
книги из ГПНТБ / Иванцов, Олег Максимович. Индустриализация строительства магистральных трубопроводов
.pdfОднако при применении этого метода получить высокое и стабильное качество сварного шва по всему периметру возможно только при точно обработанных концах труб с допуском по диа метру ±1,0 мм и при величине притупления от 1,0 до 2,0 мм. А так как выпускаемые заводами трубы имеют большие допуски, получить сварку хорошего качества при помощи автомата АМД-3 пока не представляется возможным.
Рис. |
42. Схема автоматической сварки труб в |
Рис. 43. Схема головки |для |
||||||
|
потолочном положении. |
внутренней |
|
сварки |
уста |
|||
1 — труба; 2 — бункер; з — флюс; ”4 — шнек;'а — |
новки |
Р-751. |
|
|
||||
механизм подачи; |
в — электродная проволока; 7 — |
1 — сварочная |
|
головка; |
2 — |
|||
|
нопирное устройство. |
свариваемые |
трубы; |
з — флю |
||||
|
|
|
совая подушка; |
4 — электрод |
||||
|
|
|
ная проволока; |
|
5 — пружина. |
|||
В установке Р-751 в трубах большого диаметра первый |
слой |
|||||||
шва |
варят |
изнутри специальной головкой, |
изображенной |
|||||
на рис. 43. Затем головку из трубы извлекают и другой |
голов |
|||||||
кой |
варят наружный слой. Установка |
Р-751 имеет |
проходной |
вращатель-центратор, позволяющий механизировать сборку труб. Сборка и сварка труб ведется на одном рабочем месте. Опытное применение установки на строительстве газопровода Ставро поль — Москва в 1956 г. выявило ее невысокую производитель ность и значительный расход флюса.
Возможно также применение съемных подкладных колец, но проведенные многочисленные попытки использовать кольца из красной меди, керамики, прессованной бумаги и др. из-за большой трудоемкости их установки и извлечению из труб, не обеспеченности плотного прилегания к внутренней поверхности не нашли практического применения.
В последние годы на строительстве магистральных трубопро водов получила распространение стыковая контактная сварка.
101
Она освоена для труб диаметром 219—529 мм и характеризуется
высокой механизацией всех сборочных и сварочных |
операций. |
Сборка и сварка одного стыка занимает 6—7 мин., а |
машинное |
время собственно сварки не превышает 1,5—2 мин. |
В смену |
варится около 45—50 стыков. Некоторые бригады, обслуживаю щие контактные машины, достигли более высоких результатов. Так, бригады т. Голованчука (СМУ-7 треста Нефтепроводмонтаж) и т. Карчинского (Сварочно-монтажного треста) варйт в смену по 60—70 стыков. В 1958 г. лучшими бригадами производитель ность агрегатов доведена до 100—120 стыков в смену.
Однако машины для контактной сварки имеют много конструк тивных недостатков. Они громоздки и тяжелы. Это снижает их проходимость в гористых, болотистых и лесных местностях. Машины часто выходят из строя, простой их в отдельных случаях составляет 50% рабочего времени. Недостатки контактно-сва рочных машин: большие допуски в геометрических размерах, несовершенство технологии сварки труб (диаметром 529 х 7 мм) тормозят внедрение электроконтактной сварки.
Сравнительные данные трех способов сварки магистраль ных трубопроводов (производительность 132 стыка в смену)
приведены |
в табл. 22. |
|
|
|
|
|
|
|
Таблица 22 |
|
|
Автосварка под |
Ручная ду- |
|
|
|
флюсом поворот |
|
|
Показатели |
ных стыков (две |
говая свар |
Контактная |
|
установки), руч |
ка поточно- |
сварка (два |
||
|
|
ная сварка непо |
расчленен |
агрегата) |
|
|
ным мето |
||
|
|
воротных стыков |
дом |
|
|
|
(21—22 стыка) |
|
|
|
|
|
|
|
Общее количество рабочих . . |
35—37 |
37—46 |
17 |
|
Количество |
квалифицирован |
|
|
|
ных рабочих (мастера, свар- |
|
|
|
|
щики, водители и др.) . . |
22 |
25 |
9 |
|
Количество |
электростанций |
7 |
15 |
2 |
Суммарная мощность электро-
станций, л. с...........................
