
- •ИЗДАНИЕ ВТОРОЕ, ПЕРЕРАБОТАННОЕ И ДОПОЛНЕННОЕ
- •ОСНОВНЫЕ СХЕМЫ ПРОИЗВОДСТВА ГАЗА ДЛЯ СИНТЕЗА АММИАКА
- •ОСНОВЫ ПРОЦЕССОВ ОЧИСТКИ ГАЗОВ
- •Циркуляционные процессы
- •ОЧИСТКА ПРИРОДНОГО ГАЗА ОТ ВЫСШИХ УГЛЕВОДОРОДОВ
- •АБСОРБЦИОННЫЕ МЕТОДЫ ОЧИСТКИ ГАЗОВ ОТ ДВУОКИСИ УГЛЕРОДА И СЕРНИСТЫХ СОЕДИНЕНИЙ
- •Примеры расчета абсорберов МЭА-очистки
- •Катализаторы
- •Кинетика и механизм процесса гидрирования
- •Аппаратурно-технологическое оформление процесса
- •АБСОРБЦИОННЫЕ СПОСОБЫ ОЧИСТКИ ГАЗОВ ОТ СЕРНИСТЫХ СОЕДИНЕНИЙ
- •ОЧИСТКА ГАЗОВ ОТ ОКИСИ УГЛЕРОДА
- •КАТАЛИТИЧЕСКИЕ И АДСОРБЦИОННЫЕ МЕТОДЫ УДАЛЕНИЯ ИЗ СИНТЕЗ-ГАЗА КИСЛОРОДСОДЕРЖАЩИХ СОЕДИНЕНИИ
- •Катализаторы
- •Аппаратурно-технологическое оформление
- •Катализаторы
- •2. ТОНКАЯ ОЧИСТКА ОТ ДВУОКИСИ УГЛЕРОДА МЕТОДОМ АДСОРБЦИИ
- •ОЧИСТКА ГАЗОВ ОТ ОКИСИ АЗОТА И АЦЕТИЛЕНА
- •2. СПОСОБ ОЧИСТКИ ОТ ОКИСИ АЗОТА И АЦЕТИЛЕНА МЕТОДОМ КАТАЛИТИЧЕСКОГО ГИДРИРОВАНИЯ
- •АБСОРБЦИОННЫЕ МЕТОДЫ ОЧИСТКИ ГАЗОВ ОТ АЦЕТИЛЕНА
- •Очистка пирогаза от сажи
на тарелку и выходе с нее. Пользуясь уравнением материального баланса нижней тарелки, определяют концентрацию свободного амина в растворе на входе на данную тарелку. По уравнению тепло вого баланса нижней тарелки находят температуру раствора, посту пающего на нее. Затем определяют параметры следующей (выше
лежащей) тарелки и продолжают расчет тарелок |
в верхней зоне |
||
до тех пор, |
пока |
найденная концентрация С 02 на |
выходе с п-ной |
тарелки не |
станет |
меньше заданной концентрации |
С 02 на выходе |
из абсорбера.
Рекомендуемый метод учитывает изменение коэффициента массо-
передачи 'и движущей силы по высоте абсорбера. |
|
При расчете тарелок в нижней зоне (при а > 0,5) |
исходят, как |
и при расчете насадочного аппарата, из совместного |
рассмотрения |
уравнений (IV,29)—(IV,35). Расчет ведут, начиная с нижней'та релки абсорбера. Для нахождения Лр используют значение концен трации СО2 в газе на входе в абсорбер. В результате расчета опре деляют концентрацию С 02 на выходе с нижней тарелки и степень карбонизации раствора, поступающего на нее, и начинают расчет второй (по ходу газа) тарелки. Вычисления продолжают до тех пор, пока концентрация СО2 в газе на выходе с тг-ной тарелки не станет несколько меньше концентрации С 02 в промежуточном сечении абсорбера (а ^ 0 ,5 ).
Примеры расчета абсорберов МЭА-очистки
Пример 1 . Рассчитать по эмпирическим данным высоту слоя седловидной насадки размером 50 мм в- абсорбере МЭА-очистки, необходимую для извле чения СО2 из конвертированного газа с 21 до 5% (об.) при давлении, близком к атмосферному. Расход газа 12 000 м3/ч (при н. у.), диаметр абсорбера 2 м, концентрация МЭА 2,4 кмоль/м3, степень карбонизации регенерированного раствора а 2 = 0,2 кмоль/кмоль, средняя по высоте температура раствора 40 °С.
Принимаем а х = 0,46 кмоль/кмоль. Количество поглощенной С 02 (при
=• У-)
12000 (0.21—0.05)
|
|
1 -0 ,0 5 |
= 2 0 2 0 мз/ч |
Расход раствора |
|
|
|
|
2020 |
|
|
|
|
|
|
(0 .46 -0,2). 22,4-2,4 = 144,5 мз/ч |
|||
Для колец Рапшга (см. рис. VI-26) |
Кта ^ 500 м3/(м3 *ч*кгс/см2). С учетом |
||
большей эффективности |
массопёредачи |
на седловидных насадках (стр. 7 5 ) |
|
К[а = 500*1,2 = 600 м3/(м3 *ч • кгс/см2). |
|
||
Средняя движущая |
сила |
|
|
|
0,21 —0,05 |
0,1114 кгс/см2 |
|
|
|
= |
|
|
о о , |
0,21 |
|
|
2 ,3 |
0,05 |
|
Высота насадочного слоя
2020
600 • 0,1114 • 0.785 • 2а |
9 ,6 5 м |
Пример 2. Рассчитать с помощью математической модели необратимой
хемосорбции (стр. 70) содержание С 02 в газе па выходе |
из абсорбера МЭА- |
очисткн, в котором высота насадочного слоя 9,65 м (условия |
те же, что и в при |
мере 1 ). |
|
При заданных условиях исходные параметры математической модели равны:
шг = 1,21 м/с; |
шж =0,0128 |
м/с; Вж , 2 = |
1,44 кмоль/м3; А Г1 |
= |
(0,21-273)/(22,4х |
||||||||||
Х313) = 0,0082 |
кмоль/м3; п = |
2; ПА = |
1,43-10“» м2/с; |
D B = |
1,11*10“» |
м2/с; |
|||||||||
гп = 16 750 м3/(кмоль-с); |
тг = |
2,15 |
м3 |
раствора на 1 м3 газа. |
|
||||||||||
По уравнению (11.99) при!)А г = |
3,3-10“ 5 |
м2/с; vr = 2• 10”5 м2/с; 8 = |
0,81, |
||||||||||||
с?экв = |
0,0287 м (Иег = |
2140, |
Ргг= |
0,605) получим Nur = |
52, откуда Рг = 6 х |
||||||||||
X 1 0 "2 |
м/с. |
|
|
|
|
|
= |
1,2-10“ 8 м2/с, а0 = |
100 м2/м3 (Иеж = |
427, |
|||||
По уравнению (11,100) при |
|||||||||||||||
Ргж = |
838) получим |
№иж = |
5,6, откуда |
рж = |
|
1,61 -10~4 м/с. |
|
|
|||||||
С учетом сравнительно певысокой плотности орошения |
[около 45 м3/(м2 -ч)] |
||||||||||||||
принимаем (стр. |
76) |
а Эфф/ао = 0,7 и, |
следовательно, а 5фф = |
0,7-100 = 70м2/м3. |
|||||||||||
В |
соответствии |
с |
уравнением |
(11,101) |
$ж, иСт = |
1,61 -10“4 . 1/0.7 = |
2,3х |
||||||||
Х10“4 м/с. Для |
учета поверхностной конвекции вводим поправочный коэффи |
||||||||||||||
циент, равный 1 , 6 |
(см. рис. IV,29) при средней по высоте насадки концентрации |
||||||||||||||
в газе |
14% |
(об.). |
Тогда |
рж,и ст= |
2,3-10“4 -1,6 = 3 ,6 8 -1 0 “4 |
м/с. |
|
||||||||
Значения D r = |
5-10“2 |
м2/с, £ ж ^ |
1,5 -1 0 " 2 м2/с (стр. |
7 7 ). |
|
||||||||||
В итоге безразмерные параметры модели будут равны: |
|
|
|||||||||||||
|
1,44 • 2,15 |
|
|
|
V1,44 • 1,675 • 1 0 * • 1,43 • 10-9 |
|
|||||||||
|
М ° — 2-0,0082 ~ |
189; |
Л о — |
|
3,68-10-4 |
|
|
— 15,8 |
|
||||||
|
а ~ |
|
0,0128 |
|
0.0049; |
|
1,11 «Л0-® |
= |
0,775 |
|
|||||
|
1,21-2,15 |
0 — 1,43-10*® |
|
||||||||||||
|
6 • 10-2.70.9,65 |
33,6; |
пж— |
3,68-10-4-70-9.65 |
|
||||||||||
|
гаг — |
|
i,2i |
|
|
|
ЛГН90 |
|
— 19,4 |
|
|||||
|
|
|
|
|
|
|
|
|
|
|
0,0128 |
|
|
|
|
|
|
|
1 ,2 1 - 9 ,6 5 ____ _ |
Вож = ' |
0,0128 • 9,65 |
|
|
||||||||
|
®0г== 0,71 • 5 • 10-2 |
— 330; |
0,1 • 1,5 • |
- о - = 82,5 |
|
||||||||||
|
|
|
1 0 -2 |
|
|
||||||||||
Результаты |
численного |
решения: |
|
|
|
|
|
|
|
||||||
|
|
|
|
|
|
* 1 |
= 0,278 |
У* = 0,331 |
|
|
|
|
|||
при сходимости |
материального баланса 0,089%; |
|
|
|
|
||||||||||
или |
|
|
Вж, х = Вж, %Х± = 1,44 • 0,278 = 0,4 кмоль/м3 |
|
|
||||||||||
|
|
|
|
|
а х= 0,416 кмоль/кмоль |
|
|
|
|
||||||
|
|
|
|
|
|
|
|
|
|
||||||
|
А г 2 = ЛГ(1Уг = 0,0082*0,331 = 0,00272 кмоль/м», |
или 6,95% (об.). |
|
Результаты расчета по математической модели и по эмпирическим данным отличаются. Более точным следует считать численное решение. Путем эмпири
ческого |
расчета получают несколько заниженное остаточное содержание С02 |
в газе, |
так как значения К га взяты для абсорберов с насадкой размером 25 |
и 50 мм (см. табл. IV-26).
Ниже приведены значения параметров R, М и 0 для нижнего и верхнего сечения абсорбера [при определений Ар предполагали, что сопротивлением в газовой фазе можно пренебречь; коэффициент ускорения х рассчитан по урав нению (11,90)]:
|
|
Ар, кмоль/м* |
R |
М |
0 |
х |
Верхнее |
сечение |
0,00126 |
15,8 |
571 |
0,775 |
15,8 |
Нижнее |
сечение |
0,0038 |
8,45 |
52,5 |
0,775 |
7,9 |
Пример 3. Рассчитать, как изменится по сравнению с данными в примере 2 содержание С02 на выходе из аппарата, если концентрацию МЭА увеличить до 3,3 кмоль/м3" а количество раствора уменьшить па 20%, сохранив прочие
условия постоянными. |
|
|
|
|
|
|
|
|
1»98 кмоль/м3; |
= |
||||||
Изменились следующие исходные параметры: В т%2 = |
||||||||||||||||
= 2,27 м3 раствора на 1 |
м3 газа; D A = |
1,28-10~3 м2/с; D B = |
0,85-10”9 |
м2/с, |
||||||||||||
шж = 0,0106 м/с, Рж, ист= 2,46-10"4 м/с (при Иеж = 297, |
Ргж = |
1 1 1 0 |
и ]Чиж = |
|||||||||||||
= 4,96). Безразмерные параметры: |
|
|
|
|
|
|
|
|
|
|
||||||
|
1.98-2,27 |
_ |
n w |
„ |
У1,98-1,675-10-» -1.28-10-» |
_ |
|
|
||||||||
№ о = |
2-0,0082 |
“ |
2б4’ |
|
— |
|
|
2 .46 -10 -4 |
|
|
|
—26,3; |
|
|||
|
сс = |
0.0106 |
0,00386; |
|
0= |
0.85 • 10-9 |
|
0,665; |
|
|
|
|||||
|
^ 2 i . 2 27 |
|
^ >1()-9 |
|
|
|
|
|||||||||
|
|
|
|
п г = |
- 6-10-2.70.9,65 |
= |
33,6; |
|
|
|
|
|
|
|||
|
|
|
|
|
|
1,21 |
|
|
|
|
|
|
|
|
|
|
|
2,46 • 10-4 - 70 • 9,65 |
— 15,7; |
Бог— 1,21 *9,65 |
= |
330; |
|
|
|||||||||
|
|
|
0,0106 |
|
|
|
|
|
0,71 • 5 • 10-2 |
|
|
|
|
|||
|
|
|
|
Вож |
0,0106-9,65 |
|
|
|
|
|
|
|
|
|||
|
|
|
|
0,1 • 1,5 • 10-2 |
— |
68,2 |
|
|
|
|
|
|
||||
|
|
|
|
|
|
|
|
|
|
|
|
|||||
Результаты численного решения: |
|
|
|
|
|
|
|
|
|
|
||||||
|
|
|
|
Xi = |
0,321 |
Y 2 = 0,307 |
|
|
|
|
|
|
||||
Сходимость |
материального |
баланса 0,12%. |
|
|
|
|
|
|
|
|
||||||
Вж, 1 = 1,98 • 0,321 = 0,63 кмоль/м3 |
и |
ах — 0,404 кмоль/кмоль |
|
|
||||||||||||
А г, 2 = 0,0082 *0,307 = 0,00251 кмоль/м3, |
или |
6,45% |
(об.) |
|
|
|||||||||||
Пример |
4. Рассчитать |
коэффициент |
извлечения |
ф |
двуокиси |
углерода |
||||||||||
водным раствором |
МЭА |
на |
ситчатой тарелке с |
высотой |
переливной |
перего |
родки 0,15 м при следующих исходных данных: концентрация МЭА 3,3 кмоль/м3, степень карбонизации раствора, стекающего с тарелки, 0,25 кмоль/кмоль, тем пература 40 °С, начальная концентрация СОа 10% (об.), давление 25 кгс/см2, приведенная скорость газа 0,25 м2/с, коэффициент массоотдачи рж = 5 -10~4 м/с, поверхность контакта фаз а = 250 м2/м3.
Расчет проводим в предположении, что 1) жидкость на тарелке полностью перемешивается, 2 ) сопротивлением в газовой фазе можно пренебречь:
Вж, 1 = 3,3 (1 —0,25 • 2) = 1.65 кмоль/м3
|
|
, |
|
0,1-25 |
-273 |
|
|
|
|
|
|
Аг> 1 ~ |
22,4 • 1,033 (273 + |
40) |
0 094 к м о л ь / м3 |
|
|||
и при |
JTij = 2,15 |
|
|
|
|
|
|
|
|
|
|
|
, |
0,094 |
= 0.0437 |
кмоль/м3 |
|
||
|
|
|
Ap,i = " 2 15 |
|
|
||||
При |
гп = 1,67-10"4 м3/(кмоль- с), |
D А = 1,35• 10“ 3 м2/с, |
D B = 0,9х |
||||||
X I0" 9 |
м2/с. |
|
|
|
|
|
|
|
|
|
|
1,65 |
|
|
|
У 1,65-1,67-104.1,35-10-® |
|
||
|
М = |
2 - 0,0437- = |
18,9; |
R = |
|
|
5•10-4 |
= 12,2; |
0 = 0,9 • 10-®/1,35 • 10-® = 0,67
|
|
|
|
2 (1 + 1 8 ,9 /0 ,6 7 ) |
|
Т = 8.84 |
|
|
|
|||
|
|
к = -----------г |
|
= 7 ± — |
|
|
|
|||||
|
|
, |
|
|
18.9/0,67 |
\ г |
|
|
|
|||
|
|
1 + ] / |
! + 4 ( |
12,2 |
|
) |
|
|
|
|||
Тогда |
Рж = |
5-10-4-8,84 = |
4,42-10-3 |
и |
К г = (4,42 • 10-*)/2,15 = |
2,05х |
||||||
ХЮ" 3 м/с. |
|
|
|
|
|
|
|
|
|
|
|
|
Коэффициент извлечепия ф по уравпению (IV,40) |
|
|
|
|||||||||
|
|
Ф = 1 —е |
°*25 |
|
|
=0.265 |
|
|
|
|||
Концентрация |
С 02 на |
выходе из |
тарелки |
А г, 2 = (1 |
— 0,265) |
0,094 = |
||||||
= 0,0692 кмоль/м2, или 7,35% |
(об.). |
|
|
Более точный расчет по средней |
||||||||
Расчет параметра М |
выполнен для А г,i- |
|||||||||||
концентрации С 02 |
в газе |
(0,816 |
кмоль/м3) приводит к незначительному изме |
|||||||||
нению ф от 0,265 до 0,278. |
|
обеспечить |
коэффициент извлечепия |
фа = 0,9, |
||||||||
Если в аппарате требуется |
||||||||||||
то при допущении |
ф = 0,278 |
const потребуется в соответствии с формулой |
||||||||||
(IV,39) |
|
|
|
|
|
|
|
|
|
|
|
|
|
|
|
|
ig (1-о.ф |
|
|
|
|
|
|
|
|
|
|
" = |
Jg (1-0.278“ |
~ |
8 Тар0ЛОК |
|
|
|
||||
Пример |
5. Рассчитать |
моноэтаноламиновый , абсорбер |
с частично |
зато |
пленной насадкой, работающий по двухпоточпой схеме. Расход газа 205 000 м3/ч, начальная и конечная концентрация С02 в газе 17,55 и 0,01% (об.), давление 27 кгс/см2, концентрация МЭА 3,28 кмоль/м3, степень карбонизации а тонкорегенерированного раствора 0,1, груборегенерированного раствора 0,35, насы
щенного раствора 0,7 кмоль |
С 02/кмоль МЭА, |
температура раствора на входе |
||||||||||
в абсорбер 40 °С, па выходе 65 °С, расход раствора 1040 м3/ч. |
|
|
||||||||||
Принимаем для нижней секции абсорбера |
кольца типа Палля размером |
|||||||||||
50 мм, для верхней секции — седловидную насадку размером 50 мм. |
||||||||||||
Гидродинамический расчет. Скорость подвисания для пижнего сечения ап |
||||||||||||
парата определим по уравпению (11,98) при у г = |
13,94 кг/м3, у ж= |
1000 кг/м3, |
||||||||||
L/G = |
(1040• 1000)/(205 000-0,66) |
= 7,68 кг/кг, |
а0 = |
112 м2/м3, |
е = |
0,86: |
||||||
|
Ig |
шо * 1 1 2 |
|
13,94 |
= - 0 ,4 9 - 1 ,0 4 |
(7,68) |
/13 .94 |
V /. |
|
|||
|
9.8 • 0 .863 |
1000 |
V |
1000 |
) |
|
||||||
где WQ = 0,354 |
м/с. Для системы газ — раствор МЭА WQ = |
0,85-0,354= 0,3 м/с. |
||||||||||
Принимаем с запасом 20% рабочую скорость газа в аппарате |
шг = 0,24 м/с. |
|||||||||||
Тогда |
диаметр |
абсорбера |
|
|
|
|
|
|
|
|||
|
|
|
|
|
205 000-1,033 (273 + 65) |
|
м |
|
|
|||
|
|
|
D = |
|
V-3600 • 0,24 • 27 • 273 • 0,785 = 3,8 |
|
|
|||||
|
|
|
|
|
|
|
||||||
Расчет |
WQ |
для верхней |
секции при рг — 9,35 |
кг/м3, L/G = |
(520*1000)/ |
|||||||
/(176-0,442) = 6,67 кг/кг, |
а0 = |
ЮО м2/м3, е = 0,81 |
дает |
w0 = |
0,402 м/с. |
|||||||
Рабочая |
скорость |
газа |
|
|
|
|
|
|
|
|||
|
|
|
|
|
176 000-1,033-329 |
|
|
|
|
|
||
|
|
|
Wr “ |
0,785 • (3,8)2 - 27 • 273 • 3600 = 0,205 м/с |
|
|
Газосодержание затопленного насадочного слоя в непроточной колонне определим по уравнению (11,103) при щ = 0,99, ц0 = 0,25 м/с:
|
|
Г |
(\пf |
0,24 |
WfOOOy. a |
|||
|
|
~ |
0 ,2 V 0,86 • 0,25 / |
V 13,94 ) |
|
|||
<Ро • 0,99 = 1.092—exp I , , ЛЛ. / |
0.24 |
\о ,в з / |
Ю0 0 |
\о,7б |
||||
|
|
L 1+0,01 ^ 0>86. 0i25 ) |
( |
13.94 |
) |
|||
фо = 0,434 |
м3/м3 барботажного слоя. |
|
|
|
|
|
||
Из уравнения (11,98) находим верхний предел нагрузки аппарата по'жид- |
||||||||
кости (при |
wr = 0,24 м/с |
и G = |
135 268 |
кг/ч |
L = |
3340 |
м3/ч |
или шж, Пред:= |
= 0,0818 м/с). |
режима к предельному' |
|
|
|
||||
Степень |
приближения |
|
|
|
||||
|
|
п ~ |
1Q40 |
|
|
|
|
|
|
|
3340 —0 ( 3 1 1 |
|
|
|
|
Находим значение параметра с Пр е д
0.0818 1
0.24спред (0.434- 1 /* — 1)а
£пред ="0,786. Тогда с = 0,786*0,311 = 0,244. |
Газосодержание насадочного |
|||
затопленного слоя в проточной колонне находим из |
уравнения (1 1 ,1 0 2 ): |
|||
|
Ф = -|-[1 + 0 Д 3 4 ( l - 0 ,2 4 4 |
0.0254 |
\~\ |
|
|
0,24 |
) ] |
||
|
|
|||
- ] / 4 [ l + 0 . 4 3 4 ( l - 0 . 2 4 4 i g i ) ] a-0 ,4 3 4 |
||||
Ф = 0,4425 м3/м3 |
барботажного слоя, или 0,4425*0,86 = 0,381 м3/м3 аппарата. |
|||
Количество |
удерживаемой жидкости иж = 1 — 0,381 — (1 — 0,86) = |
|||
= 0,479 м3/м3 аппарата. |
|
Нижняя (затопленная) зона |
||
'Кинетический |
расчет проводим' по зонам. |
абсорбера соответствует изменению а от 0,5 до 0,7 кмоль/кмоль, температуры от 56 до 65 °С. Объемный коэффициент массоотдачи (при w r = 0,24 м/с), по дан
ным рис. 11-11, равен 0,073 |
с"1, С учетом изменения плотности орошения |
||||
|
|
/ |
91.3 |
\о,в' |
|
|
М = 0,073 |
|
J |
= 0,0989 с- 1 |
|
Расчет скорости |
абсорбции |
проводим |
|
по математической модели (стр. 153) |
|
с помощью ЭВМ. |
Разбиваем |
зону |
на |
участки с интервалом Да = 0,01—0,04 |
и |
на каждом из участков определяем среднюю скорость абсорбции и высоту |
ватопления. Суммарная высота затопления равна 6,5 м, концентрация С02 |
|
в |
газе на выходе из зоны |
205 000 • 0,1755-1040 (0,7 - 0,5) * 22,4 • 3,28 |
• 100 = |
10,9% (об*) |
|||
205 000 -1 0 4 0 (0,7 - 0,5) * 22,4 • 3,28 |
|||||
|
|
||||
..Количество поглощенного С02 15 300 |
м3/ч. |
|
|
||
Определим по результатам численного расчета объемный коэффициент |
|||||
массопередачи Kta. |
Число единиц переноса, найденное методом графического |
||||
интегрирования по формуле (11,59), равно 0,965. |
|
1 ,8 6 кгс/сма. Тогда |
|||
Средняя движущая сила (0,1755 — 0,109) • 27/0,965 = |
|||||
|
15 300 |
|
|
|
|
К га - |
1,8 6 • 6,5 • 0,785 • 3,82 = |
115,5 мЗ/(ч«м 3 .кгс/см2) |
|||
что согласуется с |
данными табл. IV-13* |
|
|
|
168
. Средняя зона (от ?очки ввода грубогеперированного раствора до сечения абсорбера, где а = 0,#). Если концентрация СОа в газе па выходе из зоны 4% (об.),?то по уравнение материального баланса степень карбонизации раствора на входе в зону составит 0,319 кмоль/кмоль. t
Количество поглощенного С 02:
1040 (0,5 —0,319) 22,4 • 3.28= 13 800 м«/ч
Принимаем Х ря=1 50-м3/(ч-м3 • кгс/см2), см. стр. |
145. |
Определим высоту |
||||||
насадки, необходимую для извлечения С 02 из газа с 10,9 до 4% (об.). Средняя |
||||||||
движущая сила |
|
(0,109-0,04)-27 |
|
|
|
|
||
|
|
|
= 1,8 6 кгс/см2 |
|
||||
|
|
|
|
0,109-27 |
|
|||
|
|
|
|
|
|
|
|
|
|
|
|
2 ,3 lg |
0,04-27 |
|
|
|
|
|
|
|
|
13 800 |
|
|
|
|
|
|
|
Н — 150 • 1.86 • 0,785 • 3,82 ~ |
4 ,5 |
м |
|
||
Общая высота ндсадочного слоя из колец типа Палля в нижней секции |
||||||||
6,5 + 4,5 = |
11 |
м. |
‘ |
|
|
|
|
|
Верхняя |
зона. Количество поглощенного С 02 |
6900 |
м3/ч (при н. у.) |
|||||
205 000 |
(0,1755 — 0,0001) — 15 300 — 13 800 |
= |
||||||
Степень карбонизации раствора на выходе из зоны 0,287 кмоль/кмоль# |
||||||||
Средпяя движущая |
сцла: |
|
|
|
|
|
||
|
|
|
(0.04—0,0001) -27 |
= 0,18 |
кгс/см2 |
|
||
|
|
|
|
0,04-27 |
|
|||
|
|
|
|
|
|
|
|
|
|
|
|
2,3 lg |
0,0001-27 |
|
|
|
|
Принимаем |
коэффициент |
массопередачи 500/1,3 = |
385 м8/(м8 -ч-кгс/см8) |
(стр. 145); поправочной коэффициент 1,3 приближенно учитывает уменьшение
КгаГзл счет снижения плотности орошения с 100 до 46 м8/(м2 -ч) Высота насадки
6900
Н - 385 • 0,18 • 0,785 • 3,82 ** 9 м
Расчетная высота насадочного слоя в абсорбере 20 м. Принимаем с запасом высоту насадки 23 м.
Коэффициент массопередачи для аппарата в целом при средней движущей силе 0,541 кгс/см2 (определена графически) составит 256 м3/(м3 -ч-кгс/см2), что согласуется с опытными данными (табл. IV-12).
ТЕХНОЛОГИЧЕСКИЕ СХЕМЫ МОНОЭТАНОЛАМИНОВОЙ ОЧИСТКИ
Особенности технологической схемы моноэтаноламиновой очистки зависят в значительной мере от технологической схемы производ ства аммиака. В случае каталитической конверсии природного газа при атмосферном давлении с последующей медноаммиачной очисткой от окиси углерода (см. схему 1 , гл. I) целесообразно проводить одноступенчатую грубую очистку от С 02 (до 1—2,5%) до компрес сии. Дальнейшая очистка от двуокиси углерода осуществляется под давлением одновременно с удалением окиси углерода.
В технологических схемах каталитической конверсии при атмо сферном давлении с последующей промывкой газа жидким азотом (см. схему 3, гл. I) необходима предварительная тонкая очистка
от двуокиси углерода. В этом случае применяют двухступенчатую моноэтаноламиновую очистку от двуокиси углерода (до ~ 4 0 см 3/м3), перед второй ступенью газ целесообразно компримировать до давле ния (2,45—*2,94) • 105 Па (25—30 кгс/см2), равного давлению в блоке промывки газа жидким азотом. После второй ступени возхможна тонкая щелочная очистка. Однако из данных работ [106, 107] и опыта эксплуатации ряда промышленных установок следует, что
Очищенный
Рис. IV-31. Схема одноступенчатой моноэтаноламнповой очистки при атмо
сферном давлении:
1 — абсорбер; 2 — брыагоотделитель; з — кипятильник; 4 — регенератор; 5 — теплообмен ник; в — скруббер-охладитель; 7 — холодильники конденсата; 8 — насос насыщенного рас твора; 9 — водяной холодильник; 10 — насос регенерированного раствора; JJ — насос кон денсата.
при очистке под давлением 20—30 кгс/см2 можно получить газ, содержащий не более 4—5 см3 С 02/м3.
При конверсии под давлением с промывкой газа жидким азотом проводят двухступенчатую тонкую очистку при одинаковом давле нии газа в обеих ступенях.
В современных схемах с низкотемпературной конверсией окиси углерода можно вести очистку до —0,2% С 02 в газе с последующей тонкой очисткой от остатков окиси и двуокиси углерода метанировапием. При <йтом абсорбционная очистка осуществляется, как правило, в сдпу ступень (иногда по схеме с разделенными потоками). Одноступенчатая моноэтаноламиновая очистка позволяет достигать концентрации С 02 в очищенном газе менее 100 см3/м3.
На рис. IV-31 приведена схема грубой одноступенчатой моноэтаноламиновой очистки при атмосферном давлении. Конвертиро ванный газ поступает при 20—40 °С в абсорбер, орошаемый 15^-
2 0 %-ным раствором МЭА. Здесь концентрация С 02 в газе снижается |
|
|||||
от 18—20 до 1—2,5% (об.). После прохождения отбойного слоя' |
|
|||||
насадки в верхней частй~абсорбера и брызгоуловителЩ очищенный |
|
|||||
газ направляется в газогольдер и затем на компрессию. Насыщенный |
|
|||||
раствор МЭА, содержащий 0,4—0,5 моль COo/моль МЭА (в определен- |
, |
|||||
ныгуЮТовиях до Д |
и |
|
нагретый за счет теплоты |
( |
||
абсорСн^^ |
|
°С (иногда до 65—70 °С), подается ° |
||||
цейтробежиым насосом в кожухотрубчатый теплообменник, где |
|
|||||
нагревается до 90—105 dC, и затем поступает в регенератор. |
|
|||||
Регенерация проводится в аппаратах с выносными кипятиль |
|
|||||
никами |
под |
давлением |
0,167 МПа |
(или |
1,7 кгс/см2 абс). Регенери |
|
рованный раствор, 'содержащий |
0,15—0,23 моль С 09, на 1 моль |
|
||||
МЭА, при 115—120 °С проходит межтрубное пространст^о^ёплб- |
|
|||||
&бШшников, затем поступает в кожухотрубчатый холодильник, где |
|
|||||
^охлаждается |
водой до |
25—40 ^СТ и далее п6дается“"на~'орошение |
|
|||
абсорберов. |
Парогазовая смесь, выходящая из регенераторов при |
|
||||
97—105 °С, |
поступает |
в конденсатор (или скруббер-охладитель), |
|
|||
где водяные пары конденсируются, а газ охлаждается до 30—35 °С. |
|
|||||
Газ, |
выходящий из |
конденсатора, содержит более 99% (об.) |
|
|||
двуокиси углерода. Скруббер-охладитель орошается циркулиру |
|
|||||
ющим конденсатом, который проходит холодильник и далее подается |
|
|||||
насосом |
через второй холодильник |
(температура 20—30 °С) на |
|
|||
орошение. Конденсация паров возможна и в поверхностном кон |
|
|||||
денсаторе. Часть конденсата в виде флегмы отводится на орошение |
|
|||||
трех верхних тарелок регенератора и абсорбера. Количеством пода |
|
|||||
ваемой флегмы регулируется баланс в системе. Часто флегму соби |
|
|||||
рают в специальных емкостях и подают во всасывающую линию |
|
|||||
насоса, |
перекачивающего раствор в регенератор. |
|
||||
В технологическую схему моноэтаноламиновой очистки входят |
|
|||||
также узел приготовления раствора, включающий соответствующие |
|
емкости и насосы, и узел разгонки раствора. На некоторых отече ственных заводах раствор перегоняют в вакууме; в последнее время широкое применение нашла более простая и экономичная разгонка по давлением регенерации:
При проведении тонкой очистки газа некоторое распространение получили двухступенчатые схемы. В одном из вариантов двухсту пенчатой очистки давление в первой ступени процесса, близко к атмо сферному, содержание С 02 снижается от 20—22 до 3—6%. Концен трация МЭА составляет 17—20% (вес.). Давление во второй ступени абсорбции 27,4—29,4-10Б Па (28—30 кгс/см2), остаточное содер жание СО2 равно 40 см3/м3, концентрация МЭА составляет 12-15% .
Парогазовая смесь из регенератора второй ступени при 113— 115 °С поступает в среднюю часть регенератора первой ступени, на орошение которого подается флегма, подогретая в теплообменнике
до 85 °С. Температура внизу регенератора |
второй ступени 125— |
128 °С, давление до 2,35 • 105 Па (2,4 кгс/см2 |
абс), концентрация С 02 |
в регенерированном растворе 0,05—0,1 моль/моль МЭА.
При двухступенчатой очистке под давлением 25—28 кгс/см2 в обеих ступенях содержание МЭА в растворе первой ступени обычно равно 20%, в растворе второй ступени — 12%. В процессе очистки концентрация СО2 понижается от 25% до 40 см3/м3. Окончательная очистка конвертированного газа от С 02 происходит в щелочных абсорберах.
В промышленности получили распространение также схемы одноступенчатой тонкой очистки газа раствором МЭА под давлением.
При абсорбции под давлением насыщенный раствор дроссели руют только после теплообменников .(непосредственно перед реге нератором), иначе при повышенной температуре начинается десорб ция газов, ухудшающая теплопередачу; при этом появляются газовые мешки, усиливается коррозия в точках отрыва пузырьков газа. Насыщенный раствор должен направляться в теплообменники по трубному пространству снизу вверх; в верхних точках теплооб менников предусматриваются продувочные линии с направлением газа в регенератор или на сжигание. При соответствующем аппара турном оформлении теплообменников (нержавеющая сталь, про ведение процесса таким образом, чтобы не образовывались газовые мешки, например в вертикальных аппаратах) совмещение частичной десорбции с теплообменом приводит к положительному эффекту — увеличению движущей силы теплообмена и коэффициента тепло передачи;
В тех случаях, когда двуокись углерода поступает на синтез карбамида, концентрация горючих примесей в ней строго ограни чивается, поэтому необходимо проводить дополнительную очистку газа. Например, в случае абсорбции под давлением концентрация водорода в двуокиси углерода может достигать 1 —2 % при очистке по обычной схеме (см. рис. IV-31). Чем цыше давление, тем больше концентрация водорода. Это объясняется в первую очередь различ
ной |
зависимостью растворимости двуокиси углерода и водорода |
от |
давления. |
Концентрация водорода в растворе возрастает пропорционально |
давлению. Концентрация С 02 в растворе при абсорбции под давле нием незначительно превышает ее концентрацию в растворе при абсор бции без давления вследствие медленного роста растворимости С 02 при увеличении давления, а также малой скорости химической реак ции при а > 0,5. Кроме того, при а > 0,4 заметно повышается скорость коррозии, поэтому значение а часто намеренно ограничивают.
Эффективным методом получения чистой двуокиси углерода является промежуточная десорбция примесей. Этот процесс может быть осуществлен различными способами. Один из вариантов раз
работан и осуществлен в промышленном |
масштабе [117, 1181 для |
абсорбции при атмосферном давлении (рис. |
IV-32). Раствор из абсор |
бера направляют в емкость, где при |
60—70 °С происходит от- |
дувка азотом горючих примесей (расход азота не более 0,7—0,8 м3/м3 раствора), при этом концентрация примесей снижается до 0,007—
0, 01% .
Другой экономичный вариант получения чистой С 02 заключается в отдувке примесей двуокисью углерода или промежуточной десорб ции части СО2, загрязненной примесями. На 1 м3 раствора подается 2 м3 двуокиси углерода, из них около 1,5 м3 поглощается раствором МЭА. Это количество уменьшается с ростом температуры и степени карбонизации насыщенного раствора.
В случае абсорбции под давлением возможны различные варианты десорбции горючих примесей. Целесообразно проводить этот про цесс путем снижения давления до давления регенерации; полнее
примеси |
|
удаляются при по |
|
||||||
догревании раствора. Разра |
|
||||||||
ботан [117] вариант получе |
|
||||||||
ния |
чистой |
двуокиси |
угле |
|
|||||
рода, основанный-на отводе |
|
||||||||
ее |
из |
регенератора |
двумя |
|
|||||
потоками. Через верх регене |
|
||||||||
ратора уходит часть С 02 и все |
|
||||||||
примеси, |
а несколько |
ниже |
|
||||||
(на |
2 —3 |
тарелки) |
отбирает |
|
|||||
ся чистая двуокись углерода. |
|
||||||||
Последние |
годы |
в |
про |
|
|||||
мышленности |
широкое |
рас |
Рис. IV-32. Припципиальпая схема моно- |
||||||
пространение получили |
раз |
этаполаминовой очистки с отдувкой горю |
|||||||
личные |
варианты схем МЭА- |
чих примесей азотом: |
|||||||
1 — абсорбер; г — промежуточный десорбер для |
|||||||||
очистки |
|
с |
разделенными |
||||||
|
отдувки горючих; 3 — регенератор; 4 — тепло |
||||||||
потоками насыщенного и ре |
обменник; 5 — холодильник; в — кипятильник; |
||||||||
генерированного |
абсорбента |
7 — конденсатор. |
|||||||
|
[119—121]. При использова нии этих схем снижается расход тепла и увеличивается степень
очистки газа, в частности можно достичь тонкой очистки в одну ступень (менее 10 0 см3/м3) без увеличения расхода тепла.
На рис. IV-33 показана принципиальная схема простейшего варианта такой схемы — схема с двумя потоками насыщенного раствора, верхний из которых не нагревается в теплообменниках (схёма с «холодным байпасом» [121]). Схема отличается от однопо точной схемы (см. рис. IV-31) тем, что часть насыщенного раствора (около 1 0 %) направляется в обход теплообменников непосредственно в регенератор выше точки ввода основного потока насыщенного раствора. Такая схема позволяет по сравнению с обычной — одно поточной схемой — снизить расход тепла на 7—8 % за счет умень шения температуры парогазовой смеси (расчет процесса приведен ниже). Простота схемы позволила использовать ее для усовершен ствования действующих установок. При этом «холодный байпас» подают на верхние тарелки регенератора вместо флегмы.
На рис. IV-34 показан другой вариант схемы с двумя потоками насыщенного раствора. Этот вариант отличается от однопоточной схемы тем, что часть насыщенного раствора (50—70%) перегревается выше температуры потока, подаваемого по стандартной схеме.
Перегретый до 107—113 °С поток подается ниже основного потока. Такая схема позволяет снизить расход тепла на 20—30%, причем эффект частично достигается за счет увеличения поверхности тепло обмена.
Рис. IV-33. Принципиальная схема моноэтаноламиновой очистки с холодным байпасом насыщенного раствора:
1 — абсорбер; 2 — регенератор; |
з — теплообменник; 4 — холодильник; 5 — конденсатор; |
|||||||||
|
|
6 — кипятильник; |
7 — насос. |
|
|
|
||||
Рис. IV-34. Двухпоточная схема моноэтаноламиновой очистки с двумя нагре |
||||||||||
тыми потоками насыщенного раствора |
(обозначения см. рис. IV-33). |
|||||||||
При тонкой очистке газа применяют |
схемы с разделением реге |
|||||||||
нерированного |
раствора |
на |
два потока. |
Такая |
схема использована |
|||||
|
|
|
|
|
в |
агрегате |
производства ам |
|||
|
|
|
|
|
миака мощностью 1360 т/сут |
|||||
|
|
|
|
|
(процесс |
|
МЭА—ГИАП) |
|||
|
|
|
|
|
(рис. IV-35). Абсорбция осу |
|||||
|
|
|
|
|
ществляется 2 0 %-ным раство |
|||||
|
|
|
|
|
ром |
моноэтаноламина |
в аб |
|||
|
|
|
|
|
сорбере |
с ситчатыми |
тарел |
|||
|
|
|
|
|
ками с высоким барботаж- |
|||||
|
|
|
|
|
ным |
слоем |
под давлением |
|||
|
|
|
|
|
27 |
кгс/см2. |
В нижней части |
|||
|
|
|
|
|
абсорбера |
происходит |
пред |
|||
|
|
|
|
|
варительная очистка (до 1 — |
|||||
|
|
|
|
|
2 % |
СО2 |
и менее) грубо реге |
|||
Рис. IV-35. Многопоточная схема МЭА- |
нерированным раствором (со |
|||||||||
держание |
|
СО2 до 0,3— |
||||||||
очисткн |
(процесс МЭА — ГИАП) с двуАмя |
0,35 моль/моль МЭА). Топкая |
||||||||
потоками регенерированного |
раствора и |
очистка (до 100 см8/м3 и менее) |
||||||||
тремя |
потоками |
насыщенного |
раствора |
|||||||
(обозначения см. рис. |
IV-33). |
осуществляется тонко регене |
||||||||
|
|
|
|
|
рированным раствором (содер |
жание СО2 около 0,1 моль/моль МЭА). В случае необходимости
может |
быть достигнута |
очистка до 1 млн"1 С 02. Соотношение по |
|
токов |
регенерированного раствора равно 1 : 1 . На 205 000 |
м3/чгаза, |
|
содержащего около 18% |
С 02> подается 1100—1150 м3/ч |
раствора |
при 40° С. Степень карбонизации насыщенного раствора около 0,65 моль/моль. Насыщенный раствор при 60—65 °С разветвляется на три потока (в данном случае по существу объединены схемы, показанные на рис. IV-33 и* рис. IV-34).
Верхний поток (около 10%) направляется на верхнюю ситчатую тарелку (холодный байпас), средний поток (~45% ) нагревается до 90—95 °С и направляется в среднюю часть регенератора. Нижний поток дополнительно перегревается до 104—107 °С и подается еще ниже. Парогазовая смесь выходит из регенератора при температуре около 80 °С. Грубо регенерированный раствор при 110 °С подается в теплообменники. Тонко регенерированный раствор имеет темпе ратуру 125—127 °С. Такая схема благодаря разделению потоков раствора и высоким степеням карбонизации раствора характеризуется хорошими технико-экономическими показателями (стр. 279).
РЕГЕНЕРАЦИЯ МОНОЭТАНОЛАМИНА И^РАСХОД ТЕПЛА НА ОЧИСТКУ
При увеличении температуры равновесие химических реакций, протекающих при абсорбции, сдвигается влево: происходит десорб ция СО2 и регенерация МЭА. Десорбцию двуокиси углерода осуще ствляют при нагревании водяным паром, который является также десорбирующим агентом.
Расход тепла на регенерацию моноэтаноламина равен
Q — ф д е с + @ И + (?отд + Q n |
(IV ,41) |
Здесь (?дее — тепло, необходимое для |
десорбции |
двуокиси угле |
рода |
|
|
'<?дес= GCOt A H = L ( x 2- |
Xl) АН |
(IV,42) |
где АН — удельная теплота десорбции, равная по абсолютной величине инте гральной теплоте абсорбции (см. рис. IV-21);
(?„ — тепло, затраченное на нагревание
QH= LCp AtT |
(IV ,43) |
где Ср — теплоемкость раствора; А1Т — разность температур регенерирован ного и насыщенного раствора на холодном конце теплообменника, примерно равная разности температур на горячем копце в простейшей схеме;
<?отд — тепло, затраченное на образование отдувочного пара, уходя щего через верх регенератора:
QOTH= ’пгс^пгс |
(IV, 44) |
где г‘п г с ■“ удельная энтальпия парогазовой смеси; |
Gnг с — количество этой |
смеси; |
|
Qn — тепловые потери, не превышающие 5% общего расхода тепла. Все тепло Q подводится в кипятильники при температуре примерно 140—150 °С и отводится в холодильниках при температуре около
70 °С и конденсаторе парогазовой смеси (или скруббере-охладителе) при 85—110 °С. Следовательно
|
|
|
|
( V.45) |
(где |
<?хол — тепло, отведенное |
в |
холодильнике; @Конд — тепло, |
отведенное |
в конденсаторе (скруббере-охладителе), равное (?отд). |
|
|||
Обозначим температуры |
потоков в простейшей схеме |
(см. ри |
||
сунок IV-31): |
|
|
|
|
ti |
— температура в кубе |
регенератора; |
|
t2 — температура насыщенного раствора на входе в регенератор; t3 — температура регенерированного раствора на выходе из тепло
обменника (на входе в холодильник);
tA— температура регенерированного раствора на входе в абсор бер (на выходе из холодильника);
tb — температура насыщенного раствора на выходе из абсорбера; *лгс — температура парогазовой смеси на выходе из регенера
тора.
(IV,46)
(IV,47)
Далее
Gnrc = Gc02 + GH8o = G cot + ^CO* ,<г>а==^С 02 ( * + ф *) = £ (1 + Ф 2) (IV,48)
где Ф2—Рц*о, 2 ^ со2, г(слг* гл> ^)* Ая=д;2 — х г — реальная поглотительная
способность раствора.
В итоге уравнение (IV,41) можно преобразовать следующим |
образом |
||
(пренебрегая величиной (?п): |
|
|
|
•Q=-@дес + @н~Ь Qouk —L Ьх • АН + |
ЬСр • Д*т+ |
‘пгсЬ Ад; ( 1 + Ф2) == |
|
— L Ад; • AН -|- L(7pA^T-|- |
AxCPj-!" |
^ |
(IV,49) |
Некоторые этапы расчета удобнее вестИ| используя удельные
теплоты (например на 1 м3 С 02), |
т. е. |
___ |
г. л |
У— а _“ |
|
Gco 2 |
l a * |
Тогда |
|
(IV,50)
Таким образом, дхол = ддес + дн, т. е. в холодильнике в конечном итоге отводится все тепло, выделившееся в абсорбере, и тепло недорекуперации qH. Следовательно
* » = 4 1 Г + - ^ - - £ ^ = & ( А « . + 4 .,) |
(IV.51) |
Из уравнения (IV,51) можно |
исключить величину Ср с помощью |
|||||||||||
уравнения (IV,47). |
Тогда |
|
|
|
|
|
|
|
|
|
||
|
|
|
|
|
|
|
|
|
|
|
|
< IV ,52 > |
Таким образом |
|
|
|
|
|
|
|
|
|
|
|
|
*= &*+-£ф |
- |
+ |
,пРС (1 +Ф2)= ^ |
^ |
. + |
<пгс (1 + Фа) = |
||||||
|
|
= Д Н |
|
+ |
in rc ( 1 + Ф |
2) |
|
|
(IV .5 3 ) |
|||
Если при приближенном расчете пренебречь физическим теплом |
||||||||||||
двуокиси углерода, |
|
то |
q = |
~ Д Я |
+ |
CpAtT/Ax + |
1н 2о-Ф 2- |
|||||
Пренебрегая физическим |
теплом |
воды |
(флегмы), |
получим |
||||||||
Я = ~ ь П + - £ ^ |
+ |
гФл= |
£ |
^ |
+ |
гФ2 = Ь |
Н |
^ + |
гФ, (IV .5 4 ) |
|||
где iH s 0 — энтальпия |
воды; |
г — тецлота, испарения |
воды. |
|
||||||||
Значение ДН может |
быть |
рассчитано |
по |
данным рис. IV-21 |
[70, 71]. Из рисунка видно, что оно колеблется в довольно широких
пределах — от 79 JB кДж/моль |
(19 ккал/моль |
С 02) при |
а = |
0 — |
|||||||||||
0,1 |
моль |
СОа/моль |
МЭА |
до |
41,87 кДж/моль |
(10 ккал/моль) |
при |
||||||||
а == 0,7, т. е. от 3560 |
до 1870 |
кДж/м3 |
С 02 (от |
850 |
до 450 ккал/м3 |
||||||||||
С 02). |
Практически |
многие |
установки |
работают в |
интервале |
а = |
|||||||||
= |
0,15—0,45 моль |
С 02/моль МЭА. В |
этих случаях |
значение |
АН |
||||||||||
составляет |
62 кДж/моль, |
или |
16 ккал/моль (ЗОЮ |
кДж/м3, |
или |
||||||||||
720 ккал/м3 С 02). |
|
|
|
|
|
|
|
|
|
|
AtT и Ах. |
||||
|
Для расчета величины qHнеобходимо иметь значения |
||||||||||||||
Недорекуперация A tT |
на |
действующих |
установках |
обычно колеб |
|||||||||||
лется |
от |
12 до 20 °С, |
хотя при плохом |
состоянии |
теплообменных |
поверхностей эта величина существенно выше. Значение Да; колеб лется от 10 (в худшем случае) до 33 м3 С 02/м3 (при абсорбции под давлением, высокой степени насыщения раствора в абсорбере — до 0,65—0,7 моль/моль и концентрации МЭА 20%), однако обычно оно равно 12—16 м3/м3. Теплота гц,о « 1 7 8 0 кДж/м3 (425 ккал/м3 водяных паров).
Расчет величины дотд сводится к определению флегмового числа Ф,2 в верхней части регенератора. Эта величина зависит от темпера туры подогрева раствора £2 (а следовательно, и от Д£т), от степени регенерации раствора ai, от давления в регенераторе, от технологи ческой схемы процесса п может составлять от 0,4 до 8. Так, при 102 °С
12 заказ 14с0 |
177 |
и 1,7 кгс/см2 при соблюдении определенных условий флегмовое
число Ф2 ^ 1,5. |
|
|
|
= |
20 °С, Да; = 15 м3/м3, |
В распространенном случае,, когда At |
|||||
Ср = 4,187 кДж/моль |
(1 ккал/м3), |
t2 = |
102 °С, Рр = 1,7 кгс/см2, |
||
флегмовое число Ф2 = |
1,5, расход тепла |
примерно равен |
|||
д = АН + |
CP AtT |
1000 • 20 |
+ 4 2 5 - 1 ,5 = |
||
Ах |
+ гФ2 = 720-f |
15 |
|||
|
|
|
|||
= 720 +1340 -г 635 = —2700 ккал/мз С02 |
(11300 кДж/м3) |
Таким образом, в данном случае расход тепла на десорбцию составляет около 26% общего расхода тепла, на нагрев — 50%
Рис. IV-36. Зависимость температуры кипения 20%-ного раствора МЭА от сте пени карбонизации (1 кгс/см2 ^ 1 0 б Па):
1 — общее давление в регенераторе 1,4* 10е Па; 2 — то же, 1,7* 10е Па; 3 — то же, 1,9-10® Па;
4 — то же, 2,0-10* Па; 5 — то же, 2,3*10» Па; 6 — то же, 2,5*10» Па; |
7 — то же, 3*10» Па; |
8 — то же, 3,5*10» Па; 9 — то же, 4*10» Па; 10 — то же, |
4,5*10» Па. |
и потери с водяными парами — 24%. В зависимости от различных условий доля qHможет изменяться от 30 до 60%, аналогично может изменяться доля других составляющих.
Для расчета условий процесса регенерации и расхода тепла используется ряд равновесных зависимостей, в том числе приве денные выше данные по равновесному давлению С 02 над раствором
(рис. IV-13—IV-18, табл. IV-7—IV-9), по теплотам растворения (см. рис. IV-21), а также данные о давлении насыщенных паров воды над раствором. По данным о давлениях паров и С 02 над растворами были рассчитаны температуры их кипения.
