
Сварка. Оконч
.pdf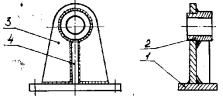
ляют конструктору просто механически повторять готовые решения. Поэтому проектирование является каждый раз творческой задачей, не исключающей, но допускающей разумную конструктивную преемственность.
Элементы сварных конструкций
Сварные изделия типа кронштейнов, шкивов, зубчатых колес принято считать деталями, хотя это, строго говоря, не соответствуют определению самого понятия «деталь», т. к. они собираются из нескольких элементов. Сварные рамы, станины, корпуса, балки относят уже к узлам. Форма и размеры отдельных элементов сварных конструкций определяются их назначением, воспринимаемыми нагрузками и типом заготовок. Например, на рис. 1 показана конструкция сварного кронштейна, предназначенного для закрепления оси блока.
Рис. 1. Сварной кронштейн
Кронштейн состоит из опорной подошвы (1), которой он крепится к раме, втулки (2), где непосредственно устанавливается ось. Втулка опирается на стенку (3). Для обеспечения необходимой жёсткости в конструкции кронштейна предусмотрено ребро (4). Все детали соединены сваркой. Отдельные элементы кронштейна изготовлены из простых заготовок: втулка — из трубы, подошва, стенка и ребро — из листового проката.
Назначая размеры на заготовки, конструктор должен исходить из возможностей существующих стандартов на прокат. Особенно это касается тех поверхностей, которые не подвергаются механической обработке. В приведённом примере наружный диаметр втулки не может быть равным 62 мм, так как по ГОСТ 8732–78 этого диаметра нет. Ближайший к нему 60 мм и 63 мм. Следовательно, наружный диаметр втулки может быть либо 60 мм, либо 63 мм.
Для сварных изделий используют сортовой, фасонный, листовой прокат, трубы, а также литые и кованые заготовки. Из фасонного проката наиболее часто используют сталь прокатную угловую (ГОСТ 8509–93), балки двутавровые (ГОСТ 8239–89), швеллеры (ГОСТ 8240–89), а также трубы водогазопроводные (ГОСТ 3262–75), бесшовные холоднотянутые (ГОСТ 8734–75) и горячекатаные (ГОСТ 8732–78) диаметром до 820 мм.
Наибольшее применение находит листовой прокат: толстолистовой (горячекатаный) с толщиной 4 ... 160 мм (ГОСТ 19903–74) и тонколистовой (холоднокатаный) (ГОСТ 19904–90).
21
Таблица 1
Предельные отклонения толщины горячекатаного листового проката нормальной точности
Толщина листа, мм |
Предельные |
Толщина, мм |
Предельные |
|
|
|
отклонения, |
|
отклонения, мм |
|
|
мм |
|
|
|
|
|
|
|
свыше 4 до 5,5 |
+0,2–0,5 |
свыше 60 до 70 |
+0,7–16 |
|
|
|
|
|
|
свыше 5,5 |
до 7,5 |
+0,25–0,6 |
свыше 70 до 80 |
+0,7–2,2 |
|
|
|
|
|
свыше 7,5 до 25 |
+0,3–0,8 |
свыше 80 до 90 |
+0,8–2,5 |
|
|
|
|
|
|
свыше 25 |
до 30 |
+0,3–0,9 |
свыше 90 до |
+0,9–2,7 |
|
|
|
100 |
|
свыше 30 |
до 34 |
+0,3–1,0 |
свыше 100 до |
+1,1–3,1 |
|
|
|
115 |
|
свыше 34 |
до 40 |
+0,4–1,1 |
свыше 115 до |
+1,4–3,5 |
|
|
|
125 |
|
свыше 40 |
до 50 |
+0,5–1,2 |
свыше 125 до |
+1,6–3,8 |
|
|
|
140 |
|
|
|
|
|
|
свыше 50 |
до 60 |
+0,3–1,3 |
свыше 140 до |
+1,9–4,2 |
|
|
|
160 |
|
Толщина листовой стали по сортаменту составляет 0,5 ... 0,8 (через 0,05 мм); 0,9 ... 1,8 (через0,1 мм); 2; 2,2; 2,5; 2,8; 3; 3,2; 3,5; 3,8; 4; 4,5; 5 ... 22 (через 1 мм); 25; 26 ... 42 (через 2 мм); 45; 48; 50; 52; 55... 110 (через 5 мм ); 120; 125; 130; 140; 150; 160 мм. (Сортамент на конкретных предприятиях может иметь ограничение).
