
- •Введение
- •Глава 1. Котельная установка морского судна
- •1.1 Потребители пара на судне
- •1.3 Назначение и классификация котлов
- •1.4 Требования к котлам
- •2.4 Основы теории топочных процессов
- •Глава 3. Топочные устройства котлов
- •3.1 Сжигание жидких топлив в топке котла
- •Глава 4. Тепловой баланс котла
- •4.1 Уравнения прямого и обратного теплового баланса
- •4.3. Уравнения теплового баланса утилизационного котла
- •Глава 5. Процессы теплообмена в котле
- •5.3 Конвективный теплообмен
- •5.5 Теплопередача в пароперегревателях
- •Глава 6. Гидродинамические характеристики котла
- •6.1 Аэродинамические и газодинамические характеристики
- •Глава 7. Конструкции котлов и их элементов
- •7.2 Главные водотрубные котлы
- •7.3 Вспомогательные водотрубные котлы
- •7.6 Утилизационные котлы
- •9.1 Причины изменения технического состояния элементов котла
- •9.2 Коррозия в судовых котлах
- •10.1 Задачи технической эксплуатации
- •Глава 11. Водные режимы котла
- •11.2 Обработка питательной воды
- •11.3 Обработка котловой воды
- •Список литературы
9. ТЕХНИЧЕСКОЕ СОСТОЯНИЕ И НАДЕЖНОСТЬ ЭЛЕМЕНТОВ КОТЕЛЬНОЙ УСТАНОВКИ
9.1. ПРИЧИНЫ ИЗМЕНЕНИЯ ТЕХНИЧЕСКОГО СОСТОЯНИЯ ЭЛЕМЕНТОВ КОТЛА
Под техническим состоянием объекта подразумевается состояние его свойств в данный момент времени, в процессе эксплуатации свойства объекта изменяются под воздействием различных факторов. Внешне это проявляется как отклонение параметров, характеризующих эти свойства, от установленных нормативно-технической документацией. Как отмечалось, изменение свойств объекта отображается в совокупности выходных его параметров, в том числе параметров материальных и энергетических выходных потоков (см. рис. 1.2), геометрических размеров и физических параметров (прочности, вязкости, твердости и т.п.) конструкционных материалов, часто называемых структурными. По изменению параметров материальных и энергетических потоков (на фиксированном режиме работы) можно судить только о том, изменилось ТС объекта или нет. На вопрос же о том, что явилось причиной изменения ТС, позволяет ответить только информация об изменении структурных параметров.
В связи с этим принято считать, что по отклонению технико-экономических показателей оценивается изменение качества функционирования технического объекта, а по отклонениям структурных параметров - изменение его технического состояния. Поэтому эффективная техническая эксплуатация любого технического объекта невозможна, если неизвестны основные причины и закономерности изменения структурных параметров под воздействием рабочих процессов и внешних воздействий.
Любой рабочий процесс в технических объектах, предназначенных для преобразования энергии, сопровождается сопутствующими процессами в той или иной степени вредными с точки зрения потребителя (отдельного человека или общества в целом). Объясняется это тем, что используемые энергоносители (топливо, вода, пар, воздух, дымовые газы и т.п.), содержащие различные примеси, не остаются нейтральными по отношению к материалам (металлам, огнеупорным и изоляционным материалам), из которых изготовлены технические объекты. Последнее особенно ярко проявляется в элементах судовых котлов, что было показано при рассмотрении теории рабочего процесса. Так, при сжигании топлива протекают сопутствующие процессы изнашивания распылителей форсунок, коксования элементов топочного устройства, разрушения кирпичной кладки топки. При анализе процессов теплопередачи в поверхностях нагрева отмечалось, что загрязнение труб отложениями золы и сажи является причиной не только ухудшения теплообмена (т.е. снижения тепловой эффективности), но и повреждений труб, обусловленных наружной коррозией, термической усталостью и разупрочнением металла вследствие перегрева при высоких температурах.
Процессы подогрева воды, парообразования и перегрева пара сопровождаются накипеобразованием, процессами химической и электрохимической коррозии и ухудшением температурного режима металла. При работе котла возможно появление циклических колебаний давления и температуры теплоносителя, обусловленное нарушениями устойчивости рабочих процессов из-за разрегулирования и нестабильности работы обслуживающих механизмов и устройств.
Таким образом, исходными причинами всех изменений структурных параметров (т.е. изменений геометрических характеристик) элементов котла и вспомогательного оборудования являются физико-химические процессы, сопутствующие рабочим процессам и протекающие на поверхностях деталей и внутри объема материалов, из которых детали изготовлены..
К таким процессам относятся различные виды коррозии, эрозия, истирание, усталостные разрушения и изменение прочностных характеристик металла под действием высоких температур. В реальных условиях эти процессы существуют всегда, но интенсивность их протекания определяется следующими факторами: загрязнением наружных и внутренних поверхностей элементов, конструктивными и технологическими недостатками, нарушениями правил технической эксплуатации.
Закономерности протекания процессов разрушения хорошо изучены теоретически. Влияние же трех групп отмеченных факторов на повреждаемость элементов котла может быть понято только
на основе анализа характерных эксплуатационных случаев аварий и отказов оборудования. Это означает, что каждый раз при отыскании причин тех или иных повреждений необходимо четко выделить доминирующий фактор и реконструировать условия протекания процессов разрушения. Именно с этих позиций и рассматриваются далее причины изменения технического состояния КУ, обусловленного повреждением их элементов.
9.2. КОРРОЗИЯ В СУДОВЫХ КОТЛАХ
Виды коррозии. В процессе работы элементы парового котла подвергаются воздействию агрессивных сред - воды, пара и дымовых газов. Различают коррозию химическую и электрохимическую.
Химическая коррозия, вызванная паром или водой, разрушает металл равномерно по всей поверхности. Скорость такой коррозии в современных судовых котлах низкая. Более опасна местная химическая коррозия, вызываемая агрессивными химическими соединениями, содержащимися в отложениях золы (серы, окислов ванадия и т.п.).
Наиболее распространенной и опасной является электрохимическая коррозия, протекающая в водных растворах электролитов при возникновении электрического тока, вызванного разностью потенциалов между отдельными участками металла, отличающимися химической неоднородностью, температурой или качеством обработки. Роль электролита выполняют вода (при внутренней коррозии) или сконденсировавшиеся пары воды в отложениях (при наружной коррозии). Возникновение таких микрогальванических пар на поверхности труб приводит к тому, что ион-атомы металла переходят в воду в виде положительно заряженных ионов, а поверхность трубы в этом месте приобретает отрицательный заряд. Если различие в потенциалах таких микрогальванических пар незначительно, то на границе металл -вода постепенно создается двойной электрический слой, который тормозит дальнейший ход процесса. Однако в большинстве случаев потенциалы отдельных участков различны, что обусловливает возникновение ЭДС, направленной от большего потенциала (анода) к меньшему (катоду). При этом с анода в воду переходят ион-атомы металла, а на катоде накапливаются избыточные электроны. В результате ЭДС и, следовательно, интенсивность процесса разрушения металла резко снижаются. Это явление называется поляризацией. Если потенциал анода уменьшается в результате образования защитной оксидной пленки или роста концентрации ионов металла в районе анода, а потенциал катода практически не изменяется, то поляризация носит название анодной.
При катодной поляризации в растворе у катода резко падает концентрация ионов и молекул, способных удалять избыточные электроны с поверхности металла. Из этого следует, что основным моментом борьбы с электрохимической коррозией является создание таких условий, когда будут поддерживаться оба вида поляризации. Практически достигнуть этого невозможно, так как в котловой воде всегда имеются деполяризаторы - вещества, вызывающие нарушение процессов поляризации.
К деполяризаторам относятся молекулы 02 и С02, ионы Н+, Сl- и SO4-, а также окислы железа и меди. Растворенные в воде СO2, Сl- и S04- тормозят образование на аноде плотной защитной оксидной пленки и тем самым способствуют интенсивному протеканию анодных процессов. Ионы водорода Н+ снижают отрицательный заряд катода.
Влияние кислорода на скорость коррозии стало проявляться в двух противоположных направлениях. С одной стороны, кислород увеличивает скорость коррозионного процесса, так как является сильным деполяризатором катодных участков, с другой - оказывает пассивирующее действие на поверхность. Обычно детали котла, изготовленные из стали, имеют достаточно прочную первоначальную оксидную пленку, которая защищает материал от воздействия кислорода до тех пор, пока не будет разрушена под действием химических или механических факторов.
Скорость гетерогенных реакций (к которым относится и коррозия) регулируется интенсивностью следующих процессов: подводом к поверхности материала реагентов (в первую очередь деполяризаторов); разрушением защитной оксидной пленки; удалением продуктов реакции от места ее протекания. Интенсивность же этих процессов во многом определяется гидродинамическими, механическими и тепловыми факторами. Поэтому меры по снижению концентрации агрессивных химических реагентов при высокой интенсивности двух других процессов, как показывает опыт
эксплуатации котлов, обычно малоэффективны. Отсюда следует, что решение проблемы предотвращения коррозионных повреждений должно быть комплексным, когда учитываются все факторы, влияющие на исходные причины разрушения материалов.
Электрохимическая коррозия. В зависимости от места протекания и участвующих в реакциях веществ различают следующие виды электрохимической коррозии: кислородную (и ее разновидность - стояночную), подшламовую (иногда называемую „ракушечной"), межкристаллитную (щелочная хрупкость котельных сталей), щелевую и сернистую.
Кислородная коррозия наблюдается в экономайзерах, арматуре, питательных и опускных трубах, пароводяных коллекторах и внутриколлекторных устройствах (щитах, трубах, пароохладителях и т.п.). Особенно сильно подвержены кислородной коррозии змеевики второго контура двухконтурных котлов, утилизационных котлов и паровых воздухоподогревателей. Кислородная коррозия протекает во время действия котлов и зависит от концентрации кислорода, растворенного в котловой воде.
Скорость кислородной коррозии в главных котлах низкая, что обусловлено эффективной работой деаэраторов и фосфатно-нитратным водным режимом. Во вспомогательных водотрубных котлах она нередко достигает 0,5 - 1 мм/год, хотя в среднем лежит в пределах 0,05 - 0,2 мм/год. Характер повреждения котельных сталей - язвы небольших размеров.
Более опасной разновидностью кислородной коррозии является стояночная коррозия, протекающая в период бездействия котла. В силу специфики работы все судовые котлы (а вспомогательные особенно) подвержены интенсивной стояночной коррозии. Как правило, стояночная коррозия не приводит к отказам котла, однако металл, подвергшийся коррозии во время остановок, при прочих равных условиях более интенсивно разрушается при работе котла.
