
- •ПРИРОДНЫЕ КАМЕННЫЕ МАТЕРИАЛЫ И ИЗДЕЛИЯ
- •Горные породы – это природные образования более или менее однородного состава и строения, образующие в земной коре самостоятельные геологические тела.
- •Минералами называются однородные по химическому составу, строению и физическим свойствам природные тела, образовавшиеся в земной коре в результате физико-химических процессов.
- •Всего в природе более 2 тыс. минералов, но в образовании горных пород участвуют всего лишь около 50. Такие минералы называются породообразующими минералами. Зная содержание минералов в горной породе, можно предопределять важнейшие ее свойства.
- •По условиям образования горные породы делятся на три основные группы: магматические, осадочные и метаморфические (см. рис.).
- •Химические
- •Рыхлые
- •Пористые
- •Изучение основных характеристик горных пород, породообразующих минералов и области их применения в строительстве.
- •3.3. Порядок выполнения работы
- •Свойства некоторых горных пород, а также области их применения в строительстве представлены в таблице.
- •Аттестационные вопросы
- •1. Что такое горная порода, минерал?
- •2. Как классифицируются горные породы по условиям образования?
- •3. Перечислить основные породообразующие минералы изверженных горных пород.
- •4. Перечислить основные породообразующие минералы осадочных горных пород.
- •6. Какие виды строительных материалов и изделий изготовляют из горных пород?
- •7. Перечислить факторы, вызывающие разрушение строительных материалов из природного камня, и способы защиты их от разрушения (коррозии).
- •8. Чем объясняется выбор способа и вида обработки поверхности природных каменных материалов?
- •Марка
Приборы, инструменты, материалы: коллекция породообразующих минералов, коллекция магматических горных пород, коллекция осадочных горных пород, коллекция метаморфических горных пород, образцы строительных материалов и изделий из природного камня, таблицы с показателями эксплуатационно-технических и эстетических свойств природных каменных материалов, породообразующих минералов, строительных материалов и изделий из горных пород, генетическая классификация горных пород, лупа, шкала твердости Мооса.
Аттестационные вопросы
1.Что такое горная порода, минерал?
2.Как классифицируются горные породы по условиям образования?
3.Перечислить основные породообразующие минералы изверженных горных пород.
4.Перечислить основные породообразующие минералы осадочных горных пород.
5.Перечислить основные эксплуатационно-технические свойства природного камня.
6.Какие виды строительных материалов и изделий изготовляют из горных пород?
7.Перечислить факторы, вызывающие разрушение строительных материалов из природного камня, и способы защиты их от разрушения (коррозии).
8.Чем объясняется выбор способа и вида обработки поверхности природных каменных материалов?
37
ЛАБОРАТОРНАЯ РАБОТА № 4
ИСПЫТАНИЕ СТРОИТЕЛЬНОЙ ВОЗДУШНОЙ ИЗВЕСТИ
4.1. Общие сведения
Строительной воздушной известью называют вяжущее, получаемое путем обжига при температуре 900…1200 0С кальциево-магниевых карбонатных горных пород (мел, известняк, доломит), содержащих не более 6…8 % глинистых и песчаных примесей. При обжиге пород происходит реакция разложения:
СаСО3 → СаО+СО2↑,
МgСО3 → MgO+CO2↑.
Различают негашеную (комовую и молотую, состоящую в основном из оксидов кальция и магния) и гашеную (состоящую из соответствующих гидроксидов) извести. Гашеную известь получают из комовой негашеной извести путем добавления небольшого количества воды:
СаО+Н2О→Са(ОН)2+Q.
Реакция гашения сопровождается выделением значительного количества тепла. По времени гашения воздушная негашеная известь классифицируется на быстрогасящуюся (время гашения не более 8 мин), среднегасящуюся (время гашения не более 25 мин),медленногасящуюся (время гашения более 25 мин).
В зависимости от содержания оксидов кальция и магния воздушная негашеная известь подразделяется на кальциевую (МgО < 5%), магнезиальную (содержание МgО от 5 до 20 %) и доломитовую (содержаниеМgОот20до 40%).
