
2074
.pdf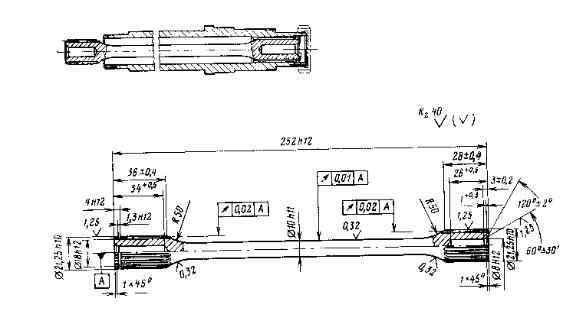
41
Для рассматриваемого вала выходной конец (Ø 2,5 j 6) цилиндрический. Стыковка с приводным механизмом в этом случае выполняется путем плотной посадки сопрягаемой детали (например шестерни) с одновременным сверлением втулки шестерни и вала и установки в отверстие фиксирующего штифта.
Для генераторов и некоторых двигателей больших мощностей применяются полые валы с расположенными внутри них гибкими валами (торсионами), которые служат для демпфирования ударных нагрузок и компенсации несоостностей между приводом и валом машины (например, привод генератора от поршневого двигателя). Чертеж такого вала приведен на рис. 2.26.
Рис. 2.26
Раньше для закрепления такого вала использовалась посадка его хвостовика на конус. В связи с тем, что при затяжке конуса происходит деформация полого вала и листа посадки подшипника, такие конструкции в настоящее время не применяются. Оба конца гибкого вала снабжаются шлицами (обычно одинаковыми). Гибкий вал закрепляется в полом валу с помощью пружинного разрезного кольца и накидной гайки как показано на рисунке. Накидная гайка служит одновременно и для закрепления подшипника. Между гайкой и торцом гибкого вала устанавливаются дистанционное кольцо и набор регулировочных шайб. Для валов малых диаметров и при невысоких частотах вращения могут применяться и более простые конструкции, где фиксация полого вала осуществляется, например, двумя разрезными пружинными кольцами.
2.3.2. Виды нагрузок на валы
2.3.2.1. Скручивающий момент от привода или нагрузки.
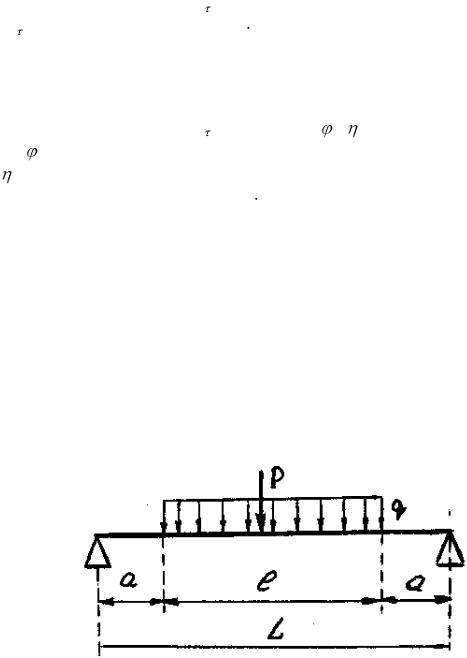
42
На валы в общем случае действуют следующие виды нагрузок: скручивающий момент от привода или нагрузки, нагрузка от массы частей ротора (при горизонтальном расположении ротора), нагрузка от остаточной неуравновешенности ротора, нагрузка от силы одностороннего магнитного притяжения, линейные и вибрационные нагрузки, изгибающий момент от внешней силы, приложенной к выходному концу вала. Рассмотрим действующие на вал нагрузки.
