
надега 3 часть
.pdf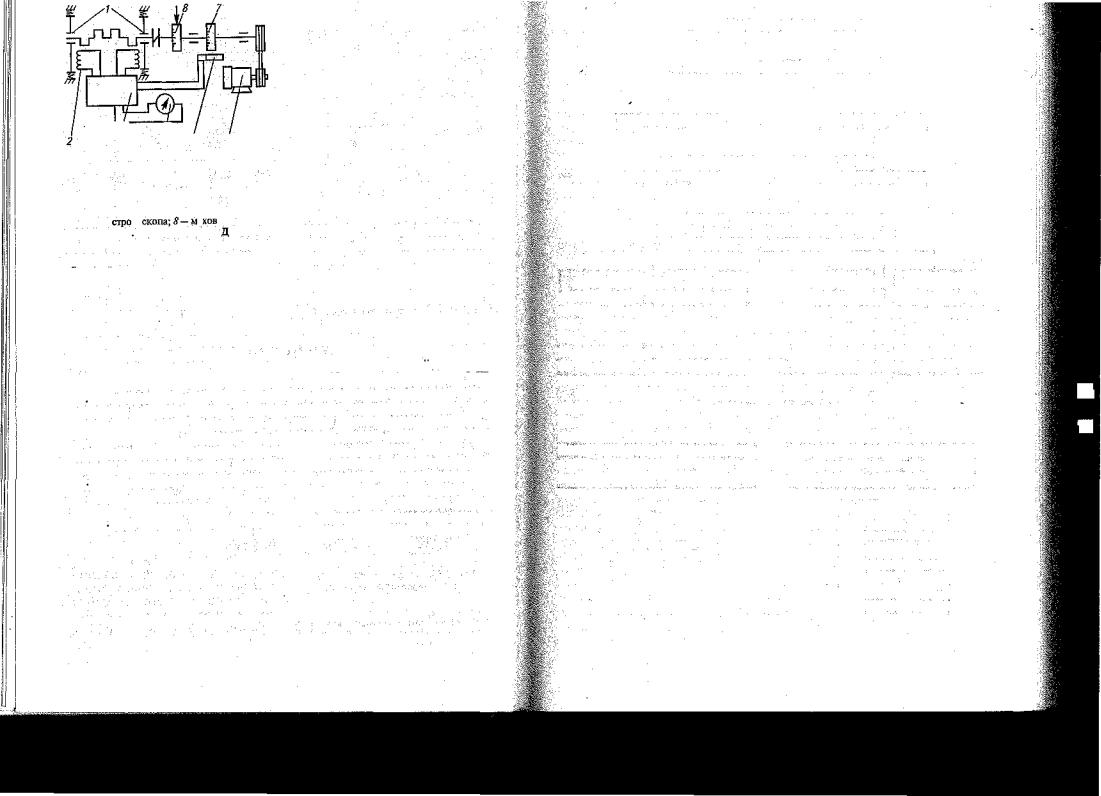
|
|
|
действием |
неуравновешенных |
|||
|
|
|
центробежных сил инерции и |
||||
|
|
|
их |
моментов люльки |
/ |
||
|
|
|
(рис. 2.28) будут колебаться в |
||||
|
|
|
горизонтальной плоскости. |
|
|||
|
|
|
Колебания опор приводят в |
||||
|
|
|
движение связанные с ними ка- |
||||
|
|
|
тушки датчиков 2, находящихся |
||||
т |
т . |
|
в магнитном поле постоянных |
||||
|
магнитов, в результате чего в |
||||||
3 |
4 5 |
6 |
обмотках катушек |
наводится |
|||
Рис. 2.28. Схема машины для |
ЭДС, |
значение которой будет |
|||||
динамической балансировки коленчатых |
пропорционально |
амплитуде |
|||||
|
валов: |
|
колебаний. |
Таким |
образом, |
||
i —люльки; 2—датчик колебаний; 3 — блок |
датчики 2 преобразуют механи- |
||||||
усиления; 4—миллиамперметр; 5 —лампа |
|||||||
стробоскопа; 6— электродвигатель; 7—лимб |
ческие колебания люлек в элек- |
TpH4ecKHe6°CHra^ibiaoT™aT4HKOB подводятся к блоку усиления 3.
Далее они поступают на миллиамперметр 4, шкала которого проградуирована в единицах дисбаланса (г-см), и на безынерционную лампу 5 стробоскопа, которая освещает цифры на вращающемся лимбе 7. Цифры показывают угол (в градусах) расположения дисбаланса. Угловое расположение дисбаланса отсчитывают по лимбу и устанавливают по стрелке на маховике 8.
Дисбаланс и его уравновешивание измеряют поочередно для каждой из опор (правой и левой). Для этого на пульте управления
расположен переключатель.
Натаком принципе основано устройство применяемой на ремонтных предприятиях универсальной балансировочной машины МЪУ4 Она состоит из механической части, измерительного устройства с датчиком и стробоскопом и электропривода с устройством для автоматической смазки вкладышей под шейки балансируемой детали.
Балансировку проводят при вращении детали. Через некоторое время после достижения заданной частоты вращения детали с помощью электромагнитов автоматически растормаживаются люльки Далее определяют дисбаланс и угол его расположения для одного конца детали. Снимают часть металла (у коленчатого вала, например, с противовеса), добиваясь допустимого значения дисбаланса Затем те же операции выполняют для другого конца детали. Когда двигатель выключают, электромагниты обесточиваются и запирают люльки.
Масса, г, снимаемого или добавляемого металла
G = M/r, |
(2Л2) |
где М—дисбаланс (показания миллиамперметра), г-см; г— расстояние от оси вращения детали до места снятия металла или прикрепления груза, см.
Из формулы (2.11) можно установить, для какихдеталей достаточ-
но статической балансировки, а для каких необходима динамическая. Статической балансировки достаточно для коротких деталей (шкивов, маховиков, дисков сцепления и т.д.), у которых длина меньше диаметра и не может быть большого плеча L пары сил, а значит, возмущающий момент практически равен нулю. В то же время вследствие большогодиаметра (большое г) их статическая неуравновешенность может быть большой [см. формулу (2.10)]. И наоборот, для деталей с большей длиной, значительно превосходящей диаметр (коленчатые валы, барабаны и т. д.), первостепенное значение имеет динамическая неуравновешенность, и их обязательно подвергают динамической балансировке. Динамическая неуравновешенность включает в себя и статическую неуравновешенность, но не наоборот.
Обычно детали ответственных сборочных единиц динамически балансируют отдельно, а затем всю сборочную единицу балансируют в сборе. Так поступают, например, с коленчатым валом в сборе с маховиком и сцеплением. Нормы дисбаланса приведены в технических требованиях на ремонт машин.
2.8. СБОРКА, ОБКАТКА И ИСПЫТАНИЕ ОБЪЕКТОВ
Сборка объектов ремонта. При сборке различают работы, которые имеют к ней непосредственное отношение и выполняются в сборочном цехе, а также вспомогательные и пригоночные. В связи с тем что в процессе сборки используют детали, бывшие в эксплуатации и годные к дальнейшей эксплуатации, а также имеющие некоторое искажение геометрической формы и размеров, возможно возникновение ряда погрешностей во взаимном расположении элементов собранного соединения.
Чтобы выдержать необходимый зазор (натяг), необходимо вводить в размерные цепи неподвижный компенсатор (шайбы или прокладки). Например, для получения требуемого натяга в соединении плоскость головки цилиндров — бурт гильзы цилиндров после обработки посадочного места в блоке под верхний буртик гильзы устанавливают необходимое число прокладок (колец), а для обеспечения нужного зазора в роликовом подшипнике между крышкой и наружным кольцом размещают несколько регулировочных прокладок.
В машинах находится приблизительно следующее количество соединений: типа цилиндрический вал — втулка — 35...40 %, резьбовых — 15...25, плоскостных — 15...20, конических — 6...7, сферических — 2...3 % и др. По конструкции их можно разделить на следующие группы (рис. 2.29): неподвижные разъемные (резьбовые, пазовые и конические); неподвижные неразъемные (соединения запрессовкой, заклепочные); подвижные разъемные (валы — подшипники скольжения, зубья колес, плунжеры-втулки); подвижные неразъемные (некоторые подшипники качения, запорные клапаны). При сборке машин используют универсальный монтажный инструмент, съемники и специальные приспособления.