Количество тракторов ....
Количество грузовых автома-
ШИН........................................
Вспомогательные материалы
Выработка на одного человека
в смену, стыки....................
5 x 454-2x110= 445
5
1
Качественные
электроды, элек тродная проволо
ка, флюс, поло
совое железо, горюче-смазочные
3,57
15X45=675
3
2
Качественные элек троды, го рюче-сма зочные
Всреднем
3,2
2X420 = 840
4
_
Горючесмазочные
7,8
102
Из приведенной таблицы видно, что наиболее производитель ным и механизированным способом сварки магистральных трубо проводов является контактный способ.
В текущем семилетии предусматривается широкое внедрение контактной сварки. В 1960 г. намечается сварить этим методом 60% всего объема магистральных трубопроводов диаметром 529 мм и менее.
Для совершенствования контактной сварки имеет значение испытание качества стыков. Оно не может выполняться обычными методами. О качестве стыка можно судить только по механиче ским испытаниям образцов, вырезанных из стыка. Качество стыков зависит в основном от силы сварочного тока, величины и скорости оплавления и осадки.
ВНИИСТ и институт Оргэнергогаз разработали двухканальнып прибор автоматического контроля за технологическими па раметрами электрокоптактной сварки. Контролю будут подвер гаться все 100% стыков.
Величины сварочного тока и перемещения стыкуемой трубы за весь цикл сварки прибор записывает на бумажной ленте, движущейся с заданной синхронной скоростью. Полученная диаграмма позволяет легко установить степень нарушения того или иного параметра сварки, влияющего на общий технологи ческий процесс.
Дистанционный контроле за величиной оплавления и осадки производится при помощи сельсинов, один из которых — дат чик — установлен на подвижной части сварочной головки, а дру гой — приемник — вмонтирован внутри прибора. Запись тока за весь процесс сварки стыка производится па той же ленте па раллельно с записью перемещения.
Прибор снабжен автоматическим печатающим устройством для записи очередного сварного стыка.
. Институт электросварки им. Е. О. Патона работает над соз данием агрегатов для контактной сварки труб диаметром 720— 1020 мм. Испытания опытной машины для труб диаметром 720 мм показали вполне. удовлетворительное качество сварки. Стык
сваривался сварочной |
головкой весом 7,5 т с наружным охва |
||||||
том. |
Время сварки стыка 1,5—2 мин., причем кольцевые транс |
||||||
форматоры питались |
от |
той |
же |
передвижной |
электростан |
||
ции, |
которая используется |
для |
сварки труб |
диаметром |
|||
529 |
мм. |
|
|
|
|
|
|
Для трубопроводов большого диаметра головки с наружным |
|||||||
■охватом |
громоздки |
и |
тяжелы. |
Институт электросварки |
|||
им. |
Е. О. |
Патона создал для труб большого диаметра сварочные |
головки, размещаемые внутри труб. Применение таких головок улучшит условия центровки труб, повысит производительность, упростит обслуживание контактных агрегатов.
Условия проведения сварочно-монтажных работ при строи- 'тельстве магистральных трубопроводов весьма специфичны.
103
Выполняются они на равнинной, гористой, лесистой, боло тистой и пустынной местностях, в основном на открытом воздухе, в различных метеорологических условиях, круглосезонно.
Несмотря на различные условия производства сварочно-мон тажных работ, т. е. различную протяженность трассы, рельеф местности, климатические и метеорологические условия, сроки строительства, длину п диаметр свариваемых труб и др., орга низация сварочно-монтажных работ в настоящее время осуще ствляется по следующим трем основным схемам.
Первая схема, наиболее распространенная в Советском Союзе, включает вывозку труб с железнодорожных станций на свароч ные базы (автосварочные установки), где их сваривают в секции поворотной автоматической сваркой иод флюсом, после чего секции вывозят на трассу и соединяют в нитку ручной сваркой.
