
Filimonov_KP_TMM
.pdf
Определение основных размеров кулачковых механизмов. На первом этапе синтеза кулачковых механизмов определяются их основные
размеры: минимальный радиус кулачка R0 и смещение e для механизмов с поступательно движущимся толкателем, минимальный радиус R0 и межосевое расстояние l0 для кулачковых механизмов с коромыслом.
Стремление создать механизм с малыми габаритами приводит к ограничению угла давления ϑ , который определяет соотношение между реакциями в опорах толкателя и полезной нагрузкой, действующей на толкатель (рис. 3.1 и 3.2), т. е.
ϑi ≤ϑдоп . Причем, при силовом замыкании высшей пары и нереверсивном режиме работы
(кулачок вращается только в одном направлении) это условие должно удовлетворяться только на фазе удаления, так как на фазе возвращения толкатель движется под действием пружины.
Для случая геометрического замыкания высшей пары или при реверсивном режиме работы кулачковых механизмов с силовым замыканием высшей пары условие ϑi ≤ϑдоп
должно удовлетворяться как на фазе удаления, так и на фазе возвращения ведомого звена. На практике для кулачковых механизмов с поступательно-движущимся толкателем
обычно принимают ϑдоп = 30°, для коромысловых — 45°.
При проектировании кулачковых механизмов можно вместо ϑ задать угол передачи движения γ = 90 −ϑ . Это острый угол, заключенный между касательной к профилю
кулачка в точке касания и линией движения толкателя.
Аналитический метод определения основных размеров кулачковых механизмов с роликовым выходным звеном заключается в решении уравнений (3.1) или (3.2)
относительно искомых параметров при ϑi ≤ϑдоп на фазе удаления либо на фазе удаления и возвращения.
Для поступательно движущегося роликового толкателя
|
|
′ |
−e |
|
2 |
|
|
|
R0i = |
|
si |
′ |
+ e |
2 |
. |
(3.3) |
|
|
|
|
− si |
|
||||
|
tgϑдоп |
|
|
|
|
|
31
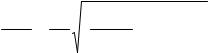
Так как при e = const значения |
R0i |
зависят от |
si |
и si′, то за искомое принимается |
||||||
наибольшее R0Э , полученное из уравнения (3.3). Чтобы определить угол ϕЭ , при котором |
||||||||||
R0i будет наибольшим, возьмем частную производную ∂R0 / ∂ϕ и приравняем ее нулю: |
||||||||||
∂R0i |
|
∂ |
|
′ |
−e |
|
2 |
|
|
|
= |
|
si |
|
′ |
+ e |
2 |
= 0 , |
|||
∂ϕ |
∂ϕ |
|
|
|
− si |
|
||||
|
tgϑдоп |
|
|
|
|
|
||||
откуда |
|
|
|
|
|
|
|
|
|
|
|
|
si′′= si′ tgϑдоп . |
|
|
|
(3.4) |
Подставив в формулу (3.4) выражения для si′ и si′′ определяем ϕЭ , затем s′Э и sЭ′′ и
подставляем в уравнение (3.3).
При геометрическом замыкании высшей пары условие ϑi ≤ϑдоп должно выполняться как на фазе удаления, так и на фазе возвращения:
2 |
s′уэ −e |
|
2 |
|
2 |
|
2 |
|
s′ |
−e |
|
2 |
2 |
|
|
|
|
′ |
|
|
|
|
вэ |
|
′ |
|
|
||||
R0Э |
|
+ e |
|
; |
R0Э |
|
|
+ e |
|
. |
|||||
= |
− sуэ |
|
= |
− tgϑдоп |
− sвэ |
|
|||||||||
|
tgϑдоп |
|
|
|
|
|
|
|
|
|
|
|
На фазе возвращения принимаем − tgϑдоп , так как в этом случае ϑдоп имеет знак,
противоположный знаку ϑдоп на фазе удаления. Приравнивая правые части, определяем е:
e = 0.5(s′уэ + sвэ −(sуэ − sвэ ) tgϑдоп ). |
(3.5) |
||||
По формуле (3.3) определяем R0Э . |
|
|
|
||
При e = 0 равенство (3.3) упрощается: |
|
|
|
||
|
si′ |
|
′ |
|
|
R0i = tgϑдоп |
− s |
(3.6) |
|||
|
При силовом замыкании высшей пары и нереверсивном режиме работы механизма условие ϑi ≤ϑдоп должно удовлетворяться только на фазе удаления, тогда расчетные формулы принимают вид:
|
|
e = 0.5(s′уэ |
− sуэ tgϑдоп ); R0Э = |
e |
. |
(3.7) |
|
|
|
||||
|
|
|
|
sinϑдоп |
|
|
Если для заданного закона движения толкателя уравнение (3.4) получается сложным, |
||||||
можно принять |
′ |
′ |
|
|
|
|
sэ |
= smax , а к значению R0i , подсчитанному по формуле (3.3), прибавить |
|||||
приращение ∆R |
и рассчитать ϑi для |
0 ≤ϕi ≤ϕy . Если условие ϑi ≤ϑдоп |
не будет соб- |
людаться, то к значению R0i + ∆R нужно добавить снова ∆r и т. д. (т раз), пока ϑi не будет удовлетворять условию ϑi ≤ϑдоп на заданных фазах. Тогда R0Э = R0i + m∆R .
