
3643
.pdf
Russian Journal of Building Construction and Architecture
The concrete mix was prepared in the following steps:
1)50 % of the design amount of the cement was preliminarily mixed with the hydration water containing the superplasticizer “Relamix Т-2”;
2)the resulting slurry was loaded into a PRE bunker and exposed to hydromechanochemical activation for 2 min;
3)then the resulting cement slurry was loaded into PRE, the remainder of the cement was added as well as large and fine fillers;
4)the components of the concrete mix were mixed into a concrete mixer for 5 min [6].
The cube samples sized 10 × 10 × 10 сm were prepared from the concrete mixes. After 1, 3, 7 and 28 days of normal humidity hardening the samples were exposed to mechanical testing. The strength of the samples was identified in accordance with the GOST (ГОСТ) 18105-2010. Frost resistance of heavy concrete was identified in accordance with the GOST (ГОСТ) 10060-2012 harmonized in compliance with EN 12390-9:2006. The indices of the porous structure were identified in accordance with the GOST (ГОСТ) 12730.4-78.
Sulfate resistance of the cement composition s was identified using sample beams sized 4 × 4 × 16 cm prepared from a cement and sand solution with the cement : sand ratio = 1 : 3. The sulfate resistance coefficient Кс was identified by means of comparing the composition s solidified in water environment with those solidified in a 5 % Na2SO4 solution. The experiment was conducted for 180 days. The kinetics of heat emission of the cement paste was identified using a temperature logger Thermochron DS1921G.
3. Results and discussion. The results of the effect of the mix, hydromechanoactivation of the cement slurry on the kinetics of hardening of heavy concrete are shown in Fig. 1. The investigated composition s are 1 is control one; 2 is the composition modified using the supplement Relamix Т-2”; 3 is the composition exposed to hydromechanical activation with no superplasticizer; 4 is the composition obtained by means of hydromechanoactivation of the cement slurry with Relamix Т-2.
Fig. 1 suggests that the largest amount of the compression strength limit was observed throughout the entire hardening of cement in the composition № 4 (by 60––249 % compared with the control one) particularly on the first day of hardening.
Hydromechanoactivation of cement (composition № 3) causes a significant increase in the concrete strength compared to the composition № 2 modified with the superplasticizer.
In this respect the authors [34] argue that hydromechanochemical activation leads to a 30 to 100 % increase in the strength of cement somposites on the first day of hardening, from 0 to 70 % after 28 days.
50
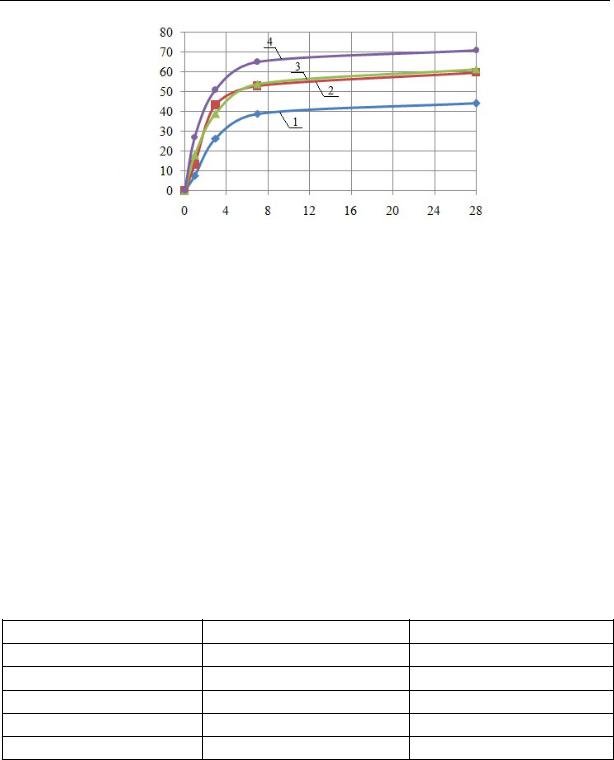
Issue № 3 (43), 2019 ISSN 2542-0526
MPa
Compression strength limit,
Length of hardening, days
Fig. 1. Kinetics of hardening of heavy concrete.
