
- •В.Н. ШИШЛЯЕВ
- •Шишляев В.Н.
- •1.2. Диаграммы состояния системы железо - углерод
- •1.5. Графитообразование в чугунах
- •1.6. Влияние различных факторов на кристаллизацию чугуна
- •1.6.1. Влияние химического состава
- •1.6.2. Влияние скорости охлаждения
- •1.6.4. Влияние модифицирования
- •2.1. Классификация чугунов
- •2.2. Структура и механические свойства чугунов
- •2.2.2. Структурные диаграммы чугуна
- •2. 3. 6. Модифицирование серых чугунов
- •2.4.4. Модифицирование КЧ
- •3. ЛИТЕЙНЫЕ СТАЛИ
- •3.3.1.1. Взаимодействие железа с легирующими элементами
- •3.3.3. Легированные стали со специальными свойствами
- •Библиографический список
Рекомендуемый химический состав ковкого чугуна
Марка |
|
Химический состав чугуна |
Сг ! |
|
|
|||
С |
Si |
Мп |
р I |
S |
ESi+C |
|||
|
|
не более |
! |
|||||
|
|
|
|
|
|
|
||
КЧ 33-8 |
2,6-2,8 |
|
0,4-0,6 |
0,12 |
0,20 |
0,08 i |
37 -4,2 |
|
КЧ 35-10 |
2.5-2.8 |
1.1-1.3 |
0.3-0.6 |
0,12 |
0.20 |
о.об! 3.6 |
-4.0 |
|
КЧ 37-12 |
2,4-2.7 |
1.2-1.4 |
0.3-0.6 |
0.12 |
0,20 |
0.06! 3.6 |
-4,0 |
|
КЧ 50-5 |
2,5-2,8 |
1.1-1.3 |
0.3-1.0 |
0,10 |
0,20 |
0,08! |
3,6 |
-3,9 |
КЧ 80-1.5 |
2 .4-27 |
' 1.2-1.4 |
0.3-1,0 |
0,10 |
0,06 |
0,081 |
3,6-3,9 |
2.4.4. Модифицирование КЧ
Основное противоречие, существующее при производстве отливок из ковкого чугуна, а именно необходимость избежать графитизации при охлаждении отливки в форме и увеличить скорость ее протекания при отжиге, может быть сглажено путем ком бинированного модифицирования.
М одиф икаторы для КЧ можно подразделить на два типа: стабилизирующие и графитизирующие.
К модификаторам первого типа - стабилизирующим
относятся: Bi, Те, Sb, Mg, S и другие элементы. Они стабилизируют цементит и предотвращают графитизацию при охлаждении толстостенных отливок, но не оказывают заметного отрицательного влияния на графитизацию при отжиге. Более широкое практическое применение нашли Bi, Те и сплавы, содержащие эти элементы (Bi - Те, Те - Си, Fe - Те и т. д.) Обычно присадки Bi или Те составляют не более 0,001-0,010 % от массы жидкого чугуна. Эффективность теллура выше, чем висмута, и расход его соответственно ниже. С целью уменьшения угара висмут рекомендуется вводить в виде лигатур Bi - Mn, Bi - Sb, Bi - Sb и др. Действие теллура усиливается при наличии алюминия, образующего на поверхности окисную пленку, препятствующую испарению теллура. При работе следует учитывать, что теллур и висмут являются токсичными элементами.
К модификаторам второго типа - графитизирующим - относятся AI, В, Ti, Са и другие элементы. Они ускоряют графитизацию при отжиге и повышают механические свойства чугуна. Практическое применение нашли AI и В. Алюминий вводится в чистом виде, а бор в виде ферробора, борной кислоты или борного ангидрида. Оптимальное содержание алюминия 0,01-0,03 % от массы расплава, а бора 0,002-0,003% (этому количеству равноценны 0,01-0,06 % ферробора или 0,005-0,030 % борной кислоты).
Оба типа модификаторов применяют совместно, что позволяет увеличить допустимую толщину стенок отливок и сократить продолжительность отжига.
Модифицирование КЧ требует большой аккуратности и точного соблюдения режима. При превышении указанных концентраций может быть получен противоположный результат. Так, при введении алюминия в количестве более 0,03 % усиливается графитизация при охлаждении отливок и ухудшается их отжигаемость. Удобно использовать комплексные модификаторы, содержащие как стабилизаторы, так и графитизаторы. В литературе можно встретить десятки таких комплексных модификаторов, содержащих многие из вышеназванных элементов в различных сочетаниях.
При повышенном содержании хрома используют комплексные модификаторы, содержащие азот, который образует нитриды хрома и снижает его отрицательное влияние на графитизацию. Так, чугун, содержащ ий до 0,20 % хрома, модифицируют комплексным модификатором, включающим до 0,05 % В, 0,02 % AI и до 0,25 % N в виде СаС№ (цианамид кальция) или мочевины.
2.4.5. Термическая обработка КЧ
При производстве отливок из ковких чугунов термическая обработка (ТО) является неотъемлемой частью технологического процесса. Путем ТО решаются три основные задачи:
• получение разнообразных вариантов вторичной структуры из белого
чугуна,
•улучшение структуры,
•устранение дефектов структуры чугуна.
Первая наиболее ответственная задача решается путём отжига. В ходе отжига, в соответствии с требованиями к различным маркам чугуна, формируется структура металлической матрицы, состоящая из феррита, феррита и перлита в различных количественных сочетаниях, или перлита различной формы и дисперсности, а также из графитовых включений хлопьевидной формы, наиболее характерной для КЧ. Различают два вида отжига отливок на ковкий чугун: графитизируюиций и обезуглероживающий.
Их режимы будут рассмотрены ниже.
Вторая задача решается при ТО отливок с уже сформировавшейся структурой КЧ. Цели ТО - улучшение структуры металлической матрицы для повышения прочности и износостойкости КЧ. Это повышение достигается за счет нормализации, улучшения, старения, объемной или поверхностной закалки с отпуском, а также за счет химико-термической обработки (азотирование, сульфидирование) отливок.
Третья задача ТО устранение дефектов структуры, которые могут возникнуть при предыдущей ТО.
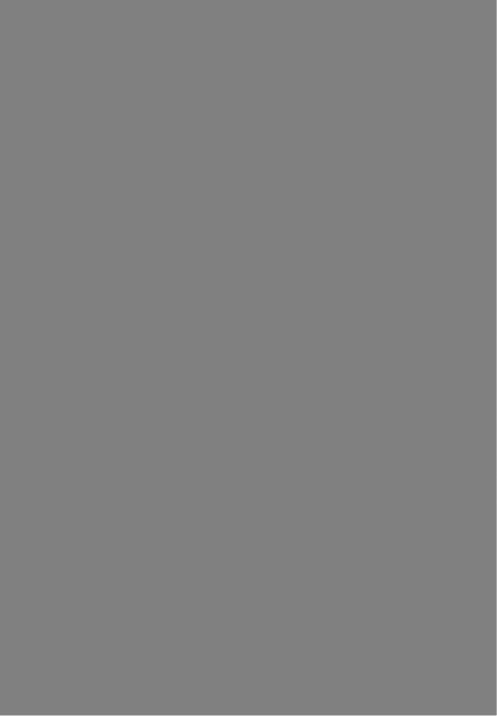
Третий этап - промежуточное охлаждение до температурного интервала эвтектоидного превращения (770-740 °С). Оно сопровождается выделением углерода из аустенита и ростом графитовых включений.
Ч е т ве рт ы й эт ап представляет собой вторую стадию графитизации, при которой графитизируется весь оставшийся углерод. Она может происходить двумя путями. Более надежным для получения чисто ферритной структуры является медленное прохождение интервала температур эвтектоидного превращения до 700 °С со скоростью не более 5 °С/ч. Второй вариант - это изотермическая выдержка при температуре 720-730 °С (пунктирная линия на графике). При первом варианте происходит превращение аустенита в феррит и графит. При втором варианте, в случае быстрого перехода критических температур, сначала образуется перлит, карбиды которого распадаются во время длительной выдержки. Если скорость охлаждения на третьем этапе велика или мала выдержка, то в структуре КЧ может присутствовать перлит. Обычно продолжительность второй стадии графитизации составляет 8-15 часов. При правильном ведении процесса отжига в чугуне образуется чисто ферритная структура с хлопьевидными графитовыми включениями.
Пятый этап - окончательное охлаждение отливок после отжига до температуры 600-550 С. Производится оно в печи, а затем на воздухе.
П родолжительность первой и второй стадий графитизации зависит от химического состава, особенно от содержания С + Si, а также от сечения и массы отливок. Для качественного чугуна суммарное содержание С и Si должно быть 3,6-3,8 %, для низкосортного - 3,9-4,1 %. Если сумма этих элементов менее 3,5 %, то задерживается процесс графитизации, а если сумма больше 4,1 %, то наблюдается выделение графита в белом чугуне, что снижает механические свойства чугуна после отжига. В любом случае рекомендуется выдерживать следующее оптимальное соотношение: Сэ = С + 0,33 Si^ 3 %. Чем больше будет Сэ, тем больше количество центров графитизации, тем мельче и равномернее распределится графит отжига.
Оптимальное соотношение марганца и серы для ферритного чугуна Mn/S = 2,0...2,5.
2.4.5.2.Графитизирующий отжиг на перлитный КЧ
Взависимости от вида проведения второй стадии графитизации может быть получена структура металлической матрицы, состоящая либо только из феррита, либо из феррита и перлита, либо из перлита или сорбита. Схемы этих режимов отжига показаны на рис. 2.13.
о
Температура,
Рис. 2.13. Влияний режима отжига на конечную структуру ковкого чугуна
Отличительной чертой отжига на перлит является ускоренное охлаждение отливок после первой стадии графитизации (см. рис. 2.13, в). Сначала необходимо медленное промежуточное охлаждение в печи до температуры 850 °С, а затем ускоренное прохождение критического интервала со скоростью не менее 100 °С/ч до температуры 650 °С и изотермическая выдержка. При сфероидизирующем варианте отжига (см. рис. 2.13, г) перлит переходит в глобулярную форму, что обеспечивает значительное повышение
механических свойств. Ещё более эф ф ективно |
получается |
сф ероидизированный (зернисты й) перлит при отжиге |
по режиму, |
показанному на рис. 2.14. Процесс получения перлитной структуры можно упростить, если для отжига использовать чугун с пониженным содержанием Si или с повышенным содержанием Мп, что позволяет ограничить склонность
Т, “С |
чугуна к граф итизации |
на |
|||
второй стадии. |
|
|
|||
|
Обычно |
для |
получения |
||
|
перлитной |
структуры |
|||
|
отжигают |
белый чугун, |
|||
|
содержащий 0,7-1,2 % Si и 0,4- |
||||
|
1,0 % Мп. Более выгодно |
||||
|
применять |
чугуны |
с |
||
|
повышенным |
содержанием |
|||
|
Мп (0,7-0,8 %), чем с |
||||
|
пониженным содержанием Si. |
||||
Рис. 2.14. Режим отжига на перлитный |
Избыточное |
содержание |
|||
марганца |
мало влияет |
на |
|||
ковкий чугун |
|||||
процесс |
|
первичной |
|||
|
|
||||
кристаллизации, поэтому процесс |
первой стадии граф итизации |
задерживается лишь незначительно, а снижение содержания кремния приводит к необходимости увеличения выдержки при первой стадии графитизации.
Как указывалось ранее, для получения перлитной структуры можно увеличить и содержание серы (0.3-0.5 %) при соблюдении отношения (Mn/S«1). Отжиг в этом случае проводится по режиму отжига ферритного КЧ. Сера способствует сфероидизации графита. Шаровидная форма графитовых включений выгодно отличает сернистые чугуны от обыкновенных перлитных КЧ.
Длительность отжига КЧ наиболее эффективно можно сократить повыш ением содержания графитизирующих элементов (С и Si) и одноврем енны м модиф ицированием белого чугуна элементами, подавляющими выделение первичного (пластинчатого) графита.
Перлитный КЧ может быть получен и дополнительной ТО готового ферритного чугуна:
•закалкой в масло с последующим отпуском на заданную твердость, что позволяет получить любую марку перлитного КЧ;
•нормализацией с последующим отпуском или без отпуска. Закалка и нормализация проводятся путем нагрева до температуры
выше критического интервала эвтектоидного превращения. При этом часть углерода вновь переходит в у-раствор, который, в зависимости от температуры и длительности выдержки и последующей скорости охлаждения, превращается перлит с различной формой и степенью дисперсности.
2.4.5.3. Обезуглероживающий отжиг белосердечного КЧ
Белосердечный КЧ (блестящий светлый излом) получают отжигом белого чугуна в окислительной среде. Исходный чугун должен иметь повышенное содержание углерода (2,8-3,4 %), пониженное содержание кремния (0,4-0,8 %), низкое содержание марганца (0,2-0,4 %) и повышенное содержание серы (0,15-0,25 %). Содержание фосфора и хрома должно быть низким (Р < 0,1 %; Сг < 0,05 %).
Полный цикл отжига продолжается несколько суток (до 140 ч). Температура нагрева достигает 1000-1050°С. Отливки укладывают в короба и засыпают свежей рудой с песком. Более экономичен отжиг в газовой среде состава: СОг = 8 %, СО = 26...28 %, Н2 = 24...26 %, Н2О = 12...14 %. О безуглероживание происходит минуя графитизацию. Постоянное обезуглероживание поверхности приводит к непрерывному растворению цементита и диффузии углерода из центра к поверхности, где углерод и окисляется. В итоге снаружи образуется полностью обезуглероженный слой глубиной несколько миллиметров, затем содержание углерода постепенно повышается, но и в центре отливки оно всегда меньше исходного. При таком распределении углерода, в конце отжига (при медленном охлаждении) на поверхности отливки образуется ф еррит.
Н есколько |
глубже |
появляется |
||
некоторое |
количество перлита. |
|||
В середине отливки |
содержится |
|||
графит в окружении феррита и |
||||
перлит. На рис. 2.15 показано, как |
||||
выглядит структура отливки |
из |
|||
белосердечного |
чугуна. Низкое |
|||
содержание |
крем ния |
и |
||
повышенное содержание серы |
||||
п р о т и в о д е й с т в у ю т |
||||
граф итизации |
|
цементита, |
||
входящ его |
в перлит, поэтому |
|||
чисто ф ерритной |
структуры |
в |
Рис. 2.15. Схема структуры отливки из |
белосердечном чугуне достичь не |
|
белосердечного КЧ: 1 - поверхность |
||
удается. |
||
отливки; 2 - поверхностное окисление; |
||
|
||
3 - феррит; 4 - перлит; 5 - графит |
|
2.5. Высокопрочные чугуны
Чугун с шаровидной формой графита (ЧШГ) занимает особое место среди железоуглеродистых сплавов. Временное сопротивление разрыву оку ЧШГ выше, чем у других чугунов, поэтому они ещё называются высокопрочными чугунами с шаровидным графитом (ВЧШГ)- Шаровидная форма графита в значительно меньшей степени ослабляет рабочее сечение матрицы и не создает таких концентраторов напряжений, как пластинчаты й графит. Механические и эксплуатационные свойства ЧШГ зависят от вида металлической матрицы. Ф ерритные ЧШГ имеют наивысшую пластичность и вязкость среди всех чугунов, а у бейнитных ЧШГ достаточно высокая для чугунов пластичность сочетается с максимальной прочностью.