Аналогично решается задача отыскания основных размеров кулачкового механизма с роликовым коромыслом на основании уравнения (3.2).
32
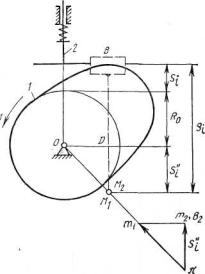
В основе графического метода определения основных размеров для кулачковых механизмов с роликовым выходным звеном лежат зависимости (3.1) и (3.2).
Если для ряда положений механизма векторы аналогов скорости si′ центра ролика толкателя (коромысла) повернуть на 90° в направлении вращения кулачка и провести лучи под углом γmin , то они определят зону возможного расположения центров вращения кулачка
(рис. 3.1, 3.2). Соединив плавной кривой концы векторов, получим график s = s(s′) . Если выбрать ось вращения кулачка в точке пересечения ограничивающих лучей, то значение R0
будет наименьшим. Выбрав центр вращения кулачка, определяют по чертежу остальные размеры кулачкового механизма.
При геометрическом замыкании высшей пары условие ϑi ≤ϑдоп должно выполняться на обеих фазах, следовательно, график s = s(s′) строится для обеих фаз (рис. 3.3, a, в) При
силовом замыкании— только на фазе удаления, так как на фазе возвращения толкатель (коромысло) движется под действием пружины. В этом случае второй ограничивающий луч проводится через точку
B0 , соответствующую началу удаления (рис. 3.3, б, г). При реверсивном режиме работы и силовом замыкании высшей пары условие ϑi ≤ϑдоп должно выполняться также на обеих фазах движения толкателя.
Для оценки работоспособности спроектированного кулачкового механизма следует построить график ϑi =ϑ(ϕ) (или γi = γ(ϕ) )
Для кулачкового механизма с поступательно движущимся плоским толкателем угол передачи движения
γ = const (в нашем случае γ = 90°) Следовательно, условие γ ≥ γmin выполняется незави-
симо от размеров кулачка. Наличие плоского толкателя предъявляет дополнительное требование к профилю кулачка, который должен быть выпуклым по всему контуру, т. е. радиус кривизны его в любой точке больше нуля ( ρ > 0). Для определения радиуса кривизны кулачка в точке касания строят заменяющий механизм и для него план аналогов
ускорений в масштабе µs′′ = µl . Из рис. 3.4 следует, что ρi |
= si + R0 + si′′. |
Кулачок имеет выпуклый профиль, если радиус кривизны его в любом положении |
|
будет удовлетворять условию: |
|
ρi = si + R0 + si′′> 0 . |
(3.8) |
33

Существует два метода определения R0 . Первый (метод Геронимуса) — неравенство
(3.8) приводится к виду: 1 > |
− s′′ |
. Приняв 1 = tg 45°, получим: |
|
||||
|
|
||||||
|
s + R0 |
|
|
|
|
|
|
|
|
tg 45° > |
− s |
′′ |
(3.9) |
||
|
|
|
|
||||
|
|
s + R0 |
|||||
|
|
|
|
||||
По условию (3.9) строится график s = s(s"). Под углом 45° к оси s проводится |
|||||||
касательная к этой кривой на участке, где s′′ < 0 . |
За центр вращения кулачка выбирается |
||||||
любая точка, лежащая ниже точки пересечения касательной с осью (см. рис. 3.3, е). |
|
||||||
Второй метод — неравенство (3.8) решается относительно R0 : |
|
||||||
|
|
R0 > −(si |
|
′′ |
(3.10) |
||
|
|
+ si ) |
|||||
Следовательно, R0 |
должно быть больше |
наибольшей отрицательной |
ординаты |
суммарного графика (si + si′′) (см. рис. 3.3, д).
При кинематическом замыкании высшей пары с помощью рамочной формы толкателя необходимо выполнение следующих условий: профиль кулачка должен быть очерчен выпук-
лой кривой постоянной ширины D = 2R0 + h ; фазовые углы находятся в следующей зависимости: ϕу =ϕв , ϕд.с. =ϕб.с. и ϕу +ϕд.с. =ϕв +ϕб.с. =180°; закон движения выходного звена sy = s(ϕ) может быть произвольно выбран только на фазе удаления, тогда на фазе воз-
вращения sв = D − s(ϕ), где D — ширина рамки; точки касания кулачка с двумя параллельными сторонами рамки лежат на одной нормали, отстоящей от оси рамки на расстоянии, равном аналогу скорости si′, а сумма радиусов кривизны профиля кулачка в точках касания равна ширине рамки D.
