
2814.Управление отходами. Механобиологическая переработка твердых бытовы
.pdf
Рис. 2.5. Схемакомпостированияотходовот уходазазелеными насаждениями парков, газонов, садов(г. Зальцбург, Австрия): 1 – доставкабиогенных отходов; 2 – промежуточный бурт; 3 – колесныйпогрузчик; 4 – измельчитель; 5 – бурт, периодически перемещаемый; 6 – дозирующий ленточный транспортер; 7 – предварительныйгрохот; 8 – контейнердлякрупных кусковых отходов; 9 – грохот; 10 – контейнердлякрупныхотходов послегрохочения; 11 – воздушный классификатор; 12 – твердыеотходы(камни); 13 – циклонный сепаратор; 14 – пылеуловитель; 15 – контейнердляпыли; 16 – компост; 17 – склад компоста; 18 – транспортировка компоста; 19 – мешалка; 20 – упаковкав мешки; 21 – укладкана поддоны
Рис. 2.6. Схема современного компостного завода фирмы Kruger (Дания) мощностью 24000 т/год: 1 – весы; 2 – приемный бункер; 3 – дробилка; 4 – реагентное хозяйство; 5 – известь; 6 – электромагнитный сепаратор; 7 – компостный реактор; 8 – финишная сортировка; 9 – готовый компост; 10 – лабораторный контроль; 11 – помещение для персонала
111

Технологические схемы и оборудование компостных участков, несмотря на существенные различия по производительности, набору технологических установок, целевым конечным продуктам, могут быть представлены схематически в следующем виде.
Каждая партия отходов, направляемых на компостный участок, проходит входной контроль, где ведется проверка сопроводительной документации, подтверждающей необходимое качество отходов и их пригодность для компостирования. Кроме проверки документации проводится визуальный контроль, а при необходимости и отбор проб для лабораторного анализа. После входного контроля по указанию оператора отходы направляются на компостный участок, где в зависимости от их качества и свойств с ними проводятся при необходимости операции по их предварительной подготовке (отбор мешающих и балластных фракций, корректировка влажности, смешение с другими партиями отходов для корректировки качества и т.д.).
После этого отходы поступают в установки по биомеханической переработке. На компостных участках в качестве таких установок обычно используются гомогенизационные биостабилизаторы – биобарабаны, биотуннели, бассейны выдержки. После завершения нахождения отходов в этих установках, прошедших начальный этап биомеханической переработки и получивших свойства несозревшего компостного материала, они направляются в бурты для созревания, а из них после необходимого по технологии и в зависимости от требований к качеству целевых продуктов проведения процедур по ворошению, увлажнению, переформированию буртов, фракционированию по крупности, удалению нежелательных примесей, дополнительного измельчения (при необходимости) формируются товарные партии готового продукта. С учетом выраженного сезонного спроса на компост он временно хранится на складах готового продукта и затем отправляется к потребителям.
Применяемые на компостных участках технологии и технические устройства – традиционные. В ряде стран предпочтение отдается биотуннелям, в других – биобарабанам и бассейнам выдержки.
В связи с тем, что наряду с современными методами компостирования на МПБО, компостных заводах, компостных участках для компостирования при полигонах захоронения ТБО, компостирования с использованием биобарабанов, биотуннелей, различных биореакторов и компостерных установок до последнего времени остается востребованным метод буртового компостирования, целесообразно более подробно осветить такие вопросы, как устройство буртов, их типы, конфигурацию и размеры, способы ворошения (перелопачивания) материалов в буртах, их перемещение, увлажнение и дренирование, а также их защиту от неблагоприятных метеофакторов.
