
Режущий инструмент (часть2)
.pdf
Режущий инструмент. Конспект лекций |
64 |
|
Существенным недостатком этих фрез является низкая производительность и точность. Низкая производительность объясняется малым числом зубьев, консольным креплением, нерациональной геометрией. Низкая точность - по-
грешностями делительного механизма и искажением профиля при переточках.
Метод изготовления колес пальцевыми модульными фрезами, так же как
идисковыми, используется в условиях единичного и ремонтного производства.
Кконструктивным и геометрическим параметрам фрезы относится: диа-
метр фрезы (D), диаметр и длина посадочного цилиндра (dПЦ, h), размер под ключ
(S), длина фрезы (L), длина рабочей части (1) количество зубьев (Z), угол профиля фрезы (α), геометрические параметры режущего клина (углы γ и α), углы стружечной канавки (Θ и Θ1), радиус дна канавки (г).
|
6 |
|
|
|
0Å |
|
|
d1 |
|
|
Q1 =60Å |
|
|
|
|
|
|
|
h |
|
|
|
X |
|
|
|
L |
|
|
|
R |
|
6 |
|
l |
|
|
|
|
|
0 |
|
|
|
|
Å |
Í |
D |
|
|
Z=4...8 |
S |
Ï.Ö. |
d |
|
|
Q=20-30Å
K
Направление образования задних углов, т. е. направление затылования влияет на степень изменения нормальных задних углов и диаметральных размеров режущей части при переточках фрезы. При образовании задних углов в радиальном направлении при переточках фрезы получаются большие изменения толщины зубьев колеса. Они не могут быть компенсированы перемещением фрезы вдоль ее оси, так как при этом получаются большие искажения профиля зубьев колеса. Компенсация изменения диаметральных размеров рабочей части фрезы при ее переточках возможна у фрез с осевым направлением затылования за счет увеличения высоты впадины, но при этом методе затылования получаются малые значения нормальных задних углов на участках режущих кромок, обрабатывающих профиль зубьев у окружности впадин. Для получения достаточных нормальных задних углов и минимальных отклонений формы и размеров зубьев при переточках фрезы затылование производят под углом 10...150.
10.2.3 Зубодолбежные головки
Зубодолбежные головки применяют для одновременного нарезания всех зубьев цилиндрических и блочных шестерен на специальных станках в массовом производстве. Работают они методом фасонного копирования. Профиль резцов головки соответствует профилю впадины нарезаемого колеса. Поэтому такая головка предназначена только для нарезания колеса с определенным числом зубьев. В процессе работы головка неподвижна, а заготовка совершая воз- вратно-поступательное перемещение, осуществляя тем самым движение резания.
Зубодолбежные головки применяют в условиях массового производства.
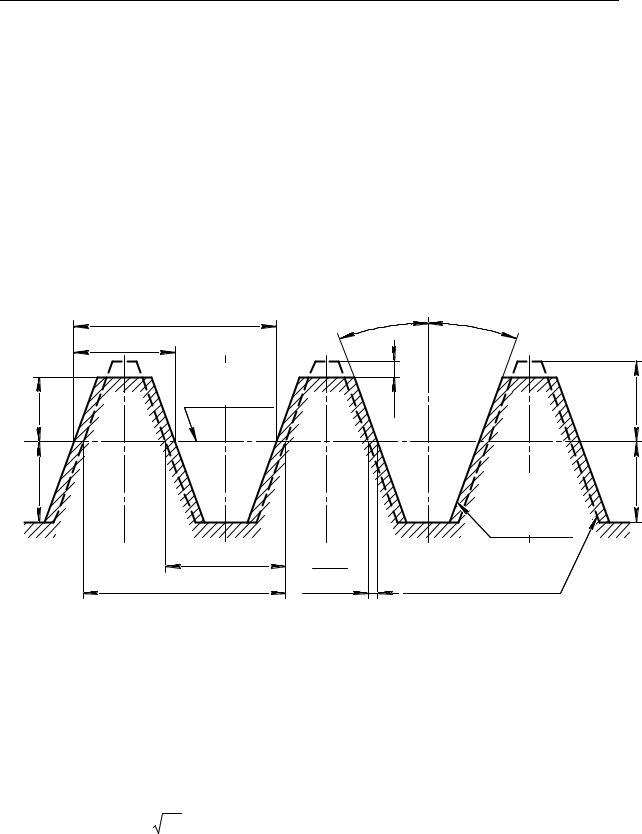
Режущий инструмент. Конспект лекций |
65 |
|
10.2 Инструменты, работающие с профилированием по методу обкатывания (огибания)
Особенностью кинематики и работы обкатных инструментов является наличие обкатного движения режущих кромок инструмента относительно обрабатываемых поверхностей заготовки. Это движение создает непрерывное изменение инструментальной поверхности, образуемой режущими кромками инструмента в процессе главного движения. Метод обкатывания позволяет нарезать зубья колес непрерывно при их плавном вращении вокруг своих осей. Вследствие этого повышается производительность и точность обработки. Кроме того, одним инструментом данного модуля можно нарезать колеса с любым числом зубьев.