Compositions: 1 is a control one; 2 is the composition modified with Relamix Т-2; 3 is the composition exposed to hydromechanical activation with no superplasticizer;
4 is the composition obtained following hydromechanoactivation of the cement with Relamix T-2
Acceleration of cement hydration during hydromechanochemical activation of cement might by due to particle dispersion. In order to determine the specific surface and dispersion composition of the cement samples and aggregate minerals, the following compositions were investigated: 1 is the original Portland cement; 2 is the composition without the supplement and hydromechanoactivation; 3 is the composition exposed to hydromechanoactivation; 4 is the composition with Relamix T-2; 5 is the composition exposed to hydromechanochemical activation with Relamix T-2. The results of the experiment are presented in Table 1 and Fig. 2.
Таble 1
Average size of the particles and specific surface of the investigated samples
Number of the composition |
Average size, mkm |
Specific surface, m2/kg |
1 |
48.47 |
298.33 |
2 |
45.87 |
324.66 |
3 |
38.35 |
356.35 |
4 |
42.25 |
331.62 |
5 |
17.10 |
427.84 |
Table 1 suggests that the specific surface of the cement samples and aggregate minerals exposed to hydromechanoactivation (composition № 3) increased by 10 % compared to the composition with no activation (composition № 2). Due to hydromechanoactivation of cement with Relamix T-2 (composition № 5) the specific surface of the cement and aggregate minerals increased by 29 % compared to the composition obtained simply with the use of Relamix T-2 (composition № 4).
51
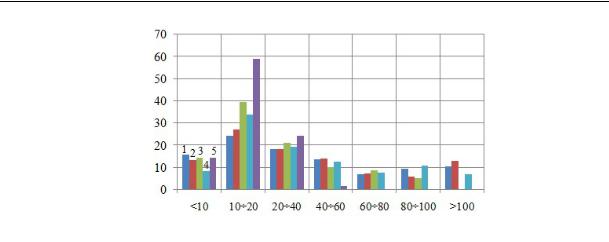
Russian Journal of Building Construction and Architecture
Fraction size, mkm
Fraction size, mkm
Fig. 2. Granulometric composition of the investigated samples. Compositions: 1 is the original Portland cement;
2 is the composition with and without hydromechanoactivation;
3 is the composition exposed to hydromechanoactivation; 4 is the composition with Relamix T-2; 5 is the composition exposed to hydromechanochemical activation with Relamix T-2
The average size of the particles of the original Portland cement (composition № 1) is 1.26 times larger than the cement and aggregate mineral particles exposed to hydromechanoactivation (composition № 3) and 2.8 times larger than that of the particles exposed to hydromechanoactivation (composition № 5).
As seen from Fig. 2, the fractions of less than 10 mkm in all the investigated compositions is not significantly different. Following hydromechanoactivation of cement the fraction output from 10 to 20 mkm increased by 1.62 times compared to the original Portland cement. During hydromechanoactivation of the binder the fraction output from 10 to 20 mkm increases by 2.43 times compared to the original Portland cement. Following hydromechanoactivation there were no powder particles larger than 60 mkm.
In [3] using the PRE equipment the cement was ground to the average of 28.7 mkm. A varying dispersion is associated with different types of Portland cement and treatment time.
An increase in the strength of the cement compositions is of research interest and can be employed to enhance the durability of the investigated compositions. In order to evaluate the effect of hydromechanoactivation of cement on the durability of the cement compositions the frost resistance and indices of the porous structure of heavy concrete was determined (Table 2) as well as sulfate resistance of the cement and sand solution (Table 3). The numbers of the compositions in Table 2 and Table 3 are given according to Fig. 1.
According to Table 2, hydromechanoactivation of cement causes a dramatic increase in the frost resistance of heavy concrete (to grade F600), which is due to a 39 % drop in the total porosity, a 74.8 % drop in the capillary porosity and a 53 % increase in the proportion of the closed pores.
