
книги из ГПНТБ / Мовчин, В. Н. Технология производства измерительных инструментов и приборов учебник
.pdfс правым свинчиванием ролики имеют левую многозаходную резьбу. Для накатывания резьб с левым свинчива нием ролики имеют правую многозаходную резьбу.
Габаритные размеры роликов и Технические условия на их изготовление установлены ГОСТ 9359—69.
Одним из основных конструктивных элементов ро лика является средний диаметр
dzр о л и к — ^ 2 р е з ь б ь Р Т
где ( Д р е з ь б ы — средний диаметр резьбы; п — число заходов ролика.
Многозаходность резьбы роликов необходима для по лучения угла подъема резьбы ролика, равного углу подъема резьбы накатываемого болта, при этом диаметр ролика в несколько раз больше диаметра обрабатывае мой резьбы. Такое соотношение необходимо, так как массивный ролик с большим диаметром облегчает форми рование профиля при накатывании резьбы. Резьбу нака тывают обычно на резьбонакатных станках, однако эф фективно использовать резьбонакатные станки в условиях серийного и единичного производства практически очень трудно. Кроме того, конструктивные особенности дета лей (многоступенчатые детали с буртиками, тройники и пр.) также делают невозможной обработку резьбы на резь бонакатных станках.
Использование резьбонакатных головок и резьбонакатпых плашек расширяет область применения накаты вания резьбы, обеспечивает получение коротких и длин ных резьб высокой точности (рис. 87). Накатывание резьбы резьбонакатными головками и плашками можно выпол нять на универсальных станках, при этом изготовление резьбы является одним из переходов общей операции ме ханической обработки.
Режимы обработки при накатывании резьбы роликами во много раз выше, чем при нарезании резьбы круглыми плашками (до 50 м/мин).
Использование резьбонакатных головок на токарно револьверных станках и токарных автоматах значительно повышает их производительность.
За последние годы разработано большое количество резьбонакатных головок и резьбонакатных плашек, изго товляемых заводом «Фрезер».
Ш л и ф о в а н и е р е з ь б ы . В производстве из мерительного инструмента и приборов часто встречаются
170
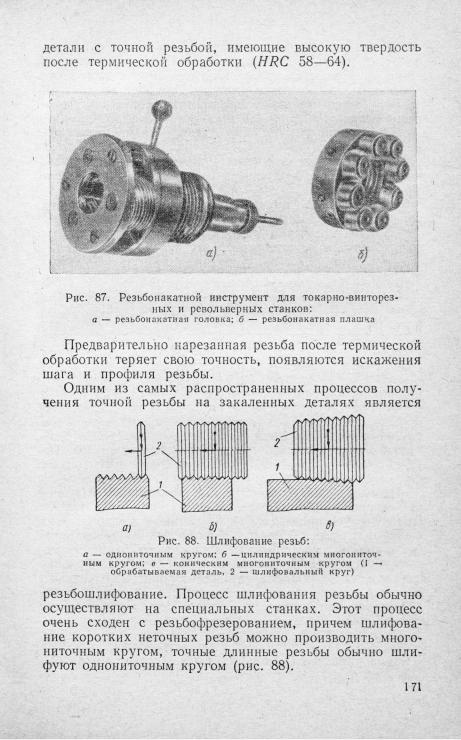
Существуют два метода шлифования резьб: шлифова ние с предварительной нарезкой резьбы (на токарных или фрезерных станках); шлифование по «цилиндру» без предварительной нарезки резьбы. Последний способ наи более производительный. Его применяют при обработке резьб с шагом s до 2—2,5 мм.
Шлифование резьбы обычно делят на предваритель ное и окончательное.
Общий припуск по среднему диаметру d2 делят нерав номерно. На окончательное шлифование оставляют V4—Vз припуска.
Шлифовальные круги выбирают в зависимости от обрабатываемого материала и от величины шага s.
