
- •Лекция 13 Меры безопасности при монтаже, пуско-наладке и
- •НПА по охране труда и мерам безопасности при эксплуатации холодильных установок
- •Особенности ОТ при эксплуатации холодильных установок
- •Продолжение
- •Продолжение
- •Продолжение
- •Продолжение
- •Особенности проведения контрольных проверок сосудов и приборов
- •Вмашинном отделении должны быть следующие документы
- •Продолжение
- •Продолжение
- •Продолжение
- •Принцип работы холодильной машины
- •Принципиальная схема работы холодильной машины
- •Назначение и особенности работы основных механизмов
- •Приборы контроля работы холодильных установок
- •Требования к средствам контроля
- •Отделение масла из хладоагента
- •Защита компрессоров от гидравлического удара
- •Средства автоматической защиты холодильных установок
- •Терморегулирующий вентиль (ТРВ)
- •Особенности применения ТРВ в схеме управления холодильной установки
- •Назначение и классификация холодильных установок
- •Требования ГОСТ 29266 «Хладоагенты органические (Хладоны)».
- •Основные свойства применяемых хладоагентов
- •Аммиак ка хладоагент как хладоагент для холодильных установок
- •Пожаровзрывоопасность аммиака
- •Фреон как хладоагент для холодильных установок
- •Продолжение
- •Первая помощь при отравлении хладоагентами
- •Особенности поставляемых АХУ
- •Особенности устройства отдельных видов компрессоров
- •Общий вид в разрезе поршневого компрессора
- •Аммиачная холодильная установка типа АКУ РО-0408-2хW6GF предприятия СООО «РефЮнитс» (г.Минск)
- •Принципиальная схема работы аммиачной установки
- •Фреоновая холодильная установка МКТ-22-2-1
- •Принципиальная схема холодильной установки МКТ-220-2-1
- •Принцип работы бытовых холодильных установок
- •Безнасосная промышленная компрессорная холодильная машина
- •Насосно-циркуляционная компрессорная холодильная машина
- •Промышленная насосно-циркуляционная холодильная машина
- •Компрессорное оборудование для охлаждения ледовых арен
- •Холодильное оборудование для систем кондиционирования зданий
- •Холодильное оборудование для заморозки грунтов в строительстве
- •Холодильное оборудование для хладокомбинатов
- •Основные причины аварий и взрывов на холодильном оборудовании
- •Требования промышленной безопасности при эксплуатации холодильных установок
- •Перечень документов для обслуживания холодильных установок
- •Требования к обслуживающему персоналу
- •Общий вид машинного отделения
- •Требования к помещениям холодильных установок
- •Продолжение
- •Требования к обеспечению микроклимату помещений
- •Продолжение
- •Требования к освещенности помещений машинных отделений
- •Требования для обеспечения безопасности объектов при использования холодильных установок с повышеным расходом аммиака
- •Требования к организации работы в машинных отделениях
- •Требования безопасности при обслуживании компрессоров и насосов
- •Организация безопасного ремонта холодильных установок
- •Продолжение
- •Продолжение
- •Определение утечек хладона из системы
- •Применяют спиртовые и пропановые галоидные ламп.
- •Применение электронных течеискателей
- •Течеискатель аммиака для холодильных установок
- •Требования безопасности по профилактики взрывов и пожаров
- •Требования к организации работы в машинных помещения при аварийной ситуации
- •Продолжение
- •Продолжение
- •Техническое освидетельствование холодильных установок
- •Продолжение
- •Инструкция по охране труда при эксплуатации камерных охлаждающих устройств фреоновых холодильных установок
- •Продолжение
- •Продолжение
- •Продолжение
- •Продолжение
- •Продолжение
Продолжение
•Ремонтный персонал следует обеспечить средствами индивидуальной защиты, в том числе промышленными противогазами с фильтрами, защищающими от воздействия паров аммиака (класс защиты не менее К2). Персонал должен знать порядок их применения, способы и приемы оказания первой помощи.
