
книги из ГПНТБ / Смирнов, В. И. Строительные машины учебник
.pdfсколько раз изменяется число оборотов (крутящий момент) при передаче вращения через редуктор. Общее передаточное число редуктора определяется как произведение передаточных чисел всех ступеней:
гР — г1• h ' гз • • • 1ц-
Одноступенчатые цилиндрические редукторы (рис. 2-8, а) вы пускаются с передаточным числом до 12,5. Больше распространены двухступенчатые редукторы (рис. 2-8, в, д), имеющие передаточное число в пределах 12,5—63,0. Для получения передаточного числа более 63 применяются трехступенчатые редукторы.
Конические редукторы (рис. 2-8,6) имеют передаточное число до 6,3 и применяются при необходимости изменить направление передаваемого вращения на 90°. Для получения большого пере даточного числа используютря ' коническо-цилиндрические редук торы (рис. 2-8,г).
В особую группу входят п л а н е т а р н ы е р е д у к т о р ы , у ко торых часть зубчатых колес имеет вращающиеся геометрические оси. На рис. 2-8, е представлена схема одноступенчатого планетар ного редуктора, в котором ведущим звеном служит центральная (солнечная) шестерня 1, а ведомым — водило 4. На осях, закреп ленных в водиле, установлены промежуточные шестерни (сателли ты) 2, которые одновременно зацепляются с центральной 1 и на ружной (эпициклической) 3 шестернями.
Эпициклическая шестерня установлена неподвижно. При вра щении солнечной шестерни сателлиты получают от нее вращение и начинают обегать по эпициклической шестерне вокруг централь ной оси, увлекая за собой водило.
Передаточное число рассмотренного планетарного редуктора находится в пределах 1,3—8,0 и определяется по формуле
где гъ и Z\ — число зубьев эпициклической и солнечной шестерен.
По конструкции планетарные редукторы весьма разнообразны. В некоторых из них ведущим элементом является водило, а ведо мым — солнечная шестерня.
В планетарных редукторах нагрузки от ведущего элемента воспринимаются одновременно несколькими сателлитами, обычно в количестве 3—6 штук. Вследствие этого их зубчатые колеса изго товляются меньших размеров по сравнению с обычными редук торами.
Основным достоинством планетарных редукторов является воз можность получения большого передаточного числа при неболь ших габаритах. К недостаткам данного типа редукторов относятся необходимость в повышенной точности изготовления, сложность сборки и ремонта.
50
Планетарные редукторы находят широкое применение в меха низмах поворота современных гусеничных машин, в приводах лебедок некоторых башенных кранов, в качестве колесных редук
торов пневмоколесных тягачей |
и большегрузных |
автомобилей |
и т. д. |
используемые на |
строительных |
Ч е р в я ч н ы е р е д у к т о р ы , |
машинах, в большинстве своем одноступенчатые с передаточным числом, равным 15—60. Для получения большого передаточного числа применяются комбинированные червячно-зубчатые редук торы.
Выбор типа редуктора определяется требованиями компоновки и особенностями конструкции машины. Обеспечивая необходимое изменение числа оборотов и крутящего момента, выбранный ре дуктор должен отвечать величине передаваемой мощности.
Глава 3
ОСИ, ВАЛЫ, ПОДШИПНИКИ, ПРУЖИНЫ И МУФТЫ
§ 3-1. Оси и валы
Оси, представляющие собой прямые стержни (рис. 3-1, а, б), служат для поддержания вращающихся вместе с ними пли на них различных деталей и работают на изгиб (ось блока грузоподъем ной машины, ось опорного катка гусеничного трактора и т. и.).
Валы в отличие от осей предназначены в основном для пере дачи крутящих моментов. Кроме крутящего момента вал в боль шинстве случаев нагружается изгибающим моментом, а иногда и осевой силой.
В зависимости от геометрической формы валы бывают прямые, коленчатые и гибкие (рис. 3-1, в, г, д, е). Наибольшее распростра нение получили прямые валы. Коленчатые валы используются в механизмах, преобразующих возвратно-поступательное движение во вращательное (двигатели внутреннего сгорания) или наоборот (поршневые насосы, лесорамы и т. д.). Гибкие валы представляют собой многозаходные витые из проволок пружины кручения. Они применякггся для передачи вращения между узлами машин, меняющими при работе свое положение относительно друг друга (механизированный инструмент, глубинные вибраторы, привод спидометра автомобиля и т. п.).