По основным показателям механических свойств ЧШГ не уступают литым углеродистым сталям, а по некоторым и превосходят их. Так, предел текучести бейнитного чугуна ВЧ 100 в 2,5-3,0 раза выше, чем у обычных конструкционных сталей. В то же время литейные свойства ЧШГ лишь немного уступают свойствам серого чугуна. Это позволяет получать из ЧШГ качественные отливки с минимальной толщиной стенок (2,5-3,0 мм) и с практически неограниченной максимальной толщиной. Опробовано получение отливок с толщиной стенки до 1000 мм. Отливки из стали и КЧ имеют существенные ограничения по толщине стенки. Так, из-за плохой жидкотекучести стали назначают минимальную толщину стенок стальных отливок не менее 8 мм. Массивные стальные отливки требуют усиленного питания, т.е. увеличения расхода металла на установку прибылей.
Отливки из КЧ не должны быть толще 60 мм, чтобы предотвратить выделение графита в сырой отливке. Благодаря меньшей плотности и лучшим литейным свойствам, масса литых изделий из ЧШГ может быть на 10-20 % меньше массы стальных отливок, поковок и штамповок.
Из ЧШГ получают разнообразные отливки массой от нескольких десятков граммов (поршневые кольца) до 200 т (станины, корпуса и другие детали ответственного назначения). ЧШГ выгодно отличаются от других ж елезоуглеродисты х сплавов и по некоторым служебным свойствам (износостойкости, герметичности, усталостной прочности).
В настоящее время наблюдается непрерывный рост выпуска отливок из ЧШГ Их доля в общем объеме отливок из железных сплавов составляет в США около 33 %, а в Японии скоро достигнет 50 %. В России долгое время делалась ставка на стальное литье, поэтому доля отливок из ЧШГ невелика (менее 10 %). Но теперь темпы роста производства и потребления отливок из ЧШГ опережают темпы роста производства и потребления отливок из других сплавов черных металлов.
В разработку способов получения ЧШГ и изыскание условий успешного применения его в промышленности большой вклад внесли наши ученые: Н.А. Александров, К.П. Бунин, А.А. Горшков, Н.Г Гиршович, А.А. Жуков, Д.П. Иванов, Н.И. Клочнев, Б.С. Мильман, А.А. Рыжиков и др. Благодаря им всесторонне изучены и опробованы условия получения высококачественных изделий из этого материала, исследованы физико механические и технологические свойства ЧШГ, установлены области наиболее эф ф ективного его применения, найдены основные технологические параметры изготовления из него отливок и создано необходимое технологическое оборудование.
2.5.1. Марки, структура и механические свойства
Отечественный стандарт ГОСТ 7293-85 "Чугун с шаровидным графитом для отливок" содержит восемь марок высокопрочных чугунов (табл. 2.7).
Условное обозначение марки включает в себя буквы ВЧ высокопрочный чугун - и цифры, указывающие минимальное значение сгв 10'1 (в МПа). В более ранних стандартах в обозначении марки чугуна указывалось и относительное удлинение (в %), например - ВЧ 50-7
В соответствии с ГОСТом марка высокопрочного чугуна определяется его временным сопротивлением при растяжении и условным пределом текучести в литом состоянии или после термической обработки. Относительное удлинение, твердость и ударная вязкость определяются при наличии требований в нормативно-технической документации и должны соответствовать нормам, приведенным в приложении к ГОСТ 7293-85 (табл. 2.8).
Марки и механические свойства ЧШ Г по ГОСТ 7293-85
Марки |
Временное сопротивление |
Условный предел |
|
при растяжении су , МПа |
текучестиаю. МПа |
||
чугуна |
|||
не менее |
|
||
ВЧ 35 |
220 |
||
350 |
|||
ВЧ 40 |
400 |
250 |
|
ВЧ 45 |
450 |
310 |
|
ВЧ 50 |
500 |
320 |
|
ВЧ60 |
600 |
370 |
|
ВЧ 70 |
700 |
420 |
|
ВЧ 80 |
800 |
480 |
|
ВЧ 100 |
1000 |
700 |
По согласованию между изготовителем и заказчиком допускается устанавливать значения относительного удлинения, твердости и ударной вязкости, отличающиеся от значений, указанных в табл. 2.7
2.8.Таблица
О тносительное удлинение и тверд ость ЧШ Г
Марка чугуна |
Относительное удлинение 8, |
Твердость НВ |
|
% (не менее) |
|||
|
140-170 |
||
ВЧ 35 |
22 |
||
ВЧ 40 |
15 |
140-202 |
|
ВЧ 45 |
10 |
140-225 |
|
ВЧ 50 |
7 |
153-245 |
|
ВЧ 60 |
3 |
192-277 |
|
ВЧ 70 |
2 |
228-302 |
|
ВЧ 80 |
2 |
248-351 |
|
ВЧ 100 |
2 |
270-360 |
Примечание: чугун марки ВЧ 35 должен иметь среднее значение ударной вязкости KCV не менее 21 Дж/см2 при температуре плюс 20 °С и 15 Дж/см2 при температуре минус 40 °С, минимальное значение ударной вязкости должно быть не менее 17 Дж/см2 при температуре плюс 20 °С и 11 Дж/см2 при температуре минус 40 °С.
Механические свойства ЧШГ, указанные в табл. 2.7 и 2.8, определяют на образцах, изготовленных из отдельно отлитых (или прилитых к отливкам) проб, ф орма и размеры которых показаны на рис. 2.16.
Рис. 2.16. Отдельно отлитые заготовки для механических испытаний ВЧШГ
Свойства у отливок из ЧШГ зависят от толщины стенки, хотя и в меньшей степени, чем у отливок из КЧ или СЧ. Влияние толщины стенки отливки проявляется: из-за уменьшения плотности отливок в результате увеличения усадочных дефектов, возрастания степени образования микротрещин, неоднородностей и несовершенства кристаллического строения, влияющих на механические свойства. Поэтому прочность и твердость ЧШГ в реальных отливках почти всегда ниже, чем в пробах. Относительное удлинение в отливках с толщиной стенки менее 50 мм выше, чем в стандартных пробах.
Главной особенностью структуры высокопрочных чугунов является форма графитовых включений. В соответствии с ГОСТ 3443-87 в чугуне может быть 5 вариантов шаровидного графита. Они показаны на рис. 2.17 Количество и размеры графитовых включений могут меняться в широких пределах. Так, шкала размеров включений предусматривает деление чугунов
на 6 баллов |
от |
ШГр 15 |
до ШГр 350; площадь графита |
может достигать |
12 %. |
|
|
М еталлическая |
матрица |
может быть ферритной, перлитной, |
бейнитной и смешанной. На рис. 2.18 приведены некоторые характерные типы микроструктуры высокопрочных чугунов с шаровидным графитом.
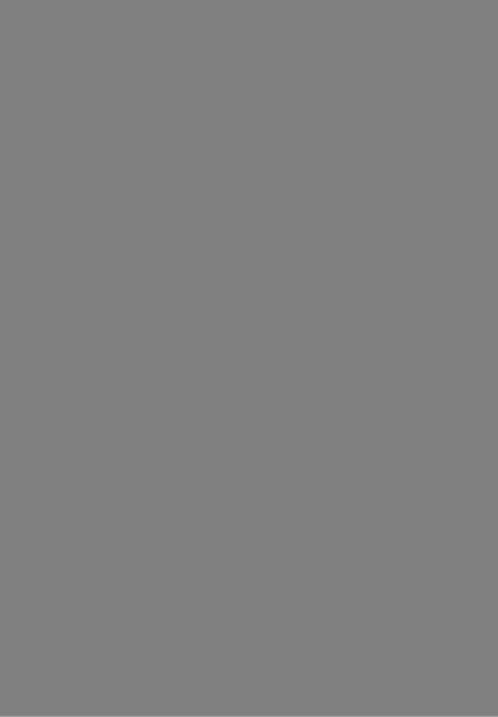
ГУ 9
DL «
о
-Ф
■ел
-ФЗ
а
в
Рис. 2.18. Некоторые характерные микроструктуры ЧШГ: а - ферритная, х 100; б - перлитно-ферритная (бычий глаз),х 200; в мартенсит ная,Х300; г - ферритно-бейнитная (твердый глаз),х300
В зависимости от типа металлической матрицы у ВЧШГ могут наблюдаться различные сочетания прочностных, пластических и других характеристик механических и служебных свойств. Чугуны ВЧ 35 и ВЧ 40 имеют ферритную матрицу. Они наиболее пластичные и малопрочные. Самый прочный чугун марки ВЧ 100 имеет бейнитную матрицу. К перлитным относятся чугуны ВЧ60, ВЧ 70 и ВЧ 80, а остальные имеют перлитно-ферритную матрицу. Структура металлической матрицы может быть изменена путем термической обработки. Так, структура, известная под названием "твердый глаз" (см. рис. 2.18, г), получается изотермической закалкой чугуна, прошедшего предварительно ферритизирующий отжиг. Она представляет собой микрооболочки бейнита или сорбита отпуска вокруг шаровидного графита при пластичном феррите в остальной части матрицы. При наличии подобной микроструктуры существенно укрепляется межфазная поверхность матрица - шаровидный графит.
У чугуна со структурой «т вердый глаз» ударная вязкость в 1,5- 2,0 раза выше, чем у перлитного чугуна со структурой «бы чий глаз» («мягкий глаз») (см. рис. 2.18, б). Такая структура характеризуется тем, что вокруг графита располагается тонкая ф ерритная оболочка, а остальная часть матрицы перлитная. Рост эвтектического графита при кристаллизации и охлаждении чугуна происходит за счет диффузии углерода из аустенита. В результате поверхностные слои аустенита обедняются углеродом и при эвтектоидном превращении вокруг графита остается ф еррит Такое разнообразие микроструктуры ВЧШГ предопределяет большой диапазон значений механических свойств, в том числе и свойств, не регламентированных ГОСТом.
При статических нагрузках ЧШГ лучш е всего работаю т в условиях сжатия. Предел прочности при сжатии у них в 3,0-3,5 раза выше, чем при растяжении. Эте связано с тем, что граф ит влияет отрицательно на сопротивление сжатию в меньшей степени, чем на сопротивление растяжению.
По ударной вязкости ЧШГ находятся на одном уровне с КЧ. Наиболее высокие значения ударной вязкости имеют ферритные чугуны (ВЧ 35, ВЧ 40), но и перлитные чугуны являются достаточно вязким материалом.
Способность конструкционных материалов нести наиболее высокие нагрузки при наименьших деформациях и массе можно оценить обобщённым показателемС702Е/р2, гдест02 - условный предел текучести, Е - модуль упругости, р - плотность:
Материал |
(СУ02Е /р 2)-10-11, П а-м 6-кг 2 |
ЧШГ |
6,81-26,38 |
КЧ |
5,51-17,84 |
ЧПГ |
1,04-7,62 |
Сталь |
6,53-11,73 |
Этот показатель позволяет выбрать наиболее выгодный, с точки зрения минимальной массы изделия, материал, и здесь ЧШГ имеют неоспоримое преимущество перед другими черными сплавами:
Аналогичным, но более простым показателем, можно считать отношение предела текучести (в отличие от серого чугуна ЧШГ имеет предел текучести при растяжении, сжатии и сдвиге) к пределу прочности при растяжении. Оно составляет 0,7-0,8 (у стали это отношение 0,5- 0,6). Так как конструкции рассчитывают на прочность, как правило, по пределу текучести, то для уменьшения массы машин и снижения расхода м атериалов выгоднее использовать материал, у которого это отношение больше.
Циклическая вязкость или демпфирующая способность материала гасить возникающие при работе механизмов вибрации у ЧШГ ниже, чем у ЧПГ, но значительно выше, чем у стали. Эта характеристика перлито ферритного ЧШГ при растяжениях 50-100 МПа составляет 4-6 %, в то время как у стали - 0,3-0,6 %.
Изделия из ЧШГ могут успешно работать при повышенных (до 500-550 °С) и пониженных до (-196 °С) температурах.
2.5.2.Физические и литейные свойства
Физические свойства ЧШГ несколько отличаются от аналогичны х свойств СЧ. В первую очередь это объясняется разобщенностью графитовых включений.
Плот ност ь ниже, чем у углеродистой стали (% на 8 %) и близка к плотности СЧ с одинаковой металлической основой. Более плотными являются бейнитные чугуны:
Матрица |
р, кг/м3 |
Ферритная |
7100-7200 |
Перлитная |
7200-7300 |
Бейнитная |
7250-7350 |
Из теплоф изических |
характеристик следует отметить |
т еплопроводност ь, которая существенно ниже, чем у СЧ (« в 1,5 раза), поэтому в отливках из ВЧШГ наблюдаются более высокие термические напряжения и эти отливки хуже работают в условиях знакопеременных тепловых нагрузок.
Электросопротивление и магнитные свойства ЧШГ являются структурно-чувствительными. Они зависят от химического состава и количественного соотнош ения структурных составляющих. Это позволяет использовать электрические и магнитные методы контроля для определения структуры ЧШГ
Из-за повышенного содержания углерода и кремния по литейным свойствам ЧШГ несколько отличаются от других чугунов. Так, жидкот екучест ь значительно лучше, чем у КЧ или СЧ высоких марок, и при равных перегревах почти в 2 раза превышает жидкотекучесть стали. Это способствует получению фасонных отливок с толщиной стенки 3- 5 мм. Для определения наименьшей толщины стенок отливок из ЧШГ можно воспользоваться следующей эмпирической зависимостью, полученной при изучении заполняемости отливок в производственных условиях:
5 ЧШГ^ L/300 + 3 мм,
где 5 - толщина стенки отливки, мм; L - длина стенки в направлении течения металла, мм. Для стали эта зависимость имеет вид
5СТ> L/200 + 4 мм.
Сопоставление этих зависимостей показывает, что отливки из ЧШГ только за счет допустимого уменьшения толщины стенок могут быть облегчены на 25 % (минимальная толщина стенок стальных отливок в большинстве случаев ограничивается ее малой жидкотекучестью, а не прочностью). Если учесть, что плотность этого чугуна на 8-10 % меньше плотности стали, то общую массу этих отливок по сравнению со стальными можно уменьшить на 33-35 %.
