
1756
.pdfи расчетной схемы, трубопровод является сложным, дорогостоящим, исключительно металлоемким и ответственным сооружением. Этим объясняется большое внимание, уделяемое разработке вопросов эксплуатационной надежности магистральных трубопроводов как в России, так и во многих странах мира.
Прочность магистрального трубопровода, его эксплуатационная надежность определяются в первую очередь силовыми факторами, свойствами и качеством труб. Для магистральных трубопроводов основными нагрузками являются внутреннее давление и продольные усилия, вызванные температурным перепадом в линейной части трубопровода вследствие различия температурных условий строительства и эксплуатации. Нормы и правила расчета, необходимые формулы и коэффициенты принимаются согласно СНиП 2.05.06—85.
Достаточно точному расчету поддаются только кольцевые напряжения, а продольные напряжения и устойчивость трубопровода определяются не только влиянием температуры, но и условиями взаимодействия трубопровода с грунтом, наличием пригрузов, опор, компенсаторов и др. Наблюдавшиеся разрушения трубопроводов не были связаны с недостаточным запасом прочности, т. е. не вызваны превышением действующих кольцевых напряжений над расчетными. Большинство разрушений было обусловлено недостаточным сопротивлением стали труб зарождению трещин, потерей продольной устойчивости при температурных воздействиях, поперечным изломом труб при просадке грунта, коррозийными повреждениями, отклонением действительных условий нагружения от расчетных в конструкциях подводных переходов в условиях весенних паводков.
Поэтому эксплуатационную надежность трубопроводов обеспечивают путем предупреждения разрушений. Так, разрушения, связанные с недостаточным сопротивлением зарождению и распространению трещин, предупреждают металлургическими методами — повышением механических свойств, качества стали и сварных соединений труб, а разрушения, свя-
10
занные с потерей местной или общей устойчивости трубопроводов, — совершенствованием методов расчета и проектирования и повышением качества выполнения строительномонтажных работ; разрабатываются и совершенствуются меры противокоррозийной защиты.
1.2. Некоторые данные о разрушениях труб на газонефтепроводах
Разрушения трубопроводов по их происхождению можно разделить на два типа:
разрушения при предпусковых испытаниях, связанные с дефектами труб, их повреждением в процессе транспортировки и строительства;
разрушения в условиях эксплуатации, происходящие изза почвенной коррозии, дефектов проектирования и выполнения: строительно-монтажных работ, нарушений режимов эксплуатации и в меньшей степени из-за скрытых дефектов труб.
Разрушения в основном металле чаще происходят в сталях с недостаточными вязкими свойствами. Такие разрушения характерны для труб диаметром 720—1220 мм, изготовленных из низколегированных горячекатаных и нормализованных сталей.
По характеру распространения разрушений последние подразделяются на хрупкие, смешанные и вязкие. Наибольшая из известных протяженность вязкого разрушения составляла 850 м, хрупкого — 2400 м. Разрушения газопроводов, длина которых превышала 100 м, составили около 6 % общего числа разрушений [1].
С ростом числа построенных газонефтепроводов повышенной мощности диаметром 1020—1220 мм из низколегированных нормализованных сталей заметно увеличилось число длинных разрывов на газопроводах и разрушений труб по сварным соединениям па нефтепроводах. Такой характер разрушений в газонефтепроводах связан в одних случаях с увеличением запаса, упругой энергии сжатого газа, в других — с не-
11
достаточными свойствами сварных соединений и наличием циклических нагрузок.
В мощных газопроводах диаметром 1420 мм при рабочем давлении 7,5 МПа из сталей контролируемой прокатки, свойства которых полностью удовлетворяли требованиям СНиП 2.05.06 — 85, число разрушений по дефектам труб незначительно, хотя таких газопроводов построено и введено в эксплуатацию более 20 тыс. км.