Основным показателем качества воздушной строительной извести является содержаниеактивных СаО+MgO, по которым определяется сорт извести. Воздушная негашеная строительная известь без добавок подразделяется на три сорта: 1, 2 и 3; негашеная порошкообразная с добавками на два сорта:1 и 2; гидратная (гашеная) без добавок и с добавками на два сорта: 1 и 2. Основные технические требования к воздушной извести представлены в табл. 4.1.
Таблица 4.1
Технические требования к воздушной строительной извести
Наименование показа- |
|
|
Норма для извести, %, по массе |
|
|
||||||
теля |
|
|
|
|
|
|
|
|
|
|
|
|
|
|
негашеной |
|
|
гидратной |
|||||
|
кальциевой |
|
магнезиальной и доло- |
|
(гашеной) |
||||||
|
|
|
|
|
|
митовой |
|
|
|
|
|
|
|
|
|
|
|
сорт |
|
|
|
|
|
|
1 |
2 |
3 |
|
1 |
2 |
|
3 |
|
1 |
2 |
|
|
|
|
38 |
|
|
|
|
|
|
|
Продолжение табл. 4.1
Активные СаО+MgO, |
|
|
|
|
|
|
|
|
не менее: |
|
|
|
|
|
|
|
|
- без добавок |
90 |
80 |
70 |
85 |
75 |
65 |
67 |
60 |
- с добавками |
65 |
55 |
- |
60 |
50 |
- |
50 |
40 |
Активный MgO, не |
5 |
5 |
5 |
20 |
20 (40) |
20 (40) |
- |
- |
более |
|
|
|
(40) |
|
|
|
|
Непогасившиеся зерна, |
7 |
11 |
14 |
10 |
15 |
20 |
- |
- |
не более |
|
|
|
|
|
|
|
|
Степень дисперсности порошкообразной воздушной извести должна быть такой, чтобы при просеивании пробы извести сквозь сито с сетками N 02 и N 008 проходило соответственно не менее 98,5 и 85% массы просеиваемой пробы.
4.2. Цель работы
Ознакомиться с основными требованиями к качеству строительной воздушной извести (кальциевой) и методами ее испытания.
4.3.Порядок выполнения работы
4.3.1.Определение содержания активных СаО+MgOвкальциевой негашеной воздушной строительной извести
Активность (содержания активных СаО+MgO) негашеной кальциевой воздушной извести определяют методом титрования навески извести 1 н раствором соляной кислоты.
Навеску извести массой 1 г помещают в коническую колбу объемом 250 мл, приливают 150 мл дистиллированной воды, добавляют 3…5 стеклянные бусины, закрывают стеклянной воронкой или часовым стеклом и нагревают до температуры кипения. После этого раствор охлаждают до температуры 20…30 0С, добавляют 2...3 капли фенолфталеина, в результате чего раствор приобретает малиновую окраску. Полученный раствор титруют при постоянном взбалтывании 1 Н раствором соляной кислоты до полного обесцвечивания. Титрование считают законченным, если в течение последующих 8 мин при периодическом взбалтывании раствор останется бесцветным.
Содержание активных окисей кальция и магния в процентах вычисляют по формуле
A= |
|
, |
(4.1) |
|
39
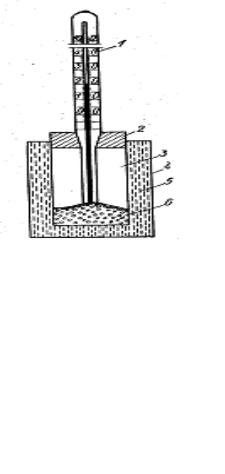
где V – объем раствора 1 Н соляной кислоты, пошедший на титрование, мл; TCaO – титр 1 Н раствора соляной кислоты;
m – масса навески извести, г.
Для точно 1 Н раствора соляной кислоты титр составляет 0,02804.
4.3.2. Определение температуры и времени гашения извести
Скорость гашения извести устанавливается по температуре и времени гашения, которые являются важными показателями, определяющими технологические параметры работы с этим материалом. При гашении извести выделяется значительное количество теплоты.