Скручивающий момент от привода или нагрузки для двигателя можно рассчитать по формуле:
|
М = 9561 Рном / n |
(2.5) |
где |
М - скручивающий момент, Н м; |
|
|
Рном - номинальная мощность, кВт; |
|
|
n - частота вращения; |
|
|
Для генератора: |
|
|
М = 9561SH cos / n |
(2.6) |
где |
cos - коэффициент нагрузки; |
|
|
- КПД; |
|
|
SH - номинальная мощность, кВ А. |
|
2.3.2.2. Нагрузка от веса деталей ротора
Данная нагрузка легко определяется по известным геометрическим размерам частей ротора. Она является распределенной, но часто в расчетах ее принимают как сосредоточенную.
Рассмотрим ошибку, которая возникает в этом случае. Для упрощения рассмотрим симметричный вал постоянного сечения с моментом инерции J (рис. 2.27) и одинаковые по абсолютному значению нагрузки: P для сосредоточенной силы; P = q l = q ( L – 2 a ) для равномерно распределенной нагрузки.
Рис. 2.27
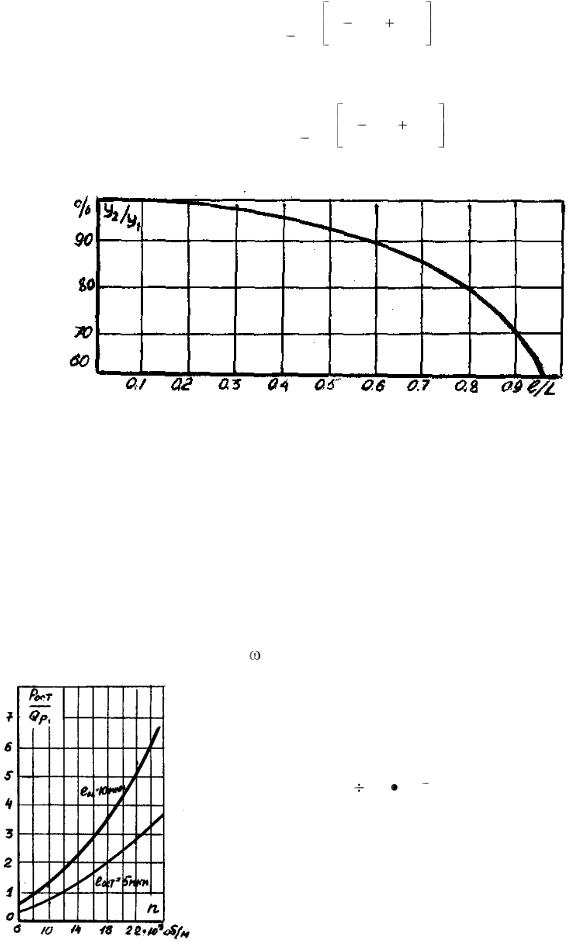
43
Прогиб вала под воздействием сосредоточенной нагрузки:
y1 = PL3 /( 48E J)
Прогиб вала под воздействием распределенной нагрузки:
y2 = |
PL4 |
|
1 |
|
5 |
3 |
a2 |
2 |
a4 |
|
48EJ (L 2a) 8 |
L2 |
L4 |
||||||||
|
|
|
где a - расстояние от опоры до наружного участка. Отношение прогибов равно:
y2 |
= |
L |
|
5 |
3 |
a2 |
2 |
a4 |
|
y1 |
(L 2a) 8 |
L2 |
L4 |
||||||
|
|
|
График этой зависимости представлен на рис. 2.28.
Рис. 2.28
(2.7)
(2.8)
(2.9)
Из графика следует, что при l / L > 0,3 для машин средней и большой мощности необходимо учитывать характер распределения нагрузки, так как замена ее на сосредоточенную может привести к значительному увеличению расчетного прогиба.
2.3.2.3. Нагрузка от остаточной неуравновешенности ротора
Данная нагрузка определяется из следующего выражения:
P ост = Q p 2 l остt = 1,096 10-2 Q p n 2 l ост ……………. (2.10)
где l ост - остаточное смещение центра массы ротора от оси вращения, м.