Расчет профиля кулачка.
Механизм с толкателем. Расчет начинается с построении центрового профиля Ц, т. е. траектории точки А (см. рис. 4.1) на вращающейся плоскости кулачка, что выполняется методом инверсии (обращенного движения). Если за полярную ось x1 принять прямую ОА,
то формулы для полярных координат ( Ri , βi ) в в i-м положении кулачка (ϕ =ϕi ) легко получаются из схемы рис. 4.1:
R = S 2 |
+ R2 |
+2S |
R2 |
−e2 |
; |
|||
i |
i |
|
0 |
|
i |
0 |
|
|
βi |
=ϕi |
−(χi − χ0 ) , |
|
(3.11) |
где χ0 = arcsin(e / R0 ) ; χi = arcsin(e / Ri ).
В формулах (3.11) автоматически учитывается знак эксцентриситета е. Направление отсчета углов противоположно направлению вращения кулачка. Произведя вычисления по
34
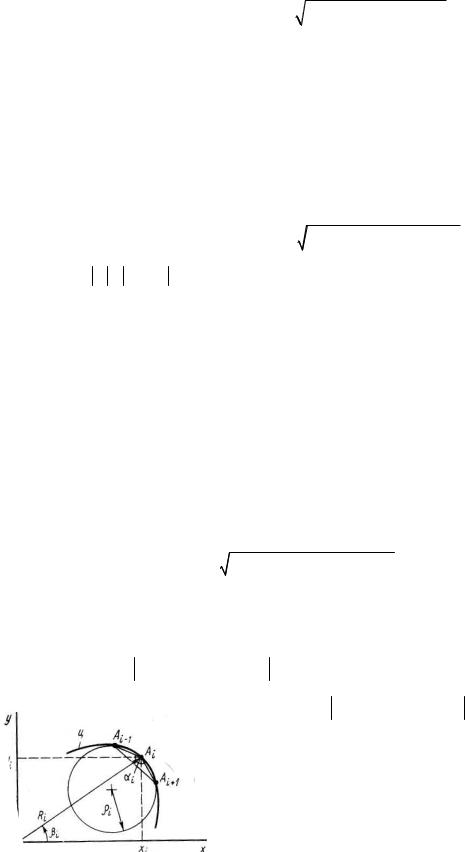
формуле (3.11) для i =1,2,...,n , получаем координаты центрового профиля для профили-
руемого участка.
|
Радиус-вектор R1i рабочего профиля P1 |
определяется из треугольника OAiB по |
|||||||||
теореме косинусов |
|
|
|
|
|
|
|
|
|
|
|
|
R |
= |
R2 + R2 |
−2R R |
p |
cosθ |
i |
, |
(3.12) |
||
|
1i |
|
|
i |
p |
i |
|
|
|
||
где Rp |
— радиус ролика; θi = arcsin(Si′cosϑi |
/ Ri ). Полярный угол вектора R1i |
в обращенном |
||||||||
движении |
|
|
|
|
|
|
|
|
|
|
|
|
|
|
β1i |
= βi |
+(θ1i −θi ) , |
|
|
(3.13) |
|||
где θ1i |
= arcsin(Si′cosϑi / R1i ) . |
|
|
|
|
|
|
|
|
|
|
Для механизма с геометрическим замыканием радиус-вектор второго рабочего профиля Р2 определяется из треугольника ОВС;
R |
= |
R2 |
+4R2 |
−4R |
R |
p |
cosδ |
i |
, |
(3.14) |
2i |
|
1i |
p |
1i |
|
|
|
|
где δi =π − θi − θ1i −θi .
Полярный угол вектора R2i
β2i = β1i ± |
arcsin(2Rp sinδi / R2i ) |
. |
(3.15) |
Знак плюс берется для фазы возврата, знак минус — для фазы удаления.
Механизм с коромыслом. Здесь, как и для механизма с толкателем, расчет профиля кулачка начинается с построения его центрового профиля Ц, т. е. траектории точки А (см. рис.