•Применяемые при ремонте детали и материалы должны соответствовать действующей технической документации и иметь документы, подтверждающие их качество.
•Для проведения технического обслуживания и ремонта оборудования, установленного в машинном, аппаратном или конденсаторном отделениях, в технологических цехах (в которых установлено оборудование аммиачной холодильной установки) необходимо пользоваться инструментом и приспособлениями, выполненными из материалов, исключающих искрообразование.
•После ремонта, а также после вынужденной остановки аммиачных насосов пуск их в работу может проводиться только с письменного разрешения ответственного специалиста аммиачной холодильной установки. После ремонтных работ необходимо проверить показания вновь установленных контрольно-измерительных и защитных приборов в соответствии с инструкциями организации-изготовителя.
•Оценка качества ремонта оборудования аммиачной холодильной установки, допуск ее в эксплуатацию должны проводиться с оформлением соответствующих актов.
•Пуск и обкатку компрессоров, насосов, вентиляторов после ремонта необходимо выполнять в соответствии с технической документацией их разработчиков и (или) изготовителей.
Определение утечек хладона из системы
•Наличие утечек хладона из системы трудно заметить вследствие отсутствия у него запаха и цвета. Утечки хладона могут иметь место из-за низкого качества изготовления оборудования, длительного срока его службы, а также вследствие вибраций.
•Хладоновые системы должны быть герметичными, потому что при утечках хладоны загрязняют атмосферу, уменьшается количество хладона в системе, в систему попадают воздух и влага (при давлении кипения ниже атмосферного), в загазованном помещении возможно удушье обслуживающего персонала, а при пользовании открытым пламенем — отравление (например, при сварке).
•Определение утечек хладона должно производиться машинистом каждую смену, а для автоматизированных установок — при каждом их техническом освидетельствовании и обслуживании.
Определяют утечки хладона разными способами: обмыливанием системы, галоидными лампами, обнаружением следов масла, электронными течеискателями.
Наиболее простым способом определения утечек хладона является обмыливание системы. Для этого приготавливается мыльная пена, в которую можно добавить несколько капель глицерина, препятствующего быстрому высыханию пены. Утечки в этом случае фиксируются по появлению пузырей.
Применяют спиртовые и пропановые галоидные ламп.
•Определение утечек хладона с помощью галоидных ламп основано на изменении цвета пламени при сгорании топлива (спирта или пропана) в присутствии F– и Cl– содержащих газов.
Для обнаружения утечек спиртовую галоидную лампу заправляют спиртом-ректификатом, затем наливают немного спирта в чашку и поджигают его. После прогрева лампы открывают клапан и регулируют высоту пламени в пределах 6—15 мм таким образом, чтобы пламя соприкасалось с медным колпачком или кольцом.
Свободный конец резинового шланга подносят к местам вероятной утечки хладона,
перемещая на расстоянии 1 —1,5 мм от поверхности. При отсутствии в воздухе, поступающем через шланг, пара хладона пламя имеет голубой цвет.
•Если в воздухе имеется пар хладона, как следствие его утечки из системы холодильной установки, то при температуре 600…700 °С происходит разложение хладона с образованием хлористого и фтористого водорода. Эти газы в присутствии раскаленной меди окрашивают пламя в цвет, зависящий от объемной концентрации хладона в воздухе, проходящего через шланг.
•Принцип действия пропановой галоидной лампы аналогичен спиртовой. Чувствительность пропановой лампы выше, а запас топлива — больше. Галоидная лампа должна обязательно входить в комплект инструмента механика хладоновых установок.
Появление на машинах, аппаратах и трубопроводах масляных подтеков свидетельствует о большой утечке хладона из системы, поскольку вязкость масла значительно выше вязкости хладона.
•Предполагаемые места утечки протирают ветошью, смоченной в растворителе (например, в бензине или ацетоне), и оборачивают чистой бумагой. Появление на бумаге масляных пятен свидетельствует о значительной утечке хладона.