Вторая схема включает вывозку труб с железнодорожной станции, но уже непосредственно на трассу и сварку их в нитку электроконтактной сваркой методом наращивания.
Третья схема применяется в отдельных случаях при сварке трубопроводов малого диаметра, небольшой протяженности или прокладываемых в сильно пересеченной местности, куда трудно доставить секции труб или невозможно обеспечить перемеще ние вдоль трассы агрегатов электроконтактной сварки. Схема включает вывозку труб с железнодорожных станций на трассу и сварку их вручную.
Базовая сварочная установка пли сварочная база не является стационарным сооружением. Обычно после сварки участка тру бопровода протяженностью около 20 км ее переводят на новое место. Поэтому все устройства базы сборио-разбориые, простые и легко перевозимые.
Базовые сварочные установки располагаются по возможности в середине сооружаемого отрезка трассы, с учетом подъездных дорог к станции разгрузки труб и к трассе. При выборе места расположения сварочной базы следует исходить из наиболее длительного использования ее на одном месте.
В некоторых случаях возможна организация трубосварочных баз в специальных или приспособленных цехах. Такое решение позволит улучшить условия работы на базе.
Так, на строительстве участка длиной 158 км первой очереди газопровода Ставрополь — Москва, работы на котором выпол нялись СМУ-77 треста № 7 Главнефтемонтаж, был использован для организации трубосварочной базы цех металлоконструкций
вг. Щекино, находящийся поблизости от трассы.
Кцеху была проложена железнодорожная ветка. Трубы раз гружались или возле цеха 30-тонным гусеничным краном, при чем специальные стропы позволяли разгружать вагон в четыре
захвата, |
или в самом цехе мостовым краном. |
В цех |
трубы подавали на специальной тележке по железно |
дорожным путям. Приводом тележки служил автокран, на ободья
104
которого были поставлены бандажи с профилем колес железно дорожных вагонов. Автокран осуществлял погрузку и разгрузку
труб.
Все технологические операции в цехе по сварке секций труб были организованы по поточному методу. Принципиальная тех нологическая схема этого цеха изображена на рис. 44.
В цехе общей площадью 1300 .и2 были организованы два по тока, которые включали участки установки подкладных колец,, центровки секций из четырех и пяти труб, а также участок авто матической сварки.
Рис. 44. Технологическая схема цеха сварки секций труб СМУ-77.
г — склад труб вместимостью 1800 шт.; 2— склад готовых секции; з — помещение для сварки труб; 4 —■ помещение для сварки фасонных деталей; 5 — склад на 154 секции из четырех труб; 6 — трансформаторная будка; 7 — кран для погрузки секций; з — склад горючего; о — помещение для гибки фасонных частей газопровода; 10 — цеховой пролет для изготовления металлоконструкций; 11 — широкая колея; 12 — стеллажи;
13 — широкая и узкая колеи.
Вальцовка с отбортовкой подкладных колец выполнялась механизированным способом на специальном устройстве к валь цам.
Для облегчения центровки труб коллективом работников цеха было разработано приспособление, представляющее собой тележки на шарикоподшипниках, легко перемещающиеся по направляю щим рельсам (рис. 45). Трубы натягивались па подкладные кольца лебедками. Во время сборки трубы вращались на тележ ках при помощи роликов, на которые их укладывали.
Описанные усовершенствования, применявшиеся при сборке, позволили бригаде из 5 человек, включая прихватчика, цент ровать за смену в среднем 14—15 секций.
Собранные секции перекатывались на роликовые опоры сва рочного стенда. Так как стенд, роликовые опоры сварочного стенда и стеллаж готовых секций были установлены на одном уровне, перекатывать секции было нетрудно.