Современные методы балансировки позволяют балансировать роторы на рабочих частотах с точностью l ост = (5 10) 10 6 м.
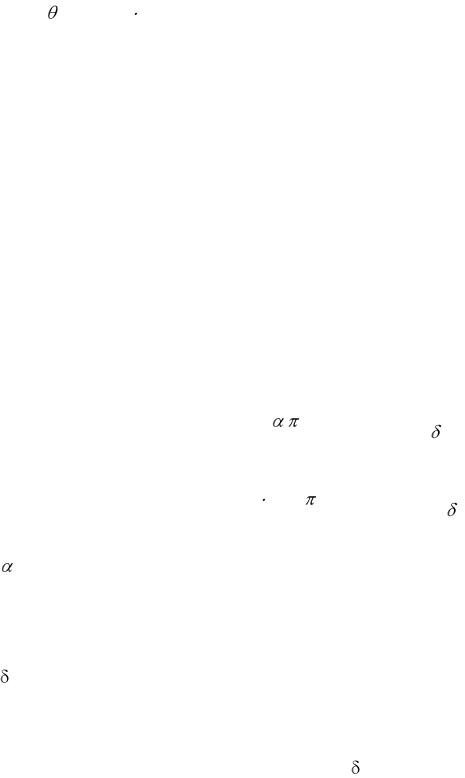
44
Зная точность балансировки роторов можно определить отношение P ост к силе тяжести Q pд для различных частот вращения:
Рост / рд = 1,116 10 -3 n2 lост |
(2.11) |
На рис. 2.29 эта зависимость представлена графически. Точка приложения силы Рост - центр массы ротора. Для высокоскоростных электрических машин в целях ограничения дополнительной нагрузки удельная неуравновешенность не должна превышать 5 мкм. Сила Рост Рис. 2.29 является вектором, вращающимся с частотой = 2
/ 30.
Относительно самого ротора этот вектор неподвижен.
2.3.2.4. Нагрузка от одностороннего магнитного притяжения
Появление сил одностороннего магнитного притяжения вызвано неизбежным изменением воздушного зазора в реальной машине из-за некоторого эксцентриситета центрах ротора и статора в геометрических, а также вследствие неидеальности самих цилиндрических поверхностей и несимметрии магнитного поля.
Силы одностороннего магнитного притяжения определяются для машин постоянного тока:
Р |
1 |
= 10 |
5 |
Da la (B/0,5) |
2 |
Кз |
l |
(2.12) |
0 |
|
|
|
Для машин переменного тока:
Р |
1 |
= 0,5 10 |
5 |
Da la (B/0,5) |
2 |
Кз |
l |
0 |
|
|
|
(2.13)
где - коэффициент полюсного перекрытия;
Da и la - внутренний диаметр статора и длина пакета;
Кз - коэффициент воздушного зазора (коэффициент Картера); l - эксцентриситет;
В- магнитная индукция в зазоре;
-величина воздушного зазора.
Значение максимума Р 01 для машин всех типов несколько меньше или
приближается к значению, определяемому следующим выражением: |
|
P max = 3 10 5 Da l a l / |
(2.14) |
Расчеты показали, что максимум Р 01 в машинах постоянного тока
достигается при индукциях в зазоре близких к 0,65 Тл, а в машинах переменного тока - при индукциях близких к 0,7 Тл.
