
УМК РТ
.pdf3.2.5. Конструктивные покрытия печатных плат
Конструктивные покрытия обеспечивают стабильность электриче- ских, механических и других параметров ПП. Покрытия могут быть метал- лические и неметаллические (табл. 3.4).
|
|
|
Таблица 3.4 |
|
|
|
Характеристики конструктивных покрытий |
||
|
|
|
||
Материал |
Толщина, мкм |
Назначение покрытия |
||
покрытия |
||||
|
|
|||
Сплав Розе |
1,5…3 |
Защита от коррозии, обеспечение паяемости |
||
Сплав |
олово- |
9…15 |
Защита от коррозии, обеспечение паяемости |
|
свинец |
|
|
|
|
Серебро |
|
6…12 |
Улучшение электрической проводимости |
|
Золото |
и его |
0,5…3,0 |
Улучшение электрической проводимости, сниже- |
|
сплавы |
|
|
ние переходного сопротивление, повышение изно- |
|
|
|
|
соустойчивости |
|
Палладий |
1…1,5 |
Снижение переходного сопротивления, повыше- |
||
|
|
|
ние износоустойчивости контактов переключате- |
|
|
|
|
лей |
|
Никель |
|
3…6 |
Защита от коррозии, повышение износоустойчи- |
|
|
|
|
вости контактов переключателей |
|
Медь |
|
25…30 |
Обеспечение электрических параметров соедине- |
|
|
|
|
ния |
Наибольшее распространение получили покрытия на основе олова и свинца, например, О-С(66)12 опл. Кроме того, применяется покрытие сплавами олова и висмута или никеля, например О-Ви(99,8)9 или Н3.0-Ви(99,8)6, а также никелевое покрытие НЗ или Н5.
Кроме контактных площадок, предназначенных для пайки, на печат- ных платах могут находиться поверхности, обеспечивающие холодный контакт. В первую очередь это относится к соединителям непосредствен- ного контактирования (например, СНП 15-96). Предъявляемые требования к таким площадкам: стабильное низкое переходное сопротивление и высо- кая износоустойчивость. В качестве многослойного покрытия использует- ся такое, в верхнем слое которого – золото или палладий, например НЗ, ЗлО,25-3,00 или СрЗ, Пд 0,25-1,00. Кроме того, иногда встречается хими- ческое золочение - Хим. Зл-0,2.
Неметаллические конструктивные покрытия (эпоксидные смолы, эмали, оксидные пленки) используют для защиты печатных проводников и поверхности основания печатной платы от воздействия припоя, элементов проводящего рисунка от замыкания навесными элементами, от влаги при
71
эксплуатации. В простейшем случае плата после монтажа всех элементов и промывки покрывается лаком (одним или несколькими слоями). Лак нано- сится методами окунания, полива или распыления, и под ним оказываются не только все проводники, но и элементы, что не всегда желательно. Неко- торые элементы не допускают лакировки, например соединители, различ- ные лепестки, контакты и ряд микросхем. При окунании лак попадает во все щели и зазоры, в которых он после полимеризации образует сгустки, причиняющие (из-за усадок) механические повреждения, так что в процес- се конструирования необходимо предусматривать зазоры, обеспечиваю- щие удаление остатков жидкого лака (в производстве для этого применяет- ся центрифугирование). При любых способах нанесения лак проникает по капиллярам во внутренние полости соединителей и выводит их из строя. Из-за сложностей технологического порядка от лакировки отказываются и защищают печатные платы масками.
Вотличие от лакировки маска не обеспечивает полной защиты всей платы, но снижение общей стоимости производства является главным ар- гументом в пользу последнего варианта, тем более что при использовании защитной маски решается ряд других задач (например, она является технологической маской при нанесении гальванического покрытия).