•Места утечек помечают. Устранение утечек производится при понижении давления в системе до атмосферного.
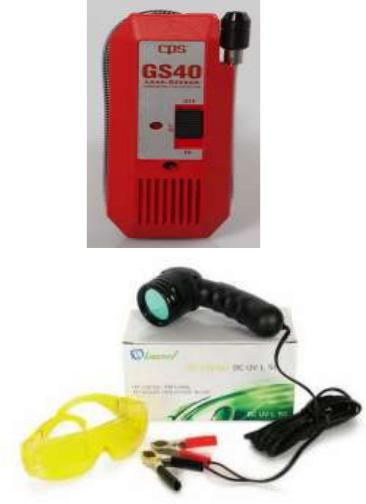
Применение электронных течеискателей
•Течеискатели – это приборы-индикаторы, функция которых – обнаружение течей различных газов
или же смеси газов, содержащих гелий, фреон, водород, пропан и другие вещества. Современный течеискатель фреона представляет собой высокотехнологичный микропроцессорный прибор, который позволяет своевременно детектировать наличие утечки наиболее распространенных видов фреонов. Его работа основывается на применении в качестве датчика, высокочувствительного первичного преобразователя полупроводникового типа.
Течеискатель
для взрывоопасных газов CPS GS40
Ультрафиолетовые течеискатели типа UV и и наборы для поиска утечек Becool позволят легко и просто найти любую утечку хладагента в холодильных системах.

Течеискатель аммиака для холодильных установок
•Взрывобезопасный течеискатель горючих газов и аммиака ТИГ-2 для обнаружения мест утечек горючих газов (метан, пропан, бутан, водород, ацетилен, пары бензина, пары спирта и др.) в трубопроводах
итехнологических емкостях, а так же аммиака в аммиачных холодильных установках.
–Порог чувствительности: не ниже 0,1 об.%;
–Время срабатывания световой и звуковой сигнализации: не более 3 сек
Требования безопасности по профилактики взрывов и пожаров
•Эксплуатация оборудования, сосуда (аппарата) или трубопровода должна быть запрещена в случаях:
•- повышения давления в оборудовании и в сосуде (аппарате, трубопроводе) выше разрешенного,
несмотря на соблюдение всех требований, указанных в инструкции;
•- неисправности предохранительных клапанов;
•- завершения срока проведения поверки предохранительных клапанов;
•- истечения срока проведения технического освидетельствования (ревизии) и (или) технического
диагностирования;
•- обнаружения в основных элементах сосуда (аппарата, трубопровода) трещин, выпучин, значительного
утончения стенок, пропусков или потения в сварных швах, течи в болтовых соединениях, разрыва прокладок;
•- возникновения пожара, непосредственно угрожающего оборудованию, сосуду (аппарату,
трубопроводу), работающему под давлением;
•- неисправности манометра (мановакуумметра);
•- истечения срока поверки установленного манометра (мановакуумметра);
•- неисправности или недостаточного количества крепежных деталей (крышек, фланцев, запорной
арматуры);
•- неисправности или недостаточного количества крепежных деталей опор оборудования, сосудов
(аппаратов, трубопроводов);
•- неисправности указателя реле уровня жидкости;
•- неисправности (отсутствия) предусмотренных проектом (паспортом оборудования) контрольно- измерительных приборов и автоматики;
•- утечки аммиака из оборудования, сосудов и трубопроводов аммиачной холодильной установки;
•- промерзания теплоизоляции сосуда (аппарата, трубопровода) более чем на 20 % от ее площади;
•- наличия более чем на 10 % площади поверхности трубопровода слоя льда (или промерзшей теплоизоляции) толщиной более наружного диаметра трубопровода.
Требования к организации работы в машинных помещения при аварийной ситуации
•Руководитель организации обязан наладить систему оповещения о возникновении аварий и инцидентов, обязан обеспечить работников, которые могут попасть в зону поражения аммиаком, средствами индивидуальной защиты.
