
2858.Оборудование литейных цехов учебное пособие
..pdfдом. Зажимы для отливок применяют механические, эксцентриковые, а также пневматические. Диаметр рабочего стола 1,8–2,0 м. Число зажимов для отливок 6–12. Диаметр шлифовального круга 500 мм. Окружная скорость кругов 35 м/с. Скорость подачи столов 1–7,5 м/мин. Производительность 150–180 отливок в час.
20.3. Очистка металлическими кругами
Развитие процесса абразивной обработки отливок привело к созданию высокопроизводительных армированных шлифовальных кругов, имеющих скорости резания до 100 м/сек. При этом в зоне контакта шлифовального круга с отливкой происходит интенсивное тепловыделение, которое приводит к размягчению тонкого слоя металла. Наличие размягченного слоя металла способствует увеличению производительности процесса. Изучение процесса высокоскоростной абразивной обработки показало, что с повышением скорости обработки различия в характеристиках шлифовальных кругов мало влияют на параметры процесса. Этот вывод явился основанием к созданию процесса шлифования металлическим быстровращающимся кругом.
Успешные опыты привели к созданию большого количества пил трения, используемых в металлургической промышленности для разрезки слитков и проката. Большая производительность, простота и надежная конструкция пил трения обеспечили им применение в течение последних десятилетий.
Существенным недостатком пил трения является сильный шум высокого тона («вой»), который вызывается вибрацией тонкого вращающегося диска.
Обработка отливок трением впервые была осуществлена в 1950–1958 гг. на Волгоградском тракторном заводе, где создан полуавтомат для зачистки отливок звена гусеницы (трака) стальным быстровращающимся кругом.
Главными преимуществами процесса очистки трением (по сравнению с абразивной обработкой) является отсутствие выде-
381
лений пыли, содержащей частицы кварца, и высокая стойкость стального диска.
В соответствии с гипотезой, предложенной П.М. Келлерманом [24], в зоне контакта быстровращающегося диска с отливкой выделяется большое количество тепла. Температура на контактной поверхности отливки повышается до температуры плавления металла. Каждая точка поверхности диска, выходя из зоны контакта, увлекает за собой частицы расплавленного металла. При этом более крупные из них под действие центробежной силы отрываются от поверхности диска, а мелкие остаются. Быстрое вращение дисков создает мощный вихревой поток воздуха, охлаждающий диск. Застывшие на поверхности диска частицы металла напоминают абразивные зерна. Как и абразивные зерна, они врезаются в размягченный слой разогретого металла в зоне контакта и удаляют его. В процессе резания прилипшие частицы металла изнашиваются, и к моменту выхода из зоны контакта большинство зерен превращается в тонкие лепестки, которые под действием воздушного потока быстро остывают и теряют способность держаться на поверхности диска.
Налипание частиц металла происходит непрерывно, с каждым оборотом стального диска. Выполнив работу, прилипшая частица отлетает от поверхности, а на ее место налипает следующая. Непрерывное восстановление на рабочей поверхности вращающегося диска частиц металла, выполняющих функцию рабочего инструмента при зачистке, позволило создать инструмент, стойкость которогов 100 развыше, чем у абразивного круга.
Высокая стойкость инструмента позволяет создавать оборудование для зачистки фигурных поверхностей отливок, что практически невозможно при абразивном круге. Резкое снижение уровня шума высокого тона (в сравнении с пилами трения) достигается за счет увеличения толщины диска.
На базе этого метода на ряде заводов созданы полуавтоматические станки для обработки целого ряда деталей при серийном и массовом производстве.
382
Внедрение полуавтоматических станков повысило производительность труда в 3–5 раз, резко улучшило санитарногигиенические условия и безопасность труда по сравнению с очисткой абразивными кругами.
Вопросы для повторения
1.Сущность процесса зачистки отливок абразивными кру-
гами.
2.Конструкции станков для зачистки отливок абразивными кругами.
3.Преимущества и недостатки зачистки абразивными кру-
гами.
4.Сущность процесса зачистки отливок металлическими кругами.
21. ЭЛЕКТРОТЕРМОМЕХАНИЧЕСКАЯ, ИЛИ ЭЛЕКТРОКОНТАКТНАЯ ОЧИСТКА
Электротермомеханическая очистка, или, точнее, зачистка неровностей отливок, производится быстровращающимися стальными дисками при пропускании электрического тока между диском и отливкой.
Электроконтактный способ обработки металлов был открыт в 1925 г., но в промышленности начал использоваться только с 1951 г. Этот способ обработки основан на использовании тепла, выделяющегося при прохождении электрического тока через участки цепи с повышенным сопротивлением, которое возникает в месте контакта диска-инструмента и обрабатываемой отливки.
Принцип действия установки для электроконтактной зачистки (рис. 21.1) состоит в следующем. Диск 1 вращается электродвигателем 3 через клиноременную передачу 2. Обрабаты-
383

ваемая деталь 4 закрепляется на подвижном столе 5. Переменный ток в зону контакта подается через трансформатор 6.
