
Проект_Маш_Пр-ва_КУРСОВОЙ ПРОЕКТ
.pdf2 . К УР С ОВ О Й ПР ОЕ К Т
Согласно ГОСТ 14004-83 коэффициент Кз.о=1 для массового производства; 1<Кз.о≤10 для крупносерийного; 10<Кз.о≤20 для среднесерийного; 20<Кз.о≤40 для мелкосерийного. Для единичного производства величина Кз.о не регламентируется.
При укрупненном проектировании для определения типа производства можно воспользоваться табл. 2.
|
|
|
|
|
Таблица 2 |
|
Примерное количество изделий, выпускаемых в течение года |
||||||
|
при различных типах производства |
|
||||
|
|
|
|
|
|
|
|
|
|
Тип производства |
|
||
Трудоемкость |
|
|
|
|
|
|
Единичное |
Мелко- |
Средне- |
Крупно- |
Массовое |
||
изделия, ч |
серийное |
серийное |
серийное |
|||
|
|
|||||
|
|
Количество изделий по годовой программе, шт. |
||||
|
|
|
|
|
|
|
Свыше 10 000 |
До 10 |
10–25 |
25–100 |
Свыше 100 |
– |
|
|
|
|
|
|
|
|
1 000–10 000 |
До 20 |
20–50 |
50–250 |
250–5 000 |
Св. 5 000 |
|
|
|
|
|
|
|
|
100–1 000 |
До 40 |
40–100 |
100–500 |
500–10 000 |
Св. 10 000 |
|
|
|
|
|
|
|
|
10–100 |
До 80 |
80–150 |
150–750 |
750–15 000 |
Св. 15 000 |
|
|
|
|
|
|
|
|
1–10 |
До 100 |
100–250 |
250–1 500 |
1 500–30 000 |
Св. 30 000 |
|
|
|
|
|
|
|
|
До 1 |
До 150 |
150–500 |
500–3 000 |
3 000–50 000 |
Св. 50 000 |
|
|
|
|
|
|
|
Обработка деталей в массовом и крупносерийном производствах осуществляется на непрерывно-поточных, а в среднесерийном – переменно-поточных и групповых линиях, такт выпуска которых определяется по формуле
t |
|
|
60FдmK н |
, мин, |
вып |
|
|||
|
|
П |
||
|
|
|
где Fд –действительный годовой фонд времени станка при работе в одну смену, ч; m – число рабочих смен в сутки; Кн – коэффициент, учитывающий затрату времени на организацию технологического процесса (переналадки с одного наименования детали на другое, подналадку оборудования и т.д., Кн=0,8…0,9); П – годовая программа выпуска изделий.
2.3.4. Намечается состав участков цеха [1, 17].
В зависимости от принятой схемы организации производства и характера выпускаемого изделия в состав цеха могут входить различные отделения и участки.
Вобщем случае в состав цеха входят:
1)производственные отделения и участки, к которым относятся отделения (участки) для непосредственного осуществления технологических процессов обработки деталей, сборки подузлов, узлов и общей сборки, а также окраски, испытания, консервации и упаковки готовых изделий;
Кначалу главы
Коглавлению
11

2 . К УР С ОВ О Й ПР ОЕ К Т
2)вспомогательные отделения и участки, где размещаются мастерские вспомогательного характера (для ремонта оборудования и технологической оснастки, заточки инструментов), контрольное отделение, цеховые склады (основных и вспомогательных материалов, заготовок, деталей, инструментов) и др.;
3)служебные помещения для технической части цеха и административнотехнического персонала;
4)бытовые помещения для размещения гардеробных, уборных, умывальных, душевых, курительных и др.
Необходимо наметить состав производственных и вспомогательных отделений, а также служебных и бытовых помещений для проектируемого цеха.
2.4.Расчет основных показателей механического отделения
2.4.1.Производится расчет потребного количества производственного оборудования механического отделения и разбивка его по видам.
Определение необходимого (расчетного) количества станков С для механических участков при укрупненном проектировании осуществляется по трудоемко-
сти годового выпуска изделий Ти, действительному фонду времени работы станка при работе в одну смену Fд и режима работы цеха (количества рабочих смен в сутки) m по следующей формуле:
С Ти , шт.
