
книги / Управление большими системами. УБС-2017
.pdf
Информационные технологии в управлении техническими системами и технологическими процессами
4. Идентификация управляемого динамического объекта с использованием его нейросетевой модели
Управляемые технологические объекты могут быть идентифицированы по данным пассивных наблюдений за его координатами в режиме автоматического регулирования.
Предлагаемый способ заключается в параметрической идентификации динамики объектов с замкнутой системой регулирования частотным методом по нейросетевой модели системы. Сбор в режиме наблюдения информации осуществляется в виде измеряемых временных трендов входных и выходных координат управляемого объекта и регулятора. По экспериментальным данным обучается динамическая нейронная сеть.
Отличительной особенностью предлагаемого подхода является следующее. На основе обученной нейронной сети создается модель объекта с системой управления, состоящая из сети, имитирующей поведение управляемого объекта, и модели регулятора, формирующей сигнал управляющего воздействия, со структурой и значениями параметров, отвечающими алгоритму регулирования реальной системы (рис. 5). Модель регулятора обеспечивает адекватную исследуемому объекту работу его нейросетевой модели, так как нейронная сеть была обучена для условий функциональной зависимости значений управляющего воздействия регулятора от значений управляемой величины на выходе объекта.
Рис. 5. Модель объекта с системой управления
На построенной модели (см. рис. 5) проводится активный вычислительный эксперимент по определению частотных характеристик интересующих исследователя каналов передачи
323
361
Управление большими системами. Выпуск XX
«вход-выход». Экспериментальные динамические характеристики аппроксимируются типовыми передаточными функциями каналов управляемых объектов с запаздыванием.
Подход исследовался на имитационной модели системы регулирования. С применением изложенного подхода найдены параметры передаточной функции канала контролируемого возмущения объекта, отличающиеся от заданных не более чем на 6 % [4]. При исследовании управляемого лабораторного объекта (см. рис. 3) модель объекта в виде передаточных функций, найденных предложенным способом, прогнозирует температуру печи с максимальной абсолютной погрешностью не более 3,4 °C. Среднее квадратичное отклонение температуры печи от реального значения не превышает 1,2 °C.
С применением изложенного подхода проведена идентификация некоторых каналов промышленной вакуумной колонны, предназначенной для разделения предварительно нагретого мазута на фракции.
В качестве объекта идентификации взят контур регулирования уровня на «глухой» тарелке второго слоя насадки. Обучающая и тестовая выборки экспериментальных данных включают уровень на «глухой» тарелке второго слоя насадки, выходной сигнал регулятора и 5 параметров, оказывающих влияние на регулируемую величину, являющихся контролируемыми возмущениями. Обучена динамическая нейронная сеть. На основе обученной нейронной сети создана модель технологического объекта с системой регулирования. На модели технологического объекта с системой регулирования проведен вычислительный эксперимент по определению частотных характеристик каналов «вход-выход». По полученным данным каналы технологического объекта аппроксимированы передаточными функциями апериодического звена первого порядка с чистым запаздыванием.
Для сравнительной оценки полученных результатов построена имитационная модель технологического объекта (без системы управления), описанная найденными передаточными функциями каналов объекта. Коэффициент корреляции для прогнозируемого имитационной моделью уровня на «глухой» та-
324
362

Информационные технологии в управлении техническими системами и технологическими процессами
релке второго слоя насадки и его реального значения превышает 0,6. Абсолютная погрешность не превышала 0,14 %, при диапазоне изменения уровня равного 0,33 %.
Рис. 6. Тестирование имитационной модели технологического объекта
5. Заключение
Рассмотрены подходы к применению искусственных динамических нейронных сетей в задачах управления и идентификации технологических объектов.
Предложенные способы адаптивного управления по модели, где в качестве модели выступает динамическая нейронная сеть, показали свою эффективность в рамках исследования методом имитационного моделирования.