52
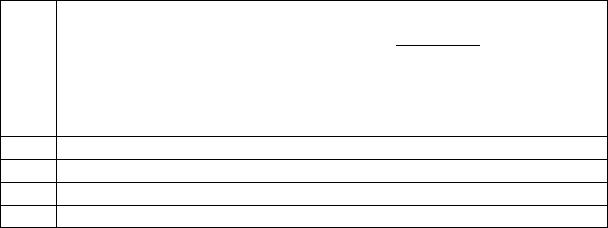
Issue № 3 (43), 2019 |
ISSN 2542-0526 |
|
|
|
|
|
|
|
|
|
|
|
|
|
|
|
Таble 2 |
|
|
|
|
Indices of the porous structure and frost |
resistance of heavy concrete |
|
|
||||||||
|
|
|
|
|
|
|
|
|
|
|
|
|
|||
compositiontheofNumber |
Water absorption according |
Homogeneity sizeporetheof |
sizeAverage pores,theof (*100) |
volumeTotal porestheof |
theofVolume capillaryopen pores |
theofVolume |
capillaryclosed pores |
Microporosity index |
resistanceFrostgrade F |
||||||
min15 |
|
min30 |
|
hour1 |
hour24 |
||||||||||
|
|
to the mass, %, after |
|
|
Indices of the porous structure |
|
|
||||||||
|
|
|
|
|
|
|
|
|
|
|
|
|
|
|
|
1 |
2.5 |
|
3.2 |
|
3.5 |
|
4.5 |
0.34 |
55.4 |
14.4 |
12.7 |
|
1.7 |
2.0 |
200 |
|
|
|
|
|
|
|
|
|
|
|
|
|
|
|
|
2 |
1.9 |
|
2.3 |
|
3.0 |
|
3.6 |
0.62 |
34.2 |
9.4 |
7.4 |
|
2.0 |
1.6 |
300 |
|
|
|
|
|
|
|
|
|
|
|
|
|
|
|
|
3 |
1.1 |
|
1.8 |
|
2.6 |
|
3.4 |
0.66 |
31.8 |
8.1 |
5.8 |
|
2.3 |
1.5 |
400 |
|
|
|
|
|
|
|
|
|
|
|
|
|
|
|
|
4 |
0.8 |
|
1.5 |
|
1.9 |
|
3.1 |
0.72 |
25.5 |
5.8 |
3.2 |
|
2.6 |
0.8 |
600 |
|
|
|
|
|
|
|
|
|
|
|
|
|
|
|
|
Table 3 suggests that hydromechanoactivation of the binder causes a 40 % increase in the sulfate resistance of the cement solution compared to the control composition (composition 1) and a 10 % one compared to the composition 2 modified with Relamix T-2 and thus an increase in the frost resistance in corrosive environments.
An increase in the physical and mechanical properties of the cement composites is associated with morphology changes and hydrate growth of the cement stone.
Number of the composition
1
2
3
4
|
|
|
|
|
|
|
|
Таble 3 |
|
|
Sulfate resistance test of the cement and sand solution |
|
|
|
|||||
Average density |
|
|
Bending strength limit, МPа |
|
Compression strength limit, |
|
|
||
|
|
|
|
|
|||||
|
|
|
|
|
МPа |
|
|
||
of the cement and |
|
Water/ |
|
|
|
|
|
|
|
|
In the 5 % |
|
|
In the 5 % |
|
Кс |
|||
sand solution, |
|
Cement |
|
solution |
|
|
solution |
|
|
|
In the water |
|
In the water |
|
|
||||
kg/m3 |
|
|
of the natrium |
|
of the natrium |
|
|
||
|
|
|
|
sulfate |
|
|
sulfate |
|
|
2343 |
|
0.50 |
7.03 |
4.78 |
52.2 |
35.5 |
|
0.68 |
|
2365 |
|
0.355 |
8.05 |
6.92 |
66.8 |
57.5 |
|
0.86 |
|
2374 |
|
0.50 |
7.44 |
6.70 |
67.2 |
60.5 |
|
0.90 |
|
2389 |
|
0.355 |
8.73 |
8.29 |
71.2 |
67.6 |
|
0.95 |
|
|
|
|
|
|
|
|
|
|
|
In order to determine the nature of the hydrate growth X-ray phase analysis of the investigated samples from 1 to 28 days was conducted. According to the X-ray phase analysis results using the Rietveld method Table 4 was composed where the mineral composition of the investigated samples from 1 to 28 days is shown.
