
2790.Современные методы высокоэффективной абразивной обработки труднообр
..pdf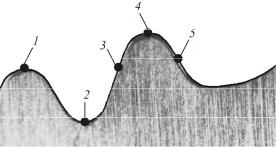
Для измерения величины радиусов скругления применен метод заливки и образования слепков радиусной поверхности. Полученный отпечаток по радиусу на слепке (пластинке) замеряли на микроскопе (контрольном проекторе ×100), применяемом в цехах для замера профиля «елочного» замка лопаток. Измерение профиля «елочного» паза проводили по пяти точкам (рис. 125) по вершинам, по впадинам и по боковым поверхностям.
Рис. 125. Профиль «елочного» паза (замеры радиусов скругления по пяти точкам): 1, 4 – вершина; 2 – впадина; 3, 5 – боковые поверхности
Методика экспериментальной работы в лабораторных условиях предусматривала разбиение всех пазов диска на 7 секторов и проведение обработки диска по 7 вариантам.
Первый вариант (сектор 3) – обработка острых кромок мягкой щеткой Ø150 (зерно 320 меш (№ 5), толщина нити 0,5 мм). Результат – радиус по вершинам «елочного» профиля 0,1–0,12 мм, по впадинам 0,07–0,12 мм, по боковому профилю 0,05–0,15 мм. Количество двойных ходов – 3 с реверсом щетки на обратном ходу.
Второй вариант (сектор 4) – обработка острых кромок более жесткой щеткой (зерно 180 меш (№ 8), толщина нити 1,0 мм). Результат – радиус по вершинам 0,07–0,12 мм, по впадинам 0,09– 0,22 мм, по боковому профилю 0,06–0,15 мм. Количество двойных ходов – 3 с реверсом щетки.
Третий вариант (сектор 1) – обработка острых кромок самой жесткой щеткой Ø200 мм (зерно 120 меш (№ 10), толщина нити
281
1,0 мм). Скорость увеличили в 1,5 раза. Количество двойных ходов 7 с реверсом вращения щетки. Результат – радиус по вершинам 0,25– 0,5 мм, по впадинам 0,12 мм, по боковому профилю 0,15–0,2 мм. В этом случае из-за большой скорости на детали появилось налипание – нагрелись и оплавились концы щетки.
Четвертый вариант (сектор 2) обработку произвели жесткой щеткой, но меньшего диаметра (зерно 120 меш, толщина нити 1,0 мм, Ø150 мм). Для получения большей величины радиуса количество двойных ходов щетки увеличили до 10. Результат – радиус по вершинам 0,18–0,22 мм, по впадинам 0,12–0,28 мм, по боковым про-
филям 0,09–0,25 мм.
В результате предварительных исследований установлено, что съем металла с кромок производится только в том случае, когда рабочая поверхность щетки расположена перпендикулярно к обрабатываемой поверхности детали.
Учитывая тот факт, что полимерно-абразивной щеткой обеспечить радиус 0,8–1,2 мм очень проблематично, то далее обработку диска провели с выполнением предварительной зачистки мест скругления абразивными шарошками.
Пятый вариант (сектор 5) – предварительная зачистка острых кромок абразивной шарошкой, установленной на высокоскоростную бормашинку мод. 200.
Шестой вариант (сектор 6) – предварительная зачистка острых кромок игольчатой твердосплавной борфрезой, установленной на высокоскоростную бормашинку мод. 200.
Седьмой вариант (сектор 7) – предварительная зачистка каплевидной твердосплавной борфрезой, установленной на высокоскоростную бормашинку мод. 200. После такой механической зачистки острых кромок абразивными и твердосплавными шарошками на кромках деталей образовалась фаска, которую затем скругляли полимерной щеткой (зерно 120 меш, толщина нити 1,0 мм). Результат – на всех поверхностях «елочного» профиля образовалась удовлетворительная фаска со скругленными краями радиусом до 0,8 мм на уровне серийной обработки.