|
P=pmn |
a |
a |
|
|
S=0,5P |
|
|
|
|
Начальная |
|
|
=1,25m |
=m |
прямая |
Ñè |
|
|
|
|
|||
a |
|
|
|
fè |
h |
|
|
|
h |
=1,25m |
|
|
Контур |
=1,25m |
|
|
зубчатой |
||
f |
|
|
aè |
|
h |
|
|
рейки |
h |
|
|
|
|
|
|
Sè |
DSàè |
Контур инструмен- |
|
|
Pè=Ð |
2 |
тальной рейки |
|
|
Инструментальная рейка лежит в основе образования исходной и произ- |
|||
водящей поверхностей. Параметры контура инструментальной рейки отлича- |
||||
ются от исходного контура рейки следующими элементами: |
|
1Высота ножки инструментальной рейки hfU больше высоты головки зубчатой рейки ha на величину Си = (0,25 ÷ 0,3) × mn. Это необходимо для того, чтобы исключить из процесса резания впадину инструментальной рейки, т. е. наружный диаметр колеса инструментальной рейкой не обрабатывается при зубонарезании.
2Толщина зуба инструментальной рейки Sи больше толщины зуба зубчатой
рейки S на ∆S ≈0,1 mn . Увеличение толщины зуба инструментальной рейки, не-
обходимо для утонения зуба нарезаемого колеса чтобы образовать боковой зазор у сопряженных колес с фланкированными зубьями. У нефланкированных колес этот зазор можно получить смещением инструмента к центру колеса.
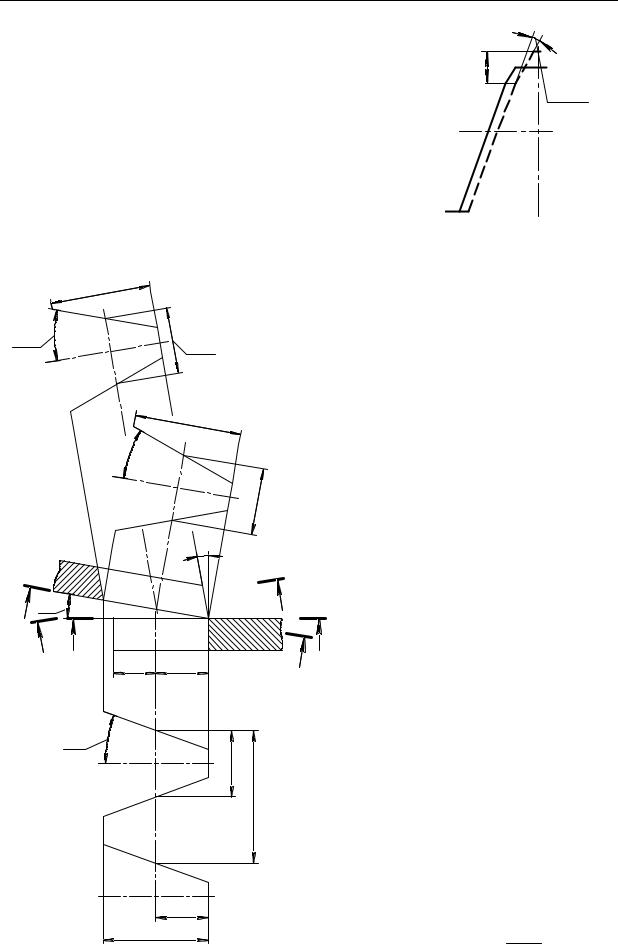
Режущий инструмент. Конспект лекций |
66 |
|
3 Для корригирования зубьев колес у зубчатой рейки делают фланк, представляющий срез головки на величину hФ под углом αФ. В отличие от зубчатой рейки фланк инструментальной рейки представляет собой утолщение ножки зуба, определяемое высотой hФИ и углом αФИ фланка. Обычно высота фланка hФИ = 0,5mn, a угол αФИ = 50.