34.4) в обращенном движении. Полярные координаты |
центрового профиля ( Ri , βi ) |
|||||||||||||||||||||||||
относительно оси x1 для i-го положения (ϕ =ϕi |
) вычисляется по формулам, учитывая, что |
|||||||||||||||||||||||||
направление отсчета углов противоположно направлению вращения кулачка. |
|
|
|
|
||||||||||||||||||||||
|
|
R = |
L2 |
+l2 |
−2l l |
k |
cos(ψ |
i |
+ψ |
0 |
) ; β |
i |
=ϕ |
i |
±(γ |
0 |
−γ |
) , |
|
|
(3.16) |
|||||
|
|
i |
0 |
k |
0 |
|
|
|
|
|
|
|
|
i |
|
|
|
|
|
|
||||||
где ψ |
i |
— угол поворота коромысла О1А в i-м положении; ψ |
0 |
= arccos |
|
(l2 |
+l2 |
− R2 )/(2l l ) |
|
— |
||||||||||||||||
|
|
|||||||||||||||||||||||||
|
|
|
|
|
|
|
|
|
|
|
|
|
|
|
|
|
|
|
0 |
k |
0 |
0 k |
|
|
угол, характеризующий начальное положение коромысла;
γ0 = arccos (R02 +l02 −lk2 )/(2R0l0 ) ;
γi = arccos (Ri2 +l02 −lk2 )/(2Ril0 ) .
При расчете угла βi знак плюс берется, если на фазе
удаления направления вращения кулачка и коромысла противоположны (см. рис. 3.4), и знак минус — если одинаковы. Произведя вычисления по формулам (3.16) для
i =1,2,...,n получаем координаты центрового профиля для
Рис. 3. 4
35
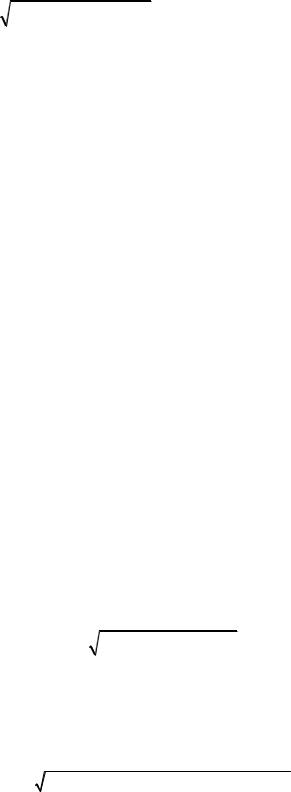
всего профилирующего участка.
Радиус-вектор R1i рабочего профиля P1 определяется из треугольника ОАВ по теореме косинусов:
R1i = |
2 |
2 |
′ |
/ Ri ) , |
(3.17) |
Ri |
+ Rp −2Ri Rp cosθi , θi = arcsin(ψilk cosϑi |
||||
где Rp — радиус ролика. |
|
|
|
|
|
Полярный угол, для которого вычислен R1i |
в обращенном движении, |
|
|||
β1i |
= βi +(θ1i −θi ) , θ1i |
′ |
|
(3.18) |
|
= arcsin(ψilk cosϑi / R1i ) |
|
Для механизма с геометрическим замыканием полярные координаты точки С второго рабочего профиля P2 (см. рис. 4.4) определяются из треугольника ОВС по формулам (3.14), (3.15).
Определение радиуса ролика. При проектировании кулачкового механизма с роликом значение Rp радиуса ролика может быть задано конструктором. В этом случае производится проверка правильности выбранной величины. Если Rp не задано, то эта
величина рассчитывается. Должны удовлетворяться следующие неравенства: |
|
|
Rp ≤ 0.7ρmin ; Rp ≤ 0.4R0 |
(3.19) |
|
где ρmin — минимальный радиус кривизны центрового профиля кулачка; R0 |
— |
|
радиус базовой окружности. Выше рассмотрен расчет координат профиля кулачка ( Ri |
, |
βi ), |
i =1,2,...,n . По этим величинам для каждых трех точек на центровом профиле кулачка Ai−1 ,
Ai , Ai+1 (рис. 4.6) определяется радиус описанной окружности ρi , который и будет
приближенным значением радиуса кривизны центрового профиля в i-й точке. Коор- |