На рис. IV-36 показана зависимость температур кипения рас творов МЭА от степени карбонизации раствора при различных давлениях. По этим данным построены равновесные линии процесса
регенерации |
(рис. IV-37). |
На |
|
|
|
|
|
|
|
|||||||
рис. IV-38 приведены |
зависи- |
|
|
|
|
|
f |
|
||||||||
М О С Т И Фр = Р п г О /Р р -Р Н 'О О Т |
|
|
|
|
3 |
|
||||||||||
температуры раствора при раз |
о,в |
|
|
|
|
|||||||||||
личных |
общих |
давлениях |
Р р. |
|
|
|
|
|||||||||
Величина Рц2о мало зависит |
|
|
|
|
|
|
||||||||||
от степени карбонизации а и |
|
|
|
|
2-j/l |
|
|
|||||||||
определяется по4 закону Рауля, |
I 0,6 |
|
|
|
Iff/ |
|
||||||||||
а величина Рр в условиях |
рав |
о |
|
|
|
|
|
|
||||||||
новесия, |
т. е. |
при температуре |
|
|
|
|
|
|
||||||||
* |
|
|
|
|
|
|
||||||||||
кипения, однозначно определена |
0,4 |
|
|
|
|
|
|
|||||||||
значениями t |
и х. |
В этом слу |
|
|
|
|
|
|
||||||||
чае |
Рр = |
Рс.Ог (t, X) |
+ |
Р н 20 (О |
|
|
|
|
|
|
|
|||||
и |
Ф2 |
= |
Фг = |
Р в о1Рсош— |
|
• |
|
|
|
|
||||||
= Р Н 20 |
( t ) l ( P р |
— |
^ Н |
20 |
(*))• |
|
0,2 |
|
|
|
|
|||||
В этом |
уравнении величина |
|
|
|
|
|
||||||||||
Р р задана, а величина Р н 2о за |
|
|
|
|
|
|||||||||||
висит только |
от |
температуры, |
|
|
|
|
|
|
|
|||||||
которая в свою очередь зави |
|
0,2 |
|
0,4 |
0,6 |
0,8 |
||||||||||
сит от концентрации С 02 в рас |
|
^ |
сС,моль/'моль |
|
|
|||||||||||
творе (при равновесии). Если |
Рис. IV-37. Равновесная линия про |
|||||||||||||||
количество |
тепла, |
поданного в |
||||||||||||||
регенератор, |
выше |
минималь |
цесса регенерации |
2 0 %-ного |
раствора |
|||||||||||
МЭА (1 кгс/см2 ^ 105 |
Па): |
|
||||||||||||||
ной |
величины, |
то |
температура |
|
||||||||||||
J — Р = |
1,7-10* Па; |
2 — Р = 2-10» Па; з — |
||||||||||||||
парогазовой смеси £пгс выше |
|
|
Р = |
2,5-10* Па. |
|
|
||||||||||
температуры |
кипения раствора |
|
|
|
|
|
|
|
||||||||
на верхней тарелке регенератора, т. е. |
Р н 2о > |
|
Рц.о (*кнп)> |
тогда |
||||||||||||
Ф2 > Фг- |
тепла |
при |
МЭА-очистке зависит |
от |
многих параметров |
|||||||||||
Расход |
технологического режима и от аппаратурного оформления про цесса. Более подробно влияние некоторых главных факторов опи сано ниже.
Давление регенерации Рр. Чем выше давление в регенераторе, тем выше температура (см. рис. IV-36). Как показано в гл. II, повышение температуры выгодно в тех случаях, когда теплота десорбции газа выше теплоты испарения растворителя. В этом случае при увеличении температуры кипения флегмовое число умень шается, так как давление газа над раствором растет быстрее, чем
давление паров растворителя. В данном случае Д //со2 = (62 кДж/ /моль) (16 ккал/моль), а Д # н 2о —40,6 кДж/моль (9,7 ккал/моль).
Следовательно, Фмнп = Рц^о/Рсо* уменьшается при увеличении
температуры кипения (за исключением высоких а). В табл. IV-17 приведены значения. Фмнн при различном давлении в регенераторе.
Как видно из таблицы, повышение давления в регенераторе
от1,67-10б до 2,45*10б Па (от 1,7 |
до 2,5 кгс/см2) позволяет при |
||
а ^ 0,5 снизить величину |
Ф*. При |
заданной |
температуре увели |
чение давления приводит |
к уменьшению Ф = |
Рцго (t)/(Pp—Pnto (/>) |
|
(см. рис. IV-38). |
|
|
|
Рис. IV-38. Зависимость флегмовых чисел |
(а — Ф < 1 ; б — Ф > 1) от темпе |
|||||
ратуры и общего давления в |
регенераторе |
Р р |
для 20%-ного |
раствора МЭА |
||
(1 |
кгс/см2 |
10б |
Па): |
|
||
1 — Р =» 1,4* 10е Па; 2 — 1,7-10» Па; 3 |
— 2,0-10» Па; |
4 — 2,5-10» Па; |
5 — 3,0-10» Па; |
|||
в — 3,6-10» Па; 7 — 4,0-10» Па; |
3 — |
4,5-10» Па; 9 — 1,9-10» Па; 10 — 2,3-10» Па. |
Таким образом, в отличие от многих процессов физической и хими ческой абсорбции в данном случае целесообразно давление в регене раторе повышать. Это позволяет при одинаковом расходе тепла полнее регенерировать раствор и, следовательно, добиться более глубокой очистки газа. При одинаковой степени очистки газа с повы шением давления можно 'снизить расход тепла.
Так как с повышением давления увеличивается температура регенерации, ограничением при МЭА-очистке является термическая устойчивость раствора. Кроме того, при чрезмерном повышении
температуры 11 возрастает тепловая нагрузка |
на теплообменники |
и, следовательно, при постоянной поверхности |
теплообмена может |
возрасти Д£т и расход тепла. |
|
Температура>парогазовой смеси /пгс. В тех случаях, когда темпе ратура в регенераторе увеличивается вследствие повышения давле ния, расход тепла снижается. Возрастание температуры при постоян
но
Таблица IV-17. |
Температура кипения 2 0 %-пого раствора МЭА |
|||||
|
|
|
|
Р Н20 |
|
|
|
и значения Ф * = Ф Мин = — *— |
|
|
|||
а, моль/моль |
*КИП |
Ф* |
*КИП |
Ф* |
*КИП |
Ф* |
|
Р общ — |
Р общ — |
^общ — |
|||
0,70 |
= 1,7 |
кгс/см2 |
= 2 кгс/см2 |
= 2,5 |
K Z C J C M 2 |
|
- 4 0 |
—0,013 |
42 |
0,03 |
48,5 |
0,03 |
|
0,65 |
54 |
0,08 |
58 |
0.09 |
63,5 |
0 ,10 |
0,60 |
67 |
0,19 |
71 |
0.19 |
77 |
0,20 |
0,55 |
79 |
0,35 |
83 |
0,35 |
89 |
0.35 |
0,50 |
89,5 |
0,63 |
93,5 |
0,60 |
92,5 |
0.60 |
0,45 |
99 |
1,15 |
103 |
1,05 |
108 |
1,0 |
0.40 |
105 |
2,07 |
109 |
1,8 |
114 |
1,7 |
Примечание. I кгс/см*= 0,9810е Па.
ном давлении связано с‘ увеличением расхода тепла. В этом случае *пгс > *кнп и Ф > Фм„„, т. е. Ф = Ри2о1(Рр—Рн*о) возрастает. При этом с повышением температуры при Рр = const величина Ф уве личивается (см. рис. IV-38).
Концентрация СОг в насыщенном растворе. Чем выше хъ тем меньше (при прочих равных условиях) циркуляция раствора и, следовательно, ниже расход тепла на нагрев qn. Кроме того, чем выше я2, тем меньше (как это следует из табл. IV-17) минимальное флегмовое число Фмнн. При этом заметно снижается температура кипения раствора. Так, температура кипения 20%-ного раствора
МЭА при Р р = |
|
1,7 кгс/см2 и а |
= 0 ,4 моль С 02 на моль МЭА равна |
|||||
105 °С, а |
при |
а |
= 0,5 |
tKll„ = |
—90 °С, при а = |
0,65 |
£KHn = |
54 °С. |
Однако |
если |
раствор |
нагревают в теплообменнике |
выше |
темпе |
|||
ратуры кипения |
(t2> |
£кнп), то |
флегмовое число |
Ф2 не равно Ф*2, |
||||
а может |
быть |
определено при |
расчете процесса |
дросселирования. |
Расчет дросселирования раствора необходим при t2 ^> JKWI- В результате дросселирования из раствора десорбируется часть двуокиси углерода и испа ряется некоторое количество воды. При этом температура раствора понижается. Следовательно, температура парогазовой смеси гПгс будет ниже температуры
| 2 и равна *2 — температуре раствора после дросселирования. Соответственно, флегмовое число Фг определяется этой температурой 12 (и повой степенью кар
бонизации аг).
При дросселирований раствора энтальпия остается постоянной, поэтому общий расход тепла рассчитывают обычным способом [уравлепие (IV.50)],
подставляя вместо Ф2 величину Ф2 . Если в формуле используется AtT (равная разности температур на холодпдм-конце теплообменника), то Ах = х2 —
а не Х2 — хх (т. е. подставляется концентрация С 02 в растворе до дросселиро
вания).
При расчете процесса дросселирования принимают, ч*го после дроссель-вен тиля достигается равновесие раствора с десорбированной парогазовой смесью. Следовательно, параметры раствора после дросселирования определяются из этОго условия, а также на основе уравнения теплового баланса дросселирования
LCp (fa- i'2) = L (х2 —х'2) AH + L (х2- х \ ) i (1 + Ф2) |
(IV,55а) |
Ср Д*др —Д^др ( А Н + ГФ2)
где
^2’ Д^др = ^2 — ^2
В уравнении (IV,55а) первый член правой части уравнения представляет собой теплоту десорбции СОо в процессе дросселировапия, пторойчлен — эпталь-
пию парогазовой смеси после дроссель-вептиля. Поскольку Фг = Ф (/г, #2)1 причем t'i = /кип (р у то при заданном t2 расчет ведут подбором t2 методом по
следовательного приближения. Задаваясь t2, можно сразу получить
h = |
+ [Д.тдр (ДЯ+ гФ')]/С Р |
|
(IV.556) |
||||
На рис. IV-39 и IV-40 приведены зависимости г2 от *2 ПРИ различных на |
|||||||
чальных концентрациях |
С 02 |
в растворе |
[122]. |
|
|
|
|
Увеличение степени карбонизации раствора позволяет существенно снизить |
|||||||
расход тепла. Так, для 15%-ного раствора (2,5 |
моль/л) при At = 20 °С и а х = |
||||||
— 0 ,2 моль/моль (tx = 118 °С) |
и при а 2 = |
0,4 |
моль/моль |
расход тепла |
при |
||
мерно равен |
|
|
|
|
|
|
|
— Сп Atf |
|
|
1000•20 |
+ |
425-1,2 = |
|
|
* = ~ д * + - ! г - |
гф = 720 + 22,4-2,5 (0 ,4 -0 ,2 ) |
|
|||||
= 3010 ккал/мз С02 (12,6 МДж/мЗ) |
|
|
|
||||
При а 2 = 0,60 моль/моль (после дросселирования при |
t = |
98 °С Ф£ |
0,8): |
||||
1000 - 20 |
|
|
|
С02 (819 МДж/м») |
|||
q = ~720 ~Ь' 22 4 Т 2 ~5 "(0 6 —0 2 )~ + 425 • 0*8 = 1955 ккал/мз |
Увеличение степени карбонизации насыщенного раствора до а — = 0,5, моль/моль достигается легко уменьшением количества цирку лирующего раствора (если правильно рассчитана высота абсорбера). Однако при а > 0,5 скорость химической реакции резко снижается, а равновесное давление быстро возрастает. Поэтому а > 0,5 можно достичь лишь при абсорбции под давлением и при продолжительном пребывании жидкости в абсорбере. Кроме того, при высокой степени насыщения раствора необходимо учитывать увеличение скорости побочных реакций и коррозии и принимать соответствующие меры.
\/ Концентрация моноэтаноламина. Увеличение концентрации МЭА при одинаковой степени карбонизации приводит к возрастанию равновесного давления С 02 над раствором (или соответственно при заданном Рсо*к уменьшению а). Однако повышается абсолютная поглотительная способность раствора (в м3/м3). Поэтому путем увеличения концентрации моноэтаноламина можно уменьшить цирку ляцию раствора вследствие увеличения его поглотительной способ ности Ах и, следовательно, уменьшить дп. Кроме того, несколько снижается (при одинаковой величине а 2) флегмовое число.
Увелцчение концентрации МЭА способствует повышению ско рости побочных реакций и коррозии. Кроме того, при очень больших концентрациях (выше 30%) заметно увеличивается вязкость раствора и соответственно при равном расходе тепла скорость процессов
Флегмодое число, моль/моль
Рис. IV-39. Равновесные зависимости параметров для расчета процесса ре генерации 20%-ного раствора МЭА:
а — при Р абс =50,14 МПа; б — при Р абс'=
= 0,17 МПа; |
в — при |
Р абс= 0,25 МПа |
||
(10 кгс/сма « |
1 МПа); |
I — кривая дрос |
||
селирования |
(зависимость |
температуры |
||
после дросселирования |
/к = |
*пГс = |
от |
температуры до дросселирования f ,) при
а = 0,6 моль С02/моль МЭА; II — то же, при а = 0,65 моль С02/моль МЭА; II I — то же, а = 0,7 моль С02/моль МЭА; 1 — зависимость флегмового числа от темпера
туры tnrc (<2); 2 — температура кипения
раствора, °С (на оси абсцисс нанесена температура
массо- и теплопередачи практически перестает возрастать (данные
В.Е. Дымова и И. Л. Лейтеса, ГИАП).
Поверхность теплообмена й коэффициент теплопередачи* Увели
чение поверхности теплообмена FT (и коэффициента теплопередачи
С с
Рис. IV-40. Зависимость равновесных условий в верхней части регенератора от температуры насыщенного раствора t2 и содержания С0 2 в насыщенном 2,5 н*.
(15%) растворе МЭА при Р р = 1,8 кгс/сма [122].
1— 0,55 моль COe/моль МЭА; 2 — 0,50 моль С02/моль МЭА; 3 —• 0-45 моль С02/моль МЭА; 4— 0,40 моль С02/моль МЭА; 5 — 0,35 моль С02/моль МЭА; в — 0,30 моль СО*/моль МЭА (АС — изменение состава насыщенного раствора в верхней части регенератора),
Кт) позволяет уменьшить величину Д^, т. е, |
снизить расход тепла |
|||
на |
нагрев раствора qH= |
CpAtT/Ax. |
Влияние |
изменения Кг и Fr |
на |
величину AtT можно |
определить |
следующим образом. Количе |
|
ство тепла, передаваемого в теплообменнике (см. схему на рис. IV-31) |
||||
|
Q T = L C p |
— fg) = K j F ^ Д = K j F т (£3 —1;}) |
Отсюда
LCpti~{- KTFTt$
|
|
|
|
|
|
Гз“ |
L C P + K TF T |
|
|
|
|
|
|
(IV,56) |
|||
и |
|
|
|
|
|
|
|
|
|
|
|
|
|
||||
|
|
|
|
|
|
L Q p (tx— ^5) |
|
|
|
|
|
|
|
|
|
||
|
|
|
|
Д*т= ts—Lh |
|
|
*1 — h |
|
|
(IV,57) |
|||||||
|
|
|
|
LCp-j-KjFт |
|
1 |
. |
KTPT |
|
|
|||||||
|
|
|
|
|
|
|
|
|
|||||||||
|
|
|
|
|
|
|
|
|
|
^ |
L Q p |
|
|
|
|
||
Таким образом, при заданных температурах |
внизу |
абсорбера th |
|||||||||||||||
и регенератора ti величина Д£х зависит от |
фактора / т = |
KrFTfLCp% |
|||||||||||||||
зависящего |
от |
характеристики теп |
|
|
|
|
|
|
|
|
|
||||||
лообменника (KTFT) и тепловой на |
|
|
|
|
|
|
|
|
|
||||||||
грузки. Фактор / х является важным |
|
|
|
|
|
|
|
|
|
||||||||
параметром |
процесса |
рекуперации |
|
|
|
|
|
|
|
|
|
||||||
тепла. |
В |
промышленных |
условиях |
|
|
|
|
|
|
|
|
|
|||||
обычно |
его значение колеблется от 4 |
|
|
|
|
|
|
|
|
|
|||||||
(на лучших |
установках) до 20. Сле |
|
|
|
|
|
|
|
|
|
|||||||
довательно, величина Д£х умень |
|
|
|
|
|
|
|
|
|
||||||||
шается |
|
почти |
пропорционально |
|
|
|
|
|
|
|
|
|
|||||
росту произведения |
KjF^ |
|
|
|
|
|
|
|
|
|
|
|
|||||
Однако чем меньше Д£х, тем выше |
|
|
|
|
|
|
|
|
|
||||||||
температура раствора на входе в ре |
|
|
|
|
|
|
|
|
|
||||||||
генератор t2, а следовательно, и |
|
|
|
|
|
|
|
|
|
||||||||
температура |
раствора |
вверху |
реге |
|
|
|
|
|
|
|
|
|
|||||
нератора и равная ей температура |
Рис. IV-41. |
Зависимость расхода* |
|||||||||||||||
парогазовой |
смеси. |
Поэтому умень |
|||||||||||||||
шение |
величин |
AtTи qH сопровож |
тепла |
q |
от |
разности температур. |
|||||||||||
дается увеличением |
флегмового чис |
Д£х на конце |
теплообменника |
||||||||||||||
(15%-ный |
раствор |
МЭА, |
<*i = |
||||||||||||||
ла Ф2 и qOTд. В результате в целом |
= |
0 ,2 |
|
|
моль/моль, |
а 2 |
= |
||||||||||
расход |
тепла снижается медленнее, |
= |
0,45 моль/моль, Р р = 0,18 МПа |
||||||||||||||
чем дн, и |
при чрезмерно |
малой ДtT |
|
|
|
(1 , 8 кгс/см^): |
сп*А* |
||||||||||
практически перестает уменьшаться. |
|
|
|
|
|
|
|
||||||||||
* — 9 о т д - ~ гФ‘»2 — Знагр = |
Х х |
» |
|||||||||||||||
На рис. IV-41 показана зависи |
|
|
|
3 |
— ДЯ; 4 — q. |
|
|
||||||||||
мость |
q от Д£х [расчет по уравнению |
|
|
|
|
|
|
|
|
|
|||||||
(IV, 54)] |
для одного из частных случаев [123]. Из рисунка видно, что |
||||||||||||||||
уменьшение |
величины |
AtT от 2 4 д о ’8°С |
(что |
требует |
более -чем |
трехкратного увеличения поверхности теплообмена) снижает расход, тепла лишь на 17%. Поэтому оптимальная величина ДtT должна быть определена технико-экономическим расчетом, т. е. с учетом капитальных затрат.
При оптимизации необходимо учитывать, что уменьшение AtT и qHсопровождается не только увеличением поверхности теплообмен ников^ конденсаторов парогазовой смеси, но и уменьшением поверх ности кипятильников и холодильников раствора, а также диаметра регенератора (последний зависит в первую очередь от количества паров воды в нижней части регенератора). В работе [122] проанали зировано влияние ряда факторов на оптимальную величину Д£х, соответствующую минимуму приведенных затрат. Показано, что
AtTопт колеблется в интервале 7—14 °С; в работе [124] при при близительном расчете получена Д^т> опт = 17 °С.
Влияние концентрации СО- в регенерированном растворе. Анализ хода рабочей линии в условиях регенерации показывает, что коли чество парогазовой смеси в регенераторе уменьшается снизу вверх. Это объясняется тем, что в нижнем сечении регенератора подни маются в основном водяные пары, количество которых уменьшается снизу вверх по мере их конденсации. Объем выделившейся двуокиси углерода заведомо меньше объема сконденсировавшихся паров,
так как только на покрытие теплоты десорбции А Я 1 моляС02[62,8—
|
|
|
|
|
83,8 кДж/моль (15—20 ккал/моль)] необ |
||||||||||
|
|
|
|
|
ходимо |
сконденсировать |
1,5— 2 |
моля воды |
|||||||
|
|
|
|
|
[АН = |
40,6 |
|
кДж/моль |
(9,7 |
ккал/моль)]. |
|||||
|
|
|
|
|
Кроме^того, |
необходимо |
тепло |
на нагрев |
|||||||
|
|
|
|
|
раствора. |
В |
итоге |
dG/dx << 0. |
Так |
как |
|||||
|
|
|
|
|
dLldx^> 0, |
то из уравнения (11,56) следует, |
|||||||||
|
|
|
|
|
что dy/dx увеличивается с ростом х, т. е. |
||||||||||
|
|
|
|
|
d2y/dx2 ^ 0. |
При |
хемосорбции |
равновесная |
|||||||
|
|
|
|
|
линия в координатах у—х обычно бывает |
||||||||||
|
|
|
|
|
выпуклой по отношению |
к оси абсцисс, |
по |
||||||||
|
|
|
|
|
этому и |
d2y*ldx2 > 0 . |
|
|
|
|
|
||||
|
|
|
|
|
На рис. IV-42 показано характерное по |
||||||||||
|
|
|
|
|
ложение рабочей |
и равновесной |
линий |
при |
|||||||
|
|
|
|
|
регенерации МЭА-раствора [15]. |
Из рисунка |
|||||||||
|
|
|
|
|
видно, что форма |
равновесной линии такова, |
|||||||||
|
брастдоре |
|
что она |
может |
касаться |
рабочей |
линии в |
||||||||
Рис. IV-42. Характерное |
точке, соответствующей не концу |
аппарата |
|||||||||||||
положение |
равновесной |
при х = Xi |
|
или х = х2, а средней его части. |
|||||||||||
(7) п рабочей |
(2) |
липли |
Следовательно, |
несмотря |
на наличие движу |
||||||||||
при |
регенерации |
17%- |
щей силы |
десорбции |
на |
концах |
аппарата, |
||||||||
ного |
водного |
раствора |
процесс |
десорбции |
может прекратиться |
||||||||||
|
МЭА. |
|
|||||||||||||
|
|
'вследствие |
|
того, |
что |
движущая |
сила |
де |
|||||||
|
|
|
|
|
|
||||||||||
сорбции |
равна |
нулю |
в средней |
его |
части. |
Поэтому |
при расчете |
процесса регенерации раствора во многих случаях необходим анализ равновесных условий по всей высоте аппарата, а не только на его концах (как это было сделано выше при расчете расхода тепла по ми нимальному флегмовому числу вверху регенератора).
Анализ выполняется по существу так же, как и расчет минималь ного расхода тепла по условиям равновесия вверху регенератора. Различие заключается только в том, что рассматривают не весь реге нератор, а последовательно снизу вверх его части и рассчитывают минимальные расходы тепла, необходимые для регенерации раствора
от |
некоторых |
концентраций |
С 02 xt {хх< • х( ^ х2) до |
конечной |
|||
концентрации х 4 |
[65, 125, 126]. В |
качестве допущения |
принимают, |
||||
что |
х = х*, т. е. t = £Кип(Рр1 х) и |
что Ф = Ф*. Если |
получаемые |
||||
расчетом значения Qmin, t (или qm\n, /) меньше соответственно |
величин |
||||||
нии |
2 и 9min, 2» найденных из условий равновесия в верхнем сече |
||||||
(сечение |
2) |
регенератора |
по |
уравнениям (IV, 49) |
и |
(IV, 54), |
т. е. если |
|
величина |
<?т т, Д?тт, 2 |
= |
Зит, х/?тт> а < |
1 * |
то |
истин |
||||||||||
ный расход тепла равен @mjni 2 (gmin, 2). |
В противном случае расход |
|||||||||||||||||
тепла равен наибольшей из величин |
|
|
(gmin, ,)• |
|
|
|
|
|||||||||||
Расход тепла для участка регенератора от xi до х х приближенно равен |
||||||||||||||||||
|
|
|
Qmin» i = |
9дес, i + Фнагр, i + |
(?отд, i = |
|
|
|
|
|
|
|||||||
|
|
|
= GCO.t * А * , + Ь С р { 1Ц Р ^ т% Xi) - |
*1) + GC0„ 1гф 1 |
|
(IV,58) |
||||||||||||
где <?со2, i= L (xi — *1 ) — количество C02, извлекаемое из |
раствора на участке |
|||||||||||||||||
от xt до хх, |
т. е. |
|
|
|
|
|
|
|
|
|
|
|
|
|
|
|
||
<?min, l = |
L (xi — х х) A H i + |
LCp ( * ! ““ * / ( Р реГ, x / ) ) + |
jZ' ( * / — |
* l ) |
г Ф / ( Р р е Г , х . ) |
|||||||||||||
|
|
|
|
|
|
|
|
|
|
|
|
|
|
|
|
|
|
(IV,59) |
Отнеся расход тепла, необходимый для регенерации раствора |
от xi |
до хХ1 |
||||||||||||||||
к 1 м3 С 02, |
извлекаемой |
во |
всем |
регенератора |
[т. е. разделив |
^ на |
Сс о = |
|||||||||||
— L {х2 ~ |
яг)], получаем |
|
|
|
|
|
|
|
|
|
|
|
|
|
|
|||
7 m ln , |
i = |
Q i t дес“Ь Q l, н а г р |
о т д = |
xi—хл |
_ |
|
Сп(1%т> |
v\ — |
|
, |
||||||||
~х |
|
A H i -f* |
V |
\ |
P er* i ) ______ /_ |
|||||||||||||
|
|
|
|
|
|
|
2 |
|
1 |
|
|
|
х2 |
хх |
|
|
|
|
|
|
|
|
+ |
г |
XI—X1 |
ф |
|
|
|
|
|
|
|
|
|
(IV,60) |
|
|
|
|
|
|
|
х2 — Х\ |
*(р рег» xi) |
|
|
|
|
|
|
|
||||
При х = |
х2 уравнение (IV,60) |
переходит |
в уравнение _(_IV,54). |
qit дес ^ |
|
|||||||||||||
Из уравнения (IV,60) следует, что, |
если |
АЯ / ^ |
АЯ2, |
то |
?дес,2* |
|||||||||||||
Однако |
величина д/, 0тд |
может |
быть и |
больше |
д0тд,2- Величина д/, отд зависит |
от количества газа в данном сечении регенератора и от Ф* = ^н*О^СО** Значение GCOaвозрастает пропорционально ж/, а Ф* нелинейно уменьшается с ро стом Xi (см. табл. IV-17), что указывает на возможность максимума на кривой
qi, отд — xi*
В качестве примера на рис. IV -43 приведена зависимость д0тд от концент рации СО2 в растворе по мере его регенерацпп. Из рисунка видно, что в нижнем
сечении регенератора (xi |
-* д^) необходимый расход отдувочного-тепла |
д/, 0тд |
||
равен |
нулю. Это объясняется тем, что |
в уравнении (IV ,60) при хх Ф 0 |
доля |
|
С 02 |
l(xi — x^)!(x2 — Sj)], |
извлекаемого |
па этом участке регенератора |
(изме |
нение концентрации от ж/ до хх), по отношению к общему количеству С 02 при ац -+ 0 также стремится к нулю, а Ф* имеет конечное значение.
При возрастании хь значепие Ф/ уменьшается, a Xi — хх увеличивается, поэтому при малых хх (т. е. при тонкой регенерации) величина д/;0тд может про ходить через максимум, от которого будет зависеть общий расход тепла. Из графика на рис. IV-43 видно, что чем глубже регенерация, тем быстрее возра стает дотд,2 и максимум сдвигается в область малых xi\ при полной регенерации,
т. е. при xi -►0 , величина ^.отд-* оо, так как в данном случае Рсо2стремится
к нулю (а Ф* -► оо) быстрее, чем (ац — хх)/(х2 — д:х) -► 0. В результате и общий расход тепла qmin, i также может проходить через максимум.
Таким образом, в регенераторе имеется некоторое критическое сечение при х х ^ хкр ^ а:2, от количества отдувочного пара в кото ром зависит расход тепла. Если расход тепла, подаваемого в кипя тильник, меньше величины, минимально необходимой для десорбции в сечении хкр, fo процесс не идет (рабочая линия пересекается с равно весной линией). Следовательно, при малых значениях ах (в данном случае при аг ^ 0,15 моль/моль) расход тепла будет выше, чем
показывает расчет по уравнению (IV,54), и должен определяться по уравнению (IV,60).
Анализ условий в верхней части абсорбера показывает, что, как правило, тонкая регенерация при очистке от С 02 не является необходимой. Так, при a t = 0,15 моль/моль давление паров 20%-ного раствора МЭА при 30 °С составляет 3,33 Па (0,025 мм рт. ст.). Это означает, что при атмосферном давлении наименьшая концентра ция С 02 в очищенном газе у\ — 0,025/735 = 0,000034 = 0,0034%,
Рис. IV-43. Зависимость удельного расхода тепла на получение отдувочного пара дотд(я) от текущей степени карбонизации 2,5 н. раствора МЭА при различ ной концентрации С02 (ai) в регенерированном растворе и при Р р = 0,18 МПа (1 , 8 кгс/см2):
2 |
— ccj = 0,05 моль С02/моль МЭА; |
2 — = |
0,085 моль С02/моль |
МЭА; 3 — а, = |
= |
0,1 моль COi/моль МЭА; 4 — а х = |
0,15 моль С02/моль МЭА; 5 — a = |
0,2 моль С02/моль |
|
МЭА; 6 — at — 0,25 моль С02/моль МЭА; 7 — a t = |
0,3 моль*С02/моль МЭА. б — зависимость |
удельного расхода тепла на получение отдувочного пара чотд от at при тех же условиях, по строенная по максимумам на кривых рис. IV-43, а.
а при давлении 24,5-105 Па (25 кгс/см2) у* = 1,4*10“ 4%. Реальная величина у у*. Примем, что если у* = 0,1у, то равновесное давление на выходе из абсорбера не влияет на движущую силу абсорбции, а следовательно, степень регенерации не влияет на сте пень очистки. В "этом случае концентрация С 02 в очищенном газе равна примерно 0,03% при Р = 0,98-105 Па (1 кгс/см2) и 0,001 % при Р = 24,5-105 Па (25 кгс/см2). Следовательно, при такой и более грубой очистке газа отпадает необходимость в регенерации до а ^
^0,15 моль/моль.
Втаких случаях оптимальная степень регенерации определяется из условия минимального расхода тепла. При снижении xt можнб
увеличить емкость раствора Дя (т. е. уменьшить днаГр). Однако при этом, как следует из изложенного выше, возрастают флегмовое число в верху регенератора Ф2 и значение дотд. Следовательно, существует величина хи при которой расход тепла минимален.
Уравнение (IV,60) может быть использовано не непосредственно для расчета расхода тепла, а для расчета зависимости Ф2 от xt и затем с помощью уравнения (IV,54) для расчета q. Действительно,
количество отдувочного тепла, выходящее через верх аппарата, равно разности между отдувочным теплом в критическом сечении и теплом, потраченным Да нагрев и десорбцию раствора выше этого сечения (т. е. соответственно от t2 до £кр и от х2 до якр):
гФ2 —ГФкр>-[д я *«= *кр + |
Ср fap |
tj) |
(IV,61) |
х 2 — Х 1 |
Х2— |
Х1 |
|
Используя формулу (IV,61), можно определить минимальный расход тепла и оптимальное значение x t. В работе [125] оптимум най ден совместным решением уравнений типа (IV,54) и (IV,60).
а,,моль СО2!моль МЭД
Рис? IV-44. Зависимость минимального расхода тепла g при моноэтаноламиновой очистке от а х при Р р = 0,18 МПа (1,8 кгс/см2) п Д£т = 15 °С (<х2 = 0,4 моль С02/моль МЭА):
1 — ДЯ; 2—<70ТД| а[расход тепла на отдувку COt при расчете по уравнению (IV, 44)]; з—днагр; 4 — ДН + д нагр;‘ 5 — днаГр+ Д Я + д 0ТД, 2 [п0 УРавненш0 (IV,54)]; 6 — дОТД(по рис. IY-43); 7 — gmin / [п0 уравнению (IV,60)].
Рис. IV-45. Зависимость флегмового числа Ф2 от степени карбонизации регене рированного 2,5 н. раствора МЭА (при условии, что Ф2 не зависит от темпера туры насыщенного раствора).
На рис. IV-44 |
показана приближенная зависимость |
q и его |
|
составляющих от |
ах для одного |
из частных случаев. Как видно |
|
из рисунка, величина а0пт = 0,15 |
моль/моль. Практически a i, 0пт > |
||
> 0,15 моль/моль, |
так как расчет проведен при условии, |
что дви |
жущая сила десорбции в критическом сечении равна нулю. Анализ работы промышленных агрегатов, работающих по однопоточной схёме (см. рис. IV-31), показал, что а 0Пт колеблется от 0,17 до 0,23.
На рис. IV-45 в |
качестве примера показана зависимость Ф2 |
от а 1- При глубокой |
регенерации флегмовое число в верху регене |
ратора (и соответственно температура парогазовой смеси) быстро возрастает* при уменьшении а*. Расчеты проведены при ряде упро щающих условий (в частности, принято, что при изменении аА
величины At, х2 остаются постоянными, т. е. фактически не учи тывается влияние степени регенерации на коэффициент массопередачи в абсорбере и на режим теплообмена). Например, при умень шении х 1 несколько снижается и х2, т*е- замедляется рост Ах и уменьшение днагр. Полный учет всех факторов представляет собой более сложную задачу, которую целесообразно решать с -помощью ЭВМ [126, 127].
Из изложенного следует, что расчет флегмового числа Ф2 целе сообразно проводить в общем случае по уравнению (IV,61). Однако для многих частных случаев возможен следующий упрощенный расчет.
1 . Определить концентрацию С 02 в регенерированном растворе
(она меньше, |
равна или выше оптимальной величины, близкой |
к 0,15—0,23); |
если a i ^>а0пт> то величина Ф2 не зависит от a i- |
2. Определить температуру раствора t2 на входе в регенератор (равна ли она температуре кипения, выше или ниже ее).
3. |
Если a 1 ^ а опт и t2 = |
tKlin, то Ф2 = |
Ф2 и его находят по дан |
ным табл. IV-17. |
|
|
|
4. |
Если сы^аопт» но |
£2 <! ^кип» то |
Ф2 < Фг и оно зависит |
только от температуры t2\ в этом случае его находят по графикам на рис. IV-38 или расчетом по уравнению
РПгО
Ф2 - р Р~~РПгО
5.Если a i ^ а 0пт» но *2>Укип, тоФ 2 находятпо t'2, т. е. с учетом
дросселирования |
раствора [см. |
уравнения |
(IV, 55) |
и |
рис. IV-39]. |
|
6 . Если a i < C a 0iiT> то расчет ведут по |
уравнению |
(IV,61). При |
||||
этом учитывается |
температура |
раствора |
на |
входе |
в |
регенератор, |
так как всегда Упгс t'2, а t'2 ^ t2.
Влияние циркуляции раствора. Увеличение циркуляции раствора равнозначно уменьшению величины Ах (см. выше).. Однако с повы шением L одновременно возрастают коэффициенты массо- и тепло передачи ка и кг (в степени меньше единицы). При этом ка — Z,0»7, кт— JL0,8. В целом с ростом L увеличивается AtT.
Рассмотрим влияние |
L на |
д„агр. Так |
как GCo 2 = |
* а^ аДУср. лог |
(где ка — коэффициент |
массопередачи, а |
Fa — поверхность массо- |
||
обмена в абсорбере), то |
|
^ |
|
|
|
ф нагр |
LCр |
|
|
#нагр — Gco, |
kaFа А*/ср. лог |
(I V ,62) |
Следовательно, величина днагр изменяется обратно пропорцио
нально ка. Если ка |
^ A L 0*7, то |
|
|
|
_________ LCp А*т |
_ _ L°»3C p М т |
(IV , 63) |
||
Унагр |
AL°*‘Fa А уер , лог |
AF& А*/Ср. лог |
||
|
Если в уравнение (IV,57) ввести зависимость кт
At j —- |
*1--tb |
h - h |
|
kTFr |
BFr |
||
|
|||
Таким образом |
L C t |
14 L02CP |
|
|
|
||
CpL**(U-h) |
|
ClL^Hh-h) |
|
Ян = |
|
Al/cp. лог AF* (L0*Cp + BFr) |
Al/cp. лог^4/'а ^1 + L°*2Cp )
то
(IV,64)
(IV ,6 5 )
Построение равновесной и рабочей линий процесса регенерации.
Равновесную линию строят по |
данным рис. IV-13—IV-18, т. е. |
находят величину у* = PcoJPpei |
как функцию концентрации С 02 |
в растворе при заданном давлении в регенераторе, причем для каж дого значения а СОг находят Рсо* при t = £кнп. Если сопротивление регенератора велико, необходимо учитывать увеличение Р рег в на правлении сверху вниз.
Равновесную линию можно построить также по данным: Ф* =
= -Рн2о/РсО*- |
|
|
|
|
|
|
Так |
как |
|
|
|
|
|
|
t |
рсо2 = |
рсо2 |
|
|
|
|
у |
Рр*г |
PusO + Pc02 |
|
|
|
ТО |
|
|
|
|
|
|
|
-рг = - ^ ^ + 1 = ф*+ 1 |
у * = ф«+ Г |
Ф * = 7 Г -1 |
(IV.66) |
||
Расчет рабочей линии |
[6 , 128]' проводится, |
по существу, |
с |
по |
||
мощью |
тех же соотношений материально-теплового баланса, |
что |
Н расчет оптимальной степени регенерации. Различие проявляется при сопоставлении уравнения (IV,59) (записанного в приближенном виде без учета физического тепла ПГС и с некоторыми другими
допущениями) |
для минимального |
расхода тепла в |
i-ом |
сечении |
|
я уравнения для произвольного расхода тепла |
Qt ^ |
(?Iui |
|
||
Q i ^ L ( X i — *!) AHi + LCp |
— |
|
|
(IV.67) |
|
Уравнение |
(IV,67), по существу, является |
уравнением |
рабочей |
ли*ши в упрощенном виде с учетом указанных допущений. Уравне
ние (IV,59) для |
Qm\n, i является |
уравнением |
рабочей линии, |
касаю |
||
щейся равновесной |
линии. |
В реальном |
процессе |
Qt >> QmiIlt t. |
||
Следовательно, |
при |
заданном |
температура парогазовой |
смеси |
||
U ^ tj (рреГ, х.) |
соответственно |
Ф, (//) ^ Ф* (ярег, /•>. |
По существу, |
|||
в Уравнение (IV,67) |
заложено |
одно из двух допущений: либо при |
||||
расходе тепла Qt > |
Qm\n, ,• устанавливается |
термическое равновесие |
на каждой тарелке, т. е. температура раствора, стекающего с нее, раьна температуре парогазовой смеси, уходящей вверх (т. е. tLnrc =
= tit ж). |
Тогда |
Xi^>xU т. е. отсутствует равновесие |
процесса |
десорбции |
и tM> |
£кип; либо в любой точке регенератора |
£ж = гкнп |
и xt = xtu. |
>, но отсутствует термическое равновесие между |
парогазовой |
смесью и раствором (titnrcy> ж)* |
Данные о кинетике процесса ренегерации ограничены, поэтому невозможно с уверенностью отдать предпочтение одному из этих допущений. В работе [126] получено, что в любой точке регене ратора tt = £кнп. Это означает, что в процессе регенерации медлен ным является процесс теплообмена парогазовой смеси и жидкости,
а не процесс десорбции, что не доказано. |
|
Однако оба допущения приводят к |
одинаковым уравнениям |
(без учета физического тепла парогазовой |
смеси). |
Для расчета уравнение (IV,67) удобно использовать в следующем виде:
Ql — L C p (ti — tj+i) |
|
Ах = (дг/ц.1 — х{) |
(IV,68) |
L ( A H i + |
r O i ) |
где Qi — количество тепла, приходящее на данную тарелку снизу с парогазовой смесью; А х — изменение концентрации раствора на тарелке; — */+ 1 — изменение температуры раствора на данной тарелке.
Расчет |
ведут следующим образом: |
|
|
|
|||
1 ) задаются |
концентрацией |
С 02 в регенерированном |
растворе |
||||
на выходе из. кипятильника x t |
(кипятильник работает при прямо |
||||||
токе жидкости |
и паров); |
|
|
|
|
||
2) определяют концентрацию С 02 на входе в кипятильник (выход |
|||||||
из регенератора). При этом принимают, что температуры На входе |
|||||||
и выходе |
из кипятильника одинаковы, |
т. е. |
|
|
|||
|
|
|
Д # к и п --- |
Q KHU |
|
|
(IV.69) |
|
|
|
L ( А Н + Ф г ) |
|
|||
|
|
|
|
|
|
||
где #кип — количество тепла, подведенное в кипятильник с теплоносителем; |
|||||||
3) |
задавая в |
уравнении |
(IV,68) |
температуру |
ti+1, |
находят по |
|
равновесным данным |
Ф/ + 1 и затем х1+1. |
|
|
||||
Величина |
равна разности между |
количествами |
тепла, под |
||||
веденного в ( I - |
I ) - O M сечении и отведенного в г-ом. сечении |
с паро |
|||||
газовой смесью, |
т. е. |
|
|
|
, |
|
|
|
|
Qi ~ (<?со„ |Ф/в11-<?соЯв*+1 Ф/) г |
|
(IV’70) |
где
GCOui —GCOtt 1-1 + L (xl —xi-l)
При вводе и выводе раствора в нескольких точках по высоте регенератора рабочая линия представляет собой ряд участков, стыки между которыми (места ввода и вывода раствора) определяют расчетом смешения потоков раствора.
В работе [128] уравнение рабочей линии (с учетом физического тепла всех потоков) выглядит следующим образом:
Wj (Ф/— Ф/+1 ) (r/-f Ср At)-\-[w{ (9,25-|-6,4Ф/+1 — CpLj)\ At
т {Ф/+1 г/ + А Я — [9,25 + 6,4Ф/+1— Ср (1 + Ф/+1)] ДЯ) 1 ’ }
где L, w, m — соответственно потоки раствора, С 02 и МЭА, моль/ч; С, г, ДЯ — соответственно теплоемкость раствора, теплота испарения и интегральная те плота растворения С 02; Ф — флегмоцос число.
В уравнение введены теплоемкости воды и С 02, равные соответст венно 18 и 9,25 кал/(моль*°С), ц эмпирическая зависимость г от температуры.
Иа рис. IV-42 в качестве примера приведена рабочая линия процесса регенерации.
Построением рабочей и равновесной линий регенератора за канчивают технологический расчет регенератора и расчет расхода тепла.
Расход тепла при использовании схем очистки
сразделенными потоками
Впоследние годы в промышленности широкое распространение получили различные варианты схем МЭА-очистки с разделенными потоками абсорбента [119—121, 125]. Такие схемы применяются также и в других процессах очистки, например при очистке горячими растворами поташа. Основная задача, решаемая при создании таких схем, — снижение расхода тепла при обеспечении заданной степени очистки газа.
Целесообразность таких схем [119] следует из второго закона термодинамики, по которому необходимым условием снижения расхода энергии является увеличение обратимости процесса. Это может быть достигнуто приближением рабочей линии процесса к равйовесной. (При обратимом процессе рабочая линия совпадает с равновесной.) Это условие является необходимым, но недостаточ ным, т. е. оно дает лишь принципиальную возможность снизить расход тепла. Практически этот путь не всегда может привести к же лаемому результату, так как снижение потерь от необратимости на одной стадии может сопровождаться увеличением потерь на других стадиях.
Строго говоря, тепло в процессе не расходуется, а лишь теряет
свой потенциал, |
переходя от t = |
140—160 °С (пар, подаваемый |
в кипятильник) |
до t = 70—100 °С |
(парогазовая смесь, раствор |
в холодильнике). Увеличение обратимости позволяет снизить при рост энтропии, т. е. уменьшить потери работоспособной энергии — эксергии [123]. Поэтому оно может привести не к снижению расхода пара, а к другим положительным эффектам.
Выше было показано, что при однопоточной схеме, т. е. при вводе и выводе всех потоков на концах регенератора, рабочая линия регенерации вследствие криволинейности равновесной линии может приблизиться к ней лишь в одной точке. Следовательно, даже при идеальной эксплуатации и бесконечно большой высоте аппарата процесс регенерации будет далек от обратимости. Ход равновесной линии зависит в значительной мере от физико-химических свойств данной системы. Ход рабочей линии может быть изменен, если
13 За к, 1 ЛG 0 |
193 |
вводить и выводить потоки энергии, вещества (или того и другого) по всей высоте регенератора. В идеальном процессе число потоков должно быть бесконечно велико. Состав и температура потоков должны соответствовать равновесным условиям в соответствующих точках аппарата.
Способы инженерного решения этой задачи могут быть разно образными. Практически применяются (см. выше) схемы с двумя потоками регенерированного раствора и с двумя или тремя#потоками насыщенного раствора.^
Схемы с разделенными потоками регенерированного раствора (см. рис. IV-35 и IV-46) позволяют глубоко регенерировать часть
Рис. IV-46. Равновесная и рабочая линии при регенерации но схеме с двумя потоками регенерированного МЭА-раствора:
1 — равновесная линия; 2 — рабочая линия зоны грубой регенерации; 3 — рабочая линия зоны тонкой регенерации; 4 — рабочая линия процесса в кипятильнике; 5 — точка вывода грубо регенерированного раствора; 6 — точка входа в кипятильник; 7 — точка вывода тонко регенерированного раствора.
раствора при одновременном некотором сокращении расхода тепла [125]. При анализе зависимости расхода тепла от степени регенера ции было показано, что флегмовое число увеличивается при умень шении концентрации С 02 в регенерированном растворе, особенно если а х <^0,15—0,2 моль/моль. Из рис. IV-42 видно, что при глубо кой регенерации рабочая линия в верху аппарата сильно откло няется вниз от равновесной, т. е. у <jy*, Ф > Ф*. В результате, несмотря на увеличение поглотительной способности раствора, общий расход тепла возрастает.
В то же время необходимость глубокой регенерации раствора иногда возникает при тонкой очистке газа. В этом случае при выводе, раствора из регенератора двумя потоками можно избежать увеличе ния расхода тепла. При отводе грубо регенерированного раствора из регенератора в точке 5 (см. рис. IV-46) угол наклона части рабо чей линии ниже точки 5 уменьшается вследствие снижения отноше ния LIG [см. уравнение (11,55)] и она приближается к равновесной линии.
Нижнюю часть регенератора можно рассматривать как отдель ной аппарат. Выходящая из этого аппарата парогазовая смесь (ПГС)ц является теплоносителем и используется для регенерации
раствора в верхней части регенератора. Доля глубоко регенериро ванного раствора не должна быть слишком велика, иначе количество тепла, уходящего с (ПГС)н, будет больше необходимого [возрастут потери тепла с (ПГС)ц]. Расчет теплового баланса показывает, что доля двуокиси углерода, выводимой на тонкую регенерацию до а = = 0,08—0,1 моль/моль, должна составлять 30—40% общего количе ства СО2 в условиях процесса, изображенного на рис. IV-35. Этому соответствует доля глубоко регенерированного раствора, равная примерно 40—50 %.
Расход тепла при разделении потоков регенерированного рас твора снижается не только при тонкой очистке (вследствие умень шения флегмового числа при глубокой регенерации), но и при грубой очистке (за счет увеличения поглотительной способности рас твора). В последнем случае (т. е. при переходе в действующей уста новке грубой очистки на глубокую регенерацию части раствора) расход тепла можно снизить иногда на 1 0 —1 2 %, но в ряде случаев эта величина составляет лишь 3—4%.
При тонкой очистке переход на более грубую регенерацию части раствора дает больший эффект, который может достигать 25% (если раствор при однопоточной схеме регенерировался до концентрации СО2 менее 0 ,1 моль/моль).
Схемы с разделенными потоками насыщенного раствора подробно описаны в работах [119—121]. Основная цель, которую преследуют при разделении потоков насыщенного раствора, заключается в сни жении температуры парогазовой смеси на выходе из регенератора и соответственно в уменьшении потерь тепла с парогазовой смесью. При заданных давлении в регенераторе и степени регенерации флегмовое число зависит только от температуры насыщенного раствора
(Ф2 (*пгс) ^ |
Ф2 (г2) ^ |
Ф(,.,). Поэтому, чем ниже t2, тем |
меньше |
Ф2. |
Если t 2 |
£Кигм |
то верхняя зона (см. рис. IV-33) |
от |
£кип |
до t = t2 превращается в зону теплообмена парогазовой смеси с рас твором. Формально в этой зоне мог бы протекать иногда процесс абсорбции, однако скорость абсорбции заведомо меньше скорости
теплообмена. Следовательно, уменьшая t 2, |
можно |
было бы свести |
к нулю потери тепла с парогазовой смесью |
дотд. |
Однако при этом |
возрастают AtT и потери тепла в холодильнике дхол. Поэтому, как показано выше, существует оптимальная величина Д£т.
Использование схем с разделенными потоками позволяет путем введения раствора в регенератор цвумя-тремя потоками, нагретыми до разных температур, достичь малого значения Д£т и одновременно снизить потери тепла с парогазовой смесью.
Рассмотрим в упрощенном виде тепловой баланс верхней части регенератора при двухпоточной схеме (см. рис. IV-33, обозначения
указаны на рисунке) при условии,4 что tnrc = |
t2 |
LxonCp(£3-- £а)Н" ДЯ^ХОЛ (^2--*з) “1“ ^ (®2 |
^l) Г^2 = |
= L (х3 — х { ) гФ3 = Ь (#2 **т) гФ3— L (х2 —х3) гФ 3
где Lxол — количество более холодного (верхнего) потока; L = Ьхол + £г®р — общая циркуляция.
Правая часть уравнения представляет собой количество тепла, поступающего с парогазовой смесью в верхнюю зону аппарата (от t9 до Q . Отсюда можно записать, что
1Ср (*з“ |
(х2—хз) + (*2— *з) гф3 = г [(я2 *i) (Фз — ф а)1 |
где I = LxoJL — доля более холодного раствора, необходимая для полного использования тепла парогазовой смеси.
Отсюда оптимальная величина I
Ахг (Ф3 — Ф")
(IV,72)
Ср (*3- Q + Д*2-з (АЯ + гФз)
Если десорбция в верхнем участке регенератора не происходит, то уравнение (IV,72) упрощается
Дат (Ф3 — Ф2)
(IV,73)
Двухпоточная (или трехпоточная) схема может быть применена в различных вариантах: с увеличением поверхности теплообмена и при постоянной поверхности за счет ее перераспределения. Неко торые варианты таких схем были приведены выше (см. рис. IV-33 и рис. IV-34). Во втором случае расход тепла снижается вследствие не только разделения потоков, но и увеличения поверхности тепло обмена. Однако применение двухпоточной схемы позволяет более эффективно использовать теплообменники.
Рассмотрим |
пример |
процесса очистки: В жЭА = 2 ,5 моль/л, а 1 = 0,2 |
моль |
|||||||||
С 02/моль |
МЭА, |
а а = 0,4 |
моль/моль, |
2, = 118 °С, |
Д*т = |
20 °С, |
t2 = |
98 °С, |
||||
Ф2 = |
1,1 |
моль Н 20 /моль |
С 02, iHjO = |
520 ккал/м3 паров |
Н 20 (2,18 МДж/м3). |
|||||||
Тогда |
|
- |
Ср^т |
|
|
|
980 • 20 |
|
. |
л |
, , |
|
|
|
+ |
1 Ф2= 720+ |
|
|
|||||||
|
q = A H + |
Дд; |
2 2t4 . 2 ,5 (0,4—0,2) |
+ |
520-1,1 — |
|
||||||
|
|
|
= —3040 ккал/мз С02 (12,7 МДж/м3) |
|
|
|
|
|||||
Если |
увеличить |
в 2,4 раза поверхность теплообмена, то |
|
A t2 = |
10 °С, |
t2 = |
||||||
= 108 °С, |
Ф2= |
2,3, 1*Н а 0 = |
530 ккал/м3 паров Н 20 |
(2,22 |
МДж/м3) |
|
||||||
|
|
|
980.10 |
|
|
+ 530 • 2,3 = —2820 ккал/м3 COs (12,0 МДж/м3) |
||||||
q = 720 -f ~22 4 .~2 5 (0~4 —0 2) |
т. е. расход тепла уменьшится примерно па 7%. При двухпоточной схеме можно перегреть часть (1 — 1) раствора до 14)8 °С, а верхний поток оставить при преж ней температуре (т. е. t2 = 12, Ф2 = Ф£).