10.2.1 Зубострогальные гребенки
h ÔÈ
aÔÈ
|
h |
|
N |
aUN |
Snu |
|
hP
|
|
|
|
|
|
|
|
|
|
|
|
|
|
|
|
|
|
|
|
|
|
|
|
a |
p |
|
|
|
|
|
|
|
|
||
|
|
||||||||||
u |
|
|
|
|
|
|
|
|
|||
|
|
|
|||||||||
|
|
|
|
|
|
|
|
|
|
|
|
|
|
|
|
|
|
|
|
|
|
|
|
|
|
|
|
|
|
|
|
|
|
|
|
u n S
a
P |
g |
|
N |
N |
T |
|
T |
|
hà =m |
hf =1,25m |
P |
|
|
||
|
au |
|
|
|
|
|
Snu |
|
|
|
Pu |
|
|
hau |
|
|
|
hu |
|
Гребенка – самый простой по конструкции обкатной инструмент, выполненный в виде зубчатой рейки, и предназначен для наре-
зания колес внешнего зацепления с прямыми, винтовыми и шевронными зубьями на специальных зубострогальных станках. Для полного нарезания зубьев колеса длина гребенки должна быть равна длине начальной окружности обрабатываемого колеса, однако гребенка получится слишком длинной, а станки более сложной конструкции. Поэтому гребенки делают ограниченной длины для нарезания от одного да трех зубьев колеса.
Размеры профиля гребенки в сечении Т-Т равны размерам профиля исходной инструментальной рейки. В других сечениях изменяется лишь высота зуба гребенки, а осевые размеры остаются постоянными. Поэтому:
h = |
hИ |
|
; |
h |
= h ×cosα |
|
|
||||
P |
cos |
γ |
|
N |
И |
|
|
|
|
Углы профиля на передней поверхности (Р-Р):
tgαИР =tgαИ ×cosγ
в нормальном сечении (N-N):
tgαИN = costgααИ
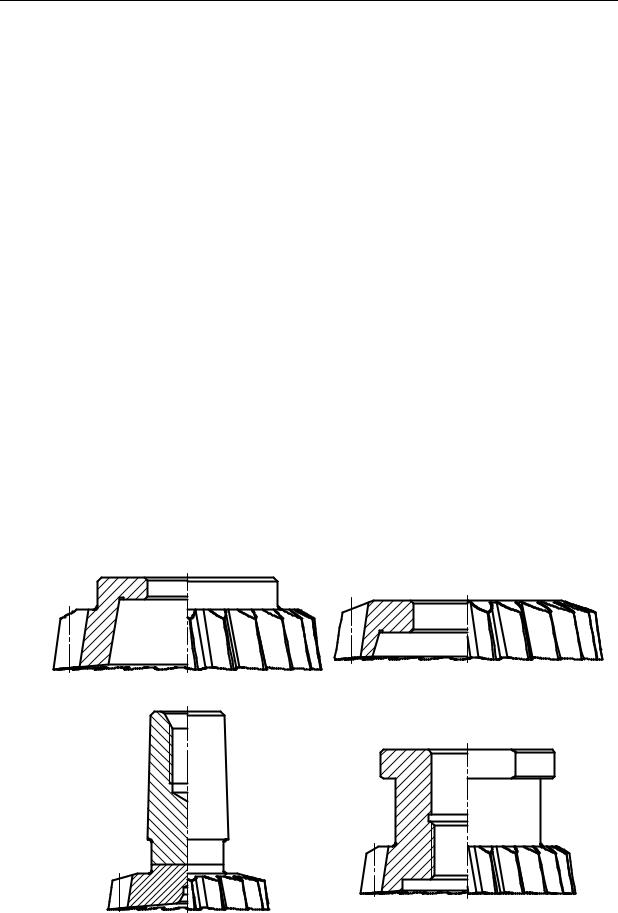
Режущий инструмент. Конспект лекций |
67 |
|
По технологическому назначению зуборезные гребенки бывают черновые, шлифовочные и чистовые.
Черновы гребенки применяют для предварительной обработки, шлифовочные — для обработки зубьев колес под последующее шлифование, чистовые - для окончательного нарезания зубчатых колес 6 - 9-й степени точности.
Геометрические параметры стандартной гребенки: у = 6°30/, а = 5°30/. У черновых гребенок передний угол принимается в зависимости от свойств обрабатываемого материала.
10.2.2 Зуборезные долбяки
В зависимости от характера обрабатываемых деталей долбяки делятся на три группы:
1)прямозубые - для нарезания прямозубых колес;
2)косозубые - для нарезания колес с винтовым зубом и шевронных колес;
3)специальные - для нарезания зубчатых деталей неэвольвентного зацепления (звездочки, шлицевые валы и т. д.)