Fдm
С учетом среднего значения коэффициента загрузки оборудования ηз для различных типов производства (единичное, мелкосерийное ηз=0,8…0,9; среднесерийное ηз=0,75…0,85; крупносерийное, массовое ηз=0,65…0,75 [5]) принятое число станков S определится из соотношения
S |
Ти |
F m |
|
|
д з |
Если количество станков получается дробным, число округляется до целого в сторону увеличения.
Для слесарной доработки деталей в механическом цехе предусматривается слесарный участок. Число рабочих мест Sсл определяется в процентном отношении от количества принятых станков (Sсл ≈2 %).
Полученное количество оборудования разбивается по типам и типоразмерам в зависимости от характера изготавливаемой продукции [10]. В табл. 3 и 4 приведён примерный состав оборудования механических цехов автомобильного и станкостроительного заводов, а в табл. 5 – процентное соотношение различных типов станков в цехах механосборочного производства.
Кначалу главы
Коглавлению
12
2 . К УР С ОВ О Й ПР ОЕ К Т
Таблица 3
Примерный состав оборудования по отдельным механическим цехам автомобильных заводов, в % от общего количества станков
|
Производство гру- |
Производство гру- |
Производство |
||||||||||
|
зовых автомобилей |
зовых автомобилей |
легковых малолит- |
||||||||||
|
грузоподъемностью |
грузоподъемностью |
ражных автомоби- |
||||||||||
|
|
2…2,5 т |
|
|
4…4,5 т |
|
|
лей |
|
||||
|
|
|
|
|
|
|
|
|
|
|
|
|
|
Типы станков |
Цех двигателей |
|
Цех шасси |
|
Автоматный цех |
Цех двигателей |
|
Цех шасси и задних мостов |
|
Цех коробки передач |
Цех двигателей |
Цех шасси |
Автоматный цех |
|
|
|
|
|
|||||||||
|
|
|
|
|
|
|
|
|
|
|
|
|
|
Токарные |
24 |
|
27 |
|
59 |
22 |
|
26 |
|
24 |
20 |
27 |
53 |
|
|
|
|
|
|
|
|
|
|
|
|
|
|
Расточные |
4 |
|
3 |
|
1,5 |
3 |
|
2 |
|
0,4 |
3 |
2 |
1 |
|
|
|
|
|
|
|
|
|
|
|
|
|
|
Сверлильные |
17 |
|
21 |
|
10,5 |
22 |
|
20 |
|
17 |
27 |
22 |
15 |
|
|
|
|
|
|
|
|
|
|
|
|
|
|
Агрегатные |
7 |
|
10 |
|
8,5 |
9 |
|
13 |
|
3 |
10 |
5 |
2 |
|
|
|
|
|
|
|
|
|
|
|
|
|
|
Протяжные |
2 |
|
3 |
|
1 |
3 |
|
3 |
|
2 |
2 |
2 |
1 |
|
|
|
|
|
|
|
|
|
|
|
|
|
|
Фрезерные |
11 |
|
10 |
|
9 |
14 |
|
8 |
|
12 |
13 |
12 |
10 |
|
|
|
|
|
|
|
|
|
|
|
|
|
|
Строгальные |
0,5 |
|
– |
|
0,1 |
– |
|
– |
|
– |
– |
– |
1 |
и долбежные |
|
|
|
|
|||||||||
|
|
|
|
|
|
|
|
|
|
|
|
|
|
|
|
|
|
|
|
|
|
|
|
|
|
|
|
Зубообрабатывающие |
14 |
|
9 |
|
– |
5 |
|
13 |
|
24 |
4 |
16 |
– |
|
|
|
|
|
|