В этом случае по уравнению (IV,73)
22,4.2.5 (0,4 - 0.2) - 425 (2.3 -1 ,1 )
1~ |
980(108-98) |
~ ~ 0 ,58 |
. Л<т = 0,58 • 20 + 0.42 • 10 = ~16 °С
Поверхность теплообмена при этом должна быть увеличена лишь в 1,5 раза. Расход тепла
„ |
980 • 10 |
. |
9* = 720+ 2 2 ,4 -2 5 (0 4 -0 2 ) |
+ 520-1.1 = 2690 ккал/мз С02 (11,25 МДж/м») |
Таким образом, при почти втрое меньших дополнительных затратах на тепло обменники достигнут больший эффект (1 1 ,5 %).
Эффект от применения двухпоточной схемы возрастает при уве личении степени карбонизации насыщенного раствора, когда в верх
ней |
зоне |
регенератора |
идет десорбция С 02 (Л#2-з > |
0). При этом |
доля |
холодного потока уменьшается [уравнение (IV,72)], что позво |
|||
ляет снизить Д£т. |
|
|
||
При |
двухпоточной |
схеме большую роль играет |
правильная |
организация теплообмена. Наибольший эффект от применения
двухпоточпой схемы (при |
одинаковом |
значении AtT) равен |
|
|||||
|
|
|
bq = q — c f |
г(Ф 2 — Ф') |
|
( I V ,74) |
||
В пределе при Ф2 |
0 эффект от разделения потоков насыщенного |
|||||||
абсорбента |
может |
достигать 20—25%. |
|
|
||||
Это подтверждено результатами опытно-промышленных испыта |
||||||||
ний [119, |
120] |
и |
промышленной эксплуатации |
процесса |
[121]. |
|||
Расчет процесса |
приведен |
в работах |
[119—121]. |
|
|
|||
Распространен вариант двухпоточной схемы без -увеличения |
||||||||
поверхности |
теплообмена |
(схема |
с |
«холодным |
байпасом» |
[1 2 1 ], |
||
см. рис. IV-33). В |
работе |
[121] |
приведена методика расчета этой |
схемы. При подаче части (около 10%) насыщенного раствора в обход теплообменников возрастают потери тепла с регенерированным раствором (температура его перед холодильником увеличивается примерно на 2 °С). Однако при этом уменьшается температура паро газовой смеси, что в итоге при правильном выборе доли холодного потока позволяет снизить расход тепла на 7—8 %.
При расчете задаются значениями С, Дя, |
i5, |
L±1 Кт, |
FT1 J2, |
|
*4, |
Ф2 — параметрами работы действующей |
однопоточной |
схемы |
|
(см. |
рис. IV-31). Затем определяют для различных значений |
I вели |
чины *3, |
$4, Ф3, Ф2, AtT, ф", Aq = g* — q" по уравнениям, |
при |
веденным в работе [1 2 1 ], и находят оптимальное значение Z, соответ |
||
ствующее |
максимуму Ад: |
|
|
Дд= г ( Ф ^ - ф'а) - ^ г ( * ; - ‘;)= Д 7 ПГс - д ? Р |
( I V ,75 ) |
где Адпгс — снижение расхода тепла за счет использования тепла парогазовой смеси; Адр — увеличение потерь тепла с регенерированным раствором в хо лодильнике при переходе на схему с «холодным байпасом»
(IV.76)
(пз баланса верхней зоны регенератора между t\ и /3)
(IV,77)
(из теплового баланса теплообменника 3).
Кроме того, для определения t3 используется система уравнений:
<?;=KTFTд = KTFT(*;- |
ч)= LCP - |
ч) |
(IV,78) |
|
Q ' = K TFTb t; = L C p (1 |
- 1 ) (t3- h ) |
|
(IV,79) |
|
(fj— h) —(<4~ h) |
|
(IV,80) |
||
2,3 lg |
1 — *3 |
|
||
l |
-rf- |
|
|
|
6 |
г4“ *5 |
|
|
|
Данные [121] показали, что при |
внедрении |
описанной |
схемы |
с «холодным байпасом» храсход тепла снизился от 2,56 ккал/1000 м3 СО2 (или 10,7 ГДж/1000 м3) до 2,36 ккал/1000 м3 С 02 (или 9,87 ГДж/1000 м3) [без учета затрат на вакуумную разгонку в обоих случаях].
Более сложный вариант — многопоточная схема (см. рис. IV-35) — позволил в сочетании с высоким насыщением раствора при абсорб ции под давлением снизить расход тепла при МЭА-очистке до 1220— 1300 ккал/м3 СО2 (5,11—5,45 МДж/м3) (включая разгонку раствора под давлением), т. е. примерно в два раза по сравнению с расходом тепла в лучших агрегатах, работавших под атмосферным давлением по однопоточной схеме и при низких степенях насыщения раствора.
Аппаратурное оформление и кинетика процесса регенерации растворов аминов. Разложение карбаматов и карбонатов, диффузия молекул СОо в жидкости к поверхности раздела фаз, переход их в парогазовую фазу и диффузия молекул С 02 в основную массу газа сопровождаются испарением воды из раствора. Энергия активации реакции разложения карбаматов составляет [129] 115 кДж/моль (27,5 ккал/моль).
Литературные данные по кинетике процесса регенерации проти воречивы. По мнению авторов работы [15], лимитирующей стадией является разложение сравнительно стойких химических соединений. По данным [108], разложение карбаматов протекает в основном до статочно быстро. К. п. д. тарелок имеют значения, близкие для процессов, скорость которых контролируется диффузией в газовой фазе. Сделан вывод о том, что по крайней мере в исследованных условиях скорость массопередачи при десорбции С 02 из раствора МЭА такова же, что и при абсорбции хорошо растворимого газа.
Наиболее полно кинетика процесса регенерации исследована в работе [107]. Авторы изучали процесс десорбции С 02 в опытном аппарате с пятью ситчатыми тарелками. Тарелки имели стесненный слив жидкости; высота сливного порога составляла 30—130 мм. По опытным данным были рассчитаны коэффициент массопередачи и к. п. д. тарелки
где хПу хк и .г* — соответственно концентрация С 02 в жидкостп, начальная, конечпая и равновесная со средней на тарелке концентрацией С02 в газовой фазе.
Коэффициент массопередачи, рассчитанный по жидкой фазе, увеличивается при повышении степени карбонизации а, плотности орошения и высоты пенного слоя; влияние скорости газа незначи тельно. К. п. д. тарелок уменьшается при понижении степени карбо
низации: при |
а |
= |
0,4—0,5 величина ц составляет 0,25—0,4, при |
а = 0,25—0,3 |
у\ |
= |
0,15—0,25. К. п. д. снижается также при увеличе |
нии скорости жидкости, причем особенно заметно — при больших расходах жидкости.
Результаты исследования позволили рекомендовать следующий оптимальный режим работы ситчатых тарелок: скорость газа — 1,2—2 м/с; скорость жидкости — 40--60 м/ч; высота пены — не более 200—250 мм. Для указанного режима рекомендуется следу ющее расчетное уравнение (при концентрации МЭА 2—2,5 моль/л):
11 = 7,48 + 57,49а+ 31«2
Анализ опытных данных приводит к заключению, что при высо ких а разложение карбаматов не является лимитирующей стадией. Диффузионные сопротивления в газовой и жидкой фазах, вероятно, соизмеримы. При уменьшении а все большее сопротивление начи нает оказывать жидкая фаза, причем существенное значение имеет скорость разложения химических соединений.
Регенератор имеет выносной кипятильник кожухотрубчатого типа. В нижней части регенератора расположена глухая тарелка колпачкового типа, с которой раствор МЭА стекает по трубопро воду в трубки кипятильника. Из кипятильника пар и кипящий раствор подаются в нижнюю часть (куб) регенератора; регенериро ванный раствор выводится из аппарата, а пар поступает под глухую тарелку, барботирует через раствор, находящийся на тарелке, и под нимается вверх по регенератору.
В верхней части регенератора расположен распределитель ороше ния и тарелки для промывки газа флегмой от паров и брызг МЭА.
Ранее на отечественных заводах применялись регенераторы глав ным образом с кольцевой керамической насадкой, располагавшейся двумя слоями высотой по 6 м. В процессе эксплуатации насадка регенератора изнашивается, что приводит к уменьшению эффектив ности аппарата и увеличению расхода пара. Кроме того, вследствие забивки теплообменников кусками насадки снижается температура насыщенного раствора перед регенератором (т. е. возрастает недорекуперация), что вызывает дополнительное увеличение расхода пара. Поэтому дальнейшее использование насадки в регенераторе следует считать перспективным только при повышении ее механической проч ности, а также в случае применения термостойких пластических материалов. Данные по эксплуатации промышленных насадочных регенераторов диаметром 3,2 м при давлении в верхней части 0,166 МПа (1,7 кгс/см2) приведены в табл. IV-18.
Концентра |
Концентра |
Флегмовос |
Расход пара |
ция СО£ в |
|||
ция, % |
растворе,г/л |
число Ф2 |
|
аО
я°
G -
Расход |
|
Я 1Q |
Я° |
|
|
« § |
|
|
|
|
|
раствора, |
а . |
|
|
a D |
|
|
|
|
|||
м3/ч |
|
ю |
>» |
0) |
|
|
>• S |
|
|
|
т/т |
|
Ен |
Н |
|
|
о |
|
|
т/ч |
|||
|
|
а ** |
я о |
|
|
я м |
|
|
Nib |
||
|
|
~s g |
аи |
|
|
&! |
|
|
|
||
|
◄3 |
д ой |
Sg |
|
|
|
|
|
|
||
|
|
|
§8 |
|
|
|
|
||||
|
со а |
|
а й |
|
|
« 2 |
|
|
|
|
|
|
Я* |
|
ня |
|
|
|
|
|
|
||
|
Регенератор• «AS i; |
температура раствора па входе 100 9С |
|
||||||||
315 |
11,7 |
1,70 |
114 |
42,0 |
13,6 |
101 |
1,71 |
1,75 |
32,6 |
|
|
400 |
11.8 |
1.87 |
115 |
41,8 |
15,2 |
97 |
1,20 |
1,30 |
33,4 |
|
|
420 |
12.0 |
2,00 |
117 |
40,3 |
14.8 |
98 |
1,30 |
1,30 |
33,4 |
|
|
440 |
11.6 |
1,87 |
117 |
37,0 |
14,4 |
99 |
1,42 |
— |
36,9 |
|
|
450 |
11.0 |
2,20 |
117 |
33,0 |
13,2 |
100 |
1,55 |
1.71, |
38,7 |
|
|
|
Регенератор |
Л5 2; температура раствора |
на входе 110 9С |
|
|||||||
350 |
19,3 |
1.4 |
и б |
46.5 |
18,8 |
102 |
1,87 |
— |
32,5 |
|
|
|
|
||||||||||
370 |
19,6 |
1,3 |
117 |
61,2 |
28,2 |
98 |
1,47 |
— |
30,8 |
|
|
380 |
20,0 |
1.3 |
117 |
61,6 |
30,4 |
99 |
1,41 |
— |
29,9 |
|
Зарубежные фирмы пшроко используют в регенераторах насадку различных типов [130].
В настоящее время все большее распространение получают та рельчатые регенераторы. Так, на основании опытных данных, полученйых на лабораторной и модельной установках [107], для извле чения СО2 из топочных газов рекомендован промышленный регене ратор с ситчатыми тарелками. Аппарат диаметром 0,67 м имеет семь ситчатых тарелок со стесненным сливом жидкости, свободное сече ние тарелок 17%, высота сливного порога 70 мм. Степень извлечения СО2 из раствора МЭА составляет 0,5—0,55. Гидравлическое сопро тивление тарелок в среднем 490 Па (50 мм вод. ст.).
Заслуживает внимания также опыт эксплуатации регенераторов с ситчатыми тарелками [6 , 108] со свободным сливом. В одном из них диаметром 3 м использованы ситчатые тарелки с высотой слив ной перегородки 0,35 м. Свободное сечение тарелок 3,5%, диаметр отверстий 6 мм, расстояние между тарелками 0,8 м. Регенератор имеет семь тарелок и включен в схему в качестве первой ступени регенерации. Аппарат работает устойчиво в широком диапазоне нагрузок, в частности при расходе раствора 360 м3/ч и нагрузке кипятильника по пару 30 т/ч. При дальнейшем увеличении нагрузки по пару наступает захлебывание аппарата.
Регенератор обеспечивает регенерацию 17%-ного раствора МЭА от 55—60 до 16—20 г/л и до 28—33 г/л для 22—33%-ного раствора.
Температура насыщенного |
раствора |
составляет 78 °С, температура |
в верхней части аппарата |
—102 °С, |
в нижней части — 115 °С. |
В тарельчатом регенераторе [108, 131] диаметром 3 м нагрузка по раствору и парогазовой смеси увеличена благодаря применению тарелок с большим свободным сечением (до 1 0 %) и увеличению площади переливных устройств от 0,37 до 0,75 м2. Сечение переливов выбрано с таким расчетом, чтобы скорость жидкости в них не пре вышала 0,1—0,2 м/с. В регенераторе 14 тарелок, расстояние между ними изменяется по высоте аппарата от 1 ,2 м в пижпей части до 0,8 м в верхней части. Высота сливной перегородки уменьшена до 0,2—0,25 м. Ниже приведены показатели работы такого регене ратора:
Расход раствора, м3/ч |
380—500 |
|
Расход пара, |
т/ч . . |
35—52 |
Концентрация МЭА, % |
13—15 |
|
Температура, |
°С |
90 |
насыщенного раствора . . . |
||
в верхней |
части регенератора |
1 0 0 — 1 0 1 |
в нижней |
части регенератора |
123 |
Сопротивление аппарата |
0,294 |
|
1 1 а . 10-5 |
|
|
кгс/см2 . . . |
0,3 |
|
Содержание С 02, г/л |
49—50 |
|
в насыщенном растворе |
||
па 12-й тарелке |
36,6 |
|
на 7 -й тарелке |
25,5 |
|
на 2-й тар ел к е..................................................... |
17,0 |
|
в регенерированном растворе |
14—15 |
Таким образом, примерно одна треть общего количества С 02 извлекается на семи нижних тарелках, остальные две трети — на семи верхних.
Вагрегатах синтеза аммиака мощностью 1360 т/сут работает регенератор с ситчатыми тарелками, диаметр которого 4,5 м, число тарелок 22 (в нижней секции 10 ); в верхней части его расположены 3 колпачковые тарелки. Регенератор обеспечивает производитель ность по раствору до 1200 м3/ч в верхней секции и до 600 м3/ч в ниж ней секции.
Вверхней секции перфорированная часть тарелок имеет свобод ное сечение 5% (тарелки №№ 16—22) и 8 % (тарелки №№ 11—15). Площадь сечения сливного кармана 1,92 м2. Напряженность слива составляет около 350 м3/(м-ч). Скорость парогазовой смеси в барботажной части тарелки — 0,8—1,6 м/с. В нижней секции все тарелки имеют свободное сечение 8 %; напряженность слива около 200 м3/(м -ч), скорость парогазовой смеси 1,4—1,7 м/с; высота сливного порога всех тарелок 0 ,22 м.
Объем парогазовой смеси Удгс резко изменяется по высоте аппа рата (более чем в два раза) и может быть рассчитан по формуле
^ п гс™ ^ * |
ai) |
0*22,4L (1 + Ф/) |
где а а и а х — степени карбонизации |
раствора на входе и выходе из зоны; |
|
L — количество раствора, м3/ч; |
Ф* — флегмовое число в данном сечении реге |
|
нератора» |
|
|
Анализ работы регенератора показывает, что тарелки работают в неравномерном режиме; часть жидкости протекает через отверстия.
Для процесса регенерации, проходящего с точки зрения кинетики сравнительно легко, целесообразно применять более простые по конструкции тарелки провального типа.
В табл. IV-19 приведены сравнительные данные [131] испытаний регенератора с тарелками провального типа и насадочного регенера тора с высотой насадочного слоя 12 м на 16%-ном растворе МЭА. Диаметр обоих аппаратов 1,6 м; свободное сечение тарелок 25%; диаметр отверстий 6,5—7 мм; тарелки изготовлены из углероди стой стали.
Таблица IV-19. Показатели работы регенераторов в насадкой и с провальными тарелками
|
|
|
Тарельчатый регенератор |
|
|
|||
112,5 |
43,2 |
18,3 |
9,13 |
1 0 2 |
123 |
103 |
3,26 |
0,577 |
117,0 |
43,0 |
16.4 |
9,37 |
102,5 |
123,5 |
103,5 |
3,00' |
0,618 |
120,5 |
43.0 |
16,4 |
9,25 |
103 |
123,6 |
103 |
2,93 |
0,618 |
131,1 |
38,8 |
16,4 |
9,13 |
1 0 2 |
124 |
103 |
3,12 |
0,577 |
133,5 |
40,4 |
17,4 |
9,22 |
103 |
123 |
103,5 |
3,06 |
0,570 |
138,8 |
41,2 |
19,7 |
9,31 |
102,5 |
122.5 |
104 |
3,12 |
0,522 |
|
|
|
Насадочный |
регенератор |
|
|
|
|
-51,9 |
48,5 |
21,4 |
4,25 |
103,5 |
12 0 |
105 |
3,03 |
0,588 |
51,9 |
49,3 |
2 0 ,8 |
4,25 |
103.5 |
12 0 |
105 |
2,87 |
0,578 |
51.9 |
46,7 |
21,7 |
4,25 |
103,5 |
119 |
104 |
3,28 |
0,535 |
51,9 |
42,5 |
18,4 |
4,12 |
105,5 |
1 2 0 |
105,5 |
3,29 |
0,577 |
Из табл. IV-19 следует, что при одинаковой глубине регенерации, степени извлечения и удельном расходе пара производительность регенератора с тарелками провального типа вдвое превышает про изводительность насадочного регенератора. Удельный расход пара в регенераторе с ситчатыми тарелками вследствие большего гидра влического сопротивления несколько превышает расход пара в наса дочном регенераторе и регенераторе с провальными тарелками (при прочих равных условиях).
Успешно эксплуатируется промышленный регенератор диаметром 3 м с тарелками провальйого типа [431]. Для регенерации раство ров МЭА применяют также клапанные тарелки. В однопоточных
схемах очистки число тарелок обычно колеблется от 1G до 25 [132]. В двухиоточных схемах число тарелок возрастает до 30—35.
Втабл. IV-20 приведены результаты обследования регенератора
спереливными клапанными тарелками, работающего на Черкас
ском ХК (данные получены Вераняном Р. С., Газизулииым В. М. и Рощиным Б. Е.).
Таблица IV -20. Показатели работы регенератора с клапанными тарелками
PelJ Х О Д , |
м3/ч |
раствора |
парогазовой смеси в ниж нем сечении |
Содержание
Г О . п
творс> г/л
на на входе вы ходе
Концентрация МЭА, % (масс.)
|
Температура, °С |
выхоназа кипяизде тильника |
парогазовой вынасмеси регеизходе нератора |
|
раствора в |
раствора в |
конвертиро гаванного |
||
абсорбере |
регенераторе |
|
|
|
вход выход |
вход выход |
|
|
|
505 |
, 60 |
400 |
72,3 |
10,4 |
15,4 |
33 |
57 |
90 |
1 2 1 |
' |
127 |
10 0 |
490 |
60 |
400 |
76,6 |
10 ,6 |
16.3 |
32 |
57 |
90 |
1 2 1 |
127 |
10 0 |
|
512 |
60 |
400 |
76.8 |
9,8 |
15,5 |
37 |
60 |
90 |
1 2 2 |
|
126 |
1 0 1 |
П р и м е ч а н и е . Давление в регенераторе 174 кПа (1,78 кгс/см*).
В регенераторе диаметром 4,5 м имеется 25 тарелок; на одной тарелке расположено 810 клапанов. Скорость *парогазовой смеси изменяется от 0,4 м/с в нижнем сечении колонны до 1,05 м/с в верх нем сечении. Сопротивление регенератора составляет 0,342-105 Па (0,35 кгс/см2). Среднее значение числа единиц переноса для регене ратора с клапанными тарелками, определенное методом графиче ского интегрирования, равно 17,9, что заметно выше, чем для реге нераторов с насадкой и ситчатыми тарелками. Указанный результат получен при расходе конвертированного газа 92 370 м3/ч (объем газа при н. у.).
Таким образом, расчет процесса регенерации слагается из следу ющих этапов:
определяют (стр. 155) степень карбонизации насыщенного рас твора и задаются технологической схемой процесса (определяют число потоков насыщенного и регенерированного растворов);
определяют оптимальные технологические параметры процесса регенерации (степень карбонизации каждого из потоков регенериро ванного раствора и затем температуру верха и низа регенератора);
рассчитывают расход тепла; строят рабочую и равновесную линию регенератора; определяют
число теоретических тарелок (или число единиц переноса); если изве стны коэффициент полезного действия тарелок или высота единицы переноса, определяют число тарелок или высоту насадки. Исходя из уравнений для предельных нагрузок рассчитывают диаметр аппа рата; зная число тарелок или высоту насадки, рассчитывают сопро тивление регенератора;
после гидродинамического и кинетического расчета аппарата уточняют расход тепла.
ПОБОЧНЫЕ РЕАКЦИИ ЭТАНОЛАМИИОВ С КОМПОНЕНТАМИ ГАЗА
При очистке газа от двуокиси углерода протекает ряд побочных процессов, в которых принимают участие двуокись углерода, кисло род, сернистые соединения, материалы аппаратуры и др. Скорость этих побочных реакций обычно невелика по сравнению со скоростью основных реакций. Однако при длительной циркуляции раствора в системе накапливаются побочные продукты. Это приводит к заби ванию и коррозии оборудования, ухудшает очистку, увеличивает расход тепла (вследствие уменьшения коэффициентов массо- и тепло передачи) и потери МЭА.
Термическая устойчивость водных растворов алканоламинов. В отсутствие двуокиси углерода МЭА в водном растворе термически устойчив. Так, при нагревании до 200 °С 20%-ного раствора МЭА в течение 120 ч и 58%-ного раствора МЭА в течение 70 ч его кон центрация не изменялась [пределы точности анализа 0 ,2 % (масс.)].
ДЭА и ТЭА менее термически устойчивы. При повышенных
температурах (ДЭА |
выше |
180 °С, ТЭА выше 170 °С) происходит |
их поликонденсация |
[133] |
с образованием смол. Таким образом, |
при наличии в растворе МЭА примесей ДЭА и ТЭА (что возможно при использовании некоторых сортов технического МЭА) скорость накопления примесей в растворе может увеличиваться. Целесо образно использовать МЭА, не содержащий ДЭА и ТЭА.
Реакции моноэтаноламина с двуокисью углерода. Показано, что при повышенных температурах возможно взаимодействие МЭА с СО2 с образованием нерегенерируемых продуктов. Эти реакции наиболее важны для процессов очистка газа конверсии метана, который почти не содержит кислорода и сернистых соединений. Описаны [134] следующие реакции МЭА с С 02* Первая стадия взаимодействия — образование оксазолидона-2
Н2С -С Н 2
(IV,81)
С
II
О
Многие исследователи считают, что при нагревании карбамата частично образуется оксазолидон-2. Возможно также, что оксазо- лидон-2 образуется непосредственно из N-оксиэтилкарбаминовой кислоты.
ц г _ртт
носi i 2CHaNH соон |
о; |
(IV,42) |
о
Вторая стадия процесса — реакция оксазолидоиа-2 с другой молекулой МЭА. При этом образуется 1 -(2-оксиэтил)-пмидазолидон-2
Н2С—СИ2 |
Н2С -С Н 2 |
|
'^N1-1 + HOCITJCHJNHO — ►H0CH2CIIa— |
) NH- ; - II 20 (IV,83) |
с |
с |
4 |
II |
о |
|
белое кристаллическое вещество, т. пл. 56,5 °С, т. кип. 182 °С при |
|
0,1 мм рт. ст., |
ограниченно растворимое в воде. Имидазолидон |
не вызывает коррозии, но, имея высокую температуру плавления, может забивать аппаратуру.
Третья стадия — гидролиз |
этого соединения с образованием |
|
К-(2-оксиэтил)-этилендиамииа (ОЭЭДА) |
||
Н2С -С И о |
|
|
НОСНоСНо—N/ |
\ . NII-j-IToO |
HOGH2CH2NHCH2CH2NH2 + COO |
\ |
/ |
|
|
С |
|
|
|
(IV,84) |
вязкой жидкости, т. кип. 243 °С, смешивающейся с водой во всех отношениях и обладающей щелочными свойствами. В процессе абсорбции ОЭЭДА может реагировать с С 0 2 с образованием других соединений. В итоге образуется смесь продуктов, регенерируемая при более высокой температуре, чем карбаматы и карбонаты МЭА. Показано, что в присутствии ОЭЭДА в растворе увеличивается ско рость коррозии [134].
Механизм побочных реакций МЭА с С 02 изучен не полностью. Известно, в частности, что оксазолидон-2 может образоваться и при обычных температурах, если в газе присутствует сероокись углерода. В работе [135] подробно изучен механизм и кинетика побочных реакций МЭА с С 02. В частности, на некоторых предприятиях, где на очистку поступает газ шахтной каталитической конверсии метана, был исследован состав рабочих растворов (табл. IV-21).
Таблица IV-21, |
Хроматографический анализ промышленных растворов МЭА |
||||
|
Концентрация, % |
(масс.) |
|
Доля продуктов |
|
|
|
|
|
|
|
|
|
оксазо- |
пмндазо- |
другие |
акций МЭА с |
МЭА |
ОЭЭДА |
СО 2, % (отн.) |
|||
лидоп-2 |
лидон |
примеси |
|
||
19,8 |
0,2 |
Следы |
0,3 |
0,9 |
35,7 |
15,5 |
0,5 |
Т о ж е |
0,2 |
0,1 |
87,5 |
16,2 |
0,1 |
0,1 |
— |
0,1 |
66,7 |
14,3 |
0,1 |
0,1 |
Следы |
0,1 |
66.7 |
13,7 |
0,1 |
0,1 |
0,11 |
0,5 |
37,5 |
14,7 |
0,5 |
Следы |
0,4 |
0,3 |
75,0 |
Из таблицы видно, что основную часть примесей в растворах МЭА составляют, как правило, три продукта побочных реакций МЭА с С 02, доля которых иногда снижается до 35%. Однако при очистке топочных газов, содержащих 4—5% кислорода, большую часть примесей составляют продукты окисления МЭА [136].
Исследование взаимодействия МЭА с С 02 при температурах до 200 °С [135] показало, что в первый момент в растворе появляется оксазолидон-2 (рис. IV-47), концентрация которого затем несколько снижается и остается в дальней
|
шем невысокой и постоянной (не |
||||||
|
более 0,04 |
моль/л). Это указывает |
|||||
|
на то, что |
оксазолидон-2 является |
|||||
|
промежуточным |
продуктом, |
кото |
||||
|
рый быстро превращается в другие |
||||||
|
вещества. |
|
Концентрация |
имид- |
|||
|
азолидона непрерывно возрастает |
||||||
|
во |
времени |
(если |
он не выводится |
|||
|
из системы). Концентрация ОЭЭДА |
||||||
|
в |
растворе |
выше |
концентрации |
|||
|
оксазолидона-2 , но в отличие от |
||||||
|
имидазолидона |
проходит |
через |
||||
|
максимум. |
|
Это |
указывает |
либо |
||
|
на |
возможность |
|
обратной |
реак |
||
|
ции ОЭЭДА до имидазолидона-2 |
||||||
Рис. IV-47. Зависимость концентра |
(уравнение IV,84), либо на даль |
||||||
ций МЭА и продуктов реакции в |
нейшее превращение ОЭЭДА в не |
||||||
водном растворе от времени реак |
расшифрованные |
соединения. |
|||||
ции при 200 °С (концентрация |
|
Так как ОЭЭДА является ще |
|||||
С02 — 0,5 моль/л [135]): |
|
||||||
I — МЭА; 2 — имидазолидон; з — окси- |
лочным соединением, то и оно, и |
||||||
этилэтилендиамин; 4 — оксазолидон. |
продукты |
его дальнейшего взаимо |
|||||
|
действия |
с |
СО2 |
титруются |
при |
анализе, что приводит к завышению результатов анализа МЭА. Было показано [135], что при реакции МЭА с оксазолидоном-2
может образоваться ]Ч,№-диэтилолмочевина (ДЭМ)
Н2С -С Н 2 |
ИОСН2СИ2—NI-I |
|
с/" ^NH-fHOCI-I4CII2NIIa — ► |
^ С = 0 |
(IV.85) |
|
ИОСН2СИ2—NH |
|
О
соединение обычно неустойчивое, переходящее при высокой темпера туре в водной среде в имидазолидон-2
H O C I-I2C H 2N II |
и 2с—с и 2 |
|
\ ]= 0 — ► I |
I |
(IV.8G) |
II0CH2CII2NII |
V c i I 2CH2OII |
|
|
О |
|
Было |
показано |
[135], что оксазолидон-2 |
относительно" легко |
|||||
гидролизуется в водном растворе, |
особенно в присутствии]^ аОН, |
|||||||
т. е. реакция |
(IV,82) протекает |
в |
обратную |
|
|
|
||
сторону. |
|
|
|
|
|
|
|
|
В работе |
[135] |
подробно изучен |
механизм |
|
|
|
||
и кинетика отдельных стадий процесса превра |
|
|
|
|||||
щения МЭА, |
в том числе реакции МЭА с окса- |
|
|
|
||||
золидопом-2 в водной и неводной средах, а |
\ |
\ |
o V |
|||||
также выведено кинетическое уравнение про |
Со |
|
||||||
цесса превращения МЭА. Было изучено влия |
<1 |
|
|
|||||
ние температуры, |
концентрации С 0 2 и МЭА и |
- |
|
|
||||
времени |
на |
скорость побочных реакций. МЭА |
|
|
|
с СО2, |
что позволило более |
точно сформули |
|
|
_______ |
|
3\ |
|
||||||||||
ровать рекомендации по технологическому ре |
|
|
|
|
|
|||||||||||||
жиму процесса МЭА-очистки. |
|
|
|
|
|
|
|
|
ih'-rfX |
|
||||||||
|
Ранее |
[136] были приведены разнообраз |
|
Рис. IV-48. Зависи |
||||||||||||||
ные рекомендации по условиям стабильной |
|
|||||||||||||||||
работы |
установок МЭА-очистки. |
К ним отно |
|
мость |
убывания |
кон |
||||||||||||
сятся, |
в частности, снижение температуры теп |
|
центрации |
МЭА от |
||||||||||||||
|
температуры |
|
|
(про |
||||||||||||||
лоносителя, |
подаваемого |
в |
кипятильник, |
до |
|
должительность |
пре |
|||||||||||
140—150 °С, |
уменьшение |
концентрации |
МЭА |
|
бывания — 8 |
ч): |
||||||||||||
до |
15% |
и степени карбонизации насыщенного |
|
1 — начальная |
концен |
|||||||||||||
раствора |
до |
а = 0,35—0,45 |
моль |
С 02 |
на |
|
трация С02а 0«= 0,5 моль |
|||||||||||
|
СО*/мольМЭА; 2 —а 0 = |
|||||||||||||||||
1 моль МЭА. Эти меры приводят, однако, к уве |
|
= |
0,3; 3 — а 0 «= 0,18. |
|||||||||||||||
личению циркуляции раствора и, следователь |
|
|
|
|
|
|
|
|||||||||||
но, расхода тепла. Ограничение |
температуры теплоносителя услож |
|||||||||||||||||
няет и удорожает процесс (например, |
приводит к невозможности |
|||||||||||||||||
использовать |
конвертированный |
газ с t |
= |
180—190 °С в качестве |
||||||||||||||
|
|
|
|
|
|
теплоносителя). |
|
|
|
|
|
|
|
|||||
|
|
|
|
|
|
|
В то же время опыт показал, что |
|||||||||||
|
|
|
|
|
|
соблюдение |
только |
этих мер |
не га |
|||||||||
|
|
|
|
|
|
рантирует |
|
надежной |
эксплуатации |
|||||||||
|
|
|
|
|
|
промышленных |
установок. Это |
объ |
||||||||||
|
|
|
|
|
|
ясняется |
тем, что |
побочные реакции |
||||||||||
|
|
|
|
|
|
и |
при |
низких |
значениях а, Смэл и |
|||||||||
|
|
|
|
|
|
*мэл протекают с конечной скоростью |
||||||||||||
|
|
|
|
|
|
[135], т. е. в замкнутой системе, при |
||||||||||||
|
|
|
|
|
|
малых |
потерях |
растворителя и в от |
||||||||||
|
|
|
|
|
|
сутствие разгонки]и' фильтрации рас |
||||||||||||
|
|
|
|
|
|
твора |
продукты |
побочных |
реакции |
|||||||||
|
|
|
|
|
|
накапливаются |
в |
цикле. |
|
|
|
|||||||
Рис. IY-49. Зависимость степени |
|
На |
рис. |
IV-48 |
показана |
зависи |
||||||||||||
мость убывания МЭА,, в растворе от |
||||||||||||||||||
превращения МЭА при побочных |
||||||||||||||||||
реакциях |
МЭА с С 02 от степени |
температуры. Как |
следует |
из |
ри |
|||||||||||||
карбопизации |
раствора (началь |
сунка, |
скорость |
превращения |
МЭА |
|||||||||||||
ная концентрация МЭА 3,1 моль/л; |
увеличивается |
примерно в |
1 ,6 —1 ,8 |
|||||||||||||||
|
время |
нагревания 8 ч); |
|
раза при повышении температуры на |
||||||||||||||
J |
t — 200 вС; |
2 — t — 180 °Cl |
3 •— |
|||||||||||||||
каждые 10 °С. |
|
|
|
|
|
|
|
|||||||||||
|
|
|
— 165° G. |
|
|
|
|
|
|
|
|
В промышленных условиях средняя температура раствора зави сит от времени пребывания его в «горячих» точках системы, которое наиболее велико в теплообменниках. В результате при tx = 120 °С средняя температура равна примерно 90 °С, но может быть и выше (до 110 °С) в зависимости от времени пребывания раствора в реге
нераторе. |
|
Степень превращения МЭА в начальный период (время т |
0) |
возрастает почти пропорционально начальной степени карбониза
ции раствора (рис. IV-49), |
т. е. |
реакция имеет первый |
порядок по |
С 02. Аналогичные данные |
[135] |
показывают, что при |
одинаковой |
начальной степени карбонизации (в моль С 02 /моль МЭА) реакция превращения МЭА в начальный период протекает по второму по
рядку по МЭА (при равной |
концентрации С 02 в моль/л |
реакция |
идет по первому порядку): |
|
|
УМЭА = |
^МЭА^МЭА^СО* |
(IV,87) |
где С° — концентрация в начальный момент.
Это уравнение соответствует реакции (IV,81). Было показано [135]f что константа скорости кх превращения МЭА по реакции (IV,81) значительно ниже константы к2 реакции (IV,83), т. е. процесс лими тируется медленной первой реакцией, но может ускоряться после дующими реакциями. Следовательно, накопление примесей в рас творе способствует быстрой деградации раствора. На это ускорение указывает также то, что константа скорости связывания С 02 меньше аналогичной константы для МЭА в 2,2—2,7 раза (табл. IV-22).
Таблица IV-22. Константы скорости побочных реакций МЭА и С02 при т-*0
[в л/(моль«с)]
Температура, °С |
■Ь’МЭА |
Ксо, |
200 |
1,4 • 1 0 “ 5 |
0,5 -ЧО-з |
180 |
3,8-10-6 |
1.5-Ю 'б |
165 |
1,4 -1 0 -6 |
0,5-10-6 |
Энергия активации Е в уравнении К = Ае~Е,пт для превра щения МЭА составляет 105,2 кДж/моль (25,6 ккал/моль), для С 02 — 118,3 кДж/моль (28,8 ккал/моль). Предэкспоненциальные множители А равны соответственно 1,5 -10~14 и 2,1 -10"13 см%.
Скорость взаимодействия МЭА с оксазолидоиом-2 значительно выше скорости реакции (IV,81) и весьма велика даже при низких температурах. Константа скорости этой реакции /с2, мэл при 70 °С
равна 9 ,9 -10'5, при 90 °С — 3 ,2 -10~6 |
и при |
110 °С — 1,2 X |
|
X 10' 4 л/(моль*с). Следовательпо, при наличии в растворе |
оксазо- |
||
лидона-2 , который появляется в первую |
очередь |
в зонах |
высоких |
температур, деградация раствора может протекать и при темпера туре абсорбции.
Данные по гидролизу оксазолидона-2 показали, что скорость гидролиза и равновесие этой реакции сильно зависят от наличия NaOH в растворе. Поэтому NaOH целесообразно добавлять при разгонке (см. ниже), а также в рабочий раствор [137].
Кинетическое уравнение процесса превращения МЭА по реак циям (IV?81)—(IV,83) может быть записано в следующем виде [135];
|
|
___________ С&эа (2«°-1)_________ |
|
|
|
|
СМЭА - |
2ао (ехр [*1С°,ЭА (2а°—1) т]) - 1 |
(IV,88) |
При а 0 |
0,5 |
уравнение упрощается |
|
|
|
|
|
^М ЭА - 1+АчСмэдТ |
(IV>89) |
где С'мЭА» а СО* |
начальные концентрации МЭА и С 02; т — время; |
СМЭА— |
||
текущая |
концентрация |
МЭА. |
|
Для производственных условий, когда концентрации МЭА и С0 2 поддерживаются постоянными, можно использовать более простое уравнение:
^^МЭА
|
|
|
' = |
2А:1с м э а с С0* |
|
|
(IV,90) |
|
Значения |
кх в уравнениях |
(IV,88)—(IV,90) |
равны |
при 200 °С |
||||
1,0• 10^5, при |
180 °С — 1,7* 10"6 и при 165 °С — 0,7 • 10"6 л/(моль-с). |
|||||||
Расчет по уравнению (IV,90) показал, что в рабочих условиях |
||||||||
(Смэа = |
1,7—3,3 |
моль/л, Ссо, |
= 0,5—1,7 |
моль/л, |
£ср = 90— |
|||
110 °С) |
скорость |
накопления |
примесей в |
растворе |
составит от |
|||
2,7• 10~6 |
до |
1,4-Ю "4 моль/(л*ч). |
Анализ |
работы промышленных |
установок, а также опытно-промышленные исследования показали,
что скорость |
накопления примесей" («смол») в растворе колеблется |
|
в пределах |
0,1—0,15 г/(л-сут) |
[6 ,8 • 10“6 — 1,0-10~4 моль/(л-ч)], |
т. е. находится в соответствии с |
расчетной величиной. |
Способы борьбы с последствиями побочных реакций МЭА с С02 вытекают из приведенных выше данных. Указанные выше способы снижения скорости побочных реакций (уменьшение температур и концентраций, введение ингибиторов типа NaOH, КОН, Na2C03) позволяют частично облегчить эту задачу. Так, после введения NaOH в раствор МЭА химические потери на одной из установок снизи лись в 1,6 раза [137]. Расход щелочи составил 0,13 кг/кг сэконо мленного МЭА. Однако необходимым условием является вывод из цикла продуктов побочных реакций путем разгонки или фильтра ции раствора либо сочетанием обоих методов. Показано [135], что абсолютная величина химических потерь при реакциях МЭА с С 02
невелика и составляет около 0,1 |
кг/т NH 3, или 0,03 кг на 1000 м3 |
|
очищаемого |
газа. |
|
I х» Заказ |
14G0 |
209 |
Диэтаноламин вступает в побочные реакции с С 02 значительно энергичнее.
Окисление моноэтаноламина. Окисление моноэтаноламипа воз можно при его плохом хранении (наличие контакта с воздухом), при подсосе воздуха в систему очистки и в основном при очистке газов, содержащих кислород (топочные газы и др.). Показано [136], что в этом случае окисление играет основную роль при деградации моноэтаноламина.
Исследованию механизма окисления МЭА посвящен ряд работ. Детальное исследование рабочих растворов МЭА с установки выделе ния СО2 из топочных газов [136] показало, что в этих растворах содержатся щавелевая и муравьиная кислоты, а также небольшое количество уксусной кислоты. Все они находятся в виде сильно диссоциированных солей с МЭА (так называемые «свободные» кис лоты). Кроме того, в растворе обнаружены «связанные» органиче ские кислоты (видимо, оксикислоты), а также аминокислоты. Кор розионная активность «связанных» кислот и аминокислот высока, выше, чем активность муравьиной кислоты. Это объясняется, воз можно, их способностью к образованию комплексов с железом. В целом продукты окисления МЭА являются значительно более коррозионно-активными, чем продукты побочных реакций МЭА
сС 02.
Вработе [138] приведен следующий механизм окисления МЭА;
NH2CIT2CHsOH 1 н °Д - H2N—СН2—С—И ,/а° 2^ HaN—сн2—с—он -
|
* |
II • |
д |
-и ,о, —к, |
НОСИ,—С—ОН |
Н С - С —он |
нос—с—он |
|
А |
о о |
о о |
Таким образом, первоначальным продуктом окисления является а-аминоальдегид, затем глицин, гликолевая кислота и щавелевая кислота..В работе [136] показано, что щавелевая кислота переходит в муравьиную кислоту
(СООН)2 ► Ы С00И + С 0 2 |
(IV,91) |
Эти кислоты могут приводить к коррозии аппаратуры с образо ванием нерастворимых солей железа. Кроме того, они взаимодейст вуют с МЭА с образованием амидов, что приводит к дополнительным потерям МЭА. Следовательно, в данном случае при накоплении побочных продуктов в растворе возможно ускорение процесса дегра дации МЭА. Последнее подтверждается анализом результатов про мышленной эксплуатации установок выделения двуокиси углерода из топочных газов, содержащих 4—5% кислорода [139]. Показано, что
|
|
С = |
с 0екх |
где С — текущая |
концептрация |
смол; |
т — время; Со — концентрация смол |
в момент начала |
отсчета (т = |
0). |
|
Таким образом, концентрация продуктов окисления возрастает экспоненциально и зависит не столько от начальных условий (каче ство МЭА, состав газа и т. д.), сколько в первую очередь от количе ства примесей в растворе, ускоряющих его деградацию.
При наличии в газе сернистых соединений кислород может ре агировать с МЭА и другим путем (см. далее).
Способы борьбы с окислением МЭА могут быть разнообразными, наиболее простым из них является предохранение раствора от кон такта с воздухом и в первую очередь разгонка и фильтрация. Однако при очистке газов, содержащих кислород, должны быть использо ваны другие методы; например, введение в раствор ингибиторов окис ления. Этот метод до настоящего времени еще не используется в про
мышленности. |
|
|
|
|
|
|
|
|
|
|
||
В ГИАП |
разработан |
простой метод |
|
|
|
|
|
|||||
резкого снижения, окисления МЭА, при |
|
Д ЗД ~ 35% (‘т с ) |
||||||||||
менение которого |
позволяет использо |
|
|
|
|
|
||||||
вать МЭА при очистке воздуха и даже |
|
|
|
|
|
|||||||
чистого кислорода от двуокиси угле |
f |
|
|
|
|
|||||||
рода. Окисление МЭА происходит при |
|
|
|
|
||||||||
взаимодействии, |
растворенного |
в |
про |
1 |
|
ъ |
|
|
||||
цессе |
абсорбции |
кислорода с моноэта- |
f ? |
|
г» |
|
|
|||||
■-< |
к |
|
|
|||||||||
ноламином. |
Скорость |
окисления |
при |
|
|
|||||||
температурах абсорбции невелика, но |
t т |
|
\ ° |
|
|
|||||||
|
|
|
|
|||||||||
она резко возрастает при нагревании |
/ |
|
\ |
iъ |
|
|||||||
раствора. Поэтому при промежуточной |
|
|
|
|
|
|||||||
отдувке кислорода по схеме, приведен |
|
|
|
|
|
|||||||
ной на рис. IV-32, |
скорость окисления |
|
|
|
|
|
||||||
резко |
уменьшается (не менее чем в 5— |
0 |
2 |
* |
6 |
8 10 |
||||||
6 раз). |
|
|
|
|
|
|
|
|
Время, |
я |
|
|
Побочные реакции МЭА и ДЭА с |
Рис. IV-50. Зависимость кон |
|||||||||||
сернистыми |
соединениями. Наличие в |
центрации МЭА и ДЭА в цикле |
||||||||||
газе |
органических |
сернистых |
соедине |
от продолжительности контак |
||||||||
ний приводит к большим потерям МЭА. |
т а ^ |
COS |
(скорость продувки |
|||||||||
COS 77 см3/мин; концентрация |
||||||||||||
Так, |
сероуглерод реагирует с |
МЭА с |
COS 98%; |
скорость |
циркуля |
|||||||
образованием N-этилолдитиокарбамино- |
ции МЭА — 44 см3/мин: ДЭА — |
|||||||||||
вой кислоты |
[140, |
141]; при ее нагре |
56 см3/мин; температура аб |
|||||||||
вании протекают реакции, приводящие |
сорбции |
40 °С; |
регенерации |
|||||||||
|
|
104 °С). |
|
|||||||||
к частичной |
регенерации МЭА (в пре |
|
|
|
||||||||
|
|
|
|
|
||||||||
делах 50%). |
Сероокись углерода реаги |
|
|
|
|
|
||||||
рует с МЭА |
с образованием N-оксиэтилтиокарбаминовой |
|
кислоты, |
|||||||||
которая при гидролизе |
образует |
МЭА, С 02 |
и H 2S и может перехо |
дить в оксазолидон-2. Следовательно, при наличии в газе сероокиси углерода в растворе может накапливаться оксазолидон-2 , который способен к быстрой реакции с МЭА.
Сероводород обратимо реагирует с МЭА. Однако в присутствии кислорода может образовываться тиосульфат (RNH2)2- S20 3, не регенерируемый в обычных условиях [142]. При очистке газов, содержащих сероорганические соединения, рекомендуют применять
ДЭА, не вступающий |
с ними в реакцию |
[143]. На рис. IV-50 при |
ведены данные [143] |
по скорости химического превращения МЭА |
|
и ДЭА, полученные |
н а’циркуляционной |
установке в присутствии |
|
COS. Из рисунка видно, что ДЭА практически не реагирует с COS, |
||||
|
в то время как концентрация МЭА быстро уменьшается. |
||||
|
Другие побочные реакции. В кубовом остатке [144] |
после раз |
|||
|
гонки рабочего раствора обнаружено большое количество N-ацетил- |
||||
|
этаноламина. Высказано предположение, что он является продуктом |
||||
|
реакции МЭА с кетоном или уксусной кислотой, попадающими в очи |
||||
|
щаемый газ. Раствор использовался для очистки газа, который мог |
||||
|
содержать примесь ацетилена; N-ацетилэтаноламин не корродирует |
||||
|
углеродистую сталь. |
|
|
|
|
|
|
ВСПЕНИВАНИЕ РАСТВОРА II МЕРЫ БОРЬБЫ С НИМ |
|||
) |
Вспенивание раствора приводит к потерям МЭАи к другим послед |
||||
|
ствиям.,! Оно возникает, как правило, в абсорбере. Вспенивание |
||||
|
может быть вызвано разнообразными причинами, в |
частности |
|||
|
наличием примесей, заносимых в систему с очищаемым газом (пыль |
||||
|
катализаторов и др.). Доказано, что сульфид железа является интен |
||||
|
сивным |
пенообразователем |
[145]. |
Пенообразователями |
являются |
|
также тяжелые углеводороды, смазочные масла, а также органиче |
||||
|
ские кислоты, тиосульфаты и другие продукты деградации МЭА. |
||||
|
Кроме того, к вспениванию могут приводить некоторые ингибиторы |
||||
|
коррозии, а также соли, растворенные в воде, используемой для |
||||
|
приготовления раствора МЭА (что обусловливает необходимость |
||||
|
применения только парового конденсата). |
|
|||
|
Показано [145], что вспенивание чаще возникает в |
аппаратах |
|||
|
с высокими нагрузками по газу и жидкости. Признаком вспенивания |
||||
|
является резкое увеличение перепада давления в. аппарате, поэтому |
||||
|
для своевременного предупреждения вспенивания необходим кон |
||||
|
троль за |
этим показателем. |
|
|
|
|
Наилучшими способами борьбы со вспениванием также является |
||||
|
вывод примесей из системы, т. е. разгонка и фильтрация раствора. |
||||
|
Эти методы более надежны, чем применение антивспенивателей, |
||||
|
действие которых кратковременно. Некоторые антивспениватели |
||||
|
хорошо гасят пену в момент ее образования, но при добавлении их |
||||
|
в раствор до образования пены могут приводить к ее стабилизации. |
||||
|
Иногда чрезмерное количество антивспенивателя также может при |
||||
|
вести ко вспениванию. Однако в некоторых случаях использование |
||||
|
антивспенивателей неизбежно |
[96]. |
Показано, что добавки анти- |
всцеиивателей позволяют резко (более чем в 5 раз) снизить унос моноэтаноламина с очищенным газом.
Известны разнообразные антивспениватели, к ним в основном относятся силиконовые масла и высококипящие спирты, хороший эффект [95] дает эмульсия 21-2А (или КЭ10-12). Последняя предста вляет собой композицию на основе полиметилсилоксановой и полиэтилсилоксановой жидкостей. Добавление ее в количестве 0,0005—
0,005% (масс.) в расчете на активное вещество IIMC-200A позволяет существенно увеличить предельную нагрузку по газу в абсорбере (см. выше стр. 151), а также уменьшить брызгоупос. Перед приме нением антивспенивателей рекомендуется испытать их на образцах раствора. Для системы емкостью 500 м3 в первоначальный момент необходимо добавлять 50 кг эмульсии, общий расход — 5—7 т/год. Эмульсию разбавляют в 20—30 раз и после перемешивания непре рывно вводят в систему.
[ КОРРОЗИЯ АППАРАТУРЫ И МЕРЫ БОРЬБЫ С НЕЙ
Коррозия аппаратуры возникает при неправильной эксплуа тации системы очистки или вследствие недостатков при изготовлении и монтаже аппаратов. Ранее указывалось, что основной причиной коррозии является взаимодействие продуктов побочных реакций
сметаллом [6].
Вопределенных условиях, особенно при повышенной темпера туре, возможно образование комплексов железа с моноэтаполамином хелатного типа
Такие же соединения могут образовать ОЭЭДА и другие поли амины [146]. При охлаждении раствора и взаимодействии этих соединений с сероводородом выпадает в осадок сернистое железо, а исходный компонент, участвующий в образовании хелата, регене рируется и вновь реагирует с железом в тех частях установки, где поддерживается высокая температура. Таким образом, продукты коррозии не расходуются в процессе коррозии, а накапливаются в растворе.
При высоких температурах может протекать реакция между металлическим железом и угольной кислотой с образованием рас творимого бикарбоната железа. При десорбции С 02 в регенераторе бикарбонат железа превращается в нерастворимый карбонат железа, который осаждается на стенках аппаратов и трубопроводов.
Скорость коррозии возрастает при увеличении температуры, концентраций МЭА и С 02 в растворе, что связано в первую очередь с увеличением скорости побочных реакций. Следовательно, в этих условиях скорость коррозии может быть снижена при соответству ющем увеличении производительности разгонки и фильтрации.
Скорость коррозйи стали различных марок в водном растворе МЭА, содержащем С 02, изучена в ряде работ [147—149]. Устано влено, что скорость коррозии стали Ст.З в 10—100 раз выше скорости коррозии нержавеющей стали марки 1Х18Н10Т [147, 148]. Кроме того, коррозия углеродистой стали резко возрастает в местах ее контакта с легированными 'сталями L146]. Наблюдались случаи
коррозии нержавеющих сталей [150]. Наибольшей стойкостью к кор розионному растрескиванию и межкристаллитной коррозии обла дает сталь марки 0Х21Н6М21 [151].