Щ
:п
128 |
129 |
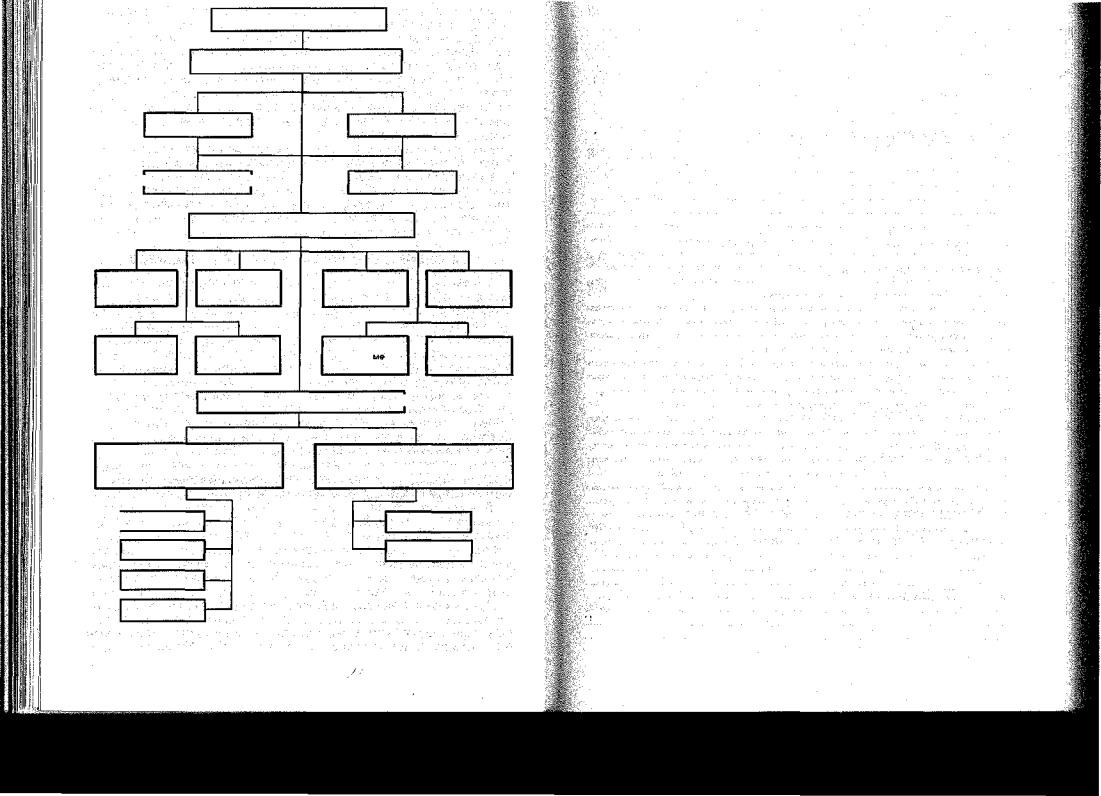
Соединения деталей машин
По конструктивным признакам
Неподвижные Подвижные
I |
Разъемные |
I |
Неразъемные |
|
|
|
По технологическим признакам |
|
|
Резьбовые |
Прессовые |
Заклепочные |
Вальцовочные |
Сварные |
Паяные |
Клеев |
Получаемые |
||
гибкой |
|||||
|
|
|
|
||
|
|
По контактным признакам |
I |
||
Соединения с непосредственным |
Соединения с контактом по его поверх • |
||||
|
контактом по его поверхности |
ности через промежуточный слой |
|||
|
|
|
|
материала |
|
[ |
Общим |
|
|
Общим |
|
|
Местным |
|
|
Местным |
|
|
Линейным |
|
|
|
Точечным |
Рис. 2.29. Схема соединений деталей машин |
|
С б о р к а р е з ь б о в ы х с о е д и н е н и й включает в себя: подачу деталей, их установку и предварительное ввертывание (наживлепие), подвод и монтаж инструмента, завинчивание, затяжку, отвод инструмента, дотяжку, стопорение для предохранения от самоотшшчивания. Предварительное ввертывание выполняют вручную.
При постановке шпильки она должна иметь плотную посадку, а се ось — быть перпендикулярна к поверхности детали, в которую она завинчена. Неперпендикулярность приводит к появлению значнтельных дополнительных напряжений в резьбе при работе и в итоге — к обрыву детали.
Для ввертывания шпильки служат ручной и механизированный шпильковерты. При завинчивании она удерживается специальными головками за резьбу или за ненарезанную часть. При использовании ручных шпильковертов применяют ключи, головка которых имеет внутренние спиральные канавки с помещенными в них роликами, удерживаемыми обоймой. Во время поворачивания головки ролики плотно охватывают ненарезанную часть шпильки и ведут ее вместе с ключом.
При завинчивании механизированным инструментом шпильки удерживаются за резьбовую часть.
Резьбовые соединения собирают с предварительной затяжкой, степень которой для болта или винта зависит от сил, нагружающих соединение. Особенно важно ее правильно выбрать при сборке ответственных соединений (например, шатунных и коренных подшипников). Необходимый момент затяжки резьбового соединения достигают применением динамометрических ключей. Момент контролируют по шкале, жестко зафиксированной на тарированном упругом стержне. На нем же устанавливают и рукоятку ключа. C'l релку, относительно которой определяют момент затяжки, жестко крепят на головке ключа.
Во избежание перекоса деталей, закрепляемых несколькими резьбовыми соединениями, следует строго соблюдать порядок за- '1яжки и выполнять ее в два-три приема.
Резьбовые соединения, работающие при циклических нагрузках л вибрации, стопорят. Для этого применяют контргайки, деформируемые и пружинные шайбы, разводные шплинты и шплинтовочную проволоку.
Контргайку нужно завинчивать и затягивать после полной загяжкиосновнойгайки.
Стопорную деформируемую шайбу устанавливают так, чтобы ее усик входил в паз вала. Часть деформированной шайбы, выступающей из-под гайки, необходимо отгибать на одну из ее граней и на грань одной из скрепляемых деталей.
11ружинные шайбы после затяжки гаекили болтовдолжны полнос1ыо прилегать к поверхности деталей и болтов или гаек. При сборке допускается использование пружинных шайб, бывших в употреблении, еслиихконцыразведены нарасстояние, превышающее толщину
131
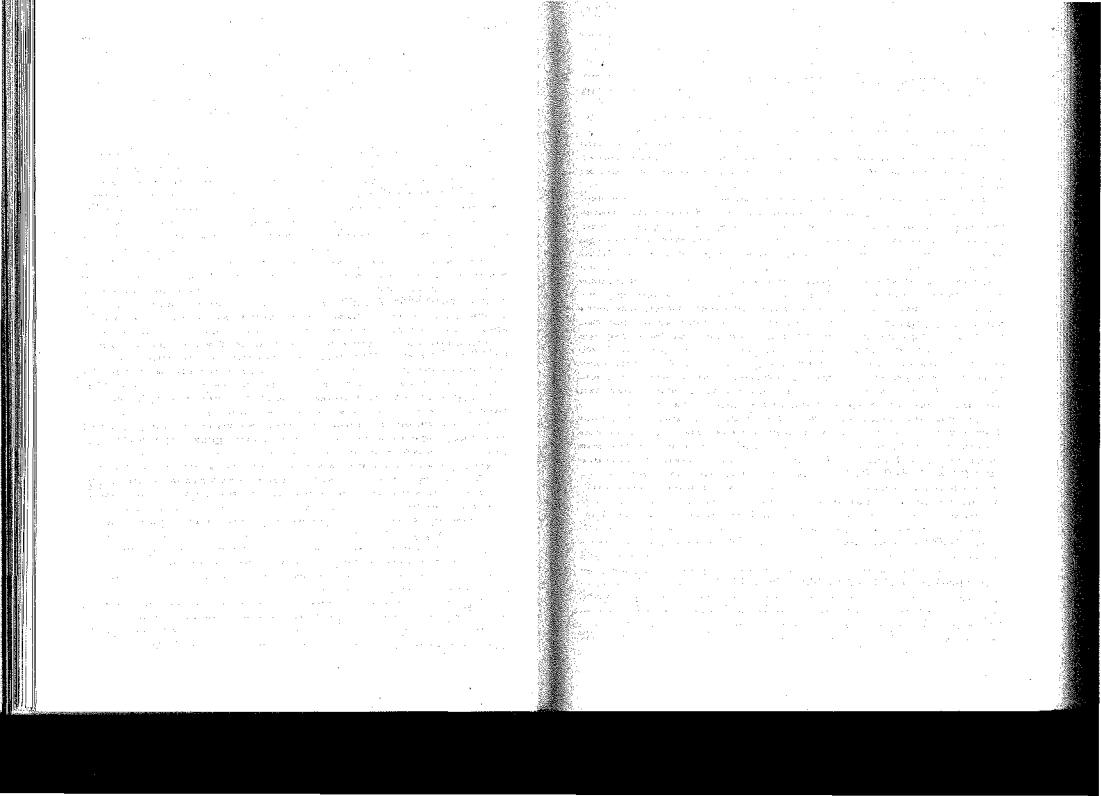
шайбы в 1,5 раза. Не допускается постановка шайб, внутренний размер которых не соответствует диаметру болта или шпильки.
Для стопорения разводным шплинтом его нужно устанавливать так, чтобы головка полностью утопала в прорези гайки, а концы были разведены по оси болта (один — на болт, другой — на гайку).
При шплинтовке проволокой ее следует вводить в отверстие болтов крест-накрест. После этого концы проволоки туго скручивают вместе и обрезают на расстоянии 5...7 мм от начала скрутки.
Сборку ш п о н о ч н ы х и ш л и ц е в ы х с о е д и н е н и й рекомендуется выполнять после тщательного осмотра соединяемых деталей. На их поверхностях не должно быть заусенцев, задиров и забоин. При наличии таких дефектов их необходимо устранить. В сельскохозяйственных машинах наиболее распространены призматические, сегментные и клиновидные шпонки.
Шпоночное соединение собирают в такой последовательности. Сначала шпонку устанавливают легкими ударами медного молотка в паз вала (сегментные и призматические шпонкидолжны входить в паз с некоторым натягом), а затем на вал насаживают охватывающую деталь (шкив, звездочку, шестерню и т.д.). Такие шпонки в пазу охватывающей детали располагают с некоторым зазором. В случае необходимости их подгоняют по пазам вала и охватывающей детали припиливанием или шабрением.
