
книги из ГПНТБ / Классификация режущего инструмента Всесоюзный научно-исследовательский инструментальный институт (ВНИИ) под редакцией д-ра техн. наук И. И. Семенченко. 1960- 3 Мб
.pdf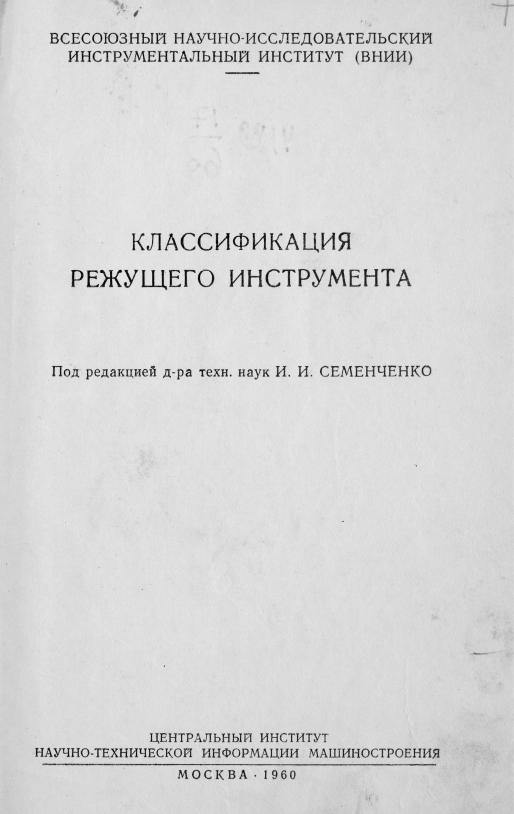
в |
ffW йУЬЛИ‘..-ч'г.Я |
i |
41 w |
й AL- |
j |
Н/^ЛЧ(й;>ТЕХНимсСКАЯ 1 |
|||
i| . |
SWB^OTE1^ poop |
j |
Канд. техн, наук М. И. ЮЛИКОВ
КЛАССИФИКАЦИЯ РЕЖУЩЕГО ИНСТРУМЕНТА
Раздел I
КЛАССИФИКАЦИЯ РЕЖУЩЕГО ИНСТРУМЕНТА,
ОСНОВАННАЯ НА ИЗУЧЕНИИ ЕГО КИНЕМАТИКИ В ПРОЦЕССЕ ФОРМООБРАЗОВАНИЯ ПОВЕРХНОСТИ ИЗДЕЛИЯ
ИСХОДНЫЕ ПОЛОЖЕНИЯ
За длительный период развития обработки металлов резанием
возникло много разнообразных видов и типов металлорежущих
инструментов и накопился богатый опыт по их конструированию,
производству и эксплуатации. Однако теоретические исследования,
основанные на обобщении этого опыта, часто отстают от требований практики. До настоящего времени теория конструирования режу щего инструмента представляет изложение ряда практических и теоретических данных, относящихся к конкретным видам инструмен
та: резцам, сверлам, зенкерам, разверткам и т. д. В области же
разработки общей теории конструирования режущего инструмента в настоящее время предпринимаются лишь первые шаги, к кото рым, в частности, относится работа проф. Г. И. .*Грановского
Анализ указанной работы показывает, что:
а) из двух основных функций режущего инструмента — формо образования и снятия припуска — в ней рассматривается главным образом лишь первая функция;
б) главной задачей кинематики резания считаются анализ и классификации принципиальных кинематических схем резания
иочертаний внешнего контура обрабатываемых изделий.
Впринципиальные кинематические схемы резания входят абсо
лютные движения, сообщаемые в процессе резания инструменту
иобрабатываемому изделию механизмом станка.
*Г. И. Грановский. Кинематика резания, Машгиз, 1946.
3
Движения холостых циклов, в течение которых инструмент
и обрабатываемое изделие не имеют контакта, принципиальными
кинематическими схемами не выражаются; в) классификация принципиальных кинематических схем реза
ния основана на количестве и относительном расположении так называемых элементарных движений. В качестве последних при няты прямолинейное и вращательное движения.
