
книги из ГПНТБ / Игнатов, А. А. Кривошипные горячештамповочные прессы
.pdfРис. 154. Горизонтальный транспортер,, применяемый на ■АЗЛК
... 253.
простой способ механизации состоит в том, что заготовки, нагретые в индукторе, автоматически толкателем подаются по склизу к прессу. После их штамповки на прессе поковки то же по склизу подаются к обрезчику. Далее обрезанная поковка по конвейеру попадает в специальный ящик, а обрезанный заусенец склады вается обрезчиком в другой ящик.
В настоящее время в кузнечных цехах заводов для перемеще ния заготовок и поковок применяются специальные транспортеры: цепной (рис. 153) и горизонтальный пластинчатый (рис. 154). Размеры транспортеров определяются по месту установки, воз можностью их установки к прессам и нагревательным устройствам. Эти транспортеры работают хорошо и находят широкое приме нение в кузнечных цехах.
СРЕДСТВА АВТОМАТИЗАЦИИ ПРЕССОВ
Одним из важнейших этапов автоматизации процесса штам повки поковок в прессах следует считать автоматизацию переноса заготовок из ручья в ручей, их съем и уборку со штампов.
При разработке процессов автоматизации штамповки на прес сах следует учитывать следующие факторы: число поковок в пар тии, изготовляемых на прессе без переналадки на другую деталь; продолжительность выталкивания поковки и возможное застре вание ее в ручьях штампа; продолжительность работы инстру мента и выход его из строя по различным причинам (нагрев штам пов при неудовлетворительном охлаждении, образование разгарных трещин и т. д.).
До сих пор еще мало внедрено в производство средств автома тизации процесса штамповки поковок на кривошипных горяче штамповочных прессах из-за их сложности и недостаточной на дежности работы, хотя имеются на этот счет предложения зару бежных фирм (Нейшенел, Крайзер-Нейшенел, Эймуко, Шмерал и др.), а также отечественных заводов и научно-исследователь ских учреждений (ЗТМП, ЭНИКМАШ и др.).
На рис. 155 показана |
схема автоматизированной установки |
с использованием пресса |
(Рн = 5000 тс), предложенная фирмой |
Коматцу для штамповки поковок массой до 50 кг. В этой схеме,
кроме КГШП |
(Рн — 5000 |
тс), |
показаны |
два |
автоматических |
манипулятора, |
обрезной пресс |
(Рн = 500 |
тс), |
индукционные |
|
нагревательные |
устройства, |
ковочные вальцы. |
|
• Существуют следующие приводы механизмов переноса поковок на прессах: механический —■от привода пресса или отдельного приводного устройства; пневматический — за счет воздуха, подаваемого из цеховой сети.
На рис. 156 автоматическое устройство вписано в штамповое пространство пресса. Нагретая заготовка по трубе А питателя поступает от нагревателя, захватывается грейферным устрой ством, передается по позициям штамповки, затем по склизу Б поступает в тару.
254
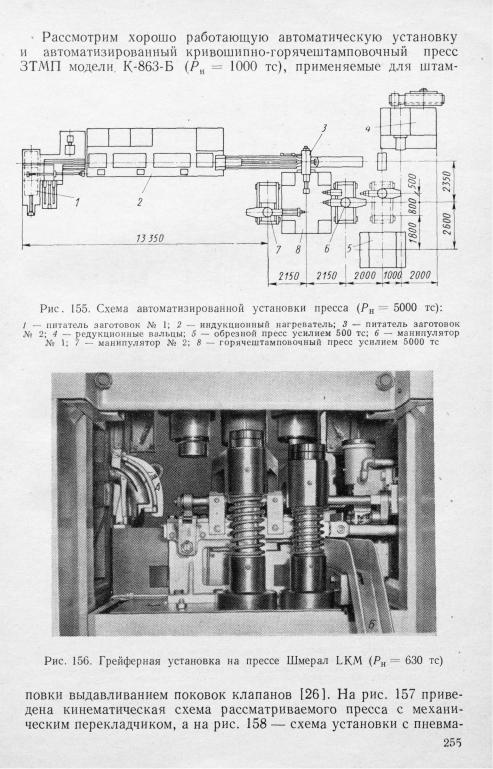
(1расч=Ш,1г=3,0?
