
Оборудование для физико-механической обработки материалов
..pdfМинистерство образования и науки Российской Федерации
Государственное образовательное учреждение высшего профессионального образования «Пермский государственный технический университет»
А.В. Беляев, С.Х. Загидуллин, В.М. Беляев
ОБОРУДОВАНИЕ ДЛЯ ФИЗИКО-МЕХАНИЧЕСКОЙ
ОБРАБОТКИ МАТЕРИАЛОВ
Утверждено Редакционно-издательским советом университета
в качестве учебного пособия
Издательство Пермского государственного технического университета
2011
ELIB.PSTU.RU
УДК 66.022.5 Б44
Рецензенты:
канд. техн. наук Н.М. Рябчиков (ООО «УралПромБезопасность»);
канд. техн. наук Е.Р. Мошев (Пермский государственный технический университет)
Беляев, А.В.
Б44 Оборудование для физико-механической обработки материалов: учеб. пособие / А.В. Беляев, С.Х. Загидуллин, В.М. Беляев. – Пермь: Изд-во Перм. гос. техн. ун-та, 2011. – 82 с.
ISBN 978-5-398-00577-6
Даны общие сведения о процессах измельчения, классификации, смешения и гранулирования твердых материалов. Рассмотрены конструкции и принцип действия основного оборудования для осуществления перечисленных механических процессов.
Предназначено для студентов специальностей «Машины и аппараты химических производств» и «Машины и аппараты нефтегазопереработки» очной и заочной форм обучения.
УДК 66.022.5
ISBN 978-5-398-00577-6 |
© ГОУ ВПО |
|
«Пермский государственный |
|
технический университет», 2011 |
|
2 |
ELIB.PSTU.RU
ОГЛАВЛЕНИЕ |
|
ВВЕДЕНИЕ................................................................................... |
5 |
1. ИЗМЕЛЬЧЕНИЕ ТВЕРДЫХ МАТЕРИАЛОВ....................... |
6 |
1.1. Физические основы измельчения.................................. |
6 |
1.2. Классификация измельчителей...................................... |
12 |
1.3. Устройство дробилок ..................................................... |
14 |
1.3.1. Щековые дробилки............................................... |
14 |
1.3.2. Конусные дробилки.............................................. |
16 |
1.3.3. Валковые дробилки .............................................. |
18 |
1.3.4. Молотковые дробилки.......................................... |
20 |
1.3.5. Роторные (отражательные) дробилки................. |
22 |
1.3.6. Дезинтеграторы и дисмембраторы...................... |
23 |
1.4. Устройство мельниц....................................................... |
24 |
1.4.1. Барабанная (шаровая и стержневая) мельница.... |
24 |
1.5. Циклы работы измельчителей....................................... |
29 |
2. КЛАССИФИКАЦИЯ И СОРТИРОВКА МАТЕРИАЛА....... |
30 |
2.1. Грохочение...................................................................... |
30 |
2.1.1. Способы грохочения............................................. |
32 |
2.1.2. Устройство грохотов............................................ |
34 |
2.1.2.1. Плоские неподвижные грохоты.............. |
34 |
2.1.2.2. Барабанные грохоты................................ |
35 |
2.1.2.3. Валковые грохоты.................................... |
37 |
2.1.2.4. Плоские качающиеся грохоты................ |
39 |
2.1.2.5. Гирационные (полувибрационные) |
|
грохоты.................................................................. |
40 |
2.1.2.6. Вибрационные инерционные грохоты... |
41 |
2.1.2.7. Вибрационные электромагнитные |
|
грохоты.................................................................. |
42 |
2.1.2.8. Дуговые и конусные сита (щелевые |
|
сита) ....................................................................... |
44 |
2.2. Гидравлическая классификация.................................... |
45 |
2.2.1. Отстойник-конус (вертикальный отстойник)..... |
45 |
2.2.2. Отстойник Брандеса (горизонтальный |
|
отстойник) ....................................................................... |
46 |
2.3. Механическая классификация. ...................................... |
47 |
2.3.1. Шнековые (спиральные) классификаторы ......... |
47 |
3 |
|
ELIB.PSTU.RU
2.3.2. Реечные классификаторы..................................... |
48 |
2.3.3. Гидроциклоны....................................................... |
