
Промышленное применение лазеров
..pdf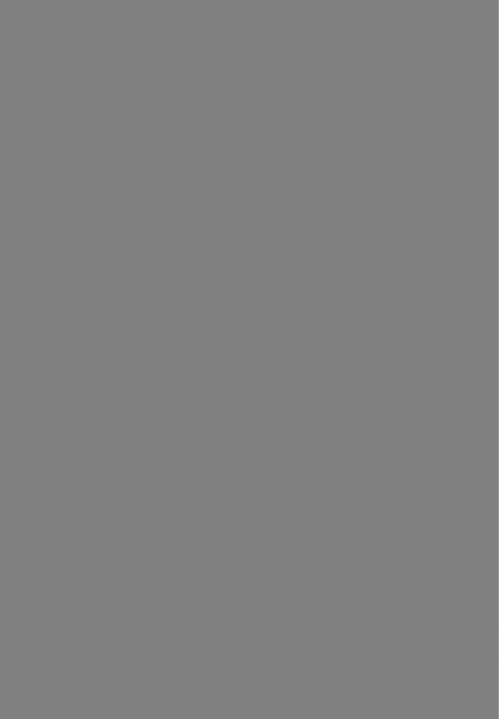
метки, зенковки входной части, снятия заусенцев, существенно по вышается производительность обработки.
К деталям, для изготовления которых целесообразно примене ние лазерной технологии, относится также большая номенклатура специальных видов крепежа с отверстиями под шплинт или контро вочную проволоку. Эти отверстия в большинстве случаев имеют диахметр более 1 мм при толщине заготовки в зоне обработки 2+3 мм. Механическое сверление таких отверстий затруднено из-за их распо ложения на криволинейных или находящихся под углом к оси сверла плоскостях.
Отклонения диаметральных размеров обработанных с помощью лазерной установки отверстий обычно лежат в пределах 10+12 % но минала, что соответствует 6+7 квалитету.
Для повышения точности и качества прошиваемых отверстий могут быть использованы различные технологические приемы: ульт развуковая модуляция излучения; подача в зону обработки синхрон но с излучением струи воздуха или газа; выполнение обработки в жидкой среде; использование дополнительных доводочных опера ций, например калибровки пуансоном, наложение на обрабатывае мую поверхность экрана с целью устранения конусной (кратерной) части отверстия.
Для интенсификации лазерного прошивания отверстий можно использовать предварительный нагрев металлической заготовки, на ложение ультразвуковых колебаний на заготовку, подвод энергии электрического разряда в зону лазерного воздействия (электролазерная обработка). Эти приемы дают возможность увеличить диаметр отверстий и улучшить качество получаемой поверхности.
Лазеры нетрудно приспособить для обработки неметаллических материалов. Обычно с помощью лазера с фиксированными парамет рами можно испарить значительно большее количество неметалли ческого материала, чем металла, что, по крайней мере частично, обу словлено различием значений удельной теплопроводности. Особенно легко испаряются органические материалы. В данном случае выгод нее использовать С02-лазеры. поскольку многие неметаллические
материалы имеют очень сильное поглощение на длине волны 10,6 мкм. Для эффективной пробивки отверстий во многих неметал лических материалах можно использовать С 02-лазер, работающий в режиме повторяющихся импульсов со средним уровнем мощности ~100 Вт. Для этих же целей используются также рубиновые лазеры и лазеры на АИГ с неодимом, работающие в непрерывном режиме или режиме повторяющихся импульсов.
С помощью рубинового лазера можно пробивать узкие глубо кие отверстия в относительно толстых образцах хрупких материалов (например, в керамике или кремнии). Так, в глиноземе были сделаны отверстия с аспектным отношением (отношением глубины отверстия к его диаметру), превышающим 25. Такое аспектное отношение вы ше досгижихмых отношений при изготовлении отверстий малого диаметра в керамике обычными методахми. Рубиновым лазером, ра ботающим в режиме повторяющихся импульсов, можно пробить ке рамику толщиной 3,2 мм.
Из-за высокой хрупкости керамики сверление обычными спо собами, как правило, выполняется на «сыром» ^материале, до того как он подвергнется обжигу. При обжиге размеры изделия могут изме ниться. Лазерная пробивка отверстий выполняется уже после обжи га, и поэтому эти проблемы не возникают. Использование лазера для пробивки отверстий в твердой, обожженной при высокой температу ре глиноземной керамике может оказаться перспективным, посколь ку обычные методы сверления керамики очень сложны и требуют, как правило, применения сверлильных головок из закаленной стали с алмазными наконечниками. Чрезвычайно трудно на основе сущест вующей технологии получить небольшие отверстия диаметром менее 0,25 мм. В тохм случае, когда толщина керамики превышает диаметр получаемого отверстия, часты поломки сверла. С помощью лазера хможно пробивать в указанном хрупком материале небольшие отвер стия без риска растрескивания образца.