ГОСТ 19903–74 регламентирует, кроме толщины, размеры по ширине, длине, а также предельные отклонения размеров. Предельные отклонения толщины горячекатаной листовой стали нормальной точности при ширине листов
1000 … 1500 мм даны в тaбл. 1.
Ширина листов — 500 ... 1000 (через 50 мм) 1100; 1250; 1406; 1420; 1500
... 3000 (через 100 мм); 3200 ... 3800 (через 260 мм). При этом длина может быть от 1000 до 12000 мм:
Холоднокатаный прокат может поставляться и в рулонах массой до 20 т. Листовой прокат бывает повышенной (группа А) и нормальной точности (группа Б) пo толщине. Изготавливают листовой прокат из сталей угле-
родистых обычного качества (ГОСТ 380–71), углеродистых качественных (ГОСТ 1050–74), низколегированных (ГОСТ 19282–73), легированных качественных (ГОСТ4543–71), высоколегированных коррозионностойких и жаростойких (ГОСТ 5632–72) и других сплавов специального назначения.
22
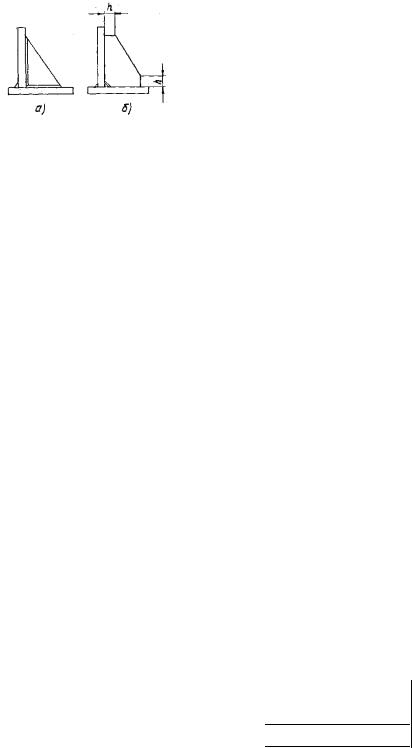
Пример обозначения толстолистого проката горячекатаного группы Б, толщиной 25 мм из стали 20 без указания размеров листа:
лист |
Б25 ГОСТ 19903 – 74 |
. |
|
сталь 20 ГОСТ 1050 – 88 |
При разработке конструкции рёбер жёсткости, косынок и других подобных им деталей следует избегать острых углов (Рис. 2.2), так как в зоне острого угла металл элемента при сварке оплавляется и не обеспечивается полноценность шва. Поэтому перед сваркой острые углы надо срезать так, чтобы размер h (Рис. 2) был в 2–3 раза больше катета шва.
Рис. 2. Приварка ребра: а — неправильно; б — правильно
Приварка рёбер жёсткости приводит к концентрации напряжений. Для уменьшения её рекомендуется ребра приваривать с двух сторон.
Необходимость применять в отдельных случаях гибку элементов предъявляет свои требования к конструкции. Места сгиба изогнутых элементов очерчиваются по наружному и внутреннему контуру радиусами концентричных окружностей, то есть R r (Рис. 3, а). Неправильное изображение согнутого элемента показано на Рис. 3, б и 3, в.
Величина радиуса r зависит от материала детали, его состояния и направления волокон относительно гибки. Наименьшие допустимые радиусы гибки листов и полос в зависимости от толщины металла приведены в Табл. 2.
Наименьший допустимый радиус гибки профильного металла в холодном состоянии рекомендуют брать равным 25-кратной толщине или высоте симметричного профиля.
Рис. 3. Гибка листов: а — правильно; б и в — неправильно
Таблица 2
Наименьшие радиусы гибки листового материала
Материал |
Радиус, мм |
Материал |
Радиус, мм |
Сталь 15, 20, Ст. 3 |
0,1 |
Сталь 35, 40, Ст. 5 |
0,3 |
Сталь 25, 30,Ст. 4 |
0,2 |
Сталь 45, 50, Ст. 6 |
0,5 |
|
|
23 |
|
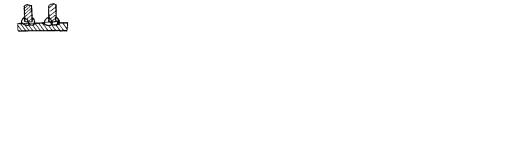
Максимальная простота конфигурации элементов сварных деталей из сортового проката является основным условием технологичности их конструкций. Существенным фактором повышений технологичности сварных деталей и конструкций является уменьшение числа типоразмеров элементов, необоснованного разнообразия толщины листового проката, диаметра прутков, труб, номеров профилей и т. д.