||||||||||||||
динаты точек A в системе Ox1 y1 |
|
|
|
|
|
|
|
|
|
|
|
|
||
i |
|
|
|
|
|
|
|
|
|
|
|
|
||
|
|
xi |
= Ri cos βi ; yi = Ri |
sin βi |
|
|
(3.20) |
|||||||
Длина сторон треугольника Ai−1 |
Ai Ai+1 : |
|
|
|
|
|
|
|
|
|||||
|
|
A = |
(x − x |
j |
)2 +(y |
k |
− y |
j |
)2 , |
(3.21) |
||||
|
|
|
kj |
|
|
k |
|
|
|
|
|
|||
где k, j = i −1,i,i +1. |
|
|
|
|
|
|
|
|
|
|
|
|
||
Решая треугольник Ai−1 Ai Ai+1 , получаем |
|
|
|
|
|
|
|
|
||||||
ρi = |
|
Ai−1Ai+1 /(2sinαi ) |
|
, αi |
= 2arctg(D /(p − Ai−1Ai+1)) ; |
|
||||||||
|
|
|
||||||||||||
|
|
D = ( p − Ai−1Ai+1)( p − Ai−1Ai )( p − Ai Ai+1)/ p |
(3.22) |
|||||||||||
где p — полупериметр треугольника Ai−1 Ai |
Ai+1 . |
|
|
|
|
|
|
|
|
|||||
Произведя вычисления по формулам (3.20)... |
(3.22) для i = 2,3,...,n −1, |
находим |
||||||||||||
значение ρmin = min ρi . Для заданной величины Rp |
|
проверяются условия (3.19). |
|
36
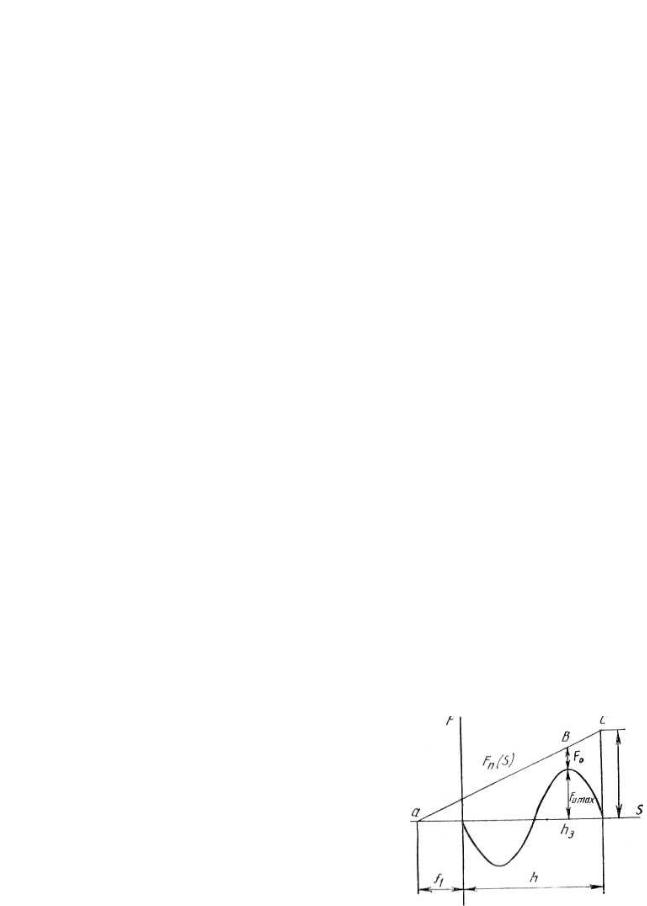
Определение жесткости замыкающей пружины. В механизмах с силовым замыканием необходимо установить такую пружину, чтобы в процессе работы не произошел отрыв выходного звена от профиля кулачка. Наибольшая сила упругости пружины должна быть больше максимальной силы инерции выходного звена в области, где возможен отрыв выходного звена от поверхности кулачка.
При построении графика Fи (s) изменения силы инерции выходного звена в функции перемещения за положительное направление Fu принимается направление, при котором она стремится оторвать выходное звено от профиля кулачка. Для гарантии непрерывного прижатия выходного звена к кулачку необходимо наличие некоторой минимальной реакции между нимиF0 . Предварительное натяжение пружины f1 составляет 20—40 % его наибольшего значения h. Сила упругости пружины линейно зависит от деформации. Сле-
довательно, соединив точки а и b прямой, получим зависимость Fпр (s) |
(рис. 3.5). Отрезок у в |
|||||||||||||
масштабе |
µF |
|
изображает наибольшую |
|
силу пружины |
Fпр max = µF y , или |
||||||||
F |
= (F |
+ F |
) |
|
f1 + h |
. Жесткость пружины |
|
|
|
|
||||
|
|
|
|
|
|
|||||||||
пр max |
0 |
и max |
|
|
f1 + hэ |
|
|
|
|
|
|
|
|
|
|
|
|
|
|
|
C = |
Fпр max |
= |
|
F |
+ F |
|
||
|
|
|
|
|
|
|
|
|
0 |
и max |
, |
(3.23) |
||
|
|
|
|
|
|
|
|
|
|
|
||||
|
|
|
|
1 |
f1 |
+ h |
|
|
|
f1 + hэ |
|
|||
|
|
|
|
|
|
|
|
|
|
|
где f1 — предварительное натяжение пружины; h — максимальное перемещение толкателя; hэ — перемещение толкателя, соответствующее максимальному значению силы инерции
.
