
книги / Расчёт и проектирование систем обеспечения безопасности.-1
.pdf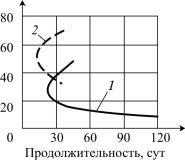
Образование жирных кислот приводит к понижению рН воды; однако иловая жидкость обладает буферными свойствами, что ограничивает снижение рН. Впрочем, в некоторых случаях возникает необходимость подщелачивания воды Na2CO3 [10].
Биоценоз анаэробного активного ила содержит до 1,5·1010 кислотообразующих и до 107 метанообразующих микроорганизмов; в составе биоценоза не более 1 % аэробных микроорганизмов, а также инфузорий и грибов, которые попадают в метантенк вместе с очищаемой водой.
Весь ход сбраживания лимитируется возможностями и состоянием популяции метанообразующих бактерий, чрезвычайно чувствительных к температурным условиям и имеющих малую скорость роста.
Метанообразующие бактерии относятся к разным популяциям: термофилов и мезофилов. Как следует из рис. 2, оптимальные температуры воды для термофилов около +53 ° С, для мезофилов +32 ° С. Применяется также популяция термофилов, для которой оптимальной считается температура +65 ° С (экстратермофилы). Даже небольшое отклонение температурыот оптимума существенно снижает скорость окисления.
То обстоятельство, что процессы, |
|
|
|
относящиеся к двум фазам сбражива- |
|
|
|
ния, совмещены во времени и осущест- |
|
|
|
вляются в одном объеме, не позволяет |
|
|
|
создать для них оптимальные условия. |
|
|
|
Специальные эксперименты под- |
|
|
|
твердили целесообразность проведения |
|
|
|
кислого и метанового брожения в раз- |
|
|
|
ных реакторах, раздельно. На рис. 15.5 |
Рис. 15.5. Влияние температуры |
||
приводится схема установки с разделе- |
|||
на продолжительность сбраживания: |
|||
нием фаз сбраживания. Реакторы вто- |
1 – |
мезофильное сбраживание, |
|
рой ступени должны работать с пони- |
2 – |
термофильное сбраживание |
женной (в 3–5 раз) удельной (на 1 м3 вместимости) нагрузкой.
Сравнение мезофильного и термофильного режимов сбраживания осадков показывает, что в терфильных условиях значительно интенсивнее иглубже происходит гидролиз твердого вещества, но образующийся анаэробный ил имеет очень большое удельное сопротивление и плохо обезвоживается. Процесс двухфазного термофильно-мезофильного сбраживания позволяетиспользоватьпреимуществаэтихдвухрежимов(рис. 15.6) [10].
361
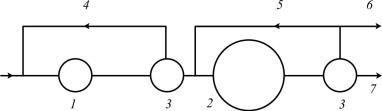
Рис. 15.6. Схемараздельного по фазам сбраживания: 1, 2 – метантенки кислой игазовой фаз; 3 – отстойники; 4 – рециркуляция осадкакислой фазы; 5 – рециркуляцияосадкащелочной (газовой) фазы;
6 – сбрососадка; 7 – отведение
Исследования показали, что двухфазное сбраживание (экстратермофильное в течение 0,6–1,0 суток, а затем мезофильное в течение 10 суток) увеличивает распад беззольного вещества осадка сравнительно с мезофильным однофазовым в 1,2–1,6 раза. Установки для двухфазового сбраживания представляют собой двухступенчатые метатенки разной вместимости с учетом продолжительностью процессов на каждом из двух этапов.
Расчет метантенков наиболее подробно разработан для условий стабилизации осадков городских сточных вод.
По исследованиям доктора технических наук Л.И. Гюнтер, предел сбраживания жиров составляет более 70 %, белков – 48 %, углеводов – 62,5 %. Для обычной композиции осадков городских сточных вод предел полного сбраживания, в пересчете на беззольную часть осадка, принимается:
Rlim = (0,92Cfat + 0,62Cgt + 0,34Cpzt) 100 %,
где Сfat, Cgl, Cpzt – содержание жиров, углеводов и белков в г на 1 г беззольной части.
Фактический распад беззольной части зависит от продолжительности сбраживания, исходной концентрации органики, ее вида и температуры осадков. Распад определяется по формуле
Rr = Rlim – krDmt,
где kr – коэффициент, зависящий от влажности сбраживаемой среды, т.е. учитывающий концентрацию органики; Dmt – доза суточной загрузки осадка, %, от вместимости метантенка, доза обратно пропорциональна продолжительности процесса.
В формуле не учитывается температура, так как предполагается, что она поддерживается оптимальнойвзависимостиот принятого режима.
362
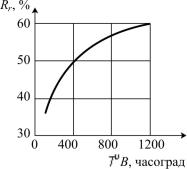
Рис. 15.7. График распада органики
В США распад определяется по величине произведения температуры на продолжительность сбраживания (рис. 15.7). Таким образом, влажность осадка не учитывается.