По конструкции долбяки классифицируются на следующие группы:
а) дисковые - применяются для колес внутреннего и наружного зацепления при больших диаметрах; б) чашечные - для нарезания зубьев в упор;
в) хвостовые - для колес внутреннего зацепления малого диаметра, где недопустимо применение и изготовление дискового долбяка; г) втулочные - являются видоизмененным типом хвостового долбяка;
д) сборные.
à |
á |
â |
ã |
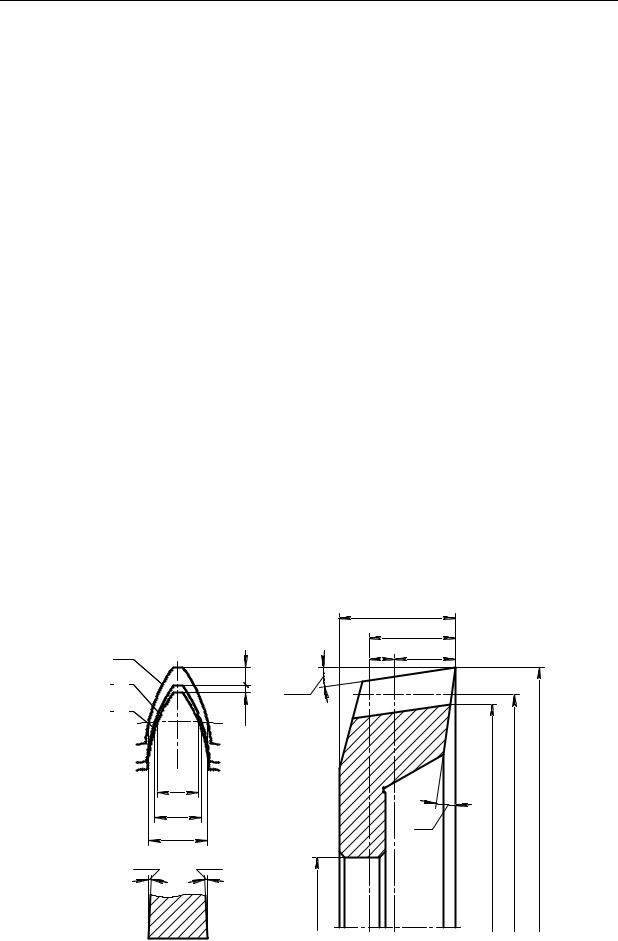
Режущий инструмент. Конспект лекций |
68 |
|
Согласно ГОСТ 9323-79 долбяки изготавливают 5-ти типов и 3-х классов точ-
ности:
1 - дисковые прямозубые (АА, А, В); 2 - дисковые косозубые (А, В); 3 - чашечные прямозубые (АА, А, В);
4- хвостовые прямозубые (В);
5- хвостовые косозубые (В). Классы точности применяют:
АА - для нарезания колес 6-й степени точности; А - для нарезания колес 7-й степени точности; В - для нарезания колес 8-й степени точности;
10.2.2.1 Конструктивные и геометрические параметры долбяка
Долбяк как инструмент получается из цилиндрического зубчатого колеса путем создания передних и задних углов по всему контуру режущих кромок. В результате этого задание поверхности получаются похожими на коническое колесо с равновысоким зубом. Однако в отличие от конического колеса, у которого образующая начального конуса расположена на конической поверхности, у долбяка образующая начального (делительного) цилиндра лежит на цилиндрической поверхности. Делительный диаметр является постоянным в любом сечении, перпендикулярном к оси долбяка.
Для создания задних углов на вершине зубьев (αВ) и на его боковых сторонах (αБ), зубья долбяка образуются путем смещения исходной рейки и имеют в каждом сечении перпендикулярном к оси долбяка свою особую величину смещения контура χ = ξИ × mn, где ξИ - коэффициент смещения контура исходной инструментальной рейки.