Для определения температуры и времени гашения извести вычисляют необходимую массу навески извести в граммах по формуле
|
|
|
|
, |
(4.2) |
|
|
|
|
||||
|
|
где А – содержание активных окисей кальция и |
||||
|
магния в извести, %. |
|
||||
Рис. 4.1 . Термостатная |
Навеску извести помещают в |
термосную |
||||
колба: |
колбу (рис. 4.1), приливают 25 мл воды, имеющей |
|||||
1– термометр; |
||||||
температуру 20 0С, и быстро перемешивают дере- |
||||||
2 |
– пробка; |
|||||
3 |
– внутренний ци- |
вянной палочкой. Колбу закрывают пробкой с |
||||
линдр; |
термометром на 100 0С (при этом ртутный шарик |
|||||
4 |
– фарфоровый сосуд; |
термометра должен быть полностью погружен в |
||||
5 |
– изоляционный слой; |
|||||
смесь) и оставляют в покое. Температуру реаги- |
||||||
6 |
– смесь извести с |
|||||
водой |
рующей смеси фиксируют через каждую минуту, |
|||||
|
|
начиная с момента добавления воды. |
Определе- |
ние считается законченным, если в течение 4 мин температура не повышается более чем на 1 0С.
За время гашения принимают время с момента добавления воды до начала момента, когда рост температуры не превышает 0,25 0С в минуту. За температуру гашения извести принимается максимальная достигнутая в этом процессе температуру извести.
40
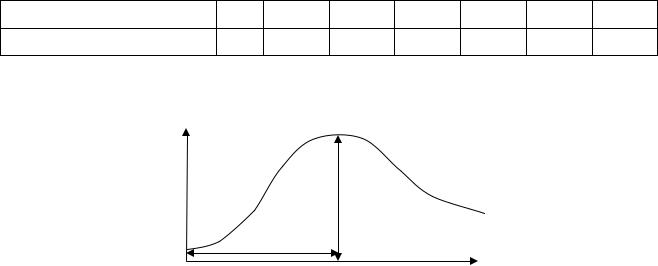
Результаты испытаний записывают в табл. 4.2.
Таблица 4.2
Результаты определения температуры и времени гашения извести
Время гашения, мин 1 |
2 |
3 |
4 |
5 |
… |
N |
Температура, 0С
По данным таблицы 4.2 строят график гашения извести (рис. 4.2), по которому дают заключение о типе испытанной извести по времени гашения.
Т,°С
Т
tгaш
t, мин
Рис. 4.2. График гашения извести
4.3.3.Определение содержания непогасившихся зерен
Впроцессе гашения извести некоторое количество ее частиц может либо вообще не погасится, либо гасится настолько медленно, что процесс гашения закачивается в кладке или штукатурном слое. В этом случае расширение извести может привести к появлению внутренних напряжений в уже затвердевшем материале и его разрушению.
Для определения содержания непогасившихся зерен в металлический со-
суд цилиндрической формы вместимостью 8…10 л наливают 3,5…4 л нагретой до температуры 85…90 0С воды и всыпают 1 кг извести, непрерывно перемешивая содержимое до окончания интенсивного выделения пара. Полученное тесто выдерживают в течение 2 ч, а затем разбавляют холодной водой до консистенции известкового молока и промывают на сите N 063 слабой непрерывной струей воды, слегка растирая мягкие кусочки стеклянной палочкой с рези-
новым наконечником. Остаток на сите высушивают при температуре 140…150 0С до постоянной массы и взвешивают. Содержание непогасившихся зерен в процентах вычисляют по формуле
41

, |
(4.3) |
где m – остаток на сите после высушивания, г.
Приборы, инструменты, материалы: представительная проба воздушной строительной извести, фенолфталеин, 1 н раствор соляной кислоты, дистиллированная вода, коническая колба объемом 250 мл, мерный цилиндр, электроплитка, термостатная колба, ртутный термометр на 100 0С, секундомер, металлическая емкость на 10 л, сито № 063.
Аттестационные вопросы
1.К какому виду вяжущего по условиям твердения относят воздушную строительную известь?
2.Какие требования предъявляются к сырьевым материалам для производства воздушной строительной извести?