Рис. 21.1. Схема электроконтактной установки
При работе станка происходит соприкосновение двух электродов (инструмента и изделия) под небольшим давлением, что приводит к образованию в месте контакта повышенного сопротивления. Проходящий через место контакта электрический ток разогревает, размягчает и плавит металл, облегчая удаление его с изделия. Для предотвращения плавления инструмента ему придают большую скорость вращенияи искусственно охлаждают.
Процесс съема металла определяется количеством тепла, выделяющегося в зоне контакта, которое зависит от числа контактных мостиков и величины тока в рабочем контуре. При малом числе контактных мостиков, что соответствует обработке литых деталей, сила тока будет достаточна для оплавления этих мостиков. Кроме того, дуги короткого замыкания, образующиеся при разрыве контактных мостиков, также способствуют оплавлению поверхности изделия.
Основными показателями, характеризующими процесс электроконтактной обработки, являются:
1) производительность – скорость съема металла с обрабатываемой детали в единицу времени (например, в кг/ч);
384
2)качество обработанной поверхности (чистота поверхности, глубина слоя с измененной структурой и т.д.);
3)обрабатываемость металла электроконтактным способом, оцениваемаяудельным расходомэлектроэнергии вкВт·ч/кг.
Электроконтактная обработка, являясь разновидностью электроэрозионной обработки, характеризуется отсутствием генератора импульсов, так как импульсивность тока создается за счет относительного перемещения поверхности электродов. Другой особенностью этого способа является проведение процесса в воздушной атмосфере в отличие от других видов эрозионной обработки, проводимых в электролите.
Возможность проведения электроконтактной обработки при различных значениях параметров процесса обусловливает наличие ряда разновидностей обработки [15].
При низком напряжении (до 12 В) съем металла происходит за счет нагрева контактных перемычек. Дуговые разряды
взоне обработки отсутствуют или занимают в тепловом балансе межэлектродного промежутка незначительное место. При среднем напряжении (до 22 В) дуговые разряды в тепловом балансе зоны обработки занимают значительное место. При повышенном напряжении (свыше 22 В) дуговые разряды, если отсутствует давление в зоне контакта, играют главную роль при съеме металла.
Точные границы между режимами установить трудно, так как они зависят от ряда причин: теплофизических свойств металла изделия и инструмента, теплообмена межэлектродного промежутка с окружающей средой, наличия давления в зоне контакта, которое, в свою очередь, может определяться технологическими условиями обработки изделия.
Особенностью электрофрикционного способа обработки являются наличие большого давления в зоне контакта и, как следствие, дополнительное тепловыделение в зоне контакта, вызванное трением инструмента по обрабатываемой детали.
385
Удаление металла при электроконтактной обработке обусловлено главным образом тепловыми процессами. Выделение тепла в зоне контакта обусловлено как тепловым действием тока, так и трением.
Как следует из принципиальной схемы электроконтактной установки (см. рис. 21.1), станки для очистки имеют простую конструкцию. Перемещение-подача в зависимости от геометрической и технологической особенностей отливки может иметь характер как вращения, так и прямолинейного перемещения.
Прототипом станка для электроконтактной зачистки отливок является отрезное металлорежущее оборудование, режущим инструментом которого является дисковая пила. В период 1955– 1960 гг. на Челябинском, Волгоградском и Харьковском тракторных заводах были внедрены станки для электроконтактной зачистки звеньев гусеницы (траков). Конструкции этих станков обеспечивают большое давление в зоне контакта инструментдеталь, что является основанием для отнесения этого процесса к категории электрофрикционной зачистки.
Инструмент – диск в работе установки подвергается действию тепла, электрических разрядов и окислительных процессов. Все это требует обеспечения не только конструктивной прочности, но и высокой износостойкости. При мягких режимах и низкой производительности стойкость стального диска (по данным Волгоградского тракторного завода) достигает 500 000 операций против стойкости абразивного круга – 2000 операций.
При форсированных режимах, обеспечивающих высокую производительность съема металла, износ инструмента недопустимо высок. Это явление вызвано тем, что тепло, возникающее в зоне контакта, распространяется не только на отливку, но и на инструмент.
386

22. ОЧИСТКА ОТЛИВОК В ГАЛТОВОЧНЫХ БАРАБАНАХ
Очистка отливок в галтовочных барабанах происходит за счет взаимного трения и соударения отливок между собой и наполнителем, а также со стенками барабана при его вращении. Одновременно с выбивкой стержней и очисткой отливок от формовочной смеси, окалины и пригара в галтовочных барабанах отбиваются литники, удаляются заусенцы и заливы по линии разъема, закатываются выступающие остатки литников.
