
Оборудование для физико-механической обработки материалов
..pdf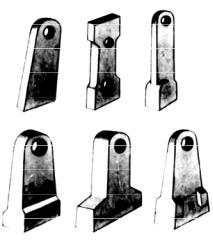
На вращающемся горизонтальном валу насажены диски, между которыми шарнирно подвешены молотки (рис. 1.12).
Рис. 1.12. Молотки (била)
Материал дробится под действием ударов быстровращающихся (с окружной скоростью 30–55 м/с) молотков. Дробление происходит также при ударах кусков материала, отбрасываемых молотками, о плиты. Дополнительно материал измельчается путем удара, раздавливания и некоторого истирания на колосниковой решетке, через которую измельченный материал разгружается, падая вниз. Степень измельчения дробилки i = 10…15.
По мере износа молотки заменяют или перевешивают на другое место с целью балансировки ротора.
Молотковые дробилки отличаются высокой производительностью (на единицу массы машины), пониженным удельным расходом энергии на дробление и высокой степенью измельчения по сравнению со щековыми и конусными дробилками. Недостатками молотковых дробилок являются значительный износ молотков и плит, сложность балансировки ротора.
Молотковые дробилки применяются для дробления хрупких и волокнистых материалов, а также материалов с малой аб-
21
ELIB.PSTU.RU

разивностью (уголь, известняк) и мало пригодны для измельчения прочных и абразивных (быстрый износ) или влажных материалов (более 15 % воды).
1.3.5. Роторные (отражательные) дробилки
Из материала, поступающего на измельчение в роторную дробилку (рис. 1.13), на решетке отсеивается мелочь, и материал поступает на ротор, вращающийся с окружной скоростью 12– 70 м/с (в зависимости от требуемой степени измельчения). Лопатками ротора куски материала отбрасываются на шарнирно подвешенные отражательные щитки. Измельчение осуществляется ударами лопаток и при ударах кусков о щитки. Кроме того, отраженные от щитков куски на большой скорости сталкиваются с кусками материала, отброшенными ротором, при этом происходит дополнительное самоизмельчение материала. Поэтому
Рис. 1.13. Схема роторной (отражательной) дробилки: 1 – решетка; 2 – ротор; 3 – лопатки; 4 – щитки; 5 – цепная завеса
22
ELIB.PSTU.RU

отражательные дробилки близки по принципу действия к мельницам без мелющих тел и могут использоваться для тонкого измельчения.
Цепная завеса служит для предотвращения вылета кусков материала из загрузочной воронки дробилки.
Благодаря многостадийному измельчению в пространствах между щитками и ротором получается достаточно однородный продукт, а достигаемая степень измельчения i = 40…50.
1.3.6. Дезинтеграторы и дисмембраторы
Дезинтегратор представляет собой дробилку ударного действия, рабочим органом которой являются два вращающихся в разные стороны ротора (рис. 1.14).
Рис. 1.14. Устройство дезинтегратора: 1, 2 – диски; 3 – пальцы; 4, 5 – валы; 6, 7 – шкивы; 8 – загрузочная воронка
Каждый ротор состоит из дисков, закрепленных с помощью ступиц на отдельных валах. На дисках имеются стальные цилиндрические пальцы, размещенные по концентрическим окружностям так, что каждый ряд пальцев одного ротора входит между двумя рядами другого. Валы роторов приводятся во вращение от индивидуальных электродвигателей через шкивы.
23
ELIB.PSTU.RU

|
|
Дробимый материал пода- |
|
|
ется через загрузочную воронку |
|
|
к центру роторов. Пальцы, рас- |
|
|
положенные по внутренней ок- |
|
|
ружности, дробят материал и от- |
|
|
брасывают его куски к следую- |
|
|
щему концентрическому ряду, |
Рис. 1.15. |
Схема движения |
вращающемуся в противопо- |
ложном направлении (рис. 1.15). |
материала в дезинтеграторе |
Таким образом, материал |
|
|
|
последовательно и многократно |
дробится пальцами ротора. Расстояние между пальцами последнего ряда определяет максимальный размер кусков раздробленного продукта.
В отличие от дезинтеграторов дисмембраторы имеют один ротор. Внутренняя стенка корпуса выполняет роль второго (неподвижного) диска, то есть является статором. Пальцам дисмембратора, установленным в статоре и роторе, часто придают форму ножей для измельчения материала срезом и разрывом.
Все описанные ударно-центробежные измельчители высокопроизводительны, позволяют получать высокую степень измельчения и используются в широком диапазоне степеней измельчения. Недос-
татками этих машин являются повышенный износ дробящих тел, большое пылеобразование, необходимость точной балансировки роторов.
1.4.Устройство мельниц
1.4.1.Барабанная (шаровая и стержневая) мельница
Барабанная мельница – это машина, в которой материал измельчается внутри вращающегося корпуса (барабана) под воздействием мелющих тел или самоизмельчением. Мелющи-
24
ELIB.PSTU.RU

ми телами служат металлические шары ( 25…150 мм) или стержни.
Барабанная мельница (рис. 1.16) состоит из горизонтального цилиндрического корпуса, закрытого торцовыми крышками с пустотелыми цапфами, установленными в подшипниках. Мельница приводится во вращение через зубчатый венец от шестерни приводного вала. Барабан и крышки мельницы футерованы стальными плитами, поверхность которых для уменьшения проскальзывания мелющих тел часто выполняется волнообразной или ступенчатой (рис. 1.17 и 1.18). Материал в мельницу подается питателем через загрузочную цапфу. Измельченный материал удаляется через разгрузочную цапфу на другом конце аппарата.
Рис. 1.16. Схема барабанной мельницы (с шарами): 1 – корпус; 2, 3 – крышки; 4 – подшипник; 5 – зубчатый венец; 6 – плита футеровки; 7 – загрузочная цапфа; 8 – разгрузочная цапфа; 9 – мелющие тела
25
ELIB.PSTU.RU

