
2074
.pdf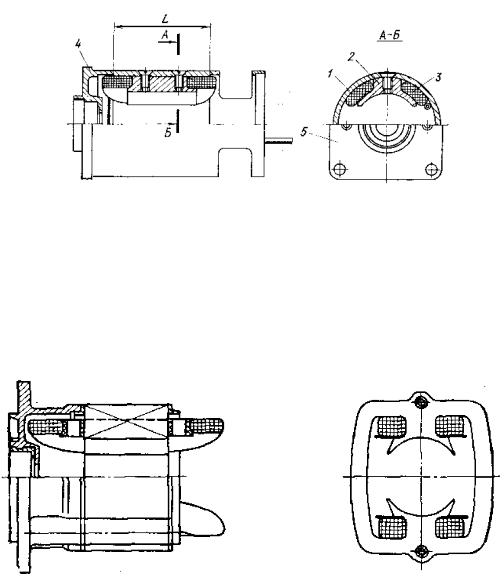
61
Рис. 2.45
Изготовление всего корпуса со щитом 4 и фланцем 5 из ферромагнитного материала (стали) позволяет упростить конструкцию, хотя и увеличивает ее массу, поскольку ферромагнитный материал требуется только на длине L, где корпус 1 выполняет функцию магнитопровода. Остальные участки могут быть изготовлены из легких сплавов. Двухщитовые конструкции, в которых масса снижена за счет применения щитов из легких сплавов, показана на рис. 2.46.
Рис. 2.46
В этих конструкциях магнитопровод индуктора представляет собой пакет, собранный из листов электротехнической стали. Применение штамповки и отсутствие отъемных полюсов является положительными свойствами этих конструкций. В качестве недостатков рассматриваемых конструкций можно отметить, что для намотки катушек прямо на полюсах конфигурация пакета должна быть именно такой, как показано на рис. 2.46. Необходимо отметить, что такая конфигурация влечет за собой увеличение потоков рассеяния в магнитной системе и массы самого магнитопровода, а также усложнение конструктивных решений вариантов стыковки магнитопровода со щитами вследствие нецилиндричности его формы. В связи с этим двухщитовые бескорпусные конструкции не получили широкого распространения.
Для машин больших мощностей из-за значительных размеров корпуса более целесообразным решением является применение двухщитовой корпусной конструкции. Кроме упрощения технологии она обеспечивает
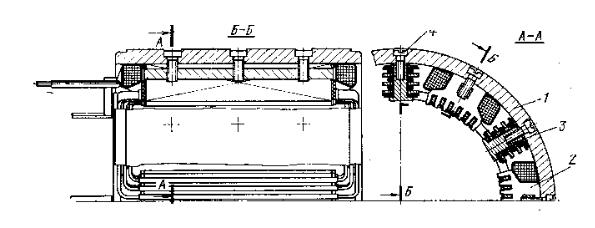
62
значительное уменьшение массы. Корпус такой машины с основными и дополнительными полюсами показан на рис.2.47.
Рис. 2.47
Ярмо статора такой машины 1 выполнено из стальной трубы. Основные полюсы 2 собраны из штампованных листов и скреплены стяжной шпилькой 2, расклепанной с двух сторон. Дополнительные полюса 3 - целые. Они сделаны из профилированного проката. Как основные, так и дополнительные полюса прикреплены к ярму с помощью болтов 4.
Рассмотрим однощитовую конструкцию корпуса электрических машин. Корпус машин постоянного тока однощитовой конструкции встречается сравнительно редко. Это объясняется тем, что корпус машин постоянного тока должен быть магнитопроводящим, т.е. выполняется из стали. В то же время магнитопроводящей должна быть часть корпуса, расположенная на длине полюса. Поэтому применение однощитовой конструкции корпуса в машинах постоянного тока приводит к значительному увеличению веса машины, а следовательно и стоимости изделия. Наиболее широко однощитовая конструкция корпуса используется в асинхронных двигателях. Эскиз корпуса асинхронного двигателя показан на рис. 2.48.