За последние годы в ЭНИМСе были проведены исследования (канд. техн, наук А. О. Этин, М. Б. Юхвидом и др.), которые бази ровались на основных положениях работы проф. Г. И. Грановского. Назначением исследований являлись разработка всевозможных
методов обработки основных поверхностей деталей машиностроения |
|
(тел вращения, плоскостей и винтовых поверхностей) и дача реко |
|
мендаций промышленности по выбору того или иного метода обра |
|
ботки, исходя из заданных параметров изделия и |
инструмента. |
В качестве критерия целесообразности применения того или иного |
|
метода обработки приняты следующие факторы: машинное время |
|
обработки, расход мощности, затрачиваемой на удаление единицы |
|
объема припуска, и расчетная величина отклонения |
изделия от |
требуемой формы.
В указанном направлении продолжаются работы и в настоящее время. Научная и практическая ценность этих работ, безусловно, большая: достаточно сказать, что если только принять во вни мание такую проблему, как обоснование типажа металлорежущих станков, то трудно что-либо сделать в этом направлении без опре деленных научно обоснованных данных, которые могут быть полу
чены в первую очередь в результате исследования кинематических закономерностей, имеющих место при осуществлении инструментом процесса резания.
Несмотря на определенные успехи, имеющиеся в настоящее время в области изучения кинематических закономерностей процес
са резания, следует признать, что проведено еще мало исследований, которые касались бы непосредственно теории конструирования ре жущего инструмента.
Учитывая сказанное, в настоящей работе поставлена задача:
на основе изучения кинематической стороны работы режущего ин
струмента обосновать и научно классифицировать все многообра зие имеющегося в настоящее время режущего инструмента; оценить
его преимущества и недостатки; получить данные о направлениях и перспективах дальнейшего развития режущего инструмента но вых видов.
Поставленная задача решается исходя из следующих основных методических положений:
1. Кинематика металлорежущего инструмента должна не только включать изучение тех кинематических закономерностей, которые имеют место непосредственно в процессе резания инструментом, но и рассматривать эти же закономерности с учетом всех движений, ко торые совершает инструмент в процессе обработки детали.
4
2. Рассматриваемые движения режущего инструмента отли чаются друг от друга не количеством и расположением элементар ных составляющих движений — прямолинейного и кругового, а целевым назначением: например, движение на глубину резания;
движение вдоль образующей или направляющей поверхности из делия; холостой ход перехода от обработки данной поверхности
изделия к обработке следующей поверхности того же изделия
ит. д.
3.Из движений целевого назначения образуются циклы движе ний инструмента. Под циклом движений инструмента понимается
совокупность целевых движений, обеспечивающих выполнение той
или иной части технологического процесса механической обработ ки (рез, ход, проход, переход и т. д.).
4.В качестве оценки производительности работы инструмента принимаются лишь кинематические показател, т. е. L — протяжен ность движений цикла обработки; v— скорость движений цикла обработки; t — продолжительность цикла обработки.
5.Для повышения производительности работы металлорежу щего инструмента необходимы: а) сокращение протяженности дви жений цикла; б) совмещение движений цикла; в) устранение не которых движений цикла обработки; г) рациональный выбор фор мы траектории движений цикла обработки, обеспечивающей воз
можность увеличения скорости движений.
6.Для определения полного комплекта движений целевого наз начения рассматривается кинематика наиболее простого режущего инструмента — резца с «точечным» формообразованием — при осу
ществлении им формообразования и снятия припуска не только одной элементарной поверхности того или иного вида (плоскости, тела вращения, винтовой поверхности и т. д.), не только при обра
ботке детали как сочетания нескольких элементарных поверхнэс тей, но и при обработке партии или потока деталей.
7.В качестве основных средств повышения производительности обработки металлорежущих инструментов в направлениях, указан ных в п. 5, принимаются: а) замена кинематических движений цик
ла |
обработки |
так называемыми конструктивными * движениями; |
|
б) |
рациональное совмещение оставшихся кинематических движе |
||
ний с конструктивными движениями; |
в) применение рациональных |
||
схем резания. |
|
|
|
|
Исходя из |
поставленной цели и |
принятого метода решения |
задач, возникающих при достижении этой цели, автор проделал определенную работу по изучению кинематики формообразования и схем резания и их связи с кинематикой инструмента.
Ниже кратко изложены лишь результаты проведенной работы, связанные с обоснованием классификации режущего инструмента
Определение термина «конструктивные движения» будет дано ниже.