Подходы к параметрической идентификации технологических объектов передаточными функциями каналов «вход-выход» по результатам вычислительных и натурных экспериментов подтвердили корректность, а также высокую аппроксимирующую способность примененной динамической рекуррентной нейронной сети. Подходы применимы для идентификации управляемых технологических объектов с непрерывным характером процессов по данным наблюдений технологических переменных в режимах эксплуатации.
325
363
Управление большими системами. Выпуск XX
Литература
1.Адаптивный ПИД-регулятор с минимизацией числа изменений выходного сигнала / А.М. ШУБЛАДЗЕ, С.В. ГУЛЯЕВ,
А.А. ШУБЛАДЗЕ, В.Р. ОЛЬШВАНГ, В.А. МАЛАХОВ, С.И. КУЗНЕЦОВ, А.В. КРОТОВ // Автоматизация в промыш-
ленности. – 2010. – № 12. – С. 7–10.
2.ШАРОВИН И.М., СМИРНОВ Н.И., РЕПИН А.И. Применение искусственных нейронных сетей для адаптации САР в процес-
се их эксплуатации // Промышленные АСУ и контроллеры. – 2012 – №. 4 – C. 27–32.
3.ШУМИХИН А.Г., БОЯРШИНОВА А.С. Идентификация сложного объекта управления по частотным характеристикам, полученным экспериментально на его нейросете-
вой динамической модели // Автоматика и телемеханика. – 2015. – № 4. – С. 125–134.
4.ШУМИХИН А.Г., БОЯРШИНОВА А.С. Параметрическая идентификация управляемого объекта в режиме его эксплуатации с применением технологии нейронных сетей // Вестник ПНИПУ. Электротехника, информационные технологии, сис-
темыуправления. – 2016. – №19. – С. 102–110.
ARTIFICIAL NEURAL NETWORKS APPLYING
TO CHEMICAL-ENGINEERING PROCESSES CONTROL ALGORITHMS AND IDENTIFICATION TASKS
Anna Boyarshinova, Perm National Research Polytechnic University, Perm, assistant (boyarshinovaann@gmail.com).
Alexander Shumikhin, Perm National Research Polytechnic University, Perm, Doctor of Technical Science, professor, head of department of automation of technological processes (atp@pstu.ru).
Abstract: We have considered approaches to artificial dynamic neural networks applying to chemical-engineering processes control algorithms and identification tasks. Control systems with adaptation algorithms outlined. The control systems are open–closed and com-
326
364
Информационные технологии в управлении техническими системами и технологическими процессами
bined. A dynamic neural network represents a model of object. We show the control systems estimates by modeling. Results of research on control object parametric identification with its dynamic neural network model are given. Neural network is trained on the data of control object operating. The resulting model simulates the behavior of the system and lets us find the system’s output, including outputs for periodic test influences. By the resulting complex frequency response we find the parameters of the channel transfer function. We show an example of identification for “input–output” channels with a delay of the imitational object under random noise at the input. Results of imitational modeling and full-scale experiments with laboratory and plant objects are given.
Keywords: technological process, neural network, modeling, adaptation algorithms, control system, identification.
327
365

Управление большими системами. Выпуск XX
УДК 621.771.23 ББК 78.34
МАТЕМАТИЧЕСКОЕ МОДЕЛИРОВАНИЕ ПРОЦЕССА ФОРМОИЗМЕНЕНИЯ ПОВЕРХНОСТНОГО ДЕФЕКТА ПОДКАТА
ВПРОЦЕССЕ ХОЛОДНОЙ ПРОКАТКИ
СИСПОЛЬЗОВАНИЕМ ПРОГРАММНОГО КОМПЛЕКСА КОНЕЧНО-ЭЛЕМЕНТНОГО АНАЛИЗА
Мещерякова А.О.1
(Липецкий государственный технический университет, Липецк)
В работе предложена математическая модель, позволяющая отследить трансформацию поверхностных дефектов типа «раковина» на любой стадии деформации процесса холодной прокатки, а также приведены результаты исследования формоизменения дефекта с помощью конечно-элементного анализа. Материалы работы могут быть применены в металлургическом производстве для повышения качества поверхности холоднокатаных полос.
