
книги / Переработка, обогащение и комплексное использование твердых полезных ископаемых. Обогатительные процессы и аппараты
.pdfной восприимчивостью или диэлектрической проницаемостьд, в этом случае действуют соответственно лоренцовы, Магнитке или электрические силы, определяющие совместно с силами тяжести погружение или выталкивание зерен из жидкости.
В качестве сепарирующей жидкости используются элек тролиты — водные растворы повареной соли, кислот, щело чей, солей меди и железа. Изменением величины тока в элек тролите или обмотках электромагнита можно изменять эффек тивную (кажущуюся) плотность жидкости в широких преде лах (от 1 до 10 т/м3), создавая хорошие возможности для гра витационного обогащения различных минеральных комплексов.
Исходный матери ал в установку для МГД-сепарации (рис. 11.13) подается питате лем 1 через разделитель ный канал 2, располо женный в зазоре между полюсами электромаг нита 3. Электролит из сборника 4 насосом 5 подается в загрузочную часть канала. Ток под водится к электролиту
через электроды б, ус
Рис. 11.13. Схема установки МГД-сепарации тановленные в канале,
продукты разделения поступают в приемники 7 с сетками для дренажа электролита.
Трудности использования процесса МГД-сепарации свя заны с вихревым характером лоренцовой силы. Возникающие возле частиц локальные вихревые течения, а также циркули рующие течения на входе и выходе сепаратора существенно затрудняют разделение частиц. Для широкого промышленно го использования процесса необходимо проведение работ так же по сокращению расхода электроэнергии, увеличению про изводительности сепаратора, снижению химической агрессивносги электролитов и их стоимости.
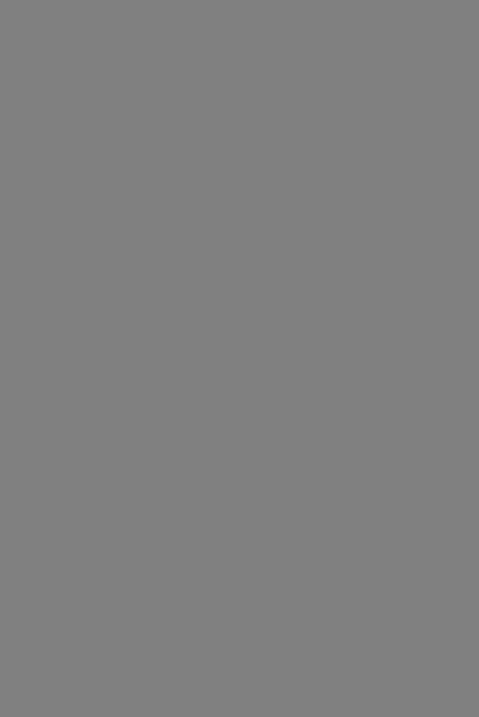
12
ОБЕЗВОЖИВАНИЕ ПРОНУ КТОВ ОБОГАЩЕНИЯ
12.1. Назначение и оБшая характеристика процессов и п р о о у к т о в обезвоживания
Обезвоживанием называется разделение твердой и жидкой фаз. Ему могут подвергаться не только конечные, но и про межуточные продукты обогащения, осуществляемого обычно в водной среде. Причинами обезвоживания являются: необходи мость снижения затрат на транспортирование продуктов обо гащения (концентратов); переход от мокрых процессов обога щения к сухим или к операциям, требующим меньшей разжи женности пульпы; необходимость организации на фабрике полного водооборота с целью снижения себестоимости про дукции и охраны окружающей среды.
Для обезвоживания крупнозернистого и кускового мате риала достаточно операции дренирования, при которой избы ток воды удаляется самотеком. Из тонкозернистого материа ла вода удаляется значительно труднее и для его обезвожива ния обычно требуется несколько последовательных операций:
сгущение или центрифугирование (до влажности 30—50 %) пу тем осаждения частиц под действием силы тяжести или цен тробежных сил; фильтрование (до влажности 10— 15 %) путем отделения твердых частиц от жидкости пропусканием пульпы через пористые перегородки; сушка (до влажности 0,5—5,0 %) для удаления влаги под действием температуры.