Перед сборкой неподвижных шлицевых соединений надо также убедиться в отсутствии заусенцев, забоин и задиров. Шлицевые соединения выполняют с высокой точностью и не требуют подгонки. Их собирают вручную без особого усилия.
Клиновидныешпонкивходятвканавкивалаиохватывающейдеталиснатягом. Ихустанавливаютвпазлегкимиударами медного молотка. Уклон шпонки и паза в охватывающейдеталидолжен совпадать. В противном случае возможен перекос соединяемыхдеталей.
После сборкишпоночныхи шлицевыхсоединенийих следуетпроверить на биение охватывающей детали относительно охватываемой.
Сборка узлов п о д ш и п н и к о в с к о л ь ж е н и я —одна из ответственныхопераций сборки, таккак от правильности ее выполнения во многом зависитдолговечность работы машины.
В тракторах, автомобилях и сельскохозяйственных машинах применяют цельные и разъемные подшипники скольжения. В первом случае подшипник выполнен в виде втулки из антифрикционного металла или же из обычного металла с залитым внутри слоем антифрикционного сплава или полимерного материала, а во втором — состоит из двух частей (вкладышей) с диаметральным разъемом.
Сборка неразъемных подшипников заключается в запрессовке их в корпус, закреплении от проворачивания и подгонке отверстия по валу. Втулку можно запрессовывать ударами молотка через наставку, прессом или с помощью винтовых приспособлений. Очень важно правильно установить втулку для предотвращения перекоса. При использовании несложных приспособлений можно добиться требуемого направления и исключить ее перекос.
Перед запрессовкой втулка и отверстие корпуса должны быть тщательно очищены, а острые углы — опилены. Для устранения возможности появления задиров поверхность детали смазывают матинным маслом. Следует иметь в виду, что после запрессовки ее внутренний диаметр уменьшается. Поэтому втулки растачивают или развертывают.
Втулку крепят от проворачивания несколькими способами. Если
унее есть опорный буртик, то стопорят штифтом (сверлят отверстие
вопорном буртике и в корпусе подшипника и запрессовывают штифт) или винтом (в буртике сверлят отверстие, а в корпусе подшипниканарезаютрезьбу). В противном случае сверлятотверстие со стороны торца втулки так, чтобы оно образовалось частично во втулке и частично в корпусе. В это отверстие запрессовывают штифт.
Разъемные подшипники-вкладыши могут быть толстостенными и тонкостенными. Их изготовляют из малоуглеродистой стали и заливают антифрикционным сплавом слоем 0,7...3,0 мм для толстостенных и 0,3...1,3 мм для тонкостенных подшипников.
Перед установкой вкладышей проверяют правильность их прилегания к постелям с помощью щупа (щуп толщиной 0,05 мм не должен проходить в местах соприкосновения вкладыша с постелью) или на краску (пятно отпечатка должно занимать не менее 80 % поверхности постели). Вкладыши загоняют в постель легкими ударами деревянного молотка через деревянную планку, находящуюся на обеих стыковых поверхностях вкладыша.
Окончательная операция сборки разъемных подшипников скольжения — укладка вала в подшипники. Вкладыши должны хорошо прилегать к его шейке. Этого достигают точностью изготовления вкладышей у тонкостенных или расточкой у толстостенных подшипников. При сборке тонкостенных деталей необходимо создать определенный натяг при их посадке в гнезда, что обеспечит полное прилегание и необходимую прочность соединения. Натяг в соединении вкладыша с гнездом создается после затяжки болтов крышки благодаря выступанию края вкладыша над плоскостью разъема корпуса подшипника.
Подшипники качения нужно монтировать в следующем порядке: тщательно промыть подшипник в дизельном топливе и посадоч-
ные поверхности на валуи в корпусе, смазав их тонким слоем масла; нагреть в масляной ванне до температуры 90 "С те подшипники,
которые устанавливают с натягом при монтаже на вал; напрессовывать подшипник на вал с помощью гидравлического
стационарного или переносного пресса, атакже винтового приспособления.
При напрессовке подшипника на вал следует прикладывать усилие к его внутреннему, а при запрессовке в гнездо — к наружному кольцу, используя подкладные кольца или монтажные стаканы.
Для напрессовки и запрессовки подшипника одновременно на вал и в корпус служат специальные оправки, которые одновремен-
132 |
133 |
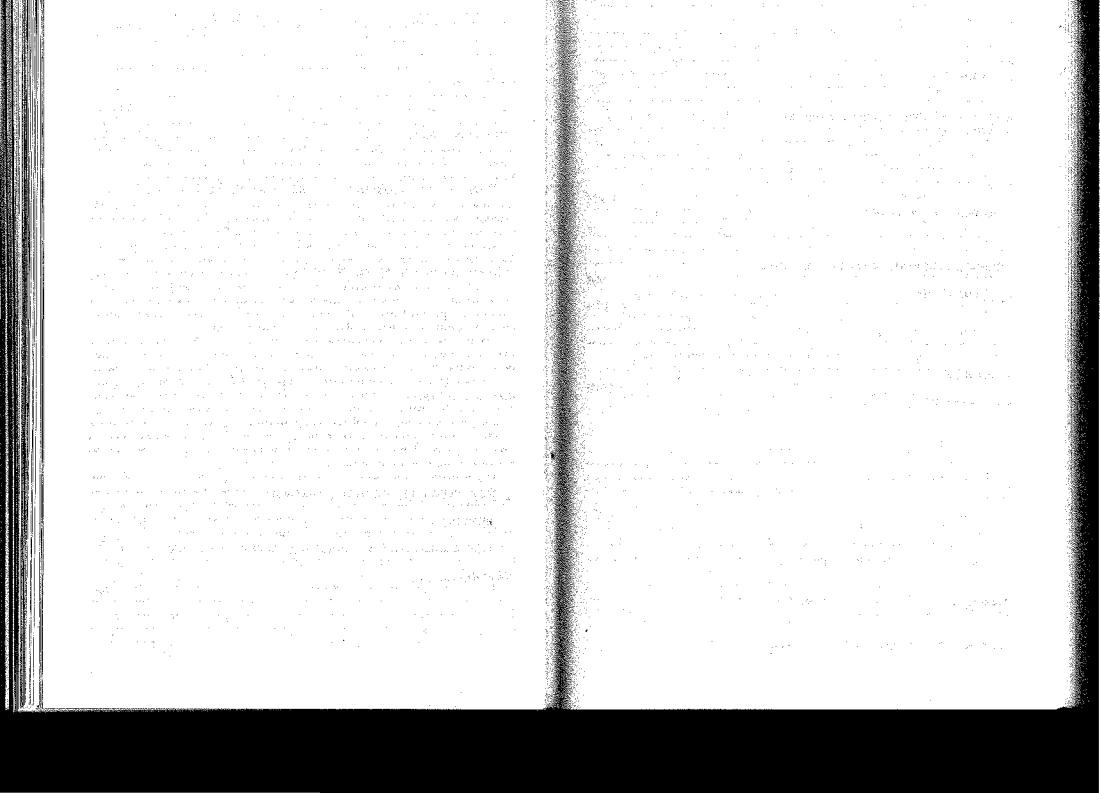
но опираются на оба кольца. После сборки он должен проворачиваться без заеданий.
Уплотнения в виде самоподжимных и войлочных сальников картонных прокладок служат для предупреждения вытекания масла из узлов и попадания в них грязи. Поэтому при их монтаже необходимо проявлять большую осторожность, чтобы не повредить их. Так, при запрессовке самоподжимных резиновых сальников на валы с острыми кромками или шлицами надевают предохранительные оправки. Поверхность валов, соединяемая с сальником, должна быть гладкой, без заусенцев и забоин.
Годные к дальнейшей работе войлочные сальники тщательно промывают в дизельном топливе, просушивают, а затем проваривают в масле. После монтажа они должны касаться вала по всей поверхности.
Прокладки изготовляют из картона, паронита, пробки, металла, асбеста и т. п. Они должны быть ровными, без утолщений и пустот. Поверхности деталей, между которыми размещают прокладки, должны быть ровными, без забоин и заусенцев. При установке прокладок все их отверстия должны совпадать с соответствующими отверстиями соединяемых деталей.
С б о р к а з у б ч а т ы х п е р е д а ч —одна из операций сборки при ремонте. Перед ней необходимо проверить торцовое и радиальное биение, расстояние между центрами, боковой зазор между зубьями и прилегание рабочих поверхностей зубьев. Биение проверяют после установки их на соединяемых деталях с помощью стойки с индикаторами. Прилегание рабочих поверхностей зубьев зацепляющихся шестерен проверяют на краску. Для этого на них наносят тонким слоем краску и затем поворачивают шестерни несколько раз. По отпечаткам краски на зубьях второй шестерни проверяют взаимный контакт зубьев зацепляющихся шестерен.
С помощью калиброванных оправок и микрометрических инструментов (например, штихмаса) контролируют расстояние между осями валов зубчатых передач. Непараллельность и перекос осей зубчатых колес устанавливают с помощью валов калибров. Боковой зазор между зубьями колес определяют прокатыванием между ними свинцовой пластины. Замерив толщину сплющенных частей пластины, находят боковой зазор.
Рассмотрим технологический процесс сборки при ремонте трактора ДТ-75М из восстановленных сборочных единиц.
1. Устанавливают раму на тележку или подставку с помощью кран-балки.
2.Монтируют кран-балкой на раму задний мост в сборе с коробкой передач и слегка закрепляют болтами.