Â
|
|
|
H |
|
|
1 |
|
b |
à |
|
|
0 |
1 |
a |
|
|
|
c |
|
|
|
||
2 |
|
|
|
|
|
2 |
|
|
|
|
|
|
c |
|
|
|
|
|
S2 |
|
|
|
|
|
S0 |
|
|
|
a |
|
|
|
|
d |
|
|
|
g |
f |
d |
|
|
|
|
|||
|
S1 |
|
d |
||
|
|
|
|
|
|
aÁ |
aÁ |
|
|
|
|
|
|
dîòâ. |
|
|
|
2 |
|
0 |
|
1 |
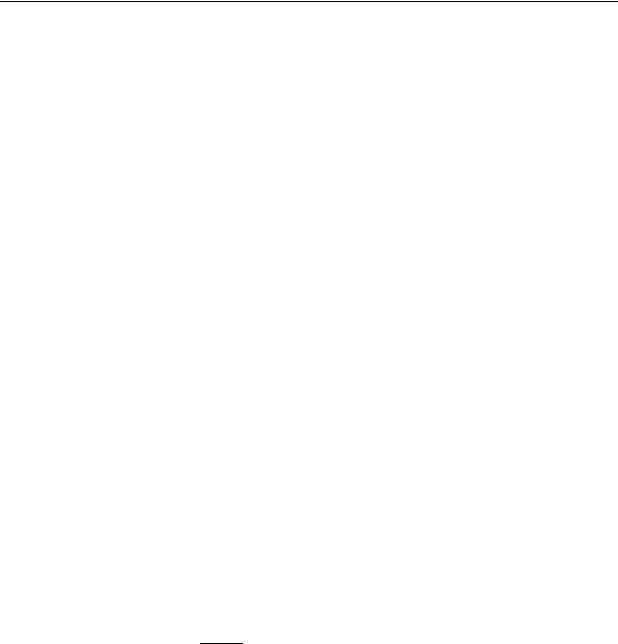
Режущий инструмент. Конспект лекций |
69 |
|
Различают три основных сечения долбяка, перпендикулярных к его оси. Сечение 1 – 1, проходящее чрез вершинные режущие кромки нового долбяка, называется начальным. В этом сечении смещение исходного контура
рейки будет положительным и максимальным χ1 = +ξИ×mn = а×tgαВ. Сечение 0 – 0 называется исходным. В нем смещение исходного конту-
ра равно нулю. Это сечение называется также и расчетным, так как в нем определяются основные параметры долбяка.
Сечение 2 – 2 называемое конечным, соответствующее окончательно сточенному долбяку. Сечение образовано отрицательным смещением исходного контура рейки χ2 = -ξИ×mn = b×tgαВ.
В лубом сечении профиль зуба будет очерчен по эвольвенте. Во избежание искажений профиля, эвольвенты должны быть образованы от одного и того же основного цилиндра диаметром DО = d×cosα = mn×Z×cosα.
Согласно ГОСТ 9324-79 долбяки делают с номинальными делительны-
ми диаметрами равными 25, 38, 50, 75, 100, 125, 160, 200, 360. Фактический де-
лительный диаметр отличается от номинального, что вытекает из условия d = mn×Z, где Z — число зубьев долбяка, которое является целым. Предпочтительно принимать число зубьев в пределах от 30 до 60 если долбяк не фланкирован (желательно учитывать условие ZШ < Z < ZК)
Диаметр окружности выступов на передней поверхности: da = mn × Z + 2 × mn × (f’ + C’) + 2a × tgaB
где f' - коэффициент высоты головки зуба. Для стандартного зацепления f’ = 1. C’ - коэффициент радиального зазора. Для ст. зацепления C’ = 0,25.
Диаметр окружности впадин по передней поверхности:
df = mn × (Z – 2,5) + 2a × tgαB
Толщина зуба по дуге делительной окружности:
S0 = π ×2mn +∆Sau - в основной плоскости;
S1 = S0 + 2a × tgαБ – на передней поверхности. где αБ – боковой задний угол. Находится в пределах 2 – 4 градусов.
tgαБ = tgαB × tgα
Углы резания
Передний угол на вершине зубьев γ у чистовых долбяков принимают равным 5 градусам, а у черновых от 10 до 12.
Задний угол на вершине зубьев αв у стандартных долбяков равен 6 градусам, у чистовых долбяков увеличивают до величины 8-9 градусов, а для черновых до 12
При определении параметров косозубого долбяка расчеты остаются теми же, лишь необходимо учитывать угол наклона зубьев β при расчете делительного диаметра.
