
1756
.pdf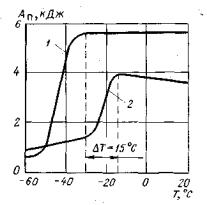
Рис. 4. Зависимость поглощенной энергии удара от температуры испытаний образцов ОХУТТ из
стали Х-70 контролируемой прокатки (/) и стали нормализованной 14Г2ФА-У (2)
С сталь контролируемой прокатки (кривая 1) и нормализованная (кривая 2) разрушаются вязко, однако сопротивление вязким разрушениям у стали Х-70 на 40 % выше, чем у 14Г2АФ-У. При этом нормализованная сталь практически не имеет температурного запаса вязкости, а у стали Х-70 он составляет | ∆T | = 15 °С. Известно, что при распространении разрушения в газопроводе охрупчивающим фактором наряду с отрицательной температурой является скорость деформирования металла. Поэтому отсутствие температурного запаса вязкости у стали 14Г2АФ-У в условиях газопровода может привести к хрупкому разрушению.
Для большинства сталей уменьшение вязкой составляющей в изломе от 100 до 80 % приводит к заметному снижению поглощенной энергии удара. В целях сопоставимости данных по различным сталям целесообразно в технических условиях на поставку труб рекомендовать определение поглощенной энергии на образцах ДWТТ производить при минимальной температуре эксплуатации.
20
1.4. Методика проведения натурных испытаний отрезков газопровода
Натурные пневматические испытания отрезков трубопроводов сопровождаются взрывами большой мощности, распространением ударной волны на расстояние до нескольких километров и разлетом отделившихся частей на несколько сот метров. Поэтому проводятся они вдали от населенных пунктов, зданий и других сооружений.
При натурных испытаниях используют отрезок газопровода длиной 150—250 м с приваренными на его торцах сферическими заглушками. Выбор такой длины испытываемой секции не случаен. Для современных мощных газопроводов особенно опасны вязкие протяженные разрушения, предупредить которые наиболее трудно. Для изучения вязкого характера разрушения необходимо обеспечить длительное поддержание давления в вершине трещины. При истечении сжатого газа из разрушившегося газопровода потоки перемещаются в горизонтальной и вертикальной плоскостях. Взаимодействие потоков приводит к образованию внутри секции трех областей с различным по величине давлением: рв—давление в вершине движущейся трещины; рд — давление в диаметрально противоположной зоне; рр — давление на концевых участках секции, которое в начальный момент разрушения равно испытательному давлению.
Движение газа в зону разрушения осуществляется за счет перепада давления в трубе. Благодаря постоянному поступлению сжатого газа из концевых участков испытываемой секции в область вершины трещины давление рв поддерживается на уровне, достаточном для распространения разрушения. Максимальная скорость изменения давления в вершине трещины (скорость декомпрессии) достигается не мгновенно, а в течение некоторого промежутка времени от момента инициирования разрушения.
Средняя скорость перемещения волны пониженного давления вдоль оси трубопровода составляет для природного газа
21
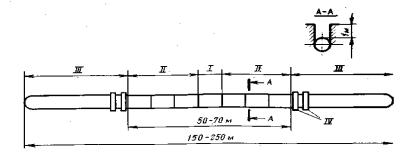
примерно 400 м/с. Это значение принимают при определении оптимальной длины испытываемой секции. Расчет показывает, что при ожидаемой средней скорости распространения трещины 200 м/с длина трубной секции должна быть не менее 150 м. При большей скорости распространения трещины общую длину испытываемого отрезка увеличивают до 200—250 м.
В целом испытываемый отрезок газопровода состоит из трех участков, каждый из которых выполняет определенную функцию (рис. 5). В центре отрезка находится труба инициирования разрушения. По обе стороны от нее расположены исследуемые участки, на которых регистрируются параметры разрушения. Исследуемые участки заканчиваются ограничителями разрушений, предназначенными для остановки трещины. Они могут быть различной конструкции. Далее идут концевые участки, которые являются постоянными и служат для аккумулирования энергии сжатого воздуха, необходимого для поддержания давления в вершине трещины. Концевые участки прочно закрепляются в траншее бетонными пригрузами, засыпаются грунтом для предотвращения продольных и поперечных перемещений.
