
Трубопроводная арматура техническое обслуживание ревизия и ремонт
..pdf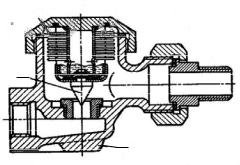
туры в конденсатоотводчике, при заполнении его конденсатом, уменьшается давление в сильфоне, вследствие чего золотник поднимается и начинается слив конденсата из системы.
Когда в конденсатоотводчик начинает поступать пар, температура в нем повышается и жидкость в сильфоне испаряется, давление при этом возрастает и золотник опускается, закрывая выход.
2
3
1
Рис. 25. Термостатический |
Рис. 26. Поплавковый |
конденсатоотводчик: 1 – корпус; |
конденсатоотводчик |
2 – диск; 3 – крышка; 4 – ось |
|
Для выпуска охлажденного конденсата используются также поплавковые конденсатоотводчики, которые могут быть как с открытым, так и закрытым поплавком. Конденсатоотводчик с открытым поплавком представлен на рис. 26.
Такой конденсатоотводчик работает следующим образом. Когда конденсат поступает во внутрь корпуса, поплавок всплывает и запирает выходное отверстие. По мере поступления конденсата он переливается и заполняет поплавок. Поплавок при этом тонет, а выходное отверстие открывается, и часть конденсата за счет давления пара отводится наружу.
21
Стр. 21 |
ЭБ ПНИПУ (elib.pstu.ru) |
3. МАРКИРОВКА ТРУБОПРОВОДНОЙ АРМАТУРЫ
Условное обозначение трубопроводной арматуры состоит из букв и цифр. Первые две цифры обозначают тип арматуры. Основные типы трубопроводной арматуры представлены в табл. 1.
|
|
Таблица 1 |
|
Основные типы трубопроводной арматуры |
|
|
|
|
№ п/п |
Тип арматуры |
Условное |
|
|
обозначение |
1 |
Кран спускной |
10 |
2 |
Кран для трубопровода |
11 |
3 |
Запорное устройство указателя уровня |
12 |
4 |
Вентиль запорный, клапан отсечной |
13, 14, 15, 22, 24 |
5 |
Клапан обратный |
16 |
6 |
Клапан предохранительный |
17 |
7 |
Клапан перепускной |
20 |
8 |
Регулятор давления (клапан редукционный) |
18, 21 |
9 |
Клапан регулирующий |
25, 26 |
10 |
Клапан смесительный |
27 |
11 |
Задвижка |
30, 31 |
12 |
Затвор дисковый |
32 |
13 |
Конденсатоотводчик |
45 |
Буквы, следующие за первыми цифрами, обозначают материал корпуса (табл. 2).
Таблица 2
Условное обозначение материала корпуса трубопроводной арматуры
№ п/п |
Материал корпуса |
Условное |
|
|
обозначение |
1 |
Углеродистая сталь |
с |
2 |
Легированная сталь |
лс |
22
Стр. 22 |
ЭБ ПНИПУ (elib.pstu.ru) |
Окончание табл. 2
№ п/п |
Материал корпуса |
Условное |
|
|
обозначение |
3 |
Коррозионностойкая (нержавеющая) сталь |
нж |
4 |
Серый чугун |
ч |
5 |
Ковкий чугун |
кч |
6 |
Высокопрочный чугун |
вч |
7 |
Латунь, бронза |
Б |
8 |
Алюминий |
а |
9 |
Пластмассы (кроме винипласта) |
п |
10 |
Винипласт |
вп |
11 |
Фарфор |
к |
12 |
Титановый сплав |
тн |
13 |
Стекло |
ск |
Далее в маркировке могут следовать от одной до трех цифр. При наличии трех цифр первая из них обозначает вид привода, две последние – номер модели. Условное обозначение привода трубопроводной арматуры представлено в табл. 3.
