
книги / Расчёт и проектирование систем обеспечения безопасности.-1
.pdf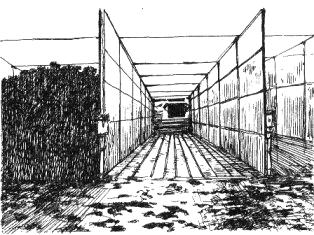
Широкое распространение этот метод получил в 90-х годах того же века, когда для производства компоста фазы 1 стали использовать аэрированные полы, бункеры и тоннели (рис. 15.1).
Таблица 15.1 Эволюция продолжительности компостирования (по П.А. Сычову)
Год |
Продолжительность стадий компостирования, дни |
|||
Предварительное |
Плоская куча |
Бурт, бункер, |
Итого |
|
|
увлажнение |
|
тоннель фазы 1 |
|
1970 |
11 |
7 |
8 – бурты |
26 |
1980 |
9 |
6 |
7 – бурты |
22 |
1990 |
5 |
44 |
6 – бурты |
15 |
1994 |
5 |
4 |
6 – бункер |
15 |
1996 |
1* |
0 |
6 – тоннель |
7 |
Рис. 15.1. Биотоннель
Для проведения фазы 1 тоннели используют только в тех странах, где запрещено проводить компостирование на улице из-за выделения вредных газов в окружающую среду. В остальных странах грибоводы используют бункеры и аэрированные полы [8].
Тоннели (полностью закрытые системы для проведения фазы 1) более требовательны к качеству перемешивания и влажности загружаемой смеси исходных компонентов, чем бункеры (открытые системы).
Преимуществами использования бункеров и аэрированных полов являются:
351
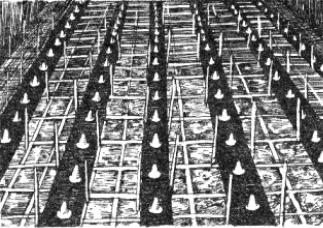
1)независимость от погодных условий (особенно в случае приготовления компоста на улице);
2)возможность контролирования процесса;
3)сохранение большего количества питательных веществ для шампиньонов (однако больший риск появления конкурентов за субстрат);
4)отсутствие перебивки компоста, а следовательно, улучшение структуры компоста;
5)большая однородность компоста;
6)сокращениеплощадей, используемыхдляприготовлениякомпоста;
7)уменьшение потери сухого вещества за фазу 1 и образование большего количества компоста из такого же количества исходных компонентов – из 1 т соломы можно получить 3,5 т компоста фазы 1.
Применением систем компостирования с аэрацией можно улучшить качество компоста, произвести больше компоста за тот же или более короткий срок.
Принцип устройства аэрированных полов, бункеров и тоннелей фазы 1 основан на том, что подача воздуха в компостируемую массу осуществляется через систему труб, проложенных под полом. В этих трубах делают отверстия, в которые вставляют форсунки (рис. 15.2).
Рис. 15.2. Аэрированные полы
Трубы с форсунками располагают вдоль бункера или тоннеля. Они погружены в бетон так, что верх форсунок каждой трубы находится на дне желоба 30-миллиметровой ширины и 20-миллиметровой глубины.
352
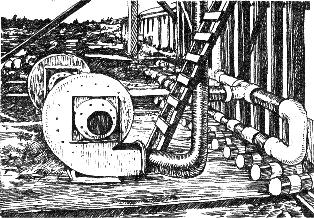
Сначала трубы фиксируют железной арматурой сверху и снизу. Затем на форсунки накладывают деревянные рейки и заливают бетоном (толщина около 35 см). Когда бетон застынет, рейки убирают. Наличие желоба предохраняет форсунки от повреждения погрузчиками или другими машинами, которые могут работать на аэрированном полу, в бункере или в тоннеле. Кроме того, желоб способствует распределению воздуха под компостом и удалению излишков воды [8].
