
- •ВВЕДЕНИЕ
- •СОСТАВ, СТРУКТУРА И ОСНОВНЫЕ СВОЙСТВА ДОРОЖНО-СТРОИТЕЛЬНЫХ МАТЕРИАЛОВ
- •ПРИРОДНЫЕ КАМЕННЫЕ МАТЕРИАЛЫ
- •ИСКУССТВЕННЫЕ МАТЕРИАЛЫ НА ОСНОВЕ МИНЕРАЛЬНЫХ ВЯЖУЩИХ И МЕЛКОЗЕРНИСТЫХ ЗАПОЛНИТЕЛЕЙ
- •БЕТОНЫ (ЦЕМЕНТОБЕТОНЫ)
- •СБОРНЫЕ БЕТОННЫЕ И ЖЕЛЕЗОБЕТОННЫЕ ИЗДЕЛИЯ
- •МАТЕРИАЛЫ И ИЗДЕЛИЯ ИЗ ПЛАСТМАСС
- •ОРГАНИЧЕСКИЕ ВЯЖУЩИЕ МАТЕРИАЛЫ
- •АСФАЛЬТОБЕТОН
Г л а в а 6
БЕТОНЫ (ЦЕМЕНТОБЕТОНЫ)
§ 6. 1. ОПРЕДЕЛЕНИЕ, ОСНОВНЫЕ ТЕХНИЧЕСКИЕ ТРЕБОВАНИЯ И КЛАССИФИКАЦИЯ
Бетоном называют строительный материал, полученный в результате пере мешивания, укладки, уплотнения и затвердения рационально рассчитанной смеси из щебня (или гравия), песка, цемента, воды и добавок. Смесь перечис ленных компонентов до затвердения называют бетонной смесью.
Бетон является основным строительным материалом, его производят бо лее 250 млн. м3 в год. Бетоны широко применяют в промышленных, граждан ских, гидротехнических и других сооружениях, из них выполняют монолитные (изготовляемые на месте строительства), сборные (изготовляемые инду стриальным способом на заводах, полигонах) элементы сооружений (фунда менты, колонны, перекрытия и др.), дорожные и аэродромные покрытия. Бе тон можно применять в машиностроении для изготовления массивных дета лей машин. Широкое применение бетона объясняется тем, что изделию из него можно придавать требуемые свойства, размеры, вид поверхности; бетонные работы можно выполнять в короткие сроки и в любое время года. Выбирая составляющие и применяя рациональную технологию производства бетонных смесей, управляя процессами структурообразования бетона, его физико механические свойства (плотность, прочность, долговечность и др.) можно регулировать в широких пределах и заданном направлении. Возможность полной механизации и автоматизации технологических процессов — сущест венная положительная характеристика бетона как прогрессивного строитель ного материала.
Вместе с тем бетон имеет и недостатки, главнейшим из которых является сравнительно малая прочность при изгибе (растяжении). Для устранения указанного недостатка в бетонные элементы в необходимых случаях вводят металлические стержни, сетки (арматуру). Вследствие длительного тверде ния бетонов конструкции из них нельзя вводить в эксплуатацию непосред ственно после укладки смеси; за твердеющим бетоном необходим тщательный уход.
Научно обоснованное решение вопросов технологии позволяет устра нять и такие отрицательные свойства бетона, как недостаточная устойчи вость в агресссивных средах, деформация при усадке и набухании, недоста точная жаростойкость и др.
Свойства бетонов определяются качеством составляющих и в значитель ной степени их структурой (строением). Правильно выбирая материалы, регу лируя структуру бетонов при одних и тех же составляющих, можно в широких пределах изменять их свойства. Структура бетона определяется крупностью, гранулометрическим составом, формой зерен и количественным соотношени ем его компонентов, их взаиморасположением и структурными связями, а так же наличием пор и дефектов. Структура неоднородна вследствие различных свойств компонентов (щебня, песка, цементного камня). Кроме того, в струк туре бетона имеется много дефектов (микротрещин, пор), возникающих в процессе изготовления бетонных изделий. Это является причиной возникно вения в бетоне внутренних напряжений с высокой степенью концентрации на границах раздела фаз, что существенно влияет на его механические свойства:
Для установления основных закономерностей влияния структуры на свойства бетонов целесообразно выделить следующие ее разновидности: макроструктуру, которая определяется крупной составляющей — щебнем (гравием) и строительным раствором (смесью песка, цемента и воды); мезоструктуру, которая формируется песком и затвердевшим цементом; микроструктуру— цементным камнем.
Макро- и мезоструктуры определяются количеством, крупностью, формой зерен щебня (гравия) и песка. В зависимости от соотношения составляющих можно выделить базальную, поровую и контактную макро- и мезоструктуры. В бетоне с базальной макроструктурой зерна щебня не образуют взаимных контактов, вследствие чего свойства бетона обусловливаются преимущест венно свойствами раствора.
При постепенном насыщении макроструктуры щебнем до состояния взаимного контактирования зерен создается поровая структура, при которой образуется компактный щебенистый каркас, способный воспринимать значи тельные внешние усилия. При дальнейшем увеличении содержания щебня возникает контактная макроструктура, характерная для крупнопористых бетонов.
Микроструктура цементного камня представляет неоднородную капил лярно-пористую коагуляционно-кристаллическую структуру, образующуюся в результате взаимодействия цемента с водой. Свойства микроструктуры зависят от минералогического состава цементного клинкера, добавок, тон кости помола цемента, количества воды затворения, условий твердения и пр. Рациональное сочетание указанных факторов позволяет регулировать фор мирование микроструктуры цементного камня,придавать ему определенные свойства.
Основной классификацией бетонов по структурным признакам является деление по объемной массе:
особо тяжелые с объемной массой более 2600 кг/м3 имеют сложную струк туру и изготовляются с применением заполнителей, защищающих от рентге новских и гамма-лучей (например, стальные опилки, барит и др.);
тяжелые с объемной массой 2100—2600 кг/м3, у которых структура плот ная, щебень из плотных и тяжелых горных пород или плотных металлурги ческих шлаков, песок кварцевый;
облегченные с объемной массой 1800—2000 кг/м3 могут иметь плотную структуру, но с применением щебня из пород пониженной плотности или круп нопористую с применением щебня из плотных пород;
легкие с объемной массой 1000—1800 кг/м3, чаще 1300—1500 кг/м3, обла дающие плотным или крупнозернистым строением, с применением пористого щебня и песка, шлаковой пемзы (термозита), керамзита, перлита;
особо легкие с объемной массой менее 1000 кг/м3, чаще 500—800 кг/м3, с пористой структурой без щебня и песка (ячеистый бетон) или с применением пористого песка или пористого щебня в сочетании с поризованным цементным камнем.
Наряду с делением бетонов по структурным признакам их классифициру ют по виду компонентов (различают цементный, известковый, гипсовый, ке рамзитовый, термозитовый бетон и т. д.). По назначению и условиям примене ния бетоны разделяют на: обычный — для изготовления фундамента, колонн, блоков зданий, пролётных строений мостов; дорожный — для устройства дорожных и аэродромных покрытий; гидротехнический — для возведения плотин, шлюзов и прочих гидротехнических сооружений; специальный — теплоизоляционный, жароупорный, кислотостойкий и др. Иногда делят бето ны и по технологическим признакам (вибрированный, трамбованный, вакуумбетон и др.).
Формирование оптимальной структуры бетона тесно связано с технологи ческими свойствами бетонной смеси, в первую очередь с.такими физическими константами, как сопротивление сдвигу и вязкости. Однако их определение, особенно в строительных лабораториях, чрезвычайно затруднено, так как бе тонная смесь является грубодисперсной. Ее свойства изменяются во времени и для нее характерна ярко выраженная тиксотропность — способность обра тимо восстанавливать первоначальную структуру и свойства после снятия механического воздействия, например вибрационного (рис. 6.1).
Вследствие тиксотропного разжижения облегчается перемешивание сме си, ее транспортирование в виброжелобах, следовательно, и формирование необходимой структуры бетона. Способы виброуплотнения смесей базируют ся на понижении прочности их структуры, уменьшении вязкости в процессе уплотнения смеси.
Явлением тиксотропии объясняется технико-экономический эффект вибри рования смеси, при котором значительно сокращается расход механической энергии на уплотнение’бетонных смесей.
Для сохранения подвижности необходимо поддерживать определенную интенсивность механических воздействий. При прекращении вибрирования структура смеси восстанавливается, вследствие чего теряется временно при обретенная подвижность.
Тиксотропия смесей обусловливает необходимость характеризовать их свойства при неразрушенной, разрушенной и частично разрушенной структу рах. Грубодисперсность смесей, изменяемость их свойств во времени затруд няют разработку простых методов, компактных и удобных приборов для опре деления показателей сопротивления сдвигу, вязкости. Поэтому разработаны другие показатели оценки технологических свойств бетонных смесей, а имен но подвижность и жесткость (удобоукладываемость) .
Подвижность и жесткость бетонной смеси характеризуют ее способность равномерно распределяться в армированном пространстве опалубки и уплот няться при заданной интенсивности механических воздействий. Показателем подвижности смеси является величина осадки (в см) изготовленного из нее стандартного конуса под действием силы тяжести. Жесткость характеризу ется временем (в с), необходимым для расплыва (пластической деформации)
конуса, изготовленного из бетонной сме си, до равномерного распределения ее в цилиндрическом сосуде прибора, установ ленного на стандартном вибростоле, кото рый колеблется с частотой 3000 кал/мин при амплитуде 0,5 мм.
Осадка конуса непосредственно свя зана с сопротивлением сдвигу, а удобо укладываемость — с вибровязкостью бе тонной смеси:
Рис 6.1. Схема тиксотропного разуп рочнения бетонной смеси:
вибрирование; ОВ — остановка вибратора
Т= 2S Ч- kT’
где т и г\ — соответственно сопротив ление сдвигу и вязкость бетонной смеси; Р — масса бетонного конуса; k — коэффи циент пропорциональности; S = f ( 0 K) — площадь основания расплывшегося кону са; Т — жесткость смеси, с.
Бетонная смесь |
Осадка |
Жест |
Бетонная смесь |
Осадка ко |
Жест |
|
конуса, см |
кость, |
нуса, см |
кость, с |
|||
|
Особо жесткая |
_ |
200 |
Малоподвижная |
1—5 |
15—25 |
Повышенно жест |
_ |
|
Умеренно подвиж |
|
|
кая |
100—200 |
ная |
6 - 9 |
5 - 1 5 |
|
Жесткая |
— |
60—100 |
Подвижная |
9—18 |
_ |
Умеренно жесткая |
|
25-60 |
Текучая (литая) |
18 |
— |
Наряду с этим предъявляют требования к однородности и пластичности бетонных смесей. Эти показатели обычно определяют визуально. Например, о пластичности судят по степени нарушения сплошности и расслоения дефор мированного стандартного конуса в процессе определения подвижности. Все смеси независимо от подвижности и удобоукладываемости должны быть достаточно пластичными и однородными. По показателям подвижности и жесткости бетонные смеси подразделяют на подвижные и жесткие (табл. 6.1).
Технологические свойства бетонной смеси зависят от состава и структуры. Важным фактором, определяющим технологические свойства смеси и форми рование структуры бетона, является содержанием воды. При малом количест ве вода, взаимодействуя с минеральными составляющими смеси, сорбируется на поверхности зерен, поэтому смесь является жесткой. Затем с увеличением количества воды образуются мениски в местах контактов зерен, она заполня ет капилляры смеси. В этом случае незначительное увеличение содержания воды способствует уменьшению трения между зернами заполнителя, сниже нию вязкости цементного теста, а в результате повышается подвижность бе тонной смеси. Если начинает отделяться вода (т. е. исчерпана водоудержи вающая способность), бетонная смесь расслаивается, нарушается однород ность ее структуры. В этом случае вода скапливается в верхнем слое, вслед ствие чего снижается прочность и долговечность бетона, или под зернами щебня, что ослабляет прочность сцепления с растворной частью.
В пластичных смесях для достижения заданной подвижности и жесткости требуется определенное количество воды (водопотребность смеси), которое зависит от качества исходных составляющих. Подвижность смеси зависит от вида цемента. Цементы с минимальной нормальной густотой цементного теста увеличивают подвижность бетонной смеси.
При постоянной подвижности увеличение количества цемента улучшает
пластичность бетонной смеси.
Мелкозернистые пески ухудшают подвижность смеси, что объясняется их повышенной удельной поверхностью, вследствие чего требуется больше це ментного теста для обволакивания их зерен. Поэтому при выборе песков для бетонов отдают предпочтение крупно- и среднезернистым чистым пескам, содержащим малое количество пылевато-глинистых примесей.
С уменьшением крупности щебня, увеличением в нем количества зерен лещадной формы, а также с повышением шероховатости их поверхности снижается подвижность смеси. Можно значительно улучшить технологичес кие свойства бетонных смесей, введя в них поверхностно-активные вещества. Например, добавка сульфитно-спиртовой барды или сульфитно-дрожжевой бражки увеличивает подвижность смеси с 2 до 6—8 см, уменьшает ее водопо требность до 10%. Еще более эффективно действие так называемых супер пластификаторов. На свойства смеси сильное влияние оказывают техноло гические свойства цементного теста (водоцементное отношение, предопре
деляющее вязкость теста и его количество). Объем цементного теста опреде ляют по формулам:
С = Ш / р ) +1 В и с т ’\В = В — ЯСМ<1,65НГ,
^ ИСТ .ПЯТИ см ^ »
где Ц — количество цемента; р — плотность цемента; Вист, £ затв, Всм— соответственно вода, входящая в цементное тесто, вода затворения бетонной смеси и вода, расходуемая на смачивание песка и щебня; Н Г — нормальная
густота цементного теста.
С увеличением количества цементного теста при постоянной его вязкости (постоянном В/Ц) подвижность смеси возрастает, технологические свойства улучшаются. Если цементное тесто заполняет только пустоты между запол нителями, то смесь получается жесткой, неудобообрабатываемой. В пластич ных смесях зерна песка и щебня раздвинуты некоторой прослойкой цементно го теста. Обычно количество цементного теста в жестких смесях составляет 170—190 л, а в подвижных — более 200 л на 1 м3 бетонной смеси.