При неблагоприятных условиях эксплуатации и отсутствии
специальных мер коррозия может принять катастрофический харак |
|||||||||||||
|
OJ* |
|
|
|
|
|
тер и за 5—6 мес вывести из |
||||||
SCNJ |
4» |
|
|
|
|
строя |
почти |
все |
оборудова |
||||
|
|
■— |
Г— * |
||||||||||
I * W |
л----- |
ние, |
работающее |
при темпе |
|||||||||
|
|
|
|
|
ратуре выше 100 °С (включая |
||||||||
Ci ^ |
И< |
1 |
|
|
|
|
|
|
|
|
|
||
o 3 |
|
|
|
насосы) |
[139]. |
Эрозионно |
|||||||
CXro |
|
|
|
||||||||||
|
<+5 |
60 |
70 |
90 |
ЮЗ |
/20 t35 |
коррозионному разрушению |
||||||
|
|
концент рация С O 9 ? 2/л |
|
подвергается |
даже |
оборудо |
|||||||
|
|
|
вание, находящееся в контак |
||||||||||
|
|
|
|
|
|
|
|||||||
Рис. IV-51. Зависимость |
скорости корро |
те с жидкостью при темпера |
|||||||||||
зии углеродистой стали от концентрации |
туре |
окружающей |
среды. |
||||||||||
СОо в 2 0 %-ном растворе |
МЭА и темпера- |
Наиболее |
сильной |
коррозии |
|||||||||
|
|
|
туры |
[147]: |
|
обычно подвержены |
теплооб |
||||||
1 — при 40 °С; 2 — при 60 °С; 3 — при 100 °С; |
|||||||||||||
менники, |
кипятильники, а |
||||||||||||
|
|
4 — при 130 °С. |
|
||||||||||
|
|
|
|
|
|
|
также конденсаторы флегмы, |
||||||
регенераторы |
и дроссельные |
вентили на линии насыщенного рас |
|||||||||||
твора. |
|
|
|
|
|
|
|
|
|
|
|
Исследование влияния степени карбонизации раствора на ско рость коррозии [147] показало, что скорость коррозии возрастает примерно пропорционально концентрации двуокиси углерода в рас
творе |
(при |
малых |
а), |
достигая макси |
|
|
|
|
|
||||||
мума [0,3—0,4г/(м2• ч),или0,3—0,4мм/год ] |
|
|
|
|
|
||||||||||
при |
некотором |
значении |
а |
(в |
моль |
|
|
|
|
|
|||||
С 02/моль МЭА), |
выше которого |
скорость |
|
|
|
|
|
||||||||
коррозии уже не зависит от а . Чем ниже |
|
|
|
|
|
||||||||||
температура, |
тем |
сильнее |
сказывается |
|
|
20 |
30 |
||||||||
влияние степени |
карбонизации раствора |
|
|
||||||||||||
(рис. IV-51). Так, |
при 130 °С |
скорость |
|
Концентрация МЭЙ, % |
|||||||||||
коррозии максимальна уже при а = 0,45, |
Рис. IV-52. Зависимость ско |
||||||||||||||
при 100 °С — при а |
= |
0,57, |
при 60 °С — |
рости |
коррозии |
углероди |
|||||||||
стой |
стали |
(Ст. |
3) |
от кон |
|||||||||||
при а = 0,7 и |
при |
40 °С — при |
а = |
||||||||||||
центрации |
МЭА |
в растворе |
|||||||||||||
=0,9. Эти данные, в отличие от ранее опу |
|
|
[147]: |
|
|
||||||||||
бликованных |
[36], |
позволяют |
сделать |
J —при 100°; 2 — при |
130 °С, |
||||||||||
вывод, что |
при |
соответствующих |
усло |
|
|
|
|
|
виях можно поддерживать высокие степени карбонизации. Приведенные данные получены в статических условиях, при которых в растворе накапливалось большое количество продуктов деградации МЭА, т. е. без их вывода из системы. Это могло привести к завышенной скорости коррозии. Однако эти данные не могут харак теризовать скорость коррозии в момент десорбции С 02 из высококарбонизованных растворов. Опытно-промышленные испытания [147] показали, что при 115 °С и а = 0,65 моль С0 2/моль МЭА скорость коррозии углеродистой стали может достигать 0,34 г/(м2• ч). Увеличение концентрации МЭА приводит к возрастанию скорости
коррозии (рис. IV-52), а также к увеличению опасности (для 30 %- ыого раствора МЭА) коррозионного растрескивания аппаратуры.
Повышение температуры |
греющего пара от |
1,5 |
|
|
|
|||||
150 |
до |
180—190 °С |
|
способствует |
резкому |
|
? |
|
||
|
|
|
|
|||||||
увеличению коррозии |
углеродистой стали |
|
|
! |
|
|||||
(от 0,2 до 1,8 мм/год), |
рис. IV-53. |
Следова |
1 V |
|
/ |
|
||||
тельно, кипятильники, работающие в подоб |
|
/ |
\ |
|||||||
ных условиях, должны быть изготовлены из |
|
|
1 |
|
||||||
нержавеющей стали. Это же условие должно |
с* |
|
1 |
|
||||||
быть соблюдено при |
использовании ij каче |
г |
|
У |
|
|||||
стве |
теплоносителя |
конвертированного газа |
|
г |
|
|||||
[152]. Нержавеющая |
сталь Х18Н10Т прак |
0,5 |
|
|
|
|||||
► |
|
J |
|
|||||||
тически не разрушается в обычных условиях |
1 |
/ |
2 |
|
||||||
регенерации раствора. |
|
|
|
|
|
|
||||
Было |
показано, |
что |
ОЭЭДА, |
а также |
<5 4't i l |
№ |
ISO |
|||
другие продукты деградации МЭА, выводи |
ЛЮ |
|
||||||||
|
Температура^С |
|||||||||
мые с кубовым остатком, |
являются корро |
|
||||||||
|
|
|
|
|||||||
зионно-активными [147]. |
Коррозионно-эро |
Рис. IV-53. Зависимость |
||||||||
зионное разрушение аппаратуры вызывается |
скорости коррозии стали |
|||||||||
также наличием абразивных частиц, попада |
в 20% -ном растворе МЭА |
|||||||||
от температуры (концен |
||||||||||
ющих в раствор в результате механического |
трация |
С02 — 60 |
г/л): |
|||||||
разрушения керамической насадки либо тор |
Т — Ст. 3; 2 — Ст. Х18Н10Т. |
|||||||||
крет-бетона, которым |
покрывают регенера |
|
|
|
|
торы. Ранее указывалось, что весьма высокой коррозионной актив ностью обладают продукты окисления МЭА.
В работах |
И. К. Бурцевой |
|
и И. А. Левина (ГИАП) |
показано, |
||||||||||
0.20 |
|
|
|
что при коррозии углеродистой стали в рас |
||||||||||
|
|
|
творах МЭА образуется атомарный водород. |
|||||||||||
|
|
|
|
|||||||||||
|
|
|
|
Он может диффундировать |
в сталь, что при |
|||||||||
> 0,15 |
|
|
|
водит в дальнейшем к растрескиванию кор |
||||||||||
<м |
|
|
|
|||||||||||
£ |
|
|
|
пусов регенераторов и других аппаратов. |
||||||||||
Ч 0J2 |
|
|
|
Одним |
из |
средств |
борьбы с растрескива |
|||||||
I |
|
|
|
нием является отжиг сварных швов. |
|
|||||||||
|
|
|
За |
годы |
эксплуатации |
установок |
моно- |
|||||||
!от |
|
|
|
этаноламиновой очистки накоплен большой |
||||||||||
| ' |
|
|
|
опыт |
борьбы с |
коррозией |
и с химической |
|||||||
I № |
|
|
|
деградацией |
моноэтаноламина. |
|
|
|||||||
|
|
|
|
Ниже |
приведены |
некоторые |
рекоменда |
|||||||
100 |
200 |
500 |
ции |
[36, |
145], которые следует |
учитывать |
||||||||
при проектировании |
и эксплуатации основ |
|||||||||||||
|
Время, ч |
|
||||||||||||
|
|
ных аппаратов моноэтаноламиновой очистки. |
||||||||||||
Рис. IV-54. Зависимость |
||||||||||||||
Регенератор. |
Для |
снижения коррозион |
||||||||||||
скорости |
коррозии Ст. 3 |
ного |
разрушения |
верхней |
части регенера |
|||||||||
от времени |
в карбонизо- |
|||||||||||||
ванном |
2 0 % -ном рас |
тора и конденсатора флегма должна содер |
||||||||||||
творе МЭА |
(кривая 1) и |
жать |
около 0,5% |
моноэтаноламина. Регене |
||||||||||
в том же |
растворе, со |
рацию |
раствора |
целесообразно |
вести |
при |
||||||||
держащем |
|
0,05% |
мета- |
минимальной температуре (не выше 127 °С) |
||||||||||
ванадата |
натрия |
(крит |
||||||||||||
вая 2). |
|
и, следовательно, при минимальном давлении, |
определяемом сопротивлением коммуникаций па линии |
жид |
кости и газа (хотя расход пара при более высоком давлении |
сни |
жается, см. выше). |
|
Кипятильник. В кипятильнике практически не должна проис ходить десорбция .двуокиси углерода (т. е. она должна заканчи ваться в регенераторе), иначе возможна эрозия трубок кипятиль ника. В качестве теплоносителя рекомендуется применять пар низ кого давления (0,3—0,4 МПа, 3—4 кгс/см2) при 131—140 °С, но не выше 150 °С, так как иначе значительно возрастает температура стенок труб. Для снижения температуры пара рекомендуется перед входом в кипятильник впрыскивать в него конденсат. Необходимо также, чтобы коэффициенты теплопередачи не были слишком высо кими, так как интенсивное кипение приводит к усилению коррозии. Если в качестве теплоносителя применяют пар или конвертирован ный газ при более высокой температуре, скорость химической дегра дации раствора возрастает и, следовательно, увеличивается скорость коррозии. Поэтому необходимо повышать интенсивность разгонки раствора, определяемую скоростью его деградации.
Для предотвращения местных перегревов верхняя трубная решетка должна,быть покрыта слоем раствора высотой 15—20 см. Нижнюю решетку следует устанавливать не менее чем на 15 см выше дна кипятильника для уменьшения отложения примесей и улучше ния циркуляции.
Чтобы предотвратить образование застоев С 02 в кипятильнике, раствор целесообразно вводить в разные части аппарата.
Трубки кипятильника необходимо располагать по квадрату для облегчения их чистки. Расстояние между трубками не должно быть малым, чтобы предотвратить увеличение скорости потоков и эрозию предохранительной пленки. В некоторых случаях для облегчения выхода паров рекомендуется вынимать часть трубок с образованием проходов в форме букв V или X.
Теплообменники. Скорость потока в теплообменниках не должна превышать 1 м/с во избежание эрозии аппаратуры. Коррозии под вергаются секции теплообменников, в которых раствор перегре вается выше температуры кипения и происходит десорбция С 02. Поэтому раствор не следует перегревать выше температуры кипения (или верхние секции теплообменников следует изготовлять из нержа веющей стали). При абсорбции под давлением целесообразна про межуточная отдувка менее растворимых газов. Горячий раствор должен идти сверху вниз, холодный — снизу вверх.
Одним из эффективных методов борьбы с коррозией в период пуска является создание на поверхности аппаратуры коррозионностойкой пленки. Для этого систему в течение длительного времени промывают при интенсивной циркуляции сначала конденсатом и в течение 8—12 ч 4—8 %-ным раствором щелочи и вновь водой, а за тем 0,5%-ным подогретым водным раствором моноэтаноламииа [153].
Кроме того, для снижения коррозии могут быть использованы ингибиторы коррозии, в частности хромат калия [154—156], сода
[148, 157, 158], сульфит натрия, ]М,]Ч-диэтанолглицип, натриевая соль этилендиаминтетраацетата. Одним из наиболее распространен ных ингибиторов является метаванадат натрия [148, 160, 161], количество которого в растворе должно составлять около 0,05%. При этом скорость коррозии стали в 15%- и 20%-ных растворах МЭА снижается в 10—20 раз. На рис. IV-54 показано влияние инги битора на скорость коррозии [160].
Все ингибиторы можно разделить на 3 группы: окисляющего типа, осаждающего и адсорбирующего типа. Разработан комбини рованный ингибитор «Амип Гард» [152], который является весьма эффективным средством, так как сочетает свойства трех типов инги биторов. Авторы утверждают, что применение такого ипгибитора позволяет работать без разгонки МЭА, снизить потери МЭА на 40— 60%, а также уменьшить расход тепла за счет увеличения концен трации МЭА и СО2 в растворе. При применении ингибиторов кон центрация МЭА может быть увеличена до 30%.
Опыт эксплуатации современных промышленных агрегатов пока зал, что главным условием стабильной работы агрегатов МЭАочистки (т. е. отсутствие коррозии, вспенивания и забивки аппара туры) является хорошее качество рабочего раствора МЭА (снижение содержания в растворе продуктов побочных реакций — не более 0,2%, солей жесткости и механических примесей). Соблюдение всех упомянутых условий облегчает работу установок (позволит сни зить скорость накопления примесей), но не гарантирует ее стабиль ности. Главным условием стабильности является непрерывный вы вод примесей из раствора с помощью разгонки и фильтрации.
Если агрегат работает в более жестких условиях (высокая кон центрация кислорода и органических сернистых соединений в ис ходном газе, высокие температуры и т. п.), это должно компенсиро ваться соответствующим повышением производительности разгонки и фильтрации.
РАЗГОНКА РАСТВОРА МЭА
Перечисленные выше меры, принимаемые для снижения ско рости побочных реакций и коррозии аппаратуры, не позволяют полностью ликвидировать эти явления. Кроме того, стремление улучшить технико-экономические показатели моноэтаноламиновой очистки обусловливает проектирование установок с повышенными концентрациями МЭА и двуокиси углерода в растворе, использование высокотемпературных источников тепла и т. д. Поэтому все агрегаты моноэтаноламиновой очистки независимо от условий работы и со става газа должны быть оборудованы установками для разгонки моноэтанол^мина в присутствии щелочи.
Разгонке моноэтаноламина является главным средством сниже ния химических потерь амина и коррозии, она особепно необходима при очистке моыоэтаноламином коксового газа [162], содержащего большое количество сернистых и цианистых соединений. Разгонку проводят в специальном аппарате — перегопном кубе (или смоло
выделителе), куда подается пар. На разгонку поступает небольшая часть раствора. При этом отводят чистый дистиллят, а в кубе нака пливаются продукты побочных реакций.
При взаимодействии со щелочью часть побочных продуктов разлагается с образованием свободного амина. Кроме того, при раз гонке раствора из системы непрерывно выводятся механические примеси (шлам, бой керамических колец), что снижает эрозию оборудования. В промышленной практике используются непрерыв ная и периодическая разгонка, разгонка в вакууме и при давлении регенерации. Раствор МЭА подается на разгонку либо с линии нагне тания насоса, либо непосредственно из куба регенератора.
Минимальная производительность разгонки может быть рассчи тана из условия постоянства концентраций продуктов побочных реак
ций, т. е. |
F„aK = Ушв (где FHaK и |
FPbIB — соответственно скорости |
|||
накопления примесей в растворе и вывода их на разгонку |
и фильтра |
||||
цию,* если она работает). Поскольку |
FHaK= Vno6V, a FBbIn = |
LCno6 |
|||
(здесь Fno6 — скорость |
побочных |
реакций, в г/(л-ч); |
F — объем |
||
раствора |
в системе, л; |
L — производительность разгонки, |
л/ч; |
||
Споб — допустимая норма концентрации примесей в растворе, |
г/л). |
Величина СПоб зависит либо от коррозионной активности примесей, либо от их влияния на вспенивапие, и т. д' Следовательно
|
|
LCno6 = Vno6V и L = -7 7 -°— - |
(IV,92) |
|
|
^поб |
|
В |
качестве |
нормы может быть принята С^об = 2 г/л |
или 0,2% |
[174]. |
Тогда |
для системы, в которой объем раствора |
составляет |
500 м3/ч, с учетом приведенных выше данных о скорости побочных реакций производительность разгонки будет равна 2 м3/ч при сред ней температуре системы 110 °С и 0,25 м3/ч при tcp = 90 °С и непре рывной работе. Практически она должна быть несколько выше, так как разгонку периодически необходимо останавливать. Кроме того, возможны случайные загрязнения системы (пыль катализато ров, осмоление вследствие перегревов при пуске и т. п.). Поэтому для быстрой очистки системы необходим запас производительности разгонки.
При периодической разгонке раствора производительность уста новки должна быть еще выше. Ранее показано, что после первона чального пуска и работы на чистом растворе МЭА примеси в количе стве 2 г/л могут накапливаться в полностью замкнутом цикле в тече ние 10 сут, а при наиболее благоприятных условиях — не более
чем за 100 сут. |
|
|
Схема вакуум-разгонной установки |
[163, 164] |
приведена па |
рис. IV-55. Она включает хранилище 8, |
где раствор |
МЭА смеши |
вается со щелочью с помощью циркуляционного насоса 7, напорный бак-мерник 5, перегонный куб 4, холодильник-конденсатор 2, брызгоотделитель 7, вакуум-насос 6 и сборник дистиллята 5. Перегонка осуществляется в две стадии. Первая стадия —• перегонка МЭА при подпитке раствором. По мере отгопки МЭА и воды в кубе нака
пливаются высококипящие примеси и температура повышается. По достижении определенного предела подпитку прекращают и начинают вторую стадию — выщелачивание амина при непрерывной подпитке конденсатом (отгонка с водяным паром). После того как содержание амина в дистилляте снизится до 0,5%, разгонку пре кращают и выгружают кубовый остаток.
Ркс. IV-55. Технологическая схема установки вакуумной разгонки раствора МЭА [163]:
1 — брызгоотделитель; 2 — холодильник-конденсатор; 3 — напорный бак-мерник; 4 — пере гонный куб; 5 — сборник дистиллята; 6 — вакуум-насос; 7 — насос; 8 — хранилище рас твора МЭА.
Первую стадию разгонки ведут обычно при разрежении 66,7—
73,3 кПа |
(500—550 |
мм |
рт. ст.) [остаточное давление |
(2,3—3,1) |
X |
X 104 Па |
(185—235 |
мм |
рт. ст.)], вторую — в менее |
глубоком |
ва- |
кумме 2,7 *104 Па (200 мм рт. ст.). Изменение остаточного давления в первой стадии от 236 до 533 мм рт. ст. [(13,1 -|_7,1)‘104 Па] при установившемся режиме существенно не влияет на процесс отгонки. Вначале отгоняется чистая вода, затем, по мере установления равно весия между составами поступающего раствора и дистиллята, темпе ратура увеличивается от 80 до 105—110 °С [при разрежении 66,6 — 70,6 кПа (500—530 мм рт. ст.)]. После прекращения подпитки перед подачей конденсата рекомендуется несколько упарить раствор, чтобы уменьшить продолжительность второй стадии и увеличить выход амина.
При остаточном давлении 235 мм рт. ст. (3,104 кПа) температура должна быть не выше 125 °С, при 535 мм рт. ст. (7,1 кПа) — не выше 135 °С; при превышении температуры начинается отгонка смол.
Вторую стадию отгонки МЭА более выгодно проводить при остаточпом давлении 535 мм рт. ст. (7,1 кПа). Чем менее глубокий вакуум поддерживается в аппарате, тем (по условиям равновесия) больше амина в отгоняемой смеси и, следовательно, тем меньше водяного пара требуется для отгонки амина.
Количество добавляемой к pacTBQpy щелочи составляет 1 моль на 1 моль связанного амина. Роль щелочи заключается не только в регенерации связанного амина, но и в связывании летучих про дуктов побочных реакций, уменьшении кислотности раствора и, следовательно, в снижении уноса примесей и в уменьшении корро зии разгонного куба.
Общие потери амина при вакуумной разгонке не превышают 0,08 кг/т NH3, эта величина зависит в основном от потерь свободного амина с кубовым остатком.
Вместо щелочи может применяться сода или содовопоташная смесь [162].
Другой способ — высокотемпературная разгонка при атмосфер ном давлении или давлении регенерации [145, 165—169]. При раз гонке под давлением регенерации практически не затрачивается тепло: пары из разгонного аппарата направляются в регенератор (под глухую тарелку). Это значительно упрощает процесс, так как вместо восьми аппаратов, показанных на рис. IV-55, для разгонки достаточно лишь одного.
При повышении давления увеличивается температура кипения раствора. В этих условиях некоторые продукты побочных реакций, например оксазолидон-2 , регенерируются до мопоэтаноламина. Однако большая часть примесей не может быть превращена в МЭА. В то же время повышение температуры приводит к увеличению скорости деградации (осмоления) МЭА. Расчет показывает, что на установках очистки конвертированного газа (т. е. при относи тельно малой доле раствора, выводимого на разгонку) количество МЭА, дополнительно потерянного замечет повышения температуры, крайне невелико. Общие потери МЭА при разгонке под давлением
не превышают 0,11 кг/т NH3 (0,03 кг/1000 |
м3 газа) [135]. |
|
|
Разгонка под давлением регенерации |
может |
осуществляться |
|
в аппарате — смоловыделителе, изображенном на |
рис. IV-56, |
либо |
|
в перегонном кубе, применяемом для вакуумной разгонки |
(см. |
||
рис. IV-55). Емкость разгонного куба должна быть примерно в 100 |
|||
раз больша количества раствора, отбираемого на разгонку в 1 |
мин |
[145]. Разгонка проводится в две стадии (полунепрерывный процесс). Продолжительность первой стадии разгонки зависит от концентра ций примесей в растворе. При температуре 139—146 °С отбор рас твора прекращается и в аппарат добавляют конденсат.
Для более полного извлечения амипа из кубового остатка и очи стки аппарата в него подают острый пар. Кубовый остаток удаляют
промывкой водой. Щелочь добавляется при заполнении куба рас твором обычно в количестве около 2—3% (масс.) или в соответствии с рекомендациями, приведенными выше. Избыток щелочи или соды нежелателен, так как при этом повышается температура кипения и начинается кристаллизация солей.
Показатели типичного режима работы аппарата для разгонки приведены на рис. IV-57. В присутствии щелочи выход МЭА не сколько повышается, но при малой скорости деградации амина
Пары МЭА
Кубовый остаток
Рис. IV-56. Аппарат для разгонки МЭА при давлении регенерации.
.этой величиной можно пренебречь. Разгонка под давлением регене рации 166—235 кПа (1,7—2,4 кгс/см2) детально исследована [135, 166, 167] в аппаратах, показанных на рис. IV-55 и IV-56.
Анализ кубового остатка при разгонке МЭА под давлением пока зал, что в конце первой стадии концентрация ОЭЭДА возрастает до 6,7—7,8% (при содержании ОЭЭДА в рабочем растворе 0,02%), причем увеличение происходит не только за счет механического накопления (по балансу), но и вследствие дополнительной дегра дации раствора. Концентрация оксазолидона-2 , наоборот, снижается по сравнению с балансом (в рабочем растворе 0,05%, в кубе 0,07— 0,1%). Сумма примесей в кубовом растворе в конце первой стадии близка к 25%, дополнительные потери МЭА за счет побочных реак ций не превышают 0,04 кг/т ГШ3. В целом количество накапливае мых примесей в кубе может быть рассчитано по уравнению (IV,88)
[135].
Изучена та#же регенерация (разгонка) МЭА при очистке коксо вого газа [162]» проводимая при 200—220 °С в присутствии щелочи, что позволяет более полно извлекать амин из образующихся побоч ных продуктов-
При разгонке под давлением иногда наблюдается брызгоунос примесей с парогазовой смесью. Это может быть объяснено недоста точным сепарационным пространством в аппарате или чрезмерным
|
|
Вреу.Р, сут |
Рис. IV-57. Характеристика |
режима |
разгонки раствора МЭА при Рпаб. = |
= |
0,98-10б |
Па (1 кгс/см2): |
1 — общая щелочность кубового раствора; 2 — концентрация свободного МЭА в кубовом рас творе (включая МЭА в виде бикарбоната, карбоната и карбамата); 3 — концентрация связан ного МЭА (в виде продуктов побочных реакций) в кубовом растворе; 4 — температура в кубе; 5 — производительность; 6 — концентрация МЭА в дистилляте.
расходом пара. Кроме того, к брызгоуносу приводит также либо очень высокий, либо слишком низкий уровень жидкости (оголение трубчатки).
ФИЛЬТРАЦИЯ РАСТВОРА
Фильтрацией можно удалять как взвешенные частицы, так и рас творенные примеси. Введение стадии фильтрования существенно облегчает работу установки разгонки. На фильтрацию направляют небольшую часть циркулирующего раствора (от 1 до 25%).
Применяют различные типы фильтров. Весьма эффективен для этой цели активированный уголь. Емкость угля КАД составляет 25—30%, несколько ниже емкость угля АР-3. Перед фильтром, с ак тивированным углем устанавливают фильтр с гравием, что способ ствует увеличению срока службы угля, а также позволяет очистить раствор от взвешенных примесей. Применяются и другие типы филь тров [170], например диатомовая земля (листовые фильтры из диа томовой земли, нанесенные на сетку из нержавеющей стали [171]).
Преимущество такого Фильтра перед фильтром из активированного угля заключается в ^ом, что на нем не адсорбируются ингибиторы коррозии. При фЧльурац#и рекомендуется поддерживать скорость раствора около 8 Д/(м#н-м2), хотя в ряде случаев скорость достигает 20—60 л/(мин-м2)ч Высота фильтрующего слоя в одном адсорбере не превышает 3 ц.
Уголь меняют ид# регенерируют, если проба раствора после фильтрации становится мутной, окрашенной или вспенивается. Обычно первый ЦИкд работы угл#- может составлять 4 мес, после первой регенерации семь недель, затем 3—4 недели, после чего уголь заменяют. Фильтр рекомендуют устанавливать после клапана на линии вывода раствора из абсорбера (при абсорбции под давле нием) либо на линии нагнетания насоса регенерированного раствора.
При очистке газа растворами ДЭА фильтрация является основ ным способом удаления примесей из раствора.
Опыт эксплуатации угля АР-3 на системе МЭА-очистки в произ водстве аммиака мощностью 600 т NH3 в сутки (~ 9 0 тыс. м3/ч очи щаемого газа) показал, что за 1,5 мес. работы при отсутствии раз гонки удалось снизить концентрацию примесей с 6 до 4 г/л. Расход жидкости составлял 1—2 м3/ч. Уголь полностью отрабатывался за 2 мес.
Расходные коэффициенты при МЭА-очистке
Основной статьей расхода при МЭА-очистке является расход тепла, который сильно колеблется в зависимости от условий (состав
и давление очищаемого газа, |
степень очиртки, схема очистки). |
Если абсорбция производится |
при атмосферном давлении (а „ас = |
= 0,4 моль/моль), то расход тепла обычно составляет до 11,74 МДж/м3 (2800 ккал/м3 С 02). Показано, что при проведении разгонки МЭА под давлением, при хорошем состоянии теплообменников, поддер жании концентрации МЭА 20% и использовании схем с разделен ными потоками расход тепла может быть снижен до 7,95—8,38 МДж/м3
(1900-2200 ккал/м3 |
С 02). |
|
При абсорбции цод |
давлением (анас = 0,6—0,65 моль/моль), |
|
при недорекуперации |
At |
= 12—13 °С и при использовании много |
поточных схем расход тепла составляет 5,23—5,46 МДж/м3 (1250— 1300 ккал/м3 С 02).
Главными причинами перерасхода тепла являются следующие: плохое состояние теплообмениой и массообмепной аппаратуры, вызванное нерегулярной разгонкой и плохой фильтрацией раствора; неоптимальная степень регенерации раствора (либо чрезмерная,
либо недостаточная циркуляция раствора); чрезмерная очистка газа. При увеличении сверх нормы степени
очистки газа расход тепла резко возрастает. Поэтому ограничение не только максимума, по и минимума концентрации С 02 в очищен ном газе позволяет снизить расход тепла.
Таким образом, при заданной нагрузке по газу и заданной кон центрации МЭА расход тепла минимален, если степень очистки газа не глубже заданной, а также поддерживается оптимальная степень регенерации (оптимальная циркуляция раствора). Кроме того, важно поддерживать равномерное распределение раствора по тепло обменникам.
Расход электроэнергии при МЭА-очистке обычно невелик и соста вляет 72—108 МДж/т NH3 (20—30 кВт-ч/т NH3) или 18— 28,8 МДж/1000 м3 (5—8 кВт-ч/1000 м3 очищаемого газа).
Расход моноэтаноламина при хорошей эксплуатации установки может быть снижен до 0,2 кг/т NH3 (0,05 кг па 1000 м3 газа); практи чески он составляет 0,4—0,5 кг/т NH3 и более. Потери могут быть «химическими» (точнее потери с кубовым остатком при разгонке в виде побочных продуктов и свободного МЭА), за счет уноса с газом и механическими. «Химические» потери моноэтаноламина при очи стке конвертированных газов в тех случаях, когда температура гре ющего пара не превышает 150 °С, составляют 0,05—0,1 кг/т NH3, т. е. эта доля в общих потерях амина относительно невелика. При очистке кислородсодержащих и коксового газов увеличивается ско рость побочных реакций и возрастают химические потери.
Унос с газом обычно невелик (менее 0,1 кг/т NH3), хотя при опре деленных условиях он составляет существенную часть потерь. Из данных о давлении паров моноэтаноламина следует, что при абсорб ции при атмосферном давлении потери паров моноэтаноламина (без брызгоуноса) могут составлять 0,4—0,5 кг/т Н3. В таких слу чаях необходимы промывка газов конденсатом или флегмой на кол пачковых тарелках в верхней части абсорбера и установка брызгоотбойников.
К потерям МЭА приводит также вспенивание раствора (см. выше).
ОЧИСТКА ГАЗА РАСТВОРАМИ ДЭА
Диэтаноламин нашел широкое применение как хемосорбент при очистке газов, особенно природного газа [171]. Одной из причин широкого распространения ДЭА является возможность очистки газов, содержащих сероорганические соединения. Кроме того, тем пература кипения ДЭА выше, чем МЭА (меньше давление насыщен ных паров), что позволяет вести абсорбцию при более высокой темпе ратуре. Такая необходимость возпикает при наличии в природном газе тяжелых углеводородов. Повышение температуры абсорбции позволяет избежать конденсации углеводородов и вспенивания.
Одип из вариантов процесса очистки газа раствором ДЭА назы вается ДЭА-СНПА-процессом [172]. Он эффективен при очистке газа под высоким давлением (6 ,86—7,35 МПа, 70—75 кгс/см2), что по зволяет достичь высоких степеней карбонизации ДЭА-раствора (до 1 моль С 02 на моль ДЭА). В табл. IV-23 приведено сравнение основпых показателей ДЭА-процесса и ДЭА-СНПА-процесса [171] при очистке природного газа от H 2S и С02.
Показатель
Содержание в очищенном газе H2S, мг/м3
С0 2, см3 /м3 Концентрация ДЭА, % (масс.)
Содержание суммы H2S и С02 в насыщенном растворе, моль/моль ДЭА Расход пара на регенерацию, кг/м3
Температура раствора на входе в аб сорбер, °С
Абсолютное давление в десорбере МПа кгс/см2
Температура, °С низа десорбера
раствора на входе в десорбер верха десорбера
Расход ДЭА, мг/м3 сырого газа Расход отдувочного тепла q0тд,' % от
общего расхода тепла Содержание в регенерированном рас
творе, г/л
со2
H2S
ДЭА-СНПА- ДЭА-процесс процссс
8.0 |
1,1-3.4 |
60,0 |
До 500 |
2 0 — 22 |
25 -30 |
0 ,6 —0,7 |
0,77—1,0 |
ЮО— 1 1 0 |
108—132 |
50 |
|
|
0,245 |
|
2,5 |
130 |
— |
1 1 0 |
|
1 1 0 |
— |
200 |
6 4 -8 0 |
26 |
— |
1,0 |
— |
0 00 1 сл |
— |
|
Из таблицы видно, что процесс ДЭА-СНПА отличается от ДЭАпроцесса увеличением (до 25—30%) концентрации ДЭА и высокими степенями его карбонизации. Равновесие в системе ДЭА—Н 20 —С 02 изучали ряд авторов [73, 74, 82, 84, 85]: в работах [73, 74] по лучены данные при низких степенях карбонизации раствора (до
0,4 моль/моль), в работе [82] — под давлением. |
Исследована также |
||||
растворимость |
H 2S |
в |
присутствии С 02 [111]. |
На рис. IV-58 |
при |
ведены данные |
[73, |
74] по растворимости С 02 |
в растворах |
ДЭА. |
|
При сравнении |
с аналогичными данными для системы МЭА— |
||||
Н 20 —С 02 видно, что |
при прочих равных условиях (температура, |
||||
концентрация |
амина |
и С 02) давление С 02 над раствором |
ДЭА |
выше, чем над раствором МЭА. Следовательно, при применении ДЭА нельзя достичь столь же тонкой очистки газа, как при МЭА-очистке. Соответственно, ДЭА может регенерироваться глубже и с меньшим расходом тепла на отдувку, чем МЭА. Показано, что при одинаковой концентрации С 02 в насыщенном растворе расход тепла при очистке раствором ДЭА может быть снижен в 1,4 раза по сравнению с очист кой МЭА [74, 126]. Это частично объясняется возможностью более глубокой регенерации ДЭА (а0пт = 0,02—0,05 моль С 02/моль), а также уменьшением флегмового числа.
Однако скорость абсорбции растворами ДЭА ниже, чем раство рами МЭА, что приводит к увеличению габаритов абсорбера. ДЭА отличается меньшей термической устойчивостью. Рабочий раствор
15 Заказ 1460 |
225 |
ДЭА нельзя подвергать разгонке под давлением, так как для этого требуется чрезмерно высокая температура. Кроме того, температура кипения продуктов побочных реакций ДЭА с С 02 близка к темпера туре кипения ДЭА, поэтому ДЭА очищают фильтрованием —10% раствора через активированный уголь. Уголь затем подвергают регенерации паром и промывке водой (1 раз в трое суток).
Рис, IV-58. Зависимость равновесного давления С02 от степени карбонизации раствора ДЭА [109, 110] при различных температурах ( /—V) и концентрациях ДЭА (1—5):
I — при 25 °С; I I — при 40 °С; I I I — при |
50 «С; |
IV — при |
60 °С; V — при 75 °С; I — |
0,5 моль/л; 2 — 1,0 моль/л; 3 — 2,0 моль/л; |
4 — 5,0 моль/л; |
5 — 8,0 моль/л (зачерненные |
|
точки — данные |
[98]). |
|
На небольших установках применяются патронные фильтры волокнистого типа со сменными элементами, за которыми иногда следует угольный фильтр. На крупных установках используются фильтры листового типа, на которые нанесены в качестве фильтрующего слоя мелкозернистый асбест и порошок угля. Срок службы фильтра от 1 нед. до 3 мес. Применяются также фильтры трубчатого типа, изготовляемые из пористых пластиковых цилиндров, на кото рых нанесен слой фильтрующего материала. Осадок и отработанный слой фильтрующего материала периодически смывают (отсасывают) при обратном ходе промывной воды.
При очистке природного газа в раствор ДЭА обычно добавляют антивспениватель. Для нейтрализации и разложения продуктов побочных реакций в рабочий раствор добавляют также Na2C03 (или NaOH) в количестве, в 1,5 раза превышающем количество
примесей. Кроме фильтрования используют и другие методы очистки растворов ДЭА от продуктов побочных реакций. Так, [143] к части рабочего раствора добавляют NaOH или КОН, отгоняют воду (до остаточного содержания 5—10% Н аО), затем смешивают с изопро пиловым (или другим) спиртом. При этом примеси осаждаются, их
фильтруют, спирт отгоняют из |
раствора |
и раствор |
возвращают |
в цикл. |
|
|
|
Используется также метод |
разгонки |
[143] при |
атмосферном |
давлении с добавлением солей калия (для снижения температуры плавления). Вместо обычного куба используется ректификационная колонна с кубом. Из куба периодически отбирают соли, из паровой фазы куба — ДЭА, сверху отводятся пары воды.
3. ОЧИСТКА ГАЗА РАСТВОРАМИ ДИИЗОПРОПАНОЛАМИНА
Растворы диизопропаноламина (ДИПА, фирменное название процесса АДИП) начали применяться для очистки газа от кислых компонентов в конце 50-х годов. В настоящее время ДИПА исполь зуется как в водных растворах (до 40%), так и в смеси с сульфоланом (процесс «Сульфинол»).
На рис. IV-59 и IV-60 приведены полученные в ГИАП экспери ментальные данные по растворимости С 02 в растворе, содержащем 3,3 моль/л ДИПА. Сопоставление с растворимостью С 02 в водных растворах МЭА такой же концентрации показывает, что раствори мость СО2 в растворах ДИПА в условиях абсорбпщи близка к рас творимости С 02 в МЭА. Так, при 30 °С и давлении С 02, равном 1,013*10БПа и 5,07• 105 П а(1и 5 кгс/см2), растворимость С 02 в 3,3 н. водном растворе ДИПА равна соответственно 50 и 60 м3/м3, а в 3,3 н. водном растворе МЭА — 51,5 м3/м3 и 61,5 м3/м3.
Однако равновесное давление С 02 при малых а и высоких темпе ратурах (т. е. в условиях регенерации) над раствором ДИПА суще ственно выше. Так, при а = 0,1 моль С 02 на 1 моль амина и 100 °С давление С 02 над растворами ДИПА и МЭА (3,3 моль/л) равно 1,333 -104 Па и 6,66-102 Па (соответственно 100 и 5 мм рт. ст.). Это дает возможность существенно облегчить условия регенерации ДИПА за счет снижения температуры кипения. Кроме того, уменьшаются фЛСгмовые числа. В результате этого уменьшается расход тепла, поверхность теплообмена (из-за снижения температуры регенерации), а Также скорость побочных реакций.
На рис. IV-61 приведены приближенные зависимости темпера туры кипения раствора ДИПА от степени его карбонизации при различных давлениях. Графики построены путем экстраполяции зависимостей lg Рсо, от 1IT (см. рис. IV-59). При этом давление насыщенных паров воды рассчитывали по закону Рауля. Сопоста вление данных рис. IV-36 и рис. IV-61 показывает, что температура кйЪения растворов ДИПА существенно ниже, чем растворов МЭА.
cn
r=>
2,3 |
2 ,5 |
2,7 |
2 ,9 |
3,1 |
3,3 |
3 ,5 |
|
|
f/T -Ю3 |
|
|
|
Рис. IV-59. Давление С02 над |
водным раствором |
диизоцропаноламина |
(3,3 моль/л) при различных температурах и степенях карбонизации: |
||
1 — а г = 0,113 моль COf/моль ДИПА; |
2 — а = 0,222; 3 — а |
= 0,320; 4 — а = 0 390' |
5 — а = 0,463. |
|
Ру 10 5Па
Рис. IV-60. Растворимость С02 в водном растворе ДИПА (3,3 моль/л):
1 — i при 30 °С; 2 — при 80 °С; 3 — при 20 °С.
Ниже сопоставлены температуры кипения растворов МЭА в °С и ДИПА (3,3 моль/л) при Рр — 167 кПа, или 1,7 кгс/см2:
|
|
|
|
|
|
а = 0,4 моль/моль |
а = 0,1 моль/моль |
|
||||||
|
|
|
МЭА |
|
|
|
105 |
|
|
118 |
|
|
|
|
|
|
ДИПА |
|
|
|
78 |
|
|
111 |
|
|
|
||
Соответственно при а = |
0,4 значение |
Фт!п |
для |
раствора МЭА |
||||||||||
равно 2,07, а для раствора ДИПА |
— 0,64. |
|
|
|
|
|||||||||
В( литературе |
приведе |
|
|
|
|
|
|
|
|
|||||
ны |
основные |
параметры |
|
|
|
|
|
|
|
|
||||
процесса в различных |
ус |
|
|
|
|
|
|
|
|
|||||
ловиях |
[173, |
174]. |
Так, |
|
|
|
|
|
|
|
|
|||
ДИПА-процесс применяет |
|
|
|
|
|
|
|
|
||||||
ся для очистки газа под> |
|
|
|
|
|
|
|
|
||||||
давлением от 490 кПа до |
|
|
|
|
|
|
|
|
||||||
2,45 МПа (5—25 |
кгс/см*), |
|
|
|
|
|
|
|
|
|||||
содержащего до 5,5% С 02 |
|
|
|
|
|
|
|
|
||||||
и от 0,5 до 15% H 2S. Про |
|
|
|
|
|
|
|
|
||||||
цесс ведут |
в |
тарельчатом |
|
|
|
|
|
|
|
|
||||
абсорбере |
с 15—25 тарел |
|
|
|
|
|
|
|
|
|||||
ками. |
Концентрация H 2S |
|
|
|
|
|
|
|
|
|||||
в очищенном газе от 0,0002 |
|
|
|
|
|
|
|
|
||||||
до |
0,01%. |
Расход |
теп |
|
|
|
|
|
|
|
|
|||
ла |
составляет |
5,44— |
Рис, IV-61. Зависимость |
температуры ки |
||||||||||
9,65 МДж/м3 |
кислого газа |
|||||||||||||
(1300—2300 ккал/м3). |
пения водных |
растворов ДИПА (3,3 моль/л) |
||||||||||||
|
от степени карбонизации и давления: |
|||||||||||||
ДИПА значительно бо |
1 |
— Р = |
1,66-10» Па (1,7 иге/см*); |
2 |
—. Р = 1,86 X |
|||||||||
лее устойчив |
в среде COS, |
х |
10» Па |
(1,9 кгс/см*); |
3 |
— |
Р |
=» 2,94-10» Па |
||||||
чем |
МЭА, |
который |
реа |
|
|
|
(3 кгс/см*). |
|
|
|
||||
|
|
|
|
|
|
|
|
гирует с сероокисыо угле рода с образованием тиокарбонатов. Диалканоламины (ДЭА, ДИПА)
реагируют с COS только до тиокарбонатов, |
которые регенериру |
||
ются в обычных условиях в регенераторе с |
образованием |
H 2S, |
|
СО2 и амина, что исключает необходимость |
разгонки |
раствора. |
|
Однако скорость поглощения COS мала (степень извлечения |
50%). |
||
В случае применения раствора ДИПА в сульфолане |
раствори |
||
мость COS увеличивается и достигается более полное ее извлечение. |
|||
Так же, как при очистке от С 02, расход |
тепла на очистку от |
H 2S раствором ДИПА меньше, чем раствором МЭА, за счет снижения теплоты растворения и уменьшения флегмового числа (выше давле ние газа над раствором). Так, при а = 0,4 моль H 2S на 1 моль амина значения ДЯ для МЭА, ДЭА и ДИПА соответственно равны 60,8, 37,7 и 37,3 кДж/моль (14 500, 9100 и 8900 кал/моль H 2S). Вследствие того, что парциальное давление H 2S и С 02 над раствором ДИПА выше, чем над раствором МЭА, ДИПА регенерируется глубже и при более низкой температуре, чем МЭА. Ниже приведены флег-
мовые числа [173] при очистке газа от H 2S растворами МЭА, ДЭА и ДИПА, в зависимости от требований к качеству очищенного газа:
|
Жесткие |
Умеренные |
|
требования |
требования |
МЭА |
3,0 |
2,5 |
ДЭА |
2,5 |
2,0 |
ДИПА |
1,8 |
0,9 |
При АДИП-процессе практически отсутствует коррозия аппара туры. Расходы на ремонт составляют 2—3% первоначальной стои мости оборудования. Годовой расход ДИПА не превышает половины первоначального заполнения системы.
4. ОЧИСТКА ГАЗОВ ВОДНЫМИ РАСТВОРАМИ ПОЛИАМИНОВ
Поглотительная способность этаноламинов в соответствии со стехиометрией химической реакции не может превышать 1 моль газа на 1 моль амина.
Существует возможность увеличения поглотительной способности и скорости абсорбции за счет повышения концентрации МЭА в рас творе. Однако эта возможность ограничена, во-первых, опасностью коррозионного разрушения и растрескивания сталей в среде 30 %- ного и более МЭА [147]. Кроме того, В. Е. Дымовым и И. Л. Лейтесом (ГИАП) показано, что при постоянном расходе тепла в реге нераторе скорость абсорбции С 02 раствором МЭА достигает макси мума при очистке 30%-ным раствором, поэтому многие исследова тели изучали возможность применения для очистки газов аминов, содержащих две или три аминные или иминные группы (полиамиыов) [175—180]. Такие соединения должны обладать более высо кой поглотительной способностью по отношению к СОа. Так, у диами нов она может быть равна в пределе 2 моль С 02 на 1 моль амина.
Описано |
применение |
диэтилентриамина (ДЭТА) |
[175, |
176]. |
||||
тетраэтиленпентамина |
(ТЭПА) |
[177], |
этилендиамина |
(ЭДА) |
[178]. |
|||
смесей |
полиаминов |
(ПЭПА) |
[179], |
гексаметилендиамина |
(ГМД) |
|||
и др. |
[180]. |
Недостатком большинства полиаминов |
является их |
|||||
|
|
Таблица |
I V -24. |
Свойства полиаминов |
|
|
||
|
|
|
|
|
|
Температура, °С |
|
|
|
Подиамин |
|
Относит, моле- |
|
|
|||
|
|
кулярная масса |
плавления |
|||||
|
|
|
|
|
|
кипения |
||
Гексаметилендпампн (ГМД) |
|
116,14 |
196 |
42 |
||||
Оксиэтилэтилендиамин |
|
|
104,13 |
243,3 |
_ |
|||
(ОЭЭДА) |
|
|
|
|
|
|
|
|
Диэтилентриамин (ДЭТА) |
|
103,16 |
207,1 |
—39 |
|
крайне высокая коррозионная активность (исключение составляет разработанный в ГИАП и ВНИИнефтехим абсорбент ДА-1, не вызы
вающий коррозии). В табл. IV-24 |
приведены основные |
свойства |
|
некоторых полиаминов. |
|
|
|
Механизм реакции ЭДА с С 02 |
описан |
в литературе |
[178]. На |
рис. IV-62—IV-67 приведены данные по |
равновесию в |
системах |
СО2 — растворы различных ди- и триаминов. Как видно из рисун ков, при одинаковой концентрации С 02 в растворе давление С 02 над растворами полиаминов значительно ниже, чем над растворами
Рис. IV-62. Зависимость давления С02 над водными растворами диамина ДА-1 (сплошные линии) и МЭА (3,3 моль/л) (пунктирные лпнии) от температуры
и степени карбонизации:
<5_— а = 0,175'моль СО,/моль амина; |
2 , "б — а = 0,311; |
39 7 — а = 0,41; 4 — а = |
— 1,02 моль |
С02/модь диамина. |
|
МЭА, и соответственно выше их поглотительная способность. Так, при 50 °С и концентрации С 02 в растворе 0,31 моль С 02 на 1 моль амина давление С 02 над раствором ДА-1 равно 0,15 мм рт. ст., в то время как над раствором МЭА при тех же условиях оно соста вляет 1 мм рт. ст. Равновесная концентрация СОа в 2,5 н. растворе МЭА при 760 мм рт, Ст. и 20 °С составляет 43 м3/м3, а в 2,5 н. раство рах ДА-1 — около 70 м3/м3, в ГМД — более 75, в ДЭТА — 90 м3/м3 (в 3,3 н. растворе ДЭТА — 111 м3/м3).
Приведенные данные показывают, что на стадии абсорбции поли амины должны иметь несомненные преимущества перед МЭА. Однако наряду с этим уменьшение равновесного давления СОа над рас творами неизбежно приводит к ухудшению регенерации этих
PCOvw *па
Рис. IV-63. Растворимость |
С02 при 20 °С в водных растворах аминов: |
1 —* МЭА (2,в моль/л); 2 |
— ГМД (2,5 моль/л); 8 ДА-1 (2,5 моль/л). |
]*ис. |
IV-64, |
Растворимость С02 при 20 °С в водных растворах аминов: |
1 |
— Л1УЛ |
(2,5 моль/л); 2 — ДЭТА (2,5 моль/л); 3 — ДЭТА (3,0 моль/л). |
хемосорбентов. Поэтому регенерацию таких хемосорбентов целесооб разно вести либо при более высокой температуре (до 140—150 °С), а следовательно, во избежание увеличения флегмового числа и при более высоком давлении 2,94—3,92 кПа (3—4 кгс/см2), либо огра ничиться значительно более грубой регенерацией. Для ДЭТА кон центрация СОа в регенерированном растворе при Р? = 1,47 КПа (1,7 кгс/см2) должна составлять около 0,6 моль СО2 на 1 моль ДЭТА. Однако и в этом случае реальная поглотительная способность 3,3 н. раствора ДЭТА примерно вдвое выше поглотительной способности МЭА такой же концентрации (при насыщении его до а = 0,65 моль СО2 на 1 моль МЭА и регенерации до а = 0,2).
Преимуществом многих полиаминов является более высокая скорость абсорбции двуокиси углерода. Ю. В. Аксельрод и А. И. Мо розов (ГИАП) изучали некоторые свойства ДЭТА и скорость абсорб ции раствором ДЭТА. Так, на рис. IV-68 приведены данные, полу ченные Ю. В. Аксельродом и А. И. Морозовым по сравнительной скорости хемосорбции С 02 водными растворами ДЭТА и МЭА при атмосферном давлении в пленочной колонне. Установлено, что скорость абсорбции С 02 водными растворами ДЭТА сущест венно выше во всем диапазоне степеней карбонизации, чем скорость абсорбции растворами МЭА. При умеренных степенях насыщения скорость поглощения С 02 раствором ДЭТА в 1,7—2 раза превы шает скорость поглощения раствором МЭА той же концентрации, причем преимущество ДЭТА сохраняется во всем диапазоне кон центраций СО2 в газе.
Константа скорости химической реакции С 02 с ДЭТА при 23 °С составляет 18 400 м3/(кмоль«с), что более чем в два раза превышает константу скорости взаимодействия С 02 с МЭА. В результате при
а> 0,5 скорость абсорбции раствором ДЭТА, как видно из рис. IV-68,
в3—20 раз выше, чем раствором МЭА. Средняя скорость поглощения
С 02 в диапазоне 0 < а < 0 ,7 5 для раствора ДЭТА в 2—2,5 раза выше, чем/ для МЭА.
Наличие экстремумов на графике зависимости скорости абсорб ции от а объясняется, по-видимому, неравноценностью аминогрупп в молекуле ДЭТА. Скорость взаимодействия С 02 с различными аминогруппами зависит от их положения в молекуле ДЭТА и при определенных условиях (исчерпывание крайних аминогрупп, гид ролиз продуктов реакций и др.) может возрастать.
Высокая скорость абсорбции С 02 растворами ДЭТА в значи тельной мере обусловлена также большим по сравнению с МЭА эффектом поверхностной конвекции. Интенсивность поверхностной конвекции в растворе ДЭТА сохраняется вплоть до а ^ 1, в то время Как для растворов МЭА поверхностная конвекция не обнаруживается Уже при а = 0,5.
Расчеты, проведенные на основе экспериментальных данных, Доказали возможность создания процесса очистки растворами ДЭТА Д других диили триаминов, в котором применительно к агрегату Мощностью 1360 т NH3 в сутки диаметр абсорбера не будет
4ff
РС 0 2 > ® *Па
Рис. IV-65. Давление С02 над раство |
Рис. IV-6 6 . Растворимость С02 в |
||||||
ром ДЭТА |
(4,75 |
моль/л): |
водных растворах ОЭЭДА (3,3 мо ль/л |
||||
1 — концентрация СО* |
25,4 |
г/л; |
2 |
— то же, |
при |
20 °С: |
|
64,8 г'л; з — то же, |
|
138 г/л ; |
4 |
— то же, |
J — 2,5 моль/л, |
2 — 3,3 моль/л. |
|
192,6 |
г/л. |
|
|
|
|
|
Рис. IV-67. Давление С02 над раство-^ |
Рис. IV-6 8 . Зависимость скорости |
||
рами ОЭЭДА (3,3 моль/л): |
поглощения С02 водными растворами |
||
- а - |
0,703 |
моль СО,/моль ОЭЭДА; г _ |
ДЭТА (кривая 1) и МЭА (кривая 2) |
а = |
0,414; |
з — а = 0,175 моль/моль. |
от степени карбонизации в пленоч |
|
|
|
ной колонне при Р с 0 = 1,013 •10бПа |
(1 атм).
