
Оборудование для физико-механической обработки материалов
..pdf
Достоинства:
простота конструкции;
отсутствие движущихся частей;
малое истирание частиц;
непрерывность работы;
низкая энергоемкость.
Недостатки:
сравнительно низкое качество смешивания;
ограниченность применения (только для хорошо сыпучих материалов с близкими физико-механическими свойствами).
3.1.6. Планетарно-шнековые смесители
Данная конструкция представляет собой корпус конического типа с установленным внутри шнеком (рис. 3.11).
Во время работы шнек совершает одновременно вращательное и планетарное движения. При помощи шнека материал поднимается в верхнюю часть аппарата, откуда под действием силы тяжести вновь опускается вниз. Затем цикл повторяется.
Данные смесители применяют для перемешивания как сыпучих, так и пастообразных материалов.
Достоинства:
высокое качество смеши-
вания.
Недостатки:
ограниченность внутренного объема аппарата (до 6 м3);
сложность привода; |
Рис. 3.11. Устройство плане- |
периодичность работы. |
тарно-шнекового смесителя |
61
ELIB.PSTU.RU

3.1.7. Конусно-шнековые смесители
Данная конструкция представляет собой корпус конического типа, внутри которого располагается мешалка. Загрузка материала в аппарат производится периодически сверху, а выгрузка снизу (рис. 3.12).
Рис. 3.12. Схема конусно-шнеко- вого смесителя: 1 – конический шнек; 2 – цилиндрический шнек
Мешалка состоит из двух шнеков (с левой и правой навивкой), установленных на одном валу. При вращении вала конический шнек бóльшего диаметра способствует подъему материала вдоль стенки корпуса, а шнек меньшего диаметра продвигает материал сверху вниз. Таким образом происходит принудительное перемешивание материала.
Достоинства:
простота конструкции;
высокая эффективность.
Недостатки:
непригодность для влажных и липких материалов;
периодичность работы.
4. ГРАНУЛИРОВАНИЕ
Наряду с процессами дробления и измельчения в химической промышленности часто возникает обратная задача – укрупнение порошкообразных материалов с получением готового продукта в виде гранул определенного размера, формы и проч-
62
ELIB.PSTU.RU
ности. Гранулированию могут подвергаться не только порошки, но и расплавы, суспензии и пасты.
Гранулированные материалы обладают следующими преимуществами:
хорошая сыпучесть и высокая насыпная плотность;
высокая плотность структуры гранул;
меньшая пылимость и слеживаемость при хранении
итранспортировании;
бóльшая пригодность для процессов автоматизированного и механизированного дозирования, смешивания, транспортирования.
Для гранулирования используют следующие основные методы:
окатывание порошков в присутствии жидких связующих добавок;
разбрызгивание расплавов на отдельные капли с последующим охлаждением их при свободном падении в специальных башнях (метод приллирования);
распыливание суспензий в псевдоожиженном слое гранул с одновременной сушкой;
прессование порошков под большим давлением с последующим дроблением прессата и классификацией продукта.
Выбор конкретного метода гранулирования определяется рядом факторов:
свойствами исходного материала (порошок, расплав, суспензия);
требованиями к готовому продукту;
мощностью производства и др.
63
ELIB.PSTU.RU

4.1. Метод окатывания на движущихся поверхностях
Процесс состоит из нескольких стадий:
смешивание исходного порошка и частиц рéтура* со связующей жидкостью;
образование зародышей гранул за счет действия капиллярных сил притяжения между смоченными частицами порошка;
рост и окатывание зародышей с уплотнением их внутренней структуры за счет сил взаимных ударов и ударов о внутреннюю поверхность гранулятора сырцовых гранул. Величина сил при взаимных ударах гранул может достигать нескольких десятков атмосфер.
упрочнение малопрочных коагуляционных контактов частиц внутри гранул за счет сушки и кристаллизации связующей жидкости;
классификация сухих гранул по размерам. Мелкая фракция возвращается в виде рéтура и служит зародышем новых гранул. Крупную фракцию дробят и дополнительно грохотят,
асредняя фракция выводится на склад готовой продукции. Механизм гранулообразования методом окатывания чрез-
вычайно сложный и многофакторный. Интенсивное гранулирование происходит в строго определенных для каждого материала условиях.
Большое влияние оказывает химический состав и расход связующей жидкости. При недостатке связующего вещества степень гранулирования низка, гранулы плохо окатаны и малопрочны. При чрезмерном увлажнении образующиеся гранулы слипаются друг с другом с образованием крупных комков.
Большое значение имеют и следующие факторы:
скорость вращения гранулятора;
степень заполнения гранулятора материалом;
*Рéтур – это отсев, возвращаемый обратно в цикл (добавляемый
кисходному продукту). Размер частиц, как правило, менее 1 мм.
64
ELIB.PSTU.RU