53

Russian Journal of Building Construction and Architecture
|
|
|
|
|
|
|
|
|
|
|
Таble 4 |
|
|
|
Mineral composition of the investigated samples |
|
|
|
|||||
|
|
|
|
|
|
|
|
|
|
|
|
theofNumbercomposition* |
|
|
|
|
Mineral composition, % |
|
|
|
|
||
theofAgesample, days |
|
|
|
|
|
|
|
|
|
Total,% |
|
SiO |
Ca |
Ca |
|
Ca |
Ca(OH) |
Ca |
CaCO |
Ca |
|||
|
|
|
O |
|
|
|
|
|
|
|
|
|
|
|
2 |
|
|
|
|
|
|
|
|
|
|
2 |
∙ 26H |
4 |
|
2 |
2 |
SiO |
3 |
O |
|
|
|
3 |
Ca2SiO - α |
|
Fe |
4 |
|
||||
|
|
|
|
|
|
5 |
|
|
|
|
|
|
|
|
12 |
|
|
O |
|
|
|
2 |
|
|
|
|
|
|
) |
|
|
|
|
||
|
|
|
(OH) |
4 |
|
+3 |
|
5 |
|
∙2H |
|
|
|
|
4 |
|
(Al, |
|
3 |
|
SO |
|
|
|
|
|
) |
SiO |
|
|
|
|
|
|
|
|
|
|
(SO |
|
2 |
|
|
|
2 |
|
|
|
|
|
2 |
2 |
|
|
|
|
|
|
|
|
|
|
Al |
|
|
|
|
|
|
|
|
|
|
|
6 |
|
|
|
|
|
|
|
|
|
|
|
|
|
|
|
|
|
|
|
|
1 |
1 |
2.41 |
9.07 |
13.00 |
|
13.83 |
8.64 |
53.05 |
– |
– |
100 |
|
|
|
|
|
|
|
|
|
|
|
|
28 |
2.78 |
8.90 |
11.33 |
|
15.75 |
11.69 |
34.45 |
15.10 |
– |
100 |
|
|
|
||||||||||
|
|
|
|
|
|
|
|
|
|
|
|
2 |
1 |
3.73 |
9.41 |
10.34 |
|
14.38 |
3.30 |
55.66 |
– |
3.18 |
100 |
|
|
|
|
|
|
|
|
|
|
|
|
28 |
2.57 |
10.77 |
11.74 |
|
15.77 |
23.74 |
25.69 |
9.72 |
– |
100 |
|
|
|
||||||||||
|
|
|
|
|
|
|
|
|
|
|
|
3 |
1 |
4.91 |
10.12 |
16.85 |
|
13.78 |
9.52 |
44.82 |
– |
– |
100 |
|
|
|
|
|
|
|
|
|
|
|
|
28 |
2.61 |
8.91 |
11.56 |
|
19.91 |
17.88 |
27.04 |
12.09 |
– |
100 |
|
|
|
||||||||||
|
|
|
|
|
|
|
|
|
|
|
|
Note: *1 is the control composition; 2 is the composition with Relamix Т-2; 3 is the composition following hydromechanoactivation with Relamix Т-2.
According to Table 4, the largest amount of the ettringite (Ca6Al2(SO4)3(OH)12∙26H2O) is formed in the composition № 3, which is 12 % more compared to the control composition (composition № 1). It is known that in the saturated solution Са(ОН)2 the ettringite is first released in the colloid fine-dispersion state precipitating on the surface of the particles 3СаО-А12О3, slows down their hydration and enhances cementation [17].
In the composition № 3 exposed to hydromechanoactivation there is the least original alit mineral (Ca3SiO5), which is 16 % less compared to the control composition, which indicates a more complete cement hydration and causes a larger compression strength of heavy concrete in the first days of hardening.
An increase in the calcium hydroxide (Ca(OH)2) in the solidifying stone composition, which is the hydrolysis product of the original materials, indicates faster cement hydration. In the composition № 3 there is the most calcium hydroxide. According to the results of the quantitative analysis, the content of Ca(OH)2 in the composition № 3 is 10 % larger compared to the composition № 1 and 2.88 times compared to the composition № 2. At the grade age of the investigated samples there is an increase in the calcium hydroxide (Ca(OH)2) with the most calcium hydroxide in the composition № 2 and the least in the composition № 1.
