
Химия и технология древесной массы
..pdf
а
CSF |
746 |
700 |
657 |
617 |
580 |
545 |
513 |
483 |
454 |
427 |
402 |
378 |
355 |
334 |
314 |
°ШР |
12 |
14 |
16 |
18 |
20 |
22 |
24 |
26 |
28 |
30 |
32 |
34 |
36 |
38 |
40 |
CSF |
294 |
276 |
258 |
241 |
225 |
210 |
196 |
182 |
168 |
155 |
143 |
131 |
120 |
109 |
98 |
°ШР |
42 |
44 |
46 |
48 |
50 |
52 |
54 |
56 |
58 |
60 |
62 |
64 |
66 |
68 |
70 |
б
Рис. 7. Шкала соотношения между степенью помола в канадских градусах (CSF) и в градусах Шоппер-Риглера (°ШР): а – линейка, б – числовые значения
5. ОПРЕДЕЛЕНИЕ ФРАКЦИОННОГО СОСТАВА ДРЕВЕСНОЙ МАССЫ
Для ДМ характерна большая размерная неоднородность составляющих ее волокнистых элементов, которая определяется путем сортирования (фракционирования) через металлические сита разных номеров. Это позволяет одновременно оценить и ее фракционный состав.
Фракционный состав ДМ определяется следующими факторами: видом и свойством древесного сырья и режимами его предварительной обработки; способом получения ДМ и типом основного аппарата, используемого для дефибрирования или размола древесины, и т.д.
ДМ наряду с волокнами нормальной длины содержит значительное количество обрывков волокон – мелочи. В ТММ больше длинных волокон (длиной свыше 2 мм), чем в ДДМ (около 40 % против 10–12 %). Коротковолокнистая фракция древесной массы может включать в себя фрагменты лучевых клеток, получаемые в результате отделения трахеид; обрывки срединной пластинки; материал первичных стенок, состоящий из фрагментов внешней оболочки различных размеров; короткие и тонкие фибриллы из вторичной стенки; некоторое количество очень тонких волокон.
21

Порядок выполнения работы
Фракционирование ДМ по длине волокна осуществляется на аппарате типа ФДМ, принцип работы которого заключается в мокром сортировании навески ДМ через ряд последовательно установленных сеток различных номеров с последующим количественным определением сухого вещества полученных фракций.
Фракционатор древесной массы (рис. 8) представляет собой трехступенчатую центробежную сортировку проточного типа с цилиндрическими каркасами 4 с сетками, две из которых помещены в корпус 5.
Верхняя сетка № 9/9 предназначена для удержания грубого волокна, средняя № 20 миткалевого переплетения – среднего волокна, нижняя № 40 – мелкого волокна (номер сетки означает число проволок основы на 1 см погонной длины). Высота сеток 75 мм, диаметр 150 мм. Внутри каждой сетки помещена четырехлопастная перфориро-
Рис. 8. Фракционатор ванная мешалка 6 с частотой вращения древесной массы 173 об/мин. Зазоры между лопастями
мешалок и сетками 3 мм.
В откидной воронке 2 установлен кольцевой спрыск 1, который при помощи гибкого шланга соединен с водяной магистралью от регулятора расхода воды. В верхней части аппарата установлен переливной патрубок 3 для отвода промывной воды во время фракционирования. Нижний патрубок 7, снабженный трехходовым краном, служит для заполнения аппарата водой перед началом фракционирования и для выпуска ее из аппарата после его окончания.
Для фракционирования берут навеску древесной массы с точностью до 0,01 г из расчета 5 г абсолютно сухого вещества из пред-
22
варительно отобранной средней пробы и готовят из нее 1 л волокнистой суспензии. Включают в работу предварительно заполненный водой аппарат и подают в него воду через верхний спрыск
спостоянным расходом 10 л/мин. Подготовленную суспензию начинают выливать равномерной струей в работающий аппарат, одновременно включают секундомер, в течение 15 с споласкивают кружки водой (100–150 мл) и выливают ее в аппарат. По истечении 5 мин с начала выливания пробы аппарат выключают, прекращают подачу воды на спрыск и выпускают из него оставшуюся воду. После освобождения от воды верхней сетки кратковременным открыванием спрыска смывают оставшиеся на сетке волокна ко дну каркаса, открывают откидную воронку и извлекают из аппарата каркас
ссеткой и мешалкой. Отверстие в дне каркаса закрывают снизу ре-
зиновой пробкой (37×43×44 мм), одновременно поднимают пробкой мешалку и, не допуская выхода волокон через отверстие, смывают слабой струей воды волокна с мешалки и сетки ко дну каркаса. Затем вынимают мешалку и тщательно собирают оставшиеся волокна в фарфоровую чашечку, высушивают их в сушильном шкафу до постоянной массы и взвешивают с точностью 0,01 г. Получают первую фракцию Г (грубое волокно).