3.Перечислите основные разновидности воздушной строительнойизвести.
4.Как определяют содержание СаО + MgO активных?
5. Как проводят определение скорости гашения извести?
6. Раскройте методику определения содержания непогасившихся зерен?
42
ЛАБОРАТОРНАЯ РАБОТА № 5
ОПРЕДЕЛЕНИЕ ОСНОВНЫХ СВОЙСТВ ГИПСОВЫХ ВЯЖУЩИХ ВЕЩЕСТВ
5.1. Общие сведения
Гипсовые вяжущие - это порошкообразные материалы, состоящие из полуводного гипса (CaSO4 · 0,5H2O), получаемые тепловой обработкой (температура в пределах 130…180 0С) природного гипсового камня (СаSO4·2H2O) или гипсосодержащих техногенных отходов (фосфогипс). При тепловой обработке происходит следующая реакция:
CaSO4·2H2O → CaSO4·0,5H2O + 1,5H2O.
Гипсовые вяжущие по традиции условно разделяют на: строительный гипс, состоящий из β-полугидрата, формовочный гипс того же состава с повышенными техническими свойствами и высокопрочный гипс, состоящий из α- полугидрата.
Гипсовые вяжущие вещества твердеют в воздушно - сухих условиях в результате реакции гидратации, присоединяя при этом 1,5 молекулы воды:
CaSO4 0,5H2O+1,5H2O → CaSO4 2H2O.
В зависимости от сроков схватывания гипсовые вяжущие вещества делятся на быстротвердеющие, нормальнотвердеющие имедленно твердеющие(табл. 5.1).
Таблица 5.1
Классификация гипсовых вяжущих веществ в зависимости от сроков схватывания
Вид вяжущего |
Индекс сро- |
Срок схватывания, мин |
|
|
ков тверде- |
|
|
|
начало, не ра- |
конец, не позд- |
|
|
ния |
||
|
нее |
нее |
|
Быстротвердеющий |
А |
2 |
15 |
Нормальнотвердеющий |
Б |
6 |
30 |
Медленнотвердеющий |
В |
20 |
Не нормируют |
В зависимости от предела прочности на сжатие гипсовые вяжущие подразделяются на следующие марки: Г-2, Г-3, Г-4, Г-5, Г-6, Г-7, Г-10, Г-13, Г-16, Г-19, Г-22, Г-25. Минимальное значение предела прочности каждой марки гипсового вяжущего представлено в табл. 5.2.
43
Таблица 5.2
Марки гипсовых вяжущих веществ по прочностным показателям
Марка вяжущего |
Предел прочности образцов-балочек в возрасте 2 ч, |
|
|
МПа (кгс/см2), не менее |
|
|
при сжатии |
при изгибе |
Г-2 |
2(20) |
1,2(12) |
Г-3 |
3(30) |
1,8(18) |
Г-4 |
4(40) |
2,0(20) |
Г-5 |
5(50) |
2,5(25) |
Г-6 |
6(60) |
3,0(30) |
Г-7 |
7(70) |
3,5(35) |
Г-10 |
10(100) |
4,5(45) |
Г-13 |
13(130) |
5,5(55) |
Г-16 |
16(160) |
6,0(60) |
Г-19 |
19(190) |
6,5(65) |
Г-22 |
22(220) |
7,0(70) |
Г-25 |
25(250) |
8,0(80) |
В зависимости от степени помола гипсовые вяжущие подразделяются на грубого, среднего и тонкого помола (табл. 5.3).
Таблица 5.3
Классификация гипсовых вяжущих веществ в зависимости от тонкости помола
Вид вяжущего |
Индекс степе- |
Максимальный остаток на сите с |
|
ни помола |
размерами ячеек в свету 0,2 мм, %, |
|
|
не более |
Грубого помола |
I |
23 |
Среднего помола |
II |
14 |
Тонкого помола |
III |
2 |
В условных обозначениях гипсового вяжущего указывается марка по прочности, индекс сроков твердения и индекс степени помола, например:
Г-5 А II.
