
- •Лекция 13 Меры безопасности при монтаже, пуско-наладке и
- •НПА по охране труда и мерам безопасности при эксплуатации холодильных установок
- •Особенности ОТ при эксплуатации холодильных установок
- •Продолжение
- •Продолжение
- •Продолжение
- •Продолжение
- •Особенности проведения контрольных проверок сосудов и приборов
- •Вмашинном отделении должны быть следующие документы
- •Продолжение
- •Продолжение
- •Продолжение
- •Принцип работы холодильной машины
- •Принципиальная схема работы холодильной машины
- •Назначение и особенности работы основных механизмов
- •Приборы контроля работы холодильных установок
- •Требования к средствам контроля
- •Отделение масла из хладоагента
- •Защита компрессоров от гидравлического удара
- •Средства автоматической защиты холодильных установок
- •Терморегулирующий вентиль (ТРВ)
- •Особенности применения ТРВ в схеме управления холодильной установки
- •Назначение и классификация холодильных установок
- •Требования ГОСТ 29266 «Хладоагенты органические (Хладоны)».
- •Основные свойства применяемых хладоагентов
- •Аммиак ка хладоагент как хладоагент для холодильных установок
- •Пожаровзрывоопасность аммиака
- •Фреон как хладоагент для холодильных установок
- •Продолжение
- •Первая помощь при отравлении хладоагентами
- •Особенности поставляемых АХУ
- •Особенности устройства отдельных видов компрессоров
- •Общий вид в разрезе поршневого компрессора
- •Аммиачная холодильная установка типа АКУ РО-0408-2хW6GF предприятия СООО «РефЮнитс» (г.Минск)
- •Принципиальная схема работы аммиачной установки
- •Фреоновая холодильная установка МКТ-22-2-1
- •Принципиальная схема холодильной установки МКТ-220-2-1
- •Принцип работы бытовых холодильных установок
- •Безнасосная промышленная компрессорная холодильная машина
- •Насосно-циркуляционная компрессорная холодильная машина
- •Промышленная насосно-циркуляционная холодильная машина
- •Компрессорное оборудование для охлаждения ледовых арен
- •Холодильное оборудование для систем кондиционирования зданий
- •Холодильное оборудование для заморозки грунтов в строительстве
- •Холодильное оборудование для хладокомбинатов
- •Основные причины аварий и взрывов на холодильном оборудовании
- •Требования промышленной безопасности при эксплуатации холодильных установок
- •Перечень документов для обслуживания холодильных установок
- •Требования к обслуживающему персоналу
- •Общий вид машинного отделения
- •Требования к помещениям холодильных установок
- •Продолжение
- •Требования к обеспечению микроклимату помещений
- •Продолжение
- •Требования к освещенности помещений машинных отделений
- •Требования для обеспечения безопасности объектов при использования холодильных установок с повышеным расходом аммиака
- •Требования к организации работы в машинных отделениях
- •Требования безопасности при обслуживании компрессоров и насосов
- •Организация безопасного ремонта холодильных установок
- •Продолжение
- •Продолжение
- •Определение утечек хладона из системы
- •Применяют спиртовые и пропановые галоидные ламп.
- •Применение электронных течеискателей
- •Течеискатель аммиака для холодильных установок
- •Требования безопасности по профилактики взрывов и пожаров
- •Требования к организации работы в машинных помещения при аварийной ситуации
- •Продолжение
- •Продолжение
- •Техническое освидетельствование холодильных установок
- •Продолжение
- •Инструкция по охране труда при эксплуатации камерных охлаждающих устройств фреоновых холодильных установок
- •Продолжение
- •Продолжение
- •Продолжение
- •Продолжение
- •Продолжение
Продолжение
•Для вновь возводимых АХУ с количеством аммиака в АХУ более 500 кг датчики автомати- ческих газосигнализаторов аммиака должны быть встроены в контур теплоносителя (в промежуточных системах охлаждения) и оборотного водоснабжения. Такие датчики должны обеспечивать включение сигнальных ламп и сигналов тревоги в машинном отделении и (или) на мониторе системы управления, при этом, они не должны вызывать срабатывание сирен и не должны инициировать процедуру эвакуации людей.
•Машинное, аппаратное и конденсаторное отделения, площадки ресиверов, где возмож- ны утечки аммиака, должны быть оснащены по внешнему периметру системой осаждения паров аммиака, сохраняющей работоспособность при срабатывании системы ПАЗ. При этом необходимо обеспечить непрерывный контроль содержания паров аммиака в воздухе, преду- сматривающий световую и звуковую сигнализацию о достижении опасных концентраций, автоматическое включение устройств защиты и оповещения людей, находящихся в зоне потенциального поражения как непосредственно на объектах, так и на прилегающих к ним территориях.