Из табл. 9 следует, что чем меньше шаг резьбы, тем тверже круг и меньше размер зерна.
Таблица 9
Рекомендуемые шлифовальные круги для термически обработанных материалов
Ш а г |
р е з ь б ы s |
в |
мм |
А б р а з и в н ы й |
З е р н и с т о с т ь |
Т в е р д о с т ь |
|
м а т е р и а л |
|||
|
|
0,4—0,8 |
КЗ |
М40—М28 |
СТ1 —С2 |
1—1,5 |
КЗ—ЭБ |
4—5 |
Cl—С2 |
2—4 |
КЗ—ЭБ |
5—6 |
СМ1 |
4—6 |
ЭХ |
8—12 |
СМ1 |
Скорость резания при резьбошлифовании выше,, чем при обычном шлифовании (в среднем принимается 50 м/с). Такая скорость достигается за счет размера кругов. По ГОСТ 2424—67 (форма 2П) диаметры кругов изготовляют с размерами 450—500 мм при высоте 10 мм.
Одной из самых ответственных вспомогательных опе раций при резьбошлифовании является правка круга. Правку круга производят зачеканенными в медную дер жавку алмазами. Правку однониточных кругов выпол няют при помощи специальных приспособлений с руч ным управлением. В настоящее время резьбошлифоваль ные станки оснащают автоматическими приспособлениями. Качество правки круга проверяют при наладке станков на образцах изготовленных деталей. При этом проверяют прямолинейность сторон резьбы и половину угла про
филя |
Проверку производят в контрольном пункте |
ОТК на универсальном микроскопе с ножами (рис. 89),
172
Точность выполнения резьбового профиля на резьбо шлифовальных станках должна удовлетворять требова ниям, предъявляемым к изготовлению рабочих и конт рольных резьбовых калибров.
Для изготовления резьбы с точным шагом (ходом) на резьбошлифовальных станках применяют те же при способления, что и на токарных станках, т. е. коррекцион ные линейки и наборы коррекционных зубчатых колес. Настройку станков ведут так же по образцам деталей (эталонам).
Рис. 89. Схема измерения |
Рис. 90. Схема измерения |
|
угла профиля |
резьбы |
шага (хода) резьбы |
на универсальном |
микро |
|
скопе с ножами
Шаг точных резьб проверяют на универсальном микро скопе по левым и правым сторонам профиля. Такой ме тод дает более точное определение величины шага (хода) резьбы, так как исключает погрешность установки в цент рах (рис. 90).
При изготовлении резьбы ее средний диаметр d2 из меряют микрометром с резьбовыми вставками или наи более точным методом при помощи трех калиброванных проволочек и микрометра, оптиметра или любого рычаж ного прибора с ценой деления, обеспечивающей точ ность изготовления (рис. 91).
При обработке резьбы в центрах необходимо большое внимание обратить на тщательность и точность изгото вления центровых отверстий, особенно у термически обработанных деталей.
После термической обработки центровые отверстия следует зачищать на центрошлифовальных станках. Также очень хорошие результаты получаются после зачистки
центров твердосплавным зенкером с углом 60° на свер лильных станках.
173
При обработке небольших деталей иногда исполь зуют центры с шариками на концах. Меньшая (линей ная) поверхность касания обеспечивает совпадение осей детали и станка с большой точностью, но эти центры имеют существенный недостаток — быстрый износ.
Рис. 91. Схема |
измерения среднего |
диаметра |
резьбы: |
а — м и к р о м е т р о м с |
р е з ь б о в ы м и в с т а в к а м и ; |
б — м етодом |
т р е х п р о в о |
л о ч е к ; М — р а з м е р б л о к а и з м е р и т е л ь н ы х п л и т о к д л я у с т а н о в к и п р и б о р а ; d 2 — р а з м е р и з м е р я е м о г о с р е д н е г о д и а м е т р а
Глубину резания при шлифовании резьбы принимают при предварительном шлифовании 0,03—0,05 мм, при окончательном шлифовании 0,005—0,01 мм.