Основной причиной возникновения стояночной коррозии является попадание кислорода в воду, если котел заполнен, или в пленку влаги на поверхности металла, если котел осушен. Большую роль при этом играют хлориды и NaOH, содержащиеся в воде, и водорастворимые отложения солей.
При наличии в воде хлоридов интенсифицируется равномерная коррозия металла, а если в ней содержится незначительное количество щелочей (меньше 100 мг/л), то коррозия локализуется. Чтобы избежать стояночной коррозии при температуре 20 - 25 °С в воде должно содержаться до
200 мг/л NaOH.
Внешние признаки коррозии с участием кислорода: локальные язвы l небольшого размера (рис. 9.1, а), заполненные продуктами коррозии бурого цвета, которые образуют бугорки над язвами.
Удаление кислорода из питательной воды является одним из важных мероприятий по снижению кислородной коррозии. С 1986 г. содержание кислорода в питательной воде для судовых вспомогательных и утилизационных котлов ограничивается 0,1 мг/л. Методы снижения кислорода в воде рассматриваются далее.
Однако и при таком кислородосодержании питательной воды в эксплуатации наблюдаются коррозионные повреждения элементов котла, что. свидетельствует о преобладающем влиянии процессов разрушения оксидной пленки и вымывании продуктов реакции из очагов коррозии. Наиболее наглядным примером, иллюстрирующим влияние этих процессов на коррозионные повреждения, являются разрушения змеевиков утилизационных котлов с принудительной циркуляцией.
Коррозионные повреждения при кислородной коррозии обычно строго локализованы: на внутренней поверхности входных участков (см. рис. 9.1, а), в районе гибов (рис. 9.1, б), на выходных участках и в колене змеевика (см. рис. 9.1, в), а также в пароводяных коллекторах утилизационных котлов (см. рис. 9.1, г). Именно на этих участках (2- область пристенной кавитации) гидродинамические особенности потока создают условия для разрушения оксидной пленки и интенсивного вымывания продуктов коррозии. Действительно, любые деформации потока воды и пароводяной смеси сопровождаются возникновением кавитации в пристенных слоях расширяющегося потока 2, где образующиеся и тут же схлопывающиеся пузырьки пара обусловливают разрушение оксидной пленки вследствие энергии гидравлических микроударов. Этому способствуют также знакопеременные напряжения в пленке, вызванные вибрацией змеевиков и колебаниями температуры и дав-
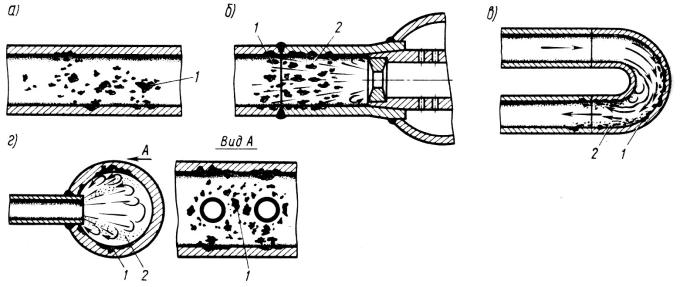
лений. Повышенная же локальная турбулизация потока на этих участках вызывает активное вымывание продуктов коррозии.
Рис. 9.1. Повреждения при кислородной коррозии.
На прямых выходных участках змеевиков оксидная пленка разрушается из-за ударов о поверхность капелек воды при турбулентных пульсациях потока пароводяной смеси, дисперснокольцевой режим движения которой переходит здесь в дисперсный (см. рис. 6.2) при скорости потока до 20 - 25 м/с. В этих условиях даже невысокое кислородосодержание (~ 0,1 мг/л) обусловливает интенсивное разрушение металла, что приводит к появлению свищей на входных участках змеевиков утилизационных котлов типа Ла Монт через 2-4 года эксплуатации, а на остальных участках - через 6 - 12 лет.
В качестве иллюстрации к изложенному рассмотрим причины повреждения змеевиков экономайзеров двух утилизационных котлов типа КУП1500Р (см. рис. 7.12, г), установленных на лихтеровозе ' Индира Ганди" (типа "Алексей Косыгин"), который вступил в эксплуатацию в октябре 1985 г. Уже в феврале 1987 г. из-за «повреждений заменены экономайзеры обоих котлов. Через 3 года и в этих экономайзерах появляются повреждения змеевиков, расположенные на участках до 1-1,5 м от входного коллектора. Характер повреждений свидетельствует (рис. 9.2, а, б) о типичной кислородной коррозии с последующим усталостным разрушением (поперечные трещины). Однако природа усталости на отдельных участках различна. Появление трещины (а ранее - растрескивание оксидной пленки) в районе сварного шва (см. рис. 9.2, а) является следствием знакопеременных напряжений, обусловленных вибрацией пучка труб и конструктивной особенностью узла соединения змеевиков с коллектором (к изогнутому штуцеру диаметром 22x3 приварен конец змеевика диаметром 22x2). Разрушение же оксидной пленки и образование усталостных трещин на внутренней поверхности прямых участков змеевиков, удаленных от входа на 700 - 1000 мм (см. рис. 9.2, б), обусловлены знакопеременными термическими напряжениями, возникающими в период ввода котла в действие, когда на горячую поверхность подается холодная вода. При этом действие термических напряжений усиливается тем, что оребрение змеевиков затрудняет свободное расширение металла трубы, создавая дополнительные напряжения в металле.
Подшламовая коррозия обычно наблюдается в главных водотрубных котлах на внутренних поверхностях экранных и парообразующих труб притопочных пучков, обращенных к факелу. Характер подшламовой коррозии - язвы овальной формы с размером по большой оси (параллельной оси трубы) до 30 - 100 мм. На язвах имеется плотный слой окислов в виде „ракушек" 3 (рис. 9.3). Подшламовая коррозия протекает в присутствии твердых деполяризаторов - окислов железа и меди 2, которые осаждаются на наиболее теплонапряженных участках труб в местах активных центров коррозии, возникающих при разрушении оксидных пленок. Сверху образуется рыхлый слой накипи и продуктов коррозии 1. Образующиеся „ракушки" из продуктов коррозии прочно сцеплены с основным металлом и могут быть удалены только механическим путем. Под „ракушками" ухудшается теплообмен, что приводит к перегреву металла и появлению выпучин. Для вспомогательных котлов этот вид коррозии не характерен, но при высоких тепловых нагрузках и соответ-
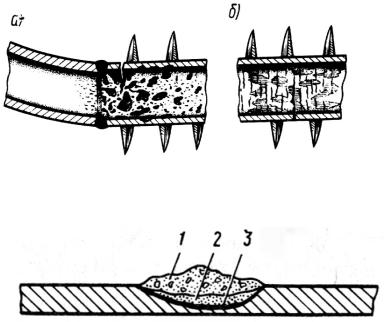
ствующих режимах водообработки не исключено появление подшламовой коррозии и в этих котлах.
Рис. 9.2. Коррозионные повреждения змеевиков экономайзеров утилизационных котлов КУП1500П теплохода “Индира Ганди”.
Рис. 9.3. Повреждения парообразующей трубы при подшламовой коррозии.
Щелочная хрупкость металла (межкристаллитная коррозия) появляется в котлах при повышенных концентрациях NaOH в котловой воде в местах высоких местных напряжений (вальцовочных и клепочных соединениях), в трещинах, раковинах и т.п., где при упариваний воды резко возрастает локальная концентрация щелочи, солей и других агрессивных соединений.
По своей природе щелочная хрупкость является частным случаем электрохимической коррозии, протекающей по границам зерен напряженного металла в щелочном концентрате котловой воды.
Щелочная хрупкость интенсифицируется также водородом, образующимся на катодах, который легко диффундирует в металл, создавая дополнительные напряжения по границам зерен и возникновения микротрещин (рис. 9.4).
Щелевая коррозия возникает в узких щелях, заполненных электролитом. Такие щели всегда имеются в арматуре котла и в вальцовочных соединениях, в которых вальцовка произведена не на полную толщину стенки трубной доски. В узких щелях обычно затруднены обмен воды и доступ кислорода, поэтому концентрация агрессивных примесей повышена, а кислород распределен по глубине неравномерно, что способствует возникновению замкнутого гальванического элемента и интенсивному протеканию коррозии. Скорость коррозии в значительной степени зависит от размеров щели. В настоящее время нет конструкционных материалов, стойких против щелевой коррозии.
Примером разрушения от электрохимической коррозии может служить также сернистая коррозия труб поверхностей нагрева котла. При температуре дымовых газов ниже точки росы на трубах хвостовых поверхностей нагрева котлов происходит конденсация паров воды, содержащихся в дымовых газах. В образовавшихся капельках воды растворяются содержащиеся в газах окислы серы и образуются слабые растворы кислот, выполняющие роль электролита. Сернистая коррозия может протекать только при температурах ниже точки росы, поэтому при полной нагрузке котла она не опасна. При работе на малых нагрузках и в бездействующем котле имеются благоприятные условия для интенсивного коррозионного разрушения труб. На практике сернистой коррозии (коррозионные язвины 3) подвержены также корневые участки труб пароперегревателей и экранных труб (рис. 9.5). Появление воды в районе корней труб связано не только с конденсацией паров из газов в период бездействия, но и с обмывом наружных поверхностей труб при чистках. Так как на коллекторе 2 всегда имеются отложения золы 4 (из-за трудности доступа к ним и невозможности полной очистки), то при обмыве труб 1 вода попадает на них, растворяет соединения серы,
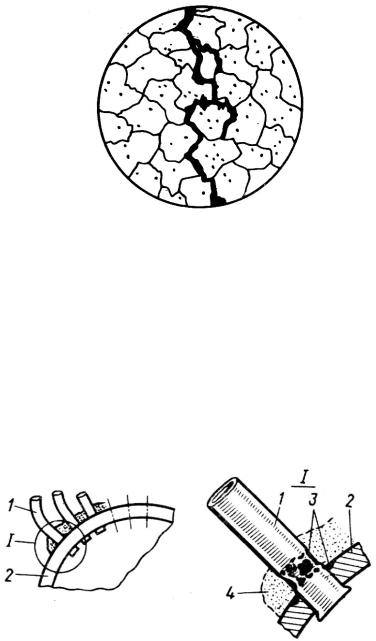
проникает под слой отложений и создает условия для протекания сернистой коррозии. Методами борьбы с коррозией являются своевременная очистка котлов, применение различных присадок к топливу и сжигание его с малыми избытками воздуха.
Рис. 9. 4. Схема развития межкристаллической коррозии (щелочной хрупкости).
