
журнал для КР по англ
.pdf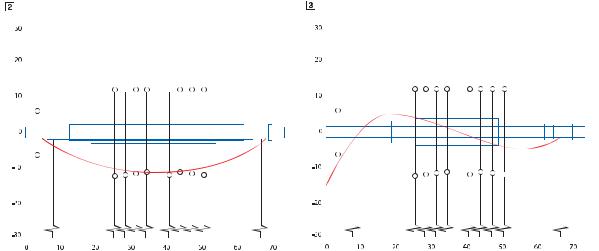
Большинство роторов этого класса вращается с частотой, ниже частоты, на которой проявляется влияние второго критического режима, так называемой первой изгибной волны, при которой вал принимает форму синусоиды с узловыми точками, расположенными за пределами центрального сечения радиального подшипника скольжения, как показано на .
Обязательное требование для высокоскоростных роторов
Балансировка на рабочей частоте необходима для отдельных роторов, работающих ниже второй критической скорости, и обязательна для каждого ротора, вращающегося со скоростью равной либо превышающей вторую критическую.
Некоторые из таких высокоскоростных роторов требуют также дополнительной корректировки остаточного дисбаланса при низких частотах; это необходимо для того, чтобы ротор мог преодолеть первую критическую скорость без чрезмерного отклонения от оси.
Чрезмерное отклонение вала в процессе пуска и остановки влечет за собой увеличение зазоров в уплотнителях вала, а также может привести к повреждению подшипников, к увеличению трения между вращающимися поверхностям и элементами неподвижных деталей корпуса.
Несмотря на то, что все производители машин и оборудования имеют собственные балансировочные стенды для балансировки оборудования на рабочих частотах, последние, в основном, используются для балансировки новых роторов в процессе производства и лишь изредка – для оказания своим клиентам услуг при послепродажном обслуживании.
Независимые ремонтные компании могут получить услуги высокочастотной балансировки по рыночным ценам лишь на нескольких таких стендах. Поскольку объем заказов на поставку нового оборудования сейчас высок как никогда, производите-
лям оборудования в настоящее время особенно сложно включить в план работы собственных балансировочных стендов дополнительные заказы в соответствии с графиком капитальных ремонтов заказ- чика.
Обширный опыт
Подразделение Sulzer Turbo Services производит капитальный ремонт разнообразных вращающихся узлов. Проведение балансировки на рабочих частотах выполняется либо по желанию клиента, как одна из ремонтных операций согласованного перечня, либо когда это требуется исходя из истории эксплуатации механизма .
Sulzer Turbo Services также принимает участие в модернизации оборудования, когда положительный эффект изменения конструкции уплотнителей и подшипников можно продемонстрировать на стенде до их ввода в эксплуатацию.
Для наилучшего обслуживания своих клиентов Sulzer Turbo Services имеет два скоростных балансировочных стенда
– один из крупнейших и самых современных стендов в США, находящийся неподалеку от Хьюстона, в штате Техас , и второй стенд в г. Винтертур, в Швейцарии.
Оба стенда проходят регулярные техни- ческие проверки и модернизацию для поддержания их в хорошем рабочем состоянии.
Эти два специализированных балансировочных стенда обеспечивают надежное и своевременное обслуживание всех шести региональных ремонтных компаний Sulzer Turbo Services, а также выполнение прямых заказов производителей оборудования и наших клиентов.
Оба стенда оборудованы самым современным электронным и диагностическим оборудованием, обеспечивающим возможность выявления и устранения неисправностей.
ПАНОРАМА
Генераторы
Одна из областей применения таких стендов, которую мы разработали специально для генераторов – процедура, позволяющая нам выявлять короткозамкнутые витки и анализировать работу генератора при помощи зонда магнитного потока в воздушном зазоре. Зонд воспринимает изменения в плотности радиального потока по мере того, как поверхности ротора проходят мимо него.
Полученная форма волны покажет наличие одного или нескольких короткозамкнутых витков за счет усиления кратковременных изменений потока при рабочей частоте вращения поля.
Для выполнения данной процедуры генератор работает с обычной рабочей скоростью и с обычным возбуждением. Данная процедура позволяет выявить неполадки, способные нарушить правильную работу и образовать небольшие участки перегрева поля генератора, которые невозможно обнаружить в обыч- ных условиях до запуска оборудования. В большинстве случаев устранение этих проблем на месте эксплуатации может потребовать вынужденного останова оборудования.
Научно-исследовательская база
Благодаря своим уникальным характеристикам, наши балансировочные стенды также используются научно-ис- следовательскими отделами компаний Sulzer Turbo Services, Sulzer Metco Surface Coatings и научно-исследовательским центром Sulzer Innotec для разработки и эксплуатационных испытаний различ- ных проектов уплотнительных систем.
Испытания включают в себя измерения срока службы различных покрытий, наносимых на сегментированные уплотнительные кольца для использования в следующем поколении паровых и газовых турбин.
|
|
Первый критический режим |
|
|
|
Второй критический режим |
||||||||||||||||||||||||||||||||||||
|
|
|
|
|
|
|
|
|
|
|
|
|
|
|
|
|
|
|
|
|
|
|
|
|
|
|
|
|
|
|
|
|
|
|
|
|
|
|
|
|
||
Радиус вала (дюйм) |
|
|
|
|
|
|
|
|
|
|
|
|
|
|
|
|
|
|
|
Радиус вала (дюйм) |
|
|
|
|
|
|
|
|
|
|
|
|
|
|
|
|
|
|
||||
|
|
|
|
|
|
|
|
|
|
|
|
|
|
|
|
|
|
|
|
|
|
|
|
|
|
|
|
|
|
|
|
|
|
|
|
|
||||||
|
|
|
|
|
|
|
|
|
|
|
|
|
|
|
|
|
|
|
|
|
|
|
|
|
|
|
|
|
|
|
|
|
|
|
|
|
||||||
|
|
|
|
|
|
|
|
|
|
|
|
|
|
|
|
|
|
|
|
|
|
|
|
|
|
|
|
|
|
|
|
|
|
|
|
|
||||||
|
|
|
|
|
|
|
|
|
|
|
|
|
|
|
|
|
|
|
|
|
|
|
|
|
|
|
|
|
|
|
|
|
|
|
|
|
||||||
|
|
|
|
|
|
|
|
|
|
|
|
|
|
|
|
|
|
|
|
|
|
|
|
|
|
|
|
|
|
|
|
|
|
|
|
|
||||||
|
|
|
|
|
|
|
|
|
|
|
|
|
|
|
|