44

5.2. Цель работы
Ознакомиться с методиками оценки основных показателей качества низкообжиговых гипсовых вяжущих веществ.
5.3.Порядок выполнения работы
5.3.1.Определение тонкости помола
Тонкость помола гипсовых вяжущих веществ оценивают по остатку на сите с размером ячеек в свету 0,2 мм. Для определения тонкости помола навеску вяжущего массой 50 г, взвешенную с погрешностью не более 0,1 г и предварительно высушенную в сушильном шкафу в течение 1 ч при температуре 50±5 0С, высыпают на сито и производят просеивание вручную или на механической установке. Просеивание считают законченным, если при контрольном просеивании сквозь сито на бумагу в течение 1 мин проходит не более 0,05 г вяжущего.
Остаток на сите взвешивают и определяют тонкость помола в процентах по формуле
%, |
(6.2) |
где m1 – масса остатка на сите;
m – исходная масса навески цемента.
За тонкость помола принимают среднеарифметическое значение результатов двухопределений. Результаты заносят в табл. 5.4.
Таблица 5.4
Определение тонкости помола цемента
Номер |
Масса на- |
Масса остатка на |
Тонкость помола, % |
||
опыта |
вески, г |
сите, г |
|
|
|
полученное зна- |
среднее зна- |
||||
|
|
|
|||
|
|
|
чение |
чение |
|
|
|
|
|
|
45
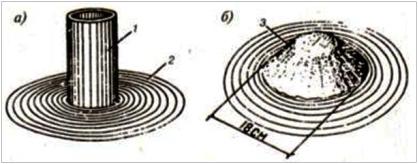
5.3.2. Определение стандартной консистенции (нормальной густоты) гипсового теста
Стандартная консистенция (нормальная густота) гипсового теста – это такая консистенция, при которой диаметр расплыва гипсового теста, вытекающего из цилиндра (вискозиметра Суттарда) при его поднятии, составляет
180 ± 5 мм.
Стандартная консистенция гипсового теста характеризуется количеством воды затворения, выраженном в процентах, как отношение массы воды, необходимой для получения гипсовой смеси стандартной консистенции, к массе гипсового вяжущего. Считается, что чем выше водопотребность вяжущего, тем выше пористость получаемого камня и, соответственно, ниже его прочность и морозостойкость.
Для определения нормальной густоты в предварительно протертую влажной тканью чашу вливают воду, количество которой зависит от свойств гипсового вяжущего (как правило, берется в пределах 150...220 мл), а затем в течение 2…5 с всыпают от 300 до 350 г гипсового вяжущего. Смесь перемешивают ручной мешалкой в течение 30 с, начиная отсчет времени от начала всыпания гипсового вяжущего в воду. Цилиндр (рис. 5.1) устанавливают в центре стекла, предварительно протирают их влажной тканью. Затем заполняют цилиндр гипсовым тестом и через 45 с, считая от начала засыпания гипсового вяжущего в воду, или через 15 с после окончания перемешивания, цилиндр оченьбыстроподнимают вертикальнона высоту15…20 см и отводят всторону.
Рис. 5.1. Определение нормальной густоты на вискозиметре Суттарда
а) цилиндр на стекле; б) определение расплыва гипсового теста.
1 – цилиндр высотой 100 мм и внутренним диаметром 50 мм; 2 – стеклянная пластина с концентрическими окружностями; 3 – расплыв гипсового теста.
Диаметр расплыва измеряют линейкой в двух перпендикулярных направлениях с погрешностью не более 5 мм и вычисляют среднее арифметическое значение. Если диаметр расплыва гипсового теста отличается от 180 ± 5 мм, то испытание повторяют с измененной расходом воды. Результаты испытаний заносят в табл. 5.5.