Трубы диаметром 150–170 мм располагают параллельно на расстоянии 400–600 мм друг от друга (по центру), а форсунки – на расстоянии 400 мм (по центру) друг от друга вдоль каждой трубы. Во время строительства пола форсунки не имеют отверстий для выхода воздуха. Их просверливают наверху каждой форсунки позже, при наладке системы. Лучше вначале сделать отверстие как можно меньше, порядка 4–6 мм, а затем уже расширить его, если количество воздуха будет недостаточным. Количество же воздуха напрямую зависит от величины создаваемого давления. Это давление может быть 500 Па в системах низкого давления и может доходить до 7000 Па в системах высокого давления. Отверстия в форсунках очень маленькие, поэтому они редко забиваются. Открытая поверхность пола в отличие от тоннелей фазы 2 составляет всего 0,06–0,08 % от общей площади пола.
Воздух из вентилятора попадает вначале в приемную трубу (ресивер или расширитель) и уже оттуда поступает в каждую трубу, расположенную под полом бункера. Это обеспечивает одинаковое давление воздуха во всех трубах (рис. 15.3).
Рис. 15.3. Ресивер
353
С противоположной стороны каждую трубу изгибают под углом 90° на глубину 60–70 см и опускают в яму, наполненную водой, в которую через форсунки и трубы стекает и вода из компоста. Из ямы должен быть сделан сток в канализацию. Возможен и другой вариант, когда все трубы снова соединяют вместе, и уже от этой соединительной трубы отходит U-образно изогнутая дренажная трубка, которая заглублена настолько, чтобы поддержать нужное давление в трубах (глубину рассчитывают, исходя из давления, которое развивает вентилятор). Общий дренаж обеспечивает полный контроль стока воды и ее удаление в резервуар для повторного использования. Вода в резервуаре должна снабжаться кислородом, чтобы предотвратить риск развития анаэробной микрофлоры. Трубы и пол должны иметь небольшой уклон, обеспечивающий сток воды. Уклон труб и пола располагают в направлении от вентилятора к дренажной трубке.
Производительность вентилятора для данной системы должна составлять максимально 25 м3/т компоста в час (в 10 раз меньше, чем производительность вентилятора, используемого для тоннелей фазы 2). Время включения и выключения вентилятора задают таймером. Желательно также, чтобы работа вентилятора была связана с системой измерения кислорода для контроля подачи воздуха при слишком низком содержании кислорода в компосте. Вентилятор должен развивать высокое давление 6000–7000 Па и при этом должен сохранять свою производительность.
Системы с высоким давлением имеют некоторые преимущества, связанные с большей скоростью воздуха, выходящего из каждой форсунки, а также с тем, что гарантируют лучшее распределение воздуха – выход одинакового объема воздуха по всей площади пола.
Компостируемые материалы могут быть уложены более высоким слоем (до 4 м), обеспечивая лучшее использование площади. Очень важно, что системы с низким давлением (например, тоннель фазы 2) требуют, чтобы компост в них покрывал всю площадь пола, чтобы слой имел одинаковый вес и толщину, иначе воздух будет проходить не сквозь компостируемую массу, а сквозь свободное пространство [8].
В системах с высоким давлением объем и напор воздуха, выходящего из каждой форсунки, одинаков и не зависит от толщины слоя компоста и качества загрузки бункера.
354
Расчет количества и размера бункеров зависит от следующих показателей:
1)количество компоста фазы 2, необходимое для загрузки в камеры еженедельно;
2)количество «зеленого» компоста, необходимое для загрузки
втоннели фазы 2 еженедельно;
3)продолжительность фазы 1 (от длительности процесса зависит количество требуемых бункеров);
4)количество бункеров, необходимых для загрузки существующих тоннелей фазы 2;
5)высота загрузки бункера и количество компостируемой смеси на 1 м2 пола бункера.
