
книги из ГПНТБ / Мовчин, В. Н. Технология производства измерительных инструментов и приборов учебник
.pdf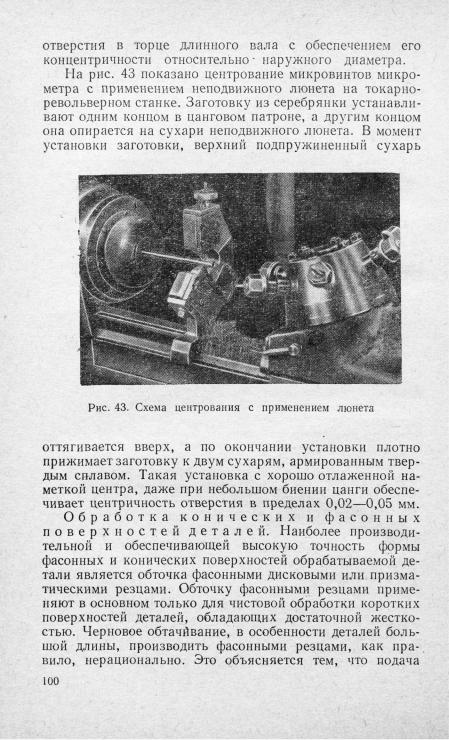
в радиальном направлении ограничивается глубиной резания, которая при точении фасонными резцами рав няется длине обрабатываемой поверхности (точнее длине развертки профиля обрабатываемой поверхности детали).
Увеличение радиальной подачи при черновой обточке приводит к вибрации резца и возникновению огранки на детали, кроме того, фасонные резцы обычно изготовляют из быстрорежущей стали и стойкость их резко снижается
Рис. 44. Схема обтачивания конических поверхностей
при обточке черной и имеющей окалину поверхности заготовки.
Схемы методов обтачивания конических поверхностей показаны на рис. 44, а, б, б, г. На рис. 44, а показана схема обтачивания при помощи смещения задней бабки. Величину смещения задней бабки определяют по формуле
х = L sin а,
где а — половина угла конуса при вершине; L — длина обрабатываемой детали.
Обтачивание конусов при помощи смещения задней бабки является простой по наладке операцией и не требует каких-либо специальных приспособлений, но при этом соприкосновение центрового отверстия с центром станка происходит только в двух точках '(рис. 38), и, очевидно, такой метод обработки приведет к разбивке и искажению формы центровых отверстий в детали. Дальнейшая обра
101
ботка точных деталей с использованием испорченных баз практически невозможна. Метод обработки конусов за счет смещения задней бабки можно применять для из готовления деталей невысокой точности или можно реко мендовать в качестве предварительной обработки кони ческих поверхностей с конусностью от 1 : 50 до 1 : 20 (угол при вершине конуса до 3°).
На рис. 44, б показана схема обтачивания конусов с конусностью, большей 1 : 20, т. е. с углом при вершине 2а от 3 до 24° при помощи копировальной линейки, уста новленной на требуемый угол а. При перемещении про дольного суппорта поперечный . суппорт, соединенный тягой с роликом, установленным в копировальной линейке, перемещается вместе с резцом с поперечном направлении. Для перемещения поперечного суппорта по копиру необ ходимо предварительно разъединить винт и гайку попереч ной подачи. Обточка с помощью копировальной линейки не портит центровые отверстия и, обеспечивая высокую точность, применяется для обработки ответственных де талей.
На рис. 44, в показана схема обтачивания коротких конических поверхностей под любым углом при помощи поворота верхнего суппорта.
На рис. 44, г приведена схема обтачивания конусов путем сочетания двух движений — продольного и одно временно поперечного движения резца. Такой метод при меняют в серийном производстве со специальной подго товкой и настройкой станка.
Обтачивание фасонных поверхностей деталей больших размеров производят на станках, имеющих копироваль ную линейку. Такое обтачивание аналогично обработке конусов, оно отличается лишь формой направляющей части линейки (рис. 45, а).