•Помещения аммиачной холодильной установки, где возможны утечки аммиака, должны быть оснащены автоматическими газосигнализаторами и оборудованы предупреждающей световой и звуковой сигнализацией.
•Машинное, аппаратное и конденсаторное отделения, площадки ресиверов, где возможны утечки аммиака, должны быть оснащены по внешнему периметру системой осаждения паров аммиака, сохраняющей работоспособность при срабатывании системы противоаварийной автоматической защиты.
Система противоаварийное автоматической защиты – это система безопасности, которая включает следующие основные части: средства измерения, средства контроля выхода опасного параметра за допустимые пределы, средства выработки управляющего воздействия, исполнительные механизмы, средства сигнализации.
•Необходимо обеспечить непрерывный контроль содержания паров аммиака в воздухе,
предусматривающий световую и звуковую сигнализацию о достижении опасных концентраций, автоматическое включение устройств защиты и оповещения людей, находящихся в зоне потенциального поражения, как непосредственно на объектах, так и на прилегающих к ним территориях.
•АХУ, представляющие потенциальную опасность для прилегающих общественных, жилых и производственных зданий и имеющие в своем составе одну тонну аммиака и более, должны дополнительно оснащаться специализированной системой контроля обстановки и оповещения при авариях на объектах, использующих токсические вещества.
•Локализация и ликвидация аварий и инцидентов на аммиачной холодильной установке должна осуществляться по соответствующему плану. Работники АХУ, участвующие в локализации и ликвидации аварий и инцидентов, должны быть обеспечены средствами индивидуальной защиты и переносным индикатором-течеискателем аммиака,, предназначенным для контроля содержания паров аммиака в воздухе рабочей зоны и имеющим цифровую индикацию текущей концентрации аммиака. Он при этом должен быть во взрывоопасном исполнении. Руководить этими работами должно ответственное лицо из числа руководителей или специалистов АХУ.
Продолжение
•В организации, эксплуатирующей аммиачную холодильную установку, разрабатывается план локализации и ликвидации аварий, который является частью плана предупреждения и ликвидации чрезвычайных ситуаций.
•Не реже 1 раза в квартал со всеми работниками компрессорного цеха должны проводиться
тренировки(поочередно) по одной из позиций плана локализации и ликвидации аварий. Не реже одного раза в год должны проводиться учебные тревоги. Для этой цели в машинном отделении устанавливается сирена, звуковой сигнал которой должен отличаться от сигнала срабатывания приборов автоматики аммиачной холодильной установки. Эта же сирена должна быть включена для оповещения обслуживающего персонала о действительно происшедшем выбросе аммиака и необходимости срочно покинуть помещение и собраться в установленном месте для последующего проведения эвакуации оставшихся в помещении людей и ликвидации последствий аварии.
•Если произошел аварийный выброс аммиака (гидравлический удар, разрыв трубопровода, взрыв, вспышка, нарушение герметичности сосудов и т. п.), то в первую очередь необходимо подать сигнал об опасности, произвести аварийное отключение аммиачной холодильной установки и принять меры к эвакуации людей из опасной зоны, а затем действовать согласно плану локализации и ликвидации аварий. В этом плане должны быть учтены все виды и места возможных аварий в условиях эксплуатации, обслуживания, ремонта аммиачной холодильной установки, а также меры по максимально быстрой локализации и ликвидации аварий, действия работников в случае их возникновения. Вызов аварийно-спасательных подразделений должен предусматриваться при всех видах аварий с выбросом аммиака.
•К проведению работ по локализации и ликвидации аварий и инцидентов в загазованных зонах помещений, наружных установках аммиачной холодильной установки допускаются лица,
обученные для работы в дыхательных аппаратах со сжатым воздухом (в изолирующих противогазах) и не имеющие медицинских противопоказаний для работы в таких аппаратах.