Технологические свойства бетонных смесей определяются объемом и вяз костью растворной составляющей (рис. 6.2). Показано, что смесь не расслаи вается, если сопротивление сдвигу растворной составляющей равно (4ч- 8)10~4МПа. Если сопротивление сдвигу раствора больше оптимального, удобоукладываемость смеси ухудшается. При сопротивлении сдвигу меньше оптимального из растворной части отделяется вода, бетонная смесь рас слаивается, а ее пластичность становится неудовлетворительной.
В подвижных бетонных смесях базальтовой макроструктуры сопротивле
ние сдвигу |
растворной |
части |
практически |
|
постоянно |
и |
равно |
(4ч- |
||||||
|
|
|
8) 10 |
4 МПа. Осадка конуса |
таких |
сме |
||||||||
|
|
|
сей регулируется за счет изменения тол |
|||||||||||
|
|
|
щины растворной пленки. Например, если |
|||||||||||
|
|
|
необходимо увеличить подвижность, в бе |
|||||||||||
|
|
|
тонную смесь добавляют воду, цемент и пе |
|||||||||||
|
|
|
сок в определенных отношениях, что обес |
|||||||||||
|
|
|
печивает постоянство сопротивления сдви |
|||||||||||
|
|
|
гу смеси, равное (4ч-8) |
Ю-4 МПа. Это |
||||||||||
|
|
|
повышает |
толщину |
|
растворной пленки, |
||||||||
|
|
|
увеличивает |
содержание |
растворной |
сос |
||||||||
|
|
|
тавляющей и уменьшает количество щеб |
|||||||||||
|
|
|
ня в смеси. При необходимости уменьшить |
|||||||||||
|
|
|
подвижность |
смеси |
поступают |
наоборот. |
||||||||
|
|
|
Однако уменьшение толщины растворной |
|||||||||||
|
|
|
пленки ограничивается из-за образования |
|||||||||||
|
|
|
структуры, при которой зерна щебня кон |
|||||||||||
|
|
|
тактируют, |
|
толщина |
растворной |
пленки |
|||||||
|
|
|
становится |
|
минимально |
возможной, |
ее |
|||||||
|
|
|
дальнейшее |
|
уменьшение |
резко |
ухудшает |
|||||||
|
|
|
жесткость |
(удобоукладываемость) |
(рис. |
|||||||||
|
|
|
6.3), |
поэтому |
в таких (жестких) |
смесях |
||||||||
|
|
|
толщина растворной |
пленки |
практически |
|||||||||
|
|
|
постоянна, |
|
а |
их |
Удобоукладываемость |
|||||||
|
|
|
регулируется за счет изменения вязкости |
|||||||||||
Рис. 6.2. Влияние сопротивления сдвигу |
растворной составляющей. |
|
|
|
ха |
|||||||||
растворной составляющей на |
удобо |
Помимо |
|
отмеченных |
структурных |
|||||||||
укладываемость бетонной смеси |
(d^ — |
рактеристик |
|
смесей, |
ряд |
особенностей |
||||||||
толщина |
растворной пленки) |
имеет |
технико-экономическое |
значение. |
||||||||||
|
|
|
Подвижные смеси в отличие от жестких характеризуются повышенным содержа нием воды, что, в свою очередь, требует увеличения расхода цемента. Количество цемента определяется не только соображе ниями достижения потребной прочности бетона, но и необходимостью обеспечить соответствующие технологические свой ства смеси. Это приводит к повышенному расходу цемента. В жестких смесях вслед ствие ограниченного содержания воды количество цементного теста и песка дове дено до минимума. Однако при примене нии жестких бетонных смесей возникает ряд технологических помех. Эти смеси труднее перемешивать и уплотнять.
Применение тех или иных смесей опре деляется технологическим оборудованием, особенностями элементов бетонируемых конструкций. С усложнением конфигура ции элементов, увеличением насыщения их арматурой подвижность смеси повы шают. В табл. 6.2. приведены требования к подвижности и жесткости бетонных сме сей, используемых для изготовления неко торых элементов конструкций.
Вид конструкций
Рис. 6.3. Зависимость удобоукладываемости бетонной смеси от толщины рас творной пленки:
1 — крупнозернистый песок; 2 — среднезерннстын песок; 3 — мелкозернистый песок; 4 — цемент ное тесто
Т а б л и ц а . 6.2
Способ уплотнения
Вибрированием |
Вручную |
|
Осадка конуса, см |
Жесткость, с |
Осадка конуса, см |
Сборные железобетонные конструкции, |
из |
>40 |
|
готовляемые на заводах и полигонах |
0 |
3—6 |
|
Подготовка под фундаменты, полы |
1—2 |
35—25 |
|
Основания дорожных покрытий |
|
|
|
Массивные неармированные конструкции. |
25—15 |
3—6 |
|
Дорожные покрытия |
2—4 |
||
Балки, колонны большого и среднего се |
15—10 |
6—8 |
|
чения |
4 - 6 |
||
Железобетонные конструкции, сильно |
на |
|
|
сыщенные арматурой (бункера, тонкие стен |
|
|
|
ки, пролетные строения арочных и балочных |
10—5 |
8— 15 |
|
мостов) |
6—12 |
||
Конструкции, выполняемые путем подвод |
— |
— |
|
ного бетонирования |
12—18 |
§ 6.3. ОБЫЧНЫЙ (ТЯЖЕЛЫЙ) БЕТОН
•Наибольшее распространение в строительстве получил тяжелый бетон. Его применяют для изготовления бетонных и железобетонных конструкций, пролетных строений и опор мостов, устройства дорожных покрытий и др.
Важнейшей характеристикой бетона является пористость, которая в значительной степени определяет его свойства. С увеличением пористости заметно возрастают водопоглощение, водонасыщение, водопроницаемость, уменьшаются прочность, морозостойкость и долговечность бетона. По ристость бетона
Я б = / 7 Г + Я к + Л „озд + Я 3 + Я Мз,
где Яг — поры геля в долях от объема бетона, которые могут быть вычис лены в зависимости от степени гидратации а и расхода цемента Ц (т/м3);
Лг = 0,29Я; Як— поры контракции; |
/7К= (В /Ц —0,5а )Ц\ /7возд— поры, |
образованные вовлеченным воздухом |
(Лвозд = 2ч-6%); /73— поры в запол |
нителях; /7МЗ— пространство между зернами заполнителя, не заполненное цементным тестом (для тяжелых бетонов /7МЗ= 0).
Ориентировочно пористость бетонов
У пор = ( 1 Y O/ Y ) >
где уо — объемная масса бетонов, кг/м3; у — плотность бетонов, получен ная как'средневзвешенная величина от плотности щебня, песка и цементного камня, г/см3
Так как плотности щебня, песка и продуктов взаимодействия цемента с водой близки, а плотность бетонов колеблется в небольших пределах (2650—2700 кг/м3) , пористость по существу зависит только от объемной мас сы бетона.
Таким образом, деление бетонов по их объемной массе практически является классификацией по величине их пористости.
Обычно пористость тяжелых бетонов составляет 10—15%, в отдельных случаях 5—7%. Дальнейшее понижение пористости затруднено вследствие сложности уплотнения жестких бетонных смесей и удаления из них воздуш ной составляющей. Для оценки пористости важны показатели, характеризую щие крупность, распределение пор, их форму и степень замкнутости. Размер пор и их строение определяет, в частности, характер связи воды, заключен ной в порах, ее способность к миграции в бетоне, что существенно влияет на водопоглощение, водонасыщение, водопроницаемость и другие свойства.
Фильтрация воды в бетонах происходит по порам и капиллярам в цемент ном камне при размере их диаметра больше 1 мкм, а также по микрополостям в местах контактов заполнителей и цементного камня.
Водопоглощение. У тяжелых бетонов водопоглощение колеблется в преде лах 2—4% по массе (или 5—10% по объему), их водонасыщение больше. Разница между водопоглощением и водонасыщением обусловлена объемом замкнутых пор в бетоне.
Показателем водонепроницаемости бетона служит гидростатическое дав ление, при котором вода не просачивается через образец, испытуемый по стэндартной методике. По водонепроницаемости бетоны делят на несколько ма рок: В-2, В-4, В-6, В-8 (цифра обозначает величину гидростатического давле ния, при котором вода не просачивается).
Водопроницаемость, водопоглощение и водонасыщение бетона могут быть значительно снижены, если приготовлять бетон с низким водо-цемент ным отношением при достаточном количестве цементного теста, а также введении в бетон поверхностно-активных добавок, Они видоизменяют микро структуру бетона за счет уменьшения водопотребности бетонной смеси, вовле чения некоторого количества воздуха в поры, которые блокируют сообщение между отдельными капиллярами и микрополостями. Эффективным способом
понижения водопроницаемости являет |
|
|||||||
ся кольматация пор |
высокомолекуляр |
|
||||||
ными моно- и полимерными веществами |
|
|||||||
(битумы, |
сера, метилметакрилат). |
|
||||||
Прочность бетона. Ведущий показа |
|
|||||||
тель |
механических |
|
свойств |
бетона — |
|
|||
марка бетона — предел прочности при |
|
|||||||
сжатии |
бетонных |
|
кубов |
размером |
|
|||
15x15x15 см в возрасте 28 сут при |
I |
|||||||
твердении в нормальных условиях (тем |
||||||||
пература |
18—20°С |
и |
относительная |
Рис. 6.4. Схема испытания бетонных об |
||||
влажность окружающей |
среды 90— |
разцов: |
||||||
100%). Для тяжелых бетонов установ |
лывание |
|||||||
|
|
|
|
|
|
|
|
а — на растяжение; б — на изгиб; в — на раска |
лены такие марки: 50, 100, 150, 200, |
|
|||||||
250, |
300, |
400, |
500, |
600. |
|
|
|
Показатель прочности бетона в значительной степени зависит от методики испытания, в частности от вида его деформирования и скорости нагружения. С уменьшением скорости нагружения показатели прочности уменьшаются, приближаясь к некоторому пределу — длительной (долговременной) проч ности бетона 7?д. Допускаемые напряжения в бетонной конструкции должны быть меньше этой величины, однако ее определение затруднено, так как' требуется длительное время для получения показателя /?д. Поэтому проч ность бетона определяют при определенной (стандартной) скорости нагруже ния образца. На показатель прочности заметное влияние оказывают размер, форма и качество испытуемого образца. С уменьшением размера грани об разца в 2 раза его показатель прочности возрастает более чем на 10%. При определении показателя прочности на образцах, тщательно изготовленных в высококачественных формах, его можно повысить до 20%. Показатели прочности бетонов зависят от их влажности, условий твердения, поэтому ис пытание должно производиться со строгим соблюдением стандартной мето дики (ГОСТ 10180—78).
При расчете некоторых конструкций (например, бетонных покрытий и ос нований) в качестве расчетной прочности бетона принимают предел проч ности на растяжение при изгибе. Марка бетона при изгибе определяется проч ностью при изломе неармированных бетонных балочек размером
15x15x50 см сосредоточенными силами (рис. 6.4). |
|
|
||||
Пре^л прочности |
при изгибе |
/?изг и предел прочности при сжатии /?сж |
||||
связаны зависимостью |
И3 1 |
I Ж ' |
где а = 0,6—0,7. Соотношение |
I-J |
колеб- |
|
лется в пределах 6—10. |
|
|
А нзг |
|||
конструкций и изделий (трубы, |
|
резервуа |
||||
Для |
некоторых бетонных |
|
||||
ры и др.) |
ведущим показателем качества бетона является его сопротивление |
растяжению. Предел прочности при растяжении определяют с помощью осевого растяжения образцов. Его можно определить и с помощью раскалы
вания бетонного образца.
Для тяжелых бетонов прочность при растяжении /?р меньше прочности при сжатии в 8—20 раз (меньшее соотношение соответствует бетонам мар ки 50, большее — марки 600 и более). Прочность при растяжении изменяется в большей степени, чем прочность при сжатии, в зависимости от наличия
микротрещин и других дефектов в структуре бетона. Поэтому соотношение |
|
D |
может служить показателем качества (дефектности) |
этих величин |
|
Ар |
^ |
структуры |
бетона. Чем больше |
тем больше дефектов в структуре |
бетона, тем |
ниже его качество. |
' р |
fa |
|
|
|
|
|
|
|
|
Прочность |
бетона |
как |
|
материала |
|||||||
МПа |
|
|
|
|
'чV |
|
|
|
конгломератного |
строения |
|
зависит от |
||||||||
70 / |
|
|
|
|
|
|
|
прочности |
отдельных |
его |
составляющих |
|||||||||
|
|
|
|
V |
|
|
(цементного камня, зерен щебня и пес |
|||||||||||||
Г |
|
|
|
|
|
|
ка), |
прочности |
|
сцепления |
между |
ними, |
||||||||
ВО |
|
|
|
|
|
\ |
|
|
а также |
особенностей |
структуры бетона |
|||||||||
50 |
|
|
|
|
|
|
|
|||||||||||||
|
|
/ |
/ |
|
|
|
- Л г Ш |
в целом. |
|
|
|
|
|
|
|
|
|
|
||
40 |
|
|
|
|
\ |
|
Прочность |
бетона |
прямо |
|
пропорцио |
|||||||||
|
|
X ' N |
|
|
|
|||||||||||||||
|
|
/ |
|
' Ш |
нальна |
активности |
цемента |
(рис. |
6.5.). |
|||||||||||
30 |
|
/ |
/ |
/ |
|
|
||||||||||||||
|
|
|
|
|||||||||||||||||
|
/ |
/ |
|
|
|
|
Ч ; |
С понижением |
водо-цементного отноше |
|||||||||||
|
/ |
|
|
|
|
ния |
до |
|
определенного предела |
проч |
||||||||||
20 |
f |
|
|
|
|
|
|
|||||||||||||
|
|
|
|
|
|
|
|
ность бетона данного состава и при дан |
||||||||||||
/ / |
|
|
|
|
|
|
ш |
|||||||||||||
10 |
|
|
|
|
|
|
|
|
ном |
способе |
уплотнения |
|
повышается. |
|||||||
О |
|
|
|
|
|
|
|
''ZOO |
Извест-но, что количество воды для |
|||||||||||
|
|
|
|
|
|
|
|
|||||||||||||
0,1 |
|
0,2 |
0,3 |
0,4 |
0,5 |
0,6 |
0,7 В/Ц |
процессов гидролиза и гидратации цемен |
||||||||||||
|
|
|
|
|
|
|
|
|
та составляет Ю—20% от его массы |
|||||||||||
Рис. 6.5. Зависимость прочности бетона |
(В/Ц = 0,10-^0,25). |
Однако |
в |
этом |
слу |
|||||||||||||||
Rf) от активности цемента /?ц и водо- |
чае |
смесь |
получается |
жесткой |
и трудно |
|||||||||||||||
цементного |
отношения |
(верхняя кри |
обрабатываемой, |
ее |
трудно |
перемешать, |
||||||||||||||
вая получена |
при |
сильном |
уплотнении |
|||||||||||||||||
|
|
|
|
бетонной смеси) |
|
укладывать в |
|
опалубку |
и |
|
уплотнять. |
|||||||||
|
|
|
|
|
|
|
|
|
При |
этом |
структура |
бетона |
формиру |
ется неплотной и пониженной прочности.