Для сварки сначала использовался модернизированный полу автомат ПШ-5, затем был смонтирован стенд типа стендов треста Нефтепроводмоитаж с постоянным рабочим местом сварщика и
105-
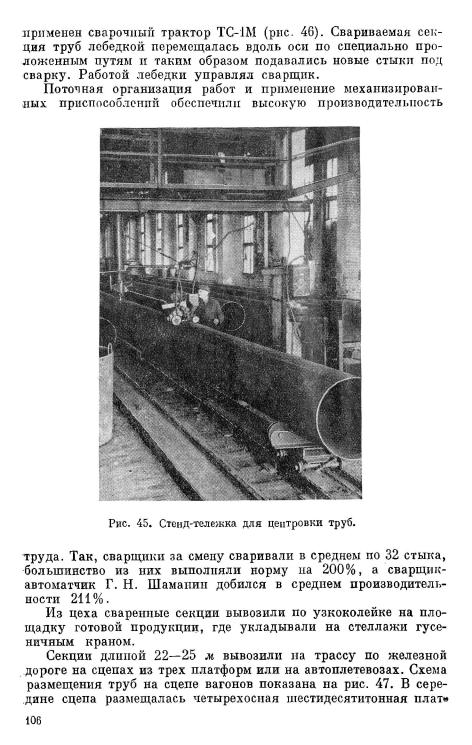
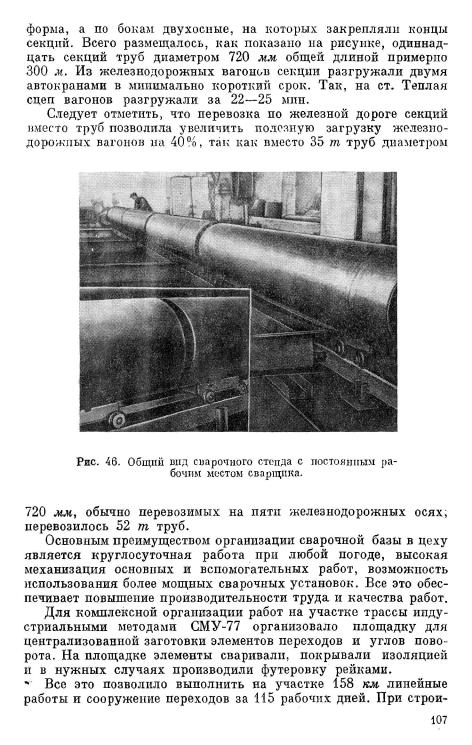
2500. 8160
тельстве участка средний темп со-, ставлял 1,4 км готового трубо провода в день.
Описанная цеховая органи зация сварочной базы является частным примером.
Технология и сама схема ор ганизации работ на базах имеют существенные недостатки.
На трубосварочных базах многие операции выполняются вручную, это операции по под готовке труб под сборку, ручная правка концов, транспортировка труб и секций внутри установки по стеллажам, стягивание труб ручной лебедкой при сборке в секции, закрепление и освобож дение концов секций труб в тор цовом вращателе и др. Сущест венно снижается производитель ность из-за разбросанности ра бочих мест.
Одной из трудоемких опера ций сварочно-монтажных работ является сборка стыка труб. Особенно сложно собрать стык труб большого диаметра. Даже бригады высококвалифицирован ных рабочих затрачивают на вы полнение этой операции около
20мин.
Время, затрачиваемое на сбор
ку секции, из трех труб диа метром 820 X 9 мм (по данным СМУ-10 Сварочно-монтажного тре ста), приведено в табл. 23.
Сварщик Омельяненко и ин женер Сорочинский разработали усовершенствованную схему ор ганизации работ на трубосвароч ной базе (рис. 48).