Задний щит 2 отливается заодно с корпусом 1. Гнездо для установки подшипника имеет запрессованную стальную втулку 3. Пакет железа 4 с обмоткой переменного тока закреплен в корпусе стопорными винтами 5. Выводы обмотки проходят через отверстие в приливе, на котором закреплена выводная коробка. Отверстия 6 и 7 в щите и в корпусе предназначены соответственно для входа и выхода охлаждающего воздуха, который нагнетается установленным на роторе вентилятором.
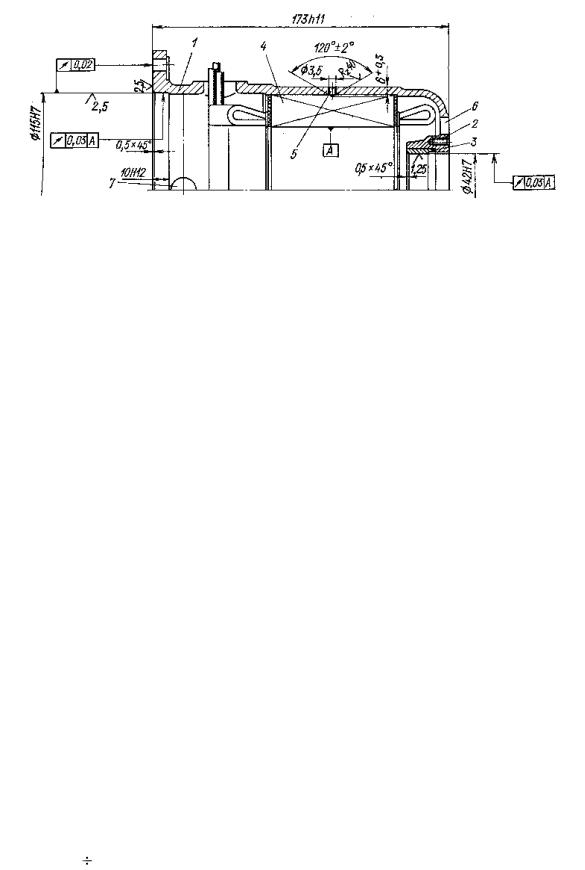
63
Рис. 2.48
Скрепление листов электротехнической стали в пакете статора может производиться склейкой, сваркой продольными швами по наружному диаметру и запрессовкой в тонкостенный стальной стакан. Выбор метода скрепления пакета должен производиться с учетом многих факторов, к числу которых относятся: длина пакета, диаметр соответствующих размеров паза, толщина листа и т.д. Наиболее технологичным из перечисленных способов является сварка пакетов по наружному диаметру. Для монолитности конструкции, крайние листы делаются более толстыми или изготавливаются из обычных листов путем точечной сварки нескольких.
Бесщитовая конструкция и конструкция с неразъемными щитами используются в специальных типах электрически машин, поэтому на практике встречаются сравнительно редко.
2.5.3. Конструкции подшипниковых щитов
Подшипниковые щиты предназначены для закрепления в них узлов подшипников.
Подшипниковые щиты изготавливаются литьем под давлением из алюминия. В машинах большой мощности они выполняются либо чугунным литьем, либо свариваются из стального проката. В машинах защищенного исполнения при радиальной системе вентиляции передний и задний подшипниковые щиты унифицированы; при аксиальной системе вентиляции их не унифицируют из-за наличия вентилятора, размещенного с одной стороны.
При радиальной системе вентиляции для повышения ее эффективности на внутренней части подшипниковых щитов крепят направляющие воздух щитки, выполненные из листовой стали в виде воронок. Щитки располагают на расстоянии (5 7) мм от торцов лопаток ротора.
Подшипниковые щиты закрытых машин глухие. При выполнении таких щитов из алюминиевых сплавов у них предусматривают оребренные торцы, увеличивающие поверхность охлаждения.