Рис. 5. Схема отрезка газопровода для натурных испытаний: 1 — труба для инициирования разрушения; //
— исследуемые участки; /// — постоянные концевые участки (ресиверы); IV—ограничители разрушений
Разрушение инициируется в центральной трубе с помо-
22
щью поверхностного надреза и местного взрыва. При этом толщина стенки трубы под надрезом должна с небольшим запасом выдерживать заданное разрушающее давление. Длина инициирующего надреза обычно составляет 400 мм, что значительно превышает критическую длину трещины. Это способствует быстрому образованию и распространению трещины в центральной трубе.
Большую техническую трудность при натурных испытаниях представляет дистанционная регистрация параметров разрушения: температуры металла труб, скорости распространения трещины, значения разрушающего давления и скорости его падения в различных сечениях испытываемой секции, размеров зоны пластических деформаций металла. Температура металла труб на различных участках секции определяется с помощью ряда термопар с автоматической записью на электронном потенциометре. Разрушающее давление фиксируется самопишущим манометром, соединенным по отводному трубопроводу с испытываемой секцией. Скорость разрушения регистрируется с помощью записи временных интервалов разрыва проволочных или других датчиков на запоминающем электронном осциллографе или магнитографе. Датчики скорости представляют собой калиброванную проволоку, покрытую изоляцией. Датчики наклеивают по ходу будущего разрушения с определенным шагом. Недостатком этого метода записи скорости разрушения является возможный разрыв датчика пластической деформацией перед вершиной движущейся трещины. Однако это не должно принципиально влиять на общий характер изменения скорости разрушения, так как временная ошибка для всех датчиков одинакова.
Скорость падения давления в различных сечениях испытываемого отрезка газопровода измеряется с помощью специальных датчиков и регистрируется на электронном осциллографе или магнитографе. Датчики ввинчивают в сквозное отверстие с резьбой в стенке трубы. С внешней стороны датчики закрывают приваренными к трубе толстостенными металлическими колпаками, предотвращающими их повреждение при
23
раскрытии бортов труб. Деформация металла труб в процессе разрушения регистрируется с помощью тензодатчиков, наклеенных на поверхность в поперечном и продольном направлениях. Датчики размещаются непосредственно около ожидаемой траектории трещины и с некоторым смещением от нее по периметру трубы. Тензодатчики регистрируют значения деформаций до 5%. Записанные деформации позволяют оценить размер пластической зоны перед вершиной движущейся трещины и с учетом знака определить изменение формы трубы в разные моменты процесса разрушения.
Подготовленный к испытанию исследуемый участок опускают в траншею и приваривают к постоянным концевым участкам испытываемого отрезка. В зависимости от цели эксперимента трубы полностью или частично засыпают грунтом. С помощью компрессорной установки поднимают давление в отрезке газопровода до заданного значения и локальным взрывом инициируют разрушение из центральной трубы. Нагружение трубы производят воздухом или природным газом (метаном). Скорость декомпрессии метана и воздуха в трубопроводе примерно одинаковая, и поэтому выбор нагружающей среды практически не влияет на результаты эксперимента. В то же время использование воздуха вместо природного газа упрощает технику проведения испытания и исключает возможность возгорания при взрыве.
Натурные испытания отрезков газопроводов позволяют выявить следующие данные: длину и характер распространения разрушения (вязкий или хрупкий); траекторию и скорость распространения трещины; влияние грунта, температуры и давления па работу металла в трубопроводе; установить сопротивление металла труб разрушению.
2. СТАЛИ ДЛЯ ТРУБ ГАЗОНЕФТЕПРОВОДОВ
Во второй половине XX в. магистральные трубопроводы динамично развивались по всем основным параметрам; диа-
24
метру труб, величине рабочего давления, дальности перекачки. Заметно снизилась температура транспортируемого газа, резко возросла мощность газопроводов.
В короткий исторический срок была создана новая, важная отрасль народного хозяйства — трубопроводный транспорт, предназначенный для доставки нефти, газа и их продуктов на дальние расстояния. Причем нефть и газ становятся одним из основных источников энергии и сырья для многих отраслей народного хозяйства, а их доля в топливноэнергетическом балансе страны составляет примерно 70 %.