•При достижении концентрации аммиака более 20 мг/куб. м система ПАЗ должна обеспечить
срабатывание сигнализации об опасной концентрации в помещении управления (операторной) АХУ и на входе в загазованное помещение, а также включение аварийной вентиляции.
•Холодильные камеры допускается не оборудовать аварийной вентиляцией в следующих случаях. При достижении концентрации аммиака в машинном (аппаратном, конденсаторном) отделении АХУ более 1500 мг/куб. м (0,21 %) система ПАЗ должна обеспечить отключение электропитания всей холодильной установки, включение аварийной вентиляции, включе-ние аварийного освещения, включение сигнализации в помещении управления (оператор-ной) АХУ и на входе в загазованное отделение АХУ, а также включение наружной сирены, обеспечивающей предупреждение об аварийной ситуации на всей территории субъекта промышленной безопасности.
•При достижении концентрации аммиака более 1500 мг/куб. м в остальных помещениях
АХУ система ПАЗ должна обеспечить отключение электропитания оборудования в загазо- ванном помещении, включение аварийной вентиляции, включение сигнализации в помещении управления (операторной) АХУ и на входе в загазованное помещение, а также включение наружной сирены, обеспечивающей предупреждение об аварийной ситуации на объекте.
Продолжение
•Для вновь строящихся (реконструируемых) АХУ в целях минимизации последствий выброса аммиака из трубопровода холодильных камер АХУ в случае аварийной ситуации в проекте должно быть предусмотрено оснащение жидкостных аммиачных трубопроводов, подающих аммиак в приборы охлаждения камер, быстродействующей запорной автоматической арматурой и системой аварийного отсоса паров из приборов охлаждения камер.
•Отсечение (отключение) аварийной холодильной камеры от питающих трубопроводов
должно осуществляться при достижении концентрации аммиака более 20 мг/куб. м. Работа быстродействующих отсечных устройств (клапанов) должна быть сблокирована с системой ПАЗ.
•АХУ, представляющие потенциальную опасность для прилегающих общественных, жилых и производственных зданий и имеющие в своем составе 1 и более тонн аммиака, должны дополнительно оснащаться специализированной системой контроля обстановки и оповещения при авариях на объектах, использующих токсические вещества (далее – ССК).
•Система ССК должна обеспечивать обнаружение аварийных утечек аммиака, постоянный контроль за уровнем загазованности контролируемых объектов, автоматическую регистрацию метеопараметров в зоне размещения объекта, автоматическую передачу информации о состоянии объекта в центр оперативного управления соответствующего городского (районного) отдела по чрезвычайным ситуациям МЧС РБ, прогноз распространения зоны химического заражения за территорию объекта, автоматическое формирование перечня мероприятий, которые должны быть выполнены силами аварийно-спасательных служб для ликвидации последствий аварии, в том числе и на прилегающих к аварийному объекту территориях.
•Система ССК должна в автоматическом режиме работы обеспечивать:
•- сбор информации о концентрации аммиака в месте установки датчиков автоматических газосигнализаторов аммиака, включение устройств сигнализации, защиты и оповещения;
•- контроль уровня загазованности территории АХУ;
•- измерение метеоданных в месте аварии;
•- прогнозирование формы, размеров, расположения и динамики распространения зоны поражения;
•- отображение зоны поражения на электронной карте-схеме местности;
•- формирование последовательности действий дежурного персонала объекта;
•- автоматическую передачу данных об аварии в городской (районный) центр оперативного управления МЧС РБ.

Принцип работы холодильной машины

Принципиальная схема работы холодильной машины

Назначение и особенности работы основных механизмов
Приборы контроля работы холодильных установок
•Большинство холодильных установок имеет не менее четыре манометров, которые могут быть отключены каждый отдельным ручным запорным вентилем. В целях повышения срока службы манометров их следует перекрывать ручными запорными вентилями. Для замера необходимо запорный вентиль открыть настолько, чтобы не дрожала стрелка.
•Манометр высокого давления показывает давление хладагента в ресивере. При нормальном режиме охлаждения показание манометра на 0,02 МПа из-за потери давления в конденсаторе ниже фактического значения давления нагнетания, которое контролируется реле максимального давления, подключенным к компрессору.
•Манометр давления всасывания показывает давление на стороне всасывания компрессора. С его помощью можно контролировать давление включения и выключения реле минимального давления.