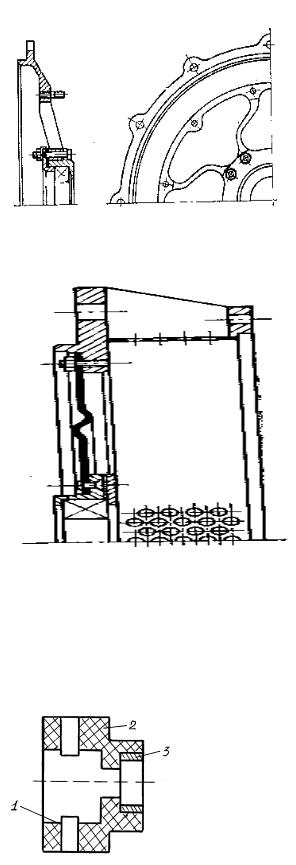
64
Щиты имеют цилиндрическую круговую заточку (замок) для посадки на заточку станины при сборке машины. Для крепления к станине в щитах имеются отверстия для болтов. В центральной части щитов предусматривается установка стальной втулки со сквозной проточкой, предназначенной для посадки подшипников качения.
Для защиты подшипников от воздействия радиальных сжимающих сил, возникающих при изменениях температуры применяются щиты с изогнутыми ребрами. Эскиз такого подшипникового щита приведен на рис. 2.49. Другая конструкция подшипниковых щитов, предназначенная в том числе для компенсации температурных расширений - конструкция с плоской мембраной, которая приведена на рис.
2.50.
Плоская мембрана позволяет несколько изменить общепринятую схему закрепления подшипников. В этой конструкции подшипник имеет
возможность перемещаться в аксиальном направлении для компенсации температурных расширений и всех допусков по корпусу, валу и щиту. Поэтому в машине с таким щитом внутренние а также наружные кольца в обоих подшипниках закрепляются в аксиальном направлении.
В настоящее время свойства пластмасс с хорошими механическими и изоляционными характеристиками позволило применить их для изготовления щитов коллекторных машин постоянного тока небольшой
мощности. Один из таких щитов показан на рис.2.51.
В этой конструкции щит объединен с щеткодержателем, окно 1 под щетку выполняется непосредственно в щите. В корпус щита 2 запрессована также втулка 3 для запрессовки подшипника.
2.6.Щетки и щеткодержатели
2.6.1.Основные сведения о щетках и щеточном
контакте

65
Щетки служат для съема и подвода тока к вращающемуся коллектору или контактным кольцам.
|
Классическая теория коммутации построена на предположении, что |
|
Рис. 2.51 |
между щеткой и коллектором (контактным кольцом) существует |
|
только контактная проводимость. Проведенные в последнее время |
||
|
||
|
работы в значительной степени изменили представление о природе щеточного |
|
|
контакта. Тем не менее они не привели пока к созданию новой общепринятой |
|
|
теории коммутации, на основании которой можно было бы создать |
|
|
законченную методику расчета. Переходное падение напряжения между |
|
|
щеткой и коллектором определяется материалом щетки и коллектора, |
|
|
давлением в месте контакта и состоянием пленки (политуры) на коллекторе. |
|
|
Пленка образуется в результате электрохимических процессов в зоне контакта |
|
|
и имеет сложную структуру, а процесс ее образования носит динамический |
|
|
характер. Непосредственно на меди имеется слой окиси, в наружную |
|
|
поверхность которого внедрены чешуйки графита. При вращении коллектора |
|
|
одновременно идет как сошлифовка пленки щеткой, так и образование новых |