превышать 3,2 м, а регенератора — 3,8 м. При одинаковом расходе тепла количество циркулирующего раствора снижается примерно вдвое по сравнению с процессом МЭА-очистки.
Ниже приведены технологические показатели процесса очистки газа растворами ДЭТА:
Расход конвертированного газа (при н. у.), м3/ч |
205 000 |
||
Давление на входе в абсорбер |
2,74 |
||
МПа . |
. |
||
кгс/см2 ..................... |
|
28 |
|
Концентрация С02, % (об.) |
17,5 |
||
на |
входе |
. . . |
|
на |
выходе |
0 ,0 1 |
|
Расход раствора, |
мз/ч . . . |
600 |
|
Степень карбонизации раствора |
|
||
в верхней части абсорбера . |
0,6 |
||
в верхней части регенератора |
1,5 |
||
Температура, °С |
|
95 |
|
насыщенного раствора на выходе из абсорбера . . |
|||
регенерированного раствора на выходе из регенера |
|||
|
тора ...................................................... |
|
135 |
парогазрвой смеси из регенератора |
1 1 0 |
||
Расход тепла на |
регенерацию |
21 |
|
ГДж/ч |
|
||
Г к а л /ч ...................................................... |
|
50 |
|
Гидравлическое сопротивление абсорбера |
. 0,507-105 |
||
Па . . |
|
||
кгс/см2 |
|
0,5 |
Таким образом, ДЭТА и другие полиамины могут найти приме нение для очистки газов, несмотря на высокую коррозионную актив ность большинства из них. В ряде случаев возможно использование оборудования из нержавеющей стали либо применение ингибиторов коррозии.
5. ОЧИСТКА ГАЗА РАСТВОРОМ ДИГЛИКОЛЬАМИНА
Дигликольамин (ДГА) — фирменное название алканоламина (2,2-аминоэтоксидиэтанола, или р,р-гидроксиламиноэтилового эфира) H0(CH2)20(CH2)2NH2, используемого в процессе очистки «Эконаншн» [181—183]. Схема процесса не отличается от обычной схемы МЭА-очистки (см. рис. IV-31). Основное отличие процесса — высо кая концентрация хемосорбента (не менее 65%), что позволяет существенно уменьшить количество циркулирующего растворителя и соответственно снизить расход тепла (на 18—20%) и уменьшить габариты аппаратуры.
Установлено, что, несмотря на высокую концентрацию ДГА, коррозионная активность такого раствора не выше, чем при МЭА- о'шстке. Однако в работе [183] указывается на возрастание коррозии.
Для разложения соединений ДГА с COS и CS2 часть раствори теля подвергают разгонке, поэтому процесс можно использовать Дйя очистки газов, содержащих сероорганические соединения. Применяют также фильтрацию раствора от примесей [183].
В растворы ДГА рекомендуется добавлять ингибитор коррозии [183]. Разработаны [183] методы борьбы с побочными реакциями ДГА и регенерации ДГА из продуктов побочных реакций. Недоста ток растворителя [143] — высокая стоимость, сравнительно боль шие потери.
6. ОЧИСТКА ГАЗОВ РАСТВОРАМИ АЛКАНОЛАМИНОВ В ОРГАНИЧЕСКИХ РАСТВОРИТЕЛЯХ
Растворы МЭА и других алканоламинов в воде имеют недоста ток, связанный с тем, что концентрация «активного» компонента в растворе невелика. Основную часть абсорбента составляет разба витель — вода. Приведенные ранее данные по расходу тепла при МЭА-очистке показывают, что основную часть составляют расход тепла на нагрев днагр и на отдувку дотд. Вода имеет большую тепло емкость, что обусловливает большое значение #нагр; велики также теплота испарения и давление насыщенных паров, что, в свою оче редь, влияет на величину дотд.
В последние годы разработаны методы очистки газа растворами алканоламинов в органических растворителях (или в смесях воды и органического растворителя). Кроме более низких теплоемкостей, давления насыщенных паров и теплоты испарения, преимуществом органических растворителей является то, что при абсорбции под давлением они сами начинают поглощать С 02 (за счет физической абсорбции), причем десорбция этой части растворенного газа дости гается лишь сбросом давления.
Наличие органических абсорбентов в растворе позволяет про водить комплексную очистку от различных примесей, например от тех органических сернистых соединений, которые не взаимодей ствуют с алканоламинами. Наконец, при малой концентрации воды в растворе наряду с очисткой можно проводить осушку газа. В от личие от чисто физической абсорбции в данном случае можно до стичь тонкой очистки в одну ступень.
Разработаны разнообразные варианты такого процесса. В каче стве алканоламина используется МЭА, ДЭА, ДИПА, а в качестве
органического разбавителя — сульфолан (процесс |
«Сульфинол» |
|
[171, 184—193]), метанол (процесс «Амизол» |
[194]), |
а также N- |
метилпирролидон, тетрагидрофуриловый |
спирт, |
бензиловый |
спирт и другие продукты, относящиеся к разнообразным классам органических соединений [184, 195—199].
К разбавителю предъявляется ряд требований: термохимическая устойчивость в смеси с водой, алканоламином
и с компонентами очищаемого газа; доступность и низкая стоимость;
смешиваемость с амином, водой и продуктами реакции (по край ней мере отсутствие твердой фазы);
низкие теплоемкость, давление насыщенных паров, вязкость рабочего раствора;
петоксичность; возможность разделения абсорбента и продуктов побочных
реакций.
Приведены [195, 198] эскпериментальные данные по раствори мости СО2 в смесях МЭА с различными органическими растворите^ лями. На рис. IV-69 в качестве примера показана зависимость растворимости С 02 от давления С 02 при 20 °С и давлениях до 1,013-10б Па (1 кгс/см2) в различных растворах МЭА.
рс о ^ °
Рис* |
IV-69. Растворимость двуокиси углерода при 2 0 °С в растворах МЭ |
|
(2,5 моль/л) в различных разбавителях: |
1 ^ 3 |
метаноле; 2 — в тетрагидрофуриловом спирте; 3 — в бензиловом спирте; 4]— в моно- |
|
метиловом эфире этиленгликоля; 5 — в воде. |
Из графиков видно, что растворимость С 02 в аминоорганических растворах при низких давлениях несколько ниже, чем в аминоводиых растворах. Это указывает на возможность более глубокой регенера ции аминоорганических растворов. В табл. IV-25 приведены дан ные по равновесному давлению С 02 над аминоорганическими рас творами.
На рис. IV-70 приведены данные о давлении С 02 над растворами МЭА в этиленгликоле, N-метилпирролидоне и тетрагидрофуриловом спирте, содержащем около 13% воды. Из рисунка следует, что при очистке растворами МЭА в органических растворителях растворимость С 02 быстрее убывает с ростом температуры; теплота растворения также соответственно выше у аминоорганических
растворов. |
|
|
Коэффициент массопередачи при |
абсорбции С 02 |
растворами |
МЭА в органических растворителях |
при одинаковых |
температуре |
ц степени карбонизации раствора на входе в абсорбер ниже, чем при абсорбции водными растворами МЭА, вследствие большей вязкости раствора. Однако в процессе абсорбции аминооргапический абсор бент нагревается больше (вследствие меньшей теплоемкости), чем
|
|
Таблица 7V-25. Парциальное Давление С02 над растворами МЭА в этиленгликоле (ЭП |
|
|
||||||||||||
|
|
|
N -нетилпирролидоне (N-МП) и тетрагидрофуриловом спирте (ТГФС) |
|
' |
|
|
|||||||||
|
|
__________________________ (в Па; 1 Па = |
7,5 •10-з мм рт. ст.) |
|
|
|
|
|
|
|||||||
°с |
|
|
|
|
|
Степень карбонизации, моль СОв/моль МЭА |
|
|
|
|
|
|||||
0,05 |
|
|
0,40 |
0,06 |
|
|
|
|
|
|
|
|
|
|
|
|
|
0 ,1 1 |
0,20 |
0 , 1 1 |
0,20 |
0,40 |
0,07 |
0 , 1 1 |
0 ,2 2 |
0,39 |
0,08 |
0,25 |
0,39 |
— |
|||
|
20% МЭА Н~ э г |
|
20% МЭА + |
ЭГ + 5% Н 20 |
20% М ЭА + Э Г + 13% Н 20 |
15% М ЭА+ЭГ+13,8 % IUO |
||||||||||
20 |
— |
— |
— |
82,6 |
— |
— |
— |
104 |
_ |
_ |
_ |
_ |
_ |
|
78,6 |
|
30 |
_ |
|
||||||||||||||
— |
— |
— |
279 |
— |
— |
— |
344 |
_ |
— |
_ |
172 |
_ |
145,5 |
|
||
40 |
— |
— |
45,3 1 8 2 2 |
— |
— |
45,3 |
910 |
_ |
_ |
45,3 |
503 |
_ |
73,4 |
373 |
|
|
50 |
— |
57,4 |
140 |
2390 |
— |
46.7 |
148 |
2260 |
_ |
32 |
1 1 2 |
1540 |
_ |
207 |
1005 |
|
60 |
24 |
98.7 |
383 |
6020 |
32 |
92,3 |
384 |
4370 |
32 |
70,6 |
325 |
3910 |
44.7 |
602 |
_ |
_ |
70 |
60 |
275 |
1 0 1 0 |
— |
81,3 |
243 |
995 |
— |
76 |
164.5 |
870 |
_ |
77,3 |
1430 |
||
75 |
82,7 |
— |
— |
— |
— |
— |
— |
— |
109 |
_ |
_ |
_ |
— |
_ |
|
|
80 |
154 |
665 |
2800 |
— |
197,5 |
564 |
2620 |
_ |
177 |
362 |
1820 |
_ |
167.5 |
_ |
_ |
_ |
90 |
353 |
1585 |
6640 |
— |
485 |
1310 |
— |
-- ' |
425 |
1083 |
|
— |
381 |
— |
— |
— |
°С |
0 ,12 |
0 ,2 1 |
0,3 |
0,44 |
0,06 |
0 ,1 1 |
0,23 |
0,35 |
0,04 |
0 ,12 |
0,24 |
0,42 |
0,08 |
0 ,2 1 |
0,35 |
0,44 |
|
20% МЭА + N-М П |
|
20% M 9A + N-MH + 5% Н 20 |
20%МЭА +N -M U +12.6 %Н20 |
20% М Э А + Т Г Ф С + |
|||||||||||
|
|
|
14,4% Н20 |
|
||||||||||||
20 |
— |
— |
_ |
_ |
.— |
— |
_ |
36 |
_ |
_ |
_ |
_ |
— |
— |
74,6 |
1830 |
25 |
— |
_ |
_ |
259 |
__ |
— |
_ |
_, |
_ |
_ |
_ |
_ |
--- |
— |
— |
2760 |
30 |
— |
— |
42,2 |
499 |
— |
— |
— |
92 |
— |
— |
— |
117,2 |
— |
29,4 |
227 |
5060 |
35 |
— |
— |
_ |
826 |
.— |
— |
— |
_ |
_ |
_ |
_ |
_ |
■-- |
— |
— |
— |
40 |
— |
34,7 |
139 |
1470 |
— |
— |
70,6 |
299 |
— |
— |
44 |
356 |
— |
84 |
714 |
— |
45 |
— |
— |
— |
2430 |
.— |
— |
_ |
_ |
_. |
_ |
_ |
_ |
--- |
— |
— |
— |
50 |
58,6 |
168 |
535 |
|
.— |
44 |
227 |
923 |
_ |
37,3 |
157,5 |
1055 |
36 |
241 |
2080 |
— |
60 |
213 |
583 |
1635 |
_ |
50.6 |
150 |
705 |
3070 |
32 |
106,6 |
440 |
2810 |
93.4 |
673 |
— |
— |
70 |
620 |
1810 |
— |
162.5 |
448 |
2 0 10 |
_ |
81,3 |
277 |
1270 |
|
261 |
1690 |
— |
— |
|
80 |
2090 |
— |
_ |
_ |
461 |
1325 |
— |
_ |
213 |
683 |
3230 |
2 |
— |
— |
— |
— |
90 |
|
— |
— |
— |
1230 |
3240 |
— |
— |
488 |
— |
— |
— |
|
|
|
|
водный раствор МЭА, поэтому вязкость такого абсорбента сни жается. Кроме того, оптимальная степень карбонизации a i регене рированного иеводного раствора МЭА меньше, чем a i водного рас
твора. |
В |
итоге, |
коэффициент |
массопередачи К а в абсорбере при |
|||||||||
очистке растворами МЭА в N-метилпирролидоне и в тетрагидрофу- |
|||||||||||||
риловом |
спирте |
|
при |
опти |
|
|
|
||||||
мальном |
режиме |
выше или |
|
|
|
||||||||
равен Ка для |
очистки |
вод |
|
|
|
||||||||
ным раствором |
|
МЭА. |
|
|
|
|
|
||||||
|
Процесс |
очистки |
раство |
|
|
|
|||||||
рами МЭА в разных раство |
|
|
|
||||||||||
рителях изучен в опытно-про |
|
|
|
||||||||||
мышленных |
условиях |
[198] |
|
|
|
||||||||
в абсорбере диаметром 300 мм |
|
|
|
||||||||||
и |
высотой слоя насадки (сед |
|
|
|
|||||||||
ла |
«Инталокс») |
|
4 м. |
Абсор |
|
|
|
||||||
бер работал при атмосферном |
|
|
|
||||||||||
давлении. |
Установка |
пред |
|
|
|
||||||||
ставляла |
собой |
|
полную |
мо |
|
|
|
||||||
дель простейшей |
технологи |
|
|
|
|||||||||
ческой |
схемы. |
|
|
|
|
|
|
|
|
|
|||
|
На рис. IV-71 |
показана |
|
|
|
||||||||
зависимость |
удельного |
рас |
|
|
|
||||||||
хода тепла на этой установке |
|
|
|
||||||||||
от степени карбонизации ре |
|
|
|
||||||||||
генерированного |
|
раствора |
|
|
|
||||||||
при расходах газа и раствора |
|
|
|
||||||||||
соответственно |
100 и |
1 м3/ч |
|
|
|
||||||||
(расход |
тепла |
рассчитан |
по |
|
|
|
|||||||
тепловому балансу). Как вид |
телях |
от температуры: |
|||||||||||
но из рис. IV-71, расход тепла |
|||||||||||||
при замене |
воды другим раз |
j — 20% МЭА + |
Н ,0; |
2 — 20% МЭА + JV -M 0 - |
|||||||||
тилшфролидон + |
12,6% |
н 20; 3 — 20% МЭА + |
|||||||||||
бавителем снижается в 1,5— |
+ ТГФС + 14,4% |
Н20; |
4 — 20% МЭА + ЭГ + |
1,8 |
раза |
при |
оптимальном |
+ 1,3% |
Н20; |
1 — концентрация |
СО* в растворе |
|
МЭА 0,08 моль/моль; 2 — то же, |
0,1 моль/моль; |
|||||||
режиме. |
Оптимальная вели |
3 — то |
же, |
0,11 моль/моль; |
4 — то же, |
|||
чина а 1 |
равна 0,05—0,1 (вме |
|
|
0,12 моль/моль. |
|
|||
|
|
|
|
|||||
сто |
0,23). |
|
|
|
|
|
|
|
|
Данные |
по |
степени извлечения |
С 02 |
различными |
растворами |
||
показаны на рис. IV-72. Из сопоставления рис. IV-71 и IV-72 сле |
||||||||
дует, что при оптимальных значениях ах |
степень извлечения невод |
ным раствором МЭА выше, чем водным, хотя при одинаковых зна
чениях ах |
наблюдается противоположная зависимость. |
В табл. IV-26 приведены основные технологические параметры |
|
процессов |
очистки растворами МЭА в различных разбавителях. |
Из таблицы |
видно, что из изученных растворителей только |
|
раствор МЭА в |
этиленгликоле (ЭГ) по всем показателям уступает |
|
водному раствору МЭА. Другие |
растворители — растворы МЭА |
|
в Г^метилпирролидоне (N-МП) и |
в тетрагидрофуриловом спирте |
Таблица IV-26. Оптимальные режимы очистки газов от СО> при работе на разных абсорбентах
(L = 1 мз/ч, 6?= 100 мз/ч, Ух— 19—21%) [198]
Р аств ор М ЭА
П ар ам етр ы
в в оде |
в N -М П |
в Т ГФ С |
в Э Г |
Концентрация |
|
|
|
|
||
МЭА, |
моль/л |
|
|
3,49 |
||
Н20, |
% |
|
% (об.) |
80 |
||
растворителя, |
|
|||||
Давление в регенераторе, |
|
|||||
Р per |
|
|
|
|
|
168- |
кПа |
|
|
|
|
||
кгс/см2 |
С0 2, % |
|
1,7 |
|||
Концентрация |
|
|
||||
в исходном |
газе |
|
20,4 |
|||
в очищенном газе у2 |
2,6 |
|||||
Температура раствора, |
°С |
|
||||
на входе в абсорбер |
23 |
|||||
на выходе из абсорбера |
39 |
|||||
Разность |
температур, °С |
|
||||
на горячем конце теп |
1 2 |
|||||
лообменника |
|
|
|
|||
на холодном конце |
те |
9 |
||||
плообменника |
|
|
||||
Температура, °С |
|
|
|
|||
низа регенератора |
|
115 |
||||
ПГС |
|
|
раствора |
99 |
||
насыщенного |
103 |
|||||
на входе |
в регенера |
|
||||
тор |
|
|
|
|
|
|
Концентрация С02, |
|
|
||||
моль/моль МЭА |
|
|
|
|||
в регенерированном |
0 ,2 1 |
|||||
растворе |
|
|
|
|
||
в насыщенном растворе |
0,423 |
|||||
Поглотительная способ |
16,8 |
|||||
ность, м3 С02/мЗ рас |
|
|||||
твора |
|
|
|
|
|
|
Степень |
извлечения |
С02 |
0,83 |
|||
в абсорбере ф |
|
|
|
|||
Флегмовое число в верхней |
0,89 |
|||||
части регенератора, мз/мз |
|
|||||
Расход тепла, |
МДж/м3 |
|
|
|||
(ккал/м3 С02) |
|
|
|
|||
на |
нагрев |
раствора |
2,24 (535) |
|||
7 н а г р |
?отд_ |
|
2,39 (570) |
|||
на |
отдувку |
|
||||
на |
десорбцию |
АН |
|
3,35 (800) |
||
общин д0бщ |
|
|
7,98 (1905) |
3,1 |
3,28 |
3,44 |
3 |
9 |
6 |
78 |
71 |
73 |
108 |
168 |
127,5 |
1 , 1 |
1,7 |
1.3 |
19,2 |
19,1 |
20 ,8 |
1,3 |
1,7 |
9,1 |
39 |
40 |
38 |
74 |
70 |
57 |
25 |
23 |
24 |
4 |
1 0 |
15 |
135 |
135 |
140 |
103 |
85 |
105 |
1 1 0 |
1 1 2 |
ИЗ |
0,07 |
0,08 |
0,143 |
0.348 |
0,286 |
0,331 |
19,0 |
16 |
14,5 |
0,93 |
0,91 |
0,56 |
0,13 |
0,29 |
0,04 |
0,544 (125) |
1,34 (320) |
3,1 (740) |
0,335 (80) |
0,754 (180) |
0,109 (26) |
4,48 (1070) |
3,25 (780) |
3.77 (900) |
5,34 (1275) |
5,38 (1286) |
6,97 (1666) |
(ТГФС) имеют лучшие по казатели, чем водный раствор. Так, некоторое уменьшение концентрации СО2 в насыщенном рас творе компенсируется воз можностью более глубо кой регенерации раствора (при минимальном расходе тепла). Флегмовое число при очистке аминооргани ческими растворами не превышает 0,3, поэтому расход тепла на отдувку весьма мал.
При очистке аминоор ганическими растворами целесообразно поддержи вать минимальное давле ние в регенераторе. Кон центрация воды в разба вителе может колебаться от 1 до 20% (минимальный расход тепла при содер жании 7—10% воды). Тер мохимическая устойчи вость аминоорганических растворов несколько ниже водных растворов МЭА. Наиболее устойчивы рас-
12
X w >
I
Рис. 1У-71. Зависимость удельного расхода тепла q при очистке от С 02 растворами МЭА (3,3 моль/л) в различных разбавителях от степени карбонизации регенерированного рас твора:
1 — в ода, 2 — N -м ети лп и рр оли дон |
+ 3 % воды ; 3 — |
|
тетр аги др оф ури ловы й сп и рт + 9 % |
воды; |
4 — эти лен |
гл и к ол ь + 6% воды |
[1 9 8 ]. |
|
Рис. IV-72. Зависимость степени из влечения С0 2 в абсорбере при очистке растворами МЭА в органических растворрхтелях от степени карбонизации ах регенерированного раствора (обо
значения см. рис. IV-71) [198].
творы МЭА в ТГФС и в некото рых других спиртах, в таких рас творах минимальна скорость кор розии. Очистку этих растворов целесообразно осуществлять филь трацией.
П РО Ц ЕСС «А М И ЗО Л »
Процесс «Амизол» [194] осно ван на абсорбции растворами ДЭА или МЭА в метаноле. Схема про цесса приведена на рис. IV-73. Абсорбент комплексно поглощает С 02, H 2S, меркаптаны, углеводо роды, влагу. Процесс абсорбции ведут при 35 °С, а регенерацию — при 80 °С. Это позволяет снизить
16 Заказ 1460 |
241 |
расход тепла по сравнению с известными ранее процессами и за
траты на теплообменную аппаратуру. |
|
|
|
|
|
|
||
¥ Недостаток |
процесса — унос большого |
количества паров мета |
||||||
нола, поэтому |
необходима промывка газа водой, однако расход |
|||||||
|
|
|
тепла на |
ректификацию про |
||||
|
|
|
мывных вод невелик, а потери |
|||||
|
|
|
метанола ничтожны. |
|
||||
|
|
|
Процесс |
изучен при дав |
||||
|
|
|
лении 2,94 |
МПа (30 кгс/см2) |
||||
|
|
|
и 20 °С. При этом достигнута |
|||||
|
|
|
очистка |
до |
10 |
ррм С 02, |
||
|
|
|
0,1 ррм GOS |
и 0,3 ррм H 2S. |
||||
|
|
|
Побочные реакции этанол- |
|||||
|
|
|
аминов с СО2 и COS в ме- |
|||||
|
|
|
танольном растворе идут зна |
|||||
|
|
|
чительно |
медленнее, |
чем в |
|||
|
|
|
водных растворах |
(скорость |
||||
Рис. IV-73. Схема процесса «Амизол»: |
их примерно в 10 |
раз |
ниже, |
|||||
1 — а бсор бер ; 2 — р еген ер атор ; з — к олон н а р ек |
чем |
при |
МЭА-очистке, и в |
|||||
тиф икации м етан ола; |
4 — |
кипяти льн и к и ; 5 — |
100 |
раз |
ниже, |
чем |
при' |
|
теплообм енник; |
6 — |
холоди л ьн и к и . |
ДЭА-очистке). Концентрация |
|||||
|
|
|
||||||
|
|
|
примесей |
в |
растворе |
посте |
пенно возрастает, и через 1—2 года эксплуатации следует про водить разгонку раствора. На рис. IV-73 показана схема исполь зования тепла паров метанола после ректификации промывных вод.
Рис. IV-74. Использование процесса «Амизол» при комбинированной очистке природного и конвертированного газов:
1 — стади я пром ы вки раствором А м и зол ; 2 — стади я к он верси и С Н 4 и вы сок отем п ературн ой к он верси и СО \ 3 — стади я н и зк отем п ер атур н ой к он верси и С О ; 4 — стади я общ ей р еген ер а ции; 5 — стади я д р о ссел и р о в а н и я .
Это тепло используется при регенерации раствора и его разгонке. Пары МЭА и метанола из разгонного куба направляются в регене ратор.
Коррозия углеродистой стали практически отсутствует (менее 0,1 мм в год).
Процесс «Амизол» можно использовать в производстве аммиака для очистки природного газа от сернистых соединений и конверти рованного газа от С 02 (рис. IV-74). В такой схеме потоки абсорбента после очистки природного и конвертированного газов регенериру ются в одном регенераторе.
ПРОЦЕСС «СУЛЬФИНОЛ»
Первые сведения об этом процессе были опубликованы в 1963 г., позднее появились сообщения [187] о свойствах растворителя и испы таниях процесса в опытно-промышленном масштабе и в заводских условиях. В 1965 г. в США работали три промышленные установки по очистке синтез-газа после паровой конверсии метана и высоко температурной конверсии углеводородов. Однако опубликованные результаты испытаний относятся в первую очередь к очистке при родного газа от сероводорода и двуокиси углерода.
В процессе «Сульфинол» в качестве абсорбента используется раствор алканоламина в двуокиси тетрагидротиофена, или циклотетраметиленсульфоне (сульфолане).
н , < г |
^ с н 2 |
\/
S
оо
Сульфолан получают взаимодействием бутадиена с двуокисью серы и последующим гидрированием сульфолена в сульфолан [188, 232].
Температура плавления сульфолана 8-—10 °С, температура кипе ния 285—288 °С (747 мм рт. ст.), плотность dj8,2 = 1,2723, показа
тель преломления JID ,а = 1,4833. Это химически устойчивое высоко полярное соединение (дипольный момент р = 4,58) является хорошим растворителем многих органических веществ, в частности
ароматических |
соединений и полимеров. |
В качестве |
другого компонента применяют моноэтаноламин |
или диэтаноламин, однако наилучшим является диизопропаноламин. Примерный состав абсорбента: 30% диэтаноламина, 64% сульфолана, 6% воды [191].
Даже при небольшом парциальном давлении двуокиси углерода, равном 0,245 МПа (2,5 кгс/см2), в условиях опытно-промышленной установки [187] поглотительная способность абсорбента составляла 33,5 м3/м8. В тех же условиях водный раствор моноэтаноламина поглощал 22—28 м3/м3 С 02.
При увеличении давления различие становится более сущест венным. Так, при суммарном давлении С 02 и H 2S, равном 1,27 МПа
(13 кгс/см2), растворимость их в водном моноэтаноламине составляла 32 м3/м3, а в растворителе процесса «Сульфинол» 70 м3/м3. При этом остаточная концентрация двуокиси углерода была равна 100— 1000 см3/м3 очищенного газа.
Преимуществом абсорбента является возможность одновремен ной тонкой очистки от меркаптанов и сероуглерода. Степень извле чения меркаптана [187] 95%, причем наличие даже таких примесей, как сероокись углерода, не приводит к химическим потерям суль фолана.
Кинетика процесса более благоприятна, чем кинетика моноэтаноламиновой очистки. Так, на опытно-промышленной установке была достигнута концентрация С 02 в насыщенном абсорбенте^равная 80% от равновесной [187]. На выходе из абсорбера концентрация при месей в газе была также близка к равновесной. В табл. IV-27 при ведены сравнительные данные [187] о работе абсорбера диаметром 1,2 м на водном моноэтаноламиновом растворе и сульфинольном растворителе. Абсорбер имел 23 клапанные тарелки, расстояние
между которыми 600 мм. Газ содержал 1,6% |
H 2S и 6,9% |
С 02, очи |
|
стки вели при 6,57 МПа (67 кгс/см2). |
|
|
|
Таблица IV-27, Показатели работы абсорбера при МЭА-очистке |
|||
и в процессе |
«Сульфинол» |
|
|
-V. |
Моноэтанол- |
Процесс «Сульфинол» |
|
|
|
||
Показатели |
аминовая |
1-й режим |
2-й режим |
|
очистка |
||
Расход, м3/ч |
24 700 |
35 800 |
35 800 |
газа |
|||
жидкости |
64,2 |
71,5 |
76 |
Концентрация кислых газов в насы |
33,5 |
45 |
42,5 |
щенном растворе, мз/мз |
|
130 |
|
Содержание H2S в газе на выходе, |
< 2 0 0 |
< 2 0 |
|
см3 /м3 |
|
|
|
Как следует из таблицы, замена моноэтаноламиповой очистки способом «Сульфинол» позволяет увеличить почти в 1,5 раза на грузку по газу. При этом для обеспечения нормальной работы реге нератора его диаметр пришлось увеличить в 1,5 раза. Регенератор имел 18 клапанных тарелок, остальное оборудование — теплооб менники, холодильники, хранилище, узел приготовления раствора— могут быть такими же, как и при моноэтаноламиновой очистке.
По данным [188], регенерацию ведут при 65 °С. Общий расход пара при очистке методом «Сульфинол» снижается в 2—2,5 раза по сравнению с моноэтаноламиновой очисткой и на 10% по сравнению с очисткой горячими растворами поташа. Это объясняется умень шением количества отдувочного пара и значительным снижением расхода пара на покрытие недорекуперации в теплообменниках, так
как теплоемкость смешанного растворителя вдвое ниже теплоем кости водных растворов МЭА. Кроме того, уменьшается удельное
количество циркулирующего |
абсорбента. |
При сульфинольной очистке абсорбер и регенератор могут быть |
|
заполнены обычной насадкой, |
используются и ситчатые тарелки. |
/У Смешанный растворитель |
в процессе «Сульфинол» растворяет |
компоненты очищаемого газа лучше, чем водный раствор МЭА, поэтому в зависимости от состава газа и требований к чистоте дву окиси углерода возможна промежуточная отдувка примесей из насыщенного раствора путем снижения давления в емкости, устано вленной между абсорбером и теплообменником. В остальном тех нологическая схема не отличается от схемы моноэтаноламиповой очистки.
U Капитальные затраты в процессе |
«Сульфинол» на 30% ниже, |
чем при моноэтаноламиповой очистке, |
и на 10% меньше, чем при |
очистке горячим раствором поташа [190, 191]. Кроме того, при суль финольной очистке коррозия снижается в несколько раз по срав
нению |
с коррозией под действием раствора МЭА. |
В |
условиях очистки растворитель химически и термически |
стабилен, деградация сульфолана не наблюдается. Скорость дегра дации диизопропаноламина при установившемся режиме сульфи нольной очистки (через 700 ч работы) в 4 раза ниже скорости дегра дации амина при водной МЭА-очистке, поэтому поверхность тепло обмена в меньшей степени загрязняется продуктами деградации. Преимуществом абсорбента является также отсутствие вспенивания. Несмотря на то, что давление паров смешанного растворителя мало, отходящие газовые потоки рекомендуется, как и при моноэтаноламиновой очистке, промывать водой.
В качестве активного компонента в процессе «Сульфинол» может применяться и МЭА [200], несмотря на то, что раствор МЭА в суль фолане расслаивается. Предложено [200] заменит* диизопропаноламин (ДИПА) моноизопропаноламином (МИПА). Скорость абсорбции раствором МИПА, как и растворами всякого первичного алканоламина, в несколько раз выше скорости абсорбции раствором ДИПА. Кроме того, вязкость раствора МИПА меньше, а теплопроводность— выше. Данные промышленной эксплуатации процесса «Сульфинол» [181, 201] показывают, что расход тепла на очистку составляет 3,56—7,13 МДж/м3 (850—1700 ккал/м3 С 02). Концентрация общей серы в очищенном газе может быть снижена до 23 мг/м3 и менее, двуокиси углерода (при необходимости) — до 5 см3/м3.
В процессе эксплуатации установок очистки «Сульфинол» воз никли также некоторые трудности [201]. Так, при сбросе давления в линии насыщенного раствора после абсорбера начинается быстрая десорбция газа. В результате движения двухфазного потока про исходит вибрация трубопроводов, которая может привести к их
разрушению (если не предусмотрены специальные |
меры) [186]. |
Кроме того, возможно вспенивание раствора, для |
предупрежде |
ния которого необходима добавка антивспенивателя. |
Недостатком |
процесса «Сульфинол», препятствующим его применению в производ стве аммиака, является загрязнение газа серой и отравление катали затора метанирования. Для защиты катализатора после абсорбера предложено устанавливать адсорбер с активированным углем [202].
7.ОЧИСТКА РАСТВОРАМИ-КАРБОНАТОВ
Внастоящее время процесс абсорбции С 02 и H 2S растворами карбонатов при обычной температуре почти не применяется вслед ствие относительно малой абсорбционной емкости этих растворов и, главное, малой скорости химической реакции, сопровождающей процесс
Na2C03 + C02 + H20 2NaHC03
В литературе [5] приведены данные о растворимости двуокиси углерода в растворах карбонатов. Давление С 02 над растворами {в мм рт. ст.) может быть рассчитано по эмпирическому уравнению *
Ах2лп>29. |
|
|
Р С0 2- К г (\ —х) (В — t) |
|
|
где К г — коэффициент Генри для системы С 02 — Н 20; |
t — температура, СС; |
|
х — степень превращения в бикарбонат; А = 76, В = |
185 — для растворов |
|
соды и соответственно 25 и 150 для растворов поташа; N — концентрация кар |
||
боната, г-экв/л: |
|
|
Уравнение справедливо для 0,5—2 н. растворов соды при |
18— |
|
65 °С и для 1—2 н. растворов поташа при 0—40 °С. |
|
|
Скорость абсорбции С 02 растворами солей |
практически |
пол |
ностью лимитируется скоростью медленно протекающей реакции в жидкой фазе
С02 + 0 Н -= Н С 0 ;
Скорость абсорбции не зависит от скорости газа и примерно пропорциональна удерживающей способности абсорбера по Жид кости [203].
Коэффициент массопередачи при абсорбции двуокиси углерода содой возрастает при увеличении скорости жидкости, pH раствора, температуры и концентрации ионов натрия (до 2н.). Скорость Жид кости входит в уравнение массопередачи в степени от 0,28 до 0,84 в зависимости от различных условий, а температура жидкости_ в степени 0,6. Коэффициент массопередачи уменьшается при увели чении вязкости жидкости и концентрации бикарбоната, а тацЖе при повышении концентрации ионов натрия более 2 н.
Скорость абсорбции не зависит |
от размера |
колец |
иасацки |
и концентрации С 02 в газовой фазе. Коэффициент |
полезного Дей |
||
ствия барботажной тарелки [204] равен 0,07. Значения |
коэффи |
||
циента массопередачи колеблются в |
пределах 0,63 • 10“ 5 — lJBST х |
* Если P CQ2 измеряется в Па, дробь после знака равенства умножают
на коэффициент 133,3.
X 10"5 кмоль/(м3-ч-Па) [0,64—1,92 кмоль/(м3-ч-атм)]. Коэффи циенты массопередачи для растворов поташа примерно на 30— 40% выше, чем для растворов соды [205].
Кинетика десорбции С 02 из поташных растворов изучена меньше.
Известно, что коэффициент массопередачи при десорбции в |
2,4 |
раза выше, чем при абсорбции [204]. По некоторым данным, |
этот |
коэффициент не зависит от скорости пара и уменьшается при увели чении концентрации соды. Основное сопротивление десорбции сосре доточено в жидкой фазе и лимитируется скоростью разложения бикарбоната. На скорость десорбции также оказывает сильное влия ние скорость образования пузырьков в жидкой фазе, поэтому для десорбции предпочтительны тарельчатые колонны.
Методы очистки относительно дешевыми растворами карбонатов имеют серьезный недостаток, обусловленный малой растворимостью солей (особенно бикарбонатов) в воде при .обычных температурах. Кроме того, скорость взаимодействия двуокиси углерода с карбона тами весьма мала, что приводит к увеличению циркуляции раствора, возрастанию габаритов аппаратуры и расхода пара на регенерацию* содовых и поташных растворов.
'ОЧИСТКА ГОРЯЧИМИ РАСТВОРАМИ ПОТАША
Внастоящее время широкое распространение получила очистка газа от С 02 горячими растворами карбонатов, активированными различными добавками [206—232].
Методы очистки газов горячим раствором поташа [206] основаны прежде всего на возрастании растворимости солей в воде при увели чении температуры, поэтому для очистки могут быть использованы более концентрированные растворы) Поскольку растворимость солей калия в воде выше растворимости солей натрия, для абсорбции применяют растворы поташа.
Важным преимуществом процесса абсорбции при высоких тем пературах является значительное увеличение скорости гидратации двуокиси углерода и, следовательно, скорости абсорбции в целом. Эти физико-химические особенности позволили осуществить такой процесс очистки, в котором абсорбция и регенерация проводятся почти при одинаковых температурах, причем абсорбция протекает при повышенном давлении, а регенерация — при давлении, близком К' атмосферному.
Теплота растворения С 02 в поташных растворах примерно в 2,5 раза меньше теплоты растворения в водном растворе моноэтаноламина и равна [104] 6,04• 102 кДж/кг (144 ккал/кг СО2). Так как теплота растворения определяет скорость снижения растворимости
газа при увеличении температуры, то растворимость С 02 в раство рах К 2С03 в этих условиях изменяется медленнее растворимости в моноэтаноламине. Например, по данным Бокарда и Мэйлэрда [207], при давлении 0,71 МПа (7 кгс/см2) и повышении температуры от 65,6 до 132,2 °С растворимость двуокиси углерода в 30%-ном растворе К 2С03 уменьшается лишь в 1,6 раза. Такое снижение
растворимости СО2 компенсируется увеличением концентрации
к2со3.
Растворимость двуокиси углерода в горячем поташе в большей степени зависит от давления, чем в растворах моноэтаноламина, поэтому при снижении давления двуокись углерода частично десор бируется. ___
^ Наконец, в производстве аммиака и в других процессах на очи стку поступает горячий газ после конверсии, что также делает вы-
|
|
|
|
|
|
|
годным процесс |
абсорбции при высо |
||||||||
|
|
|
|
|
|
|
кой |
температуре. (Проведение |
абсорб |
|||||||
|
|
|
|
|
|
|
ции при повышенных температурах по |
|||||||||
|
|
|
|
|
|
|
зволило резко снизить затраты на тепло |
|||||||||
|
|
|
|
|
|
|
обменную |
аппаратуру, а также умень |
||||||||
|
|
|
|
|
|
|
шить расход |
тепла.Г |
|
|
||||||
|
|
|
|
|
|
|
|
Наиболее |
подробные сведения о рас |
|||||||
|
|
|
|
|
|
|
творимости |
|
солей |
в системе К 2С03— |
||||||
|
|
|
|
|
|
|
КНС03—Н 20 приведены в работах [207, |
|||||||||
|
|
|
|
|
|
|
208]. На рис. IV-75 |
показана раствори |
||||||||
|
|
|
|
|
|
|
мость в системе |
K 2C03—KHC03—II20 |
||||||||
|
|
Температура?С |
при |
различной |
степени |
превращения |
||||||||||
|
|
карбоната |
в |
бикарбонат |
[15]. |
|
||||||||||
Рис. IV-75. Условия |
выпа |
|
||||||||||||||
] |
Температура раствора в абсорбере не |
|||||||||||||||
дения |
осадка |
|
в |
растворах |
1должна превышать температуру кипения |
|||||||||||
|
К 2С03-К Н С 0 3—Н20: |
при атмосферном давлении. Максималь |
||||||||||||||
1 — кон ц ен трац и я |
солей к а л и я (в |
|||||||||||||||
ная концентрация поташа должна быть |
||||||||||||||||
пересчете н а K 2COs) |
25%; |
2 — то |
||||||||||||||
ж е, |
30%; з — то |
ж е , |
35%; 4 — то |
такой, чтобы при степени превращения |
||||||||||||
ж е , |
40%; 5 — то |
ж е , |
45%; 6 — то |
|||||||||||||
|
<е, |
50 %; 7 — то |
ж е, 60 %. |
карбоната |
в |
бикарбонат, |
равной 80— |
|||||||||
|
|
|
|
|
|
|
90%, |
осадок не выпадал. Из приведен |
||||||||
ных данных следует, |
что |
предельная концентрация поташа в рабо |
||||||||||||||
чем растворе должна быть не выше 40%. |
|
|
|
|
|
|||||||||||
|
Опубликованы данные |
[15, |
207] по |
растворимости С 02 |
в 20— |
40%-ных растворах поташа при 65—132,2 °С и давлении от 1,013 кПа до 7,1 -102 кПа (0,01—7 кгс/см2). Изучена [208] также растворимость СО2 при температурах до 170 °С. В тех же работах приведены дан ные, необходимые для расчета процесса (давление насыщенных паров
воды, плотность, вязкость, |
теплоемкость). |
f Для абсорбции горячим |
раствором поташа и его регенерации |
могут быть использованы аппараты как с насадкой, так и с ситчатыми тарелками. ‘
Принципиальная технологическая схема простейшего варианта поташной очистки от двуокиси углерода показана на рис. IV-76, а. Парогазовая смесь после конверсии окиси углерода охлаждается водой в скруббере-конденсаторе до 107—110 °С (предельная темпе ратура устанавливается в соответствии с балансом воды в цикле очистки и тепловым балансом абсорбера). Газ, насыщенный водя ными парами, поступает на чабсорбцию. Раствор поташа подается в абсорбер при температуре около 107 °С и нагревается в нижней его части до 116 °С за счет теплоты абсорбции.
Концентрация поташа обычно составляет не 40, а 30% (иногда до 25%). Это объясняется тем, что при работе с насыщенными (по КНС03) растворами в случае отклонения от нормального технологи-
L A |
А |
|
2*
лI
1 |
f |
|
Рис. 1У-76. Принципиальные схемы |
очистки газа горячими растворами поташа: |
а — однопоточная схем а (гр у б ая очистка); |
б — схем а с двум я потокам и раствора н а абсорб |
цию (разли чн ы е тем пературы потоков); в — схем а с двум я потокам и регенери рованн ого рас твора (разли чн ы е тем пературы и степени регенераци и п отоков р аствора, подаваем ого н а аб сорбцию ); г — схем а с трем я потокам и регенери рованн ого р аств о р а; 1 — абсорбер; 2 — реге н ератор; 3 — насосы ; 4 — холоди льн и ки ; 5 дроссель-венти ли .
ческого режима возможна забивка трубопроводов солями, эрозия насосов и др.
Насыщенный абсорбент без подогрева дросселируется в регене ратор, где при снижении давления до 1,12-102—1,67 • 102 кПа(1,14— 1,7 кгс/см2) и отдувке водяным паром происходит десорбция дву окиси углерода. В процессе десорбции раствор может даже несколькоохлаждаться. Затем его вновь подают на абсорбцию. Таким образом, при очистке горячим раствором поташа капитальные затраты сни жаются за счет отсутствия теплообменников.
Максимальная поглотительная способность 40%-ного- раствора поташа при полном переходе карбоната в бикарбонат равна 90 м3/м3. Практически вследствие использования поглотительной способности карбоната лишь на 70—80% и неполной регенерации она составляет 28—35 м3/м3 (может колебаться от 20 до 50 м3/м3).
Приведенная на рис. IV-76, а схема процесса позволяет очистить газ до концентрации 0,5—0,6% С 02. Более тонкая очистка (до 0,1— 0,2% C 02J может быть достигнута при использовании схемы с раз деленными потоками (рис. IV-76, б — г) [210, 211]. Часть раствора (см. рис. IV-76, б), примерно г/3, охлаждается на 20—30 °С для сни жения равновесного давления С 02 над раствором и подается на оро шение в верхнюю часть абсорбера. Такая схема позволяет снизить расход пара на регенерацию при тонкой очистке от С 02. Кроме того, при тонкой очистке газа регенерированный раствор отбирают из разных точек регенератора. При этом более 75% раствора от водят из средней части аппарата и подают в среднюю часть абсор бера; остальной раствор регенерируется полностью и после охла ждения подается в верхнюю часть абсорбера (см. рис. IV-76, в). Наиболее совершенна трехпоточная схема (см. рис. IV-76, г).
Более экономична, по-видимому, грубая одноступенчатая поташ ная очистка газа с последующей тонкой очисткой раствором моно этаноламина. Содержание С 02 в газе снижается при очистке рас твором поташа в двух скрубберах до 2%, затем после абсорбции 18—20%-ным раствором МЭА до 0,1% С 02 и 6 см3/м3 H 2S.
Из изложенного выше следует, что процесс очистки газа от С 02 торячим раствором поташа имеет ряд положительных особенностей, позволяющих существенно снизить расход тепла. Например, при моноэтаноламиновой очистке примерно 40—60% тепла расходуется на подогрев раствора вследствие недорекуперации в теплооб менниках. При очистке горячим раствором поташа эта статья рас хода в значительной мере (при грубой очистке — полностью) отпадает.
Кроме того, при моноэтаноламиновой очистке 25—30% тепла расходуется на разложение соединений моноэтаноламина с дву окисью углерода. При поташной очистке, как указано выше, эта величина уменьшается в 2,5 раза, поэтому пар расходуется в основ ном лишь на отдувку С 02 в десорбере, а также на покрытие тепло вых потерь в окружающую среду.
В результате расход тепла при поташной очистке составляет
около 5,45 |
МДж/м3 (1300 ккал/м3 С 02), |
т. е. примерно в два раза |
|||
ни*ке, чем при стандартной (см. рис. IV-31) схеме МЭА-очистки, и |
|||||
примерно равен расходу тепла в усовершенствованном |
процессе |
||||
МЭА-ГИАП (см. табл. IV-34). |
|
|
|
|
|
Изучена |
зависимость расхода |
пара |
от |
циркуляции |
раствора |
и парциального давления С 02 |
в газе |
по |
однопотонной схеме |
и по схеме с разделенными потоками раствора. Вначале, до давле ния С 02 3—4 кгс/см2; расход пара резко снижается, т. е. при увели чении парциального давления С 02 в конвертированном газе умень
шается количество пара, расходуемого на десорбцию. Дальнейшее увеличение Рсо2 не приводит к снижению расхода пара.
Минимальное количество пара, которое необходимо подавать в десорбер для отдувки двуокиси углерода (без учета расхода на нагревание, химическую реакцию и тепловые потери), может ©цггь рассчитано, как и при моноэтаноламиновой очистке, по уравнениям (IV,44) и (IV,48).
Кроме экономии пара, очистка горячим раствором поташа имеет и другие преимущества. Процессы абсорбционной очистки обычно связаны с необходимостью охлаждения конвертированного газа, который в дальнейшем вновь должен нагреваться (например, при последующем метанировании), поэтому в случае очистки поташным раствором уменьшается расход воды на охлаждение конвертирован ного газа, а также частично отпадает ее расход на охлаждение рас творителя. Кроме того, снижаются затраты на абсорбент (по сравнению с моноэтаноламиновой очисткой). Капитальные затраты снижаются главным образом за счет уменьшения поверхности теплообменной аппаратуры.
Результаты проведенного [211—213] технико-экономического анализа показали, что преимущество поташной очистки воз растает при увеличении Pcot-
Процесс горячей поташной очистки имеет также серьезные не достатки. Основной из них — сильная коррозия оборудования. В качестве ингибитора коррозии применяют бихромат калия [212], добавляемый в количестве 3 г/л. При наличии в газе сероводорода расход ингибитора значительно возрастает вследствие взаимодей ствия с ним сероводорода. Таким образом, несмотря на принципиаль ную возможность одновременной очистки газа от сероводорода и двуокиси углерода, практически процесс применим только для отмывки С 02. Большие трудности вызывает также эрозия оборудо вания (особенно насосов) при пересыщении раствора вследствие выпадения солей железа и др. Для борьбы с эрозией раствор филь труют, а задвижки промывают конденсатом, присоединяя его затем к раствору.
Работа насосов может осложняться кавитацией, возникающей при неудачной конструкции машип или понижении давления на вса сывающей линии. Это также приводит к эрозионно-коррозионному разрушению чугунных кожухов, вращающихся частей. Поэтому вращающиеся части, а также клапаны и трубопроводы для насы щенного раствора рекомендуется изготовлять из нержавеющей хромоникельмолибденовой стали [209, 212].
ОЧИСТКА ГАЗА ГОРЯЧИМИ РАСТВОРАМИ КАРБОНАТА КАЛИЯ, АКТИВИРОВАННЫМИ ДИЭТАНОЛАМИНОМ
Последние годы широкое распространение получила очистка газа растворами горячего поташа, в которые в качестве активач^ра добавляют диэтаноламин (ДЭА). К таким процессам относятся
«Бенфилд», «Карсол». В процессе «Карсол» абсорбентом является 25—28%-ный раствор поташа, содержание ДЭА в нем составляет около 1,8%. Кроме того, в раствор добавляют ингибитор коррозии — пятлокись ванадия (0,4%) и антивспениватель (различные сили
коновые масла). |
|
|
|
|
•— |
|
|
|
|
|
|
|
|
|||||
|
Технологическая схема процесса «Карсол» в агрегате мощностью |
|||||||||||||||||
1360 т |
NH3 в сутки приведена |
на рис. IV-77. |
Абсорбция осущест |
|||||||||||||||
|
|
|
|
|
|
|
|
|
|
|
вляется |
по |
двухпоточыой |
|||||
|
|
|
|
|
|
|
|
|
|
|
схеме. Большая часть (80%) |
|||||||
|
|
|
|
|
|
|
|
|
|
|
раствора |
(грубо |
регенери |
|||||
|
|
|
|
|
|
|
|
|
|
|
рованный раствор) подает |
|||||||
|
|
|
|
|
|
|
|
|
|
|
ся в среднюю часть абсор |
|||||||
|
|
|
|
|
|
|
|
|
|
|
бера при 100—103 °С, мень |
|||||||
|
|
|
|
|
|
|
|
|
|
|
шая часть раствора — при |
|||||||
|
|
|
|
|
|
|
|
|
|
|
65—70 °С в верхнюю часть |
|||||||
|
|
|
|
|
|
|
|
|
|
|
абсорбера. |
Это |
позволяет |
|||||
|
|
|
|
|
|
|
|
|
|
|
достичь содержания в газе |
|||||||
|
|
|
|
|
|
|
|
|
|
|
до 0,1—0,15% С 02 (иногда |
|||||||
|
|
|
|
|
|
|
|
|
|
|
до 0,05-0,08% ). |
|
||||||
|
|
|
|
|
|
|
|
|
|
|
Абсорбцию ведут в на |
|||||||
|
|
|
|
|
|
|
|
|
|
|
садочных |
абсорберах (ке |
||||||
|
|
|
|
|
|
|
|
|
|
|
рамические |
седла |
«Инта- |
|||||
|
|
|
|
|
|
|
|
|
|
|
локс»). |
Насыщенный рас |
||||||
|
|
|
|
|
|
|
|
|
|
|
твор при 106—110 °С вна |
|||||||
|
|
|
|
|
|
|
|
|
|
|
чале поступает в турбины, |
|||||||
Рис. IV-77. Технологическая схема процесса |
затем |
направляется в ре |
||||||||||||||||
генераторы. |
|
Регенерацию |
||||||||||||||||
очистки |
газа |
горячим |
раствором |
К 2С 03, |
ведут |
по |
схеме с разделе |
|||||||||||
|
|
активированным |
ДЭА: |
|
|
|
||||||||||||
1 — абсорбер; |
2 |
— сепаратор; |
з |
— гидравлические |
нием |
потоков |
регенериро |
|||||||||||
турбины; 4 — регенераторы; 5, 1 0 |
— воздушные хо |
ванного раствора. |
Высота |
|||||||||||||||
лодильники; 6 |
— газовый кипятильник; |
7 — паро |
абсорберов около 58 м, вы |
|||||||||||||||
вой |
кипятильник; |
8 — теплообменник; |
9, 1 1 |
— |
||||||||||||||
|
|
|
|
|
фильтры. |
|
|
|
|
|
сота |
регенераторов |
65 м. |
|||||
прерывная фильтрация |
|
|
|
|
|
В схеме предусмотрена не |
||||||||||||
раствора (около 2% от общего |
количества) |
|||||||||||||||||
на |
активированном угле. |
|
|
|
|
|
|
|
|
|
|
|
||||||
|
Процесс «Бенфилд» отличается от процесса «Карсол» в основном |
|||||||||||||||||
более высокой концентрацией |
К 2С03 и ДЭА. Преимуществом про |
|||||||||||||||||
цессов |
«Карсол» и «Бенфилд» является относительно низкий расход |
|||||||||||||||||
тепла |
[около |
5,45 МДж/м3 (1300 ккал/м3 С 02) |
|
без |
учета |
тепла |
||||||||||||
горячего |
конвертированного |
газа, |
поступающего |
|
в |
абсорбер], |
||||||||||||
а также малые затраты на теплообменные поверхности |
вследствие |
|||||||||||||||||
близости температур абсорбции и регенерации. |
|
|
|
|
|
|
||||||||||||
|
Однако |
этот метод |
имеет ряд |
недостатков. Так, |
при |
сравнении |
с процессом МЭА-ГИАП установлено, что расход тепла в усовершен ствованном процессе МЭА-очистки несколько ниже, чем в процессе «Карсол», и существенно (почти в 2 раза) снижается циркуляция раствора. Благодаря этому, а также вследствие уменьшения скорости абсорбции габариты абсорберов и регенераторов в процессе «Карсол»
значительно больше, чем при МЭА-очистке; выше также расход электроэнергии и ниже степень очистки, что приводит к потерям водорода на стадии метанирования (4 моля водорода на 1 моль С 02)
ис продувочными газами на стадии синтеза аммиака. Определенные трудности вызывает пуск агрегатов в зимнее
время (возможность кристаллизации бикарбоната калия), корро зия, выщелачивание керамической насадки. В связи с опас ностью коррозии в горячем поташном растворе не допускается концентрация ионов С1“ более 15 мг/л, поэтому для приготов ления раствора может быть использован только поташ марки «хч» или «чда». Необходима тщательная промывка системы перед пу ском.