В такой же последовательности собирают вторую и третью фракции и после сушки получают соответственно количество среднего (С) и мелкого волокна (М).
Суммарную массу абсолютно сухих волокон Г, С, М вычитают из абсолютно сухой навески и получают четвертую фракцию волокна Мл (мелочь, мельштоф) – таблица.
Фракционный состав ДМ
Ступень сортирования |
Номер сетки |
Фракция волокна |
I |
9 |
Г – грубое волокно |
II |
20 |
С – среднее волокно |
III |
40 |
М – мелкое волокно |
Эти 3 фракции остают- |
Четвертая фракция про- |
Мельштоф (мелочь) |
ся на ситах |
ходит через сито № 40 |
|
23

Содержание в древесной массе каждой фракции вычисляют по формуле
Х= 100m ;
РКсух
где X – содержание отдельной фракции, %;
m – масса абсолютно сухого волокна фракций, г;
Р – навеска древесной массы, взятой для испытания, г; Ксух – коэффициент сухости навески.
Содержание в древесной массе мелочи (мельштофа)
Мл = 100 – (Г + С + М),
где Г, С, М – содержание грубого, среднего и мелкого волокон, %. Весьма полная характеристика массы по длине волокон получается на анализаторе размеров волокон FS-200 фирмы «Каяни электрикс Лимитед» (Финляндия). Длина волокон определяется оптическим методом. Водно-волокнистая суспензия низкой концентрации прокачивается через капилляр, помещенный в оптическую систему прибора. Лазерный луч формирует световое отображение волокон на детекторе. Это изображение пропорционально длине волокон. Сигнал детектора усиливается и преобразуется в цифровую форму для вычислений в микропроцессоре, который рассчитывает среднюю длину волокон по классам. Данные распределения волокон по длине выводятся на принтер в цифровом и/или графическом виде. Диапазон измерения задается в интервале от 0 до 7,2 мм. Скорость анализа 40–60 волокон в секунду. Формула для расчета
среднеарифметической длины волокон, мм, следующая:
L = |
∑ni li |
, |
|
∑ni |
|||
ср |
|
||
|
|
где ni – число волокон;
li – длина волокон, мм.
Расширенный анализ свойств волокон позволяет провести установка L&W «Файбертестер». Прибор состоит из устройства для анализа вместе с ПК, который управляет тестированием образ-
24

ца, обрабатывает данные и гене- |
|
|
рирует отчет по показаниям. Схе- |
|
|
ма прибора приведена на рис. 9. |
|
|
На вращающемся столике |
|
|
(карусель) для образцов можно |
|
|
размещать до 6 стаканов с дезин- |
|
|
тегрированной массой. ПК запо- |
|
|
минает идентификацию (ID) каж- |
|
|
дого образца, после чего образец |
Рис. 9. Прибор установки «Фай- |
|
всасывается в прибор и разбавля- |
бертестер»: 1 – индикатор текущей |
|
ется до требуемой для измерения |
операции |
в последовательности |
концентрации. |
измерения; 2 – вращающийся сто- |
|
Суспензия волокон прокачи- |
лик с 6 |
стаканами (бутылками); |
вается через измерительную ячей- |
3 – пробоотборник с трубкой для |
|
ку, где она фотографируется. Изо- |
всасывания образца |
|
|
|
бражения затем обрабатываются с помощью программы для анализа изображений. Пользователь может настроить варианты выдачи отчета в разных видах. В отчет по умолчанию включены следующие параметры волокон:
–длина, среднее значение;
–ширина, среднее значение;
–форма, т.е. частное от деления проекции длины на фактическую длину;
–мелочь – выражается как процент волокон короче 0,2 мм относительно числа волокон длиннее 0,2 мм;
–грубость, т.е. вес волокна на единицу длины. Для этого должен быть известен вес навески по сухому волокну.