|
|
|
|
|
|
|
|
|
|
|
|
|
|
|
|
|
|
|
|
|
||||||
|
|
|
|
|
|
|
|
|
|
|
|
|
|
|
|
|
|
|
|
|
|
|
|
|
|
|
|
|
|
|
|
|
|
|
|
|
||||||
|
|
|
|
|
|
|
|
|
|
|
|
|
|
|
|
|
|
|
|
|
|
|
|
|
|
|
|
|
|
|
|
|
|
|
|
|
||||||
|
|
|
|
|
|
|
|
|
|
|
|
|
|
|
|
|
|
|
|
|
|
|
|
|
|
|
|
|
|
|
|
|
|
|
|
|
||||||
|
|
|
|
|
|
|
|
|
|
|
|
|
|
|
|
|
|
|
|
|
|
|
|
|
|
|
|
|
|
|
|
|
|
|
|
|
||||||
|
|
|
|
|
|
|
|
|
|
|
|
|
|
|
|
|
|
|
|
|
|
|
|
|
|
|
|
|
|
|
|
|
|
|
|
|
|
|
|
|
|
|
|
|
|
|
|
|
|
|
|
|
|
|
|
|
|
|
|
|
|
|
|
|
|
|
|
|
|
|
|
|
|
|
|
|
|
|
|
|
|
|
|
|
|
|
|
|
|
|
|
|
Осевое расположение (дюйм) |
|
|
|
|
|
|
|
|
Осевое расположение (дюйм) |
||||||||||||||||||||||||||
|
|
|
|
|
|
|
|
|
|
|
|
|
|
|
|
|
|
|
|
|
|
|
|
|
|
|
|
|
|
|
|
|
|
|
|
|
|
|
|
|
|
|
Sulzer Технический обзор 4/2009 | 19
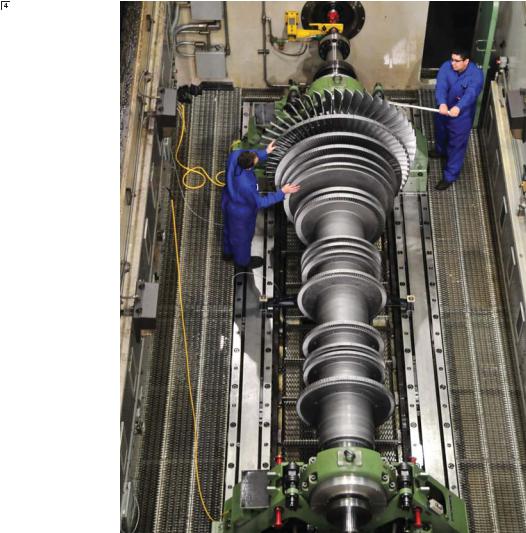
ПАНОРАМА
Некоторые элементы, влияющие на баланс ротора
Существуют множество различных конструкций роторов, предназначенных для работы на газе или на жидкости. Поскольку на его части действуют различные нагрузки, используются различ- ные конструкционные материалы.
Некоторые примеры приведены ниже:
•Цельные поковки для паровых турбин и расширителей горячего газа
•Кованые валы, на которые в горя- чем виде насаживаются диски или рабочее колесо
•Кованые валы, на которые в горя- чем виде насаживаются все диски, полумуфты и прочие детали
•Кованые диски или блоки дисков, скрепленные болтами друг с другом, с одним центральным или несколькими периферийными болтовыми стяжками при помощи сцепления с V-образными зубьями или сцеплением с круговыми зубьями, передающими крутящий момент между дисками и на обрезанные концы вала
Высокоскоростная паровая турбина, типичный пример высокочастотной балансировки
•Сварные цилиндрические узлы – их можно найти в очень больших паровых турбинах или высокоскоростных осевых роторах компрессоров, когда сердцевина вала выполнена из полых цилиндров, спаянных между собой лазером роликовыми сварными швами для уменьшения веса узла ротора
•И, наконец, комбинация вышеуказанных методов.
Возбуждение вибрационных режимов усложняется применением различных материалов, их разным качеством, различными размерами и жесткостью ротора.
Любой дисбаланс, выявленный по всей длине ротора, который совпадает с отклонением в форме колебаний, приводит к усилению отклонения в этих точках.
Если его не исправить, такой дисбаланс создает дополнительное вибрационное воздействие на подшипник.
Смещение отдельных дисков или групп дисков по длине вала или вне центральной оси в процессе работы маши-
ны может создать определенные проблемы, особенно если смещение массы усиливается.
Процесс обеспечения качества
При производстве нового ротора его необходимо балансировать на рабочей частоте – это одна из операций, обеспе- чивающих его качество.
Исходные балансировочные работы дают владельцу базовую кривую ротора для ее последующего сравнения с результатами последующих проверок.
Кроме того, очень важно учитывать все элементы, закрепленные на валу, поскольку они могут отразиться на качестве балансировки и на реакции ротора.
Для низкочастотной балансировки ротора и снижения вибрации используется поэтапная сборка и балансировка ротора после каждого этапа.
Данный метод много раз использовался подразделением Sulzer Turbo Services для ремонта роторов, в истории эксплуатации которых видны проблемы с вибрацией.
Однако даже поэтапная сборка и балансировка не обеспечивают плавность работы полностью собранного ротора, поскольку при этом не учитываются вибрации, вызванные возбуждением системы по мере ее ускорения свыше критической скорости и до ее рабочей скорости.
В ходе технической проверки ротора целесообразно проверять грузы, добавленные для корректировки неизбежного дисбаланса ротора.
Задача любого процесса балансировки заключается в использовании минимального количества грузов для корректировки дисбаланса ротора.
Работа при скоростях выше первой критической скорости
Многие высокоскоростные гибкие роторы работают при скорости, превышающей первую критическую скорость. Для таких роторов очень важно исправить реакцию на дисбаланс на первой критической скорости по двум причинам:
• Дисбалансная |
ñèëà |
è |
возникаю- |
||
щие отклонения вала могут быть |
|||||
настолько |
опасными, |
÷òî |
ротор |
||
не пройдет |
первую |
критическую |
|||
скорость или |
заденет |
уплотнители |
|||
вала. Даже при минимальном кон- |
|||||
такте между валом и уплотнителя- |
|||||
ми произойдет увеличение |
зазора |
||||
уплотнителя и снижение эффек- |
|||||
тивности всей установки. Это так- |
|||||
же создаст локальный нагрев вала, |
|||||
который |
способствует |
усилению |
отклонения на первой критической скорости и может привести к постоянному изгибанию вала.
20 | Sulzer Технический обзор 4/2009
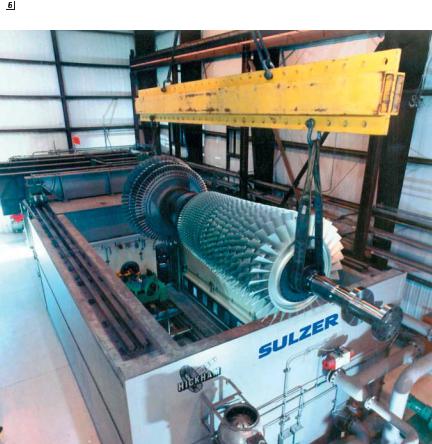
•При включении и выключении ротор может слишком долго оставаться на первой критической скорости, даже если скорости ускорения и замедления контролируются, и это может привести к существенному повреждению установки.
Балансировка на рабочем месте по сравнению с балансировкой на рабочей скорости
Ротор можно достаточно эффективно балансировать на месте установки внутри его корпуса и с его системой подшипников.
Тем не менее, ограничивающим фактором может стать сложный доступ к балансировочным плоскостям.
Некоторые машины позволяют решить эту проблему за счет добавления одного или нескольких смотровых отверстий на каждой из двух торцевых панелей, что позволяет устранить необходимость снятия всей половины верхнего кожуха.