|
|
|
|
|
|
|
|
Шлифовальные |
20 |
|
16 |
|
8,4 |
21 |
|
12 |
|
17 |
20 |
13 |
8 |
и полировальные |
|
|
|
|
|||||||||
|
|
|
|
|
|
|
|
|
|
|
|
|
|
|
|
|
|
|
|
|
|
|
|
|
|
|
|
Резьбонарезные |
0,5 |
|
1 |
|
2 |
1 |
|
3 |
|
0,6 |
1 |
1 |
9 |
|
|
|
|
|
|
|
|
|
|
|
|
|
|
Удельное значение |
|
|
|
|
|
|
|
|
|
|
|
|
|
автоматов и полуав- |
|
|
|
|
|
|
|
|
|
|
|
|
|
томатов в составе ме- |
10 |
|
18 |
|
37 |
27 |
|
24 |
|
35 |
18 |
11 |
34 |
таллообрабатываю- |
|
|
|
|
|
|
|
|
|
|
|
|
|
щих станков |
|
|
|
|
|
|
|
|
|
|
|
|
|
|
|
|
|
|
|
|
|
|
|
|
|
|
|
Кначалу главы
Коглавлению
13
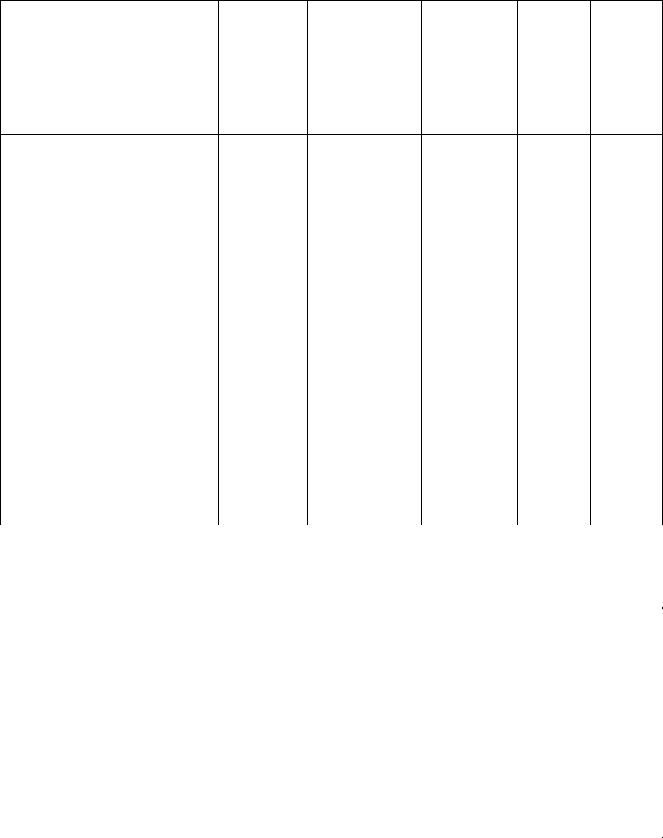
2 . К УР С ОВ О Й ПР ОЕ К Т
Таблица 4
Примерный состав оборудования механических цехов станкостроительных заводов, в % от общего количества станков
Заводтокарно- |
винторезн. и спец. агрегат- |
ныхстанков |
Заводпрецизионныхрезьбошлиф., червяч.- шлиф. и зубошлиф. станков |
Заводгоризонтальнои коор- динатно-рас- точныхстанков |
Заводтокарноревольверных станков |
Заводзубообрабатывающих станков |
Типы станков |
|
|
|
|
|
|
Токарно-винторезные |
|
21 |
12 |
16 |
12 |
18 |
||
|
|
|
|
|
|
|
|
|
Токарно-револьверные |
|
4 |
7 |
3 |
5 |
5 |
||
|
|
|
|
|
|
|
|
|
Токарные автоматы |
|
– |
1 |
– |
1 |
1 |
||
и полуавтоматы |
|
|||||||
|
|
|
|
|
|
|||
Карусельные |
|
2 |
1 |
1 |
1 |
2,5 |
||
|
|
|
|
|
|
|
|
|
Расточные |
|
6 |
5 |
7 |
6 |
6 |
||
|
|
|
|
|
|
|
|
|
Координатно-расточные |
|
2 |
– |
– |
– |
– |
||
|
|
|
|
|
|
|
|
|
Сверлильные |
|
10 |
6 |
5 |
11 |
5 |
||
|
|
|
|
|
|
|
|
|
Фрезерные |
|
15 |
13 |
13 |
14 |
11 |
||
|
|
|
|
|
|
|
|
|
Строгальные |
|
5 |
4 |
8 |
2 |
4 |
||
и долбежные |
|
|||||||
|
|
|
|
|
|
|||
Протяжные |
|
1 |
1 |
1 |
1 |
1 |
||
|
|
|
|
|
|
|
|
|
Шлифовальные |
|
12 |
22 |
13 |
13 |
12 |
||
|
|
|
|
|
|
|
|
|
Зубообрабатывающие |
|
6 |
6 |
9 |
6 |
10 |
||
|
|
|
|
|
|
|
||
Специальные, агрегатные |
15 |
21 |
22 |
25 |
23 |
|||
автоматы и полуавтоматы |
||||||||
|
|
|
|
|
||||
Отрезные |
|
1 |
1 |
2 |
3 |
1,5 |
||
|
|
|
|
|
|
|
|
|
|
|
|
|
|
|
|
Таблица 5 |
|
Процентное соотношение различных типов станков |
|
|||||||
в цехах механосборочного производства [5] |
|
|||||||
|
|
|
|
|
|
|||
|
|
Цех непоточного |
Цех поточного про- |
Цех поточного про- |
||||
Станки |
|
изводства со сред- |
изводства с боль- |
|||||
|
|
производства |
||||||
|
|
|
ним объемом вы- |
шим объемом вы- |
||||
|
|
|
|
|||||
|
|
|
|
|
|
|
|
|
Простые токарные |