Оптимальное водо-цементное отношение, при котором прочность бетона наибольшая, определяется условиями удобообрабатываемости смеси. При обычных условиях уплотнения (вибрирования) оптимальное В/Ц нахо дится в пределах 0,4—0,5, а при усиленном уплотнении (вибропрессовании, виброштамповании) — 0,25—0,4. Если в бетоне значение В/Ц выше опти мального, создается избыток свободной воды, которая увеличивает пори стость цементного камня, а следовательно, понижает прочность бетона.
Прочность бетона может быть представлена зависимостью
R d — А 1А 2Л з R и ,
где Л,, А2, А3 — коэффициенты, количественно учитывающие влияние особенностей макро-, мезо- и микроструктуры на прочность бетона.
Коэффицснт микроструктуры
где к w с — коэффициенты, |
зависящие от свойств |
цемента |
технологии |
|
приготовления |
цементобетонных смесей, а также от |
методики |
определе |
|
ния прочности |
цементобетона и |
активности цемента. |
|
|
После подстановки значения А3 в предыдущую формулу получим: |
||||
|
R6 = Al |
- с) /?„ |
|
|
При обычной технологии приготовления смесей применительно к бето нам 28-суточного возраста значения коэффициентов к и с могут быть опреде лены по табл. 6.3. Для бетонов, твердение которых осуществляется в пропа рочных камерах, значение коэффициента k должно быть уменьшено на 10—15%.
При твердении в. нормальных ус ловиях прочность бетона после 3 сут твердения, как установил проф. Б. Г Скрамтаев, увеличивается приблизи тельно пропорционально логарифму суток твердения.
Коэффициент k в зависимости от возраста бетона
Т а б л и ц а 6.3
|
Цемент испытывался в растворе |
||
Коэффи- |
пластичном консистенции |
||
цнснты |
Сжатие |
Изгиб |
Растяжение |
|
|||
k |
0,58 |
0,42 |
0,21 |
С |
0,50 |
0,30 |
0,30 |
kn |
= lg п |
km |
lg т ' |
где kn, km— значения коэффициентов при твердении бетона через п и т суток.
Коэффициент k зависит также от добавок, вводимых в бетонную смесь и, в частности, добавок-ускорителей.
Численные значения коэффициентов макро- и мезоструктуры (Л,, Л2) определяются свойствами щебня и песка (табл. 6.4 и 6.5). Существенное влияние на прочность бетонов оказывает прочность сцепления зерен щебня с раствором и зерен песка с цементным камнем (рис. 6.6), которая зависит от химико-минералогического состава цемента, чистоты и шероховатости поверхности зерен щебня.
Если прочность зерен щебня R3 ниже определенного предела — для гра нитов R3< (2,0-^2,4)/?б, для известняков /?з< (1,5-^2,0)/?б — прочность бе тона может существенно уменьшиться (рис. 6.7). Количество щебня и песка в бетоне, их зерновой состав, форма и крупность зерен играют важную роль в формировании оптимальных структур бетона, поэтому указанные парамет ры могут изменить прочность бетона на 15—20%.
Для ряда конструкций, в том числе дорожных плит, важное значение имеет усталостная прочность бетона — его способность сопротивляться воз
действию многократных |
переменных нагрузок. Эти нагрузки расшатывают |
||||||
|
|
|
|
|
Т а б л и ц а |
6.4 |
|
|
|
|
А\ при сжатии |
Ах при изгибе |
|
||
Щебень |
|
Пластичные |
Жес 1 кие |
Пластичные |
Жесткие |
|
|
|
|
|
|
||||
|
|
|
смеси |
смеси |
смеси |
смеси |
|
Известняковый и шлаковый |
щебень |
1,08 |
1,13 |
1,17 |
1,22 |
|
|
Фракционированный гранитный щебень |
1,08 |
и з |
1,08 |
М3 |
|
||
Рядовой гранитный |
щебень. |
|
1,00 |
1,05 |
1,00 |
1,05 |
|
Фракционированный |
гравий |
|
|
||||
Рядовой гравий |
|
|
0,94 |
1,00 |
0,90 |
0,95 |
|
Щебень, имеющий пылевато-глинистую |
0,90 |
|
0,85 |
|
|
||
пленку |
|
|
|
|
|
||
|
|
|
|
|
Т а б л и ц а |
6.5 |
|
|
|
А2 при сжатии и аодопотребности песков, % |
|
|
|||
Песок |
|
|
7 - 9 |
9 - 1 2 |
/12 |
при изгибе |
|
|
|
|
|
|
|
||
Искусственный (высевки) |
|
1,10 |
1,05 |
|
1,15 |
|
|
Чистый, кварцевый |
|
|
1,00 |
0,95 |
|
1,00 |
|
С сильно окатанными зернами, |
0,95 |
0,90 |
|
0,93 |
|
||
а также загрязненный |
|
|
|
|
|
|
|
|
ПСЖ1 |
структуру бетона, вследствие |
чего |
он |
||||
|
|
|
|
МПа |
разрушается при более низких напря |
||||||
|
|
|
|
30 |
жениях, чем от однократного нагруже |
||||||
|
|
|
|
|
ния. Взаимосвязь между разрушающи |
||||||
|
|
|
|
20 |
ми напряжениями ау и количеством |
||||||
|
|
|
|
циклов нагружений N, приложенных до |
|||||||
|
|
|
|
|
разрушения |
бетона, |
представлена |
на |
|||
|
|
|
|
10 |
рис. 6.8. Если |
ау = /?,(/?,— прочность, |
|||||
0 |
0,0 |
1,1 |
1,8 Ос,МПа |
|
характеризующая однократное |
разру |
|||||
|
|
|
|
|
шение бетона при скорости нагружения, |
||||||
0 |
0,25 |
0,50 0,75Rc/Rp |
|
равной |
скорости нарастания напряже |
||||||
|
|
|
|
|
ний в пределах одного цикла), бетон |
||||||
Рис. 6.6. Влияние прочности сцепления |
разрушается за один цикл. С уменьше |
||||||||||
Rc зерен щебня с раствором на проч |
нием, ау |
возрастает |
количество |
цикли |
|||||||
ность |
бетона |
(прочность раствора |
ческих |
нагружений |
N до разрушения |
||||||
|
Яр = 2,4 МПа): |
|
бетона. |
Если ау</?у(/?у — физический |
|||||||
|
• — растяжение; |
X — сжатие |
|
||||||||
|
|
|
|
|
предел усталости, при котором бетон |
||||||
|
|
|
|
|
практически не разрушается), то бетон |
||||||
Оизг£, |
|
|
|
|
не только не разрушается при |
цикли |
|||||
|
|
|
|
ческом нагружении, но наблюдается не |
|||||||
МПа |
|
|
|
|
|||||||
|
|
|
|
которое |
упрочнение, обусловленное |
||||||
|
|
|
|
|
|||||||
о |
|
|
|
|
микропластическими |
деформациями |
в |
||||
|
|
|
|
структуре, уменьшающими концентра |
|||||||
|
|
|
|
|
цию напряжений в бетоне. |
бетонов |
|||||
о |
|
|
|
|
Усталостная |
прочность |
|||||
|
|
|
|
возрастает с улучшением однородности |
|||||||
|
2 |
4 |
5 |
5р.з,МПа |
структуры бетонов больше, чем стати |
||||||
Рис. 6.7. Влияние прочности зерен щеб |
ческая. Высокая усталостная прочность |
||||||||||
ня Яв на |
прочность бетона |
R6 |
характерна |
для |
мелкозернистых бето |
||||||
|
|
|
|
|
нов естественного твердения, приготов |
||||||
|
|
|
|
|
ленных |
на |
известняковом и шлаковом |
щебне. Особенно отрицательно влияют на усталостную прочность низкая прочность сцепления между составляющими, увеличение неоднородности их свойств. Уменьшение водоцементного отношения, введение в смесь поверхностно-активных веществ способствуют некоторому повышению усталостной прочности, увлажнение бетонов резко уменьшает ее. У воздушно сухих бетонных образцов при многократном нагружении (1 млн. циклов) оу= (60Ч-70) %, у водонасыщенных а у= (254-40) % от прочности однократно го нагружения,, определяемого в стандартных условиях.
Деформации под нагрузкой. Бетон является упруго-вязко-пластичным ма териалом, вследствие этого при некоторой длительности действия механи ческой нагрузки в образце наряду с упругими возникают и вязко-пластичные деформации.
Если в некоторый момент времени снять нагрузку, то деформация бетона уменьшится на величину, равную начальной упругой деформации. Затем происходит медленное восстановление некоторой части мгновенно обратимых
, деформаций (см. рис. 1.2).
Упругие деформации характеризуются полной упругой деформацией, а также модулем упругости
I00000
36
1,7 +
* с
где /?сж — предел прочности бетона при сжатии, МПа.
Модуль упругости бетона зависит не только от прочности, но и от его структуры, свойств песка, щебня и др. При равной прочности с уменьшением крупности щебня модуль упругости уменьшается, с ростом крупности увели чивается.
Зависимость относительной деформации бетона от приложенного напря жения не прямолинейна (рис. 6.9), вследствие этого с ростом напряжений модуль упругости изменяется-. Поэтому при экспериментальном определении модуля упругости пользуются формулой
Е= 0,2/?„п
Е|
где Rnn— призменная прочность бетона, МПа (предел прочности при сжатии призмы 15x15x60 или 10x10x40 см);е, — относительная дефор мация бетона при а = 0,2/?пп.
Для напряжений а>0,2/?пп определяют переменную величину — модуль деформации как отношение напряжений к полной относительной деформа ции.
Для бетонов марок 200—400 модуль упругости находится в пределах
3 • 104—4 • 104 МПа. |
При o = Rtl (длительной прочности) модуль деформа |
ции уменьшается на |
10—25% по сравнению с модулем упругости. |
Необратимые упруго-пластические деформации, возникающие под влия нием постоянной нагрузки, называют деформациями ползучести. Они могут превышать упругие деформации бетона в несколько раз и возрастают с увели чением постоянной нагрузки и времени ее действия. Деформации ползучести определяются структурой бетона, прежде всего микроструктурой цементного камня. Гелевая составляющая цементного камня, а также развитие микро трещин в бетоне под воздействием механической нагрузки в основном обусловливают ползучесть (вязко-пластические деформации). Повышенные тонкость помола цемента и водо-цементное отношение способствуют росту деформаций ползучести. С увеличением количества щебня и песка ползучесть бетона уменьшается.
Деформации бетона учитывают, решая многие задачи и в первую очередь при расчете и технологии производства железобетонных конструкций.