В литературе опубликованы многочисленные данные, необхо димые для расчета процесса [207, 208, 214]. При выборе темпера турного режима большую роль играют условия выпадения твердой
фазы. С |
достаточной степенью точности их |
можно определить |
|||
по графикам на рис. IV-75, однако при наличии в растворе ДЭА и |
|||||
V 2Orj температура |
выпадения |
осадка |
несколько |
повышается. |
|
Растворимость С 02 в поташ-диэтаноламиновых растворах, а также |
|||||
давление |
паров |
воды над |
этими |
растворами изучены [214] |
при температуре от 60 до 120 °С, давлении до 0,811 МПа (8ткгс/см2), концентрациях К 2С03 от 20 до 30% и ДЭА от 1,5 до 10%. В табл. IV-28 приведено [214] давление паров воды и С 02 над растворами, содер жащими 25% К 2С03 и 1,5% ДЭА.
Исследование влияния концентрации К 2С03 на поглотительную способность раствора при 100 °С и концентрации ДЭА, равной 5% (0,5 моль/л), показало, что растворимость С 02 (в моль/моль К 2С03 +
+ ДЭА) |
несколько уменьшается |
при увеличении концентрации |
|
К 2С03 |
(но |
увеличивается, если |
ее измерять в м3/м3). |
На рис. |
IV-78 показана зависимость растворимости С 02 в амино- |
поташных растворах от содержания ДЭА. Зависимость давления паров воды над растворами поташа и ДЭА от степени карбонизации
раствора показана н^ |
рис. IV-79; данные |
по растворимости С 02 |
|
в 30%-ных растворах |
К 2С03 приведены на |
рис. lV-80. |
|
Ниже, в табл. IV-29, приведены данные по плотности амино |
|||
поташных растворов при различных температурах [214]. |
|||
Исследование скорости |
абсорбции С 02 |
горячими растворами |
|
поташа с добавками ДЭА |
[214] в аппарате |
с мешалкой показало, |
что ускоряющее действие ДЭА, как правило, невелико. Так, при содержании около 4% ДЭА коэффициент ускорения при малых
степенях карбонизации не превышает 1,5. Однако он |
возрастает |
до 2 при высоких степенях насыщения (т. е. в условиях |
низа абсор |
бера), когда абсолютное значение коэффициента массопередачи мало. В условиях верха абсорбера, очевидно, главную роль играет сни
жение |
парциального давления С 02 над раствором при добавлении |
||
ДЭА, |
т. е. возможность более тонкой очистки. |
|
|
В |
табл. IV-30 приведены теплоты растворения |
[214] С 02 |
в по |
ташных растворах (25% К 2С03), активированных |
ДЭА. |
ч |
Рис. IV-78. Зависимость растворимости С 02 в растворах К 2С 03 + ДЭА - f Н20 от концентрации ДЭА при 60 °С (а) и 120 °С (б) и различном давлении С02:
1 — при 1,013* 10® Па; (1 атм); 2 *- при 2,026-10» Па (2 атм); 3 — при 3,093- ЮЧПа (3 атм); 4 — при 5,065*10® Па (5 атм); 5 — при 6,078-10® Па (6 атм). Концентрация КаС03 в растворе
25%.
Степень карбонизации, моль 0 0 % /моль К 2 С О 3 +ДЗЛ |
|
|
Рис. IV-79. Зависимость давления паров воды над растворами К 2С 03 + |
ДЭА-f- |
|
|
+ Н20 от степени карбонизации раствора; |
|
в — 25% К аСОв + |
10% ДЭА; б — 20% К.СО. + 10% ДЭА; 1 — 60 °С; 2 — 80 °С; 3— 100 °С* |
|
4 |
— 120 °С (пунктирная линия — расчет по вакону Рауля). |
* |
Таблица IV -2 8 . Давление двуокиси углерода и паров воды над растворами, содержащими 25% К 2С03 и 1,5% ДЭА [214]
|
|
(105 Па = |
1,02 кгс/см2) |
|
|
Концентрация |
|
рсо*. |
Концентрация |
•Рн.О. |
рсо *• |
СО* в рас |
Р Н*0» |
СО* в рас |
|||
творе, см* (при |
Па- Ю-* |
Па- 10-* |
творе, см3 |
Па10- ' |
П а -10-1 |
н. у.)/см# |
|
|
(при н. у.)/см8 |
|
|
|
При 60 °С |
|
|
При 80 °С |
|
0 |
0,18 |
0 |
0 |
0,441 |
0 |
11,7 |
0,18 |
— |
16,5 |
0,441 |
0.203 |
20,0 |
0,18 |
— |
22,8 |
0,441 |
0,385 |
24,2 |
0,18 |
0,24 |
30,3 |
0,441 |
0,476 |
33,1 |
0,18 |
0,73 |
34,9 |
0,441 |
1,25 |
39,0 |
0,18 |
1,20 |
38,8 |
0,421 |
1,68 |
39,1 |
0,18 |
1,57 |
40,6 |
0,410 |
2,37 |
42,4 |
0,17 |
1,95 |
45,9 |
0,380 |
4,25 |
46,2 |
0,16 |
2,87 |
48,0 |
0,370 |
4,47 |
47,9 |
0,15 |
3,40 |
49,1 |
0,365 |
5,30 |
50,8 |
0,15 |
5,30 |
52,5 |
0,365 |
6.75 |
52,8 |
0,15 |
5,83 |
53,3 |
0,365 |
7,40 |
55,5 |
0,15 |
7,57 |
— |
|
|
|
При 100 °С |
|
|
При 120 °С |
|
0 |
0,960 |
0 |
0 |
1,82 |
0 |
18,2 |
0,960 |
0,355 |
14,0 |
1,82 |
0,304 |
22,8 |
0,960 |
0,456 |
18,5 |
1,82 |
0,456 |
28,0 |
0,960 |
0,73 |
22,4 |
1,81 |
0,466 |
32,5 |
0,950 |
1,29 |
25,0 |
1,81 |
0,812 |
37,3 |
0,916 |
1,98 |
30,0 |
1,71 |
1.175 |
41,7 |
0,846 |
3,02 |
34,1 |
1,59 |
1,72 |
44,3 |
0,810 |
3,79 |
38,3 |
1,55 |
2,90 |
45,8 |
0,780 |
4,74 |
42,1 |
1.53 |
3,91 |
48,6 |
0,770 |
6,08 |
43,9 |
1,49 |
5,00 |
51,1 |
0,748 |
7,73 |
46,3 |
1,48 |
5.62 |
|
|
|
46,9 |
1,48 |
6,48 |
|
|
|
48,8 |
1,47 |
7,12 |
Таблица |
IV -29. Плотность аминопоташных растворов |
|
||
|
|
(в г/сма) |
|
|
Состав раствора, моль/л |
|
Температура, °С |
|
|
К*СО* |
ДЭА |
20 |
60 |
120 |
1.71 |
0,17 |
1,184 |
1,165 |
1,138 |
1.71 |
1.12 |
1,200 |
1,181 |
1.152 |
2,23 |
0,17 |
1,234 |
1,216 |
1,187 |
2,2 |
1,18 |
1,261 |
1,241 |
1,210 |
2,83 |
0,19 |
1,304 |
1,283 |
1,255 |
2.83 |
1,24 |
1,304 |
1,282 |
1.255 |
-------------- ч -----
Таблица IV-30. Теплоты растворения С02 в растворах К 2С03 + ДЭА
(в кДж/моль) *
Концентрация ДЭА, %
Степень карбонизации, моль СО, на моль
(К,СОя + ДЭА) |
1,5 |
---- |
5 |
10 |
0,2 |
27,6 |
|
30,1 |
31,8 |
0,4 |
22,2 |
|
23,0 |
24,7 |
0,6 |
17,2 |
|
18,0 |
18,4 |
0,8 |
14,6 |
|
16,7 |
16,7 |
* 1 кД ж = 0,2389 ккал.
Одной из серьезных проблем в процессах очистки горячими растворами поташа является выбор насадки для абсорбера и регене ратора. Раствор поташа представляет собой коррозионно-активную
Растворимость, моль СО%/моль К2СО3 +ДЗР
Рис. IV-80. Растворимость С02 в растворах, содержащих 30% К2С03 и ДЭА (а - 5 % ; б — 1 0 %):
1 — при 80 °С; 2 — при 100 °С; 3 — при 120 °С.
среду, особенно при высокой степени карбонизации раствора [216]. В связи с этим крайне нежелательно применять насадку из углеро дистой стали. Доказано, что. керамическая насадка выщелачивается горячим раствором К 2С03, и при охлаждении регенерированного
раствора выпадает осадок S i0 2 (в холодильниках и др.). Скорость выщелачивания зависит от типа керамики. Недостаток полипро пиленовой насадки заключается в ее размягчении при 115 °С. Поли пропилен со стеклянной арматурой стоек до 125—138 °С.
Важной проблемой является также вспенивание раствора, сильно снижающее максимальную нагрузку по газу [216]. Причины вспе нивания при поташной очистке могут быть различными. Так, из поли
пропиленовой |
насадки |
могут |
|
||||||
выщелачиваться вспенивающие |
|
||||||||
вещества, |
применяемые при ее |
|
|||||||
изготовлении |
(например, |
|
при |
|
|||||
садки, |
использующиеся |
|
при |
|
|||||
формовании насадки). К вспени |
|
||||||||
ванию могут приводить продук |
|
||||||||
ты |
коррозии металлической на |
|
|||||||
садки. |
Наиболее надежным ви |
|
|||||||
дом |
насадки |
в |
условиях |
по |
|
||||
ташной очистки |
является |
на |
|
||||||
садка |
из |
нержавеющей |
стали |
|
|||||
[216]. |
|
|
|
|
|
|
|
|
|
Разрабатываются различные |
|
||||||||
варианты усовершенствованных |
|
||||||||
процессов |
горячей |
поташной |
|
||||||
очистки. |
Так, |
был |
предложен |
|
|||||
[215] |
вариант процесса |
«Бен- |
Рис. IV-81. Принципиальная схема про |
||||||
филд», |
названный |
«Хайпур» |
цесса «Хайпур»: |
||||||
(«Высокая чистота»). Схема это |
1 — абсорбер; 2 — регенератор; 3 — насосы; |
||||||||
го |
процесса |
|
приведена |
на |
4 — теплообменник; 5 — холодильники; 6 — |
||||
рис. IV-81. Газ |
подвергается |
кипятильники. |
|||||||
|
двухступенчатой очистке двумя различными абсорбентами: грубая очистка — активированным Поташным раствором «Бенфилд», тон кая очистка — другим абсорбентом (абсорбент не назван). Процесс «Хайпур» позволяет очищать газ до содержания менее 50 ррм С 02, а иногда и глубже, до 1—20 ррм H 2S, а также от COS. Тепло паро газовой смеси после регенерации абсорбента, применяемого для тонкой очистки, используется для регенерации раствора «Бенфилд».
Расход тепла в процессе «Хайпур» на 22% ниже, чем в процессе «Бенфилд». Снижаются также потери водорода, связанные с метанированием в новых процессах производства аммиака.
Описан [217] идентичный процессу «Хайпур» комбинированный процесс очистки газа, в котором грубая очистка осуществляется раствором горячего поташа, активированного ДЭА. Схема процесса аналогична схеме процесса «Хайпур». Расход тепла в таком про цессе на 10% ниже, чем в процессе «Бенфилд», при одинаковых капитальных затратах. Абсорбция раствором К 2С03 + ДЭА про водится при 106—110 °С. Температура раствора ДЭА на входе во вторую ступень очистки 40—60 °С. В данном процессе не сколько иная схема теплообмена по сравнению с процессом «Хайпур».
17 Заказ 1460 |
Ч 257 |
Насыщенный раствор из абсорбера тонкой очистки подогревается не регенерированным раствором, а насыщенным раствором из абсорбера грубой очистки.
Возможно применение в поташных растворах МЭА вместо ДЭА. Недостатком МЭА в данном случае является более высокое давление пасыщенных паров и связанная с этим необходимость промывки газа водой. Однако вопрос о применении МЭА не исключается при некотором изменении технологической схемы процесса.
При очистке газа от двуокиси углерода растворами горячего поташа применяются различные ингибиторы коррозии. В отсутствие ингибиторов скорость достигает 1 г/(м2-ч). Эффективным ингиби тором коррозии является V20 5. По данным ГИАП, добавка пятиокиси ванадия в количестве 0,4% позволяет снизить коррозию в растворе поташа, активированном ДЭА, в 25 раз. Кроме того, эффективными ингибиторами являются бура и бихромат калия.
В процессе очистки пятивалентный ванадий постепенно восста навливается, поэтому для окисления ванадия в регенератор пери одически подают воздух. В противном случае резко усиливается коррозия, выпадает осадок, содержащий железо и ванадий, вызы вающий вспенивание.
ОЧИСТКА МЫШЬЯКОВИСТО-ПОТАШНЫМИ РАСТВОРАМИ (ПРОЦЕСС «ДЖАММАРКО-ВЕТРОКОКК»)
Повышение температуры и добавка ДЭА при абсорбции горячим раствором поташа ускоряют процесс, однако в конечном итоге это позволяет лишь незначительно уменьшить размеры аппаратуры. Было установлено, что значительно более активными катализаторами реакций, протекающих при абсорбции С 02 и регенерации раствора, являются соединения трехвалентного мышьяка [218—220].
Механизм процессов, протекающих при поглощении кислых газов мышьяково-поташными растворами и их десорбции, изучен не полностью. Один из вариантов можно представить в следующем виде [221]:
bC02 + 2K3As08 + 3Ha0 |
6KHC08 + Asa0 8 |
С0а+ К аС03 + Н а0 ^ |
2КНС03 |
При регенерации равновесие этих реакций сдвигается влево. Изучено [220] влияние различных добавок на скорость абсорб
ции двуокиси углерода поташными растворами в статических усло виях в реакторе с электромагнитной мешалкой. На рис. IV-82 приведена зависимость коэффициента ускорения абсорбции Q^K1!Q0 2,5 н. раствором К 2С03 от концентрации As20 3 в растворе (где Qо = dcp/dx — скорость поглощения двуокиси углерода, объем С 02 в 1 с). В начальный период времени, когда равновесное парциаль ное давление С 02 над раствором равно нулю, движущая сила равна парциальному давлению С 02 в газовой фазе.

Из рисунка следует, что наибольшее ускорение процесса абсорб ции наблюдается при содержании до 30 г/л Аз20 3. В этих условиях скорость абсорбции увеличивается в 2,7 раза по сравнению со ско ростью абсорбции раствором неактивированного поташа. Дальней шее повышение концентрации As20 3 приводит к относительно мед
ленному |
увеличению |
ско |
|
|
|
|
|
|
|
|
|
||||||
рости |
абсорбции, |
однако |
с* 3,2 |
|
|
|
|
|
|
|
О — |
||||||
|
|
|
|
|
2 |
|
|
||||||||||
до |
содержания |
102 |
г/л |
|
|
|
|
|
|
|
|||||||
A S 20 3 |
(и л и |
0,5 |
М) |
уско |
|
|
|
|
|
|
|
3 |
|
||||
ряющее |
действие |
сохра |
&<м2,8 |
|
|
|
|
|
|
|
|||||||
|
|
|
|
|
|
|
|
||||||||||
няется. |
По данным [222], |
|
|
|
|
|
|
|
|
||||||||
ускоряющее |
|
действие |
О |
|
|
|
|
|
|
|
|
||||||
|
О |
|
|
|
|
|
|
|
|
||||||||
A S 20 3 снижается по дости |
2,4 |
|
|
|
|
|
|
|
|
||||||||
жении |
концентрации |
его |
|
|
|
|
|
|
|
|
|
||||||
в растворе 0,75 |
моль/л. |
|
|
|
|
|
|
|
1 |
|
|||||||
С увеличением степени |
2,0 |
|
|
|
|
|
|
|
|
||||||||
карбонизации |
раствора |
|
|
|
|
|
|
|
|
|
|||||||
возрастает |
ускоряющее |
|
|
|
|
|
|
|
|
|
|||||||
действие As20 3 [220]. Авто |
1,6 |
|
|
|
|
|
|
|
|
||||||||
ры |
рекомендуют |
следу |
|
|
|
|
|
|
|
|
|
||||||
ющие |
оптимальные |
усло |
1,2 |
|
|
|
|
|
|
|
|
||||||
вия: |
соотношение |
мышь |
|
|
|
|
|
|
|
|
|||||||
яка |
и |
калия в |
растворе |
$ |
|
|
|
|
|
|
|
|
|||||
[A s]/[К] |
= |
0,145, |
темпе |
I 0,8 |
|
|
|
40 |
|
60 |
80 |
|
|||||
ратура |
|
абсорбции |
60 °С. |
|
20 |
|
|
100 |
|||||||||
|
|
|
|
|
|||||||||||||
В результате ускоряющего |
|
|
|
|
A s20 3 ,£>//7 |
|
|||||||||||
действия |
мышьяка |
в про |
О |
4 |
J___ L _J___I |
I |
L |
|
|||||||||
мышленных |
абсорберах |
8,1 |
12,1 |
16,1 |
20,1 24,2 |
|
|
||||||||||
|
|
[AS]/[K],(г-amом/г-атом}102 |
|||||||||||||||
удается |
достичь степени |
|
|
||||||||||||||
|
|
|
|
|
|
|
|
|
|||||||||
насыщения |
раствора |
до |
Рис. IV-82. Ускоряющее |
действие мышьяко |
|||||||||||||
85—90% |
равновесной. |
вистого |
ангидрида |
в |
начальный момент аб |
||||||||||||
Из |
данных |
[220] |
сле |
сорбции С02 активированным поташным рас |
|||||||||||||
дует, |
|
что при |
60 °С рас |
твором |
[220] |
при |
60 °С |
и |
при |
различной |
|||||||
творимость двуокиси угле |
|
скорости вращения мешалки: |
|||||||||||||||
1 — 120 об/мин; |
2 — 400 об/мин; 8 — 900 об/мин. |
||||||||||||||||
рода в мышьяково-поташ |
|||||||||||||||||
|
|
|
|
|
|
|
|
|
|||||||||
ных |
растворах |
несколько |
|
|
|
|
|
|
|
|
|
выше растворимости в неактивированных растворах поташа. При высоком парциальном давлении С 02 различие поглотительных способностей этих растворов становится более заметным. При дав лении 2,67 -104 Па (200 мм рт. ст.) растворимость С 02 в поташ ных растворах почти не увеличивается, так как соответствует стехиометрическому соотношению компонентов; в мышьяково-по
ташных |
растворах |
растворимость |
возрастает |
вследствие реакции |
||
с арсенитом. При |
105 °С в |
условиях |
регенерации растворимость |
|||
С 02 в мышьяково-поташных |
растворах меньше |
растворимости в по |
||||
ташных |
растворах. |
|
|
|
|
|
Давление С 02 над мышьяково-поташными растворами в большей |
||||||
степени |
зависит от температуры, |
чем |
над |
неактивированными |
поташными растворами (рис. IV-83). Это способствует достижению тонкой очистки (см. гл. И).
При абсорбции под давлением емкость растворителя близка к емкости моноэтаноламиновых растворов. В схеме такой очистки предусмотрен промежуточный десорбер, в котором часть двуокиси углерода выделяется при снижении давления. Дальнейшая регене рация раствора проводится паром. Температура абсорбции 70 °С, регенерации — 105 °С.
При мышьяково-поташной очистке содержание С 02 в очищенном газе может быть снижено до 0,05%, однако при тонкой очистке заметно возрастает расход пара на регенерацию раствора, поэтому наиболее рационально снижать содержание С 02 до 1%, но не ниже 0,2-0,'5% .
Экономичность этого метода очистки значительно возрастает, если регенерацию раствора проводить продувкой его воздухомВозможен вариант двухступенчатой регенерации воздухом и паромПри такой схеме около 35—40% С 02 можно получить в чистом виде, пригодном для синтеза карбамида. В первой стадии регенераций достигается остаточное содержание бикарбоната 20%, а во второй до 2,5%.
Расход пара при очистке методом «Джаммарко-Ветрококк» за^ висит от парциального давления С 02 в газе. Так [224], при Р =*
= 2,25 МПа (23 кгс/см2) и содержании С 02, |
равном |
16,5%, при |
|
мышьяково-поташной |
очистке до 1000 см3 С 02 |
в 1 м3 |
газа расход |
пара составляет 1,5 |
т/т NH3. |
|
|
Схема промышленной установки мышьяково-поташной очистки газа высокотемпературной конверсии метана с последующей про мывкой газа от СО жидким азотом приведена на рис. IV-84. Ско рость гааа в абсорбере около 0,1 м/с, общая высота насадки 26 м.
Рис. IV-84. Схема промышленной установки очистки газа от С 02 мышьяково поташным раствором:
1 — абсорбер; 2 — агрегаты мотор-насос-турбина; з — экспанзеры; 4 — теплообменники; 5 — холодильник раствора; 6 — регенератор; 7 — насосы; 8 — кипятильник; 9 — конденса тор; ю — холодильник газа; и — колонна щелочной очистки.
Объем насадки регенератора 85 м3 на 100 м3 регенерируемого раствора* высота насадки (в зоне массообмена) около 25 м.
Опыт эксплуатации установки мышьяково-поташной очистки показывает, что наличие в растворе солей двухвалентного железа отрицательно сказывается на состоянии рабочего раствора. Железо может попадать в раствор вследствие уноса катализаторной пыли из отделения конверсии окиси углерода, из сырья, используемого
для приготовления рабочего раствора, и |
другими путями. |
При |
||
pH ^ 9 ,7 в нижней части абсорбера могут |
выпадать |
соли |
двух |
|
валентного железа. При увеличении концентрации С 02 |
из |
раствора |
||
выделяются также соли трехвалентного железа, поэтому pH |
в нижней |
части абсорбера не должно превышать 8,9. Как в абсорбере, так и в десорбере возможно некоторое выщелачивание колец Рашига, что может привести к выпадению осадка кремниевых солей. Кроме того, при охлаждении до 35—40 °С насыщенного раствора выпадает осадок КНС03.
Чтобы предупредить забивку насадки, предложено [224] часть раствора (до 5%) выводить из абсорбера с целью выделения из него солей железа и поддержания их допустимой концентрации в цирку лирующем растворе. Для этого через раствор пропускают двуокись углерода или конвертированный газ (чтобы отношение ионов бикар боната и карбоната составило 10 1). Подкисление проводят при давлении абсорбции (во избежание десорбции С 02) в аппарате с мешалкой и обогревом. Карбонаты железа отделяют фильт рованием.
В некоторых случаях, чтобы исключить осаждение солей Fe2 + , в регенератор подают кислород, при этом двухвалентное железо окисляется до трехвалентного. Одновременно As3+ окисляется до As6+ , а в присутствии даже небольшого количества пятивалент ного мышьяка (10—20 г/л) резко снижается поглотительная способ ность раствора (примерно на 15%). Пятивалентный мышьяк может накапливаться в растворе и вследствие нарушения правил эксплуа
тации установки. |
р, |
Преимуществом мышьяково-поташного процесса является |
воз |
можность одновременной очистки газа от С 02 и сероводорода, если содержание последнего не превышает 1,5%. В случае необходимости можно селективно извлекать сероводород, растворимость которого значительно выше растворимости двуокиси углерода. При этом содержание H 2S в очищенном газе снижается до 1 см3/м3. Преиму щество мышьяково-поташной очистки заключается в незначительной потере малорастворимых газов (до 0,15%).
Наиболее существенным недостатком процесса является сильная токсичность мышьяка, что обусловливает необходимость ликви дации сточных вод и проливов абсорбента.
Предложены другие, нетоксичные катализаторы процесса асборбции СО2 поташными растворами: например, соли борной, ванадиевой
и других кислот, различные органические основания |
[224], соли |
||
аминокислот |
[225] и др. |
[226—229]. |
|
Используется также процесс очистки поташными |
растворами |
||
с добавками, |
называемый |
«Катакарб» [230—232]. В этом способе |
в среднюю часть абсорбера подают абсорбент, регенерируемый снижением давления, а в верхнюю часть, для тонкой очистки, — абсорбент, регенерируемый нагреванием. Очищенный газ содержит до 0,03—0,07% С 02. Указывается, что раствор не коррозионно активен. Абсорбцию и десорбцию ведут в тарельчатых аппаратах.
Наиболее широкое распространение получил описанный выше процесс очистки раствором К 2С03 с добавкой ДЭА.
8. ФИЗИЧЕСКАЯ АБСОРБЦИЯ ОРГАНИЧЕСКИМИ РАСТВОРИТЕЛЯМИ
Выше было указано, что процессы очистки газов от двуокиси углерода и сероводорода, основанные на абсорбции хемосорбентами, имеют принципиальный недостаток, заключающийся в том, что рас ход тепла на 1 м3 очищенного газа увеличивается с повышением концентрации С 02 в исходном газе. Растворимость двуокиси угле рода в этих растворителях с ростом парциального давления обычно возрастает медленнее. В первую очередь это относится к хемосорб ции водными растворами моноэтаноламина и в меньшей степени — растворами горячего поташа.
В современных схемах синтеза аммиака газ поступает на очистку под давлением до 2,94 МПа (30 кгс/см2). В этих условиях эффективны процессы физической абсорбции органическими растворителями. В настоящее время такие процессы используются главным образом для очистки природного газа с высоким содержанием двуокиси углерода и сероводорода, однако они могут быть применены и для очистки конвертированного газа.
Флюор-процесс [233—238]. В качестве абсорбентов применяют пропиленкарбонат (запатентованы также триацетат глицерина, бутоксидиэтиленгликольацетат и метокситриэтиленгликольацетат). Наи более дешевым из них является пропиленкарбонат С4Нв0 3 — бес цветная жидкость, основные свойства которой приведены ниже:
Температура, °С |
|
|
|
|
|
|
242 |
|
||
|
кипения |
|
|
|
|
|
|
|
|
|
|
п л а в л е н и я ..................... |
|
|
|
— 49 |
|
||||
Плотность при 20° С, г/см3 |
|
|
|
|
1,2 |
|
||||
Показатель преломления |
|
|
|
|
1,4208 |
|
||||
Вязкость при 18° С, сст |
|
|
|
|
6,64 |
|
||||
Давление насыщенных паров при 27° С |
|
(6,64*10-6 м2/с) |
|
|||||||
|
|
|
|
|||||||
|
Па . . |
|
|
|
. |
|
|
0,666 |
|
|
|
мм рт. ст. |
|
|
|
|
|
0,005 |
|
||
Таблица IV-31. |
Растворимость С02 в пропиленкарбоиате под давлением |
|||||||||
|
|
|
|
(в м3 при н. у'./м*) |
|
|
|
|
||
Р*, МПа |
Рас |
р *, |
Рас |
|
Р*. |
Рас |
Р*. |
Рас |
р*. |
Рас |
твори |
твори |
|
твори |
твори |
твори |
|||||
|
мость |
МПа |
мость |
|
МПа |
мость |
МПа |
мость |
МПа |
мость |
|
При 25 °С |
|
|
|
|
При |
40 -°С |
|
|
|
7 0,286 |
8,5 |
0,876 |
28,5 |
|
0,223 |
5,0 |
0.862 |
20,8 |
1,365 |
36,7 |
0,309 |
9,2 |
0,903 |
29,0 |
|
0,301 |
6,8 |
0,920 |
22,4 |
1.45 |
39,5 |
0,324 |
9,7 |
1,049 |
32,6 |
|
0.334 |
7,8 |
0,963 |
24,8 |
1,555 |
41.8 |
0,608 |
19,0 |
1,130 |
37,4 |
|
0,534 |
12 ,0 |
1 , 1 1 |
27,3 |
1.73 |
45.6 |
0,631 |
19,2 |
1,315 |
44,1 |
|
0,589 |
13,6 |
1.14 |
28,6 |
|
|
0,874 |
28,4 |
1,60 |
58,5 |
1 |
0,60 |
13,5 |
1,33 |
34,6 |
|
|
* 1 МПа = 10,2 кгс/см3.
В табл. JV-31 приведены экспериментальные данные о раствори мости двуокиси углерода в пропиленкарбонате [234].
Из приведенных данных следует, что растворимость С 02 в про пиленкарбонате примерно в 3 раза выше растворимости С 02 в воде, что и определяет преимущество этого
|
|
|
метода |
очистки. |
Теплота растворения |
||||||
|
|
|
двуокиси углерода |
в |
пропиленкарбо- |
||||||
|
|
|
пато 3500 кал/моль. Растворимость се |
||||||||
|
|
|
роводорода примерно втрое выше, чем |
||||||||
|
|
|
двуокиси углерода; теплота его раство |
||||||||
|
|
|
рения |
3700 |
кал/моль. |
|
|
|
|||
|
|
|
На |
рис. IV-85 показана зависимость |
|||||||
|
|
|
растворимости С 02 |
в |
пропиленкарбо |
||||||
|
|
|
нате от давления |
[239]. |
Изучена рас |
||||||
|
|
|
творимость |
азота |
и |
водорода |
в про |
||||
|
|
|
пиленкарбонате |
[240 ]. |
Селективность |
||||||
|
|
|
пропиленкарбоната |
С = |
а со 2/ан 2 (а — |
||||||
|
|
|
в м3 при н. у. на 1 м3) |
снижается |
от 17 |
||||||
|
|
|
до 9 с |
повышением |
общего давления |
||||||
|
|
|
от 9,8 до 29,4 МПа (от 100 до 300 кгс/см2). |
||||||||
Рис. IV-85. |
Зависимость |
рас |
Данные, полученные на опытно-про |
||||||||
мышленной |
установке |
[241, 242], пока |
|||||||||
творимости |
чистой С0 2 |
(1) и |
|||||||||
С 02 из азотоводородной смеси |
зали, что |
коэффициент |
массопередачи |
(2)в пропиленкарбонате от зависит от плотности орошения и не
давления при 40 °С (Н2 |
: N2 = |
зависит от скорости |
газа и концентра |
= 3 : 1 , концентрация |
С 02 в |
ции С 02. |
|
смеси 17,74%). |
|
|
|
|
|
Основное преимущество Флюор-про- |
|
цесса заключается |
в том, что десорбция С 02 происходит только |
||
за счет снижения |
давления, поэтому энергия |
расходуется в ос- |
Очищенный.
Рис. IV-8 6 . Технологическая схема очистки газа (Флюор-процесс):
1 |
— |
ц ен тр обеж н ы й к ом п р ессор; 2 — |
систем а м етан и рован и я; 3 — |
ц ен тр обеж н ы й к ом п р ессор ; |
4 |
— |
а бсор бц и о н н ая к ол о н н а; 5 — сеп ар атор ср едн его давл ен и я ; в |
— сеп ар атор н и эк ого д а в л е |
|
|
|
н и я ; 7— реген ер атор ; |
8 — н а со с д л я ц и р к у л и р у ю щ его р а ст в о р а . |
новном только на перекачивание абсорбента. Такой способ десорб ции может быть осуществлен лишь при достаточно высоком парци альном давлении двуокиси углерода в газе.
Для расчета процесса могут быть использованы соотношения, приведенные в главе II.
Технологическая схема процесса по существу не отличается от схемы водной очистки (рис. IV-86). В нее включена стадия про межуточной десорбции. В случае отсутствия этой стадии двуокись углерода загрязняется компонентами конвертированного газа и теряется часть азотоводородной смеси. Так как количество абсор бента, подаваемого на орошение, практически не меняется при из менении парциального давления двуокиси углерода в газе, то в схеме с промежуточной десорбцией потери азотоводородной смеси можно свести практически к нулю за счет рециркуляции потока газа, десорбированного в первом десорбере.
Давление в промежуточном десорбере, как и в случае водной очистки, должно быть несколько ниже давления С 02 над насыщен ным раствором, тогда десорбция водорода и других газов будет протекать при отдувке двуокисью углерода.
В схеме используется энергия сжатого растворителя после про межуточного десорбера (аналогично системе мотор — насос — тур бина в водной очистке). Возможна также установка турбины перед промежуточным десорбером. После промежуточной десорбции сле дует стадия десорбции при атмосферном давлении и затем путем продувки воздухом. В этом случае концентрация С 02 в очищенном газе может быть снижена до 0,3%.
Расчеты [236, 237] показывают, что Флюор-процесс экономичен
в том случае, когда парциальное, давление С 02 |
в исходном газе |
|
превышает 3,92-105—6,86 • 106 Па (4—7 кгс/см2) |
при содержании |
|
С 02 в очищенном газе 1—3%. При |
производстве аммиака после |
|
промывки газа пропиленкарбонатом |
необходима |
последующая тон |
кая очистка раствором МЭА. Пользуясь этим способом, можно одновременно очищать газ от сероводорода, сероуглерода, меркап танов и сероокиси углерода. Процесс пригоден для очистки газа, полученного высокотемпературной конверсией углеводородов под да влением, в котором содержится обычно до 30% двуокиси углерода. Поскольку при высокотемпературной конверсии не требуется пред варительная очистка от серы, ее можно удалять вместе с двуокисью углерода пропиленкарбонатом. При очистке от сероводорода, а также при совместной очистке от С 02 и H 2S Флюор-процесс экономичен и при парциальных давлениях сероводорода более низких, чем указанное выше давление двуокиси углерода.
Важным преимуществом процесса является низкий расход тепла (только на тонкую доочистку газа раствором МЭА). Разработан вариант очистки газа пропиленкарбонатом при 0 °С. Это поз воляет уменьшить циркуляцию растворителя и расход электро энергии.
Описано [238, 243—245] применение физической абсорбции про пиленкарбонатом для очистки синтез-газа под давлением до 9,8— 13,7 МПа (100—140 кгс/см2). В этих условиях преимущество физической абсорбции наиболее очевидно. При очистке пропилен
карбонатом под давлением 2,65 МПа (27 кгс/см2) основной статьей расхода является расход электроэнергии на перекачивание абсор бента, который в этих условиях несколько выше, чем при МЭАочистке. На вторую стадию МЭА-очистки может поступать гай, содержащий от 5 (в случае десорбции С 02 из пропиленкарбоната только сбросом давления) до 0,3% С 02 (при десорбции продувкой азотом или воздухом).
Сравнение термодинамической эффективности процесса пропиленкарбонатной очистки с МЭА-очисткой приведено ниже (стр. 278).
ПРОЦЕСС «ПУРИЗОЛ»
Другим способом физической абсорбции С 02 и H 2S является процесс «Пуризол» [246, 247], принципиально не отличающийся от Флюор-процесса. В качестве абсорбента используется N-метил- пирролидон — растворитель, уже нашедший широкое применение для выделения ацетилена из газов окислительного пиролиза метана
(см. гл. X). |
|
свойства N-метилпирролидона C5H9ON при |
||||
Физико-химические |
||||||
ведены в гл. X. |
|
|
хорошим абсорбентом при очистке |
|||
N-Метилпирролидон является |
||||||
газов от меркаптанов (Л. Ф. Сокодина и др., |
Хим. пром., 1971, |
|||||
№ И , с. 828—829). Его преимуществом по сравнению |
с другими |
|||||
растворителями |
является более |
высокая поглотительная способ- |
||||
Таблица IV-32. Растворимость газов в N-метилпирролидоне [178] |
||||||
|
|
(в м 3 п р и н . у . / м 3) — |
|
|
||
|
|
|
Т ем п ер а т у р а , °С |
|
||
Д а в л ен и е 1 0 е П а , |
|
|
|
|
|
|
|
|
20 |
|
2 3 ,5 |
|
35 |
|
|
Двуокись |
углерода |
|
|
|
0.68 |
|
_ |
|
2,0 |
|
_ |
1.013 |
|
3,95 |
|
— |
|
3,0 |
10,13 |
|
— |
|
— |
|
3,2 |
|
|
Сероводород |
|
|
__ |
|
0,415 |
I |
_ |
I |
14,3 |
I |
|
1,013 |
1 |
48,8 |
1 |
— |
1 |
25,0 |
|
|
Метан |
_ |
| |
__ |
|
1,013 |
I |
0,28 |
I |
|||
56,7 |
1 |
— |
1 |
1 2 ,2 |
1 |
— |
|
|
Пропан |
|
|
|
|
0,598 |
| |
|
1 |
1.9 |
| |
— |
* 1 0 е П а = 1 ,0 2 к г с /с м 2.
ность и одновременно возможность сравнительно легкой регенера ции (вследствие более резкой зависимости растворимости мерка птанов от температуры).
В табл. IV-32 приведена растворимость С 02 и других газов в N-метилпирролидоне.
При 20 °С и давлении 1,013-10Б Па в 1 м3 N-метилпирролидона
растворяется 4 м3 |
С 02; растворимость сероводорода |
в |
12 раз |
больше, поэтому N |
-метилпирролидон можно применять |
для |
селек |
тивного извлечения сероводорода из газов, содержащих двуокись углерода. N-метилпирролидрн не токсичен и не обладает коррозион
ной активностью. |
Недостаток его, |
как |
и |
большинства |
раствори |
|||
телей, применяемых для абсорбции |
двуокиси углерода, — отно |
|||||||
сительно |
высокая |
стоимость. |
|
|
|
|
|
|
Основные показатели процесса очистки приведены в обзоре |
||||||||
[181]. Указывается |
[247], что при 2,06—2,74 МПа (21—28 ктс/щ2) |
|||||||
очистка растворами МЭА и К 2С03 дешевле, чем N-метилпирроли- |
||||||||
доном. |
|
|
|
|
|
|
|
|
Ниже |
и далее в таблице на |
стр. |
268 приведены |
некоторые |
||||
параметры процесса «Пуризол» при |
очистке |
природного газа [143]. |
||||||
|
|
Температура абсорбента, |
°С |
|
|
|||
Исходный газ |
|
|
|
|
|
0—15 |
||
1 -й |
абсорбер |
|
|
|
|
|
|
|
|
на входе . |
|
|
|
|
|
|
20 |
2 -й |
на выходе |
|
|
|
|
|
|
30 |
абсорбер |
|
|
|
|
|
24 -28 |
||
|
на входе . |
|
|
|
|
|
||
|
на выходе . |
|
|
|
|
4 0 -44 |
||
Последний десорбер на входе |
|
|
|
|
|
130 |
||
|
|
Давление |
|
|
10ft Па |
кгс/см2 |
||
|
|
|
|
|
|
|||
Исходный газ |
|
|
|
|
50.9 |
|
52 |
|
1 -й |
десорбер |
|
|
|
|
35.3 |
|
36 |
2 -й |
десорбер |
|
|
|
|
15,8 |
|
16 |
3-й |
десорбер |
|
|
|
|
1,47 |
|
1,5 |
|
|
Состав газа, |
% |
(об.) |
Иа входе |
На выходе |
||
|
|
|
|
|
|
|||
HoS |
|
|
|
|
1 - 1 0 |
0 .0 2 —6,2 |
||
сб2 |
|
|
|
|
8 -2 6 |
6 — 20 |
||
СН4 |
|
|
|
|
70—80 |
75—90 |
^Чтобы снизить потери дорогостоящих растворителей, необходима тщательная промывка отходящих газовых потоков водой. Промывку осуществляют в колоннах с колпачковыми или клапанными тарел ками при весьма малом соотношении вода — газ. Показано в про мышленном масштабе, что при правильном расчете таких аппаратов можно практически полностью извлекать пары и брызги раствори теля при минимальном расходе воды, подаваемой на орошение.
Параметры |
1-й вариант |
2-й вариант |
З-й вариант |
Исходный газ |
|
2,83 |
2,83 |
Объем, млн. м3/сут |
2,83 |
||
Давление |
|
36,3 |
74,5 |
105 Па |
74,5 |
||
кгс/см2 |
76 |
37 |
76 |
Температура, °С |
43 |
27 |
27 |
Состав, % (об.) |
64,53 |
|
—* |
Н 2 |
— |
||
С02 |
33,15 |
1,0 |
15,0 |
H 2 S |
— |
34,0 |
6,0 |
со |
1,50 |
— |
— |
с н 4 |
0,44 |
63,7 |
75,0 |
С2Н в- С 4Н 10 |
_ |
1,1 |
— |
С5Н 12 |
— |
0,2 |
— |
N 2 |
0,38 |
— |
4,0 |
Очищенный газ |
|
|
|
Состав, % (об.) |
96,44 |
|
|
н 2 |
— |
— |
|
с о 2 |
0,1 |
1,2 |
13.6 |
H 2S |
_ |
2,0 |
2 см3/мЗ |
СО |
2,24 |
— |
— |
СИ4 |
0,59 |
95,4 |
82,0 |
с 2н 8— С4Н ю |
_ |
1,4 |
— |
свн 12+ |
_ |
— |
— |
N2 |
0,63 |
— |
4,4 |
Расходные коэффициенты |
|
|
|
Электроэнергия (без учета ре |
|
|
|
куперации) |
2100 |
1600 |
1100 |
кВт |
|||
ГДж/ч |
7,56 |
5,76 |
3,96 |
Пар (2,94-103 Па, или |
1,7 |
0,65 |
1,3 |
3 КГС/СМ2), т/ч |
|
|
(Р = 3.92Х |
|
|
|
Х105 Па, |
Потери абсорбента, кг/ч |
3 |
5 |
4 КГС/см2) |
4 |
При расчете количества воды, подаваемой на орошение про мывных тарелок, принимают, что промываемый газ почти не со держит влаги (так как он осушен органическим растворителем). Поэтому количество воды, подаваемой на верхнюю тарелку, будет равно
|
|
Zf= LH+ «^нао+ Z>6p |
|
|
|
|
где Z-H — количество |
воды, |
стекающей |
(в смеси с |
растворителем) |
с |
нижней |
промывной тарелки; |
Ьиас — количество |
воды, необходимой для |
насыщения |
|||
газа влагой; L$p — количество воды, необходимое |
для компенсации |
брызго- |
||||
уноса; обычно £бР :^2 -ьЗ |
L Hac. |
|
|
|
|
Величина £ бр, как и Z/Hac, может быть рассчитана с достаточной степенью точности. Большое количество воды на промывку подавать нежелательно, так как это может привести к обводнению системы
и, следовательно, к усложнению схемы и к затратам энергии на под держание баланса воды в системе. Количество воды, отводимой из цикла, должно быть равно количеству влаги, приносимой с ис ходным газом и с промывной водой. Этим определяется мини мальное содержание воды в растворителе.
Целесообразен вывод промывных вод в отдельный аппарат для ректификации. Значительная часть влаги (иногда вся вода) может быть удалена из раствора при десорбции двуокиси углерода.
В процессе «Пуризол» и других аналогичных процессах часть раствора непрерывно отводят на ректификацию вместе с промыв ными водами. Для уменьшения расхода тепла на ректификацию и потерь растворителя очищаемый газ подвергают предварительной осушке в том же абсорбере. Исходный газ в зоне осушки промывают частью насыщенного абсорбента, поступающего на ректификацию, и затем подают в основную зону абсорбции. Большая часть насы
щенного |
абсорбента отводится (до зоны осушки) на десорбцию. |
|||
|
|
ПРОЦЕСС «СЕЛЕКСОЛ» |
|
|
Это один из вариантов очистки |
газов физической |
абсорбцией. |
||
В качестве абсорбента применяют диметиловый эфир |
полиэтилен |
|||
гликоля |
[199, 249—255], основные |
физико-химические свойства |
||
которого |
приведены |
ниже: |
|
|
Температура, °С |
|
|
|
|
|
кипения |
. . . . |
|
151 |
|
замерзания |
. —22н-—29 |
||
Давление паров при 2 5° С |
|
1,33 |
||
|
Па |
|
|
|
|
мм рт. ст. . . |
|
0,01 |
|
Вязкость при 25°С |
|
|
||
|
Па • с |
. . . |
5 , 8 - 10- 3 |
|
|
сП . |
|
5,8 |
|
Теплоемкость при 25^°С |
|
2,43 |
||
|
кДж/(кг • К) |
|
|
|
|
ккал/(кг • °С) |
|
|
0,5 |
Для абсорбента характерна высокая селективность при извле чении сероводорода (растворимость II2S в 7 раз выше растворимости С 02). Поглотительная способность растворителя по отношению к органическим сернистым соединениям также весьма велика. Данные по растворимости газов в растворителе «Селексол» даны в [143].
В процессе очистки природного газа при 6,86 МПа (70 кгс/см2) растворитель регенерируют сначала снижением давления до 1,67 МПа (17 кгс/см2), потом до 1,18—1,37 МПа (12—14 кгс/см2), а затем ступенчато до 3,92 МПа, 0,69 -105 и 0,196• 106 Па (соответственно до 4, 0,7 и 0,2 кгс/см2) и десорбируют сероводород отдувкой воз духом и паром. Кроме того, десорбцию можно вести в вакууме.
Описано [254] несколько вариантов технологических схем про цесса в зависимости от соотношения С 02 и H 2S в газе. Для очистки
газа, |
содержащего большое количество С 02 и малое количество |
H 2S, |
применяют двухпоточную схему абсорбции. ЧВ верхней части |
абсорбера происходит в основном очистка от сероводорода. Г*ш после первой ступени десорбции возвращается в абсорбер. Иногда перед подачей раствора в абсорбер его умеренно охлаждают.* Про цесс применяют для грубой очистки от С 02 (3,5—2,5% в очищенном газе), при этом содержание H 2S снижается до 6 мг/м3.
Основная трудность в применении органических растворителей типа «Селексол» заключается в их высокой стоимости и дефицит ности. Кроме того, метод не экономичен при малых концентрациях примесей в исходном газе.
ОЧИСТКА ХОЛОДНЫМ МЕТАНОЛОМ (ПРОЦЕСС «РЕКТИЗОЛ»)
Основным преимуществом процесса очистки газа от С 02 холод ным метанолом является резкое увеличение растворимости двуокиси
углерода при понижении |
температуры. При этом |
уменьшается |
|
циркуляция раствора и |
возрастает |
селективность |
растворителя. |
Из уравнения (11,38) |
следует, что |
требуемая степень очистки |
может быть легче достигнута путем понижения температуры абсорб ции Гв, чем повышения температуры десорбции Гр [256]. Так, даже при Тр —►оо
, |
, |
Р2, р |
АН |
-1 |
lg l/г.в —lg |
р |
2,3/? |
Тв |
Чем ниже температура абсорбции Гв, тем при меньшей разности (Тв—Тр) можно достичь требуемой степени очистки.
Проведение абсорбции при низких температурах позволяет расширить ассортимент абсорбентов, использовать* для очистки самые дешевые из них, которые не могут применяться при обычной температуре из-за высокого давления насыщенных паров.
В литературе опубликованы данные о растворимости газов в различных растворителях при низких температурах. Наиболее подробно растворимость изучена в работе [257]. Растворимость С 02
в |
мол. |
долях |
при |
парциальном давлении С 02 до |
1,013* 10б Па |
||
(1 |
кгс/см2) и |
температуре до 45 °С почти для |
всех |
растворителей |
|||
описывается законом Генри (значения коэффициентов Генри |
[257] |
||||||
Кг = Р!х приведены |
в табл. IV-33). |
|
|
|
|||
|
При |
60 °С растворимость С 02 в ацетатах, |
углеводородах |
и их |
галоидопроизводных несколько отклоняется от закона Генри и может быть рассчитана по уравнению Кричевского — Ильинской (в уцрощенном виде):
где / 2 — летучесть двуокиси углерода, |
атм; А — коэффициент, |
зависящий |
|
от температуры и давления, атм-см3. |
|
|
|
Ниже приведены |
значения коэффициентов Л*10“ 3 при —60 °С: |
||
Метилацетат |
-5,87 |
Йодистый этил |
29,20 |
Этилацетат . . |
-6,40 |
Толуол |
26,00 |
«-Пропилацетат |
—7,07 |
Этилбензол |
34.40 |
Изобутилацетат |
—13,05 |
н-Гексан |
8.40 |
Хлороформ |
—23,20 |
«-Гептан |
32.40 |
Таблица IV-S3. |
Коэффициенты Генри для растворов С02 |
|
|||||
|
|
в различных |
растворителях |
|
|
|
|
(в атм/мол. доля, или в 0,986-10® Па/мол доля) |
|
|
|||||
|
Температура, °С |
|
Температура, °С |
||||
Растворитель |
-2 5 ,2 -4 5 ,3 -6 0 ,5 |
Растворитель |
-2 5 ,2 -4 5 ,3 -6 0 ,5 |
||||
|
|
||||||
Метилацетат |
11,81 |
5,78 |
2,86 |
«-Бутиловый |
50.50 |
26,18 |
14,18 |
Этилацетат |
12,25 |
6,17 |
3.04 |
спирт |
51,54 |
26,49 |
14,84 |
к-Пропилацетат |
12,55 |
6 ,10 |
3,07 |
«-Пропиловый |
|||
Дпэтиловый эфир |
14,81 |
6,90 |
3,51 |
спирт |
40.68 |
23.65 |
15,16 |
Этилформиат |
15,35 |
7,70 |
3,80 |
Толуол |
|||
Изобутилацетат |
15,93 |
7,57 |
3,81 |
Изопропиловый |
59,99 |
30,13 |
16,38 |
Ацетон |
14,63 |
7,17 |
3.83 |
спирт |
43,21 |
24,99 |
16,60 |
Метилэтилкетон |
15,30 |
7,72 |
4,21 |
Этилбензол |
|||
Диметилформами д |
18,35 |
9,05 |
— |
«-Гексан |
39,20 |
25,90 |
17,55 |
«-Бутиловый эфир |
24,04 |
13,07 |
7,46 |
Изобутиловын |
64,55 |
32,72 |
17,72 |
Хлороформ |
29,52 |
16,32 |
10 ,2 0 |
спирт |
39,45 |
29,70 |
19,50 |
Метиловый спирт 41,50 19,82 10.25 |
«-Гептан |
||||||
Этиловый спирт |
46,48 |
23,53 |
1 2 , 1 1 |
Йодистый этцл |
52,36 |
31,49 |
2 0 ,10 |
|
|
|
|
отор-Бутиловый |
69,45 |
39,54 |
23,45 |
|
|
|
|
спирт |
|
|
|
Теплота растворения двуокиси углерода в метиловом спирте составляет 16,55 кДж/моль (4050 кал/моль). Данные о теплотах растворения в других растворителях, а также о влиянии содержа ния воды в метаноле на растворимость двуокиси углерода приведены в работе [257]. Из этих данных следует, что растворимость дву окиси углерода в растворителях при низких температурах велика. Так, растворимость С 02 в этилацетате, метилэтилкетоне и метиловом спирте при —60,3 °С и 1,013-10б Па соответственно равна 102,6;
96,40 и 74,9 см3/г. С |
увеличением парциального давления С 02 |
до 5,07 • 10б—10,13-10б |
Па (5—10 кгс/см2) растворимость С 02 в ме |
таноле растет примерно пропорционально давлению, а затем гораздо быстрее [314]. Данные о растворимости С 02 в метаноле под давлением
приведены на рис. IV-87. |
|
Если содержание С 02 (в |
мол. долях) меньше или равно 0,2, |
растворимость описывается |
уравнением: |
xCOt = 0A25P/P0
где Р о — давление паров сжиженной чистой С 02.