Технологичность сварных конструкций
В производстве сварных конструкций немаловажное значение играет форма и размеры изделия. Подавляющее количество брака вызывается нетехнологичностью конструкции, поэтому конструктор в своей работе должен четко представлять, как будут осуществлять сварку изделия. Исходя из практики сварочных работ, выполнен целый ряд рекомендаций и требований к сварным конструкциям. Наиболее важными будут требования, приводимые ниже.
1. Расположение сварного шва должно обеспечивать доступность сварки, т. е. необходимо предусмотреть удобство подвода электрода или сварочной проволоки (Рис. 4, а).
2. Протяжённость сварных швов и их количество должно быть минимальным. С этой целью целесообразно применять штампованные заготовки, трубы, гнутые профили и т. п. При этом необходимо унифицировать заготовки.
3.Прямолинейные и кольцевые сварные швы более предпочтительны, так как позволяют применять автоматическую сварку, сократить расход электродов, повысить точность изделий, упростить подготовку кромок и раскрой заготовок.
4.Стыковые соединения обладают большей несущей способностью и являются, как правило, более технологичными.
5.Во избежание прожога соединяемых кромок целесообразно предусматриватьсъёмныеилиостающиесяподкладкиилипредварительнуюподваркукорняшва.
6.Расположения сварных швов по возможности должно исключать необходимость кантовки конструкции, при этом следует помнить, что потолочные сварные швы являются не технологичными.
7.Необходимо предусматривать фиксацию соединяемых деталей проточками, буртиками и т. п., это повышает точность, производительность труда и удобство при сварке (Рис. 4, в).
|
Нетехнологично |
Техноло- |
Нетехноло- |
Технологично |
|
|
|
|
гично |
гично |
|
а |
|
|
д |
|
|
|
|
|
|
|
|
б |
|
|
е |
|
|
|
|
|
|
|
|
в |
|
|
ж |
|
|
|
|
|
|
|
|
г |
|
|
з |
|
|
|
|
|
|
|
|
Рис. 4. Примеры технологичности сварных конструкций
24
8.Разделка кромок является трудоёмкой операцией, её следует назначать только в необходимых случаях и предусматривать наиболее простые способы обработки (Рис. 4, г).
9.Нельзя создавать концентрацию наплавленного металла (Рис. 4, д).
10.Следует избегать сварки элементов с разной толщиной, это усложняет сварку, снижает надёжность сварных швов и создаёт концентрацию напряжений (Рис. 4, е, ж).
11.Конструкция изделия должна исключать подгонку деталей при сварке, поэтому нецелесообразны криволинейные и угловые сопряжения (Рис. 4, з).
12.При проектировании сварных конструкций необходимо учитывать возможность коробления и взаимного смещения деталей.
13.Точные элементы деталей (резьба, шлицы, сопрягаемые поверхности)
впроцессе свалки могут получить повреждения из-за разбрызгивания металла, коробления, механических воздействий и др. Необходимо предусматривать защитные мероприятия, удаление от зоны сварки или окончательную обработку после сварки.
Технологические требования к конструкциям специального назначения (резервуары, балки, станины и т. д.) имеют свои особенности и учитывают специфику сборки и сварки.
Точность сварных конструкции и заготовок зависит от многих факторов и оценка её студентами при выполнении курсовой работы затруднительна. На точность сварного изделия влияют деформация в процессе сварки, точность изготовления исходных заготовок, точность сборки перед сваркой и т. п.
Наибольшую погрешность форм и линейных размеров сварного изделия вносят сварочные деформации, т. е. поводка и коробление. Учесть влияние данных факторов не представляется возможным, так как сварочные деформации зависят от формы изделия, вида сварки и её режимов, наличия и жёсткости сборочных приспособлений и т. д. Для конкретных изделий могут быть использованы расчётные методы оценки точности.