В зависимости от содержания влаги различают продукты обогащения и обезвоживания: мокрые, из которых вода (сво бодная, гравитационная) может свободно стекать под дейст вием сил тяжести; влажные, содержащие капиллярную и пле ночную воду, удерживаемую между минеральными частица
ми; воздушно-сухие, содержащие гигроскопическую влагу, удер живаемую поверхностью частиц, и сухие, содержащие только кристаллизационную влагу.
12.2. Д ренирование
Дренирование представляет собой процесс естественной фильтрации жидкости через промежутки между твердыми ча стицами или кусками под действием силы тяжести. Оно ис пользуется для обезвоживания кускового и крупнозернистого материала в штабелях, бункерах, обезвоживающих элевато рах, механических классификаторах и на грохотах.
Обезвоживание в штабелях крупнокускового материала (до 150—200 мм) с нижним пределом крупности 0,1— 1 мм про изводится на дренажных складах, представляющих собой же лезобетонные сооружения большой вместимости с наклонным дном, в котором проложены дренажные канавы для отвода воды. Время обезвоживания мелкого материала (например, же лезного концентрата) достигает 24 ч после предварительного его сгущения в отстойниках.
Обезвоживание в бункерах обычно прямоугольной формы с пирамидальной нижней частью, оборудованной специальными затворами-выпусками с перфорированными отверстиями для стока воды, используется главным образом на углеобогати тельных фабриках для удаления воды из углей крупнее 0,6 мм.
Обезвоживанию в элеваторах с дырчатыми ковшами под вергается материал крупнее 2 мм в процессе его транспорти рования из обогатительных аппаратов или отстойников. Что бы предотвратить попадание воды из верхнего ковша в ниж ний и получить материал влажностью не более 25—30 %, эле ватор устанавливают под углом 60—70 % к горизонту.
Обезвоживание продуктов в механических (реечных и спи ральных) классификаторах происходит при их транспортиро вании по днищу классификатора. Влажность средне- и мелко зернистых железных концентратов и продуктов обогащения марганцевых руд после обезвоживания составляет 15—25 %.
Обезвоживанию на грохотах может подвергаться мате риал широкого диапазона крупности (от 0,35 до 300 мм и бо лее). Наиболее широко используются вибрационные, самоба
лансные, резонансные и дуговые грохоты с щелевидными си тами. Встряхивание и перемещение материала по грохоту значительно интенсифицируют процесс дренирования воды.
12.3. Сгуш енпе
Сгущением называется процесс разделения твердой и жидкой фаз, основанный на естественном осаждении мине ральных частиц в жидкости под действием силы тяжести.
Осаждение частиц при сгущении подчиняется рассмотрен ным ранее (см. подразд. 3.3.1) законам стесненного падения твердых тел в жидкой среде. Скорость осаждения возрастает с увеличением крупности и плотности частиц, повышением тем пературы и разбавлением сгущаемой пульпы, вызывающих уменьшение ее вязкости. Тонкодисперсные частицы оседают медленно из-за малой скорости падения, броуновского движе ния и взаимного отталкивания при одноименном заряде их по верхности. По этим причинам оседание частиц меньше 0,1 мкм практически прекращается. Решение проблемы сгущения тон кодисперсных частиц достигается применением реагентов, вы зывающих их слипание или агрегацию в результате коагуля ции или флокуляции.
Коагуляция под действием сил Ван-дер-Ваальса происхо дит при уменьшении или нейтрализации заряда поверхности частиц при использовании неорганических реагентов (кисло ты, извести, железного купороса и др.). Флокуляция обуслов лена действием органических реагентов, вызывающих или гидрофобизацию поверхности частиц и стремление их при этом сократить поверхность контакта с более полярной жидкостью
— водой (при использовании реагентов-собирателей: ксантогенатов, жирных кислот, аминов и др.), или сцепление частиц «мостиками» полимерных молекул, закрепляющихся одновре менно своими полярными группами на разных частицах (при использовании реагентов-флокулянтов: полиакриламида, сепарана, суперфлока, полиокса и др.). Магнитная флокуляция ча стиц минералов, обладающих повышенной магнитной воспри имчивостью, обеспечивается созданием магнитного поля.