Однако, если точка дисбаланса находится вне зоны смотрового отверстия, корректировка на торцевых панелях будет лишь компромиссом. Если доступ к ротору невозможен, то весь верхний кожух – или его части – придется снимать и снова устанавливать на место после каждого этапа балансировки.
Обычно для качественной балансировки требуется не менее пяти запусков.
Балансировка на половине блока ротора
Âнекоторых исключительных случаях подразделение Sulzer Turbo Services проводило балансировку ротора на месте его установки на половине блока ротора, то есть со снятой верхней половиной кожуха, снятыми нижними полукольцами уплотнения и собиранными подшипниками.
Ротор паровой турбины в таком случае обычно разгоняется воздухом, продуваемым через форсунку. Когда ротор разогнан до необходимой скорости, снимаются соответствующие показания.
Âслучае работы с крупногабаритной турбиной с механическим приводом для разгона ротора и получения необходимых показаний используется ведущий привод; однако количество допустимых пусков привода в день ограничено, поэтому такая процедура занимает довольно много времени.
Вращающийся элемент на месте установки
Балансировка вращающегося элемента на месте его установки связана с серьезными рисками и затратами. Всякий раз, когда снимается кожух, существует вероятность попадания в турбину посторонних предметов или повреждения какой-либо детали. Поскольку большинство машин являются частью какого-либо технологического процесса, такой процесс следует запускать и
Блок ротора газовой турбины, установленный на стенд. Компрессор и участки турбины скреплены болтами
ПАНОРАМА
прекращать много раз для достижения соответствующего уровня балансировки. Представьте, что вам придется просить оператора ядерной установки вставлять и извлекать топливные стержни раз шесть или более в течение четырех или пяти дней, чтобы вы смогли выполнить какиелибо технические процедуры, которые на самом деле должны выполняться в цеху, в контролируемой среде, на соответствующем оборудовании, во время запланированных остановов.
Более того, балансировка на месте установки заставит пользователя отрегулировать реакцию ротора так, чтобы скомпенсировать комбинированный эффект всех невращающихся элементов (таких, как несовпадение с осью, резонанс фундамента, резонанс трубопроводов).
Если ротор вращается внутри кожуха с нежелательными вибрациями и после проведения скоростной балансировки, возможно проблема кроется не в роторе. В этом слу- чае необходимо проверить всю систему и устранить выявленные недостатки.
Допустимые уровни дисбаланса
Очевидно, что лучше всего - отсутствие дисбаланса, но его достижение зачастую экономически невыгодно. Было проведено множество дискуссий по поводу допустимых уровней дисбаланса и в результате был выбран общий уровень на основании промышленных стандартов для различных типов машинного оборудования. Для скоростной балансировки Американский Нефтяной Институт (API) требует достижения уровня дисбаланса не более 1 мм/сек, или 7400 об/мин.
Возвратные инвестиции
Сложно представить себе более тяжелые времена для инженера, обслуживающего вращающееся оборудование, для руководителя центра технического обслуживания или директора по эксплуатации, чем ситуация, когда основной элемент какого-либо технологического процесса не запускается
âнужное время, не работает или теряет работоспособность между ремонтами.
В этом случае, производственные потери
âсочетании с расходами на исправление возникших неполадок достигают очень высокого уровня.
Динамические методы балансировки на месте установки, разработанные компанией Sulzer, помогут вам сэкономить и время, и деньги, по сравнению с общепринятыми методами ремонта на местах.
Øîí Óýñò (Shaun West)
Sulzer Turbo Services Zürcherstrasse 12 8401 Winterthur Switzerland
Òåë.: +41 52 262 34 44
Sulzer Технический обзор 4/2009 | 21
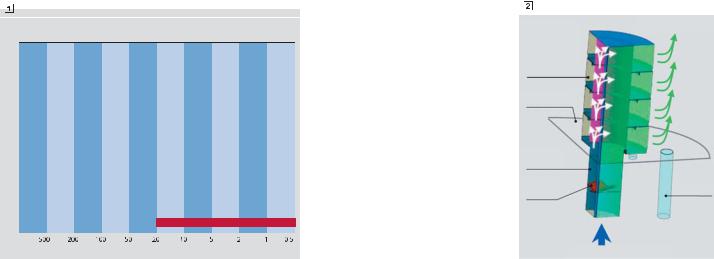
ПАНОРАМА
Новая технология улавливания капель
Во многих технологических процессах унос жидкости с потоком газа является нежелательным и может привести к повреждению вращающихся элементов компрессоров и детандеров, деградации сорбентов. В некоторых случаях капли жидкости, захваченные газовым потоком, могут привести к тому, что технологическое оборудование будет работать с меньшей производительностью
и эффективностью. Подразделение Sulzer Chemtech разработало новый продукт для отделения жидкости от газового потока – сепарационное устройство MKS Multi Cassette™.
Âбольшинстве случаев жидкость, захваченная газовым потоком, находится в виде капель. Образование и
размер капель определяются параметрами технологического процесса .
Âпроцессах с противотоком фаз, таких как ректификация и абсорбция,
|
|
|
|
|
газовая и |
жидкая |
ôàçû |
вступают |
|||||||
|
|
|
|
â |
интенсивное |
взаимодействие для |
|||||||||
|
|
|
|
|
обеспечения максимального массооб- |
||||||||||
|
|
|
|
мена между собой. |
|
|
|
|
|
||||||
|
|
|
|
|
Структурированная |
насадка, насып- |
|
||||||||
|
|
|
|
|
ная насадка и тарелки, разработан- |
||||||||||
|
|
|
|
|
ные подразделением Sulzer Chemtech, |
||||||||||
|
|
|
|
оптимизированы |
для увеличения |
||||||||||
|
|
|
|
массообмена и |
производительности. |
||||||||||
|
|
|
|
Однако одним неизбежным недостат- |
|
||||||||||
|
|
|
|
êîì ïðè |
противоточном |
контакте |
|
||||||||
|
|
|
|
|
|
|
|
|
|
|
|
|
|||
|
|
|
Ожидаемый размер капель в типовых процессах |
|
|
||||||||||
|
|
|
|
|
|
|
|
|
|
|
|
|
|
|
|
|
|
|
|
|
|
|
|
|
|
|
|
|
|
|
|
|
|
|
Капли |
|
Морось |
|
Легкий |
|
|
|
Туман |
|
|
||
|
|
|
дождя |
|
|
туман |
|
|
|
|
|
||||
|
|
|
|
|
|
|
|
|
|
|
|
|
|
||
|
|
|
|
Унос жидкости |
|
|
|
|
|
|
|
|
|
||
|
|
|
|
из водяных |
|
|
|
|
|
|
|
|
|
||
|
|
|
|
скрубберов и из |
|
|
|
|
|
|
|
|
|
||
|
|
|
|
оросительных |
|
|
|
|
|
|
|
|
|
||
|
|
|
|
|
колонн |
|
|
|
|
|
|
|
|
|
|
|
|
|
|
|
|
|
|
|
|
|
|
|
|
|
|
|
|
|
|
|
|
|
|
|
|
|
|
|
|
|
|
|
|
|
Спрей, возникающий из-за лопания |
|
|
|
|
|
|
|
|||||
|
|
|
|
пузырьков при барботаже |
|
|
|
|
|
|
|
||||
|
|
|
|
|
|
|
|
|
|
||||||
|
|
|
|
|
Унос из испарителей, колонн ректификации и абсорбции |
|
|
||||||||
|
|
|
|
|
|
|
|
||||||||
|
|
|
|
|
|
|
|
|
|
||||||
|
|
|
|
Конденсат после |
Конденсат послепромежуточного |
|
|
||||||||
|
|
|
|
|
газового |
холодильника на установке |
|
|
|
|
|
||||
|
|
|
|
холодильника |
компримирования |
|
|
|
|
|
|
||||
|
|
|
|
|
|
|
|
|
|
|
|
|
|
|
|
|
|
|
|
|
|
|
|
|
|
|
|
|
|
|
|
Конденсат после установки компримирования высокого давления
Диаметр капель (микрон)
между газовой и жидкой фазами является то, что при этом часто возникает унос капельной жидкости с газовым потоком. В других технологических процессах свободная жидкость образуется в газе в результате конденсации. В этом случае образование капель и их размер определяются образованием активных центров конденсации, что может привести к появлению сверхмалых капель, во много раз меньших, чем капли, образованные вследствие уноса жидкости в противоточных колоннах. Капли жидкости в потоке никогда не будут иметь одинаковый размер, но их размер будет находятся в определенном диапазоне, который можно охарактеризовать математически при помощи кривых логарифмически нормального распределения или нормального распределения Гаусса.
