
2798
.pdf
трик). Это аморфный полимер с нулевой степенью кристалличности с температурой стеклования Тст 90-110 оС, поэтому полистирол обладает наиболее низкой среди конструкционных термопластичных материалов ударной прочностью - стандартная ударная вязкость его не превышает 20 кДж/м2 при испытаниях образца без надреза и 2,5 кДж/м2 при испытаниях образца с надрезом. Это ограничивает применение его в изделиях, подвергаемых динамическим нагрузкам.
Ударопрочный полистирол получают методом полимеризации стирола с бутадиеновым или бутадиенстирольным каучуком.
Известны несколько марок ударопрочных полистиролов, отличающихся количеством эластифицирующих элементов и различных добавок (марки УПС, УПМ, УПК).
В табл.2.5 приведены некоторые физико-механические свойства ударопрочного полистирола марок УПС-825 ТГ и УПМ-1003. Дополнительные данные о различных свойствах ударопрочных ПС различных марок можно узнать в /4/.
Таблица 2.5
Основные свойства ударопрочных полимеров
|
Ударопроч- |
АВС- |
ПК моди- |
|
ный ПС |
пластик |
фициро- |
Показатели |
(УПС-825 ТГ, |
(АВС- |
ванный |
|
УПМ-1003) |
1106ЭАО, |
(ПК-М-1) |
|
|
АВС-1002Т) |
|
1 |
2 |
3 |
4 |
Модуль упругости |
|
|
|
при изгибе, Мпа |
2000-2500 |
- |
- |
Прочность, Мпа: |
|
|
|
при растяжении |
20-25 |
25-40 |
60-70 |
при изгибе |
35-60 |
- |
70-80 |
61

Продолжение табл.2.5
1 |
2 |
3 |
4 |
Относительное |
|
|
|
удлинение, % |
15-35 |
20 |
20-60 |
Ударная вяз- |
|
|
|
кость, кДж/м2: |
|
|
|
исходная, |
30-60 |
70 |
101-135 |
с надрезом |
6-9 |
8-9 |
20-56 |
v Ом м; |
1014 |
1014 |
1015 |
s Ом |
1013 |
1012 |
1016 |
при 106 Гц; |
2,6-2,7 |
2,9 |
2,7-3,5 |
tg при 106 Гц |
0,0003-0,0007 |
0,008 |
0,007-0,009 |
Епр, МВ/м |
25 |
- |
19 |
Теплостойкость |
|
|
|
по Мартенсу, oС |
75-80 |
76-95 |
120-130 |
Водопоглощение |
|
|
|
за 24 ч.,при 20 |
|
|
|
оС, % |
0,25 |
0,2 |
0,2 |
Интервал рабо- |
|
|
|
чих температур, |
-30 +65 |
-60 +90 |
-100 +140 |
oС |
|
|
|
В ударопрочном полистироле по сравнению с блочным ПС снижается жесткость (модуль упругости при изгибе уменьшается с 2700 Мпа до 2100 МПа) и прочность (прочность на растяжение с 35 МПа до 25 МПа), однако увеличивается ударная вязкость исходная с 20 кДж/м2 до 60 кДж/м2 и ударная вязкость с надрезом с 2 кДж/м2 до 8 кДж/м2.
При этом увеличивается относительное удлинение до
15-35 %.
С введением каучука снижается стойкость к окислению и УФ-излучению, но обычно ударопрочный полистирол
62

стабилизируют введением антиоксидантов фенольного типа, двуокиси титана.
Ударопрочный ПС применяется для изготовления различных деталей высокочастотного оборудования, корпусов приемников, телевизоров, телефонов и других изделий радиоэлектронных средств.
АВС - пластики (акрилонитрилобутадиенстирольные пластмассы) - группа конструкционных полимерных материалов, аналогичных по строению ударопрочному ПС. Повышение ударной прочности достигается эластифицированием бутадиеновым или бутадиен-стирольным каучуком. Он содержит 5-25 % бутадиенового или бутадиен-стирольного каучука, 15-20 % акрилонитрила и стирола. Некоторые диэлектрические и физико-механические свойства АВС приведены в табл. 2.5.
