
673
.pdfПреимущества предлагаемого метода: возможность получения порошков различной номенклатуры; регулирование химического состава порошков
впроцессе распыления; мобильность оборудования плазменного распыления. В процессе получения чистых металлических порошков плазменным распылением существует вероятность спекания частиц в сборнике. Такой факт можно объяснить тем, что частицы, имея высокую скорость и не успев закристаллизоваться, достигают сборника. Такие частицы объединяются в конгломераты, образуя брак. Традиционно спекание в сборнике устраняется увеличением длины пролета частиц, что увеличивает габариты оборудования. Для уменьшения длины пролета частиц предлагается использовать встречный поток газа. Регулирование процессов движения теплообмена частиц предотвращает создание конгломератов спекшихся частиц и позволяет контролировать свойства получаемых частиц порошков. Поэтому целесообразно изучение влияния противопотока газа на торможение расплавленных частиц и изменение интенсивности охлаждения частиц [1].
Целью работы является оценка влияния противотока газовой среды на охлаждение и торможение металлических частиц в условиях получения порошков плазменным распылением пруткового материала. Исследованию двухфазных потоков посвящено значительное число теоретических и экспериментальных работ [2]. Однако применительно к условиям плазменного распыления эти процессы малоизучены.
Экспериментальное определение процессов торможения и охлаждения нагретых частиц в потоке газа весьма сложно. В связи с этим для их исследования целесообразно использовать методы математического моделирования.
Движение частиц в потоке газа характеризуется скоростью движения частиц и среды, а также зависит от свойств материала частиц и среды. В данном случае поток среды постоянен, не имеет скорости или направлен навстречу движению частиц. Движение частицы в потоке газа подчиняется закону Ньютона. В общем случае движение частицы может быть записано
вследующем виде [3]:
mч |
dvч |
=∑Fi = Fc +Fд +FB +Fвр +Fтф +Fвн, |
|
||
|
dt i |
где mч – масса частицы, кг; vч – скорость частицы, м/с; t – время, с; Fс – сила сопротивления среды, Н; Fд – сила в граничном слое частицы из-за действия градиента давлений, Н; FB – сила Бассета, Н; Fвр – сила, возникающая вследствие вращениячастицы, Н; Fтф – силатермофореза, Н; Fвн – внешниесилы, Н.
Наибольшее влияние на движение частицы оказывает сила газодинамического напора газа, сила тяжести также вносит существенные поправки в расчеты. Остальными силами можно пренебречь. Следовательно, уравнение движения частиц запишется в виде
61
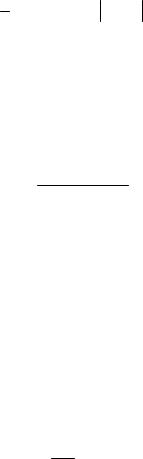
mч |
dvч |
=∑Fi = Fc +Fт. |
(2) |
|
|||
|
dt i |
|
Сила газодинамического напора
Fс = 12 Cf ρср (vср −vч )vср −vч SМ ,
где Cf – коэффициент сопротивления среды; ρср – плотность потока среды, кг/м3; vср – скорость потока среды, м/с; SМ – миделево сечение частицы,
SМ = πdч2/4, м2, dч – диаметр частицы, м.
Решение задачи движения частицы в потоке газа сводится к нахождению коэффициента сопротивления. Принято характеризовать коэффициент сопротивления как функцию от числа Рейнольдса Cf = f(Re):
Re = ρср dч (vср −vч ), µср
где µср – вязкость среды, кг/(м·с).
Для дальнейших расчетов принята зависимость Cf = f(Re) в виде [4]:
1000 |
|
|
|
0 ≤Re <0,001; |
|
|
Re−1 |
+2,448 Re−0,05 |
0,001≤Re <2; |
||
24 |
|||||
|
Re−1 |
+2,76 Re−0,2 |
2 ≤Re <21; |
||
C f = 24 |
|||||
|
Re |
−1 |
+4,536 Re |
−0,368 |
21≤Re <200; |
24 |
|
|
|||
0,44 |
|
|
|
200 ≤Re. |
|
|
|
|
|
|
|
Теплообмен частиц со средой в потоке газа характеризуется охлаждением частицы и описывается формулой классической термодинамики
mчcч dTч =∑Pi , dt i
где cч – удельная теплоемкость, Дж/(кг·К); Tч – температура частицы, К;
∑Pi – суммарная мощность, передаваемая в частицу, представляющая собой
i
сумму мощностей всех рассматриваемых для данной стадии нагрева частицы механизмов передачи.