Новая технология каплеулавливания
Сепарационное устройство MKS Multi Cassette было разработано с целью достижения высокой эффективности сепарации жидкости при сохранении высокой производительности и оптимальных затратах. Это потребовало новых идей и подходов, которые были реализованы на практике в последней разработке компании Sulzer Chemtech в области сепарации
– MKS Multi Cassette™.
MKS Multi Cassette™ состоит из вход-
ного патрубка со встроенным лопастным завихрителем и сепарационных кассет . Лопастной завихритель закручивает поток газа, тем самым способствуя выпадению части капель на внутренней стенке патрубка:
уловленная жидкость собирается в нижней кассете и затем сливается из нее на полотно опорной тарелки. После прохождения завихрителя поток газа, содержащий капли жидкости, распределяется по кассетам, проходя через кассеты в горизонтальном направлении изнутри наружу. Каждая кассета имеет несколько слоев проволочной сетки, которая эффективно отделяет оставшиеся капли как прямым перехватом (барьерный
Схема работы MKS Multi Cassette™
Чистый 4 кассеты газ
проволочной
сеткой
Опорная
тарелка
Завихряющая
труба
|
Дренажная |
Завихритель |
труба |
Газ, содержащий капли жидкости
22 | Sulzer Технический обзор 4/2009
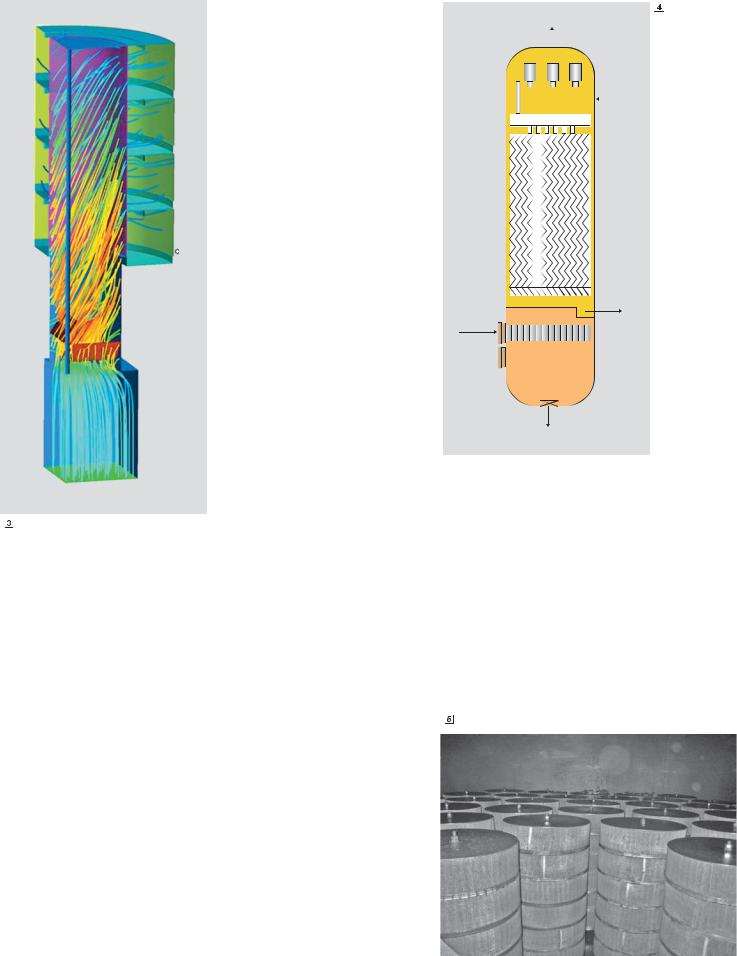
Использование вычислительной гидродинамики (CFD) для компьютерного моделирования
эффект), так и инерционным перехватом. Жидкость собирается на поддоне каждой кассеты и сливается на нижележащую кассету через систему переливных трубок. В итоге вся жидкость собирается на нижнем поддоне, также служит в качестве опоры для кассет MKS Multi Cassette™, после чего жидкость сливается из сепарационного устройства по специальным трубкам. При разработке сепарационного устройства MKS Multi Cassette были использованы компьютерные методы вычислительной гидродинамики (CFD). Компьютерное моделирование было выполнено подразделением Sulzer Innotec, что позволило проверить и оптимизировать геометрию лопастного завихрителя и распределение газового потока по кассетам .
Применение в колоннах осушки газа
Осушка природного газа в абсорберах при помощи гликоля – это широко распространенный процесс, применяемый практически на всех установках по подготовке и переработки во всем мире. При контакте влажного природ-
ного газа и гликоля (чаще всего триэтиленгликоль) в абсорбционной колонне можно выделить пары воды из потока газа. Сегодня в абсорбционных колоннах предпочитают использовать высокопроизводительную структурированную насадку, например Sulzer MellapakPlus, чтобы уменьшить диаметр колонны или увеличить производительность по газу. В зависимости от фактической скорости потока газа и физических свойств гликоля, уносится различное количество гликоля. Размер капли в данном случае может варьироваться в пределах 5-25 мкм. Для снижения уноса жидкости необходимо устанавливать в верхней части колонны сепарационные устройства. Стандартное требование по количеству унесенной жидкости составляет не более 13.7 литров на миллион стандартных куби- ческих метров газа (0.1 галлона/млн. ст. куб.ф.). Такое требование относится только к гликолю, который находится в жидком фазе. В колонне с массообменной насадкой Sulzer MellapakPlus™ необходимо устанавливать соответствующие высокопроизводительные сепарационные устройства, в противном слу- чае, необходимую производительность по газу достичь не удастся из-за ограничения по уносу гликоля ,
.