Таблица 3
Условное обозначение привода трубопроводной арматуры
№ п/п |
Тип привода |
Условное |
|
|
обозначение |
1 |
Под дистанционное управление |
0 |
2 |
Механический с червячной передачей |
3 |
3 |
То же с цилиндрической зубчатой передачей |
4 |
4 |
То же с конической передачей |
5 |
5 |
Пневматический, пневмогидравлический |
6 |
6 |
Гидравлический |
7 |
7 |
Электромагнитный |
8 |
8 |
Электрический |
9 |
Последние буквы в маркировке трубопроводной арматуры обозначают материал уплотнительных поверхностей (табл. 4) или способ нанесения внутреннего покрытия корпуса (табл. 5).
23
Стр. 23 |
ЭБ ПНИПУ (elib.pstu.ru) |
Таблица 4
Условное обозначение материала уплотнительных поверхностей трубопроводной арматуры
№ п/п |
Материал уплотнительных поверхностей |
Условное |
|
|
обозначение |
1 |
Латунь, бронза |
бр |
2 |
Монель металл |
мн |
3 |
Коррозионностойкая (нержавеющая) сталь |
нж |
4 |
Баббит |
бт |
5 |
Стеллит |
ст |
6 |
Сормайт |
ср |
7 |
Кожа |
к |
8 |
Эбонит |
э |
9 |
Резина |
р |
10 |
Пластмасса (кроме винипласта) |
п |
11 |
Винипласт |
вп |
Таблица 5
Условное обозначение способа нанесения внутреннего покрытия трубопроводной арматуры
№ п/п |
Способ нанесения внутреннего покрытия |
Условное |
|
|
обозначение |
1 |
Гуммирование |
гм |
2 |
Эмалирование |
эм |
3 |
Свинцевание |
св |
4 |
Футерование пластмассой |
п |
В отдельных случаях после букв, обозначающих материал уплотнительных поверхностей, добавляют одну или две цифры, которые обозначают вариант исполнения данного изделия.
Изделия без вставных или наплавленных колец, когда уплотнительные поверхности выполнены непосредственно на корпусе или затворе, обозначаются буквами бк (без колец).
24
Стр. 24 |
ЭБ ПНИПУ (elib.pstu.ru) |
Для изделий, поставляемых для Крайнего Севера, в конце условного обозначения добавляются буквы хл.
Кроме того, корпус трубопроводной арматуры в зависимости от материала окрашивают в серый цвет, если он изготовлен из угле-
родистой стали, голубой – из нержавеющей стали, черный – из серого или ковкого чугуна.
Привод арматуры также имеет дополнительную окраску в зависимости от материала уплотнительных поверхностей:
–бронза, латунь – красный;
–нержавеющая сталь – голубой;
–баббит – желтый;
–кожа, резина – коричневый;
–эбонит – зеленый.
Ниже приведены некоторые примеры обозначения трубопроводной арматуры.
15кч16нж – вентиль, корпус изготовлен из ковкого чугуна, управление ручное, уплотнительные поверхности – из коррозионностойкой стали.
15нж13бк – вентиль, корпус – из нержавеющей стали, без уплотнительных колец.
30с97нж – задвижка, корпус и крышка изготовлены из углеродистой стали, уплотнительные поверхности корпуса и дисков наплавлены коррозионно-стойкой сталью, привод ручной.
31нж514нж1 – задвижка, материал корпуса и крышки – 12Х18Н9Т, уплотнительные поверхности наплавлены коррозионностойкой сталью, привод механический с конической передачей, исполнение 1.
11ч37п – кран, корпус которого изготовлен из серого чугуна, привод ручной, уплотнительная поверхность – из пластмассы.
25
Стр. 25 |
ЭБ ПНИПУ (elib.pstu.ru) |
4. РЕВИЗИЯ, ТЕХНИЧЕСКОЕ ОБСЛУЖИВАНИЕ И РЕМОНТ ТРУБОПРОВОДНОЙ АРМАТУРЫ
Ревизию, ремонт и испытания трубопроводной арматуры проводят, как правило, в период ревизии трубопроводов, а также во время остановки отдельных агрегатов, установок или цехов на ремонт.