112
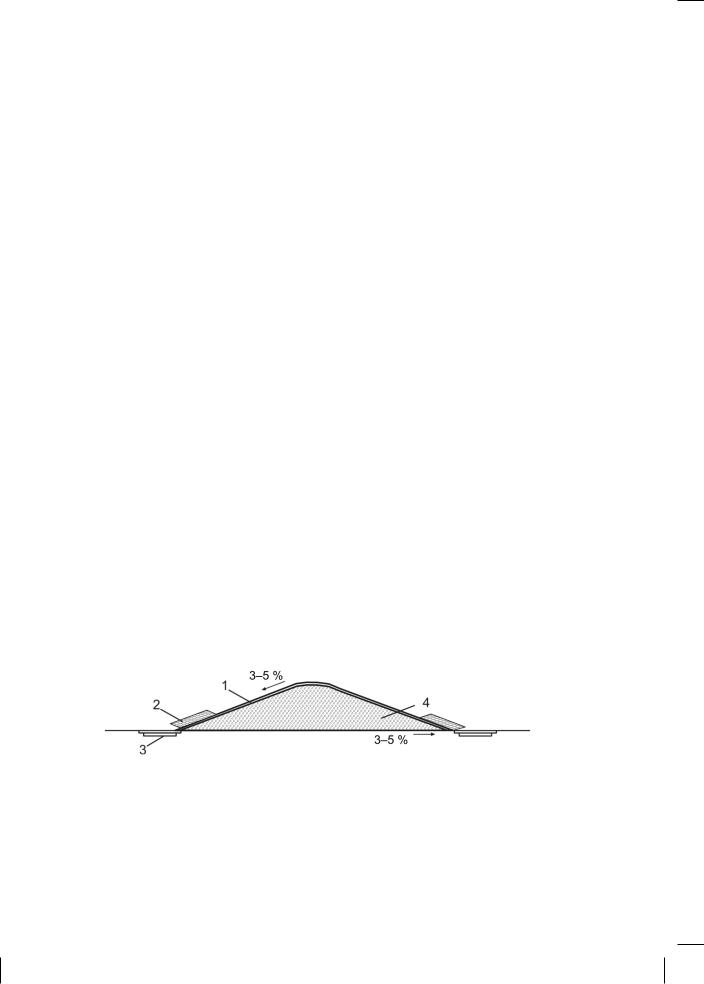
Эти вопросы также актуальны и для других методов компостирования, где в качестве дополнительных технологических процессов используется метод буртования для выдержки компоста свежего выхода до этапа его созревания, а также временного хранения готового компоста в периоды спада его сезонного спроса.
Основными типами буртов, принятыми в практике компостирования органических отходов, являются: плоские; конические; триангулярные или трапециодальные.
Плоские бурты обычно имеют небольшую высоту (обычно <1,0 м) при относительно большой ширине и длине, которые лимитируются конфигурацией земельного участка и необходимостью создания проходов для обслуживающего персонала и проезда техники. Предельная ширина плоских буртов зависит от способа их формирования (вручную или с использованием техники, имеющей определенную ширину захвата и выноса шнека, транспортера или другого устройства для перемещения субстрата в бурт), ворошения (перелопачивания) – вручную с помощью лопат, вил или специальной техники (фронтальных машин для перемещения или переформирования буртов).
Конические бурты (кучи) формируются вручную или с помощью простейших механизмов, легко перемещаются и поддаются ворошению с помощью лопат или вил, имеют большую поверхность, что способствует их быстрому охлаждению при перегревах.
Триангулярные или трапециодальные бурты легко поддаются естественной аэрации. Их ворошение (перелопачивание) и переформирование с перемещением легко осуществляются в зависимости от размеров вручную с использованием лопат или вил, с помощью фронтальных или метательных машин для перемещения компостируемого субстрата. Высота таких буртов обычно составляет 1,2–2,5 м, ширина – от 2,0 до 5,0 м.
На рис. 2.7 показано схематично устройство типичного бурта с перекрытием сверху геотекстилем, пригруженным для снижения его парусности старыми автомобильными покрышками.
Рис. 2.7. Схематический разрез бурта для компостирования органических отходов: 1 – перекрытие бурта из геотекстиля; 2 – дренаж для сбора и отвода избыточной воды (отжимной и фильтрата); 3 – накопительные емкости для избыточной воды; 4 – тело бурта
113

Боковые борта выполнены с уклонами к основанию для стока ливневой воды. Основание выполнено с уклоном в 3–5 % от центра к бокам с дренажом для сбора и отвода избыточной воды (отжимной и фильтрата) в небольшие емкости (танки), расположенные симметрично по бокам бурта.
Для улучшения аэрации, более равномерного распределения влажности субстрата в буртах и исключения застойных зон периодически проводится их ворошение или переформирование вручную, или с помощью фронтальной техники, как показано на рис. 2.8.
Рис. 2.8. Схематический разрез бурта для компостирования органических отходов с системами для его переформирования (ворошения), сбора и отвода дренажных вод: а – бурт с дренажной системой в основании; б – бурт с водопроницаемым основанием суклоном3–5 % длясбораиотведения дренажныхвод: 1 – телобурта; 2 – дренажный слой в основании бурта; 3 – накопительные емкости
для дренажной воды; 4 – емкости (ровики-траншеи) для сбора и отвода дренажной воды
Для обеспечения дренирования избыточной воды в основании бурта может устраиваться дренажный слой со сбором воды в накопительной емкости (см. рис. 2.8, а) или без дренажа, но с уклонами основания в 3–5 %, выполненного из водонепроницаемого материала со сбором дренажной воды в емкости (или ровики-траншеи) (см. рис. 2.8, б).