Деформации при изменении влажности. С изменением влажности бетон
претерпевает объемные изменения (рис. |
.10). Если постоянно бетон находит- |
||
ся во влажной среде, постепенно уве |
|
||
личивается |
его объем — набухание, |
|
|
и, наоборот, с уменьшением влажности |
|
||
происходит усадка. Усадка при твер |
|
||
дении происходит в две стадии. Пер |
|
||
вичная усадка вызвана испарением и |
|
||
возможной утечкой воды из бетонной |
|
||
смеси через |
опалубку, |
поглощением |
|
влаги опалубкой, а также основанием |
|
||
дорожной одежды. Вторичная усадка |
|
||
возникает в процессе твердения и высы |
|
||
хания бетона. Этот вид усадки частично |
|
||
обратим, так как при последующем |
|
||
увлажнении бетон расширяется. Размер |
|
||
усадки и ее развитие зависят от минера |
Рис. 6.8. Схема зависимости усталостной |
||
логического |
состава и |
добавок, тон |
прочности бетона av от количества циклов |
кости помола цемента, водо-цементного |
нагружения /V: |
||
I — кривая усталости; 2 — касательная кривая |
|||
отношения, |
свойства |
и количества |
талости |
Предел прочности В=1 |
|
|
заполнителей, температуры и |
влажно |
|||||||||||
|
|
|
|
|
|
|
сти |
окружающей |
среды. Повышенная |
||||||
|
|
|
|
|
|
|
усадка характерна для бетонов с боль |
||||||||
|
|
|
|
|
|
|
шим содержанием цемента и водо |
||||||||
|
|
|
|
|
|
|
цементным |
отношением |
(В /Д > 0,6) |
||||||
|
|
|
|
|
|
|
Температурные деформации. Коэф |
||||||||
|
|
|
|
|
|
|
фициент |
температурного |
расширения |
||||||
|
|
|
|
|
|
|
или сжатия изменяется в зависимости |
||||||||
|
|
|
|
|
|
|
от состава бетона и его влажности. |
||||||||
|
|
|
|
|
|
|
Для практических целей можно принять |
||||||||
|
|
|
|
|
|
|
коэффициент |
температурного |
расши |
||||||
|
|
|
|
|
|
|
рения бетона равным 10 • Ю-6 на 1°С. |
||||||||
|
|
|
|
|
|
|
При |
оценке |
температурных |
дефор |
|||||
|
|
|
|
|
|
|
маций в больших массивах обычно при |
||||||||
Относительная деформация |
нимают |
половину |
значения указанно |
||||||||||||
го коэффициента, полагая, что осталь |
|||||||||||||||
|
|
с~ |
|
|
|
|
ная часть компенсируется |
ползучестью |
|||||||
|
|
|
|
|
|
|
бетона. |
Температурные |
деформации |
||||||
Рис. 6.9. Кривая деформирования бе |
бетона создают напряжения в плитах |
||||||||||||||
|
|
тона: |
|
|
|
дорожных одежд и могут вызвать тре |
|||||||||
^поли» еупр> епл — соответственно полная, |
упру |
щины. Для устранения этого |
явления |
||||||||||||
гая и пластичная относительные деформации |
|||||||||||||||
|
|
|
|
|
|
|
в бетонных покрытиях устраивают тем |
||||||||
|
|
|
|
|
|
|
пературные швы. |
и |
морозостойкость |
||||||
|
|
|
|
|
|
|
Долговечность |
||||||||
|
|
|
|
|
|
|
бетона. Основы долговечности и моро |
||||||||
|
|
|
|
|
|
|
зостойкости бетона разработаны проф. |
||||||||
|
|
|
|
|
|
|
С. В. Шестоперовым. Они харак |
||||||||
|
|
|
|
|
|
|
теризуют длительность воздействия по |
||||||||
|
|
|
|
|
|
|
годно-климатических, физико-химиче |
||||||||
|
|
|
|
|
|
|
ских и механических факторов, при |
||||||||
|
|
|
|
|
|
|
которой свойства бетона не ухудшают |
||||||||
|
|
|
|
|
|
|
ся больше допустимых пределов. Долго |
||||||||
Высуши- УВлаж- |
Высушиувлаж |
вечность |
бетона |
измеряют |
единицами |
||||||||||
времени |
(с, |
сут, |
год |
и т. |
п.), |
а так |
|||||||||
Вание |
нение |
Вание |
нение |
||||||||||||
|
|
|
|
|
|
|
же |
количеством |
циклов |
воздействия |
|||||
Рис. 6.10. Схема усадки бетона при |
указанных факторов. |
|
|
|
|||||||||||
чередующихся |
увлажнении |
и |
высы |
К бетонным элементам конструкций |
|||||||||||
|
|
хании: |
|
|
|
предъявляют |
требования |
по |
морозо |
||||||
/ — расширение бетона, постоиппм находящегося |
|||||||||||||||
по влажном |
состоянии; |
2 — \садкн |
бетона |
лрн |
стойкости, которую определяют путем |
||||||||||
высыхании; |
3 — усадка и |
расширение при |
чере |
замораживания образцов |
до —15-4- |
||||||||||
дующихся высушивании н увлажнении |
|
||||||||||||||
в воде |
при |
15—20°С. |
Образцы |
-4— 20°С и последующего оттаивания |
|||||||||||
испытывают после |
28 |
сут естественного |
твердения или через 7 сут после пропаривания. Контрольные образцы твердеют в камере нормального твердения, их испытывают в эквивалентном возрасте: 7э = / + 0,8/г(/ — количество суток до испытания образцов на морозостойкость; п — число циклов испытания).
За марку бетона по морозостойкости принимают наибольшее число цик лов попеременного замораживания и оттаивания, при котором прочность образцов уменьшается не более чем на 15% по сравнению с прочностью об разцов, испытанных в эквивалентном возрасте и без потери по массе более 5% (ГОСТ 10060—76). По показателям морозостойкости (Мрз) бетоны делят на марки 50, 75, 100, 150, 200, 300, 400 и 500.
Морозостойкость — одно из главных требований к бетонам, работающим в условиях попеременного замораживания и оттаивания. К ним относятся
дорожные и гидротехнические бетоны. Бетон — пористый материал, и, если все поры в нем будут заполнены водой, он разрушится уже при первом цикле замораживания вследствие возникновения больших растягивающих напря жений из-за образования льда, объем которого на 9% больше объема воды. Обычно не все поры в бетоне заполнены водой, при замерзании часть воды переходит в поры, которые являются условно-замкнутыми.
Морозостойкость зависит от водо-цементного отношения, вида и актив ности цемента, условий твердения и возраста бетона к моменту заморажива ния, плотности бетона, качества песка и щебня.
С увеличением водо-цементного отношения морозостойкость бетона уменьшается вследствие образования большой сети водопроницаемых, взаимосвязанных капилляров, способных легко насыщаться водой. Для моро зостойких бетонов водо-цементное отношение принимают не более 0,5.
В морозостойких бетонах применяют портландцементы с содержанием алюмината С3А меньше 8%. Пуццолановые и шлакопортландцементы снижа ют морозостойкость из-за их большой водопотребности, характеризуемой повышенной густотой цементного теста. При прочих равных условиях с увели чением активности цемента, возраста бетона его морозостойкость возрастает, что обусловлено увеличением степени гидратации цемента, а следовательно, уменьшением общей пористости цементного камня.
Для морозостойких бетонов предъявляются повышенные требования к песку и щебню. В них ограничивается содержание примесей, увеличиваю щих водопотрсбпость и снижающих прочность сцепления цементного камня со щебнем. Коэффициент линейного и температурного расширения шебня не должен резко отличаться от коэффициента линейного температурного рас ширения цементного камня.
Для повышения морозостойкости бетона необходимо подбирать плотные составы из морозостойкого щебня и песка с оптимальным количеством цемен та при минимально возможном количестве воды, применять прогрессивную технологию перемешивания и уплотнения смесей, а также обеспечивать уход за свежеуложенным бетоном в начальный период твердения, в частности обработку поверхности плит битумной (дегтевой) эмульсией или разжижен ным битумом. Повышают морозостойкость гидрофобные воздухововлекаю щие добавки, способствующие образованию условно-замкнутых пор с гидро фобной поверхностью, которые в обычных условиях не заполняются водой и служат резервными порами, куда отжимается вода при замораживании бетона.
Введение в смесь уплотняющих структур добавок в виде растворов, сус пензий и эмульсий заметно понижает пористость и повышает морозостойкость бетона. Так, известны добавки, изготавливаемые на основе хлористого каль ция в сочетании с хлористым алюминием и хлористым железом, эмульсий высокомолекулярных соединений (битумные, полимерные) и др. Морозостой кость возрастает во много раз при пропитке бетонных изделий высокомолеку лярными веществами, мономерами, полимерами.
Коррозия бетона. Бетон разрушается под влиянием физико-химического воздействия факторов среды. Коррозия зависит главным образом от корро зионной стойкости цементного камня. Чем больше поверхность (внешняя и внутренняя) бетона, соприкасающаяся с агрессивной газообразной или жидкой средой, тем энергичнее коррозия бетона. Электрический ток разруша ет влажный бетон, вызывая электролиз составляющих цементный камень.
Для придания коррозионной стойкости бетону необходимо применять цементы, соответствующие агрессивности среды: шлаковый сульфатостойкий или глиноземистый, а в отдельных случаях кислотоупорный. Следует прида вать большую плотность бетону, защищать его поверхность от проникновения
газов и воды с растворенными агрессивными веществами, затирая поверх ность изделия раствором жидкого стекла с последующей обработкой хлбристым кальцием или кремнефтористым натрием, обрабатывая поверхность битумом или дегтем, битумной эмульсией, разжиженным битумом (дегтем), пленкообразующими высокомолекулярными веществами.
§ 6.4. МАТЕРИАЛЫ ДЛЯ БЕТОНА
Качество бетона зависит от качества материалов— щебня (гравия), песка, цемента, воды и добавок, которые обусловливают не только веществен ный состав, но и структуру бетона. Качество материалов регламентируется нормативно-техническими документами (ГОСТами, техническими условиями
и др.).
Щебень (гравий). Для бетона пригоден щебень, удовлетворяющий требо ваниям ГОСТ 10268—80. Его получают из скальных горных пород и искус ственных камневидных материалов (металлургических шлаков, керамики). Качество щебня как макроструктурной составляющей определяют круп ностью, зерновым составом и формой зерен, свойствами исходной породы (прочность, морозостойкость, водопоглощение, минералогический со
став и др.).
Обычно крупность щебня должна составлять не более 1/4 минимального сечения элемента конструкции и не более наименьшего расстояния между стержнями арматуры. Для бетонирования плит, полов и покрытий допускают наибольшую крупность щебня до 1/3 толщины плиты. Для массивных элемен тов сооружений можно применять и очень крупный щебень. В бетонах специального назначения (например, высокопрочных, дорожных и аэродром ных) наибольшая крупность щебня равна 40, 20 и в отдельных случаях 10 и 5 мм. Это не только улучшает физические свойства бетона, но и увеличивает его прочность при изгибе и растяжении.
Для создания плотных смесей с хорошими технологическими свойствами
применяют разнозернистый щебень, пустотность которого |
не более 45%, |
а зерновой состав укладывается в предельные кривые (рис. |
6.11). |
Предпочтительнее щебень кубовидный. Плоских (лещадных) и вытяну тых (пальцевидных) зерен не следует допускать более 25%.
При взаимодействии цементного теста с поверхностью щебня протекают физико-химические процессы, которые обусловливают прочность сцепления (адгезию) цементного камня со щебнем, а, следовательно, определяют проч ность бетона, особенно при растяжении. Высокое сцепление обеспечивает свежедробленный чистый щебень из известняков и металлургических шлаков.
У щебня из пород Тонкопористой тек
|
|
|
стуры прочность сцепления с цементным |
|||||||
Область |
|
100 |
камнем |
выше. |
Повышение |
шерохова |
||||
цепкого |
|
а* |
тости, уменьшение Количества |
смятых |
||||||
- щебня |
|
80* |
участков |
также |
способствует |
увеличе |
||||
|
|
50% |
нию сцепления |
цементного |
камня со |
|||||
|
|
щебнем. |
|
|
|
|
|
|
||
|
|
& |
|
|
|
|
|
|
||
|
|
По прочности щебень подразделяют |
||||||||
|
Область |
|
||||||||
|
. го I |
на марки: 1400, 1200, 1000, 800, 600, |
||||||||
|
крупного |
|||||||||
|
щебня |
Д |
400, 300, 200. В щебне марок 1400 и 1200 |
|||||||
“наш |
слабых |
зерен |
может быть |
не |
более |
|||||
|
||||||||||
|
5%, марок |
1000—600 — не более |
10%, |
|||||||
Рис. 6.11. Предельные кривые грануломет |
остальных |
марок — до |
15% |
(по |
||||||
массе). |
|
|
|
|
|
|
||||
рического состава |
щебня и гравия |
|
|
|
|
|
|
По морозостойкости (количеству циклов замораживания и оттаивания, при котором потеря в массе пробы крупнозернистого заполнителя не превы шает 5%) установлены следующие марки: 25, 50, 100, 150, 200, 300. Морозо стойкость. щебня в каждом отдельном случае устанавливается проектом и должна быть не ниже морозостойкости бетона.
По показателю прочности щебень должен быть примерно в 2 раза больше прочности бетона марки 300 и выше, при этом водопоглощение щебня не должно быть более 3%. Если бетон не будет подвержен замерзанию, водо поглощение щебня может быть до 5%. Для бетонов марки 300 и ниже проч ность щебня должна быть больше марки в 1,5 раза. Для специальных бето нов (дорожного, аэродромного и др.), работающих в конструкциях на изгиб
ирастяжение, следует определять прочность щебня при растяжении, которая в 1,5—2 раза должна быть выше, чем у бетона (меньшее значение для щебня из известняков и песчаников, большее — для щебня из изверженных пород).
Вщебне ограничивается содержание вредных примесей в виде сернистых
исернокислых соединений, корродирующих цементный камень, глинистых веществ (до 1% по массе) и органических соединений, которые при повышен ном их содержании разрушают бетон.
Качество гравия, как макроструктурой составляющей бетона определяет ся петрографическим составом, крупностью, гранулометрическим составом, формой и степенью окатанности зерен, количеством и качеством примесей, а также физико-механическими свойствами.
Требования к гравию по крупности и зерновому составу, водопоглощению и морозостойкости те же, что и к щебню. Лучшими разновидностями гравия являются те, которые состоят из зерен округлой, угловатой формы со слабоокатанной (шероховатой) поверхностью. Плоские окатанные зерна следует дробить.
Прочность бетона с гравием обычно на 10—15% ниже (при очень гладкой поверхности зерен даже на 30%), чем бетона со щебнем (при равном водо цементном отношении). Поэтому, если по технико-экономическим соображе ниям целесообразно, следует дробить гравий на щебень. Примесь дробленого гравия около 35% заметно улучшает его качество.
Сернистых и сернокислых примесей в гравии не должно быть более 1% в пересчете на S03, пылевато-глинистых — до 2% (по массе), а органических веществ — следы (не более эталона по колориметрической пробе).
Поскольку в месторождениях природный гравий, как правило, загрязнен пылевато-глинистыми примесями, его следует промывать в гравиемойках, а затем фракционировать. Гравий из разнопрочных зерен подвергают сепара
ции на классификаторах.
Песок. Для бетона применяют пески, удовлетворяющие ГОСТ 10268—80. Обычно это природные пески. Лишь в тех случаях, когда необходимо улуч шить качество местного природного песка, к нему добавляют искусственный песок (высевки). Вопрос обогащения местных мелкозернистых песков добав ками искусственных песков в каждом отдельном случае решается с учетом технико-экономической целесообразности.
Качество природного песка для бетона определяют его крупностью, зерно вым и минералогическим составами, формой зерен, количеством и разновид ностью примесей. Важная характеристика песка — бодопотребность, т. е. способность удерживать определенное количество воды на поверхности зерен и в пустотах. Бодопотребность (суммарный показатель качества) колеблется в пределах 5—6% для крупнозернистых и 12—13% для мелкозернистых
песков.
Крупность и зерновой состав имеют большое значение для получения бето нов заданной прочности при минимальном расходе цемента. Цементное тесто
заполняет пустоты между зернами песка и обволакивает их. Следовательно, чем меньше удельная поверхность песка и его пустотность (в крупнозер нистых песках с плотным зерновым составом), тем меньше расход цемента. Зерновой состав песка должен соответствовать предельным кривым (рис. 6.12). Крупность песков для бетона определяют в соответствии с показа телями, приведенными в табл. 6.6.
Наличие в песках органических примесей, слюды, гипса, заметно ухудша ет качество бетона. Поэтому технические условия на песок ограничивают содержание слюды не более 0,5%, гипса не более 1%, пылевато-глинистых частиц не более 3% и органических примесей по колориметрической пробе — не темнее цвета эталона. Лучшими являются слабоокатанные (ледниковые) крупнозернистые чистые пески — речные, озерные и морские. Однако в ряде случаев они содержат примеси створок ракушек, гравийные зерна, а иногда и глину. В этих случаях их необходимо прогрохачивать и промывать.