Процесс охлаждения частиц связан с тем, что на этой стадии мощность, вводимая в частицу, равна нулю, а расходуемая мощность частицы идет на нагрев среды. Процессы теплопередачи описываются сложными дифференциальными уравнениями, в большинстве случаев не имеющими аналитиче-
62

ского решения. Для решения таких задач используют метод моделирования. За основу принимается ньютоновская модель теплопередачи: количество теплоты, переносимое в единицу времени к единице площади поверхности тела, находится из
q =α∆T.
где α – коэффициент теплопередачи; ∆T – температурный напор в пограничном слое.
Решение задачи теплообмена частицы в потоке газа сводится к нахождению коэффициента теплопередачи, который зависит от свойств частицы и потока среды. Принято характеризовать коэффициент теплопередачи как функцию от числа Рейнольдса и Прандтля:
Nu =α dч = f (Re,Pr).
λпл
Для дальнейших расчетов зависимости числа Нуссельта от чисел Рейнольдса и Прандтля примем в виде [5]
|
+0,6 Re |
0,5 |
Pr |
0,333 |
0 ≤Re <2; |
2 |
|
|
|||
Nu = |
+0,459 Re0,55 |
Pr0,333 |
2 ≤Re <2 105. |
||
2 |
|||||
|
|
|
|
|
|
Частные решения для нахождения скорости, температуры и координаты частицы, движущейся в потоке среды, можно представить в виде [6]:
|
g |
(1−e |
−nt |
)+vч0e |
−nt |
|
|
3Aµср |
|
||||||||
vч = vср − |
|
|
|
|
|
, где n = |
|
|
|
, A |
=C f Re, |
||||||
|
|
|
|
|
|
2 |
|||||||||||
|
n |
|
|
|
|
|
|
|
|
|
|
4ρчdч |
|
||||
Tч =Tср (1−e−Kt )+Tч0e−Kt , где K = |
6λсрNu |
, |
|||||||||||||||
|
|||||||||||||||||
|
|
|
|
|
|
|
|
|
|
|
|
|
|
|
cρчdч |
|
|
|
|
1 |
|
|
g |
(nt |
−1+e−nt )+ |
v |
|
(1−e−nt ), |
|
||||||
x = |
|
vср − |
|
|
|
ч0 |
|
||||||||||
|
|
|
|
|
|||||||||||||
|
|
n |
|
n |
|
|
|
|
n |
|
|
|
где ρср – плотность газового потока, кг/м3; Cf – коэффициент аэродинамического сопротивления; vч0 – начальная скорость частицы, м/с; Tср – температура потока среды, К; Tч0 – начальная температура частицы, К; λср – теплопроводность газового потока, Вт/(м·К).
Расчетное сравнение ускорения и скорости теплообмена частиц в среде и с созданием противопотока представлено на рисунке. Входные регулируемые параметры плазменной горелки, используемые для расчета, представлены в таблице. Скорости противопотока среды омечены на кривых. В качестве
63
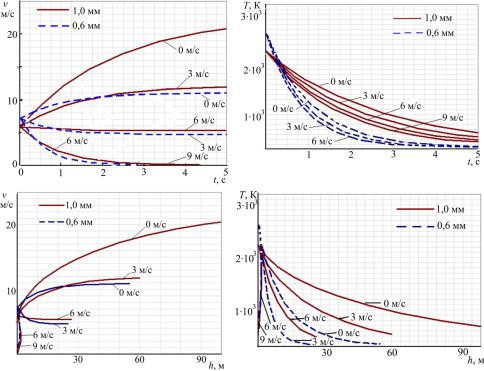
расчетного материала использовалась проволока диаметром 1,2 мм, материал проволоки 10Х18Н9Т. При воздействии противотока скорость частиц уменьшается и растет скорость охлаждения. Частицы меньших размеров имеют большую интенсивность изменения скорости и температуры в среде. С возрастанием размеров частиц для их торможения требуется создание больших скоростей противопотока, чем для меньших частиц.