Склонност ь к отделу ниже, чем у СЧ. |
|
Общая линейная усадка ВЧШГ, как и СЧ, невелика |
%). Однако |
усадка в жидком состоянии и предусадочное расширение существенно выше, чем у СЧ. Этим объясняется повышенная склонность ЧШГ к образованию хотя и локализованных, но больших по объему усадочных дефектов. Объем усадочных раковин у ЧШГ может достигать 7,5-9,0 %. Это в 4-5 раз больше, чем у серого чугуна. При литье в податливые песчано глинистые формы из-за большого предусадочного расширения происходит раздутие формы. В этом случае после образования на отливке твердой корки внутри ее будет наблюдаться деф ицит расплава. При дальнейшем охлаждении на поверхности отливки могут появиться наружные усадочные раковины (утяжины). Если жесткость формы такова, что она препятствует расширению, то увеличение внутреннего объема сплава при выделении графита (выделение из расплава 1 % С в виде графита увеличивает объем расплава примерно на 2 %) будет компенсировать процессы объемной усадки. В доэвтектических чугунах питание отливок затруднено из-за образования прочного скелета из разветвленных первичных кристаллов аустенита, в результате чего образуется рассеянная усадочная пористость.
Если использовать исходный металл эвтектического или заэвтектического состава и менее податливые формы, то можно исключить применение питающих прибылей и получать плотные отливки.
Из-за более высокого модуля упругости и пониженной теплопроводности, в отливках из ЧШГ образуются повышенные литейные напряжения. Для предотвращения образования холодных трещин и коробления отливок необходимо проектировать более жесткую конструкцию отливки и равномерно охлаждать ее после затвердевания.
Отливки из ЧШГ, в отличие от стальных, практически не склонны к образованию горячих трещин. Это обусловлено их меньшей линейной усадкой и большим предусадочным расширением.
2.5.3. Служебные свойства
Широкое распространение в промышленности ЧШГ получили не только из-за высоких механических свойств. Они обладают и некоторыми повышенными служебными свойствами.
По мере увеличения количества перлитной и бейнитной составляющих возрастает износостойкость чугуна. Детали из высоких марок ЧШГ могут работать в условиях абразивного износа и сухого трения. Низкий коэффициент трения перлитных ЧШГ позволяет использовать их в качестве антифрикционного материала.
По герметичности ЧШГ существенно превосходит СЧ, так как в нем граф итные включения изолированы друг от друга, поэтому отсутствует граф итная пористость, и отливки из ЧШГ могут выдерживать давление более 50 МПа.
Коррозионная стойкость ЧШГ не ниже, чем у СЧ, и значительно выше, чем у углеродистой стали. Трубы из ЧШГ в условиях почвенной коррозии служат дольше, чем трубы из СЧ. Коррозионная стойкость ЧШГ может быть повышена небольшими добавками Ni, Си, AI.
2.5.4. Получение графита шаровидной формы
Наиболее ответственным моментом в производстве отливок из вы сокопрочного чугуна является получение графита правильной шаровидной формы.
Формирование шаровидного графита достигается путем модифицирования чугуна при плавке или разливке. На форму, размеры и количество граф итовых включений оказывают влияние: способ модифицирования, химический состав исходного чугуна, шихтовые материалы и другие условия плавки, а также условия кристаллизации и охлаждения отливки.
2.5.4.1. Выбор химического состава
Химический состав является одним из основных факторов, определяющих физико-механические и эксплуатационные свойства ЧШГ Рекомендуемый химический состав различных марок чугунов приведен в табл. 2.9.
Углерод в ЧШГ не оказывает решающего влияния (в отличие от серых чугунов) на механические свойства. Если в СЧ высокие механические свойства могут быть получены только при пониженном содержании углерода, то, как видно из табл. 2.10, во всех марках ЧШГ содержание углерода значительно выше, чем в СЧ. Оно примерно одинаково и находится в пределах 3,2-3,8 %. Только в отливках с толщиной стенки более 100 мм содержание углерода может быть снижено до 2,7-3,2 %.
При установлении химического состава исходного металла, обеспечивающего хорошие литейные свойства ЧШГ, необходимо соблюдать следующие условия. Исходный металл должен иметь заэвтектический состав, т.е. Сэ = С + 0,3Si > 4,3 %.
При этом содержание углерода в нем должно быть не менее 3,6 %. Минимальное содержание кремния, необходимое для протекания
затвердевания по стабильной системе, зависит от толщины стенки отливки и составляет 1,5-2,5 % (нижнее значение для массивных отливок с толщиной более 80 мм, а верхнее - для отливок толщиной < 10 мм).
|
|
|
|
Таблица 2.9 |
|
|
Рекомендуемый химический состав ЧШ Г (по ГОСТ 7293-85) |
||||
|
|
Массовая доля элементов, % |
|
||
Марка |
Углерод/кремний при толщине стенки |
|
|||
чугуна |
|
отливки, мм |
|
Марганец |
|
|
до 50 |
50-100 |
св. 100 |
|
|
ВЧ 35 |
3.3-3.8 |
- 3,0-3,5 |
2.7-3.2 |
0,2-0,6 |
|
1,9-2,9 |
1,3-1,7 |
0,8-1,5 |
|||
|
|||||
ВЧ 40 |
3.3-3.8 |
3.0-3.5 |
2,7-3,2 |
0,2-0,6 |
|
1,9-2,9 |
1,2-1,7 |
0,5-1,5 |
|||
|
|||||
ВЧ 45 |
3,3-3,8 |
3.0-3.5 |
2,7-3,2 |
0,3-0,7 |
|
1,9-2,9 |
1.3-1.7 |
0,5-1,5 |
|||
|
|||||
|
|
||||
ВЧ 50 |
3,2-3,7 |
3,0-3,3 |
2,7-3,2 |
0,3-0,7 |
|
1,9-2,9 |
2,2-2,6 |
0,8-1,5 |
|||
|
|
||||
ВЧ60 |
3,2-3,6 |
3.0-3.3 |
|
0,4-0,7 |
|
2,4-2,6 |
2,4-2,8 |
|
|||
|
|
|
|||
ВЧ 70 |
3,2-3,6 |
3.0-3.3 |
|
0,4-0,7 |
|
2,6-2,9 |
2,6-2,9 |
|
|||
|
|
|
|||
ВЧ 80 |
3.2-3.6 |
|
|
0,4-0,7 |
|
2,6-2,9 |
|
|
|||
|
|
|
|
||
ВЧ 100 |
3,2-3,6 |
|
|
0,4-0,7 |
|
3,0-3,8 |
|
|
|||
|
|
|
|
Изменяя концентрацию кремния, можно получить различную структуру металлической матрицы и соответственно различный уровень механических свойств, т.е. различные марки чугуна. Устойчивая ферритная структура в литом состоянии формируется при содержании кремния более 3 %. Однако чем больше кремния в феррите, тем ниже его пластичность, а при концентрации > 3,5 % Si появляется хрупкость, даже при обычном содержании Мп и Р. Наиболее высокие значения пластичности и вязкости достигаются при 2,6-2,8 % Si. Однако кремний склонен к ликвации в феррите, поэтому для получения чугунов с высокой пластичностью содержание кремния лучше ограничивать до 2,0-2,4 %, а для достижения чисто ферритной структуры применять ТО.
При |
меньш ем |
содержании |
Ж 3,5 |
|
|
|
|
|
|
|
|
кремния |
в |
тонкостенны х |
|
|
kj |
|
|
|
|||
отливках возможно появление |
|
|
|
|
|
|
|||||
отбела. |
|
О птимальное |
: з,о |
|
|
|
|
|
|||
соотнош ение |
кремния и |
|
|
Флотаци 1 графита |
|||||||
|
|
|
|||||||||
углерода в ЧШГ можно найти по |
|
|
|
|
N |
||||||
диаграмме, приведенной на рис. |
! 2>5 |
|
к Ч ! \ |
|
|||||||
2.19. Для тонкостенных отливок |
|
|
|
Оптимальная |
|||||||
необходимо выбирать более |
|
|
Область |
( |
|
|
|||||
|
|
|
область |
|
|||||||
|
повышали X X |
\ |
|
||||||||
высокоуглеродистые чугуны, |
2,0 |
усадснны X |
' |
|
|
||||||
чем указанные на рис. 2.19 и в |
|
|
раковин |
|
|
|
|
|
|||
|
|
|
|
|
|
|
|
||||
табл. 2.10. При толщине стенки |
|
|
|
Тенденция к отбелив мию |
|
||||||
от 3 до 6 мм содержание |
1,5 |
|
|
|
|||||||
углерода может быть 4.0-4.4 %. |
3,4 |
3,5 |
3,6 |
3,7 |
3,8 |
3,9 |
|||||
Для |
ограничения флотации |
|
|
|
Массовая доля уалврода, % |
|
|||||
|
|
|
|
|
|
|
|
||||
графита, |
необходимо, чтобы |
|
|
|
|
|
|
|
|
||
углеродный эквивалент чугуна |
|
Рис. 2.19. Оптимальные соотношения |
|
||||||||
Сэ не превышал 4,6 (Сэ = |
|
|
|||||||||
|
|
С и Si, рекомендуемые для ВЧШГ |
|
||||||||
=С + 0,3Si < 4,6). |
|
|
|
||||||||
|
|
|
|
|
|
|
|
||||
|
М арганец способствует увеличению |
количества |
перлита |
и |
соответственно уменьшению феррита в матрице. Для получения чисто ферритной основы его содержание не должно превышать 0,3 %. В перлитных и бейнитных чугунах содержание Мп достигает 0,7 %. Для деталей, работающих в условиях повышенного износа (коленчатые валы и др.), рекомендуется чугун, содержащий 1,20-1,35 % Мп.
Фосфор, как и кремний, снижает пластичность и ударную вязкость, поэтому его содержание не должно превышать 0,1 %, а в отливках из ферритного чугуна и в толстостенных отливках его должно быть меньше 0,05 %.
Одним из условий успешного проведения сфероидизирующего модифицирования является ограничение содержания серы до 0,02 % и ниже (0,015 % в ВЧ 70 и 0,01 % в ВЧ 80 и ВЧ 100).
Примеси, таких элементов, как хром, медь, никель усложняют получение ферритной структуры, поэтому в чугунах ВЧ 35, ВЧ 40, ВЧ 45 они нежелательны.
Должно быть ограничено и содержание микропримесей демодиф икат оров, препятствующих образованию шаровидного графита в процессе модифицирования (%): РЬ - 0,009, Sn - 0,13, Sb - 0,026, Bi - 0,003, Ti - 0,04, As - 0,08, Al - 0,3.
Влияние демодификаторов частично или полностью устраняется добавкой рем одиф икат оров, например церия и других РЗМ.
Получение графита шаровидной формы основано на раздельной или совместной обработке жидкого чугуна с ф е р о и д и зи р у ю и ц и м и модиф икат орами, магнием, кальцием, РЗМ и комплексными присадками, содержащими указанные сфероидизирующие вещества в различных сочетаниях. Механизм этого процесса рассмотрен в раздел1.6.4.
Наибольшее распространение в качестве сфероидизирующего элемента получил магний. На практике надежно и широко освоены следующие способы получения шаровидного графита:
♦обработка жидкого металла технически чистым магнием;
♦введение магниевых лигатур с никелем, медью или ферросилицием;
применение комплексных модификаторов, содержащих магний и ♦ другие сфероидизирующие элементы.
Магний очень легкий металл, имеющий плотность 1738 кг/м3 Температуры плавления и кипения магния соответственно 651 и 1107 °С. При введении чистого магния в расплав с температурой 1400 °С он частично сгорает с обильным выделением белого дыма, значительным пироэффектом и частично испаряется. Давление паров магния достигает 0,8 Мпа (8 ат) и более, поэтому наблюдаются выбросы металла из ковша. Чтобы повысить эффективность усвоения магния и обеспечить безопасность труда рабочих, необходимо вводить магний при повышенном давлении над расплавом или использовать некоторые другие специальные методы модифицирования (табл. 2.10).
Требуемое остаточное содержание магния в чугуне для получения шаровидного графита составляет 0,04-0,06 %. Из-за различных потерь количество вводимого с модификатором магния существенно больше. Оно зависит от исходного содержания серы (S), времени (Т, мин) от момента завершения модифицирования до окончания заливки форм, температуры (t°C) металла в ковше, коэффициента (а ) усвоения магния (от 0,1 до 0,9, в зависимости от способа модифицирования и вида модификатора) и определяется по формуле:
Мд = [0,76 (S - 0,01) + (0,04-Ю,06) +Т-10'3] (f/1450)2 1/а.
В зависимости от перечисленных условий количество магния, вводимого в чугун, колеблется от 0,1 до 0,35 %.
Наиболее простым и экономичным является первый способ, т.е. обработка чистым магнием. Однако для его реализации необходимы дополнительны е производственны е площ ади и специальное оборудование: герметизированные ковши, автоклавы и т.д. Поэтому его целесообразно применять в условиях мелкосерийного производства сравнительно крупных или средних отливок.
Методы модифицирования ЧШГ магнием
Метод
обработки
В герметизированном ковше конвертерного типа металлическим магнием
Вавтоклаве металли ческим магнием
Воткрытом ковше тя желыми лигатурами
Воткрытом ковше ли гатурой, пригружаемой стальной высеч кой (сэндвич-процесс)
Вреакционной камере литниковой системы (инмолд-процесс)
Сущность |
|
Область |
метода |
|
применения |
В реакционную камеру |
Для мелкосерийного |
|
ковша загружают Мд, |
|
производства средних |
заливают чугун, герме- |
отливок |
|
тизируют и поворачи |
|
|
вают ковш. При пово |
|
|
роте ковша чугун зали |
|
|
вает реакционную ка |
|
|
меру |
__ |
__ |
Ковш с чугуном поме- |
|
Для мелкосерийного |
щают в автоклав, соз- |
|
производства мелких и |
дают давление и специ- |
средних отливок |
|
альным устройством |
|
|
вводят Mq |
|
|
Лигатуры NiMg или |
|
Для любых условий |
CuNiMg загружают на |
|
производства |
дно ковша перед залив |
|
|
кой чугуна |
|
|
Лигатуру FeSiMg по- |
|
Для любых условий |
мещают в углубление |
|
производства |
на дне ковша, прикры |
|
|
вают стальной высеч |
|
|
кой и заливают чугун |
|
|
Лигатуру FeSiMg по- |
|
Для поточно-массово- |
мещают в реакционную |
го производства сред- |
|
камеру литниковой |
|
них отливок |
системы перед залив |
|
|
кой формы |
|
|
Более простым является способ, основанный на применении различных магниевых лигатур или смесей, содержащих до 15 % магния. Лигатуры магния с медью и никелем имеют высокую плотность (6000-7500 кг/м3 ), сопоставимую с плотностью расплава, поэтому они не всплывают на поверхность. Когда необходима чисто ферритная структура, никель и медь нежелательны, так как они способствуют перлитизации чугуна. Этот способ более дорогой и энергоемкий, так как требует дополнительных затрат на приготовление лигатур.