|
|
слоев окиси (“политуры”) под влиянием температуры, влаги и |
|
|
электрохимических процессов. В правильно сконструированном щеточно- |
|
|
коллекторном узле политура держится устойчиво и обеспечивает стабильность |
|
|
всех параметров переходного контакта. На образование политуры влияют |
|
|
шероховатость и биение поверхности коллектора или контактного кольца. При |
|
|
малой шероховатости и биениях ((0,005 0,01) мм) политура образуется быстро |
|
|
и устойчива в процессе работы. Состояние поверхностной пленки можно |
|
|
определить визуальным осмотром: ровная пленка темно-серого или черного |
|
|
цвета с блестящей поверхностью свидетельствует о хорошем состоянии |
|
|
коллектора. |
|
|
Сырьем для изготовления щеток являются следующие компоненты: |
|
|
углеродистые материалы: кокс, графит; порошки металлические; порошки |
|
|
меди, олова, свинца; связующие вещества: различные смолы и т.д. |
|
|
Входящий в состав всех электрощеток графит имеет структуру с особым |
|
|
распределением междуатомных связей в кристаллической решетке. Эта |
|
|
особенность состоит в том, что вдоль слоев связи между атомами весьма |
|
|
сильные, а между слоями - слабые. Именно поэтому графит является |
|
|
материалом с относительно малым коэффициентом трения. |
|
|
Углеродистые материалы являются основной составной частью |
|
|
большинства марок щеток и определяет плотность, электрическую |
|
|
проводимость и антифрикционные свойства. Связующие вещества придают |
|
|
пластичность исходному материалу. |
|
|
Металлические порошки вводят в состав щеток для придания им ряда |
|
|
специфических свойств. При изготовлении щеток все входящие в состав массы |
|
|
компоненты тщательно размалываются, перемешиваются и прессуются. Далее |

66
смесь отжигается при температуре (800 1400) оС. Из полученных блоков или плит механическим способом получают требуемые размеры щеток.
При конструировании электрических щеток принимаются во внимание как требования к проектируемой машине, так и общие требования к щеткам, вытекающие из условий заделки токоведущих проводов, ее геометрических размеров и пр. Выбор марки щеток основывается главным образом на обобщении многолетнего опыта эксплуатации, так как химический состав и технология изготовления не позволяют точно определить поведение электрощетки в тех или иных условиях. Систематизация накопленного опыта дает возможность найти общие закономерности в методах подбора марок щеток:
1). По мере возрастания содержания меди повышается допустимая плотность тока с одновременным снижением коммутационных свойств.
2). При увеличении содержания легирующих добавок возрастает допустимая окружная скорость, увеличивается перегрузочная способность щетки по току и обеспечивается работа в тяжелых коммутационных условиях.