Обтачивание или растачивание фасонных профилей на торце детали осуществляют также с помощью копироваль ных линеек или специальных приспособлений. На рис. 45, б показана схема обработки сферической торцовой поверх ности. Перемещение резца производится по копиру, уста новленному в задней бабке или стойке, укрепленной на направляющих станины. Для свободного перемещения резца в поперечном направлении необходимо отключить суппорт от ходового винта и валика, при этом суппорт через ощупывающий палец 1 с помощью груза Q посто янно прижимается вместе с кареткой к копиру 2. Уста
102
новку резца на требуемые размеры производят переме щением верхнего суппорта, а поперечную подачу — пере мещением основного суппорта вручную.
При обтачивании ступенчатых валов вспомогательное время, затрачиваемое на выключение продольной подачи, отвод и установ резца по лимбу на требуемый диаметр
ивключение продольной подачи, составляет значительную величину и возрастает с увеличением количества ступеней. Уменьшение вспомогательного времени, а следовательно
иповышенние производительности труда, достигается за
а) |
б! |
Рис. 45. Схемы обтачивания фасонных |
поверхностей: |
а — п р о д о л ь н ы х ; 6 — т о р ц о в ы х |
|
счет механизации вспомогательных движений с помощью применения механических, гидравлических или электри ческих копировальных устройств к универсальным токар ным станкам.
Конструкции существующих копировальных устройств довольно разнообразны. Например, на рис. 46 показано копировальное приспособление для обточки ступенчатых валиков конструкции новатора В. К. Семинского.
Корпус приспособления / устанавливают на верхний суппорт вместо четырехрезцовой державки и после фикси рования положения с помощью фиксатора 13 закрепляют на оси 14 рукояткой резцедержателя. В корпусе по сколь зящей посадке 2-го класса точности установлена пиноль 2 с резцом 3 и сухарем 4, опирающимся на копир 5. Пружина 7 постоянно прижимает сухарь к копиру и регу лируется гайкой 8. Копир 5 представляет собой стальную закаленную оправку, имеющую ступени, соответствую щие профилю обрабатываемой детали. Копир установлен в направляющих втулках 6 корпуса. Правый конец
ЮЗ
копира с помощью шарнира 16 и тяги 17 соединяется со стойкой 18, закрепленной на станине станка. Для исклю чения поворота копира предусмотрена специальная шайба 15, имеющая паз, в который входит выступ оправкикопира.
При включении автоматической продольной подачи суппорт перемещается вместе с приспособлением, при этом
Рис. 46. Копировальное устройство для обтачивания ступенчатых валиков
сухарь 4 скользит по копиру 5, а резец 3 производит обта чивание первой ступени валика. При переходе сухаря
содной ступени на другую пиноль вместе с резцом под действием пружины 7 отходит вдоль своей оси до тех пор, пока сухарь 4 не дойдет до соприкосновения с другой ступенью копира. Обтачивание второй и других ступеней валика происходит аналогично.
Для получения прямого угла между ступенями валика ось пиноли установлена под углом 15°, а резец имеет передний угол в плане, равный 75°. При переходе пиноли
ссухарем с одной ступени на другую острие резца совер шает два движения: перпендикулярное к оси обрабаты ваемой детали и одновременно отход в обратном от торца детали направлении.
104
По окончании обточки валика, поперечный суппорт отводят от детали на 20—30 мм, а затем поворотом руко ятки /^относительно оси 10и соответственно эксцентрика 11 через шарик 9 перемещают пиноль вперед на такую вели чину, чтобы сухарь 4 отошел от копира и не мешал бы обратному отходу суппорта. При повороте рукоятки в дру гую сторону, пиноль с резцом устанавливают в исходное положение.
Описанное приспособление обеспечивает обточку сту пенчатых валиков с перепадом между соседними ступенями до 5 мм и с разницей между наименьшим и наибольшим диаметрами до 30 мм.
Более универсальными являются нормализованные гидравлические копировальные устройства к универсаль ным токарным станкам, позволяющие обрабатывать де тали как ступенчатой, так и криволинейной формы.
Вусловиях крупносерийного, а в некоторых случаях
исерийного производства широко применяют обработку на гидрокопировальных центровых полуавтоматах типа 1712, 1722, 1732 и др. Обтачивание ступенчатых и фасон ных поверхностей на таких полуавтоматах производят обычно одним резцом, установленным в верхнем суппорте, перемещающемся по копиру. Подрезание торцов, проточка канавок, обточка фасок и т. д. осуществляют -резцами, установленными в переднем суппорте.