Трубопроводную арматуру, установленную на газопроводах для горючих газов, рекомендуется периодически опробовать в рабочих условиях, независимо от параметров среды. При опробовании проверяют герметичность сальникового устройства и исправность действия затворного механизма без проверки герметичности уплотнительных поверхностей.
Сроки проверки состояния предохранительных и обратных клапанов, включая разбору и чистку, устанавливают в зависимости от характера работы и чистоты газа, но не реже 4000–4500 часов их работы.
Наиболее распространенными причинами выхода арматуры из строя являются:
–нарушение герметичности уплотнительных поверхностей;
–повреждение внутренней и наружной поверхности арматуры вследствие коррозии и эрозии;
–нарушение герметичности сальникового уплотнения;
–износ резьбы шпинделя (штока).
Ревизия, ремонт и испытание арматуры должны проводиться в специализированных мастерских. В отдельных случаях допускается производить ревизию арматуры путем ее разборки и осмотра на месте установки.
Обычно ревизию трубопроводной арматуры следует проводить в следующем объеме:
–внешний осмотр, проверка герметичности сальника и фланцевых соединений;
–разборка для осмотра уплотнительных поверхностей;
26
Стр. 26 |
ЭБ ПНИПУ (elib.pstu.ru) |
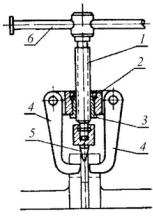
–тщательный осмотр отдельных деталей: шпинделя, клина или клапана, уплотнительных поверхностей, корпуса, сальника, а также крепежных деталей;
–замер толщины стенки корпуса и крышки (результаты замера заносят в паспорт трубопроводной арматуры)
–сборка арматуры для последующего проведения испытаний;
–проверка защиты электродвигателя, проверка надежности крепления клемм (для трубопроводной арматуры с электроприводом).
Основные операции технического обслуживания (ТО) трубопроводной арматуры заключаются в следующем:
–чистка наружной поверхности,
устранение подтеков разъемных соединений, путем обтягивания фланцев и сальника;
–замена прокладок;
–выбраковка и замена изношенных деталей;
–замена смазки в подшипниках и редукторе (для арматуры с механическим приводом);
–устранение плохого крепления клемм электродвигателя (для трубопроводной арматуре с электроприводом).
Конкретный способ ремонта трубопроводной арматуры зависит от ее конструктивного исполнения. Для этого трубопроводную арматуру снимают с трубопровода, а чтобы избежать повреждения зеркала фланца, применяют приспособление, показанное на рис. 27.
При ремонте вентиля его разбирают на стенде по соединению корпус – крышка. При необходимости осуществляют ремонт корпуса путем наплавки. Трещины заваривают после соответствующей
27
Стр. 27 |
ЭБ ПНИПУ (elib.pstu.ru) |
обработки. Однако подобное восстановление корпусов возможно только для арматуры, установленной на трубопроводах, транспортирующих не пожаро-взрывоопасные и токсичные вещества при давлении до 1,0 МПа и температуре до 200 °С.
Если толщина стенки корпуса трубопроводной арматуры достигла отбраковочной величины, арматура подлежит замене. Отбраковка литых изношенных корпусов независимо от условий работы производится, если толщина стенки достигла величины, приведенной в табл. 6.
Таблица 6
Значения отбраковочной толщины стенки
Dу, мм |
80 |
100 |
125 |
150 |
200 |
Предельная отбраковочная |
|
|
|
|
|
толщина стенки, мм |
4,0 |
5,0 |
5,5 |
6,0 |
6,5 |
Затем приступают к ремонту уплотнительных поверхностей. Если седло вентиля закреплено в корпусе запрессовкой, то оно может быть удалено с помощью приспособления, показанного на рис. 28. Когда седло посажено на резьбе, его вывинчивают с помощью специальных ключей.