Химическая коррозия. При температуре пара выше 500 °С возможна пароводяная коррозия с образованием оксидной пленки и выделением водорода. Наличие оксидной пленки снижает скорость коррозии незначительно, так как диффузия атомов кислорода и металла через пленку продолжается. Интенсивность пароводяной коррозии может быть снижена путем легирования металла хромом, кремнием и алюминием. Применяемые в судовом котлостроении легированные стали отличаются высокой стойкостью против пароводяной коррозии; повреждений труб, вызванных ею, на практике не наблюдается.
Газовая коррозия, представляющая собой процесс окисления стали топочными газами, более опасна. При этом также образуется оксидная пленка, препятствующая дальнейшему развитию коррозии, интенсивность которой зависит от скорости диффузии атомов кислорода через слой окислов и качества самой пленки.
Рис. 9.5. Повреждения труб при наружной коррозии под слоем отложения золы и сажи.
В практике эксплуатации судовых котлов процесс газовой коррозии интенсифицируется присутствием в дымовых газах окислов серы, ванадия и др., а также наличием наружных отложений золы. В этом случае коррозия труб, например пароперегревателей, представляет собой сложный физико-химический процесс взаимодействия дымовых газов и наружных отложений золы с оксидными пленками и металлом труб.
Для высокотемпературных поверхностей нагрева опасна ванадиевая коррозия, которая может протекать только при наличии отложений золы, содержащей соединения ванадия, натрия, калия и др.
Наиболее распространена теория, согласно которой интенсивное окисление металла при температуре стенок труб выше 600 °С обусловлено растворением защитной окисной пленки соединениями ванадия, а при более низкой температуре стенки - сульфатами и кислыми сульфатами щелочных металлов. Считается, что обязательным условием начала коррозии является размягчение (до полурасплавленного состояния) наружных отложений золы. Пятиокись ванадия V205 играет роль катализатора - переносчика кислорода. При этом она отдает оголенному металлу трубы ки-
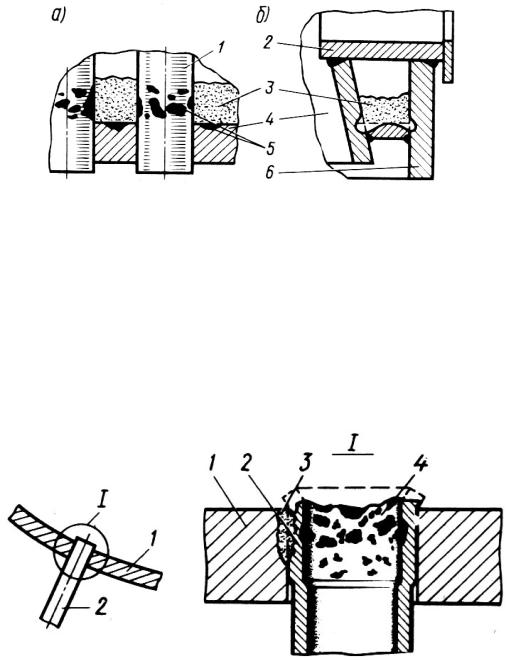
слород, восстанавливаясь до V204 но в этом состоянии весьма неустойчива и быстро окисляется до Уз05 кислородом, содержащимся в дымовых газах.
Для современных судовых котлов скорость высокотемпературной коррозии оценивается в 0,1 - 0,3 мм/год.
Смешанные виды коррозии. На практике обычно в разрушении металла принимают участие несколько процессов химической и электрохимической коррозии, которые могут протекать как последовательно, так и параллельно. Наиболее благоприятные условия для этого создаются на поверхностях элементов под слоем накипи и шлама, например на горизонтальных поверхностях трубных досок, огневой и топочных камер, жаровых труб огнетрубного котла, в водяном коллекторе водотрубного котла и т.п. Здесь идет химическое разрушение оксидных пленок под действием щелочи или пароводяной коррозии при упаривании воды под слоем, а в период бездействия котла наблюдается электрохимическая коррозия с участием деполяризаторов О2, С1-, SO4. Особенно опасна эта коррозия в том случае, когда затруднено удаление слоя шлама 3 при продувании котла. Так, часто коррозионные язвы 5 появляются на дымогарных трубах 1 вертикального огнетрубного котла в районе нижних трубных досок (рис. 9.6, а), а также на днищевых кольцах и металле топочных камер 4 (рис. 9.6, б) огнетрубных и огнетрубно-водотрубных котлов (2 - форсуночный патрубок; 6 -корпус котла).
Рис. 9.6. Повреждение элементов вертикальных огнетрубного и огнетрубно-водотрубного котлов под слоем отложений шлама со стороны воды.
В некоторых случаях одновременно протекают процессы коррозии и кавитационной эрозии . Этому виду разрушений подвержены в первую очередь колокольчики вальцовочных соединений опускных и подъемных труб водотрубного котла. При этом доминирующим процессом обычно является эрозия. Механизм возникновения кавитации на входе в опускные трубы описан ранее (см. разд. 6). В подъемных трубах (парообразующих) кавитация возникает на выходе пароводяной смеси в барабан. Сущность этого процесса заключается в том, что некоторое количество пузырьков пара при выходе струи пароводяной смеси в недогретую до кипения воду охлопывается, обусловливая гидравлические микроудары. При этом первыми начинают схлопываться пузырьки пара, расположенные на периферии струи, откуда начинается ее охлаждение при входе в недогретую до кипения воду. Именно поэтому интенсивному разрушению подвергаются кромки колокольчиков с внутренней стороны (рис. 9.7).
Рис. 9.7. Повреждение вальцовочных колокольчиков труб водотрубного котла.
Под действием коррозии повреждение 4 распространяется внутрь трубы 2. Эти разрушения при одновременном возможном протекании щелевой коррозии (повреждения 3) могут вызвать опасные повреждения труб и упуск воды (1 - пароводяной барабан). Интенсивность эрозионнокоррозионного процесса зависит от качества котловой воды и режимных факторов. При появлении признаков этого повреждения обслуживающий персонал должен обратить внимание именно на эти факторы.
Коррозия может явиться причиной опасных повреждений пароводяного барабана и бочки котла с наружной стороны под слоем изоляции в местах установки котельной арматуры. Это типичная электрохимическая коррозия в пленке воды, попадающей под изоляцию при неисправностях арматуры. В качестве деполяризаторов здесь обычно выступают ионы хлора и водорода. Например, в котлах типа VX, установленных на учебно-производственных судах, при вскрытии изоляции после 12 лет эксплуатации в нижней части бочки обнаружено в нескольких местах утонения стенок на 20 - 40 % от первоначальной толщины общей площадью язв более 500 мм2.
9.3. РАЗРУШЕНИЯ КИРПИЧНОЙ КЛАДКИ И МЕТАЛЛА ЭЛЕМЕНТОВ КОТЛА
Разрушения кладки. Возможны следующие виды разрушения кирпичной кладки: шлакоразъедание (60 % случаев разрушения), растрескивание под действием температурных напряжений (33 %), расплавление, деформации, откалывание и местное выгорание (7 %).
Под шлакоразъеданием понимают процесс разрушения кладки от одновременно действующих и взаимосвязанных процессов коррозии и эрозии. Скорость развития этого процесса зависит от химического состава золы топлива и огнеупоров, вязкости шлака, структуры огнеупоров и температуры, при которой происходит процесс. Так как в золе топочных мазутов содержится много Na, V, Ca, Mg, температура плавления шлаков, образовавшихся на поверхности кирпичной кладки, значительно ниже температуры плавления огнеупоров, поэтому шлаки частично проникают в поры кирпича, а большая их часть сползает вниз, увлекая за собой поверхностные слои кирпичной кладки.
Исключительно велика роль температуры в ускорении шлакоразъедания кирпичной кладки. Например, увеличение температуры кладки на 1 "С свыше принятой при расчете ускоряет процесс шлакоразъедания более чем на 1 %. Иными словами, повышение температуры в топке на 50 - 60 "С сверх расчетной в течение 1 - 2 ч приводит к такому же износу, как и работа при расчетных температурах в течение 2 - 3 мес.
Откалывание шлака вместе с поверхностным слоем огнеупора происходит вследствие значительных напряжений, обусловленных различием коэффициентов линейного расширения огнеупора и покрывающего его шлака. Резкие теплосмены интенсифицируют этот процесс.
Нередко кладка судовых котлов разрушается вследствие выгорания швов, когда раствор, на котором кладутся кирпичи, оказывается менее стойким, чем материал огнеупоров. Шлакоразъедание начинается со швов. В образующиеся пазы попадают агрессивные компоненты золы топлива и ускоряют этот процесс.
В практике эксплуатации наблюдается иногда так называемая поверхностная рыхлость кирпичной кладки. Сущность ее в том, что вследствие взаимодействия щелочных соединений с основными компонентами огнеупора образуются алюмосиликатные щелочи, эвтектики которых плавятся при низких температурах. При этом возникают поверхностные трещины, которые способствуют быстрому шлакоразъеданию кладки.
Опасным видом разрушения кладки является ее растрескивание под действием периодических теплосмен. В верхнем слое кирпичной кладки при резких охлаждениях возникают растягивающие термические напряжения, нередко превышающие предел текучести. Они-то и являются причиной возникновения трещин, так как на сжатие огнеупоры работают в несколько раз лучше. Появление трещин интенсифицирует процесс шлакоразъедания.
Разрушения металла, обусловленные усталостью и перегревом. Как отмечалось (см. гл. 8), при высоких температурах в металле интенсифицируются процессы ползучести и изменения структуры (обезуглероживание, графитизация и т.п.), которые могут явиться причиной разрушения элементов котла. В таких случаях обычно говорят о перегреве (или пережоге) металла. Причинами
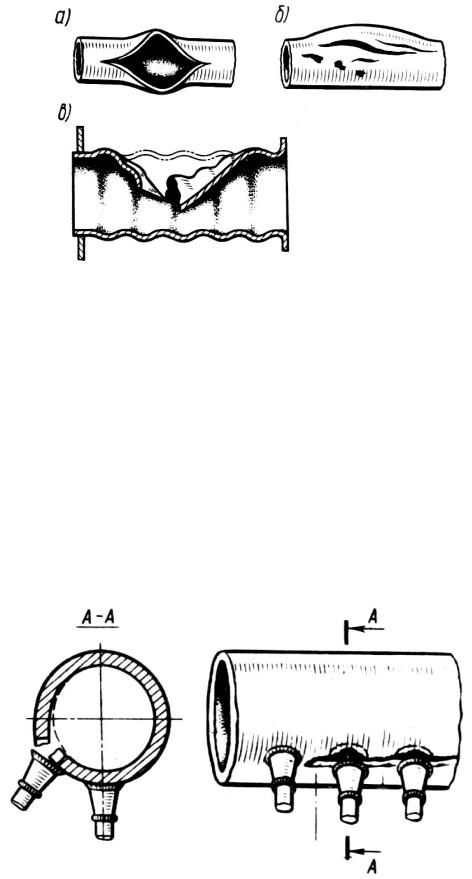
недопустимых повышений температуры металла являются наличие отложений накипи или масла, неравномерность наружного загрязнения отложениями золы и сажи, нарушения циркуляции в котле и упуски воды, обусловленные конструктивными недостатками и нарушениями инструкций по эксплуатации.