54
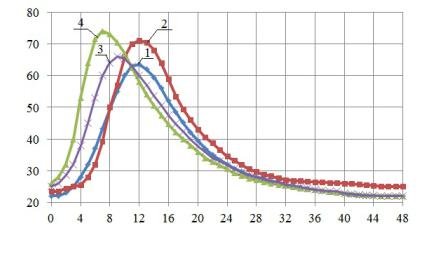
Issue № 3 (43), 2019 |
ISSN 2542-0526 |
The least original aggregate phases are in composition № 3: the content of Ca3SiO5 drops by 1.66 times, the content of Ca2SiO4 α-Ca2SiO4 by 1.47 times, which indicates a more complete cement hydration. In the composition № 3 there is a 23 % increase in the content of the crystal phase compared to the composition № 2.
An increase in the compression strength limit of the investigated compositions particularly during the first days of hardening is due to that in the specific surface of the cement powder samples and a drop in the average size of the cement particles. In order to determine the nature of cement hydration of the investigated samples a test was conducted to identify the kinetics of heat emission of the cement paste by means of the thermal calorimetry method (Fig. 5).
Temperature, ° C
Length of hydration, hours
Fig. 5. Kinetics of heat emission of the cement paste.
Numbers of the compositions correspond to those in Table 1
Fig. 5 shows that hydromechanochemical cement activation increases the hydration temperature by 20––25 °С accompanied with a 4––5 hour shift of the temperature maximum to the left, which makes cement hydration more intense. As Relamix Т-2 is introduced, the hydration of the cement paste slows down in the first hours (composition № 2) accompanied by a 2 hour shift of the temperature maximum.
Conclusions
1.Hydromechanical activation of cement in pulsed rotary equipment with the superplasticizer Relamix T-2 causes a dramatiс increase in the compression strength limit of concrete particularly in the first days of hardening.
2.The specific surface of the cement samples and aggregate minerals obtained following hydromechanochemical activation increases by 29 % compared to the control composition,
55

Russian Journal of Building Construction and Architecture
the average size decreases, the amount of cement particles and aggregate minerals sized less than 20 mkm increases by 1.34 times.
3.The frost resistance of heavy concrete obtained by means of hydromechanochemical activation of cement increases by a few steps (to grade F600), which is due to a 39 % decrease in the total porosity, a 74.8 % decrease in the proportion of the open capillary pores and a 53 % increase in the proportion of the closed pores. The sulfate resistance coefficient of the cement and sand solution increases by 40 %, which indicates an increase in the strength of a cement compostion obtained by means of the method including hydromechanochemical activation of cement.
4.The phase composition of the cement stone obtained following hydromechanochemical activation is characterized by a high content of the ettringite (Ca6Al2(SO4)3(OH)12∙26H2O) and a low content of the original phases of the Portland cement.
5.Obtaining rapid-hardening concrete by means of the method including hydromelchanochemical activation of cement in pulsed rotary equipment allows one to reduce resource and energy costs due to shorter hardening times in timbering of concrete foundations in monolith construction or shorter thermal treatment of concrete structures at ferroconcrete plants.
References
1.Avvakumov E. G., Gusev A. A. Mekhanicheskie metody aktivatsii v pererabotke prirodnogo i technogennogo syr'ya [Mechanical methods of activation in the processing of natural and man-made raw materials]. Novosibirsk, Geo publishers Publ., 2009. 155 p.
2.Bazhenov Yu. M. Tekhnologiya betona [Concrete technology]. Moscow, ASV Publ., 2002. 500 p.
3.Gorn K. S., Viktorov A. V. Osobennosti gidratatsii tsementnoi kompozitsii, aktivirovannoi v rotornopul'satsionnom apparate [Features of hydration of the cement composition activated in the rotor-pulsation apparatus]. Polzunovskii Vestnik, 2011, no. 1, pp. 56––58.