В случае уравновешивания сил, действующих на частицы, возможна остановка и изменение скорости частиц в противоположном направлении. Как следствие, становится возможной обработка частиц в подвешенном состоянии и проведение отсева частиц по фракциям. Получение чистых порошков производится в контролируемой атмосфере, с чем связано более активное взаимодействие частиц, в данном случае требуется меньше энергии для спекания, соединения частиц. Отрицательным фактором обработки частиц в подвешенном состоянии является возможность соединения расплавленных частиц между собой. Подбор оптимальных скоростей противопотока устраняет этот недостаток.
Рис. Зависимости скорости и температуры частиц от времени и длины пролета при свободном движении в среде и противотоке (v – осевая скорость частиц, Т – температура частиц, h – длина пролета частиц)
64
Параметры режимов расчета процесса распыления
Диаметр частиц |
Мощность дуги |
Расход плазмообра- |
Расход стабилизи- |
dч, мм |
Nд, кВт |
зующего газа |
рующего газа |
|
|
Qпл, л/мин |
Qст, л/мин |
1,0 |
5,0 |
3 |
5,0 |
0,6 |
7,0 |
3,8 |
5,0 |
Сделаем следующие выводы:
1. Разработан алгоритм, позволяющий производить оценку интенсивности изменения скорости и температуры частиц металлических порошков
впотоке среды в зависимости от технологических параметров процесса.
2.Установлены оптимальные значения структуры противопотока газовой среды в зависимости от размера частиц и свойств материала.
Список литературы
1.Горбис Э.Р. Теплообмен и гидродинамика дисперсных сквозных пото-
ков. – М.: Энергия, 1970. – 424 с.
2.Selberg B.P., Nicholls J.A. Коэффициент лобового сопротивления сферических частиц небольшого размера // Ракетная техника и космонавтика. – 1968. – № 3, 22. – С. 22–31.
3.Дейч М.Е., Филиппов Г.А. Газодинамика двухфазных сред. – М.: Энергоиздат, 1981. – 472 с.
4.Поляков С.П., Рязанцев О.В., Твердохлебов В.И. О нагреве и движении частиц порошка в плазменных струях // Физика и химия обработки мате-
риалов. – 1975. – № 3. – С. 43–47.
5.Нанесение покрытий плазмой / В.В. Кудинов, П.Ю. Пекшев, В.Е. Бе-
лащенко [и др.]. – М.: Наука, 1990. – 408 с.
6.Донской А.В., Клубникин В.С. Электроплазменные процессы и установки в машиностроении. – Л.: Машиностроение, 1979. – 221 с.
Получено 2.02.2012
65

УДК 621.746.628.4
В.И. Васенин, А.В. Богомягков, К.В. Шаров
V.I. Vasenin, A.V. Bogomjagkov, K.V. Sharov
Пермский национальный исследовательский политехнический университет
Perm National Research Polytechnic University
ИССЛЕДОВАНИЕ ЛИТНИКОВОЙ СИСТЕМЫ С ТРОЙНИКОМ*
INVESTIGATION INTO A GATING SYSTEM
WITH A TRIFURCATION
Представлены результаты исследования литниковой системы с тройником для разных диаметров питателей и коллекторов. Установлено, что гидравлическое сопротивление тройника зависит от отношения суммарной площади питателей к площади коллектора. Результаты исследований могут быть использованы при физическом и математическом моделировании литниковых систем и расчетах систем для жидких металлов.
Ключевые слова: литниковая система, стояк, коллектор, тройник, питатель, гидравлическое сопротивление, скорость потока, расход жидкости.
The results of research of a gating system with a trifurcation for the different diameters of feeders and collectors are presented. It is established that the hydraulic resistance depends on the ratio summary area of the feeders to area of the collector. There results can be used in physical and mathematical simulation of the gating systems and to calculation of the systems for liquid metals.
Keywords: gating system, sprue, collector, trifurcation, feeder, hydraulic resistance, flow speed, liquid flow rate.
В гидравлике вообще и в литниковых системах (ЛС) в частности широко используется гидравлическое устройство «тройник». Возможны три варианта потоков в тройнике (рис. 1). На рис. 1, а представлена схема тройника, использующегося в L-образной ЛС. Такая система нами уже исследована теоретически и экспериментально [1, 2]. На рис. 1, б изображена схема сбора потоков (при литье не используется). Нас интересует тройник на рис. 1, в – это основа крестовинной ЛС, также он применяется в разветвленной, комбинированной и кольцевой ЛС. Информация о гидравлическом сопротивлении тройников крайне мала и противоречива.