|
|
12,6 |
|
7,5 |
|
3 |
|
Револьверные |
|
|
12 |
|
6,3 |
|
3,4 |
|
Многорезцовые |
|
|
1,2 |
|
11,3 |
|
7,6 |
|
одношпиндельные |
|
|
|
|
||||
|
|
|
|
|
|
|
||
Токарные автоматы |
|
|
|
|
|
|
|
|
и полуавтоматы |
|
|
0,5 |
|
2,6 |
|
8,1 |
|
многошпиндельные |
|
|
|
|
|
|
|
|
Строгальные |
|
|
7,2 |
|
– |
|
– |
Кначалу главы
Коглавлению
14
2 . К УР С ОВ О Й ПР ОЕ К Т
|
|
|
Окончание табл. 5 |
|
|
|
|
|
|
|
Цех непоточного |
Цех поточного про- |
Цех поточного про- |
|
Станки |
изводства со сред- |
изводства с боль- |
||
производства |
||||
|
ним объемом вы- |
шим объемом вы- |
||
|
|
|||
|
|
|
|
|
Горизонтально- |
|
|
|
|
и вертикально- |
14,2 |
10 |
5,7 |
|
фрезерные |
|
|
|
|
|
|
|
|
|
Протяжные верти- |
|
|
|
|
кальные и горизон- |
0,5 |
2 |
3,6 |
|
тальные |
|
|
|
|
|
|
|
|
|
Сверлильные |
|
|
|
|
и расточные одно- |
12,5 |
17 |
12 |
|
шпиндельные |
|
|
|
|
Агрегатно- |
– |
3 |
12,6 |
|
сверлильные |
||||
|
|
|
||
|
|
|
|
|
Автоматические |
– |
– |
1,6 |
|
линии |
||||
|
|
|
||
|
|
|
|
|
Круглошлифоваль- |
9 |
7,2 |
5,5 |
|
ные |
||||
|
|
|
||
Внутришлифоваль- |
6,6 |
2,7 |
1,6 |
|
ные |
||||
|
|
|
||
|
|
|
|
|
Прочие |
23,7 |
30,4 |
35,3 |
2.4.2. Производится расчет численности работающих в цехе [9, 11].
Состав и численность работающих в цехах механосборочного производства определяется характером производственного процесса и степенью его автоматизации, уровнем специализации вспомогательных служб и другими факторами.
Общее количество, участвующих в работе механосборочного цеха, состоит из: производственных (основных) рабочих, вспомогательных (подсобных) рабочих, инженерно-технических работников, счетно-конторского персонала (служащих) и младшего обслуживающего персонала.
Кпроизводственным рабочим относят станочников и наладчиков оборудования, слесарей, мойщиков и других рабочих, занятых непосредственно выполнением операций технологического процесса обработки заготовок и сборки машин.
Квспомогательным рабочим относят транспортных и складских рабочих цеха, рабочих вспомогательных служб цеха, операторов механизмов по уборке стружки
ипроизводственных помещений, рабочих-контролеров и др.
Ккатегории инженерно-технических работников (ИТР) относят руководителей цеха (начальник цеха, его заместители, начальники участков, отделений, мастера), а также инженеров-технологов, техников, экономистов, нормировщиков, диспетчеров, механиков, энергетиков и т.д.