Большинство сварных изделий в машиностроении имеют предельные отклонения размеров в соответствии с 16–17 квалитетами точности (± IT16 / 2;
± IT17 / 2) или «грубым» (± t3 / 2) и «очень грубым» (± t4 / 2) классами точности ГОСТ 25670–83. Меньшие предельные отклонения размеров соответствуют условиям сварки при использовании точных сборочных приспособлений и надёжной фиксации деталей в процессе сварки.
Допускаемые предельные отклонения линейных размеров должны быть учтены при проектировании сварного изделия, исходных деталей и назначении припусков на механическую обработку.
25
Таблица 3
Числовые значения симметричных предельных отклонений линейных размеров и рекомендуемых припусков на механическую обработку
Интервал размеров, мм |
Предельные откло- |
Односторонний при- |
|||
|
|
нения, мм |
пуск на механическую |
||
|
|
|
|
обработку, мм |
|
|
|
± t3 / 2 |
± t4 / 2 |
||
|
|
|
|
||
|
|
|
|
|
|
Св. 30 до 120 |
± 0,8 |
± 1,5 |
3 |
... 7 |
|
|
|
|
|
|
|
Св. 120 |
до 315 |
± 1,2 |
± 2 |
3 |
... 7 |
|
|
|
|
|
|
Св. 315 до 1000 |
± 2 |
± 3 |
3 |
... 7 |
|
|
|
|
|
|
|
Св. 1000 |
до 2000 |
± 3 |
± 5 |
8 … 10 |
|
|
|
|
|
|
|
Св. 2000 |
до 3150 |
± 5 |
± 8 |
10 |
... 15 |
|
|
|
|
|
|
Св. 3150 |
до 5000 |
± 8 |
± 12 |
12 |
... 16 |
|
|
|
|
|
|
В табл. 3 приведены рекомендуемые заводами тяжёлого машиностроения припуски на механическую обработку после сварки, а также предельные отклонения линейных размеров для «грубого» и «очень грубого» классов точности, соответствующих сварным конструкциям.
При назначении припусков на механическую обработку свариваемых деталей должны учитываться предельные отклонения размеров и формы исходных заготовок сортового и листового проката, труб, отливок, поковок и т. п., которые приводятся в соответствующих стандартах.
Номинальные размеры свариваемых деталей и их предельные отклонения выбирают из условия обеспечения размеров изделия после сварки, а также из условий, обеспечивающих сборку деталей перед сваркой. При этом необходимо руководствоваться правилами составления размерных цепей, известных из курса «Взаимозаменяемость, стандартизация и технические измерения».
Сварные конструкции деталей машин
Сварные детали машин нашли широкое применение в различных отраслях машиностроения. Рассмотрим некоторые характерные примеры сварных конструкций.
Зубчатые колеса
На Рис. 5 показан блок шестерен коробки передач в двух вариантах. Изготовление блока шестерен из двух поковок путём сварки даёт экономию стали на 30–40 %.
26
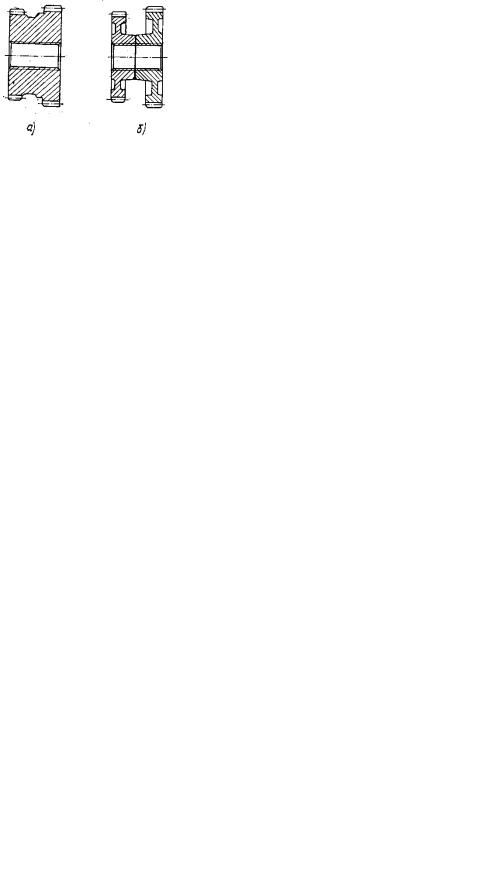
Рис. 5. Блок шестерён коробки передач цельно-штампованой (а) и сварной (б) конструкции
Сварные зубчатые колеса изготавливают уже при наружном диаметре больше 250–300 мм, чаще — при >1600 мм. Применение сварных колес вместо литых экономит до 30–40 % металла, уменьшает объём механической обработки, обеспечивает однородность механических свойств и более рациональное использование материала высокого качества.