В пластине из хрупкого материала лазером можно пробить от верстия, расположенные вблизи друг от друга или от края пластины. Лазеры можно использовать для пробивки отверстий, предназначен
ных для присоединения вводов к подложкам интегральных схем. Сверление подобных материалов обычными методами сопряжено с большими трудностями. Применение лазеров позволяет полностью исключить проблемы износа и поломки сверлильных головок.
Внескольких областях применение лазеров для пробивки от верстий достигло промышленных масштабов. Одна из них - пробив ка отверстий в драгоценных камнях. Лазеры обычно используются для пробивки отверстий в алмазах, предназначенных для применения
вкачестве фильер для вытягивания проволоки. Применение лазеров
вэтой области сулит большие выгоды, поскольку из-за высокой твердости алмаза применение прежних методов оказывается слиш ком трудоемким и дорогостоящим. Исходные отверстия для фильер пробиваются одним или несколькими импульсами рубинового лазе ра. Для того чтобы сгладить стенки полученных отверстий, необхо дима дополнительная чистовая обработка, но пробитые лазером ис ходные отверстия очень удобны для окончательной доводки. Данный пример относится к области применения, в которой лазеры имеют существенные преимущества по сравнению с другими методами. Пробивка отверстий в рубиновых камнях для часов стала обычной процедурой.
Возможность пробивки отверстий в керамике с помощью лазе ра находит применение в электронной промышленности. Для про бивки отверстий в глиноземной подложке плат электронных схем обычно используются импульсные С02-лазеры.
Внастоящее время все более широкое распространение полу чают автоматизированные лазерные системы для пробивки: сложной совокупности отверстий в материалах толщиной ~0,6 мм. В состав такой системы входят крепежное устройство для керамики, ступен чатый двигатель для перемещения крепежного устройства в необхо димое для пробивки отверстия положение и устройство цифрового контроля (которое, по существу, является небольшой ЭВМ), осуще ствляющее включение и выключение лазера и двигателя, в результа те чего обеспечивается пробивка отверстий в строго определенных местах. Оператору остается лишь установить керамическую пла
стинку и включить систему. Остальной процесс выполняется автома тически, и в керамике пробиваются нужные отверстия. На рис. 4.7 показаны отверстия, пробитые при помощи лазера.
На практике пробивка отверстий с помощью лазера имеет ряд недостатков. Один из них заключается в ограниченной глубине про никновения лазерного пучка, которая определяется ограниченным количеством энергии в лазерном импульсе. Этот недостаток можно было бы устранить, если использовать непрерывной СОг-лазер и на правлять его пучок на одно и то же место в течение длительного времени. Однако при этом тепловая энергия распространяется на значительно большую площадь и теряются все преимущества ис пользования лазера. Второй недостаток состоит в том, что удаляе мый материал вновь конденсируется вокруг входа в отверстие, в ре зультате чего входной край отверстия приобретает форму кратера. Причина этого явления состоит в том, что выходящий из отверстия испаряющийся материал легко конденсируется на первой же холод ной поверхности, которая встречается на его пути. Образовавшиеся вокруг отверстия закраины нетрудно удалить, но это означает добав ление еще одного этапа к процессу пробивки отверстия. Третий не достаток связан с общей неровностью стенок отверстия, которая обычно нежелательна. Для твердых хрупких материалов типа алмаза можно вводить этап окончательной обработки отверстия, пробитого с помощью лазера.
Из-за этих недостатков лазерная пробивка отверстий в металлах не получила столь широкого распространения, как пробивка отвер стий в керамике и аналогичных ей материалах. Связано это также с тем, что обычные методы сверления отверстий в металлах часто дают вполне удовлетворительные результаты. Но в применении к твердым хрупким материалам типа керамики, которые легко раска лываются и быстро изнашивают сверлильные головки, обычные ме тоды сверления, как правило, не дают хороших результатов. Приме нение лазеров для пробивки отверстий в таких материалах часто дает целый ряд преимуществ.
Для обработки различных диэлектрических материалов (кера мика, стекло, кварц и т.п.) применяют лазеры не только импульсного, но и непрерывного излучения.