Данные о растворимости С 02 и других газов в метаноле приве дены также в работах [258—262]. Растворимость сероводорода в 5— 6 раз превышает растворимость двуокиси углерода при прочих: равных условиях [258], что позволяет осуществить селектпвпое
разделение этих газов. |
Если мольная до^У; "Сероводорода в растворе |
не превышает 0,1, его |
растворимость описывается законом Генри |
[258]. Ниже приведены коэффициенты Генри для растворов серо водорода в метаноле:
|
мм рт. ст./мол. доля |
к г |
Температура, °С |
МПа/мол. доля |
|
О |
14 600 |
1.84 |
—25,6 |
6 600 |
0,88 |
—50,0 |
2 350 |
0,313 |
-7 8 ,5 |
500 |
0,0666 |
На рис. IV-88 приведены экспериментальные данные [258] по растворимости сероводорода при различных парциальных да
влениях |
и |
температурах. |
Теплота |
|
растворения |
сероводорода |
||||
|
|
|
|
|
|
|
|
|
|
V* |
egi tCj |
|
|
|
|
|
|
|
1,0' |
||
|
|
|
|
|
|
|
d |
|||
|
|
о |
|
|
|
|
|
|
|
С |
vj |
|
|
|
|
|
|
|
2: |
||
a |
|
|
|
|
|
|
0,5 |
|||
1 |
|
|
|
|
|
|
|
|||
A ^ |
|
|
|
|
|
|
|
|
||
I |
оC4 |
|
|
|
|
|
|
|
|
|
1 ° |
|
|
|
|
|
|
|
0 |
||
|
|
О |
/00 |
200 |
300 |
т |
500 |
|||
|
|
600 |
|
|||||||
|
|
|
|
Растворимость СО2, см3/г |
|
|
|
|||
Рис. IV-87. |
Изотермы растворимости С 02 |
в метаноле |
[257]: |
|||||||
I — при минус 26 °С; 2 — при минус |
36 °С; 3 — при минус |
45° С; 4 — при минус 60 ®С. |
19,3 кДж/моль (4600 кал/мол). Наличие двуокиси углерода в рас творе снижает растворимость сероводорода на 10—15%.
|
|
|
|
|
|
|
Опубликованные |
дан |
|||||
|
|
|
|
|
|
|
ные о растворимости дру |
||||||
|
|
|
|
|
|
|
гих компонентов конверти |
||||||
|
|
|
|
|
|
|
рованного газа в метаболе |
||||||
|
|
|
|
|
|
|
под давлением при низких |
||||||
|
|
|
|
|
|
|
температурах |
|
свидетель |
||||
|
|
|
|
|
|
|
ствуют |
о |
том, |
что селек |
|||
|
|
|
|
|
|
|
тивность метанола по отно |
||||||
|
|
|
|
|
|
|
шению |
к |
смеси |
С 02-'-Н2 |
|||
|
|
|
|
|
|
|
примерно |
в 7 раз выше се |
|||||
|
|
|
|
|
|
|
лективности |
воды; |
следо |
||||
-80 |
-60 |
|
-ч о |
-20 |
О |
вательно, потери |
водорода |
||||||
|
при этом процессе очистки |
||||||||||||
|
|
|
Температура,0С |
|
|||||||||
|
|
|
|
ничтожны. |
|
|
|
||||||
|
|
|
|
|
|
|
|
|
|
||||
Рис. IV-8 8 . Влияние температуры на раство |
Растворимость азота в |
||||||||||||
римость сероводорода |
в метаноле: |
метаноле |
минимальна при |
||||||||||
I — PH 2S — |
кПа (400 Ш1 рт. ст.); г — P H 2S — |
10 °С и медленно |
увеличи |
||||||||||
= 40 кПа (300 мм pi. |
3 — Р д 2§ = |
26,7* кПа |
вается при уменьшении или |
||||||||||
(200 мм |
рт. ст.); |
4 — PHzS |
17,3 кПа |
(150 мм |
|||||||||
повышении |
температуры |
||||||||||||
рт. ст.); |
5 — PHtS |
= |
13,3 кПа (Юь дм рт. ст.); 6 — |
||||||||||
|
PjjjS |
= |
6,67 кПа (50 мм рт. ст.). |
|
и примерно |
вдвое |
в^ппр. |
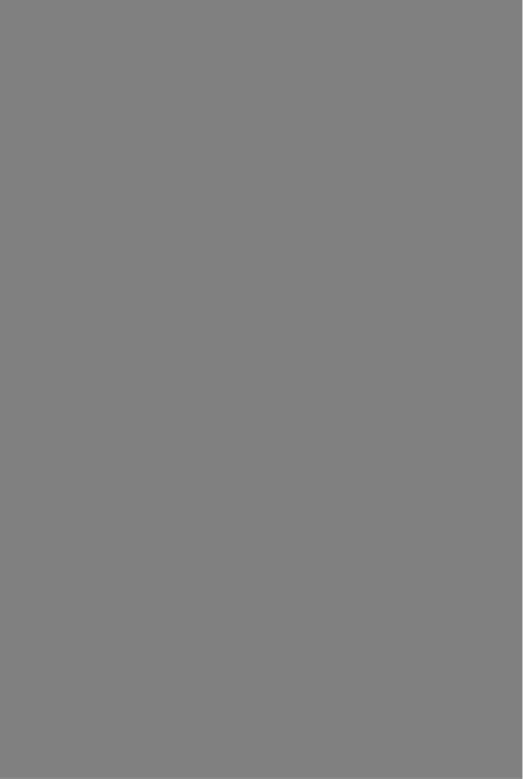
Процесс абсорбции исследован [263] в насадочной колонне диаметром 65 мм и высотой 1 м в изотермических условиях: при
скорости газа |
0,115—1,083 м/с, |
плотности |
орошения |
1,445—6,77 |
|||||||
м3/(м2«ч), при температуре —21 -f- —60 °С |
и |
давлении |
6,07-106— |
||||||||
18,25 - 10б Па |
(6—18 кгс/см2). |
|
Критерий |
Рейнольдса |
|
по |
газовой |
||||
фазе Rer изменялся от 62,5 до 840, критерий |
Прандтля (по жидкой |
||||||||||
фазе) Ргж — от 1345 до 7210. |
|
|
|
|
|
|
|
|
|
|
|
Экспериментальные данные обобщены в виде |
уравнения [263]: |
||||||||||
Nu = 0,562-10-9 Re» -42 |
^ |
У ’378 |
Р г ^ е 6^ |
^ |
у |
’66 |
|
||||
где Nu = К dJD г — диффузионный |
критерий |
Нуссельта; |
d9 — эквивалентный |
||||||||
диаметр насадки; |
D r — коэффициент диффузии С 02 |
в газовой |
среде; |
К — ко |
|||||||
эффициент массопередачи, отнесенный к газовой фазе; |
W/D — массовое соот |
||||||||||
ношение жидкость — инертный газ; р — парциальное давление |
|
С 02 |
в газовой |
||||||||
фазе; / — летучесть С02; d — наружный диаметр кольца; |
h — высота кольца. |
Скорость абсорбции сероводорода при прочих равных условиях примерно в 10 раз выше скорости абсорбции двуокиси углерода. Поскольку концентрация сероводорода относительно мала, лимити рующим процессом является абсорбция С 02.
Технологическая схема промышленной установки «Ректизол» показана на рис. IV-90. Конвертированный газ, полученный паро
кислородной конверсией метана и конверсией окиси |
углерода, |
при температуре около 35 °С и давлении 21,6 • 10б Па (22 кгс/см2) |
|
поступает в холодильник 1. Состав газа: 71,5% Н 2; 0,8% |
N 2; 0,9% |
СН4; 2,4% СО; 24,4% С 02.
Газ охлаждается в холодильнике 1 при прямом контакте с хладоагентом — 60%-ным водным раствором метанола с температурой —38 °С. Соотношение жидкость — газ ^ 0,00055 м3/м3 (при н. у.). Вследствие высокой эффективности теплопередачи при прямом контакте недорекуперация на теплом конце теплообменника не пре вышает 3 °С. Одновременно с охлаждением происходит осушка п удаление из газа некоторых примесей. При этом исключаются трудности, связанные с вымораживанием влаги в теплообменниках.
Газ, охлажденный до —35 °С, поступает на абсорбцию в колонну основной промывки 2, снабженную колпачковыми тарелками. Вы сота абсорбера 24 м, скорость газа около 1 м/с. Колонна основной отмывки состоит из трех секций. В нижней осуществляется грубая очистка газа метанолом, охлажденным в аммиачном холодильнике. Метанол из нижней части абсорбера передается далее на десорбцию. Количество циркулирующего через аммиачный холодильник метанола зависит от теплового баланса абсорбера, т. е. от теплоты абсорбции двуокиси углерода.
Во второй секции абсорбера протекает аналогичный процесс; отсюда часть метанола переходит в цикл нижней секции. В верхней
части |
абсорбера газ промывается регенерированным |
метанолом |
при |
—51 °С и соотношении жидкость — газ — 0,0003 |
м3/м3 (при |
н. у.). Раствор из верхней секции поступает на всасывающую линию насоса второй секции. Газ, выходящий из основного абсорбера,
имеет следующий состав: 2,0% С 02; 3,1% СО; 92,8% Н 2; 1,1% СН4. Далее он поступает на тонкую очистку, а затем при —50 °С напра вляется на промывку жидким азотом от окиси углерода и метана.
Десорбция проводится в несколько ступеней. Метанол, выхо дящий из куба основного абсорбера 2, дросселируется до 8 кгс/см2 (первая ступень десорбции) и поступает в нижнюю часть четырех-
Рис. IV-90. Технологическая |
схема |
промышленной |
установки очистки |
газа |
|||||
|
|
|
от С02 холодным метанолом: |
|
|
||||
1 — абсорбер -холодильн и к; 2 |
— абсорбер |
основной |
очистки; |
3 — абсорбер тонкой очистки; |
|||||
4 — ам м иачны й холоди льн и к; |
5 — теплообм енник |
си н тез-газа; 6 — десорбер ц и кл а предва |
|||||||
ри тельн ой |
очистки; |
7 — теплообм енники двуокиси |
у глерода; |
8 — вакуум -н асос; |
9 — десор |
||||
бер ц и к л а |
основной |
очистки; |
10 — ком прессор возвратны х газо в ; и — десорбер |
ц и кл а |
тон |
||||
кой очистки; 12 — теплообм енники; |
13 — отгон ная |
колон н а; |
14 — абсорбци онн ая колон на; |
||||||
|
|
15 — ректи ф и кац и он н ая колон на. |
|
|
|
ступенчатого насадочного десорбера 9. При дросселировании ме танол охлаждается до -—51 °С.
Таким образом, в цикле абсорбции — десорбции не только извлекается С 02, но и осуществляется десорбционный холодильный цикл [265, 266]. Вследствие этого раствор и газ удается охладить до температуры более низкой, чем при охлаждении жидким амми аком. Поскольку при десорбции не требуется подогрев, на этой стадии в значительной мере компенсируются затраты холода на теп лоту абсорбции соответствующего количества двуокиси углерода.
Газ, десорбируемый после первой ступени, содержащий водород и около 60% двуокиси углерода, компримируют и вместе с основным потоком вновь подают на абсорбцию. Общий объем возвратного газа не превышает 2% объема исходного газа.
Во |
второй ступени десорбции давление снижается до |
1,275 X |
X 105 |
Па (1,3 кгс/см2), в третьей ступени остаточное |
давление |
составляет 0,588 -105 Па (0,6 кгс/см2) и в четвертой 0,245-10б Па (0,25 кгс/см2). Большая часть регенерированного метанола после четвертой ступени десорбции' направляется в основной абсорбер. Во второй ступени десорбции выделяется около 60% 98,2%-ной С 02; в третьей и четвертой — чистая двуокись углерода.
В цикле топкой очистки метанол проходит сначала две ступени
десорбции путем снижения давления от 21,6 -105 |
до 6,87 *10б Па |
(от 22 до 7 кгс/см2) и от 6,87-105 до 1,175-105 Па |
(7—1,2 кгс/см2) |
в десорбере 7, окончательная десорбция проводится |
при кипячении |
в- аппарате 13. Полученный метанол после охлаждения направляют
вабсорбер тонкой очистки.
Метанол, выходящий из колонны — теплообменика 7, дроссе
лируют в аппарате 6. Газы десорбции, содержащие 9% С 02, при соединяются к возвратному газу. Метанол при 32 °С охлаждается в кожухотрубчатых теплообменниках отходящими потоками дву окиси углерода и синтез-газа из блока промывки жидким азотом. В теплообменнике 4 возмещаются потери холода за счет испарения аммиака. Таким образом, в схеме отсутствуют громоздкие тепло обменники типа газ — газ.
Все газовые потоки, содержащие пары растворителя, после
десорбции и |
регенерации метанола направляются на промывку |
в тарельчатый |
аппарат 14. |
Количество раствора, выводимого из цикла охлаждения на ректи фикацию, определяется балансом воды в этом цикле; кубовый оста ток после ректификации водно-спиртового раствора направляют на абсорбцию метанола в колонну 14, а метанол возвращают в си стему. Описаны и другие варианты технологической схемы очистки [230, 262, 267-270].
Расход энергии в процессе «Ректизол» слагается из расхода на покрытие потерь холода при недорекуперации и потерь холода в окружающую среду, на перекачивание абсорбента, создание вакуума, на абсорбцию паров воды и двуокиси углерода.
Основная часть энергии в процессе «Ректизол» расходуется на получение холода, используемого для отвода тепла абсорбции двуокиси углерода. Выше указывалось, что большая часть этой энергии компенсируется при десорбции С 02, однако часть двуокиси углерода десорбируется при нагревании раствора выше температуры окружающей среды (то же относится и к отгонке воды, поглощен ной на стадии осушки в колонне 1). Поэтому коэффициент полезного использования холода десорбции С 02 не превышает 60—70%.
Расход холода на возмещение недорекуперации и покрытие потерь в окружающую среду составляет менее 10% общего расхода энергии, а на создание вакуума — менее 5%.
В технологической схеме синтеза аммиака для получения холода весьма эффективны абсорбционные холодильные машины [266]. Они позволяют использовать низкопотенциальное тепло конвертирован
ного газа и поэтому экономичнее компрессионных аммиачных хо лодильных машин. Расход холода в процессе «Ректизол» на 1 т NH3 составляет 4,61 *10б кДж/т (110 000 ккал). В водно-аммиачной хо лодильной машине на получение 4,187 Дж (1 ккал) холода требуется примерно 16,7—21,0 кДж (4—5 ккал) тепла конвертированного газа при 140 °С. Это соответствует расходу примерно 1 т пара на 1 т аммиака.
Таким образом, процесс «Ректизол» очень экономичен [271], однако недостаток его заключается в относительной громоздкости технологической схемы. Этот процесс наиболее целесообразен для очистки газов, содержащих большое количество разнообразных примесей, и позволяет упростить существующие многоступенчатые схемы очистки таких газов, как коксовый. Процесс «Ректизол» эффективен также в тех случаях, когда в технологическую схему входит стадия глубокого охлаждений, например при промывке жидким азотом коксового или конвертированного газа. Поэтому сочетание этого процесса очистки со стадией умеренного охлаждения позволяет уменьшить общие капитальный и энергетические затраты на очистку газа от С 02 и промывку его жидким азотом.
9. ВЫБОР МЕТОДА ОЧИСТКИ ГАЗОВ
При выборе процесса очистки окончательным критерием является величина приведенных затрат, зависящих в основном от энергети ческих и капитальных затрат. Однако такой выбор во многих слу чаях труден, что объясняется влиянием на экономические показатели процесса трех групп факторов:
1) внешние технологические параметры процесса [123] — состав, давление и температура очищаемого газа, требуемая степень очистки, параметры энергоресурсов (давление пара, наличие отбросного тепла), возможность использования вторичных энергоресурсов и т. д., т. е. факторы, не зависящие от аппаратурно-технологического оформления процесса очистки;
2) внутренние параметры процесса — расход тепла, электро энергии, растворителя, отходы, тип и вес аппаратуры, а также их зависимость от параметров исходного газа и степени очистки, т. е. параметры, на которые влияет аппаратурно-технологическое офор мление процесса очистки;
3) экономические факторы — цены на энергоресурсы, сырье, отходы, аппаратуру, а также дефицитность каких-либо видов сырья (растворителей и др.) и энергии.
В литературе опубликованы разнообразные противоречивые данные о технико-экономической эффективности различных про цессов. Из изложенного выше следует, что противоречивость в зна чительной мере является следствием различия условий сравнения этих процессов, т. е. когда не одинаковы факторы по крайней мере одной из трех групп.. В частности, технологические показатели и капитальные затраты (группа 2) в одном и том же процессе могут
сильно различаться даже при одинаковых внешних технологических параметрах и экономических затратах, так как все процессы не прерывно усовершенствуются. Поэтому сравнения, выполненные с интервалом в несколько лет, приводят иногда к прямо противо положным выводам. Влияние внешних параметров на относительную эффективность различных процессов рассмотрено в работах [214,
Рис. IV-91. Термодинамическая эффективность процессов очистки газов при различных давлениях [123]:
1 — МЭА — очистка; (абсорбция при атмосферном давлении, однопоточная схема); 2 — Пропиленкарбонатная очистка до 1 % С08 с доочисткой МЭА — раствором до 100 ррм СОа; 8 — усовершенствованный процесс МЭА-очистки (процесс МЭА — ГИАП): давление 27 кгс/смя; высокие степени карбонизации, многопоточная схема; 2а, За — эксергетический КПД с уче том КПД получения электроэнергии на ТЭЦ.
N
272, 273, 329—331]. Был выполнен анализ влияния внешних па раметров на расход энергии при МЭА-очистке и для некоторых других процессов. В качестве критерия был выбран эксергетиче ский к. п. д. (см. гл. II). Иа рис. IV-91 показана зависимость эксер-
гетического к. п. д. моноэтаноламиновой |
и пропиленкарбонатной |
|||
очистки от парциального давления СО2 в исходном газе при |
одина |
|||
ковой степени очистки |
С 02 |
[123]. Из рисунка видно, при |
Р Со. = |
|
= 0,98-105 -^3,92-10б |
Па |
(1—4 кгс/см2) |
более эффективна про- |
пиленкарбонатная очистка (с доочисткой раствором МЭА). При малых РсОг более эффективна МЭА-очистка, причем ее термодина
мическая эффективность |
достаточно велика |
(цв = 16—20%) при |
|
Рсо. < 0,196-105 |
Па (0,2 |
кгс/см2). |
|
В табл. IV-34 |
приведены параметры двух |
широко распростра |
ненных процессов МЭА-очистки (МЭА—ГИАП) и очистки горячим раствором К 2С03 с добавкой ДЭА.
Сравнение проведено при одинаковой производительности по ис ходному газу и при одинаковом составе газа для двух действующих
Таблица IV-34. Сравнение процессов очистки МЭА— ГИАП и очистки раствором горячего поташа
|
|
Показатели |
Очистка |
Очистка раствором |
|
|
|
МЭА—ГИАП |
горячего поташа |
||
Давление, Па (кгс/см2) |
27.4 • 106 (28) |
27.4 • 105 (28) |
|||
Расход газа, тыс. м3 при н. у. |
205 |
205 |
|||
Состав абсорбента (водный раствор) |
20% МЭА |
25% К2С03 |
|||
|
|
|
|
|
-2 % ДЭА |
Число |
абсорберов |
|
1 |
—0,5% У20 5 |
|
м |
2 |
||||
Высота |
абсорберов, |
36 |
58 |
||
Диаметр абсорберов, |
м |
|
|
||
нижняя часть |
|
4,2 |
3,4 |
||
верхняя часть |
|
3,8 |
2 ,2 |
||
Число |
регенераторов |
1 |
2 |
||
Высота регенераторов, м |
38 |
65 |
|||
Диаметр регенераторов, м |
|
|
|||
нижняя часть |
|
4.5 |
3,7 |
||
верхняя часть |
в очищенном газе, |
4.5 |
4,5 |
||
Концентрация |
СОг |
2 0 - 1 0 0 |
500-1000 |
||
гтм |
|
|
|
|
|
ррм |
|
кДж/м3 С02 (ккал/м8 |
5230 (1250) |
5440 (1300). |
|
Расход тепла, |
|||||
при н. у.) |
|
|
|
1750 |
|
Количество циркулирующего раствора, |
1 1 0 0 |
||||
м8/ч |
|
|
|
|
ч |
|
|
|
|
|
агрегатов производства аммиака мощностью 1360 т NH3 в сутки. Как видно из таблицы, в процессе МЭА—?ГИАП расход тепла и элек троэнергии, габариты и число абсорберов и регенераторов меньше, а степень очистки газа выше, чем при горячей поташной очистке. Однако сравнение, проведенное ранее [6], дало противоположные результаты, так как те же показатели в устаревшем прежнем варианте были значительно хуже.
Таким образом, выбор процесса должен осуществляться только после детального технологического, термодинамического и (в итоге) технико-экономического анализа.
ЛИТЕРА ТУРА
1. Зельвенский Я . Д ., Хим. пром., 1937, т. 14, N° 17—18, с. 1250—1257.
2.Кричевский И . Р., Жаворонков Н. Л/., Эпельбаум В. А ., Хим. пром., 1936, т. 13, N° 16, с. 975—979.
3.Карапетьянц М. X ., Химическая термодинамика, пзд. 2-е. М., Госхимнздат,
4. |
1953. 611 с. |
Зельвенский Я . Д ., ЖФХ, 1939, т. 13, № 4, с. 514—527. |
|
5. |
Рамм В . Л/., Абсорбция газов, нзд. 2-е, М., «Химия», 1976* 655 с. |
6 . Семенова Т. А ., Лейтес И. Л ., Аксельрод Ю . В., Очистка технологических газов. М., «Химия», 1969. 392 с.
7.Бласяк Е . и др., Технология связанного азота. Т. 1, пер. с польского. М., Госхимнздат, 1961. 623 с.
8 . Юшкевич Н. Ф., Жаворонков Н. М., Зельвенский Я . Д ., Хим. пром., 1935,
т. 12, № 5, с. 472—479; № 6 , с. 565—571.
9.Юшкевич Н. Ф., Жаворонков Н . Л/., Зельвенский Я. Д ., Хим. пром., 1936,
т. 13, № 10, с. 582-589.
10.Cooper С. Л/., Christii Р. / . , Peery L . £ ., Trans. Am. Inst. Chem. Eng., 1941, v. 37, p. 979-996.
11. |
Касаткин А. Г., |
Ципарис И. H ., |
Хим. пром., |
1952, |
№ 7, |
с. 203—210. |
12. |
Аксельрод Ю. В ., |
Дильман В. В., |
Орлов Ю. А ., |
Хим. |
пром., |
1967, № 4, |
|
с. 291—294; В кн.: Химия и технология азотных удобрений. Процессы |
и аппараты. М., ОНТИ ГИАП, 1969, с. 10—19.
13.Хоблер Т. Массопередача и абсорбция. Пер. с польского. Под ред. П. Г. Романкова. Л., «Химия», 1964. 479 с.
14. Bain W. A . t Hougen О. A ., Trans. Am. Inst. Chem. Eng., 1944, v. 40, № 1,
p. 2 9 -4 9 .
15.Коуль А. Л ., Ризенфелъд Ф. C., Очистка газа. Пер. с англ. Под ред. И. И. Аб рамсона. Изд. 2-е. М., «Недра», 1968. 392 с.
16.Pollard В ., Trans. Inst. Chem. Eng., 1957, v. 35, № 1, p. 69—75.
17. |
Pollard B., |
Ind. Chem., 1961, v. 37, |
№ |
440, |
p. 481—484. |
|
|
|
||||||
18. |
Woodburn E . Г., |
«Reactor», |
1962, |
v. 1, |
p. 22—24; |
A. I. Ch. E. Journal, |
||||||||
19. |
1974, v. 20, № 5, p. 1003—1009. |
Rec. trav. chim., |
1947, v. 6 6 , № |
1—2, |
||||||||||
Van Krevelen D. W., Hoftijzer P. / . , |
||||||||||||||
20. |
p. 4 9 -67; № 7 - 8 , |
p. 513—532. |
|
|
|
ЖПХ, |
I960, |
т. 33, |
||||||
Жаворонков H. M., |
Гильденблат И. А . у Рамм В. М.у |
|||||||||||||
21. |
№ 8 , с. 1790-1800. |
|
F. A. L.y |
Trans. Am. Inst. Chem. Eng., |
1940, |
|||||||||
Sherwood |
Т. К., |
Holloway |
||||||||||||
22. |
v. 36, № |
1, |
p. 2 1 -7 0 . |
Ind. Eng. Chem., |
Fundament., |
1963, |
v. 2, |
№ 2, |
||||||
Miyachi |
T., |
Vermeulen T.y |
||||||||||||
23. |
р. 113 -126 . |
McLean A. M ., |
Ritchie |
P . D . , |
Chem. Eng. |
Sci., |
1957, |
v. 7, |
||||||
Houghton |
J.y |
№1/2, p. 2 6 -5 0 .
24.Виноградский Б. И.у Горожанкин Э. В ., Олевский В . М.у Газ. прол**> 1965, т. 10, № 7, с. 4 9 -5 3 .
25.Пат. ГДР 40205 (1965).
26.Пат. США 3191361 (1965).
27.Пат. ГДР 28489 (1964).
28.Гильденблат И. А ., «Труды МХТИ им. Д. И. Менделеева», вып. 90, с. 70— 79; Гильденблат И. А.у Аксельрод 10. В.у Лейтес И. А . Авт. свид. № 251679; Изобр., пром. образцы. Товарн. знаки, 1969, № 28, с. 43.
29.Хуторянский Ф. М. и др.у Коллоид, журн., 1974, т. 36, № 4, с. 814—817.
30. Хуторянский Ф. И.у Аксельрод Ю. В.у Дильман В. В ., ЖПХ, 1975, т. 48,
№ 1, с. 7 2 -7 7 .
31.Фурмер Ю. В. Кандидатская диссертация. М., ГИАП, 1971.
32.Резниченко 'Е . П.у «Труды Новочеркасского политехнического института»,
1972, т. |
258, |
с. 114-120; 1973, т. 268, с. 107-120. |
33. Чернеева |
Л.у |
«Холодильная техника», 1955, т. 32, N° 4, с. 44—46. |
34.Лейбуш А. Л , Шорина Е . Д ., ЖПХ, 1947, т. 20, N° 1—2, с. 69—76.
35.Davis D. S .у Chem. Proc. Eng., 1962, v. 43, № 8 , р. 383—387.
36. Dingman J. С.у Allen D. L.y Moore T. F.y Hydrocarb. Proc., 1966» v »45, N° 9, p. 285—290.
37.Гольдман А. М.у Лейбуш A. Г., «Труды ГИАП», 1959, вып. 10, c. 54-N_82.
38.Matthews J . В.у Summer J . F.y Moelwyn-Hyghes E. A ., Trans. FaradaY Soc.,
1950, v. 46, № 10, p. 797-803. |
8 , |
39. Ахвердиев Б. А ., Бипанда С. А.у Гасанов В. А ., ЖФХ, 1973, т. 4?, |
с. 2143-2144.
40.Astarita G.y Marrucci G.y Giola F.y Chem. Eng. Sci., 1964, v. 19, № 2f P* 95— 113.
41. Emmert R. F.y Pigford R. L., A. I. Ch. E. Journal, 1962, v. 8 , № 2, P* *71 —
l75*
42.Clarke J.y Ind. Eng. Chem., Fundament., 1964, v. 3, № 3, p. 239—245.
43.Nunge R. / ., Gill W. N .t A. I. Ch. E. Journal, 1963, v. 9, № 4, p. 469 -474 .
44. Ellis J. E., Trans. Inst. Chem. Eng., 1960, v. 38, № 4, p. 216—224.
45. Lund V., Faurholt C., «Dansk Tidsskrift for Farmaci», 1948, v. 22, № 5,
p.109—123.
46.Danckwerts P. V., McNeil К. M Trans. Inst. Chem. Eng., 1967, v. 45, № 1,
p. T32—T49. |
6 |
47. Brian p . L. T., |
Vivian J. E., Matiatos D . С. A ., I. Ch. E. Journal, 1967, |
v.13, JY„ 1 , p. 2 8 -3 6 .
48.McNeil к. M., Chem. Eng. Sci., 1965, v. 20, № 8 , p. 787—788.
49.Данкдертс П. В., Газо-жидкостные реакции. Пер. с англ. М., «Химия», 1973, 296 с.
50.Астарита Д ., Массопередача с химической реакцией. Пер. с англ. Под ред.
Л. А. Серафимова. Л ., «Химия», 1971. 224 с.
51. Bates R. / . , Pinching G. D ., J. Res. Nat. Bur. Stand., 1951, v. 46, № 5,
p. 349—352.
52.Glasstone S .y Schram A . F., J. Am. Chem. Soc., 1947, v. 69, № 5, p. 1213— 1214.
53.O'Rourke С. E ., Clapp L. B., Edwards J . O., J. Am. Chem. So'c., 1956, v. 78, № 10, p. 2159-2160:
54.Hall N. F., Sprinke M. R., J. Am. Chem. Soc., 1956, v. 78, № 11, p. 2570— 2572.
55. |
Шкляр p . Л., Аксельрод IO. B .t Милоградова P. M ., Газ. |
пром., |
1972, |
|
|
№ 1, с. 39—45. |
|
|
|
56. |
Pinsent В. Я> W., Pearson L ., |
Roughton F. J. W., Trans. |
Faraday |
Soc., |
|
1951, v. 47, p. 263—269;. 1956, |
v. 52, p. 1512—1520. |
|
|
57.Danckwerts P. V., Sharma M . M ., Trans. Inst. Chem. Eng., 1966, v. 44, № 8 , р. 244—280.
58.Astarita G., Giola F., Ind. Eng. Chem., Fundament., 1965, v. 4, № 3, p. 317— 324.
59.Jorgensen E., Acta Chem. Scand., 1956, v. 10, № 5, p. 747—757,
60. Jorgensen E ., Faurholt C., Acta Chem. Scand., 1954, v. 8 , p. 1141—1148.
61.Юдина Л. A . Кандидатская диссертация. M., ГИАП, 1975.
62.Аксельрод 10. В ., Любушкина Л. А ., Лейтес И. Л . } Хпм. пром., 1969, № И ,
с.840—845.
63.Аксельрод Ю. В ., Дильман В. В ., Юдина Л. А ., Теорет. основы хим. тех-
нол., 1973, т. 7, № 3, с. 320—327.
64.Аксельрод Ю. В ., Любушкина Л . А ., Лейтес И. Л ., «Труды ГИАП», 1971, вып. 6 , с. 288—300.
65. |
Клямер |
С. Д ., Газ. пром., 1971, т. 16, № 9, с. 38—42. |
|
|
||
6 6 . |
Клямер С. Д.ч Колесникова Т. Л ., ЖФХ, 1972, т. 46, № 4, с. 1056. |
№ 2, |
||||
67. |
Клямер |
С. Д ., Колесникова Т . Л . , |
Родин Ю. А ., Газ. пром., |
1973, |
||
|
с. 44—48. |
Е. Е ., J. Chem. Eng. Data, |
1959, |
v. 4, |
||
6 8 . Jones |
J . |
Froning Н. М ., Clytor |
||||
69. |
№ 1, |
p. 85—93. |
J. Chem. Eng. Data, 1975, |
v. 20, |
№ 2,. |
|
Lee / . / . , Otto F. Z>., Mather A. E ., |
||||||
70. |
р. 161—163. |
|
|
|
||
Мурзин В. Я ., Лейтес И. Л ., ЖФХ, 1971, т. 45, № 2 , с. 417—420. |
|
|||||
71. |
Мурзин В. И., Лейтес И. Л., Тюрина Л. С., «Труды ГЙАП», 1971, вып. 10, |
с. 26—37.
72.Брандт Б . Б., Сергеев С. Я ., Веранян Р. С., Теорет. основы хим. технол.,
73. |
1970, т. 4, № 2, с. 196—203; «Труды ГИАП», 1969, вып.- 22, с. 23—35. |
|||||||
Мурзин |
В. И., |
Лейтес И. Л ., |
ЖФХ, |
1971, т. 45, |
№ 1 0 , |
с. 2642—2644. |
||
74. |
Клямер |
С. Д ., |
Лейтес И. Л ., |
Мурзин |
В. Я ., Хим. |
пром., 1972, № 1, |
||
75. |
с. 41—42. |
|
|
1946, т. 19, |
№ |
9, |
с. 869—880. |
|
Шнеерсон А. Л-, Лейбуш А. Г., ЖПХ, |
||||||||
76. |
Шнеерсон А. Л-, Лейбуш А. Г., |
ЖПХ, |
1949, т. 22, |
№ |
6 , |
с. 553—557. |
77.Afascm / . W>y Dodge В. F., Trans. Am. Inst. Chem. Eng., 1936, v. 32, № 1, p. 2 7 -4 7 .
78.Reed R. M .y Wood W. R., Trans. Am. Inst. Chem. Eng., 1941, v. 37, p. 363— 384.
79.Людковская M* А ., Лейбуш А . Г ., ЖПХ, 1949, т. 22, № 6 , с. 558—567.
80. |
Лейбуш А . 7\, Шнеерсон А. Л., ЖПХ, 1950, т. 23, № 2, с. 145—152. |
||||||
81. |
Muhlbauer //., Monoghan Р ., Oil. a. Gas. J., 1957, v. 55, № 17, p. 139—145. |
||||||
82. |
Lee J. / ., Otto F. D., Mather A. 2?., J. Chem. Eng. Data, 1972, |
v. 17, |
№ 4, |
||||
|
р. 465—468; J. Chem. Eng. Data, 1973, v. 18, |
№ 1, p. 71—73; J. Chem. |
|||||
83. |
Eng. Data, 1973, v. 18, N° 4, p. 420. |
|
|
|
|
||
Bottoms R. Я ., Ind. Eng. Chem., Ind. Ed., 1931, v. 25, N° 5, p. 501—504. |
|||||||
84. |
Riegger |
E., Tartar H. F., Lihgafelter E. C., |
J. Am. Chem. Soc., |
1944, |
v. 6 6 , |
||
85. |
N° 12, |
p. 2024—2027. |
Kindrick R. C., |
Ind. |
Eng. Chem., |
1957, |
v. 49, |
Atwood |
К ., Arnold M. Я ., |
||||||
|
N> 9, p* 1439—1444. |
1947, T. 20, № |
11, |
c. 1133—1144. |
|
|
|
8 6 . Белопольский A . 27., ЖПХ, |
|
1958, |
|||||
87. Шокип И. Я ., Оглоблина И . А ., Изв. вузов. Химия и хим. технол., |
|||||||
|
N° 1 , с. 108—118; N° 2, с. 96—105. |
|
|
|
|
8 8 . Дилъман В. В,, Гаркавый А. Я ., Аксельрод Ю. Я., Хим. пром., 1975, № 9,
с. 691—694.
89.Аксельрод 10. В . и др. Авт. свид. N° 319548; Открытия. Изобр. Пром. образцы.
Товарн. знаки, 1971, № 33, с. 6 6 .
90.Аксельрод 10. В. и др., «Труды ГИАП», 1972, вып. 17^ с. 47—59.
91.Богословский 10. Я ., Фурмер Ю. В., Хуторянский Ф. М ., Азотная пром., 1973, N° 3, с. 39—42.
92.Аксельрод Ю. В., Дилъман В. В., Тителъман Л . И., Хим. и нефт. машино строение, 1970, № 6 , с. 15—16; «Труды ГИАП», 1971, вып. 6 , с. 261—272.
93.Алекперова Л. Я. Кандидатская диссертация. М., ГИАП, 1975.
94. |
Дилъман Я. Я., Аксельрод Ю. Я., Алекперова Л, Я., |
Хим. |
пром., |
1967, |
||||
95. |
N° 7, с. 532—537. |
Газ. пром., |
1972, т. 17, |
№ |
10, |
с. 39—42. |
||
Шкляр Р. 27., Хейнман Я. Я ., |
||||||||
96. |
Клямер С. Д . 1 Шкляр Р. 27., Хейнман Б. Я ., |
Газ. пром., |
1971, |
т. 1б, |
N° 4, |
|||
97. |
с. 34—36. |
ЖПХ, 1950, т. 23, |
N° 11, |
с. 1176—1186. |
||||
Лейбуш А. Г ., Шнеерсон А . 27., |
98.Горожанкин Я. Я., Кандидатская диссертация. М., ГИАП, 1967; В кн.: Химия и технология азотных удобрений. Процессы и аппараты. М. ОИТИ ГИАП 1969 с. 5_10.
99.Kohl A. L ., А Л . Ch. Е. Journal, 1956, v. 2, р. 264—271.
100.Kondo Я ., Fukuba К ., Chem. Eng. (Japan), 1958, у. 22, № 10, p. 6lO—617.
101. Gryder D. Я., Maloney J. O., Trans. Am. Inst. Chem. Eng., 1941 v 3 7 ,
р.827-834.
102.Teller A. L., Eord H. 2?., Ind. Eng. Chem., 1958, y. 50, N° 8 , p. 120i__l206.
103. |
Benson Я . E.y |
Field / . 27., Haynes |
W. P ., |
Chem. Eng. Progr., |
1956, |
v |
52, |
|
104. |
N° 10, |
p. 433 |
-438 . |
R. M ., |
Chem. Eng. Progr., |
1954 |
v |
50 |
Benson |
H. 2?., |
Field / . Я ., Jimeson |
N° 7, p. 356—364.
105.Аксельрод Ю. Я., Дилъман Я. Я., Фурмер Ю. Я., Теорет. основы хим. технол., 1973, т. 7, N° 5, с. 683—689.
106. |
Шкляр |
Р. 27., |
Аксельрод Ю. Я., Хим. |
пром., 1972, |
N° 3, |
с. 198—202. |
|
107. |
Хазан |
Р. М., |
Кандидатская диссертация. Л., ЛТИ, 1973. . |
|
|
||
108. |
Гридин Я. Д. и др., Хим. пром., 1968, № |
10, с. 26—30; № 11, с. 8 4 4 —g4 g. |
|||||
|
В кн.: Производство аммиака и азотной кислоты. Ташкент, изд. и^СТИТуТ£[ |
||||||
|
научно-технической информации УзССР, 1965, с. 133—139. |
|
|
||||
109. Гридин Я . Г.у Хим. пром., 1974, № 10, с. 786—787. |
|
|
|
||||
НО. Stage Я ., Chem.-Ing. Techn., 1970, Bd. 42, № 9/10, S. 669-673. |
|
||||||
111. |
Соломаха Г. Я ., Чехов О. С., Гореченков Я. 71., Авт. |
свид. |
№ 291718* |
||||
112. |
Открытия. Изобр. Пром. образцы. Товарн. знаки, 1971, № 4, с. 1§. |
’ |
|||||
Delnicki W. F., Wagner Г. Z., Chem. Eng. Progr., 1970, v. 6 6 , № 3, p, 50-^55. |
113.Белозеров П. А ., Чехов О. Я., Боярчук П. Г . Авт. свид. № 194764; Изобр пром. образцы. Товарн. знаки, 1967, № 9, с. 33.
114. |
Кочереин Н. А ., Казанский Я . Л7., Шульц Э. 3., Хим. пром., |
1963 |
jvfo \\ |
|
115. |
с. 66—69. |
' ’ |
' |
’ |
Дилъман Я. Я., Канун Д . Я., Аксельрод Ю. Я. В кн.: Массообменцые |
Пт)0_ |
|||
|
цессы химической технологии. Под ред. П. Г. Романкова. |
Выц |
з # |
|
|
«Химия», 1968, с. 145—146. |
’ |
|
*’ |
116.Ходак Я . А ., Лянная Г . Г ., Кривенко И. П. В кн.: Тезисы докладов Всесоюзной конференции по технологии неорганических веществ. Киев, 1966, с. 182—183.
117.Вуреафт Г. Б ., Канун П . Е ., Койда А . ЛГ. Авт. свид. № 193462 (1966);
Изобр., пром. образцы. Товарн. знаки, 1967, № 7, с. 28; Фурманов А . С.,
/Зуее А. А ., Кудиров Т. И ., Кузнецов А . С. Авт. свид. № 386838 (1972); Открытия. Изобр. Пром. образцы. Товарн. знаки, 1973, № 27, с. 51.
118. Дащков А . 5 ., Бондаренко М. Я ., Азотная пром., 1967, № 3, с. 17—23.
119.Лейтес И . Я ., Веранян Р. С., Брандт Б . Я ., Авт. свид. № 284969; Открытия. Изобр. Пром. образцы. Товарн. знаки, 1970, № 33, с. 20; Лейтес И. Л ., Брандт Б. Б ., Веранян Р. Б., Теорет. основы хим.технол.,
|
1972, т. 6, № 1, с. 29—36; Лейтес И . Я ., Веранян Р. С., Брандт Б. Б ., |
||||||
120. |
Хим. пром., 1972, № 2, с. 120—123. |
«Труды ГИАП», |
1972, |
||||
Веранян Р. Б., |
Лейтес И . Я ., |
Брандт Б . Б ., |
|||||
121. |
вып. 17, с. 5—46. |
|
Газ. пром., |
1976, |
№ |
4, |
|
Селщкий А . Я ., Нощенко И. К Л е й т е с И. Л. , |
|||||||
122. |
с. 41—43. |
Шкляр Р. Я ., |
Волошин В . Я ., Хнм. пром., |
1967, |
№ |
8, |
|
Клямер С. Д ., |
с. 50—54.
123.Лейтес И. Л ., Дымов Б. Б ., Карпова Ю. Г., Теорет. основы хим. технол., 1976, т. 10, № 5, с. 678 -690 .
124. Пименова Т. Ф., Гродник Я. Г., «Холодильная техника», 1964, № 3,
с. 47—49.
125.Лейщес Я. Я ., Брандт Б. Б ., Сичкова О. Я ., Хим. пром., 1968, № 9,
с. 22—26.
126.Клямер С. Д ., Кандидатская диссертация. М., МХТИ им. Д. И. Менде
леева, 1971; Клямер С. Д . и 5р., |
«Труды |
ГИАП», 1972, выл. 17, с. 60— |
76. |
Уварова |
В. И., Хим. пром., 1968, № 11, |
127. Гридин И. Д ., Афанасьев Я . А ., |
с.44—46.
128.Брандт Б . Б ., ВераНян Р. С., Лейтес Я . Я ., «Труды ГИАП», 1972, вып. 17,
с.29—46.
129.Matsuda М., Bull. Chem. Soc. (Japan), 1961, v. 34, № 11, p. 1665—1668.
130.McKeown К . / . , «Nitrogen», 1976, v 499, p. 28—32.
131. |
Дилъмен Б . Б ., Брандт В . Б ., |
Веранян Р. Б., «Труды |
ГИАП», 1971* |
||
132. |
вып. 6, |
с. 279—289. |
р. 241. |
|
|
Petrol. |
Ref., |
1965, v. 44, № 2, |
т. 43, вып. 3, |
||
133. |
Данов С. М ., |
Матин Я . Б ., Ефремов Р . Б ., ЖФХ, 1969, |
|||
|
с. 733—739; Матин Я . Б ., Данов Б. М ., Ефремов Р . Б ., «Кинетика и ка |
||||
|
тализ», |
1969, |
т. 10, вып. 4, с. 749—754. |
|
134.Polderman L., Dillon Б., tfteeZ A ., Oil a. Gas J., 1955, v. 54, № 2, р. 180— 182-
135.Яавикова Я . Б ., Кандидатская диссертация. М., ГИАП, 1972; Богослов
|
ский Ю. Я . и др., |
«Труды |
ГИАП», 1972, вып. 17, с. 176—186; |
Язви- |
||
|
кова Н. Б ., Зеленская Я . Р ., |
Балясникова Л . Б ., ЖПХ, 1975, т. 48, № 3, |
||||
|
с. 674—676; Язвикова Я . Б ., Лейтес Я . Я ., Сухотина А . Б., Хим. пром., |
|||||
136. |
1977, № 3, с. 185—188. |
|
Г . Б ., Хим. пром., 1972, № 11, с. 830—834 |
|||
Левкович |
М. М ., |
Колесникова |
||||
137. |
B e r l i e Б., |
PsZZer / . , |
Ronicher Б., |
Chem. Eng. Progr., 1965, v. 61, |
№ 4, |
p.82—85.
138.Scheiman M. A ., Review of MEA Chemistry. Washington, U. S. Department of Commerce Office of Technical Services, 1962. 51 p.
139.Левпович M. M, и dp., Хим. пром., 1966, № 11, с. 32—35.
140.Лейбуш А . Г., Гольдман А . М ., ГрузинцеваА . Я ., «Труды ГИАП», 1957, вып. 8, с. 124—144.
141.Струнина А . Б ., Зелъвенский Я . Д ., Ивановский Ф. Я ., «Труды ГИАП», 1957, вып. 7, с. 195—212.
142. |
Leach-man |
Б., БШя Б., Oil. a. |
Gas J., 1961, v. 59, № 30, р. 84—88. |
|
143. |
Riesenfeld |
F. Б., Kohl |
R. Б., Gas |
Purification. Ed. 2nd. Houston, Grulf |
|
Publishing |
Company, |
1974. 620 p. |
|
144.Баранов' С. Я ., Фуменко В. Я ., Швайко О. Я . Вопросы химии и хим. технол. (Республ. межвед. тем. научно-техн. сб.), 1973, вып. 31, с. 14—19.
145. |
Ballard Я ., |
Petrol. |
Ref., |
1966, v. 45, N° 4, р. 137—142. |
|
|
||||
146. |
Comeaux i?., |
Petrol. |
Ref., 1962, v. 41, N° |
5, p. 141—144. |
ГИАП», |
1973, |
||||
147. |
Бурцева И. Я., |
Левин И. А ., Швыдкий С. X ., |
«Труды |
|||||||
|
вып. 17, с. 30—39; Швыдкий С. X . и др., |
«Защита металлов», 1974, |
№ 4, |
|||||||
148. |
с. 410-413. |
|
Меренков П. Г., |
Гречко |
И. Г ., |
Азотная |
пром., |
1967, |
||
Кальман Л. А., |
||||||||||
149. |
N° 3, с. 70—81. |
|
Mat. |
Protect., 1966, |
v. 5, № |
8 , p. 25—27. |
|
|||
Oakes i?., Hager М ., |
|
|||||||||
150. |
i?oss 7\, Plarson |
C., |
Gorros. Sci., |
1964, v. 4, p. 449—451. |
|
|
151.Корягина Л. А ., Хим. пром., 1967, № 3, с. 73.
152.Butwell К. F., Hawkes E. Я ., Mago B. F.y Chem. Eng. Progr., 1973, v. 69, N° 2 , p. 57—60.
153.Ewing Я ., Oil a. Gas J., 1967, v. 65, № 44, p. 125—129.
154. |
Bienstock Я ., Field / . , |
«Corrosion», 1961, v. 17, № 12, p. 87—91. |
155. |
«Corrosion prevention», |
1960, v. 7, № 5, p. 36—38; Oil a. Gas J., 1961, v. 59, |
156. |
N° 6 , p. 138. |
Mat. Protect., 1963, v. 2, № 8 , p. 26. |
Mottey /., Fincher Я ., |
157.Hall Я ., Polderman L., Chem. Eng. Progr., 1960, v. 56, № 10, p. 52—56.
158.Попова К. Л ., «Холодильная техника», 1957, № 1, с. 39—43; Попова К. А ., Тезиков А. К., там же, 1959, № 1, с. 56—60.
159.Blashly С., Ravner Я ., J. Chem. Eng. Data, 1966, V. 11, № 3, р. 401—403.
160. |
Перин Ю. Я ., |
Хим. |
пром., |
1967, N° 12, с. 50—51. |
161. |
Oil a. Gas J., |
1966, |
v. 64, |
N° 6 , р. 138—142. |
162. |
Быков С. Т. и |
др., |
Азотная |
и кислородная пром., 1964, № 2, с. 17—20. |
163.Канун Я. Е. и др.у Азотная пром., 1968, № 2, с. 5—11.
164.Егоров В. Я. и др.. Азотная пром., 1968, № 2, с. 11—19.
165.Гринберг Я ., «Холодильная техника», 1954, № 1, с. 67—69.
166. Shell А.у Oil a. Gas J., 1968, v. 6 6 , N° 9, р. 87—88.
167.Мухаметзянов X. X ., Язвикова Я . В ., Канун Я . Я., В кн.: Химия и тех нология азотных удобрений. Очистка газов. М., изд. ОНТИ ГИАП, 1969,
с.5—14.
168. |
Кравченко Б. В.у Кривенко И. Я ., Ляшенко А. И.у Азотная |
пром., |
1973, |
169. |
N° 4, с. 1—2. |
пром., |
1973, |
Романенко Л. И.у Цикоза В. Я., Некрушец Я. Я ., Азотная |
|||
|
N° 5, с. 21—22. |
|
|
170.Смит Р. Ф.у Янгер А. X.у «Инженер-нефтяник», 1972, № 7—8, с. 104— 107.
171. |
Ильина Я. Я ., |
Клямер С. Д. |
Извлечение |
сероводорода и |
углекислоты |
|||
|
из природного газа п производство элементарной серы. Обзор. М., ЙНИИ- |
|||||||
172. |
газпром, 1969. |
46 с. |
1970, |
v. |
6 8 , |
N° |
18, p. 136—141. |
|
Dailey L. W., Oil a. Gas J., |
|
|||||||
173. |
Klein J. P.y Oil a. Gas J., 1970, v. 6 |
8 , |
№ |
9, p. 109—110. |
|
|||
174. |
Klein J . P.y «Erdol und Kohle», 1970, Bd. 23, N° 2, S. 84—89. |
|||||||
175. |
Валитов P. Я., |
Гарифзянов |
Г. Г ., |
Морозов 10. Д ., Хим. |
пром., 1971» |
|||
|
т. 47, N° 7, с. 506—508. |
|
|
, |
|
|
|
176.Аксельрод 10. В.у Лейтес И. Л.у Дильман В . В. Авт. свид. № 486767 (1973); Открытия. Изобр. Пром. образцы. Товарн. знаки, 1975, № 37, с. 14.
177. Giavarini G., Maura G.y Rinaldi G.y Chim. e. Ind. (Milan), 1973, v. 55 |
No 1, |
p. 2 3 -2 6 . |
’ " |
178.Weiland R. Я ., Trass O., Can. J. Chem. Eng., 1971, v. 49. N° 6 , p. 767—769.
179.Подвигайлова И. 71., Зейналов Б. К.у Кругликов А. А. и др.у Хцм. nnoi^.,
1970, N° 5, с. 338 -339 . |
* |
180.Фурмер Ю. В.у Хуторянский Я. М.у Морозов А. И. Авт. свид. № 476014 (1973); Открытия. Изобр. Пром. образцы. Товарн. знаки, 1975, N$ 25 с. 14.
181.«Инженер-нефтяник», 1973, N° 4, с. 87—132.
182.Chem. Week, 1968, v. 103, N° И , р. 63.
183. |
Mason J. R . у Griffith |
T. Я., Oil a. Gas J., 1969, у» 67, N° 23, p. § 7 7 1 , |
184. |
Пат. США 3681015 |
(1970). |
185.Пат. США 3352631 (1964).
186.Frazier / . , Hydrocarb. Proc., 1970, v. 49, № 4, p. 101—109.