Скорость вращения деталей при шлифовании резьбы принимают в пределах 2—3 м/мин.
2 |
1 |
2 |
1 |
6)
Рис. 92. Конструкция резьбовых калибров с твердо сплавным кольцом:
а — с ц и л и н д р и ч е с к и м к о р п у с о м ; б — с к о н и ч е с к и м к о р п у со м (/ — т в е р д о с п л а в н о е к о л ь ц о ; 2 — к о р п у с )
Указанные режимы обработки обеспечивают шерохо ватость поверхности в пределах 9—10-го классов чи стоты.
Шлифование резьбы многониточными кругами более производительно. Обработка всей нарезанной части про
174
исходит за один оборот детали. Глубину резания прини мают 0,01—0,03 мм. Точность шлифования резьбы много ниточными кругами невысокая. Этот способ применяют при предварительном шлифовании калибров, метчиков и других изделий.
За последнее время в инструментальной промышлен ности начали изготовлять инструменты и приборы, у ко торых измерительные поверхности армированы твердым сплавом. На заводе «Калибр» освоено изготов ление резьбовых калибров из твердого сплава. Конструкция та ких калибров принципиально не сколько отличается от обычных.
Твердосплавный калибр состоит из корпуса-вставки из стали 40Х
исоединенного с ней кольца из твердого сплава ВК8. Это кольцо надевают на цилиндрическую или коническую поверхность корпуса
изатем склеивают (рис. 92). Для склеивания твердосплавного кольца с корпусом калибра при меняют клей горячего отвердения на основе эпоксидной смолы ЭД-5.
Резьбу с шагом до |
s = 2,5 мм |
|
а) |
|
|
6) |
|||
нарезают на целой твердосплавной |
Рис. 93. Алмазные круги |
||||||||
заготовке. Применение пластифи |
для шлифования |
резьбы: |
|||||||
цированных |
заготовок для |
пред |
а — к о н с т р у к ц и я |
а л м а з н ы х |
|||||
варительной |
нарезки |
резьбы не |
к р у г о в |
по |
Г О С Т |
9770 — 61 |
|||
ф о р м а |
А 2 П ; |
б |
— к о н с т р у к |
||||||
дает хороших |
результатов |
из-за |
ц и я к р у г а |
Н П И Л |
|||||
значительного искажения формы и |
спекания |
(спекание |
|||||||
размеров элементов |
резьбы |
после |
|||||||
происходит при |
1350—1500° С). |
|
|
|
|
|
Резьбу на твердосплавных калибрах нарезают на резь бошлифовальных станках, причем в качестве инстру мента применяют алмазный круг.
Алмазный круг стандартной формы А2П (рис. 93, а) имеет некоторые недостатки с точки зрения нерацио нального расходования алмазов при правке.
На инструментальных заводах сейчас начали приме
няться алмазные круги конструкции НПИЛ 60° х |
350 х |
||
X 1,5 |
х |
203. Эти круги более экономны при |
правке |
(рис. |
93, |
б). |
|
175
В настоящее время алмазные шлифовальные круги выпускают по ГОСТ и стандартам предприятий, разрабо танным ВНИИАЛМАЗом.
Алмазный шлифовальный круг состоит из металли ческого или пластмассового' корпуса и режущей части — алмазоносного слоя. Форма и расположение режущей части на корпусе обусловлена назначением круга. Так же в зависимости от назначения алмазные круги изготовляют на различных связках (органических, металлических и керамических). Круги выпускают с различной концен трацией алмазов: 26; 50; 100; 150; 200%.
Для шлифования резьбы калибров с твердым сплавом рекомендуют круги с металлической связкой и концент рацией алмазов 100—150%. Режим абработки тот же, что и при шлифовании обычными абразивными кругами, т. е. скорость резания 50 м/с, глубина резания 0,005— 0,01 мм, скорость вращения детали 2—3 м/мин.