Галтовочные барабаны
(рис. 22.1) |
применяются |
||
в большинстве |
случаев |
для |
|
очистки |
толстостенных |
от- |
|
ливок с |
толщиной стенки |
свыше 10 мм и весом до 40– 50 кг. Они широко распространены в литейных цехах с крупносерийным, массовым и особенно мелкосерийным и индивидуальным характером производства.
Одним из главных преимуществ галтовочных ба-
рабанов является простота конструкции, надежность в работе, возможность включения в поточную линию, компактность и достаточно высокий уровень механизации вспомогательных операций.
Очистка литья в галтовочных барабанах имеет следующие недостатки:
1)искажение геометрических размеров за счет скругления острых граней и углов на отливках;
2)неудовлетворительные санитарно-гигиенические условия работы операторов (шум, пыль);
387
3)затруднение механизации съема, установки и крепления крышки люка при загрузке и выгрузке отливок в барабанах периодического действия;
4)необходимость периодической очистки барабанов, что несовместимо с условиями поточно-массового непрерывного производства;
5)малая производительность и большой расход электроэнергии на очистку 1 т отливок по сравнению с дробеметными барабанами.
Для ускорения процесса очистки в барабан вместе с отливками загружаются звездочки размерами от 20 до 65 мм из белого чугуна. Звездочки рекомендуется загружать в барабан в количестве 30–35 % от веса отливок [1].
Загрузка и разгрузка барабанов на большинстве заводов механизирована. По данным многих заводов, примерная продолжительность очистки 1 т чугунного литья составляет 1–1,5 ч, стального литья – 2 ч. Обычно барабан круглого сечения загружается отливками на 70–80 %.
Весьма важным является выбор частоты вращения простого круглого барабана для очистки отливок. Для увеличения контактов
искоростей скольжений отливок одна по другой частоту вращения барабана желательно увеличить. Однако с увеличением частоты вращения возрастает центробежная сила, прижимающая отливки одна к другой или к стенкам барабана. При слишком быстром вращении центробежная сила может возрасти до такой величины, что разность между ней и массой отливки станет недостаточной для преодоления сопротивления взаимному скольжению отливок. При этом процесс очисткиотливок прекратится.
Из анализа режима хорошо работающих барабанов можно установить такое эмпирическое правило: центробежная сила отливки на внутренней поверхности барабана не должна превышать половины массы отливки для большинства барабанов с внутренним диаметром свыше 700 мм. Только для малых барабанов с внутренним диаметром менее 700 мм центробежная сила должна составлять около 0,6 массы отливки [5].
388

Исходя изэтого для барабанов с диаметром 2R ≥0,7 м имеем
m πn 2 R ≤ 0,5mg,
30
где m – масса отливки; n – частота вращения барабана, об/мин; g – ускорение силы тяжести, g = 9,81 м/с2.
Отсюда получаем формулу для оптимальной частоты вращения
n ≤ |
21,2 |
об/ мин. |
(22.1) |
|
R |
|
|
Точно так же для небольших барабанов с диаметром 2R < < 0,7 м имеем
m πn 2 R ≤ 0,6mg,
30
откуда
n ≤ |
23,1 |
об/ мин. |
(22.1а) |
|
R |
|
|
В формулах (22.1) и (22.1a) радиус барабана R дан в м. Конструкции барабанов как в России, так и за рубежом
весьма разнообразны. Наибольшее распространение получили барабаны круглого и квадратного сечения, опирающиеся на цапфы или опорные ролики.
По принципу работы галтовочные барабаны разделяются на барабаны периодического действия и барабаны непрерывного действия. Барабаны периодического действия применяются в мелкосерийном и индивидуальном производстве.
Галтовочный барабан периодического действия (рис. 22.2) обеспечивает высокое качество поверхности отливок. Очистка отливок в галтовочном барабане происходит вследствие взаимных соударений и трения отливок о стенки барабана и специально отливаемые звездочки из белого чугуна, которые загружаются в барабан для повышения интенсификации процесса.
389
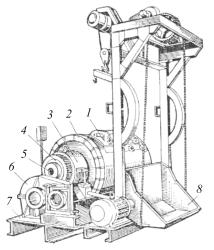
Одновременно с очисткой поверхности отливок в галтовочном барабане происходит выбивка стержней и отбивка литников.
Основные узлы галтовочного барабана: рама со стойками 7 и рабочая обечайка 2 барабана. Обечайка барабана подвешена на цапфах 4, которые входят в подшипники 3, установленные на стойках рамы.
Рис. 22.2. Очистной галтовочный барабан периодического действия
В обечайке барабана имеется загрузочный люк, закрываемый крышкой 1 с замками. Пылеотсос обеспечивается через патрубок 5, подсоединяемый к цапфе барабана и к цеховой вентиляции. Привод барабана осуществляется от электродвигателя через редуктор 6.
Для загрузки отливок барабан может быть оснащен скиповым подъемником 8. Управление барабаном и скиповым подъемником ведется с единого пульта.
При проектировании барабана в зависимости от заданных параметров определяют скорость вращения барабана, мощность
390