7
Рис. 157. Схема автоматизированного пресса К-863-Б для штамповки клапанов методом выдавливания:
1 — |
электродвигатель |
АК 104-8; |
п — 1250 |
об/мин; |
N = 125 кВт; 2 — |
ползун; 3 — ша |
тун; |
4 — кулачковые |
устройства; |
5 , 6 , 8 |
— рейки; |
7 — фрикционные |
предохранитель |
ные |
муфты; 9 — пневматический |
цилиндр; |
10 — рычаг; 11 и 14 — ролики; 12 — вытал |
|||
|
киватель; |
13 — стол; |
15 — копир; 16 — пневматический демпфер |
гнатовИ
С Л
тическим перекладчиком. В первой матрице выдавливается стер жень, во второй оформляется тарелка клапана (рис. 158). Переме щение заготовок из первой матрицы во вторую и удаление поковки из второй матрицы в лоток производится одноклещевым перегру зочным манипулятором, который смонтирован в окне правой стойки станины пресса. Заготовки нагреваются в высокочастот ном индукторе.
Автоматическое устройство состоит из бункерно-загрузочного механизма 1 индуктора; механизма загрузки 2 первой матрицы со смазывающим устройством; нижнего пневматического двух штангового выталкивателя 3\ клещевого манипулятора 4 грей ферного типа с параллельным зажимом двух штамповок одно временно; срабатывающего устройства; шкафа электроуправле ния. Автоматическая установка (см. рис. 157, 158) спроектирована по принципу управления всеми движениями механизмов уста новки и прессом, осуществляемому электропневматическими сред ствами. Предусмотрена полная блокировка всех движений меха низмов.
Процесс автоматической штамповки клапанов осуществляется следующим образом: заготовка загружается в бункер, в нижней части которого находится гильза (сменная) с лопастью, получаю щая вращение от электродвигателя через червячный редуктор. Вращающаяся гильза своей лопастью приводит в движение заго товки, которые поочередно попадают в отверстие гильзы и тем самым ориентируются в вертикальном положении. Из отверстия гильзы заготовки попадают поштучно в гнездо поворотного бара банчика. При ходе толкателя барабанчик поворачивается на 90°, и находящаяся в нем заготовка проталкивается в индуктор, а край няя, уже нагретая заготовка попадает на лоток (склиз), соединяю щий индуктор с гнездом ползушки загрузчика первой матрицы.
В конце хода толкателя подается команда на рабочий ход ползуна пресса и одновременно включается реле времени продол жительности цикла. Ползун, возвращаясь в верхнее положение, дает команду на работу нижнего выталкивателя, который при движении вверх дает команду на ход клещей вперед. В переднем положении клещам подается команда поочередно на сжатие, подъем по копиру, движение назад, опускание и разжим. Этим движением штампованная заготовка из первой матрицы перекла дывается во вторую и отштампованный клапан из второй ма трицы — в механизм сборса.
При движении клещей назад подается команда на ход нижнего выталкивателя вниз и одновременно на ход загрузчика вперед. Загрузчик с нагретой заготовкой в гнезде ползушки выходит вперед и включает на своем пути клапан дозатора маслографитной смазки. Происходит вспрыскивание смазки в матрицу первой операции и загрузка ее нагретой заготовкой. Выйдя в переднее положение, загрузчик дает себе команду на движение назад и уходит в крайнее заднее положение. Цикл штамповки закончен.
258
Следующий цикл начнется при срабатывании реле времени, которое дает команду на движение толкателя вперед. В дальней шем цикл повторяется в том же порядке.