Рассматривая причины наблюдавшихся разрушений газонефтепроводов из-за дефектов труб, следует отметить, что основное их количество приходится на сварные трубы из нормализованных или горячекатаных сталей типа 17ГС, изготовленных на давно построенных заводах с недостаточным объемом физических средств контроля качества основного металла и сварных швов. Одни такие заводы уже прекратили поставлять трубы для газонефтепроводов, другие провели соответствующую реконструкцию или в ближайшее время будут реконструированы. Производство термоупрочненных труб из дешевой и простой стали 17Г1С обеспечило надежную эксплуатацию газонефтепроводов при снижении их металлоемкости на
15 %.
1.3. Методы оценки сопротивления металла труб разрушению
Методы оценки сопротивления металла разрушению и определяемые характеристики должны позволять давать объективную оценку работоспособности труб и сравнивать свойства сталей по следующим показателям: прочности, вязкости и пластичности; сопротивлению зарождению трещин в концентраторах; сопротивлению распространению хрупким и вязким разрушениям в газопроводах; сопротивлению зарождению усталостных трещин в нефтепроводах,
До начала 60-х годов оценку сопротивления разрушению» (в то время главное внимание уделяли хрупкому разрушению) производили инженерно-экспериментальными мето-
12

дами, путем испытания различных типов образцов, например, Шарпи и Менаже (по ГОСТ 9454—78). Сериальные испытания таких образцов в широком интервале температур (от вязкого до хрупкого состояния металла) уже много десятков лет широко применяются в инженерной практике для оценки ударной вязкости или доли волокна в изломе.
Наряду с указанными простыми образцами Шарпи и Менаже в научно-исследовательской практике нашли широкое применение более крупные образцы, испытываемые на внецентренное растяжение, статический изгиб, двуосное растяжение и ряд типоразмеров широких образцов с боковыми надрезами.
В 60-х годах в научных организациях много внимания уделялось развитию линейной механики разрушения с испытанием на изгиб призматических образцов со специальным надрезом и компактных образцов на внецентренное растяжение с определением ряда характеристик материала — коэффициента интенсивности напряжения Кс, критического раскрытия трещины с, энергии продвижения трещины (Ic-интеграл).
В начале 70-х годов методы линейной механики разрушения получили широкое научное признание, при этом в ряде стран, в том числе и в СССР, были разработаны проекты соответствующих стандартов. Однако практического применения эти методы для строительных сталей низкой и средней прочности не получили, за исключением высокопрочных сталей в толстостенных конструкциях.
Линейная механика разрушения изучает поведение дефектов металла типа трещин, сопротивление металла их подрастанию. Теоретически механика разрушения позволяет установить допустимые размеры дефекта, напряжение, вызывающее подрастание трещин, при превышении которого следует ожидать разрушения конструкций в реальных условиях их эксплуатации.
Применение линейной механики разрушения для высокопрочных металлов с прочностью 1000—2000 МПа позволи-
13

ло добиться крупных успехов. Для трубопроводов, строящихся из высокопластичных и высоковязких сталей с временным сопротивлением разрыву 500—700 МПа при толщине стенки труб 12— 25 мм, аппарат линейной механики разрушения в настоящее время еще не позволяет прогнозировать поведение металла в конструкции, что связано с отсутствием состояния плоской деформации при указанных толщинах и возможно низких температурах.
Размеры дефектов, определяемые для сталей газопроводов из положений механики разрушения, значительно отличаются от фактических значений критической длины трещины, способной к самопроизвольному развитию в магистральных трубопроводах. Такое различие не случайно, ибо математическое описание состояния металла в вершине дефекта в условиях значительной пластической деформации несовершенно. Кроме того, наблюдаются изменения свойств металла при увеличении степени и скорости деформации, что приводит к различному поведению дефекта на стадиях докритического и закритического развития. Сопротивление металла труб быстро распространяющемуся протяженному вязкому или хрупкому разрушению с позиций линейной механики разрушения оценить невозможно.