Его целесообразно использовать в условиях крупносерийного и массового производства сравнительно мелких отливок.
Ш ирокое распространение получили комплексны е лигатуры, дополнительно содержащие кремний, кальций и РЗМ. К ним относятся: кремнемагниевые ФСМг2 - ФСМгЭ; кремнемагнийкальциевые ЖКМК-1 -ЖКМК-6 и КМ-1 - КМ-8. Введение в состав магниевых лигатур РЗМ, бария,
стронция увеличивает их живучесть и повы ш ает |
эф ф ективность |
м одиф ицирования. Этот способ получения ЧШГ |
является более |
универсальным. |
|
Кроме магниевых прим еняю т иттриевы е и цериевые модификаторы. Иттриевые модификаторы содержат от 99,8 (ИтМ-1) до 93 % (ИтМ-5) иттрия. Их чаще применяют совместно с лигатурами, содержащ ими магний. И спользование иттрия ограничивается дефицитностью и высокой стоимостью.
К модиф икаторам на_основе церия относятся: ф ерроцерий, цериевый мишметалл, ФЦМ-5, МЦ40 - МЦ75, ММ-5 и др. Они содержат не менее 40 % церия, а также лантан, неодим, празеодим и другие РЗМ.
Эффективность цериевых и иттриевых модификаторов ниже, чем магнийсодержащих. После модифицирования ими графит часто имеет неправильную шаровидную форму (компактный графит).
Для получения вы сококачественного ЧШГ обработки только сфероидизирующ ими модиф икаторами недостаточно. Необходимо дополнительное граф ит изирую щ ее м одиф ицирование чугуна. Оно способствует образованию зародыш ей граф ита и увеличивает количество включений шаровидного графита на единицу площади, улучшает форму включений, подавляет образование карбидов в литой структуре, устраняет структурную неоднородность в отливке, способствует формированию ферритной матрицы и снижает склонность к образованию усадочных дефектов в отливках. Для получения плотных отливок граф итизирующ ее м одиф ицирование должно обеспечить образование эвтектического графита, достаточного для компенсации объемной усадки, т.е. вызвать предусадочное расширение не менее 0,4- -0,5% . При одинаковом составе и структуре ЧШГ и ЧШГ, дополнительно обработанного графитизирующими модификаторами, последний имеет более мелкий графит и более дисперсную матрицу. Он имеет более высокие прочностные показатели, а его относительное удлинение возрастает в 1,5-2,0 раза.
В качестве инокуляторов (в современной технической литературе часто используют биологический термин инокуляция, обозначающий введение живых микроорганизмов в питательную среду, отсюда название любых вводимых добавок инокуляторы ) чаще всего применяют ферросилиций марок ФС 75 и ФС 80, содержащий примеси кальция, бария, алюминия и других элем ентов. Применение раф инированного ферросилиция неэффективно.
В отливках из чугуна, модифицированного магнием, часто наблюдаются дефекты в в и д е " черных пятен", которые представляют собой скопления
неметаллических фаз, состоящих из окислов и сульфидов магния, а также кристаллов шаровидного графита. Чтобы избежать появления "черных п я те н ", н е о б хо д и м о и сп о л ь зо ва ть для м одиф ицирования чугун
заэвтектического состава с углеродным эквивалентом 4,6 > С э>4,3 с
минимальным содержанием серы и не допускать превышения заданного
остаточного содержания магния.
2.5.5. Термическая обработка ВЧШГ
Термическая обработка отливок из ВЧШГ проводится с целями:
повысить физико-механические свойства, снять внутренние напряжения,
у л уч ш и ть |
о б р а б а ты в а е м о сть резанием |
и |
т.д . Выбор режима |
|
терм ической обработки производится исходя |
из требуемых свойств |
|||
ч угун а в |
д е та л и , исход ной м и кроструктуры |
чугуна в отливке и |
||
хи м и ч е ско го состава чугуна. Чащ е всего |
свойства |
чугуна в литом |
||
со с то я н и и |
о б е сп е ч и в а ю т тре б о ва н и я конструкции |
и терм ическая |
обработка не проводится. Для улучшения физико-механических свойств
сложных и массивных отливок, ТО которых затруднена и может привести к деф ормациям, рекомендуется использовать легирование и подбирать режим охлаждения при остывании отливок. В ряде случаев ТО может
быть проведена два раза: сначала для улучшения обрабатывемости
отливки, а затем после механической обработки для получения заданных
механических свойств чугуна в детали. Ниже приведен краткий обзор
наиболее употребительных способов ТО.
Высокотемпературный графитизируюиций отжиг применяют для устранения в чугуне структурно-свободного цементита, т.е. отбела. В некоторы х случаях отбел модиф ицированного чугуна технологически неизбежен (тонкостенное и кокильное литье, некоторые легированные
чугуны и др .) и отжиг обязательно предусматривается технологией
литья . В д р уги х случаях отжиг может применяться выборочно для устранения брака.
Д ля полной граф итизации структурно-свободного цементита необходим медленный нагрев со скоростью 100-300 °С/ч до температуры
950 °С. Длительность выдержки прямо пропорциональна толщине стенки.
Для большинства машиностроительных отливок она не превышает 2 ч.
Охлаждают отливки с печью или на воздухе.
Низкот емперат урный графитизирующий отжиг проводят для
получения ферритной матрицы вместо перлитной или феррито-перлитной.
Заключается отжиг в нагреве отливок до температуры 720-780 °С, выдержке 1-3 ч, охлаждении с печью до 600-680 °С, а затем на воздухе, в масле или в воде.
Н о р м а л и за ц и я |
пр и м еняе тся |
для ф ерритны х |
или |
ф ер р и то |
перлитны х ВЧШГ с целью получения |
чисто перлитны х или |
перлито |
||
ф е р р и тн ы х чугун ов с |
п о в ы ш е н н о й |
тв е р д о с ть ю , |
п р о ч н о сть ю и |
износостойкостью . Пластичность, вязкость и обрабаты ваемость после нормализации снижаю тся. Н агрев производят до 920 -950 °С. В ходе
выдержки (не более 3 ч) происходит растворение углерода в аустените, а
при последую щ ем бы стром охлаж дении на воздухе обеспечивается
эвтектоидное превращение с образованием перлита.
Сф ероидизирующ ий отжиг проводят для получения зернистого
перлита. Он отличается от нормализации тем, что после выдержки отливки
охлаждают с печью до 700 °С и выдерживают при этой температуре еще 3-
- 5 ч (для образования зернистого перлита) с последующим охлаждением
на воздухе или в масле.
Закалка и от пуск позволяют |
получить максимальную твердость |
и прочность. Отливки нагревают до 880 |
-920 °С и выдерживают в течение 30 |
мин. Закалка простых по конфигурации отливок осуществляется в воде, а
сложных - в масле. Температура последующ его отпуска выбирается в
зависимости от требований к твердости, прочности и пластичности.
Низкотемпературный отжиг (искусственное старение) проводят
для снятия внутренних напряжений и стабилизации размеров. Внутренние напряжения в отливках из ВЧШГ в 2-3 раза больше, чем в отливках из
серого чугуна, поэтом у |
все о тветственны е детали, разностенны е и |
сл о ж н о й ко н ф и гур а ц и и |
д о л ж н ы п о д в е р га ть с я о тж и гу д л я снятия |
внутренних напряжений, если они не проходят более сложной ТО. Отжиг
происходит в течение 2-8 ч (в зависимости от толщины) при температуре 620-650 °С. Нагрев и охлаждение должны быть медленными.
И зот ерм ическая закалка ф орм ирует бейнитны е структуры металлической основы чугуна, которые обеспечиваю т самые высокие прочностные свойства при сравнительно высокой пластичности и вязкости.
Особенность изотермической закалки заключается в том что превращение
аустенита проводят в закалочных средах (расплавы щелочей и солей) с температурой 250-450 °С (выше мартенситного превращения).
2.5.6.Применение высокопрочных чугунов
Чугун с шаровидным графитом используется во многих областях техники взамен литой и кованой стали, серого и ковкого чугуна. Половину м и р о во го п р о и зв о д ств а с о с та в л я ю т ц е н тр о б е ж н о л и ты е трубы диаметром от 50 до 2800 мм и длиной от 2 до 8 м. Их долговечность превышает долговечность стальных труб в 3-8 раз. Тюбинги (туннельные сегменты) из ВЧШГ в 2 раза легче, чем из серого чугуна и более надежны
в эксплуатации.
В тяжелом и энергетическом машиностроении из ЧШГ марок ВЧ 40, ВЧ 45, ВЧ 50 изготовляют детали паровых, газовых и гидротурбин, детали прокатных
станов и дробильно-размольного оборудования. Крупные корпусные детали
турбин массой до 50 т из ферритного чугуна получают без термической
обработки.
В металлургической промышленности наибольший удельный вес
составляют отливки валков прокатных станов - основного инструмента
прокатного производства. Стойкость валков из ВЧШГ в 3-5 раз больше,
чем валков из стали. Еще лучш е эксплуатирую тся валки из ВЧШГ,
легированного никелем, молибденом, хромом.
Особенно широкая номенклатура отливок из чугуна с шаровидным граф итом освоена в сельхозмаш иностроении, автомобилестроении и
с та н ко с тр о е н и и . |
Ч угун м арок |
ВЧ 60, |
ВЧ |
70 |
в |
мировом |
а в то м о б и л е с тр о е н и и и сп о л ь зую т |
взам ен |
стального |
проката для |
|||
и зго то вл е н и я р а сп р е д е л и те л ьн ы х |
и коленчаты х |
валов, |
крыш ек и |
стаканов подшипников и др. Из чугунов ВЧ 45 и ВЧ 50 отливают корпуса редукторов, барабаны, кронштейны, тормозные колодки, диски катков и т.п. Ранее эти детали были из литой стали. Блок-картеры, головки
цилиндров, выхлопные коллекторы, детали турбин и насосов получают из чугуна ВЧ 50 (вместо серого чугуна), а ступицы колес автомобилей, корпуса дифференциалов и т.д. - из чугуна ВЧ 40 (вместо ковкого чугуна).
М ировое производство бейнитных ЧШГ пока невелико, но эти высокопрочные, высоковязкие и высокоизносостойкие сплавы считаются наиболее перспективными. Они эффективно заменяют кованые стали, в том числе цем ентованны е, в производстве зубчатых колес, а их
номенклатура и потенциальная потребность огромны. Особо высокий те хн и ко -э ко н о м и ч е с ки й эф ф ект о б еспечивает производство из бейнитного ЧШГ коленвалов в автомобилестроении.
2.6. Чугуны с вермикулярным графитом
Вермикулярный (червеобразный) графит (ВГ), как и пластинчатый (ПГ), имеет ф орму взаимосвязанных лепестков. Однако эти лепестки отличаю тся меньш ей степенью неравновесности. Отношение длины
лепестка ВГ к его толщине обычно находится в пределах от 2 до 10, а у
ПГ значительно превыш ает 10. Лепестки ВГ имеют меньшие размеры, чем лепестки ПГ, и округлые кромки. Такая форма графита является промежуточной между пластинчатой и шаровидной. На рис. 2.20 показаны
три основные разновидности вермикулярного графита в соответствии с ГОСТ 3443-87.
Более характерными для чугуна являются извилистая (ВГф2) и
утолщенная (ВГфЗ) формы графитовых включений. В чугуне с ферритной
металлической основой обычно наблюдается извилистый червеобразный
графит.
Ч е р в е о б р а зн а я |
утол щ е н н ая |
ф ор м а |
гр а ф и та |
чащ е |
о б р а зуе тся в |
|||||
н и зко л е ги р о в а н н о м |
чугуне |
с п е р л и тн о й |
м а тр и ц е й |
и о тл и ч а е тс я |
||||||
разнообразием размеров и формы. |
|
|
|
|
|
|||||
Узелковая |
|
|
И звилистая |
|
|
Утолщ енная |
||||
|
£ |
|
о |
|
|
|
/ |
|
|
|
' |
\ |
|
|
|
|
|
|
|
||
J |
|
|
|
, |
|
|
|
|||
|
j* v .И1 |
i |
V |
L |
‘ / , |
|
|
|
||
• '* - |
Л-Ч |
(, |
\ |
w |
1 Ж' |
К |
|
|
|
|
. y |
|
|
|
|
|
|
|
|||
|
.U i. |
|
|
V |
. v |
Л |
- . |
|
|
|
|
|
|
f |
|
|
( |
|
|
|
|
v |
|
|
|
\ * V |
|
|
|
|
||
|
|
|
|
\ |
|
|
|
|
|
|
|
•*:**•>• |
|
|
|
|
|
|
|
||
|
ВГф1 |
|
|
ВГф2 |
|
|
|
|
ВГфЗ |
|
Рис. 2.20. Форма включений графита в ЧВГ. Ш кала 2 А ГОСТ 3443 - 87. хЮ О |
||||||||||
Д о л гое |
врем я ВГ |
р а ссм а тр и в а л ся |
как |
вы р ож д е нн а я ф орм а |
гр а ф и то вы х в кл ю ч е н и й ,п о л у ч е н н а я в р е зу л ь та те н е п р а в и л ь н о го
м од и ф и ци р о вани я . Т ол ько с 1968 года ЧВ Г стали и сп о л ь зо ва ть в промыш ленности как самостоятельный вид чугуна. Оказалось, что при
содержании в структуре не менее 80-90 % ВГ (остальное - ШГ, ПГ не |
|
д о п уска е тся ) чугун о б л а д а е т |
сп е ц и ф и ч е ски м со че тан и е м ф и зи ко |
механических, технологических |
и эксплуатационных свойств. |
По прочности ЧВГ находится на уровне высоких марок ЧПГ (СЧ 25, |
||
СЧ 30, СЧ 35) или превосходит их, однако его пластичность, ударная |
||
вязкость, |
вязкость разруш ения, м одуль упругости, терм остойкость, |
|
о ка л и н о - |
и р о с то у с то й ч и в о с ть , |
с о п р о ти в л я е м о с ть ко р р о зи и , |
герметичность существенно выше, чем |
у серых чугунов, и приближаются |
к а н а л о ги чн ы м |
п о ка за те л я м |
ВЧ Ш Г |
По та ки м |
п а р а м е тр а м , |
как |
дем пф ирую щ ая |
способ ность, |
теп л опр овод н о сть, |
терм оустал остная |
||
сто й ко с ть , р а зм е р н а я с та б и л ь н о с ть |
в у с л о в и я х |
те п л о с м е н , |
ЧВГ |
||
превосходит ЧШГ |
|
|
|
|
2.6.1. Марки и механические свойства
ГОСТ 28394-89 предусматривает четыре марки чугуна: ЧВГ 30,
ЧВГ 35, ЧВГ 40 и ЧВГ 45 (до 1990 г. при производстве отливок из ЧВГ руководствовались ГОСТ 7293-85, согласно которому марки ВЧ 35 и ВЧ
40 могли иметь графит вермикулярной формы). |
|
|||
М а р ки р о в ка о сущ е ствл я е тся |
буквам и ЧВГ и |
циф рами, |
||
показывающими минимально допустимое значение <7в Ю '1 (МПа). |
||||
|
|
|
|
Таблица 2.11 |
Марки и механические свойства ЧВГ (ГОСТ 28394-89) |
|
|||
Марка чугуна |
а., МПа |
I о 02, МПа |
5, % |
нв |
|
|
не менее |
|
|
ЧВГ 30 |
300 |
240 |
3,0 |
130-180 |
ЧВГ 35 |
350 |
260 |
2.0 |
140-190 |
ЧВГ 40 |
400 |
320 |
1,5 |
170-220 |
ЧВГ 45 |
450 |
380 |
______ 0 J _____ |
199-250 |
Марка чугуна определяется минимальным значением временного
сопротивления при растяжении и условным пределом текучести (табл. 2.11).