Наиболее широко применяются следующие марки щеток: 1). Медно-графито-свинцовые МГС5.
2). Медно-графито-свицовисто-оловянные МГС-7; МГС-8; МГС-74. 3). Графитовые ВТ-7.
2.6.2. Установка щеток
Радиальные щетки применяются для машин малой и средней мощности, а также для реверсивных машин рис.2.52. Одним из основных недостатков радиальных щеток является наличие нескомпенсированного опрокидывающего момента от силы трения Fтр . Результатом действия этого момента может быть неравномерный износ поверхности, соприкасающейся с коллектором или контактным кольцом: появление выработок на боковых сторонах в местах соприкосновения со стенками щеткодержателя (место А и В), зависание щетки в обойме щеткодержателя по месту выработок и увеличение искрения. Чтобы избежать этого необходимо обеспечить минимальный зазор между обоймой щеткодержателя и коллектора, а также
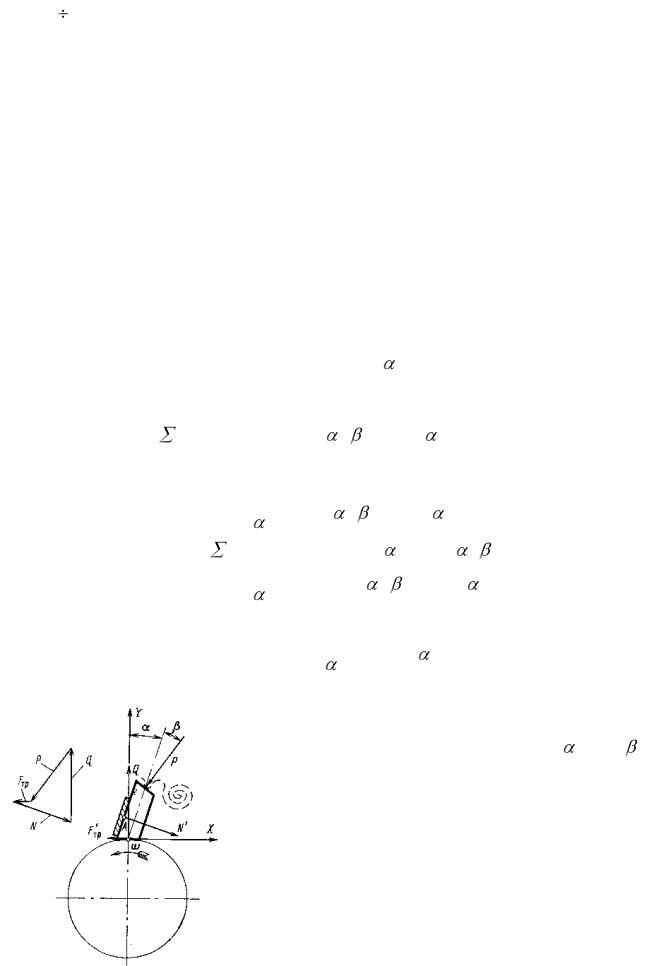
67
минимальный зазор между боковыми сторонами щетки и стенками щеткодержателя. Радиальный зазор даже для машин большой мощности никогда не должен превышать 1,5 мм, а для машин малой и средней мощности
- (0,8 1) мм.
Реактивные щетки применяются для машин средней и большой мощности. Схема такой щетки приведена на рис.2.53. При установке
реактивной |
щетки |
отсутствует |
некомпенсированный |
момент, |
|
|
опрокидывающий щетку в обойме щеткодержателя. |
||
Рис. 2.53 |
|
Щетка 1 постоянно прижата пружиной 3 к одной из |
||
|
|
стенок щеткодержателя 2, поэтому вторая |
стенка |
щеткодержателя часто отсутствует. На реактивную щетку действуют следующие силы:
1). Р - сила, развиваемая щеточной пружиной. 2). Fтр- сила трения щетки;
3).Q - реакция со стороны поверхности скольжения, направленная по нормали к этой поверхности.
4). N - сила прижатия щетки к стенке щеткодержателя. Выразим Q через давление щетки на коллектор:
|
|
|
|
Q = P |
|
at |
|
|
|
|
(2.18) |
|
|||
|
|
|
|
cos |
|
|
|
|
|
|
|||||
Из условия равновесия щетки под действием всех приложенных сил |
|||||||||||||||
можно записать: |
|
|
|
|
|
|
|
|
|
|
|
|
|
|
|
P y = 0; |
Q-P cos ( |
+ |
|
) – N sin |
= 0 |
|
(2.19) |
||||||||
После преобразований получаем: |
|
|
|
|
|
|
|
|
|
|
|
|
|||
P |
at |
|
- P cos ( |
+ |
) – N sin = 0 |
|
(2.20) |
||||||||
cos |
|
|
|||||||||||||
|
Px = 0; |
Fтр +N cos |
- P sin( |
+ ) =0 |
(2.21) |
||||||||||
P |
at |
|
Kтр – P sin ( + )+ N cos |
= 0 |
(2.22) |
||||||||||
cos |
|
||||||||||||||
Решив совместно (2.21) и (2.22) исключив из него N получим: |
|
||||||||||||||
|
|
P = p |
at |
|
(1+ Kтр tg |
) |
|
|
(2.23) |
|
|||||
|
|
cos |
|
|
|
|
|||||||||
|
|
|
|
|
|
|
|
|
|
|
|
|
|
|
|
|
|
где |
p- давление на щетку. |
|
|
|
|||||||||
|
|
|
|
Последнее |
выражение |
используется |
для |
||||||||
|
|
предварительного |