Использование местных мелкозернистых песков с повышенной удельной поверхностью и пустотностью юбычно вызывает большой расход цемента. Прогрессивная технология производства бетонных смесей (введение пласти фицирующих добавок, принудительное перемешивание и виброуплотнение) эффективно повышает использование местных мелкозернистых песков.
Цементы. Для бетона применяют портландцементы и его разновидности, а также другие виды цементов, удовлетворяющие требованиям ГОСТов, в первую очередь ГОСТ 10178—76 и ГОСТ 23464—79. Выбор цемента опреде ляется условиями работы бетонных элементов сооружений. Так, для гидро технических сооружений применяют портландцементы с умеренной экзотермией, пуццолановые и шлакопортландцемснты, для срочных работ — быстротвердеющие портландцементы и глиноземистые, для работы в агрессивных средах — сульфатостойкие цементы, для заделки стыков бетонных элемен
тов — расширяющиеся или безусадочные цементы и т. д. |
|
|||||
В зависимости от заданной прочности бетона |
(его марки) устанавливают |
|||||
активность |
(марку цемента): |
|
|
|
|
|
Марка |
бетона |
150 |
200—250 |
300 |
400 |
500 |
« цемента |
300 |
400 |
500 |
500—600 |
600 |
В технологии высокопрочных бетонов допускается превышение марки бетона над маркой цемента.
Вода. Для затворения бетонных смесей используют воду, удовлетворяю щую требованиям ГОСТ 23752—79. Обычно это чистая питьевая вода, не со
|
|
|
|
|
держащая |
свободных минеральных и |
|||||
|
|
|
|
|
органических |
кислот |
(pH — водород |
||||
I ^ |
Область |
|
|
ный |
показатель должен быть не ме |
||||||
мелкого л |
/ |
|
нее 4 и не более 12). Допустимое содер |
||||||||
§ ^ |
пест |
Ш |
|
жание растворимых |
солей и |
взвешен |
|||||
ж |
|
|
|
ных частиц приведено в табл. 6.7 Мор |
|||||||
00 |
|
|
|
||||||||
|| во |
г / f |
|
Область |
---- |
ские и озерные воды, если они удовлет |
||||||
|
крупного |
воряют указанным требованиям, можно |
|||||||||
№ |
|
песка |
|
||||||||
9 § 80 |
ч[ |
|
|
|
применять для |
производства |
бетонных |
||||
1 1 |
|
|
|
|
смесей. Болотные, торфяниковые, а так |
||||||
§|/ДО |
ОМ |
1,25 |
2,50 |
5,0 |
же |
сточные, |
загрязненные |
промыш |
|||
0 |
ленными |
отходами |
воды |
применять |
|||||||
0,10 0,50 |
|
|
|
||||||||
Размеры отверстий контрольных |
нельзя. |
|
|
|
|
||||||
|
|
|
сит, мм |
|
Качество воды определяют химиче |
||||||
Рис. 6.12. Предельные кривые грануломет |
ским анализом. В сомнительных случа |
||||||||||
ях ее пригодность проверяют опытным |
|||||||||||
|
рического состава щебня |
|
путем, сравнением показателей проч |
|
|
Т а б л и ц а 6.6 |
|||
ности образцов |
бетона |
в |
возрасте |
|
|
|
28 сут, приготовленных |
в |
равных |
Песок |
Полным остаток |
|
|
условиях на чистой и испытуемой |
нм сите № 063, % Модуль крупности |
|||||
|
по массе |
|
||||
воде. |
|
|
|
|
|
|
Добавки. Свойству бетонных сме |
Крупный |
>45 |
2,5 |
|||
сей и бетонов можно регулировать в |
Средний |
30—45 |
2,5 -2 |
|||
широких пределах с помощью доба |
Мелкий |
10—30 |
2— 1,5 |
|||
вок (табл. 6.8). К ним относятся |
Очень мелкий |
<10 |
1,5— 1,0 |
|||
поверхностно-активные |
вещества |
|
|
|
||
(гидрофильные, |
гидрофобные, воздухововлекающие), электролиты (одни |
из них ускоряют растворение минералов цемента, другие взаимодействуют с минералами цемента, образуя нерастворимые вещества, третьи понижают температуру замерзания воды затворения и т. д.), тонкомолотые добавки, которые могут проявляться как центры кристаллизации или вступать во взаимодействие с Са(ОН)2, образуя нерастворимые гидросиликаты. По воз действию на свойства бетонных смесей и бетона среди добавок выделяют регуляторы: технологических свойств бетонных смесей; структуры бетона; процессов схватывания и твердения бетонов. Могут быть и другие специаль ные добавки. Наиболее типичным представителем первой группы является сульфитно-дрожжевая бражка (сдб) — отход целлюлозно-бумажных комбинатов. Она представляет собой поверхностно-активное вещество из кальциевых солей лигно-сульфоновых кислот с примесью минеральных веществ. Сульфитно-дрожжевая бражка вводится в бетонные смеси в коли честве 0,2—0,3% от массы цемента. Это пластифицирует бетонную смесь, снижает ее водоиотребность и позволяет сократить расход цемента на 5— 7% или понизить водо-цементное отношение и увеличить прочность бетона на 10—12%.
Эффективными добавками являются суперпластификаторы, образован ные на основе меламиновой смолы или нафталин-сульфокислоты, а также модифицированной сдб. В количестве 0,2—1% от массы цемента бетонную смесь разжижают намного больше, чем сдб. Осадка конуса смеси возрастает с 1—2 до 20—24 см, что позволяет снижать водопотребность смеси более чем на 20%. При четкой организации технологии изготовления бетонных смесей можно сократить расход цемента более чем на 20% или при постоянном рас ходе цемента резко уменьшить трудоемкость уплотнения литых бетонных смесей.
Регуляторы структуры бетона, в свою очередь, делятся на воздухововле кающие, газообразующие, уплотняющие и расширяющие вещества. Из возду хововлекающих наибольшее распространение получила смола нейтрализо
ванная |
воздухововлекающая (СНВ) — абиетиновая |
смола, |
омыленная |
||
|
|
|
|
|
Т а б л и ц а 6.7 |
|
|
Максимально допустимое содержание, мг/л |
|||
|
Назначение воды |
Растворимых |
Ионов SOy |
Ионов |
Взвешенных |
|
|
солен |
|
частиц |
|
|
|
|
|
||
Для 'затворения бетонной смеси при |
|
|
|
||
изготовлении напряженных |
железобетон |
600 |
|
300 |
|
ных конструкций |
2000 |
350 |
|||
То же, |
при изготовлении |
конструкций |
2700 |
1200 |
200 |
с ненапряженной арматурой |
5000 |
||||
То же, при изготовлении неармирован- |
2700 |
3500 |
300 |
||
ных бетонных конструкций |
10 000 |
|
|
|
|
Таблица 6.8 |
|
|
|
Сокращенное |
Рекомендуемое |
Вид добавки |
Наименование добавки |
количество доба |
||
обозначение |
вок, % от массы |
|||
|
|
|
|
цемента |
Пластифицирующие |
Сульфитно-дрожжевая |
сдб |
0,15-0,3 |
|
|
бражка |
|
||
|
Мелассная упаренная пос- |
УПБ |
0,10-0,3 |
|
То же, воздухововлекающие |
ледрожжевая барда |
|||
Мылонафт |
М |
0,1—0,2 |
||
|
Пластификатор адиптино- |
ПАЩ-1 |
0,10—0,2 |
|
|
вый |
|
||
Воздухововлекающие |
Этилсиликонат натрия |
гкж-ю |
0,10—0,2 |
|
Смола |
нейтрализованная |
СНВ |
0,01-0,03 |
|
|
воздухововлекающая' |
|||
Газообразующие |
Омыленный древесный пек |
ЦНИПС-1 |
0,01—0,03 |
|
Полигидросилоксан |
ГКЖ-94 |
0,05—0,08 |
||
Уплотняющие |
Пудра |
алюминиевая |
ПАК |
0,01—0,03 |
Нитрат калия |
НК |
1,5—2,5 |
||
|
Сульфат алюминия |
СА |
1,5—2,5 |
|
Замедлители схватывания |
Хлорид железа |
ХЖ |
1,5-2,5 |
|
Сахарная патока (меласса) |
СП |
0,01—0,05 |
||
Ускорители твердения |
Метилсиликонат натрия |
ГКЖ-11 |
0,01—0,03 |
|
Сульфат натрия |
СН |
1,0—1,5 |
||
|
Нитрат |
» |
НН |
0,5— 1,0 |
Противоморозные |
Едкий |
натр |
ЕН |
0,1-0,3 |
Хлорид натрия |
ХН |
2,0—5,0 |
||
|
» |
кальция |
хк |
2,0—5,0 |
Ингибиторы |
Поташ |
|
П |
1,5—3,0 |
Нитрит натрия |
НН |
0,5— 1,0 |
||
коррозии |
Бихромат » |
БХН |
0,5—1,5 |
|
стали |
» |
калия |
БХК |
0,5—1,5 |
каустической содой. Вводят ее в количестве 0,01—0,03% от массы цемента, что способствует вовлечению в смесь до 4—5% воздуха в виде мелких пузырь ков и заметно увеличивает морозостойкость бетона.
Широко применяются кремнийорганические жидкости (ГКЖ-10, ГКЖ11, ГКЖ-94), представляющие собой водно-спиртовые растворы этил- и метилсиликата натрия. При введении их в смесь (менее 0,01% от массы цемен та) образуются мелкие пузырьки газа, что способствует повышению морозо стойкости бетона.
Из уплотняющих добавок можно назвать хлорное железо, а расширяю щих — глиноземистый цемент, сульфат алюминия. Пластифицирующие до бавки также улучшают структуру бетона.
Регуляторы схватывания и твердения делят на ускорители и замедлители. К первым относят сульфаты щелочных металлов, хлорид кальция, ко вторым — борную кислоту, сдб, буру и др.
При производстве работ зимой широко используют противоморозные до бавки. Одни понижают температуру замерзания воды и обеспечивают воз можность взаимодействия воды с минералами цемента (хлорид натрия), дру гие наряду с этим вступают в химическую реакцию с минералами цемента, ускоряют твердение и обусловливают большое выделение тепла (хлорид каль ция, нитрит-нитрат кальция).
В ряде случаев вводят добавки, чтобы уменьшить коррозию арматуры, повысить радиационную стойкость бетонов и др. Комплексные добавки, со стоящие из нескольких компонентов, обладают особенностями. Например, в ХАДИ предложены комплексные добавки, состоящие из NaOH, сдб и СНВ, т. е. из ускорителя твердения, пластификатора бетонной смеси и воздухово
влекающей составляющей. Эта добавка позволяет ускорить твердение бето на, повысить его долговечность и сократить на 10—12% расход цемента. Таким образом, применяя химические добавки, можно эффективно в широких пределах управлять свойствами бетонной смеси и бетонов, поэтому современ ная технология производства изделий немыслима без использования тех или иных добавок.
§ 6.5. ТЕХНОЛОГИЯ БЕТОННЫХ РАБОТ
Технология бетонных работ включает выбор материалов, хранение и пере работку их с целью улучшения качества, расчет состава бетонов, приготовле ние бетонной смеси и ее транспортирование к месту укладки, укладку и уплот нение (формование) бетонных смесей, обеспечение заданных условий тверде ния бетонных изделий, контроль качества затвердевших изделий.
Выбор материалов. Материалы для бетона должны соответствовать требованиям ГОСТов, СНиПов, эксплуатационным условиям работы изде лий. Материалы выбирают с учетом особенностей технологического процесса. В ряде случаев, чтобы обеспечить это соответствие, вносят коррективы в вы бор исходных материалов или в технологию производства бетонных изделий.
Расчет состава бетона. Основная цель расчета состава — определение такого соотношения составляющих, которое обеспечит требуемые свойства бетонной смеси и бетона при минимальном расходе цемента. Выбрав материа лы надлежащего качества, рассчитывают состав — расход цемента, воды, песка и щебня на 1м3 бетона. Исходными данными являются заданная марка бетона /?б и требуемая подвижность ОК или удобоукладываемость У смеси. В необходимых случаях задаются показателями морозостойкости, водонепро ницаемости и другими свойствами бетона.
Для определения ориентировочного состава бетона пользуются таблица ми И. М. Френкеля, А. И. Авакова и др. Более точно состав тяжелых бетонов рассчитывают по методу абсолютных объемов (разработан проф. Б. Г Скрамтаевым), который сводится к решению следующих четырех урав нений с четырьмя неизвестными — расход воды В (л), цемента Ц (кг), песка П (кг) и щебня Щ (кг):
1. Зависимость прочности бетона от его структуры и активности цемента
R6 = A,A2k ( U / B - c ) R n.
Решая это уравнение, определяют
В |
^ 1 ^ 2 bRц |
И |
R Q -f- А | A<i k c R n |
Коэффициенты /г, с, Л,, А2 определяют по табл. 6.3—6.5. |
подвижности, |
2. Зависимость водопотребности бетонной смеси от ее |
удобоукладываемости и свойств исходных материалов (рис. 6.13), по которой определяют расход воды на 1 м3 бетонной смеси. Зная B/U и расход воды, можно вычислить расход цемента на 1 м3 бетона: U = В:В/Ц.
3. Сумма абсолютных объемов исходных материалов в 1 м3 бетона близка
к 1000 л, поэтому, пренебрегая |
содержанием воздуха в смеси, принимают |
|||
Ц |
, в |
, П |
, Щ |
|
Yu. |
+ — |
+■ |
+ - |
■= 1000, |
YB |
YM |
|
где уц, ув, Yn* Yin — плотности цемента, воды, песка и щебня.
4. Абсолютный объем пустот в щебне равен абсолютному объему раствор ной составляющей с некоторым избытком, т. е.
J L + A + J L - J L y
Y „ |
Л’ || |
Y u |
Y о т |
где уоГ)1ц— объемная масса |
щебня; |
V — пустотность щебня в относи |
тельных величинах; а — коэффициент раздвижки зерен щебня. Для жестких бетонных смесей а = 1,054-1,10.