аб
в
Рис. 1.17. Виды футеровки: а – со спиральными выступами; б – тонкая, из катаной стали; в – рельсобетонная
а |
б |
в |
г |
д |
Рис. 1.18. Профили футеровочных плит: а – внахлестку; б – волнистая; в – с выступом; г – гладкая; д – ступенчатая
При вращении барабана мелющие тела увлекаются под действием центробежной силы и силы трения вместе с поверхностью стенок на определенную высоту, а затем свободно падают и измельчают материал ударом, раздавливанием и истира-
нием (рис. 1.19).
26
ELIB.PSTU.RU

Для эффективной работы шаровой мельницы необходимо, чтобы барабан мельницы вращался с определенной частотой (n), при которой шары в барабане падали бы с наибольшей высоты и имели бы максимальную скорость падения, так называемый «водопадный режим».
Критическое число оборотов барабана мельницы, при котором шары в верхней точке барабана из-за центробежной силы
не смогут оторваться от стенки и будут вращаться вместе с ней, определяется по следующей формуле:
1800
nкр= D , (1.8)
где nкр – критическая частота вращения барабана, об/мин; D – внутренний диаметр барабана, мм.
В большинстве случаев число оборотов шаровых мельниц принимается равным 75 % от критической частоты вращения.
n = |
32 |
. |
(1.9) |
|
|||
|
D |
|
Достоинства шаровых мельниц:
надежность;
безопасность;
простота обслуживания;
высокая степень измельчения.
Недостатки шаровых мельниц:
громоздкость;
большой вес;
27
ELIB.PSTU.RU
низкий КПД;
неравномерный помол;
износ мелющих тел и загрязнение материала продуктами этого износа;
шум при работе.
По конструкции стержневые мельницы близки к шаровым. Основное отличие заключается в форме дробящих тел, которыми служат стальные стержни 40…100 мм и длиной на 25…50 мм меньше внутренней длины барабана.
Скорость вращения барабана на 25…30 % меньше, чем в шаровых мельницах, так как стержни перекатываются без свободного падения, но вес загрузки на 20…25 % больше, чем в шаровой мельнице.
Измельчение в барабанных мельницах может осуществляться как в сухом, так и в мокром режимах. Измельчение в мокром режиме более предпочтительно, так как исключает пылеобразование и уменьшает энергозатраты на проведение процесса. Однако при этом возникает необходимость последующей сушки материала.
Достоинства стержневых мельниц:
надежность;
безопасность;
простота обслуживания;
более равномерный помол.
Недостатки стержневых мельниц:
громоздкость;
большой вес;
низкий КПД;
шум при работе.
степень измельчения ниже, чем у шаровых мельниц;
неравномерный износ стержней (в центре больше).
28
ELIB.PSTU.RU
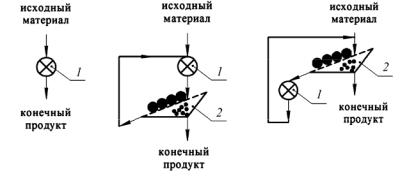
1.5. Циклы работы измельчителей
Дробилки и мельницы работают в открытом или замкнутом циклах. В открытом цикле (рис. 1.20, а) материал проходит через измельчающую машину (дробилка, мельница) только один раз. Так проводят крупное и среднее дробление, когда нет необходимости в точных размерах зерна конечного продукта. При замкнутом цикле материал неоднократно проходит через измельчитель.
Исходный продукт после измельчителя направляется в классификатор, где происходит отделение частиц с размерами превышающими требуемые (так называемая контрольная классификация) и их возвращение для повторного измельчения (рис. 1.20, б). Более мелкие частицы отводятся как конечный продукт.
При наличии мелких частиц в исходном материале производят их удаление в конечный продукт до процесса измельчения,
так называемая предварительная классификация (рис. 1.20, в).
а |
б |
в |
Рис. 1.20. Циклы работы измельчителей: а – открытый цикл; б – замкнутый цикл с контрольной классификацией; в – замкнутый цикл с предварительной и контрольной классификацией; 1 – измельчитель; 2 – классификатор
29
ELIB.PSTU.RU
Работа по замкнутому циклу широко применяется при тонком измельчении и позволяет снизить удельный расход энергии, повысить производительность измельчающей машины, гарантируя однородность и размер максимального зерна конечного продукта. Однако при этом существенно усложняется конструкция установки, так как требуется использование элеваторов. Кроме того, если попадаются недробимые тела, то они могут оставаться в цикле неопределенно долгое время.
2.КЛАССИФИКАЦИЯ
ИСОРТИРОВКА МАТЕРИАЛА
Классификация – это разделение зернистых материалов на отдельные фракции крупности.
Используют три вида классификации:
1.Грохочение – механическое разделение на ситах.
2.Гидравлическая классификация – разделение твердых частиц по размерам, основанное на различной скорости осаждения частиц в воде.
3.Воздушная сепарация (классификация) основана на различной скорости осаждения частиц в воздухе.
Грохочение является наиболее распространенным и универсальным способом классификации, позволяет разделять частицы размером от 40 мкм до 250 мм. Два других вида классификации пригодны только для частиц размером менее 2 мм.
Классификация может применяться как вспомогательная операция в циклах дробления и измельчения и как самостоятельная операция для получения готового продукта с заданными гранулометрическими характеристиками. В последнем случае этот процесс называется сортировкой.
2.1. Грохочение
Грохочение проводят путем просеивания материала через одно или несколько сит. Сита могут быть изготовлены в виде
30
ELIB.PSTU.RU