Экспериментальная ЛС (рис. 2) состоит из литниковой чаши, стояка, коллектора и тройника. Для измерения напора жидкости перед тройником
всечении 6–6 коллектора установлен пьезометр – стеклянная трубочка внут-
*В работе участвовали А.А. Константинов, В.А. Сафронов и М.Ю. Щелконогов.
66
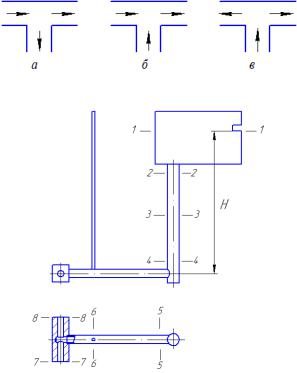
ренним диаметром 4,5 мм и длиной 400 мм. Внутренний диаметр чаши 272 мм, высота воды в чаше 103,5 мм. Продольные оси коллектора и тройника находятся в одной плоскости. Уровень жидкости Н – расстояние по вертикали от сечения 1–1 в чаше до продольных осей коллектора и тройника – поддерживался постоянным путем непрерывного доливания воды в чашу и слива ее излишков через специальную щель в чаше, H = 0,3630 м.
Рис. 1. Потоки жидкости в тройнике
Рис. 2. Литниковая система с тройником
Произведем расчет гидравлических характеристик ЛС, показанной на рис. 2. Уравнение Бернулли (УБ) для сечений 1–1 и 7–7 при работе только одного питателя с выходным сечением 7–7 запишется как
p |
|
v2 |
p |
|
v2 |
+ h(1) |
|
|
|
1 |
+ α |
1 |
+ H = |
7 |
+ α |
7 |
, |
(1) |
|
|
|
|
|
||||||
γ |
|
2g |
γ |
|
2g |
1−7 |
|
|
|
|
|
|
|
|
где p1 и p7 – давления в сечениях 1–1 и 7–7, Н/м2 (равны атмосферному давлению: p1 = p7 = pа ); γ – удельный вес жидкого металла, Н/м3; α – коэффи-
циент неравномерности распределения скорости по сечении потока (коэффициент Кориолиса), принимаем α =1,1 [3, с. 108]; g – ускорение свободного
67

падения, g = 9,81 м/с2; v1 и v7 – скорость жидкости в сечениях 1–1 и 7–7, м/с (вследствие большой разности площадей чаши S1 в сечении 1–1 и питателя S7 в сечении 7–7 можно принять v1 = 0 ); h1(1)−7 – потери напора при движении металла от сечения 1–1 до сечения 7–7, приведенные к скорости v7 (в случае работы только одного питателя), м. Эти потери напора
h(1) |
|
= |
|
ζ |
|
+ λ |
lст |
|
α |
vст2 |
+ |
|
ζ |
|
+ λ |
lк |
|
α |
vк2 |
+ |
|
ζ |
|
+ λ |
l7 |
|
α |
v72 |
, |
(2) |
|
|
ст |
|
|
|
к |
|
|
|
7 |
|
|
||||||||||||||||||
1−7 |
|
|
|
|
|
|
2g |
|
|
|
|
|
|
2g |
|
|
|
|
|
|
2g |
|
|
|||||||
|
|
|
|
|
|
|
dcт |
|
|
|
|
|
|
dк |
|
|
|
|
|
|
d7 |
|
|
|
||||||
где ζст , ζк , |
ζ7 |
– коэффициенты местных сопротивлений входа жидкости из |
чаши в стояк, поворота из стояка в коллектор и из коллектора в питатель
с выходным сечением 7–7; |
λ – коэффициент потерь на трение, принимаем |
||||||
λ = 0,03 |
[4]; |
dст |
и |
lст – |
диаметр и |
длина стояка, м, dст = 0,02408 м, |
|
lст = 0,2675 м; vст |
и vк |
– скорость металла в стояке и коллекторе, м/с; dк и lк – |
|||||
диаметр |
и длина |
коллектора |
от стояка |
до продольной оси питателей, м, |
|||
dк = 0,01603 |
м, |
lк = 0,246 |
м; |
d7 и l7 |
– диаметр и длина питателя, м; |