Относительное удлинение и твердость определяют только при наличии требований в нормативно-технической документации, и их значение
может отличаться от приведенных в таблице. |
|
|
|
М еханические |
свойства ЧВГ являются промежуточными между |
||
с в о й с тв а м и Ч П Г |
и ЧШ Г при одинаковой |
структуре |
матрицы . |
Ч у в с тв и те л ь н о с ть |
м е хан и чески х свойств к |
изменению |
скорости |
охлаждения у ЧВГ значительно меньше, чем у других видов чугунов. Предел
прочности этого чугуна с увеличением толщины стенки от 12,5 до 500
мм сн и ж а е тся тол ько на 25-30 %, тогда как у серого чугуна этот показатель уже в сечении 150 мм уменьшается почти вдвое. Это позволяет использовать ЧВГ для изготовления как крупных отливок большой массы с толщ иной стенки до 500 мм, так и разностенны х отливок сложной конфигурации независимо от массы.
2.6.2. Физические и литейные свойства
По ур овн ю ф и зи чески х свойств ЧВГ также заним ает
промежуточное положение между ЧПГ и ЧШГ Это видно из следующих данных:
Вид чугуна |
ЧВГ |
ЧПГ |
ЧШ Г |
|
Плотность, *1 0 3, кг/м3 |
7,0 |
-7,3 |
6,8-7,5 |
7,1-7,35 |
Теплопроводность , Вт/(м*К) |
35 |
-55 |
50-70 |
25-40 |
Коэф ф ициент линейного расширения |
|
|
|
9,0-12,5 |
ом о", 1/К |
12-14 |
10-13 |
Как и у ЧПГ, теплопроводность у ЧВГ повышается при увеличении
углеродного эквивалента и доли феррита в структуре матрицы. Увеличение
отно си тел ьн ого ко л и ч ества Ш Г |
в стр уктур е пр и во д и т к сниж ению |
|||||
теплопроводности. |
|
|
|
|
|
|
При литье ЧВГ более технологичен, чем высокие марки СЧ и ЧШГ |
||||||
Л инейная усадка |
ЧВ Г |
м еньш е, |
чем ЧШ Г |
и с о с та в л я е т 1,1 |
%, т.е. |
|
п р а кти ч е ски равна |
л и н е й н о й |
уса д ке |
се р о го |
ч угун а . |
О бъем |
|
со ср е д о то ч е н н о й |
уса д о ч н о й р а ко ви н ы |
за в и с и т |
от у гл е р о д н о го |
эквивалента и изменяется от 2,0- 3,5 %, что 2 раза меньше, чем у ЧШГ,
поэтому отливки можно изготовлять без прибылей.
Склонность к отбелу у ЧВГ ниже, чем у высокопрочного СЧ и ЧШГ,
поэтому можно получать тонкостенны е отливки без отбела в литом
состоянии.
2.6.3.Получение вермикулярного графита
иформирование структуры
В е р м и кул я р н ы й гр а ф и т п р е д с та в л я е т со б о й о кр угл ы е утолщ енные и большей частью короткие неразветвленные включения. Характерно, что в структуре отливок из ЧВГ наряду с вермикулярным граф итом всегда имеется до 20 % вклю чений граф ита ш аровидной
(ШГф4), компактной (ШГфЗ) и звездообразной |
(ШГф2) формы (см. рис. |
2.17). Граф ит звездообразной ф ормы чащ е |
образуется в чугунах с |
повышенным содержанием кремния (более 2,5 %) и может существенно понижать прочностны е свойства.
Вермикулярная форма графита достигается при обработке чугуна
(модифицировании) такими же сфероидизирующими присадками, как и при плавке ЧШГ, но в меньших количествах. Получение ЧВГ затруднено тем, что н ео б хо д и м о стро го ко н тр о л и р о в а ть о ста то ч н о е со д е р ж а н и е
модиф ицирующ их элементов (Мд, Се) и S. Небольш ие отклонения от
оптимальных концентраций магния (0,015-0,025 %) и серы (менее 0,015 %) приводят к образованию не вермикулярного, а пластинчатого или шаровидного граф ита.
Наряду с магниевым и цериевы м различаю т магнийцериевы й,
магнийтитанцериевый и некоторые другие способы получения ЧВГ
Совместный ввод в чугун магния церия и титана в наибольшей степени гарантирует получение вермикулярного графита. Отсутствие любого
из этих элементов приводит к образованию не только ВГ, но и графита других
ф орм. Для промы ш ленного производства ЧВГ удобнее пользоваться комплексными лигатурами: Mg - Ti - Се - Са, содержащими 4-5 % магния,
или лигатурами с РЗМ.
Х им ический состав расплава для модиф ицирования с целью
получения ЧВГ примерно такой же, как и при производстве ЧШГ Его
рекомендуется выдерживать в таких пределах (%): 3,4-3,9 С; 2,0-3,0 Si; 0,4-1,2 Мп; 0,01-0,015 S и 0,08 Р.
Н аибольш ее влияние на механические свойства |
ЧВГ в литом |
|
состоянии |
оказы ваю т углерод и марганец. Повышенное |
содержание |
кр ем ни я |
о тр и ц а те л ь н о вл и яе т на пластичность. Н ежелательны |
сочетания низкого или высокого содержания углерода и кремния. В первом случае (Сэ < 3,5) увеличивается склонность чугуна к отбелу и требуется
усиленное графитизирующее модифицирование, а во втором случае
(Сэ > 4,5) |
получается заэвтектический чугун с большим количеством |
||
точечного графита, снижающего механические свойства. |
|||
Как и при производстве ЧШГ, после основного модифицирования |
|||
п р о в о д я т |
по вто р н о е |
граф итизирую щ ее |
м одиф ицирование |
ферросилицием ФС75.
Особенностью структуры ЧВГ является повышенная склонность
кферритообразованию. Это объясняется высоким содержанием углерода
икремния в исходном чугуне и повышенным содержанием кремния в
ко м п л е ксн ы х л и га тур а х И зм енение хим ического состава и
дополнительное легирование элементами, стабилизирующими перлит (Си, V, Sb, Sn и др .), не подавляю т полностью ферритизирующего
действия лигатур и не позволяю т получать в литой структуре более
70 % перлита . Чем больш е перлита в структуре чугуна, тем выше прочность, но ниже пластичность.
Р егулировать структуру и механические свойства ЧВГ можно путем терм ической обработки.
Для получения чугуна с повышенными прочностными характеристиками
проводят норм ализацию , в ходе которой увеличивается количество перлита .
Если провести ф ерритизирую щ ий отжиг, то можно получить
чисто ферритный чугун с высокими показателями пластических свойств
(5 = 6...8 %).
Влияние термической обработки на механические свойства чугуна с вермикулярным графитом показано в табл. 2. 12.
Влияние термообработки на механические свойства ЧВГ |
|
||||
Вид ТО |
Структура |
Механические свойства |
|||
|
|
ст., МПа |
а т, МПа |
5. % |
н в |
Литое состояние |
60 % Ф + 40 % П |
416 |
323 |
3.5 |
170 |
Отжиг |
100 % Ф |
385 |
310 |
5,0 |
156 |
Нормализация |
90 % П + 10 % Ф |
480 |
411 |
2,6 |
229 |
2.6.4.Применение чугуна с вермикулярным графитом
Сочетание хорош их ф изико -м еханических и литейны х свойств открывает широкие перспективы для использования ЧВГ в современном
маш иностроении.
Экономически выгодно применять ЧВГ взамен СЧ для изготовления
д е та л е й |
о тв е тс тв е н н о го н а зн а ч е н и я . |
В этом |
сл уч а е |
не |
то л ь ко |
|
сущ ественно снижается м еталлоем кость |
изделий (на 30-40 |
%), но и |
||||
повы ш ается их эксплуатационная |
надеж ность. Х орош ие |
результаты |
||||
получены |
при и с п о л ь зо в а н и и |
этого |
ч угун а |
д л я и зго то в л е н и я |
||
кр уп н о га б а р и тн ы х б азовы х д е та л е й тя ж е л ы х |
ста н ко в |
и кузн е ч н о |
||||
прессового оборудования. |
|
|
|
|
|
|
С очетание хорош их механических свойств и теплопроводности |
||||||
обусловливает применение ЧВГ для изготовления отливок, |
работающих |
вусловиях теплосмен и значительного градиента температур, например
втурбом оторостроении, в производстве деталей м еталлургического
оборудования (ста л е ра зл и вочн ы е излож ницы , хол од ил ьны е плиты доменны х печей, кокильная оснастка и др.). Как известно, стойкость изложниц из ЧШГ в 1,5-2,0 раза выше, чем изложниц из ЧПГ Однако это
характерно только для изложниц |
массой до 15 т. При большей |
массе |
о тл и в о к п р е и м ущ е ств о Ч Ш Г |
н е зн а ч и те л ь н о . И з-за |
низкой |
теплопроводности в отливках из ЧШГ происходит накопление тепловых
напряжений, ведущих к образованию усталостных трещин и короблению. Теплофизические характеристики ЧВГ более благоприятны, и он может
успеш но конкури ро вать с Ч Ш Г в качестве м атериала для крупны х изложниц.
ЧВГ все чащ е применяется для изготовления отливок деталей
автом обильны х и судовы х двигателей (головки и блоки цилиндров,
вы хлопны е кол л екторы ), других а втом об ил ьны х деталей (картеры , корпуса подшипников, чашки дифференциала, тормозные колодки и диски
и т.п.). |
|
В н е ко то р ы х сл уч а я х |
ц е л е с о о б р а зн о и сп о л ь зо в а ть чугун с |
ве рм и кул я р ны м граф итом |
взам ен вы со ко п р о чн о го с ш аровидны м |
графитом, в особенности при изготовлении сложных малотехнологичных
деталей, в которых невозможно предотвратить образование усадочных деф ектов.
Более высокие плотность и качество металла в отливке из ЧВГ
компенсируют некоторое снижение прочности. |
|
|
||
Таким |
образом, чугун с вермикулярным графитом может быть |
|||
и сп о л ьзова н |
для |
изготовления ш ирокой номенклатуры |
деталей |
в |
м аш иностроении, |
что позволит снизить металлоемкость |
изделий |
и |
|
повысить надежность и срок службы машин и оборудования. |
|
|
2.7. Легированные чугуны со специальными свойствами
Современное машиностроение требует применения материалов, которые могли бы обеспечить длительную и надежную работу отливок
в самых разнообразных условиях эксплуатации. В число таких материалов
входят легированны е чугуны . В соответствии с ГОСТ 7769-82 они
классиф ицируются по химическому составу и специальным свойствам отливок .(табл. 2.13).
С точки зрения потребителя отливки из легированного чугуна удобнее классиф ицировать по специальным свойствам, которые они приобретают в результате легирования. Как видно из табл. 2.13, чугуны
могут быть жаростойкими, жаропрочными, износостойкими, коррозионно-
стойкими и немагнитными. В особую группу выделены антифрикционные
чугуны . Они |
реглам ентирую тся ГОСТ 1585-85. |
Кроме того, |
находят |
|
п р и м е н е н и е |
и таки е сплавы , |
состав и |
свойства |
которых |
р е гл а м е н ти р ую тся отр асл евы м и |
стандартам и и техническими |
условиями.
Для литейщиков легированные чугуны удобнее классифицировать по составу и рассматривать их как хромовые, никелевые, кремнистые, марганцевые, алюминиевые и т.д., т.е. в зависимости от преобладающей
легирующ ей добавки. В отличие от свойств конструкционных чугунов,
которы е, в первую очередь, определяются структурой, специальные свойства легированных чугунов зависят от их состава и прежде всего от содержания легирующ их элементов. При этом часто один и тот же легирующий элемент может придавать чугуну одновременно несколько сп е ци а л ьн ы х свойств . Х им ический состав является обязательной сдаточной характеристикой для отливок из легированных чугунов, что однако не исключает и требований по получению в отливке той или иной с т р у к т у р ы .
Ниже за основу принята классификация чугунов по свойствам,
внутри которой они расположены в зависимости от состава, но прежде обратите внимание на некоторые особенности их маркировки.
Маркировка легированных чугунов со специальными свойствами осуществляется при помощи букв и цифр, указывающих состав чугуна и, иногда, специальное свойство. Буквы обозначают: Ч - чугун, Г - марганец, Д - медь, Н - никель, П - фосфор, С - кремний, Т - титан, X - хром, Ю -
-алюминий. Буква Ш в конце маркировки указывает,что графит в чугуне имеет шаровидную форму;если буква Ш отсутствует, то графит пластинчатый.