Вкачестве материала защитных масок используются различные ди- электрические покрытия на основе эпоксидных смол, сухого пленочного ре- зиста (СПФ-защита), холодные эмали, оксидные пленки и др. Для изготовле- ния защитных покрытий применяются материалы фирм DuPont (Франция), MacDerm (Великобритания) и др.
Тема 3.3 ПЕРСПЕКТИВЫ РАЗВИТИЯ И МЕТОДЫ ДИАГНОСТИКИ
ПЕЧАТНЫХ ПЛАТ
3.3.1. Особенности поверхностного монтажа
Дальнейшее развитие техники печатного монтажа связано с широ- ким внедрением поверхностного монтажа. Отличительная особенность технологии монтажа на поверхность – использование безвыводных эле- ментов (без традиционных проволочных или ленточных выводов). Выво- ды у таких элементов заменены металлизированными поверхностями. Ес- ли все-таки выводы имеются, то формуются так, чтобы элементы допус- кали установку на поверхность платы. Размеры элементов, компонуемых
72
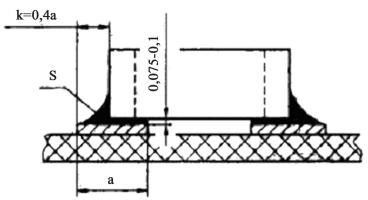
на поверхности, на один – два порядка меньше соответствующих анало- гов в традиционном исполнении.
Технологии пайки элементов условно можно разделить на два направления: пайка волной и пайка в печи. Если ориентироваться на пайку в печи, то следует использовать компоненты, способные выдер- живать кратковременный нагрев до температуры 280 ° С в течение 30 с. В месте пайки должно находиться строго дозированное количество припоя, который наносится на требуемое место с помощью специальных установок или посредством паяльной маски (трафарета). Паяльная паста, наносимая на контактные площадки, представляет собой механическую смесь мелкодиспергированного стандартного припоя (микрочастиц или микросфер) со связующим составом, в который вводятся различные добавки, предохраняющие расплавленный припой от окисления и обеспечивающие смачиваемость мест пайки (флюсы), а также блескообразующиеЗатемна платуи тустанавливаются.д. , и временно закрепляются элемен- ты, которые должны быть припаяны. Тяжелые элементы крепятся механи- чески (зиг-замками или отгибанием выводов) либо приклеиваются быст- ротвердеющим клеем. Легкие элементы (а это большинство чип-элемен- тов) удерживаются на печатной плате за счет адгезии паяльной пасты.
Далее плата подвергается кратковременному нагреву (как правило, ступенчатому) в специальных печах или конвейерных установках, где ре- жим нагрева (пайки) строго регламентирован. В печах происходит плавле- ние припоя и одновременная пайка всех элементов. После плавления часть припоя затекает под элемент и образует каплю на открытой части контакт- ной площадки. На рис. 3.13 изображено поперечное сечение места пайки и основные его размеры.
Рис. 3.13. Поперечное сечение места пайки
73
Короткое время нагрева и строгое соблюдение температурного режима обеспечивают сохранность печатной платы и элементов.
При пайке волной приклейка всех чип-элементов обязательна, иначе волна их просто смоет.
Элементы, которые по тем или иным причинам нельзя нагревать та- ким способом, следует паять отдельно на заключительном этапе (напри- мер, вручную).
3.3.2.Контроль качества и диагностика плат
Сразвитием и усложнением конструкций ПП и МПП возрастает сложность ТП, потребность в более эффективных методах и средствах контроля. Основными мерами повышения качества ПП и МПП являются: организация входного контроля материалов, межоперационный контроль, выходной контроль качества изделий. Основными видами выходного кон- троля ПП являются:
1.контроль внешнего вида;
2.инструментальный контроль геометрических параметров и оцен- ка точности выполнения отдельных элементов, совмещения слоев;
3.проверка металлизации отверстий и их устойчивости к токовой
нагрузке;
4.определение целостности токопроводящих цепей и сопротивле- ния изоляции.