3.Устанавливают двигатель в сборе и, прежде чем закрепить, регулируют соосность его с коробкой передач с помощью специальных оправок. Крепят оправки на валах сцепления и коробки передач и посредством шаблона или специальной втулки, которая передвигается на удлиненных концах валиков оправок, проверяют не-
соосность. При полном достижении соосности втулка свободно переходит с одного контрольного валика на другой. Регулировку в горизонтальной плоскости выполняют смещением двигателя, а в вертикальной — прокладками под его опоры и коробки передач. После этого надежно закрепляют двигатель и окончательно затягивают болты крепления заднего моста в сборе с коробкой передач.
4.Устанавливают гибкие и соединительные муфты. Затягивают raii ки крепления соединительной муфты до отказа ключом на плече 500 мм и стопорят шплинтами.
5.Монтируют на двигатель воздухоочиститель.
6.Размещают и закрепляют водяной и масляный радиаторы в сборе на передний брус рамы с помощью кран-балки. Покрывают краской наружные поверхности патрубков радиаторов, а затем закрепляют на них соединительные шланги. Устанавливают капот.
7.Монтируют механизм управления поворотом, навесную гидросистему, масляный бак и распределитель.
8.Устанавливают кабину. В ней закрепляют подушку и спинку сидения, механизм управления двигателем, выпускную трубу, щиток приборов и электрооборудование. С наружной стороны кабины монтируют топливный бак.
9.Устанавливают направляющие колеса, натяжное устройство и ролики.
10.Расстилают гусеницы и крепят каретки подвески по обе стороны трактора с помощью кран-балки и схваток. Опускают трактор катками кареток на гусеницы так, чтобы при соединении гусениц соединительное звено оказалось на зубьях ведущей звездочки. Стягивают гусеницы специальным приспособлением. Окончательно регулируют их натяжение винтом натяжного устройства.
11.Ставят аккумуляторыдлястартерногопускапускового двигателя.
12.Заправляют трактор водой, топливом и маслом.
13.Окончательно проверяют сборку и регулировки машины.
Обкаткаииспытаниеагрегатовимашинпослеремонта. Приобкатке
соединенные поверхности трения прирабатываются, что приводит к образованию новой микрогеометрии поверхностей, наиболее благоприятной для дальнейшей устойчивой работы соединений.
Испытание — комплексная проверка качества ремонта и установление обратной связи с его технологическим процессом.
Основная приработка соединенных поверхностей происходит в первые 2...3 ч и завершается для двигателей через 50...60, а для агрегатов трансмиссии через 100... 120 ч. Ее выполняют в два этапа: первый — обкаткой в ремонтной мастерской и второй — обкаткой в эксплуатационных условиях при работе с неполной нагрузкой.
Двигатели обкатывают на мотороремонтном участке мастерских на универсальных стендах КИ-5541, КИ-5542, КИ-5543, КИ-2139А и К.И-5274, а пусковые двигатели — на стенде КИ-2643А.
Стенд типа КИ представляет собой асинхронный электродвигатель трехфазного тока с весовым механизмом для замера мощности об катываемых двигателей.
134 |
135 |
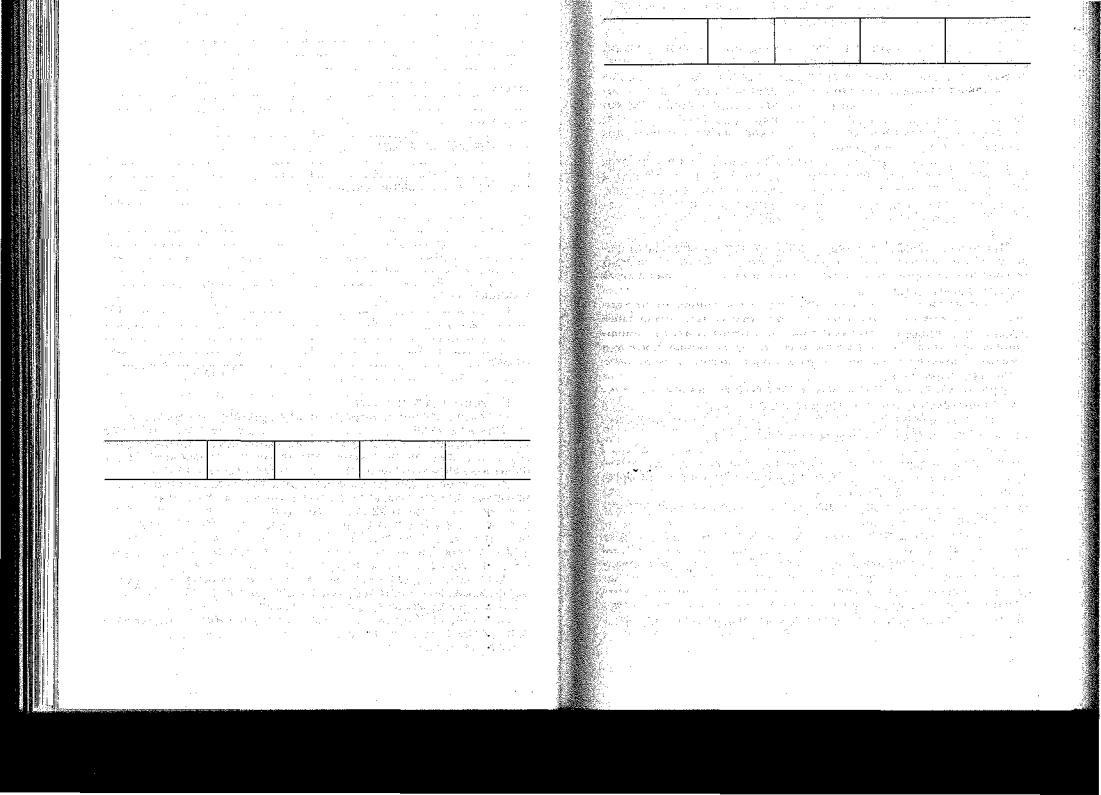
При холодной обкатке электродвигатель работает в режимедвигателя и через редуктор передает вращение на коленчатый вал обкатываемого двигателя. При горячей обкатке с нагрузкой и при испытании нагрузка испытуемого двигателя создается асинхронным электродвигателем, который начинает работать в режиме синхронного генератора. На стенде размещен редуктор, позволяющий обкатывать двигатели напрямой, повышенной или пониженнойпередаче.
Статор асинхронного электродвигателя установлен на стойках в шариковыхподшипниках и соединен с весовым механизмом, который имеет указывающий прибор с циферблатом, что позволяет измерять тормозной или вращающий момент.
Посредством реостата, включенного в цепь ротора, можно регулировать частоту вращения при холодной обкатке, а также создавать соответствующую нагрузку.
На специализированных ремонтных предприятияхдля повышения производительности и качества обкатки устраивают централизованные системы смазывания и подачи охлаждающей воды.
Дизели обкатывают на эксплуатационном масле. Холодную обкатку пусковых двигателей необходимо проводить на дизельном топливе, вводимом через систему питания, а горячую — на смеси автомобильного бензина и дизельного масла при соотношении 15 :1 по объему.
Для ускорения и улучшения приработки служат смеси масел с более низкой вязкостью, чем у штатного. Так, для двигателей со сталеалюминиевымивкладышами рекомендуется смесьдизельного (80 %) и индустриального (20 %) масел, а с вкладышами из свинцовистой бронзы — дизельного (28 %) и индустриального (72 %) масел.
Х о л о д н а я о б к а т к а (табл. 2.6) заключается во вращении коленчатого вала обкатываемого двигателя сначала с выключенной, а затем с включенной компрессией.
2.6.Режим приработкидвигателей
Этап |
|
Частота враще- |
|
Продолжитель- |
||
Двигатель |
нияколенчатого |
Нагрузка,кВт |
||||
ность, мин |
||||||
|
|
вала,мин"' |
|
|||
|
|
|
|
|||
|
Х о л о д н а я |
п р и р а б о т к а |
|
|||
Предварительная |
ЗМЗ-53 |
950...1100 |
0 |
18. .20 |
||
|
ЗИЛ-130 |
680...790 |
0 |
18. .20 |
||
Окончательная |
ЗМЗ-53 |
1250...1580 |
5,88...7,35 |
18. .20 |
||
|
ЗИЛ-130 |
1050...1250 |
7,35...8,82 |
18. .20 |
||
|
Г о р я ч ая п р и р а (5 о т к а |
|
||||
Предварительная |
ЗМЗ-53 |
1100...1350 |
0 |
12. .15 |
||
на холостом ходу |
ЗИЛ-130 |
950...1150 |
0 |
12. .15 |
||
Окончательная на |
ЗМЗ-53 |
1400... 1900 |
0 |
15. .18 |
||
холостом ходу |
ЗИЛ-130 |
1200...1400 |
0 |
15. .18 |
|
|
|
|
Продолжение |
|
|
|
Частота враще- |
|
Продолжитель- |
|
Этап |
Двигатель |
нияколенчатого |
Нагрузка,кВт |
||
ность, мин |
|||||
|
|
вала, мин "' |
|
||
|
|
|
|
||
С нагрузкой в ре- |
|
|
|
|
|
жиме: |
|
|
|
|
|
№ 1 |
ЗМЗ-53 |
1100...1350 |
9,56...11,76 |
17...20 |
|
|
ЗИЛ-130 |
950...1150 |
11,01...13,23 |
17...20 |
|
№ 2 |
ЗМЗ-53 |
1400...1550 |
19,11...23,52 |
15...17 |
|
|
ЗИЛ-130 |
1150...1300 |
22,1...27,2 |
15...17 |
|
№ 3 |
ЗМЗ-53 |
1600...2000 |
27,93...33,1 |
17...20 |
|
|
ЗИЛ-130 |
1350...1700 |
33,1...39,7 |
17...20 |
|
№ 4 |
ЗМЗ-53 |
2250...2500 |
33,1...38,2 |
12...15 |
|
|
ЗИЛ-130 |
1800...2100 |
38,2...50 |
12...15 |
|
Горячую |
о б к а т к у |
без н а г р у з к и выполняют после пус- |
ки лкигателя постепенным повышением частоты вращения коленчатого вала двигателя.