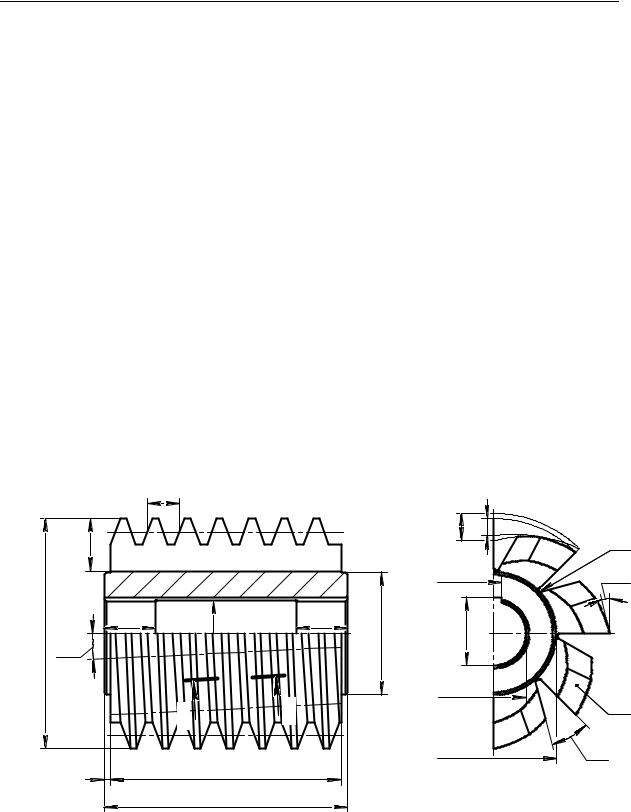
Режущий инструмент. Конспект лекций |
70 |
|
10.2.3 Червячные фрезы
Червячные фрезы применяют для обработки прямозубых, косозубых и шевронных цилиндрических колес, а также для нарезания зубьев червячных колес с различными видами зацепления.
Червячная фреза как инструмент получается из червяка путем прорезания канавок, образующих переднюю поверхность зубьев и пространство для размещения стружки и затылование зубьев для создания задних углов по всему профилю.
При проектировании червячных фрез на базе эвольвентного зацепления используют архимедов червяк с прямолинейным трапециевидным профилем в осевом сечении или конвалютный червяк с прямолинейным профилем в нормальном сечении.
Червячные фрезы бывают: цельными и сборными (с припаянными (6 < m < 15 мм) или со вставными гребенками при m > 15 мм).
Цельные червячные фрезы изготавливают 5-ти классов точности (АА, А, В, С, D). Сборные фрезы делают 4-х классов точности (А, В, С, D). Фрезы класса точности АА применяют для нарезания зубчатых колес 7-й степени точно-
сти, А - 8, В - 9, С и D- 10.
10.2.3.1Конструктивные и геометрические параметры фрезы
ÐÎÑ
D
Ê |
Ê |
|
1 |
|
r |
Í |
|
|
bØ |
|
a |
lØ |
2 |
lØ |
|
|
d |
Á |
1 |
|
|
||
w |
|
d |
Ñ |
|
|
|
|
dÎÒÂ. |
Z |
|
N |
N |
||
|
|||
|
D1 |
Q |
|
lÁ |
|
|
|
lÐÀÁ |
|
|
|
|
||
|
|
|
|
||||||||
|
|
|
|
|
|
|
|
|
|
|
|
|
|
|
|
|
|
|
|
|
|
|
|
|
|
|
|
|
|
|
|
|
|
|
|
L
Диаметр посадочного отверстия (dОТВ.) должен обеспечивать необходи-
мую жесткость оправки, на которой устанавливается фреза:
для фрез нормальной точности - dОТВ. = 20 ×mn0,373 , для фрез повышенной точности - dОТВ. = 27 ×mn0,404 .
Диаметр посадочного отверстия принимается из нормального ряда: 19, 22, 27, 32, 50 и далее через 10.
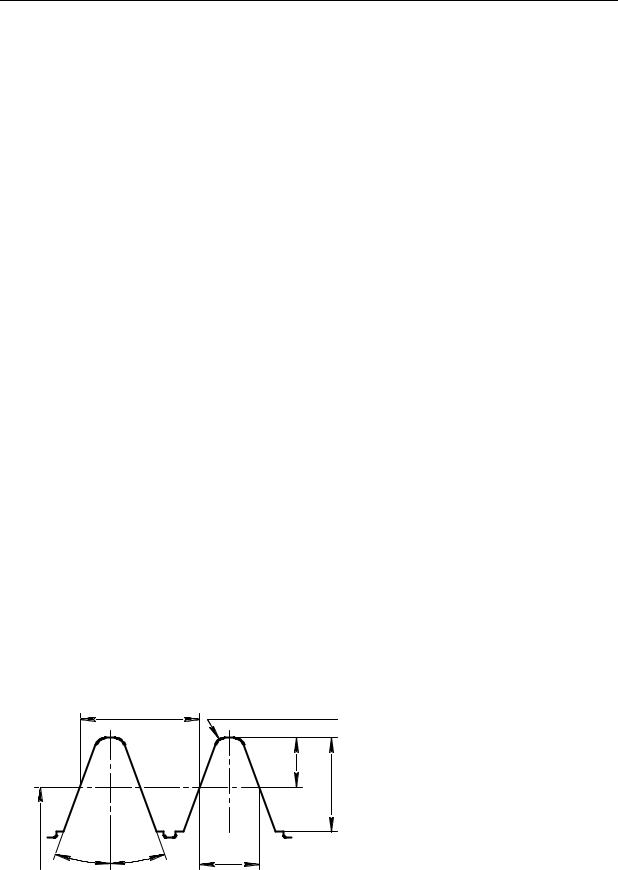
Режущий инструмент. Конспект лекций |
71 |
|
Диаметр фрезы (D) влияет на ее конструкцию, точность получаемых зубьев колес, погрешность конструкции фрезы и производительность процесса обработки.