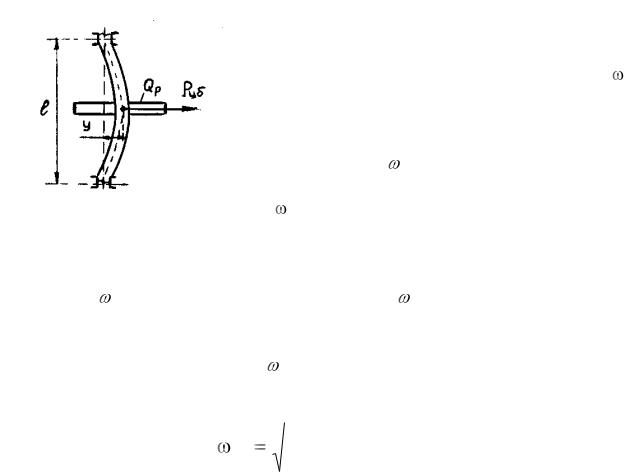
45
2.3.2.5. Общая нагрузка на вал
Нагрузки от веса частей ротора, от остаточной неуравновешенности и сил одностороннего магнитного притяжения чаще всего принимаются равномерно распределенными по длине пакета стали. Общая расчетная нагрузка от веса и магнитного притяжения находится путем их суммирования.
Сила от остаточной неуравновешенности является вращающимся вектором и не может быть сложена с названными выше нагрузками. Учитывая, что ее значения достаточно малы, ей как правило пренебрегают.
Определение общей нагрузки, действующей на вал, необходимо для определения прогиба вала от воздействия этих сил. Методики расчета прогиба вала широко известны из общей теории электрических машин и здесь не рассматриавются.
2.3.3. Критические частоты вращения
Вал электрической машины является упругим элементом с конечной жесткостью. При определенном значении частоты вращения может произойти совпадение частоты собственных колебаний вала с частотой вынужденных колебаний, вызванных вращением ротора. При таком совпадении частот прогиб вала резко увеличивается, наступает неустойчивый режим работы.
|
|
|
|
Сущность явления резонанса рассмотрим |
|||
|
|
|
на следующем примере. |
|
|||
|
|
|
|
Пусть невесомый вал с сосредоточенной |
|||
|
|
|
массой Q p вращается с угловой скоростью |
||||
|
|
|
(рис.2.30). Пусть под влиянием внешних сил, |
||||
|
|
|
вал получит прогиб у. Тогда центробежная |
||||
|
|
|
сила, действующая в сторону прогиба равна: |
||||
|
|
|
|
|
P цб = Q p |
2 Y , |
(2.15) |
|
|
|
где Q p - масса ротора; |
|
|||
|
|
|
|
- угловая частота вращения; |
|
||
Рис. 2.30 |
|
|
|
||||
|
|
Y- прогиб вала. |
|
|
|||
|
|
|
|
|
|
||
|
|
|
|
|
|
||
Эта центробежная сила уравновешивается упругими силами изогнутого |
|||||||
вала: |
|
|
|
|
|
|
|
Qp |
2 y = Ky |
|
или |
y(Qp |
2 – K) = 0 |
(2.16) |
|
где K- жесткость вала |
(т.е. сила, |
под влиянием которой вал |
получает |
||||
единичный прогиб). |
|
|
|
|
|
|
|
Из (2.16) следует, что при Qp |
2 = R прогиб вала может достигать любых |
значений. Это и характеризует условие резонанса. Отсюда может быть определено значение критической частоты:
|
|
k |
|
(2.17) |
к р |
Qр |
|||
|
|
|
|
46
В данном примере рассмотрен простейший случай, когда весом вала принебрегалось. В действительности на критическую частоту вращения значительное влияние оказывает масса вала, распределенный характер нагрузки и т.д. Расчет реальной критической частоты вращения - многофакторная задача.
Наиболее существенными факторами, оказывающими значительное влияние на критическую частоту вращения являются следующие:
1). Магнитное притяжение.
2). Характер распределения нагрузки.
3). Несимметрия момента инерции вала.
На практике при проектировании электрических машин обязательным условием является нахождение критической частоты вращения выше рабочего диапазона частот.
2.4. Узлы подшипников
2.4.1. Общие требования и классификация
Для вращающихся электрических машин узлы подшипников являются особенно важными. Статистика показывает, что 30 % отказов электрических машин приходится на подшипниковые узлы. Увеличение надежности этих узлов может резко повысить общую надежность электрических машин.
В общем случае к подшипниковым узлам предъявляются следующие требования:
1). Обеспечение точной сносности подшипников и отсутствие угловых перекосов.