Техническая характеристика пресса модели К-863-Б
Усилие пресса в конце хода ползуна, т с ............... |
1000 |
|
Величина хода ползуна, м м ............................................. |
250 |
|
Число двойных ходов ползуна в минуту . . . . |
60 |
|
Мощность главного электродвигателя, кВт . . . |
55 |
|
Общая продолжительность цикла штамповки кла |
4,3 |
|
панов, |
с ............................................................................. |
|
Часовая |
производительность, шт...................................... |
840 |
Частота тока нагревателя, Гц ............................... |
10 000 |
|
Рабочее давление воздуха, кгс/см- ............................... |
4 |
|
Масса пресса с установкой, т .......................................... |
55 |
|
Габаритные размеры, м м ............................................ |
5500X300X5500 |
Автоматизация процесса предусматривает штамповку клапа нов автомобильных и тракторных двигателей различных типов; может быть использована для штамповки клапанов других дви гателей, имеющих подобную форму. Автоматизированный пресс модели К-863-Б внедрен в производство на Куйбышевском заводе «Автотрактородеталь».
Расположение оборудования в механизированных линиях с установкой кривошипных горячештамповочных прессов по реко мендациям завода Шмерал приведено на рис. 159. Первый вариант компоновки оборудования в линии (рис. 159, а) состоит из нагре вательного устройства (индуктора) 1, кривошипного горяче штамповочного пресса 3 и обрезного пресса 5. Для подачи нагре тых заготовок от индуктора 1 к прессу 3 установлен транспор тер 2. Отштампованная деталь сбрасывается штамповщиком на склиз 4 и поступает по нему на второй транспортер 2, далее на второй склиз 4 к обрезному прессу 5. Обрезанная заготовка по третьему склизу 4 подается в тару 6. Кроме индуктора 1 могут быть использованы ковочные вальцы 7. Эта компоновка названа параллельной.
Второй вариант — параллельно-ступенчатая линия — при веден на рис. 159, б. Здесь от индуктора 1, установленного на по вышенном по отношению к прессу фундаменте, нагретая заго товка подается по склизу 4 к кривошипному горячештамповоч ному прессу 3, от которого по второму склизу 4 поступает к обрез ному прессу 5; далее от него по третьему склизу 4 — в тару 6. Кривошипный горячештамповочный пресс 3 по отношению к обрез ному прессу также установлен на более высоком фундаменте.
В третьем варианте — прямоугольной компоновке (рис. 159, в)— имеются два нагревательных устройства (индуктора) 1, соединен ных поперечным склизом 4, от которого нагретые заготовки посту пают по транспортеру 2 к склизу 4. Отштампованная заготовка, поступающая на второй склиз 4, попадает на второй транспортер 2, от него на склиз 4 и к прессу 5. Обрезанная заготовка поступает в тару.
17* |
2 5 9 |
Рис. 159. Схема расположения оборудования в автоматизированной линии для штамповки деталей:
а — I вариант; б |
II вариант; в — III вариант; 1 — индуктор; 2 — транспортер; 3 — горячештамповочный пресс; 4 — склиз; 5 — об |
|
резной пресс; 6 — тара; 7 — ковочные вальцы |
Г Л А В А |
I X |
ОБЩИЕ ЗАМЕЧАНИЯ |
ПО ОРГАНИЗАЦИИ |
ОБСЛУЖИВАНИЯ И РЕМОНТА ПРЕССОВ
Кривошипные горячештамповочные прессы, как показал опыт их эксплуатации, относятся к числу наиболее трудоемких машин по их обслуживанию и ремонту. Они требуют более высокой куль туры обслуживания и ремонта в сравнении с обычными типовыми машинами, установленными в кузнечных цехах: молотами, обрез ными прессами и горизонтально-ковочными машинами. Тяжелые условия работы прессов вызываются возможной их перегрузкой по усилию на ползуне и перегрузкой электродвигателя; высокими удельными усилиями в сопрягающихся деталях, например в шли цевых ступицах, зубчатых парах, бронзовых опорах и др. Кроме - того, следует учитывать, что прессы работают в абразивной среде, создающейся сдуваемой окалиной при штамповке деталей и нахо дящейся около пресса во взвешенном состоянии.