Рис. 9.8. Повреждения труб вследствие перегрева углеродистых и слаболегированных сталей при повышении температуры металла кратковременном до 700 0С (а), длительном до 600 – 620 0С (б), жаровой трубы под слоем отложений шлама с водяной стороны (в).
Характер повреждения труб при перегреве металла (рис. 9.8): общее увеличение диаметра труб, местное увеличение диаметров труб и изменение формы плоских поверхностей (выпучины), провисание (или прогиб) труб, сужение или проседание жаровых труб огнетрубного котла, разрывы и продольные трещины при незначительном утонении стенки в местах повреждений.
В качестве примеров повреждений от перегрева металла можно привести многочисленные выходы из строя петель пароперегревателей котлов КВГ25, разрушение опорной балки пароперегревателя на танкере «Прага», увеличение диаметра в области трубной доски коллектора пароперегревателя (выпучина по всей длине коллектора) танкера «Гдыня» из-за попадания масла в котел, проседания и разрывы жаровых труб огнетрубных котлов на танкерах типа «.Алтай» и др.
Исключительно показательным примером подобных повреждений (рис. 9.9) является образование трещины в трубной доске выходного коллектора первой секции основного пароперегревателя главного котла КВГ80/80 танкера «.Кузбасс» (ноябрь 1980 г.). Коллектор изготовлен из легированной стали. Причиной нарушения температурного режима металла коллектора явилась форсированная растопка котла. Явными признаками форсированного перегрева металла можно считать локальное увеличение диаметра коллектора и образование продольной трещины без утонения его стенки.
Рис. 9.9. Разрыв коллектора пароперегревателя котла КВГ80/80 при перегреве металла.
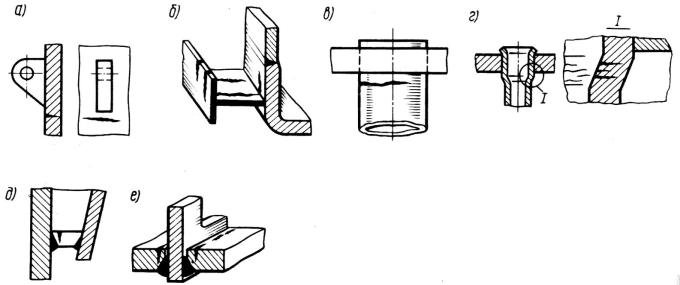
Однако повреждения из-за „чистого" перегрева металла встречаются не столь часто. Большее число повреждений элементов котлов при повышенных температурах обусловлено термоусталостными и усталостными разрушениями в виде трещин. Наиболее ярко эти причины повреждений проявляются в вертикальных огнетрубных и огнетрубно-водотрубных котлах, обладающих чрезмерной жесткостью конструкции. Жесткость конструкции заключается в том, что температурные расширения внутренних элементов (топочных камер, дымогарных и парообразующих труб, связей) сильно затруднены вследствие прочных неподатливых соединений этих элементов с корпусами (бочками) котлов. Действительно, в моменты изменения режима (растопка, остановка, сброс и наброс нагрузки) температурные удлинения внутренних элементов намного больше, чем удлинение более холодного корпуса. Это вызывает знакопеременные деформации трубных досок, днищ, огневых и форсуночных патрубков, что приводит в конечном счете к усталостным повреждениям металла в местах наибольшей концентрации напряжений в угловых сварных соединениях, в районе поперечных сварных швов и креплений (рис. 9.10).
В местах скопления шлама (у днищевого кольца или нижнего днища) усталостные явления сопровождаются коррозионными процессами, что увеличивает скорость разрушения металла (иногда такие повреждения называют коррозионной усталостью).
Особенно подвержены коррозионной усталости узлы крепления полностью охлаждаемой топочной камеры (см. рис. 7.8 и 9.10) к днищу огнетрубного котла типа UNEX СН финской постройки.
Рис. 9.10. Усталостные повреждения элементов котлов.
а – корпуса огнетрубного котла в районе ушек крепления; б – таврового кольца для крепления изоляционных щитов в районе газохода котла типа VX; в - опускной трубы котла типа AQ-3; г – вальцовочного колокольчика водотрубного котла; д – днищевого кольца водотрубного котла; е – днища котла типа UNEX CH в районе книц.
Кницы, поддерживающие топочную камеру, по технологии сборки обваривают угловым швом только снаружи. Поскольку толщина днища достигает 20 мм и более, почти всегда существует непровар швов и, следовательно, щели между кницей и днищем, в которых протекает интенсивная коррозия. Поэтому .усталостные трещины начинают развиваться с внутренней стороны днища, и контроль за их развитием практически невозможен. В результате усталостные разрушения появляются уже через 5 - 10 тыс. ч работы котла (например, в котлах судов „Самотлор", „Юлиус Фучик" и взрыв котла на теплоходе „Каменск-Уральский").
Вторым столь же жестким узлом котла является сварное соединение форсуночного патрубка 2 (рис. 9.11) с топочной камерой 1. Технологический дефект сварного шва (ненровар) в таком со-
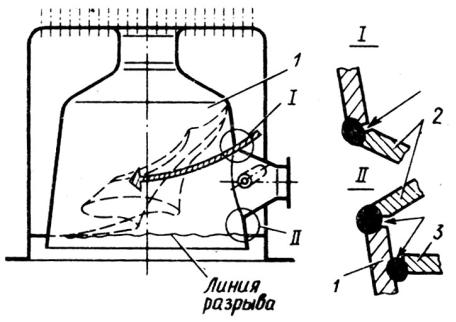
единении и развитие коррозионной усталости привели к взрыву котла VX125 на плавбазе „Северный полюс" 15 мая 1984 г. (3 - днищевое кольцо).
Рис. 9.11. Схема разрушения топочной камеры котла типа VX125 теплохода “Северный полюс”.
(стрелками указаны места непроваров)
Термоусталостное растрескивание очень часто наблюдается в местах соединения форсуночных патрубков и смотровых труб (рис. 9.Г2) с топочными камерами огнетрубных и огнетрубноводотрубных котлов. Характерным недостатком этих узлов является наличие выступающего свободного конца патрубка, металл которого подвергается циклическому нагреву до 600 - 700 °С и охлаждению до 150 - 200 °С (при работе котла в режиме включено -выключено). В результате термоциклирования и структурных превращений в металле при высоких температурах на торцах патрубка появляются усталостные продольные трещины.
Повреждения из-за конструктивных и технологических недостатков и нарушений правил технической эксплуатации котлов. Особенно отчетливо конструктивные недостатки проявились в повреждениях утилизационных котлов с принудительной циркуляцией прямоугольной компоновки с оребренными змеевиками типа AKSR на судах типов „Художник Сарьян", „Астрахань" и др. Наиболее существенными конструктивными недостатками этих котлов являются:
-отсутствие перегородки в пароводяном коллекторе, приводящее при работе одной секции к забросу пароводяной смеси в змеевики отключенной секции; вследствие упаривания воды здесь образуются накипные пробки (рис. 9.13), удалить которые практически невозможно;
-подвод газов к приемной камере котла снизу (а не сбоку), что препятствует очистке наружной поверхности змеевиков;
-отсутствие средств химической очистки котла с газовой стороны, а также технических средств контроля температуры дымовых газов за котлом.
Два последних недостатка котла при наличии оребрения змеевиков обусловливают сильное и быстрое загрязнение отложениями золы и продуктами неполного сгорания топлива (сажей, частицами кокса и каплями масла), возгорание которых может явиться причиной пожара (как это произошло в 1986 г. с утилизационным котлом теплохода „Улан-Батор").
Вероятность возгорания отложений в УК на этих судах значительно выше из-за того, что фир- мой-изготовителем главного двигателя K5SZ70/125BL установлен повышенный удельный расход цилиндрового масла (1,4-1,5 г/кВт-ч), а инструкция по эксплуатации утилизационного котла рекомендует останавливать циркуляционный насос сразу же после вывода УК из действия. Отмеченные конструктивные недостатки У К при отсутствии охлаждения змеевиков во время работы главного двигателя на малых нагрузках и на маневрах и наличии в отложениях продуктов неполного сгорания топлива и масла и являлись причиной многочисленных возгораний сажи в УК на судах серии „Астрахань" (в том числе пожара на теплоходе „Улан-Батор").
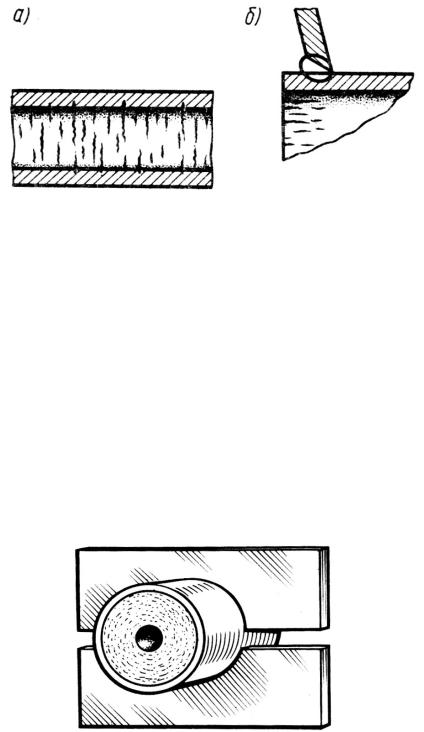
Рис. 9.12. Термоусталостное растрескивание парообразующей трубы (а), водотрубного котла и форсуночного патрубка (б) огнетрубного котла.
Интересно отметить, что вспомогательные котлы типа ESH, которыми оборудованы суда этой серии, также имеют существенные конструктивные недостатки, обусловливающие низкую надежность процессов циркуляции в экранных контурах, что послужило причиной многочисленных повреждений экранных труб (особенно заднего экрана).
Грубые нарушения правил технической эксплуатации котельных установок также могут послужить непосредственными причинами повреждений элементов судовых котлов, что убедительно подтверждается опытом их эксплуатации: более 75 % аварий обусловлены именно нарушениями инструкций по обслуживанию; более того, 95 % упусков воды, приводящих к серьезным авариям котлов, происходят по вине обслуживающего персонала, нарушающего (по незнанию или умышленно) правила технической эксплуатации котлов.