Горячую о б к а т к у под н а г р у з к о й проводят при положении рычага регулятора, соответствующем максимальной подаче топлива, и постепенном повышении нагрузки.
После окончания обкатки двигатель испытывают на развиваемую мощность и расход топлива, осматривают и устраняют неисправности.
Мощностьдвигателя, кВт, при работе на прямой передаче |
|
Ne = MKpn/9550, |
(2.13) |
где Мкр = 0.7162Р — крутящий момент на коленчатом валу двигателя, Н-м [здесь Р—нагрузка по весовому механизму, Н]; л —частота вращения коленчатого
1UUU1.
Часовой расход топлива, кг/ч,
G=3,6g/t, |
(2.14) |
где g - - масса топлива, израсходованного во время испытания, кг; t — время испытания, ч.
Для замера расхода топлива во время испытаний двигателя на стенде установлено весовое устройство.
Удельный расход топлива, г/(кВт-ч),
&=1000G/JVe. (2.15)
136 |
137 |
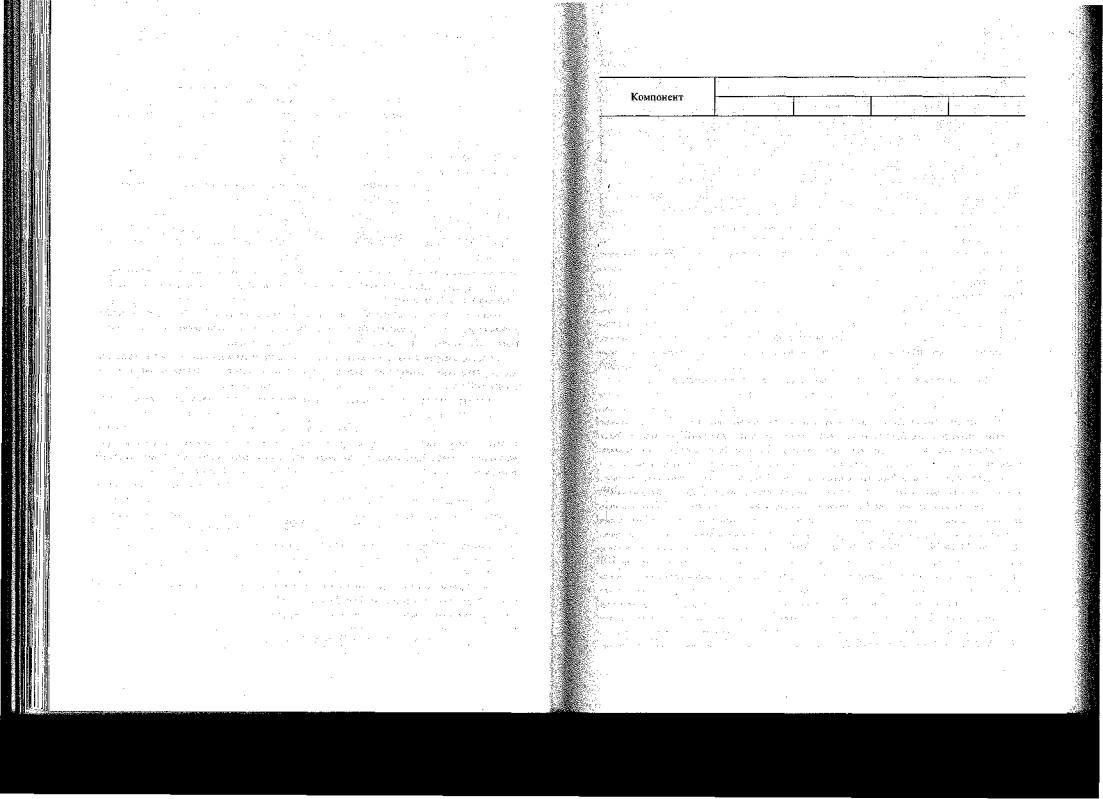
В период обкатки следует постоянно контролировать температу-
ру воды и масла, которые не должны превышать соответственно 85 и95°С.
По окончании обкатки и испытания двигатель осматривают, снимают с обкаточного стенда и устанавливают на стенд контрольного осмотра. Демонтируют поддон картера, головки цилиндров, крышки шатунных и коренных подшипников. При этом обращают внимание на состояние рабочих поверхностей шеек коленчатого вала, вкладышей и гильз цилиндров. Они не должны иметь рисок, задиров и царапин. В противном случае наблюдаются неприработанные поверхности.
Если в процессе обкатки, испытаний и контрольного осмотра были обнаружены неисправности, то их необходимо устранить и обкатывать двигатель на газу без нагрузки 10 мин. В тех случаях, когда заменялись гильзы или детали кривошипно-шатунного механизма, двигатель повторно обкатывают, испытывают и контролируют.
Число двигателей, подвергаемых контрольному осмотру (определяют в процентах от общего числа отремонтированных), зависит от уровня технологии и организации ремонта, и его устанавливает вышестоящаяорганизация.
У с к о р е н н у ю обкатку д в и г а т е л е й выполняют с помощью приработочных присадок, которые оказывают наибольшее влияние на детали цилиндропоршневой группы (ЦПГ) и криво- шипно-шатунного механизма (КШМ). Приработочные присадки добавляют либо к всасывающему в цилиндры воздуху или топливу, либо к смазочному маслу.
При введении с воздухом во всасывающий коллектор композиции из присадки АЛП-4Д и 5 % присадки ПМС-А (АЛП-ПМС), а также использовании смазочного масла ОМД-8 время обкатки, например, дизеля ЯМЗ-238НБ сокращается в 3 раза.
Присадки типа АЛП (АЛП-2, АЛП-3 и АЛП-4) для ускорения приработки вводят также в дизельное топливо в количестве 1,3...1,75 % по массе. Они представляют собой 30%-й раствор органополиалюмооксана вдизельном масле. При их сгорании образуется приработочная абразивная паста, состоящая из оксида алюминия и масла.
Ускорить приработку можно также добавлением в масло присадки МКФ-18У (композиции, включающей ОД...0,5 % хлорной меди; 4,5...9,5 % алифатического спирта С7—Ci2; 1...4 % полиалкиленилсукцинимидтетраэтиленпентамина и остальное — минеральное масло), с помощью которой в 3 раза сокращается время обкатки по сравнению с применением масел без присадок. Хороший эффект дает присадка к маслу ДФ-11, содержащая серу, фосфор и цинк.
Ь московском государственном агроинженерном университете
(МГАУ) разработано несколько присадок типа ОГМ (табл. 2.7), которые добавляют в смазочное масло.
2.7. Приработочные присадки типа ОГМ
|
Концентрация по номерам, % по массе |
|||
|
1 |
2 |
3 |
4 |
Хлорокись меди |
— |
0,1 |
0,5 |
0,9 |
Глпцерат меди |
3,0 |
— |
— |
— |
Олеиновая кислота |
2,0 |
0,5 |
2,5 |
4,5 |
Присадка ЛЗ-309/2 |
— |
0,07 |
0,35 |
0,63 |
N[инеральносмасло |
Остальное |
Остальное |
Остальное |
Остальное |
Приработочные присадки типа ОГМ к моторным маслам и присадка ОГМ-С к воздуху обеспечивают эффективную приработкудегалей ЦПГ и КШМ в течение всей обкатки. При этом снижается нриработочный износ за счет антифрикционных пленок меди, образующихся на поверхностях прирабатывающихся деталей.
Автоматизация процесса обкатки двигателей существенно облегчает труд обкатчика, обеспечивает строгое соблюдение режимов обкатки, контроль и регистрацию параметров двигателя с записью данных и, что очень важно, индивидуальную обкатку каждого двигателя с адаптацией режимов.
Разработали и эксплуатируют систему автоматизированного управления обкатки двигателей (рис. 2.30). Пульт управления системы используют для ручного режима обкатки. С помощью блока управления можно задавать программу обкатки двигателя. На информационное табло выдается информация: номер этапа обкатки, время обкатки, частота вращения коленчатого вала, мощность, температура воды и масла, давление масла. Посредством многоточечного потенциометра записываются мощность, расход топлива, юмпература воды и масла, частота вращения и давление масла.
Обкатку т р а н с м и с с и й тракторов выполняют в сборе без нагрузки с помощью приспособления СП-2807, состоящего из станины и электродвигателя мощностью 7 кВт. Его устанавливают на р;1му гусеничного трактора впереди коробки передач и прикрепляют стремянками к раме.