187. Dunn C., Freitas E ., Petrol. Ref., 1964, v. 43, № 3, p. 150—154; Dunn C.
e. a., Hydrocarb. Proc., Petrol. Ref., 1965, v. 44, № 4, p. 137—140.
188.Chem. Eng. News, 1964, v. 42, № 20, p. 50—51.
189.Herault E., «Revue de produits cliimiques», 1964, v. 67, № 1320, p. 173—175; № 1321, p. 235-241.
190. Lamanna U., Seiacovelli 0 ., Lanelli L., Gazz.* Chim. Ital., 1964, v. 94,
№5, p. 567-570.
191.Пат. США 316146 (1964).
192.Goar В ., Oil a. Gas J., 1969, v. 67, № 26, p. 117—120.
193.Hydrocarb. Proc., 1971, v. 50, № 4, p. 120.
194.Bratzler K., Doerges A ., Hydrocarb. Proc., 1974, v. 53, № 4, p. 78—81.
195.Woertz В. B., Can J. Chem. Eng., 1972, v. 50, № 1, p. 425—429.
196.Англ. пат. 1058304 (1965).
197.« Sulphur», 1972, № 103, p. 43—45.
198. Лейтес И. Л ., |
Сичкова О. П ., Шинелис А. Ф., Хим. пром., 1972, |
№ 4, |
|
с. 263—267; Сичкова О. /7., Шинелис А . Ф., Лейтес И . Л ., «Труды ГИАП», |
|||
1972, выл. 14, |
с. 66—77; Лейтес И . Л ., Дымов В. Е ., Селицкий А . 77., |
Хим. |
|
пром., 1975, № |
8, |
с. 599—602; Дымов В . 7?., Лейтес 77. 77., Мурзин В . 77., |
|
Хим. пром., 1976, |
№ 3, с. 41—44. |
|
199.Kutscher G., Smith G., Greem P ., Oil a. Gas J., 1967, v. 65, № 12, p. 116—118.
200.Пат. США 3352631 (1967).
201.Hydrocarb. Proc., 1971, v. 50, № 4, p. 93—122.
202. Пат. США 3377138 (1966); Badger M., VFiZsora 7)., J. Soc. Chem. Ind., 1947,
v. 66, № 3, p. 84—86.
203.Norman W., Absorption, Distillation and Cooling Towers. New York, Long mans, 1961. 450 p.
204.Bhargava D ., Brit. Chem. Eng., 1960, v. 5, № 5, p. 320—325.
205.Ганг С. H. и dp., ЖПХ, T . 32, № 5, c. 969—981.
206.Muddox 7?., Burns Л7., Oil a. Gas J., 1967, v. 65, № 41, p. 167—170.
207. |
'Bocard 7., |
Maylard В ., Petrol. Ref., Hydrocarb. |
Proc. 1962, |
v. 41, |
№ 4, |
. p. 128—132. |
7 |
Хим. пром., |
1965, |
№ 5, |
|
2 0 8 Людковская |
M. А ., Фридман С. Д ., Клевке В. А ., |
||||
fc |
4i9 _23. |
|
|
|
|
209ABuck Я . ,‘Leitch A., Petrol. Ref., 1958, v. 37, № И , p. 241—246. 210$Goolsbee / . , Petrol. Ref., 1960, v. 39, № 1, p. 159—160.
211.- Oil. a. Gas J., 1968, v. 56, № 6, p. 98—99.
212.Eickmeyer A ., Oil a. Gas J., 1958, v. 56, № 38, p. 106—108.
213.Katell S ., Faber / . , Petrol. Ref., 1960, v. 39, № 3, p. 187—189.
214. Карпова Ю . 71., Кандидатская диссертация. M., ГИАП, |
1972; |
Кар |
|
пова Ю. 7\, Лейтес 77. Л., Воскресенская Н. £ ., «Труды ГИАП», |
1972, |
||
вып. 17, |
с. 95—124; Соколов В. Е., Лейтес И. Л ., там же, |
с. 156—165; |
|
Карпова |
Ю. Г., Лейтес И. 77., Воскресенская Н. С., Газ. |
пром., |
1971, |
№ 8, с. 35—39.
215.Benson 77. Е., Parrish 7?. W., Hydrocarb. Proc., 1974, v. 53, № 4, p. 81—84.
216.Ruziska P. A ., Chem. Eng. Progr., 1973, v. 69, № 2, p. 67—69.
217.Thirkell 77., Hydrocarb. Proc., 1972, v. 51, № 1, p. 115—118.
218.Итал. пат. 545908 (1956).
219.Roberts D ., Danckwerts P.\ Chem. Eng. Sci., 1962, v. 17, № 12, p. 961—970.
220.Зельвенский Я. Д ., Соколов В. Е. В кн.: Химия и технология азотных удоб рений. Очистка газов. М., изд. ОНТИ ГИАП, 1965, с. 27—35; Те же, «Труды ГИАП», 1969, вып. 22, с. 36—38.
221.Jenett Е ., Oil a. Gas J., 1962, v. 60, № 18, р. 72—77.
222.Newling W., Marsh / . , Inst. Gas Eng., 1963, v. 3, № 3, p. 143—148.
223. |
Riesenfeld F,, Mullowney / . , |
Petrol. |
Ref., |
1959, v. 38, № 5, p. 161—168. |
224. |
Hoogendorn / . , Trans. Inst. |
Chem. |
Eng., |
1963, v. 41, № 8, p .264 —271. |
225.Англ. пат. 967044 (1964); пат. США 3264056 (1&66).
226.Англ. пат. 819215 (1959); белы. пат. 572242 (1962); пат. ФРГ 1077201 (1960).
227. Chem. Techn., 1972, Bd. 24, S. 7 4 -7 6 .
228.Пат. США 3714327 (1969).
229.Fert. News, 1973, v. 18, № 9, p. 20—22.
230. Hydrocarb. Proc., 1975, y. 54, Ns 4, p. 7 9 -1 3 5 .
231.Hurdy O,, Morse R ., «Nitrogen», 1968, № 51, p. 33—34.
232.Muddox R . x Burns M., Oil a. Gas J., 1968, v. 66, № 4, p. 91—94.
233.Пат. США 1201942, 1201943, 1202433 (1959); 3743699 (1971).
234. Шахова С. Ф., Бондарева Т. И ., Зубченко 10. Я ., Хим. пром., 1966, № 10,
с. 753-754.
235.Kohl А ., Buckingham Р ., Petrol. Ref., 1960, v. 39, № 5, р. 193—197.
236.Riesenfeld F., Blohm C.y Petrol. Ref., 1962, v. 41, Ns 4, p. 123—127.
237.Buckingham P ., Petrol. Ref., 1964, v. 43, № 4, p. 113—116.
238.Cook T., Tennyson F .y Chem. Eng. Progr., 1969, v. 65, № 11, p. 61—64; Speel £ ., «Erdol und Kohle», 1969, Bd. 22, № 9, S. 487.
239.Каплан Л. К ., Шахова С, Ф., Хим. пром., 1975, №,4, с. 37—40.
240. Шахова С. Ф., Зубченко Ю. Я ., Каплан Л . if., Хим. пром., 1973, Ns 2,
с.108-110.
241.Дин Взйу Тительман Л . Я ., Азотная пром., 1968, № 5, с. 5—8.
242. Дин Вэй у Шахова С. Ф., Газ. пром., 1969, JVs 2, с. 40—43.
243.Ring Т.у Mann W., Chem. Eng. Progr., 1970, v. 66, Ns 12, p. 59—63.
244.Англ. пат. 1257743 (1971).
245.Пат. США 3699218 (1972).
246. Kohrt Н.у Thorman К., Bratzler K . t «Erdol und Kohle», 1963, Bd. 16, Ns 2,
S.9 6 -9 9 .
247.Beavon D. K ., Roszkowsky T. Я ., Oil a. Gas J., 1969, v. 67, № 15, p. 138— 140.
248. Beavon D* К.у Roszkowsky T. Я ., Parsons R . ikf., Chem. Proc. Eng., 1972,
v. 53, № 1, p. 32—33.
249.Пат. ФРГ 1209559 (1966).
250.Chem.-Ing. Techn., 1967, Bd. 39, Ns 5/6, S. 198—202.
251.Пат. США 3266219 (1966).
252.Пат. США 3214892 (1965).
253.Oil a. Gas J., 1972, у. 70, Ns 47, p. 84.
254. |
Hegwer A. M.y Harris Я. A ., Hydrocarb. Proc., 1970, v. 49, |
№ |
4, p. Ю З - |
255. |
104. |
|
|
Пат. США 3594985 (1971). |
11, |
с. 48—50» |
|
256. |
Лейтес И. Л.у Адливанкина М. А. у Хим. пром., 1966, № |
257.Шендерей Е. Р ., Зелъвенский Я . Д.у Ивановский Ф. Я ., «Труды ГЙАП», 1960, вып. 11, с. 162— 164; Шендерей Е. Р ., Зелъвенскпй Я . Д ., Хим. пром.,
1959, № 4, с. 50—53; 1961, № 5, с. 13—16; Шендерей Е. Р ., Зелъвипский Я . Д.у Ивановский ф. Я ., Газ. пром., 1961, № 3, с. 42—45.
258. Зелъвенский Я . Д.у Струнина А . В.у Газ. пром., 1960, Ns 2, с. 47—50.
259.Herbert W., «Erdol und Kohle», 1956, Bd. 9, Ns 2, S. 77—81.
260.Karwat E.y Kruis Я ., «Linde-Berichte aus Technik und Wissenschaft», 1958,
Ns 3, S. 3 3 -3 8 .
261.Косяков Я . E . y Иванова A. C., Чоботъко Л . Л . у Хим. пром., 1974, Ns 6,
22_33
262.Ranke G.y Chem. Economy a. Eng. Rev., 1972, y. 4, № 5, Ns 49, p. 25—31.
263.Гелъперин И . И.у Никифоров Я. А ., Газ. пром., 1961, Ns 4, с. 39~^-45.
264.Безделъ Л . С., Теодорович В . Я ., Газ. пром., 1958, Ns 8, с. 38—43.
265.Газ. пром., 1956, Ns 9, с. 32—39.
266.Меркель Ф., Бошнякович Ф., Расчет абсорбционных холодильные маттшн. М., Госмашметиздат, 1934, 74 с.
267.Fauser G.y Chim. et Ind., 1951, v. 33, Ns 4, p. 393—396.
268.Wittman E.y Chem.-Ing. Techn., 1956, Bd. 28, Ns 1, S. 59.
269.Linton J.y Tusdall G.y Coke a. Gas, 1958, v. 20, Ns 227, p. 148—1$2.
270.Nelson W.y Oil. a. Gas J., 1955, v. 53, Ns 43, p. 134—138.
271. Боровик В.у Мирошниченко В.у Азотная пром., 1969, Ns 7, с. 5 Ю.
272.Лейтес И. Л.у Карпова Ю. Г.у Бродянский В. М.у Теорет. основы хим. технол., 1973, т. 7, Ns 1, с ..24—29.
273.Карпова Ю . Г.у Лейтес И. Л.у Газ. пром., 1971, № 10, с. 33—38.
КАТАЛИТИЧЕСКИЕ И АДСОРБЦИОННЫЕ МЕТОДЫ ОЧИСТКИ ГАЗОВ ОТ СЕРНИСТЫХ
СОЕДИНЕНИЙ
1. ОЧИСТКА ОТ СЕРОВОДОРОДА
Очистке от соединений серы (в первую очередь от сероводорода) подвергаются такие горючие газы, как коксовый, генераторные, природный и др. Содержание серы в промышленных газах колеб лется в довольно широких пределах (от 2-10“ 6—5-10" 6 кг/м3 до 2,5 • 10“ 2—4,0 -10“ 2 кг/м3) и зависит от качества сырья и способа получения газа.
Присутствующие в технологических газах серосодержащие со единения считаются вредными примесями, вызывающими коррозию трубопроводов и аппаратуры^ отравление катализаторов, ухудше ние качества продукции и загрязнение атмосферы. Поэтому очистку газа от серы необходимо проводить на самой ранней стадии его переработки.
Очистку горючих газов от сероводорода осуществляют активи рованными углями и другими твердыми поглотителями, активной
составной частью которых являются окислы железа, |
цинка, |
меди. |
|||
В зависимости от требуемой стец_ени очистки газа условно |
раз |
||||
личают грубую |
(1 • 10” 3 кг/м3), среднюю |
(2,0 -10“ 6 кг/м3) и тонкую |
|||
(1 • 10” 6 |
кг/м3) |
очистку. Тонкая очистка |
достигается |
главным об |
|
разом в |
многоступенчатом процессе. |
|
|
|
Выбор способа очистки зависит от состава, объема очищаемого газа и требований к степени его очистки. Обычно сухие способы очистки от сероводорода применяют при небольшой концентрации
его в газе — до |
0,5 • 10“ 3—1,0 • 10” 3 кг/м3 (максимум до 1,0 • 10” 3— |
1,5* 10"3 кг/м3). |
Достоинство этих методов очистки заключается |
в том, что они обеспечивают высокую степень очистки и являются селективными, в результате чего содержащаяся в газе двуокись углерода не удаляется при очистке от H 2S и не влияет на этот процесс. Поглотительный метод очистки газа основан на взаимодействии сернистых соединений с твердыми поглотителями*
ОЧИСТКА ПОГЛОТИТЕЛЯМИ НА ОСНОВЕ ОКИСИ ЖЕЛЕЗА
Процесс очистки |
газа поглотителями на |
основе |
окиси же |
леза является одним |
из старейших способов |
удаления |
сернистых |
соединений из промышленных газов [1—7] и основан на следующих
реакциях:
Fе20 3т 3H2S = Fe2S3+ ЗН2О
2Fe2S3+ 302= 2Fe20 3 + 6S
Приведенные уравнения представляют действительный механизм процесса в несколько упрощенном виде, в зависимости от условий которого могут протекать и другие многочисленные реакции.
После полного насыщения окиси железа серой ее извлекают сжиганием этой насыщенной поглотительной массы с последующей переработкой образующегося сернистого ангидрида в серную ки слоту. Регенерацию очищенной массы можно производить одно временно с очисткой газа при условии, что к нему добавлен воздух или кислород.
Существует несколько модификаций окиси железа, однако для
приготовления |
очистной |
массы [5] можно применять только а- |
и y-F^CVHgO . |
а-Форма |
содержится в болотной руде, у-форма |
входит в состав так называемого красного шлама — отхода про изводства глинозема из бокситов. Обе модификации окиси железа быстро взаимодействуют с сероводородом, а образующийся сульфид трехвалентного железа снова легко превращается в активную форму Fe20 3.
Скорость реакции поглощения сероводорода зависит от доступ ности поверхности окиси железа и, следовательно, от пористости поглотительной массы 18]. Поскольку мольный объем Fe20 3*H20 больше объема Fe20 3-H 20 , поглотительная масса должна иметь пористость не менее 50%.
Установлено [9], что гидроокиси железа при выделении из рас творов представляют собой в основном мелкокристаллический ге матит с примесью аморфной гидроокиси железа. При длительном хранении поглотительные свойства гидроокисей ухудшаются вслед ствие образования крупнокристаллического гематита с понижен ными пористостью и удельной поверхностью.
В состав поглотительной массы входят 95,5% (масс.) болотной руды, 4,0% (масс.) древесных опилок, 0,5% (масс.) извести. Перед загрузкой массу равномерно смачивают до содержания 30—40% влаги.
Сероводород связывается активной составной частью болотной руды — гидроокисью железа до сернистого железа:
ori2s + 2Fe (ОН)3 ---- у Fe2S3+ 6H20 + 62,5 кДж/моль (14,9 ккал/моль)
Оптимальные условия поглощения сероводорода: температура 28—30 °С, влажность массы не менее 30%.
После насыщения поглотительную массу регенерируют кисло родом воздуха в присутствии водяного пара. При этом железо пре вращается в гидроокись с выделением элементарной серы, которая постепенно отлагается в очистной массе:
2Fe20 3+ 302 + 6Н20 = 4Fe(OH)3 + 6S + 606,0 кДж/моль (145 ккал/моль)
Объем подаваемого на регенерацию воздуха (кислорода) регу лируют в зависимости от температуры и содержания кислорода в оборотном газе. Очистная масса считается отработанной, если содержание серы в ней достигает 50% (в пересчете на сухую массу). Сера, накапливающаяся в очистной массе, постепенно обволаки вает частицы активного Fe(OH)3 и затрудняет доступ к ним серо водорода. Отработанный поглотитель заменяют свежим и отпра вляют на сернокислотные заводы для обжига.
Рис. V-1. Принципиальная схема ящично-башенной установки:
I — I V — очистные башни; 1 — ротационная воздуходувка; 2 — гидравлический затвор возду ходувки; 3 — газодувки; 4 — предохранительный гидрозатвор; 5 — газовый охладительный скруббер; 6 — циркуляционная газодувка; 7 — скруббер регенерации; 8 — газовые гидро затворы.
Для регенерации очистной массы можно применять следующие способы:
окисление выгруженной массы кислородом воздуха; продувку через отключенный аппарат газовоздушной смеси,
содержащей 2—3%. кислорода; непрерывную регенерацию массы с добавлением в газ такого
объема воздуха, чтобы содержание кислорода в смеси в 1,5 раза превышало теоретически необходимое для окисления; при этом регенерация протекает одновременно с поглощением сероводорода.
Установки для очистки газа болотной рудой несложны и состоят обычно из четырех последовательно включенных по ходу газа аппа ратов, в каждом из которых находится несколько слоев очистной массы. Газ входит в аппарат параллельными потоками. Как правило, требуемая степень очистки достигается после третьего аппарата; четвертый поглотитель — контрольный. Система газоходов и газо вых затворов позволяет включать любой из аппаратов первым по ходу газа, а также отключать любой из них для регенерации или пере грузки очистной массы. Технологическая схема процесса показана на рис. V-1.
Установка для очистки больших объемов газа может состоять из двух и более параллельно включенных комплектов очистных аппаратов.
19 Заказ 1400 |
289 |
В зависимости от конструкции аппаратов системы очистки можно разделить на ящичную, ящинно-башенную и башенную.
Наиболее распространена башенная система. В каждой башне устанавливают 10—12 съемных корзин-царг круглой или много угольной формы с решетками для загрузки массы (2 слоя по 400 мм) (рис. V-2).
Для максимального насыщения массы серой башни переключают по ходу газа через определенные промежутки времени. Башню, предназначенную для регенерации, отключают от общего газового по тока. В таких условиях регенерация может проходить при более высокой температуре (до 40 °С) и повышенной концентрации кислорода в оборотном газе, что позволяет увеличить произ
водительность установки.
|
Применение |
болотной |
руды |
обес |
|||||||
|
печивает |
очистку |
газа |
от сероводо |
|||||||
|
рода |
до |
2,0 *10" 5 |
кг/м3. К недостат |
|||||||
|
кам |
метода |
относятся |
громоздкость |
|||||||
|
установки, |
значительные |
капитало |
||||||||
|
вложения, трудоемкая |
разгрузка от |
|||||||||
|
работанной |
массы из царг. В связи с |
|||||||||
|
этим сухую |
очистку применяют, |
как |
||||||||
|
указывалось |
выше, |
при |
низком со |
|||||||
|
держании сероводорода в газе. При |
||||||||||
|
высокой |
концентрации |
газ предва |
||||||||
Рис. V-2. Башня для сухой очист |
рительно очищают в одной из жид |
||||||||||
костных |
систем. |
|
|
|
|
|
|||||
ки газа окисью железа: |
|
|
|
|
|
||||||
Подробное |
описание технологиче |
||||||||||
1 — очистная масса; 2 — опорные ре |
|||||||||||
ских систем |
и |
комбинированных ус |
|||||||||
шетки. |
|||||||||||
|
тройств |
очистных |
установок |
при |
|||||||
|
ведено в литературе |
[2, 5]. |
|
Почти на всех работающих установках очистку газа гидроокисью железа проводят при давлении газа, близком к атмосферному, однако в случае необходимости процесс можно вести и при повы
шенном давлении. |
|
|
Для удаления сероводорода из газов |
коксовых печей в |
одном |
из вариантов применяют железную руду |
с добавками щелочи |
[10]. |
Показано [11|, что полная очистка газов от сероводорода (содержа ние его 33 • 10~3 кг/м3) достигается при использовании смеси катионита КУ-2 и гидроокиси железа Fe(OH)3. Отношение объема -газовой смеси к весу катионита равно 2 : 1 .
В работе [12] рассмотрены вопросы сероочистки газов с помощью железной руды при температуре 355—800 °С и содержании серово дорода 0,41—0,46% (об.). Установлено, что стационарный процесс сероочистки в слое протекает в диффузионной области. Достигалась 50%-ная степень использования руды.
Адсорбент может содержать железо и марганец (— по 5% (масс.) каждого [13]), а также смесь окиси железа с летучей золой [14].
Предложено также использовать для очистки [15] взвешенный слой Fe20 3 или Мп20 4 при 320—400 °С. Содержание серы в очист ных массах поддерживают не более 10%, для чего осуществляют непрерывную циркуляцию поглотителя через регенератор и адсор бер с определенной скоростью. Содержание сероводорода в очищен ном газе менее 1 см3/м3 (1 -10“ 3 м3/м3).
Имеются сведения [16], что активность железосодержащей массы
при |
сухой очистке от сероводорода повышается при воздействии |
на |
нее у-излучения. |
ОЧИСТКА ПОГЛОТИТЕЛЯМИ НА ОСНОВЕ ОКИСИ ЦИНКА
В процессе поглощения сероводорода окисью цинка образуется сульфид цинка [1, 10, 17]
ZnO + H2S = ZnS + Н20 |
(V, 1) |
При 200—500 °С реакция практически необратима. Ниже при ведены константы равновесия этой реакции при различной тем пературе:
U °С |
200 |
300 |
400 |
500 |
600 |
К |
1,09-106 0,5-10* |
9,1-103 |
2,1.10® |
7,1-102 |
|
В промышленности |
разработаны и |
использованы поглотители |
|||
на основе окиси цинка марок ГИАП-10 |
[18] и 481-Zn, причем марка |
481-Zn предназначена только для удаления сероводорода. [19]. Поглотитель 481-Zn изготовляют в виде таблеток диаметром 7,8— 8,5 мм, высотой 6—8 мм; насыпная плотность до 1,9 • 103 кг/м3, сероемкость не менее 15%. В работе [20] предложена технологи ческая схема получения данного поглотителя путем экструзии. В ка честве пептизатора применяют 15—25%-ный раствор аммиака и 5— 20% (масс.) каолина. Полученный поглотитель отличается от таблетированного повышенной механической прочностью и значительно меньшей себестоимостью при равноценной сероемкости.
Ниже приведена характеристика поглотителя ГИАП-10:
Размеры таблеток, мм |
|
|
5±1 |
диаметр |
|
|
|
высока . . . . . . |
|
|
5±1 |
Насыпная плотность, кг/м3 . |
|
|
1,4 • 103— 1,5 • Ю3 |
Кажущаяся плотность, кг/м3 |
. |
. |
2,4 • 103—2,5 • Г)3 |
Общая пористость, % ............... |
45—50 |
||
Сероемкость, % от массы поглотителя, |
не ниже |
28 |
|
Прочность при раздавливании, |
Ю5Па, не ниже |
150 |
Возможно гранулирование окиси цинка со связующими добав ками, тогда поглотитель выпускают в виде шариков [21].
Поглотитель ГИАП-10 применяют при 350—400 °С и объемной скорости до 1500 ч"1. Он обладает лучшими свойствами по сравнению с маркой 481-Zn, так как приготовляется на основе активной формы окиси цинка, полученной при 350—400 °С в результате разложения солей цинка (например, карбоната) [22]. Активная окись цинка состоит из мелких кристаллов и отличается губчатой мелкопористой структурой (удельная поверхность ZnO может достигать 60—80 м2/г), следовательно, поглотитель на ее основе обладает высокой актив ностью и сероемкостыо. О возможности получения активной окиси
.цинка говорится в работе [23].
Окись цинка, полученная разложением гидроокиси цинка, имеет менее развитую поверхность, поэтому поглотитель, приготовленный на ее основе, обладает пониженной (па 25—30%) активностью и серо емкостыо.
Впроцессе окисления паров цинка при высокой температуре получают крупнопористую окись цинка с удельной поверхностью, равной 4—8 м2/г.
Вработе [24] было исследовано формирование катализаторов
для очистки от соединений серы с выявлением основных реакций, протекающих в стадиях пастообразования, сушки и прокаливания. Для неактивной муфельной окиси цинка в качестве активатора использовался аммиачно-карбонатный раствор. Была найдена кор реляция для хемосорбентов между их динамической активностью
исероемкостыо.
Втабл. V-1 приведены физико-химические и адсорбционные
свойства окиси цинка, полученной из различных видов сырья. На основании этих данных в качестве сырья для поглотителя ГИАП10 рекомендуется использовать карбонат цинка.
Таблица V-1. Основные физико-химические свойства окиси цинка
|
Насыпная плот |
|
|
ность, |
кг/м* |
Исходное сырье |
Дисперс |
|
ность, м |
|
|
|
порошок |
таблетки |
Карбонат цинка |
1,5*10-8 |
0.76*103 |
1.5-103 |
||
Гидроокись цинка |
1,7*10-8 |
1.07 ;оз |
1.7 |
103 |
|
Окись цинка |
1,0*10-7 |
1.69*103 |
|
со |
|
товарная |
to о |
||||
о |
|||||
реактивная |
|
0,40 *Ю3 |
1.8*103 |
||
(ТУ МХП 6-08-243-72) |
|
|
|
|
Удельная |
Сероем |
|
кость |
||
поверхность, |
при |
|
м*/кг |
400 °С, |
|
|
|
% (масс.) |
32.8 |
• Юз |
32,0 |
26.9 • Юз |
21,9 |
|
6.6 |
• Ю3 |
1.7 |
4.2 |
• 103 |
4,2 |
Поглотитель ГИАП-10 применяют главным образом для очистки от сероорганических соединений; оптимальные условия процесса очистки углеводородных газов подробно описаны ниже.
Для тонкой очистки конвертированного газа [25] (в производ стве аммиака по схеме с трубчатой конверсией метана) можно при менять низкотемпературный поглотитель марки ГИАП-10-2 на основе
окислов цинка и меди [26]. Газ очищают на этом поглотителе перед подачей его на низкотемпературный катализатор конверсии окиси углерода; степень очистки газа от сероводорода от 1 • 10" 6 до 2 • 10“ 8— 6-10“8 кг/м3. Условия процесса очистки:
Температура, °С |
250-300 |
Давление, Па |
До 49.105 |
Соотношение нар : газ (п : г), не более |
(50 кгс/см2) |
0,8— 1,0 |
|
Объемная скорость (па сухой газ), ч-1 |
4000-15 000 |
Для удаления из газа небольших примесей сероводорода можно применять также отработанный низкотемпературный катализатор конверсии окиси углерода, содержащий цинк и медь.
Активной фазой ципк-медных поглотителей (помимо окиси цинка) является окись меди, восстанавливаемая водородом или окисью углерода до металлической меди. Вследствие возможности больших выделений тепла и чувствительности поглотителя к перегреву про цесс восстановления необходимо тщательно контролировать. Обычно поддерживают температуру, не превышающую 275 °С, разбавляя восстанавливающий газ (водород) инертным газом, например азо том. Вначале подают смесь азота, содержащую 0,5% водорода, и по мере восстановления концентрацию водорода в газе постепенно увели чивают. Скорость выделения тепла контролируют скоростью доба
вления |
водорода [27]. |
поглощения |
Термодинамические расчеты показали, что реакции |
||
сероводорода окисью цинка (V,l) и медью (V,2) и (V,3) |
при 200— |
|
400 °С |
практически необратимы: |
|
|
Cu+ H2S = CuS + H f |
(V,2) |
|
2Cu + II2S = Cu2S + H2 |
(V,3) |
Ниже приведены вычисленные значения констант равновесия реакций (V,2) и (V,3) [константы равновесия реакции (V,l) см. выше]:
t , °с |
К, |
200 |
8,8 |
250 |
4.4 |
300 |
2,5 |
350 |
1,6 |
400 |
1,0 |
к,
0S сл |
осл |
1,0-105
2,9 • 104
1,0-104
4,3 -103
В процессе очистки конвертированного газа, содержащего боль шое количество пара, остаточное содержание сероводорода лими тируется обратными реакциями:
ZnS + Н20 = ZnO + I12S |
(V,4) |
CuS + Н20 = CuO + II2S |
(V,5) |
Зависимость равновесных значений концентрации сероводорода от температуры при различных соотношениях приведена в табл. V-2.
Таблица V-2. Равновесные концентрации H2S реакции (V,4)
|
|
(в кг/м310е) |
|
|
|
|
Соотношение пар : газ |
|
|
Температура, °С |
0,4 |
0,6 |
0,8 |
1 |
|
||||
200 |
0.15-10-2 |
0,23 • 10-2 |
0.30 • ю-2 |
0,38 • 10-2 |
250 |
0.93 • 10-2 |
0,014 |
0,019 |
0,023 |
300 |
0.041 |
0.061 |
0,082 |
0,102 |
350 |
0.144 |
0,216 |
0,288 |
0,360 |
400 |
0.428 |
0,641 |
0,855 |
1,07 |
П р и м е ч а н и е . |
Равновесная |
концентрация |
сероводорода по |
реакции (V.5) при |
200 °С равна 0,3• 10“13 (П : Г = 0 ,4 ) , а при 400 °С составляет 0,43 • 10“* (П : Г=1).
В промышленных условиях при очистке конвертированного газа на цинк-медных поглотителях равновесное остаточное содержание сероводорода соответствует требуемой степени очистки газа.
Очистку цинк-медным поглотителем применяют, как правило, для удаления небольших примесей сероводорода, при этом погло тители не регенерируют. Регенерация их возможна, однако это усложняет и удорожает процесс.
Запатентован способ очистки газа при малом содержании серо водорода суспензией, состоящей из соединений цинка (окись, гидро окись, карбонат) [28]. Описано получение высокодисперсных окис лов цинка и других металлов (Мо, Со, РЬ) [29]. Поглотитель может содержать окись цинка и 0,1 *10" 3 — 0,2 моля соединений щелочных металлов на каждый моль цинка; окись цинка и 10—15% (масс.) глиноземистого цемента [30] или 20—40% (масс.) бентонита [31]; окись цинка и 1—20% (масс.) окиси железа [32]. Очистку можно осуществлять в стационарном или псевдоожиженном слое окисла или карбоната металла [33].
ОЧИСТКА НА АКТИВИРОВАННОМ УГЛЕ
Очистка газа от сероводорода методом окисления на активиро ванном угле один из процессов, применяемых в крупном промышлен ном масштабе. Процесс заключается в каталитическом окислении сероводорода до элементарной серы кислородом на поверхности активированного угля [3, 5, 10, 17]
IIoS •-— 0-> ---- |
►II20 + S + 53 ккал (217,0 кДж) |
(V.6) |
Чтобы реакция протекала с достаточной скоростью при обычной температуре, к очищаемому газу необходимо добавлять немного аммиака (0,2-10"3 кг на 1 м3), который, по-видимому, поддержи вает необходимую щелочность поверхности активированного угля.
Полученная в результате окисления элементарная сера задер живается активированным углем. По мере заполнения его поверх ности процесс очистки газа прекращается. Адсорбированная сера извлекается при регенерации; освобожденный от серы уголь вновь пригоден для очистки газД. Первоначальная сероемкость и активность угля после регенерации восстанавливаются практически полностью.
Процесс очистки газа от сероводорода активированным углем широко изучался в Советском Союзе [5, 17]. Были проведены иссле дования процесса окисления сероводорода на активированном угле
[34, 35] с |
целью выяснения |
физико-химических основ |
процесса |
и подбора |
эффективной марки |
угля для промышленного |
способа |
очистки. Полученные результаты показали, что скорость процесса очистки газа определяется условиями подвода реагирующих веществ к поверхности угля. Кинетика очистки газа от сероводорода не зави сит от природы активированного угля и носит внешнедиффузионный характер.
Установлено, что при уменьшении размера зерна активирован ного угля сероемкость его увеличивается. В промышленности реко мендуется применять уголь, состоящий из зерен размером 1—2 мм, при высоте слоя более 100 см достигается высокая степень насы щения угля (более 90%). Запыленность газа снижает адсорбционную способность угля, поэтому содержание пыли должно быть не выше 2—10” 6—3 • 10" 0 кг/м3.
В зоне реакции, вследствие экзотермичности окисления серово дорода до элементарной серы, происходит уменьшение относитель ной влажности газа. С учетом этого влажность газа, поступающего
на уголь, рекомендуется поддерживать близкой к |
100%. Наличие |
в очищаемом газе примесей высших углеводородов |
снижает погло |
тительную способность активированного угля вследствие постоян ного накопления на нем продуктов осмоления и полимеризации
этих примесей. |
активированных углей приведены в |
|
Данные |
о сероемкости |
|
табл. V-3. |
Отличительной |
особенностью активированных углей, |
обладающих высокой сероемкостыо, является развитая система переходных пор, объем которых превышает 0,5 • 10“ 3'м3/кг (т. е. в 5—15 раз больше, чем для промышленных активированных углей общего назначения). Сероемкие угли характеризуются также боль шим средним эффективным радиусом пор, составляющим 3*10“ 9— 3,4-10” 9 м вместо 8-10"10—1,10” 9 м для обычных активированных углей.
Наиболее эффективен для очистки газа от сероводорода специально разработанный С-уголь, получаемый с помощью парогазовой акти вации в кипящем слое химически активного и сравнительно мало зольного среднеазиатского бурого угля. Средняя сероемкость С-угля
при испытании на промышленном |
водяном газе, |
содержащем 2— |
4 г/м3 сероводорода, составляет |
112% (масс.); |
степень очистки |
99 %. Насыпная плотность угля этой марки 430—480 кг/м3, проч ность на истирание 75—85%.
|
|
|
|
Сероемкость |
|
|
Марк |
Средний |
радиус |
|
|
|
пор, |
м |
% от массы |
кг/м3 угля |
|
|
|
|
|
||
|
|
|
|
угля |
|
С-уголь (промышленный) |
3,1 • 10-9 |
138 |
520 |
||
фракция 1—2 мм |
|||||
» |
2—4 мм |
3,0.10“° |
114 |
470 |
|
АР-3 |
|
8,3-10-ю |
— |
— |
|
АГ-2 |
|
8,9 • 10-ю |
55 |
275 |
|
НАД |
|
9,6 • 10-ю |
55 |
200 |
|
СКТ |
|
9,0 • 10-ю |
87 |
335 |
На основе данных о гидравлическом сопротивлении активиро ванного угля предложены обобщенные уравнения [36] для расчета промышленных аппаратов.
Регенерацию угля производят раствором сернистого аммония следующего состава: 110—120 кг/м3 аммиака, 75—80 кг/м3 суль фидной серы. Раствор получают пропусканием через аммиачную
воду |
газообразного |
сероводорода; |
состав |
раствора |
регулируют, |
|
разбавляя его водой или раствором аммиака. |
|
|||||
В |
процессе регенерации [5] сернистый |
аммоний |
превращается |
|||
в многосерпистый по |
реакции: |
|
|
|
||
или |
|
2(NH4)2S + 3S2 = 2(NII4)2S4 |
(v,7) |
|||
(N H 4)2S -I- (/г — 1)S = |
(NI-I4)2Sn |
(V ,8) |
||||
|
Затем раствор разлагают острым паром при 125—130 °С и давле нии 1,6 -105—1,9• 105 Па (1,7—2,0 кгс/см2):
(N H 4)2S n = (N H 4)2S + ( n - 1)S |
(V ,9) |
*
Сера, получаемая в жидком виде, отделяется от раствора вслед ствие разницы плотностей, степень чистоты серы 99,92—99,97%. Пары, конденсируемые после разложения раствора, представляют собой чистый сернистый аммоний.
После извлечения серы уголь отмывают водой от раствора сер нистого аммония до отсутствия сульфидной серы в промывных водах и сушат. Общий срок службы угля в производственных условиях зависит рт содержания неудаляемых примесей, попадающих с пото ком очищаемого газа, и механического износа угля.
Принципиальная схема процесса очистки газа представлена на рис. V-3.
Каталитический способ очистки от сероводорода с помощью активированного угля имеет существенные преимущества перед очисткой окислами железа: скорость газа при каталитической очи стке в 10—15 раз выше скорости при очистке Fe20 3, соответственно
уменьшается объем аппаратуры; активированный уголь можно многократно регенерировать и вновь использовать в процессе очистки без выгрузки из аппарата; извлекаемая сера представляет собой товарный продукт высокой степени чистоты.
При очистке газа от небольших примесей сероводорода (мало сернистые природные газы, концентрированная двуокись углерода для синтеза карбамида и др.) целесообразнее использовать активи рованный уголь без периодической регенерации. При этом значи тельно упрощается схема и эксплуатация установки. Выгруженный
рис. V-3. Технологическая схема очистки газа от H2S адсорбцией на активиро ванном угле:
j, г — первый и второй адсорберы; з — выпарная установка; 4 — центрифуга; 5 — сборники.
отработанный уголь направляют в отвал или регенерируют вне очистной установки.
При окислительном способе очистки газов, содержащих значитель ные примеси двуокиси углерода, активированным углем происхо дит образование углеаммонийных солей, которые могут забивать трубопроводы и аппаратуру. В этом случае целесообразно исполь зовать активированный уголь, пропитанный 0,8%-ным водным раствором щелочи [37].
С-уголь, содержащий 0,5% щелочи от массы угля, обеспечивает цолную очистку газа от сероводорода (без добавления аммиака); сероемкость угля в таком процессе составляет 70 кг/м3. Примерно 65—75% поглощенной серы находится в свободном состоянии, 20—25% в виде сульфата. Таким образом, способ очистки газа от сероводорода активированным углем, пропитанным щелочью, характеризуется меньшей сероемкостыо угля, но более прост в экс плуатации.
Разработан метод очистки газа от сероводорода с помощью акти вированного угля, пропитанного иодом (около 1% иода от массы угля) [38]. При очистке промышленных газов с содержанием сероводорода до 100 мг/м3 образующаяся при окислении сера
задерживается в порах угля до 100% (масс.). Концентрация сероводо рода в очищенном газе менее 0,1 • 10“ 2%. Активность угля восстана вливают с помощью растворения серы, осевшей в порах, в щелочах
или сероуглероде.
Описанный периодический способ очистки газа от сероводорода может быть значительно усовершенствован, если этот процесс
С веж и й
Рис. V-4. Принципиальная схема очистки газа от H2S в кипящем слое активи рованного угля:
1 — пылеуловитель; г — очистной аппарат; з — бункер; 4 — питатель; 5 — сушильная
установка; 6 — элеватор; 7 — отделение промывки; 8 — отделение экстракции |
серы* 9 _ |
баллон аммиака; J0 — воздуходувка. * |
’ |
проводить в кипящем (псевдоожиженном) слое угля [39,40]. При этом в б—8 раз увеличивается пропускная способность очистных аппа ратов; процесс становится непрерывным и появляется возможность его автоматизации; уменьшается протяженность коммуникаций; отпадает необходимость в футеровке очистных аппаратов для за щиты их от коррозии раствором полисульфида аммония; облег чается отвод тепла реакции, что позволяет очищать газы с более высоким содержанием сероводорода; отпадает необходимость пред варительной тонкой очистки газа от пыли, но зато требуется очистка от угольной пыли после удаления сероводорода; уменьшается число обслуживающего персонала, однако требуется дополнительная аппа ратура для непрерывной регенерации угля.
ПринвдшиаЛьная схема очистки газа в кипящем сдое активиро ванного угля Представлена на рис. V-4.
°*№СТКА НА СИНТЕТИЧЕСКИХ ЦЕОЛИТАХ
Большим КласС0Л| неорганических адсорбентов являются синте тические ц еолит [41^-46]. Наиболео важная особенность цеолитов —
их своеобразна^ структура: гео |
|
Р |
е . мм pm. cm. |
|
|||||||
метрическая Однородность |
пор |
|
|
||||||||
|
V |
100 |
150 |
200 |
|||||||
[41—43]. |
|
|
|
|
|
|
50 |
||||
Высокая п о ^ отителъиая с п о |
|
|
|
|
|
||||||
собность цеол^[Тов при низких |
|
|
|
|
|
||||||
концентрациях: адсорбируемого |
|
|
|
|
|
||||||
вещества и избирательность по |
|
|
|
|
|
||||||
отношению |
ц |
определенным |
|
|
|
|
|
||||
компонентам Дают возможность |
|
|
|
|
|
||||||
эффективно |
Использовать |
их |
|
|
|
|
|
||||
для |
промышленного |
разделе |
|
|
|
|
|
||||
ния, очистки и осушки газовых |
|
|
|
|
|
||||||
смесей [46—49 ]t |
|
|
|
|
|
|
|
|
|||
В |
большинстве случаев |
ис |
|
|
|
|
|
||||
пользуется высокая адсорбцион |
|
|
|
|
|
||||||
ная |
избирательность |
|
молеку |
|
|
|
|
|
|||
лярных сит По отношению к |
|
|
|
|
|
||||||
полярным и ненасыщенным со |
Рис. Y-5. Изотермы адсорбции серо |
||||||||||
единениям. Такие полярные со |
водорода |
цеолитами различных |
марок |
||||||||
единения, |
как |
вода, |
двуокись |
1 — цеолит |
при 25 °С: |
марки |
|||||
углерода, |
сероводород, |
серни |
марки |
СаХ; |
2 — цеолит |
||||||
NaA; 3 — цеолит |
марки |
СаА; 4 — цеолит |
|||||||||
стый |
ангидрид |
и меркаптаны, |
|
марки NaX. |
|
||||||
хорошо адсорбируются |
и легко |
|
|
|
|
|
могут быть выделены из смесей с неполярными соединениями (иэ природного газа или азотоводородной смеси).
Оптимальные результаты по очистке жидких и газообразных углеводородов достигаются при содержании в них не более 2% серы. Остаточное содержание серы может быть менее 1 мг/м3. Хотя моле кулярные сита стоят значительно дороже обычных адсорбентов, но их к. п. д. и долгий срок службы окупают высокие первоначаль ные капиталовложения.
Адсорбционная способность отечественных синтетических цео литов в отношении сероводорода была изучена в работе [50]. Адсорб ционную емкость определяли вакуумно-весовым методом. Изотермы адсорбции на цеолитах различных марок представлены на рис. V-5. В исследованном интервале парциальных давлений сероводорода наибольшей емкостью обладает цеолит NaX. Цеолиты этой марки рекомендуется использовать для очистки от сероводорода экспанзерного и других газов, не содержащих двуокиси углерода [51].
В работе [52] рассматривается механизм адсорбции сероводорода на цеолитах (при содержании H 2S до 6*10“4 кг/м3), сопоставляется
стоимость очистки от H 2S |
с помощью цеолитов и других |
методов. |
Даны краткие характеристики установок, применяемых |
в США |
|
для очистки на цеолитах. |
|
|
Промышленный опыт очистки природного и других углеводо родных газов от сероводорода освещен также в работе [53]. Адсорб ционная емкость цеолитов типа А по сероводороду при насыщении равна 12—14%, причем она остается достаточно высокой и в области малых концентраций (до 6% при парциальном давлении серово дорода около 260 Па).
Рис. V-6 . Принципиальная схема очистки газа синтетическими цеолитами:
1 — адсорберы; 2 — теплообменник; 3 — компрессоры.
Описана установка для очистки природного газа от сероводо рода, состоящая из четырех колонок с насадкой из синтетического цеолита [54]. Газ проходит поочередно каждую колонку до почти полного насыщения цеолита. Для восстановления адсорбционной емкости цеолит регенерируют потоком двуокиси серы при 315 °С- Адсорбент при этом действует как катализатор, при регенерации образуются элементарная сера и вода; пары серы из регенерацион ной колонны конденсируют, 1/3 жидкой серы сжигают до двуокиси серы.
В случае применения молекулярных сит процесс сероочистки нередко совмещают с глубокой осушкой газов. При этом адсорб ционная емкость цеолитов типа А составляет около 7% (от массы адсорбента) по сероводороду и около 10% по водяному пару.
Процесс сероочистки природного газа, содержащего до 2 • 10“ 3 кг/м3 H 2S, испытан на промышленной установке [55] производитель ностью до 140 тыс. м3 газа в сутки. Длительная эксплуатация показала, что достигается практически полное обессеривание газаостаточное содержание H 2S после очистки не превышало 0,2 мг/м3 (0,2-10"6 кг/м3). Процесс проводили при давлении 30,9• 105 Па (31,5 кгс/см2).
Промышленное применение цеолитов для очистки многосерни стого природного газа с получением элементарной серы по способу Хайпеса описано в работах [56, 57].
В СССР разработана и в 1969 г. введена в эксплуатацию уста новка по очистке природного газа от сероводорода, двуокиси угле
рода и осушка его от |
влаги цеолитами |
[58]. Производитель |
||
ность установки 200 тыс. м3/сутки, |
рабочее давление 57-103 |
Па |
||
(58 кгс/см2), давление |
регенерации |
7,8* |
103—9,8• 105 Па |
(8— |
10кгс/см2).
Введение солей свинца в молекулярные сита приводит к оса
ждению сульфида свинца [59]. Автор отмечает, что адсорбция серо водорода прямо пропорциональна его концентрации; десорбция легко осуществляется парами воды. Описано удаление сероводо рода из пропана и природного газа на цеолитах марки X и приве дены изотермы адсорбции сероводорода [60].
Для очистки природных газов, содержащих наряду с сероводо родом меркаптаны и хлористый водород, служат дтойкие к кислотам синтетические цеолиты [61] типа AW500.
Принципиальная схема очистки газа синтетическими цеолитами показана на рис. V-6.
Регенерацию цеолитов проводят потоком инертного газа при температуре 300—350 °С.
Возможна также продувка очищенным газом при 300—350 °С, после чего газ десорбции промывают водой и возвращают в цикл. Предложена регенерация цеолитов паром [62].
2. ОЧИСТКА ОТ ОРГАНИЧЕСКОЙ СЕРЫ
При химической переработке газов органические соединения серы являются такой же вредной примесью, что и сероводород, так как вызывают аналогичные отрицательные явления — отравле ние катализаторов, ухудшение качества продукции, коррозию трубопроводов и аппаратуры, загрязнение атмосферы.
Вследствие усовершенствования технологических процессов про изводства аммиака, основанных на использовании высокоактивных катализаторов, возрастают требования к полноте очистки газов от сернистых соединений. В частности, в схеме с трубчатой конвер сией природного газа под давлением и низкотемпературной кон версией окиси углерода требуется очистка газа до остаточного содержания сернистых соединений не более 1 мг/м3. В процессе каталитического превращения углеводородов при стабилизации состава природного газа допускается содержание сернистых приме сей не более 0,1 мг/м3.
В состав органической серы чаще всего входят сероуглерод, сероокись углерода, тиофены, меркаптаны, сульфиды и дисульфиды. Состав и содержание органической серы в различных технологиче ских газах зависят от способа и режима их получения, содержания и состава соединений серы в исходном сырье. Концентрация сероорганических примесей в различных газах обычно колеблется от 0 до нескольких десятых процента.
В газах термического разложения угля преимущественно со держится сероуглерод. Органическая сера в генераторных газах почти целиком состоит из сероокиси углерода.
Газ, получаемый парокислородной газификацией нефти (мазута), содержит органическую серу тоже преимущественно в виде серо окиси углерода.
Содержание органических соединений серы в природных газах может изменяться в широких пределах — от нуля до нескольких десятых процента. В отечественных месторождениях природного газа большая часть органической серы находится в виде меркап танов. Кроме того, в них содержатся значительные примеси суль
фидов, дисульфидов, |
полисульфидов |
[63J. ^Сероуглерод, сероокись |
углерода и тиофены, |
как правило, |
отсутствуют. |
В природный газ, |
в котором органическая сера не найдена |
или обнаружено ее незначительное содержание, добавляют одорант. В Советском Союзе в качестве одоранта используют технический этилмеркаптан, который содержит около 5% примесей, состоящих из дисульфидов, метилмеркаптана, бутилмеркаптана и др. Норма одоризации 16 мг/м3 (в пересчете на этилмеркаптан)^ Однако из-за неравномерности дозировки его содержание может колебаться от 2— 5 до 30—50 мг/м3. В качестве одоранта можно добавлять тиофены,
в |
частности тетрагидротиофен. |
|
|||
|
Токсичность серосодержащих соедийений как примесей, отра |
||||
вляющих |
катализатор, |
различна. |
Наиболее сильнодействующая |
||
и |
трудноудаляемая |
примесь — тиофен. |
|||
|
Физико-химические свойства соединений серы подробно опи |
||||
саны в |
литературе |
[1, 3, 64]. |
|
||
|
Проведение глубокой |
очистки от |
сероорганических соединений, |
так же как и от сероводорода, рекомендуется на возможно более ранней стадии обработки газа. Выбор способа очистки обусловлен составом газов, свойствами органических соединений серы и требо ваниями к очистке. Способы очистки газа можно классифицировать следующим образом:
1) высокотемпературные, требующие подогрева газа: каталити ческий, основанный на превращении сероорганических соединений в легко удаляемые вещества (H2S или S 0 2), и поглотительный, основанный на связывании органической серы твердыми поглоти телями;
2) холодные, не требующие подогрева газа: адсорбционный, окислительный (на активированном угле).
Следует отметить, что при использовании высокотемпературных методов Очистки возможно протекание процессов термической дис социации сероорганических соединений. В табл. V-4 приведены значения температуры термической диссоциации некоторых серо органических соединений.
Термическое разложение некоторых органических сернистых соединений с образованием сероводорода может происходить,на ста дии подготовки газов к очистке в подогревателе или теплообменни-
Т а б л и ц а |
V -4 . Температура термической диссоциации некоторых |
||
|
сероорганических соединений |
|
|
Соединение |
Температура |
Соединение |
Температура |
диссоциации, °С |
диссоциации, °С |
||
W-C4 I-I9 SH |
150 |
(C2H5)2s |
400 |
W3o-C4 H9SII |
225-250 |
CeH5 SC,Hu |
350 |
CeHu SH |
2 0 0 |
C4H4 S (тиофен) |
Стабилен до 500 |
CeH5SIi |
2 0 0 |
2,5-Дпмстшгпюфен |
475 |
(CeH5)2S |
450 |
|
|
ках. Причем степень разложения зависит не только от типа серо содержащего соединения, но и от времени пребывания газа в горячей зоне. При термическом разложении не меняется общее содержание серы в очищаемом газе, происходит только превращение одного сернистого соединения в другое. Это необходимо учитывать при выборе метода очистки.
КАТАЛИТИЧЕСКОЕ ГИДРИРОВАНИЕ И ОКИСЛЕНИЕ СЕРООРГАНИЧЕСКИХ СОЕДИНЕНИЙ
Гидрирование применяют в тех случаях, когда в газе присутствуют соединения, недостаточно полно удаляемые с помощью поглоти телей. К таким соединениям относятся сероуглерод, тиофен и ди сульфиды.
Очистка газов от сероорганических соединений методом гидри рования основана на их каталитическом взаимодействии с водородом или водяным паром. Процесс взаимодействия с водяным паром обычно называют гидролизом, или конверсией сероорганических соединений. Поскольку в настоящее время в азотной промышленно сти СССР в качестве сырья используется главным образом мало сернистый природный газ, конверсионный метод применяется редко и в данной книге описан кратко.
Гидрирование и гидролиз сероорганических соединений сводятся к реакциям образования сероводорода и соединений, не содержащих серы.
Образующийся сероводород удаляют из газа известными мето дами.
На рис. V-7 приведены значения констант равновесия реакций гидрирования некоторых сероорганических соединений [2, 65, 66].
Из приведенных данных следует, что термодинамически возможно методами гидрирования и гидролиза осуществить тонкую очистку газов от сероорганических соединений. На практике удается до стигнуть 90—99,9%-ной степени превращения.
Установлено [1], что гидрирование тиофенов происходит труд нее, чем остальных сернистых соединений. А в ряду тиофеновых соединений существует следующая зависимость: тетрагидротиофеп