На плоских широких буртах с высотой >1 м происходят загрязненная естественная аэрация и отвод дренажных вод. С этой целью для плоских буртов с высотой от 2,0 до 3,5 м и шириной >20 м применяются принудительная аэрация, как схематически показано на рис. 2.9, и устройство дренажа для отвода избыточной воды.
На рис. 2.9, а показана система принудительной аэрации плоского широкого бурта небольшой высоты с устройством дренажа для отвода избыточной воды.
114

Рис. 2.9. Схематический разрезбуртадля компостирования органическихотходов
ссистемамипринудительнойи естественной аэрации, сбора иотводадренажных вод:
а– системапринудительнойаэрации сотсасываниемиочисткойвыбрасываемого воздуха идренажной системойдлясбораиотводаизбыточнойводы; б– система
принудительнойаэрациис нагнетанием воздухадляаэрации; в– системаестественной аэрацииплоскогобуртасдренажнойсистемойдлясбора иотвода избыточнойводы: 1 – воздухопроницаемое перекрытие бурта; 2 – системапринудительной аэрации
сотсасываниемвоздухаиз телабуртаиподачей его набиофильтрдля очистки; 3 – биофильтрадля очисткивыбрасываемого воздуха; 4 – дренажный слой
инакопительная емкостьдля сбораиотводадренажнойводы; 5 – система принудительнойаэрациис нагнетанием воздухав телобурта
Сооружение (устройство) буртов может осуществляться вручную или механизированным способом с использованием специальных машин и механизмов. Небольшие бурты устраиваются вручную с помощью лопат, вил, а компостируемый материал доставляется с помощью небольших тележек, тачек. Большие бурты формируются с помощью фронтальных погрузчиков, метательных машин, скреперов, бульдозеров.
Для увлажнения буртов применяются разбрызгиватели воды, подобные применяемым для полива и орошения. Избыточная влага отводится дренажными системами.
Перед формированием бурта укладываемый материал целесообразно для лучшего его перемешивания и гомогенизации пропустить через барабан-сме- ситель (миксер).
Для избежания образования в теле бурта застойных зон, неравномерной влажности субстрата, слеживаемости, анаэробных зон, ухудшения аэрации, самоуплотнения, неоднородности материала по физико-химическим свойствам и срокам нахождения в бурте («старый» и «молодой» материал), исключения неравномерности температуры (разницы в температуре между внутренними и внешними слоями субстрата в бурте), обеспечения равномерности те-
115

плопотерь и исключения перегрева (переохлаждения) отдельных слоев субстрата необходимо через определенные промежутки времени проводить ворошение (перелопачивание) бурта, а лучше – переформирование путем перемещения материала вдоль или поперек его оси.
Компостируемый субстрат в зависимости от времени закладки в бурты (ве- сенне-летний и осенне-зимний периоды), климатических и погодных условий, соотношения C/N и других ограничений, микробиальной обсемененности, физи- ко-химических свойств, отсутствия (наличия) химических веществ, влияющих на скорость биодеструкции и других обстоятельств, обычно превращается в компост требуемой степени зрелости через 8–20 недель. В период созревания субстрата бурты целесообразно защищать от излишних атмосферных осадков.
На финишных стадиях компост подвергается грохочению с целью выделения крупных непрокомпостированных включений и рассева по фракциям (по крупности) в зависимости от требований к материалу при определенном направлении использования.
При хранении готового компоста в буртах необходима его защита от атмосферных осадков, пересыхания.
Для правильного ведения процесса компостирования органических отходов методом открытого буртования с естественной аэрацией имеется ряд общепринятых методических рекомендаций.
Этим методом целесообразно перерабатывать отходы, легко поддающиеся биоконверсии.
Желательно вести сортировку и претритмент методами, при которых обеспечивается структура субстрата, не препятствующая необходимой воздухо- и водопроницаемости, не слеживающаяся.
Геометрия буртов рекомендуется (из практических соображений по их формированию, ворошению) высотой ≤ 2 м и шириной ≤ 3,5 м при условии отсутствия или одноразового перемещения.
Орошение (если оно необходимо) целесообразно совмещать с ворошением. Для обеспечения равномерного прогрева всех слоев бурта необходимо, как минимум, из санитарных соображений (для обеспечения надежности гибели патогенной микрофлоры и яиц гельминтов, а также семян сорных растений) од-
но переформирование бурта.
Желательно обеспечить необходимое время созревания компоста, которое в зависимости от сезона закладки материала в бурты, погодных и климатических условий может быть различным (больше или равно 12 мес.).