выбора |
углов |
и |
. |
|||||||||
|
|
Окончательно эти углы устанавливаются с учетом |
|||||||||||||
|
|
стандартов. После того как углы и будут выбраны |
|||||||||||||
|
|
и будет установлено давление щетки на коллектор |
|||||||||||||
|
|
с учетом всех особенностей машины, необходимо |
|||||||||||||
|
|
проверить по (2.21) |
или |
(2.22) значение N. |
По |
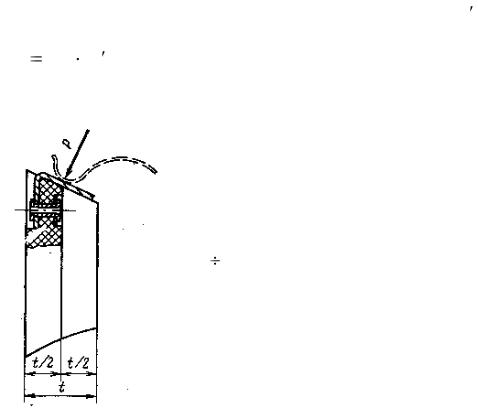
68
опыту конструирования эта сила не должна быть меньше ¼ силы прижатия щетки к коллектору. При малых N имеет место вибрация щетки.
Если у реактивной щетки изменить направление вращения коллектора, то изменится направление действия силы трения. Щетка с такой установкой получила название "волочащаяся" (рис.2.54). Характерной особенностью этих
Рис. 2.54 |
щеток является большая сила прижатия щетки к обойме N . |
|
|||||
|
Поскольку сила трения об опорную |
стенку корпуса |
|||||
|
|
||||||
щеткодержателя |
fN kт р N является демпфирующей |
при |
радиальных |
||||
перемещениях щетки, которые происходят во время работы, она оказывает |
|||||||
благоприятное |
воздействие на щеточный контакт. |
||||||
Установка |
волочащихся щеток |
применяется |
на |
||||
контактных |
кольцах машины. Расчет волочащихся |
||||||
щеток |
|
аналогичен |
расчету |
|
реактивных, |
||
только |
знак |
перед Fпр меняется на обратный. |
|
||||
Разрезные |
реактивные |
щетки |
применяются |
в |
|||
коллекторных |
машинах постоянного |
тока большой |
|||||
мощности |
((12 24) |
кВт) |
для |
улучшения |
|||
коммутации |
(рис.2.55). Они состоят из двух щеток |
||||||
одинаковой |
ширины t/2. В одной из щеток |
||||||
устанавливается |
общая нажимная шайба для упора |
||||||
щеточной |
пружины. Расчет разрезной щетки |
||||||
производится |
также как расчет обычно реактивной |
||||||
щетки шириной |
t. |
|
|
|
|
|
|
|
|
Улучшение |
|
|
коммутации |
||
происходит за счет более равномерного прижатия к коллектору каждой из |
|||||||
половин щеток. |
|
|
|
|
|
|
|
Применение |
разрезных щеток не требует никаких дополнительных |
||||||
Рис. 2.55 |
переделок в узле щеткодержателя. |
|
|
|
|
|
2.6.3. Щеткодержатели
Щеткодержатель выполняет следующие функции:
1). Определяет положение щетки относительно коллектора или контактного кольца в осевом или радиальном направлении.
2). Позволяет щетке по мере износа свободно перемещаться в радиальном направлении.
3). Осуществляет с помощью пружины постоянное нажатие на щетку с требуемым давлением.
4). Изолирует щетку и ее выводной конец от остальных частей машины. Требования, предъявляемые к конструкции щеткодержателя:
1). Обеспечение свободного радиального перемещения щетки.
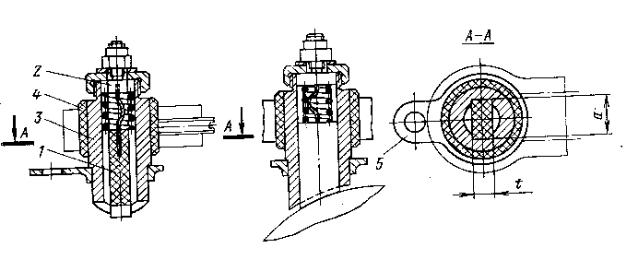
69
2). Сохранение постоянного нажатия на коллектор или контактное кольцо.