Наиболее показательным в этом отношении можно считать взрыв утилизационного котла на танкере „Алиот" в 1973 г. из-за неисправности предохранительного клапана. При расследовании аварии выяснилось, что механики „не знали" о существовании предохранительного клапана, который с момента постройки ни разу не проверялся, в результате чего тарелка была прочно заклинена в гнезде слоем накипи и ржавчины. В то же время механики, которым доверено ежегодное освидетельствование утилизационного котла, предъявляли инспектору Регистра ложный акт освидетельствования, в котором указывалось, что предохранительный клапан проверен подрывом и отрегулирован,
Рис. 9.13. Отложение накипи на выходных участках парообразующих змеевиков утилизационного котла типа AKSR.
9.4. ПРИЧИНЫ ИЗМЕНЕНИЯ ТЕХНИЧЕСКОГО СОСТОЯНИЯ ВСПОМОГАТЕЛЬНОГО ОБОРУДОВАНИЯ КОТЕЛЬНОЙ УСТАНОВКИ
Вспомогательные механизмы. К вспомогательным механизмам СКУ относятся насосы питательные, циркуляционные, подпитки теплого ящика и ( топливные. Сюда же следует отнести котельные вентиляторы.
Основными повреждениями котельных вентиляторов являются износы подшипников, трещины и обрывы рабочих лопаток и отказы электропривода. Выход из строя подшипников качения обусловлен выработкой рабочих дорожек и увеличением люфта, что приводит к смятию и растрескиванию шариков -и поломке сепараторов. Основными причинами этих повреждений обычно явля-
ются вибрация, обусловленная разбалансировкой рабочего j колеса, и отсутствие периодического j контроля за наличием смазки и чистотой рабочих поверхностей подшипников. При этом разбалансировки рабочего колеса могут быть обусловлены низким качеством ремонтно-профилактических работ или неравномерным загрязнением лопаток в процессе эксплуатации.
Трещины и обрыв рабочих лопаток обычно наблюдаются в местах их крепления к ступице, где изгибающие напряжения имеют максимальное значение. Причинами этих повреждений являются либо дефекты лопаток, появившиеся при изготовлении, либо их задевание за детали корпуса при выработке подшипников и усилении вибрации. Последняя причина в эксплуатации встречается более часто, что свидетельствует о недостаточном контроле за работой вентиляторов со стороны обслуживающего персонала.
Относительно более низкая надежность питательных и циркуляционных насосов (центробежных, вихревых и центробежно-вихревых) объясняется тем, что они работают в условиях высоких температур и механических нагрузок при одновременном воздействии агрессивной среды - питательной воды. Основными повреждениями насосов являются износы валов, подшипников и сальниковых уплотнений, коррозионно-эрозионные разрушения корпусов и рабочих колес. Высокая температура рабочей среды (особенно в циркуляционных насосах утилизационных котлов) и наличие в ней химически активных веществ приводят к затвердеванию и потере эластичности сальниковых набивок, в результате чего усиливается трение между набивкой и защитной втулкой вала.
Основной причиной быстрого износа подшипников является вибрация, обусловленная как особенностями гидродинамики потока в рабочей части насоса, так и разбалансировкой рабочих колес вследствие неравномерного изнашивания их рабочих лопаток. Характерными признаками износа подшипников являются выработка обойм, выкрашивание шариков, разрушение сепарации.
Причинами износа лопаток рабочих колес являются кавитационные разрушения участков входных кромок и тыльной поверхности лопаток (поверхностный наклеп с последующим усталостным выкрашиванием) и эрозия.
Повреждения подшипников и загрязненность циркуляционной или питательной воды обусловливают интенсивное изнашивание уплотнительных колец, ступицы рабочего колеса и его лопаток (крылаток в вихревых насосах).
В качестве питательных и подпитывающих насосов применяют иногда поршневые насосы (в основном на судах зарубежной постройки). Наиболее часто повреждения появляются в парах трения: сальник - шток и цилиндр -поршень. Реже встречаются отказы клапанной коробки из-за потери плотности затвора, повреждения редукторов, подшипников и привода насоса.
Шестеренные насосы широко применяют в топливных системах СКУ благодаря таким свойствам, как малая неравномерность подачи, относительно небольшие масса и размеры, а также возможность создания больших давлений. К основным повреждениям насосов относятся эрозионный и абразивный износ рабочих колес, задиры и питтинг на поверхности зубьев, заклинивание перепускного клапана. Причинами повреждений являются высокие механические нагрузки и наличие механических примесей, воды и химически активных веществ в топливе. Так, попадание воды на поверхность зубьев обусловливает периодическое возникновение „сухого" трения, что приводит к появлению задиров и питтинга. При этом в большей степени изнашиваются зубья ведущих шестерен, подверженных, кроме скручивающих, еще и изгибающим нагрузкам из-за износа элементов привода. Причиной заклинивания перепускного клапана часто является поломка пружины вследствие усталости металла.
Вспомогательные аппараты (теплообменные аппараты, теплые ящики и сепараторы пара). В судовых котельных установках применяют рекуперативные кожухотрубные теплообменные аппараты: конденсаторы, охлаждаемые забортной водой, паровые подогреватели топлива и воды. Причинами их неисправностей являются коррозионные разрушения трубных досок и пучков труб, истирание труб в местах крепления, нарушения плотности вальцовочных соединений и коррозионные повреждения корпусов с внутренней стороны. Наиболее распространены повреждения вальцовочных соединений, обусловленные релаксацией напряжений в них при одновременном протекании коррозии (как правило, межкристаллитной). Причиной повреждения корпусов, труб и трубных досок с паровой стороны является электрохимическая коррозия, а со стороны топлива - химическая, обусловленная наличием в нем сернистых и других агрессивных соединений. Скорости развития этих повреждений обычно малы. В агрегатированных топочных устройствах котлов
применяют электрические топливоподогреватели, основной причиной отказов которых являются повреждения нагреваемых элементов и термостатов.
Причинами отказов и неисправностей паровых сепараторов и тепловых ящиков в большинстве случаев являются повреждения установленных на них арматуры, элементов систем автоматического регулирования и защиты, а также загрязнения и коррозионные разрушения внутренних поверхностей и устройств. Наблюдаются также случаи коррозии наружных поверхностей теплых ящиков, сепараторов и тепло-обменных аппаратов под изоляцией. Причиной этих повреждений является попадание воды под изоляцию при протечках в сальниковых и фланцевых соединениях арматуры. Если отсутствует надлежащий контроль (изоляция не вскрывается по 3-5 лет), то эти повреждения могут стать причиной аварийного состояния СКУ. Так, на судах типов „Варнемюнде" и „Художник Сарьян" были случаи внезапного разрушения стенок теплых ящиков.
Трубопроводы СКУ (с путевой и соединительной арматурой) циркуляционной, питательной и топливной систем, трубопроводы продувания и импульсные, а также паропроводы, обслуживающие котельную установку.
Причины повреждений этих объектов повышенной уязвимости достаточно хорошо изучены. Это, как правило, коррозионно-эрозионный износ, локализующийся в местах деформации потока жидкости: у отводов, тройников, за арматурой, насосами, в районах фланцевых и штуцерных соединений. Локализация повреждений обусловлена тем, что при различных деформациях потока возникает пристеночная кавитация, следствием которой является разрушение оксидной пленки и протекание электрохимической коррозии с участием кислорода, растворенного в перекачиваемых жидкостях.
Подобные повреждения встречаются в трубопроводах любого назначения. В то же время трубопроводы СКУ имеют некоторые особенности, в той или иной степени отражающиеся на характере повреждений. Прежде всего они почти 2/3 календарного времени не работают, находясь на „мокром" хранении. В это время они подвержены стояночной коррозии, которая может протекать на любом участке трубопровода, где для этого имеются условия - влага и кислород. А такие условия существуют практически на всем протяжении трубопроводов, так как в период бездействия СКУ они не осушаются и не подвергаются специальной консервации. В паровых, циркуляционных и конденсат-ных трубопроводах коррозионно-эрозионный, износ интенсифицируется вследствие разрушения оксидной пленки и поврежденного слоя металла под ударами отдельных капель воды, кинетической энергии которых достаточно, чтобы в точках удара создать усилия, превышающие предел прочности. Эрозионный износ интенсифицируется также из-за наличия в перекачиваемых жидкостях твердых частиц (шлама, накипи, продуктов коррозии, песка и др.). Все перечисленные факторы обусловливают появление повреждений в виде свищей и разрывов.
На повреждения топливных трубопроводов, кроме 'того, значительное влияние оказывают содержащиеся в топливе сернистые соединения, интенсифицирующие разрушение оксидной пленки. Затраты на техническое обслуживание топливных трубопроводов в значительной степени определяются их загрязнением плотными асфальтосмолистыми отложениями, которые образуются в периоды длительного бездействия СКУ.
Арматура трубопроводов. Повреждения арматуры трубопроводов, как и котельной арматуры, связаны с ухудшением подвижности или заеданием движущихся деталей, пропусками рабочей среды через уплотнительные поверхности (неплотность затвора), коррозионно-эрозионными разрушениями рабочих поверхностей, штоков и корпусов арматуры, неплотностью сальниковых, штуцерных и фланцевых соединений, изменением натяга или поломкой регулировочных пружин и т.д. Ухудшение подвижности пар движения арматуры вызывается, как правило, загрязнением поверхностей накипью, коксом, продуктами коррозии. Заедание движущихся частей может быть следствием неправильной сборки сальниковых уплотнений, перекосом штоков и смятием на них или втулках резьбы от чрезмерного зажатия и др.
Особенно интенсивно изнашиваются посадочные поверхности арматуры, так как именно здесь происходит максимальная деформация потока, сопровождающаяся появлением пристеночной кавитации. Кроме того, в длительно закрытой запорной арматуре при некачественной притирке посадочных мест может появиться щелевая коррозия.
В крепеже фланцевых соединений паропроводов и арматуры вследствие высоких тепловых нагрузок и частых теплосмен возможны релаксация напряжений и нарушение герметичности.
И, наконец, причинами повреждений трубопроводов и арматуры могут явиться технологические дефекты -внутренние пороки металла (закаты, плены, шлаковые включения и т.п.), непровары сварных швов, поверхностные забоины, задиры, риски, а также некачественная сборка узлов сопряжения.
9.5. ОСНОВНЫЕ ПОКАЗАТЕЛИ НАДЕЖНОСТИ КОТЕЛЬНОЙ УСТАНОВКИ
Основным свойством качества котла является его надежность, так как именно она обеспечивает сохранность остальных свойств, которые не имеют практического значения, если котел ненадежен. Более того, поскольку продукция котла - теплота выработанного пара - не поддается складированию (заготовке впрок) и должна потребляться одновременно с ее производством, вопросы обеспечения высокой надежности СКУ приобретают первостепенное значение.