•Манометр давления масла подключается к гидравлическому цилиндру автоматического запорного вентиля компрессора и показывает дифференциальное давление смазки, складывающееся из давления масла, создаваемого насосом, и давления всасывания компрессора. Фактическое значение давления масла определяется как разница давлений по показаниям манометра давления масла и манометра давления всасывания.
•Манометр промежуточного давления показывает давление после ступени низкого давления компрессора. Это давление должно быть выше давления всасывания, но ниже давления нагнетания. По показаниям манометра можно определить исправную работу цилиндра высокого давления компрессора.
•На воздухосборниках или газосборниках следует применять манометры диаметром не менее 150 мм, класса точности не ниже 2,5.
•Необходимо применять манометры с такой шкалой, чтобы при рабочем давлении стрелка их находилась в средней трети шкалы. На циферблате манометра должна быть нанесена красная черта по делению, соответствующему высшему допускаемому рабочему давлению.
•Манометры следует снабжать трехходовым краном. При давлении выше 25 кгс/см2 вместо трехходового крана разрешается установка отдельного штуцера с запорным устройством для подсоединения второго манометра.
Требования к средствам контроля
•Не допускаются к применению манометры в случаях, когда:
•а) отсутствует пломба или клеймо;
•б) просрочен срок проверки манометра;
•в) стрелка манометра при его выключении не возвращается к нулевому показанию шкалы на величину, превышающую половину допустимой погрешности для данного манометра;
•г) разбито стекло или имеются другие повреждения манометра, которые могут отразиться на правильности его показаний.
•Каждая точка замера температуры должна иметь отдельный термометр. Точки замеров определяются проектом.
•Предохранительные клапаны следует устанавливать после каждой ступени сжатия компрессора на участке охлажденного воздуха или газа. Если на каждый компрессор предусмотрен один воздухосборник и на нагнетательном трубопроводе отсутствует запорная арматура, предохранительный клапан после компрессора может устанавливаться только на воздухо- или газосборнике.
•Размеры и пропускная способность предохранительных клапанов выбираются так, чтобы не могло образоваться давление, превышающее рабочее более чем на 0,5 кгс/см2 при рабочем давлении до 3 кгс/см2 включительно, на 15% при рабочем давлении от 3 до 60 кгс/см2 и на 10% при рабочем давлении свыше 60 кгс/см2.
•Установка предохранительных клапанов должна отвечать требованиям нормативно-технических документов по промышленной безопасности.
•Регулировку предохранительных клапанов следует производить на специальных стендах лицами,
допущенными к самостоятельному обслуживанию компрессорных установок, с записью о проведенной регулировке в эксплуатационной документации.
•Натяжные гайки пружинных предохранительных клапанов пломбируются, а грузы рычажных предохранительных клапанов закрепляются, закрываются металлическими кожухами и пломбируются.
•На нагнетательном трубопроводе к воздухо- или газосборнику следует устанавливать обратный клапан.
•При расположении оборудования, требующего систематического обслуживания на высоте более 1,8 м,
следует предусматривать устройства (лестницы, подставки и т.д.) для удобства и безопасного его обслуживания.
Отделение масла из хладоагента
•Маслоотделитель холодильной установки. Качественный состав масла существенно влияет на надежность работы холодильной установки, как улучшая работу системы смазки механизма компрессора, так и ухудшая работу за счет покрытия испарителя пленкой и создания дополнительного термического сопротивления, что ведет к повышению температуры испарения и повышению нагрузки на компрессор. Для предотвращения негативных эффектов служат специальные устройства, устанавливаемые на линии нагнетания, после выхода хладагента из компрессора которые называются линейные ресиверы или маслоотделители.
•Требования к качеству масла для компрессоров достаточно жесткие, во-первых, оно не должно содержать ни каких кислот и щелочей, а также примесей и, безусловно, воды, а также не должно нарушать его химического состава и меньше влиять на его физические параметры. Тип и марка используемого масла выбирается в зависимости от параметров работы холодильной установки, так как температура кипения хладагента может быть и -80°C и масло должно выдерживать такие нагрузки. Некоторые фреоны, например R12, полностью растворяется в масле, образуя однородный раствор и нет необходимости разделения, но это влечет накопление масла в испарителе, особенно в затопленных иcпарителях, и его все равно необходимо возвращать, ведь скапливаясь там, его объем уменьшается в картере компрессора и вызывает ухудшение его смазки.
•Каждая поступающая партия компрессорного масла должна иметь паспорт-сертификат с указанием физико-химических свойств масла. Доставку масла в машинный зал следует производить в специальных сосудах для каждого вида масла (ведрах и бидонах с крышками и т.п.). Не допускается использование для других целей сосудов, предусмотренных для транспортирования и хранения компрессорного масла. Сосуды следует содержать в чистоте и периодически очищать от осадков.