D = D1 + 2H
где D1 – диаметр окружности проходящей через основание стружечных кана-
вок, мм. D1 = 1,75 × dОТВ,
Н– глубина стружечной канавки, мм.
H = h + К +r |
H = h + |
K +K1 |
+r |
|
|||
И |
И |
2 |
|
|
|
|
где hИ – высота профиля фрезы, мм. hИ = hаИ + hfИ = (2,5 ÷ 2,6) × mn, К1 – величина второго затылования, мм. К1 = (1,25 ÷ 1,50) × mn.
Число зубьев фрезы (Z) должно быть по возможности наибольшим. С увеличением числа зубьев, увеличивается число резцов, уменьшается шероховатость поверхности, уменьшается толщина срезаемого слоя. Число зубьев насадных цельных фрез ограничивается условиями затылования, а сборных - условиями крепления зубьев. Для червячных фрез обычной точности принято Z = 12 ÷ 9, для прецизионных Z = 16 ÷ 12, для сборных затылованных Z = 10 ÷ 8.
Канавки, образующие переднюю поверхность зубьев и пространство для размещения стружки, могут быть винтовыми, перпендикулярными виткам зубьев фрезы на делительном диаметре в расчетном сечении, и прямыми, проходящими через ось, если передний угол γ = 0, или параллельными оси, если
γ ≠ 0.
Стандартные фрезы изготовляют с канавками первого типа. Шаг винтовой канавки Px = π×D×ctgω. Передние углы для левой и правой режущих кромок у таких фрез получаются одинаковыми.
Размеры профиля зубьев фрезы
Профиль зубьев фрезы в нормальном сечении N-N
PN r=(0,25-0,30)•mn
|
|
|
au |
|
|
|
|
h |
|
|
|
|
È |
|
|
|
|
h |
|
|
a |
a |
SN |
|
È |
È |
|||
È |
||||
d |
|
|
|
Для фрез, профилируемых на основе конволютного червяка, профиль лежит в нормальном сечении к виткам, и его размеры определяются в этом сечении. Угол профиля таких фрез аи принимается равным углу профиля, а исходного контура зубчатой рейки.
Для фрез, профилируемых на основе архимедова червяка, профиль задается в осевом сечении фрезы.
Вследствие затылования боковых поверхностей углы профиля для левой αИЛ и правой αИП стороны у них будут разными.

Режущий инструмент. Конспект лекций |
|
|
|
72 |
|
|
|
|
|
|
|
Для некорригированного зацепления шаг между зубьями профиля фре- |
|||||
зы: |
|
|
|
|
|
в нормальном сечении |
в осевом сечении |
||||
P =π ×m |
n |
P = |
Pn |
= π ×mn |
|
|
|||||
n |
X |
cosτ |
cosτ |
||
|
|
|
|||
Толщина зуба фрезы на делительной окружности: |
|
|
|
||
S0 = π ×mn +∆Sau |
∆Sau принимается равным от 0,09 мм |
||||
2 |
|
(при m = 1 мм) до 0,4 мм (при m = 25 мм) |
Стандартные червячные фрезы имеют передний угол γ = 00 и задний угол по наружному диаметру αВ = 10 - 120. Червячные фрезы могут проектироваться и изготовляться и с положительным передним углом γ = 10 – 15 , однако в данном случае необходимо произвести коррекционный расчет профиля фрезы, что усложняет их расчет. В сечении, нормальном к боковым режущим кромкам, задний и передний углы будут иными, значительно меньшими, чем для вершинной режущей кромки.
tgαБ = tgαВ × sinαИ, tgγБ = tgγВ × sinγИ.
Анализ этих уравнений показывает, что на боковых режущих кромках углы
резания получаются недостаточными. Так, для фрезы, у которой αИ = 200, γ = 100, αВ = 10 - 120, имеем γБ = 2030', αБ = 2030' – 30.