46
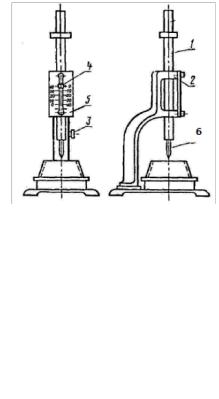
Таблица 5.5
Результаты определения нормальной густоты гипсового теста
Номер |
Масса гипса, г |
Масса |
В/Г |
Диаметр расплыва |
Нормальная |
опыта |
|
воды, г |
|
гипсового теста, мм |
густота, % |
|
|
|
|
|
|
|
|
|
|
|
|
5.3.3. Определение сроков схватывания гипсового теста стандартной консистенции (нормальной густоты)
Определение производят с помощью прибора Вика (рис. 5.2), заменяя пестик прибора на иглу. Общая масса перемещающейся части прибора Вика должна быть (300±1) г.
|
|
Перед началом испытания проверяют свобод- |
|
|
|
ное перемещение стержня и нулевое показание при- |
|
|
|
бора Вика, соприкасая иглу с пластинкой, на кото- |
|
|
|
рой установлено кольцо. |
|
|
|
Для определения сроков схватывания гипсо- |
|
|
|
вое тесто стандартной консистенции (нормальной |
|
|
|
густоты) переносят в предварительно смазанное |
|
|
|
машинным маслом кольцо, установленное на поли- |
|
|
|
рованную пластинку. Заполненное гипсовым тес- |
|
|
|
том кольцо с пластинкой для удаления попавшего в |
|
Рис. 5.2. Прибор Вика: |
тесто воздуха 4…5 раз встряхивают путем подня- |
||
тия и опускания одной из сторон пластинки при- |
|||
1 |
– цилиндрический ме- |
||
мерно на 10 мм. Излишки теста срезают линейкой и |
|||
таллический стержень; |
заполненную форму на пластинке устанавливают |
||
2 |
– обойма станины; |
||
на основании прибора Вика. Иглу прибора Вика |
|||
3 |
– стопорное устройство; |
||
доводят до соприкосновения с поверхностью гип- |
|||
4 |
– указатель; |
сового теста. Отпускают стопорный винт и игла |
|
5 |
– шкала; |
||
свободно погружается в кольцо с тестом. Погруже- |
|||
6 |
– игла |
||
ние производят через каждые 30 с, начиная с цело- |
|||
|
|
го числа минут. После каждого погружения иглу |
протирают, а пластинку вместе с кольцом передвигают так, чтобы игла при новом погружении попадала в другое место поверхности теста. Результаты записывают в табл. 5.6.
47
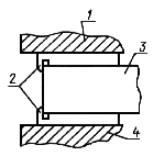
|
|
|
|
|
|
Таблица 5.6 |
||
|
|
Глубина проникания иглы |
|
|
|
|
||
|
|
|
|
|
|
|
|
|
Время, мин |
1 |
1,5 |
2 |
2,5 |
…. |
|
N |
|
Глубина погру- |
|
|
|
|
|
|
|
|
жения иглы, мм |
|
|
|
|
|
|
|
|
Началом схватывания считают промежуток времени (в мин) от начала затворения гипса водой до момента, когда игла при проникновении в гипсовое тесто первый раз не доходит до пластинки, на которую установлено кольцо. Концом схватывания считают промежуток времени (в мин) от начала затворения гипса водой до момента, когда игла прибора Вика проникает в гипсовое тесто не более чем на 1 мм.
5.3.4. Определение марки гипсового вяжущего по прочности
Определение прочностных характеристик осуществляется через 2 ч после контакта гипсового вяжущего с водой на образцах-балочках (4х4х16 см), изготовленных из гипсового теста стандартной консистенции.
Для изготовления образцов гипсовое вяжущее в количестве от 1,0 до 1,6 кг засыпают в чашку с водой, взятой в количестве, необходимом для получения теста стандартной консистенции. Смесь интенсивно перемешивают ручной мешалкой в течение 60 с до получения однородного теста, а затем заливают ее в предварительно смазанную минеральным маслом форму. Для удаления вовлеченного воздуха после заливки форму встряхивают 5-ю ударами о стол. После наступления начала схватывания излишки гипсового теста срезают линейкой, передвигая ее по верхним граням формы перпендикулярно к поверхности образцов, а через 15±5 мин после конца схватывания образцы извлекают из формы и маркируют. Испытания производят через 2 часа после затворения гипса водой.
