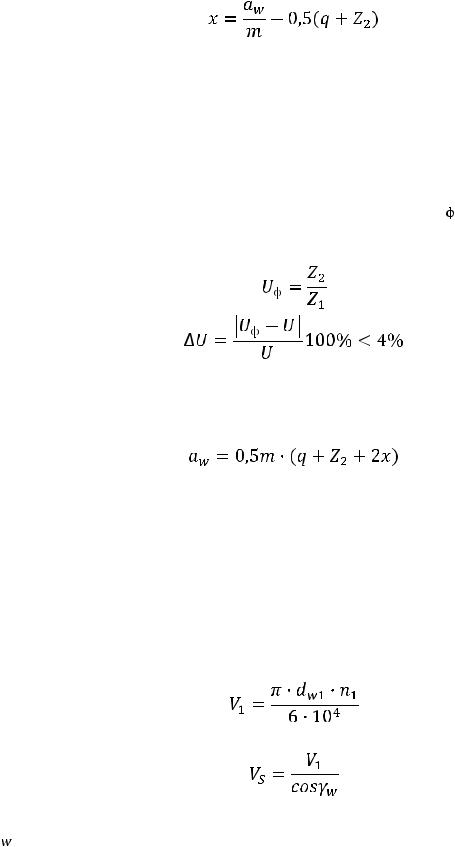
4. Для вписывания в стандартное межосевое расстояние, что облегчает унификацию корпусных деталей, червячные передачи выполняют со смещением.
Коэффициент смещения определяем по формуле
По условию неподрезания и незаострения зубьев колеса значение смеще-
ния допускается в пределах . Если это условие не выполняется, то следует варьировать значениями
. При этом
изменяется на 1…2 зуба, не превышая допустимого отклонения от передаточного числа.
5. Рассчитываем фактическое передаточное число и проверяем его от-
клонение от заданного :
6.Определяем фактическое значение межосевого расстояния
7.Определяем основные геометрические размеры передачи. При корриги-
ровании исполнительные размеры червяка не изменяются; у червячного колеса делительный и начальный диаметры совпадают, а изменяются диаметры вершин и впадин (см. пример расчета).
8. Находим окружную скорость червяка и скорость скольжения
где - начальный угол подъема линии витка червяка, град
~ 85 ~
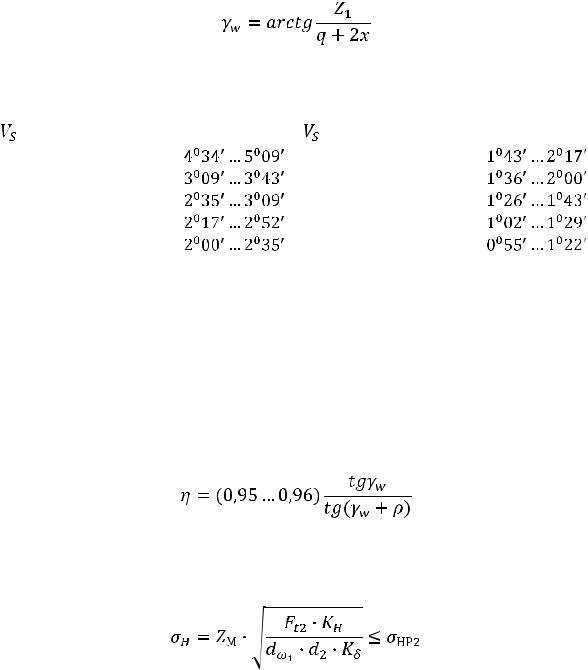
|
Таблица 2.19 – Зависимость коэффициента трения f |
и угла трения ρ от скоро- |
||||||
сти скольжения (червяк стальной, колесо из бронзы) |
|
|
|
|||||
|
, м/с |
f |
ρ |
, м/с |
f |
|
ρ |
|
|
0,1 |
0,080…0,090 |
|
2,5 |
0,030…0,040 |
|
|
|
|
0,5 |
0,055…0,065 |
|
3,0 |
0,028…0,035 |
|
|
|
|
1,0 |
0,045…0,055 |
|
4,0 |
0,023…0,030 |
|
|
|
|
1,5 |
0,040…0,050 |
|
7,0 |
0,018…0,026 |
|
|
|
|
2,0 |
0,035…0,045 |
|
10,0 |
0,016…0,024 |
|
|
9. По найденной скорости скольжения определяем приведенный угол тре-
ния. Он определяется интерполированием в зависимости от скорости скольжения
по таблице 2.19.
10. Определяем КПД редуктора с учетом потерь в опорах, потерь на раз-
брызгивание и перемешивание масла
11. Проверяем червячное колесо на контактную выносливость по формуле
где действительные контактные напряжения в зацеплении, МПа;
коэффициент, зависящий от контактирующих материалов червячной па-
ры и угла зацепления; для некоррегированного зацепления в зависимости от ма-
териалов контактирующих пар коэффициент принимает значение: сталь-бронза
= 380МПа1/2 и сталь – чугун
= 410МПа1/2;
окружная сила на червячном колесе, Н;
коэффициент нагрузки;
коэффициент, учитывающий условный угол обхвата червяка колесом.
~ 86 ~