
Организация производства
.pdf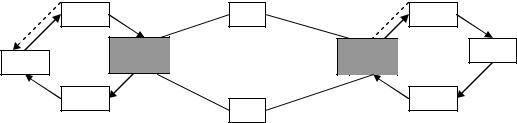
На заводах с большим количеством цехов используют цикловые маршруты. Несколько кольцевых маршрутов связывают общим кольцом, где имеются площадки для передачи грузов с одного кольца на другое.
Nтр.= G / Пр* Тэфф,
Nгр. – необходимое количество транспортных средств G – грузооборот, т/год
Пр – производительность транспортного средства (грузоподъёмность)
Основным направлением повышения качества и эффективности работы транспортного хозяйства: увеличение доли транспортных средств, углубление специализации производства, развитие кооперирования, совершенствование нормирования, учета, контроля транспортных средств, повышение уровня автоматизации производства и управления.
ОРГАНИЗАЦИЯ МАТЕРИАЛЬНО-ТЕХНИЧЕСКОГО ОБЕСПЕЧЕНИЯ СКЛАДСКОГО ОБСЛУЖИВАНИЯ ПРОИЗВОДСТВА
Доля материальных затрат может достигать 80% стоимости продукции , а удельный вес материальных запасов до 50% от общей стоимости оборотных средств. Процесс материально-технического обеспечения направлен на своевременную поставку всех требуемых материально-технических ресурсов.
В состав этих ресурсов входит: сырье, материалы, полуфабрикаты, покупное оборудование и оснастка, транспортные средства, вычислительная техника, топливо, энергия, вода и т.д.
Основными задачами материально-технического обеспечения является:
1.своевременная поставка предприятию необходимых ресурсов требуемого количества и качества
2.организация доставки, хранения, подготовки ресурсов к производству
3.учет и контроль использования ресурсов
4.снижение норм расхода ресурсов
5.анализ эффективности использования ресурсов
31
Формы снабжения материально-техническими ресурсами могут быть
транзитная и складская.
При транзитной форме материал поступает непосредственно от предприятия-изготовителя по прямым связям. При этой форе снабжения поставщик отвечает за качество, сроки и комплектность поставки. Ускоряется документооборот и расчет операции.
При складской форме предприятие получает материалы с баз и складов снабженческо-сбытовых организаций. При этой форме экономятся площади, отсутствуют сверхнормативные запасы, снижаются расходы на хранение материалов.
Эффективность использования той иной формы снабжения зависит от ряда факторов:
1.от суточной потребности в материалах
2.от затрат содержания запасов
3.от затрат на перевозку материалов от производителя к потребителю
проч.
Иногда на предприятии используются обе формы снабжения. Их рациональное соотношение определяется следующим образом:
Пусть Нт – норматив запаса при транзитной форме поставок, дн. Нс – норматив запасов при складской форме
S – общая площадь склада
α– коэффициент использования площади склада α =S полезн./ S общ.
Величина груза, который может храниться на складе равна
G=q*Sобщ.*α
q- допустимая масса груза на 1 кв.м(грузонапряженность) т/кв.м х- объём транзитной поставки за день
у- V складских поставок за день
Qдн. – среднедневной расход х+у=Qдн.
{Нт*х+Нс*у=G |
{ Нт*х+Нс*у=G |
{х+у= Qдн. |
{ х=Qдн.- у |
х/Qдн. – доля транзитных поставок у/Qдн. – доля складских поставок
Организация работы складов заключается в контроле и приеме материалов на склад, подготовка их к хранению, в счете и отпуске материалов со склада.
Материалы отпускаются со складов по материальным требованиям в единичном и мелкосерийном производстве и по лимитным картам в массовом и крупносерийном производстве. Лимитная карта содержит № цеха, дату, отпущенное количество на текущий момент и нарастающим итогом, учитывается остаток и т.д.
32
Все материалы, поступающие на склад, проходят контроль качества и проверяются на соответствие количеству, указанному в сопроводительных документах. На каждый вид материала заводится учетная карта, в которой отражается приход, расход и остаток материала.
В зависимости от 1).вида хранимой продукции различают различные склады:
-сырья и материалов
-полуфабрикатов
-готовой продукции
-инструментов
-хозяйственные
и 2). по условиям хранения:
-открытые
-полуоткрытые
-закрытые а) отапливаемые
б) неотапливаемые Склады оснащаются стеллажами, тарой, автопогрузчиками, транспорте-
рами и т.д., а также измерительным оборудованием (весы, счетчики и т.д.) Размещение склада должно обеспечивать быструю доставку материала в
цеха и из цехов на склад.
Соотношение полезной площади склада к общей – коэффициент использования площади склада:
α=Fполез/Fобщ. Определяется двумя способами.
1. по максимальной нагрузке, которая образовалась на складе Fполез.=Qmax / q , q – грузонапряженность(дополнительная нагрузка на 1 кв.м)
2. по объёмному измерителю Fполез.=Кстел.* Fстел.
F стел.=Q max/V*g*Кзап.*nяч
V – объём одной ячейки, куб.м
g– удельный вес груза в ячейке, т/куб.м К зап.- коэффициент заполнения
n – количество ячеек
Ширина проходов между стеллажами 0,8-0,9 м, а при использовании автопогрузчиков й,1-1,2 м. Внутри склада устанавливаются продольные проезды шириной 2,5-3 м и сквозные проезды по ширине ворот.
Различают следующие формы складской работы: пассивную, при которой потребители получают материалы самостоятельно и сами транспортируют в свое подразделение и активную, при которой склад доставляет материал в подразделение. Пассивная форма используется в единичном и серийном производстве, активная – в массовом и крупносерийном.
33
ОРГАНИЗАЦИЯ ОБЕСПЕЧЕНИЯ ПРОИЗВОДСТВА ТЕХНОЛОГИЧЕСКОЙ ОСНАСТКОЙ
Система обеспечения производства технологической оснасткой – комплекс мероприятий по проектированию, изготовлению, приобретению и эксплуатации оснастки, обеспечивающих выпуск продукции основного производства в установленные сроки заданного количества и качества. Обеспечение производства технологической оснасткой существенно влияет на экономические показатели основного производства.
В себестоимости продукции удельный вес затрат на оснастку составляет 2-3% в массовом. В оборотных средствах предприятия запасы инструмента составляют от 15 до 40%. Простои оборудования по вине инструментального обслуживания составляют 2-3%. Из этих данных вытекают основные задачи обеспечения производства технологической оснасткой:
1.обеспечение производственного процесса во всех его звеньях необходимой технологической оснасткой
2.поддержание необходимого уровня запасов оснастки для обеспечения ритмичного производственного процесса.
Для решения этих задач на предприятии создаются инструментальные хозяйства, которые могут содержать инструментальный цех, центральный инструментальный склад, цеховые инструментально-раздаточные кладовые, участки централизованной заточки режущего инструмента, ремонта оснастки, восстановления инструментов и проч.
По производственному назначению оснастка подразделяется на:
-инструменты
-штампы
-пресс-формы
-модели, кокили
-приспособления и пр.
По техническому назначению инструмент делится на :
режущий, абразивный, слесарно-монтажный, кузнечный, вспомогательный и пр.
По характеру действия инструмент делится на универсальный и специальный.
В целях рациональной организации инструментального хозяйства и упрощения технологической документации применяется десятичная классификация и индексация инструмента. Все многообразие оснастки делится на группы, подгруппы, виды и разновидности, в соответствии с определенными признаками.
Условное обозначение инструмента состоит из двух частей:
1.классификационная характеристика инструмента из 4-х цифр
2.типоразмер инструмента по номеру в стандарте.
Например, фреза дисковая 3-хстороняя диаметром Д=60мм шириной
14мм (в).
22 42-0002
34
типоразмер 2 группа – инструмент для обработки металла резанием
2 – подгруппа –фрезерный инструмент
4 –дисковая фреза (вид)
2 – фреза дисковая (разновидность) 3-х сторонняя Данная классификация позволяет вести автоматизированный учет
инструмента.
Планирование потребности в инструменте заключается в рпределении номенклатуры оснастки и её количестве.
Номенклатура инструмента определяется по картам применяемости инструмента в серийном и массовом производстве, а в единичном и мелкосерийном – по картам типового оснащения инструментом рабочих мест.
Карта применяемости инструмента содержит название инструмента, его индекс, вид детали, которую нужно обработать, нормы машинного времени на обработку и проч.
Карта типового оснащения приводится для определенного станка с указанием удельного веса машинного времени обработки данным инструментом в общем времени работы станка.
Применяется 3 метода расчета расхода инструмента:
1.статистический
2.по нормам оснастки
3.по нормам расхода
1.Статистический метод: определяется фактический расход инструмента на тысячу рублей валовой продукции или на тысячу часов работы той группы оборудования, где используется данный инструмент. Ипл.=Ифакт./Qфакт.*Qплан. – плановый расход инструмента в денежном выражении.
Q – расход инструмента
Расход в денежном выражении делится на среднюю себестоимость или цену данного инструмента. Плановое значение потребности в инструменте должно корректироваться с учетом организационно-технических мероприятий(ОТМ), намеченных на предприятии по сокращению расхода инструмента.
Метод применяется в единичном и мелкосерийном производстве, когда трудно установить срок службы инструмента.
2.По нормам оснастки. Норма оснастки – это количество инструментов, которые должны находиться одновременно на данном рабочем месте в течение планового периода.
m
И=Σ Ki/ Тизн
I=1
Ki – количество инструментов на рабочем мест
m – количество рабочих, одновременно применяющих данный инструмент;
35
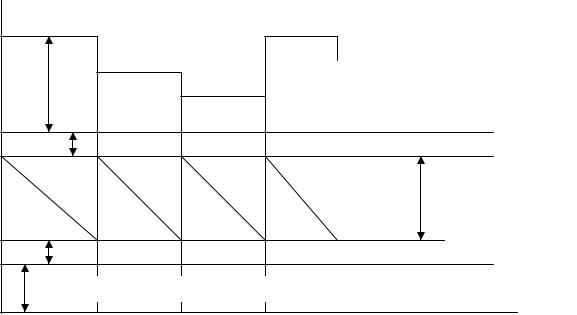
Тизн – срок службы данного инструмента.
Метод используется для инструментов долговременного пользования. 3.Метод расчета по нормам расхода. Под нормой расхода понимается количество инструментов, расходуемых при обработке одной детали или изделия. Норму определяют на 100 или на 1000 изделий.
n
И=Σ Hi * Qi
I=1
Qi – количество изделий определенного вида; Hi – норма расхода инструмента на одно изделие;
n – количество наименований изделий, для которых применяется данный инструмент.
РАСЧЕТ ОБОРОТНОГО ФОНДА ИНСТРУМЕНТА
Для бесперебойного снабжения производства инструментом на предприятии создается оборотный фонд инструмента. Оборотный фонд инструмента складывается из запасов инструмента в центральном инструментном складе (ЦИС) и расходного и страхового запаса. В инструментных раздаточно – кладовых (ИРК) инструменты на рабочих местах подвергаются заточке, ремонту, проверке.
Минимальный запас инструментов складывается из запасов:
Umin =UЦИСстрах +UИРКстрах +Uпров,рем-т,зат-ка
Максимальный оборотный фонд:
U = Umin+Uпоставки
Ирасх |
|
ЦИС |
|
|
Истрах ЦИС |
|
И расх.фонд |
|
ИРК |
|
Истрах ИРК |
|
Ирм заточки,рем,пров |
|
время |
Применяются 2 системы регулирования запасов: |
|
1. |
система максимум-минимум |
2. |
на заказ |
36
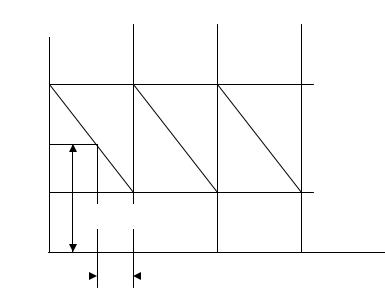
Система максимум-минимум заключается в том, что запас инструмента не должен превышать Иmax и быть ниже страхового. Для этого, чтобы при достижении определённой величины запаса выдавался заказ на получение инструмента со стороны или изготовлении его в инструментальном цехе. Величина запаса, при которой выдаётся заказ на очередную партию инструментов, называется точкой заказа.
И |
И |
max |
Итз |
И |
min |
точка заказа |
время |
Ттз |
Итз=Иmin+Ттз*Идн
Идн – среднедневной расход инструмента Ттз – время от момента выдачи заказа до поступления партии инструмента в
ЦИС, оно складывается Ттз=Тизгот.+Тоформл.док Планирование на заказ используется для инструментов однократного
применения.
На крупных заводах инструментальное хозяйство подчиняется главному инженеру завода, на мелких и средних – технологу завода.
Направления совершенствования инструментального хозяйства:
1.Унификация и стандартизация оснастки и составных частей
2.Обеспечение оптимальной работы ЦИС и ИРК
3.Совершенствование учета нормативной базы
4.Повышение эффективности ремонта и восстановление оснастки.
ОРГАНИЗАЦИЯ КОМПЛЕКСНОЙ ПОДГОТОВКИ ПРОИЗВОДСТВА
Комплексная подготовка производства - совокупность научно-техниче- ских и организационно-плановых мероприятий по созданию и освоению новых конструкций, технологических процессов и методов организации и планирования производства.
37

Понятие комплексной подготовки относится к созданию новой техники и технологии.
Комплексная подготовка делится на стадии, стадии – на этапы, этапы – на отдельные работы. Целями комплексной подготовки производства являются:
-создание изделий заданного технического уровня и качества
-сокращение длительности производственного цикла
-наращивание объёмов новой продукции
экономия материальных, трудовых и финансовых ресурсов на всех стадиях подготовки производства.
В современных условиях процесс комплексной подготовки производства имеет ряд особенностей:
1.возрастает сложность и масштабы разрабатываемых объектов, усложняется координация и организация работ, что приводит к большому числу незавершенных разработок
2.значительное отклонение фактического хода подготовки от планового. Причиной является вероятностный характер подготовки производства, обусловленный новизной и неопределенностью конечных результатов
3.неповторимость процессов научно-исследовательских и опытноконструкторских разработок, сложность проектируемых объектов является причиной многовариантных решений
4.моральное старение научных результатов.
Структура комплексной подготовки производства содержит стадии:
НИР
Производство
-теоретические и фундаментальные исследования
-поисковые исследования
-прикладные исследования
-опытно-конструкторские разработки
-проектирование новых производств
-конструкторская подготовка производства
-технологическая подготовка производства
-организационно-плановая подготовка производства
-освоение производства
Подготовка продукции к реализации(сбыт) и подготовка продукции к потреблению (сервис)
38
НИР – вид деятельности, направленной на получение новых знаний в различных областях и их воплощение на практике.
•Фундаментальные исследования относятся к непроизводственной сфере и направлены на открытие новых законов природы, общества, мышления.
•Поисковые исследования направлены на создание развития новых направлений техники, обеспечивающей повышение производительности труда, количества продукции, конкурентоспособности.
•Прикладные исследования направлены на решение конкретных проблем, таких как: разработка и совершенствование технологии производства, конструкций, машин и приборов, повышение надежности, долговечности и прочее.
Основной целью НИР является внедрение результатов НТП. К основным направлениям НТП относят: компьютеризация производства и управления на всех уровнях и во всех областях; создание материалов с заранее заданными свойствами; развитие искусственного интеллекта; расширение применения биотехнологии; совершенствование технологических процессов.
Совершенствование технологических процессов осуществляется на основе применения лазерной, плазменной, вакуумной, импульсной технологий, обработки взрывом, электрофизических и электрохимических методов обработки, малооперационной безлюдной технологии (ГПС).
В развитых странах широко применяется оценка результативности исследований. Она используется при определении научных и технических приоритетов, при решении вопросов о продолжительности той или иной программы или проекта. Оценка результативности научных исследований осуществляется с помощью разветвленной системы консультативно – экспертной службы. Созданные исследовательские советы, которые самостоятельно формируют научную политику и финансируют работы в исследовательских учреждениях и университетах, распределяют стипендии и гранды, выделяют средства на международное сотрудничество.
Например, в Великобритании действуют 7 советов, в т. ч. и по биотехнологии.
Проектноконструкторские разработки – целенаправленная деятель-
ность по конструированию и проектированию новой техники, оформлению и тиражированию конструкторской документации для организации промышленного производства продукции.
Основными этапами работ являются:
-техническое задание;
-эскизное проектирование;
-техническое проектирование;
-рабочая документация.
Первый этап представляет собой составление, согласование и утверждение ТЗ на ОКР.
39
Эскизный проект содержит разработку блок – схемы и габаритных чертежей изделия, составление эскизов, изготовление и испытание макетов.
На этапе технического проектирования производится уточнение принципиальной схемы изделия, изготовление и испытание технологического образца, разрабатывается конструкция основных узлов с учетом проведенных испытаний.
Этап рабочей документации содержит ТЗ на рабочее проектирование. Здесь разрабатываются схемы и рабочие чертежи, уточняются заявки на материалы и комплектующие, составляются карты технических условий и эксплуатационн – техническая документация, изготовляется опытный образец, проводится заводское испытание на соответствие требованиям ТЗ и технических условий. Рабочие чертежи корректируются и дорабатываются. Документация оформляется в соответствии с ГОСТОМ, на каждом этапе проводится согласование схем и чертежей и их утверждение.
Технологическая подготовка производства – совокупность мероприя-
тий, обеспечивающих технологическую готовность производства к выпуску изделий заданного объема и заданных показателей. Технологическая готовность производства означает наличие полных комплектов конструкторской и технологической документации и средств технологического оснащения.
Комплексная подготовка производства базируется на следующих стандартах:
1)ЕСКД (единая система конструкторской документации);
2)ЕСТД (единая система технологической документации);
3)ЕСТПП (единая система технологической подготовки производства); Технологическая документация содержит: технологические маршруты,
т. е. последовательность прохождения изделия по цехам и производственным участкам, операционные карты для единичных технологических процессов и карты типовой операции, где указываются переходы, технологические режимы, данные об оснастке, материалах, трудозатратах.
Единичный технологический процесс предназначается для изготовления изделий одного наименования, а типовой технологический процесс – для группы деталей с общими конструктивными и технологическими признаками.
Основными факторами сокращения длительности подготовки производства и повышения эффективности является внедрение ГОСТОВ ЕСКД, ЕСТД, ЕСППТ, унификация и типизация технологических процессов, соблюдение принципов рациональной организации производственных процессов.
40