АВС-пластики - непрозрачные, обычно темноокрашенные пластмассы, обладающие высокой ударной вязкостью, прочностью, удовлетворительными диэлектрическими параметрами ( , tg выше, чем в ударопрочном ПС), антистатическими свойствами и тропикостойкостью (в марках полимера ставится буква Т).
Применяются для изготовления деталей радиотехнического назначения, корпусов телевизоров, телефонов и других радиоэлектронных средств.
Поликарбонат модифицированный. Гетероцепные термопластические полимеры с низкой степенью кристалличности, к которым относится поликарбонат, и в условиях эксплуатации обладают большой ударной вязкостью, чем карбоцепные (см. табл. 2.3). Но с понижением температуры и при наличии концентраторов напряжения ударная вязкость их падает. Для повышения ударной вязкости с надрезом при сохранении жесткости, теплостойкости и статической прочности поликарбонат модифицируют различными добавками (фто- ропласт-42, двуокись титана, привитый сополимер АВС). Ос-
63
новные физико-механические свойства модифицированного ПК приведены в табл. 2.5.
Модифицированный ПК применяется для изготовления деталей РЭС сложной конфигурации, работающих при повышенных динамических нагрузках.
2.5. Композиционные, наполненные пластмассы
Композиционные, наполненные пластмассы представляют собой сложные композиции, состоящие из связующего вещества и наполнителя.
При производстве пластмасс в качестве связующих компонентов широко применяют фенолоформальдегидные, эпоксидные, кремнеорганические смолы, непредельные полиэфиры и их различные модификации, а также термопластичные полимеры (поликарбонат, полиамид, полиимид и другие. В качестве наполнителей используют разнообразные органические и неорганические материалы: целлюлоза, кварц, тальк, слюда, асбест, стекловолокна на основе бесщелочного алюмоборосиликатного стекла, углеродные волокна.
Особую группу наполненных материалов представляют пластмассы с листовым наполнителем, где в качестве наполнителя используются бумага, стеклоткань, ткань на основе капрона, лавсана.
Наполнители придают пластмассам высокую устойчивость к длительному нагружению, повышают статическую прочность и прочность к циклическим нагрузкам, стойкость к растрескиванию, жесткость и теплостойкость.
2.5.1. Смолы
Фенолоформальдегидные смолы (ФФС) - олигомер-
ные продукты поликонденсации фенола (C6H5OH) с формальдегидом (СН2О). В зависимости от соотношения фенола и формальдегида и условий поликонденсации образуются ново-
64
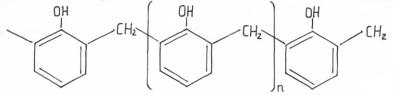
лачные (термопластичные) или резольные (термореактивные) смолы.
Смолы новолачного типа получают поликонденсацией фенола (обычно 7:6) в присутствии кислот катализаторов. Они имеют линейную структуру. Новолачные олигомеры яв-
ляются твердыми, хрупкими, прозрачными полимерами, которые растворяются в органических растворителях, плавятся при температуре 100-120 оС и не меняют своих свойств при длительном хранении и при повторных нагревах. Новолачная смола переходит в неплавкое и нерастворимое состояние (термореактивное) лишь при нагреве в присутствии отверждающих агентов, например, уротропина. Процесс отверждения при этом идет очень быстро, поэтому новолаки применяют в том случае, когда при переработке в изделия требуется высокая скорость отверждения. Феноформальдегидная смола новолачного типа без наполнителей, отвержденная при добавлении гексаметилентетрамина (уротропина) получила название карболита.
Фенолоформальдегидная смола резольного типа, которую называют бакелитом, получается поликонденсацией фенола с избытком формальдегида в присутствии щелочных катализаторов (едкий натр, едкий калий).