Расчет метантенков сводится к тому, что, задаваясь степенью распада, определяется продолжительность процесса, а по ней и вместимость метантенка:
Wmt = Qwt, м3,
где Wmt – вместимость метантенка, м3; Qw – суточная производительность метантенка в м3/сут, t – продолжительность, сут.
Зависимости, используемые для расчета метантенка, основываются на эмпирических связях между дозами загрузки, влажностью и другими параметрами. Вместе с тем такие расчеты должны базироваться на закономерностях кинетики ферментивных реакций.
Расчет метантенков для очистки высококонцентрированных сточных вод выполняется по формуле. Параметры, входящие в эту формулу, находятся опытным путем и зависят от качества очищаемой воды. Так, например, основываясь на опыте очистки некоторых конкретных видов стоков, рекомендовались к расчету: удельная скорость окисления r = 5,0–6,5 мг БПКполн на 1 г беззольной части ила в час, доза активного ила а = 20 г/л, его зольность S = 0,3 и т.д. Режим сбраживания принимается мезофильным как более устойчивый.
Считается, что очистка в метантенках целесообразна при значениях БПКполн от 6–10 до 20 г/л; установлена возможность ее применения при значениях ХПК до 75–100 кг/м3. В среднем на 1 кг снятой ХПК выделяется 0,1–0,35 м3 метана, а прирост активного ила составляет 0,05–0,5 кг. Потребность в биогенных веществах определяется отношением ХПК: азот: фосфор, которое должно составлять 100:2:0,1, что значительно меньше, чем требуется при аэробной очистке.
Опыт показывает, что снижение БПК при анаэробной очистке концентрированных сточных вод в метантенках находится в пределах 75–90 %. Таким образом, БПК после очистки остается весьма значительным и почти всегда требуется доочистка.
363
Как отмечалось, предварительная анаэробная деструкция изменяет молекулярную структуру некоторых субстратов, превращая их в менее устойчивые по отношению к аэробному окислению вещества.
При исследовании процесса биохимической очистки по схеме «метантенк– аэротенк» сточных вод фабрик первичной обработки шерсти было установлено, что на этапе аэробного окисления скорость реакции увеличивается на 12–13 %, так как происходит соответствующее уменьшение коэффициента Михаэлиса.
Анаэробный активный ил, особенно после термофильного режима, имеет высокий иловый индекс и плохо отстаивается. Поэтому существует опасность вымывания ила из метантенка. Как известно, радикальной мерой против этого служит иммобилизация микробиальной массы [9–11].
ГЛАВА 16. РАСЧЕТ СООРУЖЕНИЙ ДЛЯ ТЕРМИЧЕСКОЙ ПОДГОТОВКИ И ПЕРЕРАБОТКИ ОТХОДОВ
16.1. РАСЧЕТ И ПРОЕКТИРОВАНИЕ СООРУЖЕНИЙ ДЛЯ СУШКИ ТВЕРДЫХ ОТХОДОВ.
16.1.1. Теоретическая часть
Сушка – это процесс удаления влаги из твердого или пастообразного материала путем испарения содержащейся в нем жидкости за счет подведенного к материалу тепла. Целью сушки является улучшение качества материала (снижение его объемной массы, повышение прочности) и в связи с этим увеличение возможностей его использования. В химической промышленности, где технологические процессы протекают в основном в жидкой фазе, конечные продукты имеют вид либо паст, либо зерен, крошки, пыли. Это обусловливает выбор соответствующих методов сушки.
Наиболее широко распространены в химической технологии конвективный и контактный методы сушки. При конвективной сушке тепло передается от теплоносителя к поверхности высушиваемого материала. В качестве теплоносителей используют воздух, инертные и ды-
364
мовые газы. При контактной сушке тепло высушиваемому материалу передается через обогреваемую перегородку, соприкасающуюся с материалом. Несколько реже применяют радиационную сушку (инфракрасными лучами) и сушку электрическим током (высокой или промышленной частоты).
Методы сушки сублимацией, в жидких средах, со сбросом давления находят применение в других отраслях промышленности.
Применяемые в химической промышленности виды сушилок можно классифицировать по технологическим признакам: давлению (атмосферные и вакуумные), периодичности процесса, способу подвода тепла (конвективные, контактные, радиационные, с нагревом токами высокой частоты), роду сушильного агента (воздушные, газовые, сушилки на перегретом паре), направлениям движения материала и сушильного агента (прямоточные и противоточные), способу обслуживания, схеме циркуляции сушильного агента, тепловой схеме и т.д.
Выбор типа сушилки зависит от химических свойств материала. Так, при сушке материалов с органическими растворителями используют герметичные аппараты и сушку обычно проводят под вакуумом; при сушке окисляющихся материалов применяют продувку инертными газами; при сушке жидких суспензий используют распыливание материала. Конструкции сушилок весьма разнообразны, и выбор их определяется технологическими особенностями производства.