Рис. 12.1. Схема зон осаж дения пульпы в сгустителях (а) и конструкции одноярусны х радиальных сгустителей с центральным (б) и периферическим
(в)приводом
Внастоящее время сгущение производится в основном в цилиндрических (радиальных) сгустителях с механической раз грузкой осадка. При установившемся режиме в сгустителе мож но выделить (рис. 12.1, а): зону А осветленной жидкости, уда ляемой в слив; зону Б пульпы исходной плотности, в которой
происходит (в зависимости от содержания твердого) свобод ное или стесненное падение зерен; зону Г уплотнения, в кото рой дополнительное выделение жидкости происходит в ре зультате сжатия осадка под давлением находящегося выше материала; промежуточную зону В. Разгрузка сгущенного ма териала осуществляется медленно вращающимся в центре сгу стителя устройством, перемещающим осевшие твердые части цы к отверстию в средней части его днища. По расположению приводного механизма различают сгустители с центральным и периферическим приводом.
Сгуститель с центральным приводом может быть одноили многоярусным. Одноярусный радиальный сгуститель (рис. 12.1, 6) состоит: из цилиндрического чана 1 диаметром
от 2,5 до 50 м и глубиной от 1,5 до 5 м с горизонтальным (при малом диаметре) или коническим (при большом диамет ре) днищем и кольцевым желобом 2 для удаления слива; раз грузочной воронки 3, заглубленной по отношению к уровню слива примерно на 0,5— 1 м и снабженной металлической ре шеткой для гашения скорости потока и дефлектором — рас пределителем поступающей пульпы; механизма для разгрузки сгущенного продукта.
У сгустителей небольшого диаметра (до 18— 24 м) меха низм разгрузки осадка крепится на ферме 7. Он представляет собой вращающийся от привода 8 вал 5 с граблинами б в ви де крестовины с наклонными гребками (или в виде полуспиралей), позволяющими перемещать осадок к разгрузочному конусу 4 в центре днища. У сгустителей большего диаметра (до 50 м и более) вал заменяется сварной конструкцией, опи рающейся на центральную колонну. Для предотвращения по ломок механизма при перегрузках сгустителя, регистрируе мых указателем 10, вал вместе с граблинами может переме щаться в вертикальном направлении вручную или автомати чески механическим устройством 9.
Разгрузочный механизм сгустителей с периферическим при водом (рис. 12.1, в) диаметром до 100 м и глубиной до 7 м име ет вид рамы с гребками 3, которая опирается на центральную колонну 1 и монорельс 5, уложенный вкруговую на стенке ча на 6. У периферии рама заканчивается кареткой 4, на которой размещены электропривод, редуктор, приводной ролик и бал ласт для увеличения силы сцепления ролика с рельсом при вра щении рамы 2 вокруг центральной оси.
Окружная скорость движения граблин или гребковой ра мы у периферии составляет обычно 0,1 м/с; она уменьшается до 0,05 м/с при сгущении тонких шламов и возрастает до 0,2 м/с при сгущении грубозернистых пульп. Удельная производи тельность составляет при этом от 0,1 до 2 т/(м2 • сут) и только при сгущении магнетитовых и титаномагнетитовых концен тратов магнитной сепарации благодаря их магнитной фло куляции достигает 6—8 т/(м2 • сут).
Для откачки продукта, сгущенного до плотности 60—70 % твердого, из сгустителей малого диаметра применяют диафрагмовые насосы, а из сгустителей большего диаметра — центро
бежные песковые насосы. Слив сгустителей используется в качестве оборотной воды. Для предотвращения потерь пены с ним при сгущении флотационных концентратов перед слив ным порогом устанавливают пеноотбойник (экран), заглуб ленный ниже уровня слива. Исходная пульпа поступает в сгу ститель по трубопроводу или желобу, проложенным по не подвижной ферме 7.
Рис. 12.2. Схема цилиндрического сгустителя с осадкоуплотнителем (л) и пластинчатого сгустителя (б)
В последнее время на угольных фабриках для сгущения шламов и хвостов флотации кроме радиальных сгустителей используются также цилиндроконические сгустители с осад коуплотнителем (рис. 12.2, а), состоящие из цилиндрической 1 и конической 2 частей, питателя 3, сливного кольцевого жело ба 4 и разгрузочного устройства 5 для сгущенного продукта. Цилиндрическая часть обеспечивает необходимую степень оса ждения тонких зерен, а коническая — уплотнение осадка до 80 % твердого при удельной производительности на 1 м2 по верхности несколько большей, чем у радиальных сгустителей.