|
Аналогично ведется расчет для кулачкового механизма с коромыслом: |
|
||||||||
|
C |
|
= |
M прmax |
, |
|
(3.24) |
|||
2 |
|
|||||||||
|
|
ψ |
1 |
+ψ |
2 |
|
|
|
||
|
|
|
|
|
|
|
|
|
||
где ψ — угловое перемещение коромысла; M прmax — наибольший момент силы. |
|
|||||||||
|
|
|
|
|||||||
|
Расчеты проводятся для фазы, в которой |
|
||||||||
отрицательное значение аналога ускорения будет |
|
|
||||||||
большим по своему абсолютному значению. |
|
|
|
|
|
|
|
|
||
|
Пример 1. Спроектировать плоский кулачковый |
|
|
|||||||
|
|
|
||||||||
|
механизм с поступательно движущимся роликовым |
|
|
|||||||
|
толкателем и силовым замыканием высшей пары по сле- |
|
|
|||||||
|
|
|
|
|
|
|
|
|
|
|
дующим |
входным |
параметрам: |
ходу толкателя |
|
|
|
Рис. 3. 5 |
h = 40 мм, фазовым углам удаления ϕy =102°, дальнего |
|||
стояния |
ϕд.c = 54° |
и возвращения |
ϕв =144°. Закон движения выходного звена при |
37
удалении — параболический, при возвращении — косинусоидальный. Кулачок вращается по часовой стрелке с n = 600об/мин, допускаемый угол давления ϑдоп = 30°; масса толкателя mт =120г.
Решение аналитическое.
1. Рассчитаем перемещение si , аналог скорости si′ и аналог ускорения si′′ по соответствующим заданному закону формулам. На фазе удаления выходное звено
движется |
по |
параболическому |
|
|
закону |
|
(см. табл. 3.1, закон |
№ 2): |
для 0 ≤ϕi ≤ϕy / 2 , |
|||||||||||||||||||||||||||||||
si |
= 2h(ϕi |
/ϕy )2 , |
si′ = |
4h |
|
ϕ |
|
, |
|
|
si′′= |
|
|
4h |
|
|
1 |
; для |
ϕy / 2 ≤ϕi ≤ϕy , si |
= h[1− 2(1−ϕi /ϕy )2 ], |
||||||||||||||||||||
|
ϕ |
|
|
|
ϕ |
|
|
|
|
|
||||||||||||||||||||||||||||||
|
|
|
|
|
|
|
|
|
|
ϕ |
y |
y |
|
|
|
|
|
|
|
|
y |
|
ϕ |
y |
|
|
|
|
|
|
||||||||||
|
|
|
|
|
|
|
|
|
|
|
|
|
|
|
|
|
|
|
|
|
|
|
|
|
|
|
|
|
|
|
|
|
|
|
||||||
|
|
4h |
|
|
ϕ |
|
|
|
|
|
|
|
|
|
|
4h 1 |
|
|
|
|
|
|
|
|
|
|
|
|
|
|
|
|
||||||||
si′ |
|
|
|
|
|
|
|
|
|
|
|
|
|
|
|
|
|
|
|
|
|
|
|
|
|
|
|
|
|
|
|
|
|
|
|
|
|
|
|
|
= ϕ |
|
1 |
− ϕ |
|
|
, |
|
|
si′′= −ϕ |
|
|
ϕ |
|
|
, |
|
|
|
|
|
|
|
где |
h = 40 мм; |
|
ϕy =102° =1.78рад; |
||||||||||||||
|
|
|
y |
|
|
|
y |
|
|
|
|
|
|
|
|
|
|
y |
|
|
|
y |
|
|
|
|
|
|
|
|
|
|
|
|
|
|
|
|
||
ϕi |
= 0°;17;34;51; 68;85;102°. |
|
|
|
|
|
|
|
|
|
|
|
|
|
|
|
|
|
|
|
|
|
|
|
|
|||||||||||||||
|
|
|
На фазе возвращения выходное звено движется по косинусоидальному закону |
(см. |
||||||||||||||||||||||||||||||||||||
табл. |
|
|
3.1, |
|
закон |
|
|
№4): |
|
|
|
|
si |
|
= h − s(ϕ) = h / 2[1+ cos(πϕi |
/ϕв )]; |
si′ = − |
πh |
sinπ |
ϕi ; |
||||||||||||||||||||
|
|
|
|
|
|
|
|
|
|
|
||||||||||||||||||||||||||||||
|
|
|
|
|
|
|
|
|
|
|
|
|
|
|
|
|
|
|
|
|
|
|
|
|
|
|
|
|
|
|
|
|
|
|
|
|
|
2ϕв |
ϕв |
|
si′′= − |
π 2h cosπ |
ϕi |
, где h = 40 мм; ϕв |
=144° = 2.51рад; ϕi = 0°; 24; 48; 72;96;120;144°. |
|
|||||||||||||||||||||||||||||||||||
|
|
|
2ϕв2 |
|
|
|
|
ϕв |
|
|
|
|
|
|
|
|
|
|
|
|
|
|
|
|
|
|
|
|
|
|
|
|
|
|
|
|
|
|
|
Результаты расчетов приведены в табл. 3.2.