Весьма важным является тщательный контроль наиболее ответст- венных операций ТП (травление, металлизация, склеивание и др.), которые оказывают влияние на все остальные операции и автоматизация процесса контроля.
Классификацию методов контроля можно провести по следующим признакам:
1.по физической сути метода:
оптический;
рентгеновский;
тепловой;
электрофизический;
электрический;
радиотехнический;
металлографический;
радиационный;
ультразвуковой;
74
2.по видам связи с контролируемым объектом:
контактные;
бесконтактные;
3.по характеру воздействия на платы:
разрушающие,
неразрушающие;
4.по степени определения дефектов:
контроль работоспособности (явный дефект),
диагностический (скрытый дефект),
прогнозирующий.
Оптический метод контроля прост и нагляден, имеет высокую раз- решающую способность. Недостаток его в субъективности и низкой про- изводительности. Используются микроскопы МБС-2, МИИ-4, МРР-2Р, растровый электронный микроскоп МРЭМИ-2 и др.
Рентгеновский метод применяется для контроля токопроводяших цепей МПП и подразделяется на рентгенотелевизионный, стереорентгено- графии и томографии. Наибольшее распространение получил рентгеноте- левизионный метод с использованием рентгенотелевизионных микроско- пов МТР-1, МТР-3, МТР-4. Данный способ позволяет выявлять характер, вид и местонахождение дефектов. Однако он обладает недостаточной раз- решающей способностью для МПП и низкой производительностью кон- троля. Стереорентгенография применяется при выявлении разрывов пе- чатных проводников после прессования и в готовой плате. Томография об- ладает возможностью контроля межслойных изображений, его применяют для послойного контроля токопроводящих цепей МПП.
Тепловой контроль токопроводящих цепей МПП основан на измере- нии градиента температуры в местах локализации дефекта при нагреве, ко- торый осуществляется за счет пропускания тока через контролируемую цепь. С помощью данного метода можно обнаружить следующие дефекты печатного монтажа: пористость металлизации, короткое замыкание, утоне- ние (подтравливание) проводников, пониженное сопротивление изоляции.
75
Раздел 4
УЗЛЫ И БЛОКИ С ПЛЕНОЧНЫМИ ЭЛЕМЕНТАМИ
Тема 4.1 ПОЛУЧЕНИЕ ПЛЕНОК НЕВАКУУМНОЙ ТЕХНОЛОГИЕЙ
4.1.1. Узлы и блоки с пленочными элементами. Схема процесса получения пленок невакуумной технологией
Производство как дискретных (отдельных) полупроводниковых при- боров, так и интегральных микросхем (ИМС) в основном базируется на одних и тех же технологических процессах (эпитаксии, фотолитографии, травлении, диффузии, нанесении пленок и др.). При изготовлении всех ви- дов полупроводниковых приборов и ИМС в том или ином объеме исполь- зуется технологический процесс нанесения тонких пленок в вакууме - тон- копленочная технология.
Основными конструктивными и схемными элементами и компонен- тами как пленочных, так и толстопленочных гибридных микросхем являют- ся: диэлектрическая подложка; пленочные резисторы, конденсаторы, про- водники и контактные площадки, а также распределенные пленочные RC-, LC- и RLС-структуры; навесные бескорпусные полупроводниковые прибо- ры и микросхемы; навесные миниатюрные пассивные компоненты; корпус.
Сущность процесса изготовления толстопленочных интегральных микросхем (рис. 4.1) заключается в нанесении на керамическую подложку специальных проводниковых, резистивных или диэлектрических паст пу- тем продавливания их через сетчатый трафарет с помощью ракеля и в по- следующей термообработке (вжигании) этих паст, в результате чего обра- зуется прочная монолитная структура.