Мелкие задиры, участки коррозии, эрозии и другие дефекты уплотнительных поверхностей не более 0,5 мм устраняют путем проточки, шлифовки абразивным кругом и притиркой. Притиркой устраняются дефекты глубиной не более 0,05 – 0,08 мм с пастой ГОИ или шлифовальным порошком, разведенным в масле. При этом можно применять приспособление, представленное на рис. 29.
Дефекты глубиной более 0,5 мм устраняют, как правило, наплавкой с последующей механической обработкой (проточка, шлифовка, притирка).
Уплотнительная поверхность шпинделя должна быть зеркальной и гладкой. Перед ремонтом шпиндель очищают от следов старой сальниковой набивки, ржавчины, грязи и промывают в кероси-
28
Стр. 28 |
ЭБ ПНИПУ (elib.pstu.ru) |
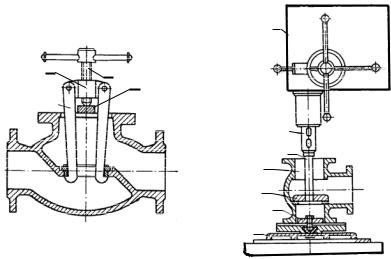
не. Как новые, так и восстановленные шпиндели на участке сальника шлифуют.
1
2 |
3 |
4 |
|
||
1 |
|
|
|
|
|
|
|
2 |
|
|
3 |
|
|
4 |
|
|
5 |
|
|
6 |
|
|
7 |
Рис. 28. Приспособление для |
Рис. 29. Приспособление для |
выпрессовки седла вентиля: |
притирки уплотнительных |
1 – захваты; 2 – траверса; |
поверхностей: 1 – сверлильный |
3 – упорный винт; 4 – подкладка |
станок; 2 – шпиндель; 3 – оправка; |
|
4 – корпус арматуры; 5 – притир; |
|
6 – прижимная шайба; 7 – плита |
Неглубокие дефекты шпинделя также устраняют притиркой. Внутренние поверхности деталей, сопрягаемые со шпинделем, проверяют также на чистоту и отсутствие овальности. После замены прокладок и сальниковой набивки собранную арматуру направляют на опрессовку.
При ремонте задвижек восстановлению подлежат:
–уплотнительные поверхности затвора;
–поверхность шпинделя и соприкасающиеся с ним детали;
–сальниковое уплотнение;
–уплотнительные поверхности фланцевых соединений;
–корпус задвижки.
29
Стр. 29 |
ЭБ ПНИПУ (elib.pstu.ru) |
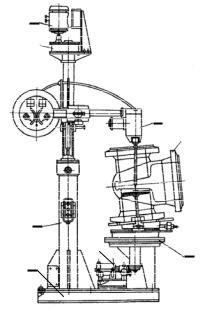
Корпуса чугунных задвижек при износе не ремонтируют, их заменяют новыми. Для задвижек, имеющих механический или электрический привод, производят:
–снятие редуктора и электродвигателя, разборку редуктора, смазку механической части электропривода;
–замену дефектных частей электрооборудования и редуктора;
–сборку и установку электропривода на задвижку. Уплотнительные поверхности задвижек (кольца) ремонтиру-
ют, как правило, без их снятия. Проточка колец ведется на токарном или расточном станке в специальном приспособлении, где за одну установку протачиваются обе поверхности. При необходимости производится наплавка уплотнительных поверхностей. Установка для наплавки представлена на рис. 30.
4
3
5
6
2
8 |
7 |
|
1
Рис. 30. Приспособление для наплавки: 1 – рама; 2 – стойка; 3 – редуктор; 4 – электродвигатель;
5 – сварочная головка; 6 – корпус наплавляемого изделия; 7 – вращающийся стол; 8 – привод вращающегося стола
30
Стр. 30 |
ЭБ ПНИПУ (elib.pstu.ru) |