4.Mukhametrakhimov R. Kh., Galautdinov A. R. Mekhanoaktivirovannoe gipsotsementno-putstsolanovoe vyazhushchee na osnove modifitsirovannogo nizkomarochnogo syr'ya [Mechanoactivated gypsum cementpozzolan binder based on modified low-grade raw materials]. Izvestiya Kazanskogo gosudarstvennogo arkhitekturno-stroitel'nogo universiteta, 2018, no. 1 (43), pp. 187––195.
5.Naidenov Yu. A., Veprinyak I. A. Innovatsionnaya tekhnologiya aktivirovaniya betonov, osnovannaya na yavlenii kavitatsii [Innovative technology of concrete activation based on the cavitation phenomenon]. Nauka XXI vek, 2013, no. 4. Available at: http://nauka21vek.ru/archives/48707.
6.Izotov V. S., Ibragimov R. A., Pimenov S. I., Galiullin R. R. Sposob prigotovleniya betonnoi smesi [Method of preparation of concrete mix]. Pat. RF, № 2559236, 2015.
7.Pimenov S. I., Ibragimov R. A., Izotov V. S. Vliyanie gidromekhanokhimicheskoi aktivatsii tsementnoi suspenzii na fiziko-mekhanicheskie svoistva tyazhelogo betona [Effect of hydro-mechanochemical activation of cement slurry on the physical and mechanical properties of heavy concrete]. Izvestiya vuzov. Stroitel'stvo, 2014, no. 11 (671), pp. 16––21.
56
Issue № 3 (43), 2019 |
ISSN 2542-0526 |
8.Pimenov S. I., Ibragimov R. A. Ispytaniya besproparochnogo sposoba proizvodstva sbornogo zhelezobetona [Testing of non-welded method of production of precast concrete]. Bezopasnost' zhiznedeyatel'nosti, 2017, no. 5 (197), pp. 32––35.
9.Prokopets V. S. Vliyanie mekhanicheskogo vozdeistviya na aktivnost' vyazhushchego veshchestva [Effect of mechanical action on the activity of the binder]. Stroitel'nye materialy, 2003, no. 9, pp. 28––29.
10.Ahmad S., Shah A., Ali K. Effect of water reducing concrete admixtures on the properties of concrete. 29th Conference on our world in concrete structures. Singapore, 2004. – Available at: https://www.researchgate.net/publication/260226968_Effect_of_water_reducing_concrete_admixtures_on_the_properties_of_concrete.
11.Alsadey S. Effect of Superplasticizer on Fresh and Hardened Properties of Concrete. Journal of Agricultural Science and Engineering, 2015, vol. 1, no. 2, pp. 70––74.
12.Alsadey S. Effects of Super Plasticizing and Retarding Admixtures on Properties of Concrete. International Conference on Innovations in Engineering and Technology. Bangkok, 2013. Available at: http://iieng.org/images/proceedings_pdf/9117E1213607.pdf.
13.Arjunan P., Silsbee M. R., Roy D. M. Chemical activation of low calcium fly ash: Part 1. Identification of suitable activators and their dosage. 2001 International ash utilization symposium. Kentucky, 2001. P. 342––349.
14.Assaad J. J., Asseily S. E. Use of water reducers to improve grindability and performance of Portland cement clinker. ACI Materials Journal, 2011, vol. 108, no. 6, pp. 619––627.
15.Barabash I. V. The mechanical activation of mineral binder. Odessa, Astroprint Publ., 2002. 100 p.
16.Bids V. A., Kutugin V. A. Physical and chemical processes in the activation of cement-sand mixture in a centrifugal mixer. Proc. of the universities. Physics, 2011, vol. 54, no. 11/3, pp. 346––349.
17.Do Q. H. Modelling properties of cement paste from microstructure: porosity, mechanical properties, creep and shrinkage: Thèse № 5881. Suisse, 2013. 163 p.
18.Fathollah S. Applied Activation Techniques on Cement-Slag Mortars and Concretes. Activation techniques, 2012. 301 p.
19.Fathollah S. Mechanical activation of cement-slag mortars. Construction and Building Materials, 2012, no. 26 (1-1), pp. 41––48.