Классификация легированных чугунов по ГОСТ 7769-82
Вид чугуна |
Марка |
Свойства отливок |
Хромистые
Кремнистые
Алюминиевые
Марганцевые
Никелевые
Низко |
ЧХ1,4X2 |
Жаростойкие |
легирован 4X3 |
Жаростойкие, износостойкие |
|
ные |
ЧХЗТ |
Износостойкие |
Высоко |
ЧХ9Н5 |
Износостойкие |
легирован ЧХ16 |
Износостойкие, жаростойкие |
|
ные |
ЧХ16М2, ЧХ22 |
Износостойкие |
|
4Х22С, 4X28 |
Коррозионно- и жаростойкие |
|
4Х28П |
Стойкие в цинковом расплаве |
|
4Х28Д2 |
Коррозионно- и жаростойкие |
|
4X32 |
Жаростойкие |
Низко |
ЧС5, ЧС5Ш |
Жаростойкие |
легирован |
|
|
ные |
|
Коррозионно-стойкие в жид |
Высоко |
4С13, 4С15, |
|
легирован 4С17, 4С15М4, кой среде |
||
ные |
4С17МЗ |
|
Низко |
чюхш |
Жаростойкие |
легирован |
|
|
ные |
4Ю6С5, |
Жаростойкие и износостойкие |
Высоко |
||
легирован 4Ю 7Х2 |
|
|
ные |
4Ю 22Ш, 4Ю 30 То же при высокой температуре |
|
ВЫСОКО- |
ЧГ6СЗШ, |
Износостойкие |
легирован 4Г7Х4 |
|
|
ные |
4Г8ДЗ |
Маломагнитные, износостойкие |
Низко |
4НХТ, 4ХМД, |
Коррозионно-стойкие в газо- |
легирован 4НМШ |
вых средах двигателей внут |
|
ные |
|
реннего сгорания |
|
4Н2Х, 4Н4Х2 |
Износостойкие |
Высоко- |
4Н11Г7Ш, |
Жаропрочные и маломагнитные |
легирован 4Н15ДЗШ |
Износостойкие, маломагнитные |
|
ные |
4Н15Д7 |
|
|
4Н19ХЗШ |
Жаропрочные и маломагнитные |
|
4Н20Д2Ш |
Жаропрочные, маломагнитные |
. |
|
и хладостойкие |
Свойство чугуна обозначают буквами, стоящими в начале марки:
А антифрикционный, Ж жаростойкий, И износостойкий (в новом ГОСТе 7769-82 обозначение свойств отсутствует). Цифры после букв показывают
среднее содержание легирующего элемента.
2.7.1. Износостойкие чугуны
Износостойкость оценивают по относительному изменению массы образца при испы тании в различных абразивных и гидроабразивных средах, а также при сухом трении и трении со смазкой.
Износостойкость находится в прямой зависимости от твердости
материала, м икротвердости и характера расположения отдельных структурны х составляю щ их. Из конструкционных нелегированных или низколегированных чугунов лучшей износостойкостью обладают ВЧШГ
перлитного или бейнитного классов.
Для работы в особо жестких условиях в контакте с абразивным
минеральны м сырьем, строительными материалами, окалиной и т.д.
прим еняю т специальны е |
износостойкие чугуны, чаще всего белые. |
О сновной особенностью |
структуры износостойких чугунов является |
наличие карбидов легирующих элементов, или легированных карбидов,
котор ы е м ож но |
р азд е л и ть на три основны е группы по типу |
кристаллической |
решетки: |
•карбиды типа МзС с орторомбической решеткой;
•карбиды типа М7 С3 с гексагональной решеткой;
•карбиды типа МгзСб с кубической решеткой.
Чем сложнее строение карбидов, тем выше их твердость и лучше
износостойкость чугуна.
К о л и ч е ств о карб ид ов в чугунах определяется в основном
содержанием углерода и составляет от 12 до 50 % (25-30 % в наиболее
распространенных марках).
Металлическая основа белых износостойких чугунов представляет
собой а у с те н и т |
и продукты |
его превращ ения. |
М аксимальную |
||||
и зносостойкость |
|
им ею т чугуны |
с прочной |
и твердой |
мартенситной |
||
основой. |
|
|
|
|
|
|
|
ГО С Т 7 7 |
6 9 -8 2 |
пред усм а три вае т |
девять |
марок |
белых |
||
и зн о со сто й ки х |
|
чугун ов |
(низколегированны й хромистый |
ЧХЗТ, |
высоколегированные хромистые ЧХ9Н5, ЧХ16, 4X16М2, ЧХ22, ЧХ28Д2, 4X32, высоколегированный марганцевый ЧГ7Х4 и низколегированный никелевы й ЧН4Х2). Химический состав белых износостойких чугунов приведен в таб л . 2 .14 . И зносостойкостью обладаю т и некоторые частично или полностью графитизированные чугуны, например ЧН2Х, ЧГ6СЗШ и др. Ниже рассматриваются только белые чугуны.
Химический состав белых износостойких чугунов по ГОСТ 7769-82
|
|
|
Массовая доля, % |
|
|
||
Марка |
|
|
|
Сг |
Прочие |
P |
l S |
|
С |
Si |
Мп |
элементы |
не более |
||
ЧХЗТ |
2,6-3,6 |
0,7-1,5 |
1,0 |
2,01-3,00 |
0,5-0,8 Си |
0,30 |
0,12 |
|
|
|
|
|
0,7-1,0 71 |
|
|
ЧХ9Н5 |
2,8-3,6 |
1,2-2,0 |
0,5-1,5 |
8,00-9,50 |
4,0-6,0 Ni |
0,06 |
0,10 |
|
|
|
|
|
0,0-0,4 Мо |
|
|
ЧХ16 |
1,6-2,4 |
1,5-2,2 |
1,0 |
13,0-19,0 |
- |
0,10 |
0,05 |
ЧХ16М2 |
2,4-3,6 |
0,5-1,5 |
1,5-2,5 |
13,0-19,0 |
1,0-1,5 Си |
0,10 |
0,05 |
|
|
|
|
|
0,5-2,0 Мо |
|
|
4X22 |
2,4-3,6 |
0,2-1,0 |
1,5-2,5 |
19,0-25,0 |
0,15 0,35 V |
0,10 |
0,08 |
|
|
|
|
25,0-30,0 |
0,15-0,35 Ti |
|
|
ЧХ28Д2 |
2,2-3,0 |
0,5-1,5 |
1.5-2,5 |
1,5-2,5 Си |
0,10 |
0,08 |
|
|
|
|
|
30,0-34,0 |
0,4-0,8 Ni |
|
|
4X32 |
1,6-3,2 |
1,5-2,5 |
1.0 |
0,1-0,3 Ti |
0,10 |
0,08 |
|
ЧГ7Х4 3,0-3,8 1,4-2,0 |
6,0-8,0 3,00-5,00 |
- |
0,10 |
0,05 |
|||
ЧН4Х2 |
2,8-3,6- I |
0.0-1.0 |
0.8-1.3 |
I0.80-2.5C |
3.5-5.0 Ni |
0.30 |
0.15 |
Стандартные хромистые износостойкие чугуны объединяет
то, что все они содержат хром. Это самый дешевый карбидообразующий
элемент. Хром растворяется в м атрице белого |
чугуна |
и в карбидах |
||
железа, а также образует специальные высокохромистые карбиды. |
||||
В чугунах, содержащ их до |
7 % Сг (ЧХЗТ), |
образуются |
карбиды |
|
ц ем ентитного типа (FeCr)3C в |
перлитной м е та л л и ч е ско й |
м атрице. |
||
М икротвердость карбидов возрастает от HV 800 |
до HV |
1100 |
по мере |
|
увеличения содержания хрома. |
|
|
|
|
В больш инстве марок чугунов, содержащ их более |
11 |
% хрома, |
присутствуют карбиды (CrFe)7C3 с твердостью до HV 1700, а в чугунах
ЧХ28Д2 и ЧХ32 - еще более твердые карбиды СгезСе.
Х ром исты е чугуны, содержащ ие карбиды типа М7С3, в литом состоянии обычно имеют перлитную матрицу. Чтобы получить более твердую
м артенситную структуру, необходим а терм ическая обработка . Из-за
склонности к образованию закалочны х трещ ин охлаж дение отливок возможно только на спокойном воздухе. Для улучшения закаливаемости и прокаливаемости и получения при охлаждении на воздухе мартенситной
или мартенсито-аустенитной металлической основы белые хромистые
чугуны л е ги р у ю т н и ке л е м (Ч Х 9Н 5, |
Ч Н 4 Х 2 ), м а р га н ц е м (Ч Г7Х 4), |
молибденом (ЧХ16М2), медью (ЧХ28Д2) |
и их сочетаниями. |
Вы сокохромисты е чугуны наряду с высокой износостойкостью обладают еще и повышенной коррозионной стойкостью и жаростойкостью.
Добавка молибдена (1-3 %) измельчает карбиды и повышает ударную
вязкость .
Никельхромистые износостойкие чугуны, содержащие до 6,0 %
никеля, им ею т торговое название "нихард" Они получили широкое
р а с п р о с тр а н е н и е в наш ей стране и за рубежом . Чугуны имеют
мартенситную структуру и карбиды (FeCr)3C (ЧН4Х2) или (CrFe)7 C3 (ЧХ9Н5).
Твердость этих чугунов достигает 650 НВ.
М арганцевохромист ы й чугун ЧГ7Х4 имеет м артенсито
аустенитную структуру уже в литом состоянии, хотя и не содержит дорогих
и деф ицитных легирующих добавок. Твердость этого чугуна с карбидами
типа МзС сравнительно невелика 390-450 НВ.
Механические свойства износостойких белых чугунов кроме
высокой твердости характеризуются умеренной прочностью при растяжении
и изгибе и практическим отсутствием пластичности. Прочность, как правило, не является сдаточной характеристикой. С увеличением содержания хрома
она возрастает от а в = 150 МПа (ЧГ7Х4) до(7в = 390 МПа (ЧХ32 и ЧХ28Д2). Литейные свойства износостойких белых чугунов значительно хуже, чем серы х чугунов. Однако их жидкотекучести достаточно для
получения отливок с толщиной стенок 6-8 мм и с ребрами толщиной 3-4 мм в обычных песчано-глинистых формах. Линейная усадка (1,6-2,2 %) близка к линейной усадке углеродистой стали. Из-за неблагоприятного сочетания низкой теплопроводности, большой усадки, высокой теплоемкости и отсутствия пластичности чугуны имеют большую склонность к образованию
горячих и холодных трещин.
Механическая обработка износостойких белых чугунов затруднена
из-за больш ого |
количества карбидов. Низколегированные чугуны с |
ка р б и д а м и МзС |
пр а кти ч е ски не поддаю тся обработке лезвийным |
инструментом. Для остальных чугунов перед механической обработкой
п р о в о д я т см |
ягча ю щ ую ТО (отж и г). Готовые детали подвергаю т |
нормализации |
или закалке для повышения твердости. |
Области применения деталей из белых износостойких чугунов вклю чаю т в себя практически все добывающие отрасли, энергетику,
металлургию, строительно-дорожную технику, оборудование, где срок
служ бы |
д е та л е й о п р е д е л я е тся абразивны м износом . Это |
детали |
|
грязевы х насосов, мелю щ ие шары малого диаметра (ЧХЗТ), |
шары, |
||
мелющ ие тела углеразмольны х мельниц, |
ковши пескометов (ЧХ9Н5), |
||
детали |
цем ентны х печей (ЧХ16), сопла |
пескоструйны х аппаратов, |
|
детали |
центробежных насосов (ЧХ28, 4X32) и т.д. |
|
Ванадиевы е износост ойкие чугуны им е ю т стр уктур у,
удовлетворяющую принципу Шарли. По этому принципу требуется полная
инверсия (латинское inversio - переворачивание; перестановка) фаз, т.е. наиболее твердые структурные составляющ ие должны залегать в виде изолированных друг от друга включений в сплошной вязкой матрице. Такая структура может быть получена при легировании белого чугуна ванадием в количестве более 8 %. В нем образуются твердые аустенитокарбидные
э в те кти ч е с ки е ко л о н и и , |
и м е ю щ и е |
вид с ф е р о л и то в , |
в сп л о ш н о й |
аустенитной (перлитной) |
м атрице . |
К олонии со сто я т из |
карб ид ного |
скелета в виде "ежа", иголки которого равномерно расходятся во все стороны из центра колонии.
В ан ад и е вы е |
чугуны о б л а д а ю т вы со ки м и и зн о с о с то й ко с ть ю , |
антиф рикционными |
свойствами, прочностью , вязкостью, стойкостью в |
условиях теплосмен. Прочность при растяжении ванадиевых чугунов до
1000 МПа, относительное удлинение до 2 %. Применение их сдерживается
и з-за вы со кой сто и м о сти и д е ф и ц и тн о с ти в а н а д и я . П утем
дополнительного легирования медью и увеличения содержания кремния
уд а л ось сн изить кол и чество ва н ад и я , нео б хо д и м о е для инверсии
стр уктур ы , |
до |
3 ,5 |
-4 ,5 %. |
П р и м е р о м |
с тр у кту р ы , со о тв е тс тв у ю щ е й |
|
п р и н ц и п у |
Ш арли, |
м огут |
сл уж и ть |
ч а с ти ч н о |
гр а ф и ти зи р о в а н н ы е |
|
(половинчаты е) |
ванадиевы е чугуны , |
в которы х |
значительная часть |
углерода присутствует в виде ПГ или ШГ, а часть связана в карбидах
ванадия. В сыром состоянии и особенно после отжига такие чугуны с ШГ
им ею т пониж енную тверд ость (ИВ 250) и хорош о об раб аты ваю тся
резанием . После закалки и отпуска они приобретаю т твердость HRC 56-60 и высокую износостойкость; их прочность достигает 1500 МПа.
Высокомарганцевые белые чугуны (15-35 % Мп) также могут
им еть и н в е р ти р о в а н н ую |
м и кр о с тр у кту р у , |
о со б е н н о |
после |
||||
в ы с о ко те м п е р а ту р н о го |
о тж и га . Т а ки е |
|
чугуны |
р е ко м е н д уе тся |
|||
и с п о л ь зо в а ть взам ен |
стал и 110Г13Л д л я |
и зго то в л е н и я |
д е та л е й , |
||||
работающих в условиях износа и ударных нагрузок. |
|
|
|
||||
В анадиевы е и вы соком арганцевы е |
чугуны |
с инвертированной |
|||||
структурой в ГОСТ пока не включены. |
|
|
|
|
|
||
2.7.2. Жаростойкие чугуны |
|
|
|
||||
Ж а р о с то й ко с ть |
о ц е н и в а е тс я |
по |
д вум |
п о ка за те л я м : |
о кал иностойкости и р остоустойчивости .
Сопротивление окалинообразованию оценивается по изменению
массы деталей. В результате окисления жаростойкие чугуны должны увеличивать массу не более чем на 0,5 г/(м2. ч).
Р о с то у с то й ч и в о с ть х а р а кте р и зу е т с п о с о б н о с ть д е та л е й из
чугуна сохранять свои размеры при повышенных температурах.
П ричинам и роста чугунов могут быть: граф итизация, окисление и порообразование. Последнее заключается в том, что при растворении графита
образуются полости, которые затем лишь частично заращиваются матрицей или вновь заполняются графитом. ГОСТ 7769-82 допускает рост не более 0,2
% при температуре эксплуатации в течение 150 ч.
Жаростойкость чугунов может быть повышена путем образования на
поверхности деталей защитных окисных пленок. Защитные свойства пленок
зависят от их сплошности, плотности, прочности сцепления с основным
металлом и химической стойкости. В наибольшей степени этим требованиям
удовлетворяют окислы алюминия, кремния, хрома, никеля и марганца. В
соответствии с ГОСТ 7769-82 к жаростойким относятся хромистые, кремнистые
никелевые и алюминиевые чугуны. При выборе чугуна необходимо
учитывать экономически оправданный уровень долговечности литых деталей.