Типичный бункер имеет ширину от 3,5 до 6 м. Высота стен от 3 до 6 м. Длину бункера определяют в зависимости от необходимого количества компоста фазы 1, учитывая, что на 1 м2 можно загрузить 1500–2000 кг компостируемой смеси.
Тоннели фазы 1 – это системы с полами, работающими под повышенным давлением подобно бункерам и аэрированным полам, но имеющими крышу, двери и отверстие для выброса воздуха и полный контроль выброса в окружающую среду. В них также есть возможность производить водно-кислотную очистку выходящего воздуха и установить добавочные биофильтры на отверстие выброса воздуха, чтобы уменьшить неприятные запахииэмиссию аммиака.
Фаза 1 в бункерах и тоннелях
Провести процесс компостирования современным методом можно двумя способами. Первый способ предполагает наличие градиента температур в компостируемой массе. Этот процесс можно осуществить в бункере. Второй – основан на том, что вся компостируемая масса находится при одинаковой температуре (отсутствие градиента температур), а для этого необходима постоянная рециркуляция воздухачерезслой компоста.
Такой процесс возможен только в тоннеле фазы 1. Но так как
внашей стране пока нет жесткого экологического контроля за выбросом
ватмосферу вредных веществ, более подходящим и менее дорогостоящим для нас является компостирование в бункерах.
Высокая температура (с градиентом)
Впроцессе компостирования в бункерах в компостируемую массу поступает очень небольшое количество воздуха (8–15 м3/т в час). Одна-
355
ко благодаря высокому давлению воздуха, создаваемому в трубах, и маленьким отверстиям форсунок воздух пронизывает весь слой компоста. Наличие направляющих (форсунок) позволяет загружать компост неравномерным слоем или не полностью загружать бункер, что невозможно сделать в тоннеле, где давление воздуха меньше, а открытая поверхность пола гораздо больше. Высота слоя компоста в бункере может быть 3,5–4 метра.
Посколку рециркуляции воздуха в бункере нет, в слое компоста возникает градиент температур. Около 15 % слоя компоста, прилегающего к полу бункера, имеет температуру в пределах 30–60 ° С. В этом слое продолжается жизнедеятельность термофильных микроорганизмов. Остальная часть компоста находится при температуре 75–83 ° С. Эта температура способствует химическим реакциям (реакция карамелизации), при которых происходит обильное выделение аммиака, разрушаются связи между лигнином и целлюлозой, происходит размягчение и потемнение соломы. Основное отличие компостирования в бункере от традиционной системы в буртах заключается в том, что почти весь компост, за исключением нижнего слоя, подвергается карамелизации при температуре 75–83 ° С и полностью отсутствует анаэробная зона. Температура компоста в бункере никогда не может превысить 83–85 ° С, и это не зависит ни от размеров компостируемой массы, ни даже от ее термоизоляции. Происходит это именно потому, что образование тепла полностью прекращается ввиду инактивации микроорганизмов при температуре выше 60 ° С.
Впроцессе компостирования в бункере концентрация кислорода
вкомпосте постепенно увеличивается от 3 до 14 %. Это происходит изза того, что, во-первых, при повышении температуры доступ воздуха увеличивается в результате естественной тяги. Во-вторых, при повышении температуры выше 60 ° С жизнедеятельность микрофлоры постепенно прекращается. В связи с этим постепенно уменьшается потребление ею кислорода. Минимальное потребление кислорода происходит при 80–83 ° С.
Необходимо проявлять осторожность при подаче воздуха, так как даже небольшой избыток воздуха может привести к охлаждению компоста. Это приведет к увеличению содержания кислорода и уменьшению уровня аммиака, который очень важен для успешного проведения фазы 2 (при высоких температурах выделение аммиака происходит более интенсивно, чем в диапазоне 40–60 ° С) [8].