49 |
2.4. Пневматическая классификация (воздушная |
|
сепарация)............................................................................... |
51 |
2.4.1. Сепарация в псевдоожиженном слое.................. |
51 |
2.4.2. Классификатор с пересыпными полками........... |
53 |
3. СМЕШИВАНИЕ....................................................................... |
54 |
3.1. Аппараты для смешивания сыпучих |
|
и пастообразных материалов (смесители) ........................... |
54 |
3.1.1. Барабанные смесители ......................................... |
55 |
3.1.2. Лопастные смесители........................................... |
57 |
3.1.3. Смеситель с псевдоожижением материала |
|
вращающимся ротором.................................................. |
58 |
3.1.4. Пневмосмеситель.................................................. |
59 |
3.1.5. Гравитационно-ударный и гравитационно- |
|
лотковый смесители....................................................... |
60 |
3.1.6. Планетарно-шнековые смесители....................... |
61 |
3.1.7. Конусно-шнековые смесители............................. |
62 |
4. ГРАНУЛИРОВАНИЕ............................................................... |
62 |
4.1. Метод окатывания на движущихся поверхностях....... |
64 |
4.1.1. Барабанный гранулятор........................................ |
65 |
4.1.2. Тарельчатый гранулятор...................................... |
66 |
4.1.3. Лопастной гранулятор.......................................... |
67 |
4.1.4. Виброгранулятор .................................................. |
68 |
4.1.5. Скоростной роторно-центробежный |
|
гранулятор....................................................................... |
69 |
4.2. Гранулирование путем разбрызгивания расплавов |
|
и охлаждение их во встречном потоке воздуха................... |
70 |
4.3. Гранулирование суспензий и плавов |
|
в псевдоожиженном слое гранул с одновременной |
|
сушкой.................................................................................... |
71 |
4.4. Гранулирование методом формования (экструзии)..... |
75 |
4.5. Гранулирование методом прессования |
|
(вальцедробления) ................................................................. |
76 |
Список рекомендуемой литературы............................................ |
81 |
4
ELIB.PSTU.RU
ВВЕДЕНИЕ
Во многих отраслях химической и нефтехимической промышленности широко применяются механические процессы, такие как: измельчение, классификация, смешение порошков, гранулирование и др.
Механические процессы используются в тех производствах, где химической переработке подвергается твердое минеральное сырье, когда процессы осуществляются в гетерогенной среде или когда готовый продукт выпускается в порошкообразной либо гранулированной формах.
В результате измельчения значительно увеличивается удельная поверхность обрабатываемого материала, что позволяет ускорить такие процессы, как растворение, сушка, выщелачивание, обжиг, химическое взаимодействие и др.
Процесс измельчения осуществляется чаще всего в замкнутом цикле с классификацией, когда крупные частицы, не удовлетворяющие требованиям, предъявляемым к размеру конечного продукта, вновь возвращаются в измельчитель для дальнейшей обработки.
Измельчение в комплексе с классификацией повышает производительность оборудования, снижает расход энергии на единицу готового продукта.
Необходимость гранулирования порошковых материалов обусловлена преимуществами гранул по сравнению с порошкообразной формой веществ. Гранулы обладают хорошей сыпучестью, не налипают на поверхность бункера, не слеживаются при хранении, не пылят при транспортировании и расфасовке.
Для получения многокомпонентных порошкообразных или пастообразных смесей используются разнообразные смесители, конструкции которых в основном зависят от свойств отдельных компонентов смеси, а также от качества и интенсивности смешения.
5
ELIB.PSTU.RU
В настоящем пособии кратко рассмотрена конструкция и принцип действия основного оборудования для осуществления перечисленных механических процессов.