Наиболее широкое распространение получили барабанные сушилки. Эти сушилки отличаются высокой производительностью и относятся к конвективным сушилкам. В качестве сушильного агента в них используют воздух и дымовые газы. В этих аппаратах сушке подвергают соли, топливо, пасты; их используют в производствах соды, удобрений, ядохимикатов [12–17].
Сушилка представляет собой (рис. 16.1) цилиндрический барабан 1, к которому крепятся бандажи 9, опирающиеся на опорные 3 и опорноупорные 6 ролики. Вращение барабану передается от электродвигателя через редуктор 4 и зубчатый венец 5, закрытый кожухом 10. Мощность двигателя – от 1 до 40 кВт. Частота вращения барабана 1–8 об/мин. Размеры корпусов сушилки нормализованы. Так, по нормали машиностроения МН 2106–61 установлены следующие диаметры бараба-
нов: 1000, 1200, (1400), 1600, (1800), (2000), 2200, 2500, 2800 мм.
365
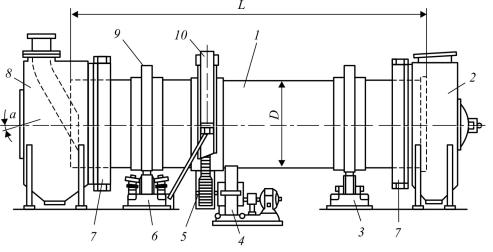
Длина барабана зависит от диаметра и составляет 4, 6, 8, 10, 12, 14, 16, 18, 20, 22 м. Обычно отношение длины L барабана к диаметру D должно быть L/D = 3,5–7,0.
Рис. 16.1. Барабанная сушилка
Высушиваемый материал подается в приемную камеру 8 и поступает на приемно-винтовую насадку, а с нее – на основную насадку. Лопасти насадки поднимают и сбрасывают материал при вращении барабана. Барабан установлен под углом а к горизонтали до 6°; высушиваемый продукт передвигается к выгрузочной камере 2 и при этом продувается сушильным агентом. Между вращающимся барабаном и неподвижной камерой установлено уплотнительное устройство 7. Выбор типа насадки зависит от материала. Для крупных кусков и налипающих материалов применяют лопастную систему насадки, для сыпучих материалов – распределительную, для пылеобразующих материалов – перевалочную с закрытыми ячейками. Барабан заполняют материаломобычно до 20 %.
Туннельные сушилки применяют для сушки долго сохнущих материалов. Высушиваемый материал помещают на вагонетки (тележки), которые проталкиваются специальным толкателем через туннель. Длина туннеля составляет 25–60 м. Воздух проходит через весь туннель; во избежание расслаивания потока воздуха по высоте и неравномерности сушки аппарат разбивают на ряд зон, на перекрытиях
366

которых устанавливают отопительно-вентиляционные агрегаты, создающие вертикальную циркуляцию воздуха. Скорость теплоносителя
2–3 м/с.
Время сушки в обычных сушилках может достигать 200 ч. В сушилке, показанной на рис. 4.28, время сушки сокращено до 20 ч за счет интенсификации процесса и изменения режима (использование воздуха
сповышенными влажностью и температурой). Основные размеры таких сушилок определяются продолжительностью сушки. Длина сушилки зависит от размеров тележек, емкости туннеля и определяется производительностью и временем сушки.
Всушилках с кипящим слоем (рис. 16.2) обычно сушат продукты
сразмерами зерен от 0,1 до 5,0 мм. Эти аппараты отличаются высокой надежностью, сокращением времени сушки за счет усиленного перемешивания материала в сушильной камере. Такие сушилки используют для сушки сульфата аммония, хлористого калия, винифлекса и целого ряда сыпучих и даже пастообразных материалов. Сушилки просты по конструкции. Материал через бункер подается на наклонную решетку, которая может получать колебания от вибратора. На сетке происходит псевдоожижение материала воздухом, поступающим снизу. Отработанный воздух проходит две параллельные щели в верхней части камеры
и отводится |
через патрубок, а материал выгружается через патрубок |
и частично |
через патрубок. В промышленности используют сушилки |
и с несколькими камерами. Разновидностью этих сушилок являются вихревые сушилки.