Сепарационное устройство MKS Multi Cassette идеально сочетается с насадкой Sulzer MellapakPlus в абсорберах осушки газа, т.к. отвечает следующим основным требованиям:
•Высокая сепарационная эффективность
•Высокая производительность
•Невысокие затраты на изготовление
•Компактные размеры
•Простая конструкция
•Простота монтажа
•Простота обслуживания Надежность и иные достоинства устройства уже подтверждены при применении во многих колоннах осушки природного газа.
Применение в сепараторах
Сепараторы (выносные), необходимые исключительно для отделения жидкости от потока газа, применяются в различных технологических процессах. Отделение углеводородных флюидов из природного газа при высоком рабочем давлении является трудной сепарационной задачей.
Во многих случаях причиной образования жидкой фазы является процесс конденсации: поскольку поверхностное натяжение между газом и жидкостью низкое, то могут образовываться очень малые и нестабильные капли. До этого момента, если сепараторы приходи-
|
|
|
|
|
|
|
|
|
|
|
|
|
|
|
|
|
|
|
|
|
ПАНОРАМА |
|
|
|
|
|
|
|
|
|
|
|
|
|
|
|
|
|
|
|
|
|
Колонна |
|
|
|
|
|
|
|
Сухой газ |
просушки |
|||||||||||||
|
|
|
|
|
|
|
|
|
|
|
|
|
|
|
|
|
|
|
|
|
природного |
|
|
|
|
|
|
|
|
|
|
|
|
|
|
|
|
|
|
|
|
|
|
|
|
|
|
|
|
|
|
|
|
|
|
|
|
|
|
|
|
|
|
|
газа гликолем c |
|
|
|
|
|
|
|
|
|
|
|
|
|
|
|
|
|
|
|
|
|
MellapakPlus™ |
|
|
|
|
|
|
|
|
|
|
|
|
|
|
|
|
|
|
|
|
|
и MKS Multi |
|
|
|
|
|
|
|
|
|
|
|
|
|
|
|
|
|
|
|
|
|
|
|
|
|
|
|
|
|
|
|
|
|
|
|
|
|
|
|
|
|
Обедненный |
Cassette™ |
|
|
|
|
|
|
|
|
|
|
|
|
|
|
|
|
|
|
|
|
триэтилен- |
|
|
|
|
|
|
|
|
|
|
|
|
|
|
|
|
|
|
|
|
|
гликоль |
|
|
|
|
|
|
|
|
|
|
|
|
|
|
|
|
|
|
|
|
|
|
|
|
|
|
|
|
|
|
|
|
|
|
|
|
|
|
|
|
|
|
|
|
|
|
|
|
|
|
|
|
|
|
|
|
|
|
|
|
|
|
|
|
|
|
|
|
|
|
|
|
|
|
|
|
|
|
|
|
|
|
|
|
|
|
|
|
|
|
|
|
|
|
|
|
|
|
|
|
|
|
|
|
|
|
|
|
|
|
|
|
|
|
|
|
|
|
|
|
|
|
|
|
|
|
|
|
|
|
|
|
|
|
|
|
|
|
|
|
|
|
|
|
|
|
|
|
|
|
|
|
|
|
|
|
|
|
|
|
|
|
|
|
|
|
|
|
|
|
|
|
|
|
|
|
|
|
|
|
|
|
|
|
|
|
|
|
|
|
|
|
|
|
|
|
|
|
|
|
|
|
|
|
|
|
|
|
|
|
|
|
|
|
|
|
|
|
|
|
|
|
|
|
|
|
|
|
|
|
|
|
|
|
|
|
|
|
|
|
|
|
|
|
|
|
|
|
|
|
|
|
|
|
|
|
|
|
|
|
|
|
|
|
|
|
|
|
|
|
|
|
|
|
|
|
|
|
|
|
|
|
|
|
|
|
|
|
|
|
|
|
|
|
|
|
|
|
|
|
|
|
|
|
|
|
|
|
|
|
|
|
|
|
|
|
|
|
|
|
|
|
|
|
|
|
|
|
|
|
|
|
|
|
|
|
|
|
|
|
|
|
|
|
|
|
|
|
|
|
|
|
|
|
|
|
|
|
|
|
|
|
|
|
|
|
|
|
|
|
|
|
|
|
|
|
|
|
|
|
|
|
|
|
|
|
|
|
|
|
|
|
|
|
|
|
|
|
|
|
|
|
|
|
|
|
|
|
|
|
|
|
|
|
|
|
|
|
|
|
|
|
|
|
|
|
|
|
|
|
|
|
|
|
|
|
|
|
|
|
|
|
|
|
|
|
|
|
|
|
|
|
|
|
|
|
|
|
|
|
|
|
|
|
|
|
|
|
|
|
|
|
|
|
|
|
|
|
|
|
|
|
|
|
|
|
Обогащенный триэтилен-
гликоль Влажный
природный
газ
Собранная
жидкость
лось проектировать, учитывая высокие скорости газового потока или просто для уменьшения габаритов и массы насколько это возможно, то применялись вихревые сепарационные элементы (Shell Swirltube) или пластинчатые каплеуловители (Sulzer Mellachevron). Однако пластинчатые каплеуловители не рекомендованы к использованию в колоннах высокого давления при наличии углеводородов в жидкой фазе, т.к. при таких условиях сепарационная эффективность будет низкая. Вихревые
MKS Multi Cassette™
Sulzer Технический обзор 4/2009 | 23
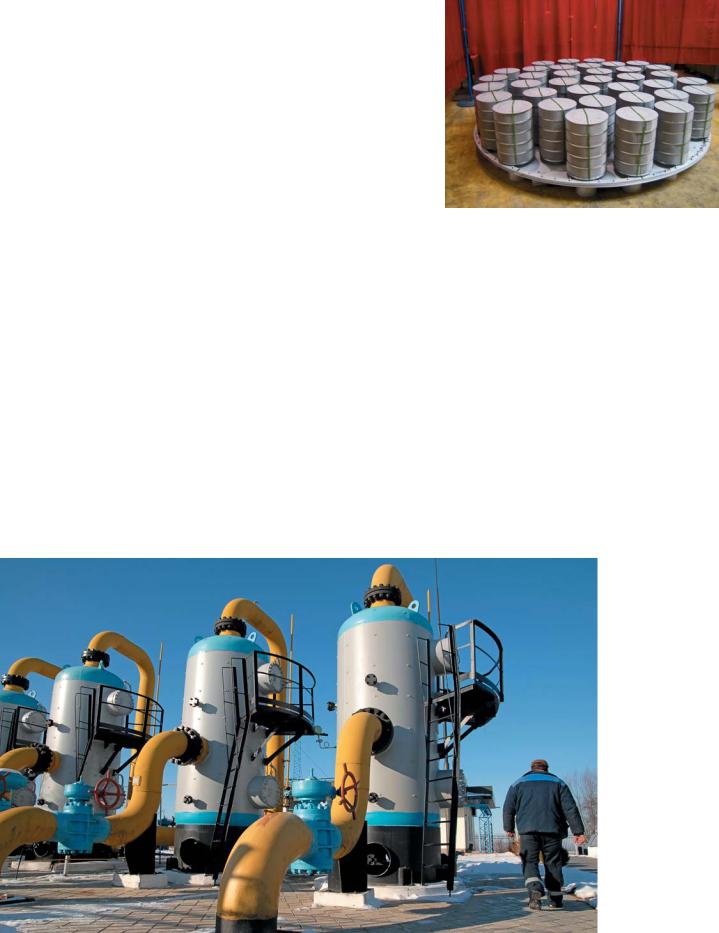
ПАНОРАМА
элементы, такие как Shell Swirltube компании Sulzer, разработаны для таких сложных эксплуатационных условий, однако для их монтажа необходимо относительно большая высота в сепараторе. При модернизации сепаратора для повышения производительности часто случается, что доступная высота ограничена. Кроме того, любые огневые работы на корпусе внутри колонны могут быть ограничены и не получиться установить дополнительные опорные элементы для сепарационных устройств.