282
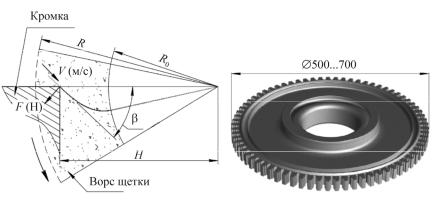
В результате проведенных предварительных исследований установлено:
1. Выполнение стабильной величины радиуса скругления 0,4±0,2 мм вполне достижимо при обеспечении следующих требований:
•линия скругляемой острой кромки детали должна быть перпендикулярна плоскости вращения щетки;
•шлифовальная головка со щеткой должна легко настраиваться по высоте детали и по направлению обработки острой кромки с поворотом вокруг своей оси (рис. 126);
•вращение щетки и детали должно реверсироваться;
•направление вращения щетки и детали – встречное;
•число двойных проходов не менее 3–5.
а |
б |
Рис. 126. Схема установки и резания острой кромки абразивной нитью (R – длина нити, R0 – радиус планшайбы) (а) и общий вид острых кромок «елочных» пазов в диске турбины (б)
2.Жесткость инструмента возрастает с уменьшением диаметра
щетки.
3.Для выполнения радиуса величиной 0,8–1,2 мм полимерной щеткой требуется предварительное образование фаски абразивной
283
или твердосплавной шарошкой. При этом на радиусе скругления кромки остается часть фаски с двумя радиусами.
4.С увеличением трудности в скруглении кромки следует использовать щетки повышенной жесткости, имеющие короткий ворс
ибольшую плотность. Применяя щетки с разной рабочей длиной волокон и их свойствами, можно изменять режущую способность щеток от очень нежной до весьма агрессивной.
5.При выборе щеток для снятия заусенцев и скругления кромок у деталей, как, впрочем, и для других операций, следует всегда иметь в виду, что эта операция может быть выполнена и другими методами. Поэтому при оценке целесообразности использования вращающихся щеток для той или иной операции в первую очередь должны приниматься во внимание производительность процесса и его экономическая эффективность.
6.Помимо плотности и жесткости ворса, большое значение здесь имеют давление щетки на обрабатываемую поверхность, расположение щетки по отношению к детали и время обработки.
7.Уменьшается шероховатость поверхности без удаления основного металла и изменения размеров детали. Съем металла производится только по кромке с образованием радиуса за короткое время.
8.Низкие капитальные затраты: щетки могут быть обычно использованы как окончательный режущий инструмент. При этом низкая стоимость обработки одной детали, относительно низкая цена щеток и высокая стойкость обеспечивают в результате очень низкую себестоимость обработки одной детали.
9.Не требуется правка щетки, так как волокна саморегулируются при обработке за счет их гибкости.
10.Экологически чистый процесс – вредное воздействие на окружающую среду отсутствует: шлам от процесса состоит из инертных абразивных частиц и металлических частиц; изношенные щетки не являются опасными отходами.
11.Недостаток щеток: ограниченное режущее действие (не удаляет крупные заусенцы с высокопрочных материалов) и невысокая температура в зоне обработки (с увеличением температуры происхо-
284
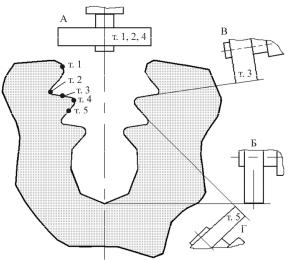
дит плавление полимерного материала и налипание его на поверхность детали, следовательно, необходима дополнительная обработка по снятию этого налипшего слоя материала).
Если требуется увеличить режущее действие ПАЩ, то необходимо: уменьшить окружную скорость щетки и увеличить глубину погружения (врезания) детали в щетку; уменьшить скорость детали; использовать прямоугольные волокна; увеличить диаметр волокна
изернистость.
Входе анализа полученных результатов было установлено, что полимерно-абразивная щетка эффективно работает только своей периферийной поверхностью. Следовательно, обработку нужно вести так, чтобы щетка располагалась по нормали к обрабатываемой поверхности, т.е. к профилю паза. Для полной обработки всех поверхностей «елочного» профиля необходимо иметь не менее четырех абразивных головок, расположенных под различными углами. Возможные положения четырех щеток А, Б, В, Г относительно поверхностей (точки 1–5) «елочного» профиля паза изображены на рис. 127.