1. ИЗМЕЛЬЧЕНИЕ ТВЕРДЫХ МАТЕРИАЛОВ
1.1. Физические основы измельчения
Во многих случаях возникает необходимость измельчения частиц твердого материала с целью увеличения поверхности контакта при обжиге, растворении, химических реакциях, флотации и других процессах.
Измельчение – это процесс уменьшения размеров частиц, как правило, до 2 мм.
Дробление – это предварительное грубое измельчение частиц до размеров не более 2…5 мм. Цель дробления – получение кускового продукта необходимой крупности, а также подготовка к измельчению и размолу.
Размол – это тонкое измельчение частиц до порошкообразного состояния размером менее 0,1 мм.
Для измельчения используется различное разрушающее воздействие (рис. 1.1).
В большинстве случаев в машинах реализуются одновременно все эти способы, но главную роль играет один из них (тот, для которого сконструирована данная машина).
Метод измельчения выбирают исходя из физико-механиче- ских свойств материала (табл. 1.1) и требуемой степени измельчения i (табл. 1.2).
6
ELIB.PSTU.RU
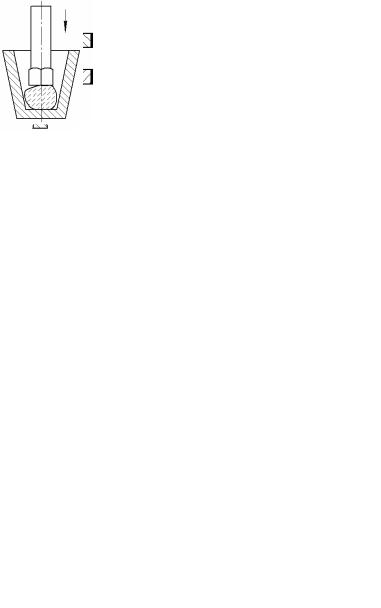
|
|
|
|
|
|
|
|
|
|
|
|
|
|
|
|
|
|
|
а |
|
б |
|
в |
|
|
|
|
|
|
|
|
|
|
|
|
|
|
|
|
|
|
г |
д |
е |
Рис. 1.1. Методы измельчения: а – раздавливание; б – раскалывание; в – истирание; г – удар; д – резание; е – излом
Таблица 1.1
Выбор метода измельчения в зависимости от свойств материала
№ |
Материал |
Метод |
|
Пример |
|||
п/п |
|
измельчения |
|
|
|
|
|
1 |
Твердый |
Раздавливание |
|
|
|
|
|
|
и хрупкий |
и удар |
|
|
|
|
|
|
|
|
|
|
|
|
|
|
|
|
|
|
|
|
|
|
|
|
|
|
|
|
|
7
ELIB.PSTU.RU
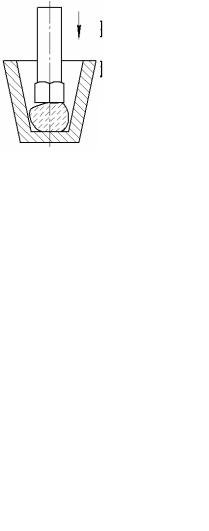
|
|
|
|
|
|
Продолжение табл. 1.1 |
|||||||
|
|
|
|
|
|
|
|
|
|
|
|
|
|
№ |
Материал |
Метод |
|
|
|
Пример |
|||||||
п/п |
|
измельчения |
|
|
|
|
|
|
|
|
|
|
|
2 |
Твердый |
Раздавливание |
|
|
|
|
|
|
|
|
|
|
|
|
и вязкий |
|
|
|
|
|
|
|
|
|
|
|
|
|
|
|
|
|
|
|
|
|
|
|
|
|
|
|
|
|
|
|
|
|
|
|
|
|
|
|
|
3 |
Хрупкий, |
Удар, раскалы- |
|
|
|
|
|
|
|
|
|
|
|
|
|
|
|
|
|
|
|
|
|
|
|||
|
средней |
вание, истира- |
|
|
|
|
|
|
|
|
|
|
|
|
твердости |
ние |
|
|
|
|
|
|
|
|
|
|
|
|
|
|
|
|
|
|
|
|
|
|
|
|
|
|
|
|
|
|
|
|
|
|
|
|
|
|
|
4 |
Вязкий, |
Истирание |
|
|
|
|
|
|
|
|
|
|
|
|
средней |
и удар |
|
|
|
|
|
|
|
|
|
|
|
|
твердости |
|
|
|
|
|
|
|
|
|
|
|
|
|
|
|
|
|
|
|
|
|
|
|
|
|
|
|
|
|
|
|
|
|
|
|
|
|
|
|
|
|
|
|
|
|
|
|
|
|
|
|
|
|
|
|
|
|
8 |
|
|
|
|
|
|
|
|
ELIB.PSTU.RU

Таблица 1.2
Зависимость степени измельчения от метода измельчения
Вид |
Рекомендуемый |
Размер |
Размер |
Степень |
|
измельче- |
метод |
исходных |
частиц после |
измельче- |
|
ния |
измельчения |