Бурное развитие трубопроводного транспорта потребовало высоконадежных труб и соответствующего развития металлургической промышленности, как в количественном, так и в качественном отношении.
Влияние магистральных трубопроводов на развитие металлургической промышленности особое. Можно без большого преувеличения сказать, что требования, выдвигаемые этой отраслью, способствовали коренному усовершенствованию технологии производства стали в части методов ее легирования и очистки от вредных примесей и разработки нового процесса прокатки. Применение контролируемой прокатки обеспечило широкую возможность управлять структурной и свойствами стали.
Нефтяная и газовая отрасли промышленности как ведущие в народном хозяйстве являются крупными потребителями стали и труб. Надежная работа магистральных трубопроводов оказывает большое влияние на многие отрасли промышленности, особенно на работу предприятий с непрерывным циклом производства, потребляющих транспортируемые по трубопроводам продукты в качестве сырья и источников энергии. Разрушения трубопроводов крайне опасны для близко расположенных сооружений, людей и окружающей природы. Например, разрушение нефтепровода может нарушить экологическое равновесие крупного района на продолжительный срок.
Все изложенное обусловливает особо жесткие требования, которые предъявляются к надежной, безотказной работе
25
магистральных трубопроводов в течение многих лет их эксплуатации. Большое народнохозяйственное значение магистральных газонефтепроводов, необходимость исключения хрупких разрушений «лавинного» типа и протяженных вязких разрывов потребовали производства стали высокой вязкости и хладостойкости. Таких требований не предъявляли к металлургической промышленности никакие другие потребители.
Сложность производства высококачественных сталей усугублялась большой потребностью нефтяной и газовой отраслей промышленности в трубах, измеряемой несколькими миллионами тонн в год. Необходима не только качественная, по и дешевая массовая сталь, которую можно поставлять в больших количествах, не прибегая к ее легированию дорогостоящими и дефицитными элементами.
Примерно до 1960 г., когда диаметр магистральных трубопроводов не превышал 820 мм, а рабочее давление — 5,5 МПа и строительство осуществлялось в средней и южной полосе страны, производство сталей для труб не представляло особой сложности. Трубы изготавливали при диаметре менее 500 мм из стандартных углеродистых сталей различных марок, а при диаметре 530—820 мм — из простых горячекатаных низколегированных или нормализованных сталей. Много внимания уделяли получению наиболее дешевых труб, в частности труб из полуспокойных сталей и наиболее простых по составу марганцевистых сталей типа 19Г. В этот период требования по вязкости сталей для труб не предъявлялись. Однако с конца 50-х годов после широкого распространения метода производства прямошовных труб на прессах и правки их в экспандерах когда наклеп и связанное с ним повышение предела текучести и временного сопротивления разрыву рассматривали как способ повышения прочности стали труб, резко возросло число разрушений по основному металлу труб при испытании их на прочность и в процессе эксплуатации. С увеличением диаметра газонефтепроводов до 1020 мм потребовалось повысить надежность труб, повысить прочность и вязкость стали, так как простые марганцевистые стали, не позво-
26
лили надежно решить эту проблему.
В60-70 х. годах прошлого столетия были проведены большие работы по созданию недорогих низколегированных сталей с гарантированной вязкостью на основе легирования их марганцем и кремнием. Лучшей из них была сталь типа 17Г1С
иее модификации. Были улучшены методы выплавки и раскисления стали в целях повышения ее однородности и снижения вредных примесей. Листопрокатные цехи перешли на поперечную прокатку металла, когда лист раскатывался в направлении, перпендикулярном к оси слитка. Была разработана технология обработки стали синтетическими шлаками, что значительно повышало характеристики ее по вязкости и пластичности. В это же время были разработаны и опробованы при производстве труб первые нормализованные дисперсион- но-упрочненные стали типа 15Г2СФ и другие, однако для их выплавки уже требовался ванадий и другие карбидо- и нитридообразующие элементы.
Врезультате проведенных работ временное сопротивление разрыву металла труб было повышено с 480 до 520—540
МПа, введены сдаточные требования по ударной вязкости (KCU-40≥0,3 МДж/м2). Полученные стали, позволили достаточно надежно обеспечить работоспособность труб диаметром до 1020 мм при положительной температуре перекачки газа.