20.Heller T., Müller T., Honert D. Cement additives based on PCE. ZKG International, 2011, no. 2, pp. 40––48.
21.Ibragimov R. A., Pimenov S. I., Kyamov I. e. a. Comparison of the effect of superplasticizing admixtures on the processes of cement hydration during mechanochemical activation. Eastern-European Journal of Enterprise Technologies, 2016, no. 6 (82), pp. 56––63.
22.Justs J., Shakhmenko G., Mironovs V., Kara P. Cavitation treatment of nano and micro filler and its effect on the properties of UHPC. Ultra-High Performance concrete and nanotechnology in construction, 2012, no. 19. Available at: https://www.researchgate.net/publication/321026193_Cavitation_treatment_of_nano_and_micro_filler_and_its_effect_on_the_properties_of_UHPC.
23.Katsioti M. e. a. Characterization of various cement grinding aids and their impact on grindability and cement performance. Construction Building Materials, 2009, vol. 23, no. 5, pp. 1954––1959.
24.Kennedy D. P. A study to determine and quantify the benefits of using power ultrasound technology in a precast concrete manufacturing environment. Ireland, Trinity College Dublin, 2012.
25.Kriskova L., Pontikes Y., Zhang F. e. a. Influence of mechanical and chemical activation on the hydraulic properties of gamma dicalciumsilicate. Cement and Concrete Research, 2014, vol. 55, pp. 59––68.
57

Russian Journal of Building Construction and Architecture
26.Kumar S. e. a. Mechanical activation of granulated blast furnace slag and its effect on the properties and structure of Portland slag cement. Cement & Concrete Composites, 2008, vol. 30, no. 8, pp. 679––685.
27.Masoero E., Thomas J. J., Jennings H. M. A reaction zone hypothesis for the effects of particle size and wa- ter-to-cement ratio on the early hydration kinetics of C3S. Journal of the American Ceramic Society, 2014, no. 97, pp. 967––975.
28.Mishra R. K., Heinz H., Müller T. e. a. Understanding the Effectiveness of Polycarboxylates as Grinding Aids. American Concrete Institute Symposium Series, 2012, vol. 288, pp. 235––251.
29.Mukhametrakhimov R. Kh., Galautdinov A. R., Lukmanova L. V. Influence of active mineral additives on the basic properties of the gypsum cement-pozzolan binder for the manufacture of building products. MATEC Web of Conferences, 2017, no. 106, pp. 1––6.
30.Plotnikov V.V. Improvement of cement composition mechanochemical activation effectiveness in the aquatic environment: Thesis. Moscow, 2000. – 427 p.
31.Pohl M., Obry S., Zysk K.-H. Operating experience with a vertical roller mill for grinding blastfurnace slag and composite cements. Cement international, 2012, vol. 10, no. 2, pp. 56––69.
32.Sayer S. M., Dahlin A. Propagation of ultrasound through hydrating cement parts at early times. Advance cement based materials, 1993, no. 1, pp. 12––21.
33.Sekulic Z. e. a. Mechanical activation of cement with addition of fly ash. Materials Letters, 1999, vol. 39, no. 2, pp. 115––121.
34.Sobolev K. Mechano-chemical modification of cement with high volumes of blast furnace slag. Cement & Concrete Composites, 2005, no. 27, pp. 848––853.
35.Souria A., Kazemi-KamyabbH., SnellingsbR., NaghizadehaR., Golestani-FardaF., Scrivenerb K. Pozzolanic activity of mechanochemically and thermally activated kaolins in cement. Cement and Concrete Research, 2015, vol. 77, pp. 47––59.
36.Temuujin J., Mackenzie K. J. D., Schmucker M. e. a. Phase evolution in mechanically treated mixtures of kaolinite and alumina hydrates (gibbsite and boemite). J. Europe Ceram. Soc., 2000, vol. 20, pp. 413––421.
37.Teoreanu I., Guslicov G. Mechanisms and effects of additives from the dihydroxy-compound class on Portland cement grinding. Cement and Concrete Research, 1999, vol. 29, pp. 9––15.
38.Weibel M., Ratan K. M. Comprehensive understanding of grinding aids. ZKG International, 2014, no. 6, pp. 28––39.