Кначалу главы
Коглавлению
15
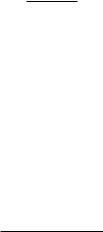
2 . К УР С ОВ О Й ПР ОЕ К Т
К служащим относят работников бухгалтерии, осуществляющих расчеты, относящиеся к данному цеху.
К младшему обслуживающему персоналу (МОП) относят операторов уборочных машин (уборщиков) административно-конторских и санитарно-бытовых помещений, работников цеховых и заводских хранилищ (архивов) технической документации и др.
2.4.2.1. В зависимости от суммарной станкоёмкости обработки определяется потребное количество производственных рабочих-станочников и в процентном отношении к нему количество слесарей механического отделения [11].
В поточно-массовом и поточно-серийном производстве число производственных рабочих определяется по количеству рабочих мест (станков), выполняющих определенную операцию, с учетом возможности многостаночного обслуживания.
Для единичного, мелкосерийного и среднесерийного производства применяется два способа определения численности производственных рабочих: по общей трудоемкости или по числу принятых станков.
При расчете по трудоёмкости (в человеко-часах) число рабочих станочников
Rст Ти ,
Fд.рSр
где Ти – трудоемкость годового выпуска изделий, ч; Fд.р – действительный годовой фонд времени работы рабочего, ч; Sр – количество станков, на которых может одновременно работать 1 рабочий (коэффициент многостаночности).
Величина коэффициента многостаночности составляет в среднем: 1,0…1,35 в единичном и мелкосерийном производстве, 1,3…1,5 – в среднесерийном, 1,9…2,2 – в крупносерийном и достигает 5 в поточно-массовом [17].
Расчет численности рабочих по принятому числу станков ведётся по формуле
Rст FдmS з.сКр , Fд.рSр
где ηз.с – среднее значение коэффициента загрузки станков; Кр – коэффициент, определяющий трудоемкость ручных работ (средняя величина Кр для массового и крупносерийного производства равна 1,02, для среднесерийного и мелкосерийно-
го – 1,05).
Помимо станочников определяется количество производственных рабочихслесарей Rсл, занятых на ручных работах. Оно принимается для массового и крупносерийного производства в размере 1–3 % от количества станочников (Rст),
адля единичного и среднесерийного 3–5 %.
2.4.2.2.Определяется потребное количество вспомогательных рабочих, инже- нерно-технических работников (ИТР), счетно-конторского персонала (служащих) и младшего обслуживающего персонала (МОП) механического отделения.
Кначалу главы
Коглавлению
16
2 . К УР С ОВ О Й ПР ОЕ К Т
При укрупненных расчетах количество вспомогательных рабочих определяется в процентном соотношении от численности производственных рабочих (табл. 6).
Таблица 6 Нормативы численности вспомогательных рабочих, ИТР и служащих [9, 11]
|
|
Вспомогатель- |
ИТР |
Служащие |
|
|
|
ные рабочие |
(% от числа ос- |
||
|
|
(% от числа про- |
|||
Цехи |
Тип производства |
(% от числа про- |
новных станков |
||
изводственных |
|||||
|
|
изводственных |
механического |
||
|
|
рабочих) |
|||
|
|
рабочих) |
цеха) |
||
|
|
|
|||
|
|
|
|
|
|
|
Массовое |
20–25 |
20–15 |
0,6–1,4 |
|
|
|
|
|
|
|
Механиче- |
Крупносерийное |
20–25 |
21–15 |
0,8–1,6 |
|
Среднесерийное |
20–25 |
22–16 |
1,1–1,9 |
||
ские, |
|
|
|
|
|
Мелкосерийное |
20–25 |
24–18 |
1,4–2,2 |
||
|
|||||
|
и единичное |
||||
|
|
|
|
||
|
|
|
|
|
|
в том чис- |
|
|
|
|
|
ле авто- |
|
|
|
|
|
матные и |
Крупносерийное и |
30–35 |
20–15 |
0,1–1,6 |
|
автомати- |
массовое |
||||
|
|
|
|||
зирован- |
|
|
|
|
|
ные |
|
|
|
|
Численность ИТР механических цехов определяется от числа основных станков цеха (см. табл. 6).
Количество служащих при укрупненных расчетах принимается в процентном отношении от числа производственных рабочих (см. табл.6).
Численность МОП определяют по нормам технологического проектирования: один человек на 500–600 м2 площади обслуживаемых помещений или 2–3 % от общего числа рабочих.