Представляет интерес процесс обработки центровочных отвер стий в заготовках из твердых сплавов. При Е = 20-^25 Дж, F = 70-^80 мм, v= 0,5-И,0 Гц, п =8-=-13 диаметр отверстия достигает 0,6-4,0 мм при глубине до 6 мм. Время прошивания составляет 5-^20 с, что позволя ет в 10-К20 раз повысить производительность процесса по сравнению с электроэрозионной или алмазной обработкой.
Лазерная обработка отверстий диаметром 0,8 мм внедрена с экономическим эффектом 307 тыс. руб. при изготовлении деталей инъекционных игл (канюлей).
Разработаны технологические процессы лазерного прошивания отверстий диаметром (0,25-Ю,35)±0,1 мм в деталях топливной аппа ратуры дизельных двигателей, газоотводящих отверстий диаметром 0,8-Ю,9 мм во вкладышах шинных пресс-форм, отверстий диаметром 4(Н50 мкм в керамических фильерах для получения искусственного волокна, отверстий диаметром 0,5-Ю.6 мм в ферритовых пластинах памяти и др.
С высокой эффективностью была внедрена лазерная технология при изготовлении часовых и приборных камней, алмазных волок. Так, прошивание одного отверстия диаметром 40+60 мкм в рубино вом камне на лазерной установке типа «Корунд» ведется с произво дительностью 1 камень в секунду, в то время как операция механи ческого сверления такого отверстия длится от 10 до 15 мин.
Приведенные примеры свидетельствуют о высокой эффектив ности лазерного прошивания отверстий в различных деталях.
4.2.3. Скрайбирование и термораскалывание
Эги виды лазерной размерной обработки применяются для раз деления хрупких и твердых материалов. Они характеризуются более высокой эффективностью по сравнению с традиционными способа
ми разделения, так как при реализации этих процессов нет необхо димости весь объем реза в материале приводить в расплавленное или испаренное состояние и таким образом тратить значительное количе ство энергии на обработку. Вместо этого, создавая с помощью лазер ного излучения особое напряженно-деформированное состояние, можно для разделения этих материалов использовать их основное свойство - хрупкость.
При традиционном скрайбировании (от английского to scribe - царапать) на поверхность хрупкого твёрдого материала наносится алмазным или твердосплавным инструментом направляющая цара пина («подрез»), по которой при приложении незначительного уси лия осуществляется разделение материала. Однако этот процесс до вольно трудоемок и обычно сопряжен с появлением высокого про цента брака.
Лазерное скрайбирование представляет собой широко распро страненный метод резки и фасонной обработки образцов, в ходе ко торого испарением охватывается лишь часть поверхности вдоль гра ницы раздела. Этот метод применим для обработки хрупких мате риалов типа керамики, кремния или стекла. Скрайбирование осуществляется путем нанесения на поверхности сплошной канавки или пробивки последовательности близко расположенных отверстий импульсным или непрерывным излучением с высокой скоростью (до 15 м/мин). После этого материал легко надламывается вдоль ли нии скрайбирования.
По сравнению с алмазным скрайбированием возможно увели чение в 2-КЗ раза глубины подреза. Благодаря бесконтактности мето да обработки достигаются высокие точность разделения материала и качество поверхноста. Оптимальная глубина подреза обычно должна составлять 25^-35 % толщины материала.
В ряде случаев для разделения материала не требуется получе ния сплошного подреза, достаточно выполнить лишь серию несквоз ных отверстий вдоль линии раздела заготовки.
Операции лазерного скрайбирования используют в микроэлек тронной промышленности для разделения пластин из кремния, арсе
нида галлия или специальной керамики (например, электрокорундовой или бериллиевой).
Раскалывание материала происходит за счет механических напря жений, возникающих в структуре при различных воздействиях извне.
При термораскалывании материала с помощью лазерного из лучения при поглощении энергии лазерного излучения происходит быстрый нагрев поверхности хрупкого материала, в результате кото рого возникают механические напряжения, приводящие к локально му расколу материала.
Величину этих напряжений можно определить из выражения
рЕТ <з = — ------,
2(1 -Ц )
где Р - линейный коэффициент термического расширения; Еупр - мо дуль упругости; Т - температура в зоне воздействия луча; р - коэф фициент Пуассона.
При перемещении материала относительно лазерного пучка тре щина распространяется вдоль пути, проходимого пучком. Разделение материала на куски происходит без разрушения его поверхности и без потерь самого материала, исключая дополнительные усилия.