6.ОПРЕДЕЛЕНИЕ СОРНОСТИ
Порядок выполнения работы
Сорность определяют путем подсчета числа соринок, видимых невооруженным глазом в смоченном листе или отливке древесной массы в проходящем свете, с последующим пересчетом ее на 1 м2
25
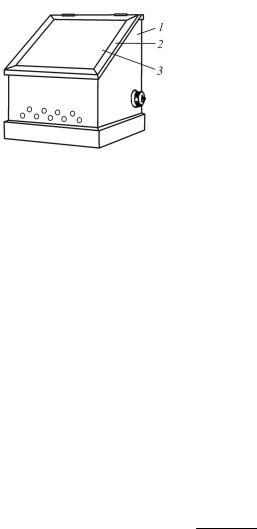
|
пробы массой 500 г а.с. волокна. Со- |
|
ринками являются посторонние вклю- |
|
чения: уголь, песчинки, коpa, костра, |
|
лубяные волокна, смоляные пятна и |
|
другие, отличающиеся по цвету от об- |
|
щего фона образца. Учитываются со- |
|
ринки площадью свыше 0,06 мм2. |
|
Аппарат для определения чистоты |
Рис. 10. Прибор для опреде- |
массы изображен на рис. 10. Он пред- |
ставляет собой световой ящик 1, с внут- |
|
ления сорности древесной |
ренней стороны окрашенный в белый |
массы |
цвет. В раму наклонной крышки 2 ящи- |
|
ка вставлено прозрачное стекло 3 размером 250 250 мм. Стекло разделено линиями для удобства подсчета. На расстоянии 40 мм от верхнего стекла параллельно ему вставлено матовое стекло для рассеивания света.
Испытуемый образец помещают на стеклянную крышку прибора, которая освещается двумя расположенными внутри ящика лампами мощностью по 100 Вт. Для вентиляции в стенках ящика имеются круглые отверстия.
Изготовляют отливку массой 1 м2 500 г а.с. волокна и на обеих сторонах влажной отливки подсчитывают число соринок. Размеры соринок определяют по их площади, сравнивая их с фигурами стандартного шаблона, который изготовлен из прозрачной пленки с нанесенными на ней черными фигурами различной формы.
Сорность ДМ определяют как сумму соринок на обеих сторонах отливки, отнесенную к 1 м2 пробы массой 500 г а.с. волокна:
С= А 100 32 , m
где С – сорность; А – сумма соринок на обеих сторонах отливки;
m – масса образца в расчете на а.с. волокно, г.
26
7.ИЗГОТОВЛЕНИЕ ОТЛИВОК ДРЕВЕСНОЙ МАССЫ
ИОПРЕДЕЛЕНИЕ ИХ ФИЗИКО-МЕХАНИЧЕСКИХ ПОКАЗАТЕЛЕЙ
Методика изготовления отливок
Отливки ДМ и целлюлозы должны изготавливаться в стандартных условиях на листоотливном аппарате ЛА-3 с вакуум-су- шильной камерой (рис. 11).
Для изготовления отливок из исходной ДМ получают волокнистую суспензию концентрацией 2–3 %. Полученную волокнистую суспензию разбавляют водой до концентрации массы примерно 0,5 % и при непрерывном перемешивании с помощью мешалки отбирают массу предварительно рассчитанного объема, необходимую для получения отливки массой 1 м2 75±1 г или 100 г/м2.
Поверхность сетки листоотливного аппарата составляет 0,0314 м2. Если требуется приготовить отливки массой 1 м2 75 г, то на одну отливку необходимо взять 75 · 0,0314 = 2,36 г абсолютно
сухого волокна; при концентрации массы 0,5 % – 2,36 1000,5 =
= 472 мл. Вначале готовят одну отливку и проверяют ее массу. Ес-
ли она соответствует требуемой массе 1 м2, то готовят остальные отливки. Если она больше или меньше нужного, то рассчитывают уточненный объем суспензии на одну отливку. Например, масса отливки получилась 2,2 г, тогда следует увеличить объем суспензии
на одну отливку до величины 472 · 2,36 = 506 мл. 2,2
Приготовляют 5–6 отливок – их достаточно для испытаний данного образца.