Основные элементы сварного зубчатого колеса — обод, ступица, диск (или диски), рёбра. При диаметре меньше 350 мм применяют конструкцию с одним диском без рёбер (Рис. 2.6, б), при da 350 мм с рёбрами жёсткости (Рис. 6, а).
Конструкции сварных зубчатых колёс со сплошным центром показаны на Рис. 6, в.
Обод сварного колеса обычно изготавливают из углеродистой стали повышенного качества, например, из сталей 35, 45. Ступицу, диск и ребра изготавливают из малоуглеродистых сталей.
Соединение ступицы с диском целесообразно выполнять с подготовкой кромок при сварке вручную. При этом уменьшается концентрация напряжений в соединениях и, следовательно, увеличивается выносливость конструкции. Если сварка ведётся на автоматах под слоем флюса, такой необходимости не возникает благодаря глубокому проплавлению металла.
Основные геометрические размеры и соотношения сварных зубчатых колёс остаются такими же, как и для целых колёс. После сварки шестерни подвергают отпуску для снятия остаточных напряжений. Затем производят механическую обработку и нарезку колеса.
а
б |
в |
Рис. 6. Конструкции сварных зубчатых колёс:
а) с ободом с рёбрами; б) с ободом без рёбер; в) со сплошным диском
27
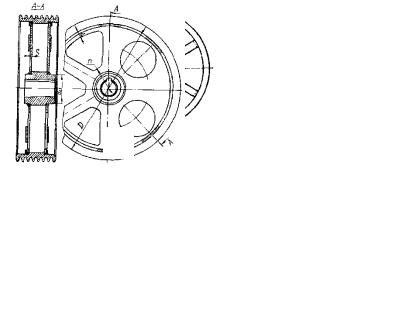
Шкивы ременных передач
Сварные шкивы ременных передач обычно изготовляют из стали, начиная с D>1500–600 мм, так как в этом случае сварные шкивы легче литых. Сварные шкивы особенно выгодны в индивидуальном и мелкосерийном производстве: отпадают расходы на изготовление моделей.
В сварных шкивах обод выполняют вальцованным из полосовой стали и сваривают односторонним или двухсторонним стыковым швом. Ступицы — из круглого проката или поковок. Ступицы к ободу крепят с помощью дисков: одного при мощности менее 30 кВт и В 350 мм; и двух — при большей мощности и ширине. С целью уменьшения веса и удобства сварки при двух дисках в них вырезают круглые или грушевидные отверстия (Рис. 7, а, б). Для повышения жёсткости приваривают рёбра (Рис. 7, в). Иногда вместо дисков ставят спицы из полосовой стали или труб. Шкивы со спицами легче, но состоят из большего числа деталей и поэтому сложнее в изготовлении, применяются при мощности менее 30 кВт.
Материалом для обода и диска служит сталь Ст 3; ступицы — Ст 5. Рёбра жёсткости выполняют из стали Ст 3 или Ст 0.
аб)
в) г)
Рис. 7. Конструкции сварных шкивов для плоских ремней: а — с одним диском; б — с двумя дисками; в — со спицами; г — для клиновых ремней
Корпуса редукторов и кронштейны
В последние годы всё шире применяют сварные корпусные детали и кронштейны. Экономически это выгодно для машин, выпускаемых в одиночных экземплярах. Сварную деталь, в случае необходимости, можно исправить, увеличить ее жёсткость. При этом отпадает необходимость в изготовлении моделей. Однако фактическая экономия в расходе металла при замене чугунной детали сварной зависит от конструктивного оформления и нагруженности детали. При одинаковых размерах сильно нагруженные корпусные детали в сварном варианте получаются меньше весом, так как стенки могут быть более тонкими. Но сварной
28
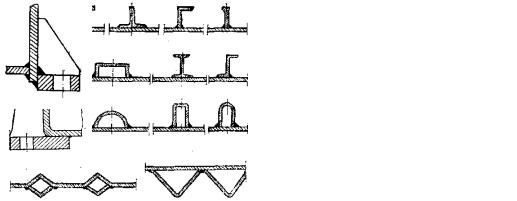
корпус состоит из большого числа деталей, вместо одной, которые необходимо соединить между собой, что приводит к удорожанию изготовления.