Решая совместно третье и четвертое уравнения, получают формулы для определения расхода щебня и песка:
Щ=____L000___ .
щ |
V |
1 ’ |
|
----- а Н------ |
|
|
Vo6m |
Vm |
Рассчитанный состав бетона уточняют экспериментальным путем, опреде ляя в пробных замесах подвижность (удобоукладываемость) смеси, а также в установленные сроки прочность стандартных бетонных образцов, изготов ленных из рассчитанной смеси.
В производственных условиях пользуются полевым составом б е т о н а , в котором расход материалов на 1 м3 бетона дается с учетом их влажности. Принято также определять номинальный состав бетона — отношение мас совых или объемных частей песка и щебня (гравия) к одной массовой или объемной единице цемента с указанием водо-цементного отношения. Напри мер, отношение цемент песок щебень = //;/7:/Д= 1:2:4 при В / Ц = 0,6.
При использовании химических добавок и применении других специаль ных мероприятий в технологии бетона приведенные уравнения уточняются (главным образом, коэффициенты), однако принцип расчета состава бетона не изменяется.
Приготовление бетонной смеси. Бетонные смеси готбвят на бетонных за водах, имеющих склады материалов, бетоносмесительные установки и под собные цехи.
При сравнительно небольших объемах работ используют передвижные
смесительные установки. |
|
|
|
|
|
|
а) |
d) |
|
|
|
|
|
|
* 1 8 0 |
|
|
|
|
|
|
%%140 V |
|
|
|
|
|
|
20 |
40 # 60 |
80 |
100 |
120 140 |
|
|
Удобоукладываемостьnoтехническому |
|||||
|
; |
, вискозиметруl9c |
, |
, |
||
2' 4 6 8 10 12 14 |
IQ |
20, 30 |
iM |
50 |
SO, |
70 |
Осадкаконуса,см |
Удобоукладываемость no способу |
|
||||
|
В.Г. Скрамтаева,с |
|
|
Рис. 6.13. Зависимость водопотребмости бетонной смеси, изготовленной с применением порт ландцемента, песка средней крупности (водбпотребность 7%) и гравия:
•«•.и,шни крупность |
а — подвижные смеси; б |
жесткие смеси; |
4 — то же, 80 |
мм. С увеличением |
||||
гриппя 10 мм; 2 |
— то |
же, |
20 |
мм; ,4 |
то же. *10 мм; |
|||
(уменынснн* м) |
полово! ребностн |
песка |
на |
1% |
расход поды подрастает |
(уменьшается) |
на 5 л |
Преимущественное применение получили установки, работающие цикли чески, в которых отдельные порции бетонной смеси последовательно проходят все стадии дозирования, перемешивания и выгрузки. Подготовленные мате риалы подают в бункера, откуда они поступают в весовые (реже объемные) дозаторы для отвешивания в необходимом количестве на замес. Затем мате риалы одного замеса поступают в мешалку барабанного или лопастного типа, перемешиваются, и после этого смесь выгружается в транспортные средства. На крупных стройках обычно работают установки непрерывного действия как наиболее производительные.
Управление современными бетоносмесительными установками, как
правило, |
автоматизировано. |
Пели |
п роительный объект значительно удален от бетонного завода |
и сметI• |
I время перевозки может утратить свои свойства, на заводе в дозиро- |
вочнеш установке допускается готовить сухую смесь из цемента, песка и щеб ня, затем перевозить ее к месту укладки и смешивать с водой в обычной бето номешалке. 11погда целесообразно дозирование воды и перемешивание смеси осуществлять в пути в автобстономешалках.
Допирование. Расход минеральных материалов на один замес бетономе
шалки |
МУлам |
|
|
м = |
(1 + UP). |
||
1000 |
|||
|
|
где М — количество исходных минеральных материалов на 1м3 бетона, кг; U3|1М— объем бетономешалки, л; W — влажность материалов в относитель ных величинах; р — коэффициент выхода бетонной смеси;
юоо |
// |
|
Р |
|
|
You |
"V |
|
где Щ, Я, Ц — расход щебня, песка, |
цемента, |
кг на 1 м3 бетона; у0|Ц, |
7оц» Yo„ — объмная насыпная масса |
щебня, |
цемента, песка, кг/м1' |
Коэффициент выхода бетона всегда меньше единицы вследствие заполне ния пустот между зернами более мелким материалом и равняется 0,60--0,65.
Расход воды на один замес
w " 11
где В — расход воды на 1 м3 бетона; lV"m, Wu— влажность щебня и песка в относительных величинах; Я, Щ — расход песка и щебня на замес бетоно мешалки, кг.
Цемент и воду дозируют только по массе с точностью до ± 1%, а заполни тели допускается дозировать по объему с точностью до ±3%. На современ ных бетонных заводах материалы дозируют с помощью автоматических весо вых дозаторов циклического или непрерывного действия. Воду дозируют с учетом влажности песка и щебня.
Перемешиванием бетонной смеси достигается равномерное распределсицо компонентов, смачивание цемента, песка и щебня водой и равномерное обво лакивание зерен песка и щебня цементным тестом. От степени смешения зави сят свойства бетона, в том числе прочность (рис. 6.14). На количество пере мешивания влияют тип бетономешалки, длительность перемешивания, степень и порядок загрузки материалов в мешалку.
ЧаI |
|
Подвижные бетонные смеси на плот |
||||
|
ном щебне и песке хорошо перемеши |
|||||
|
ваются |
в бетономешалках свободного |
||||
|
перемешивания, |
представляющих |
со |
|||
|
|
бой вращающиеся барабаны, на внут |
||||
|
|
ренних стенках которых укреплены ло |
||||
|
|
пасти. Жесткие смеси следует переме |
||||
1 |
|
шивать в бетономешалках принудитель |
||||
|
ного действия, а также в вибромешаЛ- |
|||||
a Степень смешения смеси |
ках. В ряде случаев целесообразно под |
|||||
(длительность перемешивания) |
вергать |
виброактивации |
раствор |
и |
||
|
|
цементное тесто. |
|
|
|
|
Рис. 6.14. Зависимость прочности бе |
От свойств и состава смеси, типа |
|||||
тона от |
длительности перемешивания |
бетономешалки |
и размеров смеситель |
|||
|
смеси |
ного барабана |
зависит |
оптимальное |
||
|
|
время перемешивания (табл. 6.9). |
|
|||
Продолжительность перемешивания увеличивается с уменьшением круп |
||||||
ности |
заполнителей. Если перемешивание |
будет |
меньше |
оптимального |
на 10%, прочность бетона заметно снизится. При более длительном переме шивании качество бетона несколько улучшается, но уменьшается производи тельность бетономешалок. Бетономешалка должна загружаться строго в сот ответствии с вместимостью барабана. Не допускается перемешивание смеси в большем объеме, чем это предусмотрено техническим паспортом бетономе шалки.
Для получения удовлетворительной смеси вначале вводят щебень и часть воды, после частичного перемешивания подают в бетономешалку цемент, остальное количество воды и песок. Растворимые в воде добавки подают вместе с водой.
При транспортировании бетонной смеси необходимо, чтобы она сохраня ла свою однородность. Допускается снижение подвижности смеси до 30%. Смесь транспортируют автомобилями-самосвалами, вагонетками, бетонона сосами, бадьями и др. В практике дорожного строительства ее обычно перево зят автомобилями-самосвалами. Емкости транспортных средств должны быть чистыми и не допускать в процессе перевозки потерь раствора и цементного молока. Продолжительность транспортирования смеси должна быть не более 30 мин при температуре 20—30°С, 60 мин при 10—20°С и 120 мин при 5— 10°С.
Укладка и уплотнение бетонной смеси. Укладка включает распределение, уплотнение смеси и отделку поверхности покрытия. Перед уклаДкой смеси проверяют правильность установки опалубки и арматуры в ней. Бетонную смесь в опалубке распределяют, как правило, с помощью бетоноукладчиков
слотковыми (ленточными), бункерными или шнековыми распределителями.
Вмонолитных конструкциях подвижную бетонную смесь уплотняют виб рацией. При вибрации (частота колебаний 50—20 Гц, амплитуда 0,1—0,8 мм)
|
|
|
|
Таблица 6.9 |
|
Оптимальное время перемешивания, мин. при вместимости бето |
|||
Подвижность бетонной смеси |
номешалки свободного перемешивания, л, более |
|||
|
|
- |
|
|
|
<425 |
< 1200 |
<2400 |
<4500 |
Осадка конуса более 5 см |
1 |
1— 1,5 |
2 |
3 |
Осадка конуса менее 5 см |
1 |
2 |
3 |
4 |
бетонная смесь тиксотропно разжижается и приобретает текучесть. Разжи женная смесь легко заполняет формы, зерна щебня и песка располагаются наиболее плотно, а крупные пузырьки воздуха вытесняются.
Для виброуплотнения применяют поверхностные и глубинные вибраторы (рис. 6.15). Поверхностные вибраторы устанавливают на уплотняемую смесь и через площадку сообщают ей колебания; ими уплотняют бетонные плиты; полы и т. д. Глубинные вибраторы и вибробулавы, полностью погружаясь в смесь, передают колебательные движения во все стороны. Их применяют для уплотнения бетонной смеси армированных и неармированных конструк ций, плит фундаментов, балок и др. Об эффективности виброуплотнения судят по коэффициенту уплотнения — отношению фактической объемной массы уплотненной смеси к ее теоретической объемной массе. Коэффициент уплотнения равен 0,95—0,98.
Режим виброуплотнения зависит от свойств смеси и в основном от ее удобоукладываемости, характеризует ся интенсивностью, длительностью, а также характером и формой колеба тельных движений.
Интенсивность виброуплотнения
и = о т л 2п\
где А — амплитуда |
колебаний; |
п — частота колебаний. |
|
Чем более жесткие бетонные смеси с низким водо-цементным отношением,
тем |
больше интенсивность вибрирова |
||
ния. |
Обычно |
она |
колеблется от 30 |
до 2800 см2/с3 |
(рис. |
6.16). |
Для каждой бетонной смеси име ются оптимальная амплитуда и частота колебаний. С ростом показателя жест кости, крупности зерен щебня, повыше нием их шероховатости, угловатости необходимо амплитуду колебаний уве личивать. Для бетонных смесей с пре дельной крупностью 40 мм она находит ся в пределах 0,3—0,6 мм, для мелко зернистых смесей уменьшается до 0,15 мм. Повышение амплитуды сверх указанных пределов может быть эффек тивно использовано лишь при создании дополнительного пригруза (до 25 г/см2) на поверхности уплотняемой смеси. Для обычных смесей частота вибрации находится в пределах 2800—6000 кол/мин. Повышение частоты целесо образно для мелкозернистых смесей. Высокочастотное вибрирование повы шает производительность, поскольку ускоряет тиксотропное разжижение смесей и улучшает качество поверхно сти изделий.
Рис. 6.15. Вибраторы:
а — поверхностный; б и в — глубинные; / — двигатель; 2 — гибкий вал; 3 — металлическая
площадка; 4 — вибрирующий наконечник
Рис. 6.16. График для выбора различных значений амплитуды и частоты гармони ческих колебаний при заданной интен сивности вибрации:
/ — интенсивность |
- |
колебаний |
И = 30 |
см2/с3; |
2 — |
И = 80 см2/с3; 3 |
И = 300 |
см2/с3; |
4 - И = |
1250 |
|
см2/с3; 5 — И = 280 см2/с3 |
|
Заштрихованная часть рисунка соответствует опти мальным режимам вибрирования
Для каждой бетонной смеси при принятых параметрах вибрирования устанавливают оптимальную продолжительность виброуплотнения. От недо статочного вибрирования смесь может уплотняться не полностью, вследствие чего снижается качество бетона. Чрезмерно длительное уплотнение подвиж ных смесей с большим водосодержанием вызывает их расслоение. Вибро уплотнение заканчивают, если бетонная смесь уже не оседает и образуется горизонтальная поверхность, на которой выступает цементное молоко. Продолжительность уплотнения бетонных смесей
где У — удобоукладываемость смеси, с; Ист— интенсивность вибрации, при которой определялась У в лабораторных условиях; И — интенсивность вибрации в производственных условиях.
Виброуплотнение наиболее эффективно, если оно начато через некоторое время после приготовления бетонной смеси. Обычно это время равно 40 мин. Излишняя выдержка бетонной смеси нежелательна, так как может привести к ухудшению ее технологических свойств. Целесообразно через 1—2 ч повто рить уплотнение бетонной смеси поверхностными вибраторами высокой часто ты. При этом разрушается первоначально сложившаяся дефектная структура цементного камня, вследствие чего значительно уменьшаются внутренние напряжения и на 15—20% повышается прочность бетонов. Целесообразно разночастотное виброуплотнение, например сочетание 1500 и 4500 кол/мин с амплитудами колебаний соответственно 1 и 0,4 мм.
Полезно также применять последовательно два режима: вначале низко частотный, воздействующий на жесткий скелет щебня, затем высокочастот ный — на раствор.
Наиболее благоприятно сочетание колебаний при одновременном дейст вии низкой и высокой частоты, если соотношение между частотами равно трем.
В этом случае угол сдвига фаз равен 180°, максимумы и минимумы со ставляющих колебаний совпадают, размах колебаний имеет максимальное значение.
Для увеличения уплотнения цементного камня в бетоне целесообразно пластичную смесь вакуумировать при помощи вакуумщитов Или вакуумопалубок, которые из уплотненной смеси извлекают воздух и избыточную воду. При вакуумировании повышается прочность и мор0зосТОйкость бетона, увеличивается его износостойкость и уменьшается Упадка, а также ускоря ется твердение бетона в раннем возрасте. После вакууМоо^работки хорошие результаты дает повторное виброуплотнение поверхностными вибраторами,
что способствует устранению капилляров, образоВав1иИХся при отсосе воздуха и воды из бетона.
Твердение бетона и уход за ним. Бетон набирает прочность постепенно по мере твердения цементного камня. Наибольшая скор0сть нарастания проч ности бетона наблюдается в ранние периоды тверденИя и далее постепенно уменьшается.
Скорость твердения в значительной степени за^Исит от температуры среды (табл. 6.10).