При перегрузках пресса по усилию на ползуне или плохой работе муфты возникает заклинивание (стопорение) шатунно кривошипного механизма пресса с перенапряжением его отдельных деталей, появлением трещин и поломок. При высоких удельных усилиях в сопрягающихся деталях главного вала с опорами, шатуном и др. наблюдаются их быстрый износ, раскалывание (раздавливание), задиры и т. п. По причине высоких удельных
усилий в сопрягающихся, но |
не |
трущихся |
деталях, |
например |
в соединении ступицы муфты |
или |
тормоза |
с главным |
валом и |
с дисками; ступицы маховика или малой шестерни с приемным валом и т. п., при неудовлетворительной их посадке друг с другом или малых опорных поверхностях наблюдается быстрое разру шение сопрягающихся поверхностей. В этом случае ремонтники прибегают к посадкам деталей с подогревом, что затрудняет их последующий демонтаж.
Вопросам правильной и точной подгонки сопрягающихся дета лей не уделяется достаточного внимания, и часто у ремонтников для этих операций нет нужного оборудования. Абразивная среда, в которой работают трущиеся детали прессов, заставляет закры вать их для предотвращения попадания в смазку окалины, но
261
кожухи не защищают эти детали, например, трущиеся зуочатые пары и др.
Таким образом, при слабой организации ремонта прессов, неудовлетворительном ежедневном контроле за их работой про исходит быстрый износ основных деталей: опор трения главного вала и шатуна в ползуне, деталей муфты, тормоза, зубчатой пары, деталей механизма управления и др. Следовательно, увеличатся
эксплуатационные расходы цеха на ремонт и обслужи вание прессов.
При конструировании необходимо изучать усло вия работы прессов и их деталей, а при изготовле нии прессов —■не допу скать применения техноло- I ни, которая не обеспечи вает получения точных
|
|
|
|
|
|
размеров |
по чертежам. |
||||
|
|
|
|
|
|
Наладка |
прессов |
при |
|||
|
|
|
|
|
|
установке |
штампов |
для |
|||
|
|
|
|
|
|
штамповки поковок на них |
|||||
|
|
|
|
|
|
без контроля |
нагружения |
||||
|
|
|
|
|
|
ползунов по усилию и энер |
|||||
|
|
|
|
|
|
гетическим затратам |
прес |
||||
|
|
|
|
|
|
сов, |
штамповка |
поковок |
|||
|
- площадка обслуживания тормоза (см. |
рис. 161); |
без контроля |
температур |
|||||||
1 |
ного режима нагрева |
заго |
|||||||||
2 |
— |
площадка обслуживания |
муфты |
(см. рис. |
|||||||
162); |
3 — площадка |
обслуживания деталей,рас |
товок, |
штамповка охлаж |
|||||||
положенных наверху |
пресса, |
и главным |
образом |
денных заготовок, |
особен |
||||||
|
|
электродвигателя пресса |
(см. рис. |
163) |
но на прессах, работающих близко к пределу максимальной их нагрузки, приведут к быстрому износу и поломкам основных деталей прессов. Таким образом, одной из важнейших задач, способствующих увеличению эксплуатацион ной надежности прессов, снижению расходов на их ремонт и об служивание, следует признать в первую очередь задачу создания надежно работающих приборов контроля технологического уси лия на ползуне и энергетических затрат прессов, а затем приборов предохранения прессов от перегрузок.
Опыт эксплуатации прессов, изготовленных с применением материалов низкого качества, ложное понимание экономии при постановке на прессы не соответствующих, но недорогих заме нителей, показывает увеличение расходов на их ремонт и обслу живание, Так, например, при применении для изготовления глав ных валов стали 45 вместо высоколегированной снижается срок службы главного вала в 5 раз и более.
Повышению качества и надежности работы прессов мешает односторонняя оценка металлоемкости конструкции только по
262