Обычно значения развиваемых термоупругих напряжений
в4+6 раз превышают предел прочности хрупкого материала.
Вряде случаев возникающие в зоне лазерного воздействия гра диенты температур и напряжений настолько велики, что приходится их снижать путем предварительного нагрева заготовки газовыми го
релками до Т= 150-^400° С.
Лазерное термораскалывание эффективно на операциях разде ления различных стеклянных изделий - труб, баллонов электроваку умных приборов, а также кристаллов естественных алмазов и т.п.
По сравнению со скрайбировнием метод раскола обладает сле дующим недостатком: трещина может распространяться за пределы намеченной линии раздела (что часто наблюдается при попытке по лучить угол с резкими очертаниями). Поэтому для контролируемого
разделения хрупких материалов обычно используется метод скрайбирования, а метод раскола применяется в тех случаях, когда необ ходимо избежать потерь материала в процессе разделения.
4.2.4. Поверхностная лазерная обработка
Лазерная поверхностная обработка вызывает улучшение мно гих эксплуатационных характеристик облученных материалов.
На режимах, не вызывающих разрушения материала, реализу ются различные процессы лазерной поверхностной обработки. В ос нове этих процессов лежат необычные структурные и фазовые изме нения в материале, возникающие вследствие сверхвысоких скоро стей его нагрева и последующего охлаждения в условиях лазерного облучения. Важную роль при этом играют возможность насыщения поверхностного слоя элементами окружающей среды, рост плотно сти дислокаций в зоне облучения и другие эффекты.
В зависимости от степени развития указанных явлений в мате риале различают несколько видов поверхностной лазерной обработ ки (табл. 4.5), возможность реализации которых определяется в ос новном уровнем плотности мощности излучения.
Таблица 4.5
Виды поверхностной лазерной обработки
|
Плотность |
Скорость |
Глубина ЗТВ, |
Вид обработки |
мощности, |
охлаждения, |
|
|
Вт/см2 |
°С/с |
мм |
|
|
||
Упрочнение без фазового перехода |
10J-чо4 |
104-105 |
0,1-0,5 |
Лазерный отжиг (отпуск) |
102--103 |
- |
0,05-0,1 |
Упрочнение с фазовым переходом |
ю4--ю 6 |
ю4--106 |
0,2-3,0 |
Лазерное легирование |
ю4-ч о8 |
ю4-чо5 |
0,2-2,0 |
Лазерная наплавка (напыление) |
ю4-чо5 |
ю4--106 |
0,02-3,0 |
Аморфизация поверхности |
ю6-То8 |
106--107 |
0,01-0,05 |
Шоковое упрочнение |
10у-1012 |
ю 4-чо5 |
0,02-0,2 |
Упрочнение без фазового перехода предполагает структурные изменения в материале при уровне плотности мощности излучения, не приводящем к расплавлению облученной зоны. При этом виде обработки сохраняется исходная шероховатость обрабатывающей поверхности. Быстрый локальный нагрев поверхности и последую щее охлаждение за счет теплоотвода в массив материала приводят к образованию в поверхностном слое стали специфической высоко дисперсной, слаботравящейся, дезориентированной в пространстве структуры, имеющей микротвердость, в 2+4 раза превышающую микротвердость основы (матрицы).
При малых плотностях мощности, скоростях нагрева й охлаж дения, не превышающих критических значений, может быть реали зован режим отжига (отпуска) ранее закаленных материалов. Необ ходимость такой операции возникает, например, при изготовлении листовых пружин, отбортовке краев обоймы подшипника и т.п.
Упрочнение с фазовым переходом предполагает плавление ма териала в облученной зоне. Этот вид упрочнения требует более вы сокой плотности мощности излучения, что позволяет добиться зна чительных глубин упрочненного слоя. Поверхность этого слоя имеет характерное для закалки из жидкого состояния дендритное строение. Затем идет ЗТВ, а между ней и материалом основы расположена пе реходная зона. При данном виде поверхностной обработки, естест венно, нарушается исходная шероховатость, что требует введения в технологический процесс изготовления изделия дополнительной финишной операции (шлифования).
При реализации рассмотренных видов обработки не требуется специальной среды, процесс проводится на воздухе. При этом возможна частичная диффузия составляющих воздуха в облученную зону.
Важную роль при этом также играет вид поглощающего покры тия, наносимого на поверхность для повышения эффективности об работки.
Разработано и используется большое многообразие поглощаю щих покрытий: фосфатные, хромовые, коллоидные растворы, графит, различные краски, оксиды металлов, силикаты и пр. Если для срав