Поэтому линейная механика разрушения пока не нашла применения при решении проблемы прочности нефтегазопроводов, ибо она не позволяет правильно классифицировать стали труб по их работоспособности в конструкции. В оценке свойств стали труб все еще превалируют экспериментальные методы. Однако исследовательские работы по совершенствованию положений линейной механики разрушения и накоплению данных о возможности их применения при расчете магистральных трубопроводов проводятся интенсивно. Как показали исследования, такие характеристики, как Ic-интеграл и с, являются перспективными для оценки сопротивления металла труб зарождению трещины.
Для современных мощных магистральных газопроводов
14
необходимы трубы из особо вязких сталей с временным сопротивлением разрыву 600—700 МПа, способные противостоять хрупким и вязким протяженным разрушениям. Трещиностойкость таких сталей толщиной 12—25 мм практически невозможно определить методами линейной механики разрушений. Поэтому характеристики трубных сталей, определяющие сопротивление хрупким и вязким разрушениям, устанавливают в основном инженерно-экспериментальными методами при серийных испытаниях образцов или отдельных отрезков газопроводов.
Наиболее широкое распространение практически во всех странах мира получил метод испытания на ударный изгиб образцов Шарпи и полнотолщинных образцов типа ДWТТ. В результате испытаний определяют ударную вязкость, значение вязкой составляющей в изломе и поглощенную энергию разрушения. Методики и результаты испытаний отрезков газопроводов и отдельных труб будут рассмотрены ниже.
1.3.1. Определение ударной вязкости на стандартных образцах
Ударную вязкость металла труб определяют по ГОСТ 9454— 78 на образцах 10x10x55 мм или меньшей толщины, предусмотренной государственным стандартом. Радиус дна надреза r=1±0,07 мм (надрез Менаже), r = 0,25±0,025 мм (Шарпи) и r≤0,10 + 0,17 для образцов с усталостной трещиной. Образцы испытываются на 3-точечный ударный изгиб на маятниковых копрах с энергией удара до 300 Дж. Скорость движения маятника в момент нанесения удара должна быть 5±0,5 м/с. Расстояние между опорами для установки образцов должно быть 40±0,5 мм.
Температура испытания образцов указывается в технически?: условиях или стандартах на поставку труб или стали, а при исследовательских работах испытания выполняются в интервале температур, обеспечивающем получение на образцах изломов от вязкого до полностью хрупкого.
15
В результате испытаний определяют работу удара (энергию разрушения) или ударную вязкость. Результаты испытаний шифруются KCU, KCV или KCT, где KC — символ ударной вязкости, а U, V и T указывают на остроту надреза (соответственно Менаже, Шарпи, усталостная трещина). При необходимости после буквенных обозначений вводятся индексы, из которых нижний указывает температуру испытания в оС, а
верхний— коэффициент уменьшения толщины испытываемого образца. Ударная вязкость определяется по формуле
KC=K/S0
где К — работа удара, израсходованная на разрушение образца;. S0 — площадь поперечного сечения под надрезом перед испытанием образца.
1.3.2. Испытания полнотолщинных образцов
Оценка свойств металла на полнотолщинных крупноразмерных образцах типа ДWТТ пока не стандартизирована и производится в соответствии с требованиями технических условий на. поставку труб.
Образцы изготовляют поперечные по отношению к продольной оси трубы с размерами, приведенными на рис. 2. Для устранения трубной кривизны образцы правятся посредством статической нагрузки так, чтобы остаточный прогиб не превышал 2 мм. Испытывают образцы на 3-точечный ударный изгиб на маятниковых копрах или копрах с падающим грузом с запасом энергии молота 5—15 кДж.
16
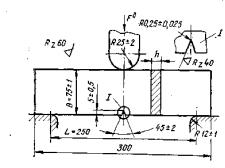
Рис. 2. Эскиз и схема испытания полнотолщинного образца типа DWTT на ударный изгиб
Мощность копра подбирают таким образом, чтобы энергия удара не менее чем на 1/3 превышала энергию разрушения образца. Надрез на образцах наносят фрезой (резаный надрез) или обжатием специальным пуансоном (прессованный надрез). Центр удара по образцу не должен отклоняться более чем на 1 мм от оси надреза, что достигается установкой образца по специальному шаблону.