Оси и валы имеют круглое сплошное или кольцевое поперечное сечение. Полые оси и валы позволяют уменьшить вес конструкции, а также пропустить через них другие детали.
Оси небольшой длины изготовляются одинакового диаметра по всей длине (рис. 3-1, а), а длинные и тяжело нагруженные делают ся фасонными (рис. 3-1,6).
4* |
51 |
Прямые валы в зависимости от назначения выполняются либо постоянного по всей длине диаметра (трансмиссионные валы,
рис. 3-1,в), либо ступенчатыми (рис. 3-1,г), получившими преиму
щественное применение. Вторая форма более удобна |
для |
уста |
||||||||||||||
новки деталей на валу. Участки |
валов и осей, которыми они опи |
|||||||||||||||
|
|
а) |
|
|
|
|
|
раются на подшипники, при вос |
||||||||
|
|
|
|
|
|
|
приятии |
радиальных |
нагрузок |
|||||||
|
|
|
|
|
|
|
|
называются |
ц а п ф а м и , |
|
при |
|||||
|
|
S) |
|
|
|
|
|
восприятии |
осевых |
нагрузок — |
||||||
|
Г-Н •• |
1 -- |
М |
-1--1Q |
п я т а м и. |
Концевые цапфы |
но |
|||||||||
|
|
ч |
|
|
|
|
|
сят название шипо в , |
а цапфы, |
|||||||
|
|
|
|
|
|
|
расположенные в средней |
части |
||||||||
|
Д |
<=> |
~tt |
- |
<=> |
ii- |
О К |
|||||||||
|
осей и валов, — шеек . Для |
вос |
||||||||||||||
|
|
|
|
|
|
|
|
|||||||||
|
|
|
|
|
|
|
|
приятия |
осевых |
нагрузок |
|
на |
||||
|
|
|
|
|
|
|
|
валах |
выполняются |
буртики, |
||||||
|
|
|
|
|
|
|
|
или диаметр цапф делается не |
||||||||
|
|
|
|
|
|
|
|
сколько |
меньшего |
размера |
|
по |
||||
|
|
|
|
|
|
|
|
сравнению с соседними участ |
||||||||
|
|
|
|
|
|
|
|
ками. Для |
уменьшения |
концен |
||||||
|
|
|
|
|
|
|
|
трации |
напряжения |
переходы |
от |
|||||
|
|
|
|
|
|
|
|
одного сечения оси или вала к |
||||||||
|
|
|
|
|
|
|
|
другому |
делаются |
плавными |
и |
|||||
|
|
|
|
|
|
|
|
называются |
г а л т е л я м и . |
|
|
|
||||
|
|
|
|
|
|
|
|
Коленчатые валы |
сложнее |
по |
||||||
|
|
|
|
|
|
|
|
конструкции. Они имеют корен |
||||||||
|
|
|
|
|
|
|
|
ные и шатунные шейки, соеди |
||||||||
|
|
|
|
|
|
|
|
ненные |
между |
собой |
щеками. |
|||||
|
|
|
|
|
|
|
|
В большинстве случаев на щеках |
||||||||
|
|
Рис. 3-1. |
Ос» и валы: |
|
с противоположной |
стороны |
|
от |
||||||||
а, |
б |
— оси; |
в, |
г — прямые |
валы; |
шатунных шеек делаются |
проти |
|||||||||
д |
— коленчатый |
вал; е — гибкий вал |
вовесы, |
уменьшающие |
нагрузки |
|||||||||||
|
|
|
|
|
|
|
|
на коренные подшипники от цен |
тробежных сил. От коренных шеек к шатунным просверливаются масляные каналы. На переднем конце коленвала ДВС, называе мого носком, крепятся детали привода других механизмов дви гателя (газораспределительная шестерня, шкив привода венти лятора), а на заднем конце выполняется фланец для крепления маховика.
Крепление деталей на осях и валах производится |
в основном |
с помощью шпонок и шлиц. Для устранения осевого |
смещения |
этих деталей используются буртики, распорные втулки, установоч ные кольца и т. п.
В качестве материала для осей и валов применяются главным образом углеродистые и легированные конструкционные стали. Тяжело нагруженные валы сложной формы, например коленча тые валы двигателей, куются также из модифицированного высоко прочного чугуна.
52
Основы расчета осей и валов
В зависимости от условий работы оси и валы рассчитываются на прочность, жесткость и на колебание (критическую скорость). Из-за опасности усталостного разрушения для осей и валов быстроходных машин ведется расчет на выносливость.