Схема аппарата представлена на рис. 11. Аппарат состоит из следующих основных частей: станины 1, предназначенной для размещения основных узлов аппарата; отливного устройства (формующей камеры) 2 для получения отливки на сетке № 40 диамет-
27
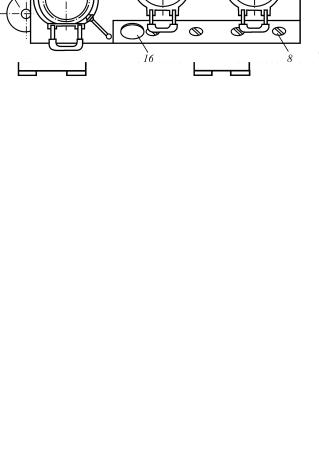
ром 200 мм при вакууме 26,6 кПа; двух сушильных камер 3 и 4 для сушки влажных отливок при температуре 100 °С и вакууме 95 кПа; вакуум-насоса 5, расположенного внизу аппарата слева; парообразователя 6 для получения водяного пара для нагрева сушильных камер; панелей управления 7 и 8.
а
б
Рис. 11. Схема аппарата модели ЛА-3 для изготовления отливок древесной массы: а – вид спереди; б – вид сверху
28
На панели управления 7, расположенной над сушильными камерами находятся: общее пусковое устройство аппарата 9; тумблер включения двигателя вакуум-насоса 10; тумблер включения электронагревателя парообразователя 11; вакуумметр сушильных камер 12; два реле времени для установки продолжительности сушки в сушилках 13 и 14.
На наклонной панели управления 8 расположены: шарнирный клапан для опорожнения отсасывающей камеры 15; вакуумметр для контроля за величиной вакуума в листоотливной камере 16; кран для подачи воды в формующую камеру аппарата 17; кран для подключения вакуума к отсасывающей камере 18; краны для подключения вакуума к сушилкам 19. Краны 17, 18, 19, 20 имеют два положения: «О» – открыто; «З» – закрыто.
Перед началом отлива необходимо подготовить аппарат к работе. При этом краны 17–20 должны быть в положении «З», а электроприборы отключены.
После подготовки и проверки аппарата приступают к изготовлению отливок древесной массы.
Листоотливную сетку смачивают водой и накладывают на опорную решетку формующей камеры, ребра которой должны быть расположены параллельно оси шарнира. Формующую камеру закрывают и прижимают к фланцу отсасывающей (вакуумной) камеры ручкой-зажимом.
Кран 17 переводят в положение «О» и заполняют формующую камеру водой до отметки 7 л. После этого кран 17 переводят в положение «З» и заливают в формующую камеру подготовленную волокнистую суспензию объемом 472 мл (расчет смотри выше), из которой формируется отливка. Далее, открывая кран 17, доливают воду в загрузочную камеру до отметки 8 л. Кран закрывают.
Осторожно, не допуская образования пены и не касаясь сетки, перемешивают суспензию размешивающим устройством 21. Затем, открыв нажатием вниз клапан 15, спускают воду из формующей камеры в отсасывающую камеру. При этом на сетке начинает формироваться слой волокнистой массы. После того как уровень сус-
29
пензии в формующей камере снижается до отметки 2 л, клапан 15 отпускают и одновременно подключают к отсасывающей камере вакуум-насос переводом крана 18 в положение «О». Когда под действием разрежения вся жидкость из формующей камеры будет удалена, образовавшуюся на сетке отливку дополнительно обезвоживают в течение 10 с. Затем кран 18 закрывают. После этого освобождают ручку-замок и откидывают корпус формующей камеры «от себя» до упора, при этом открывается клапан, обеспечивающий опорожнение вакуумной камеры.
На мокрую отливку накладывают лист чистой гладкой бумаги (писчей) диаметром 20 см. По поверхности бумаги прокатывают под собственной массой валик, обтянутый фетром. Далее мокрую отливку снимают с сетки вручную.
Сушку отливок проводят в одной из сушильных камер, управляемых кранами 19 и 20 и работающих автономно. Для этого открывают крышку сушильной камеры, приподняв ручку-замок и откинув камеру «от себя», на сетку сушильной камеры помещают лист гладкой бумаги с находящейся сверху отливкой, накрывают ее листом ватмана в виде круга диаметром 20 см, закрывают крышку, поворотом крана 19 или 20 в положение «О» подключают вакуумнасос.
Продолжительность сушки составляет 15–20 мин. По окончании сушки кран 19 или 20 переводят в положение «З», открывают крышку сушилки, вынимают высушенную отливку, отделяют от листа ватмана и покровной бумаги и взвешивают на технических весах.
Определение физико-механических свойств древесной массы
Для определения физико-механических свойств ДМ полученные стандартные отливки массой 75 или 100 г/м2 кондиционируют до равновесного состояния при относительной влажности воздуха 65±2 %, температуре 20±0,5 °С в течение 3 ч. Для ДМ определяют следующие физико-механические свойства:
30