частиц D, |
измельчения d, |
ния i |
|
|
|
мм |
мм |
|
|
Крупное |
Раздавливание, |
1500…300 |
300…100 |
2…6 |
|
дробление |
раскалывание |
|
|
|
|
Среднее |
Раздавливание, |
|
|
|
|
раскалывание, |
300…100 |
50…10 |
5…10 |
||
дробление |
удар |
|
|
|
|
|
|
|
|
||
Мелкое |
Раздавливание, |
50…10 |
10…2 |
10…50 |
|
дробление |
удар |
||||
|
|
|
|||
Тонкий |
Раздавливание, |
10…2 |
2…0,075 |
50 и более |
|
размол |
удар |
||||
|
|
|
|||
|
Истирание, |
|
|
|
|
Сверхтон- |
гидравлический |
10…0,075 |
0,075…0,0001 |
– |
|
кий размол |
удар, вибрация |
||||
|
высокой частоты |
|
|
|
Степень измельчения (i) – это отношение средневзвешенного размера частиц материала до и после измельчения.
i = |
Dср |
, |
(1.1) |
|
|||
|
dср |
|
где Dср – средневзвешенный размер частиц до измельчения, мм; dср – средневзвешенный размер частиц после измельчения, мм.
D = D1 a1 + D2 a2 + ... + Dn an , |
|||
ср |
a1 |
+ a2 |
+ ... + an |
|
где Dn – средний размер частиц n-ой фракции в исходном материале, мм; an – массовое процентное содержание частиц n-ой фракции в исходном материале.
9
ELIB.PSTU.RU
a1 + a2 + ... + an = 100 %.
Куски, получаемые в результате измельчения, не имеют правильной формы. Размеры частиц (D и d) определяют размером отверстий сит, через которые просеивают материал до и после измельчения (ситовой анализ).
Каждая машина может обеспечить только ограниченную степень измельчения. Например, для щековых дробилок i = = 3…6; для валковых дробилок i = 5…15. Поэтому на практике измельчение проводят в несколько стадий.
Крупное и среднее дробление, как правило, производится сухим способом, а мелкое дробление и размол – сухим или мокрым способами.
Мокрое измельчение имеет ряд преимуществ:
•уменьшается пылеобразование;
•улучшаются условия выгрузки материала (так как образуется подвижная суспензия);
•повышается равномерность помола;
•существенно сокращаются энергозатраты за счет эффекта Ребиндера (жидкость, проникая в микротрещины материала, оказывает расклинивающее действие; жидкость как бы «распирает» материал).
При измельчении совершается работа внешних сил, преодолевающих силы взаимного сцепления частиц материала. Механизм этого процесса чрезвычайно сложен. Поэтому в настоящее время существует около 100 гипотез, объясняющих в той или иной степени механизм измельчения, но наибольшее распространение получили только некоторые из них.
При измельчении куски реального твердого материала подвергаются сначала объемной деформации, а затем разрушаются
по сечениям, ослабленным различными дефектами (микро- и макротрещинами), с образованием новых поверхностей.
10
ELIB.PSTU.RU