По сравнению с универсальными токарными станками, оснащенными гидрокопировальными суппортами, гидро копировальные полуавтоматы, обладая большой жест костью, обеспечивают большую точность и более высокий класс чистоты обрабатываемой поверхности. Например, точность при чистовом точении может быть достигнута За— 4-го классов, а шероховатость поверхности V5—V6.
Обработку на многорезцовых станках-полуавтоматах
применяют в крупносерийном и массовом производстве для обтачивания ступенчатых и фасонных поверхностей
валов. Основным преимуществом многорезцовых станков является сокращение машинного времени за счет одновре менной работы нескольких резцов, установленных на суп портах. Основной, передний суппорт предназначен для продольного обтачивания заготовки, а поперечные суп порты — для проточки канавок, подрезки торцов, обта чивания фасонных поверхностей и т. д. На рис. 47, а показана схема обтачивания ступенчатого вала по методу деления длины. Для получения наибольшей производи
105
тельности всю длину вала разбивают на части по возмож ности равной длины. Количество резцов, устанавливаемых в переднем суппорте, равно количеству ступеней вала. Врезание и установку резцов на требуемые диаметры обра ботки производят либо после предварительной проточки канавки резцами, установленными на заднем суппорте, либо иногда двойным движением резцов переднего суп порта, т. е. перемещением в радиальном и одновременно
- 1
|
|
_ □ |
|
|
|
|
х |
1 |
J |
|
|
|
|
I I . 1 .' 1 1.'. у |
------------ |
|
б |
|
||
|
|
U tz z z z z z z ; |
з— |
|||
|
— |
|
У |
|
-Ч |
|
|
|
|
|
б SJ |
||
|
б |
. 5 |
|
|
|
|
|
|
d _ |
: |
|
|
|
|
|
а) |
|
|
|
6) |
Рис. 47. Схемы обтачивания |
на многорезцовых станках: |
|||||
а — по |
м етоду |
д е л е н и я |
д л и н ы ; |
|
б — п о м ето д у д е л е н и я п р и п у с к а |
в продольном направлении. Машинное время, затрачивае мое на обработку детали,
|
|
Тл плягп = |
I |
, |
к |
> |
|
|
„о |
~Г |
|
||
где s — подача |
в |
продольном |
направлении; |
|||
s] — подача |
в |
поперечном |
направлении; |
I — длина обрабатываемой поверхности;
б — путь резцов в поперечном направлении (врезание). Машинное время при обточке на токарном станке
гр’ _ |
4/ |
У м а ш — |
ns ■ |
Оно, очевидно, всегда значительно больше, чем на мно горезцовом станке.
При использовании в качестве заготовки проката и не возможности снятия припуска за один проход обтачива ние ведут по методу деления припуска, т. е. каждый резец снимает определенный слой и путь инструмента [равен сумме длин всех обтачиваемых ступеней. При таком спо собе обработки необходимо применять специальную кон струкцию заднего центра, обеспечивающего свободный проход резцов (рис. 47, б).
106
С учетом большой нагрузки, погрешностей при уста новке резцов и изменения сил резания по мере их вступле ния в работу, точность обработки на многорезцовых стан ках составляет 4—5-й класс, а шероховатость поверхно сти — 4—6-й класс чистоты.
К недостаткам многорезцовой обработки следует от нести повышенные требования к жесткости детали, так как радиальная сила резания возрастает при одновремен ном действии нескольких резцов. Кроме того, время на наладку и техническое обслуживание (подналадка станка, смена и заточка инструментов и т. п.) при обработке на многорезцовых станках также резко возрастает. Указан ные недостатки ограничивают применение многорезцовых станков для обработки деталей, и в некоторых случаях более выгодно применять гидрокопировальные станки.
Обработка на токарно-револьверных станках. Изго товление деталей на токарно-револьверных станках про изводят как из пруткового материала, так и из штучных заготовок. Большое количество инструментов, участвую щих в обработке, позволяет изготовлять детали сложной формы с обеспечением при обтачивании точности 4—5-го классов и шероховатости поверхности 5—6-го классов чистоты.