Модернизация сепаратора для повышения производительности
Модернизация сепаратора потребовала применение высокопроизводительных сепарационных устройств. Тем не менее, доступная высота в сепараторе не позволила применить вихревые элементы Shell Swirltube и сетчатый коалесцер KnitMesh без значительных конструкционных модификаций сепаратора.
Применение пластинчатого каплеуловителя Mellachevron также потребовало бы внесения значительных
изменений в конструкцию сепаратора, поскольку только пластинчатый каплеуловитель подходил для достижения необходимой сепарационной эффективности. В итоге, заказчик предпочел применить сепарационные устройства Sulzer MKS Multi Cassette, поскольку это решение сочетает в себе все необходимые преимущества в одном изделии .
Sulzer MKS Multi Cassette явились отличным дополнением к семейству высокопроизводительных сепарационных устройств компании Sulzer Chemtech. Надежность и эффективность сепарационных устройств MKS подтверждена применением во многих колоннах осушки природного газа и сепараторах. С новым сепарационным устройством MKS Multi Cassette, компания Sulzer
Chemtech |
может |
предложить своим |
|
заказчикам |
äàæå |
более |
современные |
и специализированные |
решения для |
сложных процессов отделения капельной жидкости от газа. Кроме того, специалисты компании Sulzer Chemtech окажут необходимое содействие при монтаже и вводе в эксплуатацию оборудования.
Тарелка с сепарационными устройствами Sulzer MKS Multi Cassette™
Дэниэл Эггер (Daniel Egger)
Sulzer Chemtech AG Sulzer-Allee 48 8404 Winterthur Switzerland
Òåë.: +41 52 262 50 08 daniel.egger@sulzer.com
Газовая станция с несколькими сепараторами
24 | Sulzer Технический обзор 4/2009
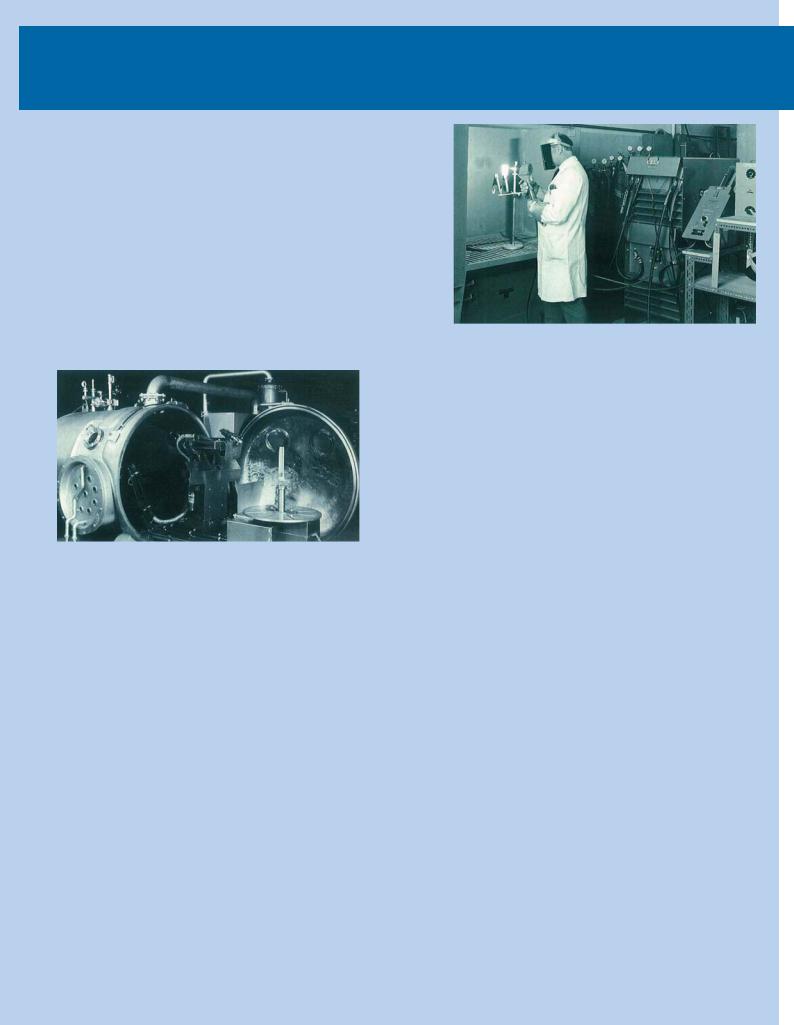
ИСТОРИЯ SULZER
История развития технологий нанесения покрытий
Сегодня подразделение Sulzer Metco включает несколько различных направлений. История компании берет свое начало в городе Винтертуре. В 1968 году небольшая группа исследователей начала изучать нанесение покрытий при помощи методов химического осаждения из газовой фазы (CVD) и газотермического нанесения. В настоящее время Sulzer Metco работает по всему миру и предлагает газотермическое и тонкопленочное нанесение как часть ее портфолио технологий защиты поверхностей и решений для клиентов
в авиации и автомобильной промышленности,
Одна из первых газотермических установок в Швейцарии
энергетике и других специализированных рынков.
Газотермическое оборудование низкого давления позволяет наносить покрытие на лопасти турбин
В 1968 году команда под руководством Ганса Бутлера (Hans Beutler) начала работу в новом исследовательском центре – в Лаборатории новых материалов. Ее сфера деятельности заключалась в разработке технологических процессов для лучшей защиты покрытий от износа и коррозии и для применения в продукции Sulzer новых материалов, используемых в строительстве самолетов и ракет.
Высококачественное покрытие
Основным стимулом их работы была необходимость поиска наилучших покрытий для тепловых турбомашин и необходимость соблюдения требований в сфере ядерной энергетики и ткацких станков. Указанные исследования были сосредоточены на процессе CVD, газотермическом нанесении покрытий и трибологии. С тех пор как стало возможным проводить несколько испытаний в день, газотермические технологии разрабатывались намного быстрее, чем методы CVD, с которым можно было проводить только одну серию
испытаний в день. В начале 1970-х велась интенсивная работа в сотрудничестве с BBC (сейчас ABB/Alstom) над разработкой высокотемпературных коррозионностойких покрытий для газовых турбин. Плазменное покрытиеSS14, разработанное командой Лаборатории Новых Материалов, являлось передовым. Данное покрытие для газотурбинных лопастей стало важным шагом вперед, который оказал существенное влияние на успех Департамента 15 (сегодня Sulzer Innotec) в последующие годы.