Однако даже высококачественные нормализованные стали не обеспечивали удовлетворительное сопротивление хрупкому распространению разрушений по газопроводу при температуре эксплуатации от —5 до —15 °С, что необходимо для газопроводов, эксплуатирующихся в северных районах страны. В связи с переходом в начале 70-х годов на строительство газопроводов диаметром 1420 мм с рабочим давлением 7,5 МПа потребовалась разработка принципиально новых типов сталей, получаемых методом контролируемой прокатки. В настоящее время это основной тип стали для труб диаметром 1020— 1420 мм при давлении 7,5 МПа.
Изложенное показывает, что стали, применяемые для из-
27
готовления труб магистральных газонефтепроводов и промысловых сетей, можно укрупнено свести к трем основным типам:
углеродистые; низколегированные на базе марганца и кремния; стали контролируемой прокатки.
В настоящей главе показаны технические возможности различных типов сталей и рациональные области их применения в газонефтепроводах.
2.1. Основные понятия о стали
Сталь — сплав железа с углеродом, включающий ряд примесей. Например, строительная углеродистая сталь может содержать углерода 0,04—0,3 %, марганца 0,1 — 1 %, кремния до 0,4%, серы и фосфора обычно не более 0,04%. В низколегированную сталь вводят специальные легирующие элементы с целью получения определенных ее свойств. В строительные низколегированные стали вводят марганец, кремний, а также микролегирующие элементы — ванадий, ниобий, титан и др. Низколегированная сталь маркируется цифрами и буквами. Например, в стали, маркированной шифром 09Г2ФБ, первые цифры 09 показывают среднее содержание углерода в сотых долях процента, первая буква Г — основной легирующий элемент (в данном случае марганец), причем следующая за буквой цифра показывает его количество — до 2%, буквы Ф и Б
—другие легирующие элементы (в данном случае ванадий и ниобий), а так как цифр за ними не стоит, то их количество составляет менее 1%. При маркировке сталей приняты следующие обозначения элементов: С — кремний, X —хром, Т — титан, М — молибден, Ю — алюминий, Р — бор, Д —медь, Н
— никель, О — кислород, А— азот и т. д.
2.1.1. Производство стали
Основной объем стали для производства труб выплавля-
28
ется в мартеновских печах и кислородно-конверторных агрегатах, а в небольших объемах — в электропечах. Объем стали, выплавляемой в кислородных конвертерах, из года в год увеличивается. Основное преимущество этих агрегатов — высокая производительность. Качество кислородно-конвертерной стали существенно зависит от степени чистоты применяемого для продувки кислорода. Фактически мартеновская и кисло- родно-конвертерная сталь применяется для изготовления труб на равных условиях, На качество и свойства стали большее влияние, чем метод выплавки, оказывают степень раскисления, характер микролегирования, методы прокатки и другие процессы производства.
По степени раскисления в процессе выплавки стали подразделяются на кипящие, т. е. не раскисленные кремнием, на полуспокойные, содержащие 0,04—0,15% кремния, и спокойные, в которых количество кремния составляет 0,16— 0,30%- Кроме кремния, спокойные стали раскисляются алюминием. Полуспокойная и кипящая стали, характеризуются наименьшей однородностью. Однако при их производстве обеспечивается максимальный выход годного металла, это наиболее дешевые сорта стали. Спокойная сталь более однородна по составу, однако выход годного металла при ее производстве на 12—15% меньше, чем при выплавке полуспокойной и кипящей сталей, так как у слитка обрезается верхняя прибыльная часть, в которой сосредоточивается основное количество, примесей, загрязняющих сталь.
Окончательное раскисление низколегированных сталей алюминием и кальцием, их модификация редкоземельными металлами (РЗМ) производится в разливочном ковше с целью улучшения структуры катаной стали, регламентации количества и формы неметаллических включений. Обработка стали в ковше РЗМ устраняет прочные остроугольные включения в металле, являющиеся концентраторами напряжений, переводит остатки оксидов и сульфидов в прочные глобулярные включения, не снижающие работоспособность стали. С повышением чистоты стали, ее однородности увеличиваются вяз-
29