5
I. КИНЕМАТИКА РЕЖУЩЕГО ИНСТРУМЕНТА, НЕ ИМЕЮЩЕГО КОНСТРУКТИВНЫХ ДВИЖЕНИЙ
Ставя перед собой задачу изучить кинематику формообразова ния, а следовательно, затраты времени на осуществление целевых движений инструмента в процессе обработки детали с тем, чтобы найти пути сокращения этого времени (т. е. повышения производи
тельности работы инструмента), нельзя ограничиваться рассмотре нием кинематических закономерностей, имеющих место лишь в мо мент резания. Иначе юворя, нельзя принимать во внимание лишь рабочие движения, которые осуществляются режущим инструментом непосредственно в тот момент, когда снимается припуск и осущест вляется процесс формообразования поверхности изделия. Необхолимо рассматривать весь комплекс движений, осуществляемых инстру ментом^ Устанавливая указанный комплекс движений, нужно исхо дить из рассмотрения всего производственного цикла обработки из делия, который тесно связан с осуществлением относительных дви жений инструмента (рабочих и холостых). Зная полную картину этих движений и стремясь, во-первых, осуществить непрерывный
процесс обработки (т. е. максимально устранить холостые движения в цикле обработки изделия) и, во-вторых, интенсифицировать сам процесс осуществления рабочих движений за счет мероприятий, указанных в п. 5 «Исходных положений», можно изыскать пути
повышения производительности с точки зрения кинематики работы инструмента. Именно здесь и находится, по нашему мнению, ключ к пониманию как существующего разнообразия режущего инстру
мента, так и путей его развития.
Исходя из этих позиций, рассмотрим продолжительность всего
производственного цикла обработки детали (рис. 1), выбирая те временные затраты, которые определяются лишь кинематикой ре жущего инструмента.
В общем случае составляющая длительности производственного цикла обработки изделия, определяемая временными затратами на
осуществление относительных |
движений |
режущего инструмента, |
|
может быть выражена формулой: |
|
||
|
п |
т |
р |
7 при |
S |
S |
К = 1 |
|
I = 1 |
j = 1 |
где: Т'—часть продолжительности производственного цикла об
работки изделия, определяемая временными затратами на осуществление относительных движений режущего инструмента;
toi |
— продолжительность |
обработки |
z-ой поверхности изде |
t |
лия (так называемое основное |
время); |
|
— продолжительность |
холостого |
перехода от обработки |
|
|
одной поверхности к обработке другой поверхности |
||
t.,K |
данного изделия; |
холостого |
перехода от обработки |
— продолжительность |
|||
|
данного изделия к |
обработке |
последующего изделия. |
е
Таким образом, необходимо последовательно рассмотреть про должительность движений инструмента: а) при обработке элемен тарной поверхности; б) при обработке изделия как сочетания эле ментарных поверхностей и в) при обработке партии или потока изделий.
Рис. 1. Продолжительность производственного цикла обработки детали (схема)
Цикл кинематических движений инструмента, не имеющего конструктивных движений (при обработке элементарной поверхности)
Рассматривая основную функцию металлорежущего инструмен та— формообразование поверхности обрабатываемого изделия,— нельзя анализировать кинематическую сторону этого процесса в отрыве от вида поверхностей деталей машиностроения.
Несмотря на большое многообразие поверхностей деталей маши ностроения, которые образуются в результате обработки их на металлорежущих станках, все они могут быть классифицированы (как и поверхности, которые не используются в настоящее время,
но |
могут быть |
использованы в дальнейшем) в зависимости |
от |
вида |
образующих |
и направляющих этих поверхностей (рис. |
2). |
Необходимость в классификации обрабатываемых поверхностей по виду их образующих и направляющих вызывается тем, что вся кий режущий инструмент, выполняя функцию формообразования, должен воспроизводить своими режущими кромками образующую поверхности изделия и перемещать ее вдоль соответствующей на правляющей этой поверхности.
7
Рис. 2. Классификация основных (элементарных) поверхностей изделий машиностроения
Из данной классификации следует, что поверхности, относящие ся к классу сложнофасонных поверхностей, у которых нет постоян ной (по форме и размерам) образующей, могут быть обработаны лишь режущим инструментом, работающим с «точечным» профи лированием. В отличие от таких поверхностей, поверхности пере коса ,* у которых имеется постоянная образующая, могут быть обработаны инструментом, работающим как с «точечным» (непол нолинейчатым), так и с линейчатым профилированием.
Всвязи с тем, что практически наиболее часто применяются по верхности переноса и что существующие разновидности инструмен та вызваны именно необходимостью получения этих поверхностей, изложенный ниже материал по кинематике инструмента и по схе мам резания будет распространяться в основном на этот класс по
верхностей.