Рис. 127. Оптимальное положение щеток относительно поверхностей «елочного» профиля паза
285
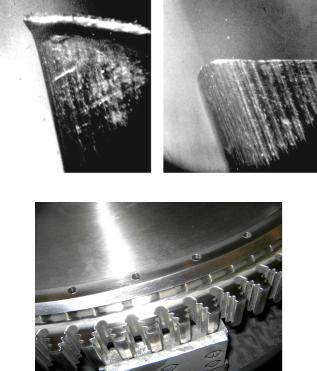
После обработки произвели замер полученных радиусов методом копирования их на медную пластинку. Радиус скругления острой кромки на диске турбины, полученный при окончательной обработке полимерно-абразивной щеткой (ПАЩ) 150 мм, зерно 120 меш, толщина нити 1,0 мм, показан на рис. 128, б. На рис. 128, а – острая кромка до обработки ПАЩ, а на рис. 128, в – поверхность после обработки ПАЩ. На рис. 129 показан общий характер равномерности скругления по всему «елочному» профилю паза диска турбины. В итоге величина радиуса составляет 0,15–0,4 мм (табл. 34).
аб
в
Рис. 128. Общий вид острой (а) и скругленной (б) кромок и «елочных» пазов диска турбины (в), обработанных ПАЩ
286
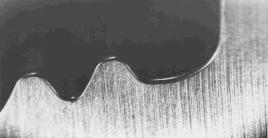
Рис. 129. Общий вид равномерного скругления кромок «елочного» паза
Таблица 34 Значения радиусов скругления при обработке поверхностей
Обрабатываемая |
Точка |
Радиус скругления, мм |
|
поверхность |
положения |
||
|
|||
Периферия зуба |
3, 5 |
0,25; 0,30; 0,15; 0,25; 0,22; 0,15; 0,20; 0,27 |
|
Впадина зуба |
2 |
0,20; 0,27; 0,22; 0,20; 0,27; 0,15; 0,15; 0,20; |
|
|
|
0,35; 0,15 |
|
Вершина зуба |
1, 4 |
0,15; 0,25; 0,27; 0,15; 0,40; 0,15; 0,25; 0,15; |
|
|
|
0,30; 0,17 |
По данным всех проведенных исследований построены диаграммы, по которым можно провести их сравнительный анализ. На рис. 130 изображены значения радиусов на поверхности паза, образованные щетками без предварительной обработки шарошками. На рисунке показана область допустимых значений радиусов скругления на диске. Необходимо, чтобы значения радиусов, полученных при обработке, попадали в интервал допустимых значений.
Анализируя диаграмму на рис. 130, можно сказать, что оптимальным вариантом для выполнения этой операции является третий вариант ( 150, зерно 120, 10 дв. проходов), так как радиусы находятся в пределах допуска на размер.
Предварительная обработка абразивными шарошками применяется на втором торце, у которого требуется обеспечить радиус скруг-
287
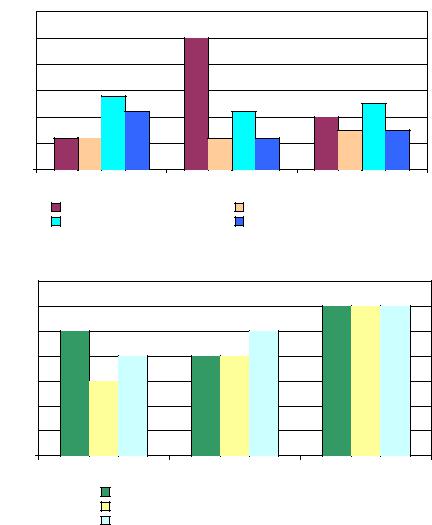
R, 0,6мм |
|
|
Область допустимых значений радиусов |
||
0,5 |
|
|
0,4 |
|
|
0,3 |
|
|
0,2 |
|
|
0,1 |
|
|
0 |
|
|
Радиус во впадине (т. 2) |
Радиус на вершине (т. 1, 4) Радиус на периферии (т. 3, 5) |
|
– Зерно 180, 200, 7 дв. проходов |
– Зерно 320, 150, 3 дв. проходов |
|
– Зерно 120, 150, 10 дв. проходов |
– Зерно 120, 150, 3 дв. проходов |
|
Рис. 130. Сравнение значений радиусов скругления на первом торце |
0,7 |
|
|
R, мм |
|
|
0,6 |
|
|
Область допустимых значений радиусов |
|
|
0,5 |
|
|
0,4 |
|
|
0,3 |
|
|
0,2 |
|
|
0,1 |
|
|
0 |
|
|
Радиус во впадине (т. 2) |
Радиус на вершине (т. 1, 4) |
Радиус на периферии (т. 3, 5) |
– Абр. шар. + |
ПАЩ зерно 120, 150, 3 дв. прохода |
|
– Игольч. фр. + ПАЩ зерно 120, 150, 3 дв. прохода |
||
– Капл. фр. + ПАЩ зерно 120, 150, 3 дв. прохода |
Рис. 131. Сравнение значений радиусов скругления на втором торце
ления R = (0,8±0,2) мм. Из представленных вариантов (рис. 131) для предварительной обработки можно применять как абразивную шарошку, так и каплевидную фрезу.