Длина фрезы (L)
L = lРАБ + 2lБ
где lБ – ширина буртиков, мм. lБ = 2 ÷ 5 мм. lРАБ – длина рабочей части фрезы, мм.
lРАБ =2 × Ra2 +R2f +(1÷4)×PХ
где Rа, Rf – радиусы наружной и внутренней окружности нарезаемого колеса, мм.
Диаметр буртиков (dБ) принимается на 1 ÷ 2 мм ниже стружечной ка-
навки.
Длина посадочных участков отверстия (l1)
l1 = (0,25 ÷ 0,30) × L
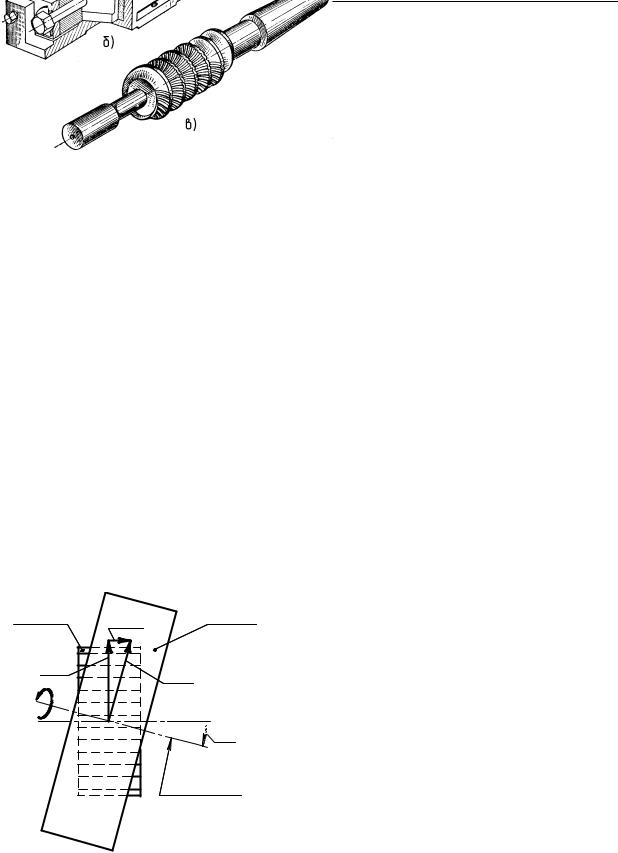
Режущий инструмент. Конспект лекций |
73 |
|
10.2.4 Шеверы
Шеверы — это сложные зуборезные инструменты, применяемые для чистовой, отделочной обработки прямозубых и косозубых цилиндрических колес, как наружного, так и внутреннего зацепления. Они повышают точность и снижают шероховатость обрабатываемой поверхности. Шеверы бывают дисковые (а), реечные (б) для обработки цилиндрических колес и червячные (в) для обработки червячных колес. Наибольшее распространение имеют дисковые шеверы в виде шестерни с винтовыми зубьями
Шеверы применяются для чистовой обработки цилиндрических колес с модулем от 0,2 до 8,0 мм с прямыми и винтовыми зубьями наружного и внутреннего зацепления. Шевингование повышает точность колес, как правило, примерно на одну степень, при этом исправляются профиль зубьев, шаг, направление зубьев, биение зубчатого венца, а шероховатость поверхности зубьев снижается с Ra – 3,2 ÷ 1,6 мкм до Ra =0,80 ÷ 0,40 мкм. Хуже исправляется накопленная погрешность шага.
Колесо |
Vñê |
Шевер |
Vê |
|
Vø |
|
|
y
Ось шевера
Где ψ - угол скрещивания осей шевера и колеса. Наиболее благоприятно, когда ψ = 10…150, а при обработке блочных колес при ограниченности свободного продольного хода ψ = 50.
Суть процесса шевингования состоит в удалении (соскабливании) крупных гребешков шероховатости в виде мелкой стружки с боковых сторон зуба.
Шевингование осуществляется при свободном беззазорном зацеплении зубьев шевера и заготовки. Принудительное вращение сообщается шеверу, колесо, находясь с ним в зацеплении, свободно вращается на оправке, установленной в центрах. Для обработки колеса по всей длине осуществляется продольная подача колеса относительно шевера. В конце продольного хода сообщается радиальная подача SРАД. – сближение осей шевера и заготовки. Радиальная подача обеспечивает врезание режущих кромок шевера в обрабатываемую поверхность зубьев заготовки.