•Отработанное масло может быть допущено к повторному использованию только после его регенерации и положительных результатов лабораторного анализа на соответствие его физико- химических свойств технической документации на масло.
•Отработанное масло следует сливать в емкость, находящуюся вне помещения компрессорной установки.
Защита компрессоров от гидравлического удара
•Самой большой угрозой при работе промышленных холодильных компрессоров является гидравлический удар, который происходит вследствие влажного хода компрессора, при котором в цилиндре накапливаются капли жидкости или масла, поступающие туда вместе с парами хладагента. Гидравлический удар приводит не только к поломке холодильного компрессора и остановке холодильной машины, но может вызвать и человеческие жертвы (особенно в аммиачных холодильных установках, которые являются объектами повышенной опасности).
•Для устранения угрозы влажного хода на линии всасывания перед компрессором устанавливается отделитель жидкости – резервуар, назначение которого состоит в улавливании, временном накоплении и выведении капель хладагента, которые вместе с паром выносятся из испарительной системы. Отделителя жидкости служит для защиты компрессоров, как при подключении установки и в процессе ее эксплуатации, так и после оттаивания испарителя.
•Принцип работы отделителя жидкости заключается в том, что с помощью гравитационных и центробежных сил относительно тяжелые капли жидкости (масла и хладагента), которые могут повредить холодильному компрессору, отделяются от нагретого пара хладагента и остаются в резервуаре, стекая по его стенке, а затем выводясь наружу по специальному трубопроводу. Само отделение происходит за счет резкого изменения скорости и направления потока перегретого пара, который сначала поступает в нисходящую трубу отделителя жидкости, потом в нижней ее части меняет направление и выходит из резервуара через восходящую трубу. Когда уровень отделенных жидкостей, скопившихся на дне резервуара, достигает нижней части нисходящей трубы, то через расположенное там маленькое отверстие выводится из сепаратора благодаря перепаду давлений. Для отделения масла также имеются специальные резервуары – маслоотделители и маслосборники.
•Цилиндрический сосуд отделителя жидкости может устанавливаться как вертикально, так и горизонтально. Иногда для увеличения скорости выпаривания жидкости в отделительный резервуар встраивается специальный теплообменник, но в таком случае велик шанс перегревания и разложения масла.
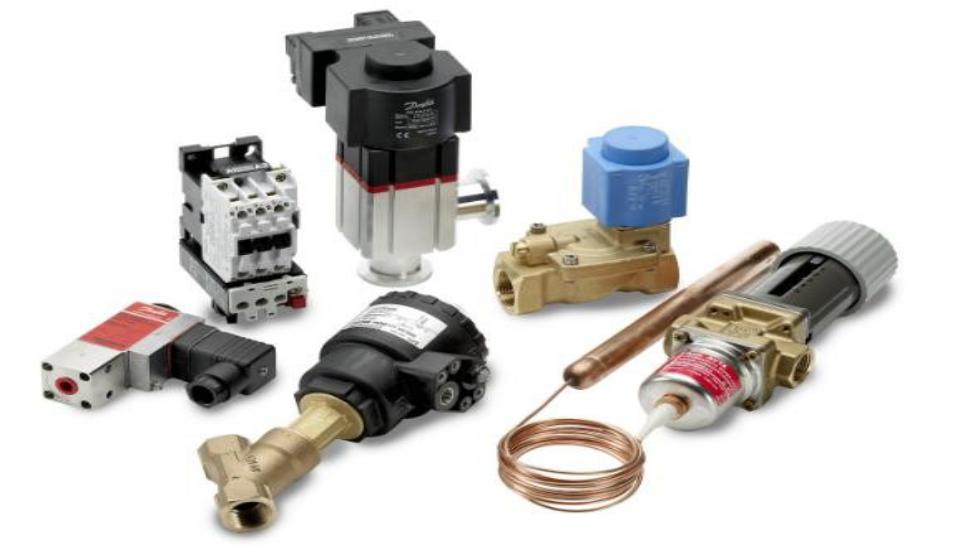
Средства автоматической защиты холодильных установок
Холодильные установки должны быть оснащены надежной системой противоаварийной защиты, обеспечивающей звуковую и световую сигнализацию при прекращении подачи охлаждающей воды, повышении температуры сжимаемого воздуха или газа выше допустимой и автоматическую остановку компрессора при понижении давления масла для смазки механизма движения ниже допустимой.