||
dп = 0,00903 |
м, lп = 0,045 |
м. Уравнение неразрывности при работе одного |
|||||
питателя vстSст = vкSк = v7 S7 . Отсюда vст |
= v7 S7 / Sст , vк = v7 S7 / Sк . Подставив |
эти значения скоростей в выражение (2), получаем такую зависимость для потерь напора между сечениями 1–1 и 7–7, приведенных к скорости v7 :
|
2 |
|
|
lст |
|
S7 |
2 |
|
|
lк |
|
S7 |
2 |
|
|
l7 |
|
|
||||||
h1(1)−7(7) |
= α |
v7 |
|
ζст + λ |
|
|
+ |
ζк + λ |
|
|
+ ζ7 |
+ λ |
. |
(3) |
||||||||||
|
|
|
|
|
|
|||||||||||||||||||
|
|
2g |
|
d |
ст |
S |
ст |
|
|
d |
к |
S |
к |
|
|
|
d |
7 |
|
|
||||
|
|
|
|
|
|
|
|
|
|
|
|
|
|
|
Часть выражения (3) в квадратных скобках – это коэффициент сопротивления ЛС от сечения 1–1 до сечения 7–7, приведенный к скорости v7 и учитывающий работу только одного питателя с выходным сечением 7–7:
ζ1(1)−7(7) |
|
|
lст |
|
S7 |
2 |
|
|
lк |
|
S7 |
2 |
|
l7 |
|
|
|
= |
ζст + λ |
|
|
+ |
ζк + λ |
|
|
+ ζ7 + λ |
. |
(4) |
|||||||
|
|
|
Sк |
|
|||||||||||||
|
|
|
dст |
Sст |
|
|
dк |
|
|
d7 |
|
Коэффициент расхода ЛС от сечения 1–1 до сечения 7–7, приведенный к скорости жидкости v7 и учитывающий работу только одного питателя,
µ1(1)−7(7) |
= |
|
1 |
. |
(5) |
|
+ ζ1−7(7) |
||||
|
1 |
|
|
Скорость металла в сечении 7–7
68
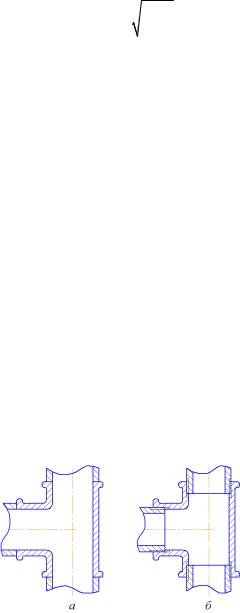
|
|
v |
(1) |
= |
1 |
|
2gH |
. |
|
|
(6) |
|||
|
|
|
|
|
|
|
|
|
||||||
|
|
|
µ |
|
|
|
|
α |
|
|
||||
|
|
7 |
|
1−7(7) |
|
|
|
|
|
|
|
|||
Расход в этом сечении |
|
|
Q(1) |
= v(1) S |
|
|
|
|
|
|
||||
|
|
|
|
7 |
. |
|
|
|
(7) |
|||||
|
|
|
|
|
7 |
7 |
|
|
|
|
|
|
|
|
Для опытной ЛС ζст = 0,10 |
[5, с. 126], ζк = 0,396 [6], ζ7 = 0,314 [6]. Рас- |
|||||||||||||
четы по формулам (4)–(7) |
дают следующие результаты: |
ζ(1) |
|
= 0,558305, |
||||||||||
|
|
|
|
|
|
|
|
|
|
|
|
1−7(7) |
|
|
µ(1) |
= 0,801076, v(1) = 2,038357 |
м/с, Q(1) |
=130,540600 10−6 |
м3/с. Экспери- |
||||||||||
1−7(7) |
7 |
|
|
|
|
|
7 |
|
|
|
|
|
|
|
ментальные данные: v(1) |
= 2,013 м/с, Q(1) |
=128,91 10−6 м3/с. |
|
|
||||||||||
|
7(эксп) |
|
|
|
|
|
7 |
|
|
|
|
|
|
Когда работают оба питателя, УБ запишется в виде (1), однако вместо коэффициента местного сопротивления поворота из сечения 6–6 в сечение 7–7 ζ7 в формуле (2) будет коэффициент сопротивления (не местного!) на деле-
ние потока ζ7д . Этот коэффициент находим по соотношению из справочника
[5, с. 277]:
ζ |
д |
= |
1+ φ(vд / v)2 |
, |
(8) |
|
|
|
(vд / v)2 |
||||
|
|
|
|
|
|
где v – скорость жидкости до деления потока, м/с; vд – скорость жидкости в одном из каналов после деления потока, м/с; ϕ – коэффициент. Коэффициент φ = 0,3 для стандартного сварного тройника (рис. 3, а), и φ =1,5 для соединения чугунных труб в тройнике на резьбе (рис. 3, б) [5].