2). Соблюдение геометрий посадочных мест.
3). Содержание допустимых температур при всех возможных режимах работы.
4). Обеспечение смазкой в процессе работы.
5). Защита смазки от выветривания и попадания в нее пыли и грязи из окружающей среды.
6). Удобство проведения регламентных работ в процессе эксплуатации. Основным элементом подшипникового узла является подшипник.
Подшипник - это часть опоры вала, непосредственно воспринимающий радиальные и аксиальные силы от ротора и обеспечивающий возможность его вращения. По роду трения, возникающего в подшипниках, их можно разделить на подшипники скольжения и подшипники качения.
Работа подшипников скольжения основана на замене сухого трения двух металлических поверхностей - шейки вала и вкладыша подшипника - жидкостным трением между двумя слоями масла, прилипающими к поверхности шейки и вкладыша. Принцип работы подшипника скольжения
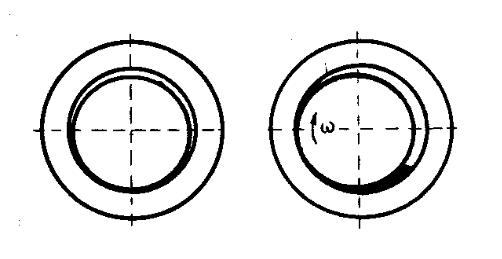
47
легко понять, рассмотрев положение шейки вала во вкладыше в неподвижном состоянии и при вращении. Рассмотрим рис. 2.31.
В неподвижном состоянии шейка вала прикасается к внутренней поверхности вкладыша в точке 1. При вертикальной нагрузке, вызываемой массой ротора эта точка будет внизу. В таком положении слой масла между шейкой вала и вкладышем отсутствует. При пуске машины в первый момент трение происходит между поверхностями шейки и вкладыша, смоченным маслом (полужидкостное трение). По мере нарастания вращения, увеличивается количество масла, захватываемого поверхностью шейки вала. Образуется клинообразная плоскость масла (рис. 2.31 а)) между поверхностью шейки вала и вкладышем (так называемый масляный клин), который как бы поднимает шейку вала и сдвигает ее по направлению острия клина. Таким образом, во время вращения машины, шейка вала и вкладыш подшипника непосредственно друг с другом не соприкасаются, так как отделены слоем вращающегося масла, а трение между двумя металлическими поверхностями заменяется трением между соседними слоями масла, имеющими различную частоту вращения. Для того, чтобы мог образоваться масляный клин между поверхностью шейки вала и вкладышем, между ними должен быть зазор. Величина клина зависит от диаметра шейки вала и скорости его вращения.
Рис. 2.31
Вкладыши подшипников скольжения изготавливают целиком из антифрикционного материала, обладающего малым коэффициентом трения и большой износостойкостью. Они могут иметь металлический корпус, залитый с внутренней стороны антифрикционным сплавом (составные вкладыши).
Материалом для целиковых вкладышей обычно служит бронза - сплав меди, свинца и олова. В последнее время, особенно для подшипников быстроходных машин, все большее применение находят металлокерамические вкладыши, прессованные из металлических порошков.