Расчет осей и валов на прочность, жесткость и выносливость рассматривается в курсе «Сопротивление материалов».
Необходимость в расчете на колебания вызвана тем, что отдельные быстроходные оси и валы при определенной угловой скорости становятся динамически неустойчивыми. Наступающий резонанс собственных и вынужденных колебаний вызывает резкое возрастание амплитуды этих колебаний и может привести к раз рушению оси или вала. Скорость вала (оси), при которой число оборотов его п соответствует частоте собственных колебаний этого вала, называется критической скоростью.
Для большинства быстроходных осей и валов основными си лами вынужденных колебаний являются возмущающие силы от неуравновешенности установленных на них деталей. Расчет осей и валов на поперечные колебания заключается в определении их критической скорости и проверке отсутствия резонанса при уста новившемся режиме работы.
Значение критической скорости определяется из выражения
где G — вес закрепленной на осп (валу) |
детали, н; |
К — сила, вызывающая прогиб оси |
или вала, равный еди |
нице, н/см, |
|
,,48EJ
А=
Стем чтобы исключить явление резонанса, скорость вращения оси или вала при установившемся движении должна быть меньше
или больше критической скорости. О приближении скорости вра щения оси или вала к критической можно судить по появлению сильной вибрации. При продолжительной работе в области резо нанса неизбежно разрушение оси или вала. Для уменьшения опас ности резонанса повышается их жесткость и угловая скорость при нимается не свыше п = 0,7я!!р.
Важное значение для уменьшения или полного устранения вынужденных колебаний имеет уравновешивание (балансировка) осей и валов вместе с установленными на них деталями. Оно достигается путем съема с вращающейся детали части металла со стороны, куда смещен центр тяжести, а также путем наплав ления металла или крепления контргрузиков на данную деталь с противоположной стороны (например, на диски колес некоторых
53
современных автомобилей, маховики двигателей, длинные кардан ные валы и др.).
§3-2. Подшипники
'Подшипники служат опорами различных вращающихся дета лей и воспринимают нагрузки, действующие на эти детали. По ха рактеру трения рабочих элементов они делятся на подшипники скольжения и подшипники качения.
Подшипники скольжения
У подшипников скольжения (рис. 3-2) цапфа вала скользит по рабочей поверхности подшипника. Они в большинстве случаев состоят из корпуса и помещенных в нем вкладышей. Корпус обычно выполняется из чугуна, а вкладыш для уменьшения трения — из антифрикционных материалов (баббит, бронза и др.).
Различают неразъемные и разъемные подшипники скольжения. У первых (рис. 3-2, а, б) корпус / и вкладыш 2 цельные; вкладыш изготовляется в виде втулки, которая запрессовывается в корпус подшипника. У таких подшипников отсутствует возможность ком пенсации их износа путем сближения одной части подшипника с другой. Они применяются в основном в простейших механизмах при небольших нагрузках и скоростях.
Корпус разъемного подшипника (рис. 3-2, в) обычно состоит из основания I и крышки 4, прикрепляемой к основанию болтами или шпильками. Вкладышей в разъемном подшипнике чаще всего два. Соответственно их расположению они называются верхним 3 и нижним 2. Эти подшипники получили преимущественное распро странение, так как более удобны при монтаже осей и валов и до
пускают регулировку зазоров в |
подшипнике |
путем |
сближения |
крышки и основания. |
|
|
|
В случае большой деформации вала или невозможности осу |
|||
ществления его точного монтажа |
применяются |
с а м о у с т а н а в |
|
л и в а ю щ и е с я п о д ш и п н и к и |
с к о л ь ж е н и я |
(рис. 3-2, г), |
вкладыши которых выполняются со сферическими опорными по верхностями пли с опорными поверхностями в виде узкого колеса. Иногда используются подшипники с самоустанавливающимися сегментными вкладышами.
Бронзовые вкладыши рекомендуется использовать в подшип никах, воспринимающих ударные нагрузки, и при реверсивном вращении вала (оси). При малой окружной скорости вала при меняются вкладыши из антифрикционных чугунов, которые значи тельно дешевле бронзовых.
Вкладыши из баббитов и свинцовистых бронз выполняют в основном в виде стальной ленты, на внутренней поверхности ко торой наплавляется тонкий слой антифрикционного материала.
54
Такие вкладыши применя ются для валов с большой скоростью вращения.