В соответствии со стандартами надежность котельной установки - это ее свойство обеспечивать судовые потребители необходимым количеством пара с установленными нормативной документацией экономичностью и параметрами пара на всех возможных режимах в течение заданного времени.
Основополагающими в теории надежности являются понятия работоспособности и отказа технического объекта, от четкого определения сущности которых зависит достоверность выводов о фактическом уровне надежности, оцениваемом по результатам статистической обработки эксплуатационных материалов.
Под работоспособностью котельной установки понимается такое ее состояние, когда она способна выполнять заданные функции (обеспечение судовых потребителей необходимым количеством пара) с параметрами (КПД, давлением и температурой пара), не выходящими за пределы, установленные нормативными техническими документами.
Отказом котельной установки считается событие, потребовавшее вывода котла из действия в период использования его по назначению или не позволившее ввести котел в действие при появлении необходимости в нем и вызвавшее вынужденное устранение обнаруженного повреждения, сопровождавшееся простоем СКУ в момент потребности в паре. Из этого определения следует, что все повреждения элементов котла и установки, обнаруживаемые во время профилактических осмотров и ремонтов, должны рассматриваться, как неисправности котельной установки, не приводящие к отказам.
Надежность как сложное свойство объекта формируется более простыми свойствами: безотказностью, ремонтопригодностью, долговечностью и сохраняемостью.
Безотказность - это свойство сохранять работоспособность без вынужденных перерывов в течение заданного времени эксплуатации. Основными показателями безотказности котла и СКУ являются: вероятность безотказной работы в течение рейса, среднее время безотказной работы (наработка на отказ) и параметр потока отказов (среднее число отказов восстанавливаемого объекта в единицу времени).
Под ремонтопригодностью понимается приспособленность котла и СКУ к предупреждению, обнаружению и устранению отказов путем проведения регламентных профилактических работ и ремонтов. Основными показателями ремонтопригодности являются среднее время восстановления и трудоемкость технического обслуживания и ремонта.
Долговечность - это свойство котла сохранять работоспособность до предельного состояния с необходимыми перерывами для технического обслуживания и ремонтов. Показатели долговечности: ресурс - наработка котла (т.е. чистое время работы) до предельного состояния и срок службы - календарная продолжительность его эксплуатации до этого состояния (или до списания).
Для котлов более показательным является срок службы, так как процессы изнашивания элементов котла протекают не только во время их действия, но и в период хранения (стояночная коррозия, загрязнение и т.п.). Отсюда следует, что сохраняемость как свойство объекта сохранять нормированные показатели в течение и после срока хранения применительно к вспомогательным и утилизационным котлам приобретает особую значимость, поскольку средняя суммарная продолжительность их хранения во времени, в течение которого КУ находится в бездействии по разным причинам) составляет 1/2 - 2/3 календарного времени эксплуатации.
Так как отказ КУ и восстановление ее работоспособности являются случайными событиями, то и все показатели надежности имеют вероятностную природу. С практической точки зрения, более простыми и психологически понятными являются следующие показатели надежности: среднее время между отказами и неисправностями восстанавливаемых объектов, средние трудоемкости и время их восстановления и срок службы (последний косвенно характеризует и сохраняемость). Именно эти показатели могут быть достаточно легко и просто использованы для непрерывного контроля технического состояния элементов КУ. В нормативно-техническую документацию эти показатели включают наряду с другими технико-экономическими показателями объекта.
При оценке указанных показателей надежности КУ и ее элементов в качестве единицы измерения целесообразно использовать сутки календарного времени. Статистические данные по отказам, неисправностям, режимам работы и восстановления КУ и ее элементов могут быть получены на основе обобщения опыта эксплуатации целых серий судов, а также по результатам специальных испытаний на надежность. Методы обработки статистических данных стандартизированы.
Оценка численных значений показателей надежности любого технического объекта на основе статистических материалов представляет собой весьма трудоемкую задачу, поэтому приведем только некоторые результаты такой оценки применительно к вспомогательным котлам основных типов. Прежде всего отметим, что надежность КУ мало зависит от режимов ее использования и типов применяемых котлов. Действительно, средняя наработка между отказами котельной установки составляет соответственно: с котлами типа КАВ 1,6/5 - 158 сут, КВВА 1,5/5 - 122 сут, Линдхольмен - 118 сут и VX - 152 сут (или в среднем 2,3-3 отказа в год).
Таблица 9.1
Элемент |
Наработка между отказами элементов котельных установок Т сут. |
||||||
КВГ34К |
КАВ1,6/5 |
КВВА1,5/5 |
КВВ-1/5А |
Пиндхоль- |
VX |
||
|
|||||||
|
|
|
|
|
мен |
|
|
Судовая котельная установка |
102 |
158 |
122 |
125 |
118 |
152 |
|
Корпус котла |
- |
3200 |
3000 |
3100 |
2700 |
1750 |
|
Воздухонаправляющее устройство |
320 |
226 |
426 |
- |
395 |
452 |
|
Клапаны: |
|
|
236 |
|
|
|
|
главный стопорный |
- |
667 |
575 |
783 |
698 |
||
предохранительный |
240 |
338 |
391 |
473 |
343 |
376 |
|
питательный |
310 |
223 |
387 |
592 |
283 |
318 |
|
продувания |
290 |
300 |
269 |
353 |
380 |
412 |
|
Воздухоуказательный прибор |
490 |
370 |
394 |
346 |
430 |
389 |
|
Прочая арматура |
316 |
345 |
350 |
334 |
389 |
412 |
|
Форсунка |
- |
247 |
216 |
415 |
567 |
456 |
|
САР |
280 |
264 |
278 |
347 |
583 |
637 |
|
Система сигнализации и защиты |
- |
375 |
250 |
463 |
303 |
367 |
|
Кирпичная кладка |
206 |
306 |
172 |
343 |
535 |
572 |
|
Насосы: |
|
|
452 |
|
|
|
|
питательный |
- |
523 |
678 |
868 |
817 |
||
топливный |
- |
900 |
930 |
985 |
880 |
822 |
|
Электровентилятор |
- |
600 |
756 |
712 |
670 |
623 |
|
Теплый ящик (чистка) |
- |
336 |
223 |
534 |
- |
- |
|
Топливоподогреватель |
- |
872 |
- |
- |
680 |
610 |
С практической точки зрения, эти цифры мало что говорят эксплуатационнику, для которого более важна информация о наиболее „слабых" элементах установки. Опыт эксплуатации показывает, что отказы собственно котла (с котельной арматурой) обусловливают менее 10 % отказов котельной установки. Основная доля (70 - 80 %) отказов приходится на элементы систем автоматики, сигнализации и защиты. Отказы кирпичной кладки становятся причиной отказов только в 2 - 3 % случаев. В остальных случаях (7 - 18 %) котельные установки отказывают из-за выхода из строя вспомогательных механизмов (прежде всего питательных насосов) и теплообменных аппаратов.
Представление о безотказности элементов котлов и установок дает табл. 9.1. При этом к отказам отдельных элементов относились все события, связанные с устранением повреждений, обнаруженных при плановых профилактических осмотрах и ремонтах еще до того, как они вызовут отказ КУ. Такие повреждения, по существу, есть потенциальные отказы установки, но при оценке наработки на ее отказ их не учитывают. В то же время именно эти события полностью определяют ремонтопригодность и долговечность установки.
Необходимо также отметить, что среднее время восстановления КУ после отказа 3 - 6 ч, средняя трудоемкость этих работ 10 - 12 чел-ч, а ущерб от одного отказа КУ в среднем 0,1 - 0,3 % первоначальной стоимости котла. Суммарные же затраты времени на техническое обслуживание (без заводских ремонтов) вспомогательных КУ колеблются от 60 до 300 ч/год.
В заключение приведем краткие рекомендации по повышению надежности оборудования КУ (и прежде всего главных элементов - котлов).
Необходимый уровень надежности технического объекта закладывается на этапах проектирования и изготовления, а реализуется в эксплуатации, основной целью которой является возможно более полное использование свойств объекта. На каждом из трех этапов существования объекта применяют хотя и специфические методы повышения надежности, но имеющие единую базу. Такие методы, как повышение квалификации исполнителей, совершенствование технической и нормативной документации, повышение качества технического надзора со стороны Регистра, а также учет уровня развития техники и технологий, оказывают определяющее влияние на уровень надежности судовых технических средств. Кроме того, надежность судовых котлов и КУ во многом зависит от уровня автоматизации, качества методов расчета, совершенства систем контроля технического состояния оборудования, качества ремонтных работ и методов испытаний. И, наконец, всегда следует помнить, что в основе всех этих методов лежит „человеческий фактор" в самом широком понимании (уровень оплаты труда и социальная защищенность, охрана труда и эстетика рабочих мест, пенсионное обеспечение и т.п.).
9.6. КОНТРОЛЬ ТЕХНИЧЕСКОГО СОСТОЯНИЯ КОТЕЛЬНОЙ УСТАНОВКИ, ТЕХНИЧЕСКОЕ ДИАГНОСТИРОВАНИЕ
Виды технического состояния объекта. В соответствии с содержанием понятия „техническое состояние" контроль предполагает оценку отклонений параметров, характеризующих ТС, от их значений, установленных нормативной документацией. Эти операции контроля служат целям своевременного обнаружения всех возможных повреждений элементов, которые могут привести к нарушениям работоспособности и снижению экономичности, появлению преждевременных и внезапных отказов, влекущих за собой серьезные аварии. В пределах допустимых отклонений этих параметров, устанавливаемых нормативной документацией, объект может иметь огромное число технических состояний, из которых в практике выделяют пары состояний: исправное - неисправное, работоспособное - неработоспособное, правильного - неправильного функционирования.
Висправном состоянии объект удовлетворяет всем требованиям нормативной и конструкторской документации (все параметры в норме), а в неисправном — не соответствует хотя бы одному из них.
Вработоспособном состоянии объект способен выполнять свои функции с техникоэкономическими показателями, удовлетворяющими требования нормативной документации. Если же хотя бы один из этих показателей выйдет за установленные пределы, то объект неработоспособен. Важно отметить, что работоспособное состояние объекта может быть как исправным, так и неисправным, т.е. объект может выполнять свои функции при наличии неисправностей отдельных деталей или узлов (например, наличие заглушенных труб является неисправностью поверхности
нагрева, а котел обеспечивает нормальные величины DK, ηK, pn, fn).
Правильно функционирующий объект может выполнять свои функции только на одном какомто режиме (например, работа котла на пониженных по требованию Регистра нагрузках), а неправильно функционирующий объект не может выполнять требуемые функции ни на одном из режимов (хотя в некоторых случаях и допускается его кратковременное использование для частичного выполнения функций). При этом в состоянии неправильного функционирования объект всегда неисправен.