При использовании периодического перемещения и переформирования буртов при их размещении на открытых площадках при естественной аэрации рекомендуемая геометрия буртов следующая: высота ≤ 3 м, ширина ≤ 5,5 м.
116

Первое переформирование (перемещение) буртов желательно проводить через 7–14 дней (для обеспечения дезодорации и санитарных требований) после 2–3 суток достижения температуры >65 °С.
Периодическое переформирование проводится в течение всей активной фазы биодекомпозиции субстрата.
Компостирование длится обычно в пределах несколько больше 6 месяцев плюс время на созревание компоста.
Возможные эмиссии загрязняющих веществ сводятся к появлению неприятных запахов, образованию зягрязненного фильтрата (отжимной воды), появлению пыли, содержащей частицы перерабатываемого субстрата, споры грибов, бактерии (при пересыхании субстрата).
В случаях, когда не обеспечивается достижение температуры компостируемого субстрата выше 65 °С в течение не менее 2–3 суток, возможно выживание патогенных микроорганизмов, яиц гельминтов и семян сорных растений.
2.7. Современные высокомеханизированные технологии компостирования органических отходов
На современных предприятиях по компостированию отходов в качестве основных элементов биостабилизации органической фракции отходов применяются гомогенизационные биобарабаны, различные системы открытых и закрытых устройств, реализующих процессы биоконверсии органических веществ в условиях принудительной аэрации, периодического перемещения компостируемого субстрата и управляемого температурно-влажностного режима.
Все разнообразие применяемых высокомеханизированных систем можно свести к следующим типам: по организации процесса компостирования – открытые и закрытые; по типу принудительной аэрации – путем создания напора или разрежения; по характеру перемещения компостируемого субстрата – без перемещения, периодического быстрого или медленного перемещения.
Внастоящее время наряду с традиционными биобарабанами используются различные типы и варианты этих систем – бассейны выдержки, биотуннели, биореакторы различных модификаций.
ВРоссии и странах СНГ традиционно для компостирования используются биобарабаны, в зарубежных странах наряду с биобарабанами наиболее часто используются биотуннели и в меньшей степени бассейны выдержки.
Впоследние десятилетия более частым стало использование биореакторов различных типов (вертикальных, горизонтальных, силосных) с принудительной аэрацией и механическим перемещением компостируемого субстрата.
117

В условиях высокомеханизированного компостирования вместо открытого буртового метода, в том числе с применением систем принудительной аэрации, более эффективно с точки зрения экономии площадей занимаемых участков организация технологического процесса и применение систем компостирования, сочетающих в себе преимущества открытого буртового метода и механизированного перемещения субстрата в процессе компостирования в закрытых (полностью или частично) помещениях и установках.
При этом облегчается ведение технологического процесса, где возможны совмещение процедур ворошения и перемещения субстрата с корректировкой его влажности, температуры, насыщения кислородом и предотвращение образования застойных анаэробных и переувлажненных зон, пересушивания субстрата в процессе активной фазы его биоконверсии. Более удобно и технологично ведение контроля за основными технологическими параметрами процесса с их оперативной корректировкой онлайн (при необходимости).
Активная принудительная аэрация способствует более быстрому протеканию фазы биоконверсии субстрата, сокращению сроков компостирования и созревания компоста.
При таких высокомеханизированных технологиях появляется возможность необходимой очистки и дезодорации удаляемого воздуха, выноса с ним из биоконверсируемого субстрата излишней воды, снижения эмиссии загрязняющих веществ в атмосферный воздух. Важным преимуществом является возможность регулирования образования сточных вод, которые можно возвращать в технологические процессы для увлажнения (при необходимости) перерабатываемого субстрата, орошения биофильтров, применяемых для очистки отходящего загрязненного воздуха, и не использовать при этом свежую воду и не сбрасывать сточную воду.
Эмиссии загрязняющих и дурно пахнущих веществ в рабочую зону и атмосферный воздух существенно снижаются из-за эффективного удаления загрязненного воздуха из установок и помещений путем его отсасывания (для обеспечения требующейся принудительной аэрации). Стоки воды практически отсутствуют из-за выноса большого объема воды в виде паров в составе удаляемого воздуха. Пыль, содержащая органические вещества, в том числе аллергены, а также микробиальную взвесь и споры грибов, удаляется вместе с загрязненным воздухом на очистку и не загрязняет воздух рабочей зоны и атмосферный воздух.
Санитарно-эпидемиологические требования по обеспечению гибели патогенной микрофлоры и яиц гельминтов также удовлетворяются в результате обеспечения в течение не менее 2–3 дней температуры перерабатываемого субстрата не менее 65 °С.