Резольные смолы в отличии от новолаков характеризуются пространственной структурой, в которой присутствуют свободные гидроксильные группы (-ОН) и метинольные группы (-СН2ОН). Резолы имеют следующее схематическое изображение:
65
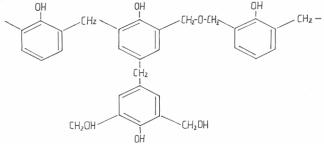
Резольные смолы отверждают путем нагревания. Процесс отверждения проходит три стадии: А, В и С. Стадия А соответствует резолу, который при нагревании плавится и пребывает в вязкотекучем состоянии, растворим в органических растворителях. На стадии В (резитол) смола переходит из вязкотекучего состояния в высокоэластическое; в этом состоянии смола не плавится, а размягчается и под действием растворителей лишь набухает. Стадия С соответствует резиту, который представляет собой твердое вещество, неплавкое и нерастворимое. Следовательно, резит является типичным термореактивным полимером. Резит в чистом виде без наполнителей обладают высокой механической прочностью, стоек к действию большинства кислот, за исключением концентрированной серной кислоты H2SO4, бензину маслам, но обладает высокой хрупкостью. При воздействии водных растворов щелочей или кипящих фенолов резиты медленно растворяются с разложением. Разложение резитов начинается при нагреве при 300 оС, оно сопровождается выделением фенола, бензола и других; при больших температурах происходит обугливание.
Резольные смолы отверждают путем нагревания. Процесс отверждения проходит три стадии: А, В и С. Стадия А соответствует резолу, который при нагревании плавится и пребывает в вязкотекучем состоянии, растворим в органических растворителях. На стадии В (резитол) смола переходит из вязкотекучего состояния в высокоэластическое; в этом со-
66
стоянии смола не плавится, а размягчается и под действием растворителей лишь набухает. Стадия С соответствует резиту, который представляет собой твердое вещество, неплавкое и нерастворимое. Следовательно, резит является типичным термореактивным полимером. Резит в чистом виде без наполнителей обладает высокой механической прочностью, стоек к действию большинства кислот, за исключением концентрированной серной кислоты H2SO4, бензину, маслам, но обладает высокой хрупкостью. При воздействии водных растворов щелочей или кипящих фенолов резиты медленно растворяются с разложением. Разложение резитов начинается при нагреве при 300 оС, оно сопровождается выделением фенола, бензола и других; при больших температурах происходит обугливание.
Резольные смолы применяются для изготовления пластиков, пресспорошков, литых пластмасс, лаков и т.д.
Фенолоформальдегидные смолы, благодаря наличию в их молекулах гидроксильных групп -ОН, полярны, поэтому диэлектрические свойства их невысокие. Они обладают высокой механической прочностью, но низкой эластичностью. Диэлектрические и физико-механические свойства фенолоформальдегидной смолы приведены в табл. 2.6.
Для направленного изменения свойств ФФС используют метод модификации, который заключается в частичной или полной замене фенола амином, мочевиной, меланином.
При замене фенола амином С6Н5NH2 получают анилиноформальдегидные смолы. Их полярные свойства выражены слабее, так как группа NH2 менее полярна, чем группа -ОН; это способствует уменьшению гигроскопичности наполненных пластмасс.
Мочевиноформальдегидная смола является продуктом поликонденсации мочевины (CO(NH2)2 и формальдегида.
Меламиноформальдегидная смола получается в результате реакции поликонденсации меланина (C3H6N6) и формальдегида.