В некоторых подшипни ках скольжения применяют ся вкладыши, изготовляе мые из порошков железа или бронзы с добавлением графита, а иногда и других примесей путем прессова ния под высоким давлением
ипоследующего спекания при высокой температуре. Благодаря большой пори стости материала вклады ши пропитываются маслом
имогут в течение про должительного времени ра ботать без подвода к ним смазки.
Из пластмассовых вкла дышей наиболее распро странены вкладыши из тек столита, древесно-слоистых
пластиков и капрона. |
По- |
|
|
|||
' следние обычно выполня |
|
|
||||
ются на металлической ос |
|
|
||||
нове и имеют, как показы |
|
|
||||
вает |
практика, |
большую |
|
|
||
износостойкость |
и малый |
Рис. |
3-2. Подшипники скольжения: |
|||
коэффициент трения. |
|
|||||
|
а, б — неразъемный; в — разъемный; г — |
|||||
Выбор материала |
вкла |
|||||
|
самоустанавливающийся |
|||||
дышей |
производится |
по |
|
|
удельному давлению р между цапфой и вкладышем:
и проверяется на нагрев, исключающий заедание сопряжения:
где Р — нагрузка на подшипник, н;
d — внутренний диаметр вкладыша, см; I — длина вкладыша, см;
v — окружная скорость цапфы, м/сек;
[р] — допускаемая удельная нагрузка, н/см2; [рц] — допускаемый скоростной коэффициент, нм/см2 • сек.
Значения [р] и \pv] приведены в табл. 3-1.
55
Т а б л ii ц а 3-1
Максимальные допускаемые значения [/;] и [ро\ для вкладышей подшипников скольжения
Материал вкладышей |
н\см2 |
нм1см2 -сек |
||
Свинцовистая |
бронза |
БрСЗО |
2500 |
2000—2500 |
. Оловянно-свинцовистая брон |
1200 |
600—800 |
||
за БрОС |
|
|
||
Оловянистый |
баббит |
Б92 |
2000 |
1500—10 000 |
Оловяннстый |
баббит |
Б16 |
1000 |
700—1000 |
Антифрикционный чугун |
200—400 |
300-400 |
||
СЧЦ-2 |
|
|
||
Железографит |
|
|
300—500 |
400—600 |
Текстолит 2Б |
|
|
1000—1500 (при |
смазке маслом) |
Работоспособность подшипников скольжения во многом зави сит от их своевременной и качественной смазки, которая умень шает трение и износ трущихся пар, отводит тепло, предохраняет детали от коррозии и обеспечивает уплотнение зазоров.
Рис. 3-3. Эпюра гидродинамического давления в мас ляном клипе и масленки:
а — масляный клин; б — прессмасленка; в — мага зинная; г — колпачковая
В зависимости от толщины масляного слоя подшипник рабо тает в режиме сухого, граничного, полужидкостного или жидкост ного трения. Сухое трение имеет место при отсутствии смазки между трущимися поверхностями и вызывает чрезмерный нагрев и износ деталей. При отсутствии постоянного и обильного под вода масла будет происходить граничное (с преобладанием сухого) или полужидкостное (с преобладанием жидкостного) трение.
56
Самым благоприятным режимом работы подшипника скольже ния является работа его при жидкостном трении, когда поверх ности подшипника и вала разделены слоем масла. Это достигается за счет использования гидродинамического избыточного давления в слое масла. Гидродинамическое давление создается в масляном клине, образующемся за счет того, что вращающийся вал увле кает за собой масло в зазор между ним и подшипником, (рис. 3-3,а).
Расчет на жидкостное трение основывается на том, что масля ный слой должен воспринимать всю нагрузку, а его толщина Лм должна быть больше суммы неровностей поверхностей цапфы R n и вкладыша R B:
R » ^ К \ |
(/? „ + Д в ), |
где К 1 — коэффициент запаса |
надежности жидкостного трения, |
принимаемый в зависимости от величины окружной скорости цапфы в пределах 3—8.