118

2.7.1. Компостирование органических отходов в биобарабанах
Биобарабаны выполняют несколько функций: гомогенизации поступающего материала путем его перемешивания, механического истирания за счет вращения барабана; сушки исходного материала за счет интенсивной принудительной вентиляции подогретым воздухом, подаваемым в биобарабан под напором, и отсасыванием из него в концевой части; биостабилизации за счет действия микроорганизмов. В отдельных случаях в систему биобарабана включают микробиологические ферментеры для обогащения подаваемого материала микрофлорой, а также нако- пители-дозаторы дляравномерной подачи биомассы вбарабан.
Пример такой установки по компостированию ТБО в гомогенизационном биостабилизаторе-биобарабане с применением микробиологического ферментера представлен на рис. 2.10.
Рис. 2.10. Установкадлякомпостирования ТБОвбиобарабане[30]: 1 – биобарабан; 2 – всасывающий вентилятор; 3 – напорный вентилятор; 4 – электрокалорифер; 5 – конвеерные весы; 6 – термодатчик;
7 – накопительсубстрата; 8 – микробиологический ферментер; 9 – насос; 10 – накопитель-дозаторбиомассы
Вращающиеся горизонтальные биобарабаны являются механизированной установкой при промышленной переработке ТБО и применяются как на МПБО, так и на компостных заводах. При использовании биобарабанов уменьшается трудоемкость процессов обезвреживания и утилизации отходов, сокращается территория, занятая установками для переработки отходов.
В России в качестве основной конструктивной части биобарабанов обычно используют элементы цементных печей.
Диаметр барабана 3–4 м, длина 20–36 м. Как правило, барабан имеет две скорости вращения: большая – для загрузки и разгрузки в течение 6–8 ч в сутки, меньшая – для ворошения, перемешивания и аэрации материала в течение остального времени.
119

На внутренней стороне стенок барабана привариваются рёбра высотой 5–8 см. Между этими рёбрами плотно набивается компостируемый материал, образуя своеобразную футеровку, которая защищает стенки барабана от истирания и служит теплоизолятором.
Внутрь барабана по специальным воздуховодам подаётся воздух для аэрации компостируемого материала. Распределительное золотниковое устройство, расположенное в одном из торцов барабана, обеспечивает подачу воздуха в воздуховоды, расположенные под слоем материала. Материал в процессе переработки частично истирается (измельчается).
Для сокращения длины подающих воздуховодов, уменьшения потерь воздуха применяют установку индивидуальных воздухоподающих агрегатов на поверхности барабанов, которые снабжаются электроэнергией при помощи скользящих контактов.
Всего за время переработки одной порции отходов для их истирания барабан должен совершать не менее 1000–1500 оборотов.
Впроцессе переработки в барабане материал уплотняется, его объёмный вес доходит до 0,6–0,7 т/м3 (объёмный вес поступающих в биобарабан отходов – 0,20–0,25 т/м3). Степень заполнения барабана 60–70 % от объёма.
Технологическая схема переработки отходов компостированием по методу Дано следующая. Отходы загружаются в приемный бункер, который оборудован горизонтальным пластинчатым питателем. Во избежание зависания мусора стены бункера строго вертикальны. Транспортёр с протектором подаёт мусор с пластинчатого питателя во вращающийся барабан. Протектор позволяет увеличить угол подъёма транспортёра с 20 до 30°, что обеспечивает более плотную компоновку агрегатов. Кроме того, транспортёр выполняет ещё одну функцию: его приводной барабан является магнитным сепаратором, извлекающим из отходов черный металл. Металл перед пакетированием на прессе очищается от налипшего мусора, вес которого в 1,5 раза превышает вес металла. Загрузка барабана осуществляется в течение 3–3,5 ч, выгрузка – за 5–6 ч. Замедленная выгрузка обеспечивает более надёжную работу последующей технологической цепи. Средний срок переработки и обезвреживания отходов в барабане – 3 суток.
Врезультате компостирования в барабане за счёт разложения органического вещества и частично сушки продукт теряет 41–12 % веса (в расчёте на исходный мусор). Из барабана обезвреженная и раздробленная за счёт вращения масса подаётся транспортёром в плоский виброгрохот. Очищенную от стекла массу (компост) при влажности 50 % отвозят к месту штабелирования, где она дозревает
втечение 2–3 месяцев [31].
Ускоренное биотермическое обезвреживание отходов в барабане можно проводить по методу Прата. Отходы обезвреживаются без предварительного
120