Проводниковые и резистивные пасты состоят из порошков металлов и их окислов, а также содержат порошки низкоплавких стекол (стеклян- ную фритту). В диэлектрических пастах металлические порошки отсутст- вуют. Для придания пастам необходимой вязкости, их замешивают на ор- ганических связующих веществах (этилцеллюлоза, вазелины).
При вжигании паст стеклянная фритта размягчается, обволакивает и затем при охлаждении связывает проводящие частицы проводниковых и резистивных паст. Диэлектрические пасты после термообработки пред- ставляют однородные стекловидные пленки.
76
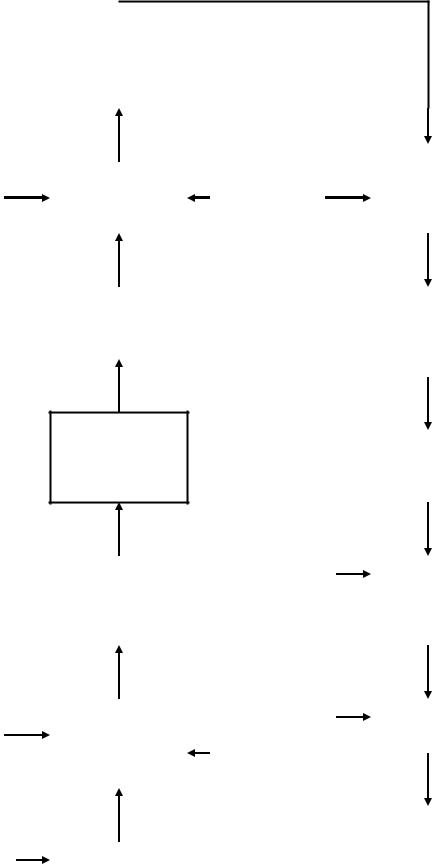
|
|
|
|
|
|
|
|
|
резисторов |
|
|
|
|
|
|
Вжигание |
|
|
|
|
дляПастарезисторов |
|
|
||||
|
|
|
|
|
|
|
|
|
|
|
Трафарет |
резисторовдля |
|
|
резисторов |
|
||||
|
|
|
|
|
||
|
|
Нанесение |
|
|
|
|
|
|
|
|
|
|
|
|
|
|
|
|
|
|
|
|
обкладок |
|
|
|
|
|
|
верхних |
|
|
|
|
|
|
Вжигание |
|
|
|
пасты диэлектрической Вжигание
|
|
|
|
иобкладок |
|
|
|
|
|
|
|
проводников |
|
|
|
|
полупроводниковдляПаста диэлектрикови |
|
|
|
Трафарет |
проводниковдля диэлектрикови |
|
|
|
|
Вжигание |
|
|||
|
|
|
|
|
|
|
|
|
|
|
|
|
|
|
|
|
|
|
|
|
|
|
|
|
|
|
|
|
|
|
|
|
|
|
|
идиэлектриков |
|
|
|
|
|
|
|
проводников |
|
|
|
|
|
|
|
Нанесение |
|
|
|
|
|
|
|
|
|
|
|
|
|
|
|
|
|
|
|
|
|
|
|
|
|
|
|
Подложка |
|
Очисткаподложки |
|
|
|
||
|
|
|
|
|
|
|
|
Выводы |
|
|
(штырьков) |
|
|
выводов |
|
|
|
Установка |
|
|
|
|
|
|
|
|
|
|
|
|
|
|
|
|
проводников |
|
|
|
выводов |
|
|
|
Лужение |
|
|
|
|
|
|
|
|
|
|
|
|
элементы |
|
резисторов |
|
|
Подгонка |
||
|
|
|
|
Активные |
|
|
|
|
|
||
|
элементов |
||
|
|
|
|
|
|
|
активных |
|
|
||
|
|
|
Монтаж |
|
|
|
|
Колпачок, компаунд |
|
|
|
|
Герметизация |
||
|
|
|
|
|
|
|
|
|
|
|
|
|
|
|
|
|
|
|
параметров |
|
|
|
Контроль |
|
|
|
|
процесса изготовления толстопленочных ГИМС |
77 |
Рис. 4.1. Схема технологического |
|
4.1.2. Исходные материалы для пленок: проводников, резисторов и диэлектриков
Проводниковые пасты изготовляются на основе золота, золота – пла- тины, золота – палладия, палладия – серебра, индия, рения.