Толщина слоя смазки при жидкостном |
трении |
определяется |
|||
по формуле |
|
|
|
) |
|
d2/i4] |
мм, |
|
|
||
18,36(78с |
|
|
|
||
|
|
|
|
|
|
где т] — динамическая вязкость масла, н-сек2/м2; |
|
||||
п — число оборотов цапфы, об/мин\ |
|
|
|
|
|
d — диаметр цапфы, мм\ |
|
|
|
|
|
6 — зазор между подшипником и цапфой, мм\ |
|
||||
q — удельная нагрузка на цапфу, н/м2; |
|
d + 1\ |
|
||
с — приведенная длина подшипника |
I |
|
|
||
|
= —j— I . |
|
|||
Для смазки подшипников строительных |
машин |
используются |
в основном консистентные смазки и жидкие масла. Консистентные смазки (солидолы, консталины, графитные смазки и др.) исполь зуются в узлах с малым выделением тепла (тихоходные машины), трудногерметизируемых узлах, а также в трудно доступных дета лях. В остальных случаях применяются жидкие масла, которые равномерно распределяются по трущимся поверхностям, обладают малым внутренним трением и хорошо работают в значительных диапазонах температур. ,
Подача консистентных смазок к подшипникам скольжения осу ществляется колпачковыми масленками (рис. 3-3, г), солидолонагнетателями через пресс-масленки (рис. 3-3, б) и автоматически действующими магазинными масленками (рис. 3-3,в), из которых смазка подается поршнем, находящимся под давлением пружины. Равномерное распределение масла по подшипнику достигается за счет смазочных канавок на вкладыше.
Преимуществами подшипников скольжения являются простота конструкции, способность работать в условиях перегрузок н уда-
57
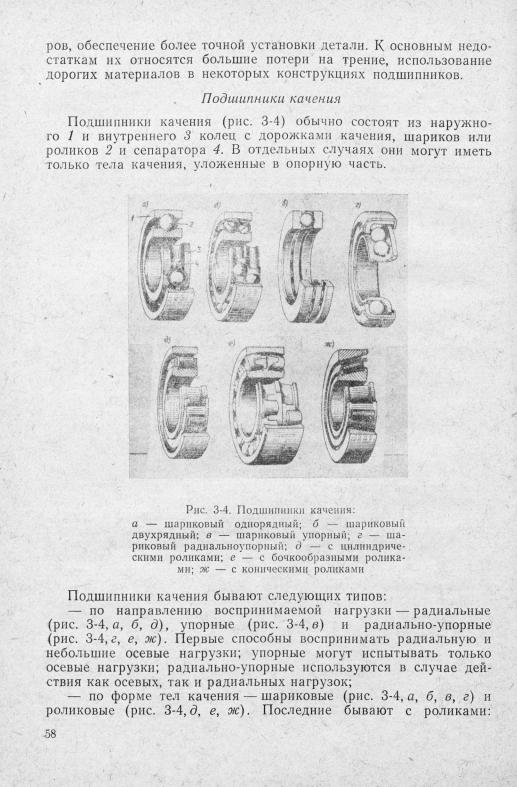
цилиндрическими короткими (рис. 3-4, д) и длинными, бочкообраз ными (рис. 3-4, е) и коническими (рис. 3-4,ж), а также с витыми
иигольчатыми;
—по числу рядов тел качения — одно- (рис. 3-4,а, в, г, д, ж),
двух- (рис. 3-4, б, е) и многорядные;
— по соотношению габаритных размеров — тяжелой, средней, средней широкой, легкой и других серий. При одинаковом внут реннем диаметре подшипники разных серий отличаются друг от друга шириной и наружным диаметром, а следовательно, и несу щей способностью.
Выбор типа подшипника зависит от назначения узла, где уста навливается подшипник; от величины, характера и направления действия нагрузки; от скорости вращения вала и температурного режима работы. При этом рекомендуется применять:
— шариковые радиальные подшипники — для быстроходных передач, воспринимающих небольшие и средние нагрузки и при наличии осевых нагрузок, не превышающих 20% от радиальной;
— роликовые цилиндрические подшипники — для узлов, вос
принимающих большую |
'радиальную и значительную осевую |
(до 70% от радиальной) |
нагрузки; |
—упорные подшипники — только для восприятия осевых на грузок при сравнительно малых оборотах вала;
—игольчатые подшипники — в узлах, работающих в условиях ударных нагрузок и воспринимающих значительные радиальные
нагрузки.
Выбор подшипника производится по размеру вала и коэффи циенту работоспособности С:
C = ± Q (n h )°':\
где Q — условная нагрузка на подшипник, я;
п — угловая скорость вращающегося кольца подшип ника, об/мин;
h — требуемый срок службы подшипника, ч.
Условная нагрузка Q определяется по следующим формулам:
— для радиальных подшипников, кроме подшипников с ци линдрическими роликами
Q^ i K b R - r - m A ) ^ ;
—для радиальных подшипников с цилиндрическими роликами
Q == ЯКкКлКт;
— для упорных подшипников
Q = АКЛК„
где R — радиальная нагрузка на подшипник, я; А — осевая нагрузка на подшипник, я;
59