Предпочтение отдают более технологичным и дешевым чугунам: хромистым,
кремнистым и алюминиевым с пониженным содержанием алюминия.
Высоконикелевые коррозионно-стойкие и жаропрочные чугуны также обладают высокой жаростойкостью. Их применение в качестве жаростойких нецелесообразно из-за высокой стоимости и дефицитности никеля.
В ы сокохром исты е белые и высокоалюминиевые чугуны имеют
наиболее вы сокий уровень жаростойкости, однако их применение
ограничивается из-за плохой обрабатываемости, склонности к образованию
трещин в отливках и дефектов в виде пористости и плен. Низкохромистые чугуны марок ЧХ1, ЧХ2 и 4X3 имеют перлитную
структуру с пластинчатым графитом, повышенное содержание углерода (3,0-3,8 %) и кремния (от 1,5-2,5 % в 4X1 до 2,8-3,8 % в 4X3). Содержание
м арганца и д опустим ы е концентрации примесей такие же, как и у
низколегированного износостойкого чугуна. Для предотвращения появления цементита рекомендуется графитизирующее модифицирование. 4угуны применяю т для изготовления деталей, работающих при сравнительно
невысоких температурах (табл. 2.15).
Высокохромистые белые чугуны 4X16, 4X28, 4X32 имеют существенно более высокую жаростойкость. Их состав приведен в табл. 2.14.
Л итейны е свойства вы сокохромисты х чугунов рассмотрены в
подразделе 2.7.1. Низкохромистые чугуны отличаются от обычных серых
повышенной склонностью к отбелу и образованию усадочных раковин. Линейная усадка растет с содержанием хрома и достигает 1,5 % при 3 %
Сг.
Кремнистый чугун при содержании 5,6 % Si имеет однофазную ферритную матрицу и поэтому отличается высокой ростоустойчивостью. Окалиностойкосгъ связана с появлением в поверхностном слое оксидов Si02.
Такая окисная пленка имеет более плотную структуру, чем оксиды железа.
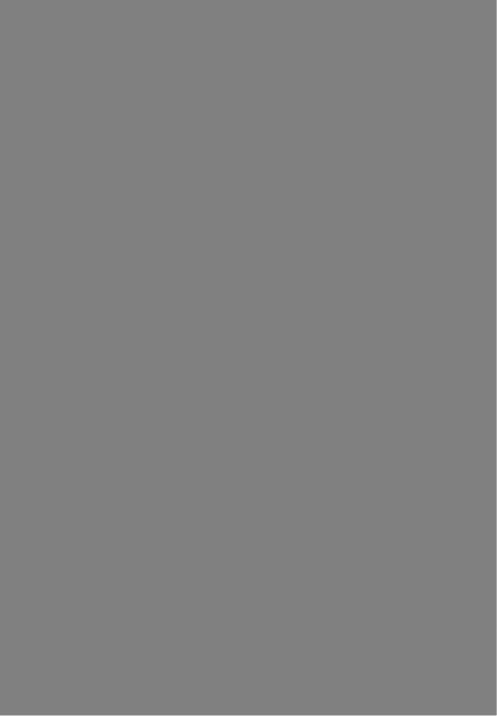
Алю м иниевы е чугуны обладают высокой жаростойкостью при содержании алюминия более 5 %. При увеличении содержания алюминия в чугуне ж аростойкость непрерывно повышается. Повышение жаростойкости связано с образованием плотной защитной пленки из AI2O3 и шпинели Fe0Al203. В сплавах, содержащих 11-17 % AI (первая карбидная зона) или более 26 % (вторая карбидная зона), графита нет. Эти чугуны становятся хрупкими, твердыми и трудно поддаются механической обработке.
В ГОСТ 7769-82 включено 5 марок алюминиевых чугунов: ЧЮХШ, ЧЮ 6С2, ЧЮ7Х2, ЧЮ22Ш и ЧЮЗО.
Н изколегированны й чугун ЧЮХШ, модифицированный магнием,
и м е е т п е р л и тн о -ф е р р и тн ую м атрицу и ш аровидны й граф ит. Его
используют для отливок, работающих при температурах до 650 °С.
Чугуны с 5-8 % AI, содержат пластинчатый графит в матрице из
легированного ф еррита и соединения РезАЮх (у-ф аза). В результате дополнительного легирования кремнием (ЧЮ6С5) или хромом (ЧЮ7Х2)
они могут эксплуатироваться при температурах до 800 °С.
Н а и б о л е е вы со ки м и показателям и ж аростойкости из
графитизированных чугунов характеризуется высоколегированный сплав
Ч Ю 22Ш (чуга л ь ). Он м ож ет им еть чисто ф ерритную матрицу при
высоком содержании легирующих добавок (22-23 % AI и 1,5-1,8 % Si) или
ф ерритную |
с различны м |
количеством у* -фазы (при более низком |
|
с о д е р ж а н и и |
а л ю м и н и я |
и крем ни я). Ш аровидная ф орма граф ита |
|
д о сти га е тся |
при м од иф ицировании |
церием или кальцием . Чугаль |
|
со хр а н я е т ж а р о сто й ко сть до 1100 |
°С. Он может противостоять и |
некоторым агрессивным средам, содержащим серу, сернистый газ, окислы
ванадия и перегреты е водяные |
пары. Этот чугун не растворяется в |
|
р аспл а ве алю м иния и является |
хорош им материалом |
для тиглей, |
используемых при плавке алюминиевых сплавов. |
|
|
В чугуне ЧЮЗО (пироф ераль) углерод находится |
в связанном |
состоянии в виде карбида AUC3, располагающегося в ферритной матрице. Наряду с жаростойкостью пирофераль имеет высокую износостойкость
при повышенных температурах. Он может использоваться для отливок,
работающих при температурах до 1200 °С в воздушной среде, в атмосфере чистого кислорода, в окислительной и восстановительной атмосферах продуктов горения. Плавильные тигли из ЧЮЗО при плавке алюминия
служат в 4 раза дольше, чем из серого чугуна.
П редел прочности при растяжении алюминиевых чугунов с
пластинчатым графитом достигает 200 МПа, а с шаровидным графитом -
400 МПа при нормальной температуре. При 800 °С прочность снижается
соответственно до 30-50 и 140-200 МПа. В отличие от других чугунов
при вы со ки х те м п е р а тур а х наблю дается резкое увеличение пластичности ЧЮЗО: от 2-3 % при 700 °С до 30-50 % при 1000 °С.

S-NiMn 13 7, |
S-NiCr 301, |
S-NiCr 20 2, |
S-NiCr 30 3 |
S-NiCr 20 3, |
S-NiSiCr 30 5 5, |
S-NiSiCr 20 5 2, |
S-Ni 35, |
S-Ni 22, |
S-NiCr 35 3. |
S-NiMn 23 4, |
|
С редний хим ический состав этой группы чугунов виден из
маркировки. Содержание углерода в первых четырех сплавах составляет 3,0 %, а в остальных от 2,0 до 2,6 %. Содержание кремния во всех чугунах, кроме кремнистых, от 1,5 до 3,0 %. Химический состав жаропрочных чугунов,
соответствующих ГОСТ 7769-82 показан в табл. 2.16. Более экономично
использовать чугуны, содержащие от 10 до 20 % никеля. Для получения
аустенитной структуры в чугунах с пониженным содержанием никеля
используется добавка марганца в количестве от 6 до 12 %.
Таблица 2.16
|
Химический состав жаропрочных чугунов по ГОСТ 77-82 |
|
|||||
Марка |
|
|
Содержание элементов, % |
|
|
||
чугуна |
С |
Si |
Мп |
Ni |
Сг |
I Р (не более) |
|
ЧН11Г7Ш |
2.3- |
3,01.8- |
2,5.0- |
8,010-12 |
1.5- |
2,5 |
0,08 |
ЧН19ХЗШ |
2.3- |
3,01.8- |
2,51.0- |
1,618-20 |
1.5- |
3,0 | |
1,10 |
Ж аропрочны е чугуны с шаровидным |
графитом |
при обычной |
температуре имеют достаточно высокую прочность (не менее 340 МПа у
ЧН19ХЗШ и не менее 390 МПа у ЧН11Г7Ш), пластичность (не менее 4 %) и
вязкость. Длительная прочность чугунов при 600 °С за время работы 1000
часов не менее 120 МПа, а скорость ползучести при этой температуре под
нагрузкой 40 МПа не менее 1.8 -10ЛЧН11Г7Ш) или 1,0 -10ЛЧН19ХЗШ).
Чугуны применяются для жаропрочных и ростоустойчивых деталей,
работающих под нагрузкой при повышенных температурах (до 600 °С). Это вы п ускн ы е ко л л е кто р ы , клапанны е направляю щ ие, корпуса
турбонагнетателей в газовых турбинах, головки поршней. Одновременно
детали будут иметь высокую коррозионную и эрозионную стойкость в щелочах, слабых растворах кислот, серной кислоты любой концентрации и н е м а гн и тн о сть (при содерж ании хрома менее 2 %). Их можно использовать и как хладостойкий материал для деталей криогенной техн и ки .
Л итейны е свойства жаропрочных чугунов уступают свойствам обычного ЧШГ, но лучше, чем у жаропрочных сталей.
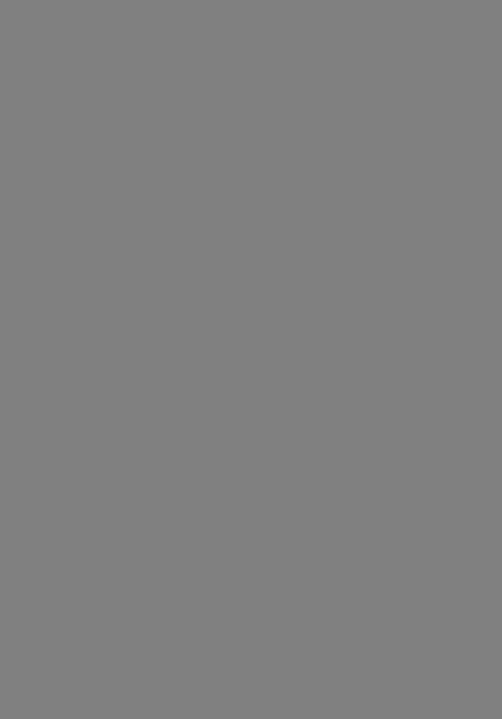
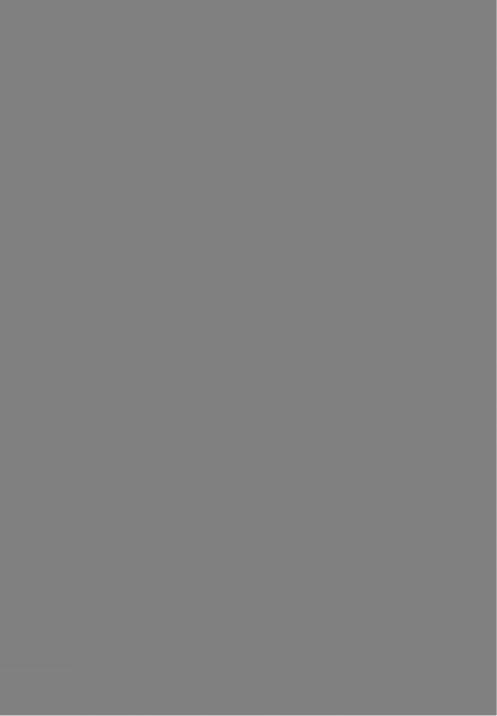
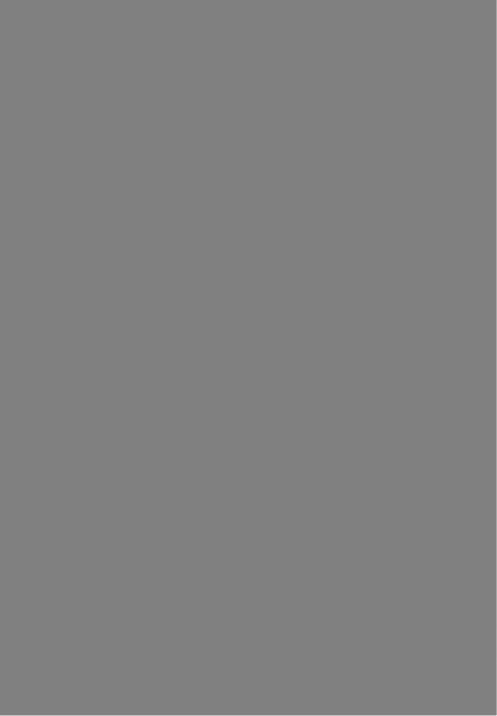
Все чугуны, соответствующие ISO 2892-73, могут быть отнесены к коррозионно-стойким, но, если нет других специальных требований, из экономических соображений лучше использовать чугуны с пластинчатым графитом (L в маркировке обозначает, что графит в чугуне пластинчатой формы).
2.7.5.Немагнитные чугуны
Кнемагнитным относятся чугуны с низкой магнитной проницаем остью . Они должны иметь стабильную аустенитную структуру. Появление карбидов в структуре чугуна нежелательно, так как они повышают магнитную проницаемость. С этой целью в никелевых чугунах до минимума ограничивают содержание хрома. Содержание марганца в них не должно превышать 8 %.
Вкачестве немагнитных применяют: аустенитные никелевые чугуны (ЧН19Д7, ЧН19ХЗШ, ЧН20Д2Ш, L-NiCuCr 15 6 2, L-NiCuCr 15 6 3 и S-Ni 22); никель-марганцевые чугуны (ЧН11Г7Ш, L-NiMn 13 7, S-NiMn 13 7
иS-NiMn 23 4); марганцевые чугуны (ЧГ8ДЗ).
Из немагнитных чугунов отливают крышки, кожухи и втулки масляных выключателей, обоймы силовых трансформаторов, колпачки и полуф ланцы трансф орматоров тока, крышки, кожухи, салазки сварочны х трансф орматоров, различные детали электрических аппаратов, машин, приборов.
2.8. Антифрикционные чугуны
Антифрикционные сплавы предназначаются для работы в узлах трения. Они должны обеспечивать нормальную работу трущихся деталей как в период приработки, так и при последующей эксплуатации, без заедания и задиров, иметь низкий коэффициент трения при работе в паре с контртелом, а также обладать высокой износостойкостью. Сплавы должны сохранять пленку смазки на поверхности трения в широком диапазоне нагрузок и скоростей скольжения при различных
тем пературах. |
|
|
|
Этим требованиям |
достаточно |
полно |
удовлетворяют |
антиф рикционны е чугуны, |
включенные |
в ГОСТ |
1585-85. В нем |
представлено 10 марок чугунов с различной металлической матрицей и графитом различной формы. Структурная многофазность чугунов позволяет в широких интервалах варьировать их свойства. Перлитная, перлито-ферритная и аустенитная структуры металлической основы сообщ аю т им хорошие несущую способность при трении и износостойкость. Износостойкость может быть повышена увеличением в структуре цементита и фосфидной эвтектики.