Продолжение
•Использование водяных завес является основным способом ограничения распространения и обеззараживания аммиачно-воздушного облака, формирующегося в результате выброса (пролива) аммиака. Их использование должно проводиться согласно требований «Инструкции по расчету сил и средств для постановки водяных завес при ликвидации последствий чрезвычайных ситуаций, связанных с выбросом (проливом) аммиака», утвержденной приказом МЧС РБ от 7 июля 2008 г. № 89. Водяные завесы образуют динамическую преграду, препятствующую распространению аммиачно-воздушного облака, способствуют снижению концентрации аммиака. Эта преграда является полупроницаемой и оказывает двойственное действие. Во-первых, проходя сквозь нее, аммиак частично связывается за счет растворения в воде. Во-вторых, водяные завесы препятствуют распространению зараженного облака, создавая дополнительные конвективные потоки, способствуют его турбуляризации и рассеиванию.
•Аварийно-спасательные работы при ликвидации аварий, связанных с выбросом аммиака, происходят, как правило, в условиях формирования вторичного облака, определяемого размерами пролива, скоростью ветра и интенсивностью парообразования.
•Эффективность применения водяных завес зависит от ряда факторов, основными из которых являются правильный выбор их параметров и схема постановки. Выбор схемы постановки водяных завес осуществляется на основе данных о площади пролива (объеме газообразного выброса), скорости ветра и концентрации аммиака в приземном слое. Чтобы рассчитать количество сил и средств для постановки водяных завес при ликвидации последствий чрезвычайных ситуаций, связанных с выбросом (проливом) аммиака, необходимо выполнить:
•- определение площади пролива, объема газообразного выброса и скорости ветра;
•- определение направления ограничения распространения аммиачно-воздушного облака;
•- определение концентрации аммиака в приземном слое воздуха в заданных точках;
•- определение требуемого уровня снижения концентрации аммиака;
•- выбор схемы постановки водяных завес;
•- расчет количества эшелонов водяных завес с учетом значений коэффициента эффективности;
•- расчет количества рукавных распылителей;
•- определение количества необходимых технических средств.
Техническое освидетельствование холодильных установок
•Техническое освидетельствование проводится перед пуском в работу и в процессе эксплуатации 1 раз в 2 года и включает внутренний осмотр, периодический осмотр и пневматическое испытание на прочность и плотность.
•Досрочное техническое освидетельствование производится после реконструкции холодильной установки, ремонта, бездействия ее более 1 года или в случае перемещения.
Периодический осмотр производится в ходе технической эксплуатации.
Перед внутренним осмотром и пневматическим испытанием аппаратов производится их освобождение от хладагента и масла, промывка водой и дегазация, отделение от системы, установка заглушек. При внутреннем осмотре сосудов особое внимание должно обращаться на выявление трещин, надрывов, очагов коррозии, раковин, дефектов сварки.
Пневматическое испытание сосудов, аппаратов и систем производится автономным воздушным компрессором, который устанавливается на безопасном расстоянии от здания за прочным экраном. Там же размещают вентили подачи и выпуска воздуха, рабочий и контрольный манометры, предохранительный клапан, тарированный на давление, превышающее давление испытания на прочность на 0,1 МПа.
•Использование аммиачного компрессора для испытаний запрещено.
•Пневматическое испытания производятся при соблюдении следующих мер предосторожности:
•- на время испытания работа холодильной установки прекращается;
•- при испытании на прочность необходимо удаление людей из помещения в безопасные места;
•- место испытания должно быть огорожено;
•- присутствие людей, не связанных с выполнением работ в охраняемой зоне, не допускается;
•- двери и окна в помещении должны быть открыты, помещение надежно провентилировано;
•- запрещается на аппаратах, находящихся под давлением, подтягивать болтовые соединения, производить сварку и обстукивание;
•- добавление в систему аммиака запрещено во избежание создания взрывоопасной смеси.