Рис. 5.3. Схема испытания
на сжатие:
1 – верхняя плита пресса;
2 – пластинки;
3 – половинка образца;
4 – нижняя плита пресса
Образцы испытывают сначала на изгиб, а затем шесть половинок балочек сразу же подвергают испытанию на сжатие с использованием стандартных металлических пластинок с площадью 25 см2 (рис. 5.3) .
Предел прочности при изгибе вычисляют как среднее арифметическое результатов трех испытаний.
Предел прочности на сжатие вычисляют как среднее арифметическое результатов шести испытаний без наибольшего и наименьшего результатов.
48
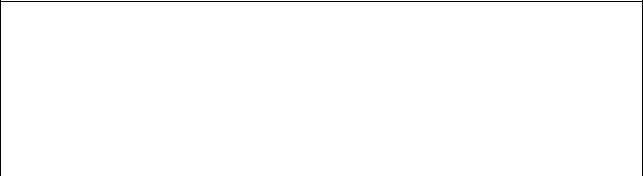
Результаты испытаний заносят в табл. 5.7.
Таблица 5.7
Результаты механических испытаний
Вид испытания
Растяжение при изгибе |
|
Сжатие |
|
|||
Номер |
Предел прочности |
Номер |
Разру- |
Предел прочности |
||
образца |
при изгибе |
образца |
шающая |
при сжатии |
||
|
Отдельного |
Среднее |
|
сила, |
Отдельного |
Среднее |
|
образца, МПа |
значение, |
|
Н (кгс); |
образца, |
значение, |
|
|
МПа |
|
|
МПа |
МПа |
|
|
|
|
|
|
|
Приборы, инструменты, материалы: гипс, вода, весы, сито с ячейками размером в свету 0,2 мм, мерный стеклянный цилиндр, чашка из коррозионностойкого материала вместимостью более 500 см, ручная мешалка, стекло диаметром более 240 мм; цилиндр из нержавеющего металла с полированной внутренней поверхностью, прибор Вика, секундомер, линейка, прибор для определения прочности при изгибе, металлические пластинки для определения половинок балочек на сжатие, гидравлический пресс мощностью 5…10 тс.
Аттестационные вопросы
1.К какому виду вяжущего по условиям твердения относятся гипсовые вяжущие вещества?
2.Что является сырьем для производства гипсовых вяжущих веществ?
3.Основные показатели, характеризующие гипсовые вяжущие вещества.
4.Как производится маркировка гипсовых вяжущих веществ?
5.Что такое нормальная густота гипсового теста и какова методика ее определения?
6.Как определяются сроки схватывания гипсового теста?
7.Методика определения марки гипса.
49
ЛАБОРАТОРНАЯ РАБОТА № 6
ОПРЕДЕЛЕНИЕ ФИЗИКО-МЕХАНИЧЕСКИХ СВОЙСТВ ЦЕМЕНТА
6.1.Общие сведения
Всовременном строительстве цемент является основным гидравлическим вяжущим веществом для производства строительных растворов, сухих строительных смесей, бетона и железобетона. Наиболее широкое применение в строительстве получили цементы на основе портландцементного клинкера: портландцемент без добавок, портландцемент с минеральными добавками, быстротвердеющий портландцемент, шлакопортландцемент, пуццолановый портландцемент и глиноземистый цемент.
Для нормативного обеспечения производителей цемента в странах СНГ методиками испытаний, гармонизированных с требованиями международного стандарта, позволяющими получить аналогичные со странами ЕС результаты, в России разработаны нормативные документы (ГОСТ 31108, ГОСТ 30515, ГОСТ 30744). При этом на территории стран СНГ для характеристики цемента допускается применять и отечественные методики, в том числе и ГОСТ 10178. Таким образом, в настоящее время на территории СНГ определение физикомеханических свойств цемента может осуществляться как по отечественным методикам (ГОСТ 10178, ГОСТ 310.1, ГОСТ 310.2, ГОСТ 310.3, ГОСТ 310.4), так и по методикам гармонизированным с требованиями международного стандарта (ГОСТ 31108, ГОСТ 30515, ГОСТ 30744).