39.Yamada K. e. a. A summary of important characteristics of cement and superplasticizers. Ninth ACI International Conference on Superplasticizers and Other Chemical Admixtures in Concrete. Seville, 2009. P. 153––164.
40.Zhang Y. M., Napier-Munn T. J. Effects of particle size distribution, surface area and chemical composition on Portland cement strength. Powder Technology, 1993, no. 83, pp. 245––252.
58
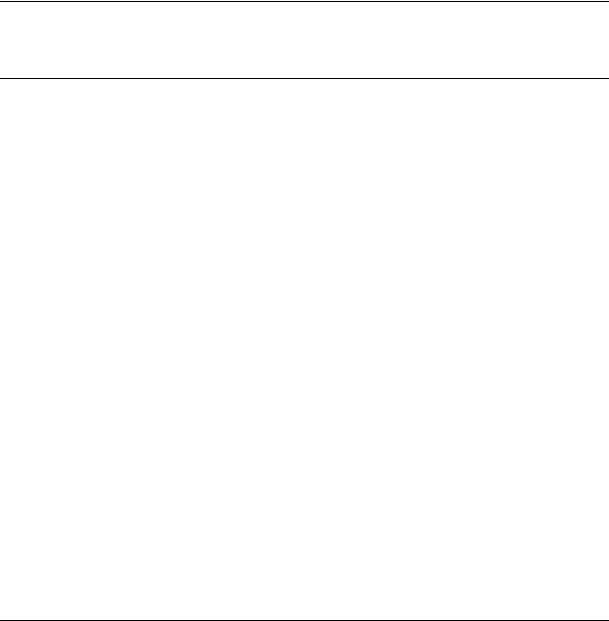
Issue № 3 (43), 2019 |
ISSN 2542-0526 |
DOI 10.25987/VSTU.2019.3.43.005
UDC 691.32
M. L. K. Khouadjia1,C. Belebchouche2, L. BensacI-Chibane3
CHARACTERIZATION OF RECOVERY FILLER FROM HOT-MIX ASPHALT PLANTS AND ITS EFFECT ON THE WORKABILITY AND COMPRESSIVE STRENGTH OF CONCRETE
University of Constantine 11, 2, 3
Constantine, Algeria
1D. Sc. in Civil Engineering. Assoc. Prof., tel. (213)559-333-376, e-mail: lyes.khouadjia@umc.edu.dz
2D. Sc. in Civil Engineering. Assoc. Prof., tel. (213)661-456-371, e-mail: belebchouche.cherif@gmail.com 3PhD in Civil Engineering. Assoc. Prof., tel. (213)550-323-867, e-mail: chibanelamria@gmail.com
Statement of the problem. The production of building materials in Algeria and the rest of the world is accompanied by the production of waste that can potentially pollute the environment. While there is an urgent need for recycling in developing countries, many waste products are not being recycled yet. Among these materials is recovery filler (RF), an abundant byproduct in the manufacturing of road bitumen mix. The principal objective of this study is to validate the use of recovery filler (RF) in ordinary concrete.
Results. The slump and compressive strength of concrete both before and after freeze-thaw cycles were examined. Recovery filler (RF) was scanned using scanning electron microscopy (SEM) to develop an advanced characterization of RF from HMA plants using two software packages: Aphelion Lab 4.4 and Astra 1.6.
Conclusions. The results showed that it is possible to obtain good workability and compressive strength when replacing cement with a 10% of recovery filler from hot-mix asphalt plants providing that superplasticizer is used.
Keywords: recovery filler, road bitumen mix, concrete slump, compressive strength, freeze-thaw cycles, Aphelion Lab 4.4, Astra 1.6.
Introduction. Currently, concrete is the most common material used in the construction industry. Due to the environmental and economic challenges that arise from its use, it is necessary to carry out research on the reuse and recycling of materials. Important types of waste and unused materials that have been used to improve the behavior and durability of concrete and asphalt concrete include dune and river sands, filler, fly ash, slag, metakaolin, pozzolan, silica fume and shungite [1––6].
© Khouadjia M. L. K.,Belebchouche C., BensacI-Chibane L., 2019
59