Ключевые слова: пластическая деформация, холодная прокатка, конечно-элементный анализ, напряжения, поверхностные дефекты
1.Введение
Внастоящее время этап развития прокатного производства характеризуется постоянным ростом требований к качеству металлопроката. Для определения качества прокатной продукции используется большое количество характеристик, таких как химический состав, механические и химические свойства металла и др. Одной из наиболее значимых характеристик является на-
1 АнастасияОлеговнаМещерякова, магистрант (mao11077@rambler.ru).
328
366
Информационные технологии в управлении техническими системами и технологическими процессами
личие на поверхности металла дефектов, своевременное выявление которых исключает попадание брака на последующие этапы обработки.
Целью работы является исследование механизма формоизменения поверхностного дефекта горячекатаного подката типа «раковина» и полосы в процессе холодной прокатки, его моделирование, а также определение влияния технологических факторов процесса на выкатываемость дефектов поверхности для разработки режимов холодной прокатки, способствующих предотвращению образования поверхностных дефектов.
Исследование трансформации поверхностных дефектов проводилось путем построения математической модели процесса на основе теории плоской пластической деформации и кинематики прокатки, а также с помощью вычислительной системы конечно-элементного моделирования DEFORM-3D, которая предназначена для анализа трехмерного течения металла при различных процессах обработки металла давлением. Моделирование на ЭВМ с использованием МКЭ позволяет наглядно продемонстрировать картину видоизменения дефектов на каждом этапе прокатки листа и выполнить анализ дополнительных параметров.
2. Математическое моделирование процесса формоизменения поверхностного дефекта подката в процессе холодной прокатки
2.1. МАТЕМАТИЧЕСКАЯ МОДЕЛЬ ТРАНСФОРМАЦИИ ПОВЕРХНОСТНОГО ДЕФЕКТА
В качестве математической модели трансформации поверхностного дефекта предложено рассматривать уравнение среднего контактного напряжения и критерий интенсивности сглаживания дефектов [4, 11].
Для вывода модели среднего контактного напряжения использовались основные уравнения плоской деформации, а также некоторые параметры очага деформации полосы и уравнение равновесия Кармана [1, 4, 5, 7, 8]. Пренебрегая влиянием упругих деформаций валков и полосы, получим [13, 15]:
329
367
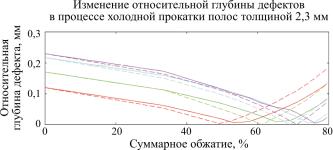
Управление большими системами. Выпуск XX
(1) |
p |
= 1,15σ |
|
(1+ |
μl |
), |
ф |
|
|||||
|
ср |
|
|
2hср |
|
|
|
|
|
|
|
|
где pср – среднее контактное напряжение; hср – средняя толщина полосы; σф – сопротивление металла пластичной деформации; μ – коэффициент трения.
Для описания процесса прокатки полосы с дефектом был принят критерий интенсивности сглаживания дефекта [2]:
(2) ζ |
δ |
= 0,19(1− e−0.9nσ3 )[1+ ( |
h02 |
+ |
9h02 |
) + (0,04 + 0,004RB )], |
|
b2 |
l2 |
||||||
|
|
|
a |
||||
|
|
|
δ |
|
δ |
|
где nσ – коэффициент напряженного состояния; bσ, l σ – ширина и длина поверхностного дефекта; RaB – шероховатость поверх-
ности рабочих валков.
Относительная глубина дефекта на i-й стадии деформации определяется как
(3) |
bi |
= |
b0 |
− ζ δ |
ln( |
h0 |
), |
hi |
h0 |
|
|||||
|
|
|
|
hi |
где bi, h i – глубина дефекта и толщина полосы на i-й стадии деформации.