На первичный вал коробки передач надевают шкив и соединяют его приводными ремнями со шкивом электродвигателя. Перед началом обкатки рычаг переключения передач ставят в нейтральное положение, проверяют правильность местоположения агрегатов, надежность их крепления и чистоту картеров. Затем контролируют Работу трансмиссии на каждой передаче включением электродвига- •юля на 1...2 мин без смазывания.
138 |
139 |
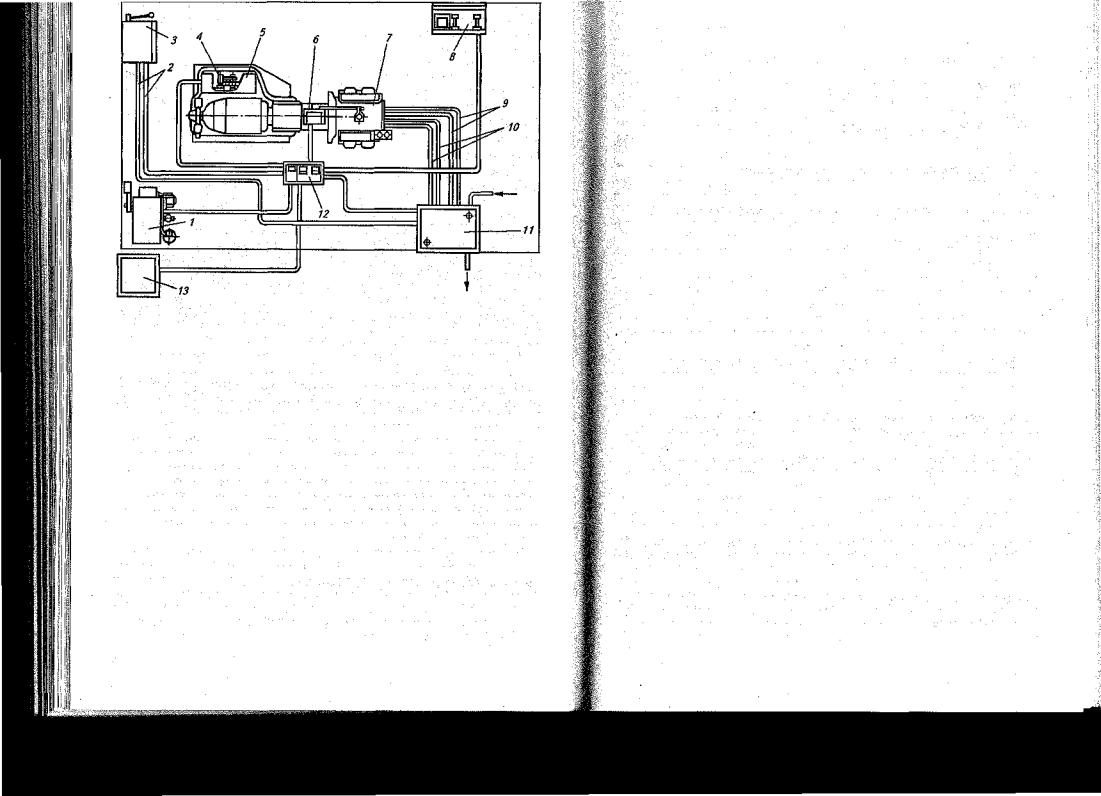
Рис. 2.30. Схема системы автоматизированного управления обкатки двигателя:
1 — реостат; 2— электрические связи; 3 — силовой шкаф; 4 — механизмлинеаризации; 5— весовой механизм; 6— исполнительный механизм управления заслонкой карбюратора; 7—двига- тель; 8— расходомер топлива; 9 — маслопроводы; 10— водопроводы; 11 — установка регулирования температуры воды и масла; 12 и 13— пульт и блок управления
Убедившись в исправности трансмиссии, заливают в картеры маловязкое маслодо номинального уровня и обкатывают по 10 мин на каждой передаче. Проверяют качество сборки, нагрев подшипников, надежность уплотнений и правильность регулировок.
Агрегаты трансмиссий колесных тракторов обкатывают также в сборе на стенде, который состоит из электродвигателя, закрепленного на подвижной плите; рамы, сваренной из уголков; специального приспособления, выполненного в виде диска. Диск соединен посредством муфты с валом электродвигателя. С помощью пневмоцилиндра электродвигатель, передвигаясь вместе с плитой на раме, прижимает приспособление к диску сцепления обкатываемой трансмиссии. Таким образом вращение от электродвигателя передаетсятрансмиссии.
Обкатку агрегатов ходовой части выполняют на специальных стендах. Так, для обкатки кареток гусеничных тракторов служит стенд, состоящий из двух продольных швеллеров. Последние соединены четырьмя поперечинами, на которых смон-
тированы электродвигатель и редуктор. Вращение передается от
электродвигателя через редуктор и цепную передачу на два вала, закрепленных в подшипниках на продольных швеллерах. На концах валов с обеих сторон расположены диски с четырьмя обрезинеянымипальцами.
Обкатываемые каретки устанавливаютна оси кронштейнов, расположенных с внешней стороны продольных швеллеров, так, чтобы обрезиненные пальцы попали между спицами катков. При включении электродвигателя пальцы, воздействуя на спицы, вращаюткатки.
После обкатки, испытания и устранения неисправностей отремонтированных агрегатов их устанавливают на машину, которую также обкатывают.
Обкатку машин после ремонта проводят на специальных стендах обкаточных участков либо пробегом на различных передачах.
Для обкатки двигателей и трансмиссии тракторов служат диагностические установки КИ-4935 ГосНИТИ.
После обкатки тракторов на стендах и устранения выявленных неисправностей рекомендуется сделать пробную поездку для опробования механизмов поворота и тормозов, гидросистемы и т. д., а затем устранить имеющиеся неисправности. Далее необходимо подтянуть гайки крепления головки блока на горя-. чем двигателе, спустить масло из всех картеров, промыть агрегаты дизельным топливом и заправить свежим маслом. У двигателя промывают также масляные, топливные фильтры и масляные каналы.
Механик-контролер окончательно проверяет отремонтированную машину. В первый период эксплуатации на ней работают с неполной нагрузкой, которую постепенно увеличивают до номи- •пальной.
2.9.ОКРАСКАМАШИН
Общие сведения о лакокрасочных материалах и покрытиях. Ла-
кокрасочные материалы представляют собой многокомпонентные составы, которые при нанесении их тонким слоем (30...100 мкм) на поверхность изделия образуют лакокрасочное покрытие, защищающее его от коррозии и придающее ему красивый внешний вид.
К основным компонентам таких материалов относят пленкообразующие вещества, растворители и пигменты. Кроме того, вихсоставмогутвходитьпластификаторы, сиккативы, наполiштелииразбавители.
Пленкообразующиевеществаспособствуютсклеиваниючастиц пигментов и наполнителей и созданию тонкой пленки, прочно удерживающейся на поверхности изделия. К ним относят: оли-
140 |
141 |
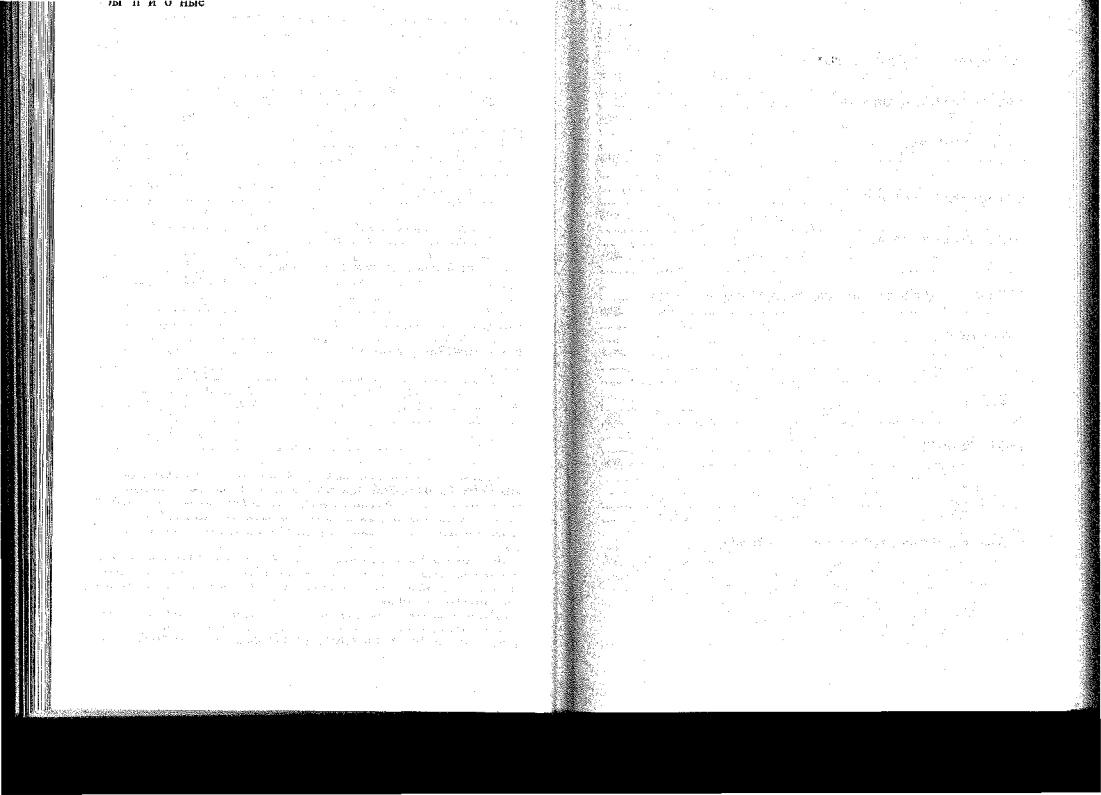
q , р р д |
и синтетические смолы, оитумы, асфальтены и |
эфиры. |
|
В зависимости от химического состава (рода пленкообразующего вещества) лакокрасочные материалы подразделяют на 42 основные группы (ГОСТ 9825): перхлорвиниловые — ХВ, пентафталевые — ПФ, глифталевые — ГФ, алкидно-акриловые — АС, сополи- мерно-акриловые — АК, нитроцеллюлозные — НЦ, фенольные — ФЛ, меламиновые — МЛ, алкидно- и масляно-стирольные — МС, эпоксидные — ЭП, полиуретановые — УР, кремнийорганические — КО, битумные — БТ и др.