Всвязи с тем, что многие производители цемента широко применяют методики оценки качества цемента гармонизированные с требованиями международного стандарта (ГОСТ 31108, ГОСТ 30515, ГОСТ 30744), то в данной лабораторной работе изучаются в основном эти методики, а отечественные методики представлены в виде ознакомительного материала.
По вещественному составу цементы подразделяют на пять типов:
-ЦЕМ I – портландцемент;
-ЦЕМ II – портландцемент с минеральными добавками;
-ЦЕМ III – шлакопортландцемент;
-ЦЕМ IV – пуццолановый цемент;
-ЦЕМ V – композиционный цемент.
По содержанию портландцементного клинкера и добавок ЦЕМ IIЦЕМ V подразделяются на подтипы А,В,С.
Класс прочности цемента – это условное обозначение одного из значений параметрического ряда по прочности цемента (МПа) в максимальные сроки, установленные нормативным документом.
Активность цемента – это фактическая прочность на сжатие образцов из стандартного цементного раствора, изготовленных и испытанных в стандартных условиях, установленных нормативным документом.
50
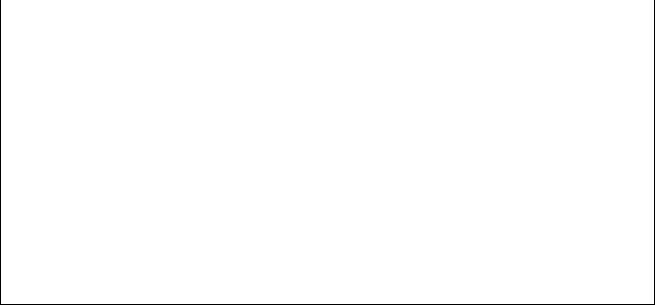
По прочности на сжатие в возрасте 28 сут. цементы подразделяют на классы: 32,5; 42,5; 52,5 (таблица 6.1).
По прочности на сжатие в возрасте 2 (7) сут. (скорости твердения) цементы подразделяют на подклассы: Н (нормальнотвердеющий), Б (быстротвердеющий) и М (медленнотвердеющий). Подкласс М применяется только для цементов ЦЕМ III/B и ЦЕМ III/С.
|
|
|
|
|
|
Таблица 6.1 |
|
Физико-механические показатели цементов |
|||||
|
|
|
|
|
|
|
Класс, под- |
Прочность на сжатие, МПа, в возрасте |
Начало |
Равномерность |
|||
класс, проч- |
|
|
|
|
схватыва- |
изменения объема |
ности це- |
2 сут, |
7 сут, |
28 сут |
ния, мин, |
(расширение), мм, |
|
мента |
не менее |
не менее |
не менее |
не более |
не ранее |
не более |
32,5М* |
- |
12 |
32,5 |
52,5 |
75 |
|
32,5Н |
- |
16 |
|
|||
32,5Б |
10 |
- |
|
|
|
|
42,5 М* |
- |
16 |
42,5 |
62,5 |
60 |
10 |
42,5Н |
10 |
- |
||||
42,5Б |
20 |
- |
|
|
|
|
52,5 М* |
10 |
|
52,5 |
- |
45 |
|
52,5Н |
20 |
- |
|
|||
52,5Б |
30 |
- |
|
|
|
|
* подкласс применяется только для цементов типа ЦЕМ III
Условное обозначение цемента должно состоять из наименования цемента, сокращенного обозначения цемента, класса по прочности, обозначения подкласса, обозначения настоящего стандарта.
Пример условного обозначения портландцемента типа ЦЕМ I, класса 42,5 быстротвердеющего:
Портландцемент ЦЕМ I 42,5 Б ГОСТ 31108 – 2016.
При использовании в испытаниях отечественных методик (ГОСТ 10178, ГОСТ 310.1, ГОСТ 310.2, ГОСТ 310.3, ГОСТ 310.4) портландцементы, в зависимости от содержания минеральных добавок, имеют обозначения: ПЦ-Д0, ПЦ-Д5, ПЦ-Д20 (табл.6.2), шлакопортландцемент – ШПЦ, пуццолановый портландцемент – ППЦ.
51