Анализируя результаты, представленные на рис. 1, можно сделать вывод, что дефекты небольшой глубины выкатываются интенсивнее, нежели дефекты с большей начальной относительной глубиной, но при высоких суммарных обжатиях есть риск повторного образования дефекта.
Рис. 1. График исследования зависимости относительных глубин дефектов от различных значений величин коэффициентов трения
330
368

Информационные технологии в управлении техническими системами и технологическими процессами
Для повышения качества прокатываемых полос путем устранения поверхностных дефектов типа «вытравленная окалина» и «рябизна» предложено осуществлять прокатку со степенью суммарной относительной деформации, определяемой из выражения [14]
(4) ε = 0,366 −1,255μ + 1,749δ0 .
(опт)
h0
2.2. МАТЕМАТИЧЕСКАЯ МОДЕЛЬ ТРАНСФОРМАЦИИ ПОВЕРХНОСТНОГО ДЕФЕКТА С ПОМОЩЬЮ МКЭ
Далее, по результатам работ [8, 9, 10, 12] было проведено математическое моделирование процесса формоизменения поверхностных дефектов типа «раковина» при холодной прокатке полосы на непрерывном пятиклетевом стане 1700 холодной прокатки с помощью специализированного программного ком-
плекса DEFORM-3D.
Программный комплекс DEFORM-3D базируется на следующихосновныхзависимостях:
– дифференциальное уравнение равновесия
(5) |
|
∂σ |
ix |
+ |
∂σ iy |
+ |
∂σ |
iz |
|
+ Gi |
= 0, |
|
|||||||||
|
|
|
|
|
|
|
|
|
|
||||||||||||
|
|
∂x |
∂y |
∂z |
|||||||||||||||||
|
|
|
|
|
|
|
|
|
|
|
|
|
|
||||||||
|
– уравнение |
зависимости |
между вектором перемещений |
||||||||||||||||||
и компонентами тензора деформаций |
|
|
|
|
|
||||||||||||||||
(6) |
ε ij |
= |
1 |
( |
∂U |
i + |
|
∂U j |
|
+ |
|
∂U |
k |
|
∂U |
k |
). |
||||
2 |
|
|
|
∂xi |
|
∂xi |
|
|
|
||||||||||||
|
|
|
|
|
∂x j |
|
|
|
|
∂x j |
|||||||||||
|
Поле допустимых скоростей узловых точек конечных эле- |
||||||||||||||||||||
ментов в матричном виде |
|
|
|
|
|
|
|
|
|
|
|
|
|
|
|||||||
(7) |
|
|
|
|
|
vi |
= [N ]{vB}, |
|
|
|
|
|
|
|
где [N] – функция формы элемента; {νB} – вектор узловых скоростей.
Условие пластичности Губера–Мизеса
(8) |
3 |
σ ij' |
σ ij' |
= σ |
2 , |
|
2 |
||||||
|
|
|
|
|
331
369

Управление большими системами. Выпуск XX
где σij’ – девиатор напряжений;
(9) σ = σ ф = σ исх + aε b − предел текучести, представленный
известным соотношением Третьякова–Зюзина, применимым для процессов холодного деформирования.
Напряжения трения на контактной поверхности определяется согласно закону Кулона–Амонтона
(10) |
|
τ = μσ , |
где µ – коэффициент трения. |
||
|
При |
моделировании процесса холодной прокатки были |
приняты |
следующие допущения: |
–влияние упругих деформаций валков и полосы не учитывается;
–скорость прокатных валков постоянна на протяжении каждого прохода;
–отсутствие уширения полосы.
При помощи SolidWorks и КОМПАС-3D, программных комплексов САПР для автоматизации работ промышленного предприятия на этапах конструкторской и технологической подготовки производства была смоделирована некоторая область подката начальной толщиной 4,5 мм. На поверхности полосы было смоделировано четыре поверхностных дефекта типа «раковина» разной глубины и с разным переходом к кратеру дефекта (рис. 2).
Рис. 2. Поверхность фрагмента смоделированной полосы с дефектами
332
370