Шлифование алмазными кругами обеспечивает высо кий класс чистоты поверхности и не требует дополни тельной полировки.
Д о в о д к а р е з ь б ы . Процесс доводки заклю чается в снятии малых слоев материала абразивными порошками при помощи притиров. Притиры обычно изготовляют из мягких или пористых материалов: чугуна, меди, свинца, имеющих способность удерживать на по верхности отдельные абразивные зерна (этот процесс называют шаржированием).
Для обработки фасонной поверхности, в том числе и резьбы, притир имеет форму обрабатываемого профиля.
Чаще всего для изготовления притиров применяют чугун, так как свинец и медь являются материалами де фицитными и дорогими. Кроме того, свинец при доводке быстро изнашивается и меняет свою форму.
Доводка резьбы — операция малопроизводительная, обычно выполняемая вручную. Режимы процесса доводки не поддаются точному регулированию.
В настоящее время доводка наружных резьб успешно заменена резьбошлифованием мелкозернистыми кругами с высокими скоростями резания. Внутреннюю резьбу диаметром не менее 30 мм, прошедшую термическую об работку, практически обрабатывать можно шлифованием, причем резьбошлифование внутренних резьб малопро изводительно, так как диаметры шлифовальных кругов также имеют небольшие размеры, вследствие чего ско-
176
роста резания низкие. Резьба, полученная внутренним шлифованием, имеет невысокую точность и низкий класс чистоты (6—7).
Для шлифования внутренней резьбы станок трудно настроить, так как контроль отдельных элементов резьбы приходится выполнять по «слепкам». Общий же контроль внутренней резьбы производят комплексным методом, т. е. по калибрам.
Доводка внутренней резьбы пока является единствен ным технологическим процессом, позволяющим вести об работку внутренней, термически обработанной резьбы. При доводке резьбы калибров притир как бы переносит все размеры элементов резьбы на резьбу обрабатывае мого изделия, вследствие чего допуски на изготовление
притиров по углу и шагу s такие же жесткие, как и
на сами калибры.
Обычно в комплект для доводки резьбовых калибров входят три притира, причем притиры изготовляют раз жимными (для малых диаметров резьбы — жесткими). Притир насаживают на конусную оправку и в процессе обработки он постепенно разжимается, компенсируя износ.
Материалом для притиров служит чугун с перлито вой структурой, для резьб мелких размеров — конструк ционная сталь. Наличие раковин на рабочей часта при тира не допускается.
Расход притиров при доводке очень велик. Одним комплектом притиров (3 шт.) можно довести не более 12—15 резьбовых калибров-колец. Технологический про цесс доводки заключается в навинчивании и свинчивании резьбового кольца на притир. Обычно притир закреп ляют в шпинделе доводочного станка. Доводочный станок прост по своей кинематике и представляет собой шпин дельную .бабку с реверсивным вращением шпинделя. Удерживая рукой резьбовое кольцо-калибр, рабочий периодически изменяет направление вращения шпинделя, в результате чего совершается осевое возвратно-посту пательное перемещение детали. Шаржирование притира происходит в процессе самой доводки.
В связи с тем, что при доводке внутренних резьб после термической обработки приходится удалять значитель ные припуски, предварительную доводку на первом при тире обычно производят более твердыми абразивными
177
материалами, применяя либо карбид кремния, либо карбид бора с зернистостью 10—12. Окончательную до водку производят на втором и третьем притирах электрокорундовым порошком М28—М20 с последующей поли ровкой пастой ГОИ.
Проведенные опыты доводки резьбы пастами «Эльбор» зернистостью М14 и М10 на чугунном притире дали поло жительные результаты.