356
Высокая температура (без градиента)
При высокотемпературном процессе без градиента температур происходит рециркуляция воздуха в тоннеле фазы 1 так же, как и в процессе проведения фазы 2. В результате температура постепенно поднимается до уровня 75–83 ° С.
Температурные различия во всем слое компоста и в воздухе под компостом можно поддерживать внутри диапазона в несколько градусов. Кислород доступен в достаточной степени, так как в системе циркулирует большое количество воздуха. После того как температура в компосте превысит 60 ° С, термофильная микрофлора постепенно исчезает из компоста. Компост становится «мертвым». Поэтому для успешного проведения фазы 2 в компост необходимо добавить микрофлору, которая обеспечит перевод аммиака в устойчивые формы азота, сделает компост селективным. Для этого в компост фазы 1 подмешивают около 10 % компоста фазы 2, где доминантным термофильным ви-
дом является Scytalidium thermophilum.
Перед началом компостирования необходимо проанализировать исходные компоненты и точно составить формулу компоста. Расчет соотношения компонентов проводят так же, как и для традиционного компостирования. Для успешного проведения процесса очень важно, чтобы исходные компоненты были хорошего качества [8–11].
15.2. РАСЧЕТ И ПРОЕКТИРОВАНИЕ СООРУЖЕНИЙ ДЛЯ АНАЭРОБНОЙ СТАБИЛИЗАЦИИ ОТХОДОВ
Всистемах очистки концентрированных биоразлагаемых стоков
ипереработки органических твердых, полужидких веществ и осадков в анаэробных условиях нет внешних акцепторов водорода. Цель анаэробного окисления – стабилизация органических соединений, содержащихся в необработанных отходах. Окисление происходит в процессах брожения и анаэробного дыхания по следующей схеме:
Одно из основных преимуществ анаэробного сбраживания – минимальное образование биологически активных твердых веществ. Другие преимущества заключаются в возможности получения полезных конечных продуктов – горючего газа и сброженного ила. Более высокую норму нагрузки также следует отнести к достоинствам анаэробных процессов.
357
Недостатки анаэробных систем – малая скорость роста микробов
иочень высокая (по сравнению с системами аэробной обработки) минимально необходимая для стабильного воспроизводства клеток продолжительность пребывания биологически активных веществ в сооружениях (2–6 сут).
Обычно анаэробные системы применяют для сбраживания осадков первичных отстойников и избыточного активного ила аэробных биохимических систем очистки бытовых вод и их смесей с некоторыми производственными стоками. Успешно используют такие системы и для переработки промышленных и сельскохозяйственных отходов с высоким содержанием твердых веществ (отходов боен, отходов процессов переработки овощей и фруктов и т.д.). В большинстве случаев удается получить достаточно стабилизированный биологически неразлагаемый после обезвоживания осадок, горючий газ (по крайней мере, для собственных нужд) и жидкий сток, обычно требующий доочистки (например, окислением в аэробных условиях). В таких системах используют одно-
идвухступенчатые емкостные сооружения с перемешиванием.
Вдвухступенчатой системе первое сооружение представляет собой биологическую установку непрерывного действия с полным перемешиванием, а второе сооружение может быть использовано для отделения и концентрирования твердых веществ. В таких системах возможен возврат части осадка из второй ступени в первую для увеличения в ней дозы биологически активных микроорганизмов и интенсификации процесса (напомним, что без рециркуляции среднее время удерживания клеток и отходов в первой ступени одинаковы). Однако применение обычных отстойников на второй ступени возможно только при условии предварительной дегазификации потока первой ступени, поскольку газовыделение препятствует отстаиванию. Поэтому двухступенчатые системы в основном используют для частичного разделения двух стадий анаэробной обработки: получения летучих органических кислот и метанового брожения.
Для выращивания метановых бактерий необходимо поддерживать оптимальные для их развития условия во второй ступени (рН 6,0–8,5; температура 37–40 ° С для мезофильного брожения и 55 ° С – для термофильного [9, 10].