Для корпусных деталей большое значение имеет жёсткость всей конструкции, поскольку именно она определяет точность взаимного расположения подшипниковых гнёзд и валов редуктора. Из условия жёсткости несущие вертикальные стенки усиливаются рёбрами, которые могут быть как из листа или полосы, так и других профилей (Рис. 8, а). Перспективно применение для этих целей гнутых элементов.
а) |
б) |
в) |
Рис. 8. Усиление вертикальных стенок (а), мест под крепёжные болты (в) и увеличение жёсткости опорных фланцев (б) корпуса редуктора
Толщина фланцев плоскости разъёма должна быть достаточной, чтобы обеспечить жёсткость корпуса и герметичность редуктора. Фланцы изготовляют из полос. Ширина и толщина их должны соответствовать ГОСТу на полосовую сталь. Ширина фланца выбирается по условию размещения болтов.
Для крепления корпуса редуктора к раме делают фланцы из полосы или листа. Фланцы приваривают вдоль длины редуктора. Для увеличения жёсткости толщину опорных фланцев принимают не меньше 1,5 диаметра отверстия и связывают их с бобышками под подшипники рёбрами (Рис. 8, б). Места постановки болтов, крепящих редуктор к раме, дополнительно усиливают рёбрами для предотвращения возможной деформации лап при затягивании гаек (Рис. 8, в). Опорные поверхности под головки болтов и гаек можно дополнительно не обрабатывать, если обеспечивается их достаточная плоскостность (отклонения не больше 1°).
Корпус редуктора требует точного изготовления, поэтому после сварки его подвергают отпуску, и механическая обработка производится после него.
Рамы приводов
Рамы входят в состав различных машин и конструкции. Они связывают в одно целое отдельные части и механизмы Рамы должны быть достаточно жёсткими, прочными, удовлетворять требованию рациональной компоновки узлов.
Проектирование сварных рам ведут из профильного (уголков, швеллеров, двутавров) или листового проката. Весьма перспективно применение гнутых профилей.
29
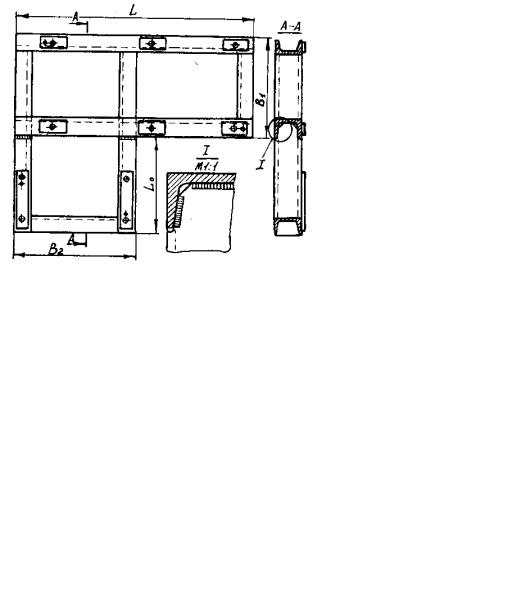
Пример сварной рамы для установки двигателя и редуктора показан на рис. 9.
На рис. 10 показаны различные способы соединения деталей. Профили деталей, примыкающих к прокатным, следует при этом предварительно подготовить механической обработкой. Детали в процессе сварки деформируются, поэтому часто базовые поверхности (специально приваренные платики) окончательно обрабатывают после сварки. Базой при этом служит нижняя поверхность рамы (в условиях единичного производства она обычно остаётся чёрной).
Поверхности рамы, подвергаемые обработке, желательно располагать в одной плоскости. При расположении платиков на разных уровнях конструкция рамы несколько усложняется. Размер H1 , определяющий разность высот плати-
ков, получают приваркой швеллеров, уголков, полос (Рис. 10, в).
Рис. 9. Сварная рама для установки двигателя и редуктора
а)
б)
в)
Рис. 10. Соединение элементов рамы непосредственно (а), с помощью косынок (б) и с опорными платиками на разных уровнях
30