Испытывают образцы при температуре, регламентированной техническими условиями, а в исследовательских целях
— в интервале температур от вязкого до полностью хрупкого излома.
В результате испытаний определяют значение вязкой составляющей в изломах образцов для оценки хладостойкости стали и энергию разрушения для оценки сопротивления распространению разрушений.
Строят диаграммы динамического деформирования для последующего определения сопротивления зарождению и распространению разрушения и средней скорости трещины, что подробно рассмотрено в гл. 5.
Значение вязкой составляющей в процентах от площади сечения образца определяют различными методами. При этом участки разрушившегося сечения под надрезом и под местом удара молота в расчет не принимают. Температура перехода
17
металла в хрупкое состояние Т80, определяемая при 80 % волокна в изломе образцов ДWТТ, наиболее удовлетворительно соответствует результатам пневматических испытаний труб диаметром 3420 мм.
Введение в технические условия на поставку труб требований по количеству волокна в изломах образцов DWТТ при температуре эксплуатации позволило предупредить хрупкие разрушения магистральных газопроводов. Возможность определения полной энергии разрушения полнотолщинных образцов DWТТ позволяет включить в оценку сопротивления металла вязкому разрушению конструктивный параметр труб — толщину стенки и тем самым повысить объективность оценки сопротивления стали разрушению в газопроводах.
Впоследние годы испытания полнотолщинных образцов
срегистрацией поглощенной энергии получили признание в ряде стран. Этому способствовала более полная по сравнению
собразцами Шарпи сходимость результатов испытаний образцов DWТТ с результатами пневматических испытаний труб при определении характеристик сопротивления вязкому разрушению.
Различные результаты, получаемые при испытании полнотолщинных образцов DWТТ и образцов Шарпи, показаны на рис.3. Температура, при которой происходит резкое падение сопротивления разрушению (кривая 2, образцы DWTT), сдвигается в положительную сторону, а температурный интервал перехода от верхнего плато к нижнему значительно сокраща-
ется (|∆T2|<|∆T1|). Из этого следует, что испытание на ударный изгиб полнотолщинных образцов DWTT является более жестким, чем испытание малогабаритных стандартных ударных образцов с надрезом по Шарпи. Это повышает надежность оценки сопротивления разрушению на полнотолщинных образцах.
18
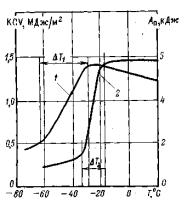
Рис. 3. Зависимость ударной вязкости по Шарпи (1)
ипоглощенной энергии удара Лп образцов ШУТТ (2) от температуры испытаний
Форма и тип надреза (резаный, прессованный или усталостная трещина) для сталей с поглощенной энергией удара Ап менее 3,6 кДж не оказывают существенного влияния на значение энергии разрушения. К этой группе сталей относятся горячекатаные и нормализованные. Для сталей контролируемой прокатки и термообработанных с Ап>3,6 кДж прессованный надрез и усталостная трещина снижают энергию разрушения образцов тем значительнее, чем выше сопротивление стали зарождению трещины. В технических условиях на поставку газопроводных труб для образцов DWTT принят резаный надрез.
Получаемые при испытании образцов DWТТ зависимости поглощенной энергии удара от температуры позволяют сравнивать различные стали не только по хладостойкости, но и по сопротивлению распространению вязких разрушений и температурному запасу вязкости (рис. 4). Верхнее плато кривых 1 и 2 соответствует полностью вязким разрушениям (100% волокна в изломах образцов). В интервале температур перехода из вязкого состояния в хрупкое происходит резкое снижение поглощенной энергии. На рис. 4 видно, что при температуре —15 о
19