Растворители — жидкости, применяемые для разведения лакокрасочных материалов до состояния, пригодного для нанесения на поверхность изделия. К ним относятся уайт-спирит, сольвент, бензол, толуол, ксилол, ацетон, спирт, бензин, а также многокомпонентные растворители, представляющие собой смесь отдельных растворителей с преобладающим содержанием одного из них. Например, растворитель РС-2 содержит 70 % по массе уайт-спирита и 30 % ксилола; растворитель № 646 — 10 % бутилацетата , 8 % этилцеллозольва, 7 % ацетона, 15 % бутилового спирта, 10 % этилового спирта и 50 % толуола.
Пигменты — это тонкоизмельченные цветные неорганические вещества, нерастворимые в воде, растворителях и пленкообразующих веществах и способные создавать с пленкообразующими веществами лакокрасочные покрытия. Их вводят в лакокрасочные материалы для придания им определенного цвета, повышения прочности и адгезии лакокрасочного покрытия.
По происхождению пигменты подразделяют на природные, синтетические и металлические. Первые (мумия коричневая, охра, железный сурик, сиена, умбра коричневая и др.) получают измельчением, обогащением и термической обработкой горных пород и минералов. Вторые (свинцовые белила, цинковые белила, зелень свинцовая, кобальт синий, свинцовый сурик, оксид хрома и др.) образуются в результате сложных технологических процессов. Третьи (золотистая бронза, алюминиевая пудра, цинковая пудра, медный порошок и др.) представляют собой тонкоизмельченные порошки цветных металлов и их сплавов.
Пластификаторы — вещества, вводимые в лакокрасочные материалы для повышения эластичности покрытий. Для пластификации пленкообразующих веществ, приготовленных на синтетических смолах, используют дибутилфталат, диметилфталат и диэтилфталат.
Сиккативы — вещества, ускоряющие процесс высыхания лакокрасочного покрытия. Например, нафтенатные жидкие сиккативы марок НФ-1 ...НФ-8, представляющие собой прозрачные растворы в органическом растворителе солей тяжелых металлов (марганец, свинец, кобальт) дистиллированных нафтеновых кислот, ускоряют высыхание масляных лаков, эмалевых и масляных красок.
142
Наполнители — порошкообразные неорганические вещества
(мел, баритовый концентрат, каолин, белила и др.), нерастворимые в иоде, растворителях и пленкообразующих веществах и добавляемые в лакокрасочные материалы для увеличения прочности и удешевления стоимости покрытий.
Разбавители — вещества, применяемые для разжижения лакокрасочных материалов, загустевших в период хранения, а также для их доведения до необходимой вязкости.
К о с н о в н ы м в и д а м готовых лакокрасочных материалов (ГОСТ 9825) относятся: лак, краска, порошковая краска, эмаль, грунтовка, шпатлевка и полуфабрикатный лак.
Лак — раствор пленкообразующих веществ в органических растворителях или в воде, образующий после высыхания твердую прозрачную однородную пленку (за исключением битумных лаков, которые образуют непрозрачную пленку).
Краска — суспензия пигмента или смеси пигментов с наполнителями в олифе, масле, эмульсии, латексе, образующая после высыхания непрозрачную однородную пленку.
Порошковая краска — сухая композиция пленкообразующего вещества с пигментами и наполнителями, образующая после сплавления, охлаждения и отверждения твердую непрозрачную пленку.
Эмаль — суспензия пигмента или смеси пигментов с наполнителями в лаке, образующая после высыхания непрозрачную твердую пленку с различным блеском и фактурой поверхности.
Грунтовка — суспензия пигмента или смеси пигментов с наполнителями в пленкообразующем веществе, образующая после высыхания непрозрачную однородную пленку с хорошей адгезией к поверхности изделия и верхним слоям лакокрасочного покрытия и предназначенная для повышения его защитных свойств.
Шпатлевка — суспензия смеси пигментов с наполнителями в ] глс11кообразующем веществе, используемая для заполнения неровностей и сглаживания окрашиваемой поверхности.
По назначению (применительно к условиям эксплуатации покрытий) основные лакокрасочные материалы (лаки, эмали, краски) делят на следующие группы: 1 — атмосферостойкие, 2 — ограниченно атмосферостойкие, 3 — консервационные, 4 — водостойкие, 5 — специальные, 6 — маслобензостойкие, 7 — химически стойкие, 8 — термостойкие, 9 — электроизоляционные и электропроводные.
При обозначении основного лакокрасочного материала указывают: вид материала (лак, краска, эмаль, грунтовка, шпатлевка), пленкообразующее вещество (МА, ПФ, ГФ, НЦ и т.д.), номер группы преимущественного назначения, присвоенный материалу порядковый номер, цвет и пр. Например, эмаль ПФ-133 — пентафталевая (ПФ) эмаль, атмосферостойкая (1), регистрационный номер 33; грунтовка ГФ-021 — глифталевая (ГФ) грунтовка (0), ре-
143
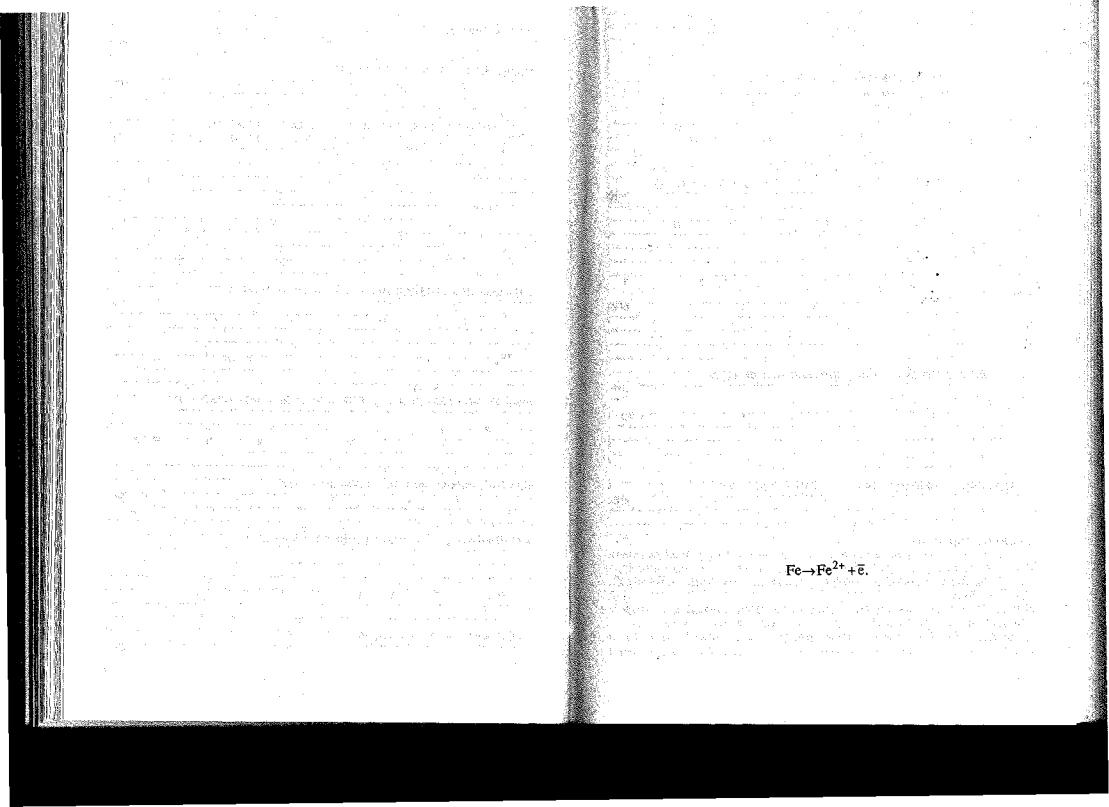
гастрационный номер21;шпатлевкаНЦ-008 — нитроцеллюлозная (НЦ) шпатлевка (00), регистрационный номер 8.
Лакокрасочные покрытия для сельскохозяйственной техники, как правило, состоят из слоя грунтовки, шпатлевки и одного или нескольких слоев эмали или краски.
Технологический процесс окраски машин. Процесс включает в себя: подготовку поверхности к окраске, грунтование, шпатлевание, нанесение наружных слоев покрытия, сушку и контроль качества покрытий.
Подготовка поверхности деталей машин к окраске. Лакокрасочные покрытия высокого качества могут быть получены только при тщательной очистке окрашиваемой поверхности от старой краски, продуктов коррозии, жировых идругих загрязнений. Присутствие на поверхности изделия загрязнений органического или неорганического происхождения снижает, а иногда и полностью исключает возможность образования адгезионных связей между окрашиваемой поверхностью.и покрытием. Некоторые из них могут вызвать подпленочную коррозию металла. При нанесении лакокрасочных материалов на хорошо очищенную поверхность капля материала смачивает окрашиваемую поверхность и растекается по ней.