Прирост прочности бетона значительно ускоряете** с повышением темпе ратуры среды и максимальной влажности.
Во влажной среде бетон приобретает значительн0 боЛьШую прочность,
чем на воздухе. |
При испарении влаги из бетона его |
оДенИе практически |
прекращается. |
’ |
^ |
Возраст бето- |
|
Относительная |
прочность бетона при температурах твердения. °с |
|
|
на, сут |
5 |
К) |
15 |
25 |
50 |
|
|||||
3 |
0 ,1 5 |
0 ,2 0 |
0 ,3 0 |
0 ,3 7 |
0 ,4 5 |
5 |
0 ,2 5 |
0 ,3 2 |
0 ,4 5 |
0 ,5 4 |
0 ,6 0 |
7 |
0 ,3 5 |
0 ,4 4 |
0 ,6 0 |
0 ,7 0 |
0 ,7 2 |
15 |
0 ,5 5 |
0 ,6 5 |
0 ,8 0 |
0 ,8 5 |
0 ,8 5 |
2 8 |
0 ,8 0 |
0 ,9 2 |
1,00 |
1,05 |
1,10 |
Уход за бетоном включает комплекс мероприятий, обеспечивающих благо; приятные условия твердения уложенной и уплотненной смеси (необходимая влажность и температура), а также способов, предохраняющих бетон от повреждения в раннем возрасте.
Уход организуют немедленно после укладки и уплотнения смеси. Уход за свежеуложенным бетоном обычно осуществляют путем покрытия его поверх ности пленкообразующими веществами. Эти вещества образуют водонепро ницаемую пленку, надежно защищающую поверхность бетона от испарения воды, гидрофобизируют и закупоривают поры поверхности, что увеличивает долговечность бетонного покрытия. В качестве пленкообразующих веществ применяют битумные эмульсии, жидкие и разжиженные битумы и др. Распре деление пленкообразующих материалов производится обычно в два приема. Первый слой наносят немедленно после окончательного уплотнения и отдел ки поверхности. Эффективно укрывать уплотняемую бетонную смесь полиэти леновой пленкой.
Контроль качества. Хорошо организованный контроль качества бетон ных работ — важнейшее условие получения бетонов и бетонных изделий за данных свойств, повышения их долговечности и снижения стоимости строи тельства. Контроль осуществляет лаборатория, он состоит в испытании мате риалов для бетона, назначении его состава, периодической проверке качества смеси и бетона, повседневной проверке качества работ на всех этапах. При контроле качества материалов и бетонов руководствуются ГОСТами
итехническими правилами.
Впроцессе приготовления смеси следует контролировать дозирование
материалов в бетономешалку, особенно воды и цемента. Необходимо система тически контролировать принятый режим перемешивания смеси (продолжи тельность, степень заполнения и скорость вращения бетономешалки), опре делять ее подвижность, а иногда и состав, объемную массу в уплотненном состоянии и коэффициент выхода бетона. Особенно тщательно контролируют условия твердения бетона, в первую очередь влажность и температуру. Если твердение проходит в неконтролируемых случайных условиях, то их свойства также случайны и, как правило, не соответствуют заданным требованиям.
Контроль прочности бетона осуществляют путем периодического отбора проб смеси данной серии замесов и изготовления из нее контрольных образ цов кубов или балок, уплотняемых тем же способом, как и бетон в конструк циях; образцы бетона должны твердеть в таких же условиях, что и конструк ции. Испытывают образцы в возрасте 28 сут или другие установленные сроки. Иногда фактическую прочность бетона определяют по образцам, взятым из конструкций путем высверливания цилиндров диаметром и высотой 10
20 см.
Распространены склерометрические, акустические, ультразвуковые мето ды определения прочности. Результаты текущего контроля заносят в специальные лабораторные журналы.

Температура окружающего |
Простой раствор |
Сложный1 |
раствор |
|
|
|
|
||
воздуха при бетонировании, |
Содержание в растворе |
Содержание в растворе |
Содержание в растворе |
|
°С |
|
|||
|
СаС12, % |
СаС12, % |
NaCI % |
|
1 |
сл |
3 - 6 |
2—4 |
1—2 |
0 •1* |
||||
|
1 |
|
|
|
—5ч----- 10 |
— |
4 - 6 |
2 |
|
— 104----- 15 |
— |
6 - 1 0 |
2—5 |
туру 50—70°С, что позволяет в течение 2—3 сут достичь проектной прочно сти бетона.
Электроподогрев бетонной смеси в элементах конструкций основан на том, что при пропускании через бетонную смесь переменного тока температу ра бетона повышается. При электроподогреве на поверхности свежеуложенной бетонной смеси укрепляют стальные плитки-электроды, через которые и пропускают электрический ток. Роль электродов могут выполнять стальные стержни железобетонных элементов конструкций. Необходимо иметь в виду, что густоармированные части могут перегреваться, в дальнейшем вызывая снижение прочности бетона из-за быстрого испарения в этих участках воды. Поэтому электроподогрев железобетонных элементов необходимо вести при пониженных напряжениях тока (50—100 В).
Скорость повышения температуры во всех случаях подогрева бетона в конструкциях должна быть небольшой (не более 5°С в час), а максимальная температура при электроподогреве — не более 60°С. При бетонировании кон струкций с модулем поберхности меньше 5 электроподогрев применять не рекомендуется.
Подогрев бетона теплым воздухом в тепляках применяется при небольших объемах работ. Тепляки устраивают из фанеры, брезента и других материа лов с отоплением обычными или электрическими отражательными печами или водяными калориферами.
Холодный бетон. Устройство дорожных и аэродромных покрытий при от рицательных температурах методом холодного бетона (без подогрева мате риалов и бетона) нашло значительное распространение в последние годы и, в частности, в суровых климатических условиях. Этот способ основан на введении в бетонную смесь больших добавок хлористого кальция и хлористо го натрия, что резко понижает температуру замерзания воды в бетонной смеси.
Кроме того, эти соли значительно пластифицируют бетонную смесь, позволяя укладывать ее при отрицательных температурах воздуха. Хло ристый кальций, в свою очередь, является ускорителем твердения.
Нарастание прочности бетона с добавками хлористых солей при отрица тельных температурах происходит относительно медленно: за 7 сут — до 30%, за 28 сут — до 50—60% и за 90 сут — до 90—100% от проектной
марки бетона.
Соли вводят в бетонную смесь в виде водных растворов, концентрация которых определяется по табл. 6.11. Раствор СаС12 допускается к примене нию с концентрацией не более 6%, так как СаС12 вызывает быстрое загусте-
вание бетонной смеси.
Холодную бетонную смесь изготовляют и укладывают только при отри цательной температуре (однако не ниже —20°С) вследствие быстрого загустевания ее при положительной температуре. Уложенная и .уплотненная смесь должна быть защищена способом термоса. Изготовление густоарми-
рованных железобетонных конструкций с применением холодного бетона не рекомендуется, так как хлористые соли вызывают коррозию стальной арматуры.
Свойства холодного бетона несколько хуже по сравнению с бетонами, твердеющими в обычных условиях. При равной прочности холодные бетоны обладают меньшей долговечностью, морозостойкостью, повышенной усадкой и хрупкостью.
§ 6.7. ДОРОЖНЫЙ ЦЕМЕНТОБЕТОН
Дорожный цементобетон — разновидность тяжелого бетона — приме няют для устройства покрытий на автомобильных дорогах, аэродромах, дорогах промышленных предприятий, городских улицах и проездах. Бетон дорожных покрытий работает в неблагоприятных условиях, так как под вергается не только воздействию транспортных средств, но и атмосферных осадков, в особенности многократно повторяющемуся увлажнению и высы ханию, замораживанию и оттаиванию, поэтому к нему предъявляют повы шенные требования по прочности, морозо- и износостойкости.
В дорожном строительстве применяют также песчаные бетоны, в которых заполнителем используют крупнозернистые пески с предельной крупностью 5 мм, и карбонатные бетоны (щебень и песок карбонатных пород). Эти бетоны дешевле обычных, поскольку для их изготовления преимущественно идут местные материалы, но при определенных условиях они обладают повышен ной деформативностью, морозостойкостью и др. Эти бетоны разработаны
вСоюздорнии.
Всоответствии с стандартами на дорожный бетон выбор и значение
марок по показателю прочности бетона должны соответствовать требовани ям (табл. 6.12). Ведущим показателем прочности дорожного бетона являет ся предел прочности при изгибе. Допускается снижение на одну марку проч ности бетона при сжатии, если обеспечена прочность при изгибе. Для авто мобильных дорог I и И категорий применяют бетоны соответственно марок 500 и 400.
Марка дорожного бетона по морозостойкости должна быть не ниже Мрз 100 (районы средней полосы СССР) и Мрз 200 (северные районы). Для устройства оснований разрешается бетон Мрз 50. Морозостойкость бе тона обеспечивается применением морозостойкого щебня, специального порт ландцемента и созданием однородной структуры при оптимальном расходе цемента и минимальном водо-цементном отношении, а также введением в
смесь гидрофобных и воздухововлекающих добавок. Рекомендуется прини мать водо-цементное отношение не более 0,5 для верхних слоев и 0,6 — для нижних слоев двухслойных покрытий.
|
|
|
|
|
|
|
Таблица 6.12 |
Дорожные покрытия |
|
|
|
Марки бетона по пределу прочности, МПа |
|||
|
на растяжение при изгибе |
|
при сжатии |
||||
|
|
|
|
||||
Однослойные и верхний слой |
|
|
|
|
|
|
|
двухслойных покрытий |
4,0; |
4,5; |
5,0 |
и 5,5 |
30; 35; 40 и 50 |
||
Нижний |
слой двухслойных |
|
|
|
|
|
|
покрытий |
и основания |
3,5; |
4,0; |
4,5 |
|
25; |
30 и 35 |
Основания усовершенство |
|
|
|
|
|
|
|
ванных капитальных покрытий |
2,0; |
2,5; |
3,0 |
и 3,5 |
10; |
15; 20 и 25 |
Важным показателем дорожного бетона является износостойкость, ко торая зависит от структуры и состава верхнего слоя дорожной плиты. Из нос увеличивается при использовании подвижных бетонных смесей с боль шим водо-цементным отношением, так как после их уплотнения на, по верхности образуется слой недостаточно прочного раствора. При твердении бетона в условиях низких температур и недостаточной влажности среды износостойкость также снижается.
Важнейшим свойством дорожного бетона является деформативность, характеризующая способность бетона деформироваться под действием на гружения и температуры. Эти свойства оцениваются показателями модуля упругости (деформации), коэффициента линейного температурного расшире ния, коэффициента Пуассона, используемыми при расчете бетонных покры тий и оснований.
Модули упругости обычных бетонов изменяются от 2 • 104 МПа (марка бетона 20 по изгибу) до 4 • 104 МПа (марка бетона 55 по изгибу). Соответс твенно для песчаных бетонов модули упругости изменяются в пределах (1,5ч-3,0) • 104 МПа, для карбонатных бетонов — (1,64-3,2) • 10* МПа. Коэффициент Пуассона находится в пределах 0,18 (обычные бетоны) — 0,22 (песчаные и карбонатные бетоны). Коэффициент линейного темпера турного расширения изменяется от 4,1 • 10_6 до 10,0 • 10_6 на1°С.
В технологии дорожных бетонов важно учитывать усадку, которая при неблагоприятных условиях может достигать 0,6 мм/м.
В связи с широким применением рельсовых комплектов машин дорожный бетон в свежёуложенном состоянии после укладки не должен деформи роваться под действием собственной массы, обеспечивать устойчивость кром ки бетонной плиты. Деформативность свежеуложенного бетона снижается с уменьшением водосодержания, увеличением количества песка и воздуха и бетонной смеси. В этом случае используют бетонные смеси с пониженным содержанием щебня и стремятся, чтобы в смеси вовлеченный воздух был в пределах 4—6%. Это также способствует увеличению морозостойкости бетона.
Материалы для приго1ч)вления дорожного бетона должны быть высо кого качества. Используют дорожный портландцемент, обычный, пластифи цированный и гидрофобный марки не менее 400, а для оснований не ниже 300. Цемент не должен содержать молотых минеральных добавок. Минерало гический состав: 50—55% алита, 20—25 белита, 20—25 алюмоферрита, не более 10% алюмината. Цементы такого состава позволяют получить с вы соким пределом прочности при изгибе, хорошей выносливостью, деформативной способностью и морозостойкостью. Не разрешаются шлакопортландцементы и пуццолановые портландцементы вследствие их пониженной мо
розостойкости.
Песок для дорожного цементобетона используется преимущественно при родный крупно-, средне- и мелкозернистый, иногда искусственный песок, высевки, причем щебень и песок одного минералогического состава. При менение мелкозернистых и очень мелкозернистых песков возможно, но с до бавкой крупнозернистых высевок. Особое внимание обращают на чистоту песка; пылевато-глинистых примесей не должно превышать 2%, органи ческие примеси не допускаются. Щебень изготавливают из прочных пород, морозостойкость должна быть не ниже марки по морозостойкости дорожных цементобетонов. Щебень применяют с оптимальным зерновым составом, а предельная крупность щебня: 40 мм для однослойного и нижнего слоя двухслойного покрытия и 20 мм для верхнего слоя двухслойного покрытия.