Толщина слоя проводника на основе композиции палладий - серебро составляет 10 - 25 мкм. Минимальная ширина (длина) проводника колеб- лется в пределах 0,15 - 0,20 мм при нанесении пасты на керамику и 0,20 - 0,30 мм при нанесении на слой диэлектрика. Минимальное расстояние между проводниковыми элементами 0,05 - 0,20 мм в зависимости от рецеп- турного состава пасты. Сопротивление квадрата проводниковой пленки на основе данной композиции колеблется в пределах 0,05 - 0,5 Ом/□.
Характеристики проводящих, резистивных и диэлектрических паст приведены в табл. 4.1.
|
|
|
|
|
|
Таблица 4.1 |
|
|
Характеристики проводящих паст |
|
|||
|
|
|
|
|
|
|
Обозначение |
Толщина |
|
Поверхностное |
|
|
|
|
удельное сопротивление |
|
Область применения |
|||
пасты |
слоя, мкм |
|
|
|||
|
|
|
ρs, Ом/□, не более |
|
|
|
ПП-1 |
10 – 20 |
|
0,05 |
Для |
изготовления |
проводни- |
|
|
|
|
ков, нижних обкладок конденсато- |
||
|
|
|
|
ров и контактных площадок пер- |
||
|
|
|
|
вого слоя с размерами сторон эле- |
||
|
|
|
|
ментов не менее 0,2 мм |
|
|
ПП-2 |
15 – 20 |
|
5,0 |
Для изготовления верхних об- |
||
|
|
|
|
кладок конденсаторов, не смачи- |
||
|
|
|
|
ваемых припоем |
|
|
ПП-3 |
15 – 25 |
|
0,05 |
Для |
изготовления |
проводни- |
|
|
|
|
ков, нижних обкладок конденсато- |
||
|
|
|
|
ров и контактных площадок под |
||
|
|
|
|
монтаж |
навесных компонентов с |
|
|
|
|
|
жесткими выводами |
|
|
ПП-4 |
15 – 25 |
|
0,05 |
Для изготовления проводящих |
||
|
|
|
|
элементов, наносимых на слой ди- |
||
|
|
|
|
электрика |
|
Резистивные пасты обычно изготовляются на основе композиций: се- ребро – палладий – окись палладия, серебро - окись рутения, висмут – руте- ний, рутений – иридий, платина – окись иридия. Опробованы также компо- зиции типа кадмий - алюминий – бор - окись молибдена. Толщина резистив- ных пленок после вжигания составляет примерно 20 мкм.
Резистивные пасты, приготавливаемые на основе композиции палла- дий – серебро, обеспечивают номинальные сопротивления резисторов от
78
25 Ом до 1 МОм. Сопротивление квадрата резистивной пленки соответст-
вует следующему ряду значений: 5, 100, 500, 1000, 3000, 6000, 20 000, 50 000 Ом/□. Температурный коэффициент сопротивления подобных паст не превышает 800 · 10-6 1/град в интервале температур – 60... + 125 ° С.
Диэлектрические пленки в толстопленочных микросхемах применя- ются в качестве диэлектриков конденсаторов, межслойной изоляции, за- щитных слоев.
Диэлектрические пасты для конденсаторов изготовляются на основе смеси керамических материалов и флюсов. Толщина пленки после терми- ческой обработки составляет 40 – 60 мкм.