Система контроля. Из изложенного следует, что оперативное получение информации, необходимой для достоверной оценки технического состояния объекта, предполагает непрерывный контроль определенной совокупности параметров объекта. Выбор этой совокупности определяется тем, какой вид технического состояния экономически целесообразно контролировать.
Ранее контроль осуществлялся путем периодического обхода работающих механизмов, осмотра и ежечасных записей показаний штатных приборов в машинный журнал. В дальнейшем для об-
легчения сбора информации о ТС стали применять приборы с дистанционными указателями, сосредоточенными сначала на местных пультах управления, а затем на пульте в ЦПУ. При этом в дополнение к показывающим приборам были введены системы аварийно-предупредительной сигнализации и защиты. По мере развития измерительной техники средств автоматизации были созданы системы централизованного контроля главных двигателей и некоторых ответственных вспомогательных установок. Кроме операций контроля, сигнализации и защиты, в СЦК предусматривалась автоматическая регистрация измерений контролируемых параметров. Однако в СЦК регистрируется ограниченное число параметров быстро развивающихся процессов повреждений и не контролируются медленные процессы разрушения (ползучесть, усталость, коррозия и т.п.).
Из краткого анализа истории развития контроля ТС судового оборудования следует, что основным направлением в создании систем контроля является переход от периодического контроля к непрерывному. При этом объем периодического контроля уменьшается, а непрерывного - возрастает. По существу, в настоящее время используется смешанный контроль ТС судового оборудования, при котором соотношение периодического и непрерывного контроля определяется назначением объекта, характером его рабочих процессов, уровнем автоматизации и экономическими соображениями.
Применительно к судовым вспомогательным котельным установкам в смешанном контроле преобладает периодический контроль ТС. При этом совокупность методов оценки параметров, аппаратуры, нормативных материалов и организационных положений, с помощью которых осуществляется смешанный контроль, представляет собой систему контроля технического состояния элементов КУ.
Организационные положения системы смешанного контроля ТС оборудования котельной установки предусматривают: непрерывный контроль качества функционирования установки; ежедневные осмотры; контроль степени загрязнения поверхностей нагрева; периодические наружные и внутренние осмотры; контроль уровня надежности элементов установки.
Непрерывный контроль качества функционирования КУ осуществляют по показаниям штат-
ных приборов, дающих информацию о технико-экономических показателях (паропроизводительности, КПД, давлению и температуре пара) и основных параметрах рабочих процессов (уровне воды в котле, температуре теплообменивающихся сред и т.п.).
При ежедневных осмотрах оценку ТС всех доступных (без разборки) для осмотра узлов и деталей осуществляют визуально по признаку „работоспособен - неработоспособен".
Контроль степени наружного загрязнения поверхностей нагрева котла осуществляют перио-
дически (не реже одного раза в 2 мес) с помощью штатных или переносных приборов, а также путем осмотров через лючки в обшивке котла или после вскрытия лазов в топку. Степень загрязнения по штатным приборам определяют по повышению температуры уходящих газов на фиксированной нагрузке при одинаковом коэффициенте избытка воздуха а, При этом приращение ∆tУХ устанавливают для котла каждого типа по результатам опыта эксплуатации и специальных теплотехнических испытаний из соображений допустимого снижения экономичности. Например, если судовладельцем допускается снижение КПД вспомогательных котлов на 4 - 5 %, то приращение температуры уходящих газов может достигать 80 - 110 °С.
Степень загрязнения с водяной стороны определяют по результатам оценки толщины слоя накипи во время проведения внутренних осмотров котла.
Периодический наружный осмотр выполняют во время проведения наружных очисток, периодичность которых устанавливают по результатам контроля степени загрязнения наружных поверхностей труб. При этом оценивают ТС всех доступных для осмотра и измерений элементов котла (труб, кирпичной кладки, топочных устройств и т.д.). При необходимости по решению старшего механика производят дефектоскопию отдельных деталей.
К этому виду контроля ТС относится и периодический осмотр элементов установки и арматуры котла. При этом контроль ТС средств автоматики и защиты (предохранительных клапанов, водоуказателей, быстрозапорных клапанов, устройств систем сигнализации и защиты, регулрующих устройств), а также котельной и путевой арматуры и трубопроводов осуществляют не реже одного раза в месяц без разборки и одного раза в год путем контрольных ревизий. Контроль ТС контрольно-измерительных приборов рекомендуется осуществлять один раз в год путем осмотров
и проверки документации и клеймения. Целесообразно совмещать эти операции контроля с подготовкой котла к ежегодному освидетельствованию.
Контроль ТС вспомогательных механизмов и аппаратов рекомендуется производить не реже одного раза в полгода без разборки с использованием переносных средств диагностики и одного раза в 2 года путем контрольной разборки. Контрольные разборки (ревизии) всех перечисленных элементов КУ должны носить выборочный характер (примерно 15 - 20 % всего числа элементов). По решению старшего механика объем контрольных разборок может быть увеличен.
Перцодический внутренний осмотр выполняют один раз в 2 года, а после второго очередного освидетельствования (т.е. через 8 лет) - ежегодно. Внеочередной внутренний осмотр производят в случае необходимости (при попадании масла в котел, упуске воды, засолении питательной воды и т. п.) по решению старшего механика. При внутреннем осмотре появляется возможность визуально оценить состояние внутренних (со стороны воды) поверхностей элементов котла, а также произвести измерения коррозионных язв, обнаружить поверхностные трещины, вырезать образцы для анализа (только по согласованию с инспектором Регистра) и произвести дефектацию.
Контроль уровня надежности элементов КУ осуществляют по показателям надежности, рассчитанным для совокупности однотипных элементов (например, для стопорных клапанов, питательных насосов и т.п.). В качестве контролируемого показателя надежности можно выбрать параметр потока отказов или среднее значение наработки между отказами. В настоящее время отраслевая информационная система
„Надежность" находится в стадии становления и не может обеспечить потребителей (в том числе экипажи судов) информацией о надежности элементов вспомогательных установок, поэтому уровень надежности элементов КУ можно оценивать приближенно путем сопоставления фактических значений наработок на отказы элементов установки на данном судне со средними их значениями, приведенными в табл. 9.1.
Методы и средства контроля. Все виды периодического контроля ТС требуют применения специальных методов и аппаратуры для измерения структурных параметров элементов, характеризующих их техническое состояние. В практике оценки ТС элементов судового оборудования используют следующие методы и средства: визуальное освидетельствование и измерения; неразрушающие методы дефектоскопии; механические и технологические испытания; химические и металлографические исследования; гидравлические испытания. Эти методы должны применяться именно в той последовательности (от простого к более сложному), в какой они перечислены.
Визуальное освидетельствование и измерения, применяемые для выяснения причин поврежде-
ний, предшествуют всем остальным методам. По количеству информации, которая может быть получена при осмотрах и измерениях, этому методу нет равных. Поэтому особенно важно уже при первом осмотре зафиксировать (записи, эскизы, фото) как можно больше деталей фактической картины внешнего проявления повреждения, не упуская никаких мелочей, которые при осмыслении могут оказаться решающими. При освидетельствовании обычно используют простейшие оптические приборы (лупы, эндоскопы) и мерительный инструмент. При вырезке образцов для анализов необходимо точно отмечать место их взятия. Особое внимание при осмотрах следует обращать на состояние рабочих поверхностей изделия -имеются ли отложения, коррозионные и механические повреждения, изменение цвета и геометрических характеристик изделия. Обычно результаты внешнего осмотра и измерений позволяют сделать предположение (более или менее обоснованное - зависит от опыта специалиста) о фактических причинах данного повреждения.
Внекоторых случаях полученной при освидетельствовании информации может оказаться недостаточно для достоверной идентификации причин повреждения, особенно тогда, когда повреждения обусловлены процессами разрушения при высоких температурах или от внутренних дефектов. В этих случаях весьма ценную информацию можно получить, используя неразрушающие методы дефектоскопии (часто их называют методами неразрушающего контроля).
Внастоящее время методы НК в условиях эксплуатации на судах применяют редко, что связано, как правило, с отсутствием высокоточной отечественной переносной измерительной аппаратуры. Однако даже имеющиеся приборы позволяют значительно повысить достоверность информации о причинах повреждения. К методам НК, которые можно применять на судах, относятся: спектральный анализ, методы оценки сплошности материалов, гидравлические испытания и др.
Спомощью спектрального анализа можно оценить локальный химический состав металла и отложений. Например, при выяснении вопроса о соответствии использованной марки стали тем условиям, в которых она работала, хорошие результаты дает полуколичественный спектральный анализ с помощью переносных стилоскопов. Для более точных анализов обычно отбирают образцы материала и передают в стационарную береговую лабораторию.
К методам оценки сплошности материалов относятся: ультразвуковая, радиационная и магнитопорошковая дефектоскопия, а также капиллярные методы, которые позволяют определять наличие поверхностных и внутренних трещин и микротрещин, технологических дефектов (закатов, плен, расслоений, шлаковых включений, непроваров), проверять плотность вальцовочных и сварных соединений, а также оценивать степень коррозионного износа в недоступных для прямого измерения местах (например, на внутренней поверхности труб).
Магнитопорошковая дефектоскопия относится к старым, хорошо зарекомендовавшим себя методам контроля сплошности металлов. С помощью МПД выявляют в основном поверхностные
иприповерхностные (на глубине до 2-3 мм) дефекты металла таких элементов котла, как барабанов, коллекторов, жаровых труб, арматуры, опор и др. В его основу положена способность металла намагничиваться под действием приложенного магнитного поля и создания над дефектом магнитного поля рассеяния. Дефекты фиксируют с помощью магнитного порошка.
Сметодом МПД в настоящее время успешно конкурируют капиллярные методы дефектоскопии, в основу которых положено свойство поверхностных дефектов выполнять роль капиллярных трубок. Жидкости, применяемые при этом, должны обладать высокой смачивающей способностью
илегко проникать в поверхностные несплошности материалов. Разработаны и выпускаются промышленностью люминесцентные и цветные жидкости, дающие примерно одинаковые результаты. Прообразом этих методов явилась мело-керосиновая проба - старый испытанный метод, в котором в качестве жидкости используют керосин, обладающий высокой смачивающей способностью. Разрешающая способность капиллярных методов примерно такая же, как и МПД.
Для выявления внутренних дефектов (несплошностей) на глубине более 3 мм применяют радиационные (рентгеновские и Y-лучи) и ультразвуковые методы НК. Радиационные методы пригодны только для береговых лабораторий из-за громоздкости и сложности аппаратуры. Ультразвуковая дефектоскопия находит все более широкое применение на судах. Обусловлено это успехами в миниатюризации переносных приборов УЗД при сохранении их достаточно высокой точности. Сейчас с помощью УЗД-приборов определяют не только наличие внутренних дефектов, но
иоценивают толщину стенок деталей, что дает возможность идентифицировать коррозионные повреждения внутренних поверхностей труб. Кроме того, с помощью УЗД-приборов можно оценить (достаточно приближенно) величину зерна в микроструктуре металла, а следовательно, и прочностные его характеристики. Следует, однако, отметить, что оснащенность отечественных судов УЗД-приборами далеко недостаточна для эффективного оперативного контроля ТС судового оборудования.