2.4.3. Подсчитывается размер производственной площади механического отделения с учетом площади, занимаемой верстаками слесарей.
При детальном проектировании цеха производственная площадь, занимаемая механическим отделением, определяется на основании разработанного плана расположения всего оборудования, рабочих мест, проездов, проходов и пр.
В случае укрупненного проектирования производственная площадь отделения определяется по удельной площади, приходящейся на 1 станок. В среднем она составляет: для малых станков 10–12, средних 15–25, крупных 25–70, особо крупных и уникальных станков тяжелого машиностроения 70–200 м2 на станок. Для линий по обработке корпусных деталей средняя площадь на станок составляет 16–25 м2, а для некоторых секций автоматических линий до 35 м2. Таким o6pазом, площадь, занимаемую станками можно подсчитать по формуле
Fст=ΣSc fc , м2,
Кначалу главы
Коглавлению
17
2 . К УР С ОВ О Й ПР ОЕ К Т
где Sc – принятое число станков данного типоразмера; fc – удельная производственная площадь, приходящаяся на 1 станок данного типоразмера.
Площадь слесарного участка определяется по следующей формуле:
Fсл=Sсл fсл , м2,
где Sсл – число рабочих мест ручной обработки; fcл – удельная площадь на 1 слесаря или рабочее место (при обработке мелких деталей 5–6, средних – 18– 25, крупных – 25–60 м2).
2.5.Расчет основных показателей сборочного отделения
2.5.1.Для сборочного отделения раздельно определяются необходимое количество стендов (верстаков) для стационарной сборки и количество рабочих мест на конвейерной сборке.
Сборка небольших узлов и сборочных единиц выполняется одним или несколькими рабочими. Если число сборочных операций не велико (не больше 8), сборка осуществляется на одном рабочем месте (стенде, верстаке). В этом случае число сборочных мест узловой сборки определяется по формуле
Мст |
Тс.у |
, |
|
Fд.сбmКп.рКз |
|||
|
|
где Тс.у – трудоемкость узловой сборки узлов на всю программу выпуска; Fд.сб – действительный годовой фонд времени работы рабочего места (стенда, верстака) при работе в одну смену, ч; m – число рабочих смен в сутки; Кп.р – коэффициент, учитывающий плотность работы (отношение числа работающих к числу рабочих мест); Кз – средний коэффициент загрузки слесарно-сборочных мест
(Кз≈0,8…0,85).
Значение коэффициента Kп.р для малых узлов (изделий) равно 1, для средних –
1,1…1,3, для крупных – 1,5…2,5.
В случае сборки узлов на конвейере число рабочих мест определяется по формуле
Мк.у |
Тсб 60 |
, |
|
tвып Кп.рКз.к |
|||
|
|
где Тсб – трудоемкость слесарных работ сборки одного узла, ч.
При поточной общей сборке на конвейере количество рабочих мест определяется по формуле
Мк |
Тс.к 60 |
, |
|
tвып Кп.рКз.к |
|||
|
|
Кначалу главы
Коглавлению
18

2 . К УР С ОВ О Й ПР ОЕ К Т
где Тс.к – трудоемкость конвейерной сборки одного изделия, ч; tвып – такт выпуска, мин; Кз.к – средний коэффициент загрузки сборочных мест на конвейере
(Кз.к≈0,8…0,85).
2.5.2. Раздельно подсчитывается потребное количество производственных ра- бочих-сборщиков для стационарной и конвейерной сборки.
Для стационарной сборки узлов (изделий) число рабочих сборщиков для сборки узлов на всю программу определяется по формуле
Rсл.ст Тс.у ,
Fд.р
где Тс.у – трудоемкость слесарно-сборочных работ на всю программу выпуска, ч; Fд.р – действительный годовой фонд времени рабочего, ч.
Число слесарей-сборщиков, работающих на конвейере общей сборки, определяется из соотношения:
Rсл.к То.сб , Fд.р
где То.сб – трудоемкость общей (конвейерной) сборки изделий на всю программу.
2.5.3. Определяется потребное количество вспомогательных рабочих сборочного отделения, младшего обслуживающего персонала, счетно-конторского персонала, инженерно-технических работников [11].
Количество вспомогательных рабочих в сборочном отделении определяется так же как и для механического отделения – в процентном отношении к производственным рабочим. В массовом производстве количество вспомогательных рабочих составляет 15…25 %, крупносерийном – 25…30 %, в среднесерийном и мелкосерийном – 25…40 % от числа производственных рабочих.