Врезультате анализа циклов движений наиболее простого ре жущего инструмента с «точечным» профилированием — резца — установлено, что в общем случае цикл обработки любой поверхно сти детали состоит из циклов резов, ходов, проходов и переходов.
Под такой терминологией понимается:
рез —• часть хода инструмента, выполняемая при одном оборо те инструмента фрезерного типа;
ход — часть прохода инструмента, при котором полностью вос производится направляющая поверхности изделия, но не воспроиз водится вся образующая, т. е. процесс формообразования заданной
поверхности изделия полностью не закончен и одновременно не
всегда снят весь припуск по толщине;
проход — часть перехода, при котором полностью воспроизво
дится как образующая, так и направляющая поверхности изделия,
но не всегда удаляется весь припуск с поверхности заготовки по толщине;
переход — часть операции, при которой обрабатывается одна или несколько поверхностей данным инструментом, при этом пол ностью воспроизводятся как образующие, так и направляющие этих поверхностей (поверхности) и удаляется весь припуск.
На основании анализа указанных циклов можно прийти к выво
ду, что цикл обработки одной поверхности изделия при примене нии резца с «точечным» формообразованием состоит из следующих девяти движений целевого назначения: а) движения врезания на заданную глубину резания — /; б) рабочего движения реза (кру
говое движение) инструмента фрезерного |
типа — 2; в) |
движения |
|
подачи вдоль направляющей поверхности |
изделия — 3; |
г) |
движе |
ния выхода из резания-—4; д) холостого |
хода хода — 5; |
е) дви |
|
жения подачи вдоль образующей поверхности изделия—6; |
ж) хо |
лостого хода прохода—7; з) движения резания — 8. Это движение совпадает с движением 3 или представляет сочетание нескольких рабочих движений инструмента (в общем случае — движений 1. 2,
*Здесь под поверхностями переноса, в отличие от толкования этого термина
вматематике, понимаются поверхности, полученные перемещением в простран стве постоянной образующей вдоль соответствующей направляющей.
9
3 и б); и) холостого хода реза |
(круговое движение) инструмента |
фрезерного типа — 9. |
(учитывая, что движение 8 обяза |
Указанные восемь движений |
|
тельно совпадает с одним из |
перечисленных движений) впол |
не объяснимы, а именно: при работе «точечным» однорезцовым ин
струментом необходимо осуществлять два движения формообра
зования— движение вдоль образующей и движение вдоль направ ляющей поверхности изделия. Для снятия припуска необходимо еще одно движение — врезание на заданную глубину резания. Та ким образом, инструмент токарного типа должен иметь три раоочих движения целевого назначения (движения 1, 3 и 6). Однако при работе инструментом фрезерного типа необходимо иметь до полнительное— четвертое, рабочее движение—круговое движе ние резания (движение 2), не совпадающее с направлением движе ния вдоль направляющей поверхности изделия.
В силу прерывистости процесса формообразования и снятия припуска возникают холостые хода, количество которых соответ ствует количеству рабочих ходов, а именно:
а) движение 4 выхода из резания вызвано прерывистостью на правляющей или образующей поверхности изделия, в результате чего прерывается процесс резания, а инструмент выходит из зоны резания;
б) холостой ход 5 возникает в результате незамкнутости направляющей поверхности изделия, а это приводит к тому, что движение подачи вдоль направляющей поверхности изделия (дви жение 3) прекращается и для его повторного осуществления необ ходимо иметь в цикле хода указанное холостое движение, обычно являющееся движением, обратным движению 3;
в) холостой ход прохода 7 возникает в результате незамкнутос
ти образующей поверхности изделия, что приводит к прекращению движения вдоль образующей (движение 6), и для его повторного осуществления необходимо иметь в цикле прохода указанное хо лостое движение;
г) холостой ход реза 9 обусловлен спецификой работы инстру мента фрезерного типа. Он возникает в результате несовпадения движения резания 2 (кругового) с движением вдоль направляю щей поверхности изделия. Для осуществления повторного реза в цикле хода реза необходимо указанное холостое движение.
Цикл кинематических движений инструмента, не имеющего конструктивных движений (при обработке детали, партии или потока деталей)
Чтобы иметь полный набор кинематических движений целевого назначения, определяющий продолжительность производственного процесса обработки изделия, необходимо дополнительно к указан ным движениям добавить еще два холостых движения, а именно:
а) холостой ход перехода от обработки данной поверхности к об работке последующей поверхности одного и того же изделия (дви
жение 10);
10