Сложность увеличения продолжительности удерживания клеток при рециркуляции и необходимость интенсификации процесса привели
358
к созданию аппаратов с насадкой, в которых анаэробные организмы растут, закрепляясь на насадке (лучше – на округлых камнях), или в заполненных жидкостью порах. При этом значительно увеличивается время пребывания активных микроорганизмов (их «возраст») и более эффективно (как при фильтрации через зернистый слой) отделяется жидкость от твердой фазы. Такие аппараты интенсивно изучаются и внедряются для анаэробной очистки сравнительно низкоконцентрированных стоков (< 750 мг/л), поскольку в этом случае не требуется интенсификации развития микробной популяции с помощью высоких доз «питания». Следует отметить, что необходимое время пребывания очищаемой жидкости в таких аппаратах нередко измеряется несколькими десятками часов.
Рассмотрим устройство, принцип работы, приемы нормированного расчета и выбора основных применяемых для анаэробных процессов сооружений – метантенков.
Различают метантенки открытого и закрытого типов (последние – с жестким или плавающим перекрытием). В сооружении с неподвижным жестким перекрытием уровень бродящей массы поддерживается выше основания горловины, так как в этом случае зеркало массы мало, велика интенсивность отвода газов и не образуется корка. Для ускорения процесса массу перемешивают и подогревают до 30–40 ° С (при мезофильном сбраживании) острым паром низкого давления (0,2–0,46 МПа). Пар подают через инжектор, рабочей жидкостью в котором является сама сбраживаемая масса. Основная циркуляция в метантенке осуществляется пропеллерной мешалкой.
Метантенки и газгольдеры для сбора выделяющихся газов (–65 % метана и –33 % диоксида углерода) – взрывоопасные сооружения, поэтому их располагают обычно на расстоянии не менее 40 м от других объектов.
Максимально возможная суточная доза загрузки в метантенк D/100 (в м /сут на 1 м сооружения) определяется тем обстоятельством, что увеличение этой дозы вызовет превышение выноса с выходящим потоком из сооружения активных бактериальных клеток над их ростом, и через определенное время в системе не останется достаточного количества действующих организмов. Типовые метантенки имеют полезный объем одного резервуара 1000–8000 м. Условно этот объем можно разделить на четыре выполняющие разные функции части: объем для образования плавающей корки, объем для иловой воды, объем для собственно сбра-
359
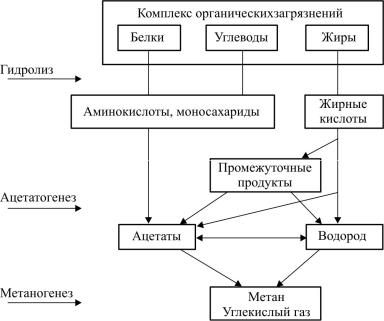
живания, объем для уплотнения и дополнительной стабилизации осадка при хранении (до 60 сут).
Для расчета выхода газа (около 8–15 м3 на 1 м3 осадка бытовых стоков) используют результаты опытного сбраживания основных компонентов перерабатываемых материалов. При сбраживании углеводов из 1 г распавшегося вещества выделяется 0,985 г газа, при переработке жиров и белков – 1,31 и 0,71 г газа соответственно.
15.2.1. Расчет метантенков
Продукты деструкции органики, получаемые в первой фазе, являются субстратом для микроорганизмов второй фазы. Состав промежуточных продуктов, образующихся при анаэробном сбраживании, зависит от состава исходных загрязнений. На рис. 15.4 приводится схема разложения основных органических примесей бытовых сточных вод: жиров, белков и углеводов. Наиболее сложен ход многоступенчатой деструкции белков. Жиры окисляются до менее устойчивого состояния жирных кислот.
Рис. 15.4. Схема анаэробного разложения органики (в конце первой фазы образуются водород и ацетаты, т.е. эфиры уксусной кислоты)
360