3). Интенсивное охлаждение щетки.
4). Отсутствие вибраций как самого щеткодержателя, так и щетки при работе машины.
5). Удобство осмотра и смены щеток.
6). Минимальная масса.
Постоянство нажатия на щетку обеспечивается характеристикой пружины. Отсутствие вибраций - жесткостью конструкции щеткодержателя и мест его крепления. Далее рассмотрим наиболее распространенные конструкции щеткодержателей.
В машинах малой мощности широкое применение получили щеткодержатели капсульного типа: конструкция приведена на рис.2.56.
Рис.2.56
В щеткодержателях такого типа ипользуются цилиндрические спиральные пружины сжатия. Обойма щеткодержателя 3, имеющая на наружной поверхности сетчатую накатку, опрессованную пластмассой 4. Слой пластмассы служит для изоляции щеткодержателя от корпуса машины. Канатик от щетки 1 впаян в отверстие направляющей 2. Нажатие на щетку осуществляется цилиндрической пружиной, которая упирается одним своим торцом на щетку, а другим на направляющую. Регулировка давления на щетку осуществляется с помощью болта 5.
Широкое применение в машинах средней мощности нашли штампованные или литые щеткодержатели, закрепленные на кольце из пластмассы (суппорт). Конструкция показана на рис. 2.57.
Преимуществом этой конструкции является то, что все щеткодержатели 1 со щеточными пружинами 3 закреплены на общем пластмассовом кольце 2 с помощью заклепок 4. Это дает возможность их точной центровки относительно оси вращения.
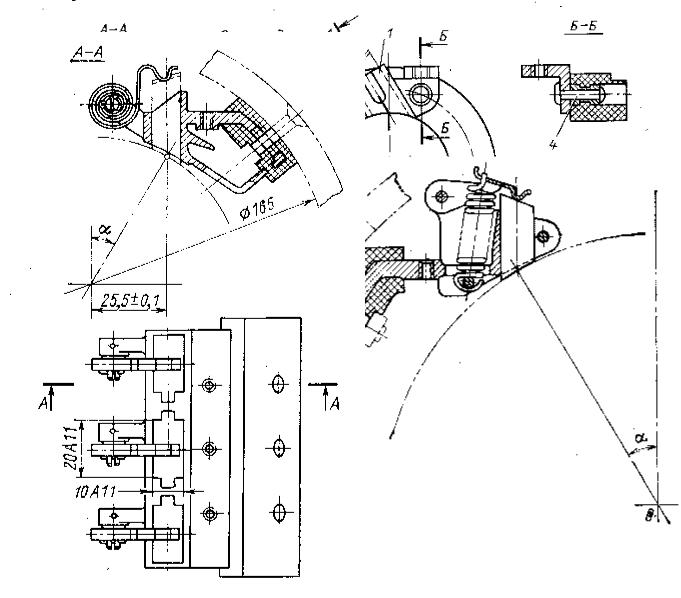
70
Для машин большой мощности наибольшее распространение получили литые щеткодержатели из алюминиевых сплавов. Конструкция одного из них приведена на рис. 2.58.
Эта конструкция со спиральными щеточными пружинами широко используется для коллекторных машин. Как правило в щеткодержателе имеется несколько гнезд для размещения нескольких щеток. От щита щеткодержатель изолирован в результате опрессовки опорной поверхности пластмассой. Добавочное ребро на корпусе увеличивает теплоотдающую поверхность щеткодержателя. Спиральные пружины запрессованы в стальные пальцы с вертикальными шлицами. Щеткодержатель крепится к подшипниковому щиту при помощи болтов.
Рис.2.57
Рис.2.58 |
Рис.2.59 |