Графитовые включения способствуют эффективному самосмазыванию при трении и удержанию пленки смазки в порах, которые образуются при выкрашивании графита. Графитизированные чугуны имеют высокую теплопроводность, что обеспечивает теплоотвод от поверхностей трения и нормальные тепловы е условия работы узла трения. По сравнению с цветными антифрикционными сплавами чугуны имеют следующ ие преимущ ества: вы сокую износостойкость, хорошую работоспособность при высоких давлениях и граничной смазке, низкую стоим ость.
Антифрикционные чугуны маркируются буквами АЧС, АЧВ или АЧК и цифрами, указывающими порядковый номер сплава. Третья буква в маркировке показывает принадлежность чугуна к определенному типу по форме графитовых включений (С - серый с пластинчатым графитом, В - высокопрочный с шаровидным графитом, К - ковкий с компактным графитом).
Таблица 2.18
Химический состав антифрикционных чугунов по ГОСТ 1585-85
Марки |
|
Содержание элементов, % |
|
|
|||
чугуна |
С |
Si |
Мп |
Си |
Прочие |
P |
S |
АЧС-1 |
3,2-3,6 |
1,3-2,0 |
0,6-1,2 |
0,8-1,6 0,2-0,5 Сг |
0,15-0,40 |
>0,12 |
|
АЧС-2 |
3,0-3,8 |
1,4-2,2 |
0,3-1,0 |
0,2-0,5 0,2-0,5 Сг |
0,15-0,40 |
>0,12 |
|
|
|
|
|
|
0,2-0,5 Ni |
|
|
АЧС-3 |
|
|
|
|
0,03-0,10 Ti |
|
|
3,2-3,8 |
1,7-2,6 |
0,3-0,7 |
0,2-0,5 .0,3 Сг |
0,15-0,40 |
>0,12 |
||
|
|
|
|
|
_0,3 Ni |
|
|
АЧС-4 |
3,0-3,5 |
1,4-2,2 |
|
|
0,03-0,10 Ti |
>0,30 |
|
0,4-0,8 |
|
0,04 Sb |
0,12-0,20 |
||||
АЧС-5 |
3,5-4,3 |
2,5-3,5 |
7,5-12,5 |
|
0,4-0,8 Al |
>0,20 |
>0,05 |
АЧС-6 |
2,2-2,8 3,0-4,0 0,2-0,6 |
|
|
0,5-1,0 |
>0,12 |
||
АЧВ-1 |
2,8-3,5 |
1,8-2,7 |
0,6-1,2 |
>0,7 |
0,03-0,08 Mg |
>0,20 |
>0,03 |
АЧВ-2 |
2,8-3,5 |
2,2-2,7 |
0,4-0,8 |
|
0,03-0,08 Mg |
>0,20 |
>0,03 |
АЧК-1 |
2,3-3,0 |
0,5-1,0 0,6-1,2 1,0-Т,5 |
|
>0,20 |
>0,12 |
||
АЧК-2 |
2.6-3.0 |
0.8-1.3 |
0.2-0.6 . |
|
. >0.25 |
>QA2___ |
Стандарт регламентирует химический состав (табл. 2.18), микроструктуру и твердость чугунов.
Серые чугуны марок АЧС-1 - АЧС-4 имеют перлитную матрицу, которая стабилизируется за счет небольших добавок хрома, меди, титана или сурьмы. Повышенное содержание фосфора обеспечивает формирование высокотвердой фосфидной эвтектики.
Чугун АЧС-5 легирован марганцем (7,5-12,5 %), поэтому имеет аустенитную структуру с включениями марганцевых карбидов, которые повышают твердость чугуна до НВ 290.
Чугун АЧС-6 имеет повышенное содержание свинца и фосфора. Такое легирование приводит к получению равномерно распределенной микропористости, которая хорошо удерживает смазку.
Перлитные чугуны АЧВ-1 и АЧК-1 предназначены для работы в узлах трения с повышенными окружными скоростями в паре со стальным термообработанным (закалка или нормализация) валом, а перлито ферритные чугуны АЧВ-2 и АЧК-2 - для работы в паре с валом без ТО.
Из антифрикционных чугунов изготавливают: разнообразные детали узлов трения (втулки, вкладыши, подшипники скольжения, ролики, уплотнения); изнаш ивающ иеся детали горнорудного и угольного оборудования, строительных и дорожных машин, тракторов и экскаваторов, сельхозмашин; некоторые трущиеся детали турбин, компрессоров, двигателей и насосов.
2.9. Синтетические чугуны
Синтетическим называют чугун, полученный при переплаве стальных отходов с соответствующим науглероживанием различными карбюризаторами (электродный бой, графитизированный порошок, кокс, каменный уголь и т.п.). Этот процесс стал возможен в результате внедрения электроплавки.
Так как стальные отходы содержат меньше примесей, чем чугунные, то и синтетический чугун существенно отличается от обычного низким содержанием серы (0,015-0,03 %), фосфора (0,02-0,04%), растворенных газов и неметаллических включений. Этим объясняется большая склонность синтетического чугуна к переохлаждению, что способствует кристаллизации по метастабильной системе и образованию отбела и междендритного графита.
При одинаковом с обычным чугуном содержании С и Si склонность к графитизации у синтетического чугуна меньше, поэтому для получения одинаковой с обычным чугуном структуры содержание Si в синтетическом чугуне должно быть больше, чем в обычном.
Синтетическим путем можно получить любую марку белого или граф итизированного чугуна, но необходимо учитывать некоторые особенности полученных сплавов.
Механические свойства синтетического серого чугуна значительно выше, чем свойства обычного чугуна с пластинчатым графитом. Это различие наиболее существенно проявляется в модифицированном состоянии, и получение высоких марок чугуна (СЧ 30, СЧ 35) заметно облегчается.
Синтетический чугун с шаровидным графитом мало отличается по свойствам от обычного ВЧШГ (при их одинаковом составе), так как свойства этих чугунов зависят главным образом от условий модифицирования и ТО. Но это справедливо лишь при нормальной температуре. При повышенных и особенно при пониженных температурах свойства синтетических чугунов лучше, что связано с более низким содержанием примесей.
По этой же причине ковкие синтетические чугуны отличаются повышенной пластичность и вязкостью, особенно при низкой температуре, их отжиг продолжительнее. Этот недостаток можно устранить путем изменения технологии модифицирования.
Белый синтетический чугун, простой и легированный, отличается больш ей дисперсностью структуры и склонностью к транскристаллизации. Последнее устраняется модифицированием РЗМ и увеличением скорости охлаждения отливок.
Служебные свойства синтетического чугуна лучше, чем обычного. В первую очередь это касается износостойкости и герметичности. Износ синтетического чугуна в условиях трения со смазкой почти в два раза меньше, чем обычного чугуна той же марки, а герметичность такова, что чугун можно применять для деталей гидроаппаратуры и других деталей, работающих при давлениях до 300-350 атм.
Литейные свойства синтетического чугуна несколько хуже, чем обычного. В первую очередь следует отметить пониженную жидкотекучесть, повышенную литейную усадку и увеличение объема усадочных раковин и пор. Это различие можно сократить повышенным перегревом, изменением концентраций углерода и кремния или модифицированием, поэтому замена обычного чугуна синтетическим не требует сущ ественного изменения технологии литья.
Синтетические чугуны целесообразно применять в следующих случаях:
• при наличии на предприятии большого количества стальных отходов или при расположении его в непосредственной близости от источников таких отходов;
• для изготовления отливок с повыш енными механическими свойствами, особенно при повышенных или пониженных температурах,
вусловиях знакопеременных и динамических нагрузок;
•для получения отливок с повыш енной герметичностью , работающих при высоких давлениях в жидких и газообразных средах;
•взамен легированных конструкционных чугунов, когда легирование направлено лишь на повышение механических свойств;
•для получения отливок сложной конфигурации при значительном торможении усадки, склонны х к образованию горячих трещ ин и значительной деформации при эксплуатации.
Вопросы для самоконтроля
Разделы 2.1, 2.2, 2.3
1. Составьте полную классификацию чугунов.
2. Какими особыми свойствами обладают графитизированные чугуны по сравнению с другими железоуглеродистыми сплавами?
3. Назовите основные разновидности формы графитовых включений? Какое влияние оказывает форма включений графита на механические свойства?
4 . Какую форму графита имеют высокопрочные чугуны?
Какие факторы в наибольшей степени влияют на структуру чугуна? 5. По каким признакам классифицируют микроструктуру чугуна?
6. Как определяется микроструктура чугуна по ГОСТ 3443-87?
7.Что такое структурная диаграмма? Нарисуйте диаграмму Маурера. 8. Как определяются приведенная и эквивалентная толщины отливки?
9. Какие возможности предоставляет структурная номограмма Жукова для анализа чугуна?
10.В чем заключается хорошая технологичность серых чугунов?
11.Перечислите марки серых чугунов? Какой чугун наиболее близок к эвтектическому?
12.0т чего зависит прочность чугуна в отливке?
13.Что является показателем качества серого чугуна? Какой чугун ценится выше и почему?
14.При каком нагружении лучше работают серые чугуны: при сжатии, растяжении или при изгибе?
15.Почему серые чугуны имеют малую чувствительность к надрезу?
1 6 . Какие ф изические свойства чугуна являются структурно чувствительными?
17.Как можно повысит жидкотекучесть чугуна?
18.Почему отливки из серого чугуна можно получать без прибылей? 19.Что такое отбел? Как оценить склонность чугуна к отбелу?
20 .Чем объясняются хорошие антифрикционные и износостойкие
свойства серого чугуна?
21. Какие элементы и в каких количествах входят в состав серого чугуна? 22. В чем заключается вредное воздействие серы на свойства серого
чугуна?
23. Как повысить прочностные характеристики серых чугунов?
24.Почему высокопрочные серые чугуны необходимо модифицировать?
25.Какие модификаторы применяют для СЧ?
26.Какой состав должен иметь серый чугун перед модифицированием?
27.Перечислите основные виды термической обработки серых чугунов.
28. Назовите основные области применения серого чугуна и наиболее
характерные |
отливки. |
2 9 . Почему |
чугун одной и той же марки в различных отраслях |
промышленности может иметь различный химический состав?
Раздел 2.4
1.Перечислите основные марки и опишите особенности ковких чугунов. 2.Чем отличается черносердечный КЧ от белосердечного?
3. Какую форму имеют графитовые включения в КЧ?
4. Почему ковкие чугуны получили такое название?
5.Какой КЧ имеет хорошую свариваемость?
6.Какие различия имеют черносердечный и белосердечный КЧ по величине усадки?
7 . Какую металлическую матрицу могут иметь КЧ и как меняются механические свойства КЧ в зависимости от вида матрицы?
8.Какие ограничения по массе и толщине стенки имеют отливки из КЧ? С чем это связано?
9.Назовите рекомендуемые химические составы для отливок из КЧ.
10. Как м одиф ицирую т КЧ? 'П еречислите стабилизирую щ ие и графитизирующие элементы.
11.Как нейтрализовать вредное влияние хрома на графитизацию чугуна?
12.Дайте характеристику совместного влияния марганца и серы. Каковы соотношения этих элементов в ферритном и перлитном КЧ?
13.Чем отличаются режимы отжига на ферритный и перлитный КЧ?
14.Как проводится обезуглероживающий отжиг?
15.Как превратить ферритный КЧ в перлитный?
16.В чем преимущество сернистого перлитного чугуна перед обычным?
17.Приведите примеры отливок из КЧ.
Разделы 2.5, 2.6
1. Какими основными преимуществами перед сталью и ЧПГ обладает ЧШГ?
2 . Какие характеристики механических свойств, регламентированных ГОСТом, являются обязательными при определении марки чугуна?
3. Почему механические свойства в отливках из ЧШГ ниже, чем в пробах? 4 . Назовите важнейш ие особенности ЧШГ как конструкционного материала.
5 . Назовите основные факторы, способствующ ие кристаллизации в чугуне шаровидного графита.
6. Каковы основные принципы выбора химического состава чугуна, при котором обеспечиваются наилучшие литейные и механические свойства? 7 . Какие основные хим ические элементы в наибольш ей степени определяют механические свойства ЧШГ?
8. Сравните эффективность действия сфероидизирующих элементов.
9. Какие элементы препятствуют получению шаровидного графита?
10. Какие добавки устраняют влияние демодификаторов?
11. Назовите основные методы модифицирования для получения высокопрочного чугуна. Какую остаточную массовую долю магния необходимо сохранить в чугуне для получения ШГ?
12. С чем связаны основные сложности модифицирования чистым магнием?
13.Как можно безопасно ввести чистый магний в расплав?
14.Какова цель вторичного модифицирования? Какие модификаторы используют при вторичном модифицировании?
15.0Ьишите литейные свойства ЧШГ? Как можно повлиять на величину предусадочного расширения?
16.При каких условиях можно получить плотные отливки из ЧШГ без применения прибылей?
17.Почему на отливках из ЧШГ могут появиться "утяжины"?
18.Что собой представляют дефекты отливок в виде черных пятен? Как предотвратить их образование?
19.Назовите основные области применения обычных конструкционных
ЧШГ
20.Какие виды термической обработки применяют для ЧШГ?
21.Что такое вермикулярный графит?
22.В чем отличие свойств ЧВГ от свойств других типов чугунов? 23.Чем отличается модифицирование ЧВГ от модифицирования ЧШГ? 24. Почему из ЧВГ можно получать более толстостенные отливки, чем из ЧПГ?
2 5 . Какие свойства ЧВГ позволяют использовать его для отливок, работающих в условиях теплосмен?
26.Опишите литейные свойства ЧВГ? Можно ли использовать для изготовления отливок из ЧВГ литейную оснастку, предназначенную для получения отливок из ЧПГ?
27.Какой химический состав рекомендуется для получения ЧВГ? 28.Чем объясняется повышенная склонность ЧВГ к ферритизации? 29. Какая ТО проводится для получения перлитного ЧВГ?
3 0 . П еречислите области применения ЧВГ и назовите наиболее характерные отливки из ЧВГ
Р азделы 2.7, 2.8 и 2.9
1. Какие основные легирующие элементы применяют для получения чугунов с особыми физическими свойствами?
2 . Какие особые свойства приобретают чугуны в результате
легирования? |
|
|
3. |
Дайте классификацию легированных чугунов. |
|
4. |
Как маркируют легированные чугуны? |
|
5 . |
Какая структурная составляющая в наибольшей степени придает |
|
чугунам износостойкость? |
|
|
6. |
Какая легирующая добавка в износостойких чугунах является основной? |
|
7. |
Какие износостойкие чугуны удовлетворяют принципу Шарли? Что |
|
такое инверсия фаз? |
«125 |