Основание компаний и приобретения
Компания Plasmatechnik AG была учреждена в Вохлене в 1970 году, примерно в то же самое время, что и Sulzer в Винтертуре, когда она делала свои первые шаги в области технологий нанесения защитных покрытий. В тесном сотруд-
ничестве с |
Sulzer, Plasmatechnik |
AG разработала сложные и очень |
|
эффективные |
системы плазмен- |
ного напыления с высокой производительностью и невысоким процентом брака. Данное предприятие было приобретено компанией Sulzer в 1985 году и стала частью группы компаний.
В 1986 году Sulzer приобрела компанию AMI, зарегистрированную в Мичигане. В результате, Sulzer не только расширила ассортимент своей продукции, в который вошли напыляемые материалы и напайка твердым припоем, но и укрепила свою репутацию и позиции в США. В 1991 году была приобретена калифорнийская компания Electro Plasma Inc.
Âконце 1970-х годов ее владелец Эрих Мюльбергер (Erich Mьhlberger)
– американский первопроходец в плазменном напылении – разработал сплавы MCrAlY, которые могли использоваться в стационарных газовых турбинах.
Â1994 году Sulzer приобрела подразделение Metco компании Perkin Elmer, головной офис которой находился в Нью-Йорке, и объединила все свои компании, задействованные в области создания материалов и технологий нанесения покрытий под именем Sulzer Metco. Metco была учреждена в 1933 году в США – в разгар Великой депрессии – выпускником Калифорнийского института технологий. Компания, начинавшая свою деятельность с пятью сотрудниками, превратилась в междуна-
родную организацию к 1994 году. В последующем были приобретены: Salzgitter AG в 1995; QCoat Ltd. в 1998; Eldim BV и Interturbine Coatings BV в 2000 году; Metaplas-
Ionon |
GmbH |
è EuroFlamm GmbH |
â 2001 |
ãîäó; |
Euroflamm Select Inc. |
и DB Thin Filmx LLC в 2002 году; а также WOKA GmbH, Ambeon, b OSU Maschinenbau GmbH в 2004 году.
На сегодняшний день Sulzer Metco предлагает широкий спектр технологий нанесения покрытий, которые, в сочетании с опытом компании, предоставляют клиентам превосходные технологии защиты поверхностей.
Габриэль Барросо (Gabriel Barroso)
Sulzer Технический обзор 4/2009 | 25
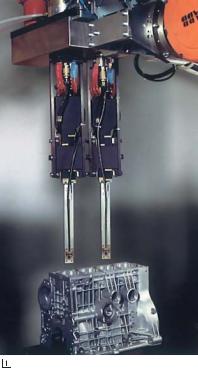
ПАНОРАМА
За гранью измерений
SUMEBore™ является полноценным решением, которое, в зависимости от области применения, придает особые свойства поверхностям цилиндров в двигателях внутреннего сгорания. Это может означать, например, уменьшение трения и увеличение стойкости к коррозии. Специалисты в области технологических линий компании Sulzer Innotec оказывают техническую поддержку при нанесении покрытия посредством компьютерного моделирования технологического процесса, позволяя визуально проверить и оценить состояние потока в цилиндре в процессе нанесения покрытия.
Sulzer Metco предлагает заказчикам не просто технологию нанесения покрытий, но и комплексное решение их проблем.
Дополнительные предложения позволяют нашим заказчикам просто и эффективно применять технологии нанесения покрытий.
SUMEBore™ является полноценным покрытием, которое, в зависимости от области применения, позволяет придавать особые свойства рабочим поверхностям цилиндров двигателей внутреннего сгорания.
Густые смазки
Густые смазки могут внедряться в покрытия при помощи порошков на основе железа и углерода.
Покрытие, нанесенное термическим напылением, обладает некоторой пористостью, благодаря которой моторное масло снижает трение, особенно при холодном запуске.
Такое покрытие обычно наносится посредством напыления материала RotaPlasma™, что является частью комплексного решения SumeBore.
При этом вращающаяся и охлаждаемая водой плазменная пушка с соплом Sulzer Metco F210 вставляется в цилиндр, подлежащий обработке . Плазменная пушка, работающая на электрической дуге, используется для разогрева газа или газовой смеси до температуры свыше 10000°C и ускорения молекул газа.
Частицы порошка плавятся на лету и, ударяясь о поверхность детали, образуют необходимое покрытие.
В зависимости от внутреннего диаметра обрабатываемого цилиндра
Покрытие литого алюминиевого блока цилиндров износостойким слоем
необходимо выполнить то или иное количество технологических циклов для получения необходимой толщины покрытия, составляющей примерно 200 μì.
Поскольку шероховатость поверхности составляет примерно 50 μм, покрытие должно пройти дополнительную обработку. В конечном итоге толщина покрытия должна достигнуть примерно 120 μì.
Температуры, превышающие 10000°C Поскольку температура струи плазмы превышает 10 000°C , обрабаты-
ваемая деталь подвергается высокотемпературному воздействию, однако при этом необходимо обеспечить точность геометрических параметров внутренней поверхности цилиндра.
Отверстия для ввода сжатого воздуха сделаны на задней стороне горелки F210 таким образом, что поверхности, находящиеся под струей плазмы, охлаждаются сразу после нанесения покрытия.
Сжатый воздух также используется для обеспечения оптимального направления струи плазмы в процессе обработки.
Дополнительная форсунка (ограждающий газ) также расположена на плазменной форсунке и служит для охлаждения деталей холодным газом (как правило, используется аргон) и ограждения их от потока горячей плазмы .
Для того, чтобы излишки нерасплавившегося порошка не образовали трещины в нанесенном покрытии, через отверстие цилиндра пропускается дополнительный аксиальный поток воздуха, который уносит все излишки порошка.
Задача такого моделирования заклю- чается в визуальном отображении потока внутри цилиндра и проверке возможности сокращения времени и материалов на выполнение процесса нанесения покрытия RotaPlasma.
Числовое моделировании потока
Для непрерывного улучшения данного технологического процесса, отношения комплексных потоков необходимо проанализировать в процессе работы.
26 | Sulzer Технический обзор 4/2009
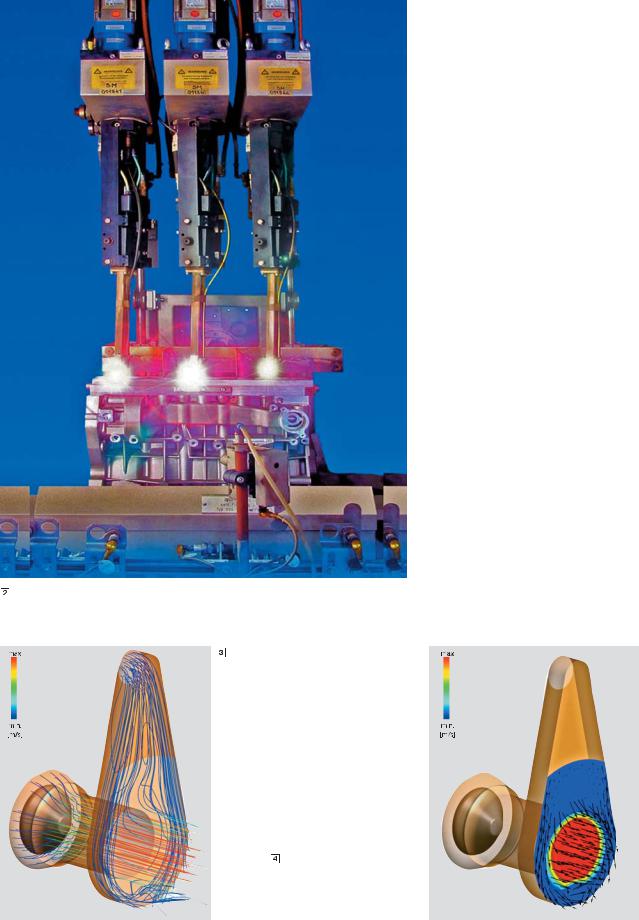
ПАНОРАМА
Однако высокие скорости и температуры данного процесса делают использование измерительных приборов практи- чески невозможным.