Способ подготовки поверхности перед окраской выбирают в зависимости от сложности поверхности, размеров и материала изделий, условий эксплуатации, программы предприятия, степени и характера загрязнений, экономической целесообразности и других факторов. В ремонтном производстве наиболее часто предварительно поверхности деталей обезжиривают щелочными растворами, органическими растворителями и пароструйным способом.
В качестве щелочных растворов используют водные растворы синтетических моющих средств МЛ-51, МЛ-52, МС-6, МС-8, МС-15, МС-17, МС-37, Лабомид-101, Лабомид-102, Лабомид-203, КМ-1 и Темп-100. Обезжириваютв моечных машинахили агрегатах для подготовки поверхности. Эти растворы пожаро- и взрывобезопасны, а также нетоксичны.
Из органических растворителей применяют бензин и уайт-спи- рит. С помощью них поверхности изделий протирают ветошью или промывают в ваннах. Однако такие растворители горючи, взрывоопасныитоксичны.
Более пригодныдля обезжиривания негорючие и невзрывоопасные хлорированные углеводороды (трихлорэтилен, перхлорэтилен, метиленхлорид, четыреххлористый углерод), хорошо растворяющие жировые загрязнения. Недостаток этих растворителей — токсичность паров. Поэтому обезжиривание хлорированными углеводородами возможно только на оборудовании, обеспечивающем безопасность обслуживающего персонала.
Сущность пароструйного способа обезжиривания заключается в
воздействии на очищаемую поверхность пароводяной струи при температуре60...95 "Сидавлении0,8...2 МПа.Дляповышенияэффекпжности в воду добавляют моющие средства. Такое обезжиривание проводят с помощью моечных машин ОМ-5359, ОМ-5360 и ОМ-2216.
Поверхности изделий, покрытых ржавчиной, перед окраской часто не очищают. Их обрабатывают химически активными веществами — модификаторами коррозии или преобразователями ржавчины, основным компонентом которых служит ортофосфорная кислота. Например, преобразователь ржавчины П-1Т содержит, %: ортофосфорной кислоты 10...15, танина 10, ацетона 10, бутанола 5...10, углекислого бария 10, хромата цинка 10 и этилового спирта 10.
Переднанесением преобразователей ржавчины поверхности изделия очищают от рыхлой и пластовой ржавчины механическим способом, а затем обезжиривают от масляных загрязнений уайтспиритом иливоднымраствором ОП-7. Толщинапродуктов коррозии на поверхностидетали недолжнапревышать 100 мкм. Преобразователи ржавчины наносяткистью иликраскораспылителем. После высыхания его рекомендуется дополнительно смачивать водой дляповышенияэффективности.
Преобразователи ржавчины преобразуют продукты коррозии железа в защитный слой химически стойких нерастворимых соединений с высокой адгезией к поверхности металла. Ортофосфорная кислота образует с ржавчиной труднорастворимые гидрофосфаты, а комплекеробразователи (танин) переводят оксидыжелеза в таннатныекомплексы.
Для повышения защитной способности против коррозии стальные изделия фосфатируют. На поверхности образуется тонкая (I ...3 мкм) защитная пленка нерастворимых солей ортофосфорной кислоты, улучшающая коррозионную стойкость покрытия и его адгезию к поверхности изделия. Фосфатируютв водных растворах моиофосфатов тяжелых металлов (цинк, железо, марганец) или щелочных металлов и аммония, иногда сдобавлением свободной фосфорной кислоты.
Образование фосфатного слоя протекает по электрохимическому механизму. Реакция начинается втонком слое раствора, примыкающего к поверхности изделия, при определенном значении рН. 11а аноде металл растворяется:
На катоде происходит водородная деполяризация: 2Н+ +2ё->Н2Т.
В результате катодного процесса концентрация протонов в при-
144 |
145 |

электродном слое уменьшается. Порог осаждения кристаллических
фосфатных пленок наступает при приближении рН к 4. Уравнения гидролитического равновесия для гидрофосфатов имеют вид
3Zn2++2H2PC>4 Zn3 (PO4 )2 +2H+ ;
3Fe2++2H2PC>4 Fe3 (PO4 )2 +4H+ .
По достижении рН, соответствующего началу осаждения, на поверхности изделия начинает образовываться пленка
Zn3(PO4)2•Fe3(PO4)2.
Для увеличения скорости фосфатирования в фосфатирующие растворы вводят ускорители, в качестве которых служат окислители (азотная и азотистая кислоты и их соли) и ионы меди и никеля. Составы готовят на основе монофосфата цинка, который гидролизуется легче, чем фосфаты железа и марганца. Для фосфатирования кузовов легковых автомобилей и кабин грузовых автомобилей применяют фосфатирующий концентрат (цинковый фосфат) КФ-1.
Г р у н т о в а н и е . Эту операцию следует проводить в возможно более короткий срок после подготовки поверхности к нанесению лакокрасочного покрытия. На подготовленную поверхность изделия наносят первый слой лакокрасочного покрытия — грунтовку, которая служит основой покрытия. Она предназначена для создания прочного антикоррозионного слоя, имеющего высокую сцепляемость с металлом и последующими слоями лакокрасочного покрытия.
Разведенную до рабочей вязкости грунтовку наносят на поверхность изделия краскораспылителем, электроосаждением или кистью. Грунт должен ложиться ровным тонким слоем, без пропусков и подтеков. С особой тщательностью его наносят на сварные швы, стараясь заполнить все поры.
При использовании грунтовки заниженной вязкости образуется слишкомтонкий слой, не способный защититьметалл откоррозии, а при нанесении грунтовки завышенной вязкости не достигается адгезия грунтовки с металлом и последующими слоями лакокрасочногопокрытия.
На ремонтных предприятиях с небольшой программой ремонта изделия не фосфатируют. На подготовленную к окраске поверхность наносят грунтовки — преобразователи ржавчины ВА-0112, ВА-01-ГИСИ или фосфатирующие грунтовки ВЛ-08, ВЛ-023 и ВЛ-02. Их можно применять и для ржавых поверхностей, с которых удаляют рыхлые и пластовые продукты коррозии.
Грунтовки — преобразователи ржавчины состоят из основы и кислотного отвердителя (ортофосфорной кислоты). Грунтовки
ВА-0112 и ВА-01-ГИСИ готовят непосредственно перед употреб-
лением, смешивая основу и кислотный отвердитель. Для приготоиления ВА-0112 на 100 частей по массе основы берут три части орюфосфорной кислоты, а для ВА-01-ГИСИ— пять—семь частоii.
Ш п а т л е в а н и е . Эта операция предназначена для сглаживания шероховатостей и незначительных неровностей на окрашиваемом поверхности. Шпатлевка представляет собой густую пастооб- p;i шую массу. Она состоит из пигментов и наполнителей, затертых ми различныхлаках.
После высыхания шпатлевка должна иметь высокую адгезию к грунтовочному слою и последующим слоям лакокрасочного покры i ия, быть твердой, хорошо шлифоваться, не набухать и не выкрашиваться при мокром шлифовании. Она не повышает защитные ci;oiicTBa лакокрасочного покрытия, но снижает его механическую прочность. Ее толстый слой может быть причиной растрескивания лакокрасочного покрытия, так как он недостаточно эластичен. Полому шпатлевать следует слоями толщиной 0,1 ...0,5 мм, а толщина иссх слоев не должна превышать 0,5...2,0 мм. Слой наибольшей толщины (2...5 мм) можно нанести при использовании эпоксидной шпатлевки ЭП-0010. Не рекомендуется использовать более пяти слое» шпатлевки.
11осле высыхания каждого слоя покрытия шлифуют сухим или мокрым способом для устранения неровностей и шероховатости, улучшения адгезии и внешнего вида. При сухом способе используЮ1 шлифовальныешкуркинатканевойилибумажнойоснове, апри мокром — водостойкие шлифовальные шкурки.
Для шлифования широко применяют электрические аппараты различной конструкции, такие, как электрические шлифовальные уиюиые машины ИЭ-2102Аи ИЭ-2103А, пневматические машины РД-!, ОПМ-3 и ОПМ-4. При ручном шлифовании шкурку надеваюi на шлифовальный резиновый блокили колодку из мягкогодерева. Промежуточные слои шпатлевки обрабатывают шлифовальными шкурками № 8...6, а последний слой — № 6...5.
Н а н е с е н и е н а р у ж н ы х слоев л а к о к р а с о ч н о г о и о к р ы т и я. Эта операция зависит от требований, предъявляемых к внешнему виду окрашиваемых поверхностей. Лакокрасочное покры 1 ие можетбытьдекоративным (улегковыхавтомобилей), обыкпопенным (у грузовых автомобилей и тракторов) и защитным (у сельскохозяйственных машин).
Для получения декоративных покрытий выполняют многослойную окраску, уделяя особое внимание отделочным работам. 11а кузова легковых автомобилей наносят до шести слоев нитро- •jMiuiii или до трех слоев синтетической эмали. Каждый последующий слой наносят на хорошо просушенный нижележащий слой, чк> не выполняют при окраске синтетическими и некоторыми ;.ipyi ими эмалями.
146 |
147 |