
140
.pdf
Рис. 24. Слоевое сжигание отходов во вращающейся барабанной печи:
1 - загрузочная воронка; 2 - толкатель; 3 - вращающаяся барабанная печь; 4 - дожигательная камера; 5 - система шлако- и золоудаления; 6 - конвейер летучей золы; 7 - котел-утилизатор; 8 - электрофильтр; 9 - дымосос; 10 - система газоочистки; - труба
25. Сжигание отходов в стационарном кипящем слое:
1- питатели отходов; 2 - решетка с отверстиями; 3 - камера сжигания; 4 - горелка; 5 - дутьевой вентилятор; 6 - циклон; 7 - электрофильтр; 8 - дымосос; 9 - труба
9.2.Пиролиз твердых бытовых отходов
Первые лабораторные установки термического обезвреживания отходов возникли в процессе изучения закономерностей их пирогенетического разло жения (пиролиза), поэтому впоследствии понятием «пиролиз» были объедине ны все системы, обеспечивающие комплексную энерготехнологическую пере работку отходов. В теплоэнергетике термохимические методы использования топлива разделяют в зависимости от условий процесса на пиролиз, газифика цию и двухступенчатое сжигание.
81


В основу классификации пиролизных установок положен температурный уровень процесса, поскольку именно температурой в реакторе определяется выход и качество продуктов пиролиза отходов того или иного состава. В соот ветствии с этим различают три разновидности пиролиза: низкотемпературный (450-550 °С), характеризующийся минимальным выходом газа, максимальным количеством смол, масел и твердых остатков; среднетемпературный (до 800 °С), при котором увеличивается выход газа, уменьшается количество смол и масел; высокотемпературный (более 800 °С), отличающийся максимальным выходом газов и минимальным количеством смолообразных продуктов.
Высокотемпературный пиролиз имеет преимущество по сравнению с дру гими методами: он обеспечивает более интенсивное преобразование исходного продукта; скорость реакций возрастает с увеличением температуры по экспо ненте, в то время как тепловые потери возрастают линейно; расширяется про межуток теплового воздействия на отходы; происходит более полный выход летучих продуктов; сокращается объем и количество остатка.
Различают высокотемпературный пиролиз с твердым (до °С) и жид ким (свыше 1400 °С) шлакоудалением. При пиролизе стремятся избегать об ласти температур в интервале 1050-1400 °С, поскольку в этом диапазоне начи нается размягчение и плавление шлаков, что может привести к неполадкам в системе шлакоудаления. Установки как с твердым, так и с жидким шлакоуда лением подразделяют в зависимости от схем организации процесса (прямоточ ная, противоточная), конструктивного оформления и принципа действия реак тора (шахтный, барабанный, плазменный), вида дутья (воздушное, кислород ное, паровое). Системы с твердым шлакоудалением отличаются, кроме того, наличием или отсутствием процесса газификации коксового остатка, характе ром подвода тепла к слою перерабатываемых отходов (внешний и внутренний нагрев).
9.3. Метод «пиролиз-газификация» с использованием обогащенного
кислородом дутья
Процесс с использованием обогащенного кисло родом дутья предназначен для получения синтез-газа при совместной термообработке пирогаза и сепарированного углеродистого остатка.
Главная часть технологической схемы данного метода, разработанного фирмой «Noell» (рис. 26) включает пиролиз дробленных (роторные ножницы) ТБО в барабанной печи при 550 °С, сепарацию черных и цветных металлов из твердых продуктов пиролиза (минеральные компоненты от твердого углероди стого остатка не отделяют), тонкое измельчение не содержащего металлов ма териала. Продукт последней операции под большим давлением инжектируют в верхнюю часть реактора газификации, куда вводят также технический кисло род и раздельно подают остальные продукты пиролиза: охлажденный пирогаз, отделенный от пиролизных масел и воды, и жидкие продукты пиролиза (масла, вода) со следами пыли.
83
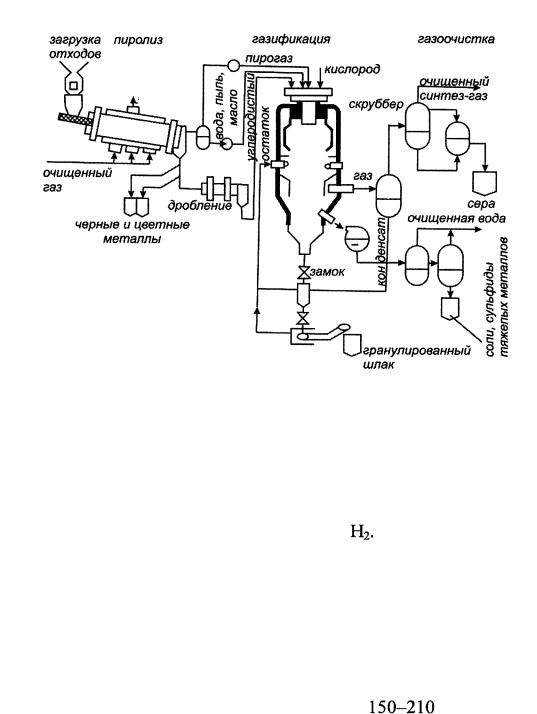



реве осадка до 35-55 °С). Достоинства метода состоят в сокращении продол жительности процесса и более высокой степени уплотнения.
Сгущение активного ила проводят в гидроциклонах, центрифугах (рис. 29) и сепараторах. Процессы протекают в поле центробежных сил при высоких скоростях разделения.
Рис. 29. Схемы установок обезвоживания осадков с применением центрифуг:
а- с раздельным центрифугированием осадков из первичного и вторичного отстойников; б - с центрифугиро ванием осадков первичных отстойников и последующим аэробным сбраживанием фугата; 1 - первичные
отстойники; 2 - аэротенки; 3 - вторичные отстойники; 4 - центрифуги; 5 - минерализатор; 6 - уплотнитель
Процесс стабилизации осадков проводят для разрушения биологически разлагаемой части органического вещества на диоксид углерода, метан и воду. Стабилизацию ведут при помощи микроорганизмов в анаэробных и аэробных условиях. В анаэробных условиях проводится сбраживание в септиках, двухъя русных отстойниках, осветлителях-перегнивателях и метантенках.
Септик представляет собой прямоугольный или круглый проточный ре зервуар, в котором из сточной воды при ее медленном движении выпадают взвешенные вещества. Выпавший осадок находится в резервуаре от 6 до ме сяцев, в течение которых он подвергается анаэробному разложению. Достоин ство септиков состоит в том, что доля задержания в них взвешенных веществ достаточно высокая. Однако, из-за непрерывного поступления свежего осадка,
87