Схема предусматривает выпол нение работ по сварке секций и их изоляции по поточному ме тоду. На площадке 100 X 80 м размещается склад труб, линия подготовки и центровки труб
108
|
Таблица 23 |
|
Операции |
Время, |
|
мин. |
||
|
||
Зачистка кромок (одного конца) . . |
2,5-8,0 |
|
Запрессовка и приварка подкладно |
6,5—16,0 |
|
го кольца ......................................... |
||
Центровка одного стыка па кондук |
8,0 |
|
торе ................................................. |
||
Прихватка стыка................................ |
10,0 |
|
Сдвигание труб вручную ................ |
2,0—4,0 |
|
Сдвигание лебедкой ............................ |
1,5 |
Рис. 48. Схема трубосварочной базы, предложенная сварщиком Омелья-
ненко |
и |
инженером |
Сорочинским. |
|
||
1 — приспособление для очистки |
кромок |
труб; |
г — приспособление для запрессовки |
|||
колеп; 3 — сварочный агрегат |
АСБ-300; |
1 — роликоопора продольная сбрасывающая; |
||||
5 — роликоопора продольная; 6 — установка для стягивания и центровки; |
7 — укрытие; |
|||||
8 — роликоопора продольная |
подающая; |
9 — покаты; |
10 — машинка |
для очистки, |
||
правки и намотки кассет; н — сварочный агрегат АСД; |
12 — вращатель; |
13 — ролико |
||||
|
опора вращения. |
|
|
|
в секции, линия автосварки труб, линия очистки и линия изо ляции секций.
Трубы длиной до 12 м подают трубоукладчиком на стеллаж линии подготовки труб. По покатам трубы подкатываются к при способлениям для очистки кромок труб 1. где электроприспособле- ,ниями концы труб с двух сторон зачищаются под сварку, а в слу чае необходимости механизированными приспособлениями вы правляются кромки труб. Затем в трубы механическим приспо-
109
соблением 2 запрессовывается подкладное кольцо и прихваты вается вручную.
Заготовка, подвальцовка и очистка подкладных колец выпол няется на специальном станке.
Подготовленные трубы электрифицированным приспособле нием подаются на линию центровки. Для продольного перемеще ния трубы накатываются на роликоопоры, у которых одна роликоопора' 5 — холостая, а вторая 8 — подающая. По роликоопорам трубы подаются в приспособление 6, где механизированным способом их поворачивают для центровки и стягивают до необхо димого зазора для сварки, а затем ставят прихватки. Собранная секция при помощи сбрасывающих роликоопор скатывается на приемный стеллаж, а с него по накатам на роликоопоры линии сварки. Последние позволяют осуществлять вращение секции и продольное перемещение. Посередине сварочной линии уста новлен приводной роликовый вращатель 12.
Сварщик может сваривать секцию в укрытии на постоянной сварочной площадке, а также, перемещая сварочный автомат, переходить от стыка к стыку.
Сваренную секцию при помощи сбрасывающих роликоопор подают на стеллаж, на котором производится приемка стыков по внешнему виду и контроль качества сварки магнитографи ческим методом илп просвечиванием гамма-лучами. Затем сек ции подают па очистку и изоляцию.
Разработанная тт. Омельяненко и Сорочинским схема меха низированной установки базовой сварки и изоляции секций пре дусматривает поточную организацию работ, ведение работ в лю бую погоду (так как подготовка труб, центровка, сварка и изоля ция производятся в укрытиях), механизацию ручных процессов, возможность быстрого преобразования установки, так как она состоит из легкомонтируемых отдельных механизмов и групп, использование только электропривода и питания от общей элек тростанции постоянного тока с низким напряжением.
В технологическую схему авторы включают очистку и изоля цию труб.
Некоторые сварщики-новаторы применили ряд усовершен ствований. Так, сварщики тт. Шмидт, Шамиков и другие приме няют цепные вращатели новой конструкции. Конец секции за крепляется во вращателе, на стык ставится сварочная головка. Сварка осуществляется сварочным трактором ПТ-56, питающимся от агрегата АСД-3-1 или АСДП-500. Сварочный трактор ПТ-56 работает совместно с вращателем.
Автосварщики тт. Константинов, Шмидт, Омельяненко, Ноздрачев и другие достигли высокой производительности сварки. Они сваривают 50—60 стыков в смену, применяя для сварки повышенную силу тока 580—600 а.
Тов. Маевский и Ноздрачев на рабочих площадках вдоль сварочных стендов на высоте 2 м натягивают трос, к которому
110