Обработка деталей на токарно-револьверных станках отличается от обработки на токарных станках:
1) возможностью изготовления деталей из прутка с за креплением последнего в цанге (при использовании цан говых зажимов необходимо применять калиброванные прутки, при закреплении в патроне могут быть исполь зованы прутки из горячекатаного проката);
2) установкой при наладке всех режущих инструмен тов, необходимых для обработки, в требуемое положение
(это дает возможность изготовлять |
всю партию деталей |
|
с одной настройки |
револьверного |
станка); |
3) более высокой |
производительностью, достигаемой |
за счет уменьшения затрат вспомогательного времени, а также совмещения переходов, т. е. одновременной обра ботки нескольких поверхностей инструментами, установ ленными в комбинированных державках;
4) |
широким применением фасонных резцов; |
5) |
применением многолезвийного инструмента, обра |
ботка с помощью которого может производиться либо по методу деления подачи (увеличение количества лезвий инструмента позволяет при сохранении одной и той же
107
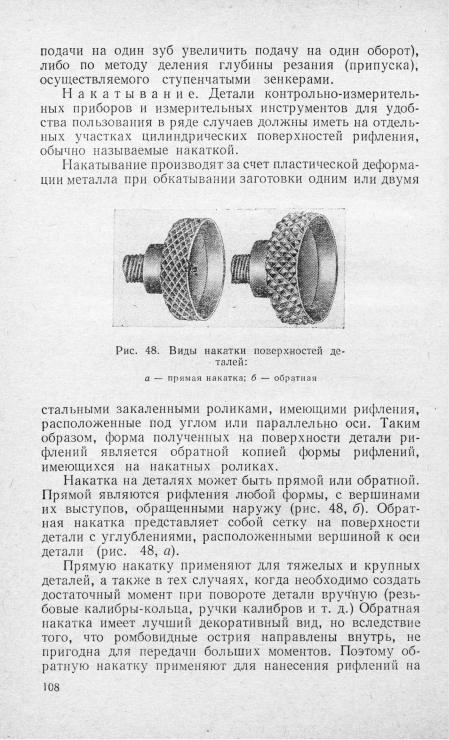
небольших деталях измерительных инструментов и при боров, например на деталях микрометров, штихмасов и т. д.
По форме рифлей и их направлению прямая накатка может быть: с параллельным расположением рифлей от носительно оси детали и сетчатой, т. е. с расположением
выступов |
под |
углом друг |
|
||||
к другу. |
|
вид |
накатки |
|
|||
Любой |
|
||||||
определяется шагом, т. е. |
|
||||||
расстоянием |
|
между |
ост |
|
|||
риями или впадинами риф |
|
||||||
лей. Шаг накатки подби |
|
||||||
рают |
в |
зависимости |
от |
|
|||
диаметра детали |
и ее на |
|
|||||
значения. |
|
|
|
|
|
|
|
Рифли, расположенные |
|
||||||
параллельно |
|
оси |
детали, |
|
|||
наносят одним или двумя |
|
||||||
роликами, |
перекрестную |
|
|||||
(сетчатую) накатку произ |
|
||||||
водят |
двумя |
роликами, |
|
||||
установленными |
в качаю |
|
|||||
щейся |
державке |
и имею |
Рис. 49. Многоосные детали: |
||||
щими разный наклон риф |
а — т и п а в т у л о к ; б — т и п а в а л о в ; в — |
||||||
лей. |
При |
|
накатывании |
з а г о т о в к а с т е х н о л о г и ч е с к и м ц е н т р о м А |
|||
державка |
с |
роликами |
пе |
|
ремещается в радиальном направлении до вдавливания во вращающуюся деталь, после чего получает продольное перемещение вдоль оси детали. При накатывании крупных шагов обработку производят за несколько проходов.
Обратную накатку выполняют одним роликом с пере мещением его только в радиальном направлении.
О б р а б о т к а м н о г о о с н ы х д е т а л е й типа втулок (рис. 49, а) может осуществляться одним из следующих способов:
1) растачиванием отверстия в детали, установленной по наружному диаметру в четырехкулачковом пат
роне; |
обтачиванием наружного диаметра с установкой |
|
2) |
||
детали по отверстию на эксцентриковой оправке; |
||
3) |
с установкой |
в специальных приспособлениях; |
4) |
при невысоких |
требованиях к точности растачиваемо |
го отверстия деталь устанавливают в трехкулачковом само-
109