Для расширения нашего понимания данного процесса и для лучшего понимания отношений между потоками, был проведен анализ потоков (расчет динамики жидкости, CFD).
CFD настолько развито, что даже комплексные потоки можно визуально отобразить на бумаге.
Ионизированный газ ведет себя по-раз- ному при разных уровнях ионизации, при этом параметры его поведения требуют табличного хранения в программе моделирования данных о материалах в соответствии с температурой (до 30000°C) и давлением (до 10 атм.).
При помощи интерполяции рассчитываем точные свойства газа. Возможность установления прямого численного соотношения между моделью потока и электромагнитной системой (магнитная гидродинамика, MHD) была намеренно опущена в этом конкретном случае, поскольку основное внимание было уделено потоку в цилиндре.
Двухэтапное моделирование
Для повышения качества конвергенции данного числового анализа, взятые параметры были разбиты на две модели. На первом этапе горячий поток из форсунки был представлен посредством искусственного источника тепла .
Примерно 9 кВт обеспечивают достижение максимальных температур газа - 14000°C.
Влияние форсунки холодного газа так-
Плазма в ходе выполнения процесса нанесения покрытия
Дополнительная форсунка охлаждающего газа расположена над плазменной форсункой для защиты деталей от потока горячей плазмы. На рисунке показаны линии потока
Моделирование горячего и холодного потоков из форсунок. Поперечное сечение на выходе из форсунки с визуальным отображением температуры (цвета) и скорости (стрелки)
Sulzer Технический обзор 4/2009 | 27
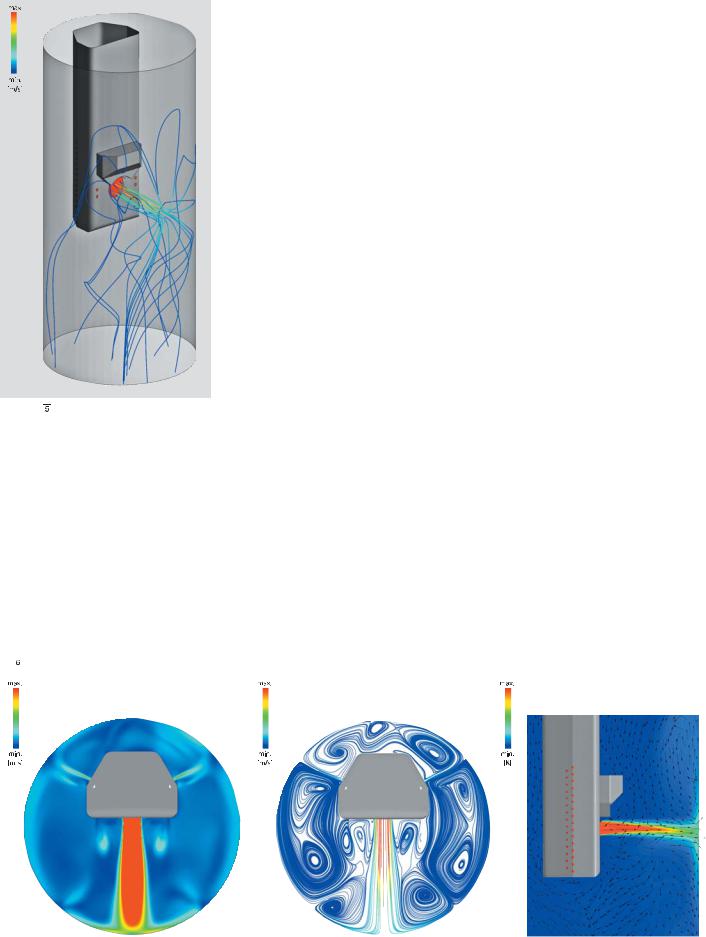
ПАНОРАМА
Визуальное отображение потока в ходе нанесения покрытия: объемный вид линий потока из
же принималось в расчет на данном, первом, этапе моделирования. Расчетное состояние потока на выходе из форсунки (скорость, температура и турбулентность) было затем использовано в модели потока в ка- честве входного значения.
Для минимизации затрат на моделирование и сокращения времени рас- чета, при расчете было принято, что вращение выполняется равномерно, а стенка цилиндра неподвижна.
Такие допущения позволили выполнить оценку параметров потока в цилиндре при равномерном вращении.
При помощи такого анализа CFD стало возможным визуально отобразить состояние потока в пределах зеркала цилиндра в процессах ,
.
Предварительно проведенные испытания напыления показали влияние давления сжатого воздуха на конеч- ное качество покрытия.
По этой причине моделирование было выполнено с двумя различными давлениями.
Если давление сжатого воздуха будет слишком высоким, площадь воздействия холодного воздуха переместится вперед по периферии стенок цилиндра в направлении покрываемой зоны и будет взаимодействовать непосредственно со струей плазмы в том месте, где она попадает на стенку цилиндра.
Это приведет к сильной нестабиль-
ности условий потока в процессе нанесения покрытия и может отрицательно сказаться на качестве готового покрытия.
Это может даже привести к тому, что частицы, которые уже были расплавлены в плазме, снова станут твердыми до попадания на стенку, и покрытие получит недопустимые дефекты.
Обширный опыт в выполнении данного процесса
Полученные результаты привели к разработке новых ноу-хау и адаптации отдельных параметров технологического процесса.
Геометрическая оптимизация пушки F210 не проводилась. Тем не менее, приобретенные знания будут реализованы в разработке новых изделий. В условиях постоянно растущих вы- числительных возможностей и появления все более точных моделей, числовое моделирование потока за последнее десятилетие переросло в очень важный проектный инструмент и стало незаменимым для процесса разработки изделий Sulzer.
Рето Вагер (Reto Wäger)
Sulzer Markets and Technology Ltd
Sulzer Innotec
Sulzer-Allee 25
8404 Winterthur Switzerland
Òåë.: +41 52 262 42 50 reto.waeger@sulzer.com
Визуальное отображение потока в ходе нанесения покрытия
Горизонтальное поперечное сечение |
Горизонтальное поперечное сечение |
Вертикальное поперечное сечение |
(скорость) |
(линии потока) |
(температура) |
|
|
|
28 | Sulzer Технический обзор 4/2009