Рис. 16.2. Сушилка с кипящим слоем
Распылительные сушилки. Распылительные сушилки применяют для обезвоживания концентрированных растворов веществ, суспензий, эмульсий, подвижных паст. Материал, подлежащий высушиванию, распыливается механическими форсунками (производство ук-
367
сусно-кислого кальция), пневматическими форсунками, центробежными дисковыми распылителями (производство антибиотиков). При этом площадь поверхности материала резко возрастает. Горячий воздух или дымовые газы подаются в сушильную камеру по прямоточной или противоточной схеме и отводятся из камеры через пылеулавливающее устройство. Высушенный материал (сушка происходит мгновенно) падает вниз и гребковым устройством выводится из камеры. Такие сушилки используют для сушки хлористого винила, меламина, триполифосфата натрия, глинозема. Для сушки применяют горячие газы, но вследствие малого времени контакта поверхность материала прогревается только до 60–70 ° С и не пересыхает. Здесь можно совмещать сушку с одновременным прокаливанием и охлаждением материала.
Высушенный материал попадает на прокалочные тарелки, которые обогреваются дымовыми газами. Материал перемешивается гребками
ипересыпается с тарелки на тарелку, а затем, после прохождения охлаждающей тарелки, выводится из сушилки.
Помимо рассмотренных типов конвективных сушилок в химической промышленности применяют и другие конструкции: ленточные, камерные, аэрофонтанные сушилки, пневмосушилки, сушилки с виброкипящим слоем и т.д.
Контактные сушилки. В контактных сушилках тепло высушиваемому материалу передается через металлическую стенку, обогреваемую паром или водой. Поверхность контакта может быть либо цилиндрической, когда паста или густой раствор высушиваемого продукта подаются на поверхность обогреваемого цилиндра (одно- и двухвальцовые сушилки), либо плоской, когда влажный продукт насыпается на горизонтальные плиты, обогреваемые изнутри паром, водой, электронагревателями. Применяют цилиндрические поверхности с наружным обогревом цилиндров
иподачей материала внутрь (гребковые, центробежно-щеточные сушил-
ки) [12–15].
Одновальцовая сушилка представляет собой полый чугунный валец 5, вращающийся от электродвигателя. Пар, обогревающий валец, поступает через патрубок 2 и цапфу 3. Влажный материал подается в лоток 9, где перемешивается мешалкой. Конденсат отводится через сифонную трубку 1. Пленка материала, образующаяся на поверхности вальца, калибруется скребком, укрепленным на оси 11, и срезается
368
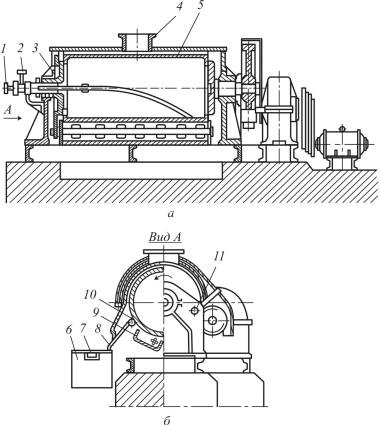
Рис. 16.3. Одновальцовая сушилка: а – основная схема; б – вид А
ножом 10. Высушенный продукт по фартуку 8 через патрубок 7 поступает в ящик 6. Влажный воздух отсасывается через патрубок 4.
16.1.2. Расчет установок
Общая схема расчета сушилки:
1. На основе уравнения материального баланса определяется количество удаляемой влаги в процессе сушки:
GH = GK + W,
GH·(100 – wн) = GK·(100 – wк),
GH, GK – расход влажного и сухого материала, W – расход испарившейся влаги,
wн, wк – влажность начальная и конечная материала.
369
2. На основе условия равновесия определяют конечное влагосодержание сушеного агента и равновесную относительную влажность сушеного агента:
xк = f (φp, tp), φp = (wp, tpм).
3. На основе расхода испарившейся влаги и разности влагосодержания сушеного агента определяется расход абсолютно сухого сушеного агента на процесс сушки:
L = |
|
W |
. |
|
X K |
− X H |
|||
|
|
4.На основе теплового баланса определяется общий расход тепла
вкалорифере сушилки:
QK = L(I2 − I0 ) + GкCк(θк − θн) + GтрСтр(tтрк − tтрн) −WCвл(θн + Qпотерь),
QK = L(I1 − I0 ),
где I0, I1, I2 – энтальпия сушеного агента перед калорифером, после калорифера и в конце процесса сушки;
Ск, Стр, Свл – удельная теплоемкость сухого материала, транспортных средств сушилки и удаляемой влаги;
θн, θк – начальная и конечная температура материала;
tтрн, tтрк – начальная и конечная температура транспортных устройств;
Qпот – внешние потери тепла в сушилке.
5. На основе общего расхода тепла определяется необходимый расход топлива:
B = QK (QpH − ηТ ) ,
Qрн – низшая теплота сгорания топлива;
ηТ – коэффициент полезного действия топки.
6. На основе знания скорости движения сушеного агента и материала определяется относительная скорость движения фаз для каждого аэродинамически различного участка сушилки:
vотнi = iгi − vтвi ;
Vгi, Vтвi – скорость сушеного агента иматериала на участке сушилки.
370