Гравий применяется только для бетонов нижних слоев покрытий. Пылева то-глинистых примесей в щебне и гравии не должно быть более 1%. Для до-
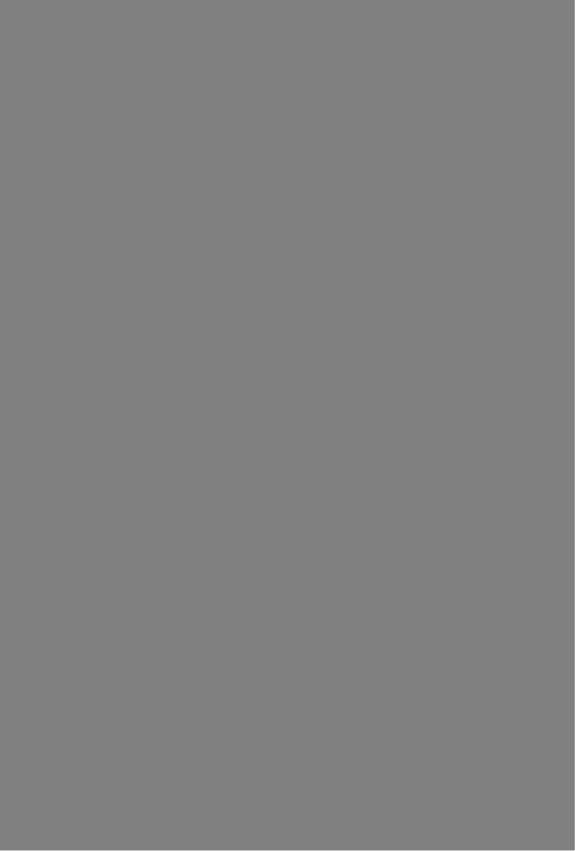
Гидротехнический бетон для гидротехнических и подземных сооружений, дорожных труб, в мостостроении должен быть плотным, устойчивым против воздействия проточных вод, а в ряде случаев и агрессивной среды. Для приготовления таких бетонов применяют пуццолановый и шлакопортландцемент, портландцемента с умеренной экзотермией, а в необходимых случаях и сульфатостойкий цемент в количестве не менее 200 кг на 1 м3 Добавки тонкомолотых кварцевых песков, доменного гранулированного шлака по вышают устойчивость бетона, снижают выделение тепла при твердении и усадку. Для улучшения технологических свойств бетонной смеси и в первую очередь уменьшения водопотребности в нее вводят пластифицирующие добавки.
Гидротехнический бетон делят на марки: по прочности 75, 100, 150, 200, 250, 300, 400, 500; по морозостойкости Мрз50 — МрзЗОО; по водонепрони цаемости В-2, В-4, В-8. Марки гидротехнического бетона определяют в 180-суточном возрасте.
Жароупорный бетон применяют для устройства сооружений, подверга ющихся действию высоких температур (дымовые трубы, футеровка печей и пр.). В качестве вяжущих используют глиноземистый, а при температурах до 1200°С портландцемент с тонкомолотыми добавками шамота, вулка нических пород, кварца. Эти добавки связывают свободную известь, кото рая выделяется при разложении гидросиликатов кальция в условиях высоких температур. Свободная известь опасна тем, что, реагируя с водой, увели чивается в объеме и разрушает бетон. В качестве щебня служат дробленые материалу из металлургических шлаков, огнеупорного шамотного кирпича и др. Предел прочности при сжатии от 7,5 до 25 МПа, водопоглощение 10—20%, объемная масса 1700—2000 кг/м3
Цветные бетоны получают путем введения в смесь щелоче^ и свето
стойких пигментов |
до |
8—10% от массы цемента |
(охры, |
умбры, сурика |
и др.) или применения |
цветных цементов. |
целей |
в строительстве |
|
Цветные бетоны |
используют для декоративных |
зданий, устройства переходных дорожек, разделительных полос на дорож ных покрытиях.
Особо тяжелые бетоны для защиты от радиоактивных лучей (гаммалучей, нейтронного излучения) изготавливают с введением щебня из барита, железной руды, лимонита, обрезков арматурного железа, металлической стружки и др. х
В тяжелых (или гидратных) бетонах в качестве вяжущего служат порт ландцемента с повышенным содержанием трехкальциевого алюмината и сульфата кальция с добавками трепела, диатомита (для предупреждения от самопроизвольного разрушения). Реже применяют глиноземистый, а иног да расширяющийся и безусадочный цементы. Прочность и долговечность особо тяжелых бетонов (гидратных) такие же, как и обычных бетонов.
Кислотоупорный бетон приготавливают из смеси кислотостойких мате риалов (кварцевого щебня, кварцевого песка и молотого кремнеземистого материала), затворенных на жидком стекле, с добавкой 10—15% кремне фтористого натрия. Ориентировочный состав кислотоупорного бетона: ще бень— 2 части, песок— 1, пылеватый наполнитель — 1, жидкое стекло — 0,5—0,7 части и кремнефтористый натрий 10—15% от жидкого стекла (по массе). Твердение такой смеси должно протекать в сухой и теплой среде, прочность бетона достигает до 15 МПа. Из кислотоупорного бетона изго тавливают элементы конструкций, подвергающихся воздействию кислот (за исключением плавиковой).
Бетоны высокой прочности (М-600 и выше) и морозостойкости (МрзЗОО и более) получают на основе портландцемента высокой активности, промы того песка и щебня с водо-цементным отношением менее 0,4. В морозостой ких бетонах рекомендуется использовать сульфатостойкий цемент. Однако для укладки бетонных смесей в этом случае необходимо интенсивное вибриро вание с пригрузом. Значительно облегчают уплотнение смесей суперплас тификаторы. Высокопрочные бетоны позволяют уменьшить материалоем кость конструкций — сократить объем бетона до 25%, а до 15—20% —
расход арматуры.
Бетонополимер — композиционный материал, в котором силикатная мат рица совмещена с органическим полимером. Технология изготовления бето нополимерных изделий включает их высушивание, вакуумирование и про питку мономером (стирол, метилметакрилат и др.), который потом полимеризуется. В этом случае прочность при сжатии возрастает в 3—4 раза, при растяжении — в 7—8 раз, а морозостойкость в 10 раз и более. Из этого мате риала изготовляют некоторые трубы, а также изделия, эксплуатирующиеся в агрессивных средах.
Дисперсно-армированный бетон (фибробетон) — композиционный ма териал, упрочненный волокнами минеральными (из бесщелочного стекла, базальта), металлическими, синтетическими (капроновыми). В этом случае повышается прочность при сжатии в 1,5—2 раза, при растяжении в 4—5 раз, резко возрастает трещиностойкость. Имеется опыт использования фибробетона в дорожных и аэродромных плитах, трубах, плитах-оболочках, кон струкциях туннелей.#
§ 6.9. ЛЕГКИЕ БЕТОНЫ
Бетоны, обладающие малой объемной массой (500—1800 кг/м3), на зывают легкими. Их прочность от 2,5 до 50 МПа. Из легких бетонов строят стены, перекрытия. Они могут быть без арматуры и армированные, с пористыми заполнителями, крупнозернистые (беспесчаные) и особо легкие ячеистые бетоны — пено- и газобетоны с объемной массой менее 600 кг/м3
|
|
|
|
|
|
|
|
В зависимости от назначения легкие |
|||||
|
|
|
|
|
|
|
бетоны |
бывают |
|
теплоизоляционные |
|||
|
|
|
|
|
|
|
(объемная масса менее 600 кг/м3, |
||||||
|
|
|
|
|
/ 7 / |
|
теплопроводность до 0,2 Вт/(м °С), |
||||||
I, |
|
|
|
|
|
конструктивные |
(объемная |
масса |
|||||
|
|
|
|
|
|
1400—1800 |
кг/м3, марка прочности — |
||||||
|
|
|
^ |
J>2 |
|
не |
менее 50, морозостойкость — Мрз |
||||||
Si |
|
|
|
|
15) |
и |
конструктивно-теплоизоляцион |
||||||
|
|
|
|
|
|
ные, в которых совмещаются свойства |
|||||||
£ ^ |
|
|
|
|
|
|
предыдущих |
видов |
легких |
бетонов. |
|||
|
|
|
|
|
|
|
|
Производство |
легких бетонов рас |
||||
|
|
|
|
|
5 |
|
ширяется в связи с тем, что они облада |
||||||
|
|
|
|
|
|
|
ют |
высоким |
коэффициентом |
конструк |
|||
|
|
|
|
|
|
|
тивного качества и хорошими изоля |
||||||
|
_ |
|
1,5 |
. 3,0 |
05 |
|
ционными свойствами. |
|
|||||
|
Прочность раствора при раст я |
|
Для |
приготовления легких бетонов |
|||||||||
|
|
жении , МПа |
|
|
используют пористый щебень и песок. |
||||||||
Рис. 6.20. Зависимость прочности бетона |
Щебень готовят из пористых горных |
||||||||||||
от прочности |
раствора и заполнителя: |
пород (пемза/вуЛканические туфы, ра |
|||||||||||
/ — прочность щебня при |
растяжении |
/?3 = 8,8 |
МПа; |
кушечник и др.), искусственных мате |
|||||||||
2 — то |
же. |
/?3 = 4,4 |
МПа; |
3 — то же, |
/?3 = 2,6 |
МПа; |
|||||||
4 — то |
же, |
6 — то же, /?3= 1,2 МПа |
/?3 = 4 |
МПа; |
риалов |
(керамзит |
перлит, |
вермику- |
|||||
/?3 = 0,5 |
МПл; |
5 — то же, |
|
|
|
|
|
|
|
I
t |
* |
|
|
4a |
0 100 ZOO 300 <*00 |
|
|
|
боды, |
к г / м 3 |
Рис. 6.21. Зависимость прочности легкого бетона и коэффициента выхода смеси от расхода воды
лит и др) и отходов промышленности (шлаковая пемза, термозит, пористые шлаки). Объемная масса этих заполнителей 300—1000 кг/м3 и прочность при сжатии 1—20 МПа.
Прочность легких бетонов лимитируется прочностью щебня (рис. 6.20). В этих бетонах недостаточно эффективно используется цемент. В бетонных смесях на пористом щебне большая часть воды отсасывается в поры щебня, поэтому они малоподвижны. Это вызывает увеличение расхода цемента на 1 м3 бетона, следовательно, возрастают объемная масса и теплопровод ность бетонов, что нежелательно. В связи с этим легкие бетоны целесообразно готовить из жестких смесей, в состав которых входят легкий щебень повы
шенного качества |
(керамзит, |
термозит), |
оптимального зернового состава |
|||
и минимальной пустотности, а также цементы высоких марок: |
|
|||||
Марка |
легкого |
бетона |
Z35 |
Z50—75 |
100— 150> |
200 |
« |
цемента |
|
200—300 |
300 |
400—500> |
500 |
Важным условием технологии легкого бетона является установление оптимального расхода воды, который находят по наибольшей прочности, для чего испытывают три — пять серий бетонных образцов с разным со держанием воды (рис. 6.21). В первом случае бетонную смесь трудно уп лотнить, а во втором она расслаивается.
Введение небольших добавок поверхностно-активных веществ повышает связность бетонной смеси на легком щебне и расширяет границы оптималь
ного водосодержания.
Смесь на легком щебне готовят аналогично тяжелым смесям, но легкие смеси перемешивают более тщательно, обычно в бетономешалках прину дительного действия. При виброуплотнении бетонных смесей на легком щебне применяют пригруз, препятствующий их расслоению вследствие малой объемной массы зерна щебня. Чем меньше объемная масса щебня, тем больше должен быть пригруз.
|
|
|
|
|
Т а б л и ц а 6.13 |
Объемная |
Коэффициент |
Объемная |
Коэффициент |
Объемная |
Коэффициент |
масса, |
теплопровод |
масса, |
теплопровод |
масса, |
теплопровод |
кг/м3 |
ности |
кг/м3 |
ности |
кг/м3 |
ности |
400 |
0,080 |
600 |
0,125 |
1000 |
0,210 |
500 |
0,095 |
800 |
0,160 |
1200 |
0,275 |
Крупнопористый бетон изготавливают из смесей беспесчаной составля ющей, вследствие чего они имеют крупнопористую структуру, малую объем ную массу и пониженный коэффициент теплопроводности. Для изготов ления крупнопористого бетона желателен щебень крупностью 10—20 мм или рядовой. 5—40 мм при соотношении цемента к щебню от 1 6 до 1 15. Этот вид бетона применяют для возведения монолитных и сборных, стен зданий.
Ячеистые бетоны характеризуются большим количеством замкнутых пор размером 0,5—2 мм. В них отсутствует щебень. Свойства ячеистых бетонов зависят от активности цемента, объема и характера пор. Чем меньше поры при равном их объеме, тем ниже теплопроводность, чем больше открытых пор, тем больше водопоглощаемость и ниже морозостойкость. Марки яче истых бетонов по прочности: 25, 50, 75, 100, 150. Зависимость между объемной массой ячеистых бетонов и их теплопроводностью приведена в табл. 6.13. Разновидностями ячеистых бетонов являются пено- и газобетон..
По условиям твердения ячеистые бетоны делятся на пропаренные и авто клавные. Для ячеистых бетонов, твердеющих в условиях естественного и тепловлажностного режима, применяют преимущественно клинкерные це менты марок 400 и 500 с введением в смесь ускорителей твердения. При получении бетонов автоклавного твердения применяют преимущественно маломагнезиальную молотую негашеную известь, к которой для замедле ния гашения добавляют гипс, сдб, жидкое стекло. В газобетоне можно ис пользовать различные цементы марки 300—400.
В ячеистых бетонах используют молотый песок, а в ряде случаев — высокодисперсные породы, маршалит, барханные пески, золу ТЭЦ, молотые породы и другие материалы, содержащие в достаточном количестве Si02.
Наиболее часто применяют клееканифольный и смолосапонитовый порообразователи, хорошим пенообразователем является препарат ГК (гидро лизная кровь).
Вкачестве газообразователя служит алюминиевая пудра марок ПАК-3
иПАК-4. Процесс газообразования происходит по реакции
ЗСа(0Н)2 + 2А1 + 6Н20 = ЗСа0 • А120 3 • 6H20 + 3H2f.
Выделяющийся водород вспучивает смесь, которая, затвердевая, сохра няет пористую структуру.
Пенобетон готовят смешением устойчивой пены с цементом (портландце ментом, шлакопортландцементом, пуццолановым портландцементом и др.) в специальных мешалках. В состав пенобетона вводят мелкозернистый и мо лотый песок. Пену получают взбиванием пенообразователей; она имеет устойчивую структуру, хорошо распределяется в смеси, что способствует образованию однородной структуры затвердевшего бетона. Смеси готовят в специальных пенобетоносмесителях; они подвижны, их подают в формы и формуют изделия на виброплощадках.
Газобетон изготавливают смешением вяжущего (портландцемента, шлакопортландцемента, пуццоланового портландцемента, извести до 10% от массы цемента), молотого кварцевого песка с газообразователем, например с порошкообразным алюминием,- в специальных газобетонных смесителях. Та кую смесь жидкой консистенции заливают в формы, в которых она затвер девает в естественных условиях, пропарочных камерах и автоклавах.