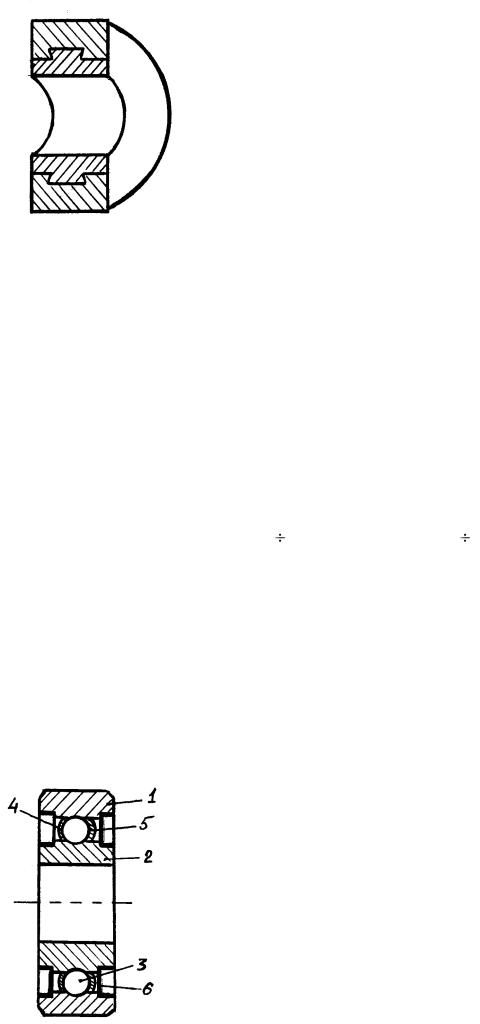
|
48 |
|
|
|
|
|
В составных вкладышах, стальной или чугунный |
||||
|
корпус залит антифрикционным сплавом (как правило |
||||
|
на оловянистой или свинцовой основе с обязательным |
||||
|
добавлением меди или сурьмы). Такие сплавы |
||||
|
называются баббитами. В корпусе вкладыша по его |
||||
|
внутренней поверхности для прочного соединения с |
||||
|
баббитовой |
заливкой, |
делают |
канавки |
|
|
трапецеидальной формы (рис.2.32). |
|
|
||
|
Наиболее |
часто встречающимися |
являются |
||
|
баббиты марки Б-83 и Б-16. Баббит марки 83, |
||||
|
обладающий лучшими механическими свойствами, |
||||
Рис. 2.32 |
используют в |
тяжелонагруженных |
подшипниках |
||
крупных электрических машин. |
|
|
|||
|
|
|
|||
Для смазки подшипников скольжения применяют жидкие минеральные масла, |
|||||
полученные |
перегонкой специальных |
сортов |
нефти. |
Наиболее часто |
применяют турбинное, индустриальное и машинное масла.
Для нормальной работы подшипника масло должно обладать определенными свойствами, из которых важнейшими являются вязкость и маслянистость.
Вязкость характеризует степень его густоты, а маслянистость - смачиваемость, т.е. способность прилипать к металлическим поверхностям.
Подшипники качения нашли наиболее широкое применение в малых и средних машинах. По сравнению с подшипниками скольжения они имеют целый ряд преимуществ, к числу которых можно отнести:
1). Меньшие потери на трение (коэффициент трения в подшипниках качения составляет всего 0,0011 0,0018, против 0,005 0,05 в подшипниках скольжения.
2). Возможность продолжительной работы до двух лет и более без добавления смазки.
3). Простоту обслуживания.
4). Меньшую стоимость подшипникового узла при массовом изготовлении подшипников.
Подшипник качения представляет собой два кольца: наружнее 1 и внутреннее 2, между которыми по окружности расположены тела качения 3.
Для равномерного распределения тел качения служит сепаратор 4, состоящий из двух колец 4 и 5, соединенных между собой заклепками. В этих кольцах имеются гнезда для размещения тел качения. На наружнем и внутреннем кольце имеются дорожки, по
которым катятся тела качения при вращении колец.
По форме тел качения, подшипники разделяют на шариковые и роликовые.
Шариковые подшипники применяют главным образом в машинах малой и средней мощности среди
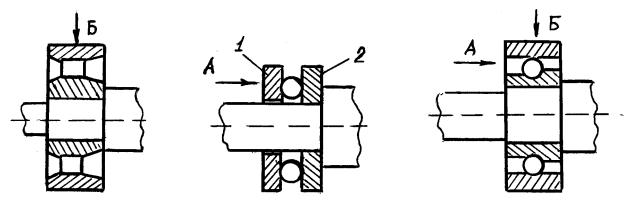
49
этих конструкций подшипников следует отметить закрытые подшипники со встроенными уплотнителями 6 (рис. 2.33), которые нашли широкое применение в последние годы. Встроенные в подшипники уплотнения выполнены в виде защитных шайб (стальных, резиновых, из органического пластика и т.д.), надежно защищающие подшипник от попадания пыли, грязи, продуктов износа щеток и других образивных частиц, снижающее ресурс работы подшипников.