Рис. 3. Виды тройников: а – стандартный сварной тройник, φ = 0,3; б – соединение чугунных труб в тройнике
на резьбе, φ =1,5
Рассчитаем ЛС с тройником с двумя работающими питателями при φ = 0,3. Чтобы найти ζ7д (и равный ему ζ8д ), запишем очевидное равенство
69

v S |
|
= 2v S |
|
= 2v S |
|
, из которого следует, что |
v |
= |
S |
к |
= |
201,816620 10−6 |
= |
|
|
|
|
7 |
|
|
|||||||||
|
|
|
v |
|
|
2 64,042073 10−6 |
||||||||
к |
к |
7 |
7 |
8 |
8 |
|
|
2S |
7 |
|
|
|||
|
|
|
|
|
|
|
к |
|
|
|
|
|
|
=1,575657 – это и есть отношение vотдv в формуле (8). Тогда по формуле (8)
находим, что ζ7д = ζ8д = 0,702788 . Уравнение неразрывности для случая работы обоих питателей будет выглядеть следующим образом:
Q = v S |
|
= v S |
|
= 2v S |
|
= 2v S |
|
. Отсюда |
v |
= v |
2S7 |
, |
v |
= v |
2S7 |
. Подставив |
|
|
|
|
|
|
|||||||||||
ст |
ст |
к |
к |
7 |
7 |
8 |
8 |
|
ст |
7 Sст |
к |
7 Sк |
эти отношения скоростей в выражение (2), получаем такую зависимость для потерь напора между сечениями 1–1 и 7–7, приведенных к скорости v7 и учитывающих работу обоих питателей:
|
2 |
|
|
lст |
|
2S7 |
2 |
|
|
lк |
|
2S7 |
2 |
|
l7 |
|
||||||
h1(2)−7(7) |
= α |
v7 |
|
ζст + λ |
|
|
+ |
ζк + λ |
|
|
+ ζ7д + λ |
. |
||||||||||
|
|
|
|
|
|
|||||||||||||||||
|
|
2g |
|
d |
ст |
S |
ст |
|
|
|
d |
к |
S |
к |
|
|
d |
7 |
|
|||
|
|
|
|
|
|
|
|
|
|
|
|
|
Выражение в квадратных скобках – это коэффициент сопротивления системы от сечения 1–1 до сечения 7–7, приведенный к скорости v7 и учитывающий работу обоих питателей:
ζ1(2)−7(7) |
|
|
lст |
|
2S7 |
2 |
|
|
lк |
|
2S7 |
2 |
|
l7 |
. |
|
= |
ζст + λ |
|
|
+ |
ζк + λ |
|
|
+ ζ7 + λ |
||||||||
|
Sст |
|
Sк |
|
||||||||||||
|
|
|
dст |
|
|
|
dк |
|
|
d7 |
Коэффициент расходаЛС от сечения 1–1 до сечения 7–7, приведенный к скорости жидкости v7 и учитывающий работу обоих питателей,
µ(2) |
= |
|
1 |
. |
|
|
|||
1−7(7) |
1 |
+ ζ1(2)−7(7) |
|
|
|
|
Скорость металла в сечении 7–7
v(2) |
= µ(2) |
2gH . |
|
7 |
1−7(7) |
α |
|
Расход в этом сечении
Q7(2) = v7(2) S7 .
Расход в системе
Q = 2Q7(2) = 2Q8(2) = 2v7(2) S7 = 2v8(2) S8 .
70