К методам НК относятся и методы косвенной оценки характеристик прочности металла по результатам измерений твердости с помощью переносных приборов - твердомеров типов ТОП-1, КПИ-ВР и др. Этот метод основан на том положении, что между твердостью материала и пределом его прочности (а также другими характеристиками) существует тесная корреляционная связь, позволяющая по измеренной твердости просто и быстро оценивать механические характеристики материалов. К сожалению, на судах этот метод почти неизвестен, хотя информация о нем имеется не только в специальной литературе, но и в широко известных справочниках.
Визуальное освидетельствование и методы НК дают в основном информацию о качественной картине повреждения. Опытному механику обычно бывает достаточно этой информации для того, чтобы установить причину повреждения и применить необходимые предупредительные меры. В тех случаях, когда характерные повреждения продолжают повторяться, несмотря на принимаемые меры, необходимо получить дополнительную информацию для установления количественных характеристик процессов разрушения. Сделать это можно с помощью механических и технологических испытаний, химических анализов и металлографических исследований микроструктуры. Все эти методы обычно применяют в стационарных береговых лабораториях. Подробные методики по их проведению имеются в специальной литературе. Здесь дана только краткая характеристика методов с целью общего ознакомления судовых механиков.
Химический анализ применяют для точного определения химического состава материалов образцов, что бывает необходимо для установления тех условий эксплуатации, которые привели к повреждению элемента.
Механические методы испытаний (на растяжение при комнатной температуре, на ударную вязкость, на твердость по Бринеллю и др.) предназначены для определения характеристик прочности и пластичности материалов, информация об изменении которых необходима при анализе температурных условий работы изделия.
Технологические методы испытаний (на загиб, сплющивание, бортование и раздачу труб, осадку и сопротивление задиру и т.п.) позволяют получить качественные характеристики пластичности материалов и проверить их способность к восприятию холодных деформаций. Они с успехом могут быть использованы судовыми механиками при анализе причин повреждений, так как позволяют выявить не только технологические дефекты (закаты, расслоения, риски, пороки сварных швов), но и эксплуатационные повреждения (трещины, охрупчивание, коррозию, изменение микроструктуры и т.п.). Технологические испытания не требуют специального оборудования, достаточно просты и производятся без больших затрат времени.
Металлографические исследования структуры материалов позволяют обнаружить пороки строения металла, обусловленнные неправильной термообработкой (образование крупных зерен, выделение цементита на границах зерен и т.п.), а также изменение структуры при высоких температурах (сфероидизация, обезуглероживание и т.п.) и агрессивном воздействии теплоносителей (меж- и транскристаллитная коррозия и т.п.). Эти исследования выполняют с использованием микроскопов с кратностью увеличения от 5 до 20 000. Трудоемкость исследований велика и выполняют их только в береговых лабораториях по решению специальных комиссий, расследующих причины аварий.
Перечисленные методы редко применяют все одновременно, обычно используют, комбинации некоторых из них в зависимости от целей анализа, причин повреждений и характера их проявления (аварии, отказы, неисправности).
Гидравлические испытания относятся к старым средствам определения несплошностей материалов и неплотностей соединений. С их помощью выявляют сквозные дефекты и трещины в деталях котла, а также повреждения прокладок и сальниковых уплотнений. Гидравлические испытания строго регламентируются Правилами Регистра и Правилами технической эксплуатации.
Полученные результаты контроля технического состояния обрабатывают и сопоставляют с допустимыми значениями отклонений параметров, которые установлены инструкциями завода-из- готовителя, Правилами технической эксплуатации котлов и нормативными документами Регистра. Результаты оценок ТС заносят в журнал технического состояния и применяют при организации технического использования КУ и планировании ее технического обслуживания и ремонта (рис. 9.14).
Техническое диагностирование. Неполнота информации, полученной при работе КУ с помощью штатных приборов, неизбежно ведет к необходимости вывода установки из действия и разборки отдельных элементов с целью получения недостающей информации о ТС. Вывод из действия и разборка элементов сопряжены со значительными затратами времени и средств. В то же время, как показывает практика, во многих случаях разборка оборудования не вызывается необходимостью. Поэтому в последние годы все больше внимания уделяется разборке и внедрению в практику методов технического диагностирования (от греч. diagnosis -распознавание, определение), главной задачей которого является оценка технического состояния объекта без его разборки (отсюда часто встречающийся термин "безразборное диагностирование").
Как отмечалось, техническое состояние того или иного элемента характеризуется совокупностью структурных параметров, которые в процессе эксплуатации изменяются вследствие протекания сопутствующих процессов (загрязнения, коррозии, усталости, ползучести и т.п.) от номинальных значений sH1, sH2, ..., sHK . до предельных sn1, sn2, ..., snK. Разности между текущими и номиальными значениями параметров ∆sTj = STJ - SHJ характеризуют степень изменения ТС, а разности между текущими и предельными значениями параметров ∆sПj = sTj - sПj - остаточный ресурс. Однако контролировать изменение структурных параметров в большинстве случаев невозможно из-за отсутствия методов и средств измерений и по экономическим соображениям. Поэтому необходимо структурные параметры заменить диагностическими параметрами, косвенно связанными с первы-
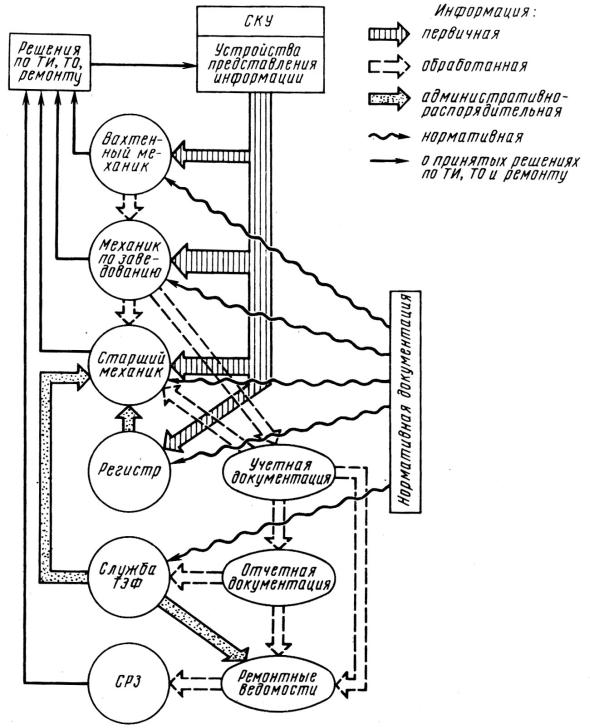
ми, несущими достаточно большое количество информации о техническом состоянии объекта диагностирования и легко измеримыми. При этом ТС оценивают по отклонению текущих значений диагностических параметров dTj от их эталонных значений dЭТj . В качестве эталонного значения диагностического параметра обычно принимают его значение, соответствующее технически исправному состоянию объекта при определенных нагрузке и внешних воздействиях. Таким образом, исправному состоянию объекта соответствует значение ∆dTj = dTj - dЭTj = 0, а неисправным состояниям ∆dTj <> 0.
Рис. 9.14. Принципиальная схема использования информации о техническом состоянии элементов СКУ.
Диагностические параметры должны удовлетворять следующим требованиям: обладать высокой чувствительностью к изменению контролируемого структурного параметра; быть достаточно информативными с точки зрения распознавания неисправности; определение его численных зна-
чений должно быть простым; число диагностических параметров для распознавания данной неисправности должно быть минимальным, а затраты на процесс диагностирования - оптимальными. Следует отметить, что создание систем технического диагностирования - процесс длительный и трудоемкий, требующий обширных знаний не только в специальной области. При этом основой всей системы является алгоритм диагностирования, представляющий собой содержание и совокупность последовательных операций по распознаванию неисправности. Современные судовые технические средства (в том числе КУ) представляют собой сложные системы с большим числом деталей и узлов, техническое состояние которых контролировать с помощью систем диагностирования практически невозможно. Поэтому при создании систем технического диагностирования обычно решаются локальные задачи по контролю ТС тех элементов, от исправности которых в первую очередь зависят качество, функционирования объекта, его экономичность и надежность. Развиваются два направления создания систем технического диагностирования: применение встроенных (в объект) диагностических средств, образующих бортовые диагностические комплексы, и комплектация судов переносными диагностическими приборами для периодической оценки технического состояния наиболее "слабых" элементов. Создание бортовых диагностических комплексов экономически целесообразно в основном для оценки ТС лавных двигателей. Для оценки ТС вспомогательного оборудования более приемлемы переносные диагностические приборы, относительно недорогие и дающие достаточное количество информации.
Создание систем технической диагностики СКУ тормозится объективными трудностями, обусловленными невозможностью эффективного контроля медленных процессов разрушения (коррозии, эрозии, ползучести, усталости и т.п.), которые определяют техническое состояние подавляющего большинства деталей и узлов элементов КУ. В настоящее время не существует систем технического диагностирования СКУ, хотя исследования в этом направлении ведутся. Реальным является возможность диагностирования степени наружных загрязнений поверхностей нагрева котлов с помощью переносных приборов - газоанализаторов, которые позволяют оперативно оценивать изменения интегрального показателя степени загрязнения - коэффициент полезного действия котла. Остальные операции контроля ТС, как указывалось, осуществляют периодически.
Контрольные вопросы и задания
1.Дать определение понятия „техническое состояние объекта".
2.Указать основные факторы, определяющие интенсивность протекания процесса разрушения элементов котла.
3.Дать общую характеристику процесса коррозии в судовых котлах.
4.Привести примеры кислородной коррозии элементов котла и раскрыть причины ее появле ния.
5.Каков механизм процесса разрушения металла, обусловленного его перегревом и термиче ской усталостью (привести примеры)?
6.Указать возможные нарушения правил технической эксплуатации, обусловливающие отказы элементов котла.
7.Выполнить анализ причин изменения технического состояния вспомогательного оборудова ния котельной установки.
8.Какова сущность показателей надежности элементов котла?
9.Дать определение понятий «исправное" и „работоспособное" состояния котла.
10.Пояснить содержание отдельных видов контроля технического состояния элементов котла.
11.Дать общую характеристику методов контроля технического состояния элементов котлов.
12.В чем заключается сущность технического диагностирования котлов?