288

При увеличении числа проходов с 3 до 15 величина радиуса на кромке увеличивается с 0,22 до 0,33 мм во впадине, с 0,12 до 0,3 мм на вершине и с 0,15 до 0,31 мм между ними (рис. 132). Наибольшее значение и наименьшую разницу имеет радиус во впадине, затем следуют точки посреди кромки и наименьшее значение радиуса и наибольшую разницу при увеличении времени обработки имеют точки на вершине.
|
0,35 |
|
|
мм |
0,3 |
|
|
радиус, |
0,25 |
|
|
0,2 |
|
|
|
Полученный |
|
|
|
0,15 |
|
|
|
0,1 |
|
|
|
0,05 |
|
|
|
|
|
|
|
|
0 |
|
|
|
Во впадине |
На вершине |
Между ними |
|
15 проходов |
10 проходов |
3 прохода |
Рис. 132. Изменение радиусов скругления при изменении числа проходов |
Можно предположить, что во время обработки ворс щетки соскальзывал во впадину между зубчиками и интенсивность скругления радиуса была во впадине изначально выше из-за большей концентрации ворса. При увеличении радиуса скругления интенсивность съема металла во впадине снижалась быстрее, и увеличение числа проходов обработки меньше повлияло на конечную величину радиуса во впадине. Согласно этому предположению, возможна обработка как вершин, так и впадин зубчиков профиля с достижением близкого по значению радиуса скругления при условии правильного выбора числа проходов обработки.
Увеличение радиуса скругления обусловливает проявление нескольких эффектов. Во-первых, чем больше достигнутый радиус скругления, тем большее, в среднем, число зерен нити одновременно
289
взаимодействует с кромкой, тем меньше удельное давление каждого зерна. Во-вторых, чем больше радиус скругления, тем толще в поперечном разрезе кромка, тем меньше концентрация напряжений в материале. Поэтому при увеличении радиуса скругления происходит снижение интенсивности скругления из-за снижения режущей нагрузки и пластической деформации. Можно предположить, что определенным условиям обработки соответствует определенная величина радиуса скругления, при достижении этой величины дальнейшая обработка становится неэффективной из-за снижения интенсивности скругления. В этом случае можно гарантировать стабильное получение радиуса в допуске при правильном выборе режима обработки и параметров режущего инструмента.
По результатам предварительных исследований принято решение механизировать слесарную обработку, для чего необходимо спроектировать установку для удаления заусенцев и скругления острых кромок. Обработку производить щеткой 150 мм, зерно 120 меш, толщина нити 1,0 мм. Рабочую поверхность полимерно-абразивной щетки (ПАЩ) устанавливать по нормали к обрабатываемой поверхности в 4 плоскостях (по нормали к вершине, впадине и периферии зуба). Таким образом, необходимо спроектировать четыре шлифовальные головки для обработки этих поверхностей. Кинематическая схема такой автоматизированной агрегатной установки и направления перемещений головок приведены на рис. 133. При обработке диск и щетка должны вращаться с реверсом. Обработку необходимо проводить на встречном движении щетки и обрабатываемой поверхности диска. На рис. 133 обозначены: 1 – обрабатываемый диск; 2 – шлифовальные головки с ПАЩ, обрабатывающие вершины и впадины профиля (а), одну и другую сторону профиля (б, г), выкружку профиля (в).
Режимы обработки: скорость вращения щетки 21–22 м/c; натяг щетки 2–5 мм; скорость вращения диска 1 об/мин. Число оборотов диска в прямом и обратном направлениях – по 3. В итоге величина радиуса скругления R = 0,2…0,6 мм на одном торце и R = 0,4…0,8 мм на другом. Для этого разработаны и внедрены две конструкции
290