Используя пленки, обеспечивающие удельную емкость С0 = 3700 пФ/см2, изготовляют конденсаторы с номинальной емкостью от 500 до 300 пФ. Пленки с С0 = 10 000 пФ/см2 позволяют производить конденсаторы в диа- пазоне от 100 до 2500 пФ. Погрешность номинальной емкости конденсато- ров обычно составляет ± 15 %. Пробивное напряжение не менее 150 В.
Величина диэлектрической проницаемости для диэлектрических паст конденсаторов на основе композиции титанат бария – окись титана – окись алюминия – легкоплавкое стекло составляет от 10 до 2000.
4.1.3. Материалы подложек и подготовка поверхности
Для обеспечения заданных электрических параметров микросхем материал подложки должен обладать:
высоким коэффициентом теплопроводности для эффективной передачи тепла от тепловыделяющих элементов (резисторов, диодов, тран- зисторов) к корпусу;
высокой механической прочностью, обеспечивающей целост- ность подложки с нанесенными элементами как в процессе изготовления микросхемы (разделение на платы, термокомпрессия, пайка, установка платы в корпус и т. д.), так и при ее эксплуатации в условиях термоцикли- рования, термоударов и механических воздействий;
высокой химической инертностью к осаждаемым материалам для снижения временной нестабильности параметров пленочных элементов, обусловленной физико-химическими процессами на границе раздела плен- ка-подложка и проникновением ионов из подложки в пленку;
стойкостью к воздействию высокой температуры в процессах формирования элементов и установки навесных компонентов;
стойкостью к воздействию химических реактивов в процессе подготовки поверхности подложки перед нанесением пленок, при электро- химических обработках и химическом осаждении пленок;
79
способностью к хорошей механической обработке (полировке, резке).
Для изготовления подложек обычно используются керамические ма- териалы или стекла. Чаще всего употребляется керамика на основе 96%-ной поликристаллической окиси алюминия. Для мощных ИМС при- меняется также бериллиевая керамика, обладающая хорошей теплопро- водностью, но требующая особых мер обеспечения безопасности при об- работке вследствие ее токсичности.
Точность получаемого в процессе трафаретной печати рисунка мик- росхемы в значительной степени зависит от плоскостности поверхности подложки и ее шероховатости. Максимальная кривизна поверхности (мак- ронеровность) не должна превышать 4 мкм на 1 мм длины. Шероховатость (микронеровность) рабочей поверхности подложки должна быть не ниже восьмого класса (Rа = 0,32 - 0,63 мкм). Слишком малая шероховатость может приводить к ухудшению адгезии наносимых пленок. Большая ше- роховатость поверхности подложки снижает надежность тонкопленочных резисторов и конденсаторов, так как при наличии микронеровностей тол- щина резистивных и диэлектрических пленок становится неравномерной.
Размеры плат определяются конкретной конструкцией применяемых корпусов ИМС. Рекомендуются размеры 8×15 мм2, 10×16 мм2 и кратные им.
4.1.4. Особенности получения рабочих рисунков из паст
Нанесение паст можно производить двумя способами: бесконтакт- ным и контактным.
При бесконтактном способе подложку, на которую нужно нанести пасту, устанавливают под сетчатым трафаретом с некоторым зазором. Пас- ту подают поверх трафарета и передвижением ракеля через отверстия в трафарете переносят на подложку в виде столбиков, копирующих отвер- стия в сетке (см. рис. 3.4). Растекаясь, столбики соединяются, образуя та- кой же рисунок, как на трафарете. Сетчатые трафареты изготовляют из ка- прона, нейлона или нержавеющей стали.
Качество трафаретной печати зависит от скорости перемещения и давления ракеля, зазора между сетчатым трафаретом и платой, натяжения трафарета и свойств пасты. Необходимо строго соблюдать параллельность платы, трафарета и направления движения ракеля.
Для устранения неравномерности толщины резисторов рекомендует- ся составлять топологию так, чтобы все резисторы располагались по длине
80