8.ОБРАБОТКА ДЕТАЛЕЙ ЗУБЧАТЫХ ЗАЦЕПЛЕНИЙ
Визмерительных инструментах и приборах зубчатые зацепления служат для передачи движения от измери тельного стержня к показывающему устройству, а в конт рольно-измерительных автоматах — для передачи дви жения на распределительный вал, поворотные меха низмы, отсчетные устройства и т. д.
Детали зубчатых передач изготовляют: .1) методом
копирования (деления), основанным на передаче формы режущего инструмента профилю зуба, колеса; 2) методом обкатки (огибания), основанным на имитировании зацеп ления и обкатывания зубчатой пары (колеса с другим колесом, с рейкой и т. д.) относительно друг друга. Зубья образуются за счет превращения одного из обка тываемых колес или рейки в режущий инструмент.
Выбор способа изготовления цилиндрических зубча тых колес определяется видом производства и требуемой точностью. Точность изготовления зубчатых колес опре деляется принятой в зависимости от конструкции изде лия степенью точности. По ГОСТ 1643—56, утвержден ному взамен ГОСТ 1643—46, установлено 12 степеней точности изготовления зубчатых колес, причем каждая степень точности устанавливает нормы кинематической точности, плавности и величины контакта зубьев. На рис. 94 приведено графическое сопоставление классов точности по ранее действующему ГОСТ 1643—46 со сте пенями точности по ГОСТ 1643—56. Степени точности 1; 2 и 12 в ГОСТ 1643—56 даны как перспективные и в дан ное время еще не применяются (ГОСТ 1643-56 действует до 1 января 1975 г. С 1 января 1975 г. вводится в дей ствие ГОСТ 1643-72).
Изготовление цилиндрических зубчатых колес с пря мыми и спиральными зубьями. 1. О б р а б о т к а з у б ч а т ы х к о л е с м е т о д о м к о п и р о в а н и я . Фрезерование цилиндрических колес с прямым зубом
методом копирования осуществляют дисковыми модуль ными фрезами на горизонтально-фрезерных станках, ос нащенных делительными устройствами, или на много
шпиндельных |
зуборезных |
|
|
// |
|||||
полуавтоматах. |
метода |
ко |
|
|
|
||||
Сущность |
С |
|
|
||||||
пирования |
заключается в |
|
|
||||||
том, что впадина между |
|
|
ю |
||||||
зубьями |
и |
соответственно |
|
|
|
||||
профиль |
зубьев |
образу |
4 |
|
|
||||
ются за счет копирования |
|
|
я |
||||||
профиля дисковой модуль |
j |
|
|||||||
? |
|
7 |
|||||||
ной фрезы. На рис. 95 по |
1 |
|
6 |
||||||
казана |
схема |
фрезерова |
СО------- 2 - ------------------------- = |
= ^ |
= 4 - з _ |
||||
ния зубьев методом копи |
Классы точности |
Степени точности |
|||||||
рования. |
Оправку |
вместе |
поотмененному |
по ГОСТ 1643-50 |
|||||
с закрепленными |
на |
ней |
ГОСТ 1643-46 |
|
|
||||
заготовками |
устанавли |
Рис. 94. Графическое сопоставление |
|||||||
вают в центры делитель |
|||||||||
норм точности по |
ГОСТ |
1643—46 |
|||||||
ного устройства или де |
и ГОСТ 1643—56 |
|
|||||||
лительной |
головки. |
При |
|
|
|
продольном ходе стола с подачей s мм/мин дисковая, мо дульная фреза, закрепленная на шпинделе станка, фре зерует впадину между зубьями. После возвращения стола в первоначальное положение заготовки поверты-
Рис. 95. Схема фрезерования зубчатых колес методом копирования
вается на г/г часть окружности и фрезеруется следую щая впадина. Производя таким образом последователь ное деление окружности на требуемое число зубьев z, фрезеруют остальные зубья колеса. Так как в основе процесса лежит и деление окружности на число
179