|
|
|
|
|
|
|
|
|
Таблица 3. 1 |
|
|
|
|
|
|
|
|
|
|
|
|
Фаза |
i |
kф/6, |
i, |
si, мм |
s'i, |
s"i, |
i, |
i, |
Ri, |
|
град |
град |
мм |
мм |
град |
град |
мм |
|
|||
|
0 |
0 |
0 |
0 |
0 |
|
- |
0 |
34,00 |
|
|
50,50 |
29,99 |
|
|||||||
|
|
|
|
|
|
|
|
|
||
Удаления |
1 |
17 |
17 |
2,22 |
14,98 |
-3,67 |
15,25 |
35,94 |
|
|
2 |
34 |
34 |
8,88 |
29,96 |
|
18,68 |
27,92 |
41,92 |
|
|
|
|
|
||||||||
|
3 |
51 |
51 |
20,00 |
44,94 |
50,50 |
29,47 |
39,97 |
52,28 |
|
|
4 |
68 |
68 |
31,11 |
29,96 |
- |
12,08 |
53,68 |
62,89 |
|
|
5 |
85 |
85 |
37,77 |
14,98 |
1,72 |
69,19 |
69,33 |
|
|
|
50,50 |
|
||||||||
|
6 |
102 |
102 |
40,00 |
0 |
13,75 |
85,75 |
71,49 |
|
|
|
|
|
||||||||
|
7 |
0 |
156 |
40,00 |
0 |
- |
|
139,75 |
71,49 |
|
|
31,25 |
|
|
|||||||
|
|
|
|
|
|
|
|
|
|
|
Возвращения |
8 |
24 |
180 |
37,32 |
- |
- |
|
164,28 |
68,89 |
|
12,50 |
27,06 |
|
|
|||||||
10 |
72 |
228 |
20,00 |
25,00 |
0 |
|
218,1 |
52,28 |
|
|
|
9 |
48 |
204 |
30,00 |
- |
- |
|
189,96 |
61,82 |
|
|
21,65 |
15,62 |
|
|
||||||
|
|
|
|
|
- |
|
|
|
|
|
|
|
|
|
|
|
|
|
|
|
|
|
11 |
96 |
252 |
10,00 |
- |
15,62 |
|
245,31 |
42,95 |
|
|
21,65 |
|
|
|||||||
|
12 |
120 |
276 |
2,68 |
- |
27,06 |
|
273,89 |
36,34 |
|
38
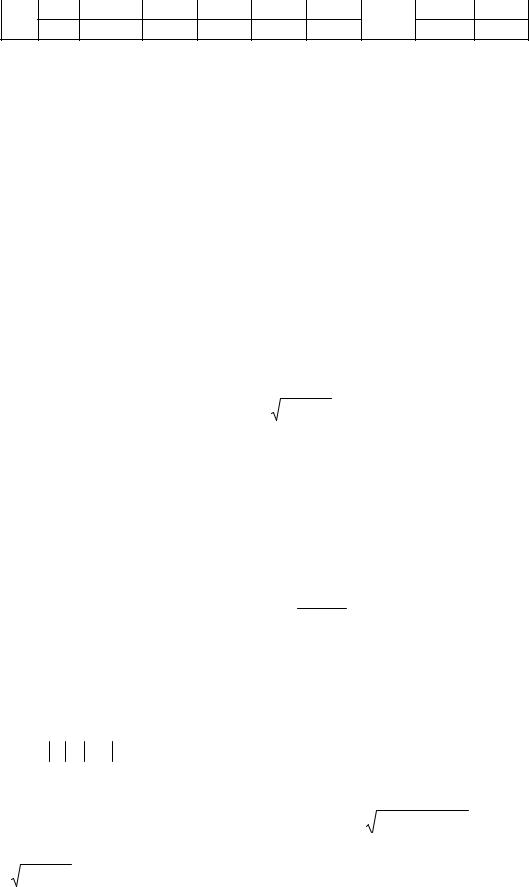
|
|
|
|
12,50 |
|
|
|
13 |
144 |
300 |
0 |
0 |
31,25 |
300,00 |
34,00 |
2. Определим основные размеры Ro и е кулачкового механизма по условию ограничения угла давления только на фазе удаления, так как высшая пара имеет силовое замыкание и кулачок вращается по часовой стрелке. В этом случае расчетными являются формулы (3.7).
Для параболического закона движения толкателя угол, при котором r0э имеет наибольшее значение, ϕy / 2 =102/ 2 = 51° = 0.89 рад, а аналог скорости s′yэ и перемещение syэ , соответствующие этому углу, s′yэ = 2h /ϕy = 44.944 мм, syэ = 0.5h = 20 мм.