Роликовые подшипники применяют в основном в машинах средней мощности, где нагрузки превышают допустимые для шарикоподшипников. Широкие допуски нагрузок на роликовые подшипники объясняется тем, что ролики имеют большую площадь соприкосновения с кольцами, чем шарики.
Рис. 2.33 В зависимости от воспринимаемой нагрузки подшипники качения разделяют на три группы:
1). Радиальные (рис. 2.34 а)) предназначены для компенсации радиальной нагрузки Б (как правило могут работать и при некоторой аксиальной нагрузке).
2). Упорные (рис. 2.34б)) предназначенны для компенсации чисто осевой нагрузки А. (кольцо 2 такого подшипника посажено на вал с натягом, а кольцо 1 вращается свободно.
3). Радиально-упорные (рис. 2.34 в)) предназначены для компенсации больших осевых нагрузок А при наличии радиальных нагрузок Б (конструктивной особенностью является наличие борта и конуса на наружнем кольце).
а) |
б) |
в) |
Рис. 2.34
Для защиты подшипников от вытекания смазки и попадания в них пыли и грязи, крышки устанавливают по отношению к валу машины с минимальным зазором, а в цилиндрической части крышек используют отверстия для заполнения подшипников смазкой.
Густые (консистентные) смазки, закладываемые в подшипники представляют собой мелкую механическую смесь минерального масла (90 %) и загустителя. Смазка уменьшает трение скольжения, способствует более
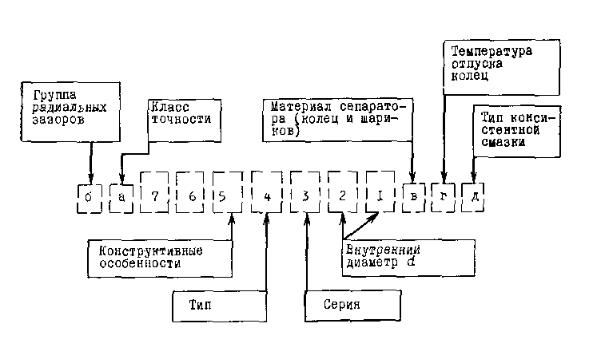
50
равномерному распределению и отводу тепла, служит для защиты от коррозии. Так как подшипники качения находят широкое применение в электрических машинах в сравнении с подшипниками скольжения, остановимся на их конструкции более подробно.
2.4.2. Подшипники качения
Условное обозначение подшипника качения (ГОСТ 3189-75), наносимое обычно на торце наружного кольца, состоит из семи условных цифр, двух дополнительных знаков впереди и трех сзади. В условном обозначении (рис.2.35) закодированы геометрические размеры, класс точности и другие параметры.
Внутренний диаметр подшипника d (1 и 2) обозначается тремя способами, в зависимости от номинального значения:
1). При d< 10 мм на месте 1 ставится диаметр в мм, а обозначение серии переносится на место 2.
2). При d от 10 до 20 мм условное обозначение следующее: d = 10-00; d =12-01; d =15-02 и d =17-03.
3). При d > 20 мм на листе 1 и 2 ставится частное от деления внутреннего диаметра на пять, так как все большие диаметры всегда кратны пяти. Например: d 5,15 и d 30 получат соответственно обозначения 5: 02 и 5: 06.
Рис. 2.35
Серии подшипников 3 и 7, применяемые в машинах, имеют следующие обозначения:
1). Особо легкая узкая 7000100.
2). Особо легкая нормальная 100.