Инженерно-технические работники (ИТР), служащие и младший обслуживающий персонал (МОП), счетно-конторский персонал (СКП) определяются в процентном отношении к общему количеству рабочих: ИТР – 7…8 %, служа-
щие – 3…5 %, МОП – 2…3 %, СКП – 1,5…3 %.
Количество контролеров ОТК может быть принято в размере 5…7 % от количества рабочих сборщиков.
Для определения численности работающих в наибольшую смену Rнаиб можно воспользоваться следующей формулой:
R
Rнаиб Ксмен ,
где R – общее количество работающих; Ксмен – коэффициент сменности, равный отношению общего числа работающих к числу рабочих в наибольшую смену.
Кначалу главы
Коглавлению
19
2 . К УР С ОВ О Й ПР ОЕ К Т
В среднем Ксмен равен: для рабочих 1,8; для служащих 1,2. На участках поточ- но-массового производства и автоматических линиях производственные рабочие по сменам распределяются поровну.
|
2.5.4. На основе проведенных расчетов составляется сводная |
|
ведомость |
||||
на всех работающих в механическом и |
сборочном отделениях с разделением |
||||||
по сменам. Форма ведомости представлена в табл.7. |
|
|
|
|
|||
|
|
|
|
|
Таблица 7 |
||
|
|
Рабочий состав цеха |
|
|
|
|
|
|
|
|
|
|
|
|
|
|
|
Категория |
Обоснование |
Численность |
|||
№ |
|
по сменам, чел. |
|||||
|
работающих |
расчета |
|||||
|
|
I |
|
II |
III |
||
|
|
|
|
|
|||
|
|
Механическое отделение |
|
|
|
|
|
|
|
|
|
|
|
|
|
1 |
|
Станочники Rст |
Расчетная формула |
|
|
|
|
|
|
|
|
|
|
|
|
2 |
|
Слесари Rсл |
В % от Rст |
|
|
|
|
3 |
|
Всего основных Rо |
Rо=Rст+Rсл |
|
|
|
|
4 |
|
Вспомогательные рабочие Rв |
В % от Rо |
|
|
|
|
5 |
|
Младший обслуживающий персонал |
В % от (Rо+Rв) |
|
|
|
|
6 |
|
Инженерно-технические работники |
В % от числа станков |
|
|
|
|
|
|
|
|
|
|
|
|
7 |
|
Счетно-конторский персонал |
В % от Rо |
|
|
|
|
|
|
|
Итого: |
|
|
|
|
|
|
|
|
|
|
|
|
|
|
Сборочное отделение |
|
|
|
|
|
|
|
|
|
|
|
|
|
8 |
|
Слесари узловой сборки Rсл.ст |
Расчетная формула |
|
|
|
|
|
|
|
|
|
|
|
|
9 |
|
Слесари-сборщики на конвейере Rсл.к |
Расчетная формула |
|
|
|
|
10 |
|
Всего основных Rсл.о |
Rсл.о=Rсл.ст+Rсл.к |
|
|
|
|
|
|
|
|
|
|
|
|
11 |
|
Вспомогательные рабочие Rв |
В % от Rсл.о |
|
|
|
|
12 |
|
Младший обслуживающий персонал |
В % от (Rсл.о+Rв) |
|
|
|
|
13 |
|
Инженерно-технические работники |
В % от (Rсл.о+Rв) |
|
|
|
|
14 |
|
Счетно-конторский персонал |
В % от (Rсл.о+Rв) |
|
|
|
|
|
|
|
Итого: |
|
|
|
|
|
|
|
|
|
|
|
|
|
|
|
Всего работающих: |
|
|
|
|
|
|
|
|
|
|
|
|
2.5.5. По технико-экономическим показателям определяется общая и производственная площадь сборочного отделения.
Под производственной площадью сборочного цеха понимается та часть его общей площади, которая занята непосредственно для осуществления технологических процессов сборки изделия. В ее состав включаются площади для размещения оборудования (верстаки, стенды и т.д.), шкафов, стеллажей и другого производственного инвентаря; хранения запасов и заделов собираемых деталей; площади, занимаемые немагистральными проходами и проездами.
Кначалу главы
Коглавлению
20