Подставив эти значения в формулы (3.7), получаем: e = 0.5(44.944 − 20 0.5770 =16.699 мм;
R0э =16.699/ 0.5 = 33.398 мм.
Принимаем R0 = 34 мм; e =17 мм; s0 = R02 −e2 = 29.445мм. При вращении кулачка по часовой стрелке положительному значению смещения е соответствует расположение линии движения толкателя слева от центра вращения кулачка (рис. ??? и рис. ???).
3. Определяем по формуле (3.1) угол давления ϑi только на фазе удаления, так как высшая пара имеет силовое замыкание и заклинивание механизма может произойти только на фазе удаления (на фазе возвращения толкатель движется под действием пружины):
ϑyi = arctg ss′yi+−se .
0 yi
Результаты вычислений заносим в табл. 3.2. На основании полученных данных строим график зависимости ϑi в функции угла поворота кулачка на фазе удаления. Масштаб построений µϑ = µϕ =1.7 град/мм (рис. 2.27, г).
Так как ϑi < ϑдоп значения Ro и е удовлетворяют условию синтеза.
4. Определяем полярные координаты центрового профиля кулачка по формулам:
|
|
|
|
|
|
α |
i |
=ϕ |
i |
−(arctg |
s0 + si |
|
−arctg |
s0 |
) ; |
R = (s |
0 |
+ s |
)2 + e2 |
, |
|
|
|
|
|
|
|
|
|
||||||||||||||
|
|
|
|
|
|
|
|
|
e |
|
e |
i |
i |
|
|
||||||
|
|
|
|
|
|
|
|
|
|
|
|
|
|
|
|
|
|
||||
где s |
|
= |
R2 |
−e2 |
= 29.445 |
мм; на фазе |
удаления |
ϕ = k |
ϕy |
, |
а на фазе возвращения |
||||||||||
0 |
|
||||||||||||||||||||
|
|
0 |
|
|
|
|
|
|
|
|
|
|
|
|
6 |
|
|
|
|
||
|
|
|
|
|
|
|
|
|
|
|
|
|
|
|
|
|
|
|
|
||
ϕi =ϕy +ϕд.c + k |
ϕв |
, k изменяется от 0 до 6. |
|
|
|
|
|
|
|
|
|
||||||||||
|
|
|
|
|
6 |
|
|
|
|
|
|
|
|
|
|
|
|
|
|
|
|
39
Результаты расчетов заносим в табл. 4.2. По полученным значениям αi и Ri строим центровой профиль кулачка. Для этого в масштабе µs = 0.001м/мм проводим окружности радиусами; e =17 мм, R0 = 34 мм и Rmax =71,49 мм. Касательно к окружности радиусом е слева проводим линию движения толкателя уу. Соединив точку пересечения направляющей уу с окружностью радиусом Ro (точку Во) с центром вращения кулачка (точка О1), получим радиус-вектор Ri-Ro, соответствующий началу удаления. От этого радиуса в направлении,
противоположном вращению кулачка, отложим полярные углы αi , на сторонах которых строим в масштабе µs радиусы-векторы Ri. Соединив плавной кривой концы радиус-
векторов, получим центровой профиль кулачка.
Для проверки правильности расчетов и построений графически определим фазовые углы построенного кулачка и сравним их с заданными: ϕy = aO1B =102°, ϕд.с. = B6O1B7 .
Чтобы получить угол ϕв , следует из точки В13 провести касательную к окружности радиусом е так, чтобы касание происходило с той же стороны, что и в начальном положении. Точку пересечения касательной с окружностью радиусом Rmax обозначим d .
Тогда B7O1d =144°. Следовательно, вычисления произведены правильно.
Определим минимальный радиус кривизны центрового профиля кулачка ρmin как радиус вписанной окружности выпуклого участка профиля кулачка, где кривизна его окажется наибольшей. На этом участке произвольно выбираем три точки k1, k2 и k3 и соединяем их двумя хордами. В середине хорд восставляем к ним перпендикуляры, точку пересечения которых М принимаем за центр вписанной окружности (рис. 2.27, б). Получим
ρmin = 22 мм.
5.Действительный профиль кулачка найдем как эквидистантную кривую, отстоящую от центрового профиля на расстоянии, равном радиусу ролика.
Радиус ролика rp выберем наименьшим из условий (3.19):
rp1 = 0.7ρmin = 0.7 22 =15.4мм
rp2 = 0.4r0 = 0.4 34 =13.6мм
Окончательно примем rp =12мм.
Для получения действительного профиля кулачка на его центровом профиле выбираем ряд точек, из которых проводим полуокружности (в сторону уменьшения радиус-
вектора кулачка) радиусом, равным радиусу ролика rp . Огибающая этих полуокружностей
и является действительным профилем кулачка.
40