67

Таблица 2.6
Свойства смол без наполнителей
Показатели |
ФФС |
ЭП на основе |
ПОС |
|
|
ЭД-20 |
|
1 |
2 |
3 |
4 |
Прочность, МПа: |
|
|
|
при растяжении |
50-60 |
80-90 |
20-45 |
при изгибе |
84-120 |
90 |
- |
Относительное |
|
|
|
удлинение, % |
1,0-1,5 |
- |
- |
Ударная вязкость, |
|
|
|
кДж/м2: |
1,5-3,0 |
8-12 |
- |
Ом м; |
109- 1010 |
1012 |
1012-1014 |
при 10 Гц; |
4,5-5,0 |
3,6-3,8 |
2,6-3,5 |
tg при 10 Гц |
0,015-0,03 |
0,014-0,013 |
0,007-0,001 |
Епр, МВ/м |
12-16 |
16-18 |
15-25 |
Дугостойкость |
плохая |
- |
- |
Теплостойкость по |
|
|
|
Мартенсу, oС |
- |
105-113 |
- |
Водопоглощение |
|
|
|
за 24 ч, при |
|
|
|
20 оС, % |
0,1-0,2 |
0,25 |
0,1 |
Нагревостойкость |
105-120 |
120-140 |
180-220 |
Эпоксидные смолы (ЭП) это олигомеры или мономеры, содержащие в молекуле эпоксидные группы, обладающие высокой активностью и способные превращаться в полимеры пространственного строения. Эпоксидные смолы являются продуктами поликонденсации многоатомных фенолов и других соединений, в которых имеется эпоксидная группа. Наиболее распространена смола, получаемая при кон-
68

денсации эпихлоргидрина глицерина (содержит эпоксидную группу) с дифенилолпропаном (диамином), называемая обычно диановой. Структурная формула диановой смолы имеет следующий вид
Эпоксидные смолы сами по себе не затвердевают и не обладают технически необходимыми свойствами. ЭП представляют собой вязкие жидкости, которые растворяются во многих органических растворителях (ацетон, толуол, хлорированные углеводороды и др.), не растворимы в воде, бензине, ограниченно растворимы в спиртах. Благодаря высокой реакционной способности эпоксидных групп ЭП сильно взаимодействуют с некоторыми веществами (отвердителями), в результате чего получается твердой полимер с пространственной молекулярной структурой.
Отверждение производится при комнатной или повышенной (90-140 оС) температурах. При этом получается полимер без пузырей, с малой усадкой, процесс отверждения не требует применения давления.
Для холодного отверждения эпоксидных смол применяют алифатические полимеры в определенном количестве (5-15 %) от массы эпоксидного олигомера. Процесс отверждения длится в течение 24 часов.
Для горячего отверждения используются ароматиче-
69
ские диамины, ангидриды карбоновых кислот и некоторые другие. Процесс отверждения происходит при температуре не ниже 100 оС в течение 4-16 ч. На свойства ЭП оказывают влияние тип отвердителя и соответствующие условия отверждения.
Некоторые физико-механические свойства ЭП приведены в табл. 2.6. Эпоксидные смолы имеют более высокие диэлектрические параметры по сравнению с фенолоформальдегидными смолами. Достоинством эпоксидов являются малая усадка, высокая смачивающая способность и адгезия к различным материалам, влагостойкость, механическая прочность, химическая стойкость и совместимость с другими видами смол. Широкое применение нашли модифицированные ЭП, получаемые путем химического взаимодействия эпоксидной смолы с кремнеорганической, фенолоформальдегидной и другими смолами.
Эпоксидные смолы как связующее вещество используют при изготовлении листовых слоистых пластмасс, прессматериалов. Эпоксидные компаунды, обладающие малой усадкой при затвердевании, применяются для пропитки и заливки отдельных узлов радиоаппаратуры, для герметизации полупроводниковых приборов и интегральных микросхем. Кроме того, отвержденные некоторые эпоксидные смолы оптически прозрачны в видимой и ближней инфракрасной областях спектра, благодаря этим свойствам они используются в оптоэлектронных приборах (фотоприемниках, светодиодах).
Кремнеорганические смолы (КО) относятся к про-
межуточным, переходным материалам от органических к неорганическим. Молекулы кремнеорганических смол с неорганическими главными цепями могут состоять из атомов Si и O (полиорганосилоксаны), атомов Si и N (полиорганосилазаны), Si и S (полиорганосилтианы). Возможны и другое химическое строение главной цепи макромолекулы КО.
В полиорганосилоксаных в качестве боковых групп могут быть органические радикалы, например, метил (-СН3),
70