угол наклона гранулятора;
температура и т.д.
В промышленности нашли широкое применение барабанные, тарельчатые (чашевые или дисковые) и лопастные грануляторы.
4.1.1. Барабанный гранулятор
Данная конструкция представляет собой полый барабан диаметром до 4 м и длиной до 11 м, вращающийся на двух бандажах (рис. 4.1).
Рис. 4.1. Схема барабанного гранулятора
Угол наклона барабана составляет от 1 до 3°. Производительность барабанного гранулятора – 30…50 т/ч.
Для введения связующего вещества используются различные распределительные устройства: форсунки, труба с распределителем в виде «пилы» и др. С целью уменьшения налипания внутри аппарата предусмотрены очистные ножи (скребки), а также покрытие внутренней поверхности аппарата гидрофобным материалом (гуммирование).
В зависимости от степени заполнения и частоты вращения барабана различают режим скольжения, челночный, перекатный и водопадный режимы. Наиболее благоприятным является перекатный режим.
Достоинства:
большая единичная мощность (до 80 т/ч);
65
ELIB.PSTU.RU

малая чувствительность к колебаниям нагрузки;
возможность совмещения гранулирования и химических реакций;
герметичность.
Недостатки:
громоздкость;
полидисперсность получаемых гранул (выход товарной фракции не более 50…65 %);
сложность визуального контроля над ходом процесса.
4.1.2. Тарельчатый гранулятор
Основная часть тарельчатого гранулятора – это наклонная тарель диаметром от 0,5 до 7,0 м, снабженная бортом (рис. 4.2).
Рис. 4.2. Схема тарельчатого гранулятора
Высота борта составляет 10…20 % от диаметра тарели. Оптимальные значения угла наклона, частоты вращения и высоты борта тарели устанавливаются опытным путем.
Место ввода сухого порошка и связующего вещества определяется требованиями к транспорту готового продукта. Для получения мелких гранул порошок подают в верхнюю часть тарели, для получения более крупных – на дно тарели.
66
ELIB.PSTU.RU

Одновременно с гранулированием в тарели наблюдается эффективная классификация гранул по размерам. Через борт самопроизвольно переваливаются только крупные гранулы, а мелкие остаются в аппарате и дорастают до требуемых размеров. Благодаря этому выход товарной фракции может достигать 90 % и более.
Достоинства:
большая интенсивность процесса;
высокая прочность гранул;
однородный гранулометрический состав продукта;
меньшая занимаемая производственная площадь;
легкость визуального контроля и регулирования.
Недостатки:
меньшая единичная мощность (до 30…50 т/ч);
бóльшая чувствительность к колебаниям нагрузки
ивлажности;
пылеобразование.
4.1.3. Лопастной гранулятор
Данная конструкция представляет собой один или два вращающихся навстречу друг другу вала с лопастями (рис. 4.3).
Рис. 4.3. Схема лопастного гранулятора
67
ELIB.PSTU.RU
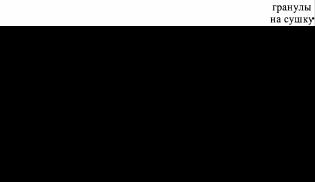
Конструкция гранулятора аналогична конструкции лопастного смесителя. Угол наклона лопастей устанавливают экспериментально. Окружная скорость вращения лопаток гранулятора составляет 1,0…1,5 м/с.
В этих аппаратах создаются хорошие условия для равномерного перемешивания материала со связующим веществом.
Достоинства:
готовый продукт отличается высокой однородностью.
Недостатки:
трудность визуального наблюдения за процессом;
налипание материала на лопатки.
4.1.4. Виброгранулятор
Данная конструкция представляет собой наклонную поверхность (вибростол), закрепленную на упругих элементах. Установленный на ней вибратор придает поверхности колебательное движение (рис. 4.4).
Гранулирование происходит в виброкипящем слое материала.
Рис. 4.4. Схема виброгранулятора: 1 – вибростол; 2 – вибратор
68
ELIB.PSTU.RU

Достоинства:
высокая интенсивность процесса;
получаемые гранулы однородные и плотные.
Недостатки:
малая площадь вибростола, что ограничивает единичную мощность гранулятора.
4.1.5. Скоростной роторно-центробежный гранулятор
Данная конструкция представляет собой цилиндрический вертикальный аппарат с установленным внутри ротором с лопатками, которые располагаются в несколько рядов и имеют возможность регулирования угла наклона (рис. 4.5).
Исходный порошок и связующая жидкость подаются в верхнюю часть аппарата. Гранулирование осуществляется в поле центробежных сил в закрученных воздушных потоках.
Достоинства:
очень большая скорость процесса (2…3 с);
компактность.
Недостатки:
сложность очистки внутренних поверхностей.
Рис. 4.5. Схема роторно-центро- бежного гранулятора
69
ELIB.PSTU.RU

4.2.Гранулирование путем разбрызгивания расплавов
иохлаждение их во встречном потоке воздуха
Этот метод широко используется для гранулирования азотных удобрений (карбамида, аммиачной селитры и т.п.), а также в порошковой металлургии. Его сущность заключается в разбрызгивании плава при помощи центробежного или статического разбрызгивателей.
В зависимости от температуры плава данная конструкция представляет собой капитальное сооружение высотой от 30…35
до 70…80 м (рис. 4.6).
Рис. 4.6. Схема грануляционной башни
70
ELIB.PSTU.RU