Для сгущения рудных тонкодисперсных продуктов начи нают применять пластинчатые сгустители (рис. 12.2, б), пред
ставляющие собой камеру 1, в которой установлены пакеты параллельных плоскостей 2 общей площадью до 1000 м2 из сте клопластика или нержавеющей стали, расположенных на рас стоянии 30—50 мм друг от друга под углом 25—60° к гори зонту. Это позволяет разделить поток на струи 4 с ламинар ным движением, значительно уменьшить путь оседания твер дых частиц и тем самым резко увеличить удельную произво дительность сгущения на горизонтальную площадь всех пло скостей. Твердые частицы оседают на наклонные плоскости, перемещаются вниз и удаляются через патрубок 5; осветлен ная жидкость поднимается вверх и сливается через патрубок 3. Разгрузка сгущенного продукта до 60—75 % твердого может быть автоматизирована; регулирование его плотности при этом может осуществляться с использованием гамма-лучей, ульт развука или электропроводности пульпы, а изменение скоро сти разгрузки — «наложением» на пакет пластин вибрации с малой амплитудой колебаний.
Для сгущения пульп, содержащих быстрооседающую твер дую фазу, например магнитную фракцию сепарации железных руд, применяют гидросепаратор, представляющий собой не высокий сгуститель с центральным приводом и используемый обычно как классифицирующий аппарат. Его использование позволяет совместить две операции — сгущение и удаление шламистых частиц породы, что очень важно при сгущении, например, магнетитовых и титаномагнетитовых концентра тов. Эффективность этих операций повышается при исполь зовании специальных магнитных дешламаторов, отличающих ся от гидросепараторов наличием намагничивающего устрой ства, состоящего из четырех катушек, расположенных в пита ющей воронке.
Для предварительного сгущения продуктов иногда исполь зуют пирамидальные отстойники и гидроциклоны, сливы ко торых поступают в радиальные сгустители, а сгущенные про дукты аппаратов обычно объединяются. В отстойниках пуль па поступает в головную часть и движется к сливному порогу на противоположной стороне. По пути движения пульпы твер дые частицы оседают в камеры и выпускаются через специ альные разгрузочные отверстия вручную через патрубки с кра
нами, при помощи диафрагмовых насосов- и автоматически через шлюзовой питатель. Обезвоживающие гидроцикло^ы и мультициклоны устанавливают обычно перед сгустителем.
12.4. Ф ильтрование
Фильтрованием называется процесс разделения твердой и жидкой фаз пульпы с помощью пористой перегородки под действием разности давлений, создаваемой разряжением или избыточным давлением воздуха. Жидкая фаза при этом про ходит через пористую перегородку в виде фильтрата, а Твер дая задерживается на ее поверхности, образуя слой осадка — кека. Разность давлений в пресс-фильтрах создается подачей пульпы на фильтрующую перегородку под давлением выше атмосферного, а в вакуум-фильтрах — созданием вакуума за пористой перегородкой ниже 0,1 МПа. В качестве пористой перегородки используют синтетические, реже хлопчатобумаж ные и шерстяные ткани, иногда металлические сетки с отвер стиями 0,1—0,2 мм.
Для обезвоживания угольных и рудных суспензий на обо гатительных фабриках применяют преимущественно вакуумфильтры, которые по конструкции основного рабочего орга на разделяются на дисковые, барабанные и ленточные.
В дисковых вакуум-фильтрах (рис. 12.3, а) фильтрация осу ществляется через боковую поверхность фильтрующих элемен тов — секторов, закрепленных на вращающемся от привода 7 валу и образующих сплошной диск 2, погруженный нижней частью в ванну б с пульпой, подаваемой сверху или через ее днище. Мешалка 4, совершая качательное маятниковое дви жение вокруг вала 1, взмучивает пульпу. Каждый сектор (рис. 12.3, б, в) представляет собой обтянутую тканью фильтрую щую камеру 8 из дерева (см. рис. 12.3, б), металла (см. рис. 12.3, в) или синтетического материала, подсоединенную через патрубок 9 (с помощью шпильки, накладки и гайки) к про дольному каналу 10 пустотелого вала У конец которого вхо дит в обойму распределительной головки 3 (см. рис. 12.3, а). Чи сло секторов равно числу